铸造工艺图
铸造工艺流程图

入库
抽检 混砂及造型 记录
工序
型砂抽检
检测
熔炼浇注工 记录 成分及金相
序
检测
检测
记录 后处理工序
外观及尺寸 检测
不合格 报废处理
合格 砂型质量检 查
本体检测或 不合格 报废 合格 记录保存
砂型硬度及 表面质量
返修或报废 不合格
合格
入库
检验记录要可靠 统计分析才有效
谢谢
造型工序工艺流程图 SHELL MOULDING PROCESS FLOW CHART
混砂工序
模具检查
工装模具 (行车)
合
格
型
砂型硬度
砂
检查外观 吹净散砂
造型 (造型机)
喷脱模剂 (造型机)
砂芯检查 (下芯前)
合 格 砂 芯
制芯工段
下芯平稳 一次到位 放置滤网
下芯 (手工)
合箱 (造型机)
浇注 (行车)
检测合格
造型工序
性能检测 (检测仪器)
水分 紧实率 透气性 湿压强度
为社会做贡献 为企业求发展
原材料验收 标准
制芯工序工艺流程图 CORE-MAKING PROCESS FLOW
覆膜砂 (入厂检验)
工装、芯盒 检查
加热温度和 结壳时间
制芯 (射芯机)
飞边、披缝 及散砂清理
干净
修芯 (手工)
砂芯型Hale Waihona Puke 制芯时间原材料验收 标准
生铁 (入厂检验)
原材料验收 标准
废钢 (入厂检验)
灰铁球铁区 分开
配料单
温度、除渣
成分、性能
配料
熔炼
炉前分析
成分化验
《铸造工艺图绘制》课件

为铸造生产提供技术指导,确保铸件的质量和生 产效率。
分类
根据用途可分为零件图和总装图。
铸造工艺图绘制的流程
确定铸造工艺方案
根据铸件需求,选择合适的铸 造方法、材料和工艺参数。
绘制总装图
将各个零件的铸造工艺图进行 汇总,绘制出完整的总装铸造 工艺图。
了解铸件需求
与设计部门沟通,明确铸件的 使用要求和性能参数。
简化绘图流程
通过减少不必要的步骤和优化绘图工具,提高绘图效率。
标准化绘图规范
制定统一的绘图标准,确保图纸的准确性和一致性。
引入模板和预设元素
利用模板和预设元素,快速生成标准化的铸造工艺图。
铸造工艺图绘制的自动化技术
01
02
03
自动化绘图软件
利用自动化绘图软件,实 现快速、准确的铸造工艺 图绘制。
参数化绘图
实践操作
通过实践操作绘制铸造工艺图, 学生可以锻炼实际操作能力和技 能水平,提高自己的综合素质和 实践能力。
案Байду номын сангаас分析
通过对实际案例的分析和讨论, 学生可以更加深入地了解铸造工 艺的应用和实际效果,提高分析 和解决问题的能力。
总结词:进阶提高
详细描述:针对复杂铸件,如何进行详细的工艺分析,制定合理的铸造工艺方案,并绘制出完整的铸 造工艺图。
实例三:特殊要求的铸造工艺图绘制
总结词:特殊处理
详细描述:针对具有特殊要求的铸件,如何根据具体要求调整铸造工艺方案,并绘制出满足要求的铸造工艺图。
PART 04
铸造工艺图绘制进阶
铸造工艺图绘制的优化技巧
PART 05
铸造工艺图绘制应用
铸造工艺图绘制在生产中的应用
