IE数据处理与常用公式
IE工程师工作指导(新手IE有必要了解下)
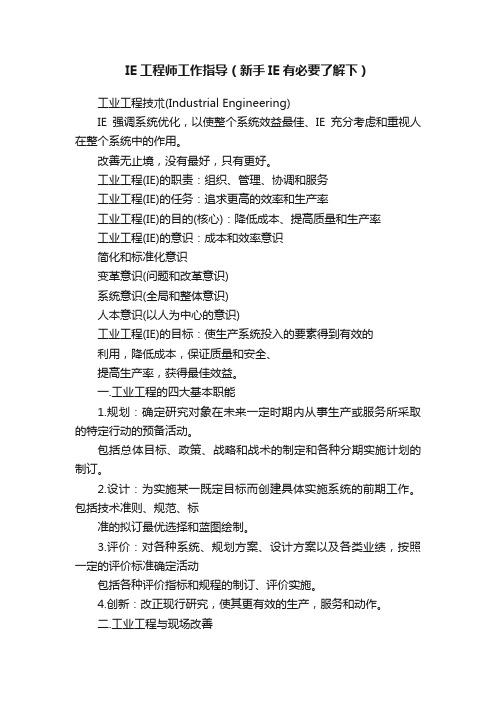
IE工程师工作指导(新手IE有必要了解下)工业工程技朮(Industrial Engineering)IE强调系统优化,以使整个系统效益最佳、IE充分考虑和重视人在整个系统中的作用。
改善无止境,没有最好,只有更好。
工业工程(IE)的职责:组织、管理、协调和服务工业工程(IE)的任务:追求更高的效率和生产率工业工程(IE)的目的(核心):降低成本、提高质量和生产率工业工程(IE)的意识:成本和效率意识简化和标准化意识变革意识(问题和改革意识)系统意识(全局和整体意识)人本意识(以人为中心的意识)工业工程(IE)的目标:使生产系统投入的要素得到有效的利用,降低成本,保证质量和安全、提高生产率,获得最佳效益。
一.工业工程的四大基本职能1.规划:确定研究对象在未来一定时期内从事生产或服务所采取的特定行动的预备活动。
包括总体目标、政策、战略和战术的制定和各种分期实施计划的制订。
2.设计:为实施某一既定目标而创建具体实施系统的前期工作。
包括技术准则、规范、标准的拟订最优选择和蓝图绘制。
3.评价:对各种系统、规划方案、设计方案以及各类业绩,按照一定的评价标准确定活动包括各种评价指标和规程的制订、评价实施。
4.创新:改正现行研究,使其更有效的生产,服务和动作。
二.工业工程与现场改善1.工业工程------Industrial Engineering是一门应用科学,兼有管理及技朮的知识领域。
2.IE是以工程技朮为基础,配合科学管理的技巧来发现、解决、预防问题﹔3.IE的最终目的是:由管理的动作,使企业能获得最大的利益(与成本或经济效益有关4.IE的操作理论均婪能符合实际的需要﹔5.IE是运用重点管理的技巧,在任何问题上做重点突破。
三.IE的定义:美国工业工程师协会的定议:“IE-------是研究人、物料、设备、能源的消息组成的综合系统的设计、改善和设置的工程技术,它应用数学、物理学等自然科学和社会科学方面的专门知识和技术,以及工程分析和设计的原理和方法来确定、预测和评价由该系统可得到的结果”。
IE 常见图文符号及运算公式

四.常用基本公式: 常用基本公式:
例:一天上班時間為480分,早會20分,生產過程中機器故障20分,模治具故障20分,一天共生產產品420sets,生產一個產品須時20分 ,流水線瓶頸工時為0.5分(含有寬放),不良率為5%,試計算: 1)總標準工時 2)作業效率 3)生產效率 4)設備綜合效率 解:根據以上介紹可知如下信息: 停止時間=早會20分 停機時間=機器故障20分+模治具故障20分=40分 總投入工時=480分 不良率=5% 1)總標準工時=420*0.5=210(分) 2)作業效率=(總標準工時/總使用工時)*100% =(總標準工時/總投入工時-停止時間-停機時間)*100% =[210/(480-20-40)]*100% =50% 3)生產效率=(總標準工時/總投入工時) *100% =(210/480)*100% =43.75% 4)設備綜合效率=時間稼動率*性能稼動率*良品率 時間稼動率=(總投入工時-停機時間)/總投入工時) *100% =[(480-40)/480]*100% =91.67% 性能稼動率=(總標準工時/負荷工時) *100% =[總標準工時/(總投入工時-停止時間)]*100% =[210/(480-20)]*100% =45.65% 良品率=1-不良率=1-5%=95% 故: 設備綜合效率=時間稼動率*性能稼動率*良品率 =91.67%*45.65%*95% =39.75%
