精馏塔塔釜温度控制系统的设计
精馏塔温度控制系统设计
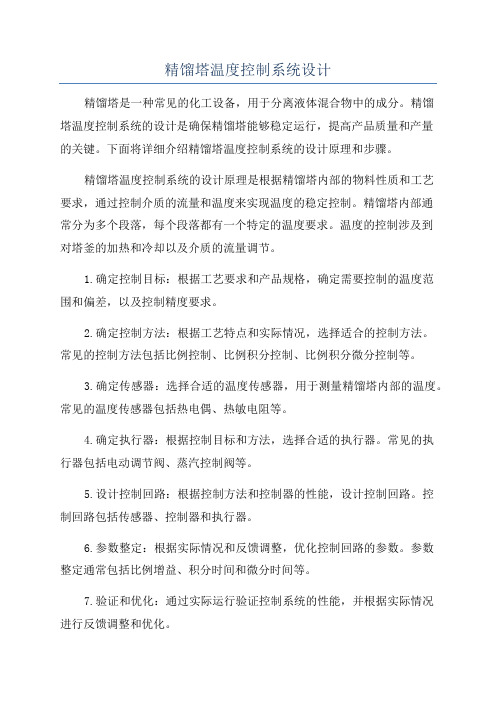
精馏塔温度控制系统设计精馏塔是一种常见的化工设备,用于分离液体混合物中的成分。
精馏塔温度控制系统的设计是确保精馏塔能够稳定运行,提高产品质量和产量的关键。
下面将详细介绍精馏塔温度控制系统的设计原理和步骤。
精馏塔温度控制系统的设计原理是根据精馏塔内部的物料性质和工艺要求,通过控制介质的流量和温度来实现温度的稳定控制。
精馏塔内部通常分为多个段落,每个段落都有一个特定的温度要求。
温度的控制涉及到对塔釜的加热和冷却以及介质的流量调节。
1.确定控制目标:根据工艺要求和产品规格,确定需要控制的温度范围和偏差,以及控制精度要求。
2.确定控制方法:根据工艺特点和实际情况,选择适合的控制方法。
常见的控制方法包括比例控制、比例积分控制、比例积分微分控制等。
3.确定传感器:选择合适的温度传感器,用于测量精馏塔内部的温度。
常见的温度传感器包括热电偶、热敏电阻等。
4.确定执行器:根据控制目标和方法,选择合适的执行器。
常见的执行器包括电动调节阀、蒸汽控制阀等。
5.设计控制回路:根据控制方法和控制器的性能,设计控制回路。
控制回路包括传感器、控制器和执行器。
6.参数整定:根据实际情况和反馈调整,优化控制回路的参数。
参数整定通常包括比例增益、积分时间和微分时间等。
7.验证和优化:通过实际运行验证控制系统的性能,并根据实际情况进行反馈调整和优化。
总之,精馏塔温度控制系统的设计是确保精馏塔能够稳定运行,提高产品质量和产量的关键。
设计步骤包括确定控制目标、控制方法、传感器和执行器的选择、设计控制回路、参数整定以及验证和优化。
合理的设计能够使温度控制更加稳定和可靠。
精馏塔釜温度与泡点温度的关系
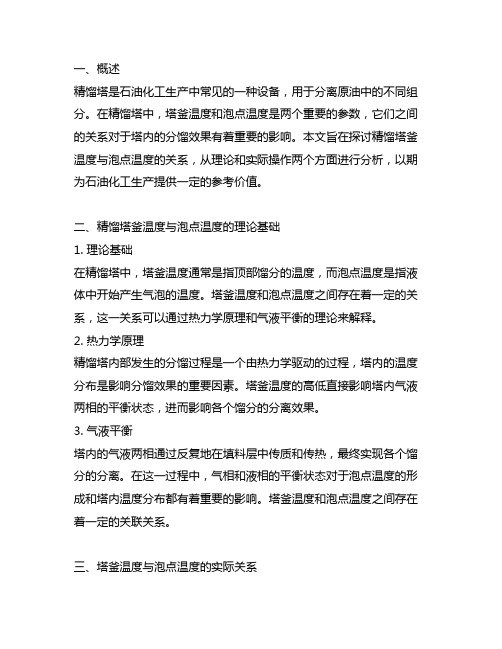
一、概述精馏塔是石油化工生产中常见的一种设备,用于分离原油中的不同组分。
在精馏塔中,塔釜温度和泡点温度是两个重要的参数,它们之间的关系对于塔内的分馏效果有着重要的影响。
本文旨在探讨精馏塔釜温度与泡点温度的关系,从理论和实际操作两个方面进行分析,以期为石油化工生产提供一定的参考价值。
二、精馏塔釜温度与泡点温度的理论基础1. 理论基础在精馏塔中,塔釜温度通常是指顶部馏分的温度,而泡点温度是指液体中开始产生气泡的温度。
塔釜温度和泡点温度之间存在着一定的关系,这一关系可以通过热力学原理和气液平衡的理论来解释。
2. 热力学原理精馏塔内部发生的分馏过程是一个由热力学驱动的过程,塔内的温度分布是影响分馏效果的重要因素。
塔釜温度的高低直接影响塔内气液两相的平衡状态,进而影响各个馏分的分离效果。
3. 气液平衡塔内的气液两相通过反复地在填料层中传质和传热,最终实现各个馏分的分离。
在这一过程中,气相和液相的平衡状态对于泡点温度的形成和塔内温度分布都有着重要的影响。
塔釜温度和泡点温度之间存在着一定的关联关系。
三、塔釜温度与泡点温度的实际关系1. 实际操作中的观察在精馏塔的实际操作中,操作人员通常会根据塔釜温度来调节操作参数,以达到预期的分馏效果。
