中碳钢连铸小方坯表面缺陷与保护渣性能选择
连铸保护渣与铸坯表面质量

第一章连铸保护渣研究前言保护渣的作用与分类保护渣与连铸工艺相适应保护渣对铸坯质量的影响一、前言连铸技术以其简化生产工序、提高金属收得率、节能降耗、提高铸坯质量和改善劳动条件等优点而得到迅速发展。
连铸自采用浸入式水口加保护渣浇注的工艺以后,它对稳定连铸工艺,扩大连铸品种,提高铸坯质量和产量都是一项极为有效的技术,因此,连铸保护渣技术已成为现代连铸技术的重要组成部分,如何不断提高连铸保护渣的适用性以提高铸坯表面质量满足连铸生产要求,是当前连铸技术发展的一项重要课题。
二、保护渣的作用与分类2.1 保护渣的作用从总体方面讲,保护渣在连铸过程中有两大功能:一是稳定连铸工艺,保证其顺行;二是提高铸坯的表面和皮下质量。
保护渣在结晶器内具有五个方面的作用。
2.1.1 在结晶器内的绝热保温作用保护渣在结晶器内对钢液面的绝热保温作用,主要是靠保护渣粉渣层厚度和粉渣层的物性来实现(粉渣层厚度、容重及含碳量)。
主要防止结晶器内钢液面结壳和弯月面处温度过低,造成铸坯表面和皮下夹杂。
应根据钢种的需要,选择保护渣的保温性能,否则,将造成铸坯表面和皮下大量夹杂。
2.1.2 防止结晶器内钢液的二次氧化保护渣在结晶器内防止钢液二次氧化的作用,主要靠保护渣液渣层来实现。
通常结晶器内液渣层厚度在10~12mm范围内,在液面稳定,水口揑入深度合理的情冴下,均能起到很好隑绝空气的作用。
2.1.3 吸收钢液中上浮夹杂物保护渣应具有吸收钢液中上浮夹杂物的能力,特别是结晶器内弯月面处的夹杂物,应及时地被保护渣同化。
否则,将会造成铸坯表面和皮下大量夹杂。
目前做到使保护渣具有吸收夹杂物的能力幵不难,而难在保护渣吸收大量夹杂物之后,还要保持其良好的性能,以满足连铸工艺的要求,特别是润滑性能和均匀传热性能。
通常夹杂物含量高的钢种,如含铝、钛和稀土元素的钢种,这些元素的氧化物迚入渣中,使保护渣的性能有较大的变化,如保护渣的碱度、熔化温度和粘度发生较大的变化。
连铸坯质量缺陷

连铸坯的质量缺陷及控制摘要连铸坯质量决定着最终产品的质量。
从广义来说所谓连铸坯质量是得到合格产品所允许的连铸坯缺陷的严重程度,连铸坯存在的缺陷在允许范围以内,叫合格产品。
连铸坯质量是从以下几个方面进行评价的:(1)连铸坯的纯净度:指钢中夹杂物的含量,形态和分布。
(2)连铸坯的表面质量:主要是指连铸坯表面是否存在裂纹、夹渣及皮下气泡等缺陷。
连铸坯这些表面缺陷主要是钢液在结晶器内坯壳形成生长过程中产生的,与浇注温度、拉坯速度、保护渣性能、浸入式水口的设计,结晶式的内腔形状、水缝均匀情况,结晶器振动以及结晶器液面的稳定因素有关。
(3)连铸坯的内部质量:是指连铸坯是否具有正确的凝固结构,以及裂纹、偏析、疏松等缺陷程度。
二冷区冷却水的合理分配、支撑系统的严格对中是保证铸坯质量的关键。
(4)连铸坯的外观形状:是指连铸坯的几何尺寸是否符合规定的要求。
与结晶器内腔尺寸和表面状态及冷却的均匀程度有关。
下面从以上四个方面对实际生产中连铸坯的质量控制采取的措施进行说明。
关键词:连铸坯;质量;控制1 纯净度与质量的关系纯净度是指钢中非金属夹杂物的数量、形态和分布。
夹杂物的存在破坏了钢基体的连续性和致密性。
夹杂物的大小、形态和分布对钢质量的影响也不同,如果夹杂物细小,呈球形,弥散分布,对钢质量的影响比集中存在要小些;当夹杂物大,呈偶然性分布,数量虽少对钢质量的危害也较大。
此外,夹杂物的尺寸和数量对钢质量的影响还与铸坯的比表面积有关。
一般板坯和方坯单位长度的表面积(S)与体积(V)之比在0.2~0.8。
