船舶建造流程图
现代船舶建造工艺流程-壳舾涂一体化造船模式
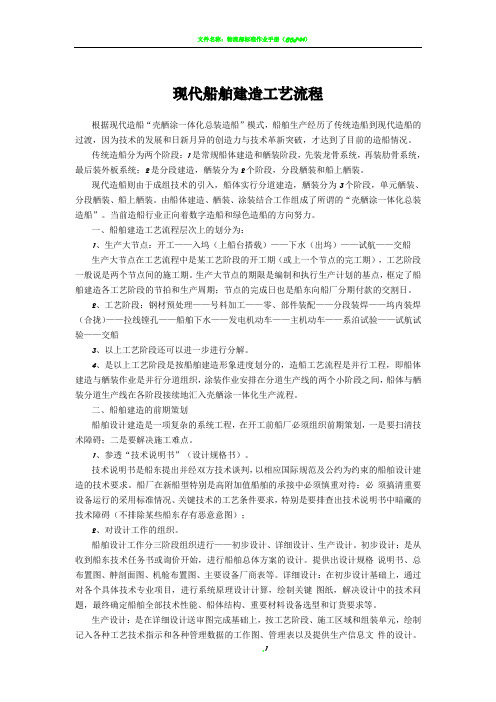
现代船舶建造工艺流程根据现代造船“壳舾涂一体化总装造船”模式,船舶生产经历了传统造船到现代造船的过渡,因为技术的发展和日新月异的创造力与技术革新突破,才达到了目前的造船情况。
传统造船分为两个阶段:1是常规船体建造和舾装阶段,先装龙骨系统,再装肋骨系统,最后装外板系统;2是分段建造,舾装分为2个阶段,分段舾装和船上舾装。
现代造船则由于成组技术的引入,船体实行分道建造,舾装分为3个阶段,单元舾装、分段舾装、船上舾装。
由船体建造、舾装、涂装结合工作组成了所谓的“壳舾涂一体化总装造船”。
当前造船行业正向着数字造船和绿色造船的方向努力。
一、船舶建造工艺流程层次上的划分为:1、生产大节点:开工——入坞(上船台搭载)——下水(出坞)——试航——交船生产大节点在工艺流程中是某工艺阶段的开工期(或上一个节点的完工期),工艺阶段一般说是两个节点间的施工期。
生产大节点的期限是编制和执行生产计划的基点,框定了船舶建造各工艺阶段的节拍和生产周期;节点的完成日也是船东向船厂分期付款的交割日。
2、工艺阶段:钢材预处理——号料加工——零、部件装配——分段装焊——坞内装焊(合拢)——拉线镗孔——船舶下水——发电机动车——主机动车——系泊试验——试航试验——交船3、以上工艺阶段还可以进一步进行分解。
4、是以上工艺阶段是按船舶建造形象进度划分的,造船工艺流程是并行工程,即船体建造与舾装作业是并行分道组织,涂装作业安排在分道生产线的两个小阶段之间,船体与舾装分道生产线在各阶段接续地汇入壳舾涂一体化生产流程。
二、船舶建造的前期策划船舶设计建造是一项复杂的系统工程,在开工前船厂必须组织前期策划,一是要扫清技术障碍;二是要解决施工难点。
1、参透“技术说明书”(设计规格书)。
技术说明书是船东提出并经双方技术谈判,以相应国际规范及公约为约束的船舶设计建造的技术要求。
船厂在新船型特别是高附加值船舶的承接中必须慎重对待:必须搞清重要设备运行的采用标准情况、关键技术的工艺条件要求,特别是要排查出技术说明书中暗藏的技术障碍(不排除某些船东存有恶意意图);2、对设计工作的组织。
船舶设计与建造.ppt
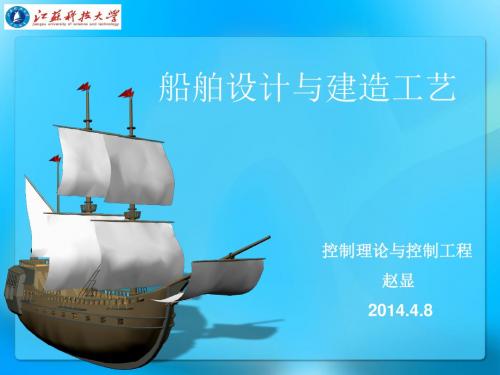
尾部立体分段
(6) 船台总装
船舶(船坞)总装主要指的是船体总装,即在船体结构 经过预装配形成的分段或总段之后在船台(船坞)完成整个 船体装配(也有下水之后再吊装上建的)的工艺阶段。船台 总装也可称之为大合拢、搭载,它对保证船舶建造质量,缩 短船舶建造周期有着很大的影响。 船台(坞)建造方法。由于产品对象和船厂的生产条件 各不相同,船台建造方式也多种多样,一些常用的建造 方法有总段建造法、塔式建造法、岛式建造法、串 联建造法。
船舶设计与建造工艺
控制理论与控制工程 赵显 2014.4.8
引言
任何一种产品都有其自身的生产模式,比如汽车的流水线 生产,飞机的脉动生产线,然而船舶生产具有其独特的特点: 生产的批量为小到中等,零部件的加工过程相似但几何形状和 尺寸不同,这就决定其生产模式的特殊性。 所谓现代造船模式,就是以统筹优化理论为指导,应用成 组技术原理,以中间产品为导向,按区域组织生产,壳、舾、 涂作业在空间上分道、时间上有序,实现设计、生产、 管理一体化,均衡、连续地总装造船。
