LTCC基板材料
LTCC生产流程

LTCC生产流程
LTCC(低温多元陶瓷)是一种具有良好兼容性、耐热性、耐湿性及抗
静电性等特性的复合材料。
LTCC的制备不仅要具备特殊的粘结方式,其
加工技术也要求非常严格,目前也是复合电子组件的主要材料。
本文将从
几个方面,介绍LTCC制作的基本生产流程。
1.材料准备
LTCC的原材料主要包括:氧化铝粉、碳化硅粉和氧化硅粉。
氧化铝粉是LTCC的主要组分,可调节LTCC的硬度和变形性能;碳化
硅粉有利于改善材料的热陶瓷性能;氧化硅粉是在热处理过程中,可以提
高氧化铝的抗拉强度。
2.原料研磨和混合
在LTCC的生产过程中,需要将上述三种粉末进行混合研磨,以获得
一定细度的粉末混合料。
混合研磨后的粉末,然后加入专用有机结合剂和
溶剂,搅拌混合,以形成有一定流动性的浆料。
3.铸型
混合、研磨以后的粉末,然后浇入到模具中,经过一定的压力和温度,使其熔结及结构定型,从而获得LTCC片材。
4.热处理
热处理是LTCC片材加工的重要环节,其主要目的是调整最终材料的
硬度和性能,其可根据需要设定不同的热处理温度、时间和压力参数,以
达到魔芯要求。
5.烧结
烧结是LTCC片材的最后一个环节,其目的是再次烧结有机结合剂。
LTCC中玻璃陶瓷复合基板材料的热性能研究的开题报告
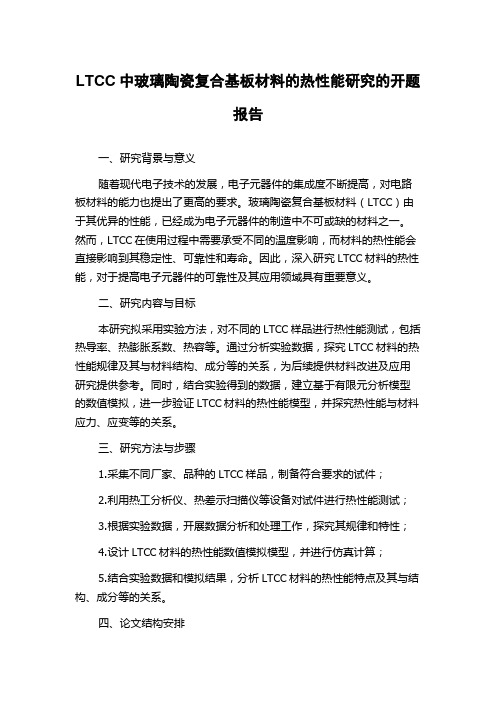
LTCC中玻璃陶瓷复合基板材料的热性能研究的开题报告一、研究背景与意义随着现代电子技术的发展,电子元器件的集成度不断提高,对电路板材料的能力也提出了更高的要求。
玻璃陶瓷复合基板材料(LTCC)由于其优异的性能,已经成为电子元器件的制造中不可或缺的材料之一。
然而,LTCC在使用过程中需要承受不同的温度影响,而材料的热性能会直接影响到其稳定性、可靠性和寿命。
因此,深入研究LTCC材料的热性能,对于提高电子元器件的可靠性及其应用领域具有重要意义。
二、研究内容与目标本研究拟采用实验方法,对不同的LTCC样品进行热性能测试,包括热导率、热膨胀系数、热容等。
通过分析实验数据,探究LTCC材料的热性能规律及其与材料结构、成分等的关系,为后续提供材料改进及应用研究提供参考。
同时,结合实验得到的数据,建立基于有限元分析模型的数值模拟,进一步验证LTCC材料的热性能模型,并探究热性能与材料应力、应变等的关系。
三、研究方法与步骤1.采集不同厂家、品种的LTCC样品,制备符合要求的试件;2.利用热工分析仪、热差示扫描仪等设备对试件进行热性能测试;3.根据实验数据,开展数据分析和处理工作,探究其规律和特性;4.设计LTCC材料的热性能数值模拟模型,并进行仿真计算;5.结合实验数据和模拟结果,分析LTCC材料的热性能特点及其与结构、成分等的关系。
四、论文结构安排第一章绪论1.1 研究背景1.2 研究现状及存在的问题1.3 研究意义与目标第二章 LTCC材料的热性能测试2.1 LTCC试件的制备2.2 热导率测试方法2.3 热容测试方法2.4 热膨胀系数测试方法第三章 LTCC材料的热性能规律分析3.1 热导率测试结果分析3.2 热容测试结果分析3.3 热膨胀系数测试结果分析第四章 LTCC材料的热性能数值模拟4.1 建立LTCC材料的热性能数值模拟模型4.2 模型的验证与分析第五章 LTCC材料的热性能与应力、应变关系分析5.1 热应力分析5.2 热应变分析5.3 结果分析与讨论第六章总结与展望6.1 研究成果与结论6.2 研究不足与展望附录:实验数据表格、图表、模型代码、热学参考文献等。
