轴承套圈热处理作业指导书
轴承内外圈热处理
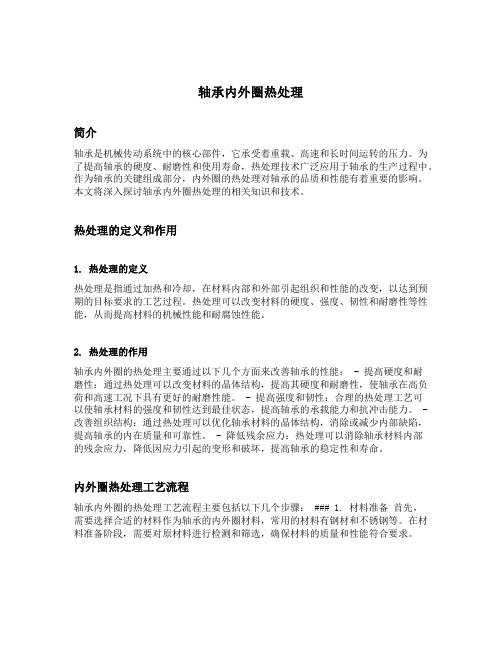
轴承内外圈热处理简介轴承是机械传动系统中的核心部件,它承受着重载、高速和长时间运转的压力。
为了提高轴承的硬度、耐磨性和使用寿命,热处理技术广泛应用于轴承的生产过程中。
作为轴承的关键组成部分,内外圈的热处理对轴承的品质和性能有着重要的影响。
本文将深入探讨轴承内外圈热处理的相关知识和技术。
热处理的定义和作用1. 热处理的定义热处理是指通过加热和冷却,在材料内部和外部引起组织和性能的改变,以达到预期的目标要求的工艺过程。
热处理可以改变材料的硬度、强度、韧性和耐磨性等性能,从而提高材料的机械性能和耐腐蚀性能。
2. 热处理的作用轴承内外圈的热处理主要通过以下几个方面来改善轴承的性能: - 提高硬度和耐磨性:通过热处理可以改变材料的晶体结构,提高其硬度和耐磨性,使轴承在高负荷和高速工况下具有更好的耐磨性能。
- 提高强度和韧性:合理的热处理工艺可以使轴承材料的强度和韧性达到最佳状态,提高轴承的承载能力和抗冲击能力。
- 改善组织结构:通过热处理可以优化轴承材料的晶体结构,消除或减少内部缺陷,提高轴承的内在质量和可靠性。
- 降低残余应力:热处理可以消除轴承材料内部的残余应力,降低因应力引起的变形和破坏,提高轴承的稳定性和寿命。
内外圈热处理工艺流程轴承内外圈的热处理工艺流程主要包括以下几个步骤: ### 1. 材料准备首先,需要选择合适的材料作为轴承的内外圈材料,常用的材料有钢材和不锈钢等。
在材料准备阶段,需要对原材料进行检测和筛选,确保材料的质量和性能符合要求。
加热处理是热处理的核心步骤,它通过加热和冷却来改变轴承材料的组织和性能。
加热处理可以分为多个阶段,包括预热、保温和冷却三个阶段。
预热阶段主要是将材料加热到合适的温度,以便于后续的变形和组织调整。
保温阶段是将材料保持在一定温度下一定时间,使材料的晶体结构发生变化。
冷却阶段是将材料迅速冷却到室温,以固定材料的新组织结构。
3. 表面处理表面处理是为了改善轴承的表面质量和耐磨性。
(完整word版)20CrNi2MoA火车轴承套圈的热处理工艺设计
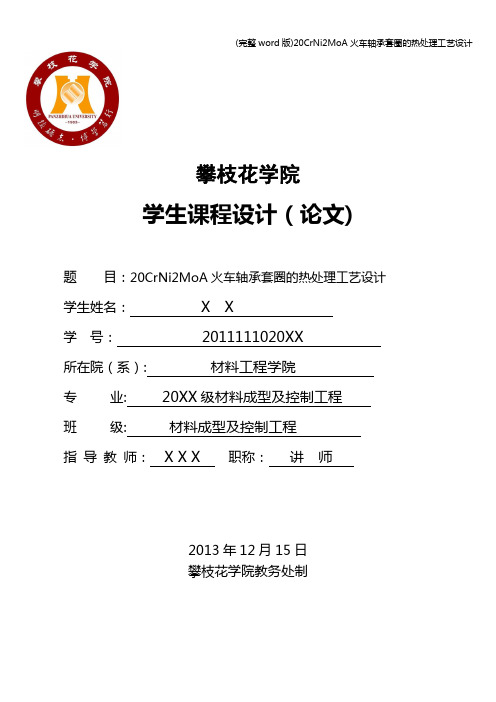
攀枝花学院学生课程设计(论文)题目:20CrNi2MoA火车轴承套圈的热处理工艺设计学生姓名:X X学号:2011111020XX所在院(系):材料工程学院专业:20XX级材料成型及控制工程班级:材料成型及控制工程指导教师:X X X 职称:讲师2013年12月15日攀枝花学院教务处制攀枝花学院本科学生课程设计任务书注:任务书由指导教师填写。
课程设计(论文)指导教师成绩评定表摘要本课设计了20CrNi2MoA火车轴承套圈的热处理工艺设计。
主要的工艺过程包括锻造、预备热处理(完全退火)、渗碳、淬火+低温回火等过程。
通过各种不同的工艺过程进行恰当的处理可以获得各种性能良好的材料并且满足各项性能的要求。