S
1
三. 常見圖文符號
18种動素的定義及符號
動素分析是由美國工程師Frank Bunker Gilbreth(1862-1924)創立的,動作分析基本要素共有18种動作,也 有文獻定義為17种,本書設定為18种.(詳見下圖)
A.工 作 有 效 推 進 的 動 作 動 素 定 義 分 類 符號 B.造 成 工 作 遲 延 的 動 作 C.動 作 本 身 不 能 推 進 作 業 NO 1 名稱 伸手 英文及縮寫 Transport Empty (TE) Grasp (G) Transport Loaded (TL) Assemble (A) Disassemble (D) Use (U) Release Load (RL) 符號說明 手中無物的形狀 分類 A 定義 空 手 移 動 ,伸 向 目 標 ,又 稱空運 手或身體的某些部位充 分控制物體 手或身體某些部位移動 物 品 的 動 作 ,又 稱 運 實 將零部件組合成一件物 體的動作 將零部物進得分離和拆 解的動作 利用器具或裝置所做的 動 作 ,稱 使 用 或 應 用 握 取 的 相 反 動 作 ,放 開 控 制物的動作
IE公式汇总范文

IE公式汇总范文IE公式是工业工程领域中常用的数学模型,它们用于描述和优化生产与运营系统的各个方面,如生产计划、库存管理、物流运输、设备维护等。
在本篇文章中,我将为您汇总一些常见的IE公式,详细介绍它们的含义和应用。
1.消耗率公式消耗率公式用于计算生产过程中所需的资源消耗率。
它可以用于评估和优化生产过程的效率。
消耗率(CR)等于单位时间内所使用的资源量(RC)除以单位产出量(OU)。
CR=RC/OU例如,如果一家工厂每小时消耗100千瓦时的电力,每小时生产100个产品,则消耗率为1千瓦时/产品。
2.经济数量公式经济数量公式用于确定最经济的订单或批量大小。
它需要考虑到订单或批量的固定成本(FC)和变动成本(VC),以及需求率(D)和库存维持成本(H)。
经济数量(EOQ)等于固定成本与需求率和库存维持成本之间的平衡点,计算公式如下:EOQ=(2*FC*D)/H3.周转率公式周转率公式用于衡量存货的转换速度。
它可以帮助评估和优化库存管理的效果。
周转率(TR)等于销售量(S)除以平均库存量(IAV)。
TR=S/IAV例如,如果一家超市每年销售1000台电视,平均库存量为100台,则周转率为10次/年。
4.马太效应公式马太效应公式用于描述生产过程中的累积效应。
它指出,当生产速度提高时,生产效率将比预期更好。
马太效应(ME)等于适应时间(AT)除于生产速度增长率(RG)。
ME=AT/RG例如,如果一项任务在提高生产速度后需要适应1天,而生产速度每提高10%,则马太效应为1天/10%=10天。
5.利润公式利润公式用于计算销售收入和成本之间的差额。
它可以帮助评估生产和销售活动的盈利能力。
利润(P)等于销售收入(R)减去成本(C)。
P=R-C6.供应链效率公式供应链效率公式用于评估供应链的整体效率。
