镁合金压铸技术的几个主要问题
镁合金压铸及机加工过程中的安全与防护

镁合金压铸及机加工过程中的安全与防护随着科技的不断进步和产品的不断升级,镁合金作为一种轻质、高强度、高刚性和高可塑性的新型材料,已经被广泛应用于汽车、飞机、3C电子和医疗器械等领域。
然而,镁合金具有易燃、易爆等特性,使得其在制造过程中存在一定的安全隐患和风险。
为了确保制造过程中的安全和防止潜在的危险,本文将从镁合金压铸和机加工两个方面探讨相关的安全措施和防护措施。
镁合金压铸过程中的安全与防护1. 防火安全镁合金在高温下容易燃烧,因此在压铸过程中必须注意防火安全。
首先,要保持作业场所清洁,避免杂物和垃圾积累引起火灾;其次,要定期检查压铸机和设备,确保其正常运行;再次,要加强对热源和电气设备的管理,避免发生火灾事故。
2. 防爆安全由于镁合金易发生氧化反应,因此在压铸过程中也存在着爆炸的风险。
为了防止爆炸事故的发生,可以采取以下措施:•安装防爆设备,如压铸机内的气门和快速切断装置等;•严格控制压铸机的温度和压力,避免镁合金处于过热和高压状态;•对压铸机和设备进行定期检查和维护,确保其完好无损。
3. 环境安全在压铸过程中,会产生一定的废气和废液,若未得到妥善处理,会对环境造成污染。
为了保护环境,以下措施可以采取:•采用先进的压铸设备和工艺,减少废气和废液的产生;•采用合适的处理方式,如蒸发、浓缩和焚烧等,将废气和废液处理干净,避免污染环境。
镁合金机加工过程中的安全与防护1. 防火安全在机加工过程中,由于加工切屑和切削油的存在,存在着火灾的风险。
为了防止火灾事故的发生,可以采取以下措施:•保持加工区域的清洁和整洁,防止杂物和垃圾积累;•对机床、夹具和工具等进行定期检查和维护,确保其正常运行;•对切削油进行管理和储存,避免因切削油泄漏或燃烧导致火灾事故。
2. 防爆安全在机加工过程中,镁合金还存在着爆炸的风险。
为了保证机加工过程中的安全,可以采取以下措施:•首先,要确保机床的质量和性能,避免机床在运行过程中产生故障;•其次,要控制镁合金的温度和压力,保持在安全范围内;•最后,要对加工过程进行严密的监控和管理,发现安全隐患及时处理。
镁合金压铸常见缺陷及对策
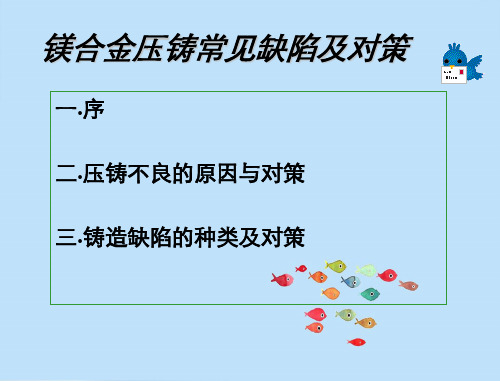
镁合金压铸常见缺陷及对 策
欠陷現象 氣泡 縮陷
续 页 (3)
原因 方法 開模太快
鑄物中含氣量太多
模內溶湯壓力增加 局部冷卻(厚肉部)
對策 手段 1.制品模內時間加強; 1.溶湯的除氣加強; 2.進料管的充填率增多; 3.射出速度放慢; 4.逃氣改善; 5.離型劑柱塞,油減量. 上升鑄造壓力. 鑄入重量增加. 改善模溫的分佈,加強熱點的冷卻.
镁合金压铸常见缺陷及对 策
C.烧 付
模具局部的遇热现象引起,模具与熔汤发生 了溶着现象,特别易发生在成形的小孔; 还有汤口的正冲部也常发生,或是模具倒勾处; 对策有: 降低局部模温,加强离型剂喷涂,抛光模具.
镁合金压铸常见缺陷及对 策
D.麻 面
三种可能:
1.模具腐蚀发生龟裂纹路,造成制品表面如哈密瓜 细纹的外观缺陷;
表面造成冷却而凝固,在充填完之前,后续熔汤所带来的热
量无法把先前所凝固部份再溶解而引起,或者,汤在流动的
途中即已经引起凝固现象,汤痕的深度很浅的话,对于机械
的强度是不至于发生问题,但是若制品要再经过电镀或涂装
的话,会引发表面抛光工时太多,甚至烤漆后表面起泡等等
问题,是不可不防的.
