锥齿轮计算
锥齿轮设计计算

锥齿轮的设计计算
.选择齿轮的资料和精度等级
资料选择查表选用大小齿轮资料均为45号钢调质。
小齿轮齿面硬度为250HBS,大齿轮齿面硬度为220HBS。
250HBS-220HBS=30HBS;切合要求;220<250<350;为软齿面。
齿轮为8级精度。
3. 试选小齿轮齿数=20 = = =70。
二.按齿面接触疲惫强度设计
由齿面接触疲惫强度设计公式
1. 试选载荷系数。
计算小齿轮传达的转矩
=
3.由表选用齿宽系数。
4.确立弹性影响系数据表得。
5.确立地区载荷系数标准直齿圆锥齿轮传动。
6.依据循环次数公式计算应力循环次数
=
查图得接触疲惫寿命系数
查图得排除疲惫极限应力
计算排除疲惫许用应力
取无效概率为1%,安全系数
=540MPa
MPa
由接触强度计算小齿轮的分度圆直径
计算齿轮的圆周速度
计算载荷系数查表得
接触强度载荷系数
按实质的载荷系数校订分度圆直径
取标准m=5.
计算齿轮的有关参数
圆整并确立齿宽三.校核齿根曲折疲惫强度确立曲折强度载荷系数
1.计算当量齿数
查表得
计算曲折疲惫许用应力
由图得弯曲疲劳寿命系数
按脉动循环变应力确立许用应力
校核曲折强度
依据曲折强度条件公式进行校核
知足曲折强度,所选参数适合。
参照资料:
1. 《机械设计手册》第四版化学工业第一版社第3卷成大先主编。
2. 《机械设计同步指导及习题全解》中国矿业大学第一版社
3.。
锥齿轮模数的概念

锥齿轮模数的概念
锥齿轮模数是指齿轮齿廓上每毫米的齿数。
在计算锥齿轮传动时,可以根据齿数和齿轮直径计算出模数。
锥齿轮模数的选择决定了齿轮的尺寸、齿廓的形状和齿轮的传动性能。
锥齿轮模数的计算公式为:
模数= 齿数/ 齿轮直径
锥齿轮的模数越大,齿轮的齿数相对较小,齿轮齿廓上的齿数密度较低,齿轮轮齿的宽度较大,可以承受更大的负载和力矩。
因此,大模数的锥齿轮适用于大功率传动。
相反,小模数的锥齿轮齿数相对较大,齿轮的齿数密度较高,齿轮齿廓上的齿数相对较小,齿轮轮齿的宽度较小,适用于转速较高、精度要求较高或空间受限的传动装置。
锥齿轮模数的选择需要考虑传动装置的具体要求和设计限制,包括负载、转速、精度、噪声、可靠性等因素。
标准直齿锥齿轮计算公式

标准直齿锥齿轮计算公式直齿锥齿轮是一种常见的机械传动装置,它能够实现两轴的平行传动,广泛应用于各种机械设备中。
在设计和制造直齿锥齿轮时,需要准确计算其参数,以确保其性能和传动效率。
本文将介绍标准直齿锥齿轮的计算公式,帮助读者更好地理解和应用这一重要的机械传动元件。
1. 齿轮传动基本参数。
在计算直齿锥齿轮的参数之前,我们首先需要了解一些基本的齿轮传动参数。
这些参数包括模数、齿数、齿宽系数、压力角等。
模数是齿轮齿数与齿轮直径的比值,通常用m表示;齿数表示齿轮上的齿的数量,用z表示;齿宽系数是齿轮齿宽与模数的比值,用b/m表示;压力角是齿轮齿廓曲线与齿轮轴线的夹角,通常用α表示。
这些参数将在后续的计算中起到重要的作用。
2. 直齿锥齿轮计算公式。
(1)齿轮传动比的计算。
齿轮传动比是指齿轮输入轴与输出轴的转速比。
对于直齿锥齿轮,其传动比可以通过以下公式计算:i = z2 / z1。
其中,i表示传动比,z1和z2分别表示从动齿轮和主动齿轮的齿数。
通过计算传动比,可以确定齿轮传动系统的速比关系,为后续的参数计算提供基础。
(2)模数的计算。
模数是齿轮的重要参数之一,它直接影响着齿轮的尺寸和传动性能。
对于直齿锥齿轮,其模数可以通过以下公式计算:m = (z1 + z2)/(2 i)。
其中,m表示模数,z1和z2分别表示从动齿轮和主动齿轮的齿数,i表示传动比。
通过计算模数,可以确定齿轮的尺寸和齿廓参数,为后续的设计提供基础数据。