20CrNi2MoA钢能承受高强度摩擦和载荷,有极高的韧性,可以作为表面强化型的渗碳钢应用于渗碳齿轮、渗碳轴承等零件上;也可以经低温回火后应用于诸如挖掘机斗齿(镐牙)、农用机械磨损件等要求耐磨损、耐冲击的零件上轴承套圈是火车中重要的承受载荷的零件.其在轮毂中起到固定连接其他部件的作用,并且在火车运动过程中起到缓冲的作用,降低主要工作部件承受的载荷,减少其损耗。
关键词:20CrNi2MoA钢,完全退火,低温回火,火车轴承套圈目录摘要 (Ⅰ)1、设计任务 (1)1.1设计任务 (1)1.2设计的技术要求 (1)2、设计方案 (2)2.1 变速箱设计的分析 (2)2。
1.1工作条件 (2)2.1.2失效形式 (2)2。
1。
3性能要求 (2)2。
2钢种材料 (3)3、设计说明 (4)3.1加工工艺流程 (4)3。
2具体热处理工艺 (4)3.2.1预备热处理工艺 (5)3。
2.2机械加工 (5)3。
2。
3渗碳工艺 (5)3。
2。
4淬火+低温回火热处理工艺 (6)4、分析与讨论 (8)5、结束语 (9)6、热处理工艺卡片 (10)参考文献 (11)1 设计任务1。
1设计任务20CrNi2MoA火车轴承套圈的热处理工艺设计。
ywy渗碳钢轴承零件热处理作业指导书

JB/T8881《滚动轴承零件渗碳热处理质量标准》。
3渗碳前技术要求
3.1渗碳炉及工装技术要求
3.1.1渗碳所用的加热炉,必须保证密封性能好。
3.1.2渗碳用炉停炉时间较长,或者经过中小修,在使用前要按工艺要求烘干。
3.1.3渗碳件入炉之前,要检查加热炉电控、温控系统、渗剂碳控装置、风机、各区仪表,,马弗及密封部位无泄露,无安全隐患,如有故障,应立即排除,否则渗碳件不允许入炉。
940℃
(渗碳)
排气根据检查结果调整滴数
3 ~5h 24~30h 20~24h 16~24h
苯(渗碳油)
图3: RJJ-160电炉,G20Cr2Ni4A滚子(硬化层小于4.0mm)渗碳剂供给量
940℃
240滴/分
(渗碳)
(排气)根据检查结果调整滴数
3~5h 14~16h 9~12h
苯(渗碳油)
图4:RJJ-280材料G20CrNi2MoA套圈渗碳剂供给量
312渗碳用炉停炉时间较长或者经过中小修在使用前要按工艺要求烘313渗碳件入炉之前要检查加热炉电控温控系统渗剂碳控装置风机各区仪表马弗及密封部位无泄露无安全隐患如有故障应立即排除否则渗碳件不允许314渗碳用支架在使用之前必须经清理表面必须保持干燥支架表面不允许有油和其它脏物
瓦房店冶矿轴承制造有限公司
6.3.2井式淬火炉,型号:RJJ-160电炉,淬火冷却采用手动压模,第一外圈每炉2件,大挡边对应摆放。第二外圈和内圈每炉分别为1件。
6.4滚子淬火加热数量规定
6.4.1箱式电炉,型号:RJX-75电炉,每炉加工12盘,RJX-105电炉,每炉加工16盘;各盘数量及其各项工艺参数详见作业指导卡。
6.4.2井式电炉,型号:RJJ-180电炉,滚子均匀摆放在筛盘上加热淬火,淬火筛盘直径为1.5米,滚子摆放间距为30~40毫米,滚子每盘加热重量规定。滚子每盘加热重量按其单重和有效直径尺寸大小来确定,滚子有效直径尺寸小于70毫米,每盘330~360kg。滚子有效直径尺寸在70~100毫米,每盘重量360~420kg。滚子有效直径尺寸大于100毫米,每盘重量430~550kg。
