部件标准化流程
设备安装调试标准化作业流程
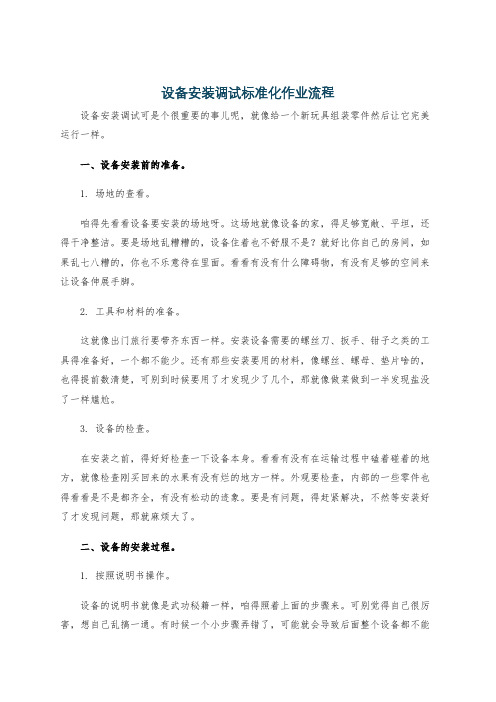
设备安装调试标准化作业流程设备安装调试可是个很重要的事儿呢,就像给一个新玩具组装零件然后让它完美运行一样。
一、设备安装前的准备。
1. 场地的查看。
咱得先看看设备要安装的场地呀。
这场地就像设备的家,得足够宽敞、平坦,还得干净整洁。
要是场地乱糟糟的,设备住着也不舒服不是?就好比你自己的房间,如果乱七八糟的,你也不乐意待在里面。
看看有没有什么障碍物,有没有足够的空间来让设备伸展手脚。
2. 工具和材料的准备。
这就像出门旅行要带齐东西一样。
安装设备需要的螺丝刀、扳手、钳子之类的工具得准备好,一个都不能少。
还有那些安装要用的材料,像螺丝、螺母、垫片啥的,也得提前数清楚,可别到时候要用了才发现少了几个,那就像做菜做到一半发现盐没了一样尴尬。
3. 设备的检查。
在安装之前,得好好检查一下设备本身。
看看有没有在运输过程中磕着碰着的地方,就像检查刚买回来的水果有没有烂的地方一样。
外观要检查,内部的一些零件也得看看是不是都齐全,有没有松动的迹象。
要是有问题,得赶紧解决,不然等安装好了才发现问题,那就麻烦大了。
二、设备的安装过程。
1. 按照说明书操作。
设备的说明书就像是武功秘籍一样,咱得照着上面的步骤来。
可别觉得自己很厉害,想自己乱搞一通。
有时候一个小步骤弄错了,可能就会导致后面整个设备都不能正常运行。
就像搭积木,你要是第一步就搭错了,后面肯定会歪歪扭扭的。
把设备的各个部件按照说明书上的指示,一个一个稳稳地安装好,该拧紧的螺丝一定要拧紧,可别松松垮垮的,不然设备运行起来就会晃悠,就像没系紧鞋带走路一样。
2. 线路的连接。
如果设备有线路的话,这可就要小心再小心了。
线路连接就像给设备接血管一样,接错了可不得了。
要仔细看清楚线路的标识,哪根线该接到哪里,千万不能马虎。
而且要把线路整理好,不能乱糟糟的缠在一起,要是缠在一起,就像一团乱麻,不仅不美观,还可能会有安全隐患呢。
三、设备的调试。
1. 初步调试。
设备安装好了之后,就可以开始初步调试啦。
ppap报告
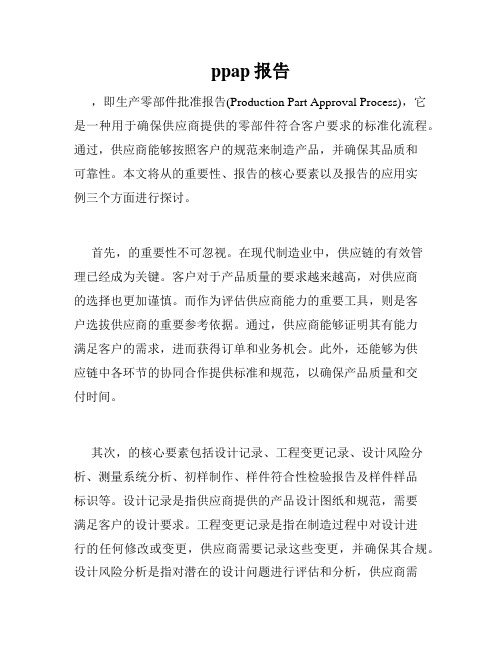
ppap报告,即生产零部件批准报告(Production Part Approval Process),它是一种用于确保供应商提供的零部件符合客户要求的标准化流程。
通过,供应商能够按照客户的规范来制造产品,并确保其品质和可靠性。
本文将从的重要性、报告的核心要素以及报告的应用实例三个方面进行探讨。
首先,的重要性不可忽视。
在现代制造业中,供应链的有效管理已经成为关键。
客户对于产品质量的要求越来越高,对供应商的选择也更加谨慎。
而作为评估供应商能力的重要工具,则是客户选拔供应商的重要参考依据。
通过,供应商能够证明其有能力满足客户的需求,进而获得订单和业务机会。
此外,还能够为供应链中各环节的协同合作提供标准和规范,以确保产品质量和交付时间。
其次,的核心要素包括设计记录、工程变更记录、设计风险分析、测量系统分析、初样制作、样件符合性检验报告及样件样品标识等。
设计记录是指供应商提供的产品设计图纸和规范,需要满足客户的设计要求。
工程变更记录是指在制造过程中对设计进行的任何修改或变更,供应商需要记录这些变更,并确保其合规。
设计风险分析是指对潜在的设计问题进行评估和分析,供应商需要识别并降低这些风险。
测量系统分析是指对用于测量的设备和工具进行评估,以确保测量结果准确可靠。
初样制作是指供应商按照客户的要求制作出第一批样品,并交付给客户进行评估和确认。
样件符合性检验报告是指供应商对样品进行全面的检验和测量,确保其符合设计要求。