镁合金压铸常见缺陷及对 策
镁合金压铸常见缺陷及对 策
欠陷現象 鑄造裂紋
续 页 (2)
原因
對策
方法
手段
1.制品的模肉時間加長;
頂出條件改善
2.冷卻速度加快;
3.加長循環時間;
1.確認脫模角;
2.制品模內時間縮短;
模具修正或鑄造條件改善 (拉模、頂出力)
3.循環時間縮短; 4.模具表面拋光;
5.冷卻減少;
6.離型劑確認或加長.
镁合金压铸技术的几个主要问题及其应用前景
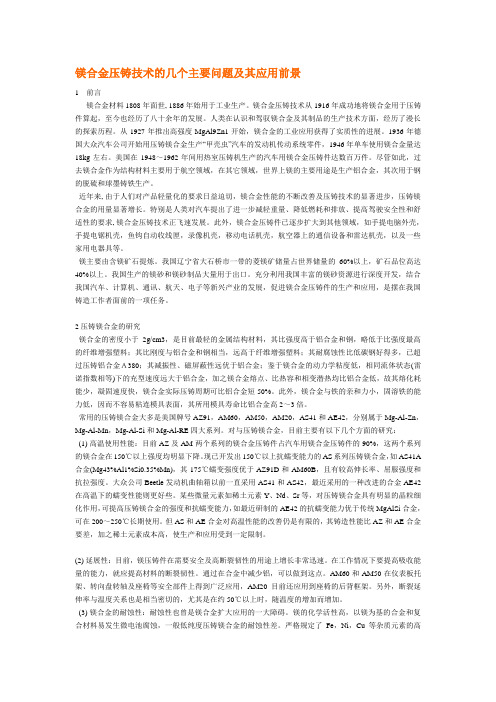
镁合金压铸技术的几个主要问题及其应用前景1前言镁合金材料1808年面世, 1886年始用于工业生产。
镁合金压铸技术从1916年成功地将镁合金用于压铸件算起,至今也经历了八十余年的发展。
人类在认识和驾驭镁合金及其制品的生产技术方面,经历了漫长的探索历程。
从1927年推出高强度MgAl9Zn1开始,镁合金的工业应用获得了实质性的进展。
1936年德国大众汽车公司开始用压铸镁合金生产“甲壳虫”汽车的发动机传动系统零件,1946年单车使用镁合金量达18kg左右。
美国在1948~1962年间用热室压铸机生产的汽车用镁合金压铸件达数百万件。
尽管如此,过去镁合金作为结构材料主要用于航空领域,在其它领域,世界上镁的主要用途是生产铝合金,其次用于钢的脱硫和球墨铸铁生产。
近年来, 由于人们对产品轻量化的要求日益迫切,镁合金性能的不断改善及压铸技术的显著进步,压铸镁合金的用量显著增长。
特别是人类对汽车提出了进一步减轻重量、降低燃耗和排放、提高驾驶安全性和舒适性的要求, 镁合金压铸技术正飞速发展。
此外,镁合金压铸件已逐步扩大到其他领域,如手提电脑外壳,手提电锯机壳,鱼钩自动收线匣,录像机壳,移动电话机壳,航空器上的通信设备和雷达机壳,以及一些家用电器具等。
镁主要由含镁矿石提炼。
我国辽宁省大石桥市一带的菱镁矿储量占世界储量的60%以上,矿石品位高达40%以上。
我国生产的镁砂和镁砂制品大量用于出口。
充分利用我国丰富的镁砂资源进行深度开发,结合我国汽车、计算机、通讯、航天、电子等新兴产业的发展,促进镁合金压铸件的生产和应用,是摆在我国铸造工作者面前的一项任务。
2 压铸镁合金的研究镁合金的密度小于2g/cm3,是目前最轻的金属结构材料,其比强度高于铝合金和钢,略低于比强度最高的纤维增强塑料;其比刚度与铝合金和钢相当,远高于纤维增强塑料;其耐腐蚀性比低碳钢好得多,已超过压铸铝合金A380;其减振性、磁屏蔽性远优于铝合金;鉴于镁合金的动力学粘度低,相同流体状态(雷诺指数相等)下的充型速度远大于铝合金,加之镁合金熔点、比热容和相变潜热均比铝合金低,故其熔化耗能少,凝固速度快,镁合金实际压铸周期可比铝合金短50%。
镁合金压铸件质量缺陷控制浅析论文

镁合金压铸件质量缺陷控制浅析论文
预览说明:预览图片所展示的格式为文档的源格式展示,下载源文件没有水印,内容可编辑和复制
镁合金压铸件质量缺陷控制浅析【摘要】本文简要的介绍了镁合金压铸产品的主要缺陷,主要分析了影响铸件质量的相关因素,如压铸模具、压铸工艺、压铸件结构、压铸合金及压铸作业等,提出了质量控制的相应方法和管理规程,使镁合金铸件质量得到进一步提高。
【关键词】材料;镁合金缺陷;质量控制;管理规程
我公司引进的布勒压铸机,最大锁模力3200kn,活塞动态注射力786kn,增压注射力2033kn。
