供应链设计与管理(第3版)课后答案,选译(最新整理)
供应链管理 第三版 Unit12 习题与答案

Chapter 12Determining Optimal Level of Product AvailabilityTrue/False1. The level of product availability is also referred to as the customer service level.Answer: TrueDifficulty: Easy2. A supply chain can use a high level of product availability to improve itsresponsiveness and attract customers.Answer: TrueDifficulty: Moderate3. A high level of product availability requires less inventory, which will keep costsdown for the supply chain.Answer: FalseDifficulty: Moderate4. A supply chain needs to achieve a balance between the level of availability andthe cost of inventory that maximizes supply chain revenues.Answer: FalseDifficulty: Hard5. Whether the optimal level of availability is high or low depends on where aparticular company believes they can maximize profits.Answer: TrueDifficulty: Moderate6. The cost of overselling is denoted by C o and is the loss incurred by a firm foreach unsold unit at the end of the selling season.Answer: FalseDifficulty: Easy7. The cost of understocking is denoted by C u and is the margin lost by a firm foreach lost sale because there is no inventory on hand.Answer: TrueDifficulty: Moderate8. The cost of underselling is a key factor that influences the optimal level ofproduct availability.Answer: FalseDifficulty: Moderate9. The costs of overstocking and understocking have a direct impact on both theoptimal cycle service level and profitability.Answer: TrueDifficulty: Easy10. As the ratio of the cost of overstocking to the cost of understocking gets smaller,the optimal level of product availability decreases.Answer: FalseDifficulty: Hard11. With reduced demand uncertainty, a supply chain manager can better matchsupply and demand by reducing both overstocking and understocking.Answer: TrueDifficulty: Moderate12. An increase in forecast accuracy increases both the overstocked andunderstocked quantity and decreases a firm’s profits.Answer: FalseDifficulty: Easy13. Supply chain managers are able to increase their forecast accuracy as leadtimes decrease, which allows them to better match supply with demand andincrease supply chain profitability.Answer: TrueDifficulty: Easy14. If quick response allows multiple orders in the season, profits increase and theoverstock quantity increases.Answer: FalseDifficulty: Hard15. Quick response results in the manufacturer making a lower profit in the shortterm if all else is unchanged.Answer: TrueDifficulty: Hard16. There is a cost associated with postponement because the production cost usingpostponement is typically lower than the production cost without it.Answer: FalseDifficulty: Easy17. Postponement is valuable for a firm that sells a large variety of products withdemand that is independent and comparable in size.Answer: TrueDifficulty: Moderate18. Postponement may increase overall profits for a firm if a single productcontributes the majority of the demand because the increased manufacturingexpense due to postponement outweighs the small benefit that aggregationprovides in this case.Answer: FalseDifficulty: Hard19. Tailored postponement allows a firm to increase its profitability by onlypostponing the uncertain part of the demand and producing the predictable partat a lower cost without postponement.Answer: TrueDifficulty: Moderate20. In tailored sourcing,firms use a combination of two supply sources, one focusingon cost and able to handle uncertainty well, and the other focusing on flexibility to handle uncertainty, but at a higher cost.Answer: FalseDifficulty: Moderate21. Tailored sourcing may be volume-based or product-based depending on thesource of uncertainty.Answer: TrueDifficulty: Easy22. In volume-based tailored sourcing, the predictable part of a product’s demand isproduced at a flexible facility, whereas the uncertain portion is produced at anefficient facility.Answer: FalseDifficulty: Moderate23. In product-based tailored sourcing, low-volume products with uncertain demandare obtained from a flexible source, while high-volume products with lessdemand uncertainty are obtained from an efficient source.Answer: TrueDifficulty: Easy24. A contract may contain specifications regarding quantity, price, time, and quality.Answer: TrueDifficulty: Easy25. Double marginalization refers to the fact that the total supply chain is dividedbetween the manufacturer and the retailer.Answer: TrueDifficulty: Moderate26. Manufacturers can use buy-back contracts to increase their own profits as wellas total supply chain profits.Answer: TrueDifficulty: Moderate27. Buybacks encourage retailers to increase the level of product availability.Answer: TrueDifficulty: Easy28. Revenue sharing with a lower wholesale price allows retailers but notmanufacturers to increase their profit.Answer: FalseDifficulty: Moderate29. Revenue sharing encourages retailers to increase the level of product availability.Answer: TrueDifficulty: Easy30. Manufacturers can use contracts with quantity flexibility to increase their ownprofits at the expense of total supply chain profits.Answer: FalseDifficulty: Easy31. With vendor-managed inventory(VMI), the control of the replenishment decisionmoves to the manufacturer instead of the retailer.Answer: TrueDifficulty: Easy32. VMI can allow a manufacturer to increase their profits as well as profits for theentire supply chain by increasing some of the effects of double marginalization.Answer: FalseDifficulty: EasyMultiple Choice1. The level of product availabilitya. is also referred to as the customer service level.b. is an important component of any supply chain’s responsiveness.c. increases revenues for the supply chain by increasing sales.d. All of the above are true.e. Only a and b are true.Answer: eDifficulty: Hard2. A supply chain can use a high level of product availability toa. improve its responsiveness and attract customers.b. reduce costs for the supply chain by reducing inventories.c. increase revenues for the supply chain by increasing sales.d. All of the above are true.e. Only a and c are true.Answer: eDifficulty: Easy3. A high level of product availability requiresa. large inventories and tends to raise costs for the supply chain.b. large inventories and tends to reduce costs for the supply chain.c. small inventories and tends to raise costs for the supply chain.d. small inventories and tends to reduce costs for the supply chain.e. none of the aboveAnswer: aDifficulty: Easy4. A supply chain needs to achieve a balance between the level of availability andthe cost of inventory thata. maximizes supply chain revenues.b. minimizes supply chain costs.c. maximizes supply chain profitability.d. maximizes supply chain availability.e. all of the aboveAnswer: cDifficulty: Moderate5. Whether the optimal level of product availability is high or low depends on wherea particular company believes they cana. minimize cost.b. maximize revenue.c. maximize profits.d. maximize product availability.e. all of the aboveAnswer: cDifficulty: Moderate6. The key factors that influence the optimal level of product availability do notincludea. the cost of overstocking the product.b. the cost of stocking the product.c. the cost of understocking the product.d. All of the above are key factors.e. None of the above are key factors.Answer: bDifficulty: Moderate7. The loss incurred by a firm for each unsold unit at the end of the selling season isa. the cost of overstocking the product.b. the cost of stocking the product.c. the cost of understocking the product.d. the cost of overselling the product.e. the cost of underselling the product.Answer: aDifficulty: Moderate8. The margin lost by a firm for each lost sale because there is no inventory onhand isa. the cost of overstocking the product.b. the cost of stocking the product.c. the cost of understocking the product.d. the cost of overselling the product.e. the cost of underselling the product.Answer: cDifficulty: Moderate9. The margin lost from current as well as future sales if the customer does notreturn should be included ina. the cost of overstocking the product.b. the cost of stocking the product.c. the cost of understocking the product.d. the cost of overselling the product.e. the cost of underselling the product.Answer: cDifficulty: Moderate10. Which of the following is not a situation involving the trade-off between the costof overstocking and the cost of understocking?a. seasonal products where all leftover items must be disposed of at the endof the seasonb. continuously stocked items where demand during stockout is backloggedc. continuously stocked items where demand during stockout is lostd. continuously stocked items where demand during stockout is redirectede. none of the aboveAnswer: dDifficulty: Moderate11. The costs of overstocking and understocking have a direct impact ona. the optimal cycle service level but not profitability.b. profitability but not the optimal cycle service level.c. both the optimal cycle service level and profitability.d. neither the optimal cycle service level or profitability.e. the optimal cycle service level and an indirect impact on profitability.Answer: cDifficulty: Moderate12. Which of the following is not a managerial lever to increase profitability?a. increasing the salvage value of each unitb. decreasing the margin lost from a stockoutc. reducing demand uncertaintyd. reducing the level of product availability below optimale. increasing forecast accuracyAnswer: dDifficulty: Moderate13. Which of the following would be a strategy to increase the salvage value of anunsold product?a. discarding the unused materialb. selling unsold product to an outlet storec. keeping the product in inventory until it sellsd. reduce the level of cycle inventorye. none of the aboveAnswer: bDifficulty: Easy14. Which of the following would be a strategy to decrease the margin lost in astockout?a. arranging for backup sourcingb. discarding the unused materialc. selling unsold product to an outlet stored. reduce the level of cycle inventorye. none of the aboveAnswer: aDifficulty: Moderate15. As the ratio of the cost of overstocking to the cost of understocking gets smaller,a. the optimal level of product availability becomes irrelevant.b. the optimal level of product availability decreases.c. the optimal level of product availability remains stable.d. the optimal level of product availability increases.e. none of the aboveAnswer: dDifficulty: Hard16. Which of the following is not an approach to reduce the uncertainty of demand?a. tailored sourcingb. quick responsec. postponementd. improved forecastinge. decreased marginAnswer: eDifficulty: Moderate17. With reduced demand uncertainty, a supply chain manager cana. increase both overstocking and understocking.b. increase overstocking and reduce understocking.c. reduce overstocking and increase understocking.d. reduce both overstocking and understocking.e. none of the aboveAnswer: dDifficulty: Easy18. A company that uses better market intelligence and collaboration to reducedemand uncertainty is making use ofa. tailored sourcing.b. quick response.c. postponement.d. improved forecasting.e. decreased margin.Answer: dDifficulty: Moderate19. A company that reduces replenishment lead time so that multiple orders may beplaced in the selling season is making use ofa. tailored sourcing.b. quick response.c. postponement.d. improved forecasting.e. decreased margin.Answer: bDifficulty: Moderate20. A company with multiple products, that chooses to delay product differentiationuntil closer to the point of sale, is usinga. tailored sourcing.b. quick response.c. postponement.d. improved forecasting.e. decreased margin.Answer: cDifficulty: Moderate21. A company that uses a more expensive short lead time supplier as a backup fora low cost, long lead time supplier is usinga. tailored sourcing.b. quick response.c. postponement.d. improved forecasting.e. decreased margin.Answer: aDifficulty: Moderate22. An increase in forecast accuracya. decreases both the overstocked and understocked quantity anddecreases a firm’s profits.b. decreases both the overstocked and understocked quantity and increasesa firm’s profits.c. increases both the overstocked and understocked quantity and decreasesa firm’s profits.d. increases both the overstocked and understocked quantity and increasesa firm’s profits.e. none of the aboveAnswer: bDifficulty: Moderate23. Supply chain managers are able toa. increase their forecast accuracy as lead times increase.b. increase their forecast accuracy as lead times decrease.c. decrease their forecast accuracy as lead times decrease.d. decrease their forecast accuracy as lead times increase.e. a product is received into stock at a store.Answer: bDifficulty: Moderate24. As lead times decrease, supply chain managers are able toa. better match supply with demand.b. better match demand with supply.c. increase supply chain cost.d. decrease product availability.e. none of the aboveAnswer: aDifficulty: Moderate25. Which of the following is not a consequence of being able to place a secondorder during the season for a seasonal product?a. The expected total quantity ordered during the season with two orders isless.b. The average overstock to be disposed of at the end of the sales season isless.c. The profits are higher.d. The average inventory level is higher.e. none of the aboveAnswer: dDifficulty: Moderate26. As the total quantity for the season is broken up into multiple smaller orders, thebuyer is better able toa. match supply and demand and increase cost.b. match supply and demand and increase profitability.c. match supply and demand and decrease profitability.d. match supply and demand and decrease product availability.e. none of the aboveAnswer: bDifficulty: Moderate27. If quick response allows multiple orders in the season,a. profits decrease and the overstock quantity decreases.b. profits decrease and the overstock quantity increases.c. profits increase and the overstock quantity decreases.d. profits increase and the overstock quantity increases.e. none of the aboveAnswer: cDifficulty: Moderate28. Quick response is clearly advantageous toa. a distributor in the supply chain.b. a retailer in the supply chain.c. a manufacturer in the supply chain.d. every step in the supply chain.e. none of the aboveAnswer: bDifficulty: Hard29. Quick response results ina. the manufacturer making a lower profit in the long term if all else isunchanged.b. the manufacturer making a lower profit in the short term if all else isunchanged.c. the retailer making a lower profit in the short term if all else is unchanged.d. the distributor making a lower profit in the short term if all else isunchanged.e. none of the aboveAnswer: bDifficulty: Moderate30. There is a cost associated with postponement because the production cost usingpostponement is typicallya. higher than the production cost without it.b. lower than the production cost without it.c. very stable.d. equal to the production cost without it.e. none of the aboveAnswer: aDifficulty: Easy31. Postponement is valuable for a firm thata. sells a large variety of products with demand that is dependent andcomparable in size.b. sells a large variety of products with demand that is independent andcomparable in size.c. sells a small variety of products with demand that is dependent andcomparable in size.d. sells a small variety of products with demand that is independent andcomparable in size.e. focuses on processes that are internal to the firm.Answer: bDifficulty: Hard32. Postponement isa. not very effective if a large fraction of demand comes from multipleproducts.b. not very effective if a small fraction of demand comes from a singleproduct.c. only effective if a large fraction of demand comes from a single product.d. effective even if a large fraction of demand comes from a single product.e. none of the aboveAnswer: bDifficulty: Hard33. When a firm uses production with postponement to satisfy a part of its demandwith the rest being satisfied without postponement, it is usinga. adjustable postponement.b. flexible postponement.c. managed postponement.d. tailored postponement.e. none of the aboveAnswer: dDifficulty: Moderate34. Under tailored postponement, a firm produces the amount that is very likely tosell usinga. the lower cost production method with postponement and produces theportion of demand that is uncertain using postponement.b. the lower cost production method without postponement and producesthe portion of demand that is uncertain using postponement.c. the higher cost production method with postponement and produces theportion of demand that is uncertain using postponement.d. the higher cost production method without postponement and producesthe portion of demand that is uncertain using postponement.e. All of the above are accurate.Answer: bDifficulty: Moderate35. In tailored sourcing,firms use a combination of two supply sources,a. one focusing on cost but unable to handle uncertainty well, and the otherfocusing on flexibility to handle uncertainty, but at a higher cost.b. one focusing on cost and able to handle uncertainty well, and the otherfocusing on flexibility to handle uncertainty, but at a higher cost.c. one focusing on cost but unable to handle uncertainty well, and the otherfocusing on flexibility to handle uncertainty at a lower cost.d. one focusing on cost and able to handle uncertainty well, and the otherfocusing on flexibility to handle uncertainty at a lower cost.e. None of the above are accurate.Answer: aDifficulty: Hard36. In volume-based tailored sourcinga. the predictable part of a product’s demand is produced at an efficientfacility.b. the uncertain portion is produced at a flexible facility.c. the predictable part of a product’s demand is produced at a flexible facility.d. all of the abovee. a and b onlyAnswer: eDifficulty: Moderate37. In product-based tailored sourcinga. low-volume products with uncertain demand are obtained from a flexiblesource.b. high-volume products with less demand uncertainty are obtained from anefficient source.c. high-volume products with less demand uncertainty are obtained from aflexible source.d. all of the abovee. a and b onlyAnswer: eDifficulty: Moderate38. A contracta. specifies the parameters within which a buyer places orders and asupplier fulfills them.b. may contain specifications regarding quantity, price, time, and quality.c. may require the buyer to specify the precise quantity required, with a verylong lead time.d. all of the abovee. a and c onlyAnswer: dDifficulty: Moderate39. Double marginalization refers to the fact that the total supply chain margin isdivided betweena. the customer and the retailer.b. the distributor and the retailer.c. the manufacturer and the retailer.d. the manufacturer and the customer.e. none of the aboveAnswer: cDifficulty: Moderate40. Each member of the supply chain makes decisions consideringa. only a portion of the total supply chain margin.b. the total supply chain margin.c. other members of the supply chain.d. customers of the supply chain.e. none of the aboveAnswer: aDifficulty: Moderate41. Buy-backs encourage retailers toa. decrease the level of product availability.b. increase the level of product availability.c. decrease the level of profitability.d. increase the level of cost.e. none of the aboveAnswer: bDifficulty: Hard42. The impact of holding cost subsidies on manufacturer and supply chain profits isa. the opposite of buy-back contracts.b. negligible.c. very much like buy-back contracts.d. a decrease the level of profitability.e. none of the aboveAnswer: cDifficulty: Moderate43. When the manufacturer charges the retailer a low wholesale price and shares afraction of the revenue generated by the retailer, it is referred to asa. double marginalization.b. buy-backs.c. holding cost subsidies.d. revenue-sharing.e. none of the aboveAnswer: dDifficulty: Easy44. Revenue sharing with a lower wholesale price allowsa. only manufacturers to increase their profit.b. only retailers to increase their profit.c. both retailers and manufacturers to increase their profit.d. neither retailers or manufacturers to increase their profit.e. none of the aboveAnswer: cDifficulty: Moderate45. With vendor-managed inventory(VMI),a. the customer is responsible for all decisions regarding product inventoriesat the retailer.b. the retailer is responsible for all decisions regarding product inventories atthe manufacturer.c. the manufacturer or supplier is responsible for all decisions regardingproduct inventories at the retailer.d. the customer is responsible for all decisions regarding product inventoriesat the manufacturer.e. none of the aboveAnswer: cDifficulty: ModerateEssay/Problems1. Explain