汽车板的成形性及冲压成形技术
汽车制造工艺冲压工艺
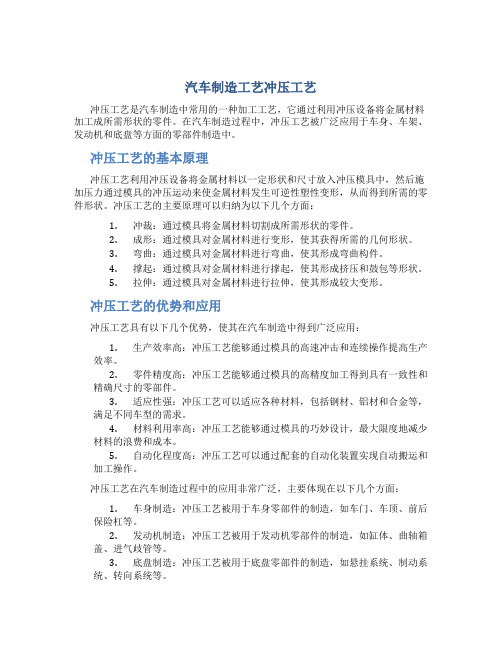
汽车制造工艺冲压工艺冲压工艺是汽车制造中常用的一种加工工艺,它通过利用冲压设备将金属材料加工成所需形状的零件。
在汽车制造过程中,冲压工艺被广泛应用于车身、车架、发动机和底盘等方面的零部件制造中。
冲压工艺的基本原理冲压工艺利用冲压设备将金属材料以一定形状和尺寸放入冲压模具中,然后施加压力通过模具的冲压运动来使金属材料发生可逆性塑性变形,从而得到所需的零件形状。
冲压工艺的主要原理可以归纳为以下几个方面:1.冲裁:通过模具将金属材料切割成所需形状的零件。
2.成形:通过模具对金属材料进行变形,使其获得所需的几何形状。
3.弯曲:通过模具对金属材料进行弯曲,使其形成弯曲构件。
4.撑起:通过模具对金属材料进行撑起,使其形成挤压和鼓包等形状。
5.拉伸:通过模具对金属材料进行拉伸,使其形成较大变形。
冲压工艺的优势和应用冲压工艺具有以下几个优势,使其在汽车制造中得到广泛应用:1.生产效率高:冲压工艺能够通过模具的高速冲击和连续操作提高生产效率。
2.零件精度高:冲压工艺能够通过模具的高精度加工得到具有一致性和精确尺寸的零部件。
3.适应性强:冲压工艺可以适应各种材料,包括钢材、铝材和合金等,满足不同车型的需求。
4.材料利用率高:冲压工艺能够通过模具的巧妙设计,最大限度地减少材料的浪费和成本。
5.自动化程度高:冲压工艺可以通过配套的自动化装置实现自动搬运和加工操作。
冲压工艺在汽车制造过程中的应用非常广泛,主要体现在以下几个方面:1.车身制造:冲压工艺被用于车身零部件的制造,如车门、车顶、前后保险杠等。
2.发动机制造:冲压工艺被用于发动机零部件的制造,如缸体、曲轴箱盖、进气歧管等。
3.底盘制造:冲压工艺被用于底盘零部件的制造,如悬挂系统、制动系统、转向系统等。
4.内饰制造:冲压工艺被用于内饰零部件的制造,如仪表盘、门板、座椅架等。
冲压工艺的发展趋势随着汽车制造技术的不断发展,冲压工艺也在不断创新与改进。
未来冲压工艺的发展主要有以下几个趋势:1.模具技术的创新:通过模具技术的创新,提高冲压工艺的制造精度和生产效率。
Autoform R7汽车热冲压成形的技术解析

Autoform R7热成型
所谓的硼钢,是指汽车上的热成型钢,因为在这种钢材中加入了硼元素,所以又 称作硼钢。是指将钢板经过950°C的高温加热之后一次成形,然后又迅速冷却, 全面提升了钢板强度,经过这样处理的钢材称之为热成型钢。
热成型钢具有极高的材料强度和机械安全性。一般的高强度钢板的抗拉强度在 400-450MPa左右,而热成形钢抗拉强度高达1300-1600 MPa,屈服度达1000Mpa 之上,每平方厘米能承受10吨以上的压力,为普通钢材的3-4倍,其硬度仅次于 陶瓷,但又具有钢材的韧性。把这种材料用在车身上,在车身重量几乎没有太大 变化情况下,承受力提高了30%,使汽车的车身强度更好。
3.转移:
指的是将加热后的钢板从加热炉中取出放进热成形模具中去。在这一道工序中, 必须保证钢板被尽可能快地转移到模具中,一方面是为了防止高温下的钢板氧化, 另一方面是为了确保钢板在成形时仍然处在较高的温度下,以具有良好的塑性。
4.冲压和淬火:
在将钢板放进模具之后,要立即对钢板进行冲压成形,以免温度下降过多影响钢 板的成形性能。成形以后模具要合模保压一段时间,一方面是为了控制零件的形 状,另一方面是利用模具中设置的冷却装置对钢板进行淬火,使零件形成均匀的 马氏体组织,获得良好的尺寸精度和机械性能。研究表明,就目前常用的热冲压 钢材而言,实现奥氏体向马氏体转变的最小冷却速率为27~30℃/s,因此要保证 模具对板料的冷却速度大于此临界值。