它可以衡量供应链的流动性和灵活性。
供应链效率(SCE)等于供应链的货币价值(VC)除以供应链流动性(VL)和供应链灵活性(VF)之和。
IE数据处理与常用公式
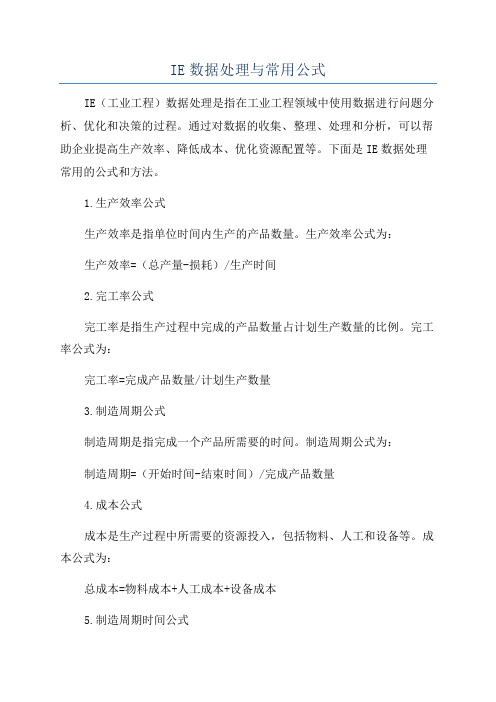
IE数据处理与常用公式IE(工业工程)数据处理是指在工业工程领域中使用数据进行问题分析、优化和决策的过程。
通过对数据的收集、整理、处理和分析,可以帮助企业提高生产效率、降低成本、优化资源配置等。
下面是IE数据处理常用的公式和方法。
1.生产效率公式生产效率是指单位时间内生产的产品数量。
生产效率公式为:生产效率=(总产量-损耗)/生产时间2.完工率公式完工率是指生产过程中完成的产品数量占计划生产数量的比例。
完工率公式为:完工率=完成产品数量/计划生产数量3.制造周期公式制造周期是指完成一个产品所需要的时间。
制造周期公式为:制造周期=(开始时间-结束时间)/完成产品数量4.成本公式成本是生产过程中所需要的资源投入,包括物料、人工和设备等。
成本公式为:总成本=物料成本+人工成本+设备成本5.制造周期时间公式制造周期时间是指完成一个产品所需要的总时间,包括加工时间、等待时间和运输时间等。
制造周期时间公式为:制造周期时间=加工时间+等待时间+运输时间6.资源利用率公式资源利用率是指生产过程中所使用的资源占总资源的比例。
资源利用率公式为:资源利用率=生产所使用的资源/总资源7.效率公式效率是指生产过程中实际产出与标准产出之间的比例。
效率公式为:效率=实际产出/标准产出8.容量公式容量是指生产过程中单位时间内能够完成的工作量。
容量公式为:容量=总资源/单位时间9.平均停留时间公式平均停留时间是指在生产过程中产品在其中一工序的平均停留时间。
平均停留时间公式为:平均停留时间=生产时间/生产数量10.时间效率公式时间效率是指单位时间内完成的工作量。
时间效率公式为:时间效率=完成工作量/单位时间以上是IE数据处理常用的公式和方法。
通过对数据进行准确的收集、整理、处理和分析,可以帮助企业发现问题、优化流程,并做出合理的决策,以提高生产效率和降低成本。
IE_公_式_汇_总

術語 定義/計算公式
在適宜的操作條件下,用最合適的操作方法,以普通熟練工人的正常速度完成標準作業所需的勞 標準工時/標準時間 動時間 標準時間=正常時間*(1+寬放率)=(觀測時間*評比係數)*(1+寬放率) 對某種作業的工時規定一個額度,即使對同一作業,由於用途不同可能有不同量值的定額,如現行 工時定額 定額、計劃定額、目標定額等 標準時間與工時定額 標準時間是制定工作定額的依據、工時定額是標準時間的結果 的關係 時間研究是一種作業測定技術,旨在決定一位合格、適當、訓練有素的操作者,在標準狀態下, 時間研究 對一特定的工作以正常速度操作所需要的時間 時間研究的研究方法 時間研究是用抽樣調查技術來對操作者的作業進行觀測,以決定作業的時間標準 三倍標準差法:正常值為x+/-3 內的數據,超出者為異常值 剔除異常值的方法
通过预测监控来检验过去起作用的预测模型是否仍然有效 利用变量(包括时间,如广告投入vs销量)之间的相互关系,通过一种变量的变化来预测另一种 因果关系模型 变量的未来变化 CYCLE TIME(C/T) 每單位工序中1個循環的作業所需的時間 週期時間 單位工序C/T的和/ 測試次數 TACK TIME(T/ 製造一件物品時所需要的實際時間 T) 作業時間/ 生產數 節拍時間
