轧机AGC培训资料.
AGC培训课件汇总

9前馈(预控)AGC
针对入口板厚变化而造成的出口板厚影响而设 置的补偿称为前馈AGC,方法是由测厚仪检测 入口板厚,根据轧制数学模型推算出入口板厚 对出口板厚的影响值,进而推算出压下指令修 正量,并进行补偿控制
10监控AGC
通过检测出口板厚而设置的板厚指令修正补偿环 称为监控AGC。尽管AGC系统中已采取了一系列 补偿措施,由于扰动因素很多,且各扰动因素对 出口板厚的影响关系复杂,不可能实现完全补偿, 因此出口板厚难免还存在微小偏差,对于要求纵 向厚差≤±(0.003~0.005)mm的冷轧机来说,应 用测厚仪进行监控是必不可少的
AGC液压系统的基本功能
AGC仅对主要扰动—轧制力的变化及影 响进行补偿,并提出了头部锁定(相对值) AGC技术。为使板厚精度达到高标准(例如, 冷轧±0.003mm,热轧;±0.02mm)必须对其 他扰动也进行补偿,完善的液压AGC系统它 包括:
AGC液压系统的基本功能
1.液压APC(Automatic Position Control)即液压位置自动控 制系统 2.轧机弹跳补偿MSC(Mill Stretch Compensation) 3.热凸度补偿TEC(Thermal Crown Compensation) 4.油膜轴承厚度补偿BEC(Beering Oil Compensation) 5.支承辊偏心补偿ECC(Eccentricity Compensation) 6.同步控制SMC(Synchronized Motion Compensation) 7.倾斜控制 8.加减速补偿 9.前馈(预控)AGC 10.监控AGC 11.恒压力AGC
以上补偿措施并非每台轧机都全部采用,需要根 据轧机的类型、精度要求和工程经验采用其中的 一些主要补偿措施
二十辊轧机AGC 演示文稿
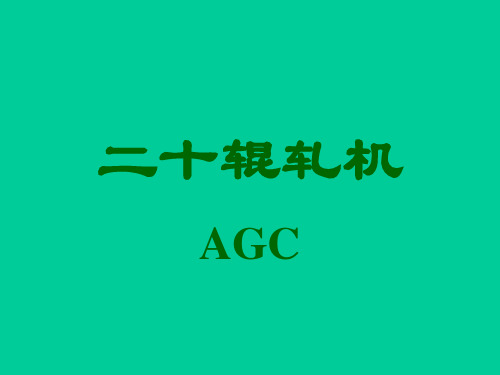
“电-液压”系统
-压下压力和位置传感器 -液压阀 -伺服阀 -液压缸(直径160MM 、行程132MM)
厚度调整
同步 压下
缸
上机架
下机架
NO.2中间 辊
工作 辊
弯辊 压下
缸
立柱
背衬 辊
NO.1中 间辊
常见的几种控制方法
• 厚度控制系统内设两种厚度控制的方法, 质量流(或前馈)及事后厚度控制(或 反馈).通常有两个开关或按钮.在控制台 上来选择运行方式.一是自动或手动选择. 在手动方式,只有操作人员才能作螺钉校 准.在自动方式,厚度控制是由其他选择设 备的状态决定的.当处于自动控制时,电脑 会根据反馈变动来作压下校正.操作人员 可用操纵杆暂时超控螺钉的动作.