the relationship between product availability and supply chain profitability.Answer: The level of product availability is measured using the cycle service level or the fill rate, which are metrics for the amount of customer demand satisfiedfrom available inventory. The level of product availability is also referred to as the customer service level. The level of product availability is an importantcomponent of any supply chain’s responsiveness. A supply chain can use a highlevel of product availability to improve its responsiveness and attract customers.This increases revenues for the supply chain by increasing sales through highproduct availability when customers come to make a purchase. However, a highlevel of product availability requires large inventories, and large inventories tendto raise costs for the supply chain. Therefore, a supply chain needs to achieve abalance between the level of availability and the cost of inventory. This optimallevel of product availability is one that maximizes supply chain profitability.Whether the optimal level of availability is high or low depends on where aparticular company believes they can maximize profits.Difficulty: Moderate2. Describe the two key factors that influence the optimal level of product availabilitywithin a supply chain.Answer: The two key factors that influence the optimal level of product availability are:• Cost of overstocking the product• Cost of understocking the productThe cost of overstocking is denoted by C o and is the loss incurred by a firm foreach unsold unit at the end of the selling season. The cost of understocking isdenoted by C u and is the margin lost by a firm for each lost sale because there is no inventory on hand. The cost of understocking should include the margin lostfrom current as well as future sales if the customer does not return. The costs of overstocking and understocking have a direct impact on both the optimal cycleservice level and profitability.Difficulty: Easy3. Decribe managerial levers to increase profitability within a supply chain.Answer: Three managerial levers to increase profitability are:1. Increasing the salvage value of each unit increases profitability (as wellas the optimal cycle service level).2. Decreasing the margin lost from a stockout increases profitability.3. Reducing demand uncertainty.One strategy to increase the salvage value of an unsold product would be selling unsold product to an outlet store.Strategies to decrease the margin lost in a stockout include arranging for backup sourcing (that may be more expensive) so customers are not lost forever andpurchasing product from a competitor on the open market.As the ratio of the cost of overstocking to the cost of understocking gets smaller, the optimal level of product availability increases. This fact explains thedifference in the level of product availability between a high-end store and adiscount store. The high-end store has higher margins and thus a higher cost ofunderstocking. It should thus provide a higher level of product availability than adiscount store with lower margins, and as a result, a lower cost of stocking out.The reduction of demand uncertainty is a significant managerial lever to improve supply chain profitability. With reduced demand uncertainty, a supply chainmanager can better match supply and demand by reducing both overstockingand understocking. A manager can reduce demand uncertainty via the following means:1. Improved forecasting:Use better market intelligence and collaborationto reduce demand uncertainty.2. Quick response: Reduce replenishment lead time so that multipleorders may be placed in the selling season.3. Postponement:In a multiproduct setting, postpone productdifferentiation until closer to the point of sale.4. Tailored sourcing:Use a more expensive short lead time supplier as abackup for a low cost, long lead time supplier.Difficulty: Moderate4. Describe the approaches a manager can use to reduce demand uncertainty.Answer: An increase in forecast accuracy decreases both the overstocked and understocked quantity and increases a firm’s profits.Quick response is the set of actions a supply chain takes that lead to areduction in the replenishment lead time. Supply chain managers are able toincrease their forecast accuracy as lead times decrease, which allows them tobetter match supply with demand and increase supply chain profitability. If quick response allows multiple orders in the season, profits increase and the overstock quantity decreases.Postponement allows a firm to increase profits and better match supply anddemand if the firm produces a large variety of products whose demand is notpositively correlated and is of about the same size. There is a cost associatedwith postponement because the production cost using postponement is typically higher than the production cost without it.In tailored sourcing,firms use a combination of two supply sources, onefocusing on cost but unable to handle uncertainty well, and the other focusing on flexibility to handle uncertainty, but at a higher cost. For tailored sourcing to beeffective, having supply sources where one serves as the backup to the other is not sufficient.Difficulty: Moderate5. Discuss the advantages and disadvantages of quick response.Answer: There are three important consequences of being able to place asecond order in the season.1. The expected total quantity ordered during the season with two ordersis less than that with a single order for the same cycle service level. Inother words, it is possible to provide the same level of product availabilityto the customer with less inventory if a second follow-up order is allowedin the sales season.2. The average overstock to be disposed of at the end of the salesseason is less if two orders are allowed.3. The profits are higher when a second order is allowed during the salesseason.In other words, as the total quantity for the season is broken up into multiplesmaller orders, the buyer is better able to match supply and demand andincrease profitability. If quick response allows multiple orders in the season,profits increase and the overstock quantity decreases.Quick response is clearly advantageous to a retailer in the supply chain,one caveat. As the manufacturer reduces replenishment lead times, allowing fora second order, we have seen that the retailer’s order size drops. In effect, themanufacturer sells less to the retailer. Thus, quick response results in themanufacturer making a lower profit in the short term if all else is unchanged. This is an important point to consider, because decreasing replenishment lead timesrequires tremendous effort from the manufacturer, yet seems to benefit theretailer at the expense of the manufacturer. The benefits resulting from quickresponse should be shared appropriately across the supply chain.Difficulty: Hard6. Explain how tailored postponement can improve profitability.。
供应链管理-第三版-Unit3-习题与答案

Chapter 3Supply Chain Drivers and ObstaclesTrue/False1. The major drivers of supply chain performance are facilities, inventory,transportation, and information.Answer: TrueDifficulty: Moderate2. The major drivers of supply chain performance are customers, facilities,inventory, transportation, and information.Answer: FalseDifficulty: Moderate3. The two major types of facilities are production sites and storage sites.Answer: TrueDifficulty: Moderate4. The two major types of facilities are distribution sites and storagesites.Answer: FalseDifficulty: Moderate5. Inventory is an important supply chain driver because changing inventorypolicies can dramatically alter the supply chain’s efficiency andresponsiveness.Answer: TrueDifficulty: Moderate6. Information is potentially the biggest driver of performance in thesupply chain as it directly affects each of the other drivers.Answer: TrueDifficulty: Easy7. Information is potentially the biggest driver of performance in thesupply chain even though it has little impact on each of the otherdrivers.Answer: FalseDifficulty: Easy8. A facility with little excess capacity will likely be more efficient perunit of product it produces than one with a lot of unused capacity.Answer: TrueDifficulty: Easy9. A facility with little excess capacity will likely be no more or lessefficient per unit of product it produces than one with a lot of unused capacity.Answer: FalseDifficulty: Easy10. The high utilization facility will have difficulty responding to demandfluctuations.Answer: TrueDifficulty: Easy11. The high utilization facility will have no more difficulty responding todemand fluctuations than one with a lot of unused capacity.Answer: FalseDifficulty: Easy12. Stock keeping unit (SKU) storage is the warehousing methodology thatuses a traditional warehouse to store all of one type of producttogether.Answer: TrueDifficulty: Moderate13. Warehouse unit storage is the warehousing methodology that uses atraditional warehouse to store all of one type of product together.Answer: FalseDifficulty: Moderate14. The components of inventory decisions include cycle inventory, safetyinventory, seasonal inventory, and sourcing.Answer: TrueDifficulty: Easy15. The components of inventory decisions include capacity, cycle inventory,safety inventory, seasonal inventory, and sourcing.Answer: FalseDifficulty: Easy16. Cycle inventory is inventory that is built up to counter predictablevariability in demand.Answer: FalseDifficulty: Easy17. Seasonal inventory is inventory that is built up to counter predictablevariability in demand.Answer: TrueDifficulty: Moderate18. Companies using seasonal inventory will build up inventory in periods oflow demand and store it for periods of high demand when they will nothave the capacity to produce all that is demanded.Answer: TrueDifficulty: Moderate19. Companies using seasonal inventory will maintain a level inventoryincrease rate of production for periods of high demand.Answer: FalseDifficulty: Easy20. A company’s ability to find a balance b etween responsiveness andefficiency that best matches the needs of the customer it is targetingis the key to achieving strategic fit.Answer: TrueDifficulty: Moderate21. Many obstacles, such as growing product variety and shorter life cycles,have made it increasingly difficult for supply chains to achievestrategic fit.Answer: TrueDifficulty: ModerateMultiple Choice1. Which of the following is not a major driver of supply chain performance?a. Facilitiesb. Inventoryc. Transportationd. Informatione. All of the above are major drivers of supply chain performance.Answer: eDifficulty: Easy2. Which of the following is not a major driver of supply chain performance?a. Customersb. Facilitiesc. Inventoryd. Transportatione. InformationAnswer: aDifficulty: Moderate3. The places in the supply chain network where product is stored, assembled,or fabricated are known asa. facilities.b. inventory.c. transportation.d. information.e. customers.Answer: aDifficulty: Easy4. All raw materials, work in process, and finished goods within a supplychain are known asa. facilities.b. inventory.c. transportation.d. information.e. customers.Answer: bDifficulty: Easy5. Moving inventory from point to point in the supply is known asa. facilities.b. inventory.c. transportation.d. information.e. customers.Answer: cDifficulty: Easy6. The data and analysis concerning facilities, inventory, transportation, andcustomers throughout the supply chain is known asa. facilities.b. inventory.c. transportation.d. information.e. customers.Answer: dDifficulty: Easy7. The two major types of facilities area. distribution sites and storage sites.b. production sites and distribution sites.c. production sites and storage sites.d. retail sites and distribution sites.e. distribution sites and inventory sites.Answer: cDifficulty: Moderate8. Which component of the supply chain decision-making framework would beestablished first?a. Customer strategyb. Supply chain strategyc. Supply chain structured. Competitive strategye. Replenishment strategyAnswer: dDifficulty: Moderate9. Which component of the supply chain decision-making framework would beestablished second?a. Customer strategyb. Supply chain strategyc. Supply chain structured. Competitive strategye. Replenishment strategyAnswer: bDifficulty: Moderate10. Which component of the supply chain decision-making framework would be usedto reach the performance level dictated by the supply chain strategy?a. Customer strategyb. Supply chain strategyc. Supply chain structured. Competitive strategye. Replenishment strategyAnswer: cDifficulty: Easy11. Which of the following is not a component of facilities decisions?a. Locationb. Capacityc. Operations methodologyd. Warehousing methodologye. All of the above are components of facilities decisions.Answer: eDifficulty: Moderate12. Which of the following is not a component of facilities decisions?a. Warehousing methodologyb. Forecasting methodologyc. Operations methodologyd. Capacitye. LocationAnswer: bDifficulty: Moderate13. Which of the following statements concerning decisions regarding locationof facilities is false?a. Deciding where a company will locate its facilities constitutes alarge part of the design of a supply chain.b. A basic trade-off here is whether to centralize to gain economiesof scale or decentralize to become more responsive by beingcloser to the customer.c. Companies must also consider a host of issues related to thevarious characteristics of the local area in which the facilitymay be situated.d. All of these statements are true.e. None of these statements are true.Answer: dDifficulty: Moderate14. Which of the following is not an issue companies need to consider infacility location decisions?a. quality of workersb. product developmentc. proximity to customers and the rest of the networkd. cost of facilitye. tax effectsAnswer: bDifficulty: Moderate15. Which of the following is not an issue companies need to consider infacility location decisions?a. quality of workersb. availability of infrastructurec. proximity to customers and the rest of the networkd. cost of facilitye. All of the above are issues companies need to consider in facilitylocation decisions.Answer: eDifficulty: Moderate16. Excess capacitya. allows a facility to be very flexible and to respond to wideswings in the demands placed on it.b. costs money and therefore can decrease efficiency.c. requires proximity to customers and the rest of the network.d. both a and be. all of the aboveAnswer: dDifficulty: Moderate17. Which of the following is a characteristic of a facility with excesscapacity?a. will likely be more efficient per unit of product it producesthan one with a lot of unused capacityb. would be very flexible and to respond to wide swings in thedemands placed on itc. would be considered a high utilization facilityd. will have difficulty responding to demand fluctuationse. none of the aboveAnswer: aDifficulty: Easy18. A facility with little excess capacitya. will likely be more efficient per unit of product it producesthan one with a lot of unused capacity.b. would be considered a high utilization facility.c. will have difficulty responding to demand fluctuations.d. All of the above are true.e. None of the above are true.Answer: dDifficulty: Moderate19. Which of the following would be a characteristic of a facility with littleexcess capacity?a. allows a facility to be very flexible and to respond to wide swingsin the demands placed on itb. costs money and therefore can decrease efficiencyc. requires proximity to customers and the rest of the networkd. will likely be more efficient per unit of product it producese. none of the aboveAnswer: dDifficulty: Moderate20. Which of the following is not a warehousing methodology?a. Warehouse unit storageb. Stock keeping unit (SKU) storagec. Job lot storaged. Cross-dockinge. All of the above are warehousing methodologies.Answer: aDifficulty: Moderate21. The warehousing methodology that uses a traditional warehouse to store allof one type of product together isa. warehouse unit storage.b. stock keeping unit (SKU) storage.c. job lot storage.d. cross-docking.e. none of the aboveAnswer: bDifficulty: Moderate22. The warehousing methodology in which all the different types of productsneeded to perform a particular job or satisfy a particular type of customer are stored together isa. warehouse unit storage.b. stock keeping unit (SKU) storage.c. job lot storage.d. cross-docking.e. none of the aboveAnswer: cDifficulty: Moderate23. The following warehousing methodology is one in which goods are notactually warehoused in a facility. Instead, trucks from suppliers, each carrying a different type of product, deliver goods to a facility. There the inventory is broken into smaller lots and quickly loaded onto store-bound trucks that carry a variety of products, some from each of thesupplier trucks.a. warehouse unit storageb. stock keeping unit (SKU) storagec. job lot storaged. cross-dockinge. none of the aboveAnswer: dDifficulty: Moderate24. All of the following are components of inventory decisions excepta. cycle inventory.b. safety inventory.c. seasonal inventory.d. sourcing.e. All of the above are components of inventory decisions.Answer: eDifficulty: Easy25. All of the following are components of inventory decisions excepta. capacity.b. cycle inventory.c. safety inventory.d. seasonal inventory.e. sourcing.Answer: aDifficulty: Easy26. The average amount of inventory used to satisfy demand between receipt ofsupplier shipments is referred to asa. cycle inventory.b. safety inventory.c. seasonal inventory.d. sourcing.e. none of the aboveAnswer: aDifficulty: Moderate27. The inventory that is built up to counter predictable variability in demandis calleda. cycle inventory.b. safety inventory.c. seasonal inventory.d. sourcing.e. none of the aboveAnswer: cDifficulty: Moderate28. The inventory held in case demand exceeds expectation in order to counteruncertainty is calleda. cycle inventory.b. safety inventory.c. seasonal inventory.d. sourcing.e. none of the aboveAnswer: bDifficulty: Moderate29. The set of business processes required to purchase goods and services isknown asa. cycle inventory.b. safety inventory.c. seasonal inventory.d. sourcing.e. none of the aboveAnswer: dDifficulty: Easy30. Cycle inventory decisions involvea. how much to order for replenishment.b. how often to place orders.c. a basic trade-off between the cost of holding larger lots ofinventory and the cost of ordering product frequently.d. all of the abovee. a and b onlyAnswer: dDifficulty: Moderate31. Cycle inventory is used becausea. the world is perfectly predictable.b. demand is uncertain and may exceed expectations.c. it involves making a trade-off between the costs of having toomuch inventory and the costs of losing sales due to not havingenough inventory.d. it focuses on processes that are external to the firm.e. it focuses on processes that are internal to the firm.Answer: bDifficulty: Moderate32. Seasonal inventory should be used whena. a company can rapidly change the rate of its production system ata very low cost.b. changing the rate of production is expensive (e.g., when workersmust be hired or fired).c. adjusting to a period of low demand without incurring large costs.d. the world is perfectly predictable.e. production rate is flexible.Answer: aDifficulty: Hard33. Sourcing involvesa. deciding the tasks that will be outsourced and those that will beper-formed within the firm.b. deciding whether to source from a single supplier or a portfolioof suppliers.c. identifying the set of criterion that will be used to selectsuppliers and measure their performance.d. selecting suppliers and negotiating contracts with them.e. all of the aboveAnswer: eDifficulty: Easy34. Which of the following are key components of transportation decisions whendesigning and operating a supply chain?a. Mode of transportationb. Route and network selectionc. In-house or outsourced. all of the abovee. none of the aboveAnswer: dDifficulty: Moderate35. Which of the following are key components of transportation decisions whendesigning and operating a supply chain?a. Software selectionb. Mode of transportationc. Source selectiond. Warehouse selectione. none of the aboveAnswer: bDifficulty: Easy36. Which of the following are key components of information that must beanalyzed to increase efficiency and improve effectiveness in a supply chain?a. Push versus pullb. Coordination and information sharingc. Forecasting and aggregate planningd. Pricing and revenue managemente. all of the aboveAnswer: eDifficulty: Moderate37. Which of the following are key components of information that must beanalyzed to increase efficiency and