随着薄板与薄带技术的发展,S/V可达10~50,若在钢中的夹杂物含量相同情况下,对薄板薄带钢而言,就意味着夹杂物更接近铸坯表面,对生产薄板材质量的危害也越大。
所以降低钢中夹杂物就更为重要了。
提高钢的纯净度就应在钢液进入结晶器之前,从各工序着手尽量减少对钢液的污染,并最大限度促使夹杂物从钢液中排除。
为此应采取以下措施:⑴无渣出钢。
板坯连铸保护渣的选择与使用
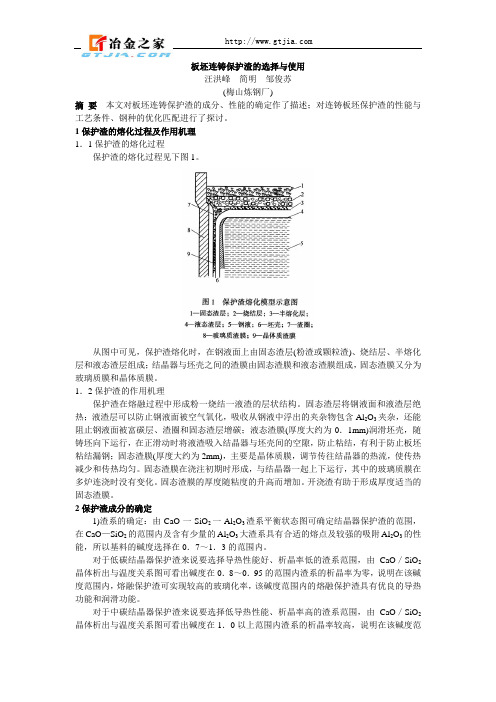
板坯连铸保护渣的选择与使用汪洪峰简明邹俊苏(梅山炼钢厂)摘要本文对板坯连铸保护渣的成分、性能的确定作了描述;对连铸板坯保护渣的性能与工艺条件、钢种的优化匹配进行了探讨。
1保护渣的熔化过程及作用机理1.1保护渣的熔化过程保护渣的熔化过程见下图1。
从图中可见,保护渣熔化时,在钢液面上由固态渣层(粉渣或颗粒渣)、烧结层、半熔化层和液态渣层组成;结晶器与坯壳之间的渣膜由固态渣膜和液态渣膜组成,固态渣膜又分为玻璃质膜和晶体质膜。
1.2保护渣的作用机理保护渣在熔融过程中形成粉一烧结一液渣的层状结构。
固态渣层将钢液面和液渣层绝热;液渣层可以防止钢液面被空气氧化,吸收从钢液中浮出的夹杂物包含Al2O3夹杂,还能阻止钢液面被富碳层、渣圈和固态渣层增碳;液态渣膜(厚度大约为0.1mm)润滑坯壳,随铸坯向下运行,在正滑动时将液渣吸入结晶器与坯壳间的空隙,防止粘结,有利于防止板坯粘结漏钢;固态渣膜(厚度大约为2mm),主要是晶体质膜,调节传往结晶器的热流,使传热减少和传热均匀。
固态渣膜在浇注初期时形成,与结晶器一起上下运行,其中的玻璃质膜在多炉连浇时没有变化。
固态渣膜的厚度随粘度的升高而增加。
开浇渣有助于形成厚度适当的固态渣膜。
2保护渣成分的确定1)渣系的确定:由CaO-一SiO2一Al2O3渣系平衡状态图可确定结晶器保护渣的范围,在CaO—SiO2的范围内及含有少量的Al2O3大渣系具有合适的熔点及较强的吸附Al2O3的性能,所以基料的碱度选择在0.7~1.3的范围内。
对于低碳结晶器保护渣来说要选择导热性能好、析晶率低的渣系范围,由CaO/SiO2晶体析出与温度关系图可看出碱度在0.8~0.95的范围内渣系的析晶率为零,说明在该碱度范围内,熔融保护渣可实现较高的玻璃化率,该碱度范围内的熔融保护渣具有优良的导热功能和润滑功能。
对于中碳结晶器保护渣来说要选择低导热性能、析晶率高的渣系范围,由CaO/SiO2晶体析出与温度关系图可看出碱度在1.0以上范围内渣系的析晶率较高,说明在该碱度范围内,熔融保护渣可实现完全的结晶化,该碱度范围内的熔融保护渣具有较低的导热功能。
连铸保护渣技术

连铸保护渣技术,作为连铸生产的关键技术之一,对连铸生产的顺行和铸坯质量有着至关重要的影响,尤其是铸坯表面缺陷,基本上都是在结晶器内形成的,与保护渣有直接关系。
近几年来,该技术在实践中,如空心颗粒渣等的开发和广泛使用,对铸坯质量的改善、连铸生产工艺的稳定起了很大促进作用。
同时渣的基础性能如润滑和传热特性的研究也一直受到人们的重视。
一、不同钢种对保护渣性能设计要求不同成分的钢种.其钢水特性及其凝固特点有别,从而决定了对保护渣性能方面的要求。
1、低碳钢首先钢中w(C)<0.08%或0.06%。
这类钢高温机械性能好,凝固过程中不存在严重的相变体积变化,内应力及裂纹敏感性小,故通常以较高拉坯速度进行生产,以提高生产率。
基于低碳钢本身的凝固特点和质量要求,设计时主要考虑渣的润滑及消耗。
