滚齿机加工原理及误差分析
滚齿机加工原理【解析】
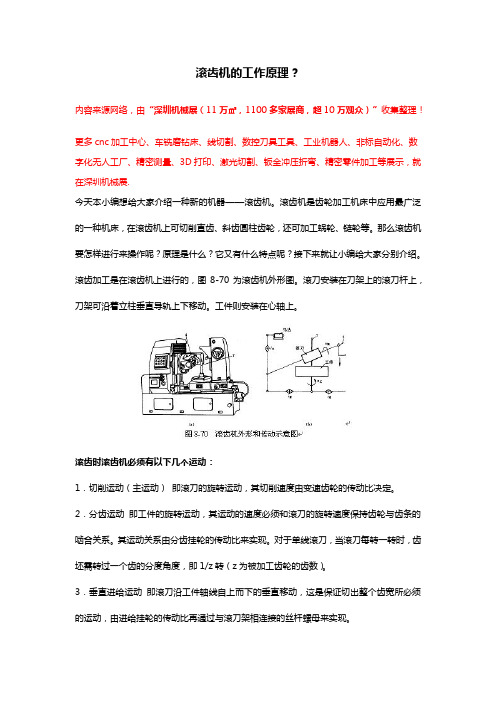
滚齿机的工作原理?内容来源网络,由“深圳机械展(11万㎡,1100多家展商,超10万观众)”收集整理!更多cnc加工中心、车铣磨钻床、线切割、数控刀具工具、工业机器人、非标自动化、数字化无人工厂、精密测量、3D打印、激光切割、钣金冲压折弯、精密零件加工等展示,就在深圳机械展.今天本小编想给大家介绍一种新的机器——滚齿机。
滚齿机是齿轮加工机床中应用最广泛的一种机床,在滚齿机上可切削直齿、斜齿圆柱齿轮,还可加工蜗轮、链轮等。
那么滚齿机要怎样进行来操作呢?原理是什么?它又有什么特点呢?接下来就让小编给大家分别介绍。
滚齿加工是在滚齿机上进行的,图8-70为滚齿机外形图。
滚刀安装在刀架上的滚刀杆上,刀架可沿着立柱垂直导轨上下移动。
工件则安装在心轴上。
滚齿时滚齿机必须有以下几个运动:1.切削运动(主运动)即滚刀的旋转运动,其切削速度由变速齿轮的传动比决定。
2.分齿运动即工件的旋转运动,其运动的速度必须和滚刀的旋转速度保持齿轮与齿条的啮合关系。
其运动关系由分齿挂轮的传动比来实现。
对于单线滚刀,当滚刀每转一转时,齿坯需转过一个齿的分度角度,即1/z转(z为被加工齿轮的齿数)。
3.垂直进给运动即滚刀沿工件轴线自上而下的垂直移动,这是保证切出整个齿宽所必须的运动,由进给挂轮的传动比再通过与滚刀架相连接的丝杆螺母来实现。
在滚齿时,必须保持滚刀刀齿的运动方向与被切齿轮的齿向一致,然而由于滚刀刀齿排列在一条螺旋线上,刀齿的方向与滚刀轴线并不垂直。
所以,必须把刀架扳转一个角度使之与齿轮的齿向协调。
滚切直齿轮时,扳转的角度就是滚刀的螺旋升角。
滚切斜齿轮时,还要根据斜齿轮的螺旋方向,以及螺旋角的大小来决定扳转角度的大小及扳转方向。
齿轮滚刀是一种专用刀具,每把滚刀可以加工模数相同而齿数不等的各种大小不同的直齿或斜齿渐开线外圆柱齿轮。
在滚齿机上除加工直齿、斜齿外圆柱齿轮外,也可以加工蜗轮、链轮。
但不能加工内齿轮。
对于加工双联齿轮和三联齿轮它也受到许多限制。
滚齿加工方法和加工方案
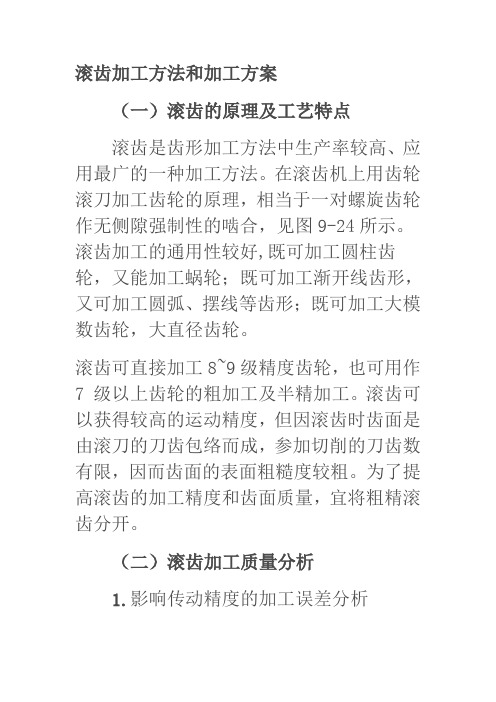
滚齿加工方法和加工方案(一)滚齿的原理及工艺特点滚齿是齿形加工方法中生产率较高、应用最广的一种加工方法。
在滚齿机上用齿轮滚刀加工齿轮的原理,相当于一对螺旋齿轮作无侧隙强制性的啮合,见图9-24所示。
滚齿加工的通用性较好,既可加工圆柱齿轮,又能加工蜗轮;既可加工渐开线齿形,又可加工圆弧、摆线等齿形;既可加工大模数齿轮,大直径齿轮。
滚齿可直接加工8~9级精度齿轮,也可用作7 级以上齿轮的粗加工及半精加工。
滚齿可以获得较高的运动精度,但因滚齿时齿面是由滚刀的刀齿包络而成,参加切削的刀齿数有限,因而齿面的表面粗糙度较粗。
为了提高滚齿的加工精度和齿面质量,宜将粗精滚齿分开。
(二)滚齿加工质量分析1.影响传动精度的加工误差分析影响齿轮传动精度的主要原因是在加工中滚刀和被切齿轮的相对位置和相对运动发生了变化。
相对位置的变化(几何偏心)产生齿轮的径向误差;相对运动的变化(运动偏心)产生齿轮的切向误差。