improve effectiveness in a supply chain?a. Software selectionb. Source selectionc. Warehouse selectiond. Forecasting and aggregate planninge. none of the aboveAnswer: dDifficulty: Moderate38. When all the different stages of a supply chain work toward the objectiveof maximizing total supply chain profitability, rather than each stagedevoting itself to its own profitability without considering total supply chain profit, it is known asa. supply chain coordination.b. forecasting.c. aggregate planning.d. revenue management.e. pricing.Answer: aDifficulty: Easy39. The art and science of making projections about what future demand andconditions will be isa. supply chain coordination.b. forecasting.c. aggregate planning.d. revenue management.e. pricing.Answer: bDifficulty: Easy40. Transforming forecasts into plans of activity to satisfy the projecteddemand is known asa. supply chain coordination.b. forecasting.c. aggregate planning.d. revenue management.e. pricing.Answer: cDifficulty: Easy41. The process by which a firm decides how much to charge customers for itsgoods and services isa. supply chain coordination.b. forecasting.c. aggregate planning.d. revenue management.e. pricing.Answer: eDifficulty: Easy42. The use of differential pricing over time or customer segments to maximizeprofits from a limited set of supply chain assets isa. supply chain coordination.b. forecasting.c. aggregate planning.d. revenue management.e. pricing.Answer: dDifficulty: Moderate43. Which of the following are technologies that share and analyze informationin the supply chain?a. Electronic Data Interchange (EDI)b. Internetc. Enterprise Resource Planning (ERP)d. Supply Chain Management (SCM) softwaree. all of the aboveAnswer: eDifficulty: Easy44. Which of the following are technologies that share and analyze informationin the supply chain?a. Internetb. Enterprise Data Planning (EDP)c. Electronic Resource Interchange (ERI)d. Chain Management (CM) softwaree. none of the aboveAnswer: aDifficulty: Moderate45. Which of the following are obstacles to achieving strategic fit?a. Increasing variety of productsb. Decreasing product lifecyclesc. Increasingly demanding customersd. Fragmentation of supply chain ownershipe. all of the aboveAnswer: eDifficulty: Easy46. Which of the following are obstacles to achieving strategic fit?a. Difficulty executing new strategiesb. Globalizationc. Increasingly demanding customersd. Fragmentation of supply chain ownershipe. all of the aboveAnswer: eDifficulty: Moderate47. Which of the following is not an obstacle to achieving strategic fit?a. Increasing variety of productsb. Decreasing product lifecyclesc. Increasingly demanding customersd. Consolidation of supply chain ownershipe. none of the aboveAnswer: dDifficulty: ModerateEssay/Problems1. List and define the four major drivers of supply chain performance.Answer: Facilities are the places in the supply chain network whereproduct is stored, assembled, or fabricated. The two major types offacilities are production sites and storage sites.Inventory is all raw materials, work in process, and finished goodswithin a supply chain. Inventory is an important supply chain driverbecause changing inventory policies can dramatically alter the supply chain’s efficiency and responsiveness.Transportation entails moving inventory from point to point in thesupply chain. Transportation can take the form of many combinations of modes and routes.Information consists of data and analysis concerning facilities,inventory, transportation, and customers throughout the supply chain.Information is potentially the biggest driver of performance in thesupply chain as it directly affects each of the other drivers.Difficulty: Moderate2. Explain the supply chain decision-making framework and the role of thefour major drivers.Answer: The goal of a supply chain strategy is to strike the balancebetween responsiveness and efficiency, resulting in a strategic fit with the competitive strategy. To reach this goal, a company uses the foursupply chain drivers discussed earlier. For each of the individualdrivers, supply chain managers must make a trade-off between efficiency and responsiveness. The combined impact of these four drivers thendetermines the responsiveness and efficiency of the entire supply chain.Most companies begin with a competitive strategy and then decide whattheir supply chain strategy ought to be. The supply chain strategydetermines how the supply chain should perform with respect toefficiency and responsiveness. The supply chain must then use the supply chain drivers to reach the performance level the supply chain strategydictates.Difficulty: Moderate3. Explain the basic trade-off between responsiveness and efficiency foreach of the major drivers of supply chain performance.Answer: The fundamental trade-off when making facilities decisions isbetween the cost of the number, location, and type of facilities(efficiency) and the level of responsiveness that these facilitiesprovide the company’s customers.The fundamental trade-off when making inventory decisions is betweenresponsiveness and efficiency. Increasing inventory will generally make the supply chain more responsive to the customer. This choice, however, comes at a cost as the added inventory decreases efficiency. Therefore,a supply chain manager can use inventory as one of the drivers forreaching the level of responsiveness and efficiency the competitivestrategy targets.The fundamental trade-off for transportation is between the cost oftransporting a given product (efficiency) and the speed with which that product is transported (responsiveness). The transportation choiceinfluences other drivers such as inventory and facilities. When supplychain managers think about making transportation decisions, they framethe decision in terms of this trade-off.Good information systems can help a firm improve both its responsiveness and efficiency. The information driver is used to improve theperformance of other drivers and the use of information is based on the strategic position the other drivers support. Accurate information canhelp a firm improve efficiency by decreasing inventory andtransportation costs. Accurate information can improve responsiveness by helping a supply chain better match supply and demand.Difficulty: Moderate4. Explain the role of each of the major drivers of supply chainperformance.Answer: Facilities are the where of the supply chain if we think ofinventory as what is being passed along the supply chain andtransportation as how it is passed along. They are the locations to orfrom which the inventory is transported. Within a facility, inventory is either processed or transformed into another state (manufacturing) or it is stored before being shipped to the next stage (warehousing).Inventory exists in the supply chain because of a mismatch betweensupply and demand. An important role that inventory plays in the supplychain is to increase the amount of demand that can be satisfied byhaving product ready and available when the customer wants it. Anothersignificant role inventory plays is to reduce cost by exploiting anyeconomies of scale that may exist during both production anddistribution. Inventory is spread throughout the supply chain from rawmaterials to work in process to finished goods that suppliers,manufacturers, distributors, and retailers hold.Inventory is a major source of cost in a supply chain and it has a hugeimpact on responsiveness. The location and quantity of inventory canmove the supply chain from one end of the responsiveness spectrum to the other.Inventory also has a significant impact on the material flow time in asupply chain. Material flow time is the time that elapses between thepoint at which Another important area where inventory has a significantimpact is throughput.Inventory and flow time are synonymous in a supply chain. Managersshould use actions that lower the amount of inventory needed withoutincreasing cost or reducing responsiveness, because reduced flow timecan be a significant advantage in a supply chain.Transportation moves product between different stages in a supply chain.Like the other supply chain drivers, transportation has a large impacton both responsiveness and efficiency. Faster transportation, whether in the form of different modes of transportation or different amounts being transported, allows a supply chain to be more responsive but reduces its efficiency. The type of transportation a company uses also affects theinventory and facility locations in the supply chain.Information could be overlooked as a major supply chain driver becauseit does not have a physical presence. Information, however, deeplyaffects every part of the supply chain. Its impact is easy tounderestimate as information affects a supply chain in many differentways. Information serves as the connection between the supply chain’svarious stages, allowing them to coordinate and bring about many of thebenefits of maximizing total supply chain profitability. Information is also crucial to the daily operations of each stage in a supply chain. For instance, a production scheduling system uses information on demand to create a schedule that allows a factory to produce the right products in an efficient manner. A warehouse management system uses information to create visibility of the warehouse’s inventory. The company can then use this information to determine whether new orders can be filled.Difficulty: Hard5. Explain the role of each of the major drivers of supply chainperformance in the competitive strategy.Answer: Facilities and their corresponding capacities to perform theirfunctions are a key driver of supply chain performance in terms ofresponsiveness and efficiency. For example, companies can gain economies of scale when a product is manufactured or stored in only one location;this centralization increases efficiency. The cost reduction, however,comes at the expense of responsiveness, as many of a company’scustomers may be located far from the production facility. The oppositeis also true. Locating facilities close to customers increases thenumber of facilities needed and consequently reduces efficiency. If thecustomer demands and is willing to pay for the responsiveness thathaving numerous facilities adds, however, then this facilities decisionhelps meet the company’s competitive strategy goals.Inventory plays a significant role in a supply chain’s ability tosupport a firm’s competitive strategy. If a firm’s competitivestrategy requires a very high level of responsiveness, a company can use inventory to achieve this responsiveness by locating large amounts ofinventory close to the customer. Conversely, a company can also useinventory to make itself more efficient by reducing inventory throughcentralized stocking. The latter strategy would support a competitivestrategy of being a low-cost producer. The trade-off implicit in theinventory driver is between the responsiveness that results from moreinventory and the efficiency that results from less inventory.The role of transportation in a company’s competitive strategy figuresprominently when the company is considering the target customer’s needs.If a firm’s competitive strategy targets a customer that demands a very high level of responsiveness, and that customer is willing to pay forthis responsiveness, then a firm can use transportation as one driverfor making the supply chain more responsive. The opposite is true aswell. If a company’s competitive strategy targets customers whose maindecision criterion is price, then the company can use transportation tolower the cost of the product at the expense of responsiveness. As acompany may use both inventory and transportation to increaseresponsiveness or efficiency, the optimal decision for the company often means finding the right balance between the two.。
(完整版)供应链管理_第三版_Unit1_习题与答案

(完整版)供应链管理_第三版_Unit1_习题与答案Chapter 1Understanding the Supply ChainTrue/False1. A supply chain includes only the organizations directly involved in supplyingcomponents needed for manufacturing.Answer: FalseDifficulty: Moderate2. A supply chain could be more accurately described as a supply network orsupply web.Answer: TrueDifficulty: Moderate3. The objective of every supply chain is to maximize the overall value generated.Answer: TrueDifficulty: Easy4. Every supply chain must include all 5 stages.Answer: FalseDifficulty: Easy5. The cycle view of a supply chain holds that the processes in a supply chain aredivided into a series of activities performed at the interface between successivestages.Answer: TrueDifficulty: Moderate6. The push/pull view of a supply chain holds that theprocesses in a supply chainare divided into 2 categories depending on whether they are initiated in response to or in anticipation of customer orders.Answer: TrueDifficulty: Easy7. The objective of customer order entry is to maintain a record of product receiptand complete payment.Answer: FalseDifficulty: Hard8. The replenishment cycle occurs at the retailer/distributor interface.Answer: TrueDifficulty: Hard9. The manufacturing cycle occurs at the manufacturer/supplier interface.Answer: FalseDifficulty: Moderate10. The procurement cycle occurs at the manufacturer/supplier interface.Answer: TrueDifficulty: Easy11. The cycle view of the supply chain is useful when considering operationaldecisions, because it specifies the roles and responsibilities of each member of the supply chain.Answer: TrueDifficulty: Moderate12. The push/pull view of the supply chain is useful when considering strategicdecisions relating to supply chain design, because it categorizes processesbased on whether they are initiated in response to or in anticipation of customer orders.Answer: TrueDifficulty: Moderate13. Pull processes may also be referred to as reactive processes.Answer: TrueDifficulty: Easy14. Pull processes may also be referred to as speculative processes.Answer: FalseDifficulty: Easy15. All supply chain activities within a firm belong to one of three macro processes –CRM, ISCM and SRM.Answer: TrueDifficulty: Easy16. There is a close connection between the design and management of supplychain flows and the success of a supply chain.Answer: TrueDifficulty: EasyEssay/Problems1. Explain the 3 decision phases (categories) that must be made in a successfulsupply chain.Answer: The 3 decision phases that occur within a supply chain are supply chain strategy (or design), supply chain planningand supply chain operation. Decisions relate to the flow of information, product and funds. The difference between categories depends upon the frequency of each decision and the time frame over which it has an impact. During the supply chain strategy phase, a companydetermines what the chain’s configurations will be, how resources will beallocated, and what processes each stage will perform. This will establish thestructure of the supply chain for several years. Supply chain planning deals withdecisions with a time frame from 3 months up to a year. The planning phasemust work within the constraints established in the strategy phase. Planningdecisions include which markets to supply from which locations, subcontractingof manufacturing, inventory policies and timing and size of marketing promotions.The supply chain operation phase operates on a weekly or daily time horizon and deals with decisions concerning individual customer orders.Difficulty: Hard答:决策的3阶段发生在一个供应链的供应链战略(或设计),供应链与供应链运作。
(完整版)供应链管理第三版Unit6习题与答案.doc
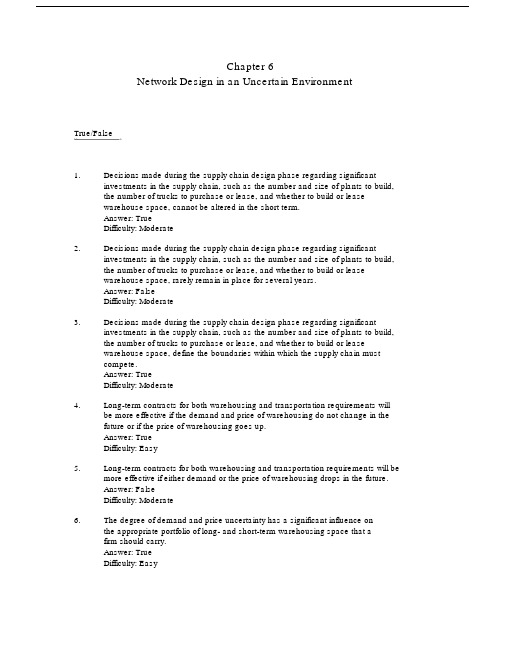
Chapter 6Network Design in an Uncertain EnvironmentTrue/False1.Decisions made during the supply chain design phase regarding significantinvestments in the supply chain, such as the number and size of plants to build,the number of trucks to purchase or lease, and whether to build or leasewarehouse space, cannot be altered in the short term.Answer: TrueDifficulty: Moderate2.Decisions made during the supply chain design phase regarding significantinvestments in the supply chain, such as the number and size of plants to build,the number of trucks to purchase or lease, and whether to build or leasewarehouse space, rarely remain in place for several years.Answer: FalseDifficulty: Moderate3.Decisions made during the supply chain design phase regarding significantinvestments in the supply chain, such as the number and size of plants to build,the number of trucks to purchase or lease, and whether to build or leasewarehouse space, define the boundaries within which the supply chain mustcompete.Answer: TrueDifficulty: Moderate4.Long-term contracts for both warehousing and transportation requirements willbe more effective if the demand and price of warehousing do not change in thefuture or if the price of warehousing goes up.Answer: TrueDifficulty: Easy5.Long-term contracts for both warehousing and transportation requirements will bemore effective if either demand or the price of warehousing drops in the future.Answer: FalseDifficulty: Moderate6.The degree of demand and price uncertainty has a significant influence onthe appropriate portfolio of long- and short-term warehousing space that afirm should carry.Answer: TrueDifficulty: Easy7.If price and demand vary over time in a global network, flexibleproduction capacity can be reconfigured to maximize profits in the newenvironment. Answer: TrueDifficulty: Moderate8. A firm may choose to build a flexible global supply chain even in the presenceof little demand or supply uncertainty if certainty exists in exchange rates or prices. Answer: FalseDifficulty: Moderate9.The present value of a stream of cash flows is what that stream is worth intoday ’ s dollars.Answer: TrueDifficulty: Easy10. Discretionary cash flow (DCF) analysis evaluates the present value of anystream of future cash flows and allows management to compare two streams ofcash flows in terms of their financial value.Answer: FalseDifficulty: Easy11.The present value of future cash flows is found by using a discount factor.Answer: TrueDifficulty: Moderate12. The rate of return k is also referred to as the present value of capital.Answer: FalseDifficulty: Easy13. A negative NPV for an option indicates that the option will lose money for thesupply chain.Answer: TrueDifficulty: Moderate14.The decision with the lowest NPV will provide a supply chain with thehighest financial return.Answer: FalseDifficulty: Moderate15.In reality, demand and prices are highly uncertain and are likely to fluctuateduring the life of any supply chain decision.Answer: TrueDifficulty: Moderate16.For a global supply chain, exchange rates and inflation are unlikely to varyover time in different locations.Answer: FalseDifficulty: Easy17.The multiplicative binomial cannot take on negative values and can be used forfactors like demand, price, and exchange rates that cannot become negative.Answer: TrueDifficulty: Moderate18. A logical objection to both the multiplicative and additive binomial is the fact thatthe underlying factor takes on two values at the end of each period.Answer: FalseDifficulty: Hard19.If uncertainty is ignored, a manager will always sign long-term contracts becausethey are typically cheaper and avoid all flexible capacity because it is moreexpensive.Answer: TrueDifficulty: Moderate20.During network design, managers need a methodology that allows them toestimate the certainty in their forecast of demand and price and thenincorporate this certainty into the decision-making process.Answer: FalseDifficulty: Hard21.Decision trees with DCFs can be used to evaluate supply chain designdecisions given uncertainty in prices, demand, exchange rates, and inflation.Answer: TrueDifficulty: Moderate22.Uncertainty in demand and economic factors should not be included in thefinancial evaluation of supply chain design decisions.Answer: FalseDifficulty: Hard23.In a complex decision tree, there are thousands of possible paths that may resultfrom the first period to the last.Answer: TrueDifficulty: Easy24.Simulation methods are very good at evaluating a decision where the pathitself is decision dependent.Answer: FalseDifficulty: Hard25.Simulation models require a higher setup cost to start and operate comparedto decision tree tools.Answer: TrueDifficulty: Easy26.The main advantage of simulation models is that they can provide low-cost evaluations of complex situations.Answer: FalseDifficulty: Moderate27.Strategic planning and financial planning should be combined during supplychain network design.Answer: TrueDifficulty: Moderate28.The evaluation of supply chain networks should not use multiple metrics.Answer: FalseDifficulty: Moderate29.Financial analysis should be used as an input to