变速箱壳体铸造工艺设计
变速箱、离合器壳体铸造工艺设计方法

零件机械加工工艺规程是规定零件机械加工工艺过程和方法等的工艺文件。
它是在具体的生产条件下,将最合理或较合理的工艺过程,用图表〔或文字〕的形式制成文本,用来指导生产、管理生产的文件。
一、机械加工工艺规程的容及作用工艺规程的容,一般有零件的加工工艺路线、各工序根本加工容、切削用量、工时定额及采用的机床和工艺装备〔刀具、夹具、量具、模具〕等。
工艺规程的主要作用如下:1.工艺规程是指导生产的主要技术文件。
合理的工艺规程是建立在正确的工艺原理和实践根底上的,是科学技术和实践经历的结晶。
因此,它是获得合格产品的技术保证,一切生产和管理人员必须严格遵守。
2.工艺规程是生产组织管理工作、方案工作的依据。
原材料的准备、毛坯的制造、设备和工具的购置、专用工艺装备的设计制造、劳动力的组织、生产进度方案的安排等工作都是依据工艺规程来进展的。
3.工艺规程是新建或扩建工厂或车间的根本资料。
在新建扩建或改造工厂或车间时,需依据产品的生产类型及工艺规程来确定机床和设备的数量及种类,工人工种、数量及技术等级,车间面积及机床的布置等。
二、制定工艺规程的原则、原始资料〔一〕制定工艺规程的原则制定工艺规程的原则是:在保证产品质量的前提下,以最快的速度、最少的劳动消耗和最低的费用,可靠加工出符合设计图纸要求的零件。
同时,还应在充分利用本企业现有生产条件的根底上,尽可能保证技术上先进、经济上合理、并且有良好的劳动条件。
〔二〕制定工艺规程的原始资料1.产品零件图样及装配图样。
零件图样标明了零件的尺寸和形位精度以及其他技术要求,产品的装配图有助于了解零件在产品中的位置、作用,所以,它们是制定工艺规程的根底。
2.产品的生产纲领。
3.产品验收的质量标准。
4.本厂现有生产条件,如机床设备、工艺装备、工人技术水平及毛坯的制造生产能力等。
5.国、外同类产品的生产工艺资料。
三、制定工艺规程的步骤〔一〕零件图样分析零件图样分析的目的在于:1.分析零件的技术要求,主要了解各加工外表的精度要求、热处理要求,找出主要外表并分析它与次要外表的位置关系,明确加工的难点及保证零件加工质量的关键,以便在加工时重点加以关注。
汽车变速箱壳体工艺及夹具设计
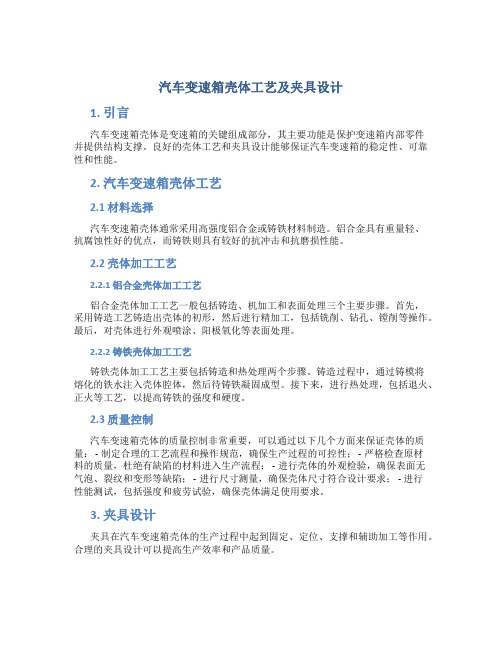
汽车变速箱壳体工艺及夹具设计1. 引言汽车变速箱壳体是变速箱的关键组成部分,其主要功能是保护变速箱内部零件并提供结构支撑。
良好的壳体工艺和夹具设计能够保证汽车变速箱的稳定性、可靠性和性能。
2. 汽车变速箱壳体工艺2.1 材料选择汽车变速箱壳体通常采用高强度铝合金或铸铁材料制造。
铝合金具有重量轻、抗腐蚀性好的优点,而铸铁则具有较好的抗冲击和抗磨损性能。
2.2 壳体加工工艺2.2.1 铝合金壳体加工工艺铝合金壳体加工工艺一般包括铸造、机加工和表面处理三个主要步骤。
首先,采用铸造工艺铸造出壳体的初形,然后进行精加工,包括铣削、钻孔、镗削等操作。
