表面粗糙度与公差等级的关系
公差配合与测量技术表面粗糙度

2.摩擦表面、承受重载荷和交变载荷表面的粗糙度数值应选小值。 3.配合精度要求高的结合面、尺寸公差和形位公差精度要求高的
表面,粗糙度选小值。 4.同一公差等级的零件,小尺寸比大尺寸,轴比孔的粗糙度值要小。
用去除材料方法获得的表面粗 糙度,Ra的最大值为 6.3μm,Ra的最小值为 3.2μm
用不去除材料方法获得的表面 粗糙度,Ry的最大值为 100μm
用去除材料方法获得的表面粗 糙度,Ra的最大值为 6.3μm,Rz的最大值为 100μm
三、表面粗糙度在图样上的标注方法
4.4 表面粗糙度数值的选择
5.要求耐腐蚀的表面,粗糙度值应选小值。 6.有关标准已对表面粗糙度要求作出规定的应按相应标准确定表
面粗糙度数值。
4.5 表面粗糙度的测量
一、比较法:
将被测表面与粗糙度标准样板相比较,通过视觉、触 感或其它方法进行比较后, 对被测表面的粗糙度作出评定的方法。
二、光切法:
利用“光切原理”测量表面粗糙度的方法。光切显微镜又称双管显微镜
表示表面是用去除材料的方法获得。如车、铣、刨、磨、钻、 剪切、抛光、腐蚀、电火花加工、
气割等
表示表面是用不去除材料方法获得。 如铸、锻、冲压变形、热轧、粉末冶金等。或者是用于保持
原供应状况的表面(包括保持上道工序的状况)
表示所有表面具有相 同的表面粗糙度
要求
二、表面粗糙度的标注
a 1、a2——粗糙度参数代号及数值(μm); 如3.2、6.3等 见表5-5
Ra越大,表面越粗糙
2.微观不平度十点高度Rz:
在取样长度l内,被测表面5个最大轮廓峰高的平均值与5个最 大轮廓的谷深的平均值之和。
表面粗糙度与公差等级的关系

加入表面粗糙度是反映零件表面微观几何形状误差的一个重要技术指标,是检验零件表面质量的主要依据;它选择的合理与否,直接关系到产品的质量、使用寿命和生产成本。
机械号件表面粗糙度的选择方法有3种,即计算法、试验法和类比法。
在机械零件设计工作中,应用最普通的是类比法,此法简便、迅速、有效。
应用类比法需要有充足的参考资料,现有的各种机械设计手册中都提供了较全面的资料和文献。
最常用的是与公差等级相适应的表面粗糙度。
在通常情况下,机械零件尺寸公差要求越小,机械零件的表面粗糙度值也越小,但是它们之间又不存在固定的函数关系。
例如一些机器、仪器上的手柄、手轮以及卫生设备、食品机械上的某些机械零件的修饰表面,它们的表面要求加工得很光滑即表面粗糙度要求很高,但其尺寸公差要求却很低。
在一般情况下,有尺寸公差要求的零件,其公差等级与表面粗糙度数值之间还是有一定的对应关系的。
在一些机械零件设计手册和机械制造专著中,对机械零件的表面粗糙度和机械零件的尺寸公差关系的经验及计算公式都有很多介绍,并列表供读者选用,但只要细心阅来,就会发现,虽然采取完全相同的经验计算公式,但所列表中的数值也不尽相同,有的还有很大的差异。
这就给不熟悉这方面情况的人带来了迷惑。
同时也增加了他们在机械零件工作中选择表面粗糙度的困难。
在实际工作中,对于不同类型的机器,其零件在相同尺寸公差的条件下,对表面粗糙度的要求是有差别的。
这就是配合的稳定性问题。
在机械零件的设计和制造过程中,对于不同类型的机器,其零件的配合稳定性和互换性的要求是不同的。
在现有的机械冬件设计手册中,反映的主要有以下3种类型:第1类主要用于精密机械,对配合的稳定性要求很高,要求零件在使用过程中或经多次装配后,其零件的磨损极限不超过零件尺寸公差值的10%,这主要应用在精密仪器、仪表、精密量具的表面、极重要零件的摩擦面,如汽缸的内表面、精密机床的主轴颈、坐标键床的主轴颈等。
