镁基复合材料制备技术、性能及应用发展概况
镁基复合材料

展望
镁基复合材料拥有优异的力学性能和物理性能,已 经显示出广阔的应用前景。 制备工艺、回收技术以及材料内部结构性能的各个 领域进行更多的原理研究及应用探索。 空间应用及交通领域 人类社会的老龄化问题日益突出,发展各种超轻结 构材料对于老年人独立工作及日常生活十分必要。
参考文献
[1] 杜文博,严振杰,吴玉锋等. 镁基复合材料的制备方法与新工艺.稀有 金属材料与工程. 2009, 38(3) [2] T W 克莱因. 金属基复合材料导论 . 余永宁,房志刚译. 北京:冶金工业 出版社. 1996. [3] 董 群, 陈 礼,清赵明久等. 镁基复合材料制备技术、性能及应用发展概 况. 材料导报. 2004, 18(4) [4] 张修庆, 滕新营.镁基复合材料的制备工艺. 热加工工艺 2004, (3) [5]方信贤, 王 莹.原位合成颗粒增强镁基复合材料研究进展.南京工程学 院学报( 自然科学版). 2008, 6(2) [6 ]南宏强 ,袁 森 ,王武孝等. 颗粒增强镁基复合材料的制备工艺研究进 展. 2006, 27(4) [7] 孙志强,张 荻,丁 剑等。原位增强镁基复合材料研究进展与原位反 应体系热力学. 材料科学与工程. 2002, 20(4) [8]胡连喜,李小强.挤压变形对SiCw/ZK51A镁基复合材料组织和性能的 影响.中国有色金属学报,2000,10 (5)
应用
应用
镁基复合材料的研究及其展望
研究方向
研究中的问题
展望
研究方向
组成及界面反应
增强相选择要求与铝基复合材料大致相同,都要求物 理、化学相容性好,润湿性良好,载荷承受能力强,尽量 避免增强相与基体合金之间的界面反应等。
制备及合成工艺
反应物的选择和反应工艺的控制。
一类新型镁材料——镁基金属有机骨架材料

2018年第37卷第9期 CHEMICAL INDUSTRY AND ENGINEERING PROGRESS·3437·化 工 进展一类新型镁材料——镁基金属有机骨架材料韩森建,王海增(中国海洋大学化学化工学院,山东 青岛 266100)摘要:镁基金属有机骨架材料(Mg-MOFs )是近年来逐渐受到关注的一类新型功能材料,其种类与结构多样化,使其在很多领域中展现出了潜在的应用价值,为镁资源的开发利用开拓了一个新的领域。
本文从Mg-MOFs 的种类、特点、制备方法、应用以及稳定性5个方面展开论述。
详细阐述了Mg-MOFs 在催化、药物缓释、光学材料、气体储存、气体吸附和分离等方面的应用,着重介绍了Mg-MOFs 的储氢能力和对二氧化碳的吸附能力及对不同混合物的选择分离能力。
提出了今后Mg-MOFs 的研究重点:优化Mg-MOFs 的制备条件,降低制备难度及成本;选择新的配体源及溶剂,开发具有结构稳定、高比表面积、功能多样的Mg-MOFs ,扩大其在气体吸附与选择性分离方向的应用;将Mg-MOFs 应用于复合材料中,拓宽其应用范围。
关键词:镁基金属有机骨架材料;羧酸配体;储氢;分离中图分类号:O6-1 文献标志码:A 文章编号:1000–6613(2018)09–3437–09 DOI :10.16085/j.issn.1000-6613.2017-2174A new material of magnesium complexes——magnesium based metalorganic frameworksHAN Senjian , WANG Haizeng(College of Chemistry and Chemical Engineering, Ocean University of China, Qingdao 266100, Shandong, China)Abstract :Magnesium based metal organic frameworks (Mg-MOFs), as a new kind of functional material, have recently drawn much research attention. Due to the diversified specie and structures, Mg-MOFs have shown potential applications in many fields, which provide a new research area for the development and utilization of magnesium resources. Five aspects on Mg-MOFs are discussed in this article, including the main types, characteristics, preparation method, applications and stability. The applications of Mg-MOFs in catalysis, drug delivery, optical properties, gas storage, adsorption and separation are elaborated, and the capacities of hydrogen storage, carbon dioxide adsorption and selective uptake are presented emphatically. In addition, the prospects and challenges in the future are pointed out. For instance: optimizing the preparation conditions of Mg-MOFs to reduce the process difficulty and costs; selecting new ligands and solvent to prepare Mg-MOFs of high surface area, developing varieties of functional Mg-MOFs with structural stability to expand their applications in gas adsorption and separation, and applying Mg-MOFs to the composite materials to extend their application range.Key words: magnesium based metal organic frameworks (Mg-MOFs); ligands of carboxylic acid; storage hydrogen gas; separation我国镁资源总储量世界第一,包括固态镁资源和液态镁资源[1]。
镁及其合金材料的优化制备及应用
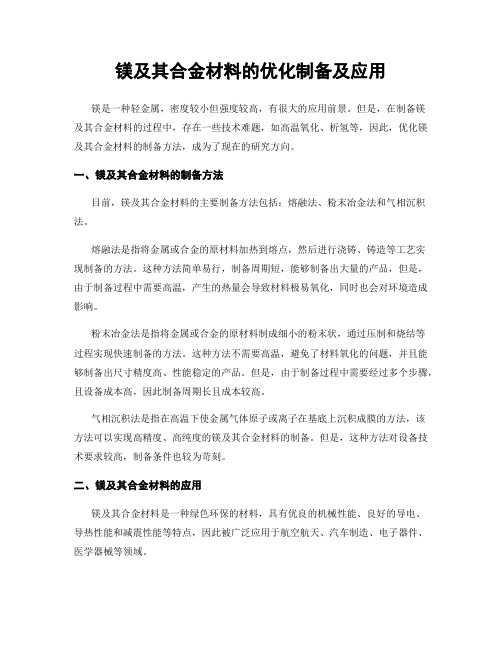
镁及其合金材料的优化制备及应用镁是一种轻金属,密度较小但强度较高,有很大的应用前景。
但是,在制备镁及其合金材料的过程中,存在一些技术难题,如高温氧化、析氢等,因此,优化镁及其合金材料的制备方法,成为了现在的研究方向。
一、镁及其合金材料的制备方法目前,镁及其合金材料的主要制备方法包括:熔融法、粉末冶金法和气相沉积法。
熔融法是指将金属或合金的原材料加热到熔点,然后进行浇铸、铸造等工艺实现制备的方法。