从工作稳定性来说,在凝固阶段中根据系统的类型可生产非常高的最终压射压力;从控制能力来说,可以对速度和最终压力曲线进行编程以适合压铸零件的几何形状,实行控制参数量。
那如何利用设备的优良性能,压铸出高品质的铸件,清楚铸件质量控制中存在的缺陷,全过程的质量控制和多方法的质量管理将起到关键性的作用。
1.镁合金压铸件主要缺陷和形成原因
镁合金压铸产品的缺陷很多,大致可以分为两大类,一类是尺寸不良,如多料,缺料,裂纹,流痕,平面度不良等;另一类是表面状态不良,如氧化,黑点,气孔等。
前者一般属于物理性质,后者属于化学性质。
总体来讲,镁合金压铸件主要可概括为冷、裂、气、欠等几大缺陷。
1.1冷
即为冷隔,多出现在大铸件离內浇口远的区域,是镁合金液相互对接或搭接单位熔合而出现的缝隙。
由于合金液分成若干股地流。
镁合金压铸常常遇到的问题
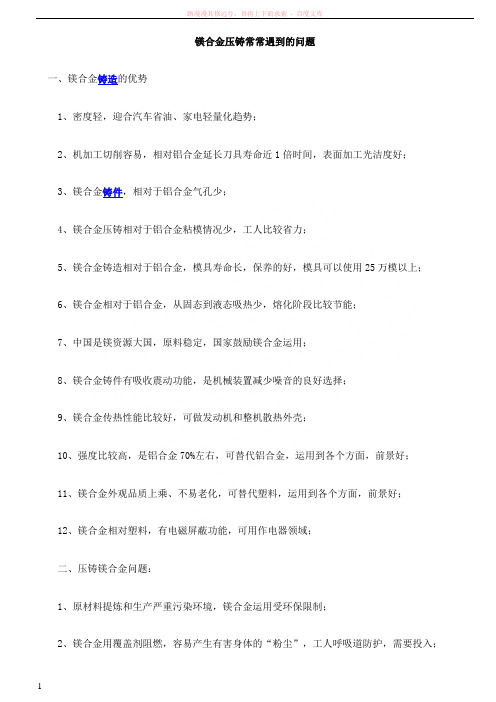
镁合金压铸常常遇到的问题一、镁合金铸造的优势1、密度轻,迎合汽车省油、家电轻量化趋势;2、机加工切削容易,相对铝合金延长刀具寿命近1倍时间,表面加工光洁度好;3、镁合金铸件,相对于铝合金气孔少;4、镁合金压铸相对于铝合金粘模情况少,工人比较省力;5、镁合金铸造相对于铝合金,模具寿命长,保养的好,模具可以使用25万模以上;6、镁合金相对于铝合金,从固态到液态吸热少,熔化阶段比较节能;7、中国是镁资源大国,原料稳定,国家鼓励镁合金运用;8、镁合金铸件有吸收震动功能,是机械装置减少噪音的良好选择;9、镁合金传热性能比较好,可做发动机和整机散热外壳;10、强度比较高,是铝合金70%左右,可替代铝合金,运用到各个方面,前景好;11、镁合金外观品质上乘、不易老化,可替代塑料,运用到各个方面,前景好;12、镁合金相对塑料,有电磁屏蔽功能,可用作电器领域;二、压铸镁合金问题:1、原材料提炼和生产严重污染环境,镁合金运用受环保限制;2、镁合金用覆盖剂阻燃,容易产生有害身体的“粉尘”,工人呼吸道防护,需要投入;3、镁合金用覆盖剂阻燃,容易产生HCL气体,和水蒸气结合,产生腐蚀性极强的稀盐酸,对工厂人员、设备和厂房基建有损害,厂房顶棚行车支撑等需要防腐蚀;4、镁合金用SF6混合气体阻燃,SF6气体由于制造混有有毒杂质,如HF等,所以需要严格管理;SF6是温室气体,在我国使用会受到限制;5、镁合金容易燃烧,熔化、保温、运输防止燃烧,有技术门槛;6、镁合金容易燃烧,熔化炉、保温炉的合金残渣清理工作量大;7、镁合金容易燃烧,如果设备比较老,机器外泄漏情况频繁,合金保温炉不密封,液压油请使用不燃油,防止火灾,生产现场易燃易爆气体和液体不要存放;8、镁合金容易燃烧,机器和熔化炉边上需要放(一大缸)黄沙放置易燃镁渣,(一大桶)阻燃覆盖剂,作为熄灭压铸过程中零星逃料产生的火情;9、镁合金的粉尘会自燃,高温镁渣也会燃烧,需要集中特殊处理;10、镁合金作为结构材料,容易受潮氧化,需要做表面处理,镀铬和阳极氧化污染环境镁合金作为结构材料,螺栓连接处因电化学腐蚀和蠕变,造成紧固件松动;11、镁合金铸件热强度低,容易产生热裂纹,造成铸件漏气和断裂;12、镁合金比热容低,热量损失快,需要模具一般需要设计加热装置;13、镁合金遇油燃烧,遇水爆炸;大块的镁合金失控燃烧,火势难以控制,以预防为主;。
镁合金压铸不良原因与对策
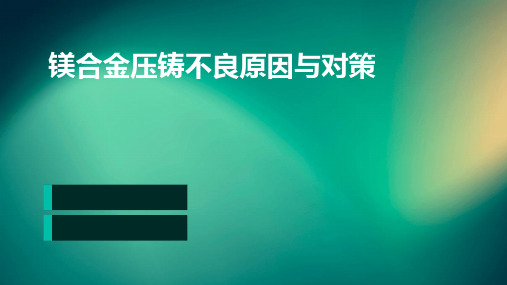
