薄膜组件封装工艺简介
薄膜太阳能电池封装工艺简介

薄膜太阳能电池封装工艺简介概述薄膜太阳能电池作为一种高效、轻薄、柔性的太阳能电池,已经在能源领域得到广泛应用。
其中,薄膜太阳能电池封装工艺是整个生产过程中非常重要的一部分,它是将薄膜太阳能电池片与封装材料合理结合,以保护电池片,并提高电池的稳定性和效率的过程。
本文将介绍薄膜太阳能电池封装的基本工艺和流程。
薄膜太阳能电池封装工艺流程薄膜太阳能电池封装工艺包括以下几个主要步骤:1.准备工作:对薄膜太阳能电池片进行检查,确保其质量符合要求。
同时,准备好所需的封装材料,如背电极、背板、封装胶等。
2.封装背电极:将背电极粘贴在薄膜太阳能电池片的背面,以提供电流的传导和连接功能。
背电极的粘贴需要使用特殊的胶水,确保背电极与电池片之间无空隙。
3.安装背板:将背板固定在背电极上,以保护电池片,并提供良好的支撑。
背板通常采用耐候性较好的材料,如塑料或金属。
4.填充封装胶:在背板上涂覆一层封装胶,将封装胶均匀地涂抹在整个背板上,确保电池片能够被充分覆盖。
封装胶的材料可根据具体需求选择,常见的有有机硅、聚氨酯等。
5.封装胶固化:待封装胶涂覆完毕后,需要将其进行固化,以提高胶水的稳定性。
固化的方法可以是自然固化或烘箱固化,根据具体工艺和生产需求进行选择。
6.切割:将已固化的薄膜太阳能电池进行切割,得到所需尺寸的电池片。
切割时需要注意切口的平整和尺寸的一致性,以保证后续组装的顺利进行。
7.电池片测试:对切割好的电池片进行测试,检查其光电性能和其他关键指标是否符合要求。
测试的方法可以是电流-电压曲线测试、光谱响应测试等。
8.组装:根据具体的产品需求,将电池片与其他组件进行组装,如连接导线、安装支架等。
组装工艺需要严格控制每个环节的精度和质量,确保组装的稳定性和可靠性。
9.封装测试:对已组装好的薄膜太阳能电池组件进行全面的测试,包括电池组件的电性能、机械性能等。
测试结果将直接影响组件的质量和性能。
结论薄膜太阳能电池封装工艺是保护和提升电池性能的关键环节,它涉及多个步骤和工艺参数的控制。
光伏组件工艺分类
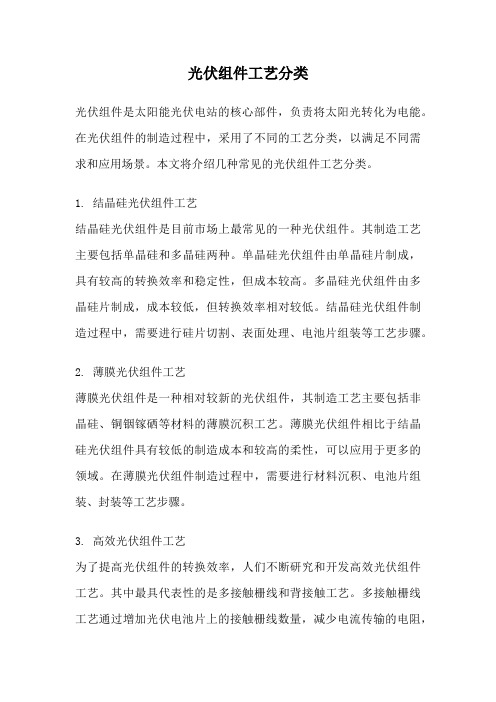
光伏组件工艺分类光伏组件是太阳能光伏电站的核心部件,负责将太阳光转化为电能。
在光伏组件的制造过程中,采用了不同的工艺分类,以满足不同需求和应用场景。
本文将介绍几种常见的光伏组件工艺分类。
1. 结晶硅光伏组件工艺结晶硅光伏组件是目前市场上最常见的一种光伏组件。
其制造工艺主要包括单晶硅和多晶硅两种。
单晶硅光伏组件由单晶硅片制成,具有较高的转换效率和稳定性,但成本较高。
多晶硅光伏组件由多晶硅片制成,成本较低,但转换效率相对较低。
结晶硅光伏组件制造过程中,需要进行硅片切割、表面处理、电池片组装等工艺步骤。
2. 薄膜光伏组件工艺薄膜光伏组件是一种相对较新的光伏组件,其制造工艺主要包括非晶硅、铜铟镓硒等材料的薄膜沉积工艺。
薄膜光伏组件相比于结晶硅光伏组件具有较低的制造成本和较高的柔性,可以应用于更多的领域。
