锂电池浆料干法混料
锂电池湿法制浆工艺和干法制浆工艺的方法及优缺点
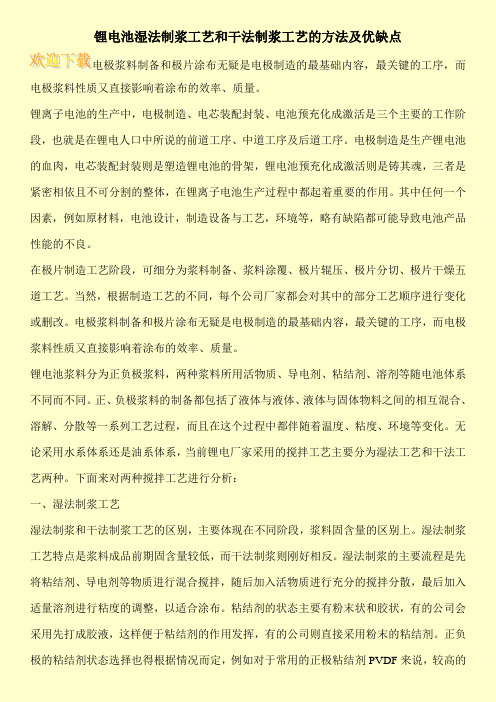
锂电池湿法制浆工艺和干法制浆工艺的方法及优缺点电极浆料制备和极片涂布无疑是电极制造的最基础内容,最关键的工序,而电极浆料性质又直接影响着涂布的效率、质量。
锂离子电池的生产中,电极制造、电芯装配封装、电池预充化成激活是三个主要的工作阶段,也就是在锂电人口中所说的前道工序、中道工序及后道工序。
电极制造是生产锂电池的血肉,电芯装配封装则是塑造锂电池的骨架,锂电池预充化成激活则是铸其魂,三者是紧密相依且不可分割的整体,在锂离子电池生产过程中都起着重要的作用。
其中任何一个因素,例如原材料,电池设计,制造设备与工艺,环境等,略有缺陷都可能导致电池产品性能的不良。
在极片制造工艺阶段,可细分为浆料制备、浆料涂覆、极片辊压、极片分切、极片干燥五道工艺。
当然,根据制造工艺的不同,每个公司厂家都会对其中的部分工艺顺序进行变化或删改。
电极浆料制备和极片涂布无疑是电极制造的最基础内容,最关键的工序,而电极浆料性质又直接影响着涂布的效率、质量。
锂电池浆料分为正负极浆料,两种浆料所用活物质、导电剂、粘结剂、溶剂等随电池体系不同而不同。
正、负极浆料的制备都包括了液体与液体、液体与固体物料之间的相互混合、溶解、分散等一系列工艺过程,而且在这个过程中都伴随着温度、粘度、环境等变化。
无论采用水系体系还是油系体系,当前锂电厂家采用的搅拌工艺主要分为湿法工艺和干法工艺两种。
下面来对两种搅拌工艺进行分析:一、湿法制浆工艺湿法制浆和干法制浆工艺的区别,主要体现在不同阶段,浆料固含量的区别上。
湿法制浆工艺特点是浆料成品前期固含量较低,而干法制浆则刚好相反。
湿法制浆的主要流程是先将粘结剂、导电剂等物质进行混合搅拌,随后加入活物质进行充分的搅拌分散,最后加入适量溶剂进行粘度的调整,以适合涂布。
粘结剂的状态主要有粉末状和胶状,有的公司会采用先打成胶液,这样便于粘结剂的作用发挥,有的公司则直接采用粉末的粘结剂。
正负极的粘结剂状态选择也得根据情况而定,例如对于常用的正极粘结剂PVDF来说,较高的。
磷酸铁锂动力电池上料搅拌设备培训
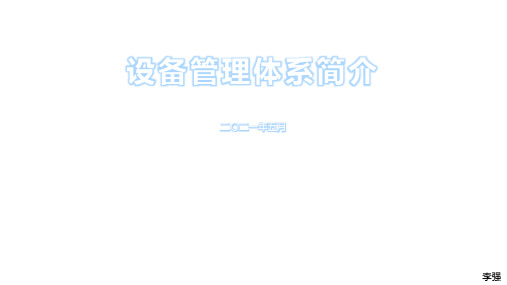
一、上料、搅拌工艺流程 1.2 匀浆系统设备流程图 1.2.1 匀浆系统正极流程图
三层 二层
PVDF
储存罐
SP 预留设备
储存罐
储存罐
发送罐
发送罐
发送罐
主材1 主材2(预留位置) 主材1
储存罐
储存罐
储存罐
主材2(预留位置) 储存罐
隔膜泵上料
隔膜泵上料
发送罐
发送罐
CNTs计 量罐
预留计量 罐
管道来料 NMP罐
目前,电极浆料的混料工艺主要分为两种: 湿法混料工艺,基本过程为溶胶-混合导电剂-混合活物质 -稀释。
干法混料工艺,基本过程为活物质、导电剂和黏结剂干 粉混合-加入适量溶剂润湿-加入溶剂高速分散破碎-稀释 调节粘度。
我厂现采用干法混料工艺 干法制浆的工艺流程是首先将活物质、导电剂等粉末物 质在一定速度下进行预混合。混合完了之后加入粘结剂 ,进行混合搅拌,逐步加入溶剂进行混合、分散,最后 加入一定量溶剂进行稀释调节到涂布所需要的粘度。