案例三
• 总结词:精确控制模具温度是提高镁合金压铸质量的关键因素之一。 • 详细描述:在镁合金压铸过程中,模具温度是一个非常重要的参数。如果模具温度过高或过低,都会导致压铸
件出现各种缺陷,如气孔、缩孔、冷隔等。因此,精确控制模具温度是提高镁合金压铸质量的关键因素之一。 为了实现精确控制模具温度的目的,可以采用先进的测温设备和技术手段,实时监测模具的温度变化情况。同 时,还需要根据生产情况和工艺要求,合理调整和控制压铸机的温度参数。通过精确控制模具温度,可以有效 地提高镁合金压铸质量,减少气孔、缩孔等缺陷的产生,提高产品的合格率。
模具结构复杂,导致排气不良、冷却不均等情况,影响压铸件质量。
模具尺寸精度和表面粗糙度未达到要求,导致压铸件表面质量差、尺寸不稳定。
模具温度控制不当
模具预热温度过低,导致镁合 金流动性下降,填充困难。
模具温度波动大,影响压铸件 尺寸和外观质量。
冷却水道设计不合理,导致模 具局部温度过高或过低,引发 压铸件开裂、缩孔等问题。
感谢您的观看
05 结论
对策实施效果总结
01
对策实施后,镁合金压铸不良率显著降低,提高了产品的质量 和稳定性。
02
通过改进压铸工艺和优化模具设计,有效解决了镁合金压铸过
程中出现的气孔、缩孔和表面质量不佳等问题。
针对镁合金的特性,采用适当的熔炼和浇注工艺,确保了镁合
03
金液的纯净度和充型能力,进一步提高了压铸件的质量。
镁合金压铸不良原因与对策
目录
• 引言 • 镁合金压铸不良原因分析 • 对策与解决方案 • 案例分析 • 结论
01 引言
镁合金压铸的重要性
镁合金压铸作为一种重要的金属成型 工艺,广泛应用于汽车、航空航天、 电子产品等领域。
镁合金熔炼铸造易出现的缺陷

镁合金熔炼铸造易出现的缺陷:由于镁合金的铸造性能较差,在镁合金的铸件生产中容易出现多种缺陷,并且较难消除,造成生产成本高。
常见的缺陷有疏松,夹渣,裂纹,气孔等。
我们必须从原辅材料开始控制质量,模具,设备,工序都要严格的控制和检验。
现做问题的分析处理,跟足去验证;1,疏松;(包跨表面脱层,明显熔合位等。
)该缺陷容易在内浇口及热节处出现。
这种缺陷一般在铸件的内部,肉眼不可见。
通过X 射线检查能检测出,由于浇口及热节部位则由于长时间处于过热状态,擬固过程中温度较高导致产生该缺陷。
防此这类缺陷要做好以下几方面的工作:(1),从工艺的角度合理设计好浇口系统,经反复实验确定直浇道,横浇道与浇口的截面积最佳之比为1:3:3;并合理进行冒口尺寸的改善,强化冒口的补缩作用,形成铸件有顺序的擬固;(2),充分利用冷铁的激冷效果帮助热节处补缩,一般冷铁是与冒口配合使用的;(3),在有疏松的位置使用暗冒口补缩,如果效果不好时,应适当增大冒口的体积或使用保温冒口,而在不易清理冒口的地方做成易割冒口。
以上的操作,实验证明都是有效的。
2,夹渣;(包跨常说的熔剂点,结疤,等等。
)该缺陷在铸件酸洗处理后,有的表面或铸件尖角处,暴露出黑斑夹杂物。
肉眼可见。
黑斑由一个接近圆形的浅色区所包围。
并以一个更黑的环为边界。
这种夹渣物一般是溶剂造成的,不但会降低铸件的力学性能,并且溶剂中的MgCl2直接降低铸件的抗腐蚀能力,镁和镁合金及易氧化,特别是ZM系列合金,更易氧化。