(1)齿轮的径向误差齿轮径向误差是指滚齿时,由于齿坯的实际回转中心与其基准孔中心不重合,使所切齿轮的轮齿发生径向位移而引起的周节累积公差,如图9—4所示。
齿轮的径向误差一般可通过测量齿圈径向跳动△Fr反映出来。
切齿时产生齿轮径向误差的主要原因如下:①调整夹具时,心轴和机床工作台回转中心不重合。
②齿坯基准孔与心轴间有间隙,装夹时偏向一边。
③基准端面定位不好,夹紧后内孔相对工作台回转中心产生偏心。
(2)齿轮的切向误差齿轮的切向误差是指滚齿时,实际齿廓相对理论位置沿圆周方向(切向)发生位移,如图9-5所示。
当齿轮出现切向位移时,可通过测量公法线长度变动公差△Fw来反映。
切齿时产生齿轮切向误差的主要原因是传动链的传动误差造成的。
在分齿传动链的各传动元件中,对传动误差影响最大的是工作台下的分度蜗轮。
分度蜗轮在制造和安装中与工作台回转中心不重合(运动偏心),使工作台回转中发生转角误差,并复映给齿轮。
其次,影响传动误差的另一重要因素是分齿挂轮的制造和安装误差,这些误差也以较大的比例传递到工作台上。
滚齿机加工原理【详解】

滚齿机加工原理内容来源网络,由“深圳机械展(11万㎡,1100多家展商,超10万观众)”收集整理!更多cnc加工中心、车铣磨钻床、线切割、数控刀具工具、工业机器人、非标自动化、数字化无人工厂、精密测量、3D打印、激光切割、钣金冲压折弯、精密零件加工等展示,就在深圳机械展.一.滚齿机介绍滚齿机是齿轮加工机床中应用最广泛的一种机床,在滚齿机上可切削直齿、斜齿圆柱齿轮,还可加工蜗轮、链轮等,这种机床使用特制的滚刀时也能加工花键和链轮等各种特殊齿形的工件。
广泛应用汽车、拖拉机、机床、工程机械、矿山机械、冶金机械、石油、仪表、飞机航天器等各种机械制造业。
齿轮加工机床品种规格繁多,有加工几毫米直径齿轮小型机床,加工十几米直径齿轮大型机床,还有大量生产用高效机床加工精密齿轮高精度机床。
二.滚齿加工的工艺特点(1)加工精度高属于展成法的滚齿加工,不存在成形法铣齿的那种齿形曲线理论误差,所以分齿精度高,一般可加工8~7级精度的齿轮。
(2)生产率高滚齿加工属于连续切削,无辅助时间损失,生产率一般比铣齿、插齿高。
(3)一把滚刀可加工模数和压力角与滚刀相同而齿数不同的圆柱齿轮在齿轮齿形加工中,滚齿应用最广泛,它除可加工直齿、斜齿圆柱齿轮外,还可以加工蜗轮、花键轴等。
但一般不能加工内齿轮、扇形齿轮和相距很近的双联齿轮。
滚齿适用于单件小批量生产和大批大量生产。
三.滚齿加工原理根据齿轮的成形原理,综合考虑滚切中对机械进给系统跟随性、快速性的要求及改造成本等因素,在保留原普通滚齿机分齿传动链的基础上,按照数控理论中两坐标圆弧插补原理,对机床的刀架垂直进给运动和水平径向进给进行数控化控制改造,实现齿轮加工。
滚齿加工是按照展成法的原理来加工齿轮的。
用滚刀来加工齿轮相当于一对交错轴的螺旋齿轮啮合。
在这对啮合的齿轮副中,一个齿数很少、只有一个或几个,螺旋角很大,就演变成了一个蜗杆状齿轮,为了形成切削刃,在该齿轮垂直于螺旋线的方向上开出容屑槽,磨前、后刀面,形成切削刃和前、后角,于是就变成了滚刀。
滚齿机的工作原理介绍
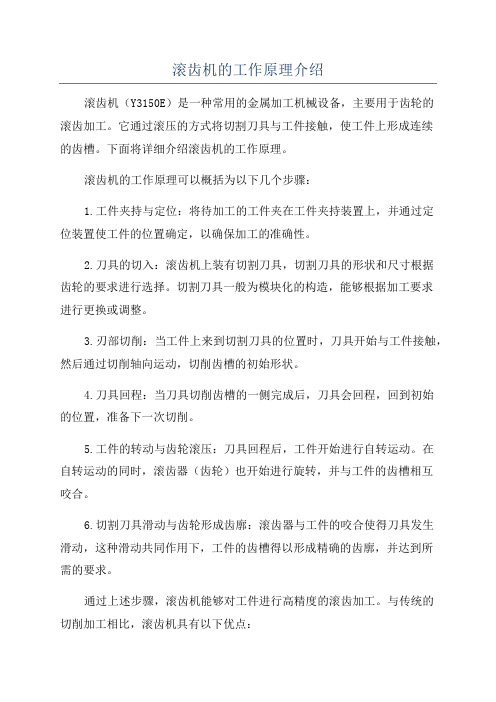
滚齿机的工作原理介绍滚齿机(Y3150E)是一种常用的金属加工机械设备,主要用于齿轮的滚齿加工。