二、设备空间布局 1600L PD搅拌机最大占地面积示意图
03
上料设备各单元简介
三、上料设备各单元简介
3.1 主材上料系统
➢主粉料原料包装为吨袋,通过洁净行吊提升至 吨袋投料站解包投料,过筛除铁后重力落料至 存储计量罐,根据配方需求,通过减重计量的 方式由螺旋喂料器喂料至复核计量罐,复核重 量后由气动比例蝶阀出料,自重落料至搅拌机
固体粉料在液体中的分散过程可以分为三个阶段,如 图所示。干法制浆工艺与湿法工艺的不同之处是第二阶 段物料之间、设备与物料之间存在较大的内摩擦力,在 各方面作用力下,物料可以达到很好的分散状态。浆料 分散程度高,对极片的质量是有利的。同时干法混料工 艺显著缩短了搅拌工艺时间。
锂电池湿法制浆与干法制浆工艺对比分析

锂电池湿法制浆与干法制浆工艺对比分析一、原理及工艺流程对比1.湿法制浆原理及工艺流程:湿法制浆主要是通过将原料和溶剂混合,形成浆料后进行磨浆。
工艺流程通常包括原料配料、搅拌混合、研磨、过滤、干燥等步骤。
2.干法制浆原理及工艺流程:干法制浆主要是将原料进行研磨后,通过机械力或喷射力将原料分散成粉末,然后进行精磨、筛分等工艺步骤。
从原理上看,湿法制浆是通过添加溶剂来使原料湿润,有助于研磨和分散,而干法制浆则是通过机械力或喷射力直接将原料分散成粉末。
两种工艺在工艺流程上主要区别在于其中涉及的具体步骤和操作顺序。
二、能耗对比1.湿法制浆的能耗:湿法制浆相对于干法制浆来说,能耗要高一些。
主要原因是在湿法制浆中需要耗费能量来加热和蒸发溶剂,同时还需要进行过滤和干燥等工序。
2.干法制浆的能耗:干法制浆相对于湿法制浆来说,能耗较低。
主要原因是在干法制浆中不需要加热和蒸发溶剂,而且无需过滤和干燥等工序。
从能耗角度来看,干法制浆具有较大的优势,能够节约能源和降低成本。
三、产品性能对比1.湿法制浆的产品性能:湿法制浆可以通过控制溶剂的使用和磨浆条件来调节产品性能。
由于溶剂的加入,湿法制浆可以得到较好的分散性和可塑性,提高材料的流动性和压片性能。
2.干法制浆的产品性能:干法制浆的产品性能受到原料的粒度和分散程度的限制。
虽然干法制浆产品的分散性和可塑性相对较差,但产品的比表面积较大,有利于提高材料的电导性和反应活性。
从产品性能角度来看,湿法制浆在可塑性和流动性方面更优,而干法制浆在电导性和反应活性方面更优。
四、环保对比1.湿法制浆的环保程度:湿法制浆需要使用溶剂和水作为浆料的介质,会产生一定的废水和废溶剂。
此外,湿法制浆还需要进行过滤和干燥等工序,需要额外处理这些固体废物。
2.干法制浆的环保程度:干法制浆不需要使用溶剂和水作为浆料的介质,不会产生污水和废溶剂。
同时,由于干法制浆省去了过滤和干燥等工序,也减少了固体废物的产生。
锂电池负极浆料配比
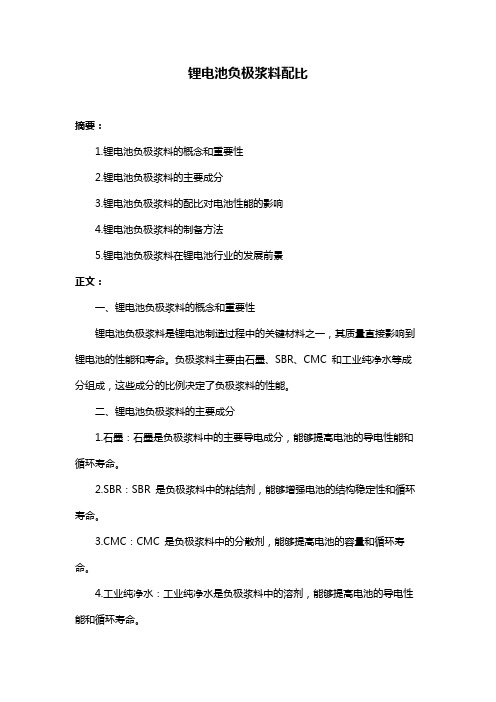
锂电池负极浆料配比
摘要:
1.锂电池负极浆料的概念和重要性
2.锂电池负极浆料的主要成分
3.锂电池负极浆料的配比对电池性能的影响
4.锂电池负极浆料的制备方法
5.锂电池负极浆料在锂电池行业的发展前景
正文:
一、锂电池负极浆料的概念和重要性
锂电池负极浆料是锂电池制造过程中的关键材料之一,其质量直接影响到锂电池的性能和寿命。
负极浆料主要由石墨、SBR、CMC 和工业纯净水等成分组成,这些成分的比例决定了负极浆料的性能。
二、锂电池负极浆料的主要成分
1.石墨:石墨是负极浆料中的主要导电成分,能够提高电池的导电性能和循环寿命。
2.SBR:SBR 是负极浆料中的粘结剂,能够增强电池的结构稳定性和循环寿命。
3.CMC:CMC 是负极浆料中的分散剂,能够提高电池的容量和循环寿命。
4.工业纯净水:工业纯净水是负极浆料中的溶剂,能够提高电池的导电性能和循环寿命。
三、锂电池负极浆料的配比对电池性能的影响
锂电池负极浆料的配比对电池性能有重要影响。
如果配比不合理,会导致电池的容量、循环寿命和安全性能下降。
因此,合理调整负极浆料的配比是提高锂电池性能的关键。
四、锂电池负极浆料的制备方法
锂电池负极浆料的制备方法主要包括湿法和干法两种。
湿法主要是将石墨、SBR、CMC 等成分加入到工业纯净水中,通过搅拌和分散等工艺制备而成。
干法则是将石墨、SBR、CMC 等成分直接混合,通过热处理等工艺制备而成。
五、锂电池负极浆料在锂电池行业的发展前景
随着电动汽车、移动设备等市场的快速发展,对锂电池的需求越来越大。
一文带你看懂锂电池匀浆工序
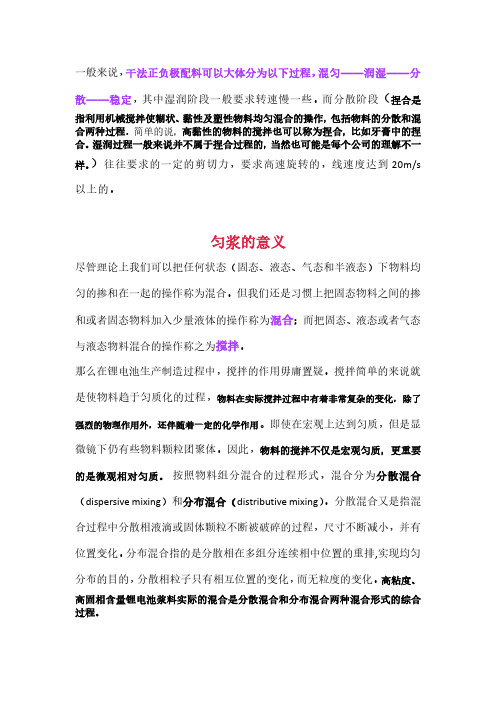
一般来说,干法正负极配料可以大体分为以下过程,混匀——润湿——分散——稳定,其中湿润阶段一般要求转速慢一些。
而分散阶段(捏合是指利用机械搅拌使糊状、黏性及塑性物料均匀混合的操作,包括物料的分散和混合两种过程。
简单的说,高黏性的物料的搅拌也可以称为捏合,比如牙膏中的捏合。
湿润过程一般来说并不属于捏合过程的,当然也可能是每个公司的理解不一样。
)往往要求的一定的剪切力,要求高速旋转的,线速度达到20m/s以上的。
匀浆的意义尽管理论上我们可以把任何状态(固态、液态、气态和半液态)下物料均匀的掺和在一起的操作称为混合。
但我们还是习惯上把固态物料之间的掺和或者固态物料加入少量液体的操作称为混合;而把固态、液态或者气态与液态物料混合的操作称之为搅拌。
那么在锂电池生产制造过程中,搅拌的作用毋庸置疑。
搅拌简单的来说就是使物料趋于匀质化的过程,物料在实际搅拌过程中有着非常复杂的变化,除了强烈的物理作用外,还伴随着一定的化学作用。
即使在宏观上达到匀质,但是显微镜下仍有些物料颗粒团聚体。
因此,物料的搅拌不仅是宏观匀质,更重要的是微观相对匀质。
按照物料组分混合的过程形式,混合分为分散混合(dispersive mixing)和分布混合(distributive mixing)。
分散混合又是指混合过程中分散相液滴或固体颗粒不断被破碎的过程,尺寸不断减小,并有位置变化。
分布混合指的是分散相在多组分连续相中位置的重排,实现均匀分布的目的,分散相粒子只有相互位置的变化,而无粒度的变化。
高粘度、高固相含量锂电池浆料实际的混合是分散混合和分布混合两种混合形式的综合过程。
锂离子电池浆料分散的主要目的将活性物质,导电剂,粘接剂等按照一定的质量比均匀的分散在溶剂中,形成具有一定黏度的稳定浆料,以用于极片的涂敷,锂离子电池制浆的工艺目的就是为制片做准备。