哈工大热处理原理与工艺大作业-精密轴承零件热处理

精密轴承是指旋转精度、外形尺寸精度高和表面粗糙度较小的轴承,
在我国的标准中是指p4级和高于P4级轴承。按照ISO的分级标准分
为:P0,P6,P5,P4,P2.等级依次增高,其中P0为普通精度, 其他等级都是 精密级别。(当然,不同分级标准,不同类型的轴承,他们的分级方法有
钢球
5、10、16级
中小型套圈
P2级 P4级
粗磨后:140~180℃,4~12h 细磨后:120~160℃,3~24h
大型钢球
20级
120~160℃,3~5h
大型、特大型套圈
P0~P6级
120~160℃,3~4h
轴承零件成品硬度要求
谢 谢
基于普通球化退火时间长、生产 效率低的缺点提出的等温温度的 高低对退火后的硬度影响很大, 温度越低则硬度越高
退火缺陷及其对策
检查项目 脱碳层 缺陷名称 脱碳层超过规定深度 补救方法 改其他型号或报废
显微组织
欠热
点状珠光体加部分 细片状珠光体 过热 粒状珠光体加部分 粗片状珠光体 粗大颗粒碳化物 网状碳化物超过规定级别
备注 , 滚子直径≤28mm
钢球
5、10、 16级 P2级、P4级
150~180℃,3~4h
钢球直径<48.76mm
Байду номын сангаас
中小型套圈
160~200℃,3~4h
附加回火(稳定化处理)
目的:附加回火的作用是消除磨削应力,迚一步稳定组织,以便于提高零件的尺寸稳
定性。
参数:
零件名称 中小型滚子 轴承零件精度等级 Ⅰ级、Ⅱ级 回火温度和时间 120~160℃,12h 120~160℃,3~4h 120~160℃,12h
轴承套圈发黑作业指导书

黑角轴承套圈发黑处理作业指导书1.目的有效规范轴承套圈发黑的操作,提高套圈的发黑质量和节约发黑成本。
2.适用范围适用于黑边产品套圈毛坯热处理后端面磨加工前的发黑处理工序。
3.具体操作流程如下:3.1发黑操作人员到车间或仓库往装配搬运物料时,应首先确认产品标识情况,确认产品的型号、需要发黑处理的数量、是否有生锈现象等;3.2 在加热发黑液的过程中注意控制发黑液温度,不能让发黑液长期处于沸腾状态;3.3通常对小产品装铁篮子,较大产品用铁丝串成串然后放入相应的溶液中,放置过程要注意轻拿轻放,不能让溶液溅出以免烧伤;3.4在盐酸除锈和发黑后要迅速放入冷水池,以免长时间接触空气引起氧化和二次生锈;冷水池中的冷水要不停循环以免被碱化或酸化;3.5 产品在发黑液中浸泡时间一般为10分钟左右,若10分钟后产品仍然不黑或有发红发黄现象应及时通知相关技术人员;3.6 发黑的质量要求以标准件为标准,目测确认是否合格,不合格的产品可放入发黑液中进行二次发黑,但时间不宜过长;3.7 停止发黑熄火后应分2~3次给发黑液中注入适量清水(10~20L)。
4.发黑液、除油去脂液、皂化液等介质溶液的要求4.1发黑液以氢氧化钠(NaOH)为主,加入适量的亚硝酸钠(NaNO2)和硝酸钠(NaNO3),具体配比参照水1000kg、氢氧化钠700kg、亚硝酸钠150kg、硝酸钠70kg配比,沸腾后温度控制在130~150摄氏度。