它通过滚压的方式将切割刀具与工件接触,使工件上形成连续的齿槽。
下面将详细介绍滚齿机的工作原理。
滚齿机的工作原理可以概括为以下几个步骤:1.工件夹持与定位:将待加工的工件夹在工件夹持装置上,并通过定位装置使工件的位置确定,以确保加工的准确性。
2.刀具的切入:滚齿机上装有切割刀具,切割刀具的形状和尺寸根据齿轮的要求进行选择。
切割刀具一般为模块化的构造,能够根据加工要求进行更换或调整。
3.刃部切削:当工件上来到切割刀具的位置时,刀具开始与工件接触,然后通过切削轴向运动,切削齿槽的初始形状。
4.刀具回程:当刀具切削齿槽的一侧完成后,刀具会回程,回到初始的位置,准备下一次切削。
5.工件的转动与齿轮滚压:刀具回程后,工件开始进行自转运动。
在自转运动的同时,滚齿器(齿轮)也开始进行旋转,并与工件的齿槽相互咬合。
6.切割刀具滑动与齿轮形成齿廓:滚齿器与工件的咬合使得刀具发生滑动,这种滑动共同作用下,工件的齿槽得以形成精确的齿廓,并达到所需的要求。
通过上述步骤,滚齿机能够对工件进行高精度的滚齿加工。
与传统的切削加工相比,滚齿机具有以下优点:1.加工效率高:滚齿技术能够在一次循环中完成整个齿轮的加工,大大提高了加工效率。
2.加工质量好:滚齿加工能够保证工件的尺寸精度和齿廓质量,降低了工件的噪声和振动,提高了齿轮的使用寿命。
3.适用范围广:滚齿机适用于多种类型的齿轮加工,包括直齿轮、斜齿轮、锥齿轮等。
4.操作简单:滚齿机的操作相对简单,只需要进行合适的夹持与定位,然后调整切割刀具和滚齿器的位置即可。
总之,滚齿机(Y3150E)是一种非常重要的金属加工设备,通过滚压的方式对工件进行齿轮加工。
它的工作原理可以通过夹持与定位、切割刀具的切入与回程、工件与滚齿器的滚压等步骤来概括。
滚齿机具有高效、高质量、适用范围广和操作简单等优点,被广泛应用于齿轮加工领域。
插齿滚齿剃齿的误差分析

★★★★★插齿★★★★★插齿误差产生原因及消除方法见表01
表01 插齿时产生误差的原因与消除方法
(续表01)
★★★★★滚齿★★★★★滚齿误差产生原因及消除方法见表02
表02 滚齿误差产生原因及消除方法
(续表02)
★★★★★剃齿★★★★★剃齿轮齿接触的偏差及其修正方法见表03
表03 轮齿接触的偏差及其修正方法
剃齿误差产生原因及其消除方法见表04
表04 剃齿误差产生原因及其消除方法
(续表04)
磨齿
典型磨齿机的磨齿误差和纠正方法如下:
1) 蜗杆砂轮磨齿机(YE7272—AZA):齿形误差(见表30)和齿向误差(表31)。
表30 齿形误差
表31 齿向误差
2)锥面砂轮磨齿机(Y7163、ZSTZ630C2)见表32
表32 锥面砂轮磨齿机的缺陷项目、原因及纠正措施
3)大平面砂轮磨齿机见表33
表33 大平面砂轮磨齿机的缺陷项目
4)蝶形砂轮磨齿机(Y7032A、SD32X、HSS30BC) 表34
表34 蝶形砂轮磨齿机的缺陷项目
锥齿轮加工误差分析
表35 误差原因及消除。
简述滚齿机工作原理
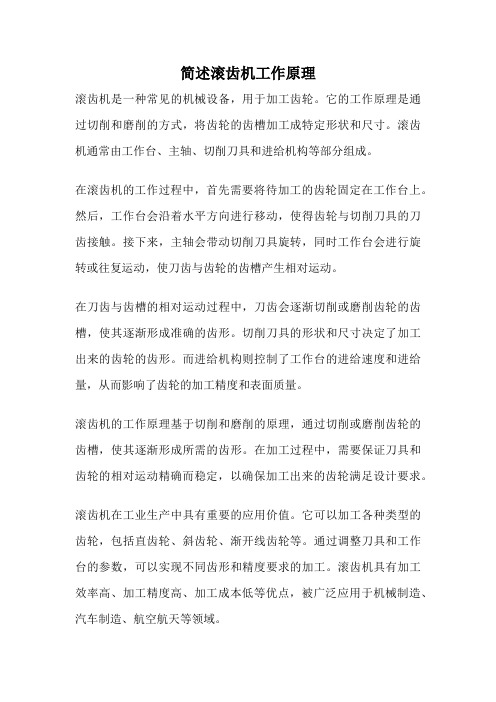
简述滚齿机工作原理滚齿机是一种常见的机械设备,用于加工齿轮。
它的工作原理是通过切削和磨削的方式,将齿轮的齿槽加工成特定形状和尺寸。
滚齿机通常由工作台、主轴、切削刀具和进给机构等部分组成。