第2类主要用于普通的精密机械,对配合的稳定性要求较高,要求零件的磨损极限不超过零件尺寸公差值的25%,要求有很好密合的接触面,其主要应用在如机床、工具、与滚动轴承配合的表面、锥销孔,还有相对运动速度较高的接触面如滑动轴承的配合表面、齿轮的轮齿工作面等。
公差与粗糙度对应关系

公差与粗糙度对应关系一、引言在制造和加工过程中,公差和粗糙度是两个常用的术语。
公差是指零件尺寸允许的偏差范围,而粗糙度则描述了表面的光滑程度。
公差和粗糙度之间存在一定的对应关系,本文将探讨公差与粗糙度之间的关系。
二、公差的定义与应用公差是指在制造和加工过程中,零件尺寸允许的偏差范围。
公差的大小决定了零件的质量,合理的公差设计可以保证零件的互换性和可靠性。
公差通常分为尺寸公差和形位公差两种。
1. 尺寸公差尺寸公差是指零件的长度、直径、厚度等尺寸大小的偏差范围。
常见的尺寸公差包括基本尺寸、上偏差和下偏差。
上偏差表示零件的尺寸允许偏大的范围,下偏差表示零件的尺寸允许偏小的范围。
2. 形位公差形位公差是指零件间的相对位置关系的偏差范围。
常见的形位公差包括平面度、圆度、直线度等。
形位公差的设计可以保证零件的装配精度和工作性能。
三、粗糙度的定义与测量粗糙度是指表面的光滑程度,也称为表面质量。
粗糙度的大小对零件的摩擦、密封、润滑等性能有很大影响。
粗糙度通常使用Ra值来表示,单位为微米(μm)。
粗糙度的测量可以使用表面粗糙度仪来进行。
表面粗糙度仪通过感应表面的微小起伏,将其转化为电信号,并通过测量和分析来得出粗糙度数值。
四、公差与粗糙度的关系公差和粗糙度虽然描述了不同的特性,但它们之间存在一定的关系。
1. 公差对粗糙度的影响公差的大小会直接影响零件的尺寸和形状,从而影响零件表面的光滑程度。
公差较小的零件往往具有较高的表面质量,而公差较大的零件则可能具有较低的表面质量。
2. 粗糙度对公差的影响粗糙度的大小也会对零件的公差设计产生影响。
在设计公差时,需要考虑表面粗糙度的影响,避免表面质量过差导致公差范围无法满足要求。
3. 公差和粗糙度的协调在实际应用中,公差和粗糙度需要相互协调,以保证零件的质量和性能。
合理的公差设计可以控制零件的尺寸和形状,而适当的粗糙度要求可以保证零件的表面质量。
五、公差与粗糙度的优化在实际制造和加工过程中,需要根据具体情况对公差和粗糙度进行优化。
表面粗糙度基础知识
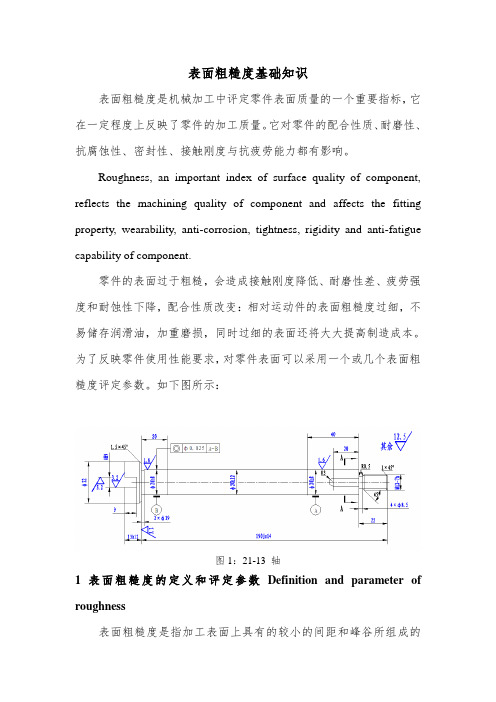
表面粗糙度基础知识表面粗糙度是机械加工中评定零件表面质量的一个重要指标,它在一定程度上反映了零件的加工质量。
它对零件的配合性质、耐磨性、抗腐蚀性、密封性、接触刚度与抗疲劳能力都有影响。
Roughness, an important index of surface quality of component, reflects the machining quality of component and affects the fitting property, wearability, anti-corrosion, tightness, rigidity and anti-fatigue capability of component.零件的表面过于粗糙,会造成接触刚度降低、耐磨性差、疲劳强度和耐蚀性下降,配合性质改变:相对运动件的表面粗糙度过细,不易储存润滑油,加重磨损,同时过细的表面还将大大提高制造成本。
为了反映零件使用性能要求,对零件表面可以采用一个或几个表面粗糙度评定参数。