铸造工艺图
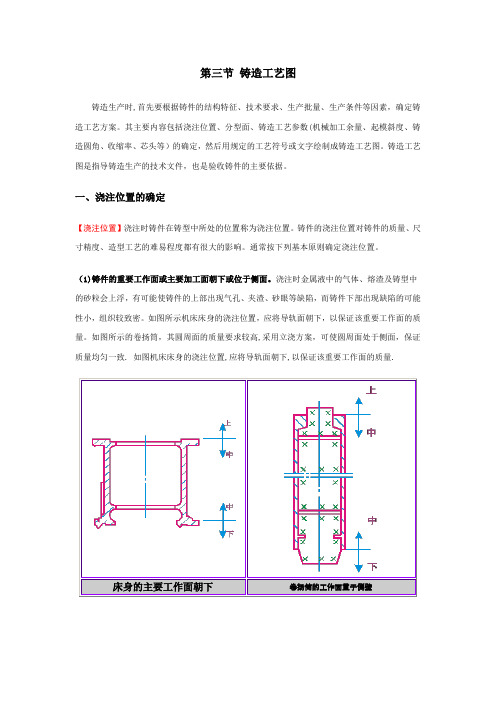
第三节铸造工艺图铸造生产时,首先要根据铸件的结构特征、技术要求、生产批量、生产条件等因素,确定铸造工艺方案。
其主要内容包括浇注位置、分型面、铸造工艺参数(机械加工余量、起模斜度、铸造圆角、收缩率、芯头等)的确定,然后用规定的工艺符号或文字绘制成铸造工艺图。
铸造工艺图是指导铸造生产的技术文件,也是验收铸件的主要依据。
一、浇注位置的确定【浇注位置】浇注时铸件在铸型中所处的位置称为浇注位置。
铸件的浇注位置对铸件的质量、尺寸精度、造型工艺的难易程度都有很大的影响。
通常按下列基本原则确定浇注位置。
(1)铸件的重要工作面或主要加工面朝下或位于侧面。
浇注时金属液中的气体、熔渣及铸型中的砂粒会上浮,有可能使铸件的上部出现气孔、夹渣、砂眼等缺陷,而铸件下部出现缺陷的可能性小,组织较致密。
如图所示机床床身的浇注位置,应将导轨面朝下,以保证该重要工作面的质量。
如图所示的卷扬筒,其圆周面的质量要求较高,采用立浇方案,可使圆周面处于侧面,保证质量均匀一致. 如图机床床身的浇注位置,应将导轨面朝下,以保证该重要工作面的质量.床身的主要工作面朝下卷扬筒的工作面置于侧壁(2)铸件的大平面朝下或倾斜浇注。
由于浇注时炽热的金属液对铸型的上部有强烈的热辐射,引起顶面型砂膨胀拱起甚至开裂,使大平面出现夹砂、砂眼等缺陷。
大平面朝下或采用倾斜浇注的方法可避免大平面产生铸造缺陷。
下图为平板铸件的浇注位置。
大平面朝下(3)铸件的薄壁朝下、侧立或倾斜。
为防止铸件的薄壁部位产生冷隔、浇不到缺陷,应将面积较大的薄壁置于铸件的下部,或使其处于侧壁或倾斜位置,如图所示。
薄壁铸件的浇注位置(4)铸件的厚大部分应放在顶部或在分型面的侧面。
主要目的是便于在厚处安放冒口进行补缩,如图阀体的冒口补缩和图卷扬筒的重要面位于侧面所示。
二、分型面的选择【分型面】是铸型组元间的接合面。
为便于起模,一般分型面选择在铸件的最大截面处.分型面的选定应保证起模方便、简化铸造工艺、保证铸件的质量。
铸造工艺图共34页
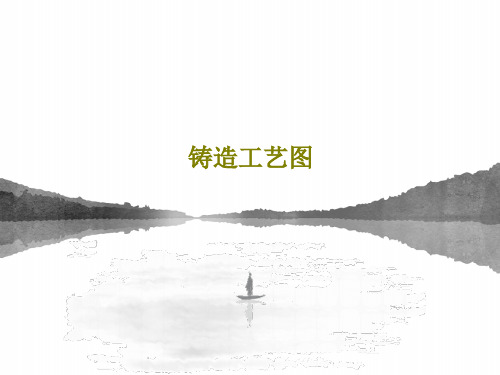
1、战鼓一响,法律无声。——英国 2、任何法律的根本;不,不成文法本 身就是 讲道理 ……法 律,也 ----即 明示道 理。— —爱·科 克
3、法律是最保险的头盔。——爱·科 克 4、一个国家如果纲纪不正,其国风一 定颓败 。—— 塞内加 5、法律不能使人人平等,但是在法律 面前人 人是平 等的。 ——波 洛克
45、自己的饭量自己知道何源泉吸 收都不可耻。——阿卜·日·法拉兹
42、只有在人群中间,才能认识自 己。——德国
43、重复别人所说的话,只需要教育; 而要挑战别人所说的话,则需要头脑。—— 玛丽·佩蒂博恩·普尔
44、卓越的人一大优点是:在不利与艰 难的遭遇里百折不饶。——贝多芬
铸造工艺图及设计实例
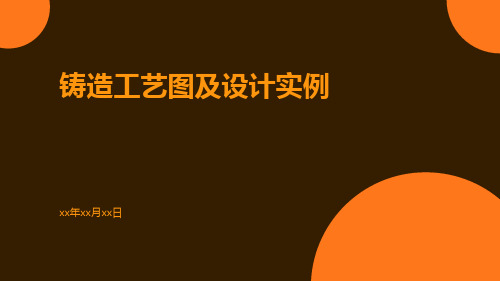