最后,对壳体进行外观喷涂、阳极氧化等表面处理。
2.2.2 铸铁壳体加工工艺铸铁壳体加工工艺主要包括铸造和热处理两个步骤。
铸造过程中,通过铸模将熔化的铁水注入壳体腔体,然后待铸铁凝固成型。
接下来,进行热处理,包括退火、正火等工艺,以提高铸铁的强度和硬度。
2.3 质量控制汽车变速箱壳体的质量控制非常重要,可以通过以下几个方面来保证壳体的质量: - 制定合理的工艺流程和操作规范,确保生产过程的可控性; - 严格检查原材料的质量,杜绝有缺陷的材料进入生产流程; - 进行壳体的外观检验,确保表面无气泡、裂纹和变形等缺陷; - 进行尺寸测量,确保壳体尺寸符合设计要求; - 进行性能测试,包括强度和疲劳试验,确保壳体满足使用要求。
3. 夹具设计夹具在汽车变速箱壳体的生产过程中起到固定、定位、支撑和辅助加工等作用。
合理的夹具设计可以提高生产效率和产品质量。
3.1 夹具类型3.1.1 固定型夹具固定型夹具主要用于固定壳体在加工过程中的位置,防止壳体移动或变形。
常见的固定型夹具包括卡盘夹具和夹块夹具。
3.1.2 辅助夹具辅助夹具用于辅助加工操作,提供支撑和定位。
常见的辅助夹具包括支撑座夹具、定位销夹具和模板夹具。
3.2 设计要点3.2.1 夹具刚性夹具在加工过程中需要承受一定的切削力、挤压力等作用,因此夹具的刚性要足够强,以确保壳体加工的准确性和稳定性。
机械制造专业毕业设计——变速箱壳体机械加工工艺设计
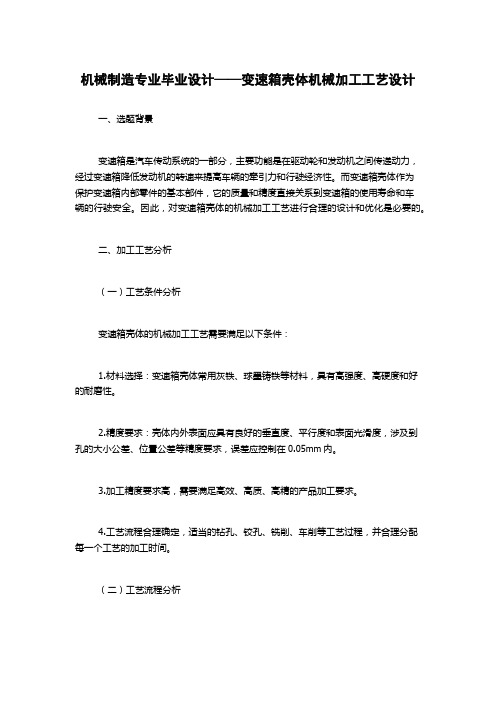
机械制造专业毕业设计——变速箱壳体机械加工工艺设计一、选题背景变速箱是汽车传动系统的一部分,主要功能是在驱动轮和发动机之间传递动力,经过变速箱降低发动机的转速来提高车辆的牵引力和行驶经济性。
而变速箱壳体作为保护变速箱内部零件的基本部件,它的质量和精度直接关系到变速箱的使用寿命和车辆的行驶安全。
因此,对变速箱壳体的机械加工工艺进行合理的设计和优化是必要的。
二、加工工艺分析(一)工艺条件分析变速箱壳体的机械加工工艺需要满足以下条件:1.材料选择:变速箱壳体常用灰铁、球墨铸铁等材料,具有高强度、高硬度和好的耐磨性。
2.精度要求:壳体内外表面应具有良好的垂直度、平行度和表面光滑度,涉及到孔的大小公差、位置公差等精度要求,误差应控制在0.05mm内。
3.加工精度要求高,需要满足高效、高质、高精的产品加工要求。
4.工艺流程合理确定,适当的钻孔、铰孔、铣削、车削等工艺过程,并合理分配每一个工艺的加工时间。
(二)工艺流程分析经过对变速箱壳体的结构和特点分析,可以确定其加工工艺流程为:锯切-车削车床粗加工-立铣机铣削-数控车床完成孔加工和尺寸精密加工-下料。
1.锯切:根据变速箱壳体的实际尺寸,切割出长度大小合适的原材料。
2.车床粗加工:对壳体的大小外形进行车削,使其达到加工后的理论尺寸。
3.立铣机铣削:借助于立铣机的加工效率和精度,对壳体上的凸台和凹槽进行铣削,使得加工尺寸和精度更加准确。