作業人員或設備上裝上無需小心作業也絕不出錯的防止出錯裝置 一般用產量對投入的比 生產率 OUT PUT /IN PUT 工時 人或機器能做的或已做的量用時間來表示 擁有人員的工時 擁有工時 擁有人員×正常作業時間 實際上沒投入到作業的工時(缺勤、休假、出差、支援等) 考勤工時 相關人員×相關時間 實際投入到作業的人員的工時 出勤工時 擁有工時-考勤工時 正常出勤工時以外追加作業的工時,即加班,特殊出勤、接受支援等 追加工時 相關人員×相關時間 投入到作業中的總工時 作業工時 出勤工時+追加工時 作業工時中去掉損失工時,實際投入到作業的工時 實際生產工時 作業工時-損失工時 不屬于作業人員責任範圍的損耗工時(會議、教育、早會、待料、材料不良、機械故障、機型變更 損失工時 、不良返工等) 相關人員×相關時間 生產產品所需的時間(標準時間)和實際用的時間之比 作業工時效率 標準工時/作業工時× 100 % 損失工時以外的純作業時間和實際生產所用的時間之比 實際生產工時效率 標準工時/實動工時× 100 % 生產產品所需的時間和純生產所需的時間之比 實際生產率 標準工時/實動工時× 100 % 為了減少生產要素的損耗,用一線監督人員的指導監督來達到適當地提升並維持作業人員對作業的 效率管理 態度的一種管理模式 標準時間/實際時間 PAC (Performance Analysis 為了能做到只要作業努力就能提升及維持能力的效率管理模式的一種。 & Control) 作業效率= 標準工時/( 可用工時-損失工時) IE七大手法 防呆法、防錯法、五五法、動改法、流程法、雙手法、抽查法 不良品修正的浪費、制造過多的浪費、庫存過多的浪費、搬運浪費﹑動作浪費、管理浪費、等待 現場九大浪費 浪費、加工過剩的浪費、人員的浪費 解決問題九步驟 1.發掘問題 2.選定題目 3.追查原因 4.分析資料 5.提出辦法 6.選擇對策 7.草擬行動 8.成果比較 9. 標准化 時間稼動率=稼動時間/負荷時間 性能稼動率=性能稼動時間/設備稼動時間=產出產品總數*單件標准工時/設備稼動時間 稼動率公式 良品率=產出良品數量/產出產品總數
IE数据处理与常用公式

步骤六:改善过程
1、装配线人员定岗、定置作业
a) 固定岗(作业员)与移动岗区分 (移动岗位:修理员、物料员、拉长、多能工) b) 由员工自已离岗去拿物料,变为专人配送物料到岗(编
岗位物料配送清单,明确数量/次、频次/天); c) 员工的作业范围要规划合理,减少不必要的走动; d) 员工离岗,设定顶岗人员机制(多能工配置)。
出勤时间
8H(28800S)或10H(36000S)(是否倒班)
出勤方式
单班/两班/三班
步骤一:现状数据调查
实际节拍时间
=实际出勤时间/实际产量
目前人均时产量
人员配置
出勤方式
步骤二:实物数据分析
1. 编制生产节拍测定表
能够看出每个岗位中的作业内容和作业顺序,所需物料、工作工具都列明
步骤二:实物数据分析
➢实施强制节拍(在自动生产线上) ➢虚拟强制节拍(在手推滚筒线上) ➢岗位之间“一个流”传递(作业台传递)
4、动作浪费改善
使用最低级动作作业
➢改善瓶颈岗位的浪费动作(明显+细小)
➢改善每个岗位的浪费动作(明显→细小)
