挤出平模头优化设计
电缆挤出用挤压式模具的设计

电缆挤出用挤压式模具的设计1模芯1)模芯外锥最大外径ΦD1:该尺寸是由模芯座的尺寸决定的,要求严格吻合,不得出现“前台”,也不可出现“后台”,否则会造成存胶死角,直接影响塑料组织和挤出表面质量。
2)内锥最大外径ΦD2:该尺寸决定于加工条件及模芯螺纹壁厚,在保证螺纹壁厚的前提下,ΦD2越大越好,便于穿线,也便于加工。
3)连接螺纹M1:该尺寸必须与模芯座的螺纹尺寸一致,保证螺纹连接紧密。
4)模芯孔径Φd1:此尺寸是影响挤出质量最大的结构尺寸,按线芯结构特性及其几何尺寸设计。
一般情况下,单线取d1=线芯直径+(0.05~0.15)mm;绞合线芯取d1=线芯外径+(0.3~1.3)mm,具体根据线芯大小而定。
5)模芯外锥最小外径Φd2:实际上是模芯出线端口厚度的尺寸,端口厚度Δ=1/2(d2-d1)不能太薄,否则影响模具使用寿命;也不宜太厚,否则塑料不能直接流到线芯上,且在结合处容易形成涡流区,引起挤出压力的波动,挤出质量不稳定,一般壁厚控制在0.5~1mm为宜。
6)模芯定径区长度l1:l1决定了线芯通过模芯的稳定性,不能设计的太长,否则造成加工困难,工艺要求的必要性也不大,一般取l1=(0.5~1.5)d1。
但同时必须考虑加工制造的因素,太短或太长,都会引起加工困难,在设计时需综合考虑,根据模芯总长度取一个合适的值。
7)模芯外锥角度β:这是设计给出的参考尺寸,从图6中不难看出,tgβ/2=(D1-d2)/[2*(L1-l2)],即(L1-l2)=(D1-d2)/[2*tg(β/2)]。
所以,模芯外锥部分长度可以依据上述决定的尺寸确定,经计算如果太长或太短,与机头内部结构配合不当,可回过头来修正锥角β,然后在计算外锥长度,直至合适。
设计时,一般模芯外锥角度β应不大于45°,与模套内锥角度γ的角度差应控制在3~10°,具体应根据机头实际结构尺寸及挤出材料的不同,选择一个合理角度。
2模套1)模套最大外径ΦD3:根据模套座(或机头内筒直径)设计,一般小于筒径2~3mm,此间隙工艺调整偏心、确保同心度的必须。
挤出机机头设计
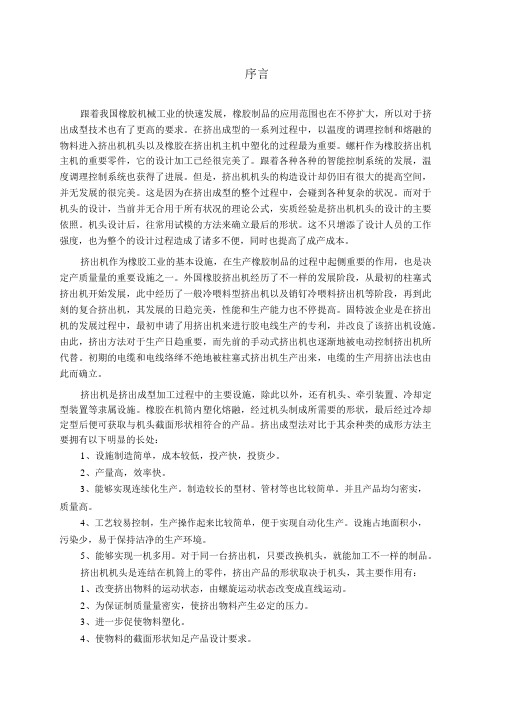
序言跟着我国橡胶机械工业的快速发展,橡胶制品的应用范围也在不停扩大,所以对于挤出成型技术也有了更高的要求。
在挤出成型的一系列过程中,以温度的调理控制和熔融的物料进入挤出机机头以及橡胶在挤出机主机中塑化的过程最为重要。
螺杆作为橡胶挤出机主机的重要零件,它的设计加工已经很完美了。
跟着各种各种的智能控制系统的发展,温度调理控制系统也获得了进展。
但是,挤出机机头的构造设计却仍旧有很大的提高空间,并无发展的很完美。
这是因为在挤出成型的整个过程中,会碰到各种复杂的状况。
而对于机头的设计,当前并无合用于所有状况的理论公式,实质经验是挤出机机头的设计的主要依照。
机头设计后,往常用试模的方法来确立最后的形状。
这不只增添了设计人员的工作强度,也为整个的设计过程造成了诸多不便,同时也提高了成产成本。
挤出机作为橡胶工业的基本设施,在生产橡胶制品的过程中起侧重要的作用,也是决定产质量量的重要设施之一。
外国橡胶挤出机经历了不一样的发展阶段,从最初的柱塞式挤出机开始发展,此中经历了一般冷喂料型挤出机以及销钉冷喂料挤出机等阶段,再到此刻的复合挤出机,其发展的日趋完美,性能和生产能力也不停提高。