最后,样件样品标识是为了标识样品的唯一性和追踪性。
最后,我们来看一下的应用实例。
以汽车行业为例,汽车制造商通常会与多家供应商合作,以满足复杂的供应链。
这些供应商可能分别负责汽车的发动机、座椅、悬挂系统等部件的制造。
在这种情况下,汽车制造商需要对每个供应商的能力进行评估和验证。
于是,就成为了汽车制造商与供应商之间的重要沟通工具。
供应商通过提交,证明其产品可以满足汽车制造商的质量和性能需求。
同时,汽车制造商根据的内容,对供应商的能力和合作意愿进行综合评估,以决定是否选择该供应商。
轨道交通设备维修中的维修工艺和标准化流程

轨道交通设备维修中的维修工艺和标准化流程随着现代城市快速发展,轨道交通作为一种高效、环保的公共交通方式扮演着重要的角色。
然而,频繁的使用和长期的运营不可避免地导致轨道交通设备出现故障和损坏,因此维修工艺和标准化流程对于保障轨道交通的安全和可靠性至关重要。
本文将探讨轨道交通设备维修中的维修工艺和标准化流程,并分析其作用与重要性。
轨道交通设备的维修工艺是指在发生故障或损坏时,通过采取一系列有条不紊的步骤进行修复和恢复正常运行的过程。
它包括故障排查、维修计划制定、维修操作以及维修后的测试与验证等环节。
首先,故障排查是维修工艺的关键环节之一。
技术人员通过仔细观察、询问乘客和检查设备等方式,确定故障的具体原因。
其次,维修计划的制定是维修工艺的重要组成部分。
在维修计划中,需要明确维修所需的设备、人员和时间,并制定详细的工作步骤。
维修操作阶段是维修工艺的核心环节,涉及到设备的拆卸、更换零部件、修复损坏部分等具体操作。
最后,在维修完成后,需要进行测试与验证,确保设备的正常运行。
维修工艺依靠各个环节的有机衔接,最终实现了轨道交通设备的维修与恢复。
标准化流程在轨道交通设备维修中同样起着至关重要的作用。
标准化流程指的是制定统一的规范和标准,确保维修工作的一致性和标准化。
标准化流程可以从多个方面提高维修效率并保证质量。
首先,它提供了一套具体的操作规范,使得在维修过程中能够按照同样的标准进行操作,减少了人为因素对维修结果的影响。
其次,标准化流程可以提供紧急情况下的应急预案,避免在处理突发事件时出现混乱和延误。
此外,标准化流程还可以提供清晰的责任划分,明确各个岗位的职责和任务,从而优化协同合作,提高工作效率。
最后,在维修过程中,标准化流程还可以提供数据收集和分析,用于维修质量的评估和改进。
维修工艺和标准化流程在轨道交通设备维修中的重要性不言而喻。
首先,它们可以最大程度地提高维修工作的效率。
采用正确的维修工艺和标准化流程,可以快速定位故障和损坏,并且能够提供相应的维修方案,避免了长时间的维修周期和资源的浪费。
产品标准化流程

产品标准化流程在当今全球化的市场环境中,产品标准化流程已成为企业成功的关键要素之一。
标准化流程对于企业来说是非常重要的,不仅能够提高产品的质量和一致性,还能够降低成本并加快产品的上市时间。
本文将详细介绍产品标准化流程,并探讨其在企业中的重要性和应用。
什么是产品标准化流程?产品标准化流程是指通过制定标准规范和流程,使得企业的产品在设计、生产、测试和销售等各个环节中具备一致性和高质量。
标准化流程能够确保产品达到预期的性能和功能,并使得产品能够满足客户的需求和期望。
产品标准化流程通常包括以下几个关键步骤:1.需求分析需求分析是产品标准化的第一步。
在这一阶段,企业需要了解客户的需求和市场趋势,以确定产品的功能和性能要求。
通过深入了解客户的需求,企业能够为产品设计和开发提供明确的目标和方向。
2.产品设计和开发产品设计和开发是产品标准化流程中最关键的环节之一。
在这一阶段,企业需要将客户的需求转化为产品设计和规范。
