UG数控加工实例
UG数控车床编程实例
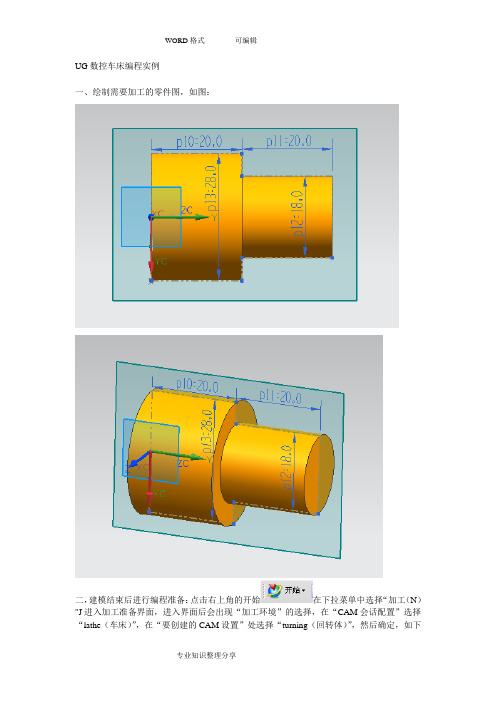
UG数控车床编程实例一、绘制需要加工的零件图,如图:二,建模结束后进行编程准备:点击右上角的开始在下拉菜单中选择“加工(N)"J进入加工准备界面,进入界面后会出现“加工环境”的选择,在“CAM会话配置”选择“lathe(车床)”,在“要创建的CAM设置”处选择“turning(回转体)”,然后确定,如下图:接下来你会在窗口的右下角看到一些工具栏:“顺序功能视图”、“机床视图”、“几何视图”、“加工方法视图”,三、编程设置1、创建程序:点击顺序功能视图,在左上角点击对应的创建程序按钮进行创建程序,出现创建程序对话框,选择和图对应的选项,注意不要选错子对象与父对象,如这里的“PROGRAM_1”是“PROGRAM”的子对象,反之父对象,如图:在上面对话框后的对话框直接确定,不用选择直接确定。
2、创建刀具:点击“机床视图”,在左上角点击对应的创建刀具按钮进行创建刀具,在弹出的对话框中选择粗车刀具“OD_80_L”,具体如图:确定进入下一步。
出现下面对话框:将刀具号命名为一号刀,如需要加刀柄的话在“夹持器”处点选“使用车刀夹持器”3、创建几合体:点击几何视图,在左上角点击对应的创建几何体按钮进行创建几何体,出现创建几何体对话框,选择和图对应的选项:(在创建几何体之前要先将系统自生成的几何体删除,右击中的“MCS_SPINLE”选择删除)选择第一个坐标后点击确定进入坐标的创建(工件坐标)点击圈选处进行坐标创建通过选择Z轴,X轴,原点的方式创建坐标系,后面就直接确定了,没有需要设置的,创建后的坐标如图:4、双击进行指定需要加工的工件,点击后再点击显示框内的待加工零件整体,确定就完事了。
5、双击进行毛坯设置,点击设置毛坯,先点击选择进行坐标点的确定,选择待加工工件的底部中心为远点,如图:设置长度为42mm,直径30mm确定完成毛坯的设置。
6、创建避让(刀具的起点和终点):点击创建几何体,在出现的对话框中选择最后一个创建避让,在几何体处选择“TURNING-WORKPLECE”确定进入下一步。
UGNX8.0数控加工典型实例教程——第2章 平面铣

第2章平面铣2.1平面铣概述平面铣(Planar Milling)是一种常用的操作类型,用来加工直壁平底的零件,可用作平面轮廓、平面区域或平面岛屿的粗加工和精加工,它可平行于零件底面进行多层铣削,典型零件如图2-1所示。
图2-1 典型平面铣零件平面铣是一种2.5轴加工方式,它在加工过程中首先进行水平方向的XY两轴联动,完成一层加工后再进行Z轴下切进入下一层,逐层完成零件加工,通过设置不同的切削方法,平面铣可以完成挖槽或者轮廓外形的加工。
平面铣的特点包括:刀轴固定,底面是平面,各侧壁垂直于底面。
2.2平面铣操作子类型进入加工界面后,单击“刀片”工具条中“创建工序”按钮,系统弹出如图2-2所示“创建工序”对话框,选择操作类型为:mill_planar(平面铣),在平面铣这一加工类型中共有16种操作子类型,每一个图标代表一种子类型,它们定制了平面铣操作参数设置对话框。
选择不同的图标,所弹出的操作对话框也会有所不同,完成的操作功能也会不一样,各操作子类型的说明见表2-1。
图2-2 “创建工序”对话框说明:1. UGNX8.0以前版本称“工序”为“操作”,笔者认为称“操作”更恰当;2. “刀片”工具条可理解为“插入”或“创建”工具条。