这种方法简单易行,制备周期短,能够制备出大量的产品,但是,由于制备过程中需要高温,产生的热量会导致材料极易氧化,同时也会对环境造成影响。
粉末冶金法是指将金属或合金的原材料制成细小的粉末状,通过压制和烧结等过程实现快速制备的方法。
这种方法不需要高温,避免了材料氧化的问题,并且能够制备出尺寸精度高、性能稳定的产品。
但是,由于制备过程中需要经过多个步骤,且设备成本高,因此制备周期长且成本较高。
气相沉积法是指在高温下使金属气体原子或离子在基底上沉积成膜的方法,该方法可以实现高精度、高纯度的镁及其合金材料的制备。
但是,这种方法对设备技术要求较高,制备条件也较为苛刻。
二、镁及其合金材料的应用镁及其合金材料是一种绿色环保的材料,具有优良的机械性能、良好的导电、导热性能和减震性能等特点,因此被广泛应用于航空航天、汽车制造、电子器件、医学器械等领域。
在航空航天领域,镁及其合金材料可以制作轻质、高强度零部件,为飞机减少重量、提高载荷能力提供了很大的空间。
同时,镁及其合金材料还可以用于制造宇航器、卫星等。
在汽车制造领域,镁及其合金材料是一种理想的轻量化材料。
与普通钢材相比,镁及其合金材料的密度小,但是强度高,可以在保证安全的前提下减少汽车的燃油消耗,降低环境污染。
在电子器件领域,镁及其合金材料因其良好的导电、导热性能而被广泛应用于电脑主板、手机等器件的散热元件制造。
在医学器械领域,镁及其合金材料因其生物相容性好、无毒害等特点而被广泛应用于人体器械的制造,如钢板、钉子、矫形器等。
镁基复合材料的制备

书山有路勤为径,学海无涯苦作舟
镁基复合材料的制备
镁及镁合金虽具有密度低、比强度大、比刚度高和抗冲击性强等诸多优点。
但是也有一些固有缺点,如硬度、刚度、耐磨性、燃点较低、不是一种良好的结构材料,使其应用受到相当大的制约。
若向镁基体中添加陶瓷颗粒或碳纤维制成复合材料,则可以在很大程度上改善镁的力学性能,提高耐热和抗蠕变性能,降低热膨胀系数等。
可作为复合材料增强相的颗粒有:氧化物、碳化物、氮化物、陶瓷、石墨和碳纤维等。
制备镁基复合材料的工艺主要是:铸造法、粉末冶金法、喷射沉积法。
铸造法
铸造法是制备镁合金复合材料的基本工艺,可分为搅拌混合法、压力浸渗法、无压浸渗法和真空渗法等。
搅拌铸造法(Stiring Casting)
此法是利用高速旋转搅拌器浆叶搅动金属熔体,使其剧烈流动,形成以搅拌旋转轴为中心的漩涡,将增强颗粒加入漩涡中,依靠漩涡负压抽吸作用使颗粒进入熔体中,经过一段时间搅拌,颗粒便均匀分布于熔体内。
此法简便,成本低,可以制备含有Sic、Al2O3、SiO2、云母或石墨等增强相的镁基复化材料。
不过也有一些难以克服的缺点:在搅拌过程中会混入气体与夹杂物,增强相会偏析与固结,组织粗大,基体与增强相之间会发生有害的界面反应,增强相体积分数也受到一定限制,产品性能低,性价比无明显优势。
用此法生产镁基复合材料时应采取严密的安全措施。
液态浸渗法(Liquid infiltration process)
用此法制备镁基复合材料时,须先将增强材料与黏接剂混合制成预制坯,用惰性气体或机械设备作用压力媒体将镁熔体压入预制件间隙中,凝固后即成为复合材料,按具体工艺不同又可分为压力浸渗法、无压、浸渗法和真空浸渗。
(完整word版)镁基复合材料制备技术、性能及应用发展概况

镁基复合材料制备技术、性能及应用发展概况摘要:镁基复合材料因其轻量化和高性能而成为当今高新技术领域中最富竞争力和最有希望采用的复合材料之一。
大致笔述了常用镁基复合材料研究概况、制备技术、性能及应用前景。