零件结构分析
零件结构分析
对零件的形状、大小、壁厚、结构特点进行分析,以便了解其铸造难度和特 殊要求。
材质选择
根据零件用途和性能要求,确定合适的材质,如铝合金、铸铁、铸钢等。
铸造方法选择
铸造方法选择
根据零件的结构特点和材质,选择合适的铸造方法,如砂型铸造、金属型铸造、 压力铸造等。
铸造工艺方案制定
研究不足与展望
研究局限性
本文所涉及的铸造工艺图设计方法仅适用于某些特定类型的铸件,对于某些复杂或大型铸 件,还需进一步研究和改进。
缺乏实际应用
虽然本文对铸造工艺图设计进行了详细探讨,但尚未在实际生产中进行验证和应用,仍需 进一步实践验证。
未来研究方向
未来可以对铸造工艺过程的数值模拟、智能化铸造工艺设计以及绿色铸造技术等方面进行 深入研究。
零件材质:青铜 零件壁厚:8mm
零件外径:150mm 加工余量:3mm
04
铸造工艺图的应用与优化
铸造工艺图的应用范围
零件制造
01
铸造工艺图是零件制造的
02
铸造模具是实现零件成型的工具,铸造工艺图为模具设计提供
了明确的结构和尺寸要求。
生产计划
03
THANKS
谢谢您的观看
铸造工艺图可帮助生产计划人员合理安排生产计划,提高生产
效率和资源利用率。
铸造工艺图的优化建议
简化结构
提高精度
简化铸造工艺图的结构,减少模具制造的难 度和成本。
提高铸造工艺图的精度,减少误差和浪费, 提高产品质量。
优化浇注系统
加强模具维护
浇注系统是铸造过程中的重要环节,优化浇 注系统可提高金属液的填充效果,减少浇不 足、气孔等缺陷。
铸造工艺图精品文档
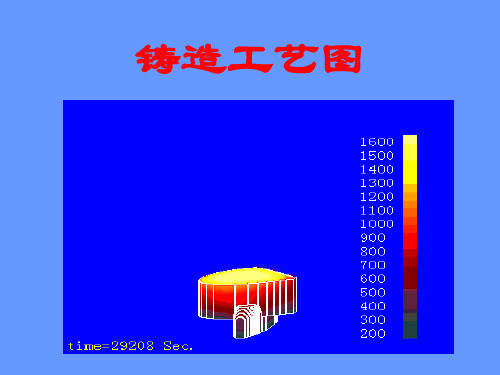
4、容易形成缩孔缩松的铸件,厚大部位放在分型面附近 的上部或侧面。
5、应减少型芯的数量,便于型芯固定和排气。 6、尽可能避免使用吊砂、吊芯或悬臂式砂芯。 7、应使合箱位置、浇注位置和铸件冷却位置一致,避免
多次翻动砂箱。
浇注位置的选择原则
下 中
铸造工艺图
铸造工艺图
利用各种工艺符号,把制造模型和铸型所需地资 料直接绘在零件图上的图样。 根据铸造工艺图绘出模型图和合箱图
零件结构的铸造工艺性分析 浇注位置 分型面的选择
1、机械加工余 量和最小铸出 孔 2、拔模斜度 3、收缩率 4、铸造圆角 5、型芯头
模型图 合箱图
确定造型方法 铸造工艺参数 型芯的数量及其设计
浇注系统设计 冒口、冷铁、铸筋设计 绘制铸造工艺图
浇注位置的选择
• 浇注位置-浇注时,铸 件在铸型中所处的位置/ 铸件的某个表面位于铸 型的上、下还是侧面。
• 浇口位置-内浇口与铸 型型腔连接处的位置/液 态金属流入铸型型腔的 位置。
上
下
浇注位置的选择原则
1、铸件的重要加工面或主要工作面应朝下 。 2、铸件的大平面应朝下,以免夹砂 。 3、为防止铸件薄壁部分产生浇不足或冷隔现象,应将面
中 上 车床床身
浇注位置的选择原则
浇注位置的选择原则
浇注位置的选择原则
分型面的选择原则