为防此镁合金在熔炼时氧化燃烧,而在熔炼中要加一定的溶剂,使之不与空气接触,由于溶剂的性能不好或操作不当,浇注工具上的溶剂容易进入到金属液中;舀取金属液不当,将溶剂带入到金属液中;由于浇注不槙,浇包上面浮着的溶剂进入到模腔中。
更可能是浇注温度较高,镁合金液在型腔中与泥芯放出的气体反应燃烧,产生二次氧化夹渣所致。
要消除这种缺陷。
具体方法如下:(1),使用带节流管的茶壶式浇包时,要磕掉粘附着的熔剂,浇包和坩埚底部少量的熔液不能浇入型腔,从坩埚中舀取金属液前,必须用浇包底部拨开液面的熔剂及氧化层。
镁合金压铸技术设备工艺缺陷和对策

镁合金压铸技术设备工艺缺陷和对策引言镁合金作为一种轻质高强度材料,在汽车、航空航天等领域具有广泛的应用前景。
在镁合金加工中,压铸技术是一种重要的加工方法。
然而,镁合金的压铸过程中常常出现一些工艺缺陷,如气孔、热裂纹等,这些缺陷会影响产品的质量和性能。
本文将针对镁合金压铸技术设备工艺缺陷进行分析,并提出相应的对策,以期提升镁合金压铸产品的质量和性能。
1. 气孔问题及对策气孔是镁合金压铸过程中常见的缺陷之一,主要是由于气体在压铸过程中被困于铸件内部或者与熔体发生反应产生气泡所致。
气孔的存在会降低产品的机械性能,并且对表面质量和涂装性能也会产生负面影响。
针对气孔问题,可以采取以下对策: - 提高熔体的氧化还原性:通过添加合适的气体剂或添加剂,增加熔体的还原能力,减少气泡产生。
- 优化冷却系统:合理设计冷却系统,控制压铸过程中的温度变化,减少气泡形成的机会。
- 改进模具设计:优化模腔结构,减少气体的积聚和滞留,提高熔体的流动性,减少气孔产生。
2. 热裂纹问题及对策热裂纹是镁合金压铸过程中另一个常见的缺陷,主要是由于熔体凝固过程中温度梯度产生的应力导致的。
热裂纹会使产品的强度和韧性降低,并且也对修复和加工造成困难。
针对热裂纹问题,可以采取以下对策: - 控制铸件的壁厚和几何形状:合理设计铸件的壁厚和几何形状,减少熔体凝固过程中的温度梯度,降低应力的产生。
-控制铸造温度和冷却速率:通过调整熔体的温度和冷却速率,控制凝固过程中的温度梯度,减少应力的产生。
- 采用合适的合金配比:选择合适的镁合金配比,使其具有较低的热膨胀系数和较高的热导率,减少热应力的产生。
3. 表面缺陷问题及对策在镁合金压铸过程中,还常常出现一些表面缺陷,如划痕、氧化和烧结等问题。
这些缺陷不仅影响产品的外观质量,还可能导致产品的腐蚀和失效。
针对表面缺陷问题,可以采取以下对策: - 控制模具表面的清洁度:保持模具表面的清洁,避免污染物和异物附着在铸件上,减少缺陷的发生。
- 1、下载文档前请自行甄别文档内容的完整性,平台不提供额外的编辑、内容补充、找答案等附加服务。
- 2、"仅部分预览"的文档,不可在线预览部分如存在完整性等问题,可反馈申请退款(可完整预览的文档不适用该条件!)。
- 3、如文档侵犯您的权益,请联系客服反馈,我们会尽快为您处理(人工客服工作时间:9:00-18:30)。
镁合金压铸技术的几个主要问题及其使用前景1前言镁合金材料1808年面世, 1886年始用于工业生产。
镁合金压铸技术从1916年成功地将镁合金用于压铸件算起,至今也经历了八十余年的发展。
人类在认识和驾驭镁合金及其制品的生产技术方面,经历了漫长的探索历程。
从1927年推出高强度MgAl9Zn1开始,镁合金的工业使用获得了实质性的进展。
1936年德国大众汽车公司开始用压铸镁合金生产“甲壳虫”汽车的发动机传动系统零件,1946年单车使用镁合金量达18kg左右。