ltcc封装基板应用场景
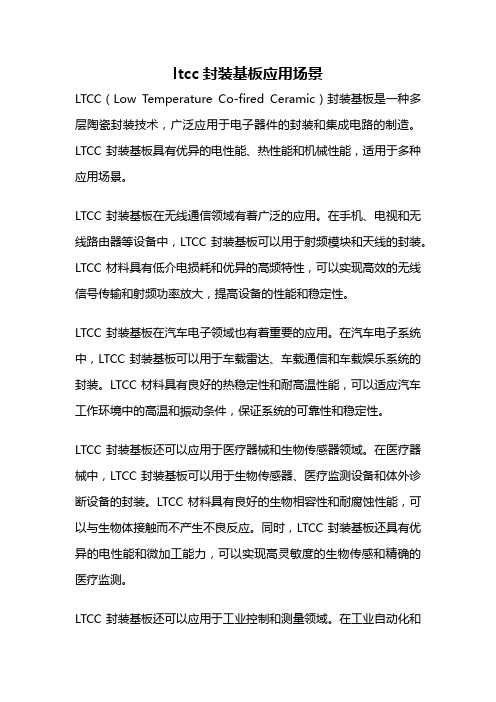
ltcc封装基板应用场景LTCC(Low Temperature Co-fired Ceramic)封装基板是一种多层陶瓷封装技术,广泛应用于电子器件的封装和集成电路的制造。
LTCC封装基板具有优异的电性能、热性能和机械性能,适用于多种应用场景。
LTCC封装基板在无线通信领域有着广泛的应用。
在手机、电视和无线路由器等设备中,LTCC封装基板可以用于射频模块和天线的封装。
LTCC材料具有低介电损耗和优异的高频特性,可以实现高效的无线信号传输和射频功率放大,提高设备的性能和稳定性。
LTCC封装基板在汽车电子领域也有着重要的应用。
在汽车电子系统中,LTCC封装基板可以用于车载雷达、车载通信和车载娱乐系统的封装。
LTCC材料具有良好的热稳定性和耐高温性能,可以适应汽车工作环境中的高温和振动条件,保证系统的可靠性和稳定性。
LTCC封装基板还可以应用于医疗器械和生物传感器领域。
在医疗器械中,LTCC封装基板可以用于生物传感器、医疗监测设备和体外诊断设备的封装。
LTCC材料具有良好的生物相容性和耐腐蚀性能,可以与生物体接触而不产生不良反应。
同时,LTCC封装基板还具有优异的电性能和微加工能力,可以实现高灵敏度的生物传感和精确的医疗监测。
LTCC封装基板还可以应用于工业控制和测量领域。
在工业自动化和仪器仪表中,LTCC封装基板可以用于传感器、执行器和控制器的封装。
LTCC材料具有良好的电绝缘性和机械强度,可以抵抗工业环境中的高温、高压和腐蚀。
同时,LTCC封装基板的多层结构和高集成度,可以实现复杂的电路设计和高精度的测量控制。
总的来说,LTCC封装基板具有广泛的应用场景。
无论是无线通信、汽车电子、医疗器械还是工业控制,LTCC封装基板都可以发挥其优异的电性能、热性能和机械性能,满足不同领域的需求。
随着电子技术的不断发展和应用的不断拓展,LTCC封装基板将会在更多的领域发挥重要作用,推动技术的进步和产业的发展。
LTCC技术
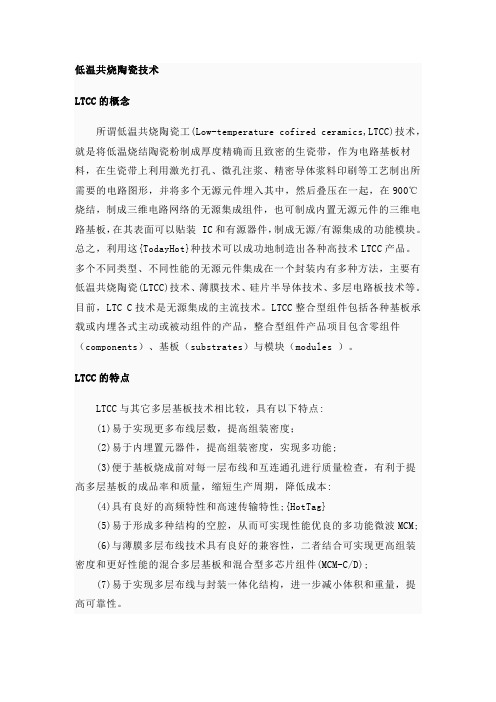
低温共烧陶瓷技术LTCC的概念所谓低温共烧陶瓷工(Low-temperature cofired ceramics,LTCC)技术,就是将低温烧结陶瓷粉制成厚度精确而且致密的生瓷带,作为电路基板材料,在生瓷带上利用激光打孔、微孔注浆、精密导体浆料印刷等工艺制出所需要的电路图形,并将多个无源元件埋入其中,然后叠压在一起,在900℃烧结,制成三维电路网络的无源集成组件,也可制成内置无源元件的三维电路基板,在其表面可以贴装 IC和有源器件,制成无源/有源集成的功能模块。
总之,利用这{TodayHot}种技术可以成功地制造出各种高技术LTCC产品。
多个不同类型、不同性能的无源元件集成在一个封装内有多种方法,主要有低温共烧陶瓷(LTCC)技术、薄膜技术、硅片半导体技术、多层电路板技术等。
目前,LTC C技术是无源集成的主流技术。
LTCC整合型组件包括各种基板承载或内埋各式主动或被动组件的产品,整合型组件产品项目包含零组件(components)、基板(substrates)与模块(modules )。