装焊车间内的平面分段流水线
ቤተ መጻሕፍቲ ባይዱ
部件拼装
部件拼装
平面分段流水线上的焊接机器人
(5) 分段制造
船体分段(section)指的是由零部件组装而成的船体 局部结构。船体分段的类型有: (1)平面分段。平面板列上装有骨材的单面平面板架, 如舱壁分段、舱口围壁分段、平台甲板分段、平行中体处的 舷侧分段等。 (2)曲面分段。曲面板列上装有骨材的单面曲面板架 ,如单层底分段、甲板分段(指有曲面梁拱的)、舷侧分 段等。 (3)半立体分段。两层或两层以上板架所组成的 非封闭分段或者是单层板架带有一列与其成交角的 板架所组成的分段。例如,带舱壁的甲板分段, 甲板室分段。
船舶建造的工艺流程

船舶建造的工艺流程船舶建造的工艺流程可以分为以下几个步骤:第一步:设计和规划船舶的建造开始于设计和规划阶段。
设计师根据客户的需求和要求,绘制出船舶的草图和设计图纸。
在设计过程中,需要考虑到船舶的用途、尺寸、载重量和航行条件等因素。
设计过程还包括选择适当的材料和船舶的结构等。
第二步:材料采购和制备一旦船舶的设计完成,就需要采购建造所需的材料。
这些材料主要包括钢板、铝板、船舶设备和配件等。
材料必须按照设计要求进行检测和认证,确保材料的质量和可靠性。
材料准备完成后,还需要进行切割、成型和加工等工艺过程,以便适应船体的结构和形状。
第三步:船体组装和焊接在船体组装和焊接阶段,各个部件被装配在一起,形成船舶的骨架。
工人们使用专业的工具和设备,将各个部件精确地安装到船体上,并通过焊接技术将它们牢固地固定在一起。
焊接过程需要严格遵守船舶建造的标准和规定,以确保焊接的质量和强度。
第四步:设备和系统安装在船体组装完成后,各种设备和系统将被安装到船舶上。
这些设备和系统包括电气系统、通信系统、水暖系统、空调系统和驾驶设备等。
在安装过程中,需要对设备进行适当的测试和调试,以确保其正常运行和安全性。
第五步:涂装和装饰完成设备安装后,船舶需要进行涂装和装饰。
这一步骤旨在保护船舶的金属表面免受腐蚀和侵蚀,并提升船舶的外观和舒适度。
在涂装过程中,采用专业的涂料和防腐材料,确保船体表面的光滑和牢固。
第六步:测试和调试最后,船舶需要进行全面的测试和调试,以确保其在海上的运行安全和性能。
包括舾装试验、船舶载重试验、漏水试验等等,对船舶的各个系统进行严格的检测和评估。
只有通过了所有的测试和调试,船舶才能交付给客户使用。
船舶建造的工艺流程是一个复杂且需要高度专业知识和技术的过程。
每个步骤都需要精细的计划和严格的质量控制,以确保船舶的质量和安全性。
船舶建造所采用的工艺和技术在不断的发展和创新中,以满足不断变化的市场需求和客户要求。
船舶制造过程ppt课件

根据放样资料提供的数据可制造样板和样箱,同时对胎架 型值,各种构件的加工信息和后续工序的连续数据提供全部施 工信息。
13
(2)钢材预处理
钢材表面一般带有氧化皮、铁钻、局部凹凸不平、翘 曲或扭曲等缺陷,需要对钢材进行矫平、除锈和涂防护底 漆等作业,这些作业统称为钢材预处理。
6.造船工艺的主要任务:一方面应根据现有技术条件为造
船生产制订优良的工艺方案和工艺方法以缩短周期、降低生产 成本、提高质量和改善生产条件;另一方面应大力研究开发新 工艺、新技术来断提高造船工艺水平,以适应社会经济不断发 展的需要。
7
三、船舶建造的内容和工艺流程