在滚齿机的工作过程中,首先需要将待加工的齿轮固定在工作台上。
然后,工作台会沿着水平方向进行移动,使得齿轮与切削刀具的刀齿接触。
接下来,主轴会带动切削刀具旋转,同时工作台会进行旋转或往复运动,使刀齿与齿轮的齿槽产生相对运动。
在刀齿与齿槽的相对运动过程中,刀齿会逐渐切削或磨削齿轮的齿槽,使其逐渐形成准确的齿形。
切削刀具的形状和尺寸决定了加工出来的齿轮的齿形。
而进给机构则控制了工作台的进给速度和进给量,从而影响了齿轮的加工精度和表面质量。
滚齿机的工作原理基于切削和磨削的原理,通过切削或磨削齿轮的齿槽,使其逐渐形成所需的齿形。
在加工过程中,需要保证刀具和齿轮的相对运动精确而稳定,以确保加工出来的齿轮满足设计要求。
滚齿机在工业生产中具有重要的应用价值。
它可以加工各种类型的齿轮,包括直齿轮、斜齿轮、渐开线齿轮等。
通过调整刀具和工作台的参数,可以实现不同齿形和精度要求的加工。
滚齿机具有加工效率高、加工精度高、加工成本低等优点,被广泛应用于机械制造、汽车制造、航空航天等领域。
总结起来,滚齿机是一种通过切削和磨削的方式加工齿轮的机械设备。
它的工作原理是利用切削刀具和齿轮的相对运动,将齿轮的齿槽加工成特定形状和尺寸。
滚齿机具有加工效率高、加工精度高、加工成本低等优点,被广泛应用于工业生产中。
通过合理调整工艺参数,可以实现不同齿形和精度要求的齿轮加工。
滚齿机的发展和应用为机械制造行业带来了巨大的便利和发展机遇。
齿轮加工误差分析及提高加工质量方法
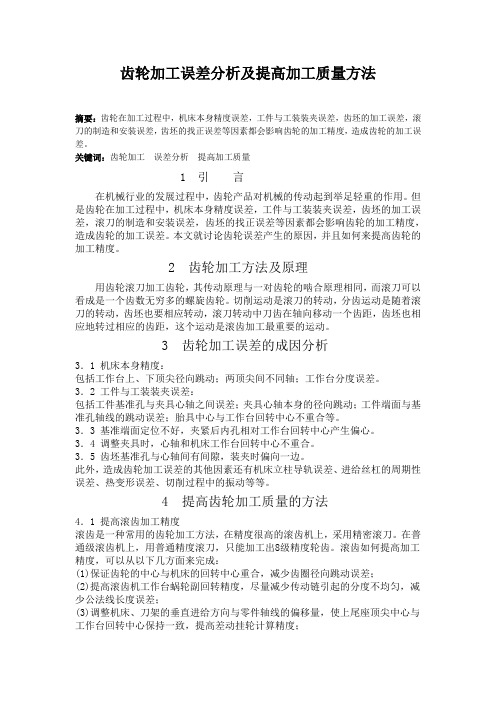
齿轮加工误差分析及提高加工质量方法摘要:齿轮在加工过程中,机床本身精度误差,工件与工装装夹误差,齿坯的加工误差,滚刀的制造和安装误差,齿坯的找正误差等因素都会影响齿轮的加工精度,造成齿轮的加工误差。
关键词:齿轮加工误差分析提高加工质量1 引言在机械行业的发展过程中,齿轮产品对机械的传动起到举足轻重的作用。
但是齿轮在加工过程中,机床本身精度误差,工件与工装装夹误差,齿坯的加工误差,滚刀的制造和安装误差,齿坯的找正误差等因素都会影响齿轮的加工精度,造成齿轮的加工误差。
本文就讨论齿轮误差产生的原因,并且如何来提高齿轮的加工精度。
2 齿轮加工方法及原理用齿轮滚刀加工齿轮,其传动原理与一对齿轮的啮合原理相同,而滚刀可以看成是一个齿数无穷多的螺旋齿轮。
切削运动是滚刀的转动,分齿运动是随着滚刀的转动,齿坯也要相应转动,滚刀转动中刀齿在轴向移动一个齿距,齿坯也相应地转过相应的齿距,这个运动是滚齿加工最重要的运动。
3 齿轮加工误差的成因分析3.1 机床本身精度:包括工作台上、下顶尖径向跳动;两顶尖间不同轴;工作台分度误差。
3.2 工件与工装装夹误差:包括工件基准孔与夹具心轴之间误差;夹具心轴本身的径向跳动;工件端面与基准孔轴线的跳动误差;胎具中心与工作台回转中心不重合等。
3.3 基准端面定位不好,夹紧后内孔相对工作台回转中心产生偏心。
3.4 调整夹具时,心轴和机床工作台回转中心不重合。
3.5 齿坯基准孔与心轴间有间隙,装夹时偏向一边。
此外,造成齿轮加工误差的其他因素还有机床立柱导轨误差、进给丝杠的周期性误差、热变形误差、切削过程中的振动等等。
4 提高齿轮加工质量的方法4.1 提高滚齿加工精度滚齿是一种常用的齿轮加工方法,在精度很高的滚齿机上,采用精密滚刀。
