纵轴式掘进机截割头的设计
纵轴式掘进机总体方案设计及其装载机构设计

摘要本文以悬臂纵轴式掘进机为背景,主要研究在给定的条件下,设计出适合工况条件的掘进机。
首先介绍的是总体方案的设计,其中包括机器各部分机构的选型;然后根据总体布置的要求对机器进行总体布置;接着对传动形式及运动元件进行选择,并进行总体参数的确定;接着计算确定截割、装载及中间运输机的生产率,并检测掘进机的整体通过性;最后对掘进机的装载机构进行分体设计。
关键词:掘进机;机构;生产率;AbstractBased on longitudinal axis cantilever-boring machine as the background, the main research in the given conditions, the design of suitable working conditions of the boring machine.First introduced to the design of the overall plan, including machinery parts of the Selection;secend According to the general layout and the requirements of the overall layout of the machinery;Then the transmission of movement and choice of components, and the determination of the overall parameters;Then calculate determine cutting, loading and transport planes between the productivity and the overall detection through the boring machine; Finally, the boring machine loaded bodies of the design.Key words: boring machine; institutions; productivity;目录前言 (1)1 总体结构方案设计 (5)1.1工作机构型式选择 (5)1.2 装载机构类型选择 (5)1.3 输送机构形式选择 (6)1.4 转运机构形式选择 (6)1.5 行走机构 (7)1.6 除尘装置型式选择 (7)1.6.1 除尘方式: (8)1.6.2除尘系统 (9)2 总体布置 (10)2.1 总体布置的内容 (10)2.2 总体布置的原则 (10)2.3具体要求 (10)3传动型式及动力元件的选择 (12)3.1 传动形式及元件选择应遵循的原则: (12)3.2 各机构对传动系统的要求及传动形式的选择 (12)4 总体参数的确定 (14)4.1 机型大小 (14)4.2 机器外形尺寸 (14)4.3 机器可掘断面 (15)4.3.1伸缩量 (15)4.3.2 悬臂长度和摆角 (15)5 生产率 (18)5.1 截割生产率 (18)5.2 装载生产率 (19)5.2.1 装载机构生产能力确定 (19)5.2.2 星轮结构尺寸确定 (20)5.2.3 中间输送机生产率 (21)6 掘进机的通过性 (22)6.1 离地最小间隙 (22)6.2 可通过巷道最小半径 (22)6.3 适应巷道坡度 (22)7 纵轴式悬臂掘进机装载机构设计 (24)7.1 铲板体结构 (24)7.2 驱动装置 (24)7.3 装载机构设计 (25)7.3.1装载机构生产能力确定 (25)7.3.2星轮结构尺寸确定 (25)7.3.3星轮转速确定 (26)7.3.4装载功率确定 (28)结语 (30)致谢 (31)参考文献 (32)附录A (33)附录B (37)前言纵轴式悬臂掘进机总体设计的任务是,根据掘进机的用途、作业情况及制造条件,合理选择机型,确定性能参数、整机尺寸及各部分的结构型式,并进行整体布置,以实现整机的各项性能指标。