1.船舶建造的内容 上世纪七十代前
上世纪七十代后
9
1.2舾装工艺
将各种船用施备、仪器、装置、设施等安装
到船上的全过程,以确保舶舶的正常航行,满
足人们在船上的工作、生活、休息等一切活动
的需要。
舾装作业系统:
在使用材料上包括钢材铝、铜等许多有色金属及合
金、非金属方面包托木材、工程塑料、水泥、陶瓷、
橡胶和玻璃及装饰材料等繁多的种类;
涉及的工种有装配工、电工、木工、管工、钳工等
4
船舶的其他装置和设备包括
锚设备与系泊设备; 舵设备与操舵装置; 救生设备; 消防设备; 船内外通信设备; 照明设备; 信号设备; 导航设备;
起货设备; 通风、空调和冷藏设备; 海水和生活用淡水系统; 压载水系统; 液体舱的测深系统和透气系统; 舱底水疏干系统; 船舶电气设备; 其他特殊设备(依船舶的特殊需 要而定)。
(3)号料
把按草图样板、样箱等放样资料进行放样展开后的各零件 图的图样及其加工、装配符号,画到平直的钢板或型钢上。
船舶概论(第九章_建造工艺)

30万吨“远大湖”号 ——中远集 团
ϒ 总长
(333米) 米 型宽 (60米) 米 航速 (15.6节) 节 总载重 298833 吨, 2002建 造, PANA MA
30万吨船坞——大连船舶重工集团
第七节 试验与交船
ϒ 试验: 系泊试验:在码头进行,检查船体、设备等安装的可 靠性,达到试航条件。 航行试验:对船舶进行全面、综合检查,有试验大纲、 设备、船检、船东参加。 ϒ 交船:将船交给船东,签订合格协议。
航行试验
ϒ ϒ ϒ ϒ
1.地点:海面或江河湖泊上 2.种类:轻载试验、满载试验 3.参与者:船厂、验船机构、船东 4.航行试验的主要项目及目的:
1)检查主机、辅机及与其有关的动力装置一起工作的可靠 性; 2)检查一切保证船舶航行的装置及机械设备工作的可靠性 3)进行抛锚试验; 4)检查船舶的航行性能,它包括:
第七章 船舶建造工艺
ϒ 第一节 造船工艺流程 ϒ 第二节 船体放样和号料 ϒ 第三节 船体构件加工 ϒ 第四节 船体装配焊接 ϒ 第五节 船舶舱室的密闭性试验 ϒ 第六节 船舶下水 ϒ 第七节 船舶舾装及交船试验
第一节:现代造船工艺流程
1、船舶制造特点
ϒ ϒ ϒ ϒ ϒ
订单型 综合型 装置型 大型结构物
船体平面分段流水线
平面分段流水线区域
钢板平台
胎架
焊接站
壳舾涂区域
干船坞
分段预舾装
分段制作区域
上层建筑分段
船舶分段涂装房
涂装区域
150T分段移动车
总段吊装
双车桥式吊车
水平船台两大总段造船
舾装码头
上海外高桥船厂的巨型船坞
第五节:船体密性试验
ϒ 目的:检查船舶外板、舱壁等焊缝有无渗漏现象,保证船舶安全 ϒ 方法: 水压试验(世界船级社认可) 气密试验: 充气试验:检查上甲板以下的舱室和储存液体的舱室 方法: 试验压力为15 - 50kPa,在1 小时内空气压力不得下降 5% ,并在被检验的焊缝外表面涂上肥皂水,以便发现缺陷 冲气试验:检验不作充气试验的舱室 方法:在焊缝的一面用压缩空气冲气,另一面涂 上肥皂水,以 检查是否有缺陷。 梨香油试验:检查通风机舱、食品储藏舱和厨房等舱室 方法:将梨香油放人舱内,密闭舱室,看在舱外是否能闻到梨香 油挥发的香气, 以检查其门和窗等的密闭性是否满足要求。
船舶建造工艺流程