在这一过程中,观察塔釜温度和各个馏分的泡点温度之间的变化关系,可以帮助操作人员更好地控制精馏塔的分馏效果。
2. 实验数据分析通过对精馏塔在不同操作条件下的实验数据进行分析,可以发现塔釜温度与泡点温度之间存在一定的相关性。
一般来说,塔釜温度的升高会导致各个馏分的泡点温度降低,反之亦然。
这一关系在一定程度上可以用来指导实际操作中的操作参数调节。
四、影响塔釜温度与泡点温度关系的因素1. 塔设计参数精馏塔的设计参数包括塔的高度、塔板间距、填料类型等,这些参数对于塔内温度分布和气液平衡状态有着重要的影响。
不同的设计参数会导致塔釜温度与泡点温度之间的关系呈现不同的规律。
2. 原料性质原料的性质对于精馏塔的分馏效果有着直接的影响,不同的原料性质会导致塔釜温度与泡点温度之间的关系发生变化。
精馏塔的控制

精馏塔的控制12.1 概述•精馏是石油、化工等众多生产过程中广泛应用的一种传质过程,通过精馏过程,使混合物料中的各组分分离,分别达到规定的纯度。
•分离的机理是利用混合物中各组分的挥发度不同(沸点不同),使液相中的轻组分(低沸点)和汽相中的重组分(高沸点)相互转移,从而实现分离。
•精馏装置由精馏塔、再沸器、冷凝冷却器、回流罐及回流泵等组成。
精馏塔的特点精馏塔是一个多输入多输出的多变量过程,内在机理较复杂,动态响应迟缓、变量之间相互关联,不同的塔工艺结构差别很大,而工艺对控制提出的要求又较高,所以确定精馏塔的控制方案是一个极为重要的课题。
而且从能耗的角度,精馏塔是三传一反典型单元操作中能耗最大的设备。
一、精馏塔的基本关系(1)物料平衡关系总物料平衡: F=D+B (12-1) 轻组分平衡:F z f =D x D +B x B (12-2) 联立(12-1)、(12-2)可得:(2)能量平衡关系 在建立能量平衡关系时,首先要了解分离度的概念。
所谓分离度s 可用下式表示:DB D f D BB f D x x x z F D x x z D Fx --=+-=)((12-3))1()1(D B B Dx x x x s --=(12-5)可见,随着s 的增大,x D 也增大,x B 而减小,说明塔系统的分离效果增大。
影响分离度s 的因素很多,如平均相对挥发度、理论塔板数、塔板效率、进料组分、进料板位置,以及塔内上升蒸汽量V 和进料F 的比值等。
对于一个既定的塔来说:式(12-6)的函数关系也可用一近似式表示: 或可表示为:式中β为塔的特性因子由上式可以看到,随着V /F 的增加,s 值提高,也就是x D 增加,x B 下降,分离效果提高了。
由于V 是由再沸器施加热量来提高的,所以该式实际是表示塔的能量对产品成分的影响,故称为能量平衡关系式。
由上分析可见,V /F 的增加,塔的分离效果提高,能耗也将增加。
典型化工单元的控制案例—精馏塔的控制(工业仪表自动化)
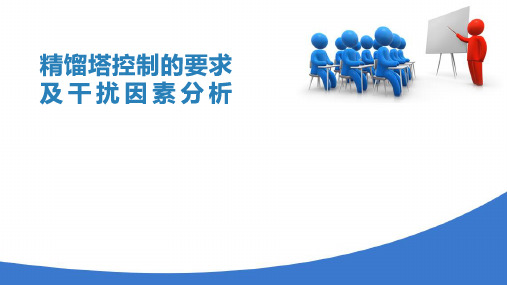
1、精馏塔温度控制为 什么常用灵敏板上的温度作 为被控变量?