• 分型面-砂箱间砂型的接触面(平面或曲面) 1、尽可能使用最少的分型面。 2、应尽量使型芯、活块数量少。 3、应尽量使铸件全部或大部分放在同一砂箱
内。 4、尽量选用平面。图2-30 5、为便于造型、下芯、合箱、检验及检查,
应尽量将型腔置于下箱
分型面的选择原则
铸造工艺图及设计实例

汇报人: 日期:
目录
• 铸造工艺图 • 铸造材料及特性 • 铸造设备及工具 • 铸造设计实例 • 铸造工艺优化及改进建议 • 铸造工艺图及设计软件应用
01
铸造工艺图
铸造工艺流程图
造型材料准备
包括对铸造用砂、型砂等的选择 、混砂、配制等过程。
模样和芯盒准备
根据图纸准备木模、木芯盒等。
造型和制芯
将模样放入芯盒内,填入型砂, 形成铸型。
落砂和清理
铸件冷却后打开铸型,去除铸件 表面和内部的残砂和夹杂物。
浇注
将熔融的金属注入铸型中。
合型
将上、下铸型组合起来,形成完 整的铸型。
铸造模具设计图
模具材料选择
根据铸造合金和模具使用条件 选择模具材料,如铸铁、铜合
金等。
模具结构设计
根据产品图纸和铸造工艺要求 ,设计模具结构,包括浇口位 置、分型面选择等。
组成。
数控铣床
用于模具型腔的铣削加工,主要由 主轴、工作台、控制系统等组成。
数控磨床
用于模具型腔的磨削加工,主要由 工作台、主轴、控制系统等组成。
铸造用辅助设备
混砂机
用于混制型砂,一般由混砂转子、型砂输送装置、润 湿装置等组成。
砂处理设备
用于对型砂进行干燥、冷却、输送等处理,一般由干 燥器、冷却器、输送装置等组成。
浇注机
用于浇注金属液体,一般由浇包、浇道、控制系统等 组成。
铸造工具及选用
1 2
模样和芯盒
用于制作铸造用的模样和芯盒,一般由木材或塑 料制成。
浇口杯和分流锥
用于浇注金属液体,一般由耐火材料制成。
3
冒口和冷铁
用于控制铸件的温度和补缩,一般由铸铁或铸钢 制成。
铸造工艺流程图
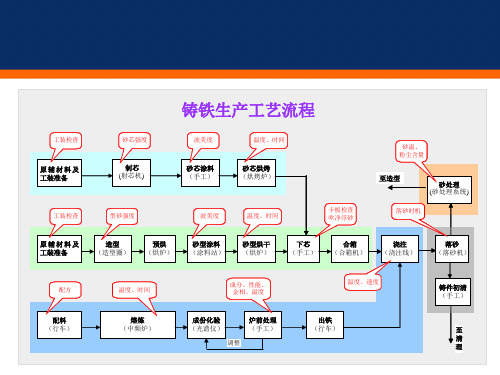
震动时效 (震动台)
清理打磨 (手工)
激振力、 时间
外观、尺寸、 机械性能
检验
油漆、 防锈
清洁度、 披缝、修补
铸件 入库
精铸生产工艺流程
制蜡料 (搅蜡机)
制蜡棒 (手工)
制蜡模 组装 (压蜡机) (手工)
回收蜡 5—8层
蜡处理 (蜡处理槽)
温度、 时间
废钢
成分、温度、 脱氧
熔炼 (中频炉)
粘涂料
粘砂
硬化
(手工) (手工) (硬化池)
风干 模壳脱蜡 (风扇) (脱蜡槽)
焙烧
浇注
Байду номын сангаас
(焙烧炉) (手工)
制涂料
配方
配方、
(搅拌机)
浓度
浓度、 时间
干燥 程度
铸件初清 (手工)
新蜡料
水玻璃、 石英砂 石英粉
氯化铵
外观、尺寸、 机械性能
抛丸处理 二次抛丸 (抛丸机)
入库
检验
清理打磨 (手工)
型砂强度
波美度
砂芯涂料 (手工)
温度、时间
砂芯烘烤 (烘烤炉)
波美度
温度、时间
卡板检查 吹净浮砂
砂温、 粉尘含量
至造型
砂处理 (砂处理系统)
落砂时机
原辅材料及 工装准备
造型 (造型圈)