极片对理想浆料的需求:(i)活物质颗粒细小均匀分散没有团聚,导电剂颗粒形成薄层弥散成导电网络,并最大量地在集流体上互锁连结活物质颗粒(ii)活物质颗粒最好细小,确保电池有高的电流密度。
锂电池合浆机的原理
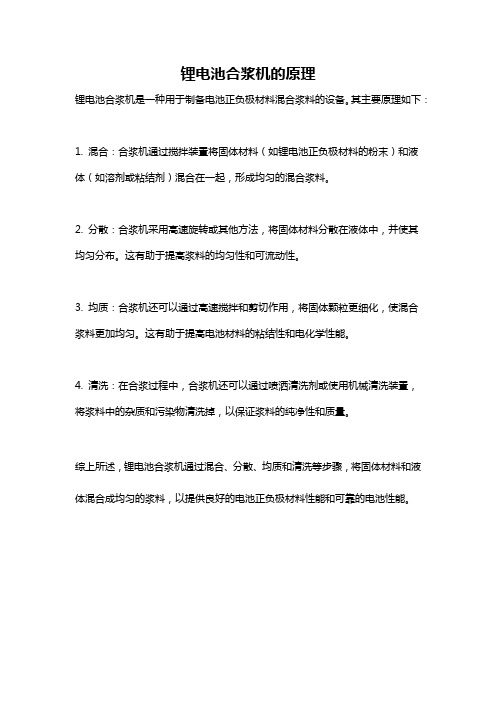
锂电池合浆机的原理
锂电池合浆机是一种用于制备电池正负极材料混合浆料的设备。
其主要原理如下:
1. 混合:合浆机通过搅拌装置将固体材料(如锂电池正负极材料的粉末)和液体(如溶剂或粘结剂)混合在一起,形成均匀的混合浆料。
2. 分散:合浆机采用高速旋转或其他方法,将固体材料分散在液体中,并使其均匀分布。
这有助于提高浆料的均匀性和可流动性。
3. 均质:合浆机还可以通过高速搅拌和剪切作用,将固体颗粒更细化,使混合浆料更加均匀。
这有助于提高电池材料的粘结性和电化学性能。
4. 清洗:在合浆过程中,合浆机还可以通过喷洒清洗剂或使用机械清洗装置,将浆料中的杂质和污染物清洗掉,以保证浆料的纯净性和质量。
综上所述,锂电池合浆机通过混合、分散、均质和清洗等步骤,将固体材料和液体混合成均匀的浆料,以提供良好的电池正负极材料性能和可靠的电池性能。
锂电池制浆工艺发展
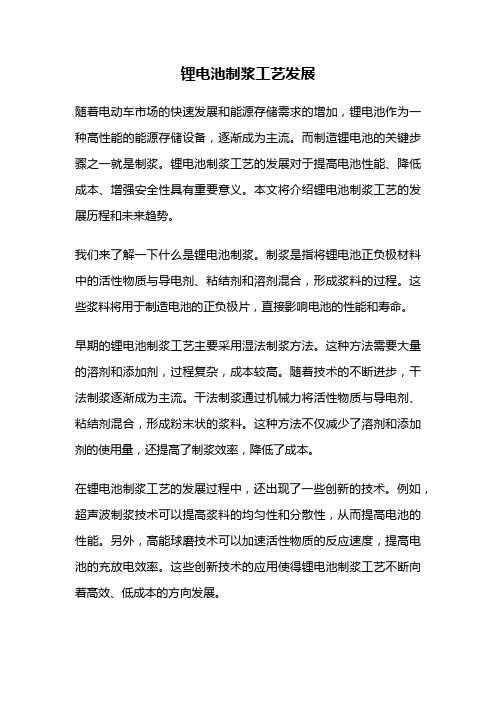
锂电池制浆工艺发展随着电动车市场的快速发展和能源存储需求的增加,锂电池作为一种高性能的能源存储设备,逐渐成为主流。
而制造锂电池的关键步骤之一就是制浆。
锂电池制浆工艺的发展对于提高电池性能、降低成本、增强安全性具有重要意义。
本文将介绍锂电池制浆工艺的发展历程和未来趋势。
我们来了解一下什么是锂电池制浆。
制浆是指将锂电池正负极材料中的活性物质与导电剂、粘结剂和溶剂混合,形成浆料的过程。
这些浆料将用于制造电池的正负极片,直接影响电池的性能和寿命。
早期的锂电池制浆工艺主要采用湿法制浆方法。
这种方法需要大量的溶剂和添加剂,过程复杂,成本较高。
随着技术的不断进步,干法制浆逐渐成为主流。
干法制浆通过机械力将活性物质与导电剂、粘结剂混合,形成粉末状的浆料。
这种方法不仅减少了溶剂和添加剂的使用量,还提高了制浆效率,降低了成本。
在锂电池制浆工艺的发展过程中,还出现了一些创新的技术。
例如,超声波制浆技术可以提高浆料的均匀性和分散性,从而提高电池的性能。
另外,高能球磨技术可以加速活性物质的反应速度,提高电池的充放电效率。
这些创新技术的应用使得锂电池制浆工艺不断向着高效、低成本的方向发展。
未来,锂电池制浆工艺的发展将主要集中在以下几个方面。
首先,绿色环保将成为制浆工艺发展的重要方向。
目前的制浆工艺中使用的溶剂和添加剂对环境有一定的污染,未来需要研发出更环保的替代品。
其次,工艺的自动化和智能化将得到进一步提升。
通过引入机器学习和人工智能等技术,可以实现制浆过程的自动控制和优化,提高生产效率和产品质量。
此外,制浆工艺还需要更好地适应不同类型的电池材料,如硅负极材料和固态电解质材料,以满足不断变化的需求。
锂电池制浆工艺的发展对于电池性能和成本具有重要意义。
