细长轴加工方法
细长轴的加工技巧

细长轴的加工技巧蚌埠液力机械厂马长明细长轴类的工件刚性很差,原来加工细长轴的方法是采用正向走刀,用90度主偏角车刀加工外圆,它的缺点是:在车削加工时很容易因车削力及重力的作用产生振动而变形,从而降低加工精度和表面光洁度,因细长轴的热扩散性能差,在切削热的作用下,会产生相当大的线膨胀,如果轴的两端为固定支承,则会因受挤压而弯曲变形。
当轴以较高速度旋转时,这种弯曲所引起的离心力,将进一步加剧轴的变形。
由于细长轴的加工时一次走刀的所需时间较长,刀具磨损大,从而增大了工件的几何形状的误差。
所以选择合理的车刀几何角度,对细长轴的加工质量有着至关重要的作用,针对细长轴在切削加工中存在的技术难点,通过实践总结出:改用75度左偏刀和反向走刀法切削细长轴类零件。
一、工件的装夹方式:(主要解决切削时产生的线膨胀)首先将棒料校直,用卡爪夹紧一端,一般在15毫米左右,在靠近卡爪5-10毫米处车出缩颈d,d的直径可随着D的大小产生变化,切退刀槽如图一所示,细长轴的另一端用弹性活动顶尖支承,当工件因切削热产生线性膨胀伸长时,弹性活动顶尖能自动后退,可以有效地补偿工件因热变形伸长,避免了热膨胀引起的变形。
心,这时在切削过程中工件就会产生振动,不能进行正常的切削。
如选用粗车时,车刀安装的位置高于机床中心0.5-1.5毫米.如图二所示,这样在实际切削加工中,工作前角γ1增大,使刀具前面磨损减小,便于切削,同时其工作后角α1则相应地减小,刀具后角的主要作用是减小和增大刀具后刀面与工件的摩擦,现在刀尖抬高0.5-1.5毫米,后角变小了,磨擦增大,切削时,刀具后刀面与工件表面有轻微的磨擦,相当于增加了一个支承点,使工件刚性增大,防止了切削时的低频振动,故而振动消失,细长轴表面的光洁度得到提高,保持了工件固有的刚性。
选用75度主偏角车刀,可有效地消除工件出现弓形,振动,车刀主前角γ为25度,γ棱边是25度,倒棱0.4-0.8毫米,由于倒棱和R4断屑槽的作用,它具有良好的断屑性能,同时由于刀尖角度的增大,增加了刀尖的强度和散热条件,车刀主后角为8度, α棱为-12度,倒棱为0.1-0.3毫米,增加了车刀后隙面支持在工件上的接触面积,防止了由于工件材料内部组织不均而产生的啃刀现象,并可消除低频振动。
细长轴类加工

1. 细长轴加工特点及措施:A、工件刚性差,易弯曲,振动图4-10:细长轴的装夹措施:跟刀架、中心架(三爪),增大车刀主偏角,减少径向切削力,改变切削方向――反向大进给。
图4-11:反向进给车削法B、工件长度长,热变形大充分冷却,弹性后顶尖,C、切削行程大:措施:耐磨材料刀具;合理几何角度车刀,减少切削用量。
2.丝杠加工(1)丝杠结构的工艺特点及要求(2)丝杠材料(3)丝杠加工工艺分析粗切:小批,车削;大批,旋风铣削;图4-15:车削梯形螺纹的切削图形精切:不淬硬丝杠:车削(旋风铣削)。
(精密螺纹车床)淬硬丝杠:“先车后磨”或“全磨”。
(螺纹磨床)A)前支承轴颈安装在中心架上,后端支在磨床床头卡盘内。
校正:前端调整中心架,后端在卡盘与轴颈之间垫薄纸片,设备简单,单件生产。
B)前后支承轴颈分别装在中心架上。
校正:用千分表校正中心架位置,调整费时,质量不稳定,小规模生产。
C)前后支承放在专用夹具的V型块上,用浮动卡头联结。