设计师和工程师需要合作,制定详细的产品规格和工艺流程,并确保产品的功能和性能达到标准要求。
3.原材料采购和供应链管理原材料采购和供应链管理是产品标准化流程中不可忽视的一环。
企业需要建立稳定的供应链,确保原材料的质量和供应的稳定性。
同时,企业还需要与供应商进行有效的合作和沟通,以确保原材料的及时交付和合理价格。
4.生产和制造生产和制造是产品标准化流程中最核心的环节之一。
企业需要建立高效的生产线和制造流程,确保产品能够按时、按量生产。
在生产过程中,企业需要进行严格的品质控制和质量检测,以确保产品符合标准要求。
5.产品测试和验证产品测试和验证是产品标准化流程中的重要环节。
企业需要对产品进行全面的测试和验证,以确保产品的性能和功能符合标准要求。
测试和验证可以包括物理测试、性能测试、安全性测试等多个方面。
6.市场推广和销售市场推广和销售是产品标准化流程中的最后一环。
一旦产品通过了测试和验证阶段,企业需要进行市场推广和销售。
设备开发标准化流程方案1
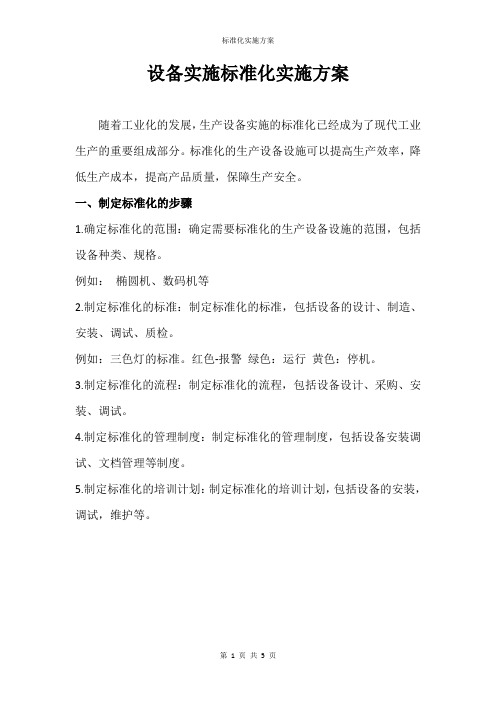
设备实施标准化实施方案随着工业化的发展,生产设备实施的标准化已经成为了现代工业生产的重要组成部分。
标准化的生产设备设施可以提高生产效率,降低生产成本,提高产品质量,保障生产安全。
一、制定标准化的步骤1.确定标准化的范围:确定需要标准化的生产设备设施的范围,包括设备种类、规格。
例如:椭圆机、数码机等2.制定标准化的标准:制定标准化的标准,包括设备的设计、制造、安装、调试、质检。
例如:三色灯的标准。
红色-报警绿色:运行黄色:停机。
3.制定标准化的流程:制定标准化的流程,包括设备设计、采购、安装、调试。
4.制定标准化的管理制度:制定标准化的管理制度,包括设备安装调试、文档管理等制度。
5.制定标准化的培训计划:制定标准化的培训计划,包括设备的安装,调试,维护等。
二、标准化的实施1.项目立项,由项目经理制定出机械设备设计生产横道图跟踪项目进度2.设备的设计开发由设计部安排机械工程师进行机构设计,作出机器装配图、零件图(零件标注按公司制定的标准)、配件并列出加工零件清单和标准件请购单,动作说明书。
由设计部安排电气工程师对设备的电路图、PLC程序进行设计并出电气BOM清单(PLC程序按照公司电气标准进行设计).3.设计审核由设计、采购、生产人员组成审核组,对所设计出的图纸进行审核,审核内容包括:1)机器结构配合是否合理:功能性(能力和精度)、稳定性、安全性、人性化(操作的便利性)和外观性。
2)所设计机器生产效率是否符合客户需求。
3)机器造价。
4)各部分机构应简单易于调试、维修。
5)各部分零件应尽量简单易于加工。
6)各执行元件选用是否合理。
7)上传设计文件(按照公司文件管理标准方式进行)4.零件加工及标准件采购1)零件加工部零件图进行机器零件加工(零件加工必须严格按照零件图上所示,零件精度,加工工艺进行加工,保证零件精度及零件加工工艺)。
如发现问题需要变更必要由设计人员进行设计文件变更后方可进行修改。
2)采购人员按照标准件清单,联系供应商进行标准件采购5.加工零件及标准件检验入库检验人员按照零件图及标准件清单,检验加工零件的尺寸精度,加工工艺,标准件的型号、安装尺寸进行检验,合格后交由仓管人员入库6.设备组装1)由装配部安排人员进行机器组装调试,装配人员按照加工零件清单及标准件清单,到仓库领取加工零件及标准件。
整木定制标准化工作流程
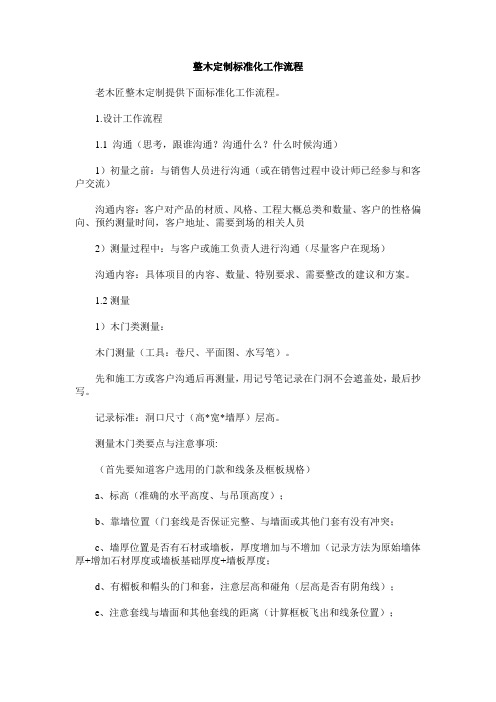
整木定制标准化工作流程老木匠整木定制提供下面标准化工作流程。