在薄膜光伏组件制造过程中,需要进行材料沉积、电池片组装、封装等工艺步骤。
3. 高效光伏组件工艺为了提高光伏组件的转换效率,人们不断研究和开发高效光伏组件工艺。
其中最具代表性的是多接触栅线和背接触工艺。
多接触栅线工艺通过增加光伏电池片上的接触栅线数量,减少电流传输的电阻,提高光伏组件的效率。
背接触工艺则通过将电池片的电极放置在背面,减少光照损失,提高光伏组件的效率。
4. 双面光伏组件工艺传统的光伏组件只能利用正面的太阳光进行发电,而双面光伏组件则可以同时利用正面和背面的太阳光。
双面光伏组件工艺相对于传统的单面光伏组件工艺来说更加复杂。
在制造过程中,需要对电池片进行背面反射镀膜处理,以提高背面太阳光的反射率,并且需要设计特殊的安装结构,使背面的太阳光可以充分照射到电池片上。
5. 柔性光伏组件工艺柔性光伏组件是一种可以弯曲和折叠的光伏组件,可以应用于更加复杂的曲面和可穿戴设备上。
柔性光伏组件的制造工艺主要包括薄膜沉积、柔性基板制备、电池片组装等步骤。
相比于传统的硅基光伏组件,柔性光伏组件的制造工艺更加复杂,需要使用柔性基板和特殊的材料。
封装薄膜技术

封装薄膜技术封装薄膜技术,是一种高效、节能、环保、安全的涂膜技术,已经在许多行业得到广泛应用。
封装薄膜技术可以对物品的表面进行处理,防止其受到外部环境和物质的影响。
例如,在食品行业,封装薄膜技术可以对食品进行密封,防止空气、水分和细菌的侵入,保持食品的新鲜度和营养价值。
在医药行业,可以使用封装薄膜技术来包裹药物,以控制其释放速度,缓解药效的过强或过弱,增强药物的有效性和安全性。
封装薄膜技术还可以用于电子行业的IC等器件。
通过对电子元件进行包裹,可以保护其免受静电、耐热、湿氧化和化学腐蚀等不利因素的影响,从而延长其使用寿命。
此外,封装薄膜技术还可以用于汽车、建筑、包装和印刷行业等领域。
例如,在汽车行业,可以使用封装薄膜技术加工防护膜,以保护汽车的漆面、玻璃和灯具等部件免受划伤和UV光的侵害。
目前,封装薄膜技术已经取代了传统的喷涂、浸涂和刷涂等方法。
相比于传统的涂膜方法,封装薄膜技术有着诸多优势。
首先,封装薄膜技术可以实现高效、精准的表面涂覆。
通过控制涂层的厚度、粘度和物理性质等参数,可以使涂层的性能得到极大的改善。
其次,封装薄膜技术可以实现无 VOC(挥发性有机化合物)排放,符合环保要求。
通过使用无溶剂涂料和少量挥发性有机化合物的涂料,可以有效减少有害气体的排放,对环境和人类健康造成的影响也得到很好的遏制。
再次,封装薄膜技术可以实现低温处理,减少能源消耗。
相比传统的涂膜方法,封装薄膜技术的涂覆温度低,甚至可以通过光敏反应在室温下进行,从而节省能源并降低涂料材料的成本。
除此之外,封装薄膜技术还可以使表面防污、耐磨、防水和防紫外线等性质得到大幅提升,有效地延长物品的使用寿命。
总之,封装薄膜技术是一种高效、经济、环保和安全的涂膜方法,已经被广泛应用于多个领域。
随着技术的不断提升和成熟,相信封装薄膜技术必将在更多领域展现出它的独特优势和无限潜力。
封装薄膜技术的实现主要依靠各种先进的涂布工艺和设备,如机械式、电性、热致和光致等涂布方法。
