碳纤维复合材料缺陷检测方法研究
碳纤维复合材料蜂窝夹芯特殊结构无损检测研究

碳纤维复合材料蜂窝夹芯特殊结构无损检测研究1.研究内容本文以碳纤维复合材料蜂窝夹芯结构试验件的过渡区为主要被检测对象,该试验件为碳纤维复合材料NOMEX蜂窝夹芯结构,预制缺陷设计较为特殊,采用发泡胶模拟预制缺陷,位于蜂窝过渡区与平板区的三角区域,缺陷宽度仅有2mm,对无损检测的实施提出了较高要求,试验件示意图如图1所示。
为掌握试验件在规定疲劳试验周期内损伤扩展特性,试验过程检测与飞机在役检测更为相似,对其检测方案及可行性的研究显得尤为重要。
1.检测方法无损检测技术是指在不损坏材料或产品原有的形状、性能的基础上,利用光、声、电、磁、热和射线等技术检测其是否有损伤,以确保其可靠性的检测技术。
利用不同的无损检测技术,对材料表面和内部进行检测,并对缺陷的类型、大小、深度、范围、数量等做出准确判断,由此可以判断材料或构件是否可以进行下一步的生产制造或者维修服役情况。
目前碳纤维复合材料蜂窝夹芯结构常用的无损检测方法通常有以下几种方法。
1.1.敲击检测法敲击检测法是使用时间最早应用范围最广的一种无损检测方法。
主要是通过对物体进行适当的敲击来获取试件的振动信息通过振动频率是否改变来判断试件内部是否含有损伤,敲击检测法主要并且广泛应用于蜂窝夹芯结构、多层结构和网状结构对胶粘剂质量的检测。
它适用于结构内部的脱胶、夹杂、分层等缺陷,但对小尺寸缺陷的检测不敏感。
传统的敲击检测是利用适当的敲击工具(小锤、硬币等)对被测材料进行敲击,并通过被测材料振动产生的声咅来判断材料的内部损伤。
现代数字敲击检测是利用传感器对振动信息进行采集,然后对采集的振动信息进行分析从而得到准确的检测结果。
1.1.超声波检测超声波检测法是目前复合材料无损检测的主要方法之一。
超声波无损检测技术主要根据复合材料自身和其缺陷对超声波传播的阻碍来判断材料表面及内部的缺陷,能检测复合材料中的内部缺陷如疏松、分层、夹杂、裂纹等,还能对材料厚度和性能进行评估。
超声波具有很强的穿透能力,可对较厚的材料进行探测,灵敏度高,操作简单,对缺陷的深度、大小,范围进行精准检测。
碳纤维复合材料蜂窝夹层结构的无损检测方法研究

( a i F PIstt,H ri 10 3 , h a H r n R tu b n i e a n 50 6 C i ) b n
AB TF ̄ T ein rd fcsi ab nf e o oi o e c mbsn wihp rsw r nrd cdi i a e .T e e S L CT h n e ee t nc ro b r mp st h n y o a d c at eeit u e nt sp p r h s i c e o h
复 合 材 料 蜂 窝 夹 层 结 构 进 行 无 损 检 测 是 十 分 重 要
的。
2 碳 纤 维 复合 材 料蜂 窝 夹层 结 构
易 出现 的缺 陷
碳纤 维复合 材料蜂 窝夹层结 构在胶 接制造过程
构。
碳纤 维复合 材料蜂 窝夹层结 构是一 种特殊 的复
中往往会 由于工 艺原 因产 生各种 缺陷 , 见表 1 详 。
形进行分析 , 并判断波形 产生 的原因 , 认为超声 脉冲反射法对碳纤 维复合材料蜂 窝夹层结构 内部 缺陷检测是一种
行之有效的方法 。 关键词 碳 纤维 复合材料 ; 复合材料蜂 窝夹层结构 ; 超声脉冲反射法 ; 陷; 缺 底波
S u y o nd s r tv si g f r Ca bo be t d n No e t uc i e Te tn o r n Fi r Co po ie Ho e c m b S n wi h Pa t m st n y o a d c r s
3 碳 纤 维 复合 材 料 蜂 窝夹 层 结构 的
dee t l ie ty af c c a ia o e te n r i g pef r a e, S h o d sr cie tsi g m u tbe c rid fcs wi d rc l fe tme h n c lprp ris a d wo k n rom nc l O t e n n e tu tv etn s a re
无损检测技术在碳纤维复合材料检测中的应用研究
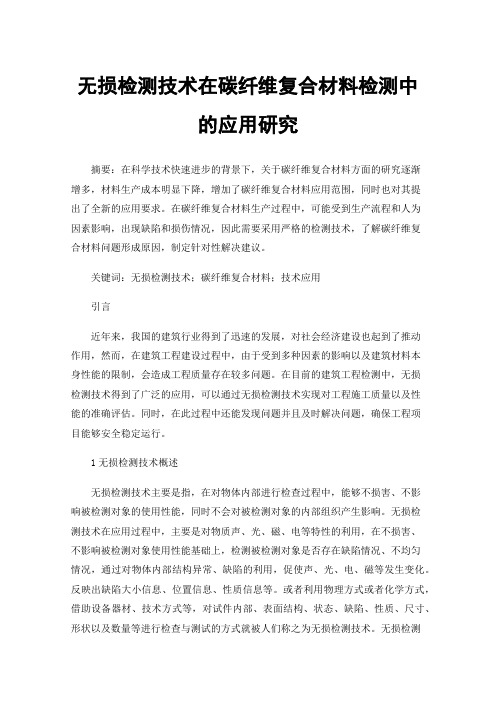
无损检测技术在碳纤维复合材料检测中的应用研究摘要:在科学技术快速进步的背景下,关于碳纤维复合材料方面的研究逐渐增多,材料生产成本明显下降,增加了碳纤维复合材料应用范围,同时也对其提出了全新的应用要求。
在碳纤维复合材料生产过程中,可能受到生产流程和人为因素影响,出现缺陷和损伤情况,因此需要采用严格的检测技术,了解碳纤维复合材料问题形成原因,制定针对性解决建议。
关键词:无损检测技术;碳纤维复合材料;技术应用引言近年来,我国的建筑行业得到了迅速的发展,对社会经济建设也起到了推动作用,然而,在建筑工程建设过程中,由于受到多种因素的影响以及建筑材料本身性能的限制,会造成工程质量存在较多问题。
在目前的建筑工程检测中,无损检测技术得到了广泛的应用,可以通过无损检测技术实现对工程施工质量以及性能的准确评估。
同时,在此过程中还能发现问题并且及时解决问题,确保工程项目能够安全稳定运行。
1无损检测技术概述无损检测技术主要是指,在对物体内部进行检查过程中,能够不损害、不影响被检测对象的使用性能,同时不会对被检测对象的内部组织产生影响。
无损检测技术在应用过程中,主要是对物质声、光、磁、电等特性的利用,在不损害、不影响被检测对象使用性能基础上,检测被检测对象是否存在缺陷情况、不均匀情况,通过对物体内部结构异常、缺陷的利用,促使声、光、电、磁等发生变化。
反映出缺陷大小信息、位置信息、性质信息等。
或者利用物理方式或者化学方式,借助设备器材、技术方式等,对试件内部、表面结构、状态、缺陷、性质、尺寸、形状以及数量等进行检查与测试的方式就被人们称之为无损检测技术。
无损检测具有非破坏性、全面性、全程性优势。
比如,非破坏性优势主要体现为,在检测过程中不会对被检测对象的使用性能产生影响;全面性优势主要体现为,在必要情况下能够实现对对象的100%检测,这也是破坏性检测无法实现的,破坏性检测通常会将其应用在原材料检测中。
因为无损检测技术不会对被检测对象使用性能造成影响,因此,不仅可以将其应用在原材料检测,还可以将其应用在中间工艺环节检测等全过程中。
碳纤维复合材料缺陷的超声检测及材料力学性能仿真研究

生高频脉冲激励信号ꎬ将信号传输到超声换能器ꎬ再由换
博看网 . All Rights
Reserved.