关键词:镁基复合材料制备技术性能应用Fabrication,Properties and Application of M agnesium—matrix CompositesDONG Qun CHEN Liqing ZHAO Mingjiu BI Jing(Institute of Metal Research,Chinese Academy of Sciences,Shenyang 110016,China)Abstract Magnesium—matrix composites with lightweight and high performance are becoming one of themost competitive and promising candidates in the applications of high—tech fields.An overview is made on the fabri—ating techniques,mechanical properties and applications for the typical magnesium—matrix composites,and theresearch trend is proposedKey words magnesium matrix composite,fabrication,properties,application. 0引言:镁基复合材料是继铝基复合材料之后又一具有竞争力的轻金属基复合材料【E1】,主要特点是密度低、比强度和比刚度高,同时还具有良好的耐磨性、耐高温性、耐冲击性、优良的减震性能及良好的尺寸稳定性和铸造性能等;此外,还具有电磁屏蔽和储氢特性等,是一类优秀的结构与功能材料,也是当今高新技术领域中最有希望采用的复合材料之一;在航空航天、军工产品制造、汽车以及电子封装等领域中具有巨大的应用前景。
镁基复合材料的应用及发展

镁基复合材料的应用及发展镁基复合材料是一种由镁合金基体和其他增强材料组成的复合材料。
镁合金具有低密度、高比强度和良好的机械性能等优点,但其在高温和腐蚀环境下的性能较差。
通过将其他增强材料与镁合金基体结合,可以改善镁合金的性能,并拓展其应用领域。
以下将详细介绍镁基复合材料的应用及发展。
一、航空航天领域镁基复合材料在航空航天领域有着广泛的应用。
由于镁合金具有低密度和高比强度,可以减轻飞机和航天器的重量,提高其燃油效率和载荷能力。
同时,镁基复合材料还具有良好的耐腐蚀性能,可以在恶劣的环境下使用。
目前,镁基复合材料已经成功应用于飞机结构、发动机零部件、导弹和航天器等领域。
二、汽车工业镁基复合材料在汽车工业中也有着广泛的应用前景。
由于镁合金具有低密度和良好的机械性能,可以减轻汽车的重量,提高燃油效率和行驶性能。
此外,镁基复合材料还具有良好的吸能性能,可以提高汽车的碰撞安全性。
目前,一些汽车制造商已经开始使用镁基复合材料制造车身和零部件,以实现轻量化和节能减排的目标。
三、电子领域镁基复合材料在电子领域也有着广泛的应用。
由于镁合金具有良好的导电性能和热传导性能,可以用于制造电子器件和散热器等。
此外,镁基复合材料还具有良好的抗电磁干扰性能,可以提高电子设备的稳定性和可靠性。
目前,一些电子产品中已经开始使用镁基复合材料,如手机、平板电脑和电视等。
四、医疗领域镁基复合材料在医疗领域也有着潜在的应用价值。
由于镁合金具有良好的生物相容性和生物降解性,可以用于制造骨科植入物和修复器械等。
此外,镁基复合材料还具有良好的抗菌性能,可以预防感染和促进伤口愈合。
目前,一些医疗器械制造商已经开始研发和应用镁基复合材料,以提高医疗器械的性能和安全性。
随着科学技术的不断进步,镁基复合材料的应用领域还将不断拓展。
未来,随着材料制备技术的改进和材料性能的提高,镁基复合材料有望在更多领域发挥重要作用。