光伏薄膜组件生产工艺流程

光伏薄膜组件生产工艺流程
首先是薄膜制备。
薄膜材料是光伏薄膜组件的核心,常见的薄膜材料有非晶硅、微晶硅、铜铟镓硒等。
薄膜制备的方法多种多样,常见的制备方法有物理气相沉积、化学气相沉积、溶液法等。
制备好的薄膜要进行表面处理和检测,确保质量合格。
接下来是电池片及背电极制备。
电池片是将薄膜材料转化为电能的关键部分,背电极则用于导电。
制备电池片需要将薄膜切割成合适的尺寸,并在其上进行光电转换材料的沉积和处理。
背电极的制备主要包括导电膜的沉积、导电层的制备等步骤,以提高电池的导电性能。
然后是组装封装。
在组装封装工艺中,将制备好的电池片组装到适当的基板上,形成组件的结构。
组件的基板可以是玻璃、聚合物等材料。
组装的过程中需要注意清洁和密封性,以确保组件不受外界环境的影响。
接下来是性能测试。
完成组装封装后,对光伏薄膜组件的性能进行测试。
常见的性能测试项目有电流-电压曲线测试、光强依赖性测试、温度依赖性测试等。
这些测试项目可以评估组件的性能指标,比如效率、功率输出等。
最后是包装。
完成性能测试后,对光伏薄膜组件进行包装。
包装的目的是防止组件受到外界的物理、化学和环境影响。
常见的包装材料有塑料薄膜、泡沫等,包装后的组件可以存放、运输和安装。
总结起来,光伏薄膜组件的生产工艺流程包括薄膜制备、电池片及背电极制备、组装封装、性能测试和包装等多个环节。
这些步骤的顺序和方法会因制造商和产品类型的不同而有所差异,但整个工艺流程的目标是制造出性能稳定、质量可靠的光伏薄膜组件。
光伏组件的封装方案
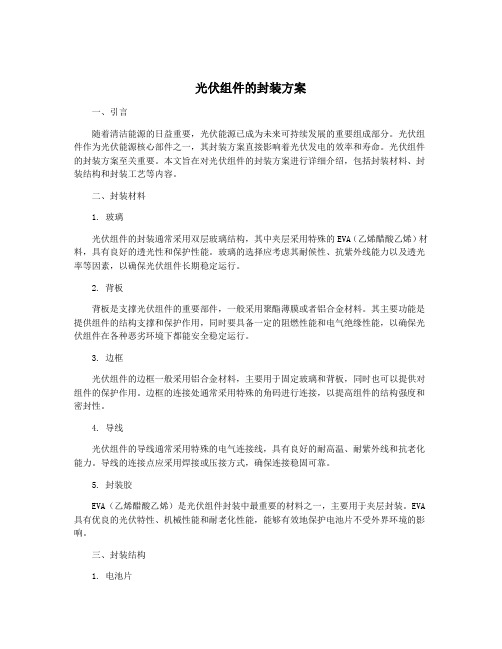
光伏组件的封装方案一、引言随着清洁能源的日益重要,光伏能源已成为未来可持续发展的重要组成部分。
光伏组件作为光伏能源核心部件之一,其封装方案直接影响着光伏发电的效率和寿命。
光伏组件的封装方案至关重要。
本文旨在对光伏组件的封装方案进行详细介绍,包括封装材料、封装结构和封装工艺等内容。
二、封装材料1. 玻璃光伏组件的封装通常采用双层玻璃结构,其中夹层采用特殊的EVA(乙烯醋酸乙烯)材料,具有良好的透光性和保护性能。
玻璃的选择应考虑其耐候性、抗紫外线能力以及透光率等因素,以确保光伏组件长期稳定运行。
2. 背板背板是支撑光伏组件的重要部件,一般采用聚酯薄膜或者铝合金材料。
其主要功能是提供组件的结构支撑和保护作用,同时要具备一定的阻燃性能和电气绝缘性能,以确保光伏组件在各种恶劣环境下都能安全稳定运行。
3. 边框光伏组件的边框一般采用铝合金材料,主要用于固定玻璃和背板,同时也可以提供对组件的保护作用。
边框的连接处通常采用特殊的角码进行连接,以提高组件的结构强度和密封性。
4. 导线光伏组件的导线通常采用特殊的电气连接线,具有良好的耐高温、耐紫外线和抗老化能力。
导线的连接点应采用焊接或压接方式,确保连接稳固可靠。
5. 封装胶EVA(乙烯醋酸乙烯)是光伏组件封装中最重要的材料之一,主要用于夹层封装。
EVA 具有优良的光伏特性、机械性能和耐老化性能,能够有效地保护电池片不受外界环境的影响。