预烘 (烘炉)
砂型涂料 (涂料站)
砂型烘干 (烘炉)
下芯 (手工)
合箱 (合箱机)
浇注 (浇注线)
落砂 (落砂机)
配方
配料 (行车)
吹氧、净化、造渣、 脱氧、温度、时间
熔炼 (电弧炉)
- 1、下载文档前请自行甄别文档内容的完整性,平台不提供额外的编辑、内容补充、找答案等附加服务。
- 2、"仅部分预览"的文档,不可在线预览部分如存在完整性等问题,可反馈申请退款(可完整预览的文档不适用该条件!)。
- 3、如文档侵犯您的权益,请联系客服反馈,我们会尽快为您处理(人工客服工作时间:9:00-18:30)。
第三节铸造工艺图
铸造生产时,首先要根据铸件的结构特征、技术要求、生产批量、生产条件等因素,确定铸造工艺方案。
其主要内容包括浇注位置、分型面、铸造工艺参数(机械加工余量、起模斜度、铸造圆角、收缩率、芯头等)的确定,然后用规定的工艺符号或文字绘制成铸造工艺图。
铸造工艺图是指导铸造生产的技术文件,也是验收铸件的主要依据。
一、浇注位置的确定
【浇注位置】浇注时铸件在铸型中所处的位置称为浇注位置。
铸件的浇注位置对铸件的质量、尺寸精度、造型工艺的难易程度都有很大的影响。
通常按下列基本原则确定浇注位置。
(1)铸件的重要工作面或主要加工面朝下或位于侧面。
浇注时金属液中的气体、熔渣及铸型中的砂粒会上浮,有可能使铸件的上部出现气孔、夹渣、砂眼等缺陷,而铸件下部出现缺陷的可能性小,组织较致密。
如图所示机床床身的浇注位置,应将导轨面朝下,以保证该重要工作面的质量。
如图所示的卷扬筒,其圆周面的质量要求较高,采用立浇方案,可使圆周面处于侧面,保证质量均匀一致。
如图机床床身的浇注位置,应将导轨面朝下,以保证该重要工作面的质量。
床身的主要工作面朝下卷扬筒的工作面置于侧壁
(2)铸件的大平面朝下或倾斜浇注。
由于浇注时炽热的金属液对铸型的上部有强烈的热辐射,引起顶面型砂膨胀拱起甚至开裂,使大平面出现夹砂、砂眼等缺陷。
大平面朝下或采用倾斜浇注的方法可避免大平面产生铸造缺陷。
下图为平板铸件的浇注位置。
大平面朝下
(3)铸件的薄壁朝下、侧立或倾斜。
为防止铸件的薄壁部位产生冷隔、浇不到缺陷,应将面积较大的薄壁置于铸件的下部,或使其处于侧壁或倾斜位置,如图所示。
薄壁铸件的浇注位置
(4)铸件的厚大部分应放在顶部或在分型面的侧面。
主要目的是便于在厚处安放冒口进行补缩,如图阀体的冒口补缩和图卷扬筒的重要面位于侧面所示。
二、分型面的选择
【分型面】是铸型组元间的接合面。
为便于起模,一般分型面选择在铸件的最大截面处。
分型面的选定应保证起模方便、简化铸造工艺、保证铸件的质量。
确定分型面应遵循如下原则。
(1)分型面应选择在模样最大截面处,以便于起模。
如图所示。
分型面选在最大直径处
(2)尽量减少分型面。
分型面少则容易保证铸件的精度,并可简化造型工艺。
对机器造型来说,一般只能有一个分型面,下图所示的绳轮铸件,大批量生产时,为便于机器造型,可按a分型方案,采用环状型芯,将二个分型面减少为一个分型面。