(1)中心孔加工粗:铣端面钻中心孔机床。
多次修磨,提高精度。
加工质量:深度--轴向尺寸,形状--圆度,位置--同轴度(2)外圆加工图4-4:组合磨削(图错须更换)图4-16:多刀切削图4-17:仿形加工图4-18:砂带磨外圆表面车削:粗、半精加工(转塔,数控,多刀半自动,液压仿形半自动车床)磨削:精加工(组合磨削,成形砂轮磨削,无心磨削,宽砂轮磨削,多片砂轮精密加工、超精加工:研磨,滚压,抛光,高光洁度磨削。
(3)精磨锥孔。
细长轴的加工工艺分析
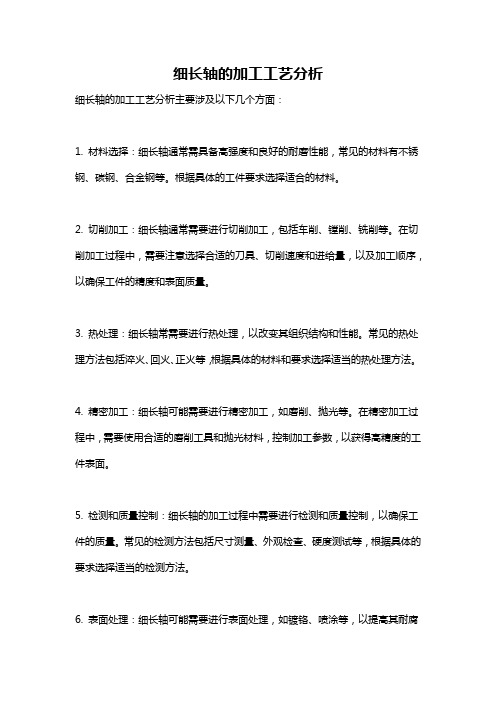
细长轴的加工工艺分析
细长轴的加工工艺分析主要涉及以下几个方面:
1. 材料选择:细长轴通常需具备高强度和良好的耐磨性能,常见的材料有不锈钢、碳钢、合金钢等。
根据具体的工件要求选择适合的材料。
2. 切削加工:细长轴通常需要进行切削加工,包括车削、镗削、铣削等。
在切削加工过程中,需要注意选择合适的刀具、切削速度和进给量,以及加工顺序,以确保工件的精度和表面质量。
3. 热处理:细长轴常需要进行热处理,以改变其组织结构和性能。
常见的热处理方法包括淬火、回火、正火等,根据具体的材料和要求选择适当的热处理方法。
4. 精密加工:细长轴可能需要进行精密加工,如磨削、抛光等。
在精密加工过程中,需要使用合适的磨削工具和抛光材料,控制加工参数,以获得高精度的工件表面。
5. 检测和质量控制:细长轴的加工过程中需要进行检测和质量控制,以确保工件的质量。
常见的检测方法包括尺寸测量、外观检查、硬度测试等,根据具体的要求选择适当的检测方法。
6. 表面处理:细长轴可能需要进行表面处理,如镀铬、喷涂等,以提高其耐腐
蚀性和装饰性。
在表面处理过程中,需要选择合适的表面处理方法和材料,控制加工参数,确保工件的表面质量。
总之,细长轴的加工工艺分析需要考虑材料选择、切削加工、热处理、精密加工、检测和质量控制,以及表面处理等方面的因素,以确保工件的加工质量和性能。
细长轴的车削加工要领

细长轴类零件的车削加工1. 中心架和跟刀架在细长轴零件加工中的应用车削细长轴工件,长度是直径10~12倍以上的长轴时,如车床光杠、丝杠等,由于这些轴本身的刚性差,加上切削力、切削热和震动等影响,车削时易产生弯曲、锥度、腰鼓度和竹节形等缺陷。
此外,在车削过程中还会引起震动,影响工件表面粗糙度。
为了防止这种现象产生,我们可以应用一种叫做中心架的特殊支承夹具。
中心架和跟刀架是车床附件之一,用卡盘顶针与中心架,或前后顶针与跟刀架装夹,可提高切削加工系统的刚性。
使用这些附加的装卡工具,可以增加工件的装卡刚度,减少震动,保证加工质量,避免零件产生鼓面,提高工件表面形状精度和表面粗糙度,并允许采用大切削用量加工,提高劳动生产率。
下面分别就中心架与跟刀架在细长轴零件中的应用加以说明。
一、中心架在细长轴零件加工中的应用1.中心架的结构中心架的结构组成如图5-1所示。
中心架一般固定在床面一定位置上,如图5-1(b)所示。
它的主体座l通过压板4和螺母5紧固在床面上。
盖子3与主体1用销作活落连接,盖子3可以打开或盖住,并用螺钉2固定。
三个爪的向心或离心位置,可以用螺钉6调节,以适应不同直径大小的工件,并用螺钉9紧固爪7和8,使爪在需要位置上固定不动。