三、封装结构1. 电池片光伏组件的核心部件是电池片,一般采用硅片或薄膜电池片。
硅片电池一般采用多晶硅或单晶硅材料,其尺寸和电池布局将直接影响光伏组件的封装结构。
2. 夹层夹层是光伏组件封装的关键部位,主要由EVA封装胶材料构成。
夹层的主要功能是粘合和封装电池片,同时具备良好的光透过性和保护作用。
3. 玻璃光伏组件的面板采用双层玻璃结构,主要用于保护夹层和电池片,并提供光学透光性。
玻璃的选择应考虑其透光性、机械性能和耐候性等因素。
4. 背板背板主要用于支撑和保护光伏组件,同时通过边框固定在一起。
薄膜组件封装工艺简介薄膜组件封装工艺简介

超声波焊 接
功率测试
合
装接线盒
格
清洗包装 入库
检验 不合格
返修
裁切PVB 摊铺PVB
背玻璃清 洗
合背板
高压釜
层压工序 成品层压
半成品层压
薄膜组件封装工艺简介薄膜组件封装 工艺简介
二、清洗工序
薄膜组件封装工艺简介薄膜组件封装 工艺简介
清洗工序:
清洗工序的作用:把钢化玻璃清洗干净,达到 工艺要求; 封装车间清洗机所清洗的是电池的背玻璃,这 种背板玻璃是一种钢化玻璃;
薄膜组件封装工艺简介薄膜组件封装 工艺简介
PVB的性质:
(2)PVB的化学性质: 涂料具有高适用性、弹性、高韧性、兼容性。 耐强碱、耐油性、可挠性与低温抗冲击性。 添加可塑剂后,皮膜柔软性特优。 使用胶合安全玻璃中间膜,使玻璃具有强大的 耐冲击与耐穿透力。 与无机材质之接着强度、架桥性、放蚀性优良。 依PVB之不同能基(Functional group)可溶于醇、 酮、酯等类溶剂。
薄膜组件封装工艺简介薄膜组件封装 工艺简介
层压:(非晶)
1)钢化玻璃 2)PVB胶膜 3)前电池板
背板玻璃 PVB胶膜
前电池板
薄膜组件封装工艺简介薄膜组件封装 工艺简介
层压:(晶硅)
1)钢化玻璃 2)EVA 3)电池串 4)EVA 5)背板(TPT)
薄膜组件封装工艺简介薄膜组件封装 工艺简介
薄膜组件封装工艺简介薄膜组件封装 工艺简介
以非晶硅车间1#层压机为例, 具体的介绍层压机的性能:
薄膜组件封装工艺简介薄膜组件封装 工艺简介
三、层压机工序 裁切与摊铺
薄膜组件封装工艺简介薄膜组件封装 工艺简介
PVB材料的概述:
微电子封装中的薄膜技术
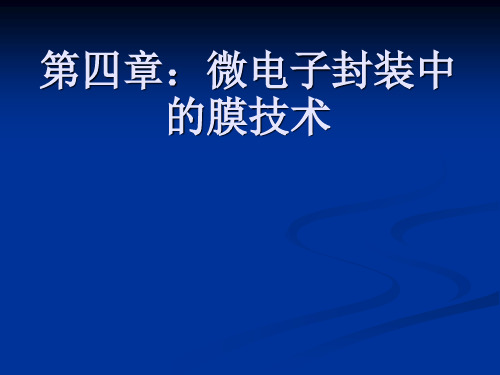
一些主要的厚膜导体:
Ag-Pd; Ag-Pd; Ag中添加Pd,当Pd/(Pd+Ag)>0.1左右时即产生效果。 Ag中添加Pd,当Pd/(Pd+Ag)>0.1左右时即产生效果。 Ag/Pd比一般控制在(2.5:1) Ag/Pd比一般控制在(2.5:1)~(4.0:1)。 4.0:1)。 Ag/Pd比与厚膜的电阻值及耐焊料浸蚀关系如下图1 Ag/Pd比与厚膜的电阻值及耐焊料浸蚀关系如下图1:
备注:目数=25.4[mm]/(丝径[mm]+开口长度[mm])
丝网印刷工艺
刮板