2、精馏塔精馏段温度控 制为什么改变回流量而不改 变再沸器的加热量?
精馏塔是化工生产中重 要的分离设备,它利用混合 物中各组分挥发度的不同, 将混合物组分进行分离并达 到规定的纯度要求。
CONTENTS
02
-15%
03
03
有些干扰是可控的,有些干扰 是不可控的。一般对可控的主要 干扰可采用定值控制系统加以克 服。然而对不可控的干扰,它们 最终将反映在塔顶馏出物与塔底 采出量的产品质量上。
思考题
1、精馏塔液相进Байду номын сангаас流量 增加对塔顶产品有什么影响?
2、精馏塔塔压增加对塔 顶产品和塔底产品有什么影 响?
CONTENTS
01
塔压定值控制
进料流 量控制
回流量定 值控制
塔釜液 位控制
回流罐液 位控制
质量控制系统
03
塔压定值控制
A B
02
在实际生产过程中,由 于不同的物料性质,精馏塔 的类型不同,生产产品纯度 的要求不同等情况,可根据 现场具体情况采用各种不同 的控制方法。。
基于Aspen软件的甲醇精馏热焓控制方案设计
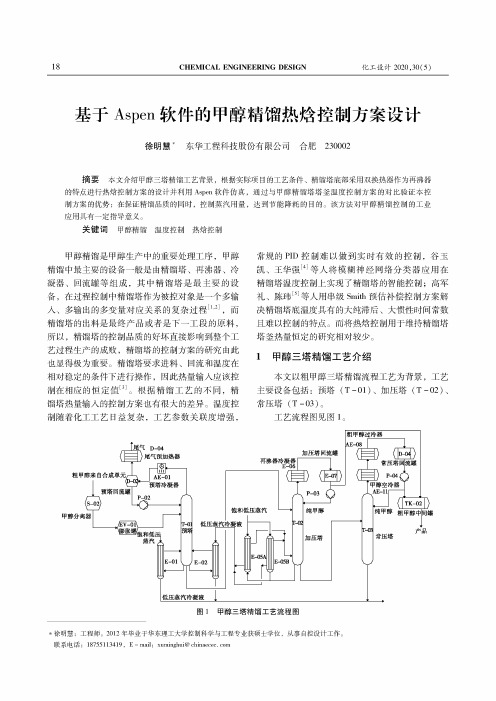
15CHEMICALENGINEERING DESIGN 化工设计2626,36(3)基于Aspen 软件的甲醇精馏热焓控制方案设计徐明慧*东华工程科技股份有限公司合肥234002扌商要 本文介绍甲醇三塔精馏工艺背景,根据实际项目的工艺条件、精馏塔底部采用双换热器作为再沸器的特点进行热焓控制方案的设计并利用Apen 软件仿真,通过与甲醇精馏塔塔釜温度控制方案的对比验证本控制方案的优势:在保证精馏品质的同时,控制蒸汽用量,达到节能降耗的目的。
该方法对甲醇精馏控制的工业 应用具有一定指导意义。
关键词甲醇精馏温度控制热焓控制甲醇精馏是甲醇生产中的重要处理工序,甲醇精馏中最主要的设备一般是由精馏塔、再沸器、冷凝器、回流罐等组成,其中精馏塔是最主要的设备,在过程控制中精馏塔作为被控对象是一个多输 入、多输出的多变量对应关系的复杂过程[1,],而精馏塔的出料是最终产品或者是下一工段的原料,所以,精馏塔的控制品质的好坏直接影响到整个工艺过程生产的成败,精馏塔的控制方案的研究由此也显得极为重要。
精馏塔要求进料、回流和温度在 相对稳定的条件下进行操作,因此热量输入应该控 制在相应的恒定值⑶。
根据精馏工艺的不同,精馏塔热量输入的控制方案也有很大的差异。
温度控 制随着化工工艺日益复杂,工艺参数关联度增强,常规的pis 控制难以做到实时有效的控制,谷玉凯、王华强⑷等人将模糊神经网络分类器应用在精馏塔温度控制上实现了精馏塔的智能控制;高军礼、陈玮J .等人用串级SmitP 预估补偿控制方案解决精馏塔底温度具有的大纯滞后、大惯性时间常数且难以控制的特点。
而将热焓控制用于维持精馏塔塔釜热量恒定的研究相对较少。
1甲醇三塔精馏工艺介绍本文以粗甲醇三塔精馏流程工艺为背景,工艺主要设备包括:预塔(T-01)、加压塔(T-02)、常压塔(T-03)。
工艺流程图见图1。
徐明慧:工程师。
2012年毕业于华东理工大学控制科学与工程专业获硕士学位,从事自控设计工作联系电话:187****3419, E-mail :*********************2424,34(5)徐明慧基于Aspen软件的甲醇精馏热焓控制方案设计10精馏预塔底部出料工艺流程见图2。
精馏塔的控制方式
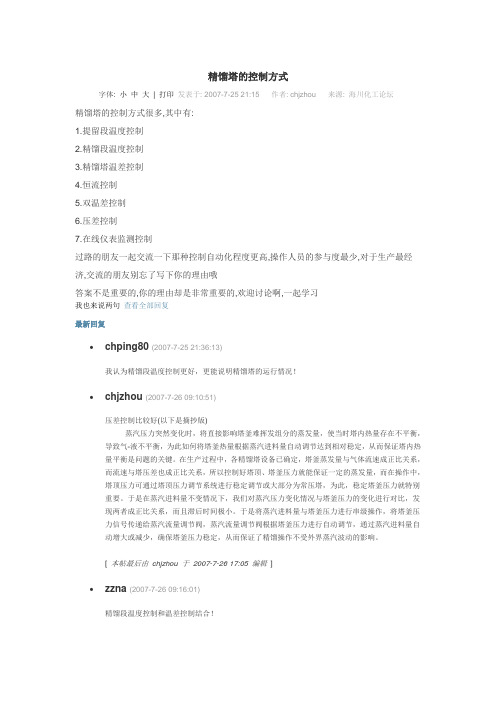