LTCC的特点LTCC与其它多层基板技术相比较,具有以下特点:(1)易于实现更多布线层数,提高组装密度;(2)易于内埋置元器件,提高组装密度,实现多功能;(3)便于基板烧成前对每一层布线和互连通孔进行质量检查,有利于提高多层基板的成品率和质量,缩短生产周期,降低成本:(4)具有良好的高频特性和高速传输特性;{HotTag}(5)易于形成多种结构的空腔,从而可实现性能优良的多功能微波MCM;(6)与薄膜多层布线技术具有良好的兼容性,二者结合可实现更高组装密度和更好性能的混合多层基板和混合型多芯片组件(MCM-C/D);(7)易于实现多层布线与封装一体化结构,进一步减小体积和重量,提高可靠性。
LTCC技术由于自身具有的独特优点,用于制作新一代移动通信中的表面组装型元器件,将显现出巨大的优越性。
产品LTCC(低温共烧陶瓷)己经进入产业化阶段,日、美、欧洲国家等各家公司纷纷推出了各种性能的LTCC产品。
LTCC基板砂轮划片工艺研究

LTCC基板砂轮划片工艺研究近年来,随着电子设备的发展,对于电子元器件的集成度和性能要求越来越高。
LTCC(Low Temperature Co-fired Ceramic)基板作为一种重要的电子封装基板材料,具有优异的性能和广泛的应用前景。
其中,砂轮划片技术在LTCC基板制备过程中起到了至关重要的作用。
本文旨在对LTCC基板砂轮划片工艺进行研究,并提出相应的改进措施。
首先,介绍LTCC基板划片工艺的基本流程。
LTCC基板划片工艺主要包括三个步骤:基板切割、砂轮选择和划片加工。
在基板切割阶段,首先将整个LTCC基板切割成合适大小的小片;然后,在砂轮选择阶段,根据需要选择合适的砂轮,并进行适当的修整;最后,在划片加工阶段,将切割好的基板小片加工成所需的形状和尺寸。
其次,探讨LTCC基板划片工艺存在的问题。
在实际操作中,LTCC基板划片过程中存在一些问题,例如砂轮磨损严重、加工精度低等。
这些问题影响了划片工艺的稳定性和效率。
针对以上问题,提出相应的改进措施。
首先,改善砂轮磨损严重问题。
可以通过调整切割速度、刀具切削角度等方式,减少砂轮的磨损。
其次,提高加工精度。
可以通过优化切割参数,如提高切割速度、降低进给速度等,来提高划片的精度和表面质量。
此外,还可以使用更高精度的加工设备和工艺,如激光切割等,来提高划片加工的精度和效率。
最后,总结LTCC基板砂轮划片工艺的研究。
LTCC基板砂轮划片工艺是LTCC基板制备过程中不可或缺的关键环节。
对于砂轮的选择、划片加工参数的优化以及加工设备的选择等方面的研究,可以提高LTCC基板划片工艺的稳定性和效率,从而满足电子设备对LTCC基板的要求。
综上所述,LTCC基板砂轮划片工艺研究是非常重要的一项工作。
通过对划片工艺的改进和优化,可以提高LTCC基板的加工精度和表面质量,满足电子设备对于高性能基板的需求,推动电子封装技术的发展。
LTCC生产方案工艺和概述部分

LTCC生产方案工艺和概述部分低温共烧陶瓷(LTCC)是一种广泛应用于微波电子器件、传感器、微机械器件等领域的封装材料。
它具有优良的性能,如低介电常数、低介电损耗、良好的热稳定性和机械强度,适用于高频和高温环境。
LTCC制造工艺繁琐复杂,需要多道工艺步骤,包括浆料制备、模具成型、干燥、烧结、金属化、焊接等。