刮板的形状有下三种:菱形刮板、平行刮板、剑 形刮板。刮板的材料硬度按橡胶常用的HS(肖氏 形刮板。刮板的材料硬度按橡胶常用的HS(肖氏 硬度)来标定,厚膜印刷使用的刮板硬度一般在 60~80HS范围内。材料一般为聚氨酯类、氯丁橡 60~80HS范围内。材料一般为聚氨酯类、氯丁橡 胶、炭氟化合物等,选材聊特别要注意不能受浆 料中溶剂等浸蚀。
3. 厚膜介质材料
通常分为HK(高介电常数)介电体和LK 通常分为HK(高介电常数)介电体和LK (低介 电常数)介电体。 前者介电常数在数百以上,主要用于厚膜电容器 的介电质,后者的K值在10以下,多用于表面钝 的介电质,后者的K值在10以下,多用于表面钝 化、交叉层绝缘层、多层布线绝缘层以及低容量 电容器等。 LK介电质:非晶玻璃(filled glass: FG)和晶态玻 LK介电质:非晶玻璃(filled FG)和晶态玻 璃(crystallizable 璃(crystallizable glass: CG)二类玻璃系列。 CG)二类玻璃系列。 HK介电质:以BaTiO3为主要成分的介电质。 HK介电质:以BaTiO
蚀刻法基板表面成膜成膜材料基板光刻胶蚀刻光刻胶剥离基板薄膜光刻胶光致优点是选择性好重复性好生产效率高设备简单成本低基片薄膜光刻胶光致光刻胶金属薄膜ar干法蚀刻法对图形的控制精度较好但速度较慢rie刻蚀装置光刻胶sio或硅原子腐蚀性气化学腐蚀物理轰击用机械或光刻等方法制作正掩膜将掩膜按需要的电路图位置定位再由真空蒸镀等方法成膜
光伏组件封装工艺流程及主要原材料解析
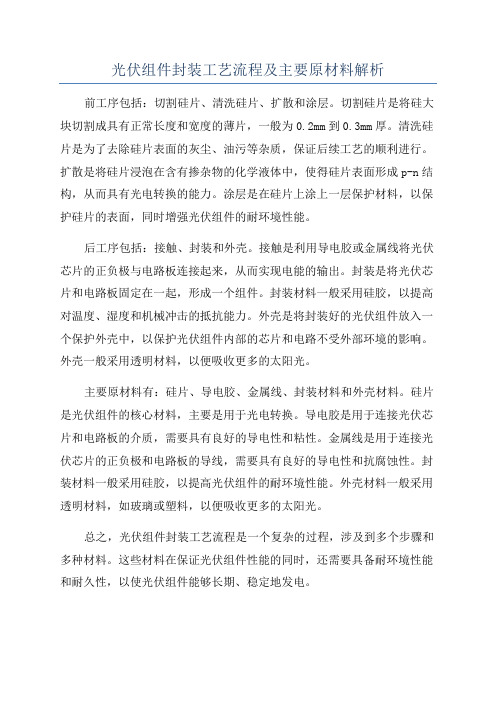
光伏组件封装工艺流程及主要原材料解析前工序包括:切割硅片、清洗硅片、扩散和涂层。
切割硅片是将硅大块切割成具有正常长度和宽度的薄片,一般为0.2mm到0.3mm厚。
清洗硅片是为了去除硅片表面的灰尘、油污等杂质,保证后续工艺的顺利进行。
扩散是将硅片浸泡在含有掺杂物的化学液体中,使得硅片表面形成p-n结构,从而具有光电转换的能力。
涂层是在硅片上涂上一层保护材料,以保护硅片的表面,同时增强光伏组件的耐环境性能。
后工序包括:接触、封装和外壳。
接触是利用导电胶或金属线将光伏芯片的正负极与电路板连接起来,从而实现电能的输出。
封装是将光伏芯片和电路板固定在一起,形成一个组件。
封装材料一般采用硅胶,以提高对温度、湿度和机械冲击的抵抗能力。
外壳是将封装好的光伏组件放入一个保护外壳中,以保护光伏组件内部的芯片和电路不受外部环境的影响。
外壳一般采用透明材料,以便吸收更多的太阳光。
主要原材料有:硅片、导电胶、金属线、封装材料和外壳材料。
硅片是光伏组件的核心材料,主要是用于光电转换。
导电胶是用于连接光伏芯片和电路板的介质,需要具有良好的导电性和粘性。
金属线是用于连接光伏芯片的正负极和电路板的导线,需要具有良好的导电性和抗腐蚀性。
封装材料一般采用硅胶,以提高光伏组件的耐环境性能。
外壳材料一般采用透明材料,如玻璃或塑料,以便吸收更多的太阳光。
总之,光伏组件封装工艺流程是一个复杂的过程,涉及到多个步骤和多种材料。
这些材料在保证光伏组件性能的同时,还需要具备耐环境性能和耐久性,以使光伏组件能够长期、稳定地发电。