在普通级滚齿机上,用普通精度滚刀,只能加工出8级精度轮齿。
滚齿如何提高加工精度,可以从以下几方面来完成:(1)保证齿轮的中心与机床的回转中心重合,减少齿圈径向跳动误差;(2)提高滚齿机工作台蜗轮副回转精度,尽量减少传动链引起的分度不均匀,减少公法线长度误差;(3)调整机床、刀架的垂直进给方向与零件轴线的偏移量,使上尾座顶尖中心与工作台回转中心保持一致,提高差动挂轮计算精度;(4)滚齿时要控制留磨量,余量不能过大,否则磨齿后齿轮的表面渗碳硬度层会被磨掉,造成硬度下降,降低齿轮的接触疲劳强度。
滚齿时产生缺陷的原因与消除方法

4、对鱼鳞:采用适当的预先热处理方法,若对齿面为最终加工时,必须避免;若后面还有剃磨等工艺时,可以不避免
控制工件两端面的平行度或安装时的径向跳动量齿圈跳动超差主要是在安装工件时它的内孔中心对于轴齿轮就是轴颈中心与工作台的回转中心不重合或偏心太大
滚齿时产生缺陷的原因与消除方法
缺陷名称
产生原因
消除办法
齿数不正确
1、机床:分齿挂轮调整的不正确;滚刀与工件的转向不配合。
2、刀具:滚刀的模数、头数、螺旋线方向等选择不当;
3、工件:齿轮毛坯尺寸不对
1、重新调整分齿挂轮与介轮;
2、选择合适的滚刀;
3、更换齿轮毛坯
齿向误差超差
主要是滚齿机刀架的垂直走刀方向与齿坯内孔中心线方向偏离,对于斜齿轮还要加上附加转动不正确的原因。归纳为:
1、机床:垂直走刀导轨与工作台的轴心线不平行;上下顶尖不同心;工作台有轴向窜动或径向跳动;分齿蜗杆、蜗轮有间隙或蜗轮副传动有周期性误差;走刀传动丝杆螺距有误差;分齿挂轮调整误差太大;差动挂轮不对,计算误差太大或刀架转动不对(加工斜齿轮时);
1、机床:工作台径向跳动;心轴对工作台回转中心不重合或长期使用磨损;心轴本身摆差太大;使用顶针加工时,上下顶针有偏摆或松动;夹具定位端面与工作台回转中心不垂直;垫圈两平面不平行或夹紧螺母端面对螺纹中心不垂直;
2、工件:内孔定心时,由于内孔与心轴配合间隙过大,引起安装偏心;外径定心时,由于外圆本身的径向跳动或椭圆度较大;工件夹紧刚性差
3、振纹:机床刀具、工件系统的好坏直接影响着振动发生的强弱(如滚刀安装不好,刃磨质量不好,刀轴尾支承间隙过大,齿坯的装夹等);
- 1、下载文档前请自行甄别文档内容的完整性,平台不提供额外的编辑、内容补充、找答案等附加服务。
- 2、"仅部分预览"的文档,不可在线预览部分如存在完整性等问题,可反馈申请退款(可完整预览的文档不适用该条件!)。
- 3、如文档侵犯您的权益,请联系客服反馈,我们会尽快为您处理(人工客服工作时间:9:00-18:30)。
滚齿机:主要用滚刀按展成法加工圆柱齿轮,蜗轮,链轮等齿面的齿轮加工机床。
滚齿机校正机构常见种类:行星式,复式偏心式,凸轮摆杆式,附加回转工作台式等。
决于齿轮机床的精度、刚度、刀具和齿轮毛坯的质量及其安装精度。
所以针对滚齿机工作台误差的滚齿机主要用滚刀按展成法加工圆柱齿轮、蜗轮、链轮等齿面的齿轮加工技术,在机械加工中占有重要地位。
因为在齿轮加工中出现了分度蜗轮的周节累计误差和周期误差,而齿轮加工精度取来源这一问题,本文使用滚齿机行星摆杆机构对其进行校正,用以减少分度蜗轮的周节累计误差和周期误差,使加工出来的齿轮达到满足加工精度的要求。