20辊轧机AGC控制原理及方法介绍
一.设备构成和主要作用
由置于出口和入口两侧的测厚仪,测出带 钢厚度,反馈到高速的计算机系统,再 去控制一个“电--液压”系统来实现对 带钢厚度的控制。
主要构成: 测厚仪 “电—液压”系统
高速计算机系统
1.测厚仪
• -镅射源(3居里) -指示灯 -检波器 • C形支架安置在轧机两侧包括: • 电气主控制包括: • -计算机 -系统输入与输出 • -彩色触摸屏 • -侧面像测量及显示软件 • 射源和微感应仪固定在一个C形支架的前
•
AGC错误
• 这是一设进厚度控制回路的安全性能,每个校正 系统将测速仪得的压下量与设定测厚仪所测的 压下量比较,如果计算出的压下量不在规定的范 围之内,那么系统假设测厚仪读数有问题并不执 行校正.如果一行内发生9次,那么AGC系统关闭 自动方式并显示系统错误.如果测厚仪出故障或 在带钢上打滑,就会发生这种情况.探测这种错 误会防止厚度控制而引起的损伤.如果发生瞬间 打滑,并少于9次,那么厚度 控制在这周期内不会 移动螺杆,并保持在自动状态内.要复位厚度控 制,就将控制于手动,然后返回自动
AGC

新型轧机系统是机、电、液、气、仪一体化的大型复杂系统,其结构与功能的复杂性决定了故障机理的复杂性以及故障诊断的困难度。轧机系统高精度与高可靠性要求使故障诊断任务更加艰巨。
这一章根据作者在轧机液压系统设计分析、故障诊断与维修领域的长期实践与积累,对现代新型轧机液压故障的症状、原因,以及故障分析的过程和方法等进行总结与提炼。主要是概括轧机控制系统(AGC系统、CVC系统、弯辊系统、活套系统)的常见故障,整理故障分析的基本思路与程序、列出故障树,并总结出故障症状与原因的关系。同时,也对轧机液压控制故障与产品质量的关系进行分析。上述内容是轧机智能诊断与监测系统的主要专家知识。
4、油缸卡死,驱动电流不为零
5、电气断线,驱动电流为零
3.2 CVC液压故障与分析
3.2.1 CVC液压故障概述
CVC主要故障有:
1) 位置传感器故障。BA给定位置设定信号,CVC油缸位移不到位,主要有:单个位置传感器测量值>极限位,或控制过程中位置传感器输出信号不变,即可能位置传感器故障;同一个辊两个位置传感器位置差|E-A|>5mm,报警;上、下两辊||UP|-|DOWN||>2mm,封锁。可能故障:液压伺服系统零点漂移、油缸卡滞等。分析位移偏差量的变化趋势。
伺服阀寿命性故障 伺服阀零偏电流趋势增大,对零偏电流I趋势分析
伺服阀突发性故障 油缸位置无法控制或偏向某一端,零偏电流突然增大
溢流阀调压力过高 当伺服系统发生故障时,可能引起油缸压力过高
溢流阀调压力过低 当伺服系统发生故障时,可能引起油缸压力过低
溢流阀损坏 压力建立不起,或起不到溢流作用
机械与电气零点不一致 伺服系统驱动零偏电流增大
6) 调节器封锁:系统应符合CVC功能投入条件,如:硬件好,传感器没有故障;开关自动状态;BA硬件好(油库准备好)等。否则调节器封锁。
AGC控制
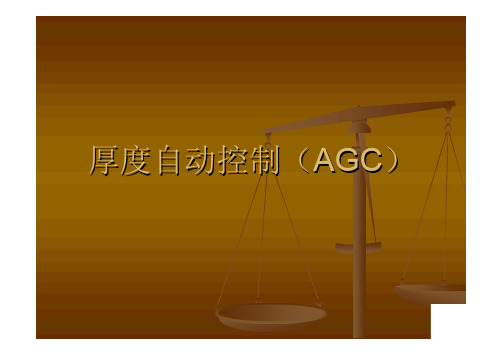
1、厚度自动控制基础
1.1P-h图的建立和运用 板带轧制过程既是轧件产生塑性变形的
过程,也是轧机产生弹性变形(即所谓弹 跳)的过程。由于轧机的弹跳,使轧出的 带材厚度h等于轧辊的理论空载S’0缝加轧机 的弹跳值。按照虎克定律,轧机弹性变形 与应力成正比,则弹跳值为P/CP