截齿排布圆周角对纵轴式掘进机截割头设计性能的影响

a n d t h u s t h e s t a b i l i t y o f l o a d i s b e t t e r .T h e s i m u l a t i o n r e s u l t s s h o w t h a t t h e Q c - t y p e c u t t i n g h e a d i s s u p e i r o r t o t h e
pi c k s p a c i n g c i r c u mf e r e n t i a l a n g l e a nd t h e UC— t y p e wi t h u n e v e n p i c k s p a c i n g c i r c u mf e r e n t i a l a n g l e a r e d e s i g n e d a n d
Zha n g Me n g— q i ’
( 1 . T a i y u a n R e s e a r c h I n s t i t u t e o f C C T E G, T a i y u a n 0 3 0 0 0 6, C h i n a ;
2 . N a t i o n a l E n g i n e e r i n g L a b o r a t o r y f o r C o a l Mi n i n g M a c h i n e y, r T a i y u a n 0 3 0 0 0 6 , C h i n a )
纵、横轴式掘进机工作原理与结构特点
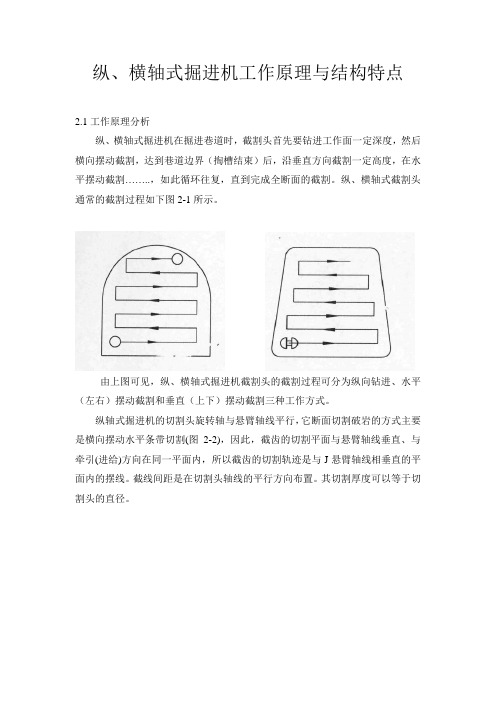
纵、横轴式掘进机工作原理与结构特点2.1工作原理分析纵、横轴式掘进机在掘进巷道时,截割头首先要钻进工作面一定深度,然后横向摆动截割,达到巷道边界(掏槽结束)后,沿垂直方向截割一定高度,在水平摆动截割……..,如此循环往复,直到完成全断面的截割。
纵、横轴式截割头通常的截割过程如下图2-1所示。
由上图可见,纵、横轴式掘进机截割头的截割过程可分为纵向钻进、水平(左右)摆动截割和垂直(上下)摆动截割三种工作方式。
纵轴式掘进机的切割头旋转轴与悬臂轴线平行,它断面切割破岩的方式主要是横向摆动水平条带切割(图2-2),因此,截齿的切割平面与悬臂轴线垂直、与牵引(进给)方向在同一平面内,所以截齿的切割轨迹是与J悬臂轴线相垂直的平面内的摆线。
截线间距是在切割头轴线的平行方向布置。
其切割厚度可以等于切割头的直径。
横轴式掘进机的切割头旋转轴与悬臂轴线相垂直,有两个切割头在输出轴的两端、相对于悬臂中心面对称布置(图2-3)。
它断面切割破岩的主要方式也是横向摆动水平条带切割。
截齿的切割平面与悬臂轴线相平行、与牵引方向相垂直,所以截齿的切割轨迹是一条中心线与悬臂轴线相垂直的螺旋线。
截线间距是在切割头的径向布置。
其切割头直径方向的切厚只能达到其直径的1/ 3左右。
4.2 纵、横轴式掘进机切割煤岩的方式分析图2表示纵轴式和横轴式工作过程不同,两类截割头的切削力FS、进给力Fp和摆动力F}的方向各异。
切削煤岩的阻力引起截割头的切削力,受切割机构功率限制,切入煤岩的阻力和保持截齿切削状态所需的力产生推进力Fe,其大小与切削力相关。
推进力Fe的方向并不都与摆动方向一致,在水平摆动过程中,纵轴式截割头的摆动力F,,的方向与截齿切削力FS和进给力Fa构成的切割平面相平行,类似横轴式切割头掏槽工况。
同样横轴式截割头在摆动切割时,摆动力凡的方向与截割平面垂直,类似纵轴式截割头掏槽工况。