国内采用的滚齿机校正构,在机床制造行业中, 一开始制造精密机床, 由于各厂的设备条件差, 在滚齿机上不能加工精度较高的蜗轮, 分度精度满足不了产品的要求。
因而, 各厂先后在各型滚齿机上采用了各种类型的校正机构, 大都取得了不同程度的效果, 制出了精密分度蜗轮。
当时, 着重引进国外现成为结构, 近几年来, 无论在结构型式上, 或在简化结构, 或校正效果等方面均有较快的发展。
我国共采用了行星式、复式偏心式、凸轮摆杆式、和附加回转工作台式等多种类型的校正机构。
RS2 型滚齿机校正机构,只能能校正分度蜗轮副的周期误差。
但结构不够紧凑,校正机构在机床的外边,需要另置地基,并将机床的罩壳也换掉。
5355M型滚齿机校正机构也属于行星式,但没有周期误差校正凸轮, 机构是封闭的。
其结构复杂, 构件将近85 种, 使用不方便, 需将机床的双蜗杆传动改成单蜗杆传动, 此时, 必需拆除一根蜗杆。
由于校正机构安装位置不够妥当,使得一部分齿轮外露。
这种结构不太适用于大型滚齿机。
FO-10滚齿机行星式校正机构,该机构有一定的简化, 它省去了四根摆杆和一根长套筒, 结构就比较紧凑一些。
它装在机床分度挂轮箱处, 不需另置地基, 但其构件的种数仍然较多, 达45种, 放大比为0.182毫米每秒。
这种机构的轮廓尺寸较大。
为了适应机床的结构特点, 5327 型滚齿机校正机构采取了另一种形式,这种机构的最大特点是, 分度挂轮可以方便地更换, 使用起来很方便。
可以加工圆柱齿轮、斜齿轮、蜗轮等, 被加工齿数不受限制。
其机构原理仍是行星式的, 因而放大系数仍比较小,0.186 毫米每秒。
除了减少了4件齿轮之外, 其他的结构并未简化, 为了安装方便, 将分度蜗杆传动改制成两段, 不仅增加了两根长轴, 而且使校正周期误差麻烦了, 安装校正机构时, 必须使轴和轴的旋转轴心被同心, 否则会有增大机床周期误差的可能。
FO-6滚齿机校正机构, 它直接装置在蜗杆的尾端, 省去了一个较大的零件, 不占用分度挂轮箱的过大空间, 也不需要另置地基, 更换机床外罩等。
其布局特点是在空间有限的情况下, 将分度挂轮作成凹形, 在凹穴的空间布置机构的其他零件。
此机构可以校正滚齿机分度蜗轮的两齿面的周节累积误差和单面的周期误差。
被加工齿数受到一定的限制。
它也属于行星式。
可以看出, 我国所采用的滚齿机校正机构, 以行星式为最普通, 在结构原理上也基本上相同, 但也是在逐步发展的, 在使用行星式校正机构的同时, 我国并设计和制造了复式偏心式校正机构,在齿轮尺寸相同的情况下, 这种机构的放大比, 要比行星式的大得多, 由于放大系数大, 在校正原始精度比较高的滚齿机时, 可以取得较好的效果, 因为此时校正凸轮的升程还是比较大的, 摆杆的校正动作也比较大。
这种形式的校正机构, 还在不断改进, 结构就简化了, 轮廓尺寸也大大地减小。
其缺点是制造工艺要求较高, 机构要求灵活, 不然会影响校正效果。
在设计时要注意不能使机构自锁。
凸轮摆杆式校正机构是我国应用得较迟的, 但结构是最简单的一种, 很实用, 校正效果比校好。
但是, 只能校正分度蜗轮的周节累积误差。
滚齿机采用摆杆式校正机构获得的校正效果好于附加回转工作台式的校正机构, 在国内应用不广, 这种校正机构适用于小型滚齿机。
工件的齿数可以不受限制。