4.数控车床完成孔加工和尺寸精密加工:应用数控车床加工各种孔位,控制每种孔的加工精度和尺寸精度,达到加工要求的公差范围。
5.下料:完成孔加工和尺寸精密加工后,进行下料作业,去除工件上多余的局部区域,形成成品。
(三)工艺路线分析1.壳体的基本形状是长方体,按照设计标准进行锯切,对毛坯进行初步处理,确保各项尺寸符合设计要求。
2.根据技术要求,按照车床工艺进行工件的粗加工,利用车削车床对外表面进行加工并达到设计要求的公差范围。
3.经过车削车床的工艺加工,为变速箱壳体提供了基础加工的前置工作,之后利用立铣机铣削壳体的凹槽和凸台等细节部位,以期获得加工公差更小、表面更光滑的加工效果。
铝合金变速箱外壳压铸模设计及工艺分析

2021年第3期/第70卷压力铸造301铝合金变速箱外壳压铸模设计及工艺分析周倩1,任浩2,王俊有3,黄明宇1(1.南通大学机械工程学院,江苏南通226019; 2.天津雄邦压铸有限公司,天津300300;3.雄邦压铸(南通)有限公司,江苏南通226300)摘要:针对铝合金铸件在压铸充填过程中常伴有气孔、缩孔、冷隔等缺陷的现象,以汽车铝合金变速箱外壳为例,分析变速箱外壳的结构特征,对其浇注系统、冷却系统、抽芯结构进行设计,确定最佳工艺参数,经过试验与分析,最终经过实际压铸生产验证,确定了工艺方案的合理性。
结果表明:当定模温度为200 t、动模为220 t、铝液浇注温度为670弋、慢压射速度为0.18 m/s、快压射速度为4.5 m/s、内浇道的压射速度为48 m/s、留模时间为30 s日寸,铸件成形品质较好。
合理压铸工艺设计不仅能提高生产效率以及产品的合格率,还能简化模具设计制造流程,减少模具开发成本。
关键词:铝合金;压铸模具;工艺分析;压铸生产铝合金具有密度小、强度较高、耐腐蚀、耐磨、导热性能好、易于加工、外形美观等方面的优点,广泛应用于汽车、航空、机械、通讯等领域111。
铝合金的成形方法,主要包括压力铸造、砂型铸造、挤压铸造等。
目前49%的铝合金产品都是通过压铸成形的。
压铸铝合金使用范围非常广泛,约占压铸件总产量的75%以上〜1。
压铸成形具有产品质量好、尺寸精度高、适合大批量生产等多方面的优势W。
在生产过程中,由于铝合金铸件伴随着热胀冷缩的物理变化,不可避免地会产生气孔、缩孔、冷隔、裂纹等缺陷,极大影响了铝合金铸件的生产合格率。
随着汽车领域对铝合金作者简介:周倩(1997-),女,硕 士研究生,主要研究材料 成形及控制工程。
E-m ail: 3281301589@通讯作者:黄明宇,男,硕士生导师,教授。
E-m ail:huang.my@ 中图分类号:TG249.2文献标识码: B文章编号:1001-4977(2021) 03-0301-05铸件产品的要求越来越严苛,需要铸造行业不断优化压铸工艺来满足产品性能的需求。
论文-变速箱体的砂型铸造
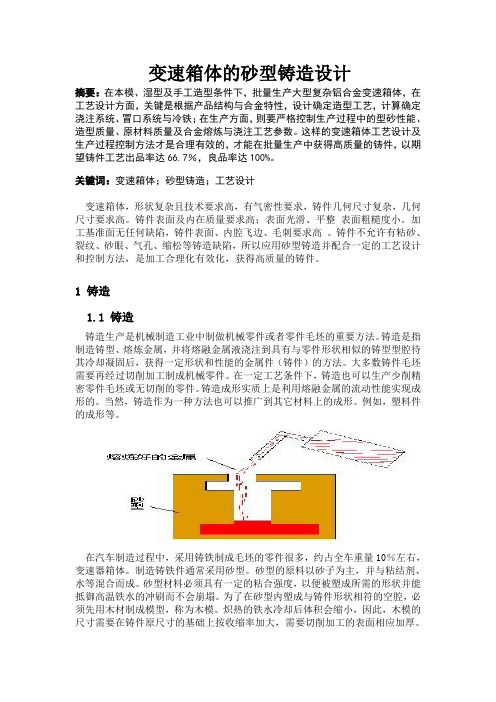