表2-1 平面铣(Planar Milling)操作子类型序号图标英文名称中文名称功能说明1 FACE_MILLING_AREA 面铣削区域用于铣削选定的表面区域2 FACE_MILLING 面铣用于铣削整个零件表面3 FACE_MILLING_MANUAL 手工面铣削可以在不同的加工表面设置不同的切削模式4 PLANAR_MILL 基本平面铣适用于使用各种切削模式进行平面类零件的粗加工和精加工5 PLANAR_PROFILE 平面轮廓铣指定切削模式为“跟随轮廓”的平面铣,仅用于精加工侧壁轮廓6 ROUGH_FOLLOW 跟随部件粗铣指定切削模式为“跟随部件”的平面粗铣7 ROUGH_ZIGZAG 往复粗加工指定切削模式为“往复”的平面粗铣8 ROUGH_ZIG 单向粗加工指定切削模式为“单向轮廓”的平面粗铣9 CLEANUP_CORNERS 清理拐角使用切削模式为“跟随部件”,清除以前操作在拐角处余留的材料10 FINISH_WALLS 精加工壁使用切削模式为“轮廓加工”,精加工侧壁轮廓,默认情况下,自动在底面平面留下余量11 FINISH_FLOOR 精加工底面使用切削模式为“跟随部件”,精加工平面,默认情况下,自动在侧壁留下余量12HOLE_MILLING 铣孔用铣刀铣孔13 THREAD_MILLING 螺纹铣适用于在预留孔内铣削螺纹14 PLANAR_TEXT 平面文本对文字曲线进行雕刻加工15 MILL_CONTROL 铣削控制创建机床控制事件,添加后处理命令16 MILL_USER 铣削用户自定义参数建立操作说明:1.第4个是通用操作,可派生出其它各种子类型,其它子类型是在通用操作的基础上派生出来的,主要是针对某一特定的加工情况而定义,即预先指定和限制了一些参数。
UG NX 10.0数控加工编程实例精讲课件第2章
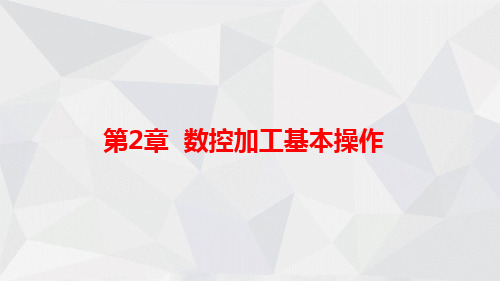
图2-23切削步距选项
2.2 切削步距
恒定 通过指定的距离常数值作为切削的步距值。在用球刀进行精加工时常使用此参数控制 步距,此参数较为直观,但要根据一定的经验给出。 残余高度 通过指定加工后残余材料的高度值来计算出切削步距值。残余髙度一般的设置都很小 ,在0.001~0.01之间,可以先大约设定一个值,系统计算后生成刀轨,再测量出刀 轨的切削步距的大小。大致就可以估计出加工的表面质量,再来调整设定值。 刀具平直百分比 以刀具直径乘以百分比参数的乘积作为切削步距值。工件的粗加工常用此参数,一般 粗加工可设定切削步距为刀具直径的50%〜75%之间。 步距计算时刀具直径是按有效刀具直径计算的,对于平刀和球刀,刀具直径指的是刀 具参数中的直径,而对于牛鼻刀,刀具直径指的是刀具参数中的直径减去两个刀角半 径的差值。 变量平均值 对于双向切削、单向切削、单向带轮廓切削方法,要求指定最大和最小两个切削步距 值,对于跟随周边切削、跟随部件切削、轮廓加工和标准驱动方法,要求指定多个切 削步距值以及每个切削步距值的走刀数量,如图2-24所示。依据可变步距的设定,可 以得到刀轨,刀轨间的距离都按设定的步距 大小和刀路数进行排列。
2.2
2.2
余量的设置和意义
