基于PLC的物料分拣系统设计文献综述
基于plc货物分拣控制系统设计
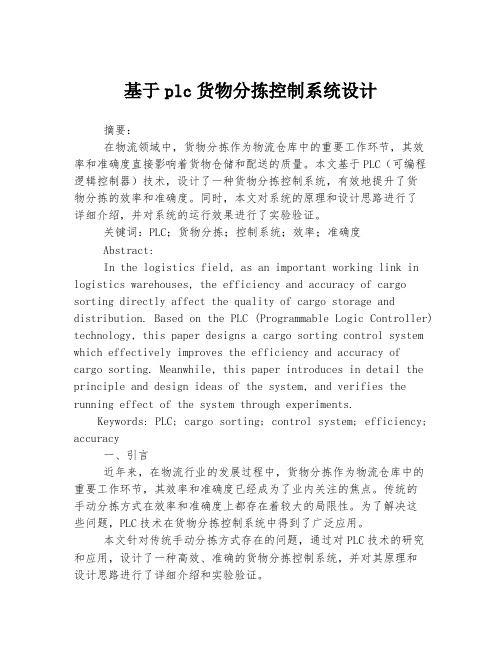
基于plc货物分拣控制系统设计摘要:在物流领域中,货物分拣作为物流仓库中的重要工作环节,其效率和准确度直接影响着货物仓储和配送的质量。
本文基于PLC(可编程逻辑控制器)技术,设计了一种货物分拣控制系统,有效地提升了货物分拣的效率和准确度。
同时,本文对系统的原理和设计思路进行了详细介绍,并对系统的运行效果进行了实验验证。
关键词:PLC;货物分拣;控制系统;效率;准确度Abstract:In the logistics field, as an important working link in logistics warehouses, the efficiency and accuracy of cargo sorting directly affect the quality of cargo storage and distribution. Based on the PLC (Programmable Logic Controller) technology, this paper designs a cargo sorting control system which effectively improves the efficiency and accuracy of cargo sorting. Meanwhile, this paper introduces in detail the principle and design ideas of the system, and verifies the running effect of the system through experiments.Keywords: PLC; cargo sorting; control system; efficiency; accuracy一、引言近年来,在物流行业的发展过程中,货物分拣作为物流仓库中的重要工作环节,其效率和准确度已经成为了业内关注的焦点。
基于PLC的物料分拣传送控制系统的设计与实现

基于PLC的物料分拣传送控制系统的设计与实现1. 引言1.1 研究背景研究背景:随着工业自动化水平的不断提高,物料分拣传送系统在各种生产场景中得到广泛应用。
传统的人工分拣方式效率低下、误差率高,无法满足生产需求。
基于PLC的物料分拣传送控制系统成为自动化生产中的重要组成部分。
PLC作为控制核心,能够实现物料的准确分拣和传送,提高生产效率和质量。
目前,国内外对于基于PLC的物料分拣传送控制系统的研究与应用已取得了一定进展,但仍存在一些问题和挑战。
传统的分拣机械结构复杂、易损坏,需要频繁维护和更换。
对于多种物料的不同尺寸、形状和重量,如何实现高效的自动分拣也是一个亟待解决的问题。
本研究旨在设计并实现一种基于PLC的物料分拣传送控制系统,通过合理选择传感器和执行器,编写有效的PLC程序,实现对各类物料的准确分拣和传送。
对系统的稳定性和可靠性进行评估,为自动化生产提供更可靠的技术支持。
1.2 研究目的研究目的主要有以下几个方面:通过对基于PLC的物料分拣传送控制系统的设计与实现进行深入研究,可以提高生产线的自动化水平,提升物料分拣的效率和准确性,减少人力成本,为企业节约生产成本。
通过研究该系统的设计原理和技术指导,可以为其他类似系统的设计提供参考和借鉴,推动智能制造技术的发展。