工艺流程1.1 工艺流程分段大合拢G3、S5图5-1 造船生产工艺流程图 主要工序说明:1、预处理:将外购的钢材通过吊车运至预处理线的输送辊道上,通过辊道送入封闭式预处理线进行抛丸除锈,除锈后通过辊道送入封闭式喷漆室喷防锈漆。
预处理线旁设有1个油漆房,通过管道将油漆吸入调漆罐内,利用搅拌设备对油漆进行调配,再通过气泵将油漆从喷漆室的顶部喷嘴喷到钢板上进行防锈处理,喷涂后自动烘干固化。
预处理工序会产生废钢丸、废油漆桶、废漆渣、抛丸废气和喷涂废气。
2、号料:根据设计需要,通过等离子切割机、火焰切割机等切割设备对外购的钢材进行切割下料。
该工序会产生废钢材,火焰切割会产生烟尘。
3、成型加工:用油压机、肋骨撑弯机等设备把钢板和型材加工成一定的形状。
4、部件焊接:将数个零件安图纸要求组装焊接成一个部件。
5、火工矫正:以天然气为热源,用火焰喷枪对钢材需要矫正的部位进行加热,利用钢材的塑性、热胀冷缩的特性,以外力或内应力作用迫使钢材的反变形,消除钢材的弯曲、翘曲、凹凸不平等缺陷,以达到矫正之目的。
矫正后自然冷却。
6、拼板上船台组装:船体通过船台滑道由纵向重力方式下水。
下水后进行船体舾装和各种机械设备的安装和调试工作。
在船舶试航时要注入压舱水。
有焊接烟尘、废焊条、焊渣、废机油等污染环节。
7、分段舾装焊接:在船体内安装设备、组件,完成整船的组装工作,并对船体进行试航。
该工序会产生焊接烟尘、废焊条、焊渣。
8、抛丸除锈:在专用的船体分段抛丸房内,在全封闭状态下高压空气完成抛丸除锈工作。
钢丸通过输送机进入集丸斗,再通过丸阀(抛丸时,丸阀打开,保证钢丸往复循环使用)进入丸罐,丸罐连有压缩空气管道和带有丸管的喷枪,操作人员身穿抛丸服,手持喷枪,对工件的焊缝进行抛丸,抛丸时,将房门关闭,使抛丸房处于封闭状态,使得抛丸处的平均粗糙度为25-50um(使用粗糙度仪测量平面取平均值),以便于油漆的附着;抛丸后用压缩空气吹清死角钢丸。
船舶建造工艺_现代造船模式
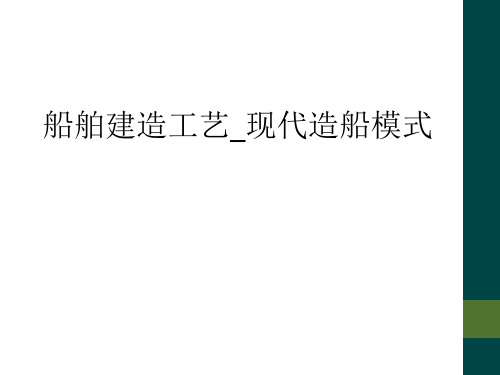
1、中间产品导向型的作业分解 原理(简称产品制造原理)
该原理按最终产品形成的制造级,以中间产品的形式对其进行作业分解和组合
中间产品是指生产的作业单元,是对最终产品进行作业任务分解的一个组成部分,也是逐级 形成最终产品的组成部分
中间产品的“产品特征”
有特定的“产品”作业任务,而且其作业任务并非由单一工种完成 有明确的“产品”质量(尺寸精度)指标 有完成“产品”作业任务所需的全部生产资源(含人、财、物),或称生产任务包
应用成组技术建立起来的现代造船模式,实际上是将船舶建造作为一个大系统,对其分解为壳、舾、 涂三种作业系统,再按区域/类型/阶段逐一分类成组而形成了各类作业的子系统
复杂造船生产作业系统示意图
对于极为复杂的生产作业系统,需要从组织“系统”的角度处理好各作业系统之间以及系统内各子系统 之间的各种相关问题,才能有效、合理地组织生产
模式特点 产品作业任务的分解和组合,除按区域/类型/阶段的分解原则和组合方式外,更体现船体建造、舾装、
涂装三大作业系统的相互结合 船舶设计、制造工艺与生产管理一体化,壳、舾、涂作业一体化 生产管理体制是按区域组织的复合专业、复合工种体制
现代造船模式的造船工艺流程见图所示
三、造船模式两大类别的特征
两类造船模式特征简要归纳如下
对比项目
传统造船模式
建模特征
系统导向型 (按功能/系统/专业)
现代造船模式
产品导向型 (按区域/阶段/类型)