2.中心架的使用(1)中心架的使用调整方法工件装上中心架之前,先在毛坯中间处车一条安装中心架卡爪的沟槽,槽的直径等于工件的直径,其宽度略比爪宽大些。
接着把中心架安装在床面适当位置上并加以固定,打开盖子3,把工件安装在两顶针中间(床尾要先调整好),用划针盘或百分表检查槽是否跳动,然后将盖子3盖好,并调整中心架3个爪,使他们与工件沟槽轻轻接触。
这时慢慢转动工件,看是否能转得动。
在爪与工件之间最好垫一层铜皮或平皮带,并加些润滑油,或者3个爪用夹布胶木制造,这样可防止擦伤工件表面。
在车削大型工件或工件转速较高时,就必须采用带滚动轴承的中心架,如图5-2所示。
(2)车削步骤车削时,先车一端,一直车到沟槽为止。
细长轴加工的弯曲变形及控制方法

紧, 定心精度较高 ; 缺点是顶尖轴 向压力可能导致工
件 弯 曲 ,无法 消 除工 件 受热 伸 长 导致 的弯 曲变形 。 解决 轴 向伸 长 问题 的简 单方 法是 人工 干预 。当工件 受 热伸 长轴 向压 紧力过 大 时 , 顶尖 会 发 出沉 闷声 , 此 时应 及 时调整 顶 紧力 , 预 紧力 大小 以用 食指 、 拇 指用 细长轴加 工的弯 曲变 形及 控制方法 力 能使 顶尖停 转 为适 当 。
证工件在全长上始终受到轴 向拉力的作用 ,从而减
小工 件振 动 与弯 曲变形 。 实 际操作 中 , 为保证 工件 可 靠拉 紧 , 一 般将 拉伸 装夹 与反 向走 刀配 合使 用 。
~
2 . 2 增 加 中间 支撑
一
定着三个切削分力的大小和比例关系。径 向切削力
随 着 主偏 角 增大 明显 减 小 ,在 6 0 。 ~7 5 。范围内, j个 切削 分力 的 比例较 为合 理 。 在 车削 细长轴 时 , 主 偏 角可 以取为 7 5 。 ~9 0 。。 刃倾 角( 人s ) 影响着 车 削 过 程 中切 削 的流 向 、刀 尖 的强度及 切 削分力 的 比例 关 系 。刃倾角 越大 , 径 向切削 力越 小 , 但 轴 向切 削 力
卜 P × 。 …奋
图三 拉伸装夹示意 图
由 图三可 见 , 采用拉 伸装 夹后 , 车 削 中工 件位 于 刀具 与 夹拉 头之 间所 受 轴 向拉力 总 量均 为 P ,卡 盘
与刀具 间 _ T 件 所 受 轴 向拉 力 p X 与走 刀方 向有 关 ,
采用弹性顶尖是解决工件因热膨胀轴 向伸长的
有效 办 法 , 如 图二 所示 。需 要注 意 的是 , 要 适 当调整
细长轴的加工方法

细长轴的加工方法细长轴的加工方法是指在机械加工过程中对于长度较长、直径相对较小的轴类工件所采取的一系列加工工艺和方法。
这类工件在许多领域中都有广泛的应用,比如汽车制造、航空航天、机械制造等。
细长轴的加工方法主要有以下几种:1. 切削加工:细长轴通常通过车床、铣床、钻床等机床进行切削加工。
在车床上,可以采用车削、车磨等方式进行加工,通过刀具不断地切削和磨削,逐步将粗加工的轴件加工成细长轴。
在铣床上,可以采用铣削、镗削等方式进行加工,通过刀具的旋转和移动,将工件表面的一定量材料切除,以达到加工精度和表面质量的要求。
2. 磨削加工:磨削是细长轴加工中常用的一种方法,通过磨削工具与工件表面的相对运动,将工件表面的一定量材料切除,以达到加工精度和表面质量的要求。