较高拉速要求尽量增大结晶器热流,加速钢水凝固,防止粘结漏钢,这要求保护渣结晶温度低、凝固温度适中,以确保低碳钢结晶器保护渣在950℃以上处于非晶体状态,使发生粘结漏钢的可能性最小。
在高速浇注时,为使足够的液态保护渣能流入铸流和结晶器内表面之间的区域,确保良好的润滑和足够的消耗,通常保护渣粘度选择较低的范围。
另外,此类钢种初生铁素体坯壳中[P]、[S]偏析小,初生坯壳强度高,铸坯振痕较深,故应使用保温性能较好的保护渣,提高弯月面初生坯壳温度,有利于减轻振痕过深带来的危去。
因此,连铸低碳钢满足以上各要求,就要通过设计具有一定的传热性能、良好的保温性能、良好的非金属吸收、良好的润滑和性能稳定的保护渣来获得。
2、中碳钢中碳钢钢水凝固过程中发生己δ→γ相变,体积强烈收缩,此钢种裂纹敏感性大,容易产生表面裂纹,特别是高拉速时。
避免纵横向裂纹是首要考虑的问题,为此,中碳钢用保护渣设计的重点应放在控制从铸坯传往结晶器的热流上,限制结晶器热通量,希望保护渣具有较大热阻。
因此,应选用凝固温度高、结晶温度也高的保护渣,利用结晶质膜中的“气隙”,使保护渣传热速度减缓,有助于减小铸坯在冷却过程中产生的热应力。
连铸方坯的缺陷及其处理
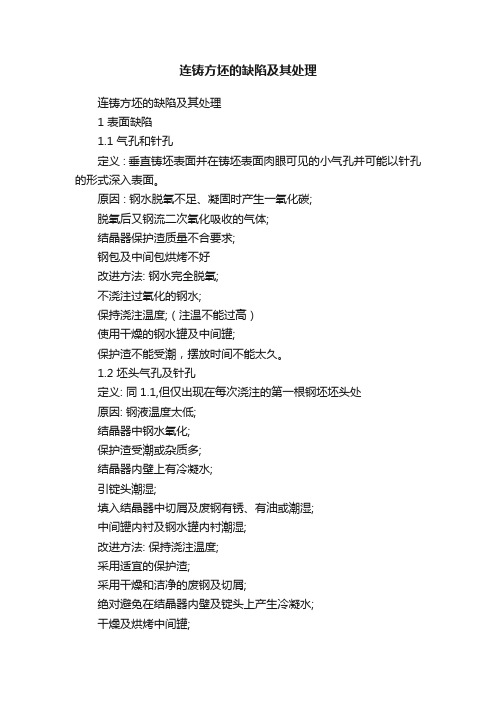
连铸方坯的缺陷及其处理连铸方坯的缺陷及其处理1 表面缺陷1.1 气孔和针孔定义 : 垂直铸坯表面并在铸坯表面肉眼可见的小气孔并可能以针孔的形式深入表面。
原因 : 钢水脱氧不足、凝固时产生一氧化碳;脱氧后又钢流二次氧化吸收的气体;结晶器保护渣质量不合要求;钢包及中间包烘烤不好改进方法: 钢水完全脱氧;不浇注过氧化的钢水;保持浇注温度;(注温不能过高)使用干燥的钢水罐及中间罐;保护渣不能受潮,摆放时间不能太久。
1.2 坯头气孔及针孔定义: 同1.1,但仅出现在每次浇注的第一根钢坯坯头处原因: 钢液温度太低;结晶器中钢水氧化;保护渣受潮或杂质多;结晶器内壁上有冷凝水;引锭头潮湿;填入结晶器中切屑及废钢有锈、有油或潮湿;中间罐内衬及钢水罐内衬潮湿;改进方法: 保持浇注温度;采用适宜的保护渣;采用干燥和洁净的废钢及切屑;绝对避免在结晶器内壁及锭头上产生冷凝水;干燥及烘烤中间罐;1.3 夹渣定义: 表面分布不均匀的夹渣,有时针孔和渣聚集,呈疏松态的外观原因: 由保护渣耐火材料颗粒和钢水氧化产物以及出钢渣等引起,随着钢流带入并被卷至铸坯表面。
改进方法: 用挡渣出钢;采用适宜的保护渣及耐火材料;钢水不能过氧化,注温要合适。
1.4 振动波纹及折叠定义: 在与铸坯轴线垂直方向上,铸坯表面上以均匀间距分布的波纹振痕,在不利的情况下出现折叠。
原因: 浇注速度波动大,使结晶器中钢液面不稳定。
改进方法: 保持均匀的浇注速度,稳定结晶器钢水液面。
调整振动频率使其与拉速相适应。
1.5 结疤与重皮定义: 铸坯角部和表面上出现的疤痕原因: 由于结晶器内坯壳破裂、钢水渗入到结晶器和铸坯之间的夹缝,以及保护渣结块造成。
改进方法: 保证结晶器具有准确的锥度,当结晶器使用时间过长而磨损会使坯壳过早脱离结晶器内壁而导致坯壳破裂。
1.6 分层: (双浇)定义: 铸坯中间出现分界层原因: 浇注中断又重新开始浇注时,使两次浇注连接出现重接。
改进方法: 浇注过程中不要断流,拉速要相对稳定,不要忽高忽低。
连铸小方坯常见的质量缺陷
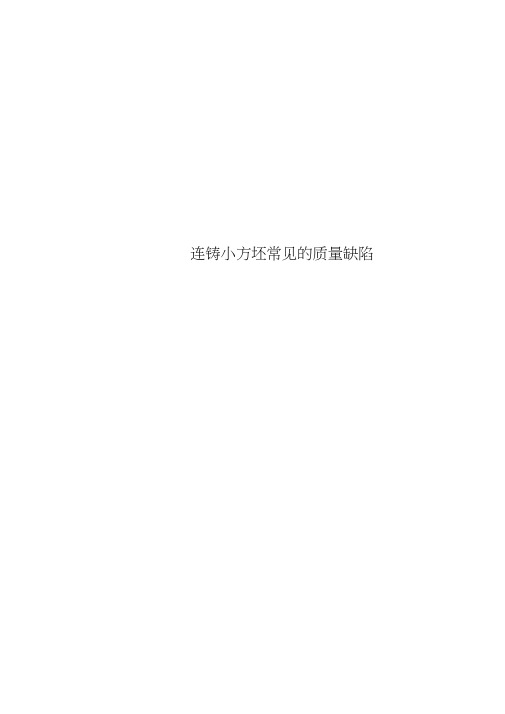