设计方式
按施工设计、分别由工艺、计划、生产等部 门分专业,按系统进行工艺设计;设计、工 艺、管理三者分离
按详细设计由生产设计部门集中进行区域性 设计;设计、工艺、管理融为一体
2、相似性原理
产品作业任务分解成门类繁多的中间产品 按作业相似特性,遵循一定准则进行分类成组,以使用形同的施工处理方法扩大中间产品的成 组批量,以尽力批量性的流水定位,或流水定员的生产作业体系
造船流程

船海讲坛】图解造船系列(1)造船工艺流程简介2015-06-26船海人一、造船生产管理模式得演变由焊接代替铆接建造钢质船,造船生产经历了从传统造船向现代造船得演变,主要推动力就是造船技术得发展。
传统造船分两个阶段:1、常规得船体建造与舾装阶段。
在固定得造船设施上先安装龙骨系统、再安装肋骨框、最后装配外板系统等。
2、由于焊接技术得引进,船体实行分段建造;舾装分为两个阶段:分段舾装与船上舾装,即开展予舾装。
现代造船又历经以下阶段:3、由于成组技术得引进,船体实行分道建造;舾装分为三个阶段:单元舾装、分段舾装与船上舾装,即开展区域舾装。
4、由于船体建造与舾装、涂装相互结合组织,实现“壳舾涂一体化总装造船”。
5、随着造船技术得不断发展,精益造船、标准造船、数字造船、绿色造船将成为船厂得努力方向。
目前国内主要船厂一般处于三级向四级过渡阶段;国内先进船厂已达到四级水平;而象上海外高桥船厂、江南长兴岛造船基地明确提出将精益造船、标准造船、数字造船、绿色造船作为发展目标。
二、船舶建造工艺流程(一)现代造船工艺流程如下简图。
(二)船舶建造工艺流程层次划分依据1、生产大节点开工——上船台(铺底)——下水(出坞)——航行试验——完工交船生产大节点在工艺流程中就是某工艺阶段得开工期(或上一个节点得完工期),工艺阶段一般说就是两个节点间得施工期。
生产大节点得期限就是编制与执行生产计划得基点,框定了船舶建造各工艺阶段得节拍与生产周期;从经营工作瞧,节点得完成日也就是船东向船厂分期付款得交割日。
开工仪式上船台仪式下水仪式散货船试航交船命名(并不意味着交船)2、工艺阶段钢材预处理——号料加工——零、部件装配——分段装焊——船台装焊(合拢)——拉线镗孔——船舶下水——发电机动车——主机动车——系泊试验——航海试验——完工交船3、以上工艺阶段还可以进一步进行分解。
4、需要说明得就是以上工艺阶段就是按船舶建造形象进度划分得,现代造船工艺流程就是并行工程,即船体建造与舾装作业就是并行分道组织,涂装作业安排在分道生产线得两个小阶段之间,船体与舾装分道生产线在各阶段接续地汇入壳舾涂一体化生产流程。
- 1、下载文档前请自行甄别文档内容的完整性,平台不提供额外的编辑、内容补充、找答案等附加服务。
- 2、"仅部分预览"的文档,不可在线预览部分如存在完整性等问题,可反馈申请退款(可完整预览的文档不适用该条件!)。
- 3、如文档侵犯您的权益,请联系客服反馈,我们会尽快为您处理(人工客服工作时间:9:00-18:30)。
船舶建造流程一、船体放样1.线形放样:分手工放样和机器(计算机)放样,手工放样一般为1:1比例,样台需占用极大面积,需要较大的人力物力,目前较少采用;机器放样又称数学放样,依靠先进技术软件对船体进行放样,数学放样精确性较高,且不占用场地和人力,目前较为广泛的采用机器放样。
2.结构放样、展开:对各结构进行放样、展开,绘制相应的加工样板、样棒。