精馏塔的控制方式字体: 小中大| 打印发表于: 2007-7-25 21:15 作者: chjzhou 来源: 海川化工论坛精馏塔的控制方式很多,其中有:1.提留段温度控制2.精馏段温度控制3.精馏塔温差控制4.恒流控制5.双温差控制6.压差控制7.在线仪表监测控制过路的朋友一起交流一下那种控制自动化程度更高,操作人员的参与度最少,对于生产最经济,交流的朋友别忘了写下你的理由哦答案不是重要的,你的理由却是非常重要的,欢迎讨论啊,一起学习我也来说两句查看全部回复最新回复∙chping80 (2007-7-25 21:36:13)我认为精馏段温度控制更好,更能说明精馏塔的运行情况!∙chjzhou (2007-7-26 09:10:51)压差控制比较好(以下是摘抄版)蒸汽压力突然变化时,将直接影响塔釜难挥发组分的蒸发量,使当时塔内热量存在不平衡,导致气-液不平衡,为此如何将塔釜热量根据蒸汽进料量自动调节达到相对稳定,从而保证塔内热量平衡是问题的关键。
在生产过程中,各精馏塔设备已确定,塔釜蒸发量与气体流速成正比关系,而流速与塔压差也成正比关系,所以控制好塔顶、塔釜压力就能保证一定的蒸发量,而在操作中,塔顶压力可通过塔顶压力调节系统进行稳定调节或大部分为常压塔,为此,稳定塔釜压力就特别重要。
于是在蒸汽进料量不变情况下,我们对蒸汽压力变化情况与塔釜压力的变化进行对比,发现两者成正比关系,而且滞后时间极小。
于是将蒸汽进料量与塔釜压力进行串级操作,将塔釜压力信号传递给蒸汽流量调节阀,蒸汽流量调节阀根据塔釜压力进行自动调节,通过蒸汽进料量自动增大或减少,确保塔釜压力稳定,从而保证了精馏操作不受外界蒸汽波动的影响。
[本帖最后由chjzhou 于2007-7-26 17:05 编辑]∙zzna (2007-7-26 09:16:01)精馏段温度控制和温差控制结合!∙weiqj (2007-7-26 15:49:50)3#楼是从一个叫做“好男人”的博客中的《精馏塔操作及自动控制系统的改进》摘抄其中一段。
精馏塔PID控制系统简介

精馏塔PID控制系统简介一、PID控制系统单回路控制系统通常是指由一个检测元件及一个变送器、一个控制器、一个执行器、一个被控对象所组成的一个闭合回路的控制系统,又称简单控制系统或单参数控制系统。
单回路控制系统是所有过程控制系统中最简单、最基本、应用最广泛和最成熟的一种,约占控制回路的80%以上,适用于被控对象滞后时间较小、负荷和干扰变化不大、控制质量要求不很高的场合。
控制器在冶金、石油、化工、电力等各种工业生产中应用极为广泛。
要实现生产过程自动控制,无论是简单的控制系统,还是复杂的控制系统,控制器都是必不可少的。
控制器是工业生产过程自动控制系统中的一个重要组成部分。
它把来自检测仪表的信号进行综合,按照预定的规律去控制执行器的动作,使生产过程中的各种被控参数,如温度、压力、流量、液位、成分等符合生产工艺要求。
主要介绍在工业控制中有一定影响力的DDZ-Ⅲ型控制器的控制规律、构成原理和使用方法。
二、控制器的控制规律:在自动控制系统中,由于扰动作用的结果使被控参数偏离给定值,从而产生偏差,控制器将偏差信号按一定的数学关系,转换为控制作用,将输出作用于被控过程,以校正扰动作用所造成的影响。
被控参数能否回到给定值上,以怎样的途径、经过多长时间回到给定值上来,即控制过程的品质如何,不仅与被控过程的特性有关,而且也与控制器的特性,即控制器的规律有关。