decision making, not asthe decision-making process.Answer: TrueDifficulty: Moderate30.One of the best ways to speed up the process of financial analysis and arrive ata good decision is to use estimates, except when it appears that finding a veryaccurate input would take an inordinate amount of time.Answer: FalseDifficulty: EasyMultiple Choice1.Decisions made during the supply chain design phase regarding significantinvestments in the supply chain, such as the number and size of plants to build, the number of trucks to purchase or lease, and whether to build or leasewarehouse space,a.can be altered in the short term.b.cannot be altered in the short term.c.cannot be altered in the long term.d.can only be altered in the short term.e.all of the aboveAnswer: bDifficulty: Easy2.Decisions made during the supply chain design phase regarding significantinvestments in the supply chain, such as the number and size of plants to build, the number of trucks to purchase or lease, and whether to build or leasewarehouse space,a.are realigned every few weeks.b.only remain in place for several years.c.rarely remain in place for several years.d.only remain in place for a few weeks.e.often remain in place for several years.Answer: eDifficulty: Hard3.Decisions made during the supply chain design phase regarding significantinvestments in the supply chain, such as the number and size of plants to build,the number of trucks to purchase or lease, and whether to build or leasewarehouse space,a.define the boundaries within which the supply chain must compete.b.have little impact on how the supply chain must compete.c.are irrelevant regarding how the supply chain will compete.d.are the only consideration regarding how the supply chain will compete.e.none of the aboveAnswer: aDifficulty: Moderate4.Long-term contracts for both warehousing and transportation requirementswill be more effective ifa.the demand and price of warehousing do not change in the future.b.the price of warehousing goes up in the future.c.demand drops in the future.d.the price of warehousing drops in the future.e. a and b onlyAnswer: eDifficulty: Moderate5.Short-term contracts for both warehousing and transportation requirements willbe more effectivea.if the demand and price of warehousing do not change in the future.b.if the price of warehousing goes up in the future.c.if either demand or the price of warehousing drops in the future.d.only if demand drops in the future.e.only if the price of warehousing drops in the future.Answer: cDifficulty: Moderate6.The degree of demand and price uncertainty hasa.no effect on the appropriate portfolio of long- and short-termwarehousing space that a firm should carry.b. a limited influence on the appropriate portfolio of long- and short-term warehousing space that a firm should carry.c. a minor influence on the appropriate portfolio of long- and short-termwarehousing space that a firm should carry.d. a significant influence on the appropriate portfolio of long- and short-termwarehousing space that a firm should carry.e.None of the above are true.Answer: dDifficulty: Moderate7.Uncertainty of demand and pricea.drives the value of building flexible production capacity at a plant.b.eliminates the value of building flexible production capacity at a plant.c.facilitates the value of building flexible production capacity at a plant.d.has no effect on the value of building flexible production capacity ata plant.e.None of the above are true.Answer: a8.If price and demand do vary over time in a global network,a.flexible production capacity should not be used in the new environment.b.flexible production capacity will be ineffective in the new environment.c.flexible production capacity can be reconfigured to minimize profits in thenew environment.d.flexible production capacity can be reconfigured to maximize profits inthe new environment.e.flexible production capacity should never be used in an uncertainenvironment.Answer: dDifficulty: Moderate9. A firm may choose to build a flexible global supply chain even in the presenceof little demand or supply uncertainty ifa.certainty exists in both exchange rates and prices.b.certainty exists in exchange rates or prices.c.uncertainty exists in both exchange rates and prices.d.uncertainty exists in exchange rates or prices.e.uncertainty exists only in exchange rates.Answer: dDifficulty: Moderate10.The present value of a future stream of cash flows is what that streama.was worth in yesterday’ s dollars.b.is wo rth in today’ s dollars.c.will be worth in future dollars.d.might be worth in future dollars.e.none of the aboveAnswer: bDifficulty: Easy11.The process of evaluating the present value of any stream of future cash flowsso that management can compare two streams of cash flows in terms of theirfinancial value isa.annual cash flow(ACF) analysis.b.discretionary cash flow(DCF) analysis.c.discounted cash flow(DCF) analysis.d.future cash flow(FCF) analysis.e.none of theabove Answer: cDifficulty: Moderate12.The present value of future cash flow is found bya.locating the correct factor on a z-table.ing a discount factor.c.plotting the function on a graph.d.adding the total of all future cash flows.e.none of the aboveAnswer: b13.The discount factor used to obtain the present value of money in the next periodwhere k represents the rate of return isa.k.b.1+k.c.1/(1+ k).d.k /(1+ k).e.none of the aboveAnswer: cDifficulty: Moderate14.The rate of return k is also referred to as thea.discount rate.b.hurdle rate.c.opportunity cost of capital.d.all of the abovee.none of theabove Answer: dDifficulty: Easy15.What is the present value of a $27 revenue that will be received in one yearwhere the rate of return is 8% (.08)?a.$2.50b.$15.00c.$25.00d.$30.00e.none of the aboveAnswer: cDifficulty: Easy16.The net present value (NPV) of a stream of cash flows is equal toa.the sum of all cash flows for all periods being considered.b.the sum of all cash flows for all periods being considered divided bythe number of periods.c.the average of all cash flows for all periods being considered.d.the average of all cash flows for all periods being considered multipliedby the number of periods.e.the sum of all cash flows for all periods being considered discountedby the rate of return for each period.Answer: eDifficulty: Hard17. A negative NPV (net present value) for an option indicates that the option willa.gain money for the supply chain.b.lose money for the supply chain.c.maximize profit for the supply chain.d.minimize profit for the supply chain.e.none of the aboveAnswer: bDifficulty: Moderate18.The decision with the highest NPV (net present value) will provide a supply chainwitha.the highest financial return.b.the lowest financial return.c. a reasonable financial return.d.the least desirable financial return.e.none of the aboveAnswer: aDifficulty: Moderate19.The NPV (net present value) of a cash stream that is equal to $100 per period for5 periods with a rate of return of 10% (.10) per period would bea.379.07.b.416.98.c.500.00.d.610.51.e.671.56.Answer: bDifficulty: Moderate20.The NPV (net present value) of a cash stream that is equal to $75 per period for5 periods with a rate of return of 10% (.10) per period would bea.221.37.b.284.30.c.312.74.d.375.00.e.none of the aboveAnswer: cDifficulty: Moderate21.In reality, demand and prices area.highly certain and not likely to fluctuate during the life of any supply chaindecision.b.highly certain and likely to fluctuate during the life of any supplychain decision.c.highly uncertain and not likely to fluctuate during the life of any supplychain decision.d.highly uncertain and likely to fluctuate during the life of any supply chaindecision.e.none of the aboveAnswer: dDifficulty: Moderate22.For a global supply chain, exchange rates and inflation area.likely to vary over time in different locations.b.not likely to vary over time in different locations.c.not likely to vary over time in any locations.d.likely to be stable over time in all locations.e.none of the aboveAnswer: aDifficulty: Easy23.The binomial representation of uncertainty is based on the assumption that whenmoving from one period to the next, the value of the underlying factor (such asdemand or price)a.has only one possible outcome.b.has only two possible outcomes - up or down.c.has many possible outcomes.d.cannot be accurately determined.e.none of the aboveAnswer: bDifficulty: Moderate24.In the commonly used multiplicative binomial, it is assumed that the underlyingfactora. moves up by a factor u > 1 with probability p.b. moves down by a factor u > 1 with probability p.c. moves down by a factor d < 1 with probability 1 –p.d.either a or be.either a orc Answer: eDifficulty: Hard25.The multiplicative binomial can be used for factors like demand, price, andexchange rates that cannot become negative because ita.can take on negative values.b.cannot take on negative values.c.can take on positive values.d.cannot take on positive values.e.all of the aboveAnswer: bDifficulty: Hard26. A logical objection to both the multiplicative and additive binomial is the fact thatthe underlying factora.takes on only one of two possible values at the end of each period.b.takes on two values at the end of each period.c.takes on one of many possible values at the end of each period.d.takes on several of many possible values at the end of each period.e.none of the aboveAnswer: aDifficulty: Moderate27.If uncertainty is ignored, a manager willa.always sign long-term contracts because they are typically moreexpensive and avoid all flexible capacity because it is more expensive.b.always sign short-term contracts because they are typically cheaperand avoid all flexible capacity because it is more expensive.c.always sign long-term contracts because they are typically cheaperand avoid all flexible capacity because it is more expensive.d.always sign short-term contracts because they are typically cheaperand avoid all flexible capacity because it is less expensive.e.none of the aboveAnswer: cDifficulty: Hard28. A decision tree isa. a graphic device used to evaluate decisions under certainty.b. a graphic device used to evaluate decisions under uncertainty.c. a tabular device used to evaluate decisions under certainty.d. a tabular device used to evaluate decisions under uncertainty.e.none of the aboveAnswer: bDifficulty: Moderate29. Decision tree analysis is based on Bellman ’ s principle, which states that for anychoice of strategy in a given state,a. the optimal strategy is the one that is selected if the entire analysis isassumed to begin in the first period.b. the optimal strategy is the one that is selected if the entire analysis isassumed to begin in the last period.c. the optimal strategy in the next period is the one that is selected if theentire analysis is assumed to begin in the last period.d. the optimal strategy in the next period is the one that is selected if theentire analysis is assumed to begin in the next period.e. none of the aboveAnswer: dDifficulty: Hard30.The first step in decision tree analysis methodology is toa.identify factors such as demand, price, and exchange rate, whosefluctuation will be considered over the next T periods.b.identify the periodic discount rate k for each period.c.start at period T, work back to Period 0 identifying the optimal decisionand the expected cash flows at each step. Expected cash flows at eachstep in a given period should be discounted back when included inthe previous period.d.identify the duration of each period (month, quarter, etc.) and the numberof periods T over which the decision is to be evaluated.e.identify representations of uncertainty for each factor; that is, determinewhat distribution to use to model the uncertainty.Answer: dDifficulty: Moderate31.The last step in decision tree analysis methodology is toa. identify factors such as demand, price, and exchange rate, whose fluctuationwill be considered over the next T periods.b. identify the periodic discount rate k for each period.c. start at period T, work back to Period 0, identifying the optimal decision andthe expected cash flows at each step. Expected cash flows at each step in agiven period should be discounted back when included in the previous period.d.identify the duration of each period (month, quarter, etc.) and the number ofperiods T over which the decision is to be evaluated.e.identify representations of uncertainty for each factor; that is, determine whatdistribution to use to model the uncertainty.Answer: cDifficulty: Moderate32.Uncertainty in demand and economic factors should be included in thefinancial evaluation of supply chain design decisions, becausea.the exclusion of certainty may have a significant impact on this evaluation.b.the exclusion of uncertainty may have a significant impact on thisevaluation.c.the inclusion of certainty may have a significant impact on this evaluation.d.the inclusion of uncertainty may have a significant impact onthis evaluation.e.none of the aboveAnswer: dDifficulty: Hard33.Flexibility should be valued by taking into account uncertainty in demandand economic factors. In general, flexibility will tend toa.decrease in value with a decrease in certainty.b.increase in value with an increase in uncertainty.c.decrease in value with an increase in uncertainty.d.increase in value with an increase in certainty.e.None of the above are accurate.Answer: bDifficulty: Moderate34. A major factor that makes the decision tree methodology quite powerful isa.the choice of certainty.b.the choice of discount rate.c.the choice of uncertainty level.d.the choice of additive factor.e.all of the aboveAnswer: bDifficulty: Moderate35.The appropriate discount rate used in decision tree methodologya.should be risk-adjusted and risk may vary by period and decision node.b.should be risk-adjusted and risk may not vary by period and decisionnode.c.should not be risk-adjusted and risk may vary by period and decisionnode.d.should not be risk-adjusted and risk may not vary by period anddecision node.e.None of the above are accurate.Answer: aDifficulty: Moderate36.Alternative approaches to decision tree analysis includea.contingent claims analysis (CCA) for discrete time analysis.b.real options for the continuous time case.c.real options for the discrete time analysis.d.all of the abovee. a and b onlyAnswer: eDifficulty: Moderate37.Contingent claims analysis (CCA) and real optionsa.adjust hurdle rate so that the risk-free discount rate may be applied ineach period.b.adjust opportunity cost of capital so that the risk-free discount rate may beapplied in each period.c.adjust rate of return so that the risk-free discount rate may be appliedin each period.d.adjust transition probabilities so that the risk-free discount rate maybe applied in each period.e.none of the aboveAnswer: dDifficulty: Moderate38.Firms should use simulation for evaluating decisions whena.underlying decision trees are simple and explicit solutions forthe underlying decision tree are difficult to obtain.b.underlying decision trees are very complex and explicit solutions forthe underlying decision tree are difficult to obtain.c.underlying decision trees are simple and explicit solutions forthe underlying decision tree are easy to obtain.d.underlying decision trees are very complex and explicit solutions forthe underlying decision tree are easy to obtain.e.none of the aboveAnswer: bDifficulty: Moderate39.In a complex decision tree there area.only a few possible paths that may result from the first period to the last.b.less than thirty possible paths that may result from the first period tothe last.c.thousands of possible paths that may result from the first period tothe last.d.an infinite number of possible paths that may result from the first periodto the last.e.none of the aboveAnswer: cDifficulty: Moderate40.Simulation methods are very good at evaluating a decision wherea.the path itself is decision dependent.b.the path itself is not decision dependent.c.the discount rate is decision dependent.d.the discount rate is not decision dependent.e.none of theabove Answer: bDifficulty: Hard41.Simulation modelsa.require a higher setup cost to start and operate compared to decisiontree tools.b.require a lower setup cost to start and operate compared to decision treetools.c.require a higher setup cost to start but less to operate comparedto decision tree tools.d.require a lower setup cost to start but more to operate comparedto decision tree tools.e.none of the aboveAnswer: aDifficulty: Hard42.The main advantage of simulation models is that they cana.provide high-quality evaluations of simple situations.b.provide high-quality evaluations of complex situations.c.provide low-cost evaluations of simple situations.d.provide low-cost evaluations of complex situations.e.provide low-quality evaluations of complex situations.Answer: bDifficulty: Easy43.Strategic planning and financial planninga.should be performed independently during supply chain network design.b.should be performed sequentially during supply chain network design.c.should be performed hierarchically during supply chain network design.d.should be performed concurrently during supply chain network design.e.should be combined during supply chain network design.Answer: eDifficulty: Hard44.The evaluation of supply chain networksa.should use only one metric.b.should use multiple metrics.c.should not use more than one metric.d.should not use multiple metrics.e.should be subjective.Answer: bDifficulty: Moderate45.Financial analysis should be used asa.the decision-making process.b.an alternative decision-making process.c.an input to decision making, not as the decision-making process.d.all of the abovee.none of the aboveAnswer: cDifficulty: Moderate46.One of the best ways to speed up the process of financial analysis and arrive ata good decision is toe estimates of inputs when it appears that finding a very accurate inputwould take an inordinate amount of time.e estimates backed up by sensitivity analysis when it appears thatfinding a very accurate input would take an inordinate amount of time.e estimates of inputs except when it appears that finding avery accurate input would take an inordinate amount of time.d.make sure that every detail is very accurate.e.none of the aboveAnswer: bDifficulty: ModerateEssay/Problems1.Explain additive and multiplicative binomial representations of uncertainty.Answer : The binomial representation of uncertainty is based on the assumptionthat when moving from one period to the next, the value of the underlying factor(such as demand or price) has only two possible outcomes - up or down. In thecommonly used multiplicative binomial, it is assumed that the underlying factoreither moves up by a factor u > 1 with probability p, or down by a factor d < 1 with probability 1 –p. In the additive binomial, it is assumed that the underlying factorincreases by u in a given period with probability p and decreases by d withprobability 1 –p. The multiplicative binomial cannot take on negative values andcan be used for factors like demand, price, and exchange rates that cannotbecome negative. It also has the advantage of the growth or decline in the givenfactor being proportional to the current value of the factor and not fixedindependent of size. A logical objection to both the multiplicative and additivebinomial is the fact that the underlying factor takes on only one of two possiblevalues at the end of each period. Certainly a price can change to more than justtwo values. But by making the period short enough, this assumption may bejustified.Difficulty: Hard2.Summarize the steps in the decision tree analysis methodology.Answer: The decision tree analysis methodology is summarized as follows:1.Identify the duration of each period (month, quarter, etc.) and the number ofperiods T over which the decision is to be evaluated.2.Identify factors such as demand, price, and exchange rate, whose fluctuationwill be considered over the next T periods.3.Identify representations of uncertainty for each factor; that is, determinewhat distribution to use to model the uncertainty.4. Identify the periodic discount rate k for each period.5.Represent the decision tree with defined states in each period, as well asthe transition probabilities between states in successive periods.6. Starting at period T, work back to Period 0, identifying the optimal decision andthe expected cash flows at each step. Expected cash flows at each step in a givenperiod should be discounted back when included in the previous period. Difficulty:Moderate3.Discuss the ideas that managers should consider to make better supply chainnetwork design decisions under uncertainty.Answer: Managers should consider the following ideas to help them make betternetwork design decisions under uncertainty:1. Combine strategic planning and financial planning during network design.Inmost organizations, financial planning and strategic planning are performedindependently. Strategic planning tries to prepare for future uncertainties butoften without rigorous quantitative analysis, whereas financial planning performsquantitative analysis but assumes a predictable or well-defined future. Decisionmakers should design supply chain networks considering a portfolio of strategicoptions —the option to wait, build excess capacity, build flexible capacity, signlong-term contracts, purchase from the spot market, and so forth. The variousoptions should be evaluated in the context of future uncertainty.2. Use multiple metrics to evaluate supply chain networks.As one metric canonly give part of the picture, it is beneficial to examine network design decisionsusing multiple metrics such as firm profits, supply chain profits, customerservice levels, and response times. Often, different metrics will recommenddifferent decisions and by using multiple metrics, the differences between thestrategic choices will become clearer. The best decisions can be made when amultitude of metrics are available, because each metric enhances the overallview of the alternatives being considered.e financial analysis as an input to decision making, not as the decision-making process. Financial analysis is a great tool in the decision-making process,as it often produces an answer and an abundance of quantitative data to back upthat answer. However appealing this may be, management should not rely solelyon financial analysis to make decisions. Use of this analysis as a large part of thedecision-making process is fine, but other inputs into the decision process that aredifficult to quantify should be included in the analysis as well. Financialmethodologies alone do not provide a complete picture of the alternatives. Theseimpacts should be considered in addition to the raw financial analysis. In the finalanalysis, management must use other inputs beyond financial analysis in thedecision-making process to get the most complete view of the alternatives possible.4. Use estimates along with sensitivity analysis. Many of the inputs into financialanalysis can be difficult, if not impossible, to nail down in a very accurate fashion.This can cause financial analysis to be a long and drawn out process. One of thebest ways to speed the process along and arrive at a good decision is to useestimates of inputs when it appears that finding a very accurate input would take aninordinate amount of time. Using estimates is fine when the estimates are backed upby sensitivity analysis. By performing sensitivity analysis on the input ’ s。