固特波企业是在挤出机的发展过程中,最初申请了用挤出机来进行胶电线生产的专利,并改良了该挤出机设施。
由此,挤出方法对于生产日趋重要,而先前的手动式挤出机也逐渐地被电动控制挤出机所代替。
初期的电缆和电线络绎不绝地被柱塞式挤出机生产出来,电缆的生产用挤出法也由此而确立。
挤出机是挤出成型加工过程中的主要设施,除此以外,还有机头、牵引装置、冷却定型装置等隶属设施。
橡胶在机筒内塑化熔融,经过机头制成所需要的形状,最后经过冷却定型后便可获取与机头截面形状相符合的产品。
挤出成型法对比于其余种类的成形方法主要拥有以下明显的长处:1、设施制造简单,成本较低,投产快,投资少。
2、产量高,效率快。
3、能够实现连续化生产。
制造较长的型材、管材等也比较简单。
并且产品均匀密实,质量高。
PP材料各种加工工艺的缺陷和对策
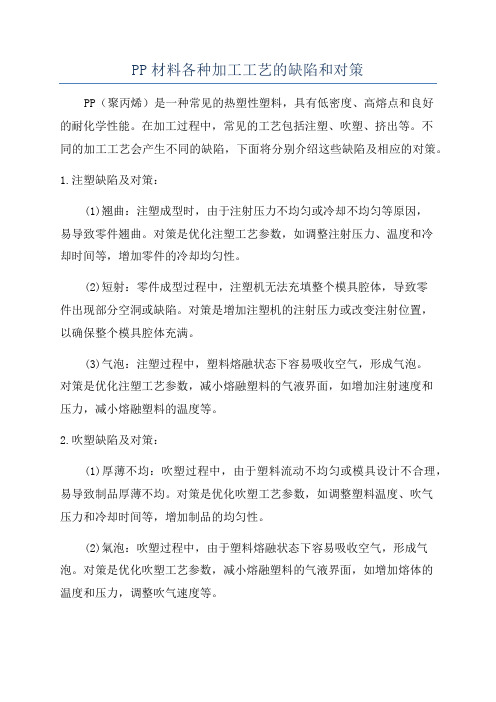
PP材料各种加工工艺的缺陷和对策PP(聚丙烯)是一种常见的热塑性塑料,具有低密度、高熔点和良好的耐化学性能。
在加工过程中,常见的工艺包括注塑、吹塑、挤出等。
不同的加工工艺会产生不同的缺陷,下面将分别介绍这些缺陷及相应的对策。
1.注塑缺陷及对策:(1)翘曲:注塑成型时,由于注射压力不均匀或冷却不均匀等原因,易导致零件翘曲。
对策是优化注塑工艺参数,如调整注射压力、温度和冷却时间等,增加零件的冷却均匀性。
(2)短射:零件成型过程中,注塑机无法充填整个模具腔体,导致零件出现部分空洞或缺陷。
对策是增加注塑机的注射压力或改变注射位置,以确保整个模具腔体充满。
(3)气泡:注塑过程中,塑料熔融状态下容易吸收空气,形成气泡。
对策是优化注塑工艺参数,减小熔融塑料的气液界面,如增加注射速度和压力,减小熔融塑料的温度等。
2.吹塑缺陷及对策:(1)厚薄不均:吹塑过程中,由于塑料流动不均匀或模具设计不合理,易导致制品厚薄不均。
对策是优化吹塑工艺参数,如调整塑料温度、吹气压力和冷却时间等,增加制品的均匀性。
(2)氣泡:吹塑过程中,由于塑料熔融状态下容易吸收空气,形成气泡。
对策是优化吹塑工艺参数,减小熔融塑料的气液界面,如增加熔体的温度和压力,调整吹气速度等。
(3)皱纹:吹塑过程中,由于冷却不均匀或模具设计不合理,易导致制品表面出现皱纹。
对策是优化吹塑工艺参数,如调整模温、吹气速度和冷却时间等,增加制品的平整度。
3.挤出缺陷及对策:(1)压力不均:挤出过程中,由于挤出机的压力分布不均或头部设计不合理,易导致制品的厚度不均。
对策是优化挤出工艺参数,如调整挤出机的压力和温度,改善头部设计,增加制品的均匀性。
(2)熔体流动不良:挤出过程中,由于挤出机的供料不均匀或模具设计不合理,易导致熔体流动不畅,出现气泡或尺寸不准确等问题。
对策是优化挤出工艺参数,如调整供料速度和温度,改善模具设计,增加制品的牢固性和精度。
(3)紧缩难度:挤出过程中,由于制品的形状复杂或大小不一,易导致模具紧缩困难,产品出现尺寸不准确或细节缺失等问题。
第八讲_空心铝型材挤压模具优化设计_2_赵云路 (2)

第八讲 空心铝型材挤压模具优化设计(2)沈阳新光模具制造公司 赵云路西南铝加工厂 刘静安 在不带穿孔装置的普通型、棒挤压机上生产空心型材,必须采用一种特殊结构的模子—分流组合模。
实心锭在挤压筒中,通过挤压机作用在挤压轴上的力使锭从模孔中挤出之前先分成几股,随后再在模孔前汇合,形成围绕模芯的环形整体而被挤出模孔,形成闭合的空心型材。