4.2除油去脂液以工业纯碱(NaCO3)水溶液作为介质,加热至沸腾状态浸泡5~10分钟即可。
4.3皂化液即热肥皂水,加热至40~70摄氏度将产品在其中浸洗1分钟左右,以防止产品氧化。
5.其它要求5.1发黑后的产品能有效降低生锈的可能,但应远离酸碱等腐蚀性较强的溶液,以免破坏发黑层。
5.2发黑过程中必须防止产品的磕碰伤。
5.3 由于发黑是强碱加热氧化过程,其过程中会产生较大的刺激性气味,操作人员要尽量避免发黑液蒸气直接喷射到皮肤,以免烧伤或刺激皮肤,若不小心有碱液溅到口中或眼睛等敏感部位,应立即用清水冲洗。
轴承套圈热处理作业指导书
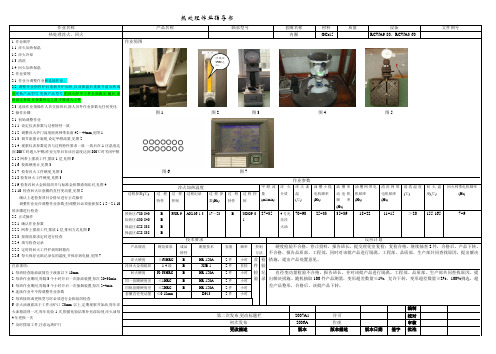
编制 第二次发布,更改标题栏 初次发布 更改描述 2007A1 2006A 版本 许可 作废 版本描述 版本日期 签字 . 校对 审核 批准
浮球在 27~35之
产品名称 作业简图
轴承型15
质量
设备 RCWA9-80,RCWA3-60
文件图号
间
图1
图2
图3
图4
图5
图6
图7 作业参数 淬火加热温度
过 程 控制 过程纪录 过 程 参 数(Hz) 过 程 特性 过程控 制 甲 醇 流 量 (ml/min) 4 号光 亮淬 火油 淬 火 介质 淬火油 温 (℃) 油槽小提 电机频率 (Hz) 油 槽 串 动 电 机 频 (Hz) 率 油槽网带电 机频率 (Hz) 清洗网带 电机频率 (Hz) 清洗温度 (℃) 回 火 温 度(℃) 回火网带电机频率 (Hz)
反应计划 硬度检验不合格,停止投料,报告班长,提交理化室复检;复检合格,继续抽查 2 件,合格后,产品下转。 方法 不合格,报告品质部、工程部,同时对该批产品进行隔离。工程部、品质部、生产部共同查找原因,提出解决 首 检 措施,提出产品处置意见。 件 验 检 纪 直径变动量检验不合格,报告班长,并对该批产品进行隔离。工程部、品质部、生产部共同查找原因,提 验 录 出解决措施。随机抽取 100 件产品测量,变形超差数量≤1%,允许下转,变形超差数量≥2%,100%挑选,超 差产品整形,合格后,该批产品下转。
热处理作业指导书
作业名称 热处理淬火、回火
1 作业顺序 1.1 淬火加热保温 1.2 淬火冷却 1.3 清洗 1.4 回火加热保温 2 作业要领 2.1 作业分调整作业和连续作业。 2.2 调整作业指停炉后重新开炉加热,以及保温后重新升温加热或 者更换产品型号.更换产品型号,把淬火炉中工件全部跑完.随后,重 新设定参数,在参数稳定之前,不准放入工件 2.3 连续作业指操作人员交接班后,除人员外作业参数无任何变化 2 操作步骤 2.1 初始调整作业 2.1.1 设定仪表参数与过程特性一致 2.1.2 调整淬火炉门高度距离网带表面 42~44mm,见图 1 2.1.3 调节流量计旋钮,设定甲醇流量,见图 2 2.1.4 观察仪表参数是否与过程特性要求一致.