热成型软区零件可使需要高强度部位抗拉、屈服强度等机械性能显著提高,达到 可以承受更大的撞击力的效果,同时也可使需要低强度部位拥有较低抗拉、屈服强 度,在碰撞时达到吸能和溃缩的作用,两者方式的结合能够有效地提高汽车的碰 撞安全性能,实现汽车轻量化。实现同一个热成型零件在不同区域有不同的机械性 能,优化零件在整车碰撞试验中的性能表现。
简述冲压弯曲成形的工艺过程及基本特点

1. 设计模具:冲压弯曲成形的第一步是设计模具。
模具根据产品的形状和尺寸要求进行设计,通常包括冲头、模座、导向柱、顶针等部件。
模具的设计要考虑产品的材料特性、成形工艺和使用要求。
2. 材料准备:冲压弯曲成形需要使用金属材料,常见的包括钢板、铝板、铜板等。
在成形之前需要对材料进行切割、整形和表面处理,以保证成形后产品的质量和外观要求。
3. 冲裁:冲裁是冲压成形的第一步,通过模具的冲头和模座对材料进行切割,得到所需的基本形状。
4. 弯曲:在冲裁完成后,需要对材料进行弯曲成形,通过模具的顶针和模具座将材料弯曲成产品需要的形状。
5. 尾料处理:在冲压弯曲成形之后,通常会有一些尾料产生,需要对这些尾料进行处理,包括回收利用和废弃处理等。
6. 检验和调整:需要对冲压弯曲成形的产品进行检验,确保产品的质量和尺寸达到要求。
同时也需要对模具和成形工艺进行调整,以满足产品的生产要求。
1. 高效率:冲压弯曲成形是一种批量生产的工艺,可以快速地完成产品的成形,提高生产效率。
2. 精度高:冲压弯曲成形可以保证产品的尺寸和形状精度,有利于产品的装配和使用。
3. 适用范围广:冲压弯曲成形可以适用于各种金属材料,成形的产品形状也可以多样化,适用范围广泛。
4. 成本低:相比其他成形工艺,冲压弯曲成形的模具制造成本低,适合批量生产和大规模生产。
5. 自动化程度高:冲压弯曲成形可以实现自动化生产,降低劳动强度,提高生产效率和一致性。
6. 适应性强:冲压弯曲成形可以适应各种复杂的产品形状和结构要求,满足不同行业的生产需求。
通过以上内容的介绍,我们可以了解到冲压弯曲成形工艺的基本过程和特点。
这种成形工艺在工业生产中有着广泛的应用,能够满足各种产品的生产需求,并且具有高效率、高精度、低成本和高自动化程度的特点。
随着科技的不断发展,冲压弯曲成形工艺将会在未来的生产中发挥越来越重要的作用。
冲压弯曲成形是金属加工中常用的一种技术,在各行业都有着广泛的应用。
汽车车门外板冲压工艺

汽车车门外板冲压工艺随着汽车工业的迅速发展,汽车车门外板的质量和外观要求越来越高。
而冲压工艺作为汽车车门外板加工的主要方法,对于保证车门质量、提高生产效率和降低成本起着至关重要的作用。
本文将介绍汽车车门外板冲压工艺的整体流程、工艺参数及对车门外板质量的影响。
一、汽车车门外板冲压工艺的整体流程汽车车门外板冲压工艺一般分为以下几个步骤:材料切割、冲孔、弯曲、成形和涂装。
首先,车门外板所需材料经过切割工艺,将大板材切割成适合冲压的小板材。
然后,根据车门外板的设计要求,在小板材上进行冲孔,以便后续的安装和组装。
接下来,利用专用的冲压模具对冲孔后的小板材进行弯曲和成形,使其形状与车门外板设计相符。
最后,经过涂装工艺,将成形后的车门外板进行表面处理,使其具备防腐蚀性和美观性。
二、汽车车门外板冲压工艺的工艺参数1. 冲压力和冲压速度:冲压力和冲压速度是决定冲压质量和效率的关键参数。
冲压力过大会导致小板材变形和裂纹,冲压速度过快会影响冲压精度。
因此,冲压力和冲压速度需要根据车门外板材料的性质和冲压模具的特点进行合理调整。