如下图所示:图1:21-13 轴1 表面粗糙度的定义和评定参数Definition and parameter of roughness表面粗糙度是指加工表面上具有的较小的间距和峰谷所组成的微观几何特性。
一般由所采用的加工方法和其他因素形成。
Caused by machining and other factors.表面粗糙度的评定参数:轮廓算数平均偏差Ra,微观不平度十点高度Rz,轮廓最大高度Ry。
表1:术语与定义Table 1: terms and definitionTerm Definition Diagram Remarks轮廓算数平均偏差Ra 在取样长度内轮廓绝对值的算术平均值Ra=微观不平度十点高度Rz 在取样长度内5个最大的轮廓峰值与5个最小的轮廓谷深的平均值之和Rz=+轮廓最大高度Ry 在取样长度轮廓峰顶线和轮廓谷底线之间的距离2 表面粗糙度的基本符号与含义2.1基本符号basic sign表示表面可用任何方法获得,当不加注粗糙度数值或有关说明(如表面处理、局部热处理)时,仅适用简化代号标注。
公差与粗糙度对应关系

公差与粗糙度对应关系公差和粗糙度是制造工程中两个重要的概念。
公差是指零件尺寸允许的最大偏差范围,而粗糙度则是表面的不光滑程度。
它们之间存在一定的对应关系,本文将就此进行探讨。
公差和粗糙度在制造工程中是必不可少的。
公差是为了保证零件的尺寸精度,在制造过程中会存在一定的误差,而公差的设置可以容许这些误差的存在,确保零件能够正常使用。
而粗糙度则是表面质量的指标,直接影响着零件的摩擦、密封和耐磨性能。
因此,公差和粗糙度的合理设置对于零件的质量和性能至关重要。
公差与粗糙度之间的对应关系主要体现在制造工艺中。
在零件的设计和制造中,需要根据零件的功能和使用要求来确定公差和粗糙度的要求。
一般来说,公差的要求越高,制造工艺的难度越大,对设备和工艺的要求也越高;而对于粗糙度的要求,需要根据零件的表面功能来确定,如需要有良好的密封性能,则需要较低的粗糙度要求。
在实际的制造过程中,公差和粗糙度的对应关系需要综合考虑多个因素。
首先是制造工艺的能力。
如果制造工艺无法满足较高的公差要求,则需要适当调整粗糙度的要求,以确保零件的尺寸精度;反之亦然。
其次是零件的功能和使用要求。
如果零件需要有较高的密封性能,则需要较低的粗糙度要求,以确保表面的平滑度和光洁度;而如果零件的功能主要是传递力或保持定位,则对粗糙度的要求可以适当放宽。
公差和粗糙度的对应关系还需要考虑到成本因素。
公差的要求越高,制造成本也会相应增加,特别是对于精密零件来说;而粗糙度的要求则主要涉及到表面处理和后续加工的成本。
因此,在确定公差和粗糙度的要求时,需要综合考虑制造成本和零件的功能要求,以寻找最佳的平衡点。
总结起来,公差和粗糙度是制造工程中不可分割的两个概念,它们之间存在一定的对应关系。
合理的公差和粗糙度设置能够确保零件的尺寸精度和表面质量,从而保证零件的功能和性能。
在确定公差和粗糙度要求时,需要综合考虑制造工艺的能力、零件的功能和使用要求以及成本因素,以达到最佳的效果。
尺寸公差、形位公差、表面粗糙度三者的关系
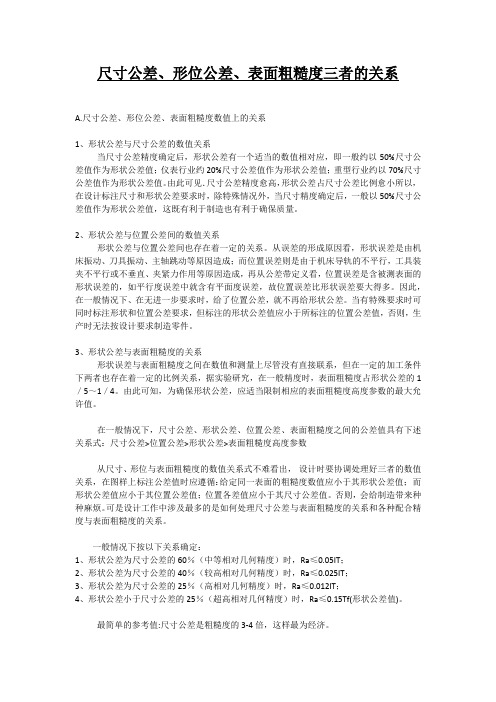
尺寸公差、形位公差、表面粗糙度三者的关系A.尺寸公差、形位公差、表面粗糙度数值上的关系1、形状公差与尺寸公差的数值关系当尺寸公差精度确定后,形状公差有一个适当的数值相对应,即一般约以50%尺寸公差值作为形状公差值;仪表行业约20%尺寸公差值作为形状公差值;重型行业约以70%尺寸公差值作为形状公差值。