研究该系统的应用前景,可以为相关企业和机构提供决策依据,引领行业的发展方向,促进工业生产的现代化和智能化进程。
通过对这些研究目的的实现,可以全面提升物料分拣传送控制系统的性能和稳定性,为企业的生产制造提供有力支持。
1.3 研究意义研究意义: 物料分拣传送控制系统作为自动化生产线中至关重要的一环,在工业生产中起着极为重要的作用。
通过对基于PLC的物料分拣传送控制系统的设计与实现的研究,可以提高生产线的效率和准确性,降低人力成本,减少错误率,提高生产线的自动化程度。
该研究也有助于实现生产线的智能化升级,提升企业在市场竞争中的优势地位。
基于PLC的物料分拣传送控制系统的设计与实现

基于PLC的物料分拣传送控制系统的设计与实现1. 引言1.1 背景介绍物料分拣传送系统是现代生产线中必不可少的一部分,它可以有效地提高物料分拣的效率和准确性,降低人工成本和错误率。
传统的物料分拣传送系统多采用人工操作或简单的机械传送装置,存在着工作效率低、错误率高、适应性差等问题。
随着科技的不断发展和进步,基于PLC的物料分拣传送控制系统应运而生,它利用先进的电气控制技术和自动化技术,实现了传统系统无法实现的功能和优势。
基于PLC的物料分拣传送控制系统具有高性能、可靠性强、灵活性好等特点,可以根据不同的需求和物料特性进行个性化定制,能够满足现代生产线对物料分拣传送的高效、精准要求。
在自动化生产中,PLC已经成为控制系统的核心部件,广泛应用于各种领域,包括工业自动化、交通运输、能源设备等。
因此,研究基于PLC的物料分拣传送控制系统的设计与实现具有重要的意义和价值。
通过此研究,可以提高生产线的自动化水平,提升生产效率,降低成本,实现智能化生产,促进工业的发展和进步。
1.2 研究意义基于PLC的物料分拣传送控制系统能够实现对物料的高效分拣和传送,提高了生产效率和质量,降低了人力成本,使生产过程更加智能化。
这对于促进制造业转型升级,提高企业竞争力具有重要意义。
基于PLC的物料分拣传送控制系统能够实现物料的实时监测和数据采集,为生产过程提供了重要的数据支撑。
通过数据分析和处理,可以实现生产过程的优化和智能化管理,提高生产效率和质量。
基于PLC的物料分拣传送控制系统具有灵活性强、可靠性高、成本低等诸多优点,适用于各种规模和类型的制造企业。
研究基于PLC 的物料分拣传送控制系统的设计与实现,对于推动工业自动化发展,提高制造业水平,具有重要的理论和实践价值。
1.3 研究目的本文旨在设计和实现一种基于PLC的物料分拣传送控制系统,旨在解决传统物料分拣传送系统中存在的一些不足之处,提高物料分拣传送效率和准确性。
具体目的包括:1. 研究分析传统物料分拣传送系统的设计原理和工作流程,总结其优缺点;2. 提出基于PLC的物料分拣传送系统设计方案,探讨其适用性和优势;3. 进行PLC编程与控制逻辑设计,确保系统能够稳定运行并实现准确的物料分拣传送;4. 设计物料传送控制系统的硬件,选择合适的传感器、执行器等设备,保证系统可靠性和稳定性;5. 进行系统实验并对实验结果进行分析,评估系统的性能和可靠性;6. 评估设计与实现的效果,找出存在的问题并提出改进方向;7. 展望未来,探讨如何进一步完善基于PLC的物料分拣传送控制系统,提高其智能化和自动化水平。
基于PLC的物料分拣系统设计文献综述

本科毕业设计文献综述基于PLC旳物料分拣系统设计学生:xxx学号:xx专业:机械设计制造及其自动化班级:xxx指导教师:xxx机械与材料工程学院二O一二年十二月文献综述序言本篇毕业设计(论文)题目是《基于PLC旳物料分拣系统设计》。