1.设计工作流程1.1 沟通(思考,跟谁沟通?沟通什么?什么时候沟通)1)初量之前:与销售人员进行沟通(或在销售过程中设计师已经参与和客户交流)沟通内容:客户对产品的材质、风格、工程大概总类和数量、客户的性格偏向、预约测量时间,客户地址、需要到场的相关人员2)测量过程中:与客户或施工负责人进行沟通(尽量客户在现场)沟通内容:具体项目的内容、数量、特别要求、需要整改的建议和方案。
1.2测量1)木门类测量:木门测量(工具:卷尺、平面图、水写笔)。
先和施工方或客户沟通后再测量,用记号笔记录在门洞不会遮盖处,最后抄写。
记录标准:洞口尺寸(高*宽*墙厚)层高。
测量木门类要点与注意事项:(首先要知道客户选用的门款和线条及框板规格)a、标高(准确的水平高度、与吊顶高度);b、靠墙位置(门套线是否保证完整、与墙面或其他门套有没有冲突;c、墙厚位置是否有石材或墙板,厚度增加与不增加(记录方法为原始墙体厚+增加石材厚度或墙板基础厚度+墙板厚度;d、有楣板和帽头的门和套,注意层高和碰角(层高是否有阴角线);e、注意套线与墙面和其他套线的距离(计算框板飞出和线条位置);f、注意洞口每个面的尺寸误差;g、注意客户对产品尺寸的特殊要求(如见光尺寸);h、要注明开启方向(如玻璃门、阴阳色门);I、窗套测量特别注意户外窗的合页位置和墙厚;j、移门如果要求轨道盒不往下吊,注意计算门洞高度;k、隐形门、隐形移门外挂移门注意安装方法;L、注意垭口造型需要的门洞尺寸与形状。
2)墙板类测量;墙板类测量(工具:卷尺、电子测量仪、平面图、水写笔)先将尺寸记录在墙面显眼处,最后抄写记录标准:小尺寸和总尺寸、特殊形状在墙面画好节点测量墙板类要点与注意事项a、标高(准确的水平高度、与吊顶高度)b、整个空间内部所有尺寸均要记录(如:吊顶边宽、电源位置、洞口位置等)c、沟通地面材料和踢脚线材料(特别容易忽略的踢脚线)d、注意吊顶的中心点位置e、注意每层楼的层高相互关系f、沟通每个墙面的具体用材(如卫生间和有些公共区域用的石材)g、注意墙角阴角线用的材料h、注意基础施工需要改动的位置I、注意门洞或窗洞的最终位置j、注意阳角包柱的尺寸测量方法3)柜体类测量;柜类测量(工具:卷尺、平面图、水写笔)a、橱柜和洗面柜注意第一次测量要减去石材或墙砖的厚度、注意门套的位置、注意进出水位;b、地暖分水器位、注意吊顶位置与高度、注意排烟管位置、电源插座位置c、衣帽间衣柜测量需注意吊顶高度及位置,灯源或插座位置(特别体系门窗套距离)d、酒柜需要注意灯源和水位是否预留、4)楼梯类测量;楼梯类测量(工具:卷尺、水平仪、放样模板、水写笔)a、直角楼梯:步高、步宽、步长、转角和平台宽度;b、旋转楼梯:步高、步宽、步长、转角和平台宽度、弧度放样、扭弯敲扁铁放样;c、整体楼梯:楼梯间长、宽、高、梁高、平台高度;d、楼梯踏步第一跑调整为单数、没跑楼梯第一步高度不高于150;e、注意三角板和踢脚线;f、注意墙面是否有木饰面或者其他材料。
装配式桥梁部件的标准化、信息化预制场施工工法(2)

装配式桥梁部件的标准化、信息化预制场施工工法一、前言装配式桥梁部件的标准化和信息化预制场施工工法是指在建造桥梁时采用预制标准化的部件,通过在预制场进行组装和施工,以提高施工效率和桥梁质量的一种施工方法。
本文将对该工法的特点、适应范围、工艺原理、施工工艺、劳动组织、机具设备、质量控制、安全措施、经济技术分析以及工程实例进行详细介绍。
二、工法特点装配式桥梁部件的标准化、信息化预制场施工工法具有以下几个特点:1. 标准化:采用模块化设计思想,桥梁部件按照标准规格进行预制,具有一定的通用性,提高了部件的生产效率和标准化水平。
2. 信息化:通过使用计算机辅助设计和工厂化生产管理系统,实现了桥梁设计和预制施工信息的管理和共享,提高了工作效率和质量控制水平。