浪费动作消除后,平衡也会打破,需重新调整生产平衡
步骤六:改善过程
常见的12种动作浪费:
活动程序
PD AC
PD AC
P-Plan D-Do C-Check A-Action
活动基本步骤
改善对象选定
现状调查
总结及标准化
效果确认
改善实施
问题点提出 设定改善目标 改善案确立
步骤一:现状调查
选定改善对象
XX工段XX生产线(班) 针对XX品号(系列)进行改善
计划产量
XX台/8H(或XX台/10H)
IE分析方法和常用计算公式
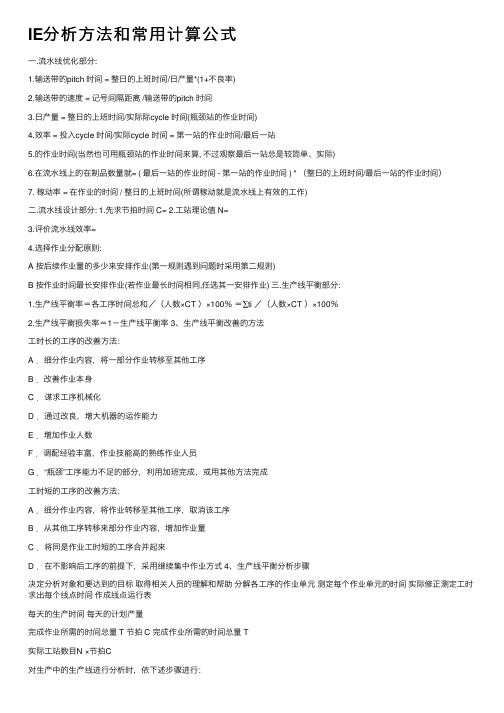
IE分析⽅法和常⽤计算公式⼀.流⽔线优化部分:1.输送带的pitch 时间 = 整⽇的上班时间/⽇产量*(1+不良率)2.输送带的速度 = 记号间隔距离 /输送带的pitch 时间3.⽇产量 = 整⽇的上班时间/实际际cycle 时间(瓶颈站的作业时间)4.效率 = 投⼊cycle 时间/实际cycle 时间 = 第⼀站的作业时间/最后⼀站5.的作业时间(当然也可⽤瓶颈站的作业时间来算, 不过观察最后⼀站总是较简单、实际)6.在流⽔线上的在制品数量就= ( 最后⼀站的作业时间 - 第⼀站的作业时间 ) * (整⽇的上班时间/最后⼀站的作业时间)7. 稼动率 = 在作业的时间 / 整⽇的上班时间(所谓稼动就是流⽔线上有效的⼯作)⼆.流⽔线设计部分: 1.先求节拍时间 C= 2.⼯站理论值 N=3.评价流⽔线效率=4.选择作业分配原则:A 按后续作业量的多少来安排作业(第⼀规则遇到问题时采⽤第⼆规则)B 按作业时间最长安排作业(若作业最长时间相同,任选其⼀安排作业) 三.⽣产线平衡部分:1.⽣产线平衡率=各⼯序时间总和/(⼈数×CT )×100%=∑ti /(⼈数×CT )×100%2.⽣产线平衡损失率=1-⽣产线平衡率 3、⽣产线平衡改善的⽅法⼯时长的⼯序的改善⽅法:A .细分作业内容,将⼀部分作业转移⾄其他⼯序B .改善作业本⾝C .谋求⼯序机械化D .通过改良,增⼤机器的运作能⼒E .增加作业⼈数F .调配经验丰富,作业技能⾼的熟练作业⼈员G .“瓶颈”⼯序能⼒不⾜的部分,利⽤加班完成,或⽤其他⽅法完成⼯时短的⼯序的改善⽅法:A .细分作业内容,将作业转移⾄其他⼯序,取消该⼯序B .从其他⼯序转移来部分作业内容,增加作业量C .将同是作业⼯时短的⼯序合并起来D .在不影响后⼯序的前提下,采⽤继续集中作业⽅式 4、⽣产线平衡分析步骤决定分析对象和要达到的⽬标取得相关⼈员的理解和帮助分解各⼯序的作业单元测定每个作业单元的时间实际修正测定⼯时求出每个线点时间作成线点运⾏表每天的⽣产时间每天的计划产量完成作业所需的时间总量 T 节拍 C 完成作业所需的时间总量 T实际⼯站数⽬N ×节拍C对⽣产中的⽣产线进⾏分析时,依下述步骤进⾏:1)对⽣产线的各⼯程顺序(作业单位)予认定,并填⼊⽣产流动平衡表中2)测算各⼯序实质作业时间以DM (Decimal Minute )为单位记⼊平衡表内(1⼈实质时间栏)注:1DM=分=秒3)清点各⼯序作业⼈数,并记⼊⼈员栏内4)1⼈实质作业时间÷⼈数 = 分配时间,记⼊时间栏5)依此分配时间划出柱状图或曲线图6)在分配的实质时间最⾼的这⼀⼯序顶点横向划⼀条点线7)计算不平衡损失上⾯斜线部分的总和即为不平衡损失的总和 T (Lose )=Σ|Tm -Ti|不平衡损失=(最⾼的DM×合计⼈数)-(各⼯序时间的合计)如下图8)⽣产线平衡率⽣产线平衡率=—————————————— 9)⽣产线不平衡损失率=1-⽣产线平衡率10)如使⽤输送带之动⼒传送,则应计算输送带的流动速度(M/时间单位)称为节拍时间,符号TC 。