工件的加工一般可分为粗加工、半精加工和精加工等步骤,每一个工序都需要 保留加工余量。 部件余量 在工件所有的表面上指定剩余材料的厚度位。 壁余量 在工件的侧边上指定剩余材料的厚度位,在每—切切削层上,它是在 水平方向测量的数位,应用于工件的所有表面,如图2-16所示。 最终底面余量 在工件的底边上指定剩余材料的厚度值,它是在刀具轴方向测 量的数值,只应用于工件上的水平表面。 检查余量 指定切削时刀具离开检查几何体的距离,如图2-16部件余量。将一 些重要的加正面或者夹具设置为检查几何体,设置余量可以起到安全保护作用 。 修剪余量 指定切削时刀具离开修剪几何体的距离,如图2-16所示。 毛坯余量 指定切削时刀具离开毛坯几何体的距离,毛坯余量可以使用负值, 所以使用毛坯余量丁以放大或缩小毛坯儿何体,如图2-16所示。在切削参数中 ,还需要说明另外一个参数毛坯距离。 毛坯距离 在工件边界或者工件几何体上增加一个偏置距离,而将产生的新的 边界或几何体作为新定义的毛坯几何体。此偏置距离即为毛坯距离,如图2-16 所示。 不要混淆毛坯余量和毛坯距离的概念,他们都用于调整和定义毛坯,但毛坯余 量应用于毛坯几何体,而毛坯距离则应用于工件几何体。
UG数控车床编程实例

UG数控车床编程实例数控车床编程是近年来工业领域中不可缺少的技术之一,也是未来工业制造的重要方向。
作为数字化和智能化制造的重要手段,数控车床编程可以将设计图纸转换为机床上的实际操作,显著提高了生产效率,减少了人为失误,大大降低了产品质量问题的发生率。
UG软件是数控编程的重要软件之一,在此我们将为大家介绍一些UG数控车床编程实例。
实例一:圆形外轮廓加工文件名:example1.prt首先打开UG软件,新建一个零件文档,命名为example1.prt,并将拉伸模式设置为公差模式。
接下来,步进到CAD界面,画出所需的圆形加工轮廓。
圆形加工轮廓圆形加工轮廓根据图纸上的直径和材料厚度,我们可以设置加工直径、退刀量以及其他加工参数,最后以铣削方式进行加工即可。
% O145G17 G40 G49 G54 G80 G90G0 Z10T1 M6S800 M3G64 P0.01M8G0 X50 Y0Z5G1 Z0 F100G2 X0 Y0 R25G1 X-25 F200Y-25X0Y0G0 Z5M30实例二:内部和外部轮廓加工文件名:example2.prt新建一个零件文档,命名为example2.prt,并将拉伸模式设置为公差模式。
接下来,步进到CAD界面,画出所需的内部和外部轮廓加工轮廓。
内部和外部轮廓加工内部和外部轮廓加工根据图纸上的直径和材料厚度,我们可以设置加工直径、退刀量以及其他加工参数,最后以铣削方式进行加工即可。
% O245G17 G40 G49 G54 G80 G90G0 Z10T1 M6S800 M3G64 P0.01M8G0 X50 Y0Z5G1 Z0 F100G41 D1 X-12.5 Y-7.5G1 X-12.5 Y7.5X0 Y7.5X0 Y0G40 X-12.5 Y0Y-7.5X-12.5G0 Z5M30实例三:圆柱形零件加工文件名:example3.prt新建一个零件文档,命名为example3.prt,并将拉伸模式设置为公差模式。
UG加工中心编程实例
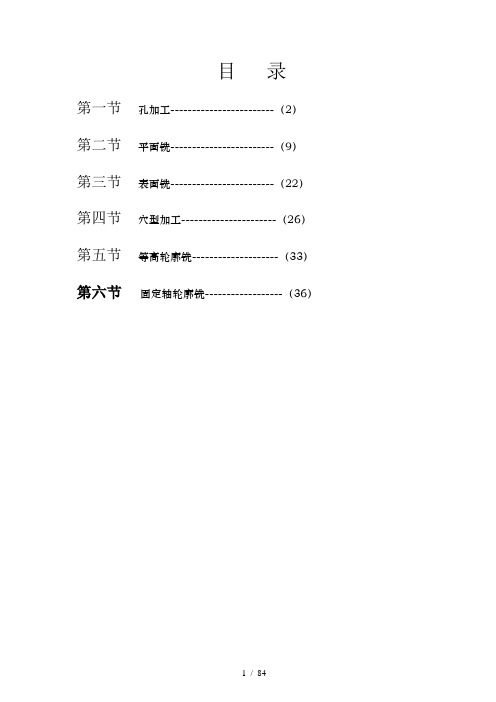
