掘进机截割部设计
掘进机截割部
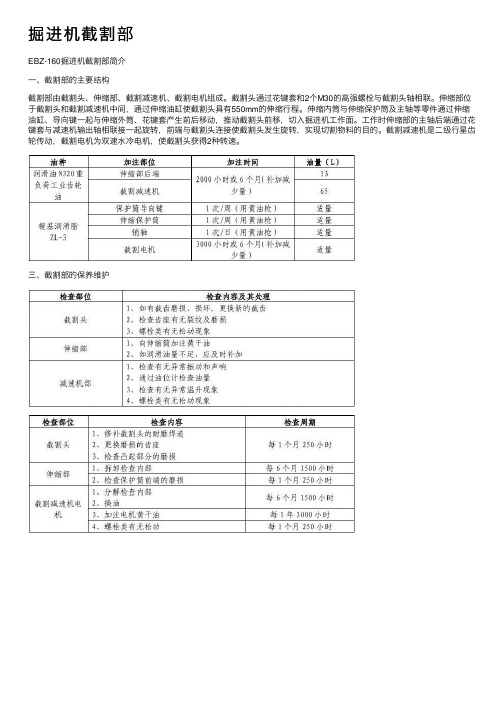
掘进机截割部
EBZ-160掘进机截割部简介
⼀、截割部的主要结构
截割部由截割头、伸缩部、截割减速机、截割电机组成。
截割头通过花键套和2个M30的⾼强螺栓与截割头轴相联。
伸缩部位于截割头和截割减速机中间,通过伸缩油缸使截割头具有550mm的伸缩⾏程。
伸缩内筒与伸缩保护筒及主轴等零件通过伸缩油缸、导向键⼀起与伸缩外筒、花键套产⽣前后移动,推动截割头前移,切⼊掘进机⼯作⾯。
⼯作时伸缩部的主轴后端通过花键套与减速机输出轴相联接⼀起旋转,前端与截割头连接使截割头发⽣旋转,实现切割物料的⽬的。
截割减速机是⼆级⾏星齿轮传动,截割电机为双速⽔冷电机,使截割头获得2种转速。
三、截割部的保养维护。
掘进机截割部设计开题报告
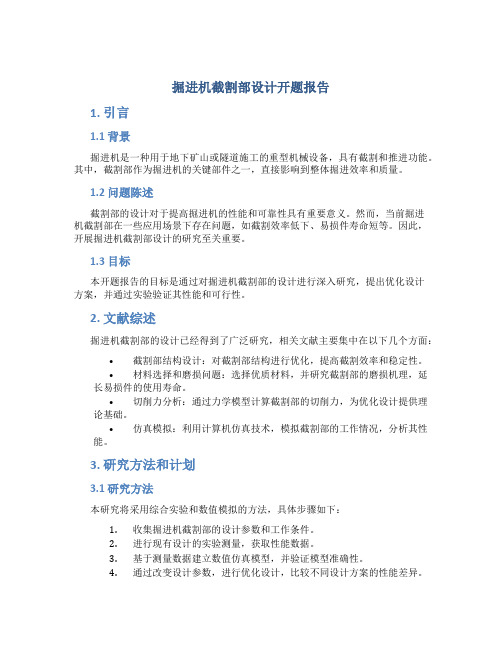
掘进机截割部设计开题报告1. 引言1.1 背景掘进机是一种用于地下矿山或隧道施工的重型机械设备,具有截割和推进功能。
其中,截割部作为掘进机的关键部件之一,直接影响到整体掘进效率和质量。
1.2 问题陈述截割部的设计对于提高掘进机的性能和可靠性具有重要意义。
然而,当前掘进机截割部在一些应用场景下存在问题,如截割效率低下、易损件寿命短等。
因此,开展掘进机截割部设计的研究至关重要。
1.3 目标本开题报告的目标是通过对掘进机截割部的设计进行深入研究,提出优化设计方案,并通过实验验证其性能和可行性。
2. 文献综述掘进机截割部的设计已经得到了广泛研究,相关文献主要集中在以下几个方面:•截割部结构设计:对截割部结构进行优化,提高截割效率和稳定性。
•材料选择和磨损问题:选择优质材料,并研究截割部的磨损机理,延长易损件的使用寿命。
•切削力分析:通过力学模型计算截割部的切削力,为优化设计提供理论基础。
•仿真模拟:利用计算机仿真技术,模拟截割部的工作情况,分析其性能。
3. 研究方法和计划3.1 研究方法本研究将采用综合实验和数值模拟的方法,具体步骤如下:1.收集掘进机截割部的设计参数和工作条件。
2.进行现有设计的实验测量,获取性能数据。
3.基于测量数据建立数值仿真模型,并验证模型准确性。
4.通过改变设计参数,进行优化设计,比较不同设计方案的性能差异。
5.选择最优设计方案,并进行实验验证。
3.2 研究计划本研究计划分为以下几个阶段:1.背景调研:对掘进机截割部的设计进行全面了解,收集相关文献并进行综述。
2.参数测量:设计并搭建实验平台,对现有设计进行性能测量。
3.数值模拟:基于实验数据建立数值仿真模型,验证模型准确性。
4.优化设计:通过数值模拟和参数调整,得出不同设计方案的性能差异。
5.实验验证:选择最优设计方案,并进行实验验证,比较实验结果与数值模拟结果的一致性。
6.结果分析:对实验结果进行分析,总结结论,并提出进一步研究的建议。
综掘机EBZ160部件构成

6、行走部
链轮及履带实现行走。
1、可选用液压油、脂缸张紧;设有弹簧减震装置。 2、履带架通过键及M24的高强度螺栓固定在本体两侧, 在其侧面有盖板,方便张紧油缸的拆卸。 3、行走减速机与履带架、行走减速机与驱动链轮采用高