当然在单件生产时,采用手工造型时,为减少工装的制造,采用b方案,三箱造型,二个分型面也是合理的。
(a)(b)
绳轮铸件的分型面
(3)尽量使分型面平直。
为了使模样制造和造型工艺简便,如图所示弯曲连杆的分型面,不应采用弯曲的分型面(b方案),而应采用平直的分型面(a方案)。
弯曲连杆的分型面
(4)尽量使铸件的全部或大部分位于同一砂箱中。
铸件处于同一砂箱中,既便于合型,又可避免错型,以保证铸件的精度。
下图水管堵头的二种分型方案,图中a分型方案较合理,使基准面与加工面位于同一砂箱中,铸件的精度易保证。
水管堵头的分型面
(5)尽量使型芯位于下箱,并注意减低砂箱的高度。
这样可简化造型工艺、方便下芯和合型、便于起模和修型。
如图缩示机床立柱的分型方案,采用Ⅱ方案比较合理,可使型腔和型芯大部分处于下箱中,便于起模、下芯、合型。
机床立柱的分型面
三、工艺参数的选定
(1)机械加工余量和公差
【机械加工余量】是指铸件加工面上预留的、准备切除的金属层厚度。
加工余量取决于铸件的精度等级,与铸件材料、铸造方法、生产批量、铸件尺寸、浇注位置等因素有关。
铸件的尺寸公差 CT,其精度等级从高到低有1、2、3......16共16个等级;加工余量等级MA,从精到粗可分为A、B、C、D、E、F、G、H、J共9个级别。
下表为砂型铸造常用铸造合金单件和小批生产时公差等级及与之配套的加工余量等级。
铸件的公差等级和加工余量等级确定后,加工余量数值可根据 GB/T11350-1989选取;公差的数值可按GB6414—86 选取。
为简化铸造工艺,铸件上的小孔和槽可以不铸出,而采用机械加工。
一般铸铁件上直径
<30mm、铸钢件上直径<40mm的孔可以不铸出。
(2)起模斜度
【起模斜度】为使模样(或型芯)易从铸型(或芯盒)中取出,在模样(或芯盒)上与起模方向平行的壁的斜度称为起模斜度,可用角度α 或宽度 a表示,提倡使用宽度a。
模样的起模斜度可采用增加壁厚、加减壁厚、减小壁厚三种取法,如图所示。
对于需要机械加工的壁必须采用增加壁厚法。
起模斜度需要增减的数值可按有关标准选取,采用粘土砂造型时的起模斜度可按
JB/T5105—1991确定。
一般木模的斜度α =0.3°~3°,a=0.6~3.0mm;金属模的斜度
α=0.2°~2°,a=0.4~2.4mm。
模样越高,斜度越小。
当铸件上的孔高度与直径之比小于1(H/D<1)时,可用自带芯子的方法铸孔,用自带芯子的起模斜度一般应大于外壁斜度。
(a) 增加铸件厚度(b)加减铸件厚度(c)减小铸件厚度
(壁厚<8mm)(壁厚:8mm~12mm)(壁厚>12mm)
起模斜度的取法
(3)收缩率
为补偿铸件在冷却过程中产生的收缩,使冷却后的铸件符合图样的要求,需要放大模样的尺寸,放大量取决于铸件的尺寸和该合金的线收缩率。
一般中小型灰铸铁件的线收缩率约取 1%;非铁金属的铸造收缩率约取1.5%;铸钢件的铸造收缩率约取2%。
( 4)铸造圆角
【铸造圆角】模样壁与壁的连接和转角处要做成圆弧过渡,称为铸造圆角。