同时,还需要进一步研究镁基复合材料的制备工艺、性能测试和应用评价等方面的问题,以推动其在实际应用中的发展。
《镁-铝复合板的制备及其抗冲击性能研究》

《镁-铝复合板的制备及其抗冲击性能研究》篇一镁-铝复合板的制备及其抗冲击性能研究一、引言随着现代工业的快速发展,复合材料因其独特的物理和化学性能,在航空航天、汽车制造、电子设备等领域得到了广泛应用。
镁/铝复合板作为一种新型的轻质高强材料,具有优异的力学性能和良好的抗腐蚀性,其制备工艺及性能研究成为了当前研究的热点。
本文旨在研究镁/铝复合板的制备工艺及其抗冲击性能,为该类材料的实际应用提供理论依据。
二、镁/铝复合板的制备1. 材料选择与准备制备镁/铝复合板的主要材料为镁合金和铝合金。
首先,根据所需的性能要求,选择合适的镁合金和铝合金板材。
然后,对所选材料进行表面处理,去除油污、氧化物等杂质,以保证复合板的结合强度。
2. 制备工艺镁/铝复合板的制备主要采用爆炸复合法和轧制复合法。
爆炸复合法是通过控制爆炸参数,使镁合金和铝合金在爆炸瞬间实现结合。
轧制复合法则是通过高温轧制,使两种金属板材在压力作用下实现结合。
(1)爆炸复合法:将镁合金和铝合金按照一定的叠层方式放置,通过控制炸药的种类、数量和爆炸参数,使两种金属在爆炸瞬间实现牢固结合。
(2)轧制复合法:首先,将镁合金和铝合金进行预处理,使其达到一定的温度和硬度。
然后,将两种金属板材在高温下进行轧制,通过施加一定的压力,使两种金属实现牢固结合。
三、抗冲击性能研究为了研究镁/铝复合板的抗冲击性能,我们采用了落锤冲击试验和弹道冲击试验。
通过这两种试验方法,可以模拟实际使用过程中可能遇到的冲击情况,从而评估复合板的抗冲击性能。
1. 落锤冲击试验落锤冲击试验是一种模拟重力冲击的试验方法。
在该试验中,我们将一定质量的钢质锤头固定在落锤试验机上,使其自由落下撞击镁/铝复合板。
通过观察和分析冲击后的试样形态、破坏程度以及残余能量等信息,评估复合板的抗冲击性能。
2. 弹道冲击试验弹道冲击试验是一种模拟高速弹体撞击的试验方法。
在该试验中,我们使用高速弹体(如钢珠或子弹)以一定的速度撞击镁/铝复合板。
镁基复合材料的应用

镁基复合材料的应用镁基复合材料是一种以镁合金为基体,与其他金属、陶瓷、聚合物等材料进行复合加工而成的新型材料。
它具有密度低、比强度高、耐热性好等优点,因此在航空航天、汽车、电子、医疗等领域有着广泛的应用前景。
镁基复合材料在航空航天领域的应用是其重要领域之一。
随着航空航天技术的发展和需求的提高,要求材料具有较轻的重量、良好的机械性能和热稳定性,镁基复合材料因其优异的特性而备受关注。
它可以用于制造飞机结构件、发动机零部件、燃料箱等,无形中减轻了飞机的自重,提高了航空器的使用效率,降低了燃油消耗,对于航空航天工业的可持续发展具有重要意义。
镁基复合材料在汽车领域也有着广泛的应用前景。
如今,人们对汽车的轻量化要求越来越高,以降低燃油消耗、减少污染、提升汽车性能和安全性。
而镁基复合材料因其轻质、高强度、抗腐蚀等特性,被广泛应用于汽车制造中,可以制造车身结构件、发动机零部件、悬挂系统等。
相对于传统的金属材料,镁基复合材料的使用可以使汽车减重,提高燃油经济性,降低尾气排放,同时提高汽车的安全性。
在电子领域,镁基复合材料也被广泛应用于各种电子产品的制造中。
它可以用来制造手机壳体、电脑外壳、平板电脑等产品的外壳,使得产品更轻便、耐用。
镁基复合材料还具有良好的导电性和热传导性,可以帮助电子产品散热,在保证产品性能的同时提高了产品的使用寿命。
医疗领域也是镁基复合材料广泛应用的领域之一。
由于镁合金具有生物相容性和生物降解性,因此被用于医疗器械的制造。
镁基复合材料可以用来制造骨骼植入物、手术器械等,与人体组织相容性好,不会对人体造成额外的伤害,并且可以在合适的时间内降解吸收,减少了二次手术的风险。