分流组合模的特点是必须有一个或几个形成内腔的芯子,芯子设计在桥上,桥把金属辟开成几股而流向模孔。
由于模桥设计的不同,分流组合模可分为平面分流模(分流模)、舌型模(桥式模)和叉架模等。
1 平面分流组合模的特点平面分流组合模一般用来生产空心和悬臂较大的半空心型材。
在建筑型材中,大多数都是外形较大,壁较薄,断面形状复杂,沟槽和丝孔较多的空心和半空心型材。
在空心型材中又出现单腔、双腔和多腔。
即使在有穿孔系统的挤压机上也很难实现挤压生产。
在生产半空心型材或断面壁厚相差悬殊的型材时,如果采用平模,无论怎样调整工作带和设计促流角或阻碍角,都很难把流速调整均匀。
若采用分流组合模,用分流孔和桥芯来调整流速,就很少出现波浪、扭拧和弯曲。
能够很顺利地生产出合格产品。
平面分流模较舌型模易加工,在挤压生产时操作简单,分离残料较舌型模易加工,生产效率高,残料较舌型模短,产品的成品率也高。
对于形状复杂的半空心型材,分流模结构可减小悬臂上的承压力,保证模具强度。
用分流模可实现多根铸锭的连续挤压,按需要的制品长度截取。
还可实现在小挤压机上挤出外形较大规格的产品,并且可以达到所给定的变形量。
用分流组合模,可采用实心铸锭在型、棒挤压机上一次生产单根和多根管材,制品内外表面好,尺寸精确。
但分流组合模和平模相比,用它生产的型材存在焊缝。
如果模具上涂油或铸锭表面不干净,制品焊缝中会存在夹渣。
若挤压温度过低或模具设计不合理,都会影响焊合质量。
另外,分流模的变形阻力较平模大,目前只限于生产一些纯铝、铝-锰和铝-镁-硅合金。
EDI的多层共挤平模头

多微层结构用共挤平模头2007年01月24日 塑料机械技术最多可挤出80个超薄层,提高薄膜和涂膜生产率,降低成本,大幅提高阻隔性能美国EDI 挤出模头公司(Extrusion Dies Industries, LLC )在2006年国际塑料展览会上宣布一种可能具有革命性的平模头系统,与常规的共挤模头相比,薄膜和涂膜的结构层数有数量级的提高,生产出带微层结构的产品,可以提高阻隔水分和气体的能力,用微层结构包封凝胶和未熔物料,使制造商能够更经济地使用高成本物料。
EDI 指出,微层技术在阻隔性包装中将得到广泛的应用。
这项技术的基础是陶氏化学公司(TheDow Chemical Company )开发的“复合层倍增器”专利,EDI 从陶氏化学公司取得了这个系统的使用许可。
标准的生产配置是,由三台或更多台挤出机担任供料的角色,将熔体送入EDI 的流线化共挤块,生产出均匀的多层“三明治”结构;然后将多层三明治结构中间产品送入EDI 采用陶氏化学公司的专利设计开发出来的复合层倍增装置。
在复合层倍增装置中,分阶段进行复合层倍增操作-例如三层倍增为十二层,十二层倍增为四十八层。
最终获得的微层结构中间产品送入EDI 的共挤歧管,使产品的宽度达到生产要求。
“目前我们还不知道实际能达到的上限,”EDI 总裁兼首席执行官Timothy C. Callahan说。
“但是我个人认为,有可能生产出80层的50微米薄膜。
”EDI 的微层技术整合了陶氏化学公司的复合层倍增器,提供成套的定制系统,包括模头、共挤块和其他用于使用最终挤出产品形成复杂结构的模头组件。
该公司将向客户转发陶氏化学公司的这项技术的使用许可。