由此可见.尺寸公差精度愈高,形状公差占尺寸公差比例愈小所以,在设计标注尺寸和形状公差要求时,除特殊情况外,当尺寸精度确定后,一般以50%尺寸公差值作为形状公差值,这既有利于制造也有利于确保质量。
2、形状公差与位置公差间的数值关系形状公差与位置公差间也存在着一定的关系。
从误差的形成原因看,形状误差是由机床振动、刀具振动、主轴跳动等原因造成;而位置误差则是由于机床导轨的不平行,工具装夹不平行或不垂直、夹紧力作用等原因造成,再从公差带定义看,位置误差是含被测表面的形状误差的,如平行度误差中就含有平面度误差,故位置误差比形状误差要大得多。
因此,在一般情况下、在无进一步要求时,给了位置公差,就不再给形状公差。
当有特殊要求时可同时标注形状和位置公差要求,但标注的形状公差值应小于所标注的位置公差值,否则,生产时无法按设计要求制造零件。
3、形状公差与表面粗糙度的关系形状误差与表面粗糙度之间在数值和测量上尽管没有直接联系,但在一定的加工条件下两者也存在着一定的比例关系,据实验研究,在一般精度时,表面粗糙度占形状公差的1/5~1/4。
由此可知,为确保形状公差,应适当限制相应的表面粗糙度高度参数的最大允许值。
在一般情况下,尺寸公差、形状公差、位置公差、表面粗糙度之间的公差值具有下述关系式:尺寸公差>位置公差>形状公差>表面粗糙度高度参数从尺寸、形位与表面粗糙度的数值关系式不难看出,设计时要协调处理好三者的数值关系,在图样上标注公差值时应遵循:给定同一表面的粗糙度数值应小于其形状公差值;而形状公差值应小于其位置公差值;位置各差值应小于其尺寸公差值。
尺寸公差形位公差、表面粗糙度数值上的关系
尺寸公差、形位公差、表面粗糙度数值上的关系一、尺寸公差、形位公差、表面粗糙度数值上的关系1、形状公差与尺寸公差的数值关系当尺寸公差精度确定后,形状公差有一个适当的数值相对应,即一般约以50%尺寸公差值作为形状公差值;仪表行业约20%尺寸公差值作为形状公差值;重型行业约以70%尺寸公差值作为形状公差值。
由此可见.尺寸公差精度愈高,形状公差占尺寸公差比例愈小所以,在设计标注尺寸和形状公差要求时,除特殊情况外,当尺寸精度确定后,一般以50%尺寸公差值作为形状公差值,这既有利于制造也有利于确保质量。
2、形状公差与位置公差间的数值关系形状公差与位置公差间也存在着一定的关系。
从误差的形成原因看,形状误差是由机床振动、刀具振动、主轴跳动等原因造成;而位置误差则是由于机床导轨的不平行,工具装夹不平行或不垂直、夹紧力作用等原因造成,再从公差带定义看,位置误差是含被测表面的形状误差的,如平行度误差中就含有平面度误差,故位置误差比形状误差要大得多。
因此,在一般情况下、在无进一步要求时,给了位置公差,就不再给形状公差。
当有特殊要求时可同时标注形状和位置公差要求,但标注的形状公差值应小于所标注的位置公差值,否则,生产时无法按设计要求制造零件。
3、形状公差与表面粗糙度的关系形状误差与表面粗糙度之间在数值和测量上尽管没有直接联系,但在一定的加工条件下两者也存在着一定的比例关系,据实验研究,在一般精度时,表面粗糙度占形状公差的1/5~1/4。
由此可知,为确保形状公差,应适当限制相应的表面粗糙度高度参数的最大允许值。
在一般情况下,尺寸公差、形状公差、位置公差、表面粗糙度之间的公差值具有下述关系式:尺寸公差>位置公差>形状公差>表面粗糙度高度参数从尺寸、形位与表面粗糙度的数值关系式不难看出,设计时要协调处理好三者的数值关系,在图样上标注公差值时应遵循:给定同一表面的粗糙度数值应小于其形状公差值;而形状公差值应小于其位置公差值;位置各差值应小于其尺寸公差值。