本文将介绍LTCC生产的工艺流程和概述。
1.浆料制备:首先是浆料的制备。
浆料是LTCC制造的基础材料,主要由陶瓷粉体、有机胶体、溶剂和助剂等组成。
浆料的质量直接影响最终产品的性能。
在浆料制备过程中,需要注意材料的比例和混合均匀度。
通常通过搅拌、过滤和分散等工艺来制备高质量的浆料。
2.模具成型:制备好的浆料通过印刷或注塑等方式注入到模具中,经过压制和成型,形成具有特定结构和尺寸的LTCC坯料。
模具成型是LTCC 生产的关键步骤,影响产品的形状和尺寸精度。
3.干燥:成型后的LTCC坯料需要进行干燥,去除水分和有机物。
干燥的温度和时间要根据材料的性质和厚度进行控制,以避免裂纹和变形。
4.烧结:干燥后的LTCC坯料需要进行烧结,使其形成致密的陶瓷结构。
烧结温度通常在1000℃以上,持续时间较长。
烧结是LTCC生产的关键工艺步骤,直接影响产品的性能和稳定性。
5.金属化:烧结后的LTCC产品需要进行金属化处理,通常是在表面镀覆导电金属,如金、银、铜等。
金属化可以提高产品的导电性能和焊接性能。
6.焊接:最后一步是进行焊接。
LTCC制品可以通过焊接与其他元器件连接,如集成电路、电阻器、电容器等。
焊接工艺需要选择合适的焊料和温度,以确保良好的连接质量。
总的来说,LTCC生产工艺是一项复杂而精细的制造过程,需要多道工艺步骤的精心控制和协调。
通过优化工艺参数和技术手段,可以提高产品的质量和稳定性,满足不同领域的需求。
未来,随着微电子技术的不断发展和应用领域的扩大,LTCC封装技术将会得到更广泛的应用。
通过不断改进工艺流程和材料性能,LTCC将会成为更多领域的重要封装材料,推动微波电子器件、传感器、微机械器件等领域的发展。
LTCC多层陶瓷基板
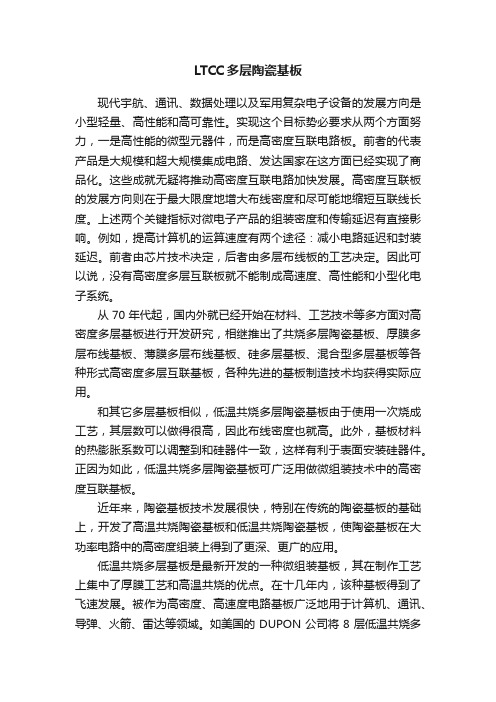
LTCC多层陶瓷基板现代宇航、通讯、数据处理以及军用复杂电子设备的发展方向是小型轻量、高性能和高可靠性。
实现这个目标势必要求从两个方面努力,一是高性能的微型元器件,而是高密度互联电路板。
前者的代表产品是大规模和超大规模集成电路、发达国家在这方面已经实现了商品化。
这些成就无疑将推动高密度互联电路加快发展。
高密度互联板的发展方向则在于最大限度地增大布线密度和尽可能地缩短互联线长度。
上述两个关键指标对微电子产品的组装密度和传输延迟有直接影响。
例如,提高计算机的运算速度有两个途径:减小电路延迟和封装延迟。
前者由芯片技术决定,后者由多层布线板的工艺决定。
因此可以说,没有高密度多层互联板就不能制成高速度、高性能和小型化电子系统。
从70年代起,国内外就已经开始在材料、工艺技术等多方面对高密度多层基板进行开发研究,相继推出了共烧多层陶瓷基板、厚膜多层布线基板、薄膜多层布线基板、硅多层基板、混合型多层基板等各种形式高密度多层互联基板,各种先进的基板制造技术均获得实际应用。
和其它多层基板相似,低温共烧多层陶瓷基板由于使用一次烧成工艺,其层数可以做得很高,因此布线密度也就高。
此外,基板材料的热膨胀系数可以调整到和硅器件一致,这样有利于表面安装硅器件。
正因为如此,低温共烧多层陶瓷基板可广泛用做微组装技术中的高密度互联基板。
近年来,陶瓷基板技术发展很快,特别在传统的陶瓷基板的基础上,开发了高温共烧陶瓷基板和低温共烧陶瓷基板,使陶瓷基板在大功率电路中的高密度组装上得到了更深、更广的应用。