供应链管理第三版Unit11习题与答案(可编辑修改word版)
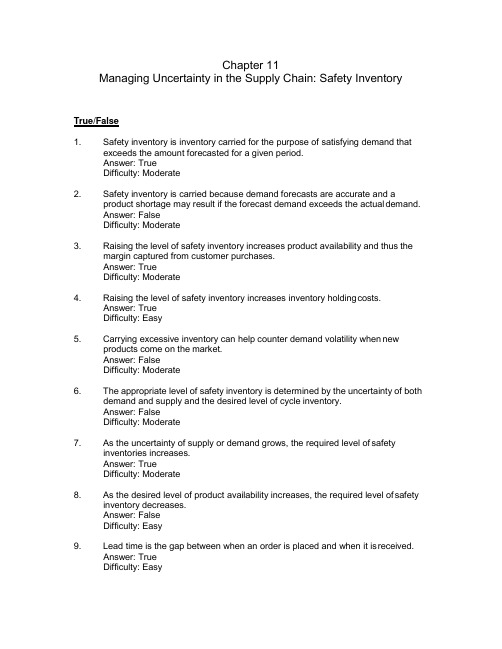
Chapter 11Managing Uncertainty in the Supply Chain: Safety InventoryTrue/False1. Safety inventory is inventory carried for the purpose of satisfying demand thatexceeds the amount forecasted for a given period.Answer: TrueDifficulty: Moderate2. Safety inventory is carried because demand forecasts are accurate and aproduct shortage may result if the forecast demand exceeds the actual demand.Answer: FalseDifficulty: Moderate3. Raising the level of safety inventory increases product availability and thus themargin captured from customer purchases.Answer: TrueDifficulty: Moderate4. Raising the level of safety inventory increases inventory holding c osts.Answer: TrueDifficulty: Easy5. Carrying excessive inventory can help counter demand volatility when newproducts come on the market.Answer: FalseDifficulty: Moderate6. The appropriate level of safety inventory is determined by the uncertainty of bothdemand and supply and the desired level of cycle inventory.Answer: FalseDifficulty: Moderate7. As the uncertainty of supply or demand grows, the required level of safetyinventories increases.Answer: TrueDifficulty: Moderate8. As the desired level of product availability increases, the required level of s afetyinventory decreases.Answer: FalseDifficulty: Easy9. Lead time is the gap between when an order is placed and when it is r eceived.Answer: TrueDifficulty: Easy10. The coefficient of variation measures the size of the relative certainty of cycleinventory.Answer: FalseDifficulty: Easy11. Product availability reflects a firm’s ability to fill a customer order out of availableinventory.Answer: TrueDifficulty: Moderate12. Order fill rate is the fraction of product demand that is satisfied from product ininventory.Answer: FalseDifficulty: Moderate13. Product fill rate is the fraction of product demand that is satisfied from product ininventory.Answer: TrueDifficulty: Moderate14. The distinction between product fill rate and order fill rate is significant in a singleproduct situation.Answer: FalseDifficulty: Hard15. Tracking order fill rates is important when customers place a high value on theentire order being filled simultaneously.Answer: TrueDifficulty: Easy16. With continuous review, inventory is continuously tracked and an order for a lotsize Q is placed at regular intervals of time.Answer: FalseDifficulty: Hard17. With periodic review, inventory status is checked at regular intervals and an orderis placed to raise the inventory level to a specified threshold.Answer: TrueDifficulty: Hard18. The expected shortage per replenishment cycle (ESC) is the average units ofdemand that are satisfied from inventory in stock per replenishment cycle.Answer: FalseDifficulty: Hard19. A shortage occurs in a replenishment cycle only if the demand during the leadtime exceeds the ROP.Answer: TrueDifficulty: Moderate20. The fill rate increases and the cycle service level decreases as the safetyinventory is increased.Answer: FalseDifficulty: Moderate21. For the same safety inventory, an increase in lot size increases the fill rate butnot the cycle service level.Answer: TrueDifficulty: Hard22. The required safety inventory grows rapidly with a decrease in the desiredproduct availability.Answer: FalseDifficulty: Easy23. The required safety inventory increases with an increase in the lead time and thestandard deviation of periodic demand.Answer: TrueDifficulty: Easy24. A goal of any supply chain manager is to reduce the level of safety inventoryrequired regardless of the affect product availability.Answer: FalseDifficulty: Easy25. In most supply chains, the key to reducing the underlying forecast uncertainty isto link all forecasts throughout the supply chain to customer demand data.Answer: TrueDifficulty: Moderate26. A reduction in supply can help dramatically reduce safety inventory requiredwithout hurting product availability.Answer: FalseDifficulty: Moderate27. Aggregation reduces the standard deviation of demand only if demand acrossthe regions being aggregated is not perfectly positively correlated.Answer: TrueDifficulty: Moderate28. In case demand in different geographical regions is about the same size andindependent, aggregation increases safety inventory by the square root of thenumber of areas aggregated.Answer: FalseDifficulty: Moderate29. If aggregation reduces the required safety inventory for a product by a smallamount, it may be best to carry the product in multiple decentralized locations t o reduce response time and transportation cost.Answer: TrueDifficulty: Moderate30. The lower the coefficient of variation of an item, the greater the reduction insafety inventories as a result of centralization.Answer: FalseDifficulty: Hard31. Manufacturer-driven substitution increases overall profitability for themanufacturer by allowing some aggregation of demand, which reduces theinventory requirements for the same level of availability.Answer: TrueDifficulty: Moderate32. Postponement allows the supply chain to delay product differentiation, whichresults in disaggregating most of the inventories in the supply chain. Answer:FalseDifficulty: Moderate33. Periodic review policies require more safety inventory than continuous reviewpolicies for the same level of product availability.Answer: TrueDifficulty: Easy34. When using a continuous review policy, a manager has to account for theuncertainty of demand during the lead time and the review interval.Answer: FalseDifficulty: EasyMultiple Choice1. Inventory carried for the purpose of satisfying demand that exceeds the amountforecasted for a given period isa. cycle inventory.b. demand inventory.c. safety inventory.d. security inventory.e. all of the aboveAnswer: cDifficulty: Easy2. Safety inventory is carried becausea. demand forecasts are accurate.b. demand forecasts are uncertain.c. adequate supplies are available.d. excess product was manufactured.e. forecast demand exceeds the actual demand.Answer: b Difficulty:Moderate3. The trade-off that a supply chain manager must consider when planning safetyinventory isa. increasing product availability versus increasing inventory holding costs.b. decreasing product availability versus decreasing inventory holding costs.c. increasing product availability versus raising the level of safety inventory.d. decreasing product availability versus decreasing the level of safetyinventory.e. none of the aboveAnswer: aDifficulty: Moderate4. The issue of product availability and the level of safety inventory is particularlysignificant in industries wherea. product life cycles are short and demand is stable.b. product life cycles are short and demand is very volatile.c. product life cycles are long and demand is stable.d. product life cycles are long and demand is very volatile.e. a and b onlyAnswer: b Difficulty:Moderate5. A key to success at which company has been its ability to provide a high level ofproduct availability to customers while carrying very low levels of safety inventory in its supply chain?a. Compaqb. Hewlett-Packardc. Delld. Packard-Belle. all of the aboveAnswer: cDifficulty: Moderate6. What key question(s) need(s) to be considered when planning safety inventoryfor any supply chain?a. What is the appropriate lead time to establish?b. What is the appropriate level of safety inventory to carry?c. What actions can be taken to improve product availability while reducingsafety inventory?d. a and b onlye. b and c onlyAnswer: e Difficulty:Moderate7. The appropriate level of safety inventory is determined bya. the uncertainty of both demand and supply.b. the desired level of product availability.c. the desired level of cycle inventory.d. the processes in a supply chain are divided into 2 categories dependingall of the abovee. a and b onlyAnswer: e Difficulty:Moderate8. As the uncertainty of supply or demand grows, the required level of safetyinventoriesa. decreases.b. increases.c. remains stable.d. both a and be. none of the aboveAnswer: bDifficulty: Moderate9. As the desired level of product availability increases, the required level of s afetyinventorya. decreases.b. increases.c. remains stable.d. both a and be. none of the aboveAnswer: eDifficulty: Moderate10. Lead time is the gap betweena. when an order is placed and when it is received.b. when an order is received and when it is put away.c. when an order is received and when it is used.d. when an order is acknowledged and when it is received.e. none of the aboveAnswer: aDifficulty: Easy11. The coefficient of variation measuresa. the accuracy of the demand forecast.b. the size of the uncertainty relative to demand.c. the relevance of cycle inventory to demand.d. the relative certainty of the forecast.e. none of the aboveAnswer: bDifficulty: Moderate12. Which of the following is not a measure of product availability?a. customer fill rateb. product fill ratec. order fill rated. cycle service level (CSL)e. none of the aboveAnswer: aDifficulty: Moderate13. The fraction of orders that are filled from available inventory is thea. customer fill rate.b. product fill rate.c. order fill rate.d. cycle service level (CSL).e. none of the aboveAnswer: cDifficulty: Easy14. The fraction of product demand that is satisfied from product in inventory is thea. customer fill rate.b. product fill rate.c. order fill rate.d. cycle service level (CSL).e. none of the aboveAnswer: bDifficulty: Easy15. The fraction of replenishment cycles that end with all the customer demand beingmet is thea. customer fill rate.b. product fill rate.c. order fill rate.d. cycle service level (CSL).e. none of the aboveAnswer: dDifficulty: Easy16. If a customer order arrives when product is not availablea. a sale results.b. the retailer allocates product to the customer.c. a stockout results.d. the order is filled from safety inventory.e. none of the aboveAnswer: cDifficulty: Moderate17. The distinction between product fill rate and order fill rate isa. not significant in a single product situation.b. significant in a single product situation.c. not significant when a firm is selling multiple products.d. significant when a firm is selling multiple products.e. both a and dAnswer: aDifficulty: Moderate18. A replenishment policya. consists of decisions regarding when to reorder and how much to reorder.b. determines the cycle and safety inventories along with the fr and the CSL.c. may take several forms.d. All of the above are true.e. None of the above are true.Answer: dDifficulty: Moderate19. A company that tracks inventory and places an order for a lot size Q when theinventory declines to the reorder point (ROP) is usinga. continuous review.b. daily review.c. occasional review.d. periodic review.e. none of the aboveAnswer: aDifficulty: Easy20. A company that checks inventory status at regular periodic intervals and placesan order to raise the inventory level to a specified threshold is usinga. continuous review.b. daily review.c. occasional review.d. periodic review.e. none of the aboveAnswer: dDifficulty: Moderate21. Which of the following is correct?a. Average inventory = cycle inventory + safety inventoryb. Average inventory = cycle inventory - safety inventoryc. Average inventory = cycle inventory x safety inventoryd. Average inventory = cycle inventory / safety inventorye. none of the aboveAnswer: aDifficulty: Easy22. The expected shortage per replenishment cycle (ESC) isa. the units of demand that are not satisfied from inventory in stock in agiven replenishment cycle.b. the units of demand that are satisfied from inventory in stock in a givenreplenishment cycle.c. the average units of demand that are not satisfied from inventory in stockper replenishment cycle.d. the average units of demand that are satisfied from inventory in stock perreplenishment cycle.e. none of the aboveAnswer: cDifficulty: Moderate23. The product fill rate (fr) is thus given bya. fr = 1 –ESC/Q + (Q – ES C)/Q.b. fr = 1 –ESC/Q – (Q – ES C)/Q.c. fr = 1 + ESC/Q = (Q + ES C)/Q.d. fr = 1 –ESC/Q = (Q – ES C)/Q.e. none of the aboveAnswer: dDifficulty: Hard24. Given a lot size of Q (which is also the average demand in a replenishmentcycle)a. the fraction of demand lost is thus ESC + Q.b. the fraction of demand lost is thus ESC –Q.c. the fraction of demand lost is thus ESC/Q.d. the fraction of demand lost is thus ESC x Q.e. none of the aboveAnswer: cDifficulty: Hard25. A shortage occurs in a replenishment cyclea. only if the demand during the lead time exceeds the ROP.b. only if the demand during the lead time is less than the ROP.c. only if the demand during the lead time exceeds the average demand.d. only if the demand during the lead time is less than the average demand.e. none of the aboveAnswer: aDifficulty: Moderate26. As the safety inventory is increaseda. fill rate increases and cycle service level decreases.b. fill rate decreases and cycle service level increases.c. both fill rate and cycle service level increase.d. both fill rate and cycle service level decrease.e. none of the aboveAnswer: cDifficulty: Moderate27. For the same safety inventory, an increase in lot sizea. decreases the fill rate but not the cycle service level.b. increases the fill rate but not the cycle service level.c. decreases both the fill rate and the cycle service level.d. increases both the fill rate and the cycle service level.e. none of the aboveAnswer: cDifficulty: Hard28. The expected shortage per replenishment cycle is shown asa. ESC = (1 + fr)Q.b. ESC = (1 –fr)Q.c. ESC = (1 + fr)/Q.d. ESC = (1 –fr)/Q.e. none of the aboveAnswer: bDifficulty: Hard29. The required safety inventorya. grows rapidly with a decrease in the desired product a vailability.b. grows rapidly with an increase in the desired product availability.c. decreases with an increase in the desired product a vailability.d. remains stable with an increase in the desired product availability.e. none of the aboveAnswer: bDifficulty: Moderate30. The required safety inventorya. increases with an increase in the lead time and the standard deviation ofperiodic demand.b. decreases with an increase in the lead time and the standard deviation ofperiodic demand.c. remains stable with an increase in the lead time and the standarddeviation of periodic demand.d. increases with a decrease in the lead time and the standard deviation ofperiodic demand.e. none of the aboveAnswer: dDifficulty: Moderate31. A goal of any supply chain manager is toa. increase the level of safety inventory required in a way that does notadversely affect product availability.b. increase the level of safety inventory required regardless of the effect onproduct availability.c. reduce the level of safety inventory required regardless of the effect onproduct availability.d. reduce the level of safety inventory required in a way that does notadversely affect product availability.e. none of the aboveAnswer: dDifficulty: Moderate32. Which of the following is not an approach to reduce the level of safety inventoryrequired in a way that does not adversely affect product availability?a. Reduce the supplier lead time.b. Reduce the underlying uncertainty of demand.c. Reduce the cost of material coming from suppliers.d. All of the above are approaches.e. None of the above are approaches.Answer: cDifficulty: Hard33. Often, safety inventory calculations in practicea. do not include any measure of supply uncertainty, resulting in levels thatmay be higher than required.b. do not include any measure of supply uncertainty, resulting in levels thatmay be lower than required.c. include measures of supply uncertainty, resulting in levels that may behigher than required.d. include any measures of supply uncertainty, resulting in levels that maybe lower than required.e. None of the above are accurate.Answer: bDifficulty: Hard34. Aggregation reduces the standard deviation of demanda. only if demand across the regions being aggregated is perfectly positivelycorrelated.b. only if demand across the regions being aggregated is not p erfectlypositively correlated.c. even if demand across the regions being aggregated is not p erfectlypositively correlated.d. whenever demand across the regions being aggregated is not perfectlypositively correlated.e. All of the above are accurate.Answer: bDifficulty: Hard35. If the number of independent stocking locations decreases by a factor of n, theaverage safety inventory is expected toa. decrease by a factor of √n.b. decrease by a factor of n.c. increase by a factor of √n.d. increase by a factor of n.e. None of the above are accurate.Answer: aDifficulty: Moderate36. Which of the following is not a major disadvantage of aggregating all inventory inone location?a. Increase in forecast accuracy of customer demand.b. Increase in response time to customer order.c. Increase in transportation cost to customer.d. All of the above are disadvantages.e. All of the above are advantages.Answer: aDifficulty: Easy37. Which of the following is not a method by which a supply chain can extract thebenefits of aggregation without having to physically centralize all inventories inone location?a. information centralizationb. specializationc. product substitutiond. component differentiatione. postponementAnswer: dDifficulty: Moderation38. Which approach to aggregation requires an information system that allowsaccess to current inventory records from each location?a. information centralizationb. specializationc. product substitutiond. component commonalitye. postponementAnswer: aDifficulty: Easy39. Which approach to aggregation would stock the fast-moving items atdecentralized locations close to the customer and slow-moving items at acentralized location?a. information centralizationb. specializationc. product substitutiond. component commonalitye. postponementAnswer: b Difficulty:Moderate40. The use of one product to