表面粗糙度和尺寸公差等级IT
表面粗糙度表面粗糙度R a值的应用范围(旧国标)5,R a的最大允许值取6.3。
因此,在不影响原表面粗糙要求的情况下,取该值有利于加工。
2.粗糙度代号H为第2种过渡方式。
它是取新国标中相应最靠近的上一档的第1系列值,如原光洁度5,R a的最大允许值取3.2。
因此,取该值提高了原表面粗糙度的要求和加工的成本。
尺寸公差等级(IT )公差(1)公差基本术语的含义1)基本尺寸;设计时给定的尺寸,称为基本尺寸。
的基本尺寸2)实际尺寸:零件加工后经测量所得到的尺寸,称为实际尺寸。
3)极限尺寸:实际尺寸允许变化的两个界限值称为极限尺寸。
它以基本尺寸确定。
两个极限值中较大的一个称为最大极限尺寸Dmax (或dmax);较小的一个称为极限尺寸Dmin(或dmin)。
)尺寸偏差;某一尺寸减其基本尺寸所得的代数差,称为尺寸偏差,简称偏差。
实际偏差=实际尺寸一基本尺寸最大极限尺寸减其基本尺寸所得的代数差,称为上偏差;最小极限尺寸减其基本尺寸所得的代数差,称为下偏差;上偏差和下偏差统称为极限偏差。
国家标准规定,孔的上偏差代号为ES,轴的上偏差代号为es;孔的下偏差代号为EI,轴的下偏差代号为ei,则:ES =孔的最大极限尺一孔的基本尺寸cs=轴的最大极限尺寸-轴的基本尺寸EI =孔的最小极限尺寸一孔的基本尺寸ei =轴的最小极限尺寸-轴的奥基本尺寸偏差值可以为正、负或零值。
5)尺寸公差,允许尺寸的变动量称为尺寸公差,简称公差。
公差等于最大极限尺寸与最小极限尺寸的代数差的绝对值;或等于上偏差与下偏差代数差的绝对值。
6)零线:图1a 中示意表明了基本尺寸相向、相互配合的孔与轴之间极限尺寸、尺寸偏差与尺寸公差之间的相互关系,为方便起见,在实际讨论的过程中,通常只画出放大了的孔和轴的公差带,称为公差与配合图解,简称公差带图,如阁l- b 所示。
在公差带图中,确定偏差的一条基准线,即零偏差线,就叩零线,通常零线表示基本尺寸。
正偏差位于零线之上。
最新公差等级与粗糙度的关系
公差等级与粗糙度的关系表面粗糙度是反映零件表面微观几何形状误差的一个重要技术指标,是验证零件表面质量的主要依据;它选择的合理与否,直接关系到产品的质量,使用寿命和生产成本。
机械零件表面粗糙度的选择有3种方法,即计算法、试验法和类比法。
在机械零件设计中应用最普遍的是类比法,此方法简单有效。
运用类比法需要有充足的参考资料。
现有的各类机械设计手册中都提供了较全面的资料和文献。
最常用的是与公差等级相适应得表面粗糙度。
通常情况下公差越小,机械零件的表面粗糙度值也越小,但是他们之间不存在固定的函数关系。
一些装饰表面除外。
在实践工作中,对于不同类型的机器,其零件在相同尺寸公差的条件下,对表面粗糙度的要求是有差别的。
这就是配合的稳定性问题。
在机械零件的设计和制造过程中,对于不同类型机器,其零件配合稳定性和互换性的要求是不同的。
在现有的机械零件设计手册中,主要有以下三种类型。
第一类主要用于精密机械,对配合的稳定性要求很高,要求零件在使用过程中和多次装配后,其零件的磨损极限不超过公差值的10%;这主要应用在精密仪器、仪表、精密量具的表面、极其重要零件表面的摩擦面,如气缸的内表面精密机床的主轴颈、坐标镗床的主轴颈等。
第二类主要用于精密机械,对配合的稳定性要求较高,要求零件的磨损极限不超过公差值得25%,要求有很好密和的接触面,其主要应用在机床、工具、与滚动轴承配合的表面、销锥孔,还有相对运动速度较高的接触面如华东轴承的配合面、齿轮的轮齿工作面等。