1.2冷轧带钢厚差产生的原因
位置内环、厚度外环和轧制力内环、厚度外环 的控制算法不同,将在下面分别叙述。位置内环、 厚度外环是根据厚差控制轧辊的位置到一定的目标 值;而轧制力内环、厚度外环是根据厚差控制轧制 压力到一定的目标值。
4.张力AGC
上述几种AGC均为压下AGC,但轧制薄而硬 的带材时(M很大),压下调节效率不高,这时 需采用张力AGC进行 厚度控制。
LRU2 F2 event
LRU3 F3 event
LRU4 F4 event
LRU5
F5 event
Old product
U NCOILER - STD1 INTERSTAND 1-2 INTERSTAND 2-3 INTERSTAND 3-4 INTERSTAND 4-5 STD5 - CO ILER
心的影响,为了进一步消除偏心往往在第一机架 或第一、二机架加上偏心控制。由于压下效率随 着带钢厚度减薄,硬度变硬而急剧变小,后面机 架一般不加偏心补偿。
A--幅值 ω--频率 ψ--初相角
从正弦波特性可知,只有两个幅值相等但反 相,频率相等且初相角相同的两个信号相加才能 完全互相抵消,否则:
1)频率不同的正弦信号无法相加,但由于频率与轧 辊转速有关,容易找准;
采用C方式,因为第五机架变形量很 小,轧制力也小,如果用低粗糙度的磨削 辊,就可能会产生打滑现象。所以第五机 架的工作辊应采用粗糙 高的毛化辊。C方 式可以充分满足后道机组对产品表面高粗 糙度的要求,由于第五机架作为平整机使 用,因而可在成品带钢上获得良好的板形。
轧机自动化培训

轧机自动化二个原理自动控制的原理:就是在没有人的参与下,利用外加的设备或装置,(控制装置或控制器)使机器,设备或生产过程的某个工作状态或参数自动的按照预定的规律运行.主要是以反馈理论为基础的自动调节过程。
反馈控制的原理:控制装置对被控装置施加的控制作用,是取自被控量的反馈信息,用来不断修正被控量和控制量之间的偏差从而实现对被控量进行控制的任务,这就是反馈控制的原理。
现代的轧机设计在自动化领域的要求越来越高,稳定性,精度,人性化等各个方面的发展都到了很高的程度,轧机自动化主要包括以下几个方面:传动方面一:硬件组成1.系统组成:高压配电室,变压器,功率补偿系统,低压配电室,低压开关柜,控制单元柜,功率单元柜,系统控制柜,继电器柜,2.各控制柜的的作用:高压柜:主要作用为了启停工厂的高压电源,显示高压电压和电流数值,高压计量3.变压器:主要作用为将高压变电所来的高压变成工厂需要的电压值,4.低压开关柜:为各设备提供抵压电源5.系统控制柜:为传动系统总控制,系统启动停止,数据计算,各单元协调运行6.继电器柜:主要为PLC数字量输出实现电源转换7.继电系统柜:主要控制一些普通电机如泵,风机等的运行控制。
8.主电机控制柜:为轧机的主要电机进行单元控制9.功率单元柜:主要电机控制的功率输出二:各主要低压柜的组成1低压开关柜内主要由:刀开关,自动开关,起停线路,显示2系统控制柜由可编程序控制器,(电源模块,中央处理单元,数字量输入输出模块,模拟量输入输出,高速计数模块,定位模块,连接模块,通讯模块,槽板)供电空开,直流电源3继电器柜由24伏或220伏继电器(根据要求选择开闭点数目),电源开关,直流电源4主要电机控制单元柜,由直流电源电机控制器或矢量型变频器,(控制板,电枢电源触发板,励磁控制板,励磁功率主回路,通讯板,卷经控制板,编码器信号接收板等)直流开关电源,工作电源开关,(变频器有整流板及逆变触发板)5功率单元柜由电抗器,冷却风机,整流调压单元(可控硅及散热片,)(变频器为快速双向可控硅IGBT)扩容的外加有过压保护线路,换向保护线路三控制思路先确定一个自动控制系统的重要组成部分PID控制理念PID控制器(比例-积分-微分控制器),由比例单元 P、积分单元 I 和微分单元 D 组成。