“我们正在与被许可人建立关系,使薄膜和涂膜加工商也能受1、EDI 提供的系统模型包括(上起) 共挤喂料块、根据陶氏化学公司专利设计 的复合层倍增器、以及多歧管模头2、在流道布局示意图中,通过复合层倍增工艺 将两种物料构成的三层“三明治”结构转化为微层 结构,然后送入多歧管模头的中央歧管,在中央歧管内 与两种作为最终结构中的表层的新 物料流拼装组合在一起益于EDI/陶氏化学公司合作开发的这套倍增器系统,降低生产成本,提高产品性能,”Callahan 说。
FDM挤出头CFD分析与混色挤出头优化设计

FDM挤出头CFD分析与混色挤出头优化设计随着时代的进步,市场对个性化定制产品的需求日益旺盛,快速成型技术(RPM—Rapid Prototyping Manufacturing)由于其能够快速将思想设计产物转化为具有一定功能的模型或可直接使用的零件的能力,始一产生就迅速被社会认可并逐渐普及起来,而熔融沉积成型技术(FDM—Fused Deposition Modeling)更是几种快速成型工艺中技术较为成熟且应用最为广泛的一种。
它将CAD三维模型切片处理后把熔融丝料按照每层切片轮廓层层堆积起来,直到完成模型。
成型过程中的原材料为热塑性材料,课题采用生物可降解塑料聚乳酸(PLA—Polylactide Acid)为成型材料,对挤出头性能模拟分析所用计算流体动力学(CFD—Computational Fluid Dynamics)软件为Star CCM+。
课题首先对若干种市面上常见的3D打印挤出头建立三维几何模型进行模拟计算,结合各个挤出头的结构特征和结构参数对挤出头性能分别进行分析,为接下来混色挤出头的设计做准备。
之后模拟分析内流道收缩段锥角、口模平直段长度以及进料速度对流动阻力的影响,结果表明口模平直段长度是影响流动阻力的重要挤出头结构参数,其值与流动阻力正相关。
接下来进行双路混色挤出头的设计,在设计出Y型双路混色挤出头之后,对其进行模拟计算得到两种丝料混合效果,进行分析后优化其结构并再次模拟,重复此过程直至得出混合效果较好的过滤式双路混色挤出头。
模拟的对比试验对Y型和过滤式双路混色挤出头分别进行模型测试,试验结果表明用模拟的方法来对双路混色挤出头进行设计是可行的,过滤式挤出头混合效果优于Y型挤出头。
之后再分别通过试验验证不同结构、总进料速度以及相对进料速度对双路混色挤出头混合效果的影响,得到结论分别验证了模拟结果。
在单色挤出头性能分析以及双路混色挤出头的设计经验基础上进行三路混色挤出头的设计工作,并对其三种丝料在不同相对进料速度下的混合情况进行模拟分析,结果表明,三路混色挤出头的混合效果在不同的相对进料速度下均较好。
铝型材挤压工艺和模具设计的仿真分析和优化

Altair HyperXtrude铝型材挤压工艺和模具设计的仿真分析和优化Altair工程软件(上海)有限公司动机–更早的设计决策解决个问题的成本使用CAE= 解决一个问题的成本题数传统方法出的问# 找模具设计模具制造试模量产HyperXtrude 唯一专业的铝型材挤压仿真软件稳态变形分析模具变形/强度分析瞬态变形分析工作带长度分析焊合长度预测压余长度预测正向/反向挤压虚拟试模材料库快捷的图形用户界面挤压模具优化中文菜单型材料头变形分析——稳态法TemperatureTemperatureVelocityProfile Deflection瞬态分析——型材变形型材变形比较模具变形分析和强度校核耦合的材料流动、热和变形分析依据挤压载荷和热载计算模具的变形和强度模具和材料的网格单元的自动更新位于模具和材料的接触表面网格单元不需要完全匹配保险杠横梁——模具几何Mandrel