satisfy demand for a different product isa. information centralization.b. specialization.c. product substitution.d. component commonality.e. postponement.Answer: cDifficulty: Easy41. Which use of common components in a variety of products has been a veryeffective supply chain strategy to exploit aggregation and reduce componentinventories?a. information centralizationb. specializationc. product substitutiond. component commonalitye. postponementAnswer: aDifficulty: Easy42. The ability of a supply chain to delay product differentiation or customization u ntilcloser to the time the product is sold isa. information centralization.b. specialization.c. product substitution.d. component commonality.e. postponement.Answer: e Difficulty:Moderate43. Which approach to aggregation has the goal of moving product differentiation asclose to the pull phase of the supply chain as possible?a. information centralizationb. specializationc. product substitutiond. component commonalitye. postponementAnswer: e Difficulty:Moderate44. Periodic review policies for inventory replenishment require safety inventory tocover demand duringa. lead time only.b. the review interval only.c. both lead time and the review interval.d. neither lead time or the review interval.e. lead time when it exceeds the review interval.Answer: cDifficulty: Moderate45. Continuous review policies for inventory replenishment require safety inventory tocover demand duringa. lead time only.b. the review interval only.c. both lead time and the review interval.d. neither lead time or the review interval.e. lead time when it exceeds the review interval.Answer: aDifficulty: Moderate46. Periodic review policies requirea. more safety inventory than continuous review policies for the same levelof product availability.b. less safety inventory than continuous review policies for the same level ofproduct availability.c. the same safety inventory as continuous review policies for the samelevel of product availability.d. no more safety inventory than continuous review policies for the samelevel of product availability.e. none of the aboveAnswer: aDifficulty: Moderate47. All inventory between a given stage in the supply chain and the final customer iscalled thea. cycle inventory.b. demand inventory.c. echelon inventory.d. safety inventory.e. none of the aboveAnswer: cDifficulty: Hard48. A distributor should decide his safety inventory levels based ona. the level of safety inventory carried by all retailers supplied by him.b. the level of safety inventory carried by other distributors.c. the level of safety inventory carried by manufacturers supplying him.d. the level of cycle inventory carried by all retailers supplied by him.e. the level of cycle inventory carried by other distributors.Answer: aDifficulty: Hard49. As retailers decrease the level of safety inventory they carry, the distributor willhave toa. decrease his or her safety inventory.b. increase his or her safety inventory.c. keep his or her safety inventory at the same level.d. increase his or her cycle inventory.e. decrease his or her cycle inventory.Answer: bDifficulty: HardEssay/Problems1. Discuss the role of safety inventory in the supply chain and the trade-offsinvolved.Answer: The primary role of safety inventory is providing product availability forcustomers when demand and supply are uncertain. The trade-off that a supplychain manager must consider when planning safety inventory involve productavailability and inventory holding costs. On one hand, raising the level of safetyinventory increases product availability and thus the margin captured fromcustomer purchases. On the other hand, raising the level of safety inventoryincreases inventory holding costs. This issue is particularly significant inindustries where product life cycles are short and demand is very volatile.Carrying excessive inventory can help counter demand volatility but can reallyhurt if new products come on the market and demand for the product in inventory dries up. The inventory on hand then becomes worthless.In today’s business environment, firms experience great pressure to improveproduct availability while increasing product variety through customization. As aresult, markets have become increasingly heterogeneous and demand forindividual products is very unstable and difficult to forecast. Both the increasedvariety and the increased pressure for availability push firms to increase the level of safety inventory they hold.At the same time, product life cycles have shrunk. This increases the risk to firms of carrying too much inventory. Thus, a key to the success of any supply chain is to figure out ways to decrease the level of safety inventory carried without hurting the level of product availability.Difficulty: Hard2. Discuss the various measures of product availability.Answer: Product availability reflects a firm’s ability to fill a customer order out ofavailable inventory. A stockout results if a customer order arrives when product is not available. There are several ways to measure product availability. Allavailability measures are defined on average over a given time frame, which can range from hours to a year.Product fill rate (fr) is the fraction of product demand that is satisfied from product in inventory. It is equivalent to the probability that product demand is suppliedfrom available inventory.Order fill rate is the fraction of orders that are filled from available inventory. In a multi-product scenario, an order is filled from inventory only if all products in theorder can be supplied from the available inventory. Order fill rates tend to belower than product fill rates because all products must be in stock for an order to be filled.Cycle service level (CSL) is the fraction of replenishment cycles that end with all the customer demand being met. A replenishment cycle is the interval betweentwo successive replenishment deliveries. The CSL is equal to the probability ofnot having a stockout in a replenishment cycle. Observe that a CSL of 60 percent will typically result in a much higher fill rate.The distinction between product fill rate and order fill rate is not significant in asingle product situation. When a firm is selling multiple products, however, thisdifference may be significant. For example, if most orders include 10 or moredifferent products that are to be shipped, an out-of-stock situation of one product results in the order not being filled from stock. The firm in this case may have apoor order fill rate even though it has good product fill rates. Tracking order fillrates is important when customers place a high value on the entire order beingfilled simultaneously.Difficulty: Moderate3. Describe the two types of ordering policies and the impact each has on safetyinventory.Answer: A replenishment policy consists of decisions regarding when to reorderand how much to reorder. These decisions determine the cycle and safetyinventories along with the fr and the CSL. There are several forms thatreplenishment policies may take. We restrict attention to two instances:1. Continuous review: Inventory is continuously tracked and an order for a lotsize Q is placed when the inventory declines to the reorder point (ROP). The time between orders may fluctuate given variable demand. When using a continuousreview policy, a manager has to account only for the uncertainty of demandduring the lead time (L).2. Periodic review: Inventory status is checked at regular periodic intervals andan order is placed to raise the inventory level to a specified threshold. In thiscase, the time between orders is fixed. The size of each order, however, can。
(完整word版)供应链管理第三版Unit1习题与答案

Chapter 1Un dersta nding the Supply ChainTrue/False1. A supply cha in in cludes only the orga ni zati ons directly in volved in suppl yingcomp onents n eeded for manu facturi ng.An swer: FalseDifficulty: Moderate2. A supply cha in con sists of all parties in volved, directly or in direct ly, in fulfilli nga customer request.An swer: TrueDifficulty: Moderate3. A supply cha in could be more accurately described as a supply n etwork orsupply web.An swer: TrueDifficulty: Moderate4. The objective of every supply cha in is to maximize the overall value gen erated.An swer: TrueDifficulty: Easy5. The objective of every supply cha in is to maximize the value gen erated for themanu facturi ng comp onent of the supply cha in.An swer: FalseDifficulty: Moderate6. Every supply cha in must in clude all 5 stages.An swer: FalseDifficulty: Easy7. The cycle view of a supply cha in holds that the processes in a supply cha in aredivided into a series of activities performed at the in terface betwee n successivestages.An swer: TrueDifficulty: Moderate8. The cycle view of a supply cha in holds that the processes in a supply cha in aredivided into 2 categories depe nding on whether they are in itiated in resp onse to or in an ticipati on of customer orders.An swer: FalseDifficulty: Moderate9. The push/pull view of a supply chain holds that the processes in a supply chainare divided into 2 categories depending on whether they are initiated in response to or in anticipation of customer orders.Answer: True Difficulty: Easy10. The push/pull view of a supply chain holds that the processes in a supply chainare divided into a series of activities performed at the interface betweensuccessive stages. Answer: False Difficulty: Easy11. The objective of the customer arrival process is to maximize the conversion ofcustomer arrivals to customer orders. Answer: True Difficulty: Moderate12. The objective of the customer arrival process is to ensure that orders are quicklyand accurately entered and communicated to other affected supply chainprocesses. Answer: False Difficulty: Moderate13. The objective of customer order entry is to ensure that orders are quickly andaccurately entered and communicated to other affected supply chain processes.Answer: True Difficulty: Moderate14. The objective of customer order entry is to maintain a record of product receiptand complete payment. Answer: False Difficulty: Hard15. The replenishment cycle occurs at the retailer/distributor interface.Answer: True Difficulty: Hard16. The replenishment cycle occurs at the distributor/manufacturer interface.Answer: FalseDifficulty: Hard17. The replenishment cycle is initiated when a supermarket runs out of stock of aparticular item. Answer: True Difficulty: Hard18. The replenishment cycle is initiated when customers load items intended forpurchase into their carts.Answer: FalseDifficulty: Hard19. The manufacturing cycle occurs at the distributor/manufacturer interface.Answer: True Difficulty: Moderate20. The manufacturing cycle occurs at the manufacturer/supplier interface.Answer: False Difficulty: Moderate21. The production scheduling process in the manufacturing cycle is similar to theorder entry process in the replenishment cycle. Answer: True Difficulty: Hard 22. The production scheduling process in the manufacturing cycle is similar to theorder fulfillment process in the replenishment cycle.Answer: FalseDifficulty: Hard23. The procurement cycle occurs at the manufacturer/supplier interface.Answer: True Difficulty: Easy24. The procurement cycle occurs at the retailer/distributor interface.Answer: FalseDifficulty: Easy25. The cycle view of the supply chain is useful when considering operationaldecisions, because it specifies the roles and responsibilities of each member ofthe supply chain. Answer: True Difficulty: Moderate26. The cycle view of the supply chain is useful when considering operationaldecisions, because it categorizes processes based on whether they are initiatedin response to or in anticipation of customer orders.Answer: FalseDifficulty: Moderate27. The push/pull view of the supply chain is useful when considering strategicdecisions relating to supply chain design, because it categorizes processes based on whether they are initiated in response to or in anticipation of customer orders.Answer: TrueDifficulty: Moderate28. The push/pull view of the supply chain is useful when considering strategicdecisions relating to supply chain design, because it specifies the roles andresponsibilities of each member of the supply chain. Answer: False Difficulty:Moderate29. Pull processes may also be referred to as reactive processes. An swer: TrueDifficulty: Easy30. Pull processes may also be referred to as speculative processes. An swer:FalseDifficulty: Easy31. Push processes may also be referred to as speculative processes. An swer:TrueDifficulty: Easy32. Push processes may also be referred to as reactive processes. An swer:FalseDifficulty: Easy33. All supply cha in activities within a firm bel ong to one of three macroprocesses CRM, ISCM and SRM.An swer: TrueDifficulty: Easy34. There is a close conn ecti on betwee n the desig n and man ageme nt ofsupply cha in flows and the success of a supply cha in.An swer: TrueDifficulty: EasyMultiple Choice1. Which of the following is not a stage within a typical supply chain?a. Customersb. Retailersc. Wholesalers/Distributorsd. Manu facturerse. All of the above are stages withi n a typical supply cha in.An swer: eDifficulty: Easy2.Which of the following is not a stage within a typical supply chain?a. Customersb. Retailersc. Wholesalers/Distributorsd. Mercha ndiserse. Comp onen t/Raw material suppliersAn swer: dDifficulty: Easy3. Supply chain profitability isa. not correlated to the value generated by the various stages of the supplychain.b.c. the total profit to be shared across all supply chain stages.the difference between the revenue generated from the customer and the overall cost across the supply chain.d. e. the total revenue generated by the distributor stage of the supply chain. b and c onlyAnswer: eDifficulty: Difficult4. Successful supply chain management requires which of the following decision phases?a. b.c.d.e. supply chain strategy/design supply chain planning supply chain operation all of the above a and b onlyAnswer: dDifficulty: Moderate5. The decision phases in a supply chain includea. b.c.d.e. production scheduling. customer relationship management. supply chain operation.supply chain orientation. all of the aboveAnswer: cDifficulty: Moderate6. The cycle view of a supply chain holds thata. b. the processes in a supply chain are divided into 2 categories. theprocesses in a supply chain are divided into a series of activitiesperformed at the interface between successive stages.c. all processes in a supply chain are initiated in response to a customerorder.d. all processes in a supply chain are performed in anticipation of customerorders.e. None of the above are true.Answer: bDifficulty: Moderate7. The push/pull view of a supply chain holds thata. the processes in a supply chain are divided into a series of activitiesperformed at the interface between successive stages.b. all processes in a supply chain are initiated in response to a customerorder.c. all response in a supply chain are performed in anticipation of customerorders.d. the processes in a supply chain are divided into 2 categories dependingon whether they are initiated in response to or in anticipation of customerorders.e. None of the above are true.Answer: d Difficulty: Moderate8. Which of the following is not a cycle in the supply chain cycle view?a. Analysis cycleb. Customer order cyclec. Replenishment cycled. Manufacturing cyclee. Procurement cycleAnswer: aDifficulty: Moderate9. Which of the following is not a cycle in the supply chain cycle view?a. Customer order cycleb. Replenishment cyclec. Manufacturing cycled. Procurement cyclee. All of the above are part of the supply chain cycle view.Answer: eDifficulty: Moderate10. The customer order cycle occurs at thea. customer/retailer interface.b. retailer/distributor interface.c. distributor/manufacturer interface.d. manufacturer/supplier interface.e. none of the aboveAnswer: aDifficulty: Easy11. Which of the following is not a process in the customer order cycle?a. Customer arrivalb. Customer qualificationc. Customer order entryd. Customer order fulfillmente. Customer order receivingAnswer: bDifficulty: Moderate12. Customer arrival refers toa. the point in time when the customer has access to choices and makes adecision regarding a purchase.b. the customer informing the retailer of what they want to purchase and theretailer allocating product to the customer.c. the process where product is prepared and sent to the customer.d. the process where the customer receives the product and takesownership.e. none of the aboveAnswer: aDifficulty: Moderate13. The objective of the customer arrival process is toa. get the correct orders to customers by the promised due date at thelowest possible cost.b. maintain a record of product receipt and complete payment.c. maximize the conversion of customer arrivals to customer orders.d. ensure that orders are quickly and accurately entered and communicatedto other affected supply chain processes.e. none of the aboveAnswer: cDifficulty: Easy14. Customer order entry isa. the point in time when the customer has access to choices and makes adecision regarding a purchase.b. the customer informing the retailer of what they want to purchase and theretailer allocating product to the customer.c. the process where product is prepared and sent to the customer.d. the process where the customer receives the product and takesownership.e. none of the aboveAnswer: bDifficulty: Moderate15. The objective of customer order entry is toa. get the correct orders to customers by the promised due date at thelowest possible cost.b. maintain a record of product receipt and complete payment.c. maximize the conversion of customer arrivals to customer orders.d. ensure that orders are quickly and accurately entered and communicatedto other affected supply chain processes.e. none of the aboveAnswer: dDifficulty: Easy16. Customer order fulfillment refers toa. the point in time when the customer has access to choices and makes adecision regarding a purchase.b. the customer informing the retailer of what they want to purchase and theretailer allocating product to the customer.c. the process where product is prepared and sent to the customer.d. the process where the customer receives the product and takesownership.e. none of the aboveAnswer: cDifficulty: Moderate17. The objective of customer order fulfillment is toa. get the correct orders to customers by the promised due date at the lowestpossible cost.b. maintain a record of product receipt and complete payment.c. maximize the conversion of customer arrivals to customer orders.d. ensure that orders are quickly and accurately entered and communicatedto other affected supply chain processes.e. none of the aboveAnswer: aDifficulty: Easy18. Customer order receiving isa. the point in time when the customer has access to choices and makes adecision regarding a purchase.b. the customer informing the retailer of what they want to purchase and theretailer allocates product to the customer.c. the process where product is prepared and sent to the customer.d. the process where the customer receives the product and takesownership.e. none of the aboveAnswer: dDifficulty: Moderate19. The replenishment cycle occurs at thea. customer/retailer interface.b. retailer/distributor interface.c. distributor/manufacturer interface.d. manufacturer/supplier interface.e. none of the aboveAnswer: bDifficulty: Easy20. The processes involved in the replenishment cycle includea. retail order receiving.b. retail order entry.c. retail order trigger.d. retail order fulfillmente. all of the aboveAnswer: eDifficulty: Moderate21. The processes included in the replenishment cycle include all of the followingexcepta. retail order receiving.b. retail order entry.c. retail order trigger.d. retail order fulfillmente. none of the aboveAnswer: eDifficulty: Moderate22.The processes included in the replenishment cycle include a. order arrival.b. production scheduling.c. retail trigger.d. manufacturing.e. receiving.Answer: cDifficulty: Moderate23.The replenishment cycle is initiated whena. the customer walks into the supermarket.b. the customer calls a mail order telemarketing center.c. customers load items intended for purchase into their carts.d. a supermarket runs out of stock of a particular item.e. a product is received into stock at a store.Answer: dDifficulty: Hard24.The manufacturing cycle occurs at the a. customer/retailer interface.b. retailer/distributor interface.c. distributor/manufacturer interface.d. manufacturer/supplier interface.e. none of the above Answer: cDifficulty: Easy25.The processes involved in the manufacturing cycle include