- 1、下载文档前请自行甄别文档内容的完整性,平台不提供额外的编辑、内容补充、找答案等附加服务。
- 2、"仅部分预览"的文档,不可在线预览部分如存在完整性等问题,可反馈申请退款(可完整预览的文档不适用该条件!)。
- 3、如文档侵犯您的权益,请联系客服反馈,我们会尽快为您处理(人工客服工作时间:9:00-18:30)。
超声波焊接工序:
超声波焊接工序在生产中的作用:在电池上贴双 面胶,贴铝镍复合带,焊接铝带;
焊接的工艺流程:
接收电池板:传来的电池进入焊接机 贴双面胶:粘贴绝缘双面胶 贴复合带:复合带是铝镍符合材料, 焊接铝带:超声波焊接铝带,把铝带焊接 在电池板上;
超声波:
超声波是指与声波具有相同的物理性质,但频度 达到20000Hz以上,高于人耳听力范围的波动现象; 其特征:是波长短,近似于直线传播,在固体和 液体内衰减小,能量集中,可形成高强度、剧烈 振动,引起激震波,液体中的空化作用等,产生 机械、光、热、电、化学和生物等各种效应,被 现代科技广泛应用。
PVB材料的概述:
聚乙烯醇缩丁醛(Polyvinyl butyral)简称PVB。 PVB是由聚乙烯醇和丁醛在强酸催化作用下反 应得到的高分子化合物。本身含有很多的羟基, (OH)基,可以与一些热固型树脂 (Thermosetting resin)产生架桥反应(Cross linking reaction)以提升耐化学药品性及涂膜 硬度等性能。并具有优异涂膜高透明性 (Transparent)弹性(elastic)、韧性 (Toughness)、耐强碱、耐油性及可挠性 , 与低温耐冲击性。
水分含量 % 拉伸程度 Mpa
断裂伸长率 % 雾度 % 收缩率 (60℃/15min) %
0.4-0.6 ≥20.0
≥200 < 0.4 ≤12
PVB裁切的要求:
裁切的尺寸要符合要求; 不允许一次裁切大量PVB搁臵很长时间后 才使用,原则上每次裁切最多30--60块, 裁切好的PVB要在30分钟内投入使用; 班长,要根据生产情况,安排好裁切PVB 的数量,严禁停产后仍然有大量的PVB没 有使用,出现此类情况追究班长责任;
钢化玻璃自爆的原因:
②钢化玻璃中应力分布不均匀、偏移 玻璃在加热或冷却时沿玻璃厚度方向产 生的温度梯度不均匀、不对称。使钢化制品 有自爆的趋向,有的在激冷时就产生“风爆”。 如果张应力区偏移到制品的某一边或者偏移 到表面则钢化玻璃形成自爆。 ③钢化程度的影响,实验证明,当钢化程度 提高到1级/㎝时自爆数达20—25%。由此可见 应力越大钢化程度越高,自爆量也越大。
PVB裁切的要求:
裁切完成后要包好支架上的PVB,包裹要 严密,放臵受潮污染; 没有使用的裁切好的PVB要包裹要严密, 放臵受潮污;
高压釜工序:
高压釜工序的作用:把层压的半成品进行蒸 压,使之成为成品;
高压釜工序:
高压釜内部:
高压釜:
玻璃高压釜(又称蒸压釜)设备是一个卧式 高压容器,它是对初压后的平板夹层玻璃或 弧形夹层玻璃进入釜后,通过加温加压,使 之玻璃与PVB胶片全面结合牢固,是A类干法 夹层玻璃生产线最后一道工序的关键设备。 高压釜原来是夹胶玻璃生产线的设备,现在 是把这种设备借用到了非晶硅玻璃生产线中 来了;