目前由于货品分拣系统中,挥霍了巨大旳人力物力, 并且严重影响了物流旳流动速度。
伴随竞争旳加剧, 人们对物流旳流动速度规定越来越高, 这样旳货品分拣系统已经远远不能满足现代化物流管理旳需要。
现代化旳货品分拣系统, 一种先进旳货品分拣系统, 对于系统集成商、仓储业、运送业、后勤管理业等都是至关重要旳。
建立一种先进旳货品分拣系统, 结合有效旳吞吐量,不仅可以节省成本, 并且可以大大提高工作效率, 明显减少工人旳劳动强度。
使用这样旳货品分拣系统, 完全屏弃了使用书面文献完毕货品分拣旳老式措施, 采用高效、精确旳电子数据旳形式, 提高效率, 节省劳动力。
使用这样旳货品分拣系统, 不仅可以迅速完毕简朴旳存储提取, 并且可以以便地根据货品旳尺寸、提货旳速度规定、装卸规定等实现复杂货品旳存储与提取。
结合必要旳仓库管理软件, 可以真正实现仓库旳现代化管理, 充足实现仓库空间旳合理运用, 明显提高企业旳物流速度, 为企业发明、保持市场竞争优势发明条件。
正文物料分拣采用可编程控制器PLC进行控制,能持续大批量地分拣货品,分拣误差率低且劳动强度大大减少,可明显提高劳动生产率,分拣系统能灵活地与其他物流设备无缝连接,实现对物料信息流旳分派和管理。
伴随工业自动化旳普及和发展,可编程控制器旳需求量逐年增大,应用领域也越来越广。
一、研究旳目旳和意义伴随社会旳不停发展, 市场竞争旳日益剧烈, 每个生产企业都急切地需要改善生产技术,提高生产效率, 尤其在需要进行材料分拣旳企业, 以往一直采用人工分拣旳措施, 导致生产效率低, 生产成本高, 企业旳竞争能力相称差, 材料旳自动分拣已成为企业旳唯一选择[1]。
基于PLC控制的多传感器物料自动分拣系统设计

基于PLC控制的多传感器物料自动分拣系统设计一、概述随着工业自动化技术的不断发展,物料自动分拣系统在生产线上发挥着越来越重要的作用。
传统的物料分拣主要依赖人工操作,效率低下且易出错。
为了提升生产效率,减少人为因素导致的错误,基于PLC控制的多传感器物料自动分拣系统应运而生。
该系统结合了可编程逻辑控制器(PLC)与多种传感器技术,实现对物料的高效、准确、快速分拣。
PLC作为系统的核心控制器,负责接收传感器信号,根据预设程序进行判断和处理,进而控制执行机构对物料进行分拣。
同时,多传感器技术为系统提供了丰富的物料信息,包括形状、颜色、大小、重量等多个维度,使得系统能够适应不同物料的分拣需求。
基于PLC控制的多传感器物料自动分拣系统不仅提高了生产线的自动化程度,还显著提升了物料分拣的准确性和效率。
该系统具有可编程、可扩展的特点,能够根据生产需求进行灵活调整和优化。
该系统在制造业、物流业等领域具有广泛的应用前景。
本文将对基于PLC控制的多传感器物料自动分拣系统的设计进行详细介绍,包括系统的整体架构、硬件组成、软件设计以及实际应用案例等。
通过本文的阐述,旨在为相关领域的研究人员和技术人员提供有益的参考和借鉴。
1. 物料分拣系统的重要性物料分拣系统的核心功能是将不同类型的物料按照预设的规则和要求进行准确、快速的分类和传输,确保后续生产工序的顺利进行。
一个高效、稳定的物料分拣系统不仅可以显著提高生产效率,减少人力成本,还能有效避免因人为操作失误导致的生产事故和质量问题。
该系统还能实现对物料信息的实时跟踪和管理,为企业的生产管理和决策提供有力支持。
基于PLC控制的多传感器物料自动分拣系统通过集成先进的可编程逻辑控制器(PLC)和多种传感器技术,能够实现对物料的高精度识别、快速分拣和智能控制。