美国在1948~1962年间用热室压铸机生产的汽车用镁合金压铸件达数百万件。
尽管如此,过去镁合金作为结构材料主要用于航空领域,在其它领域,世界上镁的主要用途是生产铝合金,其次用于钢的脱硫和球墨铸铁生产。
近年来, 由于人们对产品轻量化的要求日益迫切,镁合金性能的不断改善及压铸技术的显著进步,压铸镁合金的用量显著增长。
特别是人类对汽车提出了进一步减轻重量、降低燃耗和排放、提高驾驶安全性和舒适性的要求, 镁合金压铸技术正飞速发展。
此外,镁合金压铸件已逐步扩大到其他领域,如手提电脑外壳,手提电锯机壳,鱼钩自动收线匣,录像机壳,移动电话机壳,航空器上的通信设备和雷达机壳,以及一些家用电器具等。
镁主要由含镁矿石提炼。
我国辽宁省大石桥市一带的菱镁矿储量占世界储量的60%以上,矿石品位高达40%以上。
我国生产的镁砂和镁砂制品大量用于出口。
充分利用我国丰富的镁砂资源进行深度开发,结合我国汽车、计算机、通讯、航天、电子等新兴产业的发展,促进镁合金压铸件的生产和使用,是摆在我国铸造工作者面前的一项任务。
2、压铸镁合金的研究镁合金的密度小于2g/cm3,是目前最轻的金属结构材料,其比强度高于铝合金和钢,略低于比强度最高的纤维增强塑料;其比刚度和铝合金和钢相当,远高于纤维增强塑料;其耐腐蚀性比低碳钢好得多,已超过压铸铝合金A380;其减振性、磁屏蔽性远优于铝合金[1];鉴于镁合金的动力学粘度低,相同流体状态(雷诺指数相等)下的充型速度远大于铝合金,加之镁合金熔点、比热容和相变潜热均比铝合金低,故其熔化耗能少,凝固速度快,镁合金实际压铸周期可比铝合金短50%。
此外,镁合金和铁的亲和力小,固溶铁的能力低,因而不容易粘连模具表面,其所用模具寿命比铝合金高2~3倍。
常用的压铸镁合金大多是美国牌号AZ91,AM60,AM50,AM20,AS41和AE42,分别属于Mg-Al-Zn,Mg-Al-Mn,Mg-Al-Si和Mg-Al-RE四大系列。
对和压铸镁合金,目前主要有以下几个方面的研究:(1) 高温使用性能:目前AZ及AM两个系列的镁合金压铸件占汽车用镁合金压铸件的90%,这两个系列的镁合金在150℃以上强度均明显下降。
现已开发出150℃以上抗蠕变能力的AS系列压铸镁合金,如AS41A合金(Mg43%Al1%Si0.35%Mn),其175℃蠕变强度优于AZ91D和AM60B,且有较高伸长率、屈服强度和抗拉强度。
大众公司Beetle发动机曲轴箱以前一直采用AS41和AS42,最近采用的一种改进的合金AE42在高温下的蠕变性能则更好些[1,2]。
某些微量元素如稀土元素Y、Nd、Sr等,对压铸镁合金具有明显的晶粒细化作用,可提高压铸镁合金的强度和抗蠕变能力,如最近研制的AE42的抗蠕变能力优于传统MgAlSi合金,可在200~250℃长期使用[3]。
但AS和AE合金对高温性能的改善仍是有限的,其铸造性能比AZ和AE合金要差,加之稀土元素成本高,使生产和使用受到一定限制。
(2) 延展性:目前,镁压铸件在需要安全及高断裂韧性的用途上增长非常迅速。
在工作情况下要提高吸收能量的能力,就应提高材料的断裂韧性。
通过在合金中减少铝,可以做到这点。
AM60和AM50在仪表板托架、转向盘转轴及座椅等安全部件上得到广泛使用,AM20目前还使用到座椅的后背框架。