第三类主要用于通用机械,要求机械零件的磨损极限不超过尺寸公差的50%,没有相对运动的零件接触面,如箱盖、套筒,要求紧贴的表面、键和键槽的工作面;相对运动速度不高的接触面,如支架孔、衬套、带轮轴孔的工作表面、减速器等。
公差等级与表面粗糙度关系对应表格:详见附件表格在机械零件设计中按尺寸公差选择表面粗糙度数值时。
应根据不同类型的机器,选择相应的表值。
仅供设计时参考!仅供学习与交流,如有侵权请联系网站删除谢谢1表1公差等级与表面粗糙度值(用于精密机械)仅供学习与交流,如有侵权请联系网站删除谢谢2表2公差等级与表面粗糙度值(用于普通精密机械)表3公差等级与表面粗糙度值(用于通用机械)管仲列传管仲夷吾者,颍上人也。
尺寸公差与表面粗糙度
05 总结与展望
总结
尺寸公差与表面粗糙度是机械加工中的重要参数,它 们对产品的性能和可靠性有着显著的影响。
随着科技的不断发展,对尺寸公差与表面粗糙度的要 求也越来越高,这需要我们不断探索新的加工方法和
测量技术,以提高产品的质量和性能。
在实际应用中,应综合考虑尺寸公差与表面粗糙度的 关系,以及它们对产品性能的影响,以制定合理的加
工和测量方案。
展望
随着数字化和智能化技术的不断发展,未来的机械加工将更加依赖于先进的测量技术和数据分析方法。
新的加工方法和材料将对尺寸公差与表面粗糙度提出更高的要求,需要我们不断探索和创新,以适应新 的市场需求。
在未来,尺寸公差与表面粗糙度的研究将更加注重跨学科的合作和交流,以推动相关领域的发展和进步。
测量精度
测量精度对结果的影响很大,因此需要选择精度 合适的测量工具和正确的测量方法,以获得准确 的测量结果。
03 尺寸公差与表面粗糙度的 控制方法
加工工艺控制
加工方法选择
根据零件材料、结构、精度要求等选择合适的加工方 法,如车削、铣削、磨削等。
加工余量分配
合理分配各工序的加工余量,确保最终加工尺寸的精 度。
02
表面粗糙度越高,摩擦系数越大,磨损速度越快,从而影响零
件的耐磨性。
表面粗糙度对零件疲劳强度的影响
03
表面粗糙度越高,应力集中越严重,疲劳裂纹容易形成和扩展,
降低零件的疲劳强度。
尺寸公差对表面粗糙度的影响
尺寸公差越小,表面粗糙度越低
在加工过程中,尺寸公差越小,切削深度、进给量等工艺参数越小,从而减小 表面粗糙度。
热处理工艺
控制零件的热处理工艺,以减小变形和组织不均匀性 对尺寸精度的影响。
- 1、下载文档前请自行甄别文档内容的完整性,平台不提供额外的编辑、内容补充、找答案等附加服务。
- 2、"仅部分预览"的文档,不可在线预览部分如存在完整性等问题,可反馈申请退款(可完整预览的文档不适用该条件!)。
- 3、如文档侵犯您的权益,请联系客服反馈,我们会尽快为您处理(人工客服工作时间:9:00-18:30)。
机械零件表面粗糙度的选择
表面粗糙度是反映零件表面微观几何形状误差的一个重要技术指标,是检验零件表面质量的主要依据;它选择的合理与否,直接关系到产品的质量、使用寿命和生产成本。
机械零件表面粗糙度的选择方法有3种,即计算法、试验法和类比法。
在机械零件设计工作中,应用最普通的是类比法,此法简便、迅速、有效。
应用类比法需要有充足的参考资料,现有的各种机械设计手册中都提供了较全面的资料和文献。
最常用的是与公差等级相适应的表面粗糙度。
在通常情况下,机械零件尺寸公差要求越小,机械零件的表面粗糙度值也越小,但是它们之间又不存在固定的函数关系。
例如一些机器、仪器上的手柄、手轮以及卫生设备、食品机械上的某些机械零件的修饰表面,它们的表面要求加工得很光滑即表面粗糙度要求很高,但其尺寸公差要求却很低。