变速箱体的砂型铸造设计摘要:在本模、湿型及手工造型条件下,批量生产大型复杂铝合金变速箱体,在工艺设计方面,关键是根据产品结构与合金特性,设计确定造型工艺,计算确定浇注系统、冒口系统与冷铁;在生产方面,则要严格控制生产过程中的型砂性能、造型质量、原材料质量及合金熔炼与浇注工艺参数。
这样的变速箱体工艺设计及生产过程控制方法才是合理有效的,才能在批量生产中获得高质量的铸件,以期望铸件工艺出品率达66.7%,良品率达100%。
关键词:变速箱体;砂型铸造;工艺设计变速箱体,形状复杂且技术要求高,有气密性要求,铸件几何尺寸复杂,几何尺寸要求高。
铸件表面及内在质量要求高;表面光滑、平整表面粗糙度小。
加工基准面无任何缺陷,铸件表面、内腔飞边、毛刺要求高。
铸件不允许有粘砂、裂纹、砂眼、气孔、缩松等铸造缺陷,所以应用砂型铸造并配合一定的工艺设计和控制方法,是加工合理化有效化,获得高质量的铸件。
1 铸造1.1 铸造铸造生产是机械制造工业中制做机械零件或者零件毛坯的重要方法。
铸造是指制造铸型、熔炼金属,并将熔融金属液浇注到具有与零件形状相似的铸型型腔待其冷却凝固后,获得一定形状和性能的金属件(铸件)的方法。
大多数铸件毛坯需要再经过切削加工制成机械零件。
在一定工艺条件下,铸造也可以生产少削精密零件毛坯或无切削的零件。
铸造成形实质上是利用熔融金属的流动性能实现成形的。
当然,铸造作为一种方法也可以推广到其它材料上的成形。
例如,塑料件的成形等。
在汽车制造过程中,采用铸铁制成毛坯的零件很多,约占全车重量10%左右,变速器箱体。
制造铸铁件通常采用砂型。
砂型的原料以砂子为主,并与粘结剂、水等混合而成。
砂型材料必须具有一定的粘合强度,以便被塑成所需的形状并能抵御高温铁水的冲刷而不会崩塌。
为了在砂型内塑成与铸件形状相符的空腔,必须先用木材制成模型,称为木模。
炽热的铁水冷却后体积会缩小,因此,木模的尺寸需要在铸件原尺寸的基础上按收缩率加大,需要切削加工的表面相应加厚。
变速箱壳体铸造工艺设计

2008 年 9 月
寸过小或切边材料过少时, 材料会被拉入模具间 隙内而成为毛边, 此时必须加大冲裁的搭边尺寸 或切边余量。
3 模具的刃磨
冲压生产中对模具进行合理的刃磨, 可以有 效地提高冲模的寿命, 节省模具费用, 大幅度降低 产品成本。
文章编号: 1001-3814(2008)17-0148-03
1 生产条件
变 速 箱 壳 体 铸 件 材 质 HT200, 铸 件 质 量 82 kg, 外形尺寸 552.5 mm ×513 mm ×488.2 mm, 壁厚
收稿日期: 2007-12-21 作者简介: 吕建强( 1966-) , 男, 江苏 淮 安 人 , 高 级 工 程 师 , 学 士 , 主
[2] 付 翔. 浅 议 模 具 的 使 用 和 管 理 [J]. 现 代 机 械 , 2002, (4): 111-112.
[3] 卢金斌, 张太超 , 张 文 勇 , 等. 高 速 钢 冷 挤 压 凹 模 开 裂 失 效 分 析[J]. 模具工业, 2007, ( 1) : 68-70.