随着技术的不断进步和创新,制浆工艺将变得更加高效、低成本和环保。
未来的发展方向包括绿色环保、工艺智能化和适应新材料的需求。
相信在不久的将来,锂电池制浆工艺将取得更大的突破和进展,为电动车和能源存储领域的发展做出更大贡献。
锂电池浆料的制备工艺研究
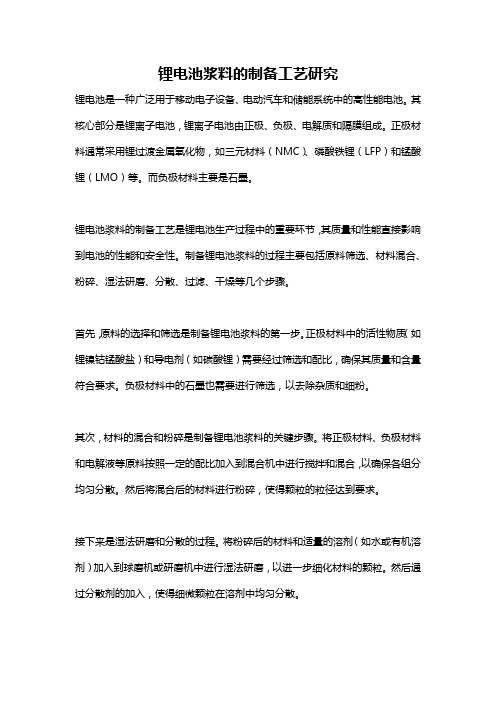
锂电池浆料的制备工艺研究锂电池是一种广泛用于移动电子设备、电动汽车和储能系统中的高性能电池。
其核心部分是锂离子电池,锂离子电池由正极、负极、电解质和隔膜组成。
正极材料通常采用锂过渡金属氧化物,如三元材料(NMC)、磷酸铁锂(LFP)和锰酸锂(LMO)等。
而负极材料主要是石墨。
锂电池浆料的制备工艺是锂电池生产过程中的重要环节,其质量和性能直接影响到电池的性能和安全性。
制备锂电池浆料的过程主要包括原料筛选、材料混合、粉碎、湿法研磨、分散、过滤、干燥等几个步骤。
首先,原料的选择和筛选是制备锂电池浆料的第一步。
正极材料中的活性物质(如锂镍钴锰酸盐)和导电剂(如碳酸锂)需要经过筛选和配比,确保其质量和含量符合要求。
负极材料中的石墨也需要进行筛选,以去除杂质和细粉。
其次,材料的混合和粉碎是制备锂电池浆料的关键步骤。
将正极材料、负极材料和电解液等原料按照一定的配比加入到混合机中进行搅拌和混合,以确保各组分均匀分散。
然后将混合后的材料进行粉碎,使得颗粒的粒径达到要求。
接下来是湿法研磨和分散的过程。
将粉碎后的材料和适量的溶剂(如水或有机溶剂)加入到球磨机或研磨机中进行湿法研磨,以进一步细化材料的颗粒。
然后通过分散剂的加入,使得细微颗粒在溶剂中均匀分散。
完成湿法研磨和分散后,需要对浆料进行过滤,去除其中的固体颗粒和杂质。
通常采用真空过滤或压力过滤的方式进行。
最后是浆料的干燥。
将过滤后的浆料倒入干燥器中,通过热风或真空干燥的方式将溶剂蒸发掉,得到干燥的锂电池浆料。
干燥的过程需要控制温度和湿度,以确保浆料的质量和性能。
需要注意的是,制备锂电池浆料的工艺是一个复杂的过程,需要考虑材料的性质和比例、混合均匀度、研磨细度、分散效果等多个因素的影响。
合理选择原料和配比、优化混合和研磨工艺、控制干燥条件等都是提高锂电池浆料质量和性能的关键。
总之,锂电池浆料的制备工艺是锂电池生产过程中不可或缺的环节,对电池的性能和安全性有着重要影响。
- 1、下载文档前请自行甄别文档内容的完整性,平台不提供额外的编辑、内容补充、找答案等附加服务。
- 2、"仅部分预览"的文档,不可在线预览部分如存在完整性等问题,可反馈申请退款(可完整预览的文档不适用该条件!)。
- 3、如文档侵犯您的权益,请联系客服反馈,我们会尽快为您处理(人工客服工作时间:9:00-18:30)。
锂电池浆料干法混料工艺为什么更好锂离子电池是一个复杂的系统工程,电池性能好坏受到原材料,电池设计,制造设备与工艺,环境等众多因素影响,任何一点缺陷都可能导致电池产品的崩塌。
因此,虽然现在关于锂电池的新材料,新设计,新工艺大量涌现,它们的产业化进程却很缓慢,锂电池并没有出现巨大的技术革新。
材料是锂电池的基础,而制造工艺也很重要。