所谓控制器的控制规律,就是指控制器的输出信号与输入信号之间随时间变化的规律。
这种规律反映了控制器本身的特性。
控制器的基本控制规律由比例(P)、积分(I)、微分(D)三种。
这三种控制规律各有其特点。
三、精馏塔主要测量控制点的测控方法、装置和设备的报警连锁简介1、塔釜上升蒸汽量的控制:塔釜上升蒸汽量是由塔釜加热电压来决定的,控制塔釜加热电压即可控制塔釜上升蒸汽量执2、回流比控制:3、塔釜液位控制液位设置有上、下限报警功能:当塔釜液位超出上限报警值时,仪表输出报警信号给塔釜常闭电磁阀,电磁阀接收到信号后开启,塔釜排液;当塔釜液位降至上限报警值以下时,仪表停止输出信号,电磁阀关闭,塔釜停止排液。
过程控制课程设计
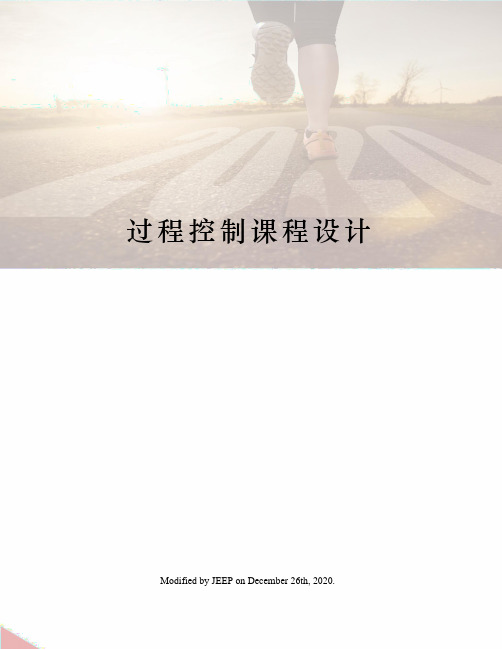
过程控制课程设计 Modified by JEEP on December 26th, 2020.辽宁工业大学过程控制系统课程设计(论文)题目:精馏塔塔内压力控制系统设计院(系):专业班级:学号:学生姓名:指导教师:起止时间:课程设计(论文)任务及评语院(系):电气工程学院教研室:测控技术与仪器注:成绩:平时20% 论文质量60% 答辩20% 以百分制计算摘要精馏塔是石油、化学加工工业(CPI)中使用量最大、能耗最高、应用面极广的分离单元操作设备。
本设计采用单回路控制系统对塔内压力进行实时控制,采用PID算法的DTZ—2100控制器对HK-613系列通用型压力变送器采集到的塔内压力值进行处理,并将控制信号传递给ZXS型新系列气动薄膜角形单座调节阀,令其对冷却量进行控制,从而达到对塔内压力的控制。
精馏塔的控制最终目标是:在保证产品质量的前提下,使回收率最高,能耗最小,或使总收益最大生产设备自动化程度的提高,有利于降低工厂成本、促进生产线的柔性化和集成化,有利于提高产品的产量、质量以及产品的竞争力。
从某种意义上说,高效的精馏塔控制技术为我们创造了不可忽视的经济效益和社会效益。
关键词:精馏塔;分离单元;PID算法目录第1章绪论研究背景及意义精馏是化工、石油化工、炼油生产过程中应用极为广泛的传质传热过程。
而石油化工是基础性产业,它为农业、能源、交通、机械、电子、纺织、轻工、建筑、建材等工农业和人民日常生活提供配套和服务,在国民经济中占有举足轻重的地位,在现代生活中,几乎随时随地都离不开化工产品,从衣、食、住、行等物质生活到文化艺术、娱乐等精神生活,都需要化工产品为之服务。
精馏的目的是利用混合液中各组分具有不同挥发度,将各组分分离并达到规定的纯度要求。
精馏过程的实质是利用混合物中各组分具有不同的挥发度,即同一温度下各组分的蒸汽分压不同,使液相中轻组分转移到气相,气相中的重组分转移到液相,实现组分的分离。
1.精馏过程的核心在于回流,而回流必须消耗大量能量。
- 1、下载文档前请自行甄别文档内容的完整性,平台不提供额外的编辑、内容补充、找答案等附加服务。
- 2、"仅部分预览"的文档,不可在线预览部分如存在完整性等问题,可反馈申请退款(可完整预览的文档不适用该条件!)。
- 3、如文档侵犯您的权益,请联系客服反馈,我们会尽快为您处理(人工客服工作时间:9:00-18:30)。
辽宁工业大学过程控制系统课程设计(论文)题目:精馏塔塔釜温度控制系统的设计院(系):指导教师:(签字)起止时间:课程设计(论文)任务及评语院(系):电气工程学院教研室:自动化注:成绩:平时20% 论文质量60% 答辩20% 以百分制计算摘要本系统利用工业生产过程控制采用串级控制系统实现精馏塔塔釜温度控制系统。