铸造圆角可减少或避免砂型尖角损坏,防止产生粘砂、缩孔、裂纹。
但铸件分型面的转角处不能有圆角。
铸造内圆角的大小可按相邻两壁平均壁厚的 1/3~1/5选取,外圆角的半径取内圆角的一半。
(5)芯头
【芯头】是指砂芯的外伸部分,用来定位和支承砂芯。
如图所示。
芯头有垂直和水平芯头两种。
芯座是指铸型中专为放置芯头的空腔。
芯头和芯座尺寸主要有芯头长度 L(高度H)、芯头斜度α 、芯头与芯座装配隙s等,其数值与型芯的长度(高度)和直径有关,应查阅相关资料后确定(本书略)。
(a)垂直芯头(b)水平芯头
芯头的结构
四、浇注系统
【浇注系统】是为填充型腔和冒口而开设于铸型中的一系列通道。
(1)浇注系统的组成与作用通常有浇口杯、直浇道、横浇道、内浇道和冒口等组成。
合理地设计浇注系统,可使金属液平稳地充满铸型型腔;控制金属液的流动方向和速度;调节铸件上各部分的温度,控制冷却凝固顺序;阻挡夹杂物进入铸型型腔。
冒口起补缩、排气和集渣作用。
(2)浇注系统的类型按金属液导入型腔的位置,浇注系统可分为底注式、顶注式、中注式、阶梯式等,见下图。
浇注系统的类型
五、铸造工艺图绘制举例
【铸造工艺图】是表示分型面、浇注位置、型芯结构和尺寸、浇注系统、工艺参数等的图样,可按规定工艺符号或文字标注在铸件图上或另绘工艺图。
例:下图为衬套零件图,材料为HT200,采用砂型铸造,年生产量200件,试绘出铸造工艺图。
(1)结构分析、确定造型方法、浇注位置和分型面。
零件上φ 48mm的孔要铸出,但内孔的小台阶不铸出,故采用简单的圆棒型芯;为简化铸造工艺,φ8mm的小孔和铸件侧壁的小台阶和小凹槽均不铸出。
铸件高度不大,可采用两箱整体模造型、垂直浇注。
分型面选在φ160mm的端面处,采用二箱整体模造型。
(2)工艺参数确定。
加工余量铸件各个面都要加工,故都应有余量。
砂型铸造灰铸铁件的公差及配套的加工余量等级为14/H。
顶面和孔的加工余量等级降一级(取J级),加工余量数值可查GB/T11350-1989选取,φ160mm和φ104mm圆周面双侧加工,每侧余量为6.0mm,底面的加工余量为6.0mm,顶面的加工余量为7.0mm,内孔的每侧的加工余量为6.0mm。
起模斜度在垂直于分型面处(平行于起模方面),按增厚法确定起模斜度。
取宽度a=1.0mm。
图9-21b中“7/6”表示考虑了加工余量和起模斜度后,上端与下端的余量。
线收缩率由于是小批生产,铸件各尺寸方向的铸造收缩率可取相同的数值,取铸造收缩率为1%。
芯头该芯头为垂直芯头。
查有关手册(本书略)得芯头尺寸,如铸造工艺图所示。
铸造圆角铸造圆角按(1/3~1/5)壁厚的方法,取R内为8mm;R外为4mm。
(3)绘出铸造工艺图。
如下图所示(不含浇注系统)。
六、铸件图
【铸件图】是反映铸件实际尺寸、形状和技术要求的图形,是铸造生产验收和检验的主要依据。
铸件图应在完成铸造工艺图的基础上绘制,下图为衬套的铸件图。
零件图铸造工艺图铸件图
衬套零件图、铸造工艺图、铸件图。