磨削加工分为外圆磨削和内圆磨削两种,分别适用于细长轴的外圆面和孔内面的加工。
常用的磨削加工方法有普通磨削、中心磨削、无心磨削和滚动磨削等。
3. 精密加工:细长轴的加工精度要求比较高,常常需要进行精密加工。
精密加工包括线切割、电火花加工、焊接等。
线切割是利用线切割机将工件切割成需要的形状,可以实现高精度的加工。
电火花加工是利用电火花放电烧蚀工件表面的加工方法,可以实现对轴件表面的高精度加工。
焊接是将两个或多个工件通过热源加热到熔融状态,使其熔合在一起的加工方法,通过焊接可以实现对细长轴的连接。
4. 其他加工方法:除了以上几种常规的加工方法外,还有一些特殊的加工方法可用于细长轴的加工。
比如深孔加工、滚压加工、冲压加工等。
深孔加工是通过刀具在细长轴上钻孔,可以实现对轴内腔的加工。
滚压加工是利用滚轮对工件表面施加压力,使其产生塑性变形,从而改善轴件的表面硬度和粗糙度。
冲压加工是将细长轴放置在冲压模具中,通过冲击力将轴件冲压成需要的形状。
细长轴的加工方法在实际应用中需要根据工件的具体要求和加工精度来选择,确保加工精度和表面质量的要求。
同时,在细长轴的加工过程中,还需要注意工艺参数的选择、刀具的使用和切削润滑的控制,以确保加工质量和工件的加工效率。
细长轴的加工方法
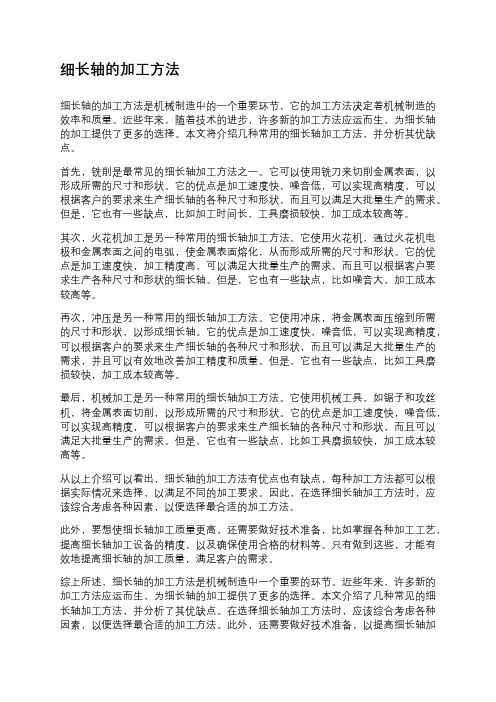
细长轴的加工方法细长轴的加工方法是机械制造中的一个重要环节,它的加工方法决定着机械制造的效率和质量。
近些年来,随着技术的进步,许多新的加工方法应运而生,为细长轴的加工提供了更多的选择。
本文将介绍几种常用的细长轴加工方法,并分析其优缺点。
首先,铣削是最常见的细长轴加工方法之一。
它可以使用铣刀来切削金属表面,以形成所需的尺寸和形状。
它的优点是加工速度快,噪音低,可以实现高精度,可以根据客户的要求来生产细长轴的各种尺寸和形状,而且可以满足大批量生产的需求。
但是,它也有一些缺点,比如加工时间长,工具磨损较快,加工成本较高等。
其次,火花机加工是另一种常用的细长轴加工方法。
它使用火花机,通过火花机电极和金属表面之间的电弧,使金属表面熔化,从而形成所需的尺寸和形状。
它的优点是加工速度快,加工精度高,可以满足大批量生产的需求,而且可以根据客户要求生产各种尺寸和形状的细长轴。
但是,它也有一些缺点,比如噪音大,加工成本较高等。
再次,冲压是另一种常用的细长轴加工方法。
它使用冲床,将金属表面压缩到所需的尺寸和形状,以形成细长轴。
它的优点是加工速度快,噪音低,可以实现高精度,可以根据客户的要求来生产细长轴的各种尺寸和形状,而且可以满足大批量生产的需求,并且可以有效地改善加工精度和质量。
但是,它也有一些缺点,比如工具磨损较快,加工成本较高等。
最后,机械加工是另一种常用的细长轴加工方法。
它使用机械工具,如锯子和攻丝机,将金属表面切削,以形成所需的尺寸和形状。
它的优点是加工速度快,噪音低,可以实现高精度,可以根据客户的要求来生产细长轴的各种尺寸和形状,而且可以满足大批量生产的需求。
但是,它也有一些缺点,比如工具磨损较快,加工成本较高等。
从以上介绍可以看出,细长轴的加工方法有优点也有缺点,每种加工方法都可以根据实际情况来选择,以满足不同的加工要求。