能器的压电效应将脉冲激励信号转换成脉冲超声波ꎮ Nhomakorabea当
声波在换能器与工件之间的耦合介质内传输时ꎬ一部分声
波被工件表面反射ꎬ反射后由换能器接收ꎬ并转换成激励
信号传输到超声脉冲激励 / 接收单元ꎬ通过单元进行信号
合介质的界面发生强烈折射ꎬ并在界面处发生轴向聚焦ꎮ
透镜和样品之间的耦合介质主要用于传播超声波ꎮ 换能
器安装在 x、y、z 三轴移动平台上ꎬ可在三维空间范围内运
4K
图 3 复合材料内部缺陷建模
模型中界面层通过插入 Cohesive 内聚力单元来连接
两材料ꎬ并模拟裂纹产生和损伤演化ꎮ 基于胶合力学理论
ZHANG Quanli 1 ꎬ ZENG Jiaheng1 ꎬ YANG Zhen1 ꎬ GUO Nan1 ꎬ CHEN Zhengsheng2 ꎬ SU Honghua1
(1. College of Mechanical and Electronic Engineeringꎬ Nanjing University of Aeromautics and Astronauticsꎬ
时ꎬ其材料的抗拉强度下降 13. 2%ꎮ 王雪明等
[15]
对碳纤
维复合材料整体成型过程中温度对材料缺陷的影响进行
动ꎮ 为了防止检测过程中近表面产生扫描盲区问题ꎬ内部
平台采用有机玻璃ꎮ 探头与平台之间采用去离子水作为
检测耦合剂ꎬ探头下沉至水中ꎬ距离工件表面约1 cmꎮ采用
徕卡 DMC 4500 光学显微镜、科视达 KH- 7700 三维视屏
增强树脂基复合材料层压板进行分层缺陷检测ꎬ获得了复
碳纤维复合材料制孔结构超声无损检测及评价
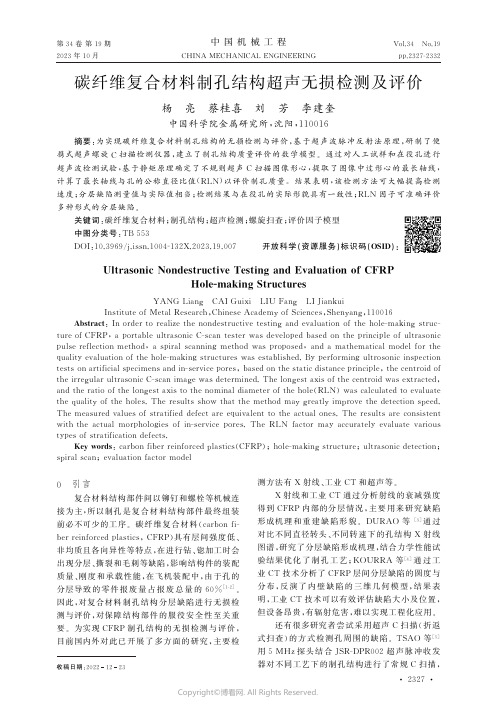
第34卷第19期中国机械工程V o l .34㊀N o .192023年10月C H I N A M E C HA N I C A LE N G I N E E R I N Gp p.2327G2332碳纤维复合材料制孔结构超声无损检测及评价杨㊀亮㊀蔡桂喜㊀刘㊀芳㊀李建奎中国科学院金属研究所,沈阳,110016摘要:为实现碳纤维复合材料制孔结构的无损检测与评价,基于超声波脉冲反射法原理,研制了便携式超声螺旋C 扫描检测仪器,建立了制孔结构质量评价的数学模型.通过对人工试样和在役孔进行超声波检测试验,基于静矩原理确定了不规则超声C 扫描图像形心,提取了图像中过形心的最长轴线,计算了最长轴线与孔的公称直径比值(R L N )以评价制孔质量.结果表明,该检测方法可大幅提高检测速度;分层缺陷测量值与实际值相当;检测结果与在役孔的实际形貌具有一致性;R L N 因子可准确评价多种形式的分层缺陷.关键词:碳纤维复合材料;制孔结构;超声检测;螺旋扫查;评价因子模型中图分类号:T B553D O I :10.3969/j .i s s n .1004 132X.2023.19.007开放科学(资源服务)标识码(O S I D ):U l t r a s o n i cN o n d e s t r u c t i v eT e s t i n g an dE v a l u a t i o no fC F R P H o l e Gm a k i n g St r u c t u r e s Y A N GL i a n g ㊀C A IG u i x i ㊀L I U F a n g㊀L I J i a n k u i I n s t i t u t e o fM e t a lR e s e a r c h ,C h i n e s eA c a d e m y o f S c i e n c e s ,S h e n y a n g,110016A b s t r a c t :I no r d e r t or e a l i z e t h en o n d e s t r u c t i v e t e s t i n g a n de v a l u a t i o no f t h eh o l e Gm a k i n g st r u c Gt u r e o fC F R P ,a p o r t a b l eu l t r a s o n i cC Gs c a nt e s t e rw a sd e v e l o p e db a s e do nt h e p r i n c i pl eo fu l t r a s o n i c p u l s e r e f l e c t i o nm e t h o d ,as p i r a l s c a n n i n g m e t h o dw a s p r o po s e d ,a n da m a t h e m a t i c a lm o d e l f o r t h e q u a l i t y e v a l u a t i o no f t h eh o l e Gm a k i n g s t r u c t u r e sw a s e s t a b l i s h e d .B yp e r f o r m i n g u l t r o s o n i c i n s pe c t i o n t e s t so n a r t if i c i a l s p e c i m e n s a n d i n Gs e r v i c e p o r e s ,b a s e d o n t h e s t a t i c d i s t a n c e p r i n c i pl e ,t h e c e n t r o i d o f t h e i r r e g u l a r u l t r a s o n i cC Gs c a n i m a g ew a s d e t e r m i n e d .T h e l o n ge s t a x i s of t h e c e n t r o i dw a s e x t r a c t e d ,a n d t h e r a t i oo f t h e l o n ge s t a x i s t o t h en o m i n a l d i a m e t e r of t h e h o l e (R L N )w a s c a l c u l a t e d t o e v a l u a t e t h e q u a l i t y o f t h eh o l e s .T h e r e s u l t s s h o wt h a t t h em e t h o dm a yg r e a t l y i m p r o v e th ed e t e c ti o ns pe e d .T h em e a s u r e dv