低温共烧多层基板是最新开发的一种微组装基板,其在制作工艺上集中了厚膜工艺和高温共烧的优点。
在十几年内,该种基板得到了飞速发展。
被作为高密度、高速度电路基板广泛地用于计算机、通讯、导弹、火箭、雷达等领域。
如美国的DUPON公司将8层低温共烧多层基板用于毒刺导弹的测试电路中。
日本富士通公司用61层低温共烧陶瓷基板制作VP2000系列超级计算机的多芯片组件,而NEC公司已做成78层低温共烧多层基板、其面积为225×225平方毫米。
CaO—B2O3-SiO2微晶玻璃LTCC基板的烧结性能研究

CaO—B2O3SiO2微晶玻璃LTCC基板的烧结性能研究在当今电子技术快速发展的时代,LTCC(低温共烧陶瓷)基板作为电子元器件的关键载体,其性能直接影响到电子产品的性能和可靠性。
LTCC基板主要由陶瓷和玻璃组成,其中玻璃相的烧结性能对于基板的微观结构和宏观性能有着重要影响。
本研究以CaO—B2O3SiO2微晶玻璃为对象,探讨了其在LTCC基板中的应用及其烧结性能。
一、引言CaO—B2O3SiO2微晶玻璃作为一种新型玻璃材料,具有优异的机械性能、热稳定性和电学性能,在电子、光学等领域具有广泛的应用前景。
将CaO—B2O3SiO2微晶玻璃应用于LTCC基板,有望提高基板的性能,满足电子产品对高性能、高可靠性基板的需求。
二、实验部分1. 材料制备本研究采用高温熔融法制备CaO—B2O3SiO2微晶玻璃,通过调整CaO、B2O3和SiO2的比例,制备出不同成分的微晶玻璃样品。
将制备的微晶玻璃与陶瓷粉料混合,经过球磨、烘干、造粒等工艺,制备出LTCC基板生坯。
2. 烧结性能测试将制备的LTCC基板生坯在一定的烧结温度和保温时间下进行烧结,采用热重分析仪(TGA)和差示扫描量热仪(DSC)对烧结过程中的热行为进行分析。
同时,采用X射线衍射仪(XRD)和扫描电子显微镜(SEM)对烧结后的基板微观结构进行表征。
3. 性能测试对烧结后的LTCC基板进行性能测试,包括热膨胀系数、抗弯强度、介电常数等,以评估CaO—B2O3SiO2微晶玻璃对LTCC基板性能的影响。
三、结果与讨论1. 烧结行为分析通过TGA和DSC分析,发现CaO—B2O3SiO2微晶玻璃在烧结过程中存在明显的熔融和结晶过程。
调整烧结温度和保温时间,可以优化微晶玻璃的烧结性能。
2. 微观结构分析XRD和SEM分析结果表明,CaO—B2O3SiO2微晶玻璃在烧结过程中形成了均匀的微晶结构,有利于提高LTCC基板的机械性能和热稳定性。
3. 性能测试结果性能测试结果表明,CaO—B2O3SiO2微晶玻璃的应用显著提高了LTCC基板的热膨胀系数、抗弯强度和介电常数等性能,满足了电子产品对高性能、高可靠性基板的需求。
- 1、下载文档前请自行甄别文档内容的完整性,平台不提供额外的编辑、内容补充、找答案等附加服务。
- 2、"仅部分预览"的文档,不可在线预览部分如存在完整性等问题,可反馈申请退款(可完整预览的文档不适用该条件!)。
- 3、如文档侵犯您的权益,请联系客服反馈,我们会尽快为您处理(人工客服工作时间:9:00-18:30)。
1、瓷基板现阶段较普遍的瓷散热基板种类共有LTCC、HTCC、DBC、DPC四种,其中HTCC属于较早期发展之技术,但由于其较高的工艺温度(1300~1600℃),使其电极材料的选择受限,且制作成本相当昂贵,这些因素促使LTCC的发展,LTCC虽然将共烧温度降至约850℃,但其尺寸精确度、产品强度等技术上的问题尚待突破。