(3)齿轮齿距的计算。
齿距是指齿轮齿廓曲线上相邻两齿顶点之间的距离,它是齿轮传动中重要的参数之一。
对于直齿锥齿轮,其齿距可以通过以下公式计算:p = π m / sin(α)。
其中,p表示齿距,m表示模数,α表示压力角。
通过计算齿距,可以确定齿轮齿廓曲线的形状和尺寸,为齿轮的加工和装配提供基础数据。
(4)齿轮齿宽的计算。
齿宽是指齿轮齿面上的有效传动宽度,它直接影响着齿轮的传动能力和使用寿命。
锥齿轮设计计算
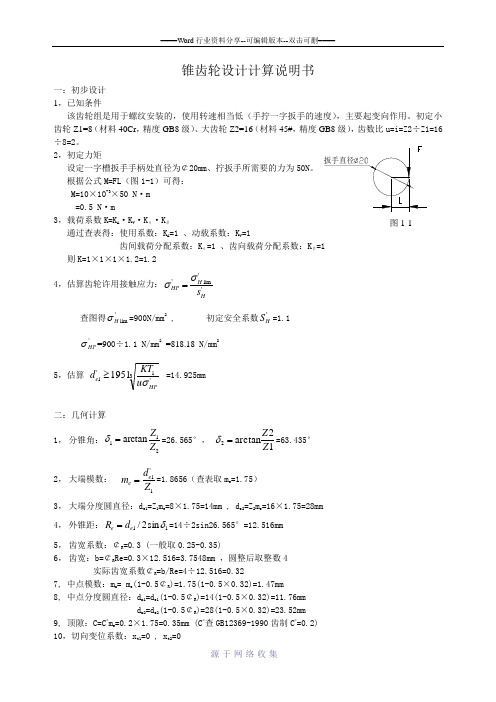
锥齿轮设计计算说明书一:初步设计1,已知条件该齿轮组是用于螺纹安装的,使用转速相当低(手拧一字扳手的速度),主要起变向作用。
初定小齿轮Z1=8(材料40Cr ,精度GB8级)、大齿轮Z2=16(材料45#,精度GB8级),齿数比u=i=Z2÷Z1=16÷8=2。
2,初定力矩设定一字槽扳手手柄处直径为¢20mm 、拧扳手所需要的力为50N 。
根据公式M=FL (图1-1)可得:M=10×10-3×50 N ·m=0.5 N ·m3,载荷系数K=K A ·K V ·K α·K β通过查表得:使用系数:K A =1 、动载系数:K V =1齿间载荷分配系数:K α=1 、齿向载荷分配系数:K β=1则K=1×1×1×1.2=1.24,估算齿轮许用接触应力:''lim 'HH HP s σσ=查图得'lim H σ=900N/mm 2 , 初定安全系数'H S =1.1'HPσ=900÷1.1 N/mm 2 =818.18 N/mm 25,估算 3'1'11951HPe u KT d σ≥ =14.925mm二:几何计算1, 分锥角:211arctan Z Z =δ=26.565°, 12arctan 2Z Z =δ=63.435°2, 大端模数:1'1Z d m e e ==1.8656(查表取m e =1.75)3, 大端分度圆直径:d e1=Z 1m e =8×1.75=14mm , d e2=Z 2m e =16×1.75=28mm4, 外锥距:11sin 2/δe e d R ==14÷2sin26.565°=12.516mm5, 齿宽系数:¢R =0.3 (一般取0.25-0.35)6, 齿宽:b=¢R Re=0.3×12.516=3.7548mm ,圆整后取整数4实际齿宽系数¢R =b/Re=4÷12.516=0.327, 中点模数:m m = m e (1-0.5¢R )=1.75(1-0.5×0.32)=1.47mm8, 中点分度圆直径:d m1=d e1(1-0.5¢R )=14(1-0.5×0.32)=11.76mmd m2=d e2(1-0.5¢R )=28(1-0.5×0.32)=23.52mm9, 顶隙:C=C *m e =0.2×1.75=0.35mm (C *查GB12369-1990齿制C *=0.2)10,切向变位系数:x t1=0 , x t2=0图1-111,高变位系数:x 1=0 ,x 2=012,大端齿顶高:h a1=(1+x 1)m e =1.75mm , h a2=(1+x 1) m e =1.75mm13,大端齿根高:h f1=(1+C *- x 1)m e =2.1mm ,h f2=(1+C *- x 2)m e =2.1mm14,全齿高:h=(2+ C *)m e =3.85mm15,齿根高:==e f f R h 11arctan θ9.5°,21f f θθ==9.5°16,齿顶角:θa1=θf2=9.5°, θa2=θf1=9.5°(采用等顶隙收缩齿) 