轧机机架AGC控制

轧机一机架AGC控制前面已经讲过AGC控制系统的组成和控制方式。
下面以一机架为例具体讲解。
一、概述冷轧轧机使用的是日立设计的UCM轧机。
其AGC控制可分为两大部分:一机架的压下控制和2-4机架的精调速度AGC控制。
来料的缺陷基本上可在一机架消除。
一机架控制的好坏将直接影响到产品的质量。
所以,在本AGC系统中一机架采用了多种控制手段,其目的就是尽可能使一机架出口厚差最小。
一.一机架控制概况为了保证一机架的带钢出口厚度,在一机架中AGC采用了如下多种控制方法。
●前馈控制(FF)●虚拟测厚仪控制(GM SMITH)●反馈控制(FB)●轧机弹性系数控制(BISRA)●支撑辊偏心控制(REC)其中,前馈控制和BISRA属于预控AGC,而它们的控制方法又完全不相同,前馈控制是利用一机架前的测厚仪直接检测厚差#1 机架图1 一机架AGC控制构成进行控制,而BISRA则利用LOADCELL检测轧制力的变化,通过快速响应的控制系统实现对来料厚差的控制。
GM-SMITH是属于监控AGC,它不仅具有反馈控制的稳定性而且还克服了反馈控制的滞后性,在低速时监控效果则更好。
这是由于出口测厚仪与一机架之间有2.75米的固定距离,所以,从出口测厚仪所测的实际值在时间上要滞后一段时间,特别在低速时这段时间相对就比较长。
反馈控制就是利用出口测厚仪进行检测和控制的,所以无法克服这滞后时间。
而GM-SMITH则利用轧制力间接计算出一机架的出口厚差进行控制,再利用出口测厚仪进行修正,所以,与反馈控制相比它就克服了这段滞后时间。
在高速轧制时,由于这段滞后时间相对比较短,已不影响监控效果,所以就直接用反馈控制。
所以,反馈控制和GM-SMITH 的切换控制,弥补了仅用反馈控制在低速时的不足,使一机架的监控效果更佳。
支撑辊偏心控制则用于补偿由于支撑辊偏心而引起的一机架出口厚度偏差。
此控制方式没有投入。
通过这几种控制方式的共同作用,使一机架出口厚差最小化。
轧机AGC培训资料
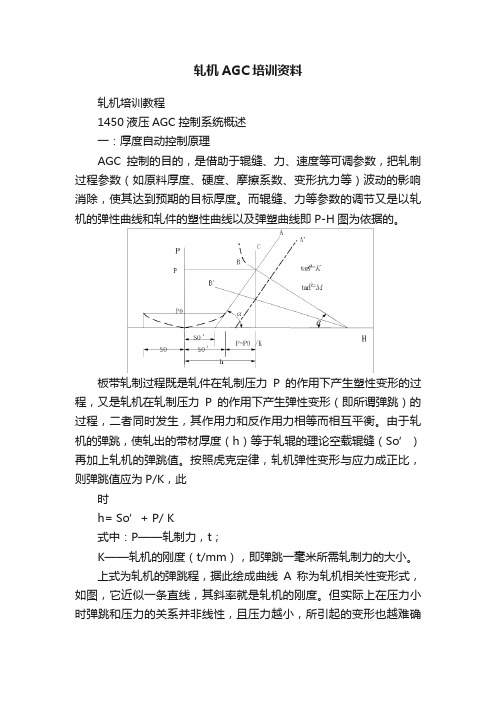
轧机AGC培训资料轧机培训教程1450液压AGC控制系统概述一:厚度自动控制原理AGC控制的目的,是借助于辊缝、力、速度等可调参数,把轧制过程参数(如原料厚度、硬度、摩擦系数、变形抗力等)波动的影响消除,使其达到预期的目标厚度。
而辊缝、力等参数的调节又是以轧机的弹性曲线和轧件的塑性曲线以及弹塑曲线即P-H图为依据的。
板带轧制过程既是轧件在轧制压力P的作用下产生塑性变形的过程,又是轧机在轧制压力P的作用下产生弹性变形(即所谓弹跳)的过程,二者同时发生,其作用力和反作用力相等而相互平衡。
由于轧机的弹跳,使轧出的带材厚度(h)等于轧辊的理论空载辊缝(So’)再加上轧机的弹跳值。
按照虎克定律,轧机弹性变形与应力成正比,则弹跳值应为P/K,此时h= So’+ P/ K式中:P——轧制力,t;K——轧机的刚度(t/mm),即弹跳一毫米所需轧制力的大小。