如果摆动力方向平行于截割平面,进给力与切割头的摆动力则呈线性关系,摆动力过大,截齿磨擦增大。
掘进机纵轴式截割头截割效率的优化设计_郝建生
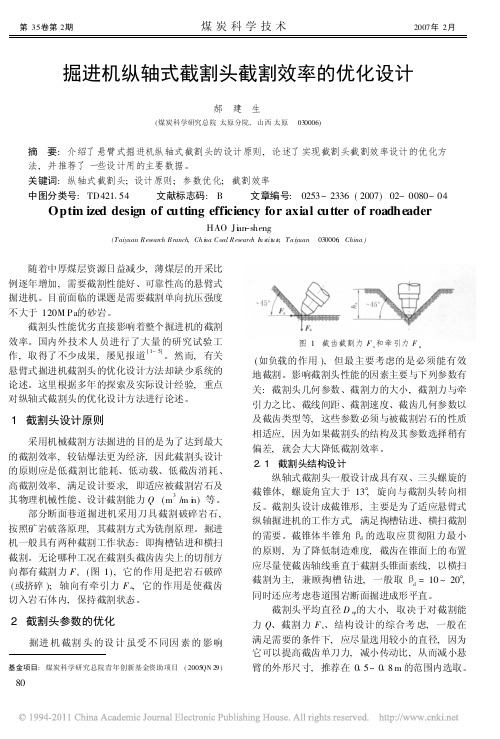
岩石名称 煤 砂岩 页岩
D
D
切屑 厚 度 ( 截 齿 截 割 煤 岩 体 的 深 度 ) , mm; 岩石的抗拉强度, M Pa ; 截齿的刀具角 , ( ); 岩石 的脆性系 数, K =
D
/M Pa
Z
/M Pa
F a /F s 0 8~ 1 0 1 8~ 2 0 1 3~ 1 5 1 1~ 1 3
图 1 截齿截割力 F s 和牵引力 F a
( 如负载的作用 ), 但最主要考虑的是必须能有效 地截割。影响截割头性能的因素主要与下列参数有 关 : 截割头几何参数、截割力的大小 , 截割力与牵 引力之比、截线间距、截割速度、截齿几何参数以 及截齿类型等, 这些参数必须与被截割岩石的性质 相适应 , 因为如果截割头的结构及其参数选择稍有 偏差, 就会大大降低截割效率。 2 1 截割头结构设计 纵轴式截割头一般设计成具有双、三头螺旋的 截锥体 , 螺旋角宜大于 13 , 旋向与截割头转向相 反。截割头设计成截锥形 , 主要是为了适应悬臂式 纵轴掘进机的工作方式, 满足掏槽钻进、横扫截割 的需要。截锥体半锥角
2 2 2 牵引力和截割力比值 切入岩石的阻力和保持截割状态所需的力产生 了牵引力。截齿牵引力和截割力比值大小 , 主要决 定于煤岩的单向抗压强度及其他物理机械性能 , 岩 石越硬 , 比值越大。对较软且脆的煤岩, 牵引力和
第 35 卷第 2 期
煤炭科学技术
加 ; 后角
2007 年 2 月
是为了减小截齿与 被截割岩体的接触 对截割
Opti m ized design of cutting efficiency for axial cutter of roadheader
纵轴掘进机可伸缩小切割头结构的设计

纵轴掘进机可伸缩小切割头结构的设计摘要:切割头是掘进机的直接工作部件,其直径的大小直接影响到截齿的破岩能力。
可伸缩切割臂因为结构比较复杂,切割头的直径也相应较大。
在目前的掘进机种类中,大部分的可伸缩切割部都存在切割头直径过大,破岩能力不足的缺点。
为了提高掘进机的破岩能力,适应岩石硬度较大的巷道,小直径切割头结构的研究,具有重大意义。
关键词:掘进机;伸缩结构;小切割头一、现状纵轴悬臂式掘进机的切割臂就功能来说主要有两种形式,即可伸缩和不可伸缩。
可伸缩的切割臂保证切割头灵活地前后移动,具有操作方便,巷道成形好等许多优点。
但因为要设计伸缩结构,导致切割臂的直径偏大,从而使切割头直径也相应较大。
不可伸缩的切割臂虽然有很多不足,但它的结构简单,尺寸相对较小,它的最大优点就是可以采用小直径切割头。
因此,掘进机产品中采用伸缩结构的切割头直径普遍比较大。
二、分析切割头是掘进机的直接工作部件,其直径的大小直接影响到截齿的切入力即破岩能力。
根据公式F=n/r,其中:F为截齿切入力、n为切割主轴输出扭矩、r 为切割头半径。
显然,截齿的破岩能力与切割头半径成反比,即切割头半径越小,截齿破岩能力越强。
不伸缩的切割臂内部结构简单,切割臂外筒直径小,切割头体的直径也比较小,但它的缺点很多,主要有:切割范围小,落料收集不灵活,巷道清底困难等。
因此,只要巷道条件允许,总是优先采用切割头可伸缩的掘进机作业。
目前,掘进机可伸缩切割臂的结构如图1所示。
图11、切割头体2、切割主轴3、动端盖4、浮动油封5、螺栓6、静端盖7、轴套8、主轴承9、伸缩筒10、切割臂外筒从图中可以看出,切割头体、切割主轴和主轴承是主要受力件。
伸缩筒带动切割头伸缩,切割臂外筒起保护和加强作用。
切割头体直径的大小直接受切割臂外筒的直径影响,可伸缩切割部因为要设计伸缩结构,所以切割臂内部结构复杂,在保证强度的前提下,外筒直径不可能缩小太多。