a l u e s of s t r a t i f i e dd e f e c t a r ee q u i v a l e n t t o t h ea c t u a l o n e s .T h e r e s u l t sa r ec o n s i s t e n t w i t h t h ea c t u a lm o r p h o l og i e so f i n Gs e r v i c e p o r e s .Th e R L Nf a c t o r m a y a c c u r a t e l y e v a l u a t ev a ri o u s t y pe s of s t r a t i f i c a t i o nd e f e c t s .K e y w o r d s :c a r b o n f i b e r r e i n f o r c e d p l a s t i c s (C F R P );h o l e Gm a k i ng s t r u c t u r e ;u l t r a s o n i c d e t e c t i o n ;s pi r a l s c a n ;e v a l u a t i o n f a c t o rm o d e l 收稿日期:202212230㊀引言复合材料结构部件间以铆钉和螺栓等机械连接为主,所以制孔是复合材料结构部件最终组装前必不可少的工序.碳纤维复合材料(c a r b o n f i Gb e r r e i n f o rc ed p l a s t i c s ,C F R P )具有层间强度低㊁非均质且各向异性等特点,在进行钻㊁锪加工时会出现分层㊁撕裂和毛刺等缺陷,影响结构件的装配质量㊁刚度和承载性能,在飞机装配中,由于孔的分层导致的零件报废量占报废总量的60%[1G2].因此,对复合材料制孔结构分层缺陷进行无损检测与评价,对保障结构部件的服役安全性至关重要.为实现C F R P 制孔结构的无损检测与评价,目前国内外对此已开展了多方面的研究,主要检测方法有X 射线㊁工业C T 和超声等.X 射线和工业C T 通过分析射线的衰减强度得到C F R P 内部的分层情况,主要用来研究缺陷形成机理和重建缺陷形貌.D U R A O 等[3]通过对比不同直径转头㊁不同转速下的孔结构X 射线图谱,研究了分层缺陷形成机理,结合力学性能试验结果优化了制孔工艺;K O U R R A 等[4]通过工业C T 技术分析了C F R P 层间分层缺陷的圆度与分布,反演了内壁缺陷的三维几何模型,结果表明,工业C T 技术可以有效评估缺陷大小及位置,但设备昂贵,有辐射危害,难以实现工程化应用.还有很多研究者尝试采用超声C 扫描(折返式扫查)的方式检测孔周围的缺陷.T S A O 等[5]用5MH z 探头结合J S R GD P R 002超声脉冲收发器对不同工艺下的制孔结构进行了常规C 扫描,7232 Copyright ©博看网. All Rights Reserved.建立了分层面积与工艺参数的对应关系.魏莹莹等[6]采用75MH z 高频超声对铺层厚度为0.2mm 的制孔结构进行了检测,认为分层缺陷的形成通常是一种发生在多层材料上的三维结构缺陷,并提出了一种三维体积分层因子的分层评价方法,但工程中C F R P 结构部件的制孔结构数量大且分布范围广,该方法难以满足在役检测的需求.综上分析,当前迫切需要一种可靠且高效的无损检测手段实现对C F R P 在役孔的检测与评价.本研究即针对C F R P 孔的结构特点,采用螺旋式扫查取代传统折返式扫查,建立了不规则缺陷的最长轴线与孔的公称孔径比值(r a t i oo f t h el o n g e s t a x i s t o t h e n o m i n a l a pe r t u r e of t h e h o l e ,R L N )评价因子模型,然后将算法集成于所研制的便携式仪器软件中,以实现对多种形式分层缺陷的检测与评价.1㊀检测原理与仪器组成常规超声波C 扫描检测扫查方式为折返式,如图1所示,分为扫查轴和步进轴[7].在扫查过程中需要对步进轴电机进行频繁的启停控制,既造成机械冲击又严重影响检测速度.图1㊀折返扫查与螺旋扫查对比F i g .1㊀C o m pa r i s o nb e t w e e n r e t r ac t a b l e s c a na nd s pi r a l s c a n 本文提出的快速螺旋扫查技术在相同扫查分辨力的前提下无需频繁启停步进轴电机,既可以减小机械冲击,又可大幅提高检测速度.以步进轴的步进精度为0.5mm 为例,若步进长度为100mm ,则每次检测就可以节省200s 时间,当步进精度更小㊁步进长度更大时,将节省更多时间.如图2所示,检测时,首先将内置5MH z 点聚焦探头的水套置于待检区域,探头焦点聚焦于工件表面,该探头既作为发射探头又作为接收探头.探头发射的超声波经过水和透声介质后在被检工件中沿直线传播.开启按键后,旋转检测机构连动探头进行螺旋扫查,C P U 实时处理超声波检测数据.当探头位于孔周围时,若孔周围无缺陷,则超声波传播至底面处发生反射,形成反射回波(底波),直至被探头接收,如图2中①所示;若孔周围存在点状小缺陷,则超声波传播至缺陷处会发生反射和折射,反射的超声波被探头接收,形成缺陷回波,折射的超声波继续向前传播,直至遇到被检工件的底面,形成底波,如图2中②所示;当探头位于孔上方时,超声波传播至透声介质底部处发生反射,形成界面波被探头接收,如图2中③所示.若孔周围存在大分层缺陷,则超声波传播至缺陷处会发生反射,传播路径被阻隔,不会形成底波,如图2中④所示[8].图2㊀超声检测原理图F i g .2㊀S c h e m a t i c d i a g r a mo f u l t r a s o n i c t e s t i n g如图3a 所示,超声波螺旋C 扫描检测仪器包括便携式主机和旋转检测机构两部分.便携检测主机由数据采集卡㊁脉冲收发器㊁控制器及驱动器组成,数据采集卡负责采集超声波信号,脉冲收发器负责触发探头并对超声波回波信号进行放大以易于数据采集,控制器及驱动器控制步进电机完成规定圈数扫查并调理编码器触发信号.如图3b 所示,高精度旋转检测装置主要由步进电机㊁传动减速机构㊁编码器㊁启动按键㊁水密封及耦合㊁探头组成.软件控制电机运行参数,经过机械传动模块驱动检测探头在既定平面内沿渐进螺旋线运动.检测探头激励出的超声波经水耦合传播到被检工件内,获取检测区域质量信息,通过接口传送到上位机进行分析与成像.编码器和精密径向步进扫查机构相匹配,探头扫查精度可达到0.065mm .