目录第一节孔加工------------------------(2)第二节平面铣------------------------(9)第三节表面铣------------------------(22)第四节穴型加工----------------------(26)第五节等高轮廓铣--------------------(33)第六节固定轴轮廓铣------------------(36)第一节孔加工1.1 例题1:编写孔位钻削的刀具路径图6-11.打开文件☐从主菜单中选择→***/Manufacturing/ptp-1.prt,见图6-12.进入加工模块☐从主菜单中选择Application→Manufacturing,进入Machining Environment对话框3.选择加工环境☐在CAM Session Configuration表中选择CAM General☐在CAM Setup表中选择Drill☐选择Initialize4.确定加工坐标系☐从图形窗口右边的资源条中选择Operation Navigator,并锚定在图形窗口右边☐选择Operation Navigator工具条的Geometry View图标,操作导航器切换到加工几何组视窗☐在Operation Navigator窗口中选择MCS_Mill,按鼠标右键并选择Edit,进入Mill_Orient对话框☐选择MCS_Origin图标,进入Points Constructor对话框,选择Reset,选择OK退回到Mill_Orient对话框☐打开Clearance开关,选择Specify,进入Plane Constructor对话框☐选择棕色显示的模型最高面,并设定Offset = 5☐连续选择OK直至退出Mill_Orient对话框5.创建刀具☐从Operation Navigator工具条中选择Machine Tool View图标,操作导航器切换到刀具组视窗☐从Manufacturing Create工具条中选择Create Tool图标,出现图6-2所示对话框☐按图6-2所示进行设置,选择OK进入Drilling Tool对话框☐设定Diameter = 3☐设定刀具长度补偿登记器号码:打开Adjust Register的开关,并设定号码为5☐设定刀具在机床刀库中的编号:打开Tool Number的开关,并设定号码为5☐选择OK退出图6-2 图6-36.创建操作☐从Manufacturing Create工具条中选择Create Operation图标,出现图6-3所示对话框☐按图6-3所示进行设置,选择OK进入SPOT_DRILLING对话框7.选择循环类型与其参数☐从循环类型列表中选择Standard Drill(三角形箭头),进入Specify Number of对话框☐设定Number of Sets = 1,选择OK进入Cycle Parameters对话框☐选择Depth进入Cycle Depth对话框,选择Tool Tip Depth,设定Depth = 3,选择OK退回到Cycle Parameters对话框☐选择Feedrate进入Cycle Feedrate对话框,设定进给率值= 60,选择OK直至退回到SPOT_DRILLING对话框8.指定钻孔位置☐从主菜单选择Format→Layer Settings,使5层为可选择层(Selectable)☐从Geometry区域选择Holes图标,并选择Select进入Point对话框☐选择Select进入选择点、孔、圆弧的对话框。
UG加工中心编程实例
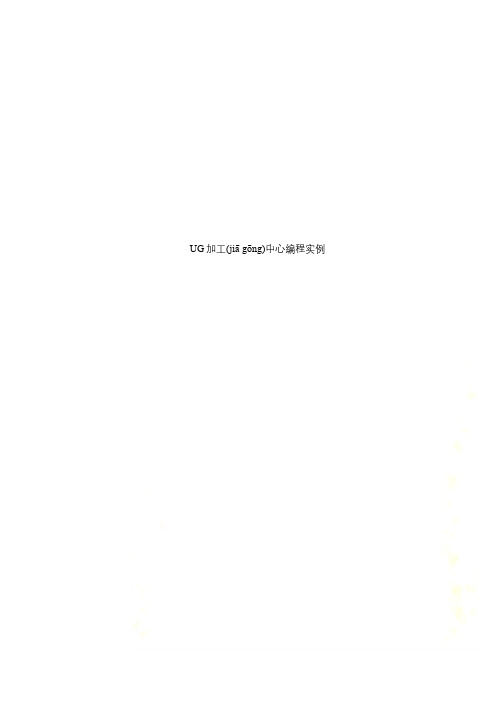