受切割头破岩能力的限制,这种结构一般只能适合半煤岩和全煤巷道。
关于纵轴式掘进机截割头外形设计的讨论

关于纵轴式掘进机截割头外形设计的讨论摘要:介绍了纵轴式掘进机截割头外形的设计要求以及重要的参数要求,联系实际的工作情况,对于截割头不同外形尺寸进行分析关键词:截割头外形参数我国各大煤矿采用的掘进机截割头,按其布置方式分为纵轴式和横轴式两大类。
而针对我国煤层的工况以及考虑使用的经济性,纵轴式截割头普遍被各种掘进机型所应用,现根据几年来我们公司设计和现场使用纵轴式截割头的情况,浅谈自己的认识。
1 截割头外形尺寸的确定截割头的外形尺寸很关键,一个合理的外形尺寸,不仅可以使截割头具有较强的破煤岩能力,而且在工作过程中可以获得较平整的巷道顶板、底板和侧帮。
(1)截割头的长度。
纵轴式掘进机截割头的长度是指沿截割臂轴向方向的长度,其值的大小影响工作效率。
截割头长度较长,工作时截割阻力增加,尤其是在截割臂摆动的过程中,会使截割臂摆动速度降低,一个工作循环的时间加长,影响掘进速度;截割头太短,钻进深度就会减小,也会使掘进机的掘进速度降低。
另外,截割头的长度与工作面的棚间距也有一定的关系,理想状态下,一次或几次掘进的距离应该等于整数倍的棚间距离(我们假设一次掘进的距离就等于一个截割头的长度),但是这种计算方式是不能实现的,因为各个地域地质条件的不同决定了工作面架设的棚间距离不同,所以这种算法不能得出固定的尺寸。
通常,根据实际经验,纵轴掘进机截割头的长度可取500~900mm,大功率的掘进机可以取到1100mm左右。
(2)截割头的直径。
我们先通过截割电机的功率来初步确定截割头的转矩:式中:P—截割头切割功率(kw)N—截割头转速(r/min)则截割头平均切割力F:式中:R—截割头的平均直径从以上计算可以推断,在功率和转速已经固定的前提下,切割力的大小与截割头直径有直接的关系,假设截割头上有m个截齿,且载荷均布,则会有:可见,若截齿数量一定,直径越大,每个截齿的切割力就越小,那么是不是截割头直径越小越好呢?显然不是的,截割头直径越小,工作面的循环时间就越长,工作效率就越低。
纵轴式掘进机截割头截齿工作角度的确定及工艺实现

越 利于纵向钻进 ,当 s= 9 0 。 时 ,其最利 于纵 向钻进 。但 是 , 在截 割头摆 动截 割 时则使 截 齿无 法楔 人 岩体 ,导致 齿 身、 齿座 等与岩体严 重摩 擦 ,以至 于无法 正常 截割 。因此 ,截 齿 的倾 斜角应考虑截齿的相对截割头的位置进行 确定。 由倾斜角的定义可知 ,倾斜角 为两个面之 间的夹角 ,随
/ _ 0 B C… c l a n ( 7 )
当截割 角很小 或 为 0 。 时( 图3 a ) ,齿尖 较易 楔人 岩体 ,
岩体受到较大的拉伸和剪切应力 ,但压应力很 小 ,很难 形成 密实核。从理论上分析 ,此时截割阻力、截割 比能耗 和产尘 量均较小 ,破岩效果较好 ,但 由于实际工况 的限制 ,这 时齿 体与岩体 之间产生严重 的摩擦 ,反而使截割力 、截割 比能耗 和产尘量很大 ,截齿寿命大大降低 。因而 ,为了使得截齿 具
f
有较好 的截割性 能 ,常使截 割角 6> ( 为截齿合 金头半锥
角) 。此 时( 图3 b ) 截齿切削刃对 岩体的力指 向 自由面 ,岩 体 受压形成发育不充分的密实核 ,且岩石的破碎是 由挤 压、剪 切和拉伸联合作用完成的 ,如果角度设计合理 ,避免齿体 与 图 4 静态截齿工作角度示意 图 根据 图 4 ,由几何关 系可得 :
截 割角 :
一 …
角, 聊 为倾 斜角 。
2 工 作 角度 的确 定方 法
2 . 1 截割 角的确 定 方法