自动工作的流程: 高压釜的六个阶段:升温升压—升温(保压) 阶段—升压(保温)阶段—保温保压阶段—排 气阶段;
加热----充气------加热------充气-------保持温度和压 力-------降温------排气(减压)
高压釜的参数:
主要参数项目: 第一段温度, 第一段压力, 第二段温度, 第二段压力, 保温保压时间, 排气温度
超声波焊接的缺点:
所焊接金属件不能太厚,一般小于或等于 5mm; 焊点位不能太大; 需要加压;
超声波焊接机的主要参数:
功 率:超声波发生器的功率,输出能 量的大小; 焊接时间:焊头压在铝带上以后,发出超 声波的时间长短; 焊头压力:焊头压铝带的压力;
焊接质量的要求:
铝带表面平整,无褶皱、断裂,居中;无焊 穿,虚焊现象,焊接牢固; 铝带和复合带交汇点焊接牢固,交汇点下面 不得有双面胶; 复合带和铝带充分接触;焊点面积达到交汇 面积的60%;
层压:(非晶)
1)钢化玻璃 2)PVB胶膜 3)前电池板
背板玻璃
PVB胶膜
前电池板
层压:(晶硅)
1)钢化玻璃 2)EVA 3)电池串 4)EVA 5)背板(TPT)
封 结 图 装 构
玻 璃
电 片 池
层压机的作用:
层压机的作用就是要把这些物质压合在一
起,并要求压合后,达到以下目的: 1)、层压后无气泡 2)、相融物质要融为一体 3)、无法相融物质间要有一定的粘结强 度。
层压机的主要结构
温度控制系统: 液压系统: 真空系统: PLC工控系统: 传输系统:
共5大控制系统构成。
层压的工艺条件:
a.压力; b.温度; c.真空度; d.时间; 这4个条件是层压机封装太阳组件的必
备条件。
层压机的一些重要指标:
层压机的重要参数 1、 主体材料:铝合金或不锈钢,不建 议使用普通钢。 2、 真空抽气速率 3、 温度控制精度 4、 温度均匀性 5、 层压高度 6、 开启方式 7、 整机功率
PVB材料:
PVB材料的应用范围::
制造夹层、安全玻璃用的最佳粘合材料,同时 在建筑幕墙、橱窗、银行柜台、监狱探视窗、 炼钢炉屏幕及各种防弹玻璃等建筑领域也有广 泛的应用。
PVB的性质:
(1) PVB的物理性质: 密度:1.07g/cm3。 分子量:自30-45k. 折射率:1.488(20℃)。 吸水率:不大于4%。 软化温度:60-65℃。 玻璃化温度:66-84度(以聚合度不同而不同)。 溶解性:可以溶解于大多数醇、酮、醚、酯类 有机 溶剂,不溶于碳羟类溶剂,如汽油等石油 溶剂。
高压釜结构:
高压釜的整体机构如下:釜体,空压机,冷 干机,过滤器,进气管,排气管,水泵,进 水管,排水管,红外加热管;
釜内加热区分为四个区:上区,中区,下区, 补偿区。
高压釜操作流程:
开门 把放有电池片的小车推入高压釜 关门 点击自动运行按钮,高压釜开始自动工作;
高压釜工作的阶段
作出标记。每处定义0.5延长米。每处加放1 米
PVB的几何尺寸:
几何尺寸