[4] 张文玉, 刘先兰. 模 具 加 工 过 程 中 的 缺 陷 及 其 预 防 措 施[J]. 机床与液压, 2006, ( 11) : 242-245.
4 模具设计要点
外 模 与 型 板 联 接 处 设 计 一 圈 30 mm 宽 、30 mm 高法兰, 以利于增设和改动螺孔和定位销孔, 同时利于在日后的模具维护中重新设置螺孔和定 位销孔。为增加模具的强度, 在模具内腔设置一定 数量的加强筋, 加强筋高度至分型面, 漏模框与外 模之间间隙取 0.5 mm。如图 4 所示。
模具刃磨量必须根据刃口端面和侧面的实际 磨损情况而定, 此外, 还应该考虑材料厚度、凹模 形状结构以及刃磨次序等相关因素。凹模经多次
解放10B汽车变速箱体加工工艺及夹具设计

解放10B汽车变速箱体加工工艺及夹具设计一、引言随着汽车工业的发展,汽车变速箱作为关键部件之一,对车辆性能和安全性起着至关重要的作用。
解放10B汽车变速箱是一款高性能变速箱,其加工工艺和夹具设计对产品质量和生产效率具有重要影响。
本文将介绍解放10B汽车变速箱体的加工工艺和夹具设计。
二、汽车变速箱体加工工艺解放10B汽车变速箱体加工工艺的主要步骤包括铸造、精度加工、热处理、表面处理和总装等环节。
2.1 铸造解放10B汽车变速箱体采用铸造工艺进行生产。
铸造过程中,需要选用高强度和耐磨损的材料,确保变速箱体的强度和耐用性。
2.2 精度加工铸造完成后的解放10B汽车变速箱体需要进行精度加工,包括外形修整、孔加工和螺纹加工等。
精度加工的目的是确保变速箱体的尺寸和形状符合设计要求。
2.3 热处理解放10B汽车变速箱体在精度加工之后需要进行热处理,以提高其硬度和耐久性。
常用的热处理方法包括淬火和回火。
2.4 表面处理表面处理是为了提高解放10B汽车变速箱体的防腐蚀性能和美观度。
常用的表面处理方法包括喷涂、电镀和磷化等。
2.5 总装经过上述工艺步骤处理后的解放10B汽车变速箱体将进行总装。
总装包括零部件的装配、检验和调试等环节。
三、夹具设计夹具是指用于固定和定位工件的装置,用来保证工件在加工过程中的稳定性和精度。
在解放10B汽车变速箱体的加工过程中,夹具的设计起着重要的作用。
夹具设计需要考虑以下几个方面:3.1 定位夹具定位夹具用于将解放10B汽车变速箱体固定在加工设备上。
在定位夹具的设计中,需要确保夹具具有足够的刚度和精度,以确保加工过程中的稳定性和精度。
3.2 夹紧夹具夹紧夹具用于夹持解放10B汽车变速箱体,以保持其固定位置。
夹紧夹具的设计需要考虑工件的形状、尺寸和材料等因素,确保夹持力合适且不会对工件造成损坏。
3.3 检测夹具检测夹具用于在加工结束后对解放10B汽车变速箱体进行检测。
检测夹具的设计需要考虑到检测的精度和准确性,以确保产品质量符合要求。
汽车变速箱体加工工艺及夹具设计
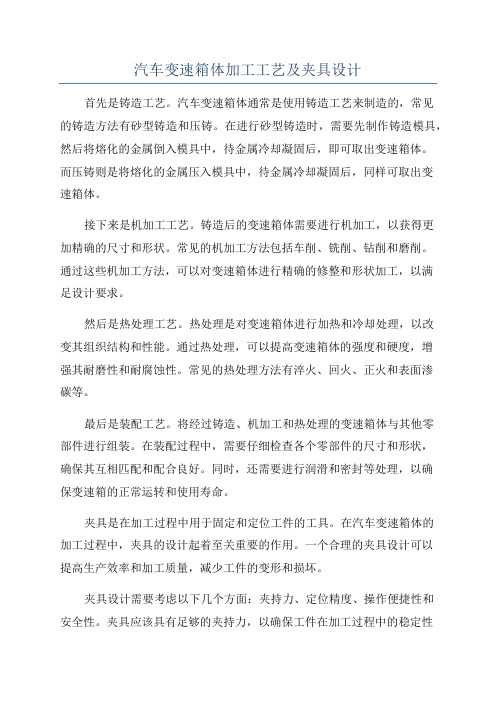
汽车变速箱体加工工艺及夹具设计首先是铸造工艺。
汽车变速箱体通常是使用铸造工艺来制造的,常见的铸造方法有砂型铸造和压铸。
在进行砂型铸造时,需要先制作铸造模具,然后将熔化的金属倒入模具中,待金属冷却凝固后,即可取出变速箱体。
而压铸则是将熔化的金属压入模具中,待金属冷却凝固后,同样可取出变速箱体。
接下来是机加工工艺。
铸造后的变速箱体需要进行机加工,以获得更加精确的尺寸和形状。