截割角 6 是一 个重 要 的工作 角 度 ,为使 截 齿具 有较 好 的截 割效 果 ,应从 截割 阻力 、截割 比能耗 以及 产尘 量 和避 免齿体 与岩体产 生摩擦 等 方面 对截 割角 占进 行 分析 。截 割 角对截 割效果 的影 响如 图 3所示 。
截齿排布圆周角对纵轴式掘进机截割头设计性能的影响

截齿排布圆周角对纵轴式掘进机截割头设计性能的影响张梦奇【摘要】以变升角螺旋线纵轴式截割头为基础,采用三维设计结合仿真的方式,对截齿按等圆周角间距排布的QC型截割头和按不等圆周角间距排布的UC型截割头进行了设计计算.计算过程的外部参数均相同.当截割头转速为30 r/min,横向移动速度为0.04 m/s,钻入深度为截割头全长时,QC型截割头主要破岩区切屑图单元面积平均值比UC型截割头大11.7%,可获得更大的岩屑块度;且有效截齿数变动量和截割合力变动量均较小,载荷稳定性更好.仿真模拟结果表明,虽然QC型截割头制造相对复杂,但设计性能优于UC型截割头.【期刊名称】《煤矿机电》【年(卷),期】2013(000)002【总页数】5页(P19-23)【关键词】截割头;截齿排布;圆周角;截割性能【作者】张梦奇【作者单位】中国煤炭科工集团太原研究院,山西太原030006;煤矿采掘机械装备国家工程实验室,山西太原030006【正文语种】中文【中图分类】TD421.5+20 引言安装锥形截齿[1]的截割头因截齿损耗少和破岩能力强已被广泛应用于悬臂式掘进机上,对截齿的截割过程和排布形式已进行了大量研究[2-4]。
截割头外形、螺旋线特性、截齿和齿座类型、截齿排布形式是纵轴式截割头的主要设计因素,降低工作过程中产生的振动是截割头优化设计目标[5,6]之一。
本文对截齿按等圆周角间距排布的QC型截割头和截齿按不等圆周角间距排布的UC型截割头的性能特点进行分析和对比。
1 纵轴式截割头设计根据现有掘进机整机设计参数,截割头设计为圆柱、圆锥和球的组合体,螺旋线数为3[7]。
为使截割头在截入深度较大的条件下能够顺利排屑以及降低截割头大端截齿和齿座的磨损,采用变升角螺旋线形式(图1),从圆柱体段到球体段,螺旋升角由12°逐渐增大为30°,且在球体上变化率较大。
在截割头大端减小升角,可减少岩屑沿螺旋线切线方向抛出时与截齿和齿座的磨损;在小端加大升角,有利于提高岩屑的排出速度。
- 1、下载文档前请自行甄别文档内容的完整性,平台不提供额外的编辑、内容补充、找答案等附加服务。
- 2、"仅部分预览"的文档,不可在线预览部分如存在完整性等问题,可反馈申请退款(可完整预览的文档不适用该条件!)。
- 3、如文档侵犯您的权益,请联系客服反馈,我们会尽快为您处理(人工客服工作时间:9:00-18:30)。
纵轴式掘进机截割头的设计
作者:廉浩冯健
来源:《中国新技术新产品》2014年第03期
摘要:本文介绍了纵轴式掘进机截割头的设计原则,讨论了提高截割头截割效率的合理方案,提供了设计用的主要数据。
关键词:截割头;设计原则;截割效率
中图分类号:TD42 文献标识码:A
1 概要
本文以纵轴式掘进机的截割头为研究对象。
截割头是掘进机的关键部件,它直接参与对工作面的掘进工作。
其设计参数较多,这些参数之间互相影响和制约,同时截割头的设计质量的好坏决定了掘进机整机的截割性能,这对截割头的使用寿命,以及整机的稳定性和可靠性都有着直接的影响。
2 工作原理
掘进机的工作过程是:操纵行走机构向工作面推进,使截割头在工作面的左下角钻入,水平摆动油缸使截割头横向截割到巷道的右侧。
然后利用升降油缸把截割头上升接近等于截割头直径的距离,并使截割头向巷道左侧截割。
如此往复截割运动,截割头就可以完成整个工作面的截割。
当然掘进机的截割方式与掘进巷道断面的大小,形状,煤岩的分布情况有关。
在截割头截落煤岩后,由装运机构将其装进掘进机中间的输送机构,再最终装进矿车或巷道输送机。
因此,纵向截割头通常的截割过程可以总结为纵向钻进、水平摆动截割和垂直摆动截割三种工作方式。
3 结构研究
3.1 影响设计的因素