最大扫查范围可达ϕ28mm ,足以覆盖常规C F R P 孔及其周边可疑区域.2㊀评价方法通过超声检测方式获取分层缺陷C 扫描成像是定量评价的原始依据,至今没有统一的标准.8232 中国机械工程第34卷第19期2023年10月上半月Copyright ©博看网. All Rights Reserved.(a)设计基本组成(b)设备设计图及工作原理图3㊀设备基本构成和工作原理F i g.3㊀B a s i c c o m p o s i t i o na n dw o r k i n gp r i n c i p l eo f e q u i p m e n t国内外学者提出了不同的评价因子,以对分层缺陷进行科学合理的评价[9].当前主要以一维直径分层因子和二维面积评价因子为主.C H E N[10]提出采用最大分层直径与孔的公称直径的比值作为分层缺陷的评价因子F d,即F d=D m a x D0(1)式中,D m a x为最大分层直径;D0为孔的公称直径.F d评价因子测量简单,是目前较常用的评价制孔结构分层程度的方法.但当最大分层直径相近,分层面积差异较大时,该方法并不适用.如图4所示,图4a㊁图4b中的最大分层直径(D m a x1㊁D m a x2)相等,F d相同,图4a在单方向发生严重的分层剥离,但图4a的分层面积比图4b的分层面积小很多,分层程度明显小于图4b的分层程度.㊀㊀(a)单方向分层损伤㊀㊀(b)多方向均匀损伤图4㊀F d相等时不适宜情况F i g.4㊀I n a p p r o p r i a t e s i t u a t i o nw h e n F d i s e q u a lF A R A Z等[11]在考虑分层面积的影响后,提出以真实分层面积与孔的公称面积的比值作为分层评价的标准F a,其表达式为F a=A d An o m(2)式中,A d为实际分层面积;A n o m为孔的公称面积.F a与F d相比可更好地评估分层的程度,但同样存在不足.因为该方法没有考虑分层向某一方向拓展严重的情况.如图5a和图5b所示,分层面积A d1与A d2相等,评估因子F a相等,但图5a分层缺陷在各个方向的拓展程度相近,而图5b 中分层缺陷沿左下方拓展严重,故图5b中孔周围实际分层更为严重.㊀(a)多方向均匀分布㊀㊀㊀(b)分层扩展不均匀图5㊀F a相等时不适宜情况F i g.5㊀I n a p p r o p r i a t e s i t u a t i o nw h e n F a i s e q u a l在二维面积评价因子模型基础上,考虑不规则分层缺陷向某方向拓展较大的情况,基于静矩原理,建立R L N评价因子数学模型,用以评价C F R P孔分层程度.具体实现过程为:通过二重积分算法确定缺陷与孔构成的不规则面积形心,计算不规则面积内通过该形心的最长轴线,最后得出最长轴线与孔的公称直径比值(R L N).形心确定方法如图6所示.图6㊀不规则面积形心提取模型F i g.6㊀I r r e g u l a r a r e a c e n t r o i d e x t r a c t i o nm o d e l假设图5b中不规则区域是一平面薄片,处于O x y平面中的面积为σ,质量为M,质量密度为ρ(x,y),则质量M为M=∬Dρ(x,y)dσ(3)其质心坐标(x-,y-)为x-=1M∬D xρ(x,y)dσ(4)y-=1M∬D yρ(x,y)dσ(5) 9232碳纤维复合材料制孔结构超声无损检测及评价 杨㊀亮㊀蔡桂喜㊀刘㊀芳等Copyright©博看网. All Rights Reserved.当ρ(x ,y )为常数时,即不规则区域为均匀分布时,M =ρσ,质心坐标(x -,y -)即为不规则平面区域D 的形心坐标,则推导出不规则二维图像形心坐标如下:x -=1σ∬Dx dσ(6)y -=1σ∬Dy dσ(7)不规则区域中任意通过该形心的直线将该图像分割成面积相等的两部分.从图6中可以看出形心位置明显与孔圆心位置不一致,这是由于分层缺陷向各方向拓展程度不同造成的,当分层缺陷向各方向拓展程度相同时,形心与孔圆心位置应重合.故可通过最长轴线与孔的公称孔径比值大小表征分层缺陷向某方向拓展程度,其表达式为F R L N=D l o n gD 0(8)式中,D l o n g 为不规则面积最长轴线.仪器的上位机软件计算流程如图7所示.图7㊀软件计算流程图F i g.7㊀S o f t w a r e c a l c u l a t i o n f l o wc h a r t 将图4和图5中单方向分层损伤㊁多方向均匀损伤和分层扩展不均匀三种情况按图7中流程计算以R L N 进行评价,结果如图8所示.由图8可以看出,三种制孔结构中实际分层严重程度从大到小为图8c ㊁图8b ㊁图8a .F d 因子评价结果为F d (c )>F d (b )=F d (a )(F d (c)表示图8c 所示的分层扩展不均匀情况下的F d 因子评价结果,其余符号类此表达);F a 因子评价结果为F a (c)=F a (b )>F a (a );若按R L N 因子进行评价,D l o n g3>D l o n g 2>D l o n g 1,结果为F R L N (c )>F R L N (b )>F R L N (a ),与实际情况一致.故通过R L N 因子评价分层程度时,既能够涵盖单方向分层损伤和多方向均匀损伤的情况,又可避免由于分层扩展不均匀性导致评价结果不合理的问题,具有工程意义.(a )单方向分层损伤㊀(b )多方向均匀损伤㊀(c)分层扩展不均匀图8㊀不同损伤情况下各评价因子对比F i g .8㊀C o m pa r i s o no f e v a l u a t i o n f a c t o r s u n d e r d i f f e r e n t d a m a ge s i t u a t i o n s 3㊀实验结果与分析人工试样为层压板结构,板厚为7.8mm ,孔的公称直径为5.2mm .试样共有4个孔,含有1个完好孔,以及3个缺陷孔,缺陷为ϕ1.5mm 平底孔,长度为4mm .分别位于试样厚度方向等间隔三处,模拟上中下三个部位的宽度为1.5mm ㊁长度为4mm 的分层缺陷,如图9所示.图9㊀人工试块F i g.9㊀M a n u a l t e s t b l o c k 使用研制的便携式仪器对人工试样中的孔进行检测,扫查的圆形区域直径为18mm ,成像闸门设置在底波区域,检测结果如图10所示.从图10和图11中C 扫描和D 扫描成像结果可以看出,不同深度位置的分层缺陷均可检出.孔周围无缺陷时,C 扫描成像结果中,红色区域为扫查区域成像,蓝色区域为孔成像;D 扫描成像结果中,深度方向无缺陷波形.当存在分层缺陷时,C 扫描成像结果中,超声波经过缺陷折射后继续向下传播,形成较弱的底波,故当闸门位于底波位置时,孔周围缺陷的C 扫描成像的色阶介于蓝色和红色之间.