上式为轧机的弹跳程,据此绘成曲线A称为轧机相关性变形式,如图,它近似一条直线,其斜率就是轧机的刚度。
但实际上在压力小时弹跳和压力的关系并非线性,且压力越小,所引起的变形也越难确定,亦即辊缝的实际零位很难确定。
为了消除这一非线性区段的影响,实际操作中可将轧辊预先压靠到一定程度,即压到一定的压力P。
然后将此时的辊缝批示定为零位,这就是所谓“零位调整”。
由图可看出:h= S0+(P-P0)/K式中S0——考虑预压变形的相当空载辊缝另一面,给轧件一定的压下量(h0-h),就产生一定的压力(P),当料厚(h0)一定,h越小即是压下量越大,则轧制压力也越大,通过实测或计算可以求出对应于一定h值的P 值,在图上绘成曲线B,称为轧件塑性变形线。
B线与A线交点的纵坐标即为轧制力P,横坐标即为板带实际厚度h。
由P-H图可以看出,如果B线发生变形(变为B’),则为了保持厚度h不变,就必须移动压下位置,使A 线移到A’,使A’和B’的交点的横坐标不变,亦即须使A线与B线的交点始终在一条垂直线C上。
厚度自动控制AGC课件

当轧件出口厚度增大时,增加 张力,降低轧制压力,减小轧辊
S K M h K
弹跳,使轧件出口厚度变小,回到
目标值。张力调节量和轧件厚差的
关系可通过弹跳方程和压力方程的
联解得到。
h S P K
P P h P T h T
图14 软硬金属对轧辊调节量的影响
(a) 厚软金属;(b) 薄硬金属
由上两式可以解出:
反馈AGC的主要缺点是,实际调厚的点不是所检测之处,存在滞 后现象。
反馈AGC的控制量为:
S K M h K
3.4 GM-AGC
为了减小反馈AGC的滞后,可以利用机架作为“侧厚仪”测量轧
出厚度,根据实测的轧制压P力* 、辊S*缝 等值,用弹跳 P0 O G K
P
图1 P-h图(弹塑性曲线)
P
M K
0
S
S(h)
h
H
图2 P-h图
P-h图在定性上比较直观,是目前讨论厚差和厚度控制现象的一个 有用工具。由于轧出厚度h即为“有载”辊缝值,因此在横坐标h上亦 很清楚地表达了“空载”辊缝值So,轧出厚度h和机座弹跳量。这样在 P—h图上可以同时表达出轧机弹性变形和轧件塑性变形的情况。
图10 S 和h 的关系
3.AGC
S ab
h cb
tan K
tan M
ab ac cb cd cd cd ( 1 1 ) cd ( K M )
tan tan
KM
KM
cb cd M
cd
h S
cb ab
M cd (K
M)
K
K M
KM
h K S
K M
K=Cp,轧机刚度系数,t/mm;M=Q,轧件塑性系数,t/mm。
- 1、下载文档前请自行甄别文档内容的完整性,平台不提供额外的编辑、内容补充、找答案等附加服务。
- 2、"仅部分预览"的文档,不可在线预览部分如存在完整性等问题,可反馈申请退款(可完整预览的文档不适用该条件!)。
- 3、如文档侵犯您的权益,请联系客服反馈,我们会尽快为您处理(人工客服工作时间:9:00-18:30)。
轧机培训教程1450液压AGC控制系统概述一:厚度自动控制原理AGC控制的目的,是借助于辊缝、张力、速度等可调参数,把轧制过程参数(如原料厚度、硬度、摩擦系数、变形抗力等)波动的影响消除,使其达到预期的目标厚度。
而辊缝、张力等参数的调节又是以轧机的弹性曲线和轧件的塑性曲线以及弹塑曲线即P-H图为依据的。