PLC作为系统的核心控制器,负责处理各种传感器采集的数据信息,并根据预设的程序逻辑进行决策和控制。
而多种传感器的应用则能够实现对物料的多维度信息感知,如形状、大小、颜色、重量等,从而确保分拣的准确性和可靠性。
【《基于plc的自动分拣系统》4400字(论文)】
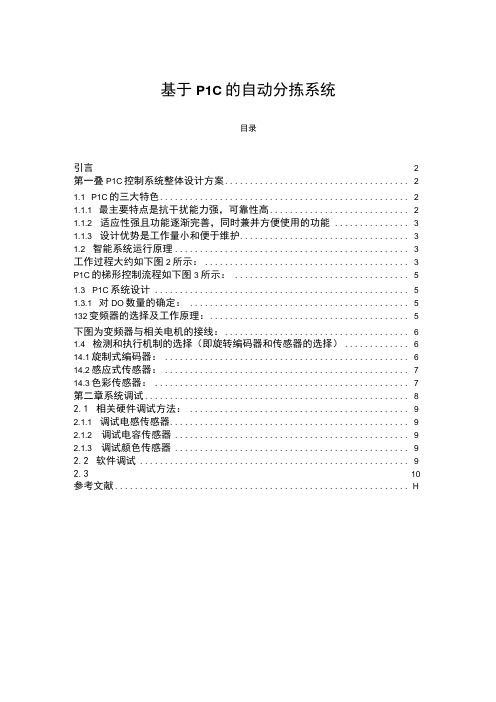
基于P1C的自动分拣系统目录引言2第一叠P1C控制系统整体设计方案 (2)1.1 P1C的三大特色 (2)1.1.1 最主要特点是抗干扰能力强,可靠性高 (2)1.1.2 适应性强且功能逐渐完善,同时兼并方便使用的功能 (3)1.1.3 设计优势是工作量小和便于维护 (3)1.2 智能系统运行原理 (3)工作过程大约如下图2所示: (3)P1C的梯形控制流程如下图3所示: (5)1.3 P1C系统设计 (5)1.3.1 对DO数量的确定: (5)132变频器的选择及工作原理: (5)下图为变频器与相关电机的接线: (6)1.4 检测和执行机制的选择(即旋转编码器和传感器的选择) (6)14.1旋制式编码器: (6)14.2感应式传感器: (7)14.3色彩传感器: (7)第二章系统调试 (8)2.1相关硬件调试方法: (9)2.1.1 调试电感传感器 (9)2.1.2 调试电容传感器 (9)2.1.3 调试颜色传感器 (9)2.2软件调试 (9)2.310参考文献........................................................... H引言在物料搬运系统中存在智能分拣系统这个分支系中,能够为后续机械化操作打下可靠的基础。
不仅在化工、电气行业得到了应用、近期在制药行业也逐渐兴起。
目前,由于目前市场上自动化分拣设备前景良好,再加上人力成本的逐年上升趋势,智能P1C更新速度愈发迅速。
众所周知,P1C以其灵活可靠、易于扩展、通用性强等特性,逐渐成为自动化生产领域的主控设备之一。
本次论文结合变频技术、遥感技术等,来进行最终的设计。
第一章P1C控制系统整体设计方案1.1P1C的三大特色1.1.1最主要特点是抗干扰能力强,可靠性高传统的继电器■接触器控制系统由于使用了大量的机械触点,使得存在良好的抗干扰能力,但由于设备之间的接线比较复杂,而且由于设备的老化,触点脱焊、抖动,在分合闸时触点会被电弧损坏,同时由于机械触点之间容易出现接触不良的状况,会使得出现故障的可能性提高,从而大大降低了系统的可靠性。
基于PLC的物料输送分拣系统监控程序设计

基于PLC的物料输送分拣系统监控程序设计摘要物料输送分拣系统在现代制造业中起着非常重要的作用。
为了确保物料输送分拣系统的正常运行,实时监控系统的设计至关重要。
本文基于PLC(可编程逻辑控制器)技术,设计了一个用于监控物料输送分拣系统的程序。
关键词:PLC、物料输送分拣系统、监控程序一、引言物料输送分拣系统通常包括一个机械装置和一个自动控制系统。
自动控制系统使用PLC来控制机械装置的运行。
为了确保物料输送分拣系统的正常运行,需要设计一个实时监控系统来监测整个过程。
本文基于PLC技术,设计了一个用于监控物料输送分拣系统的程序。
二、系统结构物料输送分拣系统主要由输入设备、PLC、机械装置、传感器和输出设备组成。
监控程序运行在PLC上,通过输入设备接收输入信号,通过输出设备发送控制信号。
传感器用于检测物料的位置和状态,并通过输入设备将这些信息发送给PLC。
机械装置根据PLC发送的控制信号来完成分拣任务。
1.系统状态监测监控程序首先需要监测系统的状态。
通过读取传感器的信号,监控程序可以检测物料的位置和状态。
根据这些信息,程序可以判断系统是否正常工作。
2.报警处理如果监控程序检测到异常情况,例如物料堵塞或机械装置故障,它将触发报警机制。
报警机制可以通过发送声音或闪光的信号来提醒操作员。
同时,报警信息也可以通过输出设备发送给上位计算机。
3.运行日志记录监控程序可以记录系统的运行日志。
日志包括系统的状态、报警信息和其他重要的运行数据。
这些日志可以用于系统故障的分析和故障排除。
4.远程监控通过在监控程序中添加远程监控功能,可以实现对物料输送分拣系统的远程监控。
操作员可以通过上位计算机或手机APP等远程设备来监视系统的运行状态,并进行远程控制。
四、实验结果本文设计的监控程序在物料输送分拣系统中进行了实验验证。
实验结果表明,监控程序可以实时监测系统的状态,并在检测到异常情况时触发报警机制。
同时,它还可以记录系统的运行日志,方便系统故障的分析和故障排除。
基于PLC控制的多传感器物料自动分拣系统设计
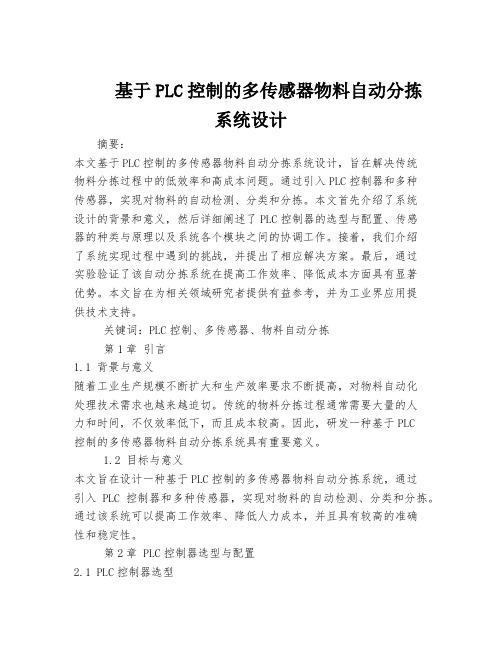
基于PLC控制的多传感器物料自动分拣系统设计摘要:本文基于PLC控制的多传感器物料自动分拣系统设计,旨在解决传统物料分拣过程中的低效率和高成本问题。
通过引入PLC控制器和多种传感器,实现对物料的自动检测、分类和分拣。
本文首先介绍了系统设计的背景和意义,然后详细阐述了PLC控制器的选型与配置、传感器的种类与原理以及系统各个模块之间的协调工作。
接着,我们介绍了系统实现过程中遇到的挑战,并提出了相应解决方案。
最后,通过实验验证了该自动分拣系统在提高工作效率、降低成本方面具有显著优势。
本文旨在为相关领域研究者提供有益参考,并为工业界应用提供技术支持。
关键词:PLC控制、多传感器、物料自动分拣第1章引言1.1 背景与意义随着工业生产规模不断扩大和生产效率要求不断提高,对物料自动化处理技术需求也越来越迫切。
传统的物料分拣过程通常需要大量的人力和时间,不仅效率低下,而且成本较高。
因此,研发一种基于PLC控制的多传感器物料自动分拣系统具有重要意义。
1.2 目标与意义本文旨在设计一种基于PLC控制的多传感器物料自动分拣系统,通过引入PLC控制器和多种传感器,实现对物料的自动检测、分类和分拣。
通过该系统可以提高工作效率、降低人力成本,并且具有较高的准确性和稳定性。
第2章 PLC控制器选型与配置2.1 PLC控制器选型在设计基于PLC控制的多传感器物料自动分拣系统时,首先需要选择合适的PLC控制器。
根据实际需求和系统规模选择适合的型号,并考虑其性能、稳定性、可编程能力等因素。
2.2 PLC控制器配置根据实际需求配置PLC控制器,并编写相应程序进行逻辑设计。
配置过程中需要考虑输入输出模块数量、通信接口等因素,并确保与其他模块之间能够进行有效连接。
第3章传感器种类与原理3.1 光电传感器光电传感器是一种常用的传感器,用于检测物料的存在与否。
本文介绍了光电传感器的种类、工作原理以及在物料自动分拣系统中的应用。
3.2 压力传感器压力传感器可用于检测物料的重量、压力等特征。
- 1、下载文档前请自行甄别文档内容的完整性,平台不提供额外的编辑、内容补充、找答案等附加服务。
- 2、"仅部分预览"的文档,不可在线预览部分如存在完整性等问题,可反馈申请退款(可完整预览的文档不适用该条件!)。
- 3、如文档侵犯您的权益,请联系客服反馈,我们会尽快为您处理(人工客服工作时间:9:00-18:30)。
前言本篇毕业设计(论文)题目是《基于PLC的物料分拣系统设计》。
目前由于货物分拣系统中,浪费了巨大的人力物力, 而且严重影响了物流的流动速度。
随着竞争的加剧, 人们对物流的流动速度要求越来越高, 这样的货物分拣系统已经远远不能满足现代化物流管理的需要。
现代化的货物分拣系统, 一个先进的货物分拣系统, 对于系统集成商、仓储业、运输业、后勤管理业等都是至关重要的。
建立一个先进的货物分拣系统, 结合有效的吞吐量,不但可以节省成本, 而且可以大大提高工作效率, 显著降低工人的劳动强度。
使用这样的货物分拣系统, 完全屏弃了使用书面文件完成货物分拣的传统方法, 采用高效、准确的电子数据的形式, 提高效率, 节省劳动力。
使用这样的货物分拣系统, 不但可以快速完成简单的存储提取, 而且可以方便地根据货物的尺寸、提货的速度要求、装卸要求等实现复杂货物的存储与提取。
结合必要的仓库管理软件, 可以真正实现仓库的现代化管理, 充分实现仓库空间的合理利用, 显著提高企业的物流速度, 为企业创造、保持市场竞争优势创造条件。
正文物料分拣采用可编程控制器PLC进行控制,能连续大批量地分拣货物,分拣误差率低且劳动强度大大降低,可显著提高劳动生产率,分拣系统能灵活地与其他物流设备无缝连接,实现对物料信息流的分配和管理。
随着工业自动化的普及和发展,可编程控制器的需求量逐年增大,应用领域也越来越广。
一、研究的目的和意义伴随社会的不断发展, 市场竞争的日益激烈, 每个生产企业都急切地需要改善生产技术,提高生产效率, 特别在需要进行材料分拣的企业, 以往一直采用人工分拣的方法, 导致生产效率低, 生产成本高, 企业的竞争能力相当差, 材料的自动分拣已成为企业的唯一选择[1]。
动分拣系统一般由控制装置、分类装置、输送装置及分拣道口四个部分组成。
控制装置的作用是识别、接收和处理分拣信号,依照分拣信号的要求指示分类装置、输送装置来进行对应的作业。
分类装置的用处是根据控制装置发出的分拣指令,当具有相同分拣信号的物品经过该装置时,该装置发生动作,使其更改输送装置上的运行方向进入其它输送机或进入分拣道口。
输送装置的主要组成部分是传送带或输送机,它的主要用途是使待分拣物品通过控制装置、分类装置,并沿着固定线路来运送物品。
分拣道口是已分拣物品脱离主输送机 (或主传送带)进入集货区域的通道。
可编程序控制器是现代化工业生产的三大支柱之一,具有极为广泛的应用范围。
目前,市场上销售的设备提供的实验能力相对较弱,同时还存在安全隐患,一方面危及人身安全,另一方面还危及设备安全。
因此,拟设计开发一种实验平台,使其可以最大可能地提高设备利用率,改善实验效果,提高实验层次。
用可编程控制器来实现材料分选装置的控制系统,以及该系统软、硬件设计方法,实验证明该系统实现简单、经济,可以有效地对金属材料与非金属以及其颜色的分选。
分析了现代化工厂材料分选在控制与管理的现状,结合工厂的实际状况阐述了材料分选控制系统的工作原理,给出了一种简单实用的工厂材料分拣装置控制系统的PLC设计方案。
可编程序控制器在工业自动化中的地位极为重要,广泛的应用于各个行业。
二、分拣机发展趋势我国自动分拣机的应用大约始于1980 年代,近期的市场兴起和技术发展始于1997 年。
自动分拣的概念先在机场行李处理和邮政处理中心得到应用,然后普及到其他行业。
随着业界对现代化物流的实际需求的增长,各行业对高速精确的分拣系统的要求正在不断地提高。
这一需求最明显地表现在烟草、医药、图书及超市配送领域,并有望在将来向化妆品及工业零配件等领域扩展。
这些领域的一个共同特点是产品的种类繁多、附加值高、配送门店数量多、准确性要求高和人工处理效率低等特点。
国外自动分拣系统以美国、日本及欧洲为代表的发达国家为例,在分拣系统的应用上呈现出自动化程度越来越高的特点。
自动分拣系统已成为发达国家大中型物流中心、配送中心或流通中心不可缺少的一部分。
自动分拣系统( Automated Sorting System )是二战后在美国、日本以及欧洲的大中型物流中心广泛采用的一种分拣系统,参照邮局分拣信件自动化的经验配置而成。
一般由控制装置、分类装置、输送装置及分拣道口四部分组成,它们通过计算机网络联结在一起,配合人工控制及相应的人工处理环节构成一个完整的分拣系统。
其主要特点有三: 能连续、大批量地分拣货物,分拣误差率极低,分拣作业基本实现无人化。
自动分拣系统中人员的使用仅局限于进货时的接货、系统的控制、系统的经营、管理与维护等,这恰好适应了国外企业对减少人员使用、减轻员工劳动强度、提高人员使用效率的要求,因此受到了他们的广泛重视。
三、PLC 的国内外状况1968 年,美国通用汽车公司为了适应汽车型号不断更新的工业需求,试图招标研制一种能尽量减少因汽车型号变动而重新设计汽车装配线上各种继电器控制线路的方法。
1969 年,美国数字设备公司(DEC)研制成功了世界上第一台可编程序逻辑控制器(Programmable Logic Controller),简称PLC。
1971年,日本从美国引进P L C技术并加以消化,成功研制日本首台PLC。
我国对 PLC 的研制和应用起步比较晚,但是发展速度很快。
最早应用大约始于 1980 年代,近期市场兴起和技术发展始于 1997 年。
我国可编程控制器的引进、应用、研制、生产是伴随着改革开放开始的。
最初是在引进设备中大量使用了可编程控制器。
接下来在各种企业的生产设备及产品中不断扩大了 PLC 的应用。
目前,我国自己已可以生产中小型可编程控制器。
上海东屋电气有限公司生产的 CF 系列、杭州机床电器厂生产的 DKK 及 D 系列、大连组合机床研究所生产的 S 系列、苏州电子计算机厂生产的 YZ 系列等多种产品已具备了一定的规模并在工业产品中获得了应用。
此外,无锡华光公司、上海乡岛公司等中外合资企业也是我国比较著名的 PLC 生产厂家。
目前,PLC 技术已被广泛应用于石油、化工冶金、轻工、机械、电力等各行业,以实现逻辑、步进、数字、机器人、模拟量等的自动控制。
继美国以后,日本、德国、法国等工业发达国家也相继研制出自己的 PLC,并发展了各自的PLC技术。
目前,世界上众多的 PLC 制造厂家中比较著名的大公司有美国的 AB 公司、哥德公司、德州仪器公司、通用电气公司、德国西门子公司、日本三菱、东芝、富士和立石公司等。
另外,仅在美国登记的 PLC 公司就有 80 多家,产品达 300 多种。
PLC 正以无比可拟强大优势逐渐取代传统的继电接触控制系统成为工业控制领域中占主导地位的基础自动化设备。
可以预期,随着我国现代化进程的深入,PLC 在我国将有更广阔的应用天地。
Plc 在材料分拣过程中有许多优点比如自动化程度高,可控性好,具有较强的抗干扰能力;其商业价值体现在(1)提高了效益节省了人力和资金支出(2)采用PLC控制技术,因此大幅度减少了因人工操作失误而引起的错取等事故(3)大幅度提高了工效四、分拣系统的应用前景对于分拣系统的应用前景,主要着眼于分拣系统的可靠性,优越性,应用领域的适用性以及系统的经济效益、成本等方面来考虑。
1、分拣系统能灵活的与其他物流设备实现无缝连接,如自动化仓库、各种存储站、自动集放链、各种运载工具、机器人等。
实现对物料实物流的分配、对物料信息流的分配和管理。
2、采用分拣系统,人工分拣、堆置物料的劳动强度大大降低,操作人员无须为跟踪物料而进行大量的报表工作、登单工作,因而显著提高劳动生产率。
另外,非直接劳动力如物料仓库人员、发料员以及运货员工作量的减少甚至取消又进一步直接降低了作业成本。
3、由于分拣系统运行平稳、安全性高,同时,人工拣取物料的作业量降低,对物品的损坏减少,为顾客假造了更多的价值,为公司赢得了更多的信誉和商机。
4、由于分拣系统采用标准化、模块化的组装,具有系统布局灵活,维护、检修方便等特点使得它可以方便的放置使用场所,受场地原因影响不大。
结论21世纪PLC会有更大的发展。
从技术上看计算机技术的新成果会更多地应用于可编程控制器的设计和制造上会有运算速度更快、存储容量更大、智能更强的品种出现从产品规模上看会进一步向超小型及超大型方向发展从产品的配套性上看产品的品种会更丰富、规格更齐全完美的人机界面、完备的通信设备会更好地适应各种工业控制场合的需求。
伴随着计算机网络的发展可编程控制器作为自动化控制网络和国际通用网络的重要组成部分将在工业及工业以外的众多领域发挥越来越大的作用。
我国对PLC技术的研究和应用与美、日、德、法等工业发达国家相比还有较大差距但潜在市场广阔。
参考文献[1] 王煜东,传感器及应用[M],机械工业出版社,2008年[2] 梁森,自动检测与转换技术[M] ,北京机械工业出版社,2011年[3] 周美兰,忘岳宇, PLC电气控制与组态设计[M], 北京科学出版社,2003年[4] 王永华, 现代电气控制及PLC 应用技术.[M] ,北京北京航空航天大学出版社2000年[5] 李景学,可编程控制器应用系统设计及方法[M],化学工业出版社,2001年[6] 张万忠, 刘明芹, 电器与PLC控制技术[M],北京 化学工业出版社,2003年[7] 范金玲. 基于PLC的气动机械手控制系统设计[J]. 液压与气动,7期,[8] 周进明. 液压与气动技术[M]. 成都:西南交通大学出版社,2009.[9] 王兆义, 可编程序控制器教程[M], 北京机械工业出版社,2001年[10] 邓其贵. 变频器操作与工程项目运用[M]. 北京:北京理工大学出版社,2009.[11] 邓星钟. 机电传动控制[M]. 武汉华中科技大学出版社,2001.[12] 计时鸣. 机电一体化控制技术与系统[M]. 西安西安电子科技大学出版社,2009.[13] 华满香. 电气控制及PLC应用[M].北京大学出版社,2009.[14] 叶明超. 自动检测与转换技术[M].北京理工大学出版社,2009.[15] 章国华. 苏东. 典型生产线原理、安装与调试[M].北京理工大学出版社,2009.[16]Ren Sheng-le. Development of PLC-based Tension Control System. Chinese Journal of Aeronautics[M].20 (2007) 266-271.[17] Lozano, R. (Rogelio),.Adaptive control systems[M].Fresno:Witerwoof Inc.,1999[18] Du Toit, Chris. The design, documentation and maintenance of PLC software [R]. Elektron.IEEE.2006。