3.下料草图:绘制相应的下料草图。
二、船体钢材预处理:对钢材表面进行预处理,消除应力。
1.钢材矫正:一般为机械方法,即采用多辊矫夹机、液压机、型钢矫直机等。
2.表面清理:a.机械除锈法,如抛丸除锈法喷丸除锈法等,目前较为广泛采用;b.酸洗除锈法,也叫化学除锈,利用化学反应;c.手工除锈法,用鎯头等工具敲击除锈三、构件加工1.边缘加工:剪切、切割等;2.冷热加工:消除应力、变形等;3.成型加工:油压床、肋骨冷弯机等。
四、船体装配:船体(部件)装配,把各种构件组合拼接成为各种我们所需的空间形状。
五、船体焊接:把装配后的空间形状通过焊接使之成为永久不可分割的一个整体。
六、密性试验:各类密性试验,如着色试验、超声波、X光等。
七、船舶下水:基本成形后下水,设计流水线以下的所有体积均为浸水体积。
1.重力下水:一般方式为船台下水,靠船舶自重及滑动速度下水;2.浮力下水:一般形式为船坞;3.机器下水:适用于中小型船舶,通过机器设备拖拉或吊下水。
八、船舶舾装:全面开展舾装系统、系泊系统、机装、电装、管装等方面的工作。
九、船舶试验:系泊试验、倾斜试验,试航(全面测试船舶各项性能)。
十、交船验收。
~~~~~~~~~~~~~~~~~~~~~~~~~~~~~~~~~~~~~~~~~~~~~~~~~~~~~~~~~~~~~~~~~~~~~~船舶建造工艺流程简要介绍本讲座从管理者的角度,按照“壳舾涂一体化总装造船”现代造船管理模式的要求,结合我国船厂的探索实践,介绍船舶建造在各工艺阶段的组织方式、应注意的问题,同时提供对施工状态的评价标准。
一、造船生产管理模式的演变由焊接代替铆接建造钢质船,造船生产经历了从传统造船向现代造船的演变,主要推动力是造船技术的发展。
传统造船分两个阶段:1、常规的船体建造和舾装阶段。
在固定的造船设施按照先安装龙骨系统、再安装肋骨框、最后装配外板系统等。
2.由于焊接技术的引进,船体实行分段建造;舾装分为两个阶段:分段舾装和船上舾装,即开展予舾装。
现代造船又历经以下阶段:3、由于成组技术的引进,船体实行分道建造;舾装分为三个阶段:单元舾装、分段舾装和船上舾装,即开展区域舾装。
4、由于船体建造和舾装、涂装相互结合组织,实现“壳舾涂一体化总装造船”。
5、随着造船技术的不断发展,精益造船、标准造船、数字造船、绿色造船将成为船厂的努力方向。
目前国主要船厂一般处于三级向四级过渡阶段;国先进船厂已达到四级水平;外高桥船厂、建设中的江南长兴岛造船基地明确提出将精益造船、标准造船、数字造船、绿色造船作为发展目标。
二、现代造船生产管理模式的特征1、船体分道建造法。
根据成组技术“族制造”的原理制造船体零件、部件和分段,按工艺流程组建生产线。
2、抛弃了舾装是船体建造后续作业这一旧概念,以精确划分的区域和阶段(单元舾装、分段舾装和船上舾装)控制舾装。
3、实行“管件族制造”,以有效手段制造多品种、小批量产品,获得生产线生产效益。
4、采用产品导向型工程分解。
把船舶划分为不同级别的中间产品,幷协调的组织分道生产和集成。
三、船舶建造工艺流程现代造船工艺流程如下简图:船舶建造工艺流程层次上的划分依据为:1、生产大节点:开工——上船台(铺底)——下水(出坞)——航海试验——完工交船生产大节点在工艺流程中是某工艺阶段的开工期(或上一个节点的完工期),工艺阶段一般说是两个节点间的施工期。