在一般情况下,有尺寸公差要求的零件,其公差等级与表面粗糙度数值之间还是有一定的对应关系的。
在一些机械零件设计手册和机械制造专著中,对机械零件的表面粗糙度和机械零件的尺寸公差关系的经验及计算公式都有很多介绍,并列表供读者选用,但只要细心阅来,就会发现,虽然采取完全相同的经验计算公式,但所列表中的数值也不尽相同,有的还有很大的差异。
这就给不熟悉这方面情况的人带来了迷惑。
同时也增加了他们在机械零件工作中选择表面粗糙度的困难。
在实际工作中,对于不同类型的机器,其零件在相同尺寸公差的条件下,对表面粗糙度的要求是有差别的。
这就是配合的稳定性问题。
在机械零件的设计和制造过程中,对于不同类型的机器,其零件的配合稳定性和互换性的要求是不同的。
在现有的机械零件设计手册中,反映的主要有以下3种类型:
第1类主要用于精密机械,对配合的稳定性要求很高,要求零件在使用过程中或经多次装配后,其零件的磨损极限不超过零件尺寸公差值的10%,这主要应用在精密仪器、仪表、精密量具的表面、极重要零件
的摩擦面,如汽缸的内表面、精密机床的主轴颈、坐标镗床的主轴颈等。
第2类主要用于普通的精密机械,对配合的稳定性要求较高,要求零件的磨损极限不超过零件尺寸公差值的25%,要求有很好密合的接触面,其主要应用在如机床、工具、与滚动轴承配合的表面、锥销孔,还有相对运动速度较高的接触面如滑动轴承的配合表面、齿轮的轮齿工作面等。
第3类主要用于通用机械,要求机械零件的磨损极限不超过尺寸公差值的50%,没有相对运动的零件接触面,如箱盖、套筒,要求紧贴的表面、键和键槽的工作面;相对运动速度不高的接触面,如支架孔、衬套、带轮轴孔的工作表面、减速器等等。
在此我们对机械设计手册中的各类表值进行统计分析,将旧的表面粗糙度国家标准(GB1031—68)转换为参照采用国际标准ISO颁布的1983年的新的国家标准(GB1031—83),采用优先选用的评定参数,即轮廓算术平均偏差值R a=(1)/(l)∫l0|y|dx。
并采用R a优先选用的第一系列数值,推导出表面粗糙度R a与尺寸公差IT之间的有关关系式为
第1类:R a≥1.6R a≤0.008×IT
R a≤0.8R a≤0.010×IT
第2类:R a≥1.6R a≤0.021×IT
R a≤0.8R a≤0.018×IT
第3类:R a≤0.042×IT
将上述3种关系式列表,如表1、表2、表3所示。
表1公差等级与表面粗糙度值(用于精密机械)
表2公差等级与表面粗糙度值(用于普通精密机械)
表3公差等级与表面粗糙度值(用于通用机械)
在机械零件设计工作中,按尺寸公差选择表面粗糙度数值时,应当根据不同类型的机器,选择相应的表值。
需要说明的是,表中R a采用第1系列值,而旧的国标R a的极限值为第2系列值,换算时会遇到数值上靠和下靠的问题。
我们在表中表值采用上靠,因为这有利于提高产品质量,个别值采用下靠。
旧国标的公差等级与表面粗糙度对应的表的内容和形式都比较复杂,对同一公差等级同一尺寸分段同一基本尺寸,孔与轴的表面粗糙度值不相同,不同配合种类数值也不相同,这是由于旧的公差与配合标准(GB159—59)的公差数值与上述因素有关。
现行的新国标公差与配合(GB1800—79)对同一公差等级同一尺寸分段内各基本尺寸的标准公差值是相同的,这样就使公差等级与表面粗糙度的对应表大为简化,也更为科学合理。
在设计工作中,表面粗糙度的选择归根到底还是必须从实际出发,全面衡量零件的表面功能和工艺经济性,才能作出合理的选择。
表中给出的公差等级与表面粗糙度值可供设计时参考。