2. 冲孔模具和弯曲模具:冲孔模具和弯曲模具是冲压工艺中的关键工具。
冲孔模具的设计需要考虑到冲孔位置、孔径和孔距等因素,以确保冲孔的准确性和一致性。
弯曲模具的设计需要考虑到弯曲角度和弯曲半径等因素,以确保车门外板的形状和尺寸符合要求。
3. 材料选择和热处理:汽车车门外板通常使用高强度钢板或铝合金板材。
材料的选择需要综合考虑强度、韧性、成本和可加工性等因素。
同时,通过热处理可以改善材料的机械性能,提高冲压质量和寿命。
三、汽车车门外板冲压工艺对车门外板质量的影响汽车车门外板冲压工艺的参数设置和工艺流程对车门外板的质量有着直接影响。
1. 尺寸精度和表面质量:冲压工艺中的冲压力、冲压速度和模具设计等因素会影响车门外板的尺寸精度和表面质量。
合理控制这些参数可以避免尺寸偏差和表面缺陷,保证车门外板的装配和外观质量。
汽车钢板的性能要求及钢板种类

汽车钢板的性能要求及钢板种类汽车钢板是用于汽车制造的重要材料之一,其性能要求及种类的选择直接关系到汽车的质量和性能。
下面将对汽车钢板的性能要求及种类进行详细阐述。
1.抗拉强度和屈服强度:汽车钢板需要具有较高的抗拉强度和屈服强度,以确保车身在受力时不会发生塑性变形或断裂。
一般来说,汽车零部件使用的钢板抗拉强度要求在350-550MPa之间,屈服强度要求在180-350MPa之间。
2. 冲击韧性:冲击韧性是指钢板在承受冲击荷载时的抗击穿能力,对汽车钢板来说尤为重要。
在碰撞等情况下,钢板需要能够吸收和分散冲击能量,以保护乘客的安全。
常用的冲击测试方法有冲击试验、Charpy V 型缺口冲击试验等。
3.塑性变形能力:汽车钢板需要具有良好的塑性变形能力,以便于制造过程中的冲压和弯曲等成形操作。
钢板的成形性能取决于其材料的塑性能和冲击韧性。
通常情况下,低碳钢板和热轧钢板具有较好的塑性变形能力。
4.良好的焊接性能:由于汽车钢板需要进行焊接连接,因此其焊接性能也是一项重要要求。
钢板的焊接性能包括焊接接头的强度、韧性和抗腐蚀能力等。
一般来说,低碳钢板和低合金钢板具有较好的焊接性能。
5.表面质量:汽车钢板需要具有较好的表面质量,能够满足汽车外观要求以及涂装和防腐等后续加工的需要。
表面质量主要通过表面处理和涂层技术来实现,如电镀、热浸镀锌和涂层等。
根据不同的应用需求,汽车钢板可以分为以下几种主要种类:1.混杂钢板:混杂钢板是由多种不同类型的钢材在热轧过程中层叠压制而成的。
其主要优点是兼具高强度和良好的塑性变形能力,可用于制造高强度的结构和安全零件。
2.常规碳钢:常规碳钢是一种含碳量较低的钢板,具有较好的焊接性能和塑性变形能力。
常用于车身面板、车架和底盘等零部件的制造。
3.热轧高强度钢板:热轧高强度钢板具有较高的抗拉强度和屈服强度,适用于制造要求高强度的零件,如承受较大载荷的结构件。
4.高强度低合金钢板:高强度低合金钢板以合金元素的添加来提高钢板的强度和塑性变形能力。
汽车钣金冲压工艺图文详解

冲压基础工艺培训
1.冷冲压:是指在常温下,利用安装在压力机上的冲模对材料施加压力, 使其产生分离或塑性变形,从而获得所需要零件的一种压力加工方 法
2.冷冲压的特点: 产品尺寸稳定,精度高,重量轻,刚度好,互换性好,高效低耗,
操作简单,易于实现自动化
冲压设备
冲压零件
模具
工艺条件
冲压零件影响因素
冲压基本工序分类
落料
BL
斜楔翻边/冲 CFL/CPI/CT
孔/修边
R
基本模具结构图 G
P
F
C M
E J
B
B
A
A
N
D
HLeabharlann DHNA
双
B
A
动B M
C
K
F
J
E
L
P G
H
J
K
U V
B
N
修翻
R M
Q