另外,断裂延伸率和温度关系也是相当密切的,尤其是在约50℃以上时,随温度的增加而增加。
(3) 镁合金的耐蚀性:耐蚀性也曾是镁合金扩大使用的一大障碍。
镁的化学活性高,以镁为基的合金和复合材料易发生微电池腐蚀,一般低纯度压铸镁合金的耐蚀性差。
严格规定了Fe,Ni,Cu等杂质元素的高纯度压铸镁合金(如AZ91D),以及含稀土的AE42,其盐雾试验的耐蚀性已超过压铸铝合金A380,远好于低碳钢[4]。
调整化学成分、表面处理和控制微观组织等均可改善其耐蚀性。
尽管提高镁合金件耐蚀性的方法众多,但若不从材质本身解决问题,耐蚀性差始终是镁合金件获得大量使用的一个技术障碍。
(4) 阻燃镁合金:在镁合金中添加Al(2.5%)、Be合金(Be加入量为0.0005%~0.03%)或含Ca合金,也可有效地防止镁合金液的氧化。
目前,一些研究者正在从事具有阻燃性能镁合金的研究[5],这一研究一旦获得成功,则镁合金就像铝合金一样熔炼和铸造,获得更为广泛的使用前景。
(5) 镁合金基复合材料:用碳化硅等颗粒增强的镁合金基复合材料已进行了多年的研究开发,目前虽尚未达到在压铸领域商业使用的阶段,但已用砂型铸造、精密铸造等方法制成了叶轮、自行车曲柄、汽车缸套等铸件,并有将这种复合材料和半固态铸造相结合,使用于压铸和挤压铸造领域的发展趋势[5]。
3镁合金压铸方式镁合金可用冷室或热室压铸机压铸。
目前对热室压铸机的改进主要包括:采用储能器增压,压射柱塞的压射速度可达6m/s;感应加热鹅颈管和喷嘴,使之保持最适宜温度;采用双炉熔化保温,并采用绝热装置和再循环管道,精确保持熔池温度。
当用普通冷室压铸机压铸镁合金时,必须对压铸机的压射系统和自动给料系统进行必要的改造,使之适用于镁合金压铸的要求。
改造的内容包括:(1) 将压射系统的快压射速度由压铸铝合金时的4~5m/s提高到6~10m/s;(2) 缩短增压过程的建压时间;(3) 提高压射力;(4) 采用电磁自动定量给料装置,防止镁合金在浇注过程中氧化;(5) 如采用真空压铸等特种压铸工艺时,配置必要的配套设备。
和其他压铸合金一样,传统的压铸技术使镁合金液以高速的紊流和弥散状态充填压铸型腔,气体在高压下或者溶解在压铸合金内,或者形成许多弥散分布在压铸件内的高压微气孔。
因此用传统压铸方法生产的镁合金压铸件不能进行热处理强化,也不能在较高温度下使用。
为了消除这种缺陷,提高压铸件的内在质量,扩大压铸件的使用范围,近20年来研究开发了一些新的压铸方法,其中包括充氧压铸,半固态金属流变或触变压铸和挤压铸造,以及几经起伏的真空压铸等。
真空压铸通过在压铸过程中抽除型腔内的气体而消除或显著减少压铸件内的气孔和溶解气体,提高压铸件的力学性能和表面质量。
目前已成功地在冷室压铸机上用真空压铸法生产出AM60B镁合金汽车轮毂,在锁型力为2940kN的热室压铸机上生产出AM60B镁合金汽车方向盘零件,铸件伸长率由8%提高至16%[6]。
充氧压铸又称无气孔压铸(Pore-Free Die Casting Process,即P.F法)。
该法在金属液充型前,将氧气或其他活性气体充入型腔,置换型腔内的空气,金属液充型时,活性气体和充型金属液反应生成金属氧化物微粒弥散分布在压铸件内,从而消除压铸件内的气体,使压铸件可热处理强化。
日本轻金属(株)用充氧压铸法生产计算机的AZ91镁合金整体磁头支架,代替原先的多层叠合支架,不但减轻了支架重量,并且取得了很大的经济效益。