连铸小方坯常见的质量缺陷作者: 日期:摘要对连铸小方坯常见的质量缺陷进行了分类,对质量缺陷形成的原因进行了分析,提出了控制小方坯质量缺陷的技术措施.关键词小方坯;质量缺陷;成因;控制近年来,随着连铸技术的发展,连铸坯的热装、热送及热轧技术取得了很大进步,产生了明显的经济效益.这一生产工艺对连铸坯的质量提出了更高的要求.本文对连铸小方坯中常见的质量缺陷及其形成原因和控制措施进行讨论.1 小方坯的表面缺陷1. 1重接1.1.1 形成原因a.因各种操作故障引起浇注中断,重新开浇后在铸坯表面易造成重接缺陷.b. 拉速慢导致铸坯表面振痕太深,形成重接.1.1.2 控制措施a.充分做好浇钢的各项准备工作,保证浇钢的正常与稳定,避免停流事故.b.保证拉速的正常与合理.1.2 夹杂与结疤1. 2.1形成原因a.结晶器液面波动剧烈,使钢液面上的保护渣或其它夹杂物卷入铸坯,在铸坯表面形成夹杂.b. 钢液在拉漏处溢出,被结晶器冷却,在铸坯表面形成缺陷.c.拉速波动过大且频繁.1.2 .2控制措施a.提高操作人员的技术素质和工作责任心,保证结晶器液面的稳定.b. 改善保护渣的性能,增加熔渣层厚度,使之提高对夹杂物的吸收能力.c. 严格工艺操作规程,稳定拉速.d.提高中间包水口和塞头的抗侵蚀性能.1.3 划痕1.3. 1 形成原因a. 二冷段机架足辊上有废钢,造成铸坯表面划痕.b. 拉矫辊不平或二次冷却不均匀,造成铸坯跑偏,铸坯与拉矫机架接触划伤铸坯表面.1.3.2 控制措施a.加强二冷段的维护,发现漏钢要及时处理干净.b .加强拉矫系统的维护,保证拉矫辊的水平度,并安装侧导向装置,防止铸坯跑偏.1.4 振痕1.4.1形成原因a. 振痕是结晶器振动的必然结果,难以完全消除,结晶器液面波动越大,振痕越深.b .拉速越慢,振动频率越低,振痕越深.c.钢种凝固特性对振痕有很大的影响.收缩敏感型钢振痕深,裂纹敏感型钢振痕浅.1.4.2 控制措施a.采用低振幅、高频率的正弦式振动.b. 采取措施保证结晶器液面的稳定.2 小方坯的内部缺陷2. 1 偏析2.1.1 形成原因 a.铸坯内部杂质元素的偏析程度是由钢种的化学成份和冷却速度决定的.一般情况下,主要取决于冷却速度.在冷却速度适当的情况下,钢种的含碳量越高,偏析越严重.b.从连铸的角度分析,铸坯内部偏析主要受二次冷却强度的影响.二次冷却强度越大,铸坯内部杂质元素偏析越严重.2. 1.2控制措施a.根据钢种的化学成份及连铸拉速的要求,选择适当的二次冷却强度.对含碳量高的钢种,采用弱冷方式.b.若有条件,对内部偏析控制要求高的钢种,宜采用二次冷却区电磁搅拌. 2.2 皮下气泡2.2.1 形成原因a.浇注过程中氢浸入钢水.b.钢水包和中间包烘烤不彻底,水汽进入钢水.c.钢水中氢和氧含量高,当钢中的H2以及 C 与O 反应生成的CO 压力大于大气压和钢水静压力时形成气泡.d. 保护渣受潮或结晶器渗水,水份进入铸坯内部.2.2.2 控制措施a.强化钢水脱氧措施.b. 采用保护渣浇注,避免钢水在浇注过程中受污染.c.钢水包和中间包要彻底烘烤,保证干燥.d.加强烧注用保护渣定置管理,防止受潮.e. 加强对结晶器的管理,避免渗、漏水现象,一旦发现渗漏及时更换.2.3 成份不匀2. 3.1 形成原因a. 钢水吹氩搅拌时间不够,顶吹氩时吹氩枪插入的深度不够,底吹氩时底吹压力不够, 从而造成钢水成份不匀.b.所加调整钢水温度的废钢与所浇钢水不是同一钢种. c.钢水混浇或倒浇.d.合金料加入时间过晚或追加料补吹氩不及时.2.3 .2 控制措施a.严格按工艺要求对钢水进行吹氩处理.b.保证所加调温废钢与所浇钢水为同一钢种.c.严禁钢水混浇或倒浇.d.出钢时,严格按时加入合金料,避免加入时间过晚;追加料后,一定要及时补吹氩.2.4 内部夹杂2.4.1 形成原因a.钢水纯净度差,钢液中杂质元素和非金属氧化物含量高.b.