17,顶锥角:δa1=δ1+θa1=36.065°, δa2=δ2+θa2=72.935°18,根锥角:δf1=δ1-θf1=17.065°, δf2=δ2-θf2=53.935°19,大端齿顶圆直径:d ae1=d e1+2h a1cos δ1=17.1304mm , d ae2=d e2+2h a2cos δ2=29.5645mm 20,冠顶距:1121sin 2δa e k h d A -==13.21775mm ,2212sin 2δa e k h d A -==5.4348mm 21,大端分度圆弧齿厚:s 1= m e (π/2+2x 1tan α+x t1)=2.7475mm , s 2=πm e - s 1=2.7475mm22,大端分度圆弦齿厚:=-=)61(212111e d s s s 2.73mm , =-=)61(222222e d s s s 2.743mm 23,大端分度圆弦齿高:=+=1121114cos e a d s h h δ 1.87mm ,=+=2222224cos e a d s h h δ 1.78mm 24,当量齿数:==111cos δz z v 8.9445(小于直齿圆柱齿轮的根切齿数17,但其工作载荷平稳、转速极小、安装空间小,故不做调整。
锥齿轮减速比计算公式

锥齿轮减速比计算公式全文共四篇示例,供读者参考第一篇示例:锥齿轮是一种常用的减速装置,广泛应用于机械传动系统中。
在设计和使用锥齿轮减速器时,减速比是一个重要的参数,它决定了输出轴的转速与输入轴的转速之间的关系。
如果要计算锥齿轮减速比,可以借助以下公式:减速比=(z1/z2)*(cosα1/cosα2)z1和z2分别为小齿轮和大齿轮的齿数,α1和α2分别为小齿轮和大齿轮的压力角。
在实际应用中,通常会根据设计要求和具体情况选择合适的齿轮参数来计算减速比。
下面将详细介绍如何应用这个公式来计算锥齿轮减速比。
要确定小齿轮和大齿轮的齿数z1和z2。
这是锥齿轮减速比计算的基础,齿数的选择通常要考虑到输出轴的扭矩需求和传动比例的要求。
一般来说,齿数较多的齿轮会提供更高的减速比,从而可以实现更大的输出扭矩。
要确定小齿轮和大齿轮的压力角α1和α2。
压力角通常为20度或30度,是影响齿轮传动效率和运行平稳性的重要参数。
压力角越大,齿轮传动的效率就越高,但同时也会增加传动噪音和振动。
在确定了齿数和压力角之后,就可以利用上面的公式来计算锥齿轮的减速比了。
假设小齿轮的齿数为20,压力角为30度,大齿轮的齿数为60,压力角为20度,那么减速比可以计算如下:减速比=(20/60)*(cos30/cos20)≈0.33*0.928≈0.306这样就得到了这组锥齿轮的减速比为0.306。
这意味着输出轴的转速是输入轴的转速的0.306倍,也就是说输出轴的转速比输入轴的转速要慢0.306倍。
锥齿轮减速比的计算可以帮助工程师设计和优化传动系统,确保系统的运行稳定性和性能指标的实现。
通过合理选择齿轮参数,可以实现不同的减速比,满足不同应用场景下的需求。
在实际工程设计中,需要考虑到齿轮的制造工艺、材料强度和耐磨性等因素,以及整个传动系统的工作环境和负载情况。
在使用锥齿轮减速器时,除了减速比的计算,还需要综合考虑各种因素,确保传动系统的可靠性和稳定性。
锥齿轮的圆周力

锥齿轮的圆周力是指在锥齿轮传动中,作用在齿面上的法向力在圆周方向上的分力。
锥齿轮的圆周力可以通过以下公式计算:
F_t=\frac{2T}{d_1}
其中,F_t为圆周力,T为传递的转矩,d_1为小齿轮的分度圆直径。
需要注意的是,上述公式仅适用于圆柱直齿轮的情况。
对于锥齿轮,由于其齿形和传动方式的复杂性,计算圆周力需要考虑更多的因素,如齿轮的几何参数、传动比、载荷分布等。