板带轧制过程既是轧件在轧制压力P的作用下产生塑性变形的过程,又是轧机在轧制压力P的作用下产生弹性变形(即所谓弹跳)的过程,二者同时发生,其作用力和反作用力相等而相互平衡。
由于轧机的弹跳,使轧出的带材厚度(h)等于轧辊的理论空载辊缝(So’)再加上轧机的弹跳值。
按照虎克定律,轧机弹性变形与应力成正比,则弹跳值应为P/K,此时h= So’+ P/ K式中:P——轧制力,t;K——轧机的刚度(t/mm),即弹跳一毫米所需轧制力的大小。
上式为轧机的弹跳方程,据此绘成曲线A称为轧机相关性变形式,如图,它近似一条直线,其斜率就是轧机的刚度。
但实际上在压力小时弹跳和压力的关系并非线性,且压力越小,所引起的变形也越难确定,亦即辊缝的实际零位很难确定。
为了消除这一非线性区段的影响,实际操作中可将轧辊预先压靠到一定程度,即压到一定的压力P。
然后将此时的辊缝批示定为零位,这就是所谓“零位调整”。
由图可看出:h= S0+(P-P0)/K式中S0——考虑预压变形的相当空载辊缝另一方面,给轧件一定的压下量(h0-h),就产生一定的压力(P),当料厚(h0)一定,h越小即是压下量越大,则轧制压力也越大,通过实测或计算可以求出对应于一定h值的P 值,在图上绘成曲线B,称为轧件塑性变形线。
B线与A线交点的纵坐标即为轧制力P,横坐标即为板带实际厚度h。
由P-H图可以看出,如果B线发生变形(变为B’),则为了保持厚度h不变,就必须移动压下位置,使A线移到A’,使A’和B’的交点的横坐标不变,亦即须使A线与B线的交点始终在一条垂直线C上。
因此,板带厚度控制实质就是不管轧制条件如何变化,总要使A线和B线交到C线上,这样就可得到恒定厚度的板带材,由此可见,P-h图的运用实际上是板带厚度控制的基础。
二. AGC的控制系统AGC的目的是消除厚差,则首先必须检测到轧制过程中的带钢的厚差时,然后再采取措施消除这一厚差。
因此,归纳为两个基本构成:a.厚度偏差的检测,目的是掌握轧制过程中,每时每刻带钢的厚度偏差的大小。
b.厚度偏差的消除:根据厚度偏差的大小,计算出调节量,输出控制信号,然后根据控制信号,调节机构动作,完成调节过程,见下图1.测量方式在厚度偏差检测当中,有直接测厚和间接测厚两种方式。
直接测量法的主要缺点是存在时间滞后问题。
为解决此问题,采用间接测厚法。
其间接测厚方式有压力测厚、张力测厚等。
间接测量的方法虽然精度较低,但传递时差小,设备简单,便于维修,故被广泛采用。
2.控制手段a. 调节压下量,即改变辊缝是AGC控制的主要方式。
一般用来消除因轧制压力的波动而造成的厚度偏差。
b. 通过改变带钢的张力来改变轧件变形抗力即塑性曲线B的斜率以实现厚度控制的目的,则称为调节张力的厚调方式。
c. 轧制速度的变化将影响到张力、摩擦系数等的变化,即影响轧制压力的变化。
故可通过调速来改变轧制压力以实现厚度自动控制的目的。
3.控制系统冷连轧AGC的形式和种类繁多,按一般调节系统的分类方法,可分为前馈AGC和反馈AGC两大类。
前馈AGC是根据轧前所测得的外扰量(原料厚度偏差δH0或温度偏差δt)来调节的。
反馈AGC是根据测量轧制之后的带钢厚度偏差来进行调节的。
根据构成AGC的两个基本环节即测量厚度偏差的方法和调节方式的不同,一般可将AGC 分为如下几种:a. 厚度AGC(h-AGC)亦称反馈AGC,它是利用测厚仪直接测量轧制之后带钢的厚度偏差δh,调节轧辊辊缝S的AGC。