上中下三部位的缺陷成像位置不同是因为每次放置的旋转检测机构相对位置不同,不影响检测与评价.D 扫描成像结果中,显示了三个不同深度下的分层缺陷.上中下分层缺陷中R L N 评价因子及分层宽度误差如表1所示.0332 中国机械工程第34卷第19期2023年10月上半月Copyright ©博看网. All Rights Reserved.㊀㊀(a )完好孔㊀㊀㊀㊀㊀㊀(b)存在上层缺陷孔㊀(c )存在中层缺陷孔㊀㊀㊀(d)存在下层缺陷孔图10㊀人工试块中制孔结构C 扫描成像F i g .10㊀C Gs c a n i m a g i n g o f t h e h o l em a k i n g st r u c t u r e i n t h e a r t i f i c i a l t e s t b l o ck㊀㊀(a )完好孔㊀㊀㊀㊀㊀㊀(b)存在上层缺陷孔㊀(c )存在中层缺陷孔㊀㊀㊀㊀(d)存在下层缺陷孔图11㊀人工试块中制孔结构检测D 扫描成像F i g .11㊀D s c a n i m a g i n g o f t h e h o l em a k i n gs t r u c t u r e i n t h e a r t i f i c i a l t e s t b l o c k由表1可以看出,与分层缺陷尺寸相比,所检出分层宽度误差最大为0.13mm ,分层长度误差最大为0.19mm ,R L N 值相近.当前扫查范围下,当孔位于扫查中心时,可测量的最大分层长度为6.4mm ,能够覆盖分层缺陷长度.为进一步验证检测及评价方法,对与人工试块制造工艺相同的C F R P 构件中两个在役孔(1号和2号)进行了检测,公称孔径同为5.2m m ,检测结果如图12所示.针对1号和2号在役制孔结构进行C 扫描成像分析,可看出1号制孔明显出现大面积分层表1㊀上中下分层缺陷检测结果T a b .1㊀U p p e r ,m i d d l e a n d l o w e r l a ye r d ef e c t d e t e c t i o n r e s u l t制孔结构分层宽度(mm )分层长度(mm )最长轴线(mm )分层宽度误差(mm )分层长度误差(mm )R L N 值F R L N 上层缺陷1.624.1511.230.120.152.16中层缺陷1.634.1911.440.130.192.20下层缺陷1.603.9211.020.100.082.12㊀㊀(a )1号孔㊀㊀㊀㊀㊀㊀㊀㊀(b )2号孔图12㊀在役构件中制孔结构检测结果F i g .12㊀T e s t i n g r e s u l t s o f d r i l l i n gs t r u c t u r e i n i n Gs e r v i c e c o m po n e n t s 缺陷,其长轴为11.90mm ,R L N 值为2.29;2号制孔出现单方向分层剥离缺陷,其长轴为6.05m m ,R L N 值为1.16.1号和2号在役制孔结构F d ㊁F a 和R L N 评价因子计算结果如表2所示.表2㊀三种评价因子计算结果T a b .2㊀C a l c u l a t i o n r e s u l t s o f t h r e e e v a l u a t i o n f a c t o r s在役制孔F dF aF R L N1号1.722.112.292号1.120.031.16㊀㊀从表2中可以看出,当1号在役孔周围明显出现大面积分层㊁缺陷较严重时,F d 值偏小;当2号在役孔周围单方向分层剥离缺陷较严重时,F a 值偏小,不符合实际严重程度.而R L N 因子评价分层程度时,能够涵盖单方向分层损伤和多方向均匀损伤时的极限情况.1号孔和2号孔服役中的实际形貌如图13所示,可看出1号孔作为结构件的连接孔,其表面已经出现明显的大面积分层;2号孔近表面也出现了单方向微弱劈裂分层,两孔实际形貌与检测结果有较好的一致性,更进一步说明该检测仪器与评价方法对C F R P 制孔结构的良好适用性,故可以通过比较R L N 值的大小评价分层缺陷的严重程度,该方法适用性强,可靠性高.若在评价因子值与孔性能之间建立评价关系,需要根据标准G B /T30968.3 2014«聚合物基复合材料层合板开孔/受载孔性能试验方法第3部分:开孔拉伸强度试验方法»做大量的有损试验,将获取的有损试验数据(不同分层缺陷大小对孔性能的影响)与无1332 碳纤维复合材料制孔结构超声无损检测及评价杨㊀亮㊀蔡桂喜㊀刘㊀芳等Copyright ©博看网. All Rights Reserved.损检测数据(如R L N 值)进行相关性研究和分析,这也是下一步的研究方向.㊀㊀㊀(a )1号孔㊀㊀㊀㊀㊀㊀㊀(b )2号孔图13㊀在役构件中制孔结构实际形貌F i g .13㊀A c t u a lm o r p h o l o g y o f h o l em a k i n g st r u c t u r e i n a c t i v e c o m po n e n t s 4㊀结论(1)本文提出了超声螺旋C 扫描检测方法,与折返式扫查相比,本文方法在相同扫查分辨力的前提下,既可以避免由于频繁电机启停带来机械冲击,又可以大幅提高检测速度.(2)研制的便携式超声波检测仪器能更加直观和准确地反映分层缺陷的大小㊁位置以及分布状况,以进行缺陷的定量和定位,可满足在役检测需求.(3)基于静矩原理,通过二重积分算法提取不规则缺陷形心,建立了不规则缺陷最长轴线与孔的公称孔径比值(R L N )评价孔质量的数学模型,可对多种类型分层缺陷进行有效评价.参考文献:[1]㊀付鹏强,蒋银红,王义文,等.C F R P 制孔加工技术的研究进展与发展趋势[J ].航空材料学报,2019,39(6):32G45.F UP e n g q i a n g ,J I A N GY i n h o n g ,WA N GY i w e n ,e t a l .R e s e a r c h P r o g r e s sa n d D e v e l o p m e n t T r e n d o f C F R P H o l e M a k i n g P r o c e s s i n g T e c h n o l o g y [J ].J o u r n a l o fA e r o n a u t i c a lM a t e r i a l s ,2019,39(6):32G45[2]㊀S V I N T H C N ,WA L L A C E S ,S T E P H E N S O N DB ,e t a l .C o r r e c t i o n t o :I d e n t i f y i n g Ab n o r m a lC F R P H o l e s U s i n g B o t h U n s u p e r v i s e d a n d S u pe r v i s e d L e a r n i n g T e c h n i q u e s o n I n Gpr o c e s sF o r c e ,C u r r e n t ,a n dV i b r a t i o nS i g n a l s [J ].I n t e r n a t i o n a lJ o u r n a lo f P r e c i s i o n E n g i n e e r i n g a n d M a n u f a c t u r i n g,2022,23:609G625.[3]㊀D U R A O L M P ,T A V A R E SJ M R S ,A L B U GQ U E R Q U E lV H CD ,e t a l .D a m a geE v a l u a t i o no f D r i l l e dC a r b o n /E p o x y La m i n a t e s B a s e d o nA r e aA s Gs e s s m e n tM e t h o d s [J ].C o m p o s i t eS t r u c t u r e s ,2013,96(4):576G583.[4]㊀K O U R R A N ,WA R N E T TJM ,A T T R I D G EA ,e ta l .M e t r o l o g i c a lS t u d y o fC F R P D r i l l e d H o l e sw i t h X Gr a y C o m p u t e d T o m o g r a p h y [J ].I n t e r n a t i o n a l J o u r n a lo f A d v a n c e d M a n u f a c t u r i n g T e c h n o l o g y ,2015,78(9/12):2025G2035.[5]㊀T S A O C C ,HO C H E N G H.C o m pu t e r i z e dT o m o Gg r a p h y a n d C Gs c a nf o r M e a s u r i n g D e l a m i n a t i o ni n t h eD r i l l i n g o fC o m p o s i t e M a t e r i a l s U s i n g V a r i o u s D r i l l s [J ].I n t e r n a t i o n a lJ o u r n a lo f M a c h i n e T o o l sa n d M a n u f a c t u r e ,2005,45(11):1282G1287.[6]㊀魏莹莹,安庆龙,蔡晓江,等.碳纤维复合材料超声扫描分层检测及评价方法[J ].航空学报,2016,37(11):3512G3519.W E IY i n g y i n g ,A N Q i n g l o n g ,C A I X i a o j i a n g,e t a l .D e t e c t i o na n d E v a l u a t i o no fL a ye r e d C a r b o n F i b e r C o m p o s i t e sb y U l t r a s o n i cS c a n n i n g [J ].A c t aA e r o Gn a u t i c a e tA s t r o n a u t i c aS i n i c a ,2016,37(11):3512G3519.[7]㊀方周倩,苗沛源,金肖克,等.碳纤维复合材料孔洞损伤超声波C 扫描无损检测[J ].纺织学报,2022,43(10):71G76.F A N GZ h o u q i a n ,M I A O P e i y u a n ,J I N X i a o k e ,e t a l .C a r b o nF i b e rC o m p o s i t e M a t e r i a lH o l eD a m a g e U l t r a s o n i c C S c a n N o n d e s t r u c t i v e D e t e c t i o n [J ].J o u r n a l o fT e x t i l e ,L a n c e t ,2022(10):71G76.[8]㊀李刚卿,周庆祥,张晓丹,等.C F R P 层压板的超声检测[J ].无损检测,2021,43(12):32G36.L I G a n g q i n g ,Z HO U Q i n g x i a n g ,Z HA N G X i a o Gd a n ,e ta l .U l t r a s o n i cT e s t i n g o fC F R P L a m i n a t e s [J ].N o n d e s t r u c t i v eT e s t i n g,201,43(12):32G36.[9]㊀朱萍玉,李永敬,孙孝鹏,等.纤维增强复合材料制孔分层缺陷检测与评价技术研究进展[J ].中国测试,2018,44(1):1G8.Z HU P i n g y u ,L IY o n g j i n g ,S U N X i a o p e n g ,e t a l .R e s e a r c hP r o gr e s s o fD e l a m i n a t i o nD e f e c tD e t e c t i o n a n d E v a l u a t i o n T e c h n o l o g y f o r F i b e r R e i n f o r c e d C o m p o s i t e s [J ].C h i n aJ o u r n a l o fT e s t i n g an d T e s Gt i n g,2018,44(1):1G8.