IE常用计算公式及报价成本计算 (1)
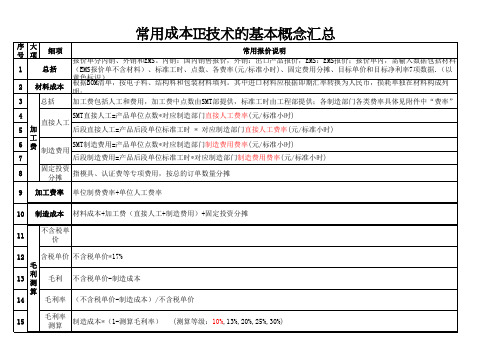
毛利率 (不含税单价-制造成本)/不含税单价 毛利率 制造成本*(1-测算毛利率) 测算 (测算等级:10%,13%,20%,25%,30%)
16
销售费用
期 间 17 财务费用 指结算帐期、材料付款方式等因素占用资金所发生的成本。 =(不含税单价*占比比率) 费 用 18 管理费用 指平台部门费用,与产品的销量、单价、合作方式、材料占比等因素有关= (不含税单价*占比比率) 19 20 税前利润 税费 目标价格减去成本和期间费用后的利润 =(毛利润-期间费用)
事业部内部发生的各项费用,报价时按年度费用预算占年度收入预算的比例计 =(不含税单价*占比比率)占比比率指占销 售收入
税 后 21 利 所得税 润 22 净利润 23 24 注意事项
内销报价仅指所得税,外销报价除所得税外还要核算出口退税损失。出口退税损失指增值税17%与退税率之间的差额造成 的损失。 税前利润*税率 当净利率大于目标净利率时,“接受报价”,当净利率小于0时,“不接受报价”,当净利率介于0与目标利率之间时“请 综合评估”。=(税前利润-税费) 外销报价单内17%的出口退税率是当前退税率,退税率会随着税收政策变动,报价时退税率不确定时,需要向财务部确 定; 当某一产品的净利率低于目标净利率时,需要综合考虑产能、年度利润目标、营业目标等因素,综合评估后进行报价。
常用成本IE技术的基本概念汇总
序 大 号 项 1 2 3 4 5 6 7 8 9 10 11 12 毛 利 13 测 算 14 15 加 工 费 细项 总括 材料成本 总括 直接人工 常用报价说明 报价单分内销、外销和EMS。内销:国内销售报价,外销:出口产品报价,EMS:EMS报价;报价单内,需输入数据包括材料 (EMS报价单不含材料)、标准工时、点数、各费率(元/标准小时)、固定费用分摊、目标单价和目标净利率7项数据.(以 黄色标识) 根据BOM清单,按电子料、结构料和包装材料填列。其中进口材料应根据即期汇率转换为人民币,损耗单独在材料构成列 明; 加工费包括人工和费用,加工费中点数由SMT部提供,标准工时由工程部提供;各制造部门各类费率具体见附件中“费率” SMT直接人工=产品单位点数*对应制造部门直接人工费率(元/标准小时) 后段直接人工=产品后段单位标准工时 * 对应制造部门直接人工费率(元/标准小时) 制造费用 SMT制造费用=产品单位点数*对应制造部门制造费用费率(元/标准小时) 后段制造费用=产品后段单位标准工时*对应制造部门制造费用费率(元/标准小时) 固定投资 指模具、认证费等专项费用,按总的订单数量分摊 分摊 加工费率 制造成本 不含税单 价 含税单价 不含税单价*17% 毛利 不含税单价-制造成本 单位制费费率+单位人工费率 材料成本+加工费(直接人工+制造费用)+固定投资分摊
- 1、下载文档前请自行甄别文档内容的完整性,平台不提供额外的编辑、内容补充、找答案等附加服务。