b. 前馈或预控AGC(H-AGC),测量轧制前带钢厚度偏差δH,调节轧辊辊缝S的AGC,简称前馈或预控AGC。
单机架可逆式轧机最基本的厚度控制环节是前馈AGC、反馈AGC和秒流量AGC。
▲前馈AGC(H-AGC),测量轧制前带钢厚度(来料)偏差δH,调节轧辊辊缝S的AGC ,简称前馈或预控AGC。
△S=△h0×(G/K)式中:△S—辊缝调节,△h0—入口带钢厚度偏差,G,K分别为带钢塑性刚度系数和轧机刚度系数▲反馈AGC(h-AGC),是利用测厚仪直接测量轧制之后带钢的厚度偏差δh,调节轧辊辊缝S 的AGC 。
△S=△h1×(1+G/K)式中:△S—辊缝调节,△h1—出口带钢厚度偏差,G,K分别为带钢塑性刚度系数和轧机刚度系数▲秒流量AGC,轧制时,轧件在轧机机架的秒流量的维持不变,即:h1v1=h2v2 =常数以上所述都是轧机一些常规的控制理论,下面我们将针对我们公司轧机AGC控制进行讲解。
三.1450液压AGC的设计1:厚度控制器系统硬件组成:液压AGC系统主要由一套SIMADYN D控制装置(FM458)、检测仪表(包括位移、压力、厚度、速度的检测)、伺服系统、压上缸等设备组成,完成压下辊缝、压力及AGC,实现带材厚度的控制。
2:厚度控制系统厚度控制系统主要由液压HGC和AGC组成,而HGC可以分为液压APC(位置控制)、压力控制两种。
AGC控制系统可以分为:前馈AGC,反馈AGC,秒流量AGC,张力AGC,以及偏心补偿,等闭环控制,AGC辅助控制功能包括压下量微调、倾斜控制、辊缝同步控制、预压靠等功能。
(1):液压HGC(1.1)液压APC(位置控制)的组成:在液压缸内安装位移传感器,用于检测实际辊缝,在位置控制方式下,每个液压缸的位置值将与计算的目标值相比较,此比较的偏差经特定运算后,送到伺服阀去引起液压油的流动以使位置偏差减少到零。
(1.2)压力控制的组成在轧制力控制方式下,轧制力控制器用来使冷轧机两侧油缸的轧制力和实测值保持与设定值一致。
根据油缸的积分特性,将轧制力控制器设计成一个比例控制器。
轧制力测量方法有压头直接测量和压力传感器间接测量两种。
当采用压力传感器方法时,传感器分别安装在液压缸活塞侧和活塞杆侧,测量的是油的压力,与活塞的面积相乘得出轧制力,总轧制力为两侧压力和减去油缸活塞杆测的压力、弯辊力的影响及轧辊平衡力,我们系统暂时活塞杆侧压力检测没有参与控制使用的是固定值906KN。
(2)液压AGC(2.1)前馈AGC前馈AGC根据轧制入口侧测厚仪测得的入口厚度偏差,经过一定的延时后对辊缝进行修正,以消除入口厚度变化对轧出厚度的影响,延时时间是根据入口侧测速脉冲编码器或激光测速仪的速度信号确定的。
前馈控制比较由轧机入口测厚仪测量的厚度值和设定的带钢厚度值之间的偏差,并对偏差信号从测厚仪到辊缝进行跟踪。
即将偏差信号保存到缓冲区,并在该偏差信号的测量点到达辊缝时取出并转换成位置偏置,通过对辊缝大小的调节实现对带钢入口厚度偏差的校正。
为将入口带钢偏差信号精确地从入口测厚仪位置跟踪到辊缝位置,需要考虑以下因素:◆测厚仪的响应时间◆带钢从测厚仪到辊缝之间的移动时间◆液压伺服缸的位置调节时间◆控制器执行时间前馈控制同样根据轧机模数和轧件模数以及厚度方程将偏差信号转换成合适的位置偏置。
△S=△h0×(G/K)式中:△S—辊缝调节,△h0—入口带钢厚度偏差,G,K分别为带钢塑性刚度系数和轧机刚度系数。