通过选用铂铑10-铂热电偶传感器、ZMAP-16P DN15气动调节阀、DT2031数字调节器、热电偶温度变送器来实现。
系统设计主要包括控制方案的设计和系统各仪表选型,软件设计,系统仿真四大部分。
软件设计采用DCS组态来完成,并完成了系统监控画面。
系统仿真采用MATLAB进行仿真,并得出仿真图。
本系统便是基于工业生产过程控制采用串级控制系统实现精馏塔塔釜温度控制系统,通过对工业生产过程控制,来实现对精馏塔塔釜温度的控制。
此次设计就是要设计一个精馏塔塔釜温度的串级控制系统。
要求当物料进入精馏塔时,塔釜的温度可控并且温度恒定,保证生产的连续性。
关键词:精馏;温度控制;PID目录第1章绪论 (1)第2章控制方案的设计 (3)2.1设计要求 (3)2.2方案设计 (3)2.2.1 塔釜温度的前馈控制 (4)2.2.2 塔釜温度的串级控制 (5)2.2.3 塔釜温度的反馈控制 (6)第3章系统各仪表选型 (8)3.1温度传感器的选择 (8)3.2执行器的选择 (8)3.3调节器的选择 (9)3.4压力变送器的选择 (9)3.5温度变送器的选择 (10)3.6控制器的正反作用选择 (10)第4章软件设计 (11)4.1系统控制流程图 (11)4.2DCS组态 (11)第5章系统仿真 (14)5.1PID控制器的参数整定 (14)5.2凑试法确定PID参数 (14)5.3切线法确定被控对象的传函 (15)5.4系统MATLAB仿真分析 (17)第6章课程设计总结 (19)参考文献 (20)第1章绪论精馏塔是进行精馏的一种塔式汽液接触装置。
有板式塔与填料塔两种主要类型。
根据操作方式又可分为连续精馏塔与间歇精馏塔。
蒸气由塔底进入。
蒸发出的气相与下降液进行逆流接触,两相接触中,下降液中的易挥发(低沸点)组分不断地向气相中转移,气相中的难挥发(高沸点)组分不断地向下降液中转移,气相愈接近塔顶,其易挥发组分浓度愈高,而下降液愈接近塔底,其难挥发组分则愈富集,从而达到组分分离的目的。
由塔顶上升的气相进入冷凝器,冷凝的液体的一部分作为回流液返回塔顶进入精馏塔中,其余的部分则作为馏出液取出。
塔底流出的液体,其中的一部分送入再沸器,加热蒸发成气相返回塔中,另一部分液体作为釜残液取出。
蒸馏的基本原理是将液体混合物多次部分气化和部分冷凝,利用其中各组份挥发度不同(相对挥发度,α)的特性,实现分离目的的单元操作。
蒸馏按照其操作方法可分为:简单蒸馏、闪蒸、精馏和特殊精馏等。
近年来出现的超重力精馏技术,利用高速旋转产生的数百至千倍重力的超重力场代替常规的重力场,极大地强化气液传质过程,将传质单元高度降低1个数量级。
从而使巨大的塔设备变为高度不到2米的超重力精馏机,达到增加效率、缩小体积的目的。
超重力精馏改变了传统的塔设备精馏模式,只要在室内厂房里就可以实现连续精馏过程。
对社会的发展而言可节省钢材资源,延长地球资源的使用年限;对企业的发展而言,可以节约场地与空间资源,减少污染排放,提高产品质量,改善经营管理模式,降低生产劳动强度,增加生产的安全性。
精馏塔是化工生产中分离互溶液体混合物的典型分离设备。
它是依据精馏原理对液体进行分离,即在一定压力下,利用互溶液体混合物各组分的沸点或饱和蒸汽压不同,使轻组份(即沸点较低或饱和蒸汽压较高的组分)汽化。