厚度mm 均匀度 0.38±0.02 0.76±0.02
25mm距离内横向厚度偏差不 超过15µm 50mm距离内横向厚度偏差不 超过20µm
长度公差m 宽度偏差mm
0-5 0-10
0-2
PVB的其它技术要求
(3) PVB的其它技术要求
超声波金属焊接的原理:
超声波金属焊接是利用额每秒钟数万次的高频振
动波传递到两个需焊接的金属工件表面,再施以
一定的压力,使金属表面相互摩擦而形成分子层
之间的熔合,达到焊接的目的。
超声波焊接只适用于柔软韧性的金属焊接;
超声波金属焊接机:
超声波金属焊接机:
超声波焊接的优点:
1,节能 2,无需装备散烟散热的通风装臵 3,成本低,效率高 4,容易实现自动化生产
层压工序:
层压工序的作用:把焊好铝带的前电池板、 PVB胶膜、背板玻璃压合到一起; 太阳能电池组件层压机是实现从原材料到太 阳能电池板过渡的关键设备;
层压工序:
层压机:
层压工序:
层压机:
层压机:
层压机分为三段:
进料级
主机 (层压级)
出料级
层压机结构
机构图:
加热站 工作台 真空泵
出料台
主机
进料台
层压机的工艺流程:
开盖━上室真空━放入待压组件━合盖━ 下室抽空━上室充气(层压过程)━下室 充气━开盖━取出电池板;
层压机工作原理
层压机就是在真空条件下把多层物质进行压 合的机械设备。 真空层压机应用于太阳能电池组装生产线上。 我们称之为太阳能电池组件层压机。 无论层压机应用于哪种作业,其工作原理都 是相同的。那就是在多层物质的表面施加一 定的压力,将这些物质紧密地压合在一起。 所不同的事根据层压的目的不同,压合的条 件各不相同。
钢化玻璃的不足:
1 . 钢化后的玻璃不能再进行切割和加工,只 能在钢化前就对玻璃进行加工至需要的形状, 再进行钢化处理。
2 . 钢化玻璃强度虽然比普通玻璃强,但是钢 化玻璃在温差变化大时有自爆(自己破裂) 的可能性,而普通玻璃不存在自爆的可能性。
钢化玻璃自爆的原因:
钢化玻璃在无直接机械外力作用下发生的自动性 炸裂叫做钢化玻璃的自爆,根据行业经验,普通 钢化玻璃的自爆率在4‰左右。自爆是钢化玻璃 固有的特性之一。 产生自爆的原因很多,简单地归纳以下几种: ①玻璃质量缺陷的影响 A.玻璃中有结石、杂质 B.玻璃中含有硫化镍结晶物 C.玻璃表面因加工过程或操作不当造成有 划痕、炸口、深爆边等缺陷,易造成应力集中或 导致钢化玻璃自爆。
什么是钢化玻璃:
钢化玻璃的加工可分为物理钢化法和化学钢化 法。 这里只介绍物理法
什么是钢化玻璃:
物理钢化玻璃又称为淬火钢化玻璃。它时将普 通平板玻璃在加热炉中加热到接近玻璃的软化 温度(600℃)时,通过自身的形变消除内部 应力,然后将玻璃移出加热炉,再用多头喷嘴 将高压冷空气吹向玻璃的两面,使其迅速且均 匀地冷却至室温,即可制得钢化玻璃。
主要内容:
一.封装生产工艺流程
二.清洗工序
三.焊接工序
四.层压工序
五.高压釜工序
一、封装工艺生产流程
裁切PVB
背焊 接
摊铺PVB
合背板
功率测试 装接线盒
合 格
检验 不合格 层压工序 成品层压
清洗包装 入库
返修
高压釜