UG加工(jiā gōng)中心编程实例UG加工(jiā gōng)中心编程实例目录第一节孔加工(jiā gōng)------------------------(2)第二节平面(píngmiàn)铣------------------------(9)第三节表面(biǎomiàn)铣------------------------(22)第四节穴型加工(jiā gōng)----------------------(26)第五节等高轮廓(lúnkuò)铣--------------------(33)第六节固定轴轮廓铣------------------(36)第一节孔加工(jiā gōng)1.1 例题1:编写孔位钻削的刀具(dāojù)路径图6-11.打开(dǎ kāi)文件☐从主菜单中选择File→Open→***/Manufacturing/ptp-1.prt,见图6-12.进入(jìnrù)加工模块☐从主菜单中选择Application→Manufacturing,进入(jìnrù)Machining Environment对话框3.选择加工环境☐在CAM Session Configuration表中选择CAM General☐在CAM Setup表中选择Drill☐选择Initialize4.确定加工坐标系☐从图形窗口右边的资源条中选择Operation Navigator,并锚定在图形窗口右边☐选择Operation Navigator工具条的Geometry View图标,操作(cāozuò)导航器切换到加工几何组视窗☐在Operation Navigator窗口(chuāngkǒu)中选择MCS_Mill,按鼠标右键并选择Edit,进入Mill_Orient对话框☐选择(xuǎnzé)MCS_Origin图标,进入Points Constructor对话框,选择Reset,选择OK退回到Mill_Orient对话框☐打开(dǎ kāi)Clearance开关,选择Specify,进入Plane Constructor对话框☐选择棕色显示(xiǎnshì)的模型最高面,并设定Offset = 5☐连续选择OK直至退出Mill_Orient对话框5.创建刀具☐从Operation Navigator工具条中选择Machine Tool View图标,操作导航器切换到刀具组视窗☐从Manufacturing Create工具条中选择Create Tool图标,出现图6-2所示对话框☐按图6-2所示进行设置,选择OK进入Drilling Tool对话框☐设定Diameter = 3☐设定刀具长度补偿登记器号码:打开Adjust Register的开关,并设定号码为5☐设定刀具在机床刀库中的编号:打开Tool Number的开关(kāiguān),并设定号码为5☐选择(xuǎnzé)OK退出图6-2 图6-36.创建(chuàngjiàn)操作☐从Manufacturing Create工具条中选择(xuǎnz é)Create Operation图标,出现图6-3所示对话框☐按图6-3所示进行设置(shèzhì),选择OK进入SPOT_DRILLING对话框7.选择循环类型及其参数☐从循环类型列表中选择Standard Drill(三角形箭头),进入Specify Number of对话框☐设定(shè dìnɡ)Number of Sets = 1,选择OK进入Cycle Parameters对话框☐选择Depth进入(jìnrù)Cycle Depth对话框,选择Tool Tip Depth,设定Depth = 3,选择OK退回到Cycle Parameters对话框☐选择Feedrate进入Cycle Feedrate对话框,设定进给率值 = 60,选择OK直至(zhízhì)退回到SPOT_DRILLING对话框8.指定(zhǐdìng)钻孔位置☐从主菜单(cài dān)选择Format→LayerSettings,使5层为可选择层(Selectable)☐从Geometry区域选择Holes图标,并选择Select进入Point对话框☐选择Select进入选择点、孔、圆弧的对话框。