在实际应用中,通常使用专业的齿轮设计软件或参考相关的工程手册来计算锥齿轮的圆周力。
这些工具和资源可以提供更准确和详细的计算方法,以满足特定的设计需求。
锥齿轮计算模版.pdf

锥齿轮传动设计1.设计参数1150150********=====d d z z u 式中:u ——锥齿轮齿数比;1z ——锥齿轮齿数;2z ——锥齿轮齿数;1d ——锥齿轮分度圆直径(mm ); 2d ——锥齿轮分度圆直径(mm )。
1.10621115021)2()2(2212221=+=+=+=u d d d R mm 25.125)33.05.01(150)5.01(11=⨯−⨯=−=R m d d φ mm同理 2m d =125.25 mm式中:1m d 、2m d ——锥齿轮平均分度圆直径(mm );R φ——锥齿轮传动齿宽比,最常用值为R φ=1/3,取R φ=0.33。
530150111===z d m 同理 2m =5式中:1m 、2m ——锥齿轮大端模数。
175.4)33.05.01(5)5.01(11=⨯−⨯=−=R m m m φ同理 2m m =4.175式中:m m 1、m m 2——锥齿轮平均模数。
2.锥齿轮受力分析因为锥齿轮1与锥齿轮2的传动比为1,且各项数据相同,则现以锥齿轮1为分析对象得:125015083.932211=⨯==m t d T F N 88.88345cos 45tan 1250cos tan 111=︒⨯︒⨯==δαt r F F N 88.88345cos 45tan 1250sin tan 111=︒⨯︒⨯==δαt a F F N 22.133020cos 1250cos 11=︒==αt n F F N 式中;1t F ——锥齿轮圆周力;1r F ——锥齿轮径向力;1a F ——锥齿轮轴向力;1n F ——锥齿轮法向载荷;α——锥齿轮啮合角;δ——锥齿轮分度角。
3.齿根弯曲疲劳强度计算(1) 确定公式内的各计算数值1) 由《机械设计》图10-20c 查得锥齿轮的弯曲疲劳强度极限=1FE σ580MPa2) 由《机械设计》图10-18取弯曲疲劳寿命系数=1FN K 13) 计算弯曲疲劳许用应力取弯曲疲劳安全系数S =1.4,由《机械设计》式(10-12)得=⨯==4.15801][111S K FE FN F σσ414.29 MPa 4) 计算载荷系数K23.235.111.15.1=⨯⨯⨯==βαF F v A K K K K K5) 查取齿形系数由《机械设计》表10-5查得8.21=Fa Y6) 查取应力校正系数由《机械设计》表10-5查得55.11=Sa Y7) 计算大、小齿轮的[]F Sa Fa Y Y σ并加以比较[]01048.029.41455.18.2111=⨯=F Sa Fa Y Y σ 由《机械设计》式(10-24)得弯曲强度的设计公式为 []27.029.4141130)33.05.01(33.055.18.283.9323.241)5.01(43222111221231=⨯+⨯⨯⨯−⨯⨯⨯⨯⨯=⨯+−≥F Sa Fa R R Y Y u z KT m σφφ 由m=5>0.27,则弯曲疲劳强度符合要求。
锥齿轮径向力计算公式

锥齿轮径向力计算公式
锥齿轮径向力的计算公式如下:
Frad = Ftan + Fper
其中,Frad表示锥齿轮的径向力,Ftan表示锥齿轮的切向力,Fper表示锥齿轮的法向力。
切向力(Ftan)的计算公式如下:
Ftan = T/ρ
其中,T表示传递给锥齿轮的转矩,ρ表示车轮与锥齿轮接触
点的半径。
法向力(Fper)的计算公式如下:
Fper = Fr*sinα/sin(β+α)