Die Plate模具上的温度分布模具表面上的法向力分布模具的变形模具上的应力分布——强度校核虚拟试模实例初始模具设计方案结果建议改进方案ObjectiveUniform exitvelocity=6m/min=1m/s•Uniform exit velocity = 6m/min = 0.1m/s Design IterationsFi t It ti R d th th l A d B b 10•First Iteration –Reduce the portholes A and B by 10 mm •Second Iteration –Increase C & D by 5 mm2nd IterationCAD1st IterationBABCD AB案例分析——汽车保险杠横梁Problem DefinitionProblem Definition¾Alloy:AA 6082¾Container Diameter:7.375 in (187.325 mm)¾Billet Length: 25 in (635 mm)¾Press Capacity: 1800 T (16 MN)¾Unit Pressure:580 MPa¾Max. Ram Speed: 41 ipm (17.357 mm/s)¾Container Temperature 441 °CProfile Type:Hollow¾Profile Type:¾Extrusion Ratio:21.93¾Extrusion Speed: 6.87 m/minRam Speed:523mm/s¾Ram Speed: 5.23 mm/s¾Part Exit Speed: 6.87 m/min¾Billet Preheat:518 °C创建有限元模型PortholesDie Plate MandrelAluminum + Tool模芯的变形模芯变形(靠近棒料一侧)下模变形Weld Chamber Bolster Side温度分布(模芯和分流孔)Mandrel Portholes, Bearing and Profile速度分布Original Bearing After 1st Modification Velocity Contours –After 2nd ModificationDecrease by 2mm Decrease by 2 mmIncrease by 3 mm棒料表皮杂质材料跟踪--压余长度预测•棒料表皮包含氧化杂质•表皮挤进型材将影响质量•最佳的压余长度预测停止挤压的时刻——棒料焊合长度计算•材料进入分流孔和导流室•不能停车清理模具•循环棒料的加载挤压•如何预测型材完全是新材料挤出?棒料的接口计算After 5 secAfter 60 sec初始工作带——出口流速不平衡初始设计——型材变形修改工作带长度工作带修改后计算结果——速度分布工作带修改后的计算结果——型材变形正向/反向挤压快捷的图形用户界面 1.Import Geometry 2.Create Project Directory 3.Select Units 4.Set Analysis Requirements Process DataAnalysis DataSelect Components5Select Materials 5.Select