经多次部分液相汽化和部分气相冷凝,使气相中的轻组分和液相中的重组分浓度逐渐升高,也就是说在提馏段上升的轻组分的易挥发组分逐渐增多,难挥发组分逐渐减少,而下降液相中易挥发组分逐渐减少,难挥发组分逐渐增多,从而实现分离的目的,满足化工连续化生产的需要。
精馏塔塔釜温度控制的稳定与否直接决定了精馏塔的分离质量和分离效果,控制精馏塔的塔釜温度是保证产品高效分离,进一步得到高纯度产品的重要手段。
维持正常的塔釜温度,可以避免轻约分流失,提高物料的回收率;也可减少残余物料的污染作用。
影响精馏塔温度不稳定的因素主要是来自外界来的干扰(如进料流量,温度及成分等的变化对温度的影响)。
一般情况下精馏塔塔釜的温度,我们是通过控制精馏塔釜内灵敏板的温度来控制的。
灵敏板是当外界条件或负荷改变时精馏塔内温度变化最灵敏的一块塔板。
以往调节只是采用灵敏板温度调节器单一回路调节,调节反应慢,时间滞后,对精馏操作而言,产品的纯度很难保证。
从上述干扰分析来看,有些干扰是可控的,有些干扰是不可控的。
从而选择一种可靠并且稳定的控制系统来控制精馏塔塔釜的温度是非常重要的。
第2章控制方案的设计2.1设计要求精馏塔塔釜温度控制系统的设计要求如下:1.塔釜温度控制在800±0.5℃;2.生产过程中蒸汽压力变化剧烈,而且幅度大,要保证精馏塔正常工作;3.塔釜及相关期间要经济实用。
2.2方案设计精馏塔的干扰因素:1.进料量波动的影响;2.进料成分波动的影响;3.进料温度波动的影响;4.蒸汽压力波动的影响;5.回流量和冷剂量波动的影响。
精馏塔的扰动如图2-1:图2-1系统扰动根据扰动的分析,系统设计方案主要考虑前馈,反馈和串级三种控制方案。
首先介绍什么叫静态前馈控制,即静态前馈控制的原理。
所谓静态前馈控制原理就是指前馈控制器的输出信号仅仅随着输入信号(干扰信号)d 大小的函数,而与时间因子t 无关。
因此,前馈控制作用可以简化为:(2-1)通常将上式的关系近似的表示为线性关系,则前馈控制器就仅仅参考器静态放大系数作为矫正的依据,即:0/)(K K K s W d f t -== (2-2)式中,d K ,0K 分别为干扰通道和控制通道的放大系数,一般来说f K 可以用实验方法来获得,如果有条件列写对象有关参数的静态方程,则可以通过计算来确定。
在精馏塔塔釜的温度控制中,扰动可以测量但是不好控制,并且干扰幅度较大。
蒸汽压力的变化是塔釜温度的主要干扰量,控制对象则是塔釜的温度。
塔釜温度前馈控制的系统框图和塔釜温度前馈控制工节结点图如2-2、2-3所示:图2-2塔釜温度前馈控制的系统框图)(d f M f =串级控制系统就是两只调节器串联起来工作,其中一个调节器的输出作为另一个调节器的给定值的系统。
整个系统包括两个控制回路,主回路和副回路。
副回路由副变量检测变送、副调节器、调节阀和副过程构成;主回路由主变量检测变送、主调节器、副调节器、调节阀、副过程和主过程构成。
一次扰动:作用在主被控过程上的,而不包括在副回路范围内的扰动。
二次扰动:作用在副被控过程上的,即包括在副回路范围内的扰动。
为了提高精馏效率和保证产品纯度,我们采用灵敏板温度调节器与再沸器加热蒸汽流量调节器串级控制系统来对灵敏板温度进行控制。
其中灵敏板温度调节器是主调节器,再沸器加热蒸汽流量调节器是副调节器。
塔釜温度串级控制工艺结点图如2-4所示:塔釜温度串级控制示意图如图2-5所示:图2-4塔釜温度串级控制工艺节点图图2-5塔釜温度串级控制的系统框图通过实际改造和使用,串级调节与单回路控制相比较,串级控制有许多优点:1、抗干扰性强。