而DBC与DPC则为近几年才开发成熟,且能量产化的专业技术,但对于许多人来说,此两项专业的工艺技术仍然很陌生,甚至可能将两者误解为同样的工艺。
DBC乃利用高温加热将Al2O3与Cu板结合,其技术瓶颈在于不易解决Al2O3与Cu板间微气孔产生之问题,这使得该产品的量产能量与良率受到较大的挑战,而DPC技术则是利用直接披覆技术,将Cu沉积于Al2O3基板之上,其工艺结合材料与薄膜工艺技术,其产品为近年最普遍使用的瓷散热基板。
然而其材料控制与工艺技术整合能力要求较高,这使得跨入DPC产业并能稳定生产的技术门槛相对较高。
2、现阶段LED散热情况LED 散热技术随着高功率LED产品的应用发展,已成为各家业者相继寻求解决的议题,而LED散热基板的选择亦随着LED之线路设计、尺寸、发光效率…等条件的不同有设计上的差异,以目前市面上最常见的可区分为(一)系统电路板,其主要是作为LED最后将热能传导到大气中、散热鳍片或外壳的散热系统,而列为系统电路板的种类包括:铝基板(MCPCB)、印刷电路板(PCB)以及软式印刷电路板(FPC)。
(二)LED芯片基板,是属于LED芯片与系统电路板两者之间热能导出的媒介,并藉由共晶或覆晶与LED芯片结合。
为确保LED的散热稳定与LED芯片的发光效率,近期许多以瓷材料作为高功率LED散热基板之应用,其种类主要包含有:低温共烧多层瓷(LTCC)、高温共烧多层瓷(HTCC)、直接接合铜基板(DBC)、直接镀铜基板(DPC)四种,以下本文将针对瓷LED芯片基板的种类做深入的探讨。
3.对四种瓷散热基板的生产流程做进一步的说明,进而更加瞭解四种瓷散热基板制造过程的差异。
2-1 LTCC (Low-Temperature Co-fired Ceramic)LTCC 又称为低温共烧多层瓷基板,此技术须先将无机的氧化铝粉与约30%~50%的玻璃材料加上有机黏结剂,使其混合均匀成为泥状的浆料,接着利用刮刀把浆料刮成片状,再经由一道干燥过程将片状浆料形成一片片薄薄的生胚,然后依各层的设计钻导通孔,作为各层讯号的传递,LTCC部线路则运用网版印刷技术,分别于生胚上做填孔及印制线路,外电极则可分别使用银、铜、金等金属,最后将各层做叠层动作,放置于850~900℃的烧结炉中烧结成型,即可完成。
详细制造过程如图1 LTCC生产流程图。
图1 LTCC生产流程图2-2 HTCC (High-Temperature Co-fired Ceramic)HTCC又称为高温共烧多层瓷,生产制造过程与LTCC极为相似,主要的差异点在于HTCC的瓷粉末并无加入玻璃材质,因此,HTCC的必须再高温1300~1600℃环境下干燥硬化成生胚,接着同样钻上导通孔,以网版印刷技术填孔与印制线路,因其共烧温度较高,使得金属导体材料的选择受限,其主要的材料为熔点较高但导电性却较差的钨、钼、锰…等金属,最后再叠层烧结成型。
2-3 DBC (Direct Bonded Copper)DBC直接接合铜基板,将高绝缘性的Al2O3或AlN瓷基板的单面或双面覆上铜金属后,经由高温1065~1085℃的环境加热,使铜金属因高温氧化、扩散与Al2O3材质产生(Eutectic) 共晶熔体,使铜金与瓷基板黏合,形成瓷复合金属基板,最后依据线路设计,以蚀刻方式备制线路,DBC制造流程图如下图2。