- 2、"仅部分预览"的文档,不可在线预览部分如存在完整性等问题,可反馈申请退款(可完整预览的文档不适用该条件!)。
- 3、如文档侵犯您的权益,请联系客服反馈,我们会尽快为您处理(人工客服工作时间:9:00-18:30)。
第一类
第九种浪费: 第九种浪费“人员的浪费”,
定义不是指人员配置多余的浪费, 而是 “仅仅利用了员工的体力, 而将员工的智力拒之门外的浪费”
识别问题
什么是3M
<勉强---Muri> 超出能力的限界,一直处在重负担的状态
<浪费---Muda> 虽然有能力,但一直从事能力以下的工作
<不均---Mura>
以人员减少为目标,产量不变
直接人员 =实测时间合计/目标节拍
步骤六:改善过程
1、装配线人员定岗作业
a) 固定岗(作业员)与移动岗区分 (移动岗位:修理员、物料员、拉长、多能工) b) 由员工自已离岗去拿物料,变为专人配送物料到岗(编
岗位物料配送清单,明确数量/次、频次/天); c) 员工的作业范围要规划合理,减少不必要的走动; d) 员工离岗,设定顶岗人员机制(多能工配置)。
计划产量
XX台/8H(或XX台/10H)
出勤时间
8H(28800S)或10H(36000S)(是否倒班)
出勤方式
单班/两班/三班
步骤一:现状数据调查
实际节拍时间
=实际出勤时间/实际产量
目前人均时产量
人员配置
出勤方式
步骤二:实物数据分析
1. 编制生产节拍测定表
能够看出每个岗位中的作业内容和作业顺序,所需物料、工作工具都列明
认识节拍及计算
• 什么是节拍(Cycle Time) 我们定义的节拍是指从作业开始到作业结
束的时间间隔,不包括作业前的等待时间。
• 实际生产节拍(TT)是指实际生产一个产品的 时间。
认识节拍及计算
工序时间分解
TT 实际生产节拍时间
Scrap 生产废品时间 Changeover 换型时间 Downtime 停机时间
人均时产量=
同机型每小时的产量 实际作业人员
流水线效率改善步骤
活动程序
PD AC
PD AC
P-Plan D-Do C-Check A-Action
活动基本步骤
改善对象选定
现状调查
总结及标准化
效果确认
改善实施
问题点提出 设定改善目标 改善案确立
步骤一:现状调查
选定改善对象
XX工段XX生产线(班) 针对XX品号(系列)进行改善
a)
步骤六:改善过程 2、同期化线边生产
主线
1、预准线与总装的同期化生产,品质异常、生产异 常能及时发现,现场快速对应能力提高; 2、同期生产的实现需要打破固有思维,考虑最适合 生产的布局方式,减少搬运,减少中间在制品,提高 工序间的平衡; 3、物料的配送方式,配送工具要发生改变。
步骤六:改善过程
∑CT=576.77 TT=13.58
作业时间 线内损失时间
CTmax=11.68
综合损失:46.2% 线内平衡损失:30.45%
TT CT
产线平衡率:69.55%
线外损失时间
产线平衡率=
∑CT 瓶颈节拍时间X工位数量
X 100%
步骤二:实物数据分析
几种生产性向上计算
系统平衡率= 产线平衡率= 工艺平衡率=
步骤二:实物数据分析
2.按照表格内容测定实物数据
1、按工步测 2、5次时间均匀 3、不能打扰员工作业 4、测工时角度能看清员工所有作业 5、异常时间要记录问题点 6、新旧员工识别
步骤二:实物数据分析
3、制作节拍图
瓶颈岗位在哪里?