因此,在选择细长轴加工方法时,应该综合考虑各种因素,以便选择最合适的加工方法。
此外,要想使细长轴加工质量更高,还需要做好技术准备,比如掌握各种加工工艺,提高细长轴加工设备的精度,以及确保使用合格的材料等。
细长轴的车削加工要领

细长轴类零件的车削加工1. 中心架和跟刀架在细长轴零件加工中的应用车削细长轴工件,长度是直径10〜12倍以上的长轴时,如车床光杠、丝杠等,由于这些轴本身的刚性差,加上切削力、切削热和震动等影响,车削时易产生弯曲、锥度、腰鼓度和竹节形等缺陷。
此外,在车削过程中还会引起震动,影响工件表面粗糙度。
为了防止这种现象产生,我们可以应用一种叫做中心架的特殊支承夹具。
中心架和跟刀架是车床附件之一,用卡盘顶针与中心架,或前后顶针与跟刀架装夹,可提高切削加工系统的刚性。
使用这些附加的装卡工具,可以增加工件的装卡刚度,减少震动,保证加工质量,避免零件产生鼓面,提高工件表面形状精度和表面粗糙度,并允许采用大切削用量加工,提高劳动生产率。
下面分别就中心架与跟刀架在细长轴零件中的应用加以说明。
一、中心架在细长轴零件加工中的应用1 .中心架的结构中心架的结构组成如图5-1 所示。
中心架一般固定在床面一定位置上,如图5-1(b)所示。
它的主体座I通过压板4和螺母5紧固在床面上。
盖子3 与主体1 用销作活落连接,盖子3可以打开或盖住,并用螺钉2 固定。
三个爪的向心或离心位置,可以用螺钉6 调节,以适应不同直径大小的工件,并用螺钉9 紧固爪7 和8,使爪在需要位置上固定不动。
2.中心架的使用(1 )中心架的使用调整方法工件装上中心架之前,先在毛坯中间处车一条安装中心架卡爪的沟槽,槽的直径等于工件的直径,其宽度略比爪宽大些。
接着把中心架安装在床面适当位置上并加以固定,打开盖子3,把工件安装在两顶针中间(床尾要先调整好) ,用划针盘或百分表检查槽是否跳动,然后将盖子3 盖好,并调整中心架3 个爪,使他们与工件沟槽轻轻接触。
这时慢慢转动工件,看是否能转得动。
在爪与工件之间最好垫一层铜皮或平皮带,并加些润滑油,或者3 个爪用夹布胶木制造,这样可防止擦伤工件表面。
在车削大型工件或工件转速较高时,就必须采用带滚动轴承的中心架,如图5-2 所示。
- 1、下载文档前请自行甄别文档内容的完整性,平台不提供额外的编辑、内容补充、找答案等附加服务。
- 2、"仅部分预览"的文档,不可在线预览部分如存在完整性等问题,可反馈申请退款(可完整预览的文档不适用该条件!)。
- 3、如文档侵犯您的权益,请联系客服反馈,我们会尽快为您处理(人工客服工作时间:9:00-18:30)。
一、细长轴的定义当工件长度跟直径直比大于20~25倍(L/d>20~25)时,称为细长轴。
二、由于细长轴本身刚性差(L/d值愈大,刚性愈差),在车削过程中会出现以下问题:1、工件受切削力、自重和旋转时离心力的作用,会产生弯曲、振动,严重影响其圆柱度和表面粗糙度。
2、在切削过程中,工件受热伸长产生弯曲变形,;车削就很难进行,严重时会使工件在顶尖间卡住。
因此,车细长轴是一种难度较大的加工工艺。
虽然车细长轴的难度较大,但它也有一定的规律性,主要抓住中心架和跟刀架的使用、解决工件热变形伸长以及合理选择车刀几何形状等三个关键技术,问题就迎刃而解了。