其中,混料工艺在锂离子电池的整个生产工艺中对产品的品质影响度大于30%,是整个生产工艺中最重要的环节。
锂离子电池的电极制造中,正负极浆料基本上都是由活物质、聚合物粘结剂、导电剂等组成。
电极浆料的混料工艺大概分为三种:(1)球磨工艺,最初来源于涂料行业;(2)湿法混料工艺,基本过程为溶胶-混合导电剂-混合活物质-稀释。
这是目前国内的主流工艺。
(3)干法混料工艺,基本过程为活物质、导电剂和黏结剂干粉混合-加入适量溶剂润湿-加入溶剂高速分散破碎-稀释调节粘度。
对电池浆料的要求,第一是分散均匀性,如果浆料分散不均,有严重的团聚现象,电池的电化学性能受到影响;第二,浆料需要具有良好的沉降稳定性和流变特性,满足极片涂布工艺的要求,并得到厚度均一的涂层。
干法混料工艺的优点最开始锂电池浆料的制造借鉴涂料行业,1999年时,韩国人就开始了研究投料顺序对浆料性质和电池性能的影响。
他们采取如图1所示四种投料工艺进行混料,采用相同的材料和配方,仅仅改变投料顺序就能改变浆料的性质。
浆料的混合程度取决于颗粒大小,粒度分布,形状,比表面积,颗粒的溶剂吸收率等,从搅拌开始到粘度稳定所需的时间和依次加入的材料的比表面积最相关。
图1 浆料制备的四种方法方法1:活物质吸收液体不充分,导电剂的比表面积比活物质颗粒大很多,表面吸收了大量的液体,液体陷入导电剂中,不能轻易流动。
方法2:活物质比表面积小,更容易释放液体。
导电剂后加入,开始吸收溶剂,粘度稳定时间更长。
方法4:活物质和导电剂同时吸收液体,润湿固体颗粒,此种方法吸收溶剂最充分,浆料分散性最好,因此,相同的固含量条件下浆料粘度最低。
研究结果发现采用第4种工艺的浆料粘度达到稳定的时间可接受,而且所制备的浆料粘度最低,如表1所示,分散性最好,而且半电池循环测试结果表明此工艺制备的电池循放电容量衰减最小(图2所示)。
表1 四种混料方法浆料的稳定粘度和从开始搅拌到稳定所需时间图2 四种混料工艺所制半电池循环测试钱龙等人采用活物质、导电剂、粘结剂干粉预混合-超高粘度的搅拌工艺,所制备的浆料与传统湿法工艺相比,该工艺生产的负极浆料具有更好的性能,浆料黏度、颗粒度和固含量稳定性等均比流体分散工艺得到的浆料要好,制成的膜片电阻率较低,粘接力较高,制成的电芯容量保持率更高。
超高粘度搅拌时,剪切力大能够更加充分分散颗粒细小容易团聚的导电剂,同时也更有利于粘结剂溶解和稳定,从而电池性能更优。
干法混料工艺基本过程固体粉料在液体中分散基本过程如图3所示,分为:(1)粉料的润湿,将附着于粉体上的空气以液体介质取代。
一种粉体要分散在液体中,首先必须被润湿,固体表面的湿润性由其化学组成和微观结构决定。
固体表面自由能越大,越容易被液体湿润;反之亦然,润湿性可用接触角大小表示。
(2)颗粒团聚体的破裂、分散,破碎团聚体主要有三种力:设备转动过程中的机械力,颗粒之间发生碰撞产生的作用力,高速分散剪切力。
(3)固体悬浮物的稳定化,阻止已经分散的颗粒发生在团聚,分散稳定作用有静电稳定、空间位阻稳定。
图3 粉料在液体中混合分散基本过程典型的干法混料工艺过程为:(1)活物质、导电剂、粘结剂粉体加入搅拌釜,进行干粉混合均匀;(2)加入适量溶剂,对粉体颗粒进行润湿,使颗粒表面吸附溶剂,同时在这种高粘度下搅拌,开始形成大的剪切力作用,充分混匀润湿粉体颗粒;(3)继续加入溶剂,高速剪切力作用下对颗粒团聚体进行分散,使导电剂均匀分布;(4)继续加入溶剂,稀释浆料,调节粘度使之适合涂布工艺。