步骤二:实物数据分析
4、平衡率分析
CT表示完成一次单位作业需要的时间 TT表示实际生产一件产品需要的时间
2、物流图制作
物流图是对搬运(布局合理性)、中间库(库存、异常)两项内
。 容平面展示找出改善内容,加快物流,缩短生产周期ห้องสมุดไป่ตู้
步骤三:实物流分析
3、瓶颈工序节拍分析
节拍分析的目的是找出非增值时间的比例,确定非增值项的改善
内容。
步骤四:现状数据汇总
步骤五:设定目标
以产量提升为目标,人员不变
目标节拍 =实测时间合计/直接人员
IE数据处理与计算 公式整理汇集
13265201520
课题目录
➢ 识别问题 ➢认识节拍及计算 ➢ 作业效率的定义 ➢ 流水线改善步骤
识别问题
什么是浪费?
◊ 不增值的活动
◊ 增值活动,但所有资源超过“绝对最少”界限的活 动
浪费类别:
第一类:不增值和超出资源的浪费(八大浪费) 第二类:没有开发利用的浪费(人员的浪费)
∑OCT ∑TT
X 100%
∑CT 瓶颈节拍时间X工位数量
∑VA VAMAX X 工位数量
X 100% X 100%
作业有效率=
∑VA ∑OCT
X 100%
工艺作业有效率 =
∑VA ∑TT
X 100%
步骤三:实物流分析
1、排拉图制作
排拉图是对生产过程做全面的了解,并掌握人员 配置情况。
步骤三:实物流分析
a)
步骤六:改善过程
1、装配线人员定岗、定置作业
a) 固定岗(作业员)与移动岗区分 (移动岗位:修理员、物料员、拉长、多能工) b) 由员工自已离岗去拿物料,变为专人配送物料到岗(编
岗位物料配送清单,明确数量/次、频次/天); c) 员工的作业范围要规划合理,减少不必要的走动; d) 员工离岗,设定顶岗人员机制(多能工配置)。
1. 两手空闲的浪费 2. 一只手空闲的浪费 3. 动作中途停顿的浪费 4. 拿的动作中途变换的浪费 5. 动作之间配合不好的浪费 6. 不懂作业技巧的浪费
在工作能力的限界上下来回波动
勉强
不均
能
力
当处在勉强、不均、浪费三种情况
时,质量是最不好的!
適
量
浪费
0点
五五识别法
识别问题
what
where
when
why
who
how
做这个? 在此处做? 要此时做? 由他做? 要这样做?
从必要性发问 从空间、面积发问 从时间柔性发问 从多能、防呆性发问 从方法性发问
隐性时间
VA 增值时间 NVA 无价值时间
操作时间(CT)
作业效率的定义
作业效率 =
产出总工时 出勤时间-无效时间
X 100%
∑标准时间ST × 生产台数
=
人 员 × 有效时间 X 100%
弊端: 作业员很难立即了解作业效率的高低。
作业效率的定义
精益生产重视的是改善、提高,参照物最多 的是自己,目标不是精益生产追求的结果,目标 是对精益生产提高的评价,因此精益生产中相对 作业效率来说,人均时产量更为直接。
3、实施节拍控制
➢实施强制节拍(在自动生产线上) ➢虚拟强制节拍(在手推滚筒线上) ➢岗位之间“一个流”传递(作业台传递)
4、动作浪费改善
使用最低级动作作业
➢改善瓶颈岗位的浪费动作(明显+细小)
➢改善每个岗位的浪费动作(明显→细小)
浪费动作消除后,平衡也会打破,需重新调整生产平衡
步骤六:改善过程
常见的12种动作浪费: