用ANSYS和FLUENT进行管壳式换热器整体分析
方瑛ANSYS作业-换热管的热分析
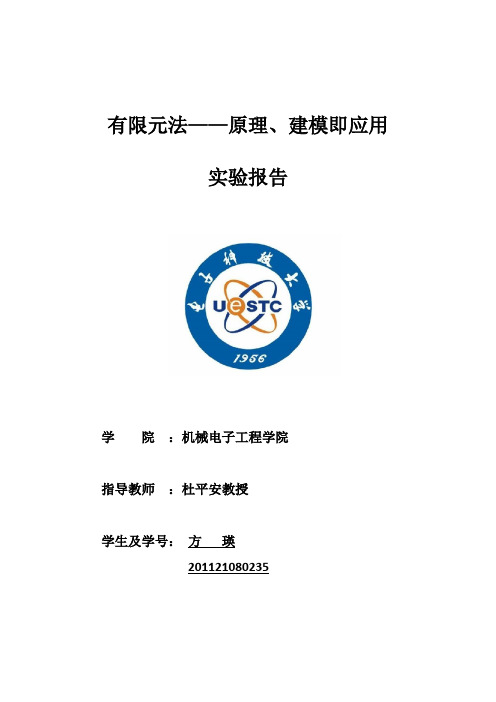
一个对话框,在 Directories 下选择的保存路径指定为初始设置中的
11
那个新建文件夹“方瑛 ANSYS 大作业”,在 Save Datebase to 下面 的输入栏中输入 Geometric model of pipe.db,单击 OK 按钮。
图 9 Offset WP 对话框
图 10 Partial Cylinder 对话框
8
3、 生成模板部分的模型:执行 Main Menu⟶Preprocessor⟶ Modeling⟶Create⟶Volumes⟶Block⟶By Dimensions,弹出 Create Block by Dimensions 对话框,如图 11 所示。输入如图所示 的数据,然后单击 OK 按钮,生成左端管板几何模型。执行 Main Menu⟶Preprocessor⟶Modeling⟶Copy⟶Volumes,弹出 Copy Volumes 拾取对话框,如图 12 所示。 用鼠标拾取刚刚生成的管板 左端部分模型,弹出另一个 Copy Volumes 对话框,如图 13 所示。 在 DX 栏中输入 0.3,单击 OK 按钮,生成的结果如图 14 所示。
Controls/Window Option 命令,弹出 Window Option 对话框。在 Location of triad 下拉列表中选择 Not Show 选项,单击 OK 按钮。
二、 定义单元类型及材料属性 1、定义单元类型
执行 Main Menu⟶Preprocessor⟶Element Type⟶ Add/Edit/Delete 命令,弹出 Element Type 对话框。单击 Add 按钮, 弹出 Library of Element Type 对话框。在左右列表中分别选择 Thermal solid 和 Brick 20node 90 选项,如图 4 所示。单击 OK 按 钮。
基于FLUENT的管壳式换热器流场的数值模拟与分析

基于FLUENT的管壳式换热器流场的数值模拟与分析鲍苏洋(南京工业大学机械与动力工程学院,南京210009)摘要:通过简化管壳式换热器模型,采用非结构网格划分,选用κ-ε湍流模型,应用CFD 软件FLUENT 对壳程流体流动和传热过程进行了数值模拟,得到了不同折流板间距情况下壳程流体温度场、压力场以及速度场的分布情况。
分析了折流板间距对壳程流体流场分布、换热器传热速率以及压力损失的影响,并得出了进口流速与传热量和压力损失之间的关系。
模拟结果与理论研究结果相符合,对管壳式换热器的设计和改进有一定的参考价值。
关键词:化工机械; 换热器; 数值模拟; 温度场; 速度场; 压力场Numerical Simulation and Analysis of Flow Field in Shell-and-Tube Heat Exchanger Based on FLUENTSuyang BAO( School of Mechanical and Power Engineering,Nanjing University of Technology,Nanjing 210009,China)Abstract: By simplified the model of shell-and-tube heat exchangers,adopted the unstructured mesh,chose the κ-εturbulence model to gain the static temperature field,velocity field and static pressure field distribution of shell by taking numerical simulation of the shell side turbulent flow and heat transfer process with the CFD software FLUENT at different baffle spacing.Analyzed the effect of baffle spacing on the distribution of shell fluid flow,heat transfer rate and pressure drop,also acquired the relationship between inlet velocity and heat transfer rate,pressure drop.The simulation results consistent with the theoretical results of shell-and-tube heat exchangers,which can be a reference for the design and improvement of shell-and-tube heat exchangers.Key words: chemical machinery; heat exchanger; numerical simulation; temperature field; velocity field; pressure field0 引言换热器是石油化工行业广泛应用的工艺设备,换热器不仅能够合理调节工艺介质的温度以满足生产工艺的需要,同时也是余热回收利用的有效设备[1]。
基于FLUENT的汽车管带式散热器整体模拟

基于FLUENT的汽车管带式散热器整体模拟邵兴杨【期刊名称】《《现代机械》》【年(卷),期】2019(000)004【总页数】4页(P25-28)【关键词】Fluent; 多孔介质; 散热性能; 风阻; 水阻【作者】邵兴杨【作者单位】贵州永红散热器公司贵州贵阳550000【正文语种】中文【中图分类】U464.138+.20 引言汽车管带式散热器换热是一个复杂的过程,存在流体流动,也存在换热过程。
在散热器初期设计时,无法制造试验件进行有效的试验分析,且简单的三维模拟无法进行精确地预测。
同时散热管、散热带结构尺寸较为微小,无法建立三维模型及划分边界层网格,这就会延长设计周期,增加成本,对新品的开发是不利的。
那么本文采用三维造型软件SolidWorks与流体有限元分析软件Fluent对散热器的散热性能、风阻、流阻进行三维模拟计算,利用多孔介质对散热管、散热带进行简化,达到初期预测的效果,并通过试验对模型进行验证。
1 整体仿真设计思路利用多孔介质体积平均化的思想,将散热管、散热带等简化为多孔介质。
计算局部单元得出多孔介质的惯性阻力系数、黏性阻力系数、等效孔隙率,再将所得系数带入整体模型的多孔介质中得出模拟数据并与试验进行对标,得出结论。
1.1 流阻整体数值模拟1.1.1 建立局部散热管模型及流体域模型图1 在SolidWorks建立散热管三维模型局部散热管与整体模型中散热管只是进口流量不同,本文按照散热管实际尺寸在SolidWorks中建立三维模型,如图1所示。
这是一个高频焊接扁管,取长度为50 mm。
将扁管模型导入Fluent中减出流域并划分网格,如图2所示。
根据散热器整体流量从1000 kg/h到5000 kg/h间,分配到48根散热管上,取每根散热管截面进口流速从0.334 m/s到1.671 m/s。
考虑到散热管长宽比较小,为获得较准的阻力,在流体壁面划分多层边界层网格。
图2 导入Fluent后的模型如表1所示,为局部散热管模拟计算在不同进口流速下的阻力。
基于FLUENT的管壳式换热器数值模拟分析

基于FLUENT的管壳式换热器数值模拟分析王文松; 刘霜【期刊名称】《《管道技术与设备》》【年(卷),期】2019(000)006【总页数】3页(P30-31,55)【关键词】管壳式换热器; FLUENT; 流场分析; 仿真模拟【作者】王文松; 刘霜【作者单位】成都理工大学工程技术学院四川乐山 614000【正文语种】中文【中图分类】TE80 引言换热器是一种广泛应用于化工、动力等行业的工业设备。
换热器能合理地调节工艺介质温度满足工艺流程的需求,也是余热、废热回收利用的有效装置[1]。
对管壳式换热器进行数值模拟分析,能有效提高换热器效率,对能源的高效利用十分重要。
随着近年来计算机和计算流体力学(CFD)的发展,CFD在研发和设计的各个阶段,具有费用低、速度快、能重复模拟分析复杂工况的优点[2]。
本文运用数值模拟的方法,对换热器进行三维建模和有限元分析,分析出了换热器内部温度场、速度场等变化关系。
1 换热器模型的建立1.1 控制方程研究对象为内部流体流动和传热过程,满足文献[3]中三类控制方程:质量守恒方程(连续性方程)、动量守恒方程和能量守恒方程。
1.2 换热器参数及计算工况本文中采用的换热器类型为壳管式换热器,为单壳程、单管程、单弓形折流板,换热器的长度为1 630 mm,壳体为Φ273×8 mm,换热管数40根,采用正三角形排列。
计算工质为热水和空气。
1.3 边界条件湍流效应对传热过程与流体流动有一定的影响,因此采用标准k-ε方程模型。
Pressure Based隐式(Implicit)求解,压力和速度解耦选用SIMPLE算法,采用二阶迎风格式,稳态不可压缩求解。
设置边界条件[4],进口流速为1 m/s,进口温度为298 K,壁面温度为378 K。
1.4 Gambit模型建立及网格划分应用Gambit建立模型和划分网格,网格划分优先使用六面体网格,不规则形状四面体网格。
六面体网格质量好,且收敛速度快,四面体网格适应能力强,能够较好地填充复杂的几何形状[5]。
基于FLUENT分析的管壳式换热器筒体腐蚀预测

基于FLUENT分析的管壳式换热器筒体腐蚀预测梁海明【摘要】换热器筒体腐蚀的影响因素众多,流体流速、温度、操作压力和介质成分等流体力学参数是影响换热器内腐蚀的关键因素。
现有的腐蚀检测方法难以全面考虑流体流速和温度等流体力学参数的影响,检测精度降低,对于缺陷的探测、描述、定位及确定缺陷大小的可靠性较差。
本文采用基于计算流体力学的数值模拟原理,利用有限体积法、RNG模型和壁面函数法,利用FLUENT软件对浮头管壳式换热器壳程流体的流动与传热进行了三维数值模拟,计算了管壳式换热器壳程的速度场、温度场和压力场,并在此基础上分析筒体的冲蚀规律。
%There are many factors affecting the corrosion of cylindrical shell of heat exchangers.The dynamic parameters such as fluid velocity,temperature,operating pressure are the most important factors.With the existing corrosion testing methods,it is difficult to fully consider the impact of fluid dynamic factors i.e.fluid velocity and temperature,etc.The testing accuracy is low.The reliabilities of defect detection,description,positioning and defect size determination are not stable and accurate.The flow and heat transfer of fluid in the shell side of floating-head shell-tube heat exchangers are simulated by 3-D numerical model with FLUENT saftware based upon fluid dynamics,limit volume method,RNG model and wall function method.The velocity field,temperature field and pressure field of shell-tube heat exchangers are calculated,and erosion corrosion is studied.【期刊名称】《石油化工腐蚀与防护》【年(卷),期】2012(029)003【总页数】6页(P46-51)【关键词】管壳式换热器;FLUENT;温度场;速度场;腐蚀【作者】梁海明【作者单位】中国石油化工股份有限公司茂名分公司,广东省茂名市525000【正文语种】中文【中图分类】TE986随着原油劣质化增加,设备腐蚀速率加剧。
基于ANSYS的换热器管板应力分析及其优化设计
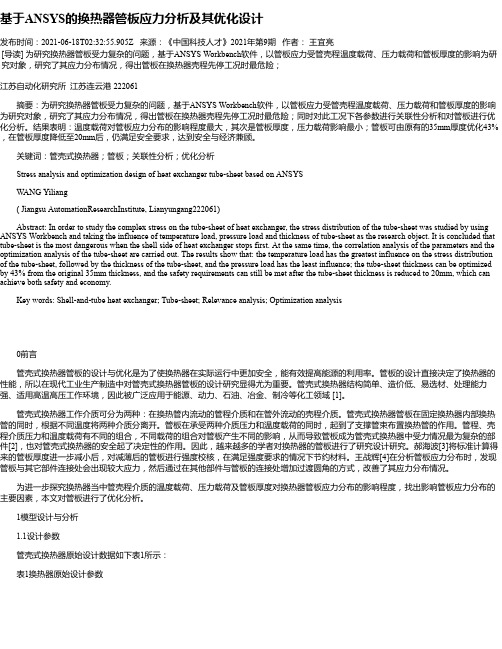
基于ANSYS的换热器管板应力分析及其优化设计发布时间:2021-06-18T02:32:55.905Z 来源:《中国科技人才》2021年第9期作者:王宜亮[导读] 为研究换热器管板受力复杂的问题,基于ANSYS Workbench软件,以管板应力受管壳程温度载荷、压力载荷和管板厚度的影响为研究对象,研究了其应力分布情况,得出管板在换热器壳程先停工况时最危险;江苏自动化研究所江苏连云港 222061摘要:为研究换热器管板受力复杂的问题,基于ANSYS Workbench软件,以管板应力受管壳程温度载荷、压力载荷和管板厚度的影响为研究对象,研究了其应力分布情况,得出管板在换热器壳程先停工况时最危险;同时对此工况下各参数进行关联性分析和对管板进行优化分析。
结果表明:温度载荷对管板应力分布的影响程度最大,其次是管板厚度,压力载荷影响最小;管板可由原有的35mm厚度优化43%,在管板厚度降低至20mm后,仍满足安全要求,达到安全与经济兼顾。
关键词:管壳式换热器;管板;关联性分析;优化分析Stress analysis and optimization design of heat exchanger tube-sheet based on ANSYSWANG Yiliang( Jiangsu AutomationResearchInstitute, Lianyungang222061)Abstract: In order to study the complex stress on the tube-sheet of heat exchanger, the stress distribution of the tube-sheet was studied by using ANSYS Workbench and taking the influence of temperature load, pressure load and thickness of tube-sheet as the research object. It is concluded that tube-sheet is the most dangerous when the shell side of heat exchanger stops first. At the same time, the correlation analysis of the parameters and the optimization analysis of the tube-sheet are carried out. The results show that: the temperature load has the greatest influence on the stress distribution of the tube-sheet, followed by the thickness of the tube-sheet, and the pressure load has the least influence; the tube-sheet thickness can be optimized by 43% from the original 35mm thickness, and the safety requirements can still be met after the tube-sheet thickness is reduced to 20mm, which can achieve both safety and economy.Key words: Shell-and-tube heat exchanger; Tube-sheet; Relevance analysis; Optimization analysis0前言管壳式换热器管板的设计与优化是为了使换热器在实际运行中更加安全,能有效提高能源的利用率。
基于ANSYS的固定管板换热器有限元分析

基于ANSYS的固定管板换热器有限元分析杨连红;王强;尹权【摘要】建立了固定管板式换热器的有限元分析模型,按标准方法计算六种工况下管板应力、壳程筒体的轴向应力以及换热管的轴向应力。
同时采用JB4732-1995的方法对管板与筒体的应力进行评定,采用GB/T151-2014的方法对换热管的轴向应力、拉脱力进行评定。
结果表明,管板及换热管满足结构的强度要求。
【期刊名称】《石油和化工设备》【年(卷),期】2016(019)005【总页数】6页(P5-10)【关键词】固定管板换热器;轴向应力;拉脱力;热应力;有限元法【作者】杨连红;王强;尹权【作者单位】中航黎明锦西化工机械集团有限责任公司,辽宁葫芦岛 125001;中航黎明锦西化工机械集团有限责任公司,辽宁葫芦岛 125001;中航黎明锦西化工机械集团有限责任公司,辽宁葫芦岛 125001【正文语种】中文固定管板换热器为石油化工装置中的典型设备之一,聚合物脱挥系统由上游换热器、一级脱挥罐、下游换热器以及二级脱挥罐组成,本文涉及的换热器是聚合物脱挥系统中的下游换热器,它起到对脱挥聚合物的加热挥发和分布器的作用。
换热器管程内介质为聚合物,其黏度很高,因此在换热管内加入螺旋内插件,是为了大幅度提高换热效果,但聚合物在换热器管内向下流动的压降很大,因此换热器内管需要高的压降。
物料在换热器出口流出直接降到下部二级脱挥罐内,挥发成分被真空泵抽出。
聚合物从二级脱挥罐底部出料,进入后续混合和造粒工段。
为了提高脱挥效果,物料在该换热器内需要60 s或更长的停留时间;设备公称直径为DN1400 mm,经工艺计算确定换热管为φ34×3 mm,管间距为48 mm,长度为2000 mm,需要换热管683根。
固定管板换热器结构简图如图1所示。
1.1 换热器设计参数如表1。
2.2 换热器材料参数如表2。
2.3 热分析材料特性参数如表3。
2.1 换热器模型的建立换热器设计时所有的开孔首先应满足GB150.1~150.4-2011《压力容器》[1]的相关规定。
基于ANSYS的翅片管式换热器端板的应力分析_王静
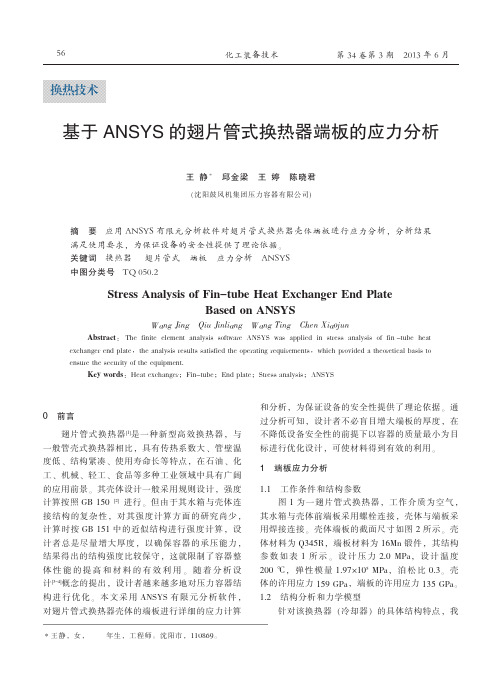
评定结果为 SⅠ=54.6 MPa<Smt=159 MPa SⅡ=58.4 MPa<1.5 Smt=238.5 MPa SⅣ= 59.5 MPa <3.0 Smt=477 MPa
评定结果合格, 筒体满足使用要求。 对于端板来说, 最大应力位置在方孔的角点
处。 在该位置沿端板厚度方向定义路径 (如图 5 所 示的 PATH 2), 沿该路径进行应力线性化, 计算得 到的端板的薄膜应力 SI=4.5 MPa, 局部薄膜应力SⅡ = 5 MPa, 薄膜应力+弯曲应力+二次应力 SⅣ= 22.9 MPa。 然 后 按 照 JB 4732 分 析 设 计 标 准 进 行 评 定 , 评定结果合格, 端板满足使用要求。
[9] 齐 洪 洋 , 高 磊 , 张 莹 莹. 管 壳 式 换 热 器 强 化 传 热 技 术 概述 [J] .压力容器, 2012,29 (7) : 73-78.
[10] Bell K J. Delaware method for shell side design. In: Palen J W, ed. Heat Exchanger Sourcebook. Washington: Hemisphere Publishing Corporation, 1986: 129-166.
[3] 付 磊 , 曾 燚 林 , 唐 克 伦. 管 壳 式 换 热 器 壳 程 流 体 流 动 与传热数值模拟 [J] . 压力容器, 2012, 29(5): 36-41.
[4] 徐 百 平 , 朱 东 升. 螺 旋 折 流 板 换 热 器 壳 程 流 动 与 传 热 数值模拟研究 [J] . 石油炼制与化工, 2005, 36 (10) : 33-36.
- 1、下载文档前请自行甄别文档内容的完整性,平台不提供额外的编辑、内容补充、找答案等附加服务。
- 2、"仅部分预览"的文档,不可在线预览部分如存在完整性等问题,可反馈申请退款(可完整预览的文档不适用该条件!)。
- 3、如文档侵犯您的权益,请联系客服反馈,我们会尽快为您处理(人工客服工作时间:9:00-18:30)。
用ANSYS和FLUENT进行管壳式换热器整体分析利用数值模拟计算软件进行管壳式换热器的流体力学和传热性能计算及评估已经成为开发和研究管壳式换热器的重要手段之一,由于结构和流道复杂,导致准确地进行换热器的流体力学性能和传热性能计算和评估有一定的困难。
而对换热器的结构性能进行准确分析一般都需要进行流固耦合模拟,如果要同时进行换热器的流体流动与传热和结构性能分析就更加困难。
般利用已知的平均温度或利用已知的换热(膜)系数对几何结构模型加载,而这些已知条件通常来源于手册提供的数据或者经验数据,并非来源于严格的换热器流体力学与传热工艺的数值计算,因此是产生结果计算偏差的主要原因之一。
目前文献对于给定工艺条件下管壳式换热器的整体温度场研究的并不多,由于准确的温度场是研究温差应力及其危害的前提,因此本文利用FLUENT 和ANSYS 软件对一台固定管板换热器的约束构件之间的整体结构在正常运行工况下的数值模拟问题进行了研究,首先从计算流体力学与传热的角度出发,利用FLUENT 软件进行换热器流体流动与传热的工艺状况数值模拟。
然后把FLUENT 软件的数值模拟结果导入ANSYS中作节点插值,完成温度场的重建,作为进行换热器的热分析以及结构分析的边界条件。
从而实现了管壳式换热器的FLUENT 和ANSYS 联合仿真模拟,综合整个过程可以很好地完成同一条件下换热器的流体力学与传热和结构性能分析,使得换热器的工艺性能计算与结构分析计算完整地结合在一起,计算精度更高。
1 CFD数值模拟本文研究的换热器结构示意如图1所示,在对实际结构进行合理简化的基础上,以影响流动和传热的主要结构建立了某固定管板式换热器温度场数值计算模型,采用分段模拟、整体综合的方法,利用FLUENT软件对该换热器在正常操作工况下的流动与传热情况进行数值模拟[8] ,得到计算流道上有关各个构件的壁温场分布。
图1 换热器结构示意图CFD模型正常工作状态下换热器的管程介质为饱和水蒸汽,蒸汽温度为110℃。
壳程介质为自来水,壳程流体进口速度为Vint=0.3m/s 。
如果完全按照实际结构建立计算模型,势必给建模以及数值分析计算带来不便,因此在数值计算之前,需要对换热器中对温度场(即流体流动)有影响的结构以及变形相互之间受到约束的构件进行分析,然后对整体结构进行适当简化。
根据换热器的安装和放置方式,运行中的换热器的结构关于垂直中心线对称,故建立对称模型。
在本文研究的换热器中,影响传热(温度场)的主要结构有导流筒、换热管、折流栅、管板、壳体,而变形受到约束的结构构件,主要有高温端和低温端管板、换热管束、壳程筒体。
因此实际建模中,模型应该包括对温度分布造成影响的结构以及产生热变形时受到约束的结构。
整台换热器的温度场数值计算模型由导流筒流道(进口段和出口段)和折流栅流道(总共六段)组成。
1.2 边界条件及求解对于三维流场数值计算的边界条件,一般分为入口边界条件、出口边界条件、固体壁面及对称面四大类型。
对于本文计算模型,边界条件的确定如下:入口边界条件:正常工作条件下,换热器壳程进口(接管)速度往往是给定的,同时考虑到壳程为不可压缩流体,故给出速度进口条件。
折流栅流道的入口边界根据上一流段的出口速度分布来给定。
出口边界条件:对于进口段模型其出口边界可定义为自由出流。
对于折流栅段,经试算后发现设置出口自由出流的边界条件也适宜。
固体壁面:直接将固体壁面定义为非滑移(静止)壁面。
壳程内件及壳体外壁面定为绝热边界,对于蒸汽流过的通道表面则为恒壁温。
在换热器中壳程内流体一般呈湍流流动状态。
本文模拟的换热器壳程流体流动的雷诺数Re≈3060 ,因此在进行模拟计算时,需要考虑为其建立合适的湍流模型。
工程上常用的是k-ε模型,考虑到RNG k-ε模型对于解这类问题的优越性,因此选择RNG k-ε模型进行分析求解。
本文计算模型中壳程流体不可压缩,不考虑体积力,因此选择分离求解器,可以更快得到收敛解。
在分离求解器中对流项的离散方法上,在计算时根据模型的情况适当结合一阶和二阶精度进行。
1.3 CFD 模拟结果通过数值模拟计算,可以知道换热器内部的流动和传热状况,可以获得流体或壁面的速度分布,温度和压力分布,还可以输出FLUENT 的温度场分析结果作为ANSYS 输入文件,为ANSYS 结构分析建立所需的边界条件,图2~图5 给出了Fluent 中典型且有代表性分段模型的壁面温度场分布。
图2 入口段CFD 模拟温度场分布图3 入口段管子及管板CFD 模拟温度场分布图4 折流栅段(四)CFD 模拟温度场分布图5 折流栅段(四)管子CFD 模拟温度场分布2 ANSYS有限元分析2.1 CFD结果数据插值本文所要解决的问题其实是要让边界条件能够从FLUENT 软件传递到ANSYS 软件中。
除了文件格式的不同外,最大的问题是网格不一致。
CFD 网格和FEA 网格往往不会一致,在CFD 里面得到结果后,需要把边界上的值从CFD 流体网格映射到FEA 固体网格上。
在CFD 里面做了流体和固体耦合传热分析后,需要把固体部分的温度输出转化到对应的ANSYS 模型,以便做热应力分析。
而ANSYS 里面的子模型操作命令(BFINT)可以把温度自由度从一个网格直接映射到另一个网格。
此时传热分析和结构分析可以使用两套不同的网格。
首先建立ANSYS 的固体结构模型,模型的形状及位置与FLUENT 中固体模型部分相吻合,以便边界的节点能得到好的插值结果,为了能够跟CFD 模型对应,ANSYS 中也采用分段划分网格的方法离散模型。
从ANSYS换热器模型中输出相应各段边界节点文件,用这些节点文件进行温度插值。
从CFD软件输出固体温度时会得到一个cdb文件。
可以根据需要对这个文件进行修改,之后读进温度文件在ANSYS 中生成表面效应单元,并求解。
在后处理器中执行BFINT命令。
对输出的节点进行插值,会得到一个包含节点温度插值结果的bfin文件,直接将bfin 文件读到ANSYS 有限元固体模型中。
这样,CFD模拟的温度场结果就通过节点插值直接加到ANSYS的有限元模型上了,也就得到了后续热分析以及结构分析所需的边界条件。
2.2 ANSYS 热分析本文利用ANSYS 对换热器进行热—结构耦合分析时,采用间接耦合方法分析温差热应力,即首先通过上述插值的方法得到有限元模型所需要的温度边界条件,读入bfin 文件到ANSYS 有限元固体模型中,把CFD 模拟的温度场结果通过节点插值直接加到ANSYS的有限元模型上。
然后就可以对已经施加边界节点温度的换热器模型进行热分析,结果得到换热器模型温度场分布,如图6-9。
通过比较图2-5与图6-9的结果可以看出,CFD温度场结果与ANSYS 热分析的温度场分布差别甚微,说明节点的插值过程误差很小。
这就从换热器流体力学及传热的角度得到了有限元结构分析所需要的准确的温度分布。
为利用Fluent的计算结果在ANSYS中进一步研究换热器的温差应力提供了保证。
由图6-9 可见,换热器管板沿轴向的温度梯度变化剧烈;而在管板径向的温度分布规律为自中心往外逐渐减小。
管板和壳体连接处的温度梯度较大,在换热管和管板连接区域温度变化很明显;壳体整体上温度变化较平缓。
管子外壁面温度沿流体流动方向逐渐升高,变化缓慢。
其中图6,图7 显示了入口段壳体和管束的壁温变化,由于壳体与主要与冷流体接触,整体温度较低,变化也较缓和,而在壳体与管板连接区域,管板高温侧和管子内壁的温度较高,壳程流体温度较低,出现由管程到壳程的急剧温度变化。
壳体温度沿着周向的分布比较均匀,接近轴对称温度分布模式。
由于入口段冷热流体温差较大,流体从入口接管流经导流结构,管板壳程侧,然后沿着管束的方向流动,流体多次改变流向和分布情况,因此入口段管子壁温变化较急剧,局部温差变化较大,在热端温度较高且相对均匀。
入口段管板壳程侧的温度变化较大,分布不均匀。
图6 入口段ANSYS温度场分布图7 入口段管子及管板温度分布图9 给出了典型的折流栅段的管束壁温分布,从中可见沿着管子轴线方向和圆周方向,局部温度分布明显不同,尤其是在有折流杆的部位,温度分布出现明显的变化,这说明,常规换热器设计计算中,采用面积平均温度的缓慢变化曲线来说明沿着流道均匀缓慢的温度变化是近似的和经验的,由于通过入口段后的流体得到充分发展,流道形状变化不大,流体分布的变化较小,因此管束在这些充分发展的流道内,由面积平均得到的温度变化均匀而缓慢。
但是实际上由于存在内件,局部温度变化是十分明显的。
图8 折流栅段(四)ANSYS温度场分布图9 折流栅段(四)管子ANSYS温度场分布图10 给出了换热器外壳的温度场,可见在两接管之间的壳程区域,沿着壳程流体从进口到出口的流动方向,外壳的壁面温度是连续缓慢升高的,两端的管箱具有较高的温度。
总体上看,壳程沿着轴线方向的温度分布近似满足轴对称条件。
图10 换热器壳体温度分布2.3 ANSYS 热应力分析热分析从整体上分析管壳式换热器工作状态下温度场,从输出的结果可见,换热器的管板、管束和壳体三大约束构件之间由于存在装配与工作条件之间的温差,以及管程和壳程之间流体温差,均会导致热应力。
图11 给出了管束、壳体与管板连接区高温端的热应力分布,从图中可见,管板的两个侧面附近具有较大的应力,而管板中心部位的应力较小,这提示管板承受了典型的弯曲应力,而由于中心部位温度高,管子热膨胀较大,从而受到管板的约束较大,因此,所产生的热应力也较大,其次,在管板与壳体连接的区域,也存在较大的热应力,从变形特征看,管箱侧应存在较大的压缩应力,这些结果与常规固定管板换热器的应力分析结果是一致的。
图11 管束、壳体与管板的应力分布图12 给出了壳体轴向热应力的变化情况,图中可见,除了在与管板连接区域存在较大的热应力外,壳程的其余部分的温差热应力并不是很大。
图12 壳体轴向(Z)应力分布图13 和图14 给出了热端管板在管程侧和壳程侧的热应力分布,可见,管板的热应力呈现中心高,布管区边缘低,而与壳体连接区热应力高的特点。
结合变形的性质,可知对于管箱一侧的管板,中心部位呈现最大拉伸应力,而与壳体连接区域出现压缩最大应力,布管区与不布管区域的结合处应力出现转折即由拉伸转化为压缩,这与一般理论分析得到的结果大致吻合。
图13 管板应力分布(管程侧)图14 管板应力分布(壳程侧)图15 给出了管子和管板的轴向应力分布情况,图中可见,轴向应力的最大值发生在管子与管板以及管板与壳体连接的区域,由于本文管板不兼法兰,管板与壳体连接的整体性较高,因此,最大的拉脱力将出现在管子与管板连接部位,尤其是管板的中心部位。
此外,沿着管束,轴向应力变化缓慢。
图15 管子和管板轴向应力分布(壳程侧)总结上述分析,可以得知,管板承受较大的近似对称弯曲热应力,同时管板与壳体以及管板与管子连接处具有较大的热应力,管板中心具有最大的拉伸应力以及管板与壳体连接区域具有最大的压缩应力。