钢水浇注过程中对钢流的保护不好,钢水二次氧化严重. c.结晶器钢液面波动严重, 造成夹杂物卷入铸坯内部. d.正常浇钢时,中间包液面过低,夹杂物上浮时间短,导致夹杂物随钢流进入铸坯内部.e.保护渣性能不良,结晶器钢液上的溶渣层太薄,熔渣吸收夹杂物的能力差.2.4. 2控制措施a. 严格按工艺要求对钢水进行吹氩处理,促使夹杂物充分上浮\b.加强钢水生产过程中的保护,如大包加覆盖剂、钢流保护浇注等防止钢水二次氧化.C 保证对中间包钢流稳定性的控制, 以提高结晶器钢液面的稳定性.d. 改善保护渣性能,提高其吸收夹杂物的能力.e.连铸正常浇钢时,保证中间包液面高度大于350m m .f. 保护渣操作应坚持勤加、少加、勤捞的原则.2.5 中心疏松和穿晶2.5.1形成原因a.中心疏松和穿晶是由钢种的凝固特性决定的,含碳量越高,越易在中心处出现疏松和穿晶.b. 二次冷却过强.铸坯二次冷却强度越大,越易在中心处出现疏松和穿晶.c. 拉速过快.拉速越快,液芯越长,钢水的补缩能力越差,越易出现疏松和穿晶.2.5.2 控制措施a.针对钢种的凝固特性,选择适当的二次冷却强度.b. 合理控制拉坯速度,使之与钢水过热度相适应.c.采用低温快铸工艺.3 小方坯的形状缺陷3.1 菱变3.1.1 形成原因a.结晶器各面或角冷却不均匀. b.结晶器磨损严重,倒锥度过小.c. 铸机二次冷却不均匀.d. 拉坯速度与钢水过热度不匹配,拉速过快.3.1 . 2 控制措施a 提高结晶器铜管的安装精度, 使结晶器各面水缝宽度一致.b.加强结晶器铜管的定期维护,保证倒锥度满足连铸工艺要求.C加强二次冷却系统的维护,保证铸坯的冷却要求. d.在一定的过热度下,正确控制铸坯的拉速e.3.2 鼓肚 3.2.1形成原因a.结晶器下口足辊安装不精确,对铸坯支撑不良.b.结晶器磨损严重,倒锥度过小.c.结晶器下口二次冷却强度不够. 3.2.2 控制措施a.保证结晶器下口足辊的安装精度,使之为坯壳提供良好的支撑.b.加强结晶器的管理,保证定期更换,避免超期服役.c. 在结晶器下口附近采用集中强冷的冷却方式.d. 控制拉坯速度,使之与钢水过热度相匹配.3.3 压扁3.3.1 形成原因a.二次冷却水量太小,铸坯矫直温度过高.b. 拉速过快,铸坯带液芯矫直.c.拉矫机矫直压力过高.3. 3.2控制措施a.保证二冷水量与拉速相匹配, 对铸坯充分冷却.b.控制拉速,使之与钢水过热度相匹配.c.及时检查并调整拉矫系统的压力,保证正常的工作压力.综上所述,必须大力加强全面质量管理,从人、机、料、法、环入手,不断提高操作工人的技术素质,增强其责任心,加强标准化操作和管理,不断进行技术攻关,使铸坯的质量缺陷得到有。
小方坯连铸中碳钢铸坯表面缺陷与保护渣性能选择
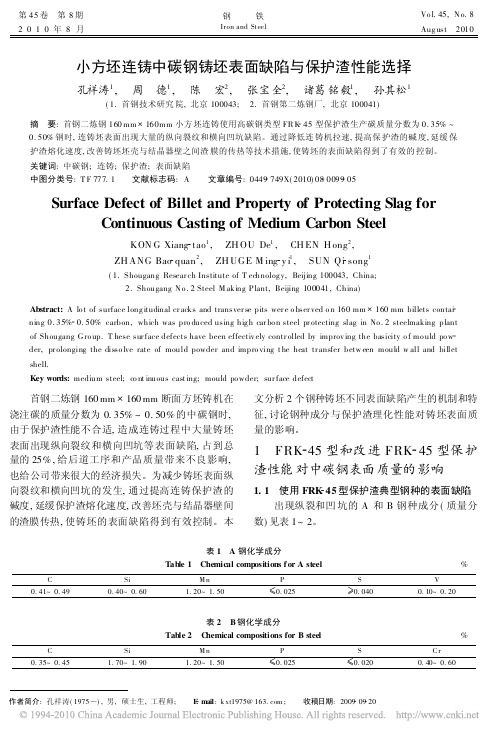
第45卷 第8期 2010年8月钢铁Iron and SteelVo l.45,N o.8Aug ust 2010小方坯连铸中碳钢铸坯表面缺陷与保护渣性能选择孔祥涛1, 周 德1, 陈 宏2, 张宝全2, 诸葛铭毅1, 孙其松1(1.首钢技术研究院,北京100043; 2.首钢第二炼钢厂,北京100041)摘 要:首钢二炼钢160mm 160mm 小方坯连铸使用高碳钢类型FR K 45型保护渣生产碳质量分数为0.35%~0.50%钢时,连铸坯表面出现大量的纵向裂纹和横向凹坑缺陷。
通过降低连铸机拉速,提高保护渣的碱度,延缓保护渣熔化速度,改善铸坯坯壳与结晶器壁之间渣膜的传热等技术措施,使铸坯的表面缺陷得到了有效的控制。