3. 预制场施工:将桥梁部件在预制场进行组装和施工,减少了现场施工时间和对交通的影响,同时也提高了构件的一致性和施工质量。
4. 施工周期短:采用装配式工法可以同时进行多个施工工序,缩短了施工周期,加快了项目进度。
5. 质量可控:在预制场进行施工,条件相对稳定,可以更好地控制施工质量,提高了整体桥梁工程的质量。
6. 环保节能:预制场生产可精确控制原材料和能源的消耗,减少了施工现场的噪音、粉尘和废弃物产生,符合环保节能要求。
工工法适用于以下情况:1. 桥梁重复性较高:桥梁设计中存在较多重复使用的部件,并且构件规格较为标准化。
2. 施工环境复杂:施工现场交通条件复杂,施工期限较短,需要减少施工对交通的影响。
3. 施工质量要求高:对桥梁的施工质量要求较高,需要通过标准化生产和预制场施工来提高施工质量控制水平。
4. 施工效率要求高:项目进度紧迫,需要缩短施工周期,加快桥梁的建设速度。
四、工艺原理装配式桥梁部件的标准化和信息化预制场施工工法的工艺原理主要包括施工工法与实际工程之间的联系以及采取的技术措施。
1. 施工工法与实际工程之间的联系:根据实际项目需求和设计要求,确定适用的施工工法,并与实际工程进行对接和调整,确保施工的准确性和可行性。
工器具保养标准化流程

工器具保养标准化流程1.检查工具表面有无损坏或划伤。
Check for any damage or scratches on the surface of the tools.2.清洁工具表面,确保无灰尘或杂物。
Clean the surface of the tools to ensure there is no dust or debris.3.用清洁剂擦拭工具表面,确保干净。
Wipe the surface of the tools with a cleaner to ensure it is clean.4.检查工具的运行状态,确保工具正常工作。
Check the operation of the tools to ensure they are functioning properly.5.润滑工具的关键部件,以减少磨损。
Lubricate the key components of the tools to reduce wear and tear.6.检查电动工具的电线和插头,确保没有损坏。
Inspect the power tools for damaged wires and plugs.7.使用适当的工具进行调整和校准。
Use the appropriate tools for adjustments and calibrations.8.检查手动工具的手柄和把手,确保牢固。
Inspect the handles of hand tools to ensure they are secure.9.清理及更换工具附件,以确保其正常工作。
Clean and replace tool attachments to ensure they function properly.10.检查工具箱和存储空间,确保工具整齐摆放。
Inspect toolboxes and storage spaces to ensure tools are organized.11.清洁和消毒工具,以防止细菌和病毒的传播。
- 1、下载文档前请自行甄别文档内容的完整性,平台不提供额外的编辑、内容补充、找答案等附加服务。
- 2、"仅部分预览"的文档,不可在线预览部分如存在完整性等问题,可反馈申请退款(可完整预览的文档不适用该条件!)。