三、使用中心架支承车细长轴在车削细长轴时,可使用中心架来增加工件刚性。
一般车削细长轴使用中心架的方法有:1、中心架直接支承在工件中间当工件可以分段车削时,中心架支承在工件中间,这样支承,L/d值减少了一半,细长轴车削时的刚性可增加好几倍。
在工件装上中心架之前,必须在毛坯中部车出一段支承中心架支承爪的沟槽,表面粗糙度及圆柱度误差要小,否则会影响工件的精度。
车削时,中心架的支承爪与工件接触处应经常加润滑油。
为了使支承爪与工件保持良好的接触,也可以在中心架支承爪与工件之间加一层砂布或研磨剂,进行研磨抱合。
2、用过渡套筒支承车细长轴用上述方法车削支承承中心架的沟槽是比较困难的。
为了解决这个问题,可加用过渡套筒的处表面接触,见图(9—2)。
过渡套筒的两端各装有四个螺钉,用这些螺钉夹住毛坯工件,并调整套筒外圆的轴线与主轴旋转轴线相重合,即可车削。
四、使用跟刀架支承车细长轴跟刀架固定在床鞍上,一般有两个支承爪,跟刀架可以跟随车刀移动,抵消径向切削时可以增加工件的刚度,减少变形。
从而提高细长轴的形状精度和减小表面粗糙度。
从跟刀架的设计原理来看,只需两只支承爪就可以了(图9--4),因车刀给工件的切削抗力F`r,使工件贴住在跟刀架的两个支承爪上。
但是实际使用时,工件本身有一个向下重力,以及工件不可避免的弯曲,因此,当车削时,工件往往因离心力瞬时离开支承爪、接触支承爪而产生振动。
如果采用三只支承爪的跟刀架支承工件一面由车刀抵住,使工件上下、左右都不能移动,车削时稳定,不易产生振动。
因此车细找轴时一个非常关键的问题是要应用三个爪跟刀架。
五、减少工件的热变形伸长车削时,由于切削热的影响,使工件随温度升高而逐渐伸长变形,这就叫“热变形”。
在车削一般轴类时可不考虑热变形伸长问题,但是车削细长轴时,因为工件长,总伸长量长,所以一定要考虑到热变形的影响。
工件热变形伸长量可按下式计算。
△L=aL△t式中a—材料线膨胀系数,1/℃;L—工件的总长,mm;△t—工件升高的温度,℃。
常用材料的线膨胀系数,可查阅有关附录表。
例车削直径为25mm,长度为1200mm的细长轴,材料为45钢,车削时因受切削热的影响,使工件由原来的21℃上升到61℃,求这根细长轴的热变形伸长量。
解已知L=1200mm;△t=61℃-21℃=40℃;查表知,45钢的线膨胀系数a=11.59×10-6 1/℃根据公式(9.5)得:△L=aL△t=11.59×10-6×1200×40=0.556mm从上式计算可知,细长轴热变形伸长量是很大的。
由于工件一端夹住,一端顶住,工件无法伸长,因此只能本身产生弯曲。
细长轴一旦产生弯曲后,车削就很难进行。
减少工件的热变形主要可采取以下措施:1、使用弹性回转顶尖用弹性回转顶尖加工细长轴,可有较地补偿工件的热变形伸长,工件不易弯曲,车削可顺利进行。
2、加注充分的切削液车削细长轴时,不论是低速切削还是高速切削,为了减少工件的温升而引起热变形,必须加注切液充分冷却。
使用切削液还可以防止跟刀架支承爪拉毛工件,提高刀具的使用寿命和工件的加工质量。
3、刀具保持锐利以减少车刀与工件的摩擦发热。
六、合理选择车刀几何形状车削细长轴时,由于工件刚性差,车刀的几何形状对工件的振动有明显的影响。