如果能保证在旋转截割的过程中,使参加截割的每个截齿都截割相同大小的煤岩,让各截齿的受力相等、运行平稳,并且产生的磨损也基本相同,这样的截割头设计是最理想的。
但是有很多因素影响截割头的设计,主要有以下几个方面:
(1)煤岩自身的性质,主要有抗截强度、硬度、磨蚀性、坚固性系数等;
(2)截割头的结构参数,主要有截割头的几何形状、外形尺寸、截齿排列、截齿数量以及截线间距等;
(3)截割头的工艺性参数,主要有摆动速度、截割头转速、切削厚度、切削深度等。
在截割头的设计上,这些因素的影响并不是孤立的,它们之间相互关联和制约。
3.2 结构形式
3.2.1 外形
截割头的外形是指截割头的几何形状,它是由截齿的齿尖所形成的外部轮廓,通常称为截割头包络面。
各截齿的齿尖位置投影到截割头主轴平面上,将这些投影的点用线连接起来,形成了齿尖的包络曲线,将形成的包络曲线绕截割头自身主轴转动就形成了截割头的空间曲面轮廓。
3.2.2 组成
纵轴式掘进机截割头主要由截割头体、截齿、截齿座、螺旋叶片、喷嘴、耐磨块等组成。
在截割头体上焊接螺旋叶片,将截齿座按照设计要求焊接在螺旋叶片上,截齿安装在齿座里。
喷嘴的位置指向截齿齿尖方向,这有利于在截割时对工作面的灭尘。
因为煤岩体具有磨蚀性,所以在截割头体上焊接耐磨块来进行保护。
3.2.3 尺寸参数
掘进机截割头的尺寸参数主要包括:截割头长度、截割头直径、螺旋头数和升角等。
(1)截割头长度
纵轴式掘进机截割头的长度是指从截割头顶端到底端在轴线方向上的距离。
截割头设计的过长,截齿的截割阻力增大,导致截割机构的摆动速度受到影响,截割能耗也会增加,如果截割功率不相适应会影响掘进速度。
反之,截割头长度过短时,虽然可以充分利用自由面和地压的作用,减小截割阻力,但是截割时间会加长,截割的工作循环次数加大,使得生产效率降低。
所以在截割头长度的设计中,应予以综合考虑。
(2)截割头直径
截割头的直径主要影响掘进机的截割力和工作循环时间。
截割头直径过大,则切向截割力降低,当截割力降到低于煤岩的截割阻力时,截割头就无法正常工作;而当截割头直径太小,截割头切向截割力增大,但是由于掘进机截割的循环时间变长,同样影响掘进机的掘进速度。
当截割功率和截割头转速一定时,单个截齿的平均截割力受到截割头直径的影响。
截割力矩为:
(3-1)
平均截割力为:
(3-2)
平均单齿截割力为:
(3-3)
式中:MC—截割头转矩,N.m;N—截割功率,kW;n—截割头转速,r/min;FC—平均截割力,N;D—截割头平均直径,m;F1C—平均单齿截割力,N;Zm—工作齿数,可取总齿数的一半,个。
(3)螺旋头数和升角
截割头螺旋叶片的头数和叶片升角的大小共同影响了截割头的排屑能力。
一般认为,截割头的螺旋叶片头数不应大于四个,因为螺旋头数越多,截齿的布置越困难,使得结构复杂,截割头重量也会增加,不利于截割的稳定性。
增大螺旋升角,会影响截割头上截齿的布置数量,单个截齿的截割力变大,但优点是截割的煤岩块度增大,减少粉尘的产出量;减小螺旋升角,截割头截割时受力更好,有利截割的稳定,但粉尘量会加大。
结语
由上可知,截割头直径越小,平均截割力就越大,平均单齿截割力也越大。
同时要提高生产率,减少工作循环时间,应该选择大直径的截割头,而且截割头长度越长,生产率也越高,向装运机构装煤的效果越好。
实践证明,截割头的合理设计直接影响着掘进机的工作效率和使用寿命,因此必须给予足够的重视。
参考文献
[1]李晓豁.掘进机纵向截割头的运动学分析及简化计算[J].黑龙江矿业学院学报,1998,Vol.8(No.3):24-28.
[2]项阳,姜年朝,等.悬臂掘进机纵轴式截割头运动学分析[J].贵州工业大学学报,1998,Vol.27(No.3):32-38.
[3]李贵轩,李晓豁,刘蕴章.掘进机械设计[M].阜新:阜新矿业学院,1992.。