UG70数控加工经典案例

从数控加工基础讲起,循序渐进,通过详细的案例分析与操作步骤演示,帮助读者快速掌握2.5轴铳削加 工、平面铳削加工等实用数控设计技术,轻松跨入行业门槛。
主要内容:第1章UG NX7.0数控加工概述(27个视频)1.1 UG NX7.0编程的常规流程1加工界面介绍2创建加工坐标系3创建平面铳4产生刀路及G 代码1.2 设置加工环境1进入加工界面的方法2加工常用工具条介绍1.3 UG NX7.0模板的设置1模板放置位置讲解2模板设置参数的讲解1.4 操作导航器1操作导航器界面讲解2操作导航器中出程序的表示方法1.5 程序组的创建1程序组父子级的创建方法2程序组的复制粘贴1.6 创建几何体组1几何体组的创建方法2几何体参数的讲解1.7 创建加工刀具1创建加工刀具的种类介绍2参数铳刀参数设置1.8 创建加工方法组1加工方法组创建的讲解2刀具的参数和刀路颜色含义的讲解1.9 刀具路径管理1刀具路径模拟2刀具路径的管理1.10 边界管理1检查边界的应用2边界的修改方法1.11 加工参数的预设置DVD1: 学习目标:1加工参数的设置方法2加工首选项的讲解1.12加工中坐标系的应用1加工坐标系的创建2加工坐标系的参数讲解1.13后置处理的设置1后处理设置方法第2章2.5轴铳削加工(23个视频)2.1二维线框尺寸分析1创建加工刀具2加工坐标系的创建3二维线框刀具路径的创建4平面铳削的参数讲解2.2设置2.5轴铳削常用参数1创建加工策略2加工边界创建技巧3切削模式的设置4切削速率的设定2.3 2.5轴面铳加工1创建刀具和加工坐标系2切削边界的设定3面铳参数的设定2.4二维图形外廓加工1刀具和加工坐标系的创建2创建加工外廓边界3修剪边界和检查边界的设定2.5二维图形内廓加工1创建加工坐标系和加工边界2加工参数的讲解2.6法兰盘二维线框粗加工1创建加工刀具2铳削几何体的创建3定加工策略4切削参数的设置技巧2.7法兰盘二维线框精加工1创建刀具和加工坐标系2平面铳削的创建3平面铳削参数的讲解第3章平面铳削加工(18个视频)3.1平面铳加工概述1创建刀具和加工坐标系2创建加工边界3平面铳削参数的讲解3.2简单平面铳加工实例1创建刀具和加工坐标系2创建平面铳削加工策略3平面铳削参数的修改3.3平面铳常用参数的设置1平面铳深度参数的修改2平面铳切削参数的讲解3平面铳进退刀参数的设置4平面铳刀具轨迹的显示3.4平面铳边界的创建1创建边界的几种方法2边界应用方法3利用边界控制刀路的方法3.5面铳加工实例1创建刀具和加工坐标系2面铳参数设置3平面铳加工参数对比3.6平面铳加工实例1创建加工坐标系和加工边界2加工参数的设置DVD2:学习目标:通过大量制造业一线实际数控加工案例的剖析与讲解,帮助学习者轻松突破铳削加工、孔类加工、刻字加工等技术瓶颈,快速提高实际工作能力。
UG数控车床编程实例
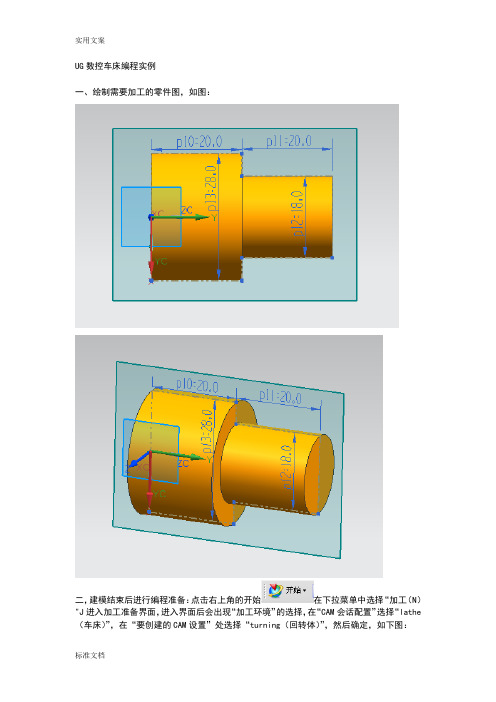