其中,Fr表示传递给锥齿轮的轴向力,α表示动压角,β表示
锥齿轮带角。
需要注意的是,以上公式仅适用于理想条件下的计算,实际情况中可能会受到摩擦、弯曲等因素的影响,导致计算结果可能会有一定偏差。
- 1、下载文档前请自行甄别文档内容的完整性,平台不提供额外的编辑、内容补充、找答案等附加服务。
- 2、"仅部分预览"的文档,不可在线预览部分如存在完整性等问题,可反馈申请退款(可完整预览的文档不适用该条件!)。
- 3、如文档侵犯您的权益,请联系客服反馈,我们会尽快为您处理(人工客服工作时间:9:00-18:30)。
由表5-67查得
0.0194
0.0064
20
x*
x*=(1+2qs)/5
0.971
1.418
21
相对齿根圆角敏感系数
=(1+ )/(1+ )
1.046
1.007
相对齿根表面状况系数
22
调质钢与渗碳淬火钢
1.002
尺寸系数
23
调质钢
Yx
Yx=1.05 0.01 Yx 1
1
24
试验齿轮应力
YST
74.213
22.269
24
大端分度圆弧齿厚
si/mm
si=m( )
3.297
25
大端分度圆弦齿厚
mm
=si /(6di2)
3.923
3.927
26
大端分度圆
mm
=hai /(4di)
2.603
2.505
表A2直齿锥齿轮的当量齿轮几何计算
序号
名称
代号/单位
计算公式和说明
结果
小轮
大轮
1
参考点锥距
Rm/mm
6.260
15
当量齿轮端面重合度
vα
vα=gvα/pvb
1.747
16
刀具齿顶高
ha0/mm
ha0=mm(ha*+c*)
2.545
17
刀尖圆角半径
a0/mm
按表选取
0.6
表A3直齿锥齿轮强度校核的原始参数
序号
名称
代号/单位
结果
1
传递功率
p/kw
4.224
2
小轮转矩
T1/N m
24.359
3
小轮转速
n1/r min
齿顶角
/(°)
等顶隙收缩 = =
2.173
20
顶锥角
δai/(°)
δai=δi+
20.607
77.738
21
根锥角
δfi/(°)
δfi=δi
16.261
73.392
22
大端齿顶圆直径
dai/mm
dai=di+zhaicosδi
54.743
22.269
23
冠顶距
Aai/mm
Aai=Rcosδi-haisinδi
3121.4
31
接触强度计算的齿间载荷系数
KHα
vα 2KHα= [0.9+ ]
1.335
32
弯曲强度计算的齿间载荷系数
KFα
KFα=KHα
1.335
33
KHαmax
KHαmax=1/ZLS2
1
34
KFαmax
KFαmax=1/
1.472
35
KHα
当KHα KHαmax时KHα=KHαmax
1
36
KFα
附录A:锥齿轮的设计
表A1直齿锥齿轮几何计算
序号
名称
代号/单位
计算公式和说明
结果
小轮
大轮
原始参数
1
齿数
zi
z1=20z2=60
20
60
2
大端模数
m/mm
圆整到标准值
2.5
3
齿宽
b/mm
取b=0.3R和b=10m中小者
24
4
齿顶高系数
ha*
GB/T 12369-1990
1
5
顶隙系数
c*
GB/T 12369-1990
mred= ( )
1.00565
12
共振转速
nE1/r mm-1
nE1=
26113.225
13
无量纲的基准速度
N
N=n1/n轮精度查得
0.9
15
Cp
查机械设计手册表
11.2
16
齿距极限偏差
fpt/μm
fpt=Ap(mm+0.25 )+Cp
15.642
17
轻齿跑合量
α/μm
α1=160fpt/ Hlim1=2.944
α2=160fpt/ Hlim2=4.171
α=0.5( α1+ α2)
3.558
18
有效齿距偏差