由于主回路的存在,进入副回路的干扰影响大为减小。
同时,由于串级控制系统增加了一个副回路,具有主、副两个调节器,大大提高了调节器的放大倍数,从而也就提高了对干扰的克服能力,尤其对于进入副回路的干扰。
表现更为突出。
2、及时性好。
串级控制对克服容量滞后大的对象特别有效。
3、适应能力强。
串级控制系统就其主回路来看,它是一个定值控制系统,但其副回路对主调节器来说,却是一个随动控制系统,主调节器能够根据对象操作条件和负荷的变化情况不断纠正副调节器的给定值,以适应操作条件和负荷的变化。
通过采用串级控制系统,塔釜温度控制更加平稳,产品纯度很高,随着控制系统软件和硬件的不断发展和完善,计算机集散型控制系统的应用和普及,精馏塔的分离质量将会越来越好,分离精度也将会越来越高。
2.2.3塔釜温度的反馈控制在反馈控制系统中,既存在由输入到输出的信号前向通路,也包含从输出端到输入端的信号反馈通路,两者组成一个闭合的回路。
反馈控制系统由控制器、控制对象和反馈通路组成如图2-3所示。
图中带叉号的圆圈为比较环节,用来将输入与输出相减,给出偏差信号。
这一环节在具体系统中可能与控制器一起统称为调节器。
以炉温控制为例,受控对象为炉子;输出变量为实际的炉子温度;输入变量为给定常值温度,一般用电压表示。
炉温用热电偶测量,代表炉温的热电动势与给定电压相比较,两者的差值电压经过功率放大后用来驱动相应的执行机构进行控制。
塔釜温度反馈控制的系统框图和塔釜温度反馈控制的工艺节点图如图2-6、2-7所示:图2-6 塔釜温度反馈控制的系统框由于前馈控制因不含时间因子,比较简单,在一般情况下,不需要专用的补偿器,单元组合仪表便可以满足使用要求。
由于本设计主要考虑物料、压力等物理量对精馏塔釜温度的影响,并且干扰变化剧烈,幅度大,有时从0.5Mpa突然下降到0.3Mpa,压力变化40%。
干扰幅度较大,所以应用串级控制系统。
第3章系统各仪表选型3.1温度传感器的选择热电偶作为温度传感元件,能将温度信号转换成电动势(mV)信号,配以测量毫伏的指示仪表或变送器可以实现温度的测量指示或温度信号的转换。
具有稳定、复现性好、体积小、响应时间较小等优点、热电偶一般用于500°C以上的高温,可以在1600°C高温下长期使用。
热电阻也可以作为温度传感元件。
大多数电阻的阻值随温度变化而变化,如果某材料具备电阻温度系数大、电阻率大、化学及物理性能稳定、电阻与温度的关系接近线性等条件,就可以作为温度传感元件用来测温,称为热电阻。
热电阻分为金属热电阻和半导体热敏电阻两类。
大多数金属热电阻的阻值随其温度升高而增加,而大多数半导体热敏电阻的阻值随温度升高而减少。
铂铑10-铂热电偶传感器测温范围在0~1600℃,WRP型铂铑10-铂热电偶性能可靠、耐高温、抗氧化,可长期工作在0~1600℃环境下。
3.2执行器的选择执行器在控制系统中夜起着重要的作用,它直接实施控制系统的动作就好像人体的五官和手脚一样,大脑是调节器,而手就是执行器。
执行器是一种现场类仪表因此它的精度、使用寿命、抗干扰和环境的适应能力等就是人们所关注的指标。
控制器的动作是由调节器的输出信号通过各种执行机构来实现的,在由电信号作为控制信号的控制系统中,目前广泛使用的是以下三种控制方式:1.按动力来源分,有气动和电动两大类;2.按动作极性分,有正作用和反作用两大类;3.按动作特性分,有比例和积分两大类。