a. receiving.b. manufacturing and shipping.c. production scheduling.d. order arrival.e. all of the aboveAnswer: eDifficulty: Moderate26.The processes involved in the manufacturing cycle include a. order trigger.b. production scheduling.c. order fulfillment.d. order entry.e. manufacturing order analysis.Answer: bDifficulty: Moderate27. The production scheduling process in the manufacturing cycle is similar to thea. order receiving process in the replenishment cycle.b. order fulfillment process in the replenishment cycle.c. order entry process in the replenishment cycle.d. order trigger process in the replenishment cycle.e. none of the aboveAnswer: cDifficulty: Hard28. The manufacturing and shipping process in the manufacturing cycle is equivalentto thea. order receiving process in the replenishment cycle.b. order fulfillment process in the replenishment cycle.c. order entry process in the replenishment cycle.d. order trigger process in the replenishment cycle.e. none of the aboveAnswer: b Difficulty: Hard29. The procurement cycle occurs at thea. customer/retailer interface.b. retailer/distributor interface.c. distributor/manufacturer interface.d. manufacturer/supplier interface.e. none of the aboveAnswer: d Difficulty: Easy30. The relationship between the manufacturer and supplier during the procurementcycle is very similar to the relationship betweena. customer and retailer.b. retailer and distributor.c. retailer and manufacturer.d. distributor and manufacturer.e. manufacturer and customer.Answer: dDifficulty: Moderate31. The cycle view of the supply chain is useful when considering operationaldecisions, becausea. it categorizes processes based on whether they are initiated in responseto or in anticipation of customer orders.b. it specifies the roles and responsibilities of each member of the supplychain.c. processes are identified as either reactive or speculative.d. it focuses on processes that are external to the firm.e. it focuses on processes that are internal to the firm.Answer: bDifficulty: Hard32. The push/pull view of the supply chain is useful when considering strategicdecisions relating to supply chain design, becausea. it categorizes processes based on whether they are initiated in responseto or in anticipation of customer orders.b. it specifies the roles and responsibilities of each member of the supplychain.c. it clearly defines the processes involved and the owners of each process.d. it focuses on processes that are external to the firm.e. it focuses on processes that are internal to the firm.Answer: aDifficulty: Hard33. Which of the following statements about pull processes is accurate?a. May also be referred to as speculative processes.b. Execution is initiated in anticipation of customer orders.c. At the time of execution, demand must be forecast.d. May also be referred to as reactive processes.e. None of the above are accurate.Answer: dDifficulty: Easy34. Which of the following is not an accurate statement about pull processes?a. May also be referred to as speculative processes.b. Execution is initiated in response to a customer order.c. At the time of execution, demand is known with certainty.d. May also be referred to as reactive processes.e. All of the above are accurate. Answer: aDifficulty: Easy35. Which of the following statements about push processes is accurate?a. May also be referred to as speculative processes.b. Execution is initiated in response to customer orders.c. At the time of execution, demand is known with certainty.d. May also be referred to as reactive processes.e. None of the above are accurate.Answer: aDifficulty: Easy36. Which of the following is not an accurate statement about push processes?a. May also be referred to as speculative processes.b. Execution is initiated in anticipation of customer orders.c. At the time of execution, demand must be forecast.d. May also be referred to as reactive processes.e. All of the above are accurate. Answer: dDifficulty: Easy37. Supply chain macro processes include which of the following?a. Customer Relationship Management (CRM)b. Internal Supply Chain Management (ISCM)c. Supplier Relationship Management (SRM)d. all of the abovee. none of the aboveAnswer: dDifficulty: Easy38. Supply chain macro processes include which of the following?39.39.40.40.41.41.42.42.43.43. a.b.c.d.e.Internal Relationship Management (IRM)Customer Relationship Management (CRM)External Relationship Management (ERM) SupplyChain Relationship Management (SCRM) none ofthe aboveAnswer: bDifficulty: ModerateSupply chain macro processes include which of the following? a. Internal Relationship Management (IRM)b. External Relationship Management (ERM)c. Supplier Relationship Management (SRM)d. Supply Chain Relationship Management (SCRM)e. none of the aboveAnswer: cDifficulty: ModerateActivities involved in the Customer Relationship Management (CRM) macro process includea. planning of internal production and storage.b. order fulfillment.c. marketing.d. supply planning.e. demand planning. Answer: cDifficulty: HardActivities involved in the Customer Relationship Management (CRM) macro process include all of the following excepta. demand planning.b. marketing.c. sales.d. order management.e. call center management.Answer: a Difficulty: HardActivities involved in the Internal Supply Chain Management (ISCM) macro process includea. marketing.b. order fulfillment.c. sales.d. order management.e. call center management.Answer: b Difficulty: HardActivities involved in the Internal Supply Chain Management (ISCM) macro process include all of the following excepta. planning of internal production and storage.b. order fulfillment.c. supply pla nning.d. dema nd pla nning.e. order man ageme nt. An swer: eDifficulty: Hard44.Activities in volved in the Supplier Relati on ship Man ageme nt (SRM)macro process in cludea. pla nning of in ter nal product ion and storage.b. order fulfillme nt.c. supply pla nning.d. supplier evaluati on a ndselect ion.e. order man ageme nt.An swer: dDifficulty: Moderate45. Activities in volved in the Supplier Relati on ship Man ageme nt (SRM)macro process in clude all of the follow ing excepta. n egotiati on of supply terms.b. desig n collaborati on.c. supply pla nning.d. supplier evaluati on and select ion.e. supply collaborati on.An swer: cDifficulty: Hard46.The phe nomenal success of 7-Eleve n Japa n is attributed toa. being in the right place at the right time.b. its supply cha in desig n and man ageme nt ability.c. hav ing 9000 locati ons.d. serv ing fresh food.e. none of the aboveAn swer: bDifficulty: Moderate47.A key issue facing Toyota isa. develop ing an in ter net market ing system.b. whether to specialize in a particular market.c. desig n of its global producti on and distributi on n etwork.d. how to impleme nt model cha nges.e. all of the aboveAn swer: cDifficulty: HardEssav/ProblemsExpla in the 3 decisi on phases (categories) that must be made in a successful 1.supply cha in.Answer : The 3 decision phases that occur within a supply chain are supply chain strategy (or design), supply chain planning and supply chain operation. Decisions relate to the flow of information, product and funds. The difference betweencategories depends upon the frequency of each decision and the time frame over which it has an impact. During the supply chain strategy phase, a companydetermines what the chain ' s configurations will be, how resources will beallocated, and what processes each stage will perform. This will establish thestructure of the supply chain for several years. Supply chain planning deals withdecisions with a time frame from 3 months up to a year. The planning phase must work within the constraints established in the strategy phase. Planning decisionsinclude which markets to supply from which locations, subcontracting ofmanufacturing, inventory policies and timing and size of marketing promotions.The supply chain operation phase operates on a weekly or daily time horizon and deals with decisions concerning individual customer orders.Difficulty: Hard2. Describe the cycle view of the processes within a supply chain.Answer: The cycle view divides the supply chain into a series of 4 cycles between the 5 different stages of a supply chain. The cycles are the customer order cycle,replenishment cycle, manufacturing cycle and procurement cycle. The customerorder cycle occurs at the customer/retailer interface and includes all processesdirectly involved in receiving and filling the customer. The replenishment cycleoccurs at the retailer/distributor interface and includes all processes involved inreplenishing retailer inventory. The manufacturing cycle typically occurs at thedistributor/manufacturer (or retailer/manufacturer) interface and includes allprocesses involved in replenishing distributor (or retailer) inventory. Theprocurement cycle occurs at the manufacturer/supplier interface and includes allprocesses necessary to ensure that the materials are available for manufacturing according to schedule.Difficulty: Moderate3. Explain the push/pull view of the processes within a supply chain.Answer: The push/pull view of the supply chain divides supply chain processesinto two categories based on whether they are executed in response to acustomer order or in anticipation of customer orders. Pull processes are initiatedin response to a customer order. Push processes are initiated and performed inanticipation of customer orders. The push/pull boundary separates pushprocesses from pull processes. This view is very useful when consideringstrategic decisions relating to supply chain design, because it forces a moreglobal consideration of supply chain processes as they relate to the customer.Difficulty: Moderate4. Explain the three macro processes within a supply chain.Answer: All processes within a supply chain can be classified into three macroprocesses which are Customer Relationship Management (CRM), Internal Supply Chain Management (ISCM), and Supplier Relationship Management (SRM).Customer Relationship Management (CRM) includes all processes that focus onthe interface between the firm and its customers such as marketing, sales, callcenter management and order management. Internal Supply Chain Management (ISCM) includes all processes that are internal to the firm such as preparation ofdemand and supply plans, preparation of inventory management policies, orderfulfillment and planning of capacity. Supplier Relationship Management (SRM)includes all processes that focus on the interface between a firm and its suppliers such as evaluation and selection of suppliers, negotiation of supply terms andcommunication regarding new products and orders.Difficulty: Moderate5. Explain why supply chain flows are important.Answer: Supply chain flows are important, because there is a close connectionbetween the design and management of supply chain flows (product, information, and cash) and the success of a supply chain. The success of many companiescan be directly traced to the design and management of an appropriate supplychain. The failure of many businesses can be linked directly to their inability toeffectively design and manage supply chain flows.Difficulty: Moderate。
供应链管理 第三版 Unit8 习题与答案

Chapter 8Aggregate Planning in the Supply ChainTrue/False1. The goal of aggregate planning is to satisfy demand in a way that minimizesprofit.Answer: FalseDifficulty: Easy2. Aggregate planning is a process by which a company determines levels ofcapacity, production, subcontracting, inventory, stockouts, and even pricing overa specified time horizon.Answer: TrueDifficulty: Moderate3. Aggregate planning solves problems involving aggregate decisions rather thanstock keeping unit (SKU) level decisions.Answer: TrueDifficulty: Easy4. Traditionally, much of aggregate planning is focused within an enterprise andmay not always be seen as a part of supply chain management.Answer: TrueDifficulty: Moderate5. Aggregate planning is an important supply chain issue because, to be effective, itrequires inputs from throughout the supply chain, but its results have little impact on the supply chain.Answer: FalseDifficulty: Moderate6. Short-term production serves as a broad blueprint for operations and establishesthe parameters within which aggregate planning decisions are made.Answer: FalseDifficulty: Easy7. The aggregate planning problem is concerned with determining the productionlevel, inventory level, and capacity level (internal and outsourced) for each period that maximizes the firm’s profit over the planning horizon.Answer: TrueDifficulty: Moderate8. To create an aggregate plan, a company must specify the planning horizon forthe plan and the duration of each period within the planning horizon.Answer: TrueDifficulty: Easy9. A planning horizon is usually between three and five years.Answer: FalseDifficulty: Moderate10. A poor aggregate plan can result in improved sales and profits if the availableinventory and capacity are unable to meet demand.Answer: FalseDifficulty: Easy11. A poor aggregate plan may result in a large amount of excess inventory andcapacity, thereby raising costs.Answer: TrueDifficulty: Moderate12. The aggregate planner must make a trade-off between capacity, inventory, andbacklog costs.Answer: TrueDifficulty: Moderate13. An aggregate plan that increases one cost typically results in the increase of theother two.Answer: FalseDifficulty: Moderate14. The time flexible strategy is where the production rate is synchronized with thedemand rate by varying machine capacity or hiring and laying off employees asthe demand rate varies.Answer: FalseDifficulty: Hard15. The time flexible strategy is where workforce (capacity) is kept stable but thenumber of hours worked is varied over time in an effort to synchronize production with demand.Answer: TrueDifficulty: Moderate16. The mixed strategy is where a stable machine capacity and workforce aremaintained with a constant output rate with inventory levels fluctuating over time.Answer: FalseDifficulty: Hard17. Most strategies that an aggregate planner actually uses are in combination, andare referred to as mixed strategies.Answer: TrueDifficulty: Easy18. A highly effective tool for a company to use when it tries to maximize profits whilebeing subjected to a series of constraints is aggregate programming.Answer: FalseDifficulty: Moderate19. To improve the quality of these aggregate plans, forecast errors must be takeninto account when formulating aggregate plans.Answer: TrueDifficulty: Moderate20. Forecasting errors are dealt with in aggregate plans using either safety backlogor safety capacity.Answer: FalseDifficulty: Moderate21. Safety inventory is defined as inventory held to satisfy demand that is higher thanforecasted.Answer: TrueDifficulty: Easy22. Safety capacity is defined as capacity used to satisfy demand that is lower thanforecasted.Answer: FalseDifficulty: Easy23. Companies should work with downstream partners to produce forecasts and withupstream partners to determine constraints when doing aggregate planning.Answer: TrueDifficulty: Easy24. The aggregate plan should be viewed primarily as an in-house tool that does notneed to be communicated to supply chain partners.Answer: FalseDifficulty: Easy25. Given that forecasts are always wrong to some degree, the aggregate planneeds to have some flexibility built into it if it is to be useful.Answer: TrueDifficulty: Moderate26. A manager should perform sensitivity analysis on the inputs into an aggregateplan to choose the best solution for the range of possibilities that could occur.Answer: TrueDifficulty: Moderate27. As inputs into the aggregate plan change, managers do not need to makechanges to the aggregate plan.Answer: FalseDifficulty: Easy28. As capacity utilization increases, it becomes less important to perform aggregateplanning.Answer: FalseDifficulty: ModerateMultiple Choice1. The process by which a company determines levels of capacity, production,subcontracting, inventory, stockouts, and even pricing over a specified timehorizon isa. aggregate planning.b. detail planning.c. inventory planning.d. sales planning.e. all of the aboveAnswer: aDifficulty: Moderate2. The goal of aggregate planning is toa. dissatisfy customers in a way that maximizes profit.b. dissatisfy customers in a way that minimizes profit.c. satisfy demand in a way that maximizes profit.d. satisfy demand in a way that minimizes profit.e. none of the aboveAnswer: cDifficulty: Easy3. Aggregate planning solves problems involvinga. aggregate decisions and stock keeping unit (SKU) level decisions.b. aggregate decisions or stock keeping unit (SKU) level decisions.c. aggregate decisions rather than stock keeping unit (SKU) level decisions.d. stock keeping unit (SKU) level decisions rather than aggregate decisions.e. b and c onlyAnswer: cDifficulty: Easy4. Aggregate planning, to be effective, requires inputs froma. all customers.b. all departments.c. all suppliers.d. throughout the supply chain.e. throughout the company.Answer: dDifficulty: Moderate5. Much of aggregate planning has traditionally been focuseda. on short-term production scheduling.b. on customer relationship management.c. within an enterprise.d. beyond enterprise boundaries.e. all of the aboveAnswer: cDifficulty: Moderate6. Which of the following are not operational parameters the aggregate planner isconcerned with?a. production rateb. workforcec. overtimed. backorderse. inventory on handAnswer: dDifficulty: Moderate7. The operational parameter concerned with the number of units completed perunit time (such as per week or per month) isa. production rate.b. workforce.c. overtime.d. backlog.e. inventory on hand.Answer: aDifficulty: Easy8. The operational parameter concerned with the number of workers/units ofcapacity needed for production isa. production rate.b. workforce.c. overtime.d. backlog.e. inventory on hand.Answer: bDifficulty: Easy9. The operational parameter concerned with the amount of overtime productionplanned isa. production rate.b. workforce.c. overtime.d. backlog.e. inventory on hand.Answer: cDifficulty: Easy10. The operational parameter concerned with demand not satisfied in the period inwhich it arises, but carried over to future periods isa. production rate.b. workforce.c. overtime.d. backlog.e. inventory on hand.Answer: dDifficulty: Easy11. The operational parameter concerned with the planned inventory carried over thevarious periods in the planning horizon isa. production rate.b. workforce.c. overtime.d. backlog.e. inventory on hand.Answer: eDifficulty: Easy12. The operational parameter concerned with the number of units of machinecapacity needed for production isa. machine capacity level.b. subcontracting.c. overtime.d. backlog.e. inventory on hand.Answer: aDifficulty: Easy13. The operational parameter concerned with the subcontracted capacity requiredover the planning horizon isa. machine capacity level.b. subcontracting.c. overtime.d. backlog.e. inventory on hand.Answer: cDifficulty: Easy14. The aggregate plana. serves as a broad blueprint for operations.b. establishes the parameters within which short-term production anddistribution decisions are made.c. allows the supply chain to alter capacity allocations and change supplycontracts.d. all of the abovee. b and c onlyAnswer: dDifficulty: Moderate15. Aggregate planning is concerned with determininga. the production level, sales level, and capacity for each period.b. the demand level, inventory level, and capacity for each period.c. the production level, inventory level, and capacity for each period.d. the production level, staffing level, and capacity for each period.e. none of the aboveAnswer: cDifficulty: Moderate16. To create an aggregate plan, a company must specifya. the planning horizon for the plan.b. the duration of each period within the planning horizon.c. key information required.d. all of the abovee. a and b onlyAnswer: dDifficulty: Moderate17. The planning horizon isa. the time period over which the aggregate plan is to produce a solution.b. the duration of each time period in the aggregate plan.c. the length of time required to produce the aggregate plan.d. the solution to the aggregate plan.e. none of the aboveAnswer: aDifficulty: Easy18. The length of the planning horizon is usually betweena. one and three months.b. three and eighteen months.c. one and three years.d. three and five years.e. none of the aboveAnswer: bDifficulty: Moderate19. Which of the following is not information needed by the aggregate planner?a. demand forecast for each period in the planning horizonb. production costsc. labor costsd. cost of subcontracting productione. cost of changing the demand forecastAnswer: eDifficulty: Moderate20. The cost of changing capacity includes thea. cost of adding machine capacity.b. cost of reducing machine capacity.c. cost of hiring workforce.d. cost of laying off workforce.e. all of the aboveAnswer: eDifficulty: Easy21. Which of the following is not a cost of changing capacity?a. cost of adding machine capacityb. cost of hiring workforcec. cost of laying off workforced. cost of overtimee. cost of reducing machine capacityAnswer: dDifficulty: Moderate22. Which of the following is not a constraint the aggregate planner needs toconsider?a. limits on stockouts and backlogsb. limits on overtimec. limits on sales commissionsd. limits on layoffse. limits on capital availableAnswer: cDifficulty: Moderate23. A poor aggregate plan can result ina. appropriate inventory levels.b. efficient use of capacity.c. better sales and lost profits.d. lost sales and lost profits.e. lost sales and better profits.Answer: dDifficulty: Hard24. The fundamental trade-offs available to an aggregate planner are betweena. capability, inventory, and backlog costs.b. capability, inventory, and sales costs.c. capacity, inventory, and backlog costs.d. capacity, inventory, and sales costs.e. none of the aboveAnswer: cDifficulty: Easy25. Which of the following is not a distinct aggregate planning strategy for achievingbalance between capacity, inventory, and backlog costs?a. adjustable strategyb. Chase strategyc. level strategyd. mixed strategye. time flexible strategyAnswer: aDifficulty: Easy26. The strategy where the production rate is synchronized with the demand rate byvarying machine capacity or hiring and laying off employees as the demand rate varies is thea. adjustable strategy.b. Chase strategy.c. level strategy.d. mixed strategy.e. time flexible strategy.Answer: bDifficulty: Moderate27. The strategy where workforce (capacity) is kept stable but the number of hoursworked is varied over time in an effort to synchronize production with demand is thea. adjustable strategy.b. Chase strategy.c. level strategy.d. mixed strategy.e. time flexible strategy.Answer: eDifficulty: Moderate28. The strategy where a stable machine capacity and workforce are maintained witha constant output rate, with inventory levels fluctuating over time, is thea. adjustable strategy.b. Chase strategy.c. level strategy.d. mixed strategy.e. time flexible strategy.Answer: cDifficulty: Hard29. Most strategies that an aggregate planner actually uses are in combination andare referred to as thea. adjustable strategy.b. Chase strategy.c. level strategy.d. mixed strategy.e. time flexible strategy.Answer: dDifficulty: Easy30. A highly effective tool for a company to use when it tries to maximize profits whilebeing subjected to a series of constraints isa. aggregate programming.b. distribution programming.c. production programming.d. linear programming.e. manufacturing programming.Answer: dDifficulty: Moderate31. When formulating aggregate plans,a. forecast errors have no impact.b. forecast errors must be taken into account.c. forecast accuracy is assumed.d. forecast accuracy is not a factor.e. none of the aboveAnswer: bDifficulty: Moderate32. Forecasting errors are dealt with usinga. safety backlog.b. safety capacity.c. safety inventory.d. all of the abovee. b and c onlyAnswer: eDifficulty: Moderate33. Inventory held to satisfy demand that is higher than forecasted isa. safety backlog.b. safety capacity.c. safety inventory.d. safety sales.e. safety workforce.Answer: cDifficulty: Easy34. Capacity used to satisfy demand that is higher than forecasted isa. safety backlog.b. safety capacity.c. safety inventory.d. safety sales.e. safety workforce.Answer: bDifficulty: Easy35. Which of the following is an approach a company can use to create a buffer forforecast error using safety inventory?a. overtimeb. carry extra workforce permanentlyc. build and carry extra inventoriesd. subcontractinge. purchase capacity or product from an open or spot marketAnswer: aDifficulty: Easy36. Which of the following is not an approach a company can use to create a bufferfor forecast error using safety capacity?a. overtimeb. carry extra workforce permanentlyc. build and carry extra inventoriesd. subcontractinge. purchase capacity or product from an open or spot marketAnswer: cDifficulty: Easy37. Aggregate planning should consider information froma. only the enterprise as its breadth of scope.b. downstream partners to produce forecasts.c. upstream partners to determine constraints.d. all of the abovee. b and c onlyAnswer: dDifficulty: Easy38. The quality of the aggregate plan can be improved by using information froma. only the local firm.b. only downstream partners.c. only upstream partners.d. all parts of the supply chain.e. none of the aboveAnswer: bDifficulty: Moderate39. The aggregate plan should be communicated toa. only the local firm.b. only downstream partners.c. only upstream partners.d. all supply chain partners who will be affected by it.e. none of the aboveAnswer: cDifficulty: Moderate40. The aggregate plan needs toa. be a final product because changes are disruptive to the supply chain.b. be considered fixed because forecasts are usually accurate.c. have some flexibility built into it because forecasts are always wrong.d. have some flexibility built into it because forecasts are usually right.e. none of the aboveAnswer: cDifficulty: Moderate41. How frequently should the aggregate plan be rerun?a. weeklyb. monthlyc. every 3 to 8 monthsd. as inputs to the aggregate plan changee. neverAnswer: dDifficulty: Hard42. As capacity utilization increases,a. it becomes less important to perform aggregate planning.b. it becomes more important to perform aggregate planning.c. it does not affect the importance of performing aggregate planning.d. it lessens the importance of aggregate planning.e. none of the aboveAnswer: bDifficulty: ModerateEssay/Problems1. Discuss the primary objective and operational parameters of aggregate planning.Answer: The goal of aggregate planning is to satisfy demand in a way thatmaximizes profit. Aggregate planning is a process by which a companydetermines levels of capacity, production, subcontracting, inventory, stockouts,and even pricing over a specified time horizon. The aggregate planner’s mainobjective is to identify the following operational parameters over the specifiedtime horizon:• Production rate: the number of units completed per unit time (such as per week or per month).• Workforce: the number of workers/units of capacity needed for production.• Overtime: the amount of overtime production planned.• Machine capacity level: the number of units of machine capacity needed forproduction.• Subcontracting: the subcontracted capacity required over the planning horizon.• Backlog: demand not satisfied in the period in which it arises but carried over to future periods.• Inventory on hand: the planned inventory carried over the various periods in the planning horizon.The aggregate plan serves as a broad blueprint for operations and establishesthe parameters within which short-term production and distribution decisions are made. The aggregate plan allows the supply chain to alter capacity allocationsand change supply contracts.Difficulty: Moderate2. Discuss the information required for aggregate planning.Answer: An aggregate planner requires the following information:• Demand forecast F t for each Period t in the planning horizon that extends over T periods• Production cos ts• Labor costs, regular time ($/hour), and overtime costs ($/hour)• Cost of subcontracting production ($/unit or $/hour)• Cost of changing capacity; specifically, cost of hiring/laying off workforce($/worker) and cost of adding or reducing machine capacity ($/machine)• Labor/machine hours required per unit• Inventory holding cost ($/unit/period)• Stockout or backlog cost ($/unit/period)• Constraints:• Limits on overtime• Limits on layoffs• Limits on capital available• Limits on stockouts and ba cklogs• Constraints from suppliers to the enterpriseThis information is used to create an aggregate plan that in turn helps a company make the following determinations:• Production quantity from regular time, overtime, and subcontracted time:used to determine number of workers and supplier purchase levels.• Inventory held: used to determine how much warehouse space andworking capital is needed.• Backlog/stockout quantity: used to determine what the customer servicelevels will be.• Workforce hired/laid off: used to determine any labor issues that will beencountered.• Machine capacity increase/decrease: used to determine if newproduction equipment needs to be purchased or idled.The quality of an aggregate plan has a significant impact on the profitability of a firm. A poor aggregate plan can result in lost sales and lost profits if the available inventory and capacity are unable to meet demand. A poor aggregate plan mayalso result in a large amount of excess inventory and capacity, thereby raisingcosts. Therefore, aggregate planning is a very important tool in helping a supply chain maximize profitability.Difficulty: Hard3. Explain the basic strategies that an aggregate planner has available to balancethe various costs and meet demand.Answer: There are essentially three distinct aggregate planning strategies forachieving balance between these costs. These strategies involve trade-offsbetween capital investment, workforce size, work hours, inventory, andbacklogs/lost sales. Most strategies that a planner actually uses are acombination of these three and are referred to as mixed strategies. The threestrategies are as follows:1. Chase strategy—using capacity as the lever: With this strategy, the productionrate is synchronized with the demand rate by varying machine capacity or hiring and laying off employees as the demand rate varies. In practice, achieving thissynchronization can be very problematic because of the difficulty in varyingcapacity and workforce on short notice. This strategy can be expensive toimplement if the cost of varying machine or labor capacity over time is high. Itcan also have a significant negative impact on the morale of the workforce. TheChase strategy results in low levels of inventory in the supply chain and highlevels of change in capacity and workforce. It should be used when the cost ofcarrying inventory is very expensive and costs to change levels of machine andlabor capacity are low.2. Time flexibility strategy—using utilization as the lever: This strategy may beused if there is excess machine capacity (i.e., if machines are not used twentyfour hours a day, seven days a week). In this case, the workforce (capacity) iskept stable but the number of hours worked is varied over time in an effort tosynchronize production with demand. A planner can use variable amounts ofovertime or a flexible schedule to achieve this synchronization. Although thisstrategy does require that the workforce be flexible, it avoids some of theproblems associated with the Chase strategy, most notably changing the size of the workforce. This strategy results in low levels of inventory but with loweraverage utilization. It should be used when inventory carrying costs are relatively high and machine capacity is relatively inexpensive.3. Level strategy—using inventory as the lever: With this strategy, a stablemachine capacity and workforce are maintained with a constant output rate.Shortages and surpluses result in inventory levels fluctuating over time. Hereproduction is not synchronized with demand. Either inventories are built up inanticipation of future demand or backlogs are carried over from high- to low-demand periods. Employees benefit from stable working conditions. A drawback associated with this strategy is that large inventories may accumulate andcustomer orders may be delayed. This strategy keeps capacity and costs ofchanging capacity relatively low. It should be used when inventory carrying andbacklog costs are relatively low.Difficulty: Moderate4. Discuss key issues to be considered when implementing aggregate planning.Answer: 1. Think beyond the enterprise to the entire supply chain. Mostaggregate planning done today takes only the enterprise as its breadth of scope.However, there are many factors outside the enterprise throughout the supplychain that can dramatically impact the optimal aggregate plan. Therefore, avoidthe trap of only thinking about your enterprise when aggregate planning. Workwith partners downstream to produce forecasts, with upstream partners todetermine constraints, and with any other supply chain entities that can improve the quality of the inputs into the aggregate plan. As the plan is only as good asthe quality of the inputs, using the supply chain to increase the quality of theinputs will greatly improve the quality of the aggregate plan. Also make sure tocommunicate the aggregate plan to all supply chain partners who will be affected by it.2. Make plans flexible because forecasts are always wrong. Aggregate plans arebased on forecasts of future demand. Given that these forecasts are alwayswrong to some degree, the aggregate plan needs to have some flexibility builtinto it if it is to be useful. By building flexibility into the plan, when future demand changes, or other changes occur, such as increases in costs, the plan canappropriately adjust to handle the new situation. A manager should performsensitivity analysis on the inputs into an aggregate plan. Using sensitivityanalysis on the inputs into the aggregate plan will enable the planner to choosethe best solution for the range of possibilities that could occur.3. Rerun the aggregate plan as new data emerges. Aggregate plans provide amap for the next three to eighteen months. This does not mean that a firm should only run aggregate plans once every three to eighteen months. As inputs into the aggregate plan change, managers should use the latest values of these inputsand rerun the aggregate plan. By using the latest inputs, the plan will avoidsuboptimization based on old data and will produce a better solution. Forinstance, as new demand forecasts become available, aggregate plans shouldbe reevaluated.4. Use aggregate planning as capacity utilization increases. Surprisingly, manycompanies do not create aggregate plans and instead rely solely on orders from their distributors or warehouses to determine their production schedules. Theseorders are driven either by actual demand or through inventory managementalgorithms. If a company has no trouble efficiently meeting demand this way,then one could claim the lack of aggregate planning may not significantly harmthe company. However, when utilization becomes high and capacity is an issue, relying on orders to set the production schedule can lead to capacity problems.When utilization is high, the likelihood of producing for all the orders as theyarrive is very low. Planning needs to be done to best utilize the capacity to meet the forecasted demand. Therefore, as capacity utilization increases, it becomesmore important to perform aggregate planning.Difficulty: Moderate。
供应链设计与管理(第3版)课后答案,选译

》》》》》》》》》》》》供应链设计与管理——概念、战略与案例研究(第3版)《《《《《《《《《《《《《(选译)第一章1.纵向一体化的企业拥有、管理并运作所有相关的业务职能。
横向一体化的企业由一些独立运营的企业组成,公司总部提供品牌、指导和一般战略。
比较并对比这两种类型企业的供应链战略。
答:纵向一体化企业旨在加强公司各业务成分之间的互动,而且经常集中地管理它们。
这样的结构,可以更容易地通过中央决策除去供应链中的不同部分之间的冲突来实现系统的整体目标。
在横向一体化公司,协调公司内部各业务的供应链通常是没有效益的。
事实上,如果横向一体化企业中的每个企业都专注于它的核心功能,并以最佳状态运行,就可能达到总体的全局最优效果。
2.如果一个企业是完全纵向一体化的,有效供应链管理是否仍然重要?答:有效供应链管理对于完全纵向一体化的公司仍然重要。
在这样的组织结构,公司的不同部门负责不同业务,通常它们都有自己的内部目标,而这些目标有时是无关联的。
这可能是由于缺乏部门之间的沟通或高层的激励政策。
比如,如果只依据收益来评估销售部门, 只依据成本来评估制造部门,公司的总体利润就难以达到最大化。
有效的供应链管理在全局最优业务操作中仍是必要的。
3.考虑一个企业重新设计其物流网络。
为数不多的几个集中仓库的优点是什么?大量靠近最终用户的仓库的优点是什么?答:少数位于市中心的仓库,允许公司利用风险分担,以提高服务水平并降低库存水平和成本。
不过,对外运输成本通常较高,交货间隔期较长。
另一方面,企业可以通过建立更多的靠近最终用户的仓库,以减少对外运输成本和交货间隔期。
然而,这种类型的系统将会使总库存水平和成本增加、规模经济下降、仓储费用增加,并且可能增加对内运输费用。
4.考虑一个企业选择运输服务提供商。
使用卡车承运商的优点是什么?使用诸如UPS这样的包裹速递公司的优点是什么?答:企业对运输服务的选择在很大程度上取决于公司要运输的产品的类型和大小,库存和交付的策略,以及对灵活性的需求:1.如果是大量而稳定的从仓库到需求点(店)运送大件物品或小件物品,货车运输会更好。
- 1、下载文档前请自行甄别文档内容的完整性,平台不提供额外的编辑、内容补充、找答案等附加服务。
- 2、"仅部分预览"的文档,不可在线预览部分如存在完整性等问题,可反馈申请退款(可完整预览的文档不适用该条件!)。
- 3、如文档侵犯您的权益,请联系客服反馈,我们会尽快为您处理(人工客服工作时间:9:00-18:30)。
》》》》》》》》》》》》供应链设计与管理——概念、战略与案例研究(第3版)《《《《《《《《《《《《《(选译)第一章1.纵向一体化的企业拥有、管理并运作所有相关的业务职能。
横向一体化的企业由一些独立运营的企业组成,公司总部提供品牌、指导和一般战略。
比较并对比这两种类型企业的供应链战略。
答:纵向一体化企业旨在加强公司各业务成分之间的互动,而且经常集中地管理它们。
这样的结构,可以更容易地通过中央决策除去供应链中的不同部分之间的冲突来实现系统的整体目标。
在横向一体化公司,协调公司内部各业务的供应链通常是没有效益的。
事实上,如果横向一体化企业中的每个企业都专注于它的核心功能,并以最佳状态运行,就可能达到总体的全局最优效果。
2.如果一个企业是完全纵向一体化的,有效供应链管理是否仍然重要?答:有效供应链管理对于完全纵向一体化的公司仍然重要。
在这样的组织结构,公司的不同部门负责不同业务,通常它们都有自己的内部目标,而这些目标有时是无关联的。
这可能是由于缺乏部门之间的沟通或高层的激励政策。
比如,如果只依据收益来评估销售部门, 只依据成本来评估制造部门,公司的总体利润就难以达到最大化。
有效的供应链管理在全局最优业务操作中仍是必要的。
3.考虑一个企业重新设计其物流网络。
为数不多的几个集中仓库的优点是什么?大量靠近最终用户的仓库的优点是什么?答:少数位于市中心的仓库,允许公司利用风险分担,以提高服务水平并降低库存水平和成本。
不过,对外运输成本通常较高,交货间隔期较长。
另一方面,企业可以通过建立更多的靠近最终用户的仓库,以减少对外运输成本和交货间隔期。
然而,这种类型的系统将会使总库存水平和成本增加、规模经济下降、仓储费用增加,并且可能增加对内运输费用。
4.考虑一个企业选择运输服务提供商。
使用卡车承运商的优点是什么?使用诸如UPS这样的包裹速递公司的优点是什么?答:企业对运输服务的选择在很大程度上取决于公司要运输的产品的类型和大小,库存和交付的策略,以及对灵活性的需求:1.如果是大量而稳定的从仓库到需求点(店)运送大件物品或小件物品,货车运输会更好。
一个很好的例子就是仓库到超市之间的杂货送货。
要注意,在本例中,我们希望的效果是货物量达到卡车满载量。
2.如果由制造商/仓库直接递送顾客的是相对低成本的项目,那么用快递公司更合适。
此外,快递公司可以根据客户的个人需要灵活的提供不同的运输方式。
5.企业库存水平较高有什么优点?有什么缺点?库存水平低有什么优点和缺点?答:1.高库存水平i. 优点:订单满足率高(服务水平)和订单执行快速。
ii. 缺点:持有成本和库存机会成本高,有因时间和报废导致价格下跌的危险,需要更多的仓储空间。
2.低库存水平i. 优点:低库存持有和仓储成本。
ii.缺点:较高缺货风险和较低的服务水平。
第二章1.服务和库存水平之间存在什么样的关系?答:一般来说,高库存水平更容易保持高服务水平。
然而,现代库存管理技术将可能不像过去一样需要通过增加库存水平来提高服务水平。
2.管理层在确定一个目标服务水平时应考虑哪些因素?答:目标服务水平取决于产品的关键性任务。
例如,考虑一个配件供应商的设备,每一个小时的停机时间是非常昂贵的。
在这种情况下,我们希望那些供应商公司的管理部门指定服务水平接近100%。
市场环境在决定目标服务水平时也扮演了重要的角色。
对于商品,消费者会期望其服务水平高,因为他们可以轻易地找到替代品。
然而,如果该产品的价值与其竞争对手有明显的差异,较低的服务水平是有可能被接受的。
例如,高端服务器,如果制造商脱销时客户愿意等待1-2周,显然是认为它优于市场上其他产品。
3.面对高需求变动会有什么不利的地方?是否会有什么好处?答:对于高需求变动有隐式和显式的坏处。
例如:1.安全库存的水平与需求变动是成正比的,即,需求变动越高,库存持有成本就越高。
2.从制造商的角度来看,高需求变动意味着设备将极大地波动,需求低时设备将闲置不用。
3.从管理的角度来看,高变动性使规划变得复杂,这需要额外的资源,精密的模型和工具。
另一方面,如果一个公司成功地实施战略应对高需求变动,而竞争对手并不成功,它便可以利用这个优势来增加市场份额或收入。
4.你认为什么时候两个商店对一个产品的需求是正相关的?什么时候又会是负相关的?答:如果两个商店的定价策略、服务水平和服务质量都相似,那我们就可以将这两个商店的需求看作正相关。
然而,假设整体市场需求是相对稳定的,其中一个商店搞促销,在这种情况下,我们就得将该促销活动看作从另家商店夺取销售量,那么这两个商店的需求将呈负相关。
第三章1.为什么对于一个企业而言,定期检查物流网络设计很重要?随着时间的推移,一个企业对其物流网络的需求如何变化?答:影响物流网络性能的因素不是静态的,就是说,它们是随时间变化的。
这些因素包括需求、产品设计、物流网络中的各种成本、法规、合同等。
这些因素需要定期评估来确保现有的配置令人满意、操作环境是最新的。
例如,服务水平需求可能会改变,由于竞争加剧通常意味着需要缩短客户订单交货期,这就要要求该公司重新设计其物流网络和建立新的接近最终用户的仓库。
2.第2节中我们看到整车运输费率结构是不对称的,为什么?答:如果卡车在返回时空载,那么TL率会变高。
联系2.2.2节的例子,卡车从伊利诺斯州(工业中心)到纽约空载回来的概率低于从纽约到伊利诺斯州相应的概率,解释了这两个城市之间的不对称成本结构。
3.给组成仓库搬运成本、固定成本和储存成本的具体内容。
答:1.搬运成本i. 材料处理中的工人劳动成本。
ii.用来将货物送至仓库的传送带、叉车、自动引导车辆(AGVs)等的成本。
这些成本有两个成分:与货物运输距离成线性正比的可变成本;与材料搬运系统的日产需求成正比的设备的采购成本,但是以非线性的方式,因为设备是以离散数量购买。
2.固定成本i. 购买或租赁土地的成本。
ii.仓库的维护成本和操作成本,包括年度折旧和公用事业费用。
Iii.货架成本,它取决于仓库容量。
iv.保险设施的成本。
3.存储成本i.库存持有资本的机会成本。
Ii.货物在仓库滞留期间价格贬值的成本。
注意,其中包括需要回收的废弃库存的风险。
4.什么是仿真?它如何帮助解决复杂的物流问题?答:仿真是一个受欢迎的绩效评估和建模工具,用于无法评估分析的复杂的随机系统。
一个仿真模型可以密切反映系统的真实状况,模拟其行为,但它也有些缺点:模拟是一个描述性的工具,即,它不能为系统的输入提供最优值。
对于一系列给定的输入,它从系统中生成一些范例输出,用来计算绩效指标的统计估算。
同时,精密的大型仿真模型系统需要大量的开发工作,通常运行时间很长。
因此,我们提倡一个两阶段的方法来解决困难的物流问题:1.使用数学优化模型来生成大量的优秀候选解决方案,将最重要的成本组件考虑进去。
2.使用一个详尽的仿真模型来评估第一阶段生成的候选方案。
第五章1.讨论一下各因素如何有助于减轻牛鞭效应的影响:电子商务和互联网、快递送货、合作预测、天天低价、供应商管理库存、供应合同。
答:a.电子商务和互联网允许上游商家,例如,供应商,获得更准确的需求信息。
它减轻了牛鞭效应,防止失真和误解的需求信息,并减少订货提前期。
b.快递送货可减少交货期和相关的需求差异。
(该公式在4.2.1和4.2.2节)在这个系统中,需求的可变性与提前期是成正比的。
C.合作预测有助于所有供应链中的利益相关者到达一个通用的、公认的最终用户需求预测从而减少牛鞭效应。
d.定期促销活动是人为的达到需求高峰和低谷,增加了客户需求的差异,放大了牛鞭效应。
通过日常低价,可以预防这些需求波动,部分的缓解牛鞭效应。
e.供应商管理库存允许供应商监控下游需求,以便明确决定保留多少库存,给它的客户输送多少。
因此,供应商不一定要依靠订单数据来预测需求来降低牛鞭效应。
f.供应合同调整供应链中的激励机制,通过确定商定的供应限制减少不确定需求,从而减少牛鞭效应。
2.讨论在供应链中能够缩短提前期的5种方法。
答:以下策略可以缩短供应链中的提前期:1.使用EDI(电子数据交换),减少订购流程中的信息提前期。
2.使用交叉运输减少/消除库存消耗的时间。
3.缺货时与附近的零售商分享库存减少提前期。
4.在整个供应链中共享需求信息,以便能够响应需求的快速波动。
5.使用延迟差异策略,让供应链中的通用产品尽可能的向下游推进,使供应链能适应一系列的相关产品的需求。
6.实施VMI(供应商管理库存)策略,这样供应商可以在库存水平变化上有更多的响应。
7.运用快递服务,如UPS减少运输提前期。
8.采用新技术,如机自动化来降低生产提前期。
第六章1.分别讨论推动式供应链和拉动式供应链的优点。
答:推动式供应链具有以下优点:1)利用了长期预测和规划2)系统的存储库存。
如果产品是通用的,库存可以马上满足客户需求,减少客户等待时间。
拉动式供应链具有以下优点:1)可使库存水平达到最小2)产品差异化时可以更好地匹配供应和需求3)减少了生产计划对预测的依赖2.亚马逊网上商店、Peapod公司、戴尔和一些家具制造商都使用了推-拉式供应链战略,尝试描述一下每一家公司都是如何运用风险分担概念的。
答:1.亚马逊:亚马逊从纯拉动式转换为推-拉式,因为销售额增大了。
边界是他们的区域性仓库。
这个变化是由于亚马逊的规模足够大,能够跨地区的汇集需求。
2.Peapod公司:类似于亚马逊,Peapod公司通过建立仓库从纯拉动式转换为推-拉式,这种仓库为一片地区的服务能力比传统仓库更强。
交货时间约束和服务水平也促使Peapod公司转为推-拉式。
3.戴尔:戴尔供应链的推-拉边界是组装。
计算机组件是标准化的,他们需要聚合这些组件来组装所有成品。
他们可以使用推动式管理在风险分担和规模经济中占优。
电脑是根据买家指定的配置定制的,电脑装配应该使用拉动式管理。
4.家具公司:生产是基于拉动式但交付是推动式,因为运输成本高,且家具公司需要从一定时期的风险分担和规模经济中汇集需求。
第七章1.考虑一个大型折扣店。
讨论对于哪些产品和供应商,折扣店应该采用直接转运战略?对于哪些产品和供应商适合采用直接装运战略?答:以沃尔玛为例1.直接转运供应商的不易坏产品如啤酒、大米和洗发水,总销售额很大但在每个商店的需求很低,正适合直接转运策略。
这些产品可以与其他小容量的货物直接转运,实现一个整车运输到每个商店。
2.直接装运对于供应商,易腐和对时间敏感的产品,如水果和牛奶,适合直接转运策略,零售商订购的货物可以直接整车运送。
第八章1.为什么第三方物流行业发展如此迅猛?答:物流是一组复杂的任务,需要大量的资源,专业的分析、相关软件和大量投资于信息技术(更新速度非常快)。
因此,除非物流是一个公司的核心竞争力并有资源来运营它,否则很难设计和实施有效的物流业务。