图2 DBC 制造流程图2-4 DPC (Direct Plate Copper)DPC亦称为直接镀铜基板,以瑷司柏DPC基板工艺为例:首先将瓷基板做前处理清洁,利用薄膜专业制造技术-真空镀膜方式于瓷基板上溅镀结合于铜金属复合层,接着以黄光微影之光阻被覆曝光、显影、蚀刻、去膜工艺完成线路制作,最后再以电镀/化学镀沉积方式增加线路的厚度,待光阻移除后即完成金属化线路制作,详细DPC生产流程图如下图3。
图3 DPC 制造流程图3、瓷散热基板特性在瞭解瓷散热基板的制造方法后,接下来将近一步的探讨各个散热基板的特性具有哪些差异,而各项特性又分别代表了什么样的意义,为何会影响了散热基板在应用时必须作为考量的重点。
以下表一瓷散热基板特性比较中,本文取了散热基板的:(1)热传导率、 (2)工艺温度、(3)线路制作方法、(4)线径宽度,四项特性作进一步的讨论:表一、瓷散热基板特性比较3-1热传导率热传导率又称为热导率,它代表了基板材料本身直接传导热能的一种能力,数值愈高代表其散热能力愈好。
LED散热基板最主要的作用就是在于,如何有效的将热能从LED芯片传导到系统散热,以降低LED 芯片的温度,增加发光效率与延长LED寿命,因此,散热基板热传导效果的优劣就成为业界在选用散热基板时,重要的评估项目之一。
检视表一,由四种瓷散热基板的比较可明看出,虽然Al2O3材料之热传导率约在20~24之间,LTCC为降低其烧结温度而添加了30%~50%的玻璃材料,使其热传导率降至2~3W/mK左右;而HTCC因其普遍共烧温度略低于纯Al2O3基板之烧结温度,而使其因材料密度较低使得热传导系数低Al2O3基板约在16~17W/mK之间。
一般来说,LTCC与HTCC散热效果并不如DBC与DPC散热基板里想。
3-2 操作环境温度操作环境温度,主要是指产品在生产过程中,使用到最高工艺温度,而以一生产工艺而言,所使用的温度愈高,相对的制造成本也愈高,且良率不易掌控。
HTCC工艺本身即因为瓷粉末材料成份的不同,其工艺温度约在1300~1600℃之间,而LTCC/DBC的工艺温度亦约在850~1000℃之间。
此外,HTCC与LTCC在工艺后对必须叠层后再烧结成型,使得各层会有收缩比例问题,为解决此问题相关业者也在努力寻求解决方案中。
另一方面,DBC对工艺温度精准度要求十分严苛,必须于温度极度稳定的1065~1085℃温度围下,才能使铜层熔炼为共晶熔体,与瓷基板紧密结合,若生产工艺的温度不够稳定,势必会造成良率偏低的现象。
而在工艺温度与裕度的考量,DPC的工艺温度仅需250~350℃左右的温度即可完成散热基板的制作,完全避免了高温对于材料所造成的破坏或尺寸变异的现象,也排除了制造成本费用高的问题。
5.jpg(44.83 KB, 下载次数: 1)006.jpg(55.12 KB, 下载次数: 1)3-3工艺能力在表一中的工艺能力,主要是表示各种散热基板的金属线路是以何种工艺技术完成,由于线路制造/成型的方法直接影响了线路精准度、表面粗糙镀、对位精准度…等特性,因此在高功率小尺寸的精细线路需求下,工艺解析度便成了必须要考虑的重要项目之一。
LTCC与HTCC 均是采用厚膜印刷技术完成线路制作,厚膜印刷本身即受限于网版力问题,一般而言,其线路表面较为粗糙,且容易造成有对位不精准与累进公差过大等现象。
此外,多层瓷叠压烧结工艺,还有收缩比例的问题需要考量,这使得其工艺解析度较为受限。