常见的机加工方法包括车削、铣削、钻削和磨削。
通过这些机加工方法,可以对变速箱体进行精确的修整和形状加工,以满足设计要求。
然后是热处理工艺。
热处理是对变速箱体进行加热和冷却处理,以改变其组织结构和性能。
通过热处理,可以提高变速箱体的强度和硬度,增强其耐磨性和耐腐蚀性。
常见的热处理方法有淬火、回火、正火和表面渗碳等。
最后是装配工艺。
将经过铸造、机加工和热处理的变速箱体与其他零部件进行组装。
在装配过程中,需要仔细检查各个零部件的尺寸和形状,确保其互相匹配和配合良好。
同时,还需要进行润滑和密封等处理,以确保变速箱的正常运转和使用寿命。
夹具是在加工过程中用于固定和定位工件的工具。
在汽车变速箱体的加工过程中,夹具的设计起着至关重要的作用。
一个合理的夹具设计可以提高生产效率和加工质量,减少工件的变形和损坏。
夹具设计需要考虑以下几个方面:夹持力、定位精度、操作便捷性和安全性。
夹具应该具有足够的夹持力,以确保工件在加工过程中的稳定性和精确性。
同时,夹具还应具有良好的定位精度,以确保工件的正确位置和形状。
操作便捷性是指夹具的设计应该简单易用,方便操作人员进行装夹和取卸工件。
同时,夹具还应具有良好的安全性,以避免意外事故的发生。
在夹具设计中,需要根据变速箱体的形状和尺寸,选择适当的夹具类型和夹持方式。
常见的夹具类型有平行夹具、三爪夹具和冲击夹具等。
同时,还需要考虑夹具的刚度和稳定性,以确保夹具在加工过程中不产生松动和变形。
总之,汽车变速箱体加工工艺和夹具设计是汽车制造中不可或缺的环节。
- 1、下载文档前请自行甄别文档内容的完整性,平台不提供额外的编辑、内容补充、找答案等附加服务。
- 2、"仅部分预览"的文档,不可在线预览部分如存在完整性等问题,可反馈申请退款(可完整预览的文档不适用该条件!)。
- 3、如文档侵犯您的权益,请联系客服反馈,我们会尽快为您处理(人工客服工作时间:9:00-18:30)。
5.3.3 变速箱壳体铸造工艺设计
(1) 生产条件
变速箱壳体铸件材质HT200,铸件质量82kg,外形尺寸552.5mm×513mm×488.2mm,壁厚10~30mm,主要壁厚10mm,如图5.3-9。
采用5t/h倒大双热风冲天炉熔炼,铁水出炉温度1400~1450℃;采用Z2140顶箱震实式造型机湿砂型造型,漏模起模,砂箱尺寸
900mm×700mmx350mm;采用Z878翻台震实式制芯机,酚醛树脂砂制芯。
(2) 工艺分析
箱体类铸件的收缩率受铁水的化学成分、浇注温度、铸件本身结构特征、铸型的退让性和型芯的退让性等多种因素的影响,尤其是化学成分、浇注温度的影响使得同一种铸件在每一炉次甚至同一炉次的尺寸都有差异。
一般灰铁件的收缩率在0.7%~1%之间。
图5.3-9 变速箱壳体
箱体类零件的尺寸精度除受铸件收缩率影响外,还受到错箱、偏芯、变形以及机械加工中的定位误差和机械加工误差的影响。
因此,要生产出合格的产品.在复杂形状箱体类铸件铸造模具设计制造中必须采取一系列的工艺措施,选择灵活适当的工艺参数。
该铸件可视作由近似长方箱体和喇叭口盘状两部分形状组成。
型芯被金属包裹面积较大。
喇叭口盘状型芯
尺寸较大,为增强型芯的排气和型芯的制造及型芯的装配,把型芯按图5.3-10主视图所示分成两块,在分芯面处开通气槽、在两端芯头处扎通砂型气孔,这样有利于浇注时型芯中的气体排出。
(3)工艺参数计算及工艺措施