- 3、如文档侵犯您的权益,请联系客服反馈,我们会尽快为您处理(人工客服工作时间:9:00-18:30)。
产品零部件标准化流程按照标准化对象分类,可以将零部件的标准化分为三类:第一类:结构的变更,即对不同结构的可进行标准化的相似零部件,在结构上进行标准化,统一为一种结构的配件,这种结构的变更根据变更的结果又可分为以原有某配件作为标准对其他配件进行变更和重新设计新的配件结构作为标准对原有配件进行变更。
这种结构的变更对产品的功能、质量有一定的影响,需要对变更后的配件进行物理性能验证,以保证标准化后配件能满足原有产品功能和质量方面的要求。
第二类:材料的变更,即对采用不同材料的可进行标准化的相似零部件,在材料方面进行标准化,统一为一种材料进行生产,此类变更对产品的质量有较大的影响,需要对变更后的配件进行全性能检验以保证标准化后配件的质量要求。
第三类:部分规格的的变更,如导管长度的标准化,此类变更对产品的质量和功能等基本无影响,只是通过统一某种规格来提高生产效率,降低生产成本,此类变更不需要对变更进行验证,只要满足变更后配件规格达到国标要求即可。
标准化流程图:1.收集产品各类配件信息各公司技术员收集公司内现有各种产品的配件信息,按照产品分类来统计各配件相关信息,包括数量,材料,规格,模具数量等基本信息,按统一格式形成分公司内配件信息汇总表,上交技术部。
2.分类整理、归纳技术部首先将各分公司技术员收集的所有配件的信息汇总,按照类别对各配件信息进行整理归纳,对同类零部件信息进行归纳汇总;然后,对同类零部件的所有图纸进行分析对比,找出各个规格的配件所存在的差异性,结合所对应产品的特性,分析其差异是否都是必须的,能否进行更换。
例:3.对可进行标准化的配件核算其标准化的效益和成本技术部对上一步分析中可以进行标准化的配件,根据根据各配件的年总需求量,单个配件所需要的原材料成本,加工成本,以及加工此类配件的模具的数量、精度等,对可进行标准化的配件从原材料成本、加工成本、换模成本等方面进行汇总,确定各标准化方案所带来的直接经济效益或成本,结合此标准化方案所带来的管理效益、质量效益等进行综合评比,以此来确定最佳的标准化方案。
例如:某类配件的A、B规格经分析可以进行标准化整合,通过以下分析确定最佳的整合方案。
4.评审确定标准化方案技术部对以上收集整理分析的结果以及初步拟定的可行性方案召集产品技术部、工艺技术部、质量部、制造部、销售部共同进行评审,综合各部门意见共同确定最终的标准化方案。
5.标准化变更设计结构变更以原有某配件作为标准统一此类配件验证用标准化配件替代其他配件对产品质量和功能的影响根据上阶段确定的标准化方案,以选择的原有某配件作为标准替代其他配件,验证此类配件代替其他配件后对该产品的质量和功能的影响是否达标。
首先由项目组成员提交验证申请,批准后由技术部进行验证,主要验证内容:标准化配件各项质量和功能指标是否满足原有配件标准;替换后配件在产品中适配性是否满足要求;对于需蘸胶组装的配件要验证蘸胶组装后及灭菌处理后抗拉力、压力等指标是否合格;产品整体性能有无变化等。
审批将上阶段的验证结果及标准化方案,上报技术部和质量部,由技术部和质量部审核,技术副总批准。
审批通过后,方可进行下阶段的验证,若审批不通过,则考虑换另一种配件作为标准配件,或是根据需求重新设计新的配件。
小批量验证审批通过后,对标准化配件进行小批量的组装生产,由于标准化配件采用的是原有某配件,只涉及部分组装工序的改变,因此在小批量试生产中,只需要验证组装过程中原先没有出现过的相关配件间的组装工艺,记录新组装方式其中的劳动强度、工作效率及因配件原因导致的不良率等临床试用将小批量生产的相关产品及时投放市场,跟踪产品在临床使用中的情况,如在运输过程中新配件脱落、与产品连接处断开等情况,临床使用中是否存在不易操作或是功能不良等问题。