其中,粉体的润湿是工艺的核心步骤,溶剂的量存在一个临界点,若溶剂偏少,不足以润湿全部粉料,那么干粉必然成团,后续想将其打开有一定难度;而且,过干的情况下,双行星搅拌机中,浆料容易“爬杆”,并不能起到搅拌的效果;如果溶剂偏多,浆料很容易流动,搅拌桨的剪切力作用效果减小,而且,捏合搅拌也起不到捏合力粉碎团聚的作用。
实际浆料的效果都可以用细度和粘度来判断:相同条件下,粘度越小,细度越小,证明分散效果越佳。
高强度干粉混合工艺近几年,干法混料工艺在第一步干粉混合步骤进一步得到优化,出现高强度干粉混合工艺改善浆料和电池特性的报道。
图4为高强度剪切混合设备Nobilta™结构示意图,搅拌拐和壁的间隙3mm,内外壁之间有一层水套冷却高速分散中产生热量导致的温升。
在混合过程中,由于高速旋转产生的高剪切力作用下,固体颗粒被高速旋转轴高速旋转而离心分离。
高速分散的强度可用弗鲁德数Fr(Froude-toolnumber)表征,定义为作用在颗粒上的离心力与重力的比值,可由式(1)描述。
当转子的半径保持不变,Fr取决于于转子速度的ω,转子的转速越高,弗鲁德数越大,表明高速分散的强度越大。
其中,ωt是转子转速,rt为转子半径,g为重力加速度。
图4 高强度剪切混合设备Nobilta™结构示意图高强度的干粉剪切分散具有两个方面的作用:一方面,高的剪切力能够使导电剂团聚体充分破碎分散,另一方面,高速分散作用下,干粉搅拌能够实现微观上的混合,在较大的活物质颗粒表面沉积形成一层由细小的分散开的导电剂沉积层,从而形成良好的导电网络。
如图5所示,一般的干粉混合强度低,导电剂没有完全分散开,在活物质颗粒表面仍旧存在团聚,而高强度干粉混合工艺使导电剂团聚体充分破碎分散,在活物质表面形成沉积层。
图5 一般干粉混合(左边)和高强度干粉混合(右边)颗粒微观形貌对比高强度的干粉分散混合主要的参数有:(1)高速分散的强度,可用弗鲁德数或转子线速度表示,(2)高速分散的时间。
图6是高强度干粉混合对涂布极片孔隙率的影响,极片涂布之后未辊压,高强度干粉混合能够降低极片的孔隙率,转速一定时,随着分散时间越长,孔隙率越低,而分散时间一定时,转速越高孔隙率越低。
图6 高强度干粉混合对涂布极片孔隙率的影响图7是高强度干粉混合对涂布极片结合强度的影响,极片涂布之后未辊压,高强度干粉混合能够提高极片的结合强度,转速一定时,随着分散时间越长,结合强度越高,而分散时间一定时,转速越高结合强度越高。
图7 高强度干粉混合对涂布极片结合强度的影响因此,采用高强度干粉混合工艺,必然能够提高电池的性能,如图8所示。
极片涂布之后辊压到相同的涂层压实密度,然后同样的负极极片组装成全电池,测试电池性能。
与不采用此工艺的电池相比,高强度干粉混合工艺可以提高电池的倍率特性和和循环性能。
图8 高强度干粉混合对电池倍率和循环性能的影响但是,如果高强度太高,或者时间太长,导电剂粉碎成细小颗粒,虽然增加了导电剂与活物质之间的接触和分散效果,但是破坏了导电剂网络的长距离导电性能,所制备的极片电阻会增加,相应的电池性能反而会变差,如图9和图10所示。