L
T
X
P
L
E
C S
G 边边 W 冲整
孔形
E
F
Y
D
A K
H
L
K
单 动
拉延方向的选择 合理的拉延方向应符合以下原则:
1.保证凸模能将工件需拉深的部位在一次拉深中完成,不应有凸 模接触不到的死区(即“倒勾”形)。 2.拉延开始时,凸模与毛坯的接触状态应良好;接触面积应尽 量大而靠近中心;凸模表面同时接触毛坯的点要多而分散,并 尽可能分布均匀,防止毛坯窜动。 3.尽可能减小拉延深度,并使各部位拉延深度趋于均匀。
压料面
B
A
A
B
A
分模线
分模线
B A
修边线
汽车车门内板冲压成形工艺分析

缺陷检测ห้องสมุดไป่ตู้针对常见的冲压成形缺陷,采用特定的检测方法和技术手段,及时发现并处理缺 陷,避免批量质量问题。
质量追溯:建立完善的质量追溯体系,对每个环节进行记录和追踪,确保产品质量可追溯, 便于问题排查和解决。
冲压成形中的应力应变分析:板料在冲压过程中,会发生应力应变,其分布和大小对成形质量 有重要影响。
冲压成形中的缺陷分析:如起皱、开裂、回弹等,与材料性质、模具设计、工艺参数等因素有 关。
材料在冲压过程中的流动与变形规律 材料的应力应变行为 材料屈服准则和本构方程 材料硬化特性对冲压成形的影响
冲压速度:根据 材料厚度和成形 要求选择合适的 冲压速度,以保 证成形质量和效
轻量化材料:如高强度钢、铝合金等,可有效降低车身重量,提高燃油经济性和 动力性能。
新型成形工艺:如热冲压、温冲压等,可提高材料成形极限和零件强度,降低生 产成本。
复合材料:如碳纤维复合材料,具有高强度、轻量化和可设计性等优点,是未来 汽车车门内板冲压成形工艺的重要发展方向。
智能化技术:如人工智能、大数据等,可实现冲压成形工艺的智能化控制和优化, 提高生产效率和产品质量。
模具刚度与强度:确保模具在冲压 过程中具有足够的刚度和强度,避 免变形和损坏。
添加标题
添加标题
添加标题
添加标题
模具结构设计:采用易于加工、装 配和维修的结构,降低制造成本。
模具冷却系统:优化冷却系统设计, 提高冷却效果,减少模具温度波动 和热疲劳损伤。
研发背景:传统冲压成形工艺存在局限性,新型工艺应运而生 主要技术:激光冲压成形、热冲压成形等 应用领域:汽车制造、航空航天等 优势与效果:提高材料利用率、减少生产成本、提高产品性能等
精密汽车冲压知识点总结

精密汽车冲压知识点总结一、汽车冲压工艺概述汽车冲压工艺是指利用模具对金属板材进行变形加工的一种金属加工工艺。
它以金属板材为原材料,通过冲裁、成形、弯曲等方法,将金属板材加工成各种零部件,用于汽车制造中。
冲压工艺在汽车制造中占据着重要地位,因为汽车的外观和结构很大程度上依赖于冲压工艺的精密度和稳定性。
二、汽车冲压工艺的基本原理1. 材料选择:汽车冲压零部件的材料选择对成形质量、成本、耐用性等方面都有重要影响。
一般选用的材料有冷轧板、热轧板、镀锌板、镀铝板等。
2. 模具设计:汽车冲压工艺中,模具的设计直接影响到成形零件的质量和稳定性。
模具设计要考虑材料的性能、成形形状、工艺要求等因素,使得成形后的零件具有精确的尺寸和表面质量。
3. 冲压过程:冲压过程是根据成形部件的形状和要求,通过模具对金属板材进行冲裁、成形、弯曲等加工,最终得到成形的零部件。
4. 附件工艺:在冲压过程中,还需要进行一些附件工艺,例如材料预处理、局部调整形状、表面处理等,以确保最终成形的零部件符合要求。
5. 设备调整:冲压设备的调整包括模具安装、冲床参数设置、润滑系统调整等,以确保工艺稳定性和生产效率。
6. 质量检验:通过严格的质量检验,可以确保冲压零部件达到设计要求,减少因为零部件质量问题导致的废品产生。