Materials6.Set Process Conditions 7.Define Bearing 8S l 8.Solve9.Check Results材料性能数据Workpiece and Tool MaterialsCommon AlloysPlots of Flowstress Curves U M difi blUser Modifiable挤压模具的优化统一的平台,无缝调用集成在HyperWorks统的平台,无缝调用•HyperXtrude, HyperStudy, HyperMorph 工作带长度的优化•平衡材料流动•减少修模分流孔的优化•平衡材料流动•确保模具在挤压过程中没有损坏•减少修模优化原理优化实例——工作带长度的优化型材截面的区域划分工作带优化过程——优化目标出口流速均匀优化前后的出口流速比较支持中文菜单建立挤压工艺数据库•挤压工艺数据•型材数据•棒料数据•挤压设备数据•可挤压合金材料HyperXtrude任务管理器一个桌面应用工具,能够实现在远程机器上提交任务。
铝型材挤压成型数值模拟及优化设计
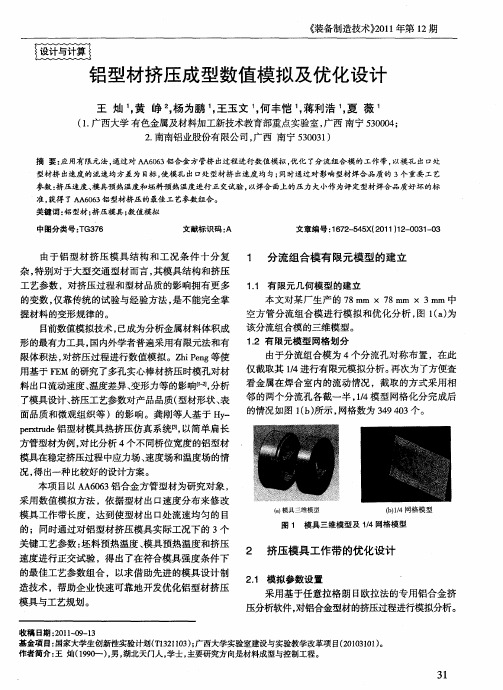
一 一
( 模具三维模型 a ) (l b/ ) 4网格模 型
图 1 模具 三维模 型及 14网格模型 /
关键工艺参数 : 坯料 预热温度 、 模具预热温度 和挤压 速度进行正交试验 ,得 出了在符合模具强度条件下 的最佳工艺参数组合 ,以求借 助先进的模具设计 制 造技术 ,帮助企业快速可靠地 开发优化铝型材挤压 模具与工艺规划。
表 2 试验方 案结果表
L 3一 l _ j
( 修 改后的工作带长度 a ) ) 出口速度分 布图 型材
图 3 修改后工作带设计 与型材 出口速度分布 图 3 2
《 装备制造技术)0 年第 l 期 21 1 2
32 虚拟 试 验结 果分 析 .
在满足模具挤压强度条件下 ,焊合室 内焊合 面 5 结束语
4 实验验证
生产试模 ,有效地提高了生产效率 ,降低 了生产成 本, 对生产实践有着重要的指导意义。
在原始工作带和工艺参数 的情下 ,进行第一 参考文献 : 次试模挤压 , 结果挤出型材 出现弯曲、 扭拧 、 波浪 、 麻 点等缺陷 ,有些位置挤 出后略向上翘 ,且上部有缩 口。通过对 比分析结果 , 发现上翘部位都在虚拟模拟
() a原工作带长度
一
( ) 出 口速度分布图像 b 型材
提高成品率 和生产率 的要求。针对该铝合金方 管型 材对焊合 品质要求较高 的情况 ,为 了获得其挤压 的
最佳温度 和速度参数 ,本文采用正交试验的方法[ 4 】 , 通过考察各组参数组合下 ,分 流组合模焊合 室内的 压力大小 , 来获得最佳挤压工艺参数。 选取 的 3 个因素为 : 坯料温度 、 模具温度和挤压 速度 。
Eq i me t u p n Ma u a t n e h oo y No 1 , 0 1 n f cr g T c n lg . 2 2 1 i
- 1、下载文档前请自行甄别文档内容的完整性,平台不提供额外的编辑、内容补充、找答案等附加服务。
- 2、"仅部分预览"的文档,不可在线预览部分如存在完整性等问题,可反馈申请退款(可完整预览的文档不适用该条件!)。
- 3、如文档侵犯您的权益,请联系客服反馈,我们会尽快为您处理(人工客服工作时间:9:00-18:30)。
挤出平模头优化设计、制造应用技术