以上由技术部派专门的技术员跟踪完成或是制定详细的信息采集单,由销售人员负责此类信息的收集与跟踪评审临床试用结束后,召集产品技术部、工艺技术部、质量部、销售部、制造部、相关分公司负责人共同对试生产结果进行评审,评审内容包括:在实际生产中,新设计的标准化零部件是否满足批量生产的条件;标准化配件是否有效的提升了产品的质量效益或是生产中的管理效益或是有效的降低了生产成本;以标准化配件取代其他配件的产品在实际的市场试用中是否还存在某些质量或功能性缺陷;是否在接下来开始大批量的生产。
根据评审的结果进行下一步的工作,若评审结果不可行,则终止或暂停此次变更,若需要改进,则重新确定是否继续采用原有某配件作为标准化配件,若原有配件不能满足要求则考虑重新设计新的配件作为标准化配件。
变更相应的技术文件小批量生产结果经评审通过后,工艺技术部着手变更相应的技术文件,相关生产车间更换模具,为大批量生产做准备。
需变更技术文件:产品结构图纸、模具图纸、产品物料采购单、作业指导书、工艺技术卡、BOM大批量生产相关分公司定制新的模具,模塑公司根据新的产品结构图纸和模具图纸重新制作模具或是对原有模具进行改制,生产车间根据变更后的相应的技术文件进行大批量的生产。
市场跟踪产品进行大批量生产后,工艺技术部继续保持对此类产品的市场跟踪半年至一年时间,及时收集市场中反馈的问题,持续改进。
重新设计新的配件作为标准统一此类配件确定配件各项要求整合原有此类配件各项功能性和工艺性要求,对其中的差异性指标进行分析,结合产品的整体要求,重新确定新的统一的标准或要求。
确定配件各项要求中要及时与原设计人员及时沟通,了解相关注意事项或隐性要求,确保各项因素都在考虑范围之内,避免因忽略了某项因素而导致重新确定的指标或要求出现偏差,而最终导致重新设计的配件在最后的验证或临床试用中出现问题。
重新设计配件图纸根据上阶段确定的标准和要求,重新绘制新的配件图纸。
审批将上阶段确定的配件的标准和设计的图纸,上报至技术部审批,有技术部经理审核,技术副总批准。
审批内容主要包括新的标准是否满足产品功能和质量要求,新设计图纸是否满足新标准利用实验模具制造样品审批通过后,根据新绘制和设计的图纸,利用实验模具注塑少量的样品样品检验首先对用实验模具注塑的样品进行外观检验,检验尺寸、形状、规格等是否符合设计要求;然后对样品进行拉力、应力等物理性能检验以及流量或过滤直径等功能性检验,验证样品是否满足所需配件的各项标准和要求;最后将样品与其他相关配件共同组装成为完整产品,验证样品与产品的匹配程度及产品的各项功能性、质量性指标是否合格样品评审样品检验合格后,召集产品技术部、工艺技术部、质量部对样品验证结果进行评审,各部门对新配件的各项性能指标重新进行审核,共同确定此项变更是否满足产品要求。
制定生产和检验标准样件评审通过后,由工艺技术部和质量部根据配件设计的各项指标和要求,重新制定新的配件的生产和检验标准,发往相关分公司小批量验证相关分公司根据制定的生产和检验标准对新设计的配件进行小批量的试生产,各分公司技术员及时最终生产的情况并记录生产中的各项信息,如:新配件在组装过程中的难易程度,新配件的生产效率,原材料及二次料的使用情况等,若是机组配件,则还要考察配件在机组中的适用情况,组装机是否需要重新调整等。
临床试用将小批量生产的相关产品及时投放市场,跟踪产品在临床使用中的情况,如在运输过程中新配件有无变形、开裂或是与产品连接处断开等情况,临床使用中是否存在不易操作或是功能不良等问题。