生产大节点的期限是编制和执行生产计划的基点,框定了船舶建造各工艺阶段的节拍和生产周期;从经营工作看,节点的完成日也是船东向船厂分期付款的交割日。
2、工艺阶段:钢材予处理——号料加工——零、部件装配——分段装焊——船台装焊(合拢)——拉线镗孔——船舶下水——发电机动车——主机动车——系泊试验——航海试验——完工交船3、以上工艺阶段还可以进一步进行分解。
4、需要说明的是以上工艺阶段是按船舶建造形象进度划分的,现代造船工艺流程是幷行工程,即船体建造与舾装作业是幷行分道组织,涂装作业安排在分道生产线的两个小阶段之间,船体与舾装分道生产线在各阶段接续地汇入壳舾涂一体化生产流程。
四、船舶建造的前期策划船舶设计建造是一项复杂的系统工程,在开工前船厂必须组织前期策划,一是要扫清技术障碍;二是要解决施工难点。
对设计部门的要求:1、必须吃透“技术说明书”(设计规格书)。
技术说明书是船东提出幷经双方技术谈判,以相应国际规及公约为约束的船舶设计建造的技术要求。
船厂在新船型特别是高附加值船舶的承接中必须慎重对待:必须搞清重要设备运行的采用标准情况、关键技术的工艺条件要求,特别是要排查出技术说明书中暗藏的技术障碍(不排除某些船东存有恶意意图),否则冒然施工将会给船厂带来灾难性的后果。
对此,各主要船厂都有过深刻的教训。
如江南厂建造的自卸船、广船建造的客滚船、厂建造的大型滚装船、三用工作船等。
因此对新船型的开发必须组织予研,进行充分的技术储备。
2、对设计工作的组织。
船舶设计工作分三阶段组织进行——初步设计、详细设计、生产设计。
初步设计:是从收到船东技术任务书或询价开始,进行船舶总体方案的设计。
提供出设计规格说明书、总布置图、舯剖面图、机舱布置图、主要设备厂商表等。
详细设计:在初步设计基础上,通过对各个具体技术专业项目,进行系统原理设计计算,绘制关键图纸,解决设计中的技术问题,最终确定船舶全部技术性能、船体结构、重要材料设备选型和订货要求等。
生产设计:是在详细设计送审图完成基础上,按工艺阶段、施工区域和组装单元,绘制记入各种工艺技术指示和各种管理数据的工作图、管理表以及提供生产信息文件的设计。
简言之:初步设计——描绘出将建造一艘什么样的船;详细设计——确定各专业各系统如何配置与运行;生产设计——指示怎样合理地建造这艘船。
目前,国各主要船厂都取得了国家级技术中心资格认证,大船重工船舶及海洋工程研究所设有开发室、船体、船装、机装、电装、居装等综合设计室以及工艺、海工、军工等专业设计室,已开发幷建造了化学品船、成品油轮、原油轮、散货船、多用途船等系列船型,对新船型首制船,如VLCC、大型集装箱船等,一般采用与国外所联合设计方式,所有生产设计任务全部由船厂承担。
因此需要尽快地充实和培养自己的生产设计队伍。
生产设计是施工设计,必须密切结合工厂的工艺流程、设施设备能力、工艺水平甚至工艺习惯,外委设计将不可避免出现修改。
船舶设计的全过程延续的时间很长,影响设计进度的突出问题是:详细设计的主要图纸和技术文件需要船东、船检(船级社)审查认可,而后进行退审修改,此时船舶已经开工,生产设计承受着施工供图需求的压力,由于准备不充分,在O版图施工情况下容易出现差错。
解决的途径是努力将详细设计与生产设计由串联式的接续组织,尽可能在一定阶段形成幷联式的交叉组织。
在设计部门组织机构设置中,有的船厂试尝将详细设计与生产设计人员编在一个综合设计室;但从努力方向看,应该开发利用计算机工作站的功能,在输入详细设计可靠数据和图形的基础上,通过三维设计、干涉检查,直接生成生产设计数据和图形。