(2.2)反馈AGC我们系统中的反馈AGC是指厚度偏差的反馈,它是监控AGC中的一种。
而张力AGC也是监控AGC中的一种。
事实上监控AGC包含以下几种:张力监控,轧制力监控,加速度监控和位置监控。
测得的出口厚度偏差,对辊缝进行修正,使出口厚度达到目标值。
由于测厚仪安装于距轧机一定距离的位置上,是典型的纯滞后控制系统,采用Smith预估补偿器改善系统的动静态特性,滞后时间是根据出口侧测速脉冲编码器或激光测速仪的速度信号确定的。
因此只可能采用调节速度较低的积分控制器来校正厚度的偏差。
也就是说,反馈控制只能校正长期的厚度偏差。
根据轧机模数和轧件模数以及厚度方程将偏差信号转换成合适的位置偏置。
△S=△h1×(1+G/K)式中:△S—辊缝调节,△h1—出口带钢厚度偏差,G,K分别为带钢塑性刚度系数和轧机刚度系数。
(2.3)秒流量AGC根据轧制过程中流入轧机与流出轧机的带钢质量恒定的原理,计算出正在轧制带材的厚度偏差,以此偏差对辊缝进行修正,使轧机轧出的带材保持较好的一致性。
流量AGC基于下述公式:V1h1 =V0 h0加入厚度偏差的公式:V1(h1+Δh1)= V0 (h0+ Δh0)Δh1 = ((h0+Δh0)* V0/V1)- h1V0 :入口带速度V1 :出口带速度h0 :入口厚度设定h1 :出口厚度设定Δh0 :入口厚度偏差Δh1 :出口厚度偏差ΔS :位置的改变量即通过测量带材的入口速度V0和出口速度V1以及出入口厚度h0,则出口厚度偏差Δh 就被确定。
为此需要有对机架两侧的速度和厚度进行动态和精确测定的测量仪表。
预测轧机出口带钢的厚度,并与设定的出口厚度比较,将其差值转换成合适的辊缝控制器的偏置ΔS。
流量AGC提供了较其它AGC方式更为有效的厚度补偿方法,如果与监控AGC控制方式相配合将是最有效的厚度控制方案。
△S=△h1×(1+G/K)式中:△S—辊缝调节,△h1—出口带钢厚度偏差,G,K分别为带钢塑性刚度系数和轧机刚度系数。
(3)预压靠控制(液压压下位置零点的标定)由于辊缝取决于工作辊的相对位置,因此在每次换辊后须重新确定辊缝的零点,即需要进行轧辊预压靠。
预压靠过程由操作工按下预压靠按钮启动,之后的预压靠全过程将自动进行,此时,压下装置,传动装置等相关设备均处于自动受控状态,并且相互联锁。
预压靠开始后,液压压下系统自动驱动轧辊相接触,并达到一个预定压力,然后,传动系统投入工作,使轧辊以慢速转动(120m/min),同时继续使轧辊达到预先设定的预压靠力,并在此时将轧辊位置设置为零,预压靠工作完成,此时将轧辊上抬,传动系统停止工作。
预压靠过程是位置控制和压力控制相互切换的过程,轧辊运动时,在位置控制方式,当轧辊相接触后,自动切换到压力控制方式。
(4)倾斜控制1:倾斜控制器优先级最高,它是直接作用在位置控制器和轧制力控制器的输出端,也就是直接作用在伺服阀的输入端。
2:由于轧机传动侧、操作侧的液压缸之间没有机械上的联结,而且两侧负载不可能完全相同,设备的动态特性也不完全一致,因此两侧的运动不能保持同步,同步控制的目的就是使位移慢的一侧加快运动,位移快的一侧减慢运动,使两侧的运动速度保持一致。
系统中采用辊缝差信号进行闭环控制。
(5)AGC增益自适应在轧制过程中,随着轧制道次的增加,带材的硬度逐渐增大,压下效率逐渐减小,AGC 的增益需要逐渐增大,以保证AGC系统的动态响应速度。