关键词:中碳钢;连铸;保护渣;表面缺陷中图分类号:T F 777.1 文献标志码:A 文章编号:0449 749X(2010)08 0099 05Surface Defect of Billet and Property of Protecting Slag forContinuous Casting of Medium Carbon SteelKON G Xiang tao 1, ZH OU De 1, CH EN H ong 2,ZH ANG Bao quan 2, ZH UGE M ing y i 1, SUN Qi song 1(1.Shougang Resear ch Institute of T echnolog y,Beijing 100043,China;2.Shougang N o.2Steel M aking P lant,Beijing 100041,China)Abstract:A lo t of surface long itudinal cr acks and transver se pits wer e o bser ved o n 160mm 160mm billets contai ning 0.35% 0.50%carbon,which was pro duced using hig h car bo n steel pr otecting slag in No.2steelmaking plant of Shougang G ro up.T hese sur face defects have been effectiv ely contr olled by improv ing the basicity o f mo uld po w der,pr olonging the disso lve rate of mould powder and impro ving t he heat tr ansfer betw een mould w all and billet shell.Key words:medium steel;co nt inuous cast ing;mould po wder;sur face defect作者简介:孔祥涛(1975 ),男,硕士生,工程师; E mail :k xt1975@ ; 收稿日期:2009 09 20首钢二炼钢160mm 160mm 断面方坯铸机在浇注碳的质量分数为0.35%~0.50%的中碳钢时,由于保护渣性能不合适,造成连铸过程中大量铸坯表面出现纵向裂纹和横向凹坑等表面缺陷,占到总量的25%,给后道工序和产品质量带来不良影响,也给公司带来很大的经济损失。
211172579_连铸方坯的常见表面缺陷及控制

管理及其他M anagement and other连铸方坯的常见表面缺陷及控制康旭辉摘要:连铸方坯表面的质量直接影响材料轧制后成品的质量,而近年来,我国部分企业在连铸方坯生产的过程中,存在诸多的表面缺陷问题,不能确保生产的质量和效果。
基于此,本文分析连铸方坯常见表面缺陷问题,提出几点表面缺陷控制的建议和措施,旨在为增强连铸方坯的表面质量提供帮助。
关键词:连铸方坯;常见表面缺陷;控制全面掌握方坯缺陷的类型、形成机理和消除途径是方坯质量控制的关键。
目前,国内外钢铁企业在钢坯质量控制方面取得了可喜的成绩,并获得了大量的生产数据和实际操作经验。
全面提高方坯质量,对提高连铸方坯成品率、改善钢材质量、节能降耗、降低成本具有重要意义。
连铸钢属于直接浇注钢水的工艺。
它的出现从根本上改变了主导了一个世纪的钢锭开坯过程。