镁基复合材料在航空航天、汽车、电子、医疗等领域有着广泛的应用前景。
随着科技的不断发展和对材料性能要求的提高,相信镁基复合材料在未来会有更广泛更深入的应用,为各行各业带来更多的发展机遇。
- 1、下载文档前请自行甄别文档内容的完整性,平台不提供额外的编辑、内容补充、找答案等附加服务。
- 2、"仅部分预览"的文档,不可在线预览部分如存在完整性等问题,可反馈申请退款(可完整预览的文档不适用该条件!)。
- 3、如文档侵犯您的权益,请联系客服反馈,我们会尽快为您处理(人工客服工作时间:9:00-18:30)。
镁基复合材料制备技术、性能及应用发展概况摘要:镁基复合材料因其轻量化和高性能而成为当今高新技术领域中最富竞争力和最有希望采用的复合材料之一。
大致笔述了常用镁基复合材料研究概况、制备技术、性能及应用前景。
关键词:镁基复合材料制备技术性能应用Fabrication,Properties and Application of M agnesium—matrix CompositesDONG Qun CHEN Liqing ZHAO Mingjiu BI Jing(Institute of Metal Research,Chinese Academy of Sciences,Shenyang 110016,China)Abstract Magnesium—matrix composites with lightweight and high performance are becoming one of themost competitive and promising candidates in the applications of high—tech fields.An overview is made on the fabri—ating techniques,mechanical properties and applications for the typical magnesium—matrix composites,and theresearch trend is proposedKey words magnesium matrix composite,fabrication,properties,application.0引言:镁基复合材料是继铝基复合材料之后又一具有竞争力的轻金属基复合材料【E1】,主要特点是密度低、比强度和比刚度高,同时还具有良好的耐磨性、耐高温性、耐冲击性、优良的减震性能及良好的尺寸稳定性和铸造性能等;此外,还具有电磁屏蔽和储氢特性等,是一类优秀的结构与功能材料,也是当今高新技术领域中最有希望采用的复合材料之一;在航空航天、军工产品制造、汽车以及电子封装等领域中具有巨大的应用前景。
构成镁基复合材料的基体合金主要分为铸造、变形和超轻等系列。
铸造系包括Mg—AI、Mg—Zn、Mg—AI—Zn、Mg—Zn—Zr、Mg—Zn—Zr—RE等,侧重于制备铸造镁基复合材料;变形系包括Mg—Mn、Mg —AI—Zn、Mg—Zn—Zr、Mg—RE等,偏重于挤压性能的复合材料应用;Mg—Li系是目前最轻质的合金系,具有较强的抗高能粒子穿透能力,以及能显著降低构件重量、节约能量和满足某些高性能的要求。
增强体可以分为颗粒、晶须、纤维等几种,增强体的选择要从复合材料应用情况、制备方法以及增强体的成本等诸多方面综合考虑。
其中,界面相容性和界面间存在的可能反应类型是镁基复合材料制备过程中首先要考虑的问题。
本文将从镁基复合材料中界面反应类型与润湿性、制备技术、组织性能和应用等几个方面对镁基复合材料发展概况进行介绍,并对其今后发展前景进行展望。