该公司还用充氧压铸法成批生产了AM60镁合金汽车轮毂和摩托车轮毂,和铝轮毂相比,重量减轻15%。
近年来美国、日本和英国等国的公司相继成功开发出镁合金半固态触变射压铸造机。
镁合金半固态触变射压铸造机以一定压力将半固态镁合金射入压铸型内而使之成形,其工作原理类似于注塑机。
它将预制的非枝晶态镁粒送入螺旋给料机构,在螺旋给料机构中将镁粒加热到半固态,并通过螺旋给料机构另一端的镁合金浆料收集室将半固态镁合金浆料送入压射室进行射压成形。
这种铸造成形方法代表了镁合金铸件生产的一个发展方向。
4镁合金熔炼作业和安全生产由于镁合金液很容易氧化,而且表面生成的氧化膜是疏松的,其致密系数α值仅为0.79,不能防止合金继续氧化。
镁合金液和大气中氧、水蒸气、氮反应生成不熔于镁液的难熔的MgO、Mg3N2等化合物,混入铸型后即形成“氧化夹渣”。
因此,熔炼合金时防氧化至关重要。
镁合金的熔体保护主要有两种方法,即熔剂保护和气体保护。
用保护熔剂熔炼通常会带来以下问题:(1) 氯盐和氟盐高温下易挥发产生有毒气体,如HCl,Cl2,HF等;(2) 由于熔剂的密度较大,部分熔剂会随同镁液混入铸型造成“熔剂夹渣”;(3) 熔剂挥发产生的气体有可能渗入合金液中,成为材料使用过程中的腐蚀源,加速材料腐蚀,降低使用寿命。
目前多数厂家使用气体保护,即用干燥的SF6、N2、CO2、SO2气体中的2~4种组成混合气体,在镁合金熔池表面形成致密的连续薄膜以阻止镁合金液的氧化。
SF6不是毒性气体,但它对地球的温室效应比CO2严重24000倍,而镁工业的SF6用量占世界总用量的7%(1996年),将来必然会限制其用量乃至停止其使用,但目前尚未找到SF6的合适替代物。
研究表明,用硫磺粉末撒于熔池表面形成的SO2对镁合金液有保护作用[7]。
镁合金压铸件生产的危险大多由加工及后处埋过程中的过失所引起。
据日本方面统计,镁合金压铸件生产过程中引发的危险,熔炼占25%,铸造占10%,加工占39%,贮藏及废弃物占16%,电气占3%,其他占7%。
显然,加工和后处理过程的危险性超过压铸过程3~4倍。
加工过程中,无论是喷砂、车削、铣削、抛光等,均不可避免会产生镁尘屑及火花,如厂房内通凤不良,空气中镁尘浓度过大,一旦火花和空气或地面的镁尘接触,轻则燃烧,重则爆炸。
因此厂房内必须安装集尘器并配备防火砂及防火设施。
5压铸型设计由于镁合金的化学、物理参数及压铸特性和铝合金有很大差异,因此铸型设计则不能完全套用铝合金压铸型设计原则[8]。
镁合金液易氧化燃烧,铸造时热裂倾向比铝合金大,在熔化、浇注及压铸型温控制等方面都比铝合金压铸复杂。
镁合金充型时间短,排气问题尤为突出,镁合金的比热容和相变潜热均比铝合金低,因而压铸过程中容易发生局部(薄截面部位)提前结晶现象,导致补缩通道堵塞,产生浇不足的缺陷。
镁合金压铸型设计主要考虑以下几个方面:(1) 压铸机选择。
采用何种形式的压铸机进行生产主要取决于铸件的壁厚。
Roland Fink在对“镁合金压铸工艺的优化”问题进行研究的过程中,通过对镁合金压铸经济性、冷室压铸和热室压铸过程分析提出,一般情况下小于1kg的铸件需要采用热室压铸机,以保证薄壁件的充满,大件则推荐采用冷室压铸机。
(2) 工艺参数。
在压铸生产过程中,选择合适的工艺参数是获得优质铸件发挥压铸机最大生产率的先决条件,是正确设计压铸模的依据。