[10]㊀C H E N W C .S o m eE x p e r i m e n t a l I n v e s t i ga t i o n s i n t h e D r i l l i n g o f C a rb o n F i b e r Gr e i n f o rc ed P l a s t i c (C F R P )C o m po s i t e L a m i n a t e s [J ].I n t e r n a t i o n a l J o u r n a l o fM a c h i n eT o o l s&M a n u f a c t u r e ,1997,37(8):1097G1108.[11]㊀F A R A Z A ,B I E R MA N N D ,W E I N E R T K.C u t Gt i n g E d g e r o u n d i n g :a n I n n o v a t i v eT o o lW e a rC r i t e Gr i o ni n D r i l l i n g C F R P C o m po s i t e L a m i n a t e s [J ].I n t e r n a t i o n a l J o u r n a lo f M a c h i n eT o o l s &M a n u Gf a c t u r e ,2009,49(15):1185G1196.(编辑㊀王艳丽)作者简介:杨㊀亮,男,1992年生,硕士研究生.研究方向为材料无损检测与评价.E Gm a i l :l y a n g @i m r .a c .c n .蔡桂喜(通信作者),男,1965年生,研究员.研究方向为无损检测与评价.发表论文30余篇.E Gm a i l :gx c a i @i m r .a c .c n .2332 中国机械工程第34卷第19期2023年10月上半月Copyright ©博看网. All Rights Reserved.。
碳纤维复合材料缺陷检测方法研究

在声场仿真中分别对样本材料、几何形状、相控阵延迟法则和探头进 行设置, 模拟出2D和3D的声场分布。在缺陷响应部分,设置不同 大小和形状的缺陷,计算声场在缺陷上的变化。
•13
碳纤维复合材料无损检测研究概况
碳纤维复合材料新型无损检测技术 3.超声检测方法
使用超声检测技术对复合材料内部的各种缺陷进行 检测,还可以利用超声检测技术测量材料的厚度。 其穿透能力强,探伤灵敏度高,易于操作,快速方 便,目前在国外发达国家超声检测技术已广泛应用 在无损检测领域。
局限性: • 对于形状复杂的材料或工件检测较困难,要求被测表面较光滑 • 需要耦合剂以减弱声波在空气中的衰减,这样可以保证声波与材料达到最大程度的耦合。 • 碳纤维复合材料板的厚度一般在 5mm 左右,属于薄板结构,声波在板内部传播会造成反射信号被噪声污
实现的,破坏性检测只能针对原材料进行
•7
碳纤维复合材料无损检测研究概况
复合材料的低导电特性和低热导率,声衰减强等特性使其不像金属材料那样容 易产生腐蚀缺陷,却极易因偶然撞击而产生不可见的裂纹、分层等现象,即使 是极微小的撞击也会在近表面产生严重的缺陷,影响材料的性能 20世纪80年代后,为解决复合材料缺陷的无损检测问题,诞生了许多新技术新 方法如:X射线检测,涡流检测、微波检测、超声检测等常规检测方法
•16
展示结构
第一步
检测方法
对碳纤维复合材料仿真实验研
究进行了详细的介绍。通过声
场仿真模块选择检测参数,包
碳纤维复合材料的无损检测技术探讨
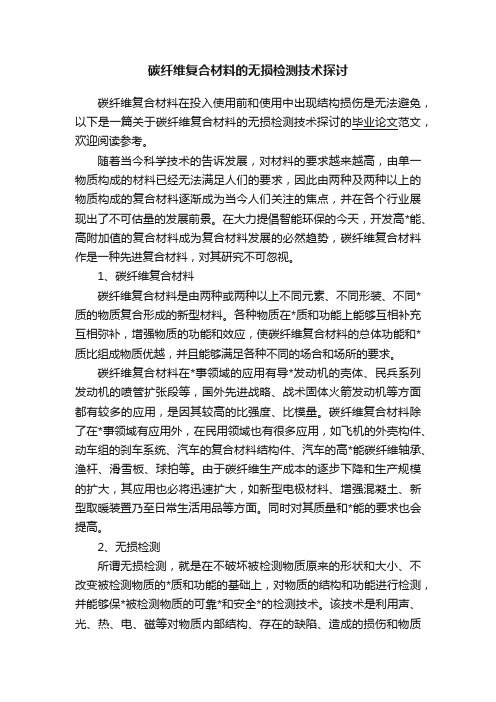
碳纤维复合材料的无损检测技术探讨碳纤维复合材料在投入使用前和使用中出现结构损伤是无法避免,以下是一篇关于碳纤维复合材料的无损检测技术探讨的毕业论文范文,欢迎阅读参考。
随着当今科学技术的告诉发展,对材料的要求越来越高,由单一物质构成的材料已经无法满足人们的要求,因此由两种及两种以上的物质构成的复合材料逐渐成为当今人们关注的焦点,并在各个行业展现出了不可估量的发展前景。
在大力提倡智能环保的今天,开发高*能、高附加值的复合材料成为复合材料发展的必然趋势,碳纤维复合材料作是一种先进复合材料,对其研究不可忽视。
1、碳纤维复合材料碳纤维复合材料是由两种或两种以上不同元素、不同形装、不同*质的物质复合形成的新型材料。
各种物质在*质和功能上能够互相补充互相弥补,增强物质的功能和效应,使碳纤维复合材料的总体功能和*质比组成物质优越,并且能够满足各种不同的场合和场所的要求。
碳纤维复合材料在*事领域的应用有导*发动机的壳体、民兵系列发动机的喷管扩张段等,国外先进战略、战术固体火箭发动机等方面都有较多的应用,是因其较高的比强度、比模量。
碳纤维复合材料除了在*事领域有应用外,在民用领域也有很多应用,如飞机的外壳构件、动车组的刹车系统、汽车的复合材料结构件、汽车的高*能碳纤维轴承、渔杆、滑雪板、球拍等。
由于碳纤维生产成本的逐步下降和生产规模的扩大,其应用也必将迅速扩大,如新型电极材料、增强混凝土、新型取暖装置乃至日常生活用品等方面。
同时对其质量和*能的要求也会提高。
2、无损检测所谓无损检测,就是在不破坏被检测物质原来的形状和大小、不改变被检测物质的*质和功能的基础上,对物质的结构和功能进行检测,并能够保*被检测物质的可靠*和安全*的检测技术。
该技术是利用声、光、热、电、磁等对物质内部结构、存在的缺陷、造成的损伤和物质的质量等进行检测,并达到对物质的判断和评价。
3、无损检测技术在碳纤维复合材料检测中的应用碳纤维复合材料在生产工艺过程中,碳纤维复合材料在生产制造和使用过程中之所以存在缺陷和遭受损伤,是由于受到碳纤维的形状和大小不规则、制作过程中的化学反应速率、各种元素的占有量、结合用的树脂的用量和粘度等的影响。
碳纤维复合材料的无损检测方法探讨

碳纤维复合材料的无损检测方法探讨作者:肖亚楠来源:《科技风》2017年第09期摘要:无损检测是一种先进的、科技含量较高的检测技术,不会对被检测物质的外观和性能造成任何不利影响,最大限度的保证了被检测物质结构和功能的完整,且检测精度高,检测结果十分可靠,现已广泛的应用到各行各业之中。
本文将对无损检测技术加以简介,并论述无损检测技术在碳纤维复合材料中的应用优势以及几种较为常用的无损检测方法,以期实现无损检测技术的迅速推广,促使无损检测在碳纤维复合材料检测工作中能够真正的发挥实效。
关键词:碳纤维复合材料;无损检测;方法;应用碳纤维复合材料是由两种及以上物质组成的新型材料,其强度高,稳定性好,功能齐全,能够很好的满足军事领域和民用领域的应用需求。
随着人们生活水平的提高,对生活环境也提出了更高的要求,碳纤维复合材料具有其他材料无法比拟的巨大优势,因此其发展前景无疑将会非常的广阔。
为了进一步提高材料性能,使碳纤维复合材料的效用得到最大化的发挥,在碳纤维复合材料中应用无损检测技术是十分必要的。