1》镁基复合材料中界面反应与润湿性镁基复合材料中可能存在的界面反应类型主要与基体种类和增强相类型以及所采用的制备方法有关。
尤其是在镁中加入Al或镁合金本身含Al元素时,界面间存在的反应情况变得异常复杂。
如表1所列,镁基体中Al主要与增强体中的氧化物和碳起化学反应,生成一些不利于材料性能的界面相,但有时这些界面相也能起到改善润湿性的作用。
有研究认为【2】,SiC /Mg间存在界面反应可使固液界面能降低;Mg在700℃时表面力较小,约为的1/2,这将促使SiC 在Mg基体中均匀分布;也有报道称TiC 在纯Mg中比在纯铝中分布更为均匀【3】。
有关B4C与Mg间的物理润湿性和界面化学相容性的研究结果表明【4,5】,Mg对B4C具有良好的润湿性,是一种较好的增强相。
SiC和TiC等碳化物常被用作镁基复合材料的增强体,主要是由于Mg不易形成稳定的碳化物以及这些碳化物具有较高的强度及化学稳定性。
如果Mg合金中含有Al元素,与碳化物接触时间长时,则会在这些镁合金中起反应形成A14C3,在界面处进一步形成MgA1204尖晶石,从而改变合金的化学成分,影响复合材料腐蚀性能。
此外,界面反应物存在使复合材料在铸造过程中流动性降低【6】。
石墨纤维增强镁基复合材料(Gr~/Mg)具有低密度、高比强度和比刚度等优良的力学性能,并可按照不同纤维含量设计出热膨胀系数在较宽温度围保持为零的材料。
早在1972年,就有人采用热压工艺制备了Gr~/Mg复合材料。
熔融镁不能直接浸润无涂层的石墨纤维,经采用等离子喷涂或物理气相沉积钛及化学镀镍等预先涂覆石墨纤维,均证明与熔融镁问有良好的润湿性。
由于钛的密度较低、熔点较高以及与镁不会形成脆性金属间化合物,故可以采用物理气相沉积。
由于Gr~/Mg复合材料存在制备工艺复杂等缺点而使人们更多地倾向于不连续增强镁基复合材料的研究。
表1 镁基复合材料常用增强体及部分界面反应2》镁基复合材料的制备技术镁基复合材料制备方法主要分为粉末冶金法、铸造法、熔体浸渗法、喷射法、薄膜冶金法以及原位合成技术等。
但在选择具体制备工艺时应考虑增强体与基体的性能,不同制备工艺所获得的复合材料性能也不尽相同,有时差异很大。
2.1 .粉末冶金法(PM法)PM工艺是较早用来制备镁基复合材料的【7】。
其特点是:对基体合金种类和增强体类型以及体积含量没有严格限制,通过粉末混合工艺可以使瓷颗粒在基体中达到分布均匀。
但此工艺设备复杂、成本偏高,不易制备形状复杂的零件;对于极细的颗粒增强体以及晶须等,还要利用特殊的分散技术以达到均匀混合的目的;粉末冶金热压态复合材料一般都需要经过挤压、轧制或锻造等二次成型后才能使用。
该法在制备A1基复合材料中得到了成功应用,尽管镁的化学活泼性高,但通过适当的气氛保护后PM 法同样适用于镁基复合材料的制备。
其中,混粉、压实、烧结3个步骤对复合材料的微观组织和性能有很大影响。
利用PM 工艺,结合低能机械合金化等特殊的粉末混合技术 ],针对不同的镁合金体系以及各种瓷增强体,已有众多的研究报道。
著名的DWA公司、ACM 公司等也采用了PM 工艺,经过二次加工成型后,获得了性能良好的管材、板材以及棒材等。
PM 法是一种通用的复合材料制备方法,只是成本稍高,过程繁琐;若与其他的工艺相结合,适当控制过程的关键参数,复合材料可以获得理想的性能。
对于制作形状复杂的零件,仍需要机加工成形。
另外,此工艺需要生产和使用对人体非常有害的超细镁合金粉末,故在生产中还应考虑必要的安全措施,而下述的铸造工艺则不存在这些缺点。
2.2 .铸造法(Casting Route)搅拌铸造是制备颗粒增强金属基复合材料的一种典型工艺,通常分为3类:①全液态搅拌铸造工艺;②半固态搅拌铸造工艺;前2类工艺属搅拌铸造法。
③搅熔铸造工艺(流变铸造法)。