选择时主要考虑以下几点:1、由于细长轴刚生差,为减少细长轴弯曲,要求径向切削力越小越好,而刀具的主偏角是影响径向切削力的主要因素,在不影响刀具强度情况下,应尽量增大车刀主偏角。
车刀的主偏角取kr=80°~93°。
2、为减少切削烟力和切削热,应该选择较大的前角,取r0=15°~30°。
3、车刀前面应该磨有R11.5~3的断屑槽,使切削顺利卷曲折断。
4、选择正刃倾角,取入=3°使切削屑流向待加工表面,并使卷屑效果良好。
5、切削刃表面粗糙度要求在Ra0.4以下,并要经常保持锋利。
6、为了减少径向切削力,应选择较小的刀尖圆弧半径(re<0.3mm)。
倒棱的宽度也应选得较小,取倒棱宽br1=0.5f。
七、车削细长轴的车刀1、刀片材料为YT15硬质合金。
2、切削用量:粗车时,切削速度vc=50~60m/min;进给量f=0..3~0.4mm/r;切削深度ap=1.5~2mm。
精车时,切削速度vc=60~100m/min;进给量f=0.08~0.12mm/r ;切削深度ap=0.5~1mm.。
3、采用乳化液作切削液。
4、适用范围:适用于车削光杠、丝杆等细长轴。
1.在什么情况下使用中心架和跟刀架?答:车削长轴时,工件如果是伸出夹具长度超过直径15倍的光滑轴(如车床光杠等),要用卡盘支持尖、跟刀架装夹,或者用前后支持尖、跟刀架装卡。
台阶轴(如车床主轴等)要用卡盘、中心架装夹。
有些特别长的工件也可以采用卡盘、支持尖、中心架、跟刀架同时进行装夹。
使用这类附加的装夹工具,可以增加工件装夹刚度,保证加工质量,减少振动,避免工件产生或鼓肚,提高工件几何精度和表面粗糙度,同时可以采用大切削用量加工,提高劳动生产率。
2.用中心架加工工件时怎样装夹和找正?答:用中心架加工工件时将打好中心孔的工件装夹好,并用尾座支持尖支持好。
用较小的切削用量支持车一段光径,其直径必须大于工件的成活直径,然后将中心架的三个支承爪卡装在光径上。
在使用中心架时,应先将架体固定在床面上,压紧上盖,然后调整三个支承爪,使它轻轻地、均匀地接触在光径上,再紧固螺钉。
在切削过程中,要不断加上润滑油,并随时注意发热情况和支承的松紧。
如果毛坯件没有预制中心孔,或者工件在中心架上装夹的部分是已经加工好的表面,不允许擦伤的情况下,便需要使用定心套筒进行装夹,如果9-2所示。
先将工件装夹在卡盘和尾座支持减之间,并校正夹固,然后退出尾座支持尖,将定心套筒固定在工件的适当位置上,用安装在小刀架上的百分表,分别在水平方向和垂直方向校正定心套筒与工件轴线的同轴度,然后再架上中心架。
定心套筒如果夹固在已经精加工的表明上,必需在夹固螺钉和工作表面垫上纯铜皮,防止压伤工件。
在确定中心架位置时,要考虑到公件加工时要有足够的刚度。
如果用后支持尖支支持,最好选取工件和中部作为忠心加支承的位置。
又如加工端面或内孔时,则在接近工件端部作为中心架支承位置。
中心架位置的确定,除考虑到工件装夹应有足够的刚度以外,还应该保证不会由于中心架的位置不合理而影响加工。
3.如何使用中心架和跟刀架?答:常见的中心架使用方法有以下三种:(1)车削长轴如图9-2所示,把中心架直接安装在工件中间,以增大长轴刚性。
在安装中心架之前,在毛坯安装中心架处先车一段放置中心架支承爪的沟槽,沟槽的宽度比支承爪稍宽,沟槽的直径稍大于工件的最后尺寸(以便精车)。