三、汽车冲压工艺的关键技术和注意事项1. 材料成形规律:不同的金属材料,在冲压过程中会有不同的成形规律。
例如冷轧板材成形要求严格,成形后的零部件尺寸和形状稳定性高,而热轧板材成形要求相对较低。
2. 模具设计与制造:模具是冲压工艺中最关键的部分,其设计和制造对成形零部件的精度和质量有直接影响,要求模具结构合理,耐磨耐用,且易于更换和调整。
3. 冲压工艺控制:冲压工艺控制是冲压车间生产管理的核心,要求在生产过程中完成对冲压参数的准确定位和控制,以保证冲压零部件的尺寸和形状精度。
4. 设备维护与保养:冲压设备是冲压工艺中的重要组成部分,需要做好设备的定期维护和保养工作,以确保设备稳定性和生产效率。
- 1、下载文档前请自行甄别文档内容的完整性,平台不提供额外的编辑、内容补充、找答案等附加服务。
- 2、"仅部分预览"的文档,不可在线预览部分如存在完整性等问题,可反馈申请退款(可完整预览的文档不适用该条件!)。
- 3、如文档侵犯您的权益,请联系客服反馈,我们会尽快为您处理(人工客服工作时间:9:00-18:30)。
●按强度级别分:有普通强度级和高强度级别;
●按冲压级别分:有商品级(CQ)、普通冲压级(DQ)、 深冲压级(DDQ)和超深冲压级(EDDQ);
●按冲压件的复杂程度分:P级(普通拉延),S级(深
拉延),Z级(最深拉延), F级(复杂冲压), HF级 (很复杂冲压)和ZF级(最复杂冲压)。
板材成形性的基本概念
罩式退火(BA) 连续退火(CA) 低(*) 低(*) 低(* * ) 低(* *)
Al (* * *)
(* * *) (#) >Ar3 (* *) 约70% 20~50 约720 ℃
(#)
低(*) (#) >Ar3 (* *) 约85% 5~20K 约850 ℃
Ti/Nb (* * *)
低(*) (* *) >Ar3或< Ar1 (* *) 高(*) 约90% (#) 约900 ℃
成形性能的内容
薄板成形性能研究方法
基本成形性研究 : 拉伸试验 金相试验、硬度试验 模拟成形性研究 : 杯突试验、拉深试验 扩孔试验、锥杯试验 成形极限研究 : 胀形试验、成形极限图
单向拉伸试验获得的力学性能指标参数
杯突试验方法
拉深试验方法
锥杯试验方法
扩孔试验方法
成型的分类及变形特征
特征材料对冲压缺陷的影响
0.015~0.03
(DDQ、EDDQ) ≤ 0.005
IF钢
(EDDQ、S-EDDQ)≤ 0.003
不同冷轧冲压板的冶金成分 控制范围参考值
钢种
CQ级
C
Si
≤0.0 3 ≤0.0 3 ≤0.0 2
Mn
≤0.2 5 ≤0.2 0 ≤0.1 5
S
≤0.00 8 ≤0.00 8 ≤0.00 8
P
≤0.0 1 ≤0.0 1 ≤0.0 1
汽车板的成形性及冲压 成形技术
主 要 内 容
1 .典型板材成形性能分析
2 .影响板材冲压成形性能因素
3. 高强度钢板在汽车上的应用情况
4 . IF钢镀层钢板
5. 先进加工成形技术在汽车上的应用
1. 典型板材成形性能分析
冲压钢板的分类
●按脱氧方式分:有沸腾钢、镇静钢和半镇静钢; ●按钢种与合金成分分:有低碳钢、低合金高强度钢、加 磷钢、超低碳无间隙原子钢(IF钢)等;
金属薄板的成形性是指板材适应各种成形加工过程的能力, 通常定义为:在给定的加工条件下,板材成首变形而不产生断 裂或失稳的能力。 具有最佳成形性的薄板材应是: (1)均匀应变分布; (2)承受平面内压缩应力而无起皱; (3)可达到较高应变而无颈缩和断裂; (4)承受平面内剪切应力而无断裂; (5)零件由凹模出来后保持其形状; (6)保持表面光洁,减低表面损伤。