而DBC虽以微影工艺备制金属线路,但因其工艺能力限制,金属铜厚的下限约在150~300um之间,这使得其金属线路的解析度上限亦仅为150~300um之间(以深宽比1:1为标准)。
而DPC则是采用的薄膜工艺制作,利用了真空镀膜、黄光微影工艺制作线路,使基板上的线路能够更加精确,表面平整度高,再利用电镀/电化学镀沉积方式增加线路的厚度,DPC金属线路厚度可依产品实际需求(金属厚度与线路解析度)而设计。
一般而言,DPC金属线路的解析度在金属线路深宽比为1:1的原则下约在10~50um之间。
因此,DPC杜绝了LTCC/HTCC的烧结收缩比例及厚膜工艺的网版网问题。
下表二即为厚膜与薄膜工艺产品的差异做简单的比较。
表二、薄膜与厚膜工艺产品之差异分析Source:瑷司柏电子-LED散热基板之厚膜与薄膜工艺差异分析4、瓷散热基板之应用瓷散热基板会因应需求及应用上的不同,外型亦有所差别。
另一方面,各种瓷基板也可依产品制造方法的不同,作出基本的区分。
LTCC散热基板在LED产品的应用上,大多以大尺寸高功率以及小尺寸低功率产品为主,基本上外观大多呈现凹杯状,且依客户端的需求可制作出有导线架 & 没有导线架两种散热基板,凹杯形状主要是针对封装工艺采用较简易的点胶方式封装成型所设计,并利用凹杯边缘作为光线反射的路径,但LTCC本身即受限于工艺因素,使得产品难以备制成小尺寸,再者,采用了厚膜制作线路,使得线路精准度不足以符合高功率小尺寸的LED产品。
而与LTCC工艺与外观相似的HTCC,在LED散热基板这一块,尚未被普遍的使用,主要是因为HTCC采用1300~1600℃高温干燥硬化,使生产成本的增加,相对的HTCC基板费用也高,因此对极力朝低成本趋向迈进LED产业而言,面临了较严苛的考验HTCC。
另一方面, DBC与DPC则与LTCC/HTCC不仅有外观上的差异,连LED产品封装方式亦有所不同,DBC/DPC均是属于平面式的散热基板,而平面式散热基板可依客制化备制金属线路加工,再根据客户需求切割成小尺寸产品,辅以共晶/覆晶工艺,结合已非常纯熟的萤光粉涂布技术及高阶封装工艺技术铸膜成型,可大幅的提升LED的发光效率。
然而,DBC产品因受工艺能力限制,使得线路解析度上限仅为150~300um,若要特别制作细线路产品,必须采用研磨方式加工,以降低铜层厚度,但却造成表面平整度不易控制与增加额外成本等问题,使得DBC产品不易于共晶/覆晶工艺高线路精准度与高平整度的要求之应用。
DPC利用薄膜微影工艺备制金属线路加工,具备了线路高精准度与高表面平整度的的特性,非常适用于覆晶/共晶接合方式的工艺,能够大幅减少LED产品的导线截面积,进而提升散热的效率。
各种瓷散热基板之例图片与其应用围如下表三。
表三、瓷散热基板之应用围5、结论经上述各瓷基板之生产流程、特性比较、以及应用围说明后,可明确的比较出个别的差异性。
其中,LTCC散热基板在LED产业中已经被广泛的使用,但LTCC为了降低烧结温度,于材料中加入了玻璃材料,使整体的热传导率降低至2~3W/mK之间,比其他瓷基板都还要低。
再者,LTCC使用网印方式印制线路,使线路本身具有线径宽度不够精细、以及网版网问题,导致线路精准度不足、表面平整度不佳等现象,加上多层叠压烧结又有基板收缩比例的问题要考量,并不符合高功率小尺寸的需求,因此在LED产业的应用目前多以高功率大尺寸,或是低功率产品为主。