随着分散强度增加,极片电阻先降低后呈现增加趋势,电池的倍率和循环性能也会相应变差。
图9 高强度干粉混合套件对极片电阻的影响图10 高强度干粉混合条件对电池倍率和循环性能的影响因此,虽然干法混料工艺显著缩短了搅拌工艺时间,浆料稳定性和分散均匀性也更好。
但是,此工艺存在工艺范围窄的缺点。
常规干法搅拌工艺中,在润湿步骤,溶剂量、搅拌转速和时间选择不合适很容易出现品质问题,而这又与原料的颗粒大小、尺寸分布、比表面积等关系密切,这些参数稍有变化,相应的溶剂量和搅拌工艺条件也需要作出调整。
如果第一步加入溶剂量过多,颗粒团聚体不容易分散,出现浆料细度大、导电剂分布不均匀的品质问题。
而如果第一步加入的溶剂过少,润湿搅拌作用力大,粘结剂也无法充分分散溶解或者出现粘结剂长链被破坏的情况,导致浆料粘度和稳定性出现问题。
这可能是限制干法混料工艺广泛应用的关键问题。
同样,高强度干粉分散混合,同样存在合适的工艺范围,在合适工艺范围内,极片和电池性能会提升,但是超出此范围,电池性能反而变差。
参考文献[1]Kim K M, Jeon W S, Chung I J, et al. Effect of mixing sequences on theelectrode characteristics of lithium-ion rechargeable batteries[J]. Journal of Power Sources. 1999, 83: 108-113.[2] 钱龙, 朱丹, 饶睦敏, et al. 锂离子电池负极分散工艺研究[J]. 电池.2016(02): 95-97.[3]Westphal B G, Mainusch N, Meyer C, et al. Influence of high intensive drymixing and calendering on relative electrode resistivity determined via anadvanced two point approach[J]. Journal of Energy Storage. 2017(11): 76-85.[4]Bockholt H, Haselrieder W, Kwade A. Intensive powder mixing for dry dispersingof carbon black and its relevance for lithium-ion battery cathodes[J]. PowderTechnology. 2016, 297: 266-274.[5]Bauer W, Tzel D N, Wenzel V, et al. Influence of dry mixing and distribution ofconductive additives in cathodes for lithium ion batteries[J]. Journal of Power Sources. 2015, 288: 359-367.。