挤出平模头在社会发展和进步中起到非常大的作用,以板、片、膜等为代表的平面挤出制品在。
各种行业内得到广泛的应用,在社会经济建设、人类生活等方面起到至关重要的作用。
目前,我们国家的重点项目西气东输工程所采用的管道包覆膜就是采用了精诚时代集团所推出的解决应用方案,同时,这种平挤出的模具产品也为包括建筑、医药、包装、家电、光学级板材防水材料等方面提供了充分的支持。
挤出平模头的流道设计
歧管是挤出模头的心脏。
它是在模身基体上加工出来的型腔,熔融的高分子材料从挤出机挤出后经过歧管就变成了所要求的最终产品,并达到宽度和厚度方面的精确成型要求。
精诚提供一系列的歧管设计,以满足不同材料和产品的特定要求,其中一些设计有:
1.标准衣架型设计,其水滴型横截面能提供流线型的物料流,适用于所有种类的聚合体。
既可用于单层挤出产品,也可用于热敏材料的复合挤出。
2.圆形腔,可以最大程度地减少热敏感型材料在挤出过程中的烧蚀。
3.标准型衣架型歧管,其加长的水滴型横断面使得具有不同流变性能的树脂在复合挤出对层与层之间分界面变形最小。
4.T形设计,具有加长的水滴型歧管横断面,而且在整个歧管长度范围内,其横断面形状及大小不变。
该款设计应用于精诚厚度控制系统的基础上。
由于厚度控制系统在产品宽度频繁改变的情况下可以很好地减小消除厚边现象,因此在单层或多层挤出涂布模头上得到了广泛的应用。
它能通过迅速调节歧管内堵块和内堵片以适应不同的幅宽,速度和材料。
5.加长型水滴管横断面是一款先进的设计,其横断面的长宽在模头的两端较大,而在模头中部较小,而歧管背线则与模唇出口线平行,从而使得所有模身螺栓距离模导出口的尺寸完全相同。
这种模身螺栓布局使得模身变形大大减少。
复杂的歧管横断面使得用单歧管模头进行多料层复合挤出时的层间分界面变形降到最低程度。
曲线型的预成型区使得物料在整个模头宽度范围内均匀一致地流出,消除了“M”形或“W”形挤出纹路现象。
精密级模唇厚度调节机构的重要性
对于高精度模头,模唇间隙微调节机构非常重要,往往间隙的调节精度直接影响到产品厚薄的精度和连续生产的稳定性,通常手动模唇调节螺栓转动一圈在1mm以上,现在我们设计采用螺栓差动机构,能够使调节机构的精度提高4倍,这样调节时间能更轻松,快捷地将产品要求提高到最佳效果。
自动控制模头技术
自动控制模头技术用于精密控制薄膜厚度,片材板材厚度和涂布厚度的首要控制技术。
这项技术除了能提高产品的质量和准确度以外,与传统的手工调节系统相比还能真正地起到节省原材料的作用。
沿着自动控制模头的柔性摸唇稠密均布着一系列的热驱动调节块,所有的自动控制系统都安装在一系列调节块的中心。
这些控制块根据后续的电脑测厚系统所给出的反馈信号作出反应。
当挤出产品的某个区域被检测到厚度超过预定值的时候,模唇上相应位置上的调节块加热器的电压自动升高,使得调节块发生热膨胀,从而减小该区域的模唇开度。
相反,检测到的厚度小于预定值的时候,则可以通过减小电压得到校正。
所有的自动控制模头都带来强制冷却空气,以减少反应时间。
自动控制平模头系列产品的模唇温控系统可与红外线、D射线、X射线等自动测厚仪相配合,经测厚仪自动横向往返准确检测后反馈数据,通过模唇调节装置的特殊热膨胀螺栓进行自动微调的方式来调节模唇口的厚度,这一种控制方式具备非常高的精度。
采用自动测厚系统,并且在测厚和模唇之间形成闭环,能准确动态显示薄膜的厚度参数,控制精度的误差≤2%,并可设定不同的检测及扫描频串参数,最高扫描频率可达20次/分。