一致后在 1 区温度达 到 800℃时通入甲醇;作业完毕后在该区温度达到 800℃时关闭甲醇 2.1.5 网带上摆放工件,摆放 1 层,见图 6 2.1.6 校准硬度计,见图 3 2.1.7 检查淬火工件硬度,见图 3 2.1.8 检查回火工件硬度,见图 3 2.1.9 检查淬回火金相组织并与标准金相图谱相比对,见图 4 2.1.10 检查回火后套圈的直径变动量,见图 5 确认上述检查项目合格后进行正式操作 调整作业允许调整作业参数,但调整后必须重新按 2.1.5~2.1.10 的步骤进行检查 2.2 正式操作 2.2.1 确认作业参数 2.2.2 网带上摆放工件,摆放 1 层,排列方式见图 6 2.2.3 按规范要求定时进行检查 2.2.4 填写检查记录 2.2.5 定时将回火工件铲到周转箱内 2.2.6 每天保存无纸记录仪的温度,并保存到电脑,见图 7 注意事项: 1 每班检查除油滚筒位于液面以下 10mm 2 每班作业期间,每隔 3 个小时开启一次除油装置,每次 20~30min 3 每班作业期间,每隔 3 个小时开启一次抽烟装置,每次 2~4min 4 连续作业中不得调整作业参数 5 每班接班或更换型号时必须进行金相组织检查 6 淬火油液面高于工件出炉口 50mm 以上,定期观察并加油,每年淬 火油箱清理一次,每年化验 1 次,根据化验结果补充添加剂,淬火油每 4 年更换一次 7 及时摆放工件,注意远离炉门 预热区:780-840 加热区:830-840 保温区:828-838 保温区:828-838 过程参数(℃) 过 程 特性
轴承套圈热处理技术

规格
共4页第1页
轴承套圈热处理变形
技术条件
编号
代替
轴承外圈淬、回火椭圆度见表1
表1
设计外径
轻、中、重系列
特轻、超轻系列允许椭圆度
特轻、窄、超轻窄系列允许椭圆度
外径设计留量
淬、回火后磨量
允许椭圆度
>
≤
≥
≤
30
50
0.25+0.15
0.15
0.45
0.15
0.18
0.20
50
80
0.30+0.20
0.18
400
500
0.55
0.55
0.70
注:
1)挠曲度采用311仪器测量,以有沟面做没量面。
2)圆柱滚子轴承的平挡圈,其挠曲度按上表执行。
3)推力套圈端面凸凹度,是其挠曲度的1/2。
4)用塞尺测得的值,是本表的1/2。
0.35+0.13
0.30
0.40+0.13
0.35
0.50+0.13
0.45
120
180
0.40+0.15
0.35
0.50+0.15
0.45
0.60+0.15
0.50
180
250
0.45+0.17
0.40
0.55+0.17
0.48
0.65+0.17
0.55
250
315
0.50+0.20
0.45
0.60+0.20
共4页第4页
编号
4、推力轴承套圈和内隔圈热处理后变形量见表4
滚动轴承热处理工艺

1.高碳铬轴承钢
• 目前,轴承行业普遍使用的主要是 GCr15、GCr15SiMn两种材料,是轴承钢
• • • •