液态金属连铸钢的概念早在19世纪中叶就被提出。
1840年,美国的销售商获得了连铸铅管的专利。
1846年,转炉的发明者贝塞默使用水冷旋转双辊连铸机生产锡箔、铅板和玻璃板。
1872年,David提出了移动式结晶器连铸的概念。
1886年~1889年,提出了立式连铸机的设计方案。
1921年,皮尔逊提出了结晶器振动的概念,即结晶器振动使板坯和结晶器之间连续的相对运动。
1933年,连铸的先驱德国准噶斯人建造了第一台1700t/月振动结晶器立式连铸机。
20世纪30年代,第一个成功铸造铜铝合金的有色金属连铸应用于生产。
目前,部分企业在连铸方坯生产的过程中,方坯表面的质量波动幅度很高,存在脱方缺陷、凹陷,缺陷和渣沟缺陷等,不能确保整体结构表面质量符合标准要求,对特钢产品生产质量造成一定的危害,因此,在连铸方坯实际生产的过程中需结合具体表面缺陷问题的发生原因与实际情况,采用有效的措施进行控制,确保连铸方坯表面质量符合标准规范,为特钢产品高质量生产夯实基础。
1 连铸方坯的常见表面缺陷和发生原因1.1 渣沟缺陷与原因从实际情况而言,连铸方坯表面出现渣沟缺陷问题,轧制以后线材表面出现裂纹缺陷问题的发生存在直接联系,从表面观察可以发现坯件有纵向贯通性的沟状缺陷问题,具体是在连铸方坯的内弧部分分布,很小一部分会在侧弧的位置,采用跟踪性轧制12.5mm绞丝钢实验的方式,可以发现线材的表面存在裂纹问题。
- 1、下载文档前请自行甄别文档内容的完整性,平台不提供额外的编辑、内容补充、找答案等附加服务。
- 2、"仅部分预览"的文档,不可在线预览部分如存在完整性等问题,可反馈申请退款(可完整预览的文档不适用该条件!)。
- 3、如文档侵犯您的权益,请联系客服反馈,我们会尽快为您处理(人工客服工作时间:9:00-18:30)。
( h eerhIs tt o eh o g ) ( o2 S e kn ln) T eR sac tu f c nl y N . t l igPat ni e T o e ma
A s a t W h nte F bt c r e h RK- 5 mo l u e o ih c r o t e w r s d t r d c h . 5 一 4 u d f x s frh a b n se l e e u e o p o u e t e 0 3 % l g 0 5 % me i m a b n se l o fs ra e l n i d n lc a k n r n v re p t wee o s r e .0 d u c r o te ,a lt u fc o gt i a r c sa d t s e s i r b e v d o u a s o e 1 0 in × 1 0 mm i es w ih we e p o u e y t e No 2 s ema i g p a to h u a g nt 6 3 6 h n b l t h c r r d c d b h . t l k n ln fS o g n l e
f r M e i m r o S e lby Co i uo si a o d u Ca bin t e ntn usCa tng W y
KONG a g a Xin to ZHOU g ANG o u n Ba q a
中碳 钢 连铸 小 方 坯 表 面缺 陷与保 护 渣 性 能选 择
孔祥涛 周
摘 要
德 诸葛铭毅 陈
宏 张宝 全
( 术研 究院 ) ( 技 第二 炼钢厂 )