但机构本身结构比较复杂, 安装不方便, 不宜用于中、大型滚齿机。
国内滚齿机的运动精度校正目前尚限于一米以下的中型机床, 大型滚齿机的校正很少, 而校正效果也不很理想, 大型滚齿机的校正具有极为重要的意义。
主要的几种国外滚齿机校正的水平,可使滚齿机加工精度提高, 如果毛坯、刀具本身的制造和安装精度在规定范围内, 校正后的滚齿机可以加工出精密蜗轮。
这说明机械式校正有广的前途, 它具有成本低, 使用方便, 效果显著等特点。
据了解上述使用效果较好的校正机构的校正凸轮, 由于生产任务紧等原因, 没有进行反复修正, 所取得的结果并不是校正的最佳效果,国外(英国和德国) 也先后采用了滚齿机自动校正措施, 其效果并不比机械式校正机构高很多, 而成本却很高, 当然也有它的优点, 从结构的复杂程度来分析, 我国近年来在结构方面有了一些发展, 较以前简化了, 构件的种数也大大减少。
同时也可看出凸轮摆杆式校正机构在桔构上的优点。
据德阿享工业大学R o lf P ie ke n b rin k 介绍在分度蜗轮为 4 米的大型滚齿机上, 采用偏心齿轮将蜗杆所引起的周期误差消除了, 而剩下的是由其他传动元件所引起的周期误差, 比较起来, 我国校正水平较之世界水平还差有一定的距离需要反复研究和修正凸轮, 不断改善校正机构的结构, 将滚齿机传动精度仪直接用于生产, 与校正机构的研究配合起来, 各国所采用的结构除了大凸轮式校正机构等以蜗杆移动作为补偿运动形式的少数几种我国未采用外, 其他也大都采用过, 尤以行星式采用最广泛。
对于一米以上的大型滚齿机的校正我们还很缺乏研究和使用, 这是我们与国外的最大差别。
国内所采用的各种校正机构, 均获得一定的效果, 行星式的桔构比较复杂, 校正机构的放大系数以复式偏心式为最大, 摆杆式使用方便结构筒单, 凸轮修正方便, 易于推广。
结构的布局以装在分度蜗杆传动轴尾端为最好。
国内校正机构的效果接近国外先进水平, 但在周期误差校正方面还有差距,对于大型滚齿机的校正机构, 国内还缺乏进一步的研究。
滚齿误差产生原因及消除方法滚齿误差产生原因消除方法一,齿圈径向圆跳动超差 1)齿坯几何偏心和安装偏心2)用顶尖装夹定位时,顶尖与机床中心偏心消除方法 1)提高齿坯基准面精度;提高夹具定位面精度;提高调整水平2)更换或重新装调顶尖二,公法线长度变动超差 1)机床分度蜗杆副制造及安装误差造成运功偏心2)机床工作台定心锥形导轨副间隙过大造成工作台运动中心线不稳定3)滚刀主轴系统轴向圆跳动过大或平面轴承咬坏消除方法 1)提高分度蜗杆副的制造精度和安装精度 2)提高工作台锥形导轨副的配合精度 3)提高滚刀主轴系统轴向精度,更换咬坏的平面轴三,齿距偏差超差 1)滚刀的轴向和径向圆跳动过大2)分度蜗杆和分度蜗轮齿距误差 3)齿坯安装偏心消除方法 1)提高滚刀的安装精度 2)修复或更换分度蜗杆副 3)消除齿坯安装误差四,基节超差 1)滚刀的轴向齿距误差,齿行误差及前刃面非径向性和非轴向性误差 2)分度蜗杆副的齿距误差 3)齿坯的安装几何偏心 4)刀架回转角度不正确消除方法 1)提高滚刀铲磨精度和刃磨精度 2)修复或更换分度蜗杆副 3)消除几问偏心 