总量的80%以上。 GCr15钢大量用来制造汽车、拖拉机等所使用的发动机轴承,机床、 电机等所使用的主轴轴承以及铁路车辆、矿山机械、通用机械用轴承。 在GB/T18254《高碳铬轴承钢》标准中,高碳铬轴承钢GCr4、GCr15、 GCr15SiMn、GCr15SiMo、GCr18Mo几种。 GCr15SiMn、 GCr15SiMo主要用于制造壁厚比较大的轴承。 GCr15SiMn适用 于制造壁厚在15mm---35mm范围内的轴承, GCr15SiMo适用于制造壁厚大 于35mm尺寸的轴承。如各种大型和特大型轴承,多用在重型机床及轧钢机 无较大冲击载荷的工作条件下。 GCr4轴承钢是限制淬透性钢,即经过合适的热处理可得到表面硬心部软的硬 度匹配,具有良好的耐磨性,抗冲击性和断裂韧性及高的接触疲劳寿命。
•
•
•
• 8套圈壁厚。≤25cm 滚子直径≤ 32cm
钢球直径≤ 50cm。
• 9套圈壁厚取22cm 套圈直径取32cm 钢球直径25cm
• 综上述条件:选择Gcr15作为材料
四、热处理工艺曲线
• 套圈:备料→锻造→球化退火→机械加工
→淬火、低温回火→检验→磨削加工 • 滚珠:备料→冷镦→硬磨→附加回火→抛 → 光
• • •
2、滚动轴承的受力分析
• 滚动轴承工作时,滚动体和套圈均受周期性交变 • •
载荷,在周期载荷作用下,在套圈和滚动体表面 都会产生小块金属金属剥落而产生疲劳损坏。 滚动体与滚道之间是点接触,故其承受接触应力 和冲击力,接触应力可达3000~3500Mpa 循环应 力可达万次/min 受纯轴向载荷时,各滚动体受力相同。受径向载 荷时,上半圈滚动体不受力。 下半圈各滚动 体受 力大小均不相同,由下列公式导出;Fmax=5Fr/z
- 1、下载文档前请自行甄别文档内容的完整性,平台不提供额外的编辑、内容补充、找答案等附加服务。
- 2、"仅部分预览"的文档,不可在线预览部分如存在完整性等问题,可反馈申请退款(可完整预览的文档不适用该条件!)。
- 3、如文档侵犯您的权益,请联系客服反馈,我们会尽快为您处理(人工客服工作时间:9:00-18:30)。
B B B B
PXR-9
AX106-1-3
17~23
B
NDOP-0 1
27~35
70~90
25~33
35~39
18~22
11~15
>20
155-165
7~9
技术要求
产品规范 规范要求 成品 特性 淬火硬度 淬回火金相组织 回火硬度 同一套圈硬度差 同批套圈硬度差 套圈直径变动量 ≥63HRC 1-4 级 60-63HRC ≤1HRC ≤2HRC ≤0.18mm B B B B B HR-150A XJB-1 HR-150A HR-150A HR-150A D913 2件 2件 2件 2件 2件 2件 小时 首检 小时 小时 小时 小时 测量技术 容量 频率 控制
反应计划 硬度检验不合格,停止投料,报告班长,提交理化室复检;复检合格,继续抽查 2 件,合格后,产品下转。 方法 不合格,报告品质部、工程部,同时对该批产品进行隔离。工程部、品质部、生产部共同查找原因,提出解决 首 检 措施,提出产品处置意见。 件 验 检 纪 直径变动量检验不合格,报告班长,并对该批产品进行隔离。工程部、品质部、生产部共同查找原因,提 验 录 出解决措施。随机抽取 100 件产品测量,变形超差数量≤1%,允许下转,变形超差数量≥2%,100%挑选,超 差产品整形,合格后,该批产品下转。
编制 第二次发布,更改标题栏 初次发布 更改描述 2007A1 2006A 版本 许可 作废 版本描述 版本日期 签字 . 校对 审核 批准