首 钢第 二炼 钢 厂 10 m l×10mm 小方 坯连 铸 使用 高碳 钢 用 F K 4 6 i 6 l R .5型保 护渣 生 产碳 含量 为
A,B 钢 连 铸 工 艺 参 数 为 :二 冷 比水 量 为
连铸坯的表面缺陷。本文分析了 A ,B两个钢种 连铸坯不同表面缺陷产生的机理和特征 ,重点讨 论了钢种成分与保护渣理化性能对连铸坯表面质
带来 较大 的经 济损 失 … 。
1 使用原保护渣及其改进后 对连铸坯表 面质量的影响
1 1 使用原 保 护渣的连 铸坯 表面 缺 陷 . 所 对 比的 A,B钢化 学成 分见表 1 。
表 1 A, B钢 化 学 成 分
钢 种 c S i Mn P S
%
首 钢第 二 炼钢 厂 10mmx10mm 8流 小方 6 6
坯连铸机 ( 简称小 方坯连铸机 )在浇注碳含量 为 03 %~05 % 的 中碳 钢 时 ,初 期 由 于使 用 .5 .0 F K一5型结 晶器保护 渣 ( 为原 保 护渣 ) 不合 R 4 称
适 ,大量 连 铸 坯 出 现 纵 裂 和 横 向 凹坑 等 表 面 缺 陷 ,有 表面缺 陷 的连铸 坯量 占中碳 钢连 铸坯 总量 的 2 % ,不利 于 后 道 工 序 和产 品质 量 ,给 公 司 5
V
为 了减少 连 铸 坯 表 面 纵 裂 和 横 向 凹 坑 的发 生 ,通过 提高 保护 渣碱 度 、延 缓保 护渣熔 速 ,改 善 了坯壳 与结 晶器 壁间 的渣膜 传热 ,有效 控 制 了
A 0 4 ~ 4 . 0- . 0 . O . O ≤0 0 5≥ 0 0 0≤O. 0 . 1 0. 9 0 4 0 6 1 2 ~1 5 .2 .4 2 B 0. 8 . 5 . 0 ̄1 9 . O . 0 ≤0 O 5≤ 0 o2 3 -0 4 1 7 . 0 1 2 ~1 5 .2 . O≤0. 0 6
0 3 %一 .0 的中碳钢时 ,大量连铸坯表面 出现纵裂 和横 向凹坑 。通过 降低连铸机 拉速 、提 高保 护渣碱 .5 0 5 % 度及延缓保护渣熔速 ,改善 了连铸坯坯壳与结 晶器壁间的渣膜传热 ,使连铸坯 的表 面缺 陷得到 了有效控制 。 关键词 连铸 中碳钢 保护渣 表面缺陷
Th l tS ra e fc sa d Ch ie o o l l x sPr p ris e Bi e u f c d De e t n oc fM u d F u e o e t l e
G o p h uhrd c gtecs n a ,i poigtebsc yo o l f xs rl gn e r .T r g e ui at grt m rv ai t fm udl e ,po n gt u o n h i e n h i u oi h
d s ou in r t ft e mo l l e n r vn e t e ma a s rb t e u d wal n i e is l t a e o u d f o h x u sa d i o i g t h r l t n f ewe n mo l a d b l t mp h r e l l s e h e s ra e d f c sc u d b f ci ey c n r l d h U.t u f c e e t o l e e e t l o t l . v o e Ke o d c n i u u a t g y W r s o t o s c si ,me i m a b n se l n n d u c r o te ,mo l u e ,s r c ee t ud f l x s u a e d fc f