3、设计审查要加强对设备材料的经济性选择。
详细设计一经确定,全船80%的成本已经固化(其中设备材料费用占全船总成本的65%左右),在人工费、专用费项目中降低成本的空间很小。
据资料统计,国船厂与国外先进船厂建造的同类船舶相比,设备裕量和材料消耗量均高出10%。
因此在主要设备、材料厂商表围,对重要设备、大宗物资必须坚持集中订货、定点订货;对金额高的常用消耗性材料,争取采用寄售或赊销方式。
对生产管理部门的要求:1、根据生产线表的要求,要详细、准确地编制《船舶生产技术准备综合日程表》,包括设备纳期表、设计出图计划等,幷进行跟踪、调度、检查、考核。
生产技术准备是船厂组织船舶建造重要的管理体系,在调度为主要管理手段时期,围绕出图、供货、配套等项目常常纠缠不清,牵扯了生产管理者极大的精力。
目前各船厂生产技术准备状况已有了很大改观:一是建立了拉动式需求计划管理体系;二是将各船只生产技术准备的职责落实到项目组;三是应用了信息技术:设计出图进度及状况、物资订货及到货情况、集配件的需求缺损件的补充等都在网上传输幷设有予警提示。
2、根据现代造船“设计、生产、管理一体化”的要求,从合同签约开始生产管理部门就应参与设计工作,如依据影响船厂生产率相关的制约因素和条件,提出分段划分意见等,供设绘各布置图参用。
在船舶设计过程中,按造船管理规程的要求,将分阶段召开A、B、C、D 等会议,其目的都是以合理和方便施工为宗旨,将管理要求和设计意图融合起来。
为此,在合同生效三个月,生产管理部门要编制出《建造方针》,该方针是指导船舶建造的纲领性文件,主要容有:(1)合同概要。
(2)建造船舶的主要技术参数和主要物量。
(3)建造方法。
包括分段划分原则;重要分段的结构特征及尺寸;分段重量的控制围;钢板规格控制;总段装配围;上层建筑整体吊装的重量计算;分段予舾装围和要求;场地分配及面积计算;船台建造方法和定位分段的确定等。
(4)新工艺新技术的应用和实施围及要求。
(5)船舶建造主要建造计划线表。
(6)质量、成本、资金等管理要求。
建造方针完成之后,船厂还要编制出《施工要领》,主要说明基本的工艺步骤、技术要点和基本的施工方法。
策划合理、容规,幷体现出很高的施工要求,如开展予舾装:“除合拢缝处的货舱区的铁舾、管系焊接件外,其它所有均应在分段阶段安装”。
3、为了在船舶建造过程中贯彻建造方针,避免流于形式缺乏约束,近年来主要船厂相继开展了一项叫做“纸上模拟造船”的活动,取得了应有的成效:在船舶开工前,船厂组织设计、工艺、生产及生产管理等主管人员,对照设计说明书,从剖析的角度,按船舶建造流程逐项找出影响设计建造的关键点,从合理性可行性出发,研究确定建造方法和技术手段,也就是说研究确定了对关键项目的予案。
从实践情况看,如果“纸上模拟造船”能够走得通,幷将具体要求落实在《建造方针》中,基本上扫除了建造中将遇到技术障碍和施工难点。
五、船舶建造过程的控制(一)钢料加工阶段钢料加工过程:钢材备料——钢材予处理线(矫平、喷砂除锈、底漆)——放样号料——构件边缘加工(切割、加工焊接坡口)——构件成型加工(非平直构件加工成应有曲度)——船体零部件装配(平面接板、框架组立)。
应关注的问题:1、钢料供应。
船厂是钢材消耗大户,从产业关系看应该与钢厂建立利益共享的战略伙伴关系。