高分析度的显示系统,以及保证全线高速高效稳定运转的全闭环控制技术,可使产品精度控制在±2%以内。
选配带有消除厚边装置的内堵式宽幅调节装置或外堵式调节装置,可生产多规格制品。
模头流道及模体表面镀铬处理,自动控制模头实现了提高挤出制品品质、节省材料、降低消耗、连续生产的稳定性和精确控制的准确性。
快速开口装置提升效益
快速开口装置适合柔性模唇,内部具有自润滑轴承的功能,能够有效避免移动部件的磨损。
它的原理是通过生产线操作一侧(模头侧面)的调节轴,能够在不停机生产时进行手动调节,此环节功能不需要停止生产或松动螺丝就能调节下模唇。
在线调整制品厚度规格,免去了停机调节、开关时所损失的时间和经济效益,而且快速开口调节装置调节时间仅需要2分钟,比起普通模头的节约十倍左右的时间。
模唇快速开口装置能在生产过程中出现原料不纯净影响产品质量时,可以快速将模唇开口调大,使因长时间生产在模具稳流段积累的杂质迅速排出,以节约时间和降低原料浪费,因这种快速开口结构是通过模层在垂直方向移动一定量的距离来实观的,所以其结构有一定的特殊性,模唇的紧固螺丝是特制的,其端面有一指示槽,它的作用是在装配过程中保证该螺丝具有方向性。
深入式加热元件使用的优越性
加热元件在平模头的使用过程中起到非常重要的作用,衡定的温度是生产高标准制品的重要条件之一。
在加热元件的选择上,原先是以加热板作为主要的加热元件,但是出于加热均衡稳定的要求考虑,加热板因其本身存在不均匀加热的因素,再加上离模体中心比较远,散热比较快等缺陷,加热板的使用不能最大程度发挥模头的功能,提升制品质量。
深入式加热元件的使用,恰好弥补了加热板的缺点,能够深入到模体内部进行有效均匀的加热,使用高温润滑油之后可以在加热元件损伤的情况下自由抽出,减少维修时间。
保温装置的使用
挤出平模头在生产过程中,会因为外部环境的不稳定而造成熔体波动,这种波动的产生会给制品的合格率带来影响。
在平模头的模体上加上保温装置后,可以有效减少80%左右的温度散发,起到了保持模体恒温的作用。
FLOW熔体流变分析
在提供给客户的平模头产品中,精诚的每一套产品全部采用了国际先进的熔体流变分析系统(FL0W软件)进行分析、设计。
根据客户的需求,帮助设计和分析制品原料的特性,通过计算机摸拟聚合物流变,获得精确的流道设计,为保证给我们的模头以最佳的流道几何设计,选用最先进的电脑模型工程技术。
商标准的表面处理技术
挤出模头的流道表面质量对模头的使用寿命,挤出制品的质量都有着较大的影响,提高模头表面的质量,目的在于提高产品品质,降低模具使用成本,提升生产效率。
精诚的电镀工艺均采用来自德国和美国表面处理技术,并使用进口的镀液检测设备实时监测镀液里的杂质含量来判断镀液的状况。
在接近无灰尘的生产车间,可以使模头表面处理能力达到最高。
绿化理念设计
为可降解的聚乳酸原料设计、制造的挤出平模头是一种新型的工业设计。
聚乳酸可以从玉米、土豆、甜菜等植物类原料中提取,生产成本较低。
制品废弃后经火焚烧后不会产生有毒有害气体,而聚乳酸制品的残留物则可以作肥料进行产出。
每种原料熔体在平模头流道中所呈现的熔性,流动性都有区别,在对聚乳酸原料的熔体流变分析后,研发部们的专家升级改良流道的性能,适应和发挥聚乳酸原料的生产。
聚乳酸的应用和发展将为市场带了来积极的一面,精诚在这一方面的研究也为无公害挤出制品的生产和应用带来了新的生机。