根据铸件特点采取中间分型、分芯方式,浇注系统开设在分型面处,采用封闭式。
为了提高铸型通气性。
在所有最高点处扎φ6mm 明出气孔,同时在最高处设一φl 00 mm 顶部缩颈冒口。
既起排气、溢流又起补缩作用。
工艺图如图5.3-10所示。
1) 工艺参数的计算
浇注时间
21(s)t ==≈
式中:t 为浇注时间( s ) ;S 为系数;G 为型内金属液总质量(kg) 。
平均静压力头
p 0c 0.125350.12548.828.9(cm)H H h =-=-⨯≈
式中:P H 为平均静压力头( cm ) ;0H 为作用于内浇道的金属液静压力头( cm ) ;c h 为铸件高度( cm ) 。
图5.3-10 变速箱壳体铸造工艺示意图
平均有效静压力头
22
2P P 222212 1.428.912.9(cm)11 1.2 1.4
k h H k k ==⨯≈++++ 式中:P h 为平均有效静压力头( cm );12k k 和为系数(直浇道与横浇道、直浇道与内浇道有效截面比)。
内浇道总断面积,
26.2(cm )F =≈∑内
式中:ΣF 内为内浇道总断面积( cm 2 ) ;F 直为直浇道断面积( cm 2) ;ΣF 横为横浇道总断面积( cm 2) 。
2 )工艺参数的校核
型内液面上升速度
48.8 2.3(cm/s)2cm/s 21
c h v t ==≈>, 符合要求。
最小剩余压力头高度
m 40tan107(cm)12cm h Ltan α==≈<,符合要求。
式中:h m 为最小剩余压力头( cm ); L 为液态金属的流程( cm ) ;α 为压力角(°) 。
3) 工艺措施
外模采用漏模起模形式。
顶面机械加工余量取4 mm ,底面、侧面机械加工余量取3 mm ,拔模斜度取1 mm 正拔模斜度,长度方向收缩率取1%。
其它方向取0.7%。
变速箱壳体机械加工时,以下面大圆盘进行主定位,上部侧面两点进行辅助定位。
由于铸件长度方向尺寸较长(约550mm ),同时结构较复杂,需采取一定的工艺措施保证,为此在方法兰背面增加1mm 厚度的工艺补正量,以保证在发生1mm 以内错箱时法兰强度不受影响。
同时对各种塔子按长度方向增加2mm 工艺补正量。
方法兰连接孔处的槽左右各增加1mm 宽度,这样有利于装配。
型芯中的各轴承孔机械加工余量双边取6mm 。
需加工的凸台机械加工余量取5mm 。
芯头按零件开口处形状随形设计,这样披缝易于清除。
上型芯头外模于型芯之间设置0.5mm 间隙。
内腔各球形塔子按图纸要求高度,增加圆弧半径,以防止偏移而造成螺孔打穿。
因变速箱壳体型芯尺寸较复杂,树脂型芯因蠕变的影响,高度尺寸变化较大,为保证型芯尺寸,在型芯高度方向留2mm 磨削余量,待型芯烘干后借助磨芯工装通过磨芯机磨削,保证高度方向尺寸。
在大喇叭状上、下型芯尾部分别设计两个平台以利磨削型芯时进行定位,同时利于下箱型芯的定位和防止型芯旋转。
在下箱型芯两端的芯头部位分别设置两处空腔.以利于下型芯时由手抬型芯或夹具夹持型芯。
生产中发现,方法兰中部常出现裂纹。
分析认为,方法兰窗口处收缩阻力大,应力很大,由于清理铸件时锤击方法兰中部,从而引起裂纹出现。
当清理铸件时,只锤击方法兰外周,不锤击方法兰中部,裂纹问题基本解决。
(注:此例工艺参数的计算与校核见《铸造手册第5卷、第三章铸造工艺设计中的相关公式》) 1.41.21F F F ∑∑直横内::=:
:。