对中心架三个支承爪的调整方法是,先调整下面两个爪,然后把盖子盖好固定,最后调整上面一个爪。
车削时,支承爪和工件接触处应经常加润滑油,并注意松禁,以防工件拉毛和摩擦发热。
(2)车端面和钻中心孔,对大而长的工件,如果在车床上车端面和钻中心孔单靠卡盘夹紧是不稳妥的,一般采用将工件的一端夹住;另一端搭中西架的办法,如图9-3所示。
安装的过程:先校正工件,然后调整支承爪,使工件旋转轴线与主轴旋转轴线一致,防止加工时损坏工具或使工件从三爪自定心卡盘上掉下来。
在加工时,为了防止中心架的支承爪剧烈磨损、拉毛工件,在中心架上面一个爪与工件之间垫一张细号砂布,并加上润滑油,砂布背面应贴住工件。
(3)车内孔或钻孔车削较长套筒类的内孔或钻孔或车内螺纹时,单靠卡盘夹紧工件是不够牢靠的,通常也使用中心架来支承工件的一端。
使用中心架的目的是抵抗径向力,防止工件弯曲变形。
主要用来车削不允许接刀的细长工件,如车床上的光杠和长丝杠等。
图9-4是跟刀架的使用示意图。
跟刀架一般只有两个支承爪,而另外一个支承爪被车刀所代替。
跟刀架固定在车床的大滑板上,随着车刀一起移动。
在安装跟刀架之前应先在工件靠尾座端车出一段外圆,以便安装跟刀架的爪卡。
调整卡爪的压力时,应当注意使接触松紧适当,否则车削是会产生振动,甚至使工件产生竹节状或螺旋形。
4.使用跟刀架和中心架应注意哪些问题?答:1)保证车床尾座支持尖和车床主轴的同轴度,否则工件会产生弯曲和锥度。
2)尾座套筒伸出部分,应当尽可能短些,以便减少振动。
3)应保证工件两端的中心孔的质量,对加工精度要求高的轴类工件,要通过研磨来提高中心孔的精度。
4)使用支持尖时,支持紧力量要适当。
5)跟刀架和中心架的支承爪圆弧面,与工件外圆应当吻合。
在必要时,对支承爪圆弧面进行休整和研磨。
6)跟刀架和中心架的支承爪在使用时的调整要适当,与工件轻触支持实。
7)在加工时,如果发现形状误差超差时,要松开支承爪重新进刀,待形状误差吵差消除后,再开车重新调整支承爪。
8)精车长轴或细长轴时,应消除工件材料的内应力。
9)如果原材料弯曲,应当预先校正。
10)合理选择车刀的角度和切削用量。
11)加工时,冷却液的浇淋要充分。
12)粗车时,跟刀架装在车刀后面,精车时,跟刀架装在车刀前面,车刀与跟刀架的距离约为20-30mm。
13)如果工件一端用卡盘装夹,另一端用中心架,在安装时,最好先用支持尖把工件支持住,并在工件的两端用百分表测量,然后再调整中心架的支承爪,防止中心架架偏,造成加工误差。
14)加工中采用中心架时,工件表面接触中心架的那一段外圆是中心架支承基准,必需先精车一刀,表面粗糙度可以低一点,但外圆不能有形状误差。
5.用中心架车销细长轴,出现外圆联接不好的原因是什么?如何解决?答:用中心架车削细长轴时,先把工件装夹在两支持尖之间(或一端用卡盘,另一端用卡盘,另一端用支持尖),在工件上对着中心架部位(一般在工件的中部)车出一个宽于中心架支承爪的凹槽,一般为30-50mm,直径应大于工件直径尺寸(留出足够的加工余量),装好中心架,调整好三个支承爪,即可进行车削加工。
车削过程中要注意已加工表面的两端应保证尺寸一致,否则应随时调整中心架卡爪位置,以保证工件中心线于主轴轴线夹角为0°。
一端车好后将工件卸下,调头重新装夹,调节中心架,再车另一端。