UG数控车床编程实例一、绘制需要加工的零件图,如图:二,建模结束后进行编程准备:点击右上角的开始在下拉菜单中选择“加工(N)"J进入加工准备界面,进入界面后会出现“加工环境”的选择,在“CAM会话配置”选择“lathe (车床)”,在“要创建的CAM设置”处选择“turning(回转体)”,然后确定,如下图:三、编程设置1、创建程序:点击顺序功能视图,在左上角点击对应的创建程序按钮进行创建程序,出现创建程序对话框,选择和图对应的选项,注意不要选错子对象与父对象,如这里的“PROGRAM_1”是“PROGRAM”的子对象,反之父对象,如图:在上面对话框后的对话框直接确定,不用选择直接确定。
2、创建刀具:点击“机床视图”,在左上角点击对应的创建刀具按钮进行创建刀具,在弹出的对话框中选择粗车刀具“OD_80_L”,具体如图:确定进入下一步。
出现下面对话框:将刀具号命名为一号刀,如需要加刀柄的话在“夹持器”处点选“使用车刀夹持器”3、创建几合体:点击几何视图,在左上角点击对应的创建几何体按钮进行创建几何体,出现创建几何体对话框,选择和图对应的选项:(在创建几何体之前要先将系统自生成的几何体删除,右击中的“MCS_SPINLE”选择删除)选择第一个坐标后点击确定进入坐标的创建(工件坐标)点击圈选处进行坐标创建通过选择Z轴,X轴,原点的方式创建坐标系,后面就直接确定了,没有需要设置的,创建后的坐标如图:4、双击进行指定需要加工的工件,点击后再点击显示框内的待加工零件整体,确定就完事了。
5、双击进行毛坯设置,点击设置毛坯,先点击选择进行坐标点的确定,选择待加工工件的底部中心为远点,如图:设置长度为42mm,直径30mm确定完成毛坯的设置。
6、创建避让(刀具的起点和终点):点击创建几何体,在出现的对话框中选择最后一个创建避让,在几何体处选择“TURNING-WORKPLECE”确定进入下一步。
将参数设置和下图一样,框选之外的不需要修改7、最后一步创建粗加工工序:点击左上角创建工序,选项要和下面图示的一样,不要选错,不然程序出错确定进入下一步按如图设置(可有可无):往下拉,现在不慌确定,拉到下面的操作,点击生成轨迹,继续后面的确定,进入下一步:选择3D动态和将速度调到最小,点击播放开始演示加工轨迹,这样编程前期完成了。
- 1、下载文档前请自行甄别文档内容的完整性,平台不提供额外的编辑、内容补充、找答案等附加服务。
- 2、"仅部分预览"的文档,不可在线预览部分如存在完整性等问题,可反馈申请退款(可完整预览的文档不适用该条件!)。
- 3、如文档侵犯您的权益,请联系客服反馈,我们会尽快为您处理(人工客服工作时间:9:00-18:30)。
题目要求:对图1.1所示的毛坯进行加工得到如图1.2所示的零件。
图1.1 毛坯图1.2 最终零件
总体实现方法:采用UG6.0软件进行加工。
首先通过平面铣削的方法对该零件的腔体部分以及带岛屿的腔体部分进行加工;然后使用三轴轮廓铣削方法对该工件的外形轮廓进行加工。
具体加工过程:
1.打开已建好的模型如图1.3所示,进入加工模块,创建mill_planar加工方式如图1.4所示,单击确定按钮完成加工方式创建。
图1.3 几何模型图1.4 铣削类型选项卡
2.单击创建刀具按钮如图 1.5所示,刀具子类型选择圆柱形平底立铣刀,刀具名称为D16r0.8,单击确定按钮对刀具参数进行设定,如图1.6所示,刀具直径选择16mm,底圆角半径选择0.8mm,其余参数保持不变。
图1.5刀具类型选项卡图1.6 刀具尺寸设置
3.单击创建操作,弹出菜单如图1.7所示,操作子类型选择粗加工,刀具选择D16r0.8,几何体选择MCS_MILL,单击确定按钮。