在氩气或COz/SF 气氛下进行镁合金熔炼,然后将SiC,加入镁熔体中,进行机械搅拌,使颗粒均匀分散于熔融镁合金中,美国Dow化学公司成功制备了颗粒增强镁基复合材料,并取得了该方法的专利。
英国镁电子公司也开发了一种搅拌工艺,它克服了颗粒沉降、聚集及搅拌吸气等问题,能控制界面反应和凝固过程。
从而控制颗粒在复合材料中的分布;随后经热挤压,制备出了性能优良的镁基复合材料;加拿大镁技术研究所也采用搅拌铸造法开发了一种制备Si /Mg复合材料的工艺。
搅熔铸造法是靠桨叶旋转产生的机械搅拌作用使半固态基体合金熔体形成的涡流来强制引入增强颗粒,在增强颗粒与先凝固的金属晶粒混合均匀后再升温浇铸,凝固后得到镁基复合材料的方法。
而上述的搅拌铸造法是在液态下搅拌,搅拌后产生的负压使复合材料很容易吸气而形成气孔,另外增强颗粒与基体合金的密度不同易造成颗粒沉积和微细颗粒的团聚等现象。
半固态成型可以减少宏观偏析,降低凝固收缩和成型温度,且瓷颗粒在基体分布均匀。
由于该工艺在很大程度上降低了镁在高温下的氧化烧损,且该工艺设备简单、成本低,最有希望应用于大规模的工业生产。
AMAX公司开发了一种可大批量生产汽车用低成本镁基复合材料零件的半固态金属成形(SSM)工艺,这是将铸造和锻压2种工艺结合在一起的方法。
其流程为:首先将增强体搅拌进熔融镁合金,然后在电磁搅拌条件下急冷铸造,最后重新加热到半固态,制备近终成形零件。
其优点是:自动化程度高,将材料制备和成形结合起来并且可以做到精确成形。
显然,该工艺在大批量生产低成本、近终成形镁基复合材料方面具有广阔的前景。
2.3.熔体浸渗法(Melt Infiltration Process)按施压方式可以分为压力浸渗、无压浸渗和负压(真空)浸渗3种。
压力浸渗是先把瓷颗粒增强相预制成形,然后将基体熔体倾入,在一定压力下使其浸渗到颗粒间隙而达到复合化的目的;其特点是可以制备高体积分数复合材料。
该工艺已很成熟,其中,预制块中增强体的分布、预制块和模具的预热温度及浸渗压力等均对复合材料结构和性能产生重要影响。
无压浸渗是熔融镁合金在惰性气体保护下,不施加任何压力对压实后的瓷预制块进行浸渗,从而制备出瓷颗粒增强镁基复合材料。
该工艺有许多优点:预制件可预先制成所需形状,渗入后制品保形性好;可获得致密且具有连续显微结构的制品;可具有理想的力学性能;工艺过程简单,相对成本较低。
该技术的关键是:寻找理想的瓷与金属熔体的结合体系,要求润湿性好,各自性能好。
研究的重点主要是复杂形状预制件的渗入工艺、缺陷的类型和控制、渗入过程组分间的相互作用以及渗入后相界面的形貌、结构等对复合材料性能的综合效应。
尽管该工艺有预制块质量影响大、体系有限、方法尚不成熟等不足,但随着研究的进展和工艺的成熟,发展前景看好。
负压浸渗靠在瓷颗粒预制块下造成的真空产生的负压而实现熔融镁合金对压实后的瓷颗粒预制块的浸渗。
通常的做法是将增强体预制块放在预制模具中,然后抽真空,将高压气体注入熔炼炉床,使熔化金属挤入模腔,浸渗预制块。
由于压力低,注入系统新颖,液压成形法可生产大的复杂近终成形零件,不会产生预制块运动、纤维损伤等问题。
由于预制块的相对密度一般较高,利用熔体浸渗法可以很容易制备出高瓷体积含量的镁基复合材料,并且材料可以获得很高的弹性模量以及极低的热膨胀系数,在电子封装材料领域中很有应用潜力。
2.4 .喷射法(Spray Forming)喷射法是一种快速凝固法,包括喷射沉积法、熔融旋压法等。
喷射沉积法首先使液态金属在高压惰性气体喷射下雾化,形成熔融合金喷射流,同时将颗粒喷入熔融合金的射流中,使液固两相颗粒混合并共沉积到预处理的衬底上,快速凝固得到镁基复合材料。
利用此法制备的镁基复合材料中颗粒在基体均匀分布,晶粒细小,界面清洁,但孔隙率较高,需进行二次加工。