低,<600℃(* * *) 高, > 700℃ (* *)
注:(#)基本无影响; (*)有影响 ; (**)重要; (***)很重要
冷轧用低碳、微碳和超低碳钢的C成分要求 钢种:
低碳钢(08Al)
成形性能 级别
(CQ、DQ)
C 含量/%
≤ 0.05
微碳钢ELC(03Al) (DDQ)
超低碳钢ULC
IF钢
100—150 250—300 45—55 1.8—2.8 0.23—0.28
汽车用钢的基本性能是冲压成形性,这三代产
品的进步也集中反映在成形性的提高方面,沸腾钢 只能用于普通冲压件,铝镇静钢则有优良的深冲性 能,无间隙原子钢则具有超深性能。
汽车板的质量要求
• • • • • • 优良的成形性能 良好的抗凹陷能力和足够的结构刚度 良好的焊接性能 优良的表面形貌和光洁度 高的耐蚀性能 良好的板形和板面平直度,严格的尺寸精度和性能 均匀性 • 零件钢板应有吸声减振效果
屈服点
◎
抗拉强度
总伸长率
n
○ ○
r
◎ △
杨氏模量
极限变形能
○ ○
△
◎
注:影响度◎>○>△
●三代冲压用钢板的性能比较
钢种 沸腾钢 屈服 (MPa) 抗拉 (MPa) 延伸 (%) r值 n值 --0.22 --0.22
180—190 290—310 44—48 1.0—1.2
铝镇静钢 160—180 290—300 44—50 1.4—1.8
2、影响板材冲压成形 性能因素
钢中碳含量与r值、延伸率的关系:
低氮控制是保证低碳钢成形性和焊接性能的重要措施
氮含量对碳钢平均 塑性应变比的影响
冲击韧性转变温度随焊接 金属氮含量的变化
低碳冲压铝镇静钢采用成分控制:
• • • • • • • 碳(C):<0.05% (0.03~0.04%) 氮(N):<0.005% 硅(Si):0.015 ~0.025% 锰(Mn):0.15~0.25% 铝(Als):0.03~0.05% 硫(S): <0.015% 磷(P):<0.015%
成形缺陷现象
深冲破裂 拉胀破裂 破裂 翻边破裂 弯曲破裂 起皱(法兰) 面变形 面应变 其它形状不良 角度变化 侧壁翘曲 尺寸精度 扭转 棱线翘曲 形状不良 ◎ ○ ◎ ◎ ◎ ◎ ◎ △ △ △ △ △ △ △ ○ ○ ○ ○ ○ ○ ○ △ △ ○ △ △ △ △ △ △ ○ ○ ○ ○ ○ ○ ○ 起皱(侧壁) ◎ ◎ △ △ △ △ ○ ○ △ △ △ ○ ○ ○ △ ○ ◎ ◎ ○ ◎ ○ ○ 材料特性值 板厚
N
≤0.00 5 ≤0.00 5 ≤0.00 4
TO
≤0.00 3 ≤0.00 3 ≤0.00 3
Als
0.030.05 0.030.05 0.030.05
≤0.0 (Q195,SPHC) 5 DQ级 (SPHD) DDQ级 (SPHE) ≤0.0 4 ≤0.0 3
碳(C)含量对钢板力学性能和成形性能的影响规律:
生产条件对连续退火软钢 薄板成形性能的影响
各工序对低碳铝镇静钢和IF钢性能的影响程度
低碳铝镇静钢 IF钢 BA或CA 低(* * *) (#)
Байду номын сангаас参数
C含量 Mn含量 微合金化元素 (Al、Ti、Nb)含量 板坯再加热温度 热轧规程 终轧温度(FT) 卷取温度(CT) 冷轧压下率 退火加热速度 最高退火温度
各种级别钢板的拉伸性能范围
CQ: Commercial Quality, DQ: Drawing Quality, DDQ: Deep Drawing Quality, EDDQ: Extra Deep Drawing Quality, S-EDDQ: Super EDDQ.
各种级别钢板的延伸率和r值性能范围