一、无损检测技术简介传统的检测技术大多具有破坏性,在检测工作完成后被测物质的外观或性能或多或少的会受到一定的影响,因此大多数检测技术都只能针对物质的某个形态或用途进行检验,这为检测工作增加了难度,同时也限制了检测技术的发展。
无损检测技术指的是在不破坏被测物质结构和性能的情况下,利用物质的内部缺陷对其进行检验的方法,通常需要借助物理仪器和设备,以便精确观察物质在接触热、光、磁时发生的变化。
无损检测技术具有动态性、实时性、兼容性的特征,所得的检测结果非常准确,基本上能够满足大多数物质的检测需求。
一般来说,无损检测技术具有以下三个特点:首先是非破坏性,指的是在采用无损检测技术时不会破坏被测物质的内部结构和性能,最大限度的保证了物质的完整性;其次是全面性,无损检测技术的检测范围广泛,可以用于对物质的全面检测;最后是全程性,无论被检测物质是原料、半成品、成品,或者是加工前、加工中、加工后都可以进行检测。
- 1、下载文档前请自行甄别文档内容的完整性,平台不提供额外的编辑、内容补充、找答案等附加服务。
- 2、"仅部分预览"的文档,不可在线预览部分如存在完整性等问题,可反馈申请退款(可完整预览的文档不适用该条件!)。
- 3、如文档侵犯您的权益,请联系客服反馈,我们会尽快为您处理(人工客服工作时间:9:00-18:30)。
12
碳纤维复合材料无损检测研究概况
碳纤维复合材料的缺陷类型有多种,在一块材料板中,有时仅存在一种缺陷, 有时会多种缺陷同时存在,其中分层、夹杂、脱粘与孔隙缺陷是最常见的缺陷
这些缺陷的存在势必会影响材料的各项性能指标,使碳纤维复合材料构件的应 用受到一定的限制,造成经济损失和安全问题。
准确、快速、有效、及时地检测出碳纤维复合材料中的缺陷对提高社会经济效 益有重大的意义
碳纤维复合材料常规检测方法 2.涡流检测技术
根据电磁感应原理来实现对工件的无损检测,通过检测材料内部 感生涡流的变化来对材料内部的缺陷实现定位。 当被检测金属工件存在缺陷时,就会导致感应涡流场强度发生变 化,分布发生改变,线圈阻抗也发生变化 高灵敏度,适用于检测非磁性含金属材料,可以自动对准工件探 伤,不需要耦合剂。但是其局限性表现在穿透能力弱,难以判断 缺陷的种类。又由于涡流是交变电流,因此涡流检测技术非常适 用于检测表面缺陷和近表面缺陷。
9
碳纤维复合材料无损检测研究概况
碳纤维复合材料常规检测方法 1.射线检测技术
材料中缺陷部位与无缺陷部位对射线的吸收能力不同,射线透过 有缺陷部位时,缺陷部分将会使X射线在物体内部的衰减发生改 变,且射线强度要高于无缺陷部位
I0 为入射线强度,I 为透射线强度,T 为材料厚度,μ 为衰减系数 由公式可知,在入射线强度相同的情况下,透射射线的强度与材 料的厚度,衰减系数有关
5
碳纤维复合材料应用背景 碳纤维复合材料
从最初在航空航天和军事工业领域的应用,逐步推广于体育休闲用品行业,近年来在工 业上获得广泛的应用,其中汽车、土木建筑、能源和电子等领域为最有前景的应用领域
6
碳纤维复合材料应用背景
碳纤维复合材料制作过程中或使用过程中会形成各种形式的缺陷: 基体和增强材料融合继而定型成为产品的过程中,存在诸多不确定因素 碳纤维复合材料的各向异性结构
7
碳纤维复合材料无损检测研究概况
无损检测NDT(Non-destructive Te变化,在不 损伤被检测对象的条件下,探测各种材料、结构件等内部或表面缺陷,并对缺 陷的位置、类型、数量、尺寸等做出判断和评价
与破坏性检测相比,NDT有如下优势: 一是非破坏性,对材料无需破坏就可以进行有效的检测,不损害材料的性能 二是全面性,可在不破坏材料的前提下实现全面的检测 三是全程性,可以在设备的使用过程中对材料进行检测,这是破坏性检测不能 实现的,破坏性检测只能针对原材料进行
碳纤维复合材料新型无损检测技术 1.错位散斑干涉法
错位散斑干涉法可以确定材料的应力场,运用该 方法可以检测分层,脱粘,或者纤维褶皱等缺陷
激光器发出激光束照射到物体表面,通过 BS分 光棱镜将入射激光束分为两路:测量光束、参考 光束,这两束激光经反射棱镜M1 和 M2反射后 在 BS 中发生干涉,产生干涉条纹,通过 CCD 和采集卡传输图像信息到 PC 中
碳纤维复合材料缺陷检测方法研究
汇报人: 金春杏 刘玉振 赵成武 导 师: 王 仲
目录
CONTENTS
01 研究背景
03 缺陷识别分类
02 仿真&实验 04 总结与展望
研究 背景
研究背景
01 02 03
碳纤维复合材料应用背景 碳纤维复合材料无损检测研究概况 碳纤维复合材料缺陷识别研究概况
4
碳纤维复合材料应用背景 复合材料
错位散斑干涉技术可适用于形状较为复杂的材料 ,但在抗干扰方面仍存在一些技术难题
13
碳纤维复合材料无损检测研究概况
碳纤维复合材料新型无损检测技术 2.热成像方法
热成像方法可以检测出金属材料和复合材料中的多种缺陷 如:分层、脱粘等。 Levar and Hamilton 利用红外热成像检测方法检测玻璃 钢与混凝土结构的粘合质量,郑立胜等人检测出了碳纤维 复合材料中的微小裂纹,王焰等人利用脉冲式主动红外热 成像法对玻璃纤维复合材料的分层缺陷良好的检测效果。
8
碳纤维复合材料无损检测研究概况
复合材料的低导电特性和低热导率,声衰减强等特性使其不像金属材料那样容 易产生腐蚀缺陷,却极易因偶然撞击而产生不可见的裂纹、分层等现象,即使 是极微小的撞击也会在近表面产生严重的缺陷,影响材料的性能 20世纪80年代后,为解决复合材料缺陷的无损检测问题,诞生了许多新技术新 方法如:X射线检测,涡流检测、微波检测、超声检测等常规检测方法
11
碳纤维复合材料无损检测研究概况
碳纤维复合材料常规检测方法 3.微波检测技术
微波检测技术主要是利用波长在 0.001m 到 1m 的电磁波在非金属复合材料中穿透力强,衰减小等特 点实现对复合材料缺陷的检测 微波检测只是对常见的分层、脱粘、气孔等有较好的检测效果,该方法仅适用于对较大面积的缺陷检测
此方法对被检测材料要求低,检验结果简单直观,易于观察,可 以长期保存。适用于复合材料中的孔隙、夹杂物、贫胶等体积型 缺陷的检测,并且有良好的成像效果。但是针对分层缺陷等平面 型缺陷,射线能量变化小,分辨率低,检测较为困难。此外射线 检测对人身安全方面有较大的影响,操作者需要经过专门的训练
10
碳纤维复合材料无损检测研究概况
复合材料是由两种以上的材料通过复合工艺组合而成的一种具有特殊性能的材料 特点:各组分含量不小于 5%;材料总体性能显著优于各组分性能;通过各种方法混合而成
碳纤维复合材料
一般碳素材料:耐摩擦、耐高温、耐腐蚀、导电性好 特有性质:密度小、质量轻,密度为 1.5—2g/cm3, 是钢材料的四分之一;
拉伸度高,与硅基纤维复合材料相比,拉伸强度是它的 3-7 倍; 高比强度,其强度大约为钢的 5 倍; 高弹性模量,弹性回复 100%,在相同的外负荷下,应变较小; 各项异性,热膨胀系数小,耐骤冷急热;耐疲劳性好