以上由技术部派专门的技术员跟踪完成或是制定详细的信息采集单,由销售人员负责此类信息的收集与跟踪评审临床试用结束后,召集产品技术部、工艺技术部、质量部、销售部、制造部、相关分公司负责人共同对试生产结果进行评审,评审内容包括:在实际生产中,新设计的标准化零部件是否满足批量生产的条件;标准化配件是否有效的提升了产品的质量效益或是生产中的管理效益或是有效的降低了生产成本;以标准化配件取代其他配件的产品在实际的市场试用中是否还存在某些质量或功能性缺陷;是否在接下来开始大批量的生产。
根据评审的结果进行下一步的工作,若评审结果不可行,则终止或暂停此次变更,若需要改进,则重新制订生产和检验标准,继续进行小批量验证。
变更相应的技术文件小批量生产结果经评审通过后,工艺技术部着手变更相应的技术文件,相关生产车间更换模具,为大批量生产做准备。
需变更技术文件:产品结构图纸、模具图纸、产品物料采购单、作业指导书、工艺技术卡、BOM大批量生产相关分公司定制新的模具,模塑公司根据新的产品结构图纸和模具图纸重新制作模具或是对原有模具进行改制,生产车间根据变更后的相应的技术文件进行大批量的生产。
市场跟踪产品进行大批量生产后,工艺技术部继续保持对此类产品的市场跟踪半年至一年时间,及时收集市场中反馈的问题,持续改进。
材料变更确定材料性能指标根据上阶段评审确定的标准化方案,若选择作为替换其他配件的标准化配件涉及材料的改变,首先要根据原有配件的相关性能确定需要更换的材料的性能指标,包括:材料的密度、透明性、柔韧性、熔点、分子结构、药溶性、抗热寒性、价格范围等开发供应商根据上阶段确定的材料性能指标,寻找可满足要求的材料,若公司内现有材料没有能满足要求的材料,则由工艺技术部会同采购部门共同开发新的材料供应商。
若公司内现有材料可满足新材料性能指标,则分析市场上可满足要求的其他材料与公司内材料的价格指标,选取最经济合理的材料作为标准化配件材料。
审批将原配件材料性能指标、经分析所确定的材料性能指标、最终确定选择的材料性能指标以及供应商资料等相关资料和新材料验证申请上报主管部门审批。
采购材料审批通过后,由采购部购置少批量实验用料,技术部对材料进行验证,检验所购材料各项性能指标是都满足要求。
(若材料是公司内原有材料,则审批通过后跳过此步骤,直接进行下阶段的验证)样品试制及检验利用原有模具或实验模具采用新材料生产相关配件,根据材料的性能指标合理调整相关的注塑工艺参数,记录最合理的工艺参数,在注塑过程中,及时记录新材料与模具的适配性(若模具不匹配则考虑重新设计模具),注塑时间,冷却时间及其他相关问题。
样件注塑完成后,对配件进行全性能检验,验证配件物理性能和化学性能是否达标,检验内容:配件的抗拉力、压力检测;配件应力检验;注塑冷却后形变量;灭菌处理后形变量;各温度条件下韧性检验;老化试验;与药液、环己酮接触条件下的化学稳定性;高温灭菌条件下有无化学反应等检验以及流量(或是过滤直径或避光性能)等功能性检验。
样品评审样件全性能检测结束后,召集产品技术部、工艺技术部、质量部共同对样件及各项检测结果,进行评审,判定新材料制造的新配件各项功能和质量性能是否达标,是否继续进行下阶段的小批量验证和临床试用。
制定生产和检验的标准样品评审通过后,根据各部门对新材料配件的相关意见和样件制作中确定的相关工艺参数以及样件检验所得的各项性能指标,由工艺技术部会同质量部,共同制定新的生产和检验标准,包括:注塑过程中的工艺参数、检验标准、原材料的使用、二次料的处理等小批量验证相关分公司根据制定的生产和检验标准对新设计的配件进行小批量的试生产,各分公司技术员及时最终生产的情况并记录生产中的各项信息,如:新材料配件在组装过程中与其他配件有无不良反应;新配件在组装过程中的难易程度,新配件的生产效率,原材料及二次料的使用情况等,若是机组配件,则还要考察配件在机组中的适用情况,组装机是否需要重新调整等。