图1.7 加工子类型选项卡
4.选择几何体,设定安全平面高于工件最高平面30mm,工件选择几何体,毛坯选择自动模块。
5.完成对工件和毛坯边界的定义。
定义应该遵循以下原则:部件选择的侧是该部件要保留的部分,毛坯选择的侧是该毛坯要去除的部分。
对于铣腔体来说,部件的边界要选择外侧,毛坯的边界要选择内侧。
但对于有岛屿的腔体则略有不同,应该分别定义,选择边界时候应该把忽略岛屿前的钩取消,即不忽略岛屿,腔体定义方向与上面一致,而岛屿恰好与其定义相反。
底面选择腔体的底面即可。
还应该注意的问题是铣削时要有深度方向的变化,这就要求我们加工前要定义一个加工起始平面,在部件选项卡中,平面选择用户自定义的方式完成对个加工部分初始高度定义,如图1.8所示。
切削层深度选择固定深度4mm。
图1.8 边界条件设定视图
6.单击切削移动按钮,策略选项卡中,添加精加工刀路,精加工步距选择50。
余量选项卡中,部件选择0.3mm,内公差选择0.03mm,外公差选择0.1mm如图1.9和1.10所示。
图1.9 策略选项卡图1.10 余量选项卡
7.单击非切削移动按钮,进刀选项卡中,最小倾斜长度选择0,线性长度选择3,最小安全距离选择3,其余参数保持不变如图1.11所示。
图1.11 进刀选项卡
8.单击进给和速度按钮,每齿进给量选0.18mm,主轴转速500r/min,进给率250mm/min,其余参数保持不变如图1.12所示。
图1.12 进给和速度选项卡
9.单击生成刀轨按钮,得到如图1.13所示的刀具轨迹。
图1.13 粗加工刀具轨迹图
10.单击确认刀轨按钮,可得到如图1.14所示的粗加工仿真图片。
图1.14 加工仿真图
11.创建精加工方法,单击PLANAR_PROFILE按钮,进入精加工模块。
步骤大致与粗加工步骤一致,只是道具选择D8r0的刀如图所示,切削参数不用设定,进给和速度选项卡中每齿进给量0.2mm,主轴转速600r/min,切削进给率300mm/min。
其余参数保持默认,单击生成刀轨按钮可生成刀具轨迹如图1.15所示。
图1.15 精加工刀具轨迹图
12使用三轴轮廓铣削方法加工工件外轮廓,创建Mill_Contour操作,程序使用以创建的Mill_SURF,刀具选用MILL_16BULL,几何体使用WORKPIECE,方法选择MILL_XS,单击确定按钮进入操作对话框。
13.单击选择几何体中的指定部件按钮进行工件的几何体的确定,再选择格式,把图层62层设为可选状态显示毛坯,单击指定毛坯按钮,完成对毛坯几何体的选择如图1.17所示。
图1.16工件几何体图1.17 毛坯几何体
14.安全平面设为25mm,非切削移动进刀选项卡中封闭区域刀具类型选沿形状斜进刀,开放区域选择圆弧进刀。
切削参数策略选项卡中精加工刀路的加工步距为50,其余参数不变。
进给和速度选项卡中,主轴速度3000r/min,切削进给率500mm/min,快进10000 mm/min,逼近1000 mm/min,进刀300 mm/min,第一刀切深500 mm/min,单步执行500 mm/min,移刀500 mm/min,退刀8000 mm/min。
单击生成刀路可得到如图1.18所示。
单击确认刀轨按钮可得到仿真图1.19,完成对整个工件的加工过程。
图1.18 刀具轨迹图
图1.19 刀具仿真图
15.进行后处理工作,选择工具→操作导航器→输出→UX_post→MILL_3_AXIS_TURBO→确定可得到数控代码如图1.20所示。
图1.20 数控代码程序。