4)调整角度齿顶部变肥,左右齿廓对称滚刀铲磨时齿形角度小或刃磨产生较大的正前角,使齿形角变小更换滚刀或重磨齿形角及前刃面齿顶部变瘦,左右齿廓对称滚刀铲磨时齿形角变大或刃磨时产生较大的负前角,使形角变大更换滚刀或重磨齿形角及前刀面齿形不对称滚刀安装对中不好,刀架回转角误差大,滚刀前刀面有导程误差保证滚刀安装精度,提高滚刀刃磨精度,控制前刀面导程误差,微调滚刀回转角齿面出棱滚刀制造或刃磨时容屑槽等分误差重磨滚刀达到等分要求齿性周期性误差滚刀安装后,径向或端圆跳动大,机床工作台回转不均匀,分齿交换齿轮安装偏心或齿面有磕碰,刀架滑板松动,齿坯装夹不合理,产生振动控制滚刀的安装精度,检查,调整分度蜗杆副传动精度,重新调整分齿交换齿轮、滑板和齿坯五,齿向误差超差 1)垂直进给导轨与工作台轴线平行度误差或歪斜上、下顶针不同轴,卜下顶针轴线与工作台回转轴线同轴度差 2)夹具和齿坯的制造、安装、调整精度低 3)分齿、差动交换齿轮误差大 4)齿坯或夹具刚性差,夹紧后变形消除方法 1)根据误差原因,加以消除 2)提高夹具、齿坯的制造和调整精度 3)重新计算分齿及差动交换齿轮,修正误差 4)改进齿还或夹具设计,正确夹紧六,撕裂 1)齿坯材质不均匀 2)齿坯热处理方法不当3)滚刀用钝,不锋利 4)切削用量选择不当,冷却不良消除方法 1)控制齿坯材料质量 2)建议采用正火处理:45钢、40cr钢、18CrMnTi 3)滚刀移位或更换新刀 4)正确选用切削用量,选用润滑性能良好的切削液,充分冷却七,啃齿 1)刀架立柱导轨太松或太紧 2)油压不稳定3)刀架斜齿轮啮合间隙大消除方法 1)调整立柱导轨塞铁松紧 2)保持油路畅通,油压稳定 3)刀架斜齿轮若磨损,应更换之八,振纹 1)机床内部某传动环节的间隙过大 2)工件与刀具的装夹刚性不够 3)切削用量选用过大 4)后托架安装后,间隙大消除方法 1)修理或调整机床 2)提高波刀装夹刚性,缩小支承间距离,加大轴径;提高工件刚性,尽量加大支承面 3)正确选用切削用量 4)正确安装后托架九,鱼鳞1)工件材料硬度过高 2)滚刀磨钝 3)冷却润滑不良齿轮加工精度及校正的效果:齿轮的加工精度是由滚齿机的分度传动链的精度所决定的。
由于传动元件不可避免地存在制造误差和安装误差, 这些误差形成相对转角误差造成被加工齿轮的运动误差和平稳性误差。
长周期误差( 低频误差) 主要由传动链的蜗轮副产生。
因此, 在机床现有精度的条件下要提高被加工齿轮的运动精度, 就必须降低蜗轮副的累积误差, 为此在传动链中迭加上了一幅值与蜗轮副累积误差相等、相位相反的同频误差, 由叠加原理, 其对被加工齿轮的影响则被抵消了, 这可利用机床的差动机构来实现。
产生补偿误差值的凸轮装在差动挂轮主轴上, 搭配一定的走刀挂轮和差动挂轮, 使其与工作台同步。
短周期误差的降低短周期误差主要由中间齿轮、分度挂轮定、传动比齿轮、滚刀轴及蜗轮齿频等误差叠加引起, 加工齿数不同, 分度挂轮与传递运动的速比亦不同, 因此其大小随加工齿数, 各齿轮的相位而变, 影响因素极其复杂。
进行了测试, 校正后的长周期误差曲线, 即滤去了高频误差信号。
经过校正, 累积误差由原来的2 2分, 降低到9分,减少了77 . 5 % 。
校正后传动链的短周期误差值从14分 ~ 22分降低到7分 ~ 12分。
与补偿前比较, 短周期误差降低了45 .5 % 。
周节累积误差:滚齿机中分度蜗轮蜗杆、多组挂轮和多对轴承是保证滚刀和工件之间正常啮合、滚切出正常齿轮的重要零件。