fpeff/μm
fpeff=fpt α
12.084
19
Bp
Bp=bfpeffC′/(FmtKA)
1.991
20
N 1.25时
Cv1
Cv1=0.32
0.32
21
1.908
2.015
6
30°切线切点处齿廓曲率半径与模数之比
= +
0.495
0.331
7
齿顶压力角
αa/(°)
αa=arccos(dvbi/dvai)
30.879
21.264
8
齿顶圆齿厚半角
a/(°)
a=180/ {1/zvi[ /2 (2x1tanα+xt1)]}
4.227
0.261
9
载荷作用角
αFa/(°)
Cv2
1 vα 2时Cv2=0.34
0.34
22
N 0.75
Cv3
1 vα 2时Cv3=0.23
0.23
23
动载系数
Kv
N 0.75,Kv=N[Bp(Cv1+Cv2) +Cv3]+1
1.0979
24
装配系数
KHβ-be
根据装配条件和接触检验条件按表3.5-5选取
1.1
25
接触强度计算的齿向载荷系数
KHβ
13
齿轮材料的密度
小轮
1/kg mm-3
7.85 10-6
14
大轮
2/kg mm-3
7.85 10-6
15
材料的弹性模量
小轮
E1
2.117 105
16
大轮
E2
2.101 105
17
材料的泊松比
小轮
1
0.3
18
大轮
2
0.269
19
齿轮精度等级
7级
20
齿面粗糙度
小轮
Rz1/μm
6.3
21
大轮
Rz2/μm
0.2
6
压力角
α/(°)
选取20°
20
7
轴交角
Σ/(°)
90°
90
8
高变位系数
xi
0
9
切向变位系数
xti
0
几何参数
10
大端分度圆直径
di/mm
di=mzi
50
150
11
分度锥角
δi/(°)
δ1=arctan
18.434
71.565
12
大端锥距
R/mm
R=0.5mz1/sinδ1
79.060
13
大端齿距
Zβ
Zβ=1
1
7
锥齿轮系数
ZK
ZK=0.8
0.8
8
尺寸系数
Zx
Zx=1
1
9
CZL
CZL=0.08( )+0.83
0.83
10
润滑剂系数
ZL
ZL=CZL+
0.947
11
CZV
CZV=0.08( )+0.85
0.85
12
速度系数
ZV
ZV=CZV+
0.947
13
小轮齿面微观不平度
Rz1/μm
Rz1 6Ra1
6.3
22
润滑油
N100L-CKC (GB/T5903-1995)
23
40°C时润滑油的名义运动黏度
v40/mm2 s-1
100
24
使用场合
微耕机变速箱
25
使用寿命
/h
7680
26
大小轮装配条件
小轮悬臂,大轮双支承
表A4直齿锥齿轮的切向力及载荷系数
序号
名称
代号/单位
计算公式和说明
结果
1
小轮转矩
T1/N m
0.879
19
工作硬化系数
Zw
HB 470时Zw=1
1
20
接触疲劳寿命系数
ZNT
查表3.5-8
1.263
21
齿面中点接触线长
lbm/mm
lbm=2 /
23.747
续表A5
22
齿面接触应力基本值
/MPa
=ZM-BZHZEZK
452.283
23
接触强度计算安全系数
SH
SH=
1.026
表A6直齿锥齿轮弯曲强度校核
序号
名称
代号/单位
计算公式和说明
结果
小轮
大轮
1
E/mm
E=( xt1/2)mm
0.319
0.319
2
G
G= ao/mm ha/mm x1
0.917
0.917
3
H
H=( 2E/mm)/Zvi
0.912
1.035
4
/rad
=2Gtan /Zvi H
47.0398
58.5849
5
危险截面齿厚与模数之比
=Zvisin( )+ ( )
YST=2
2
25
修正系数