浮球在 27~35之
产品名称 作业简图
பைடு நூலகம்轴承型号
套圈名称 内圈
材料 GCr15
质量
设备 RCWA9-80,RCWA3-60
文件图号
间
图1
图2
图3
图4
图5
图6
图7 作业参数 淬火加热温度
过 程 控制 过程纪录 过 程 参 数(Hz) 过 程 特性 过程控 制 甲 醇 流 量 (ml/min) 4 号光 亮淬 火油 淬 火 介质 淬火油 温 (℃) 油槽小提 电机频率 (Hz) 油 槽 串 动 电 机 频 (Hz) 率 油槽网带电 机频率 (Hz) 清洗网带 电机频率 (Hz) 清洗温度 (℃) 回 火 温 度(℃) 回火网带电机频率 (Hz)
热处理作业指导书
作业名称 热处理淬火、回火
1 作业顺序 1.1 淬火加热保温 1.2 淬火冷却 1.3 清洗 1.4 回火加热保温 2 作业要领 2.1 作业分调整作业和连续作业。 2.2 调整作业指停炉后重新开炉加热,以及保温后重新升温加热或 者更换产品型号.更换产品型号,把淬火炉中工件全部跑完.随后,重 新设定参数,在参数稳定之前,不准放入工件 2.3 连续作业指操作人员交接班后,除人员外作业参数无任何变化 2 操作步骤 2.1 初始调整作业 2.1.1 设定仪表参数与过程特性一致 2.1.2 调整淬火炉门高度距离网带表面 42~44mm,见图 1 2.1.3 调节流量计旋钮,设定甲醇流量,见图 2 2.1.4 观察仪表参数是否与过程特性要求一致.一致后在 1 区温度达 到 800℃时通入甲醇;作业完毕后在该区温度达到 800℃时关闭甲醇 2.1.5 网带上摆放工件,摆放 1 层,见图 6 2.1.6 校准硬度计,见图 3 2.1.7 检查淬火工件硬度,见图 3 2.1.8 检查回火工件硬度,见图 3 2.1.9 检查淬回火金相组织并与标准金相图谱相比对,见图 4 2.1.10 检查回火后套圈的直径变动量,见图 5 确认上述检查项目合格后进行正式操作 调整作业允许调整作业参数,但调整后必须重新按 2.1.5~2.1.10 的步骤进行检查 2.2 正式操作 2.2.1 确认作业参数 2.2.2 网带上摆放工件,摆放 1 层,排列方式见图 6 2.2.3 按规范要求定时进行检查 2.2.4 填写检查记录 2.2.5 定时将回火工件铲到周转箱内 2.2.6 每天保存无纸记录仪的温度,并保存到电脑,见图 7 注意事项: 1 每班检查除油滚筒位于液面以下 10mm 2 每班作业期间,每隔 3 个小时开启一次除油装置,每次 20~30min 3 每班作业期间,每隔 3 个小时开启一次抽烟装置,每次 2~4min 4 连续作业中不得调整作业参数 5 每班接班或更换型号时必须进行金相组织检查 6 淬火油液面高于工件出炉口 50mm 以上,定期观察并加油,每年淬 火油箱清理一次,每年化验 1 次,根据化验结果补充添加剂,淬火油每 4 年更换一次 7 及时摆放工件,注意远离炉门 预热区:780-840 加热区:830-840 保温区:828-838 保温区:828-838 过程参数(℃) 过 程 特性