强度特殊螺纹连接,在强震动下不松动。
4、可选用支重轮和摩擦板式行走部。
6、行走部(履带式支重轮结构)
6、行走部(整体履带结构摩擦板式)
7、后支撑部
后支承用来减
少工作时机体的振
动,防止机体横向
滑动,在两边分别 装有升降支承腿油 缸。电控箱、泵站 电机都固定在后支 承上,后部配有与 二运连接的旋转托
7、后支撑部
1、采用箱形焊接
结构;整体刚性好。
外喷雾;另一路经过切割电机后进入外喷雾,
起到灭尘和冷却截齿的作用。
液压系统包括液压油箱、变量柱塞泵、多路阀、液压先导操作台、 液压马达、油缸、冷却器以及各油管总成、胶管总成、接头、密封件, 六点压力表等,其主要部件为国际品牌(力士乐)。
9、液压系统
10、电气系统
电气系统相当于人的神经,它同液压系 统一起使掘进机各机械部分联动,完成掘进工 作。 主要由防爆操作箱、防爆电控箱、截割 电机、油泵电机、(锚杆电机)、电动滚筒、 矿用隔爆型压扣控制按钮、防爆电铃、照明灯、 防爆电缆等组成。
综掘机EBZ160部件构成
悬臂式掘进机一般由截割部、铲板部、第一运输机、本体部、行 走部、后支承、液压系统、水系统、润滑系统、电气系统10部分构成。 悬臂式掘进机产品型号编制 :
E
B
Z
160
截割机构功率 KW 纵轴式 悬臂式 掘进机
掘进机在液压、电控系统控制下,配合协调一致,轻松灵活地完
掘进机截割部设计(DOC)

2.1.2 各部件的结构型式的确定2.1.2.1 切割机构(3)行星减速器主要由箱体、减速齿轮、二级行星轮架、输入、输出轴构成。
太阳轮与行星轮相啮合,此行星轮通过两个轴承装在星轮轴上,两端装有孔用弹性挡圈,星轮装在第一级行星架相应的轴孔内,内轮与箱体组成一体并与行星轮啮合带动第一级行星架,实现第一级减速[7]。
第二级的太阳轮与第一级行星架为渐开县花键联结,太阳轮与第二行星轮啮合,此行星轮装在第二级的轮轴,此轮轴装在第二级行星架相应轴孔内。
这里内轮与减速器壳体组成一体与行星轮啮合,此星轮不仅自转还绕太阳轮公转,从而实现第二级减速器。
图2-1 EBZ200E掘进机的截割部行星减速器结构Fig.2-1 EBZ200E roadheader in Jiamusi Coal Mine Machinery Co. Ltd.2.2.4 截割机构技术参数的初步确定2.2.4.3 电动机的选择根据行业标准MT477-1996YBU系列掘进机用隔爆型三相异步电动机选择,确定截割功率为200kw,额定电压AC1140 /660 V,转速1500rpm表2-2电动机的基本参数[13]功率/kW 效率η/%功率因数/cosϕ堵转转矩堵转电流最小转矩最大转矩冷却水流量/31m h-⋅额定转矩额定电流额定转矩额定转矩200 92 0.85 2.0 6.5 1.2 2.6 1.33悬臂式掘进机截割机构方案设计3.1截割部的组成掘进机截割部主要由截割电动机、截割机构减速器、截割头、悬臂筒组成。
见图3-1.截割部是掘进机直接截割煤岩的装置,其结构型式、截割能力、运转情况直接影响掘进机的生产能力、掘进效率和机体的稳定性,是衡量掘进机性能的主要因素和指标。
因此,工作部的设计是掘进机设计的关键。
1 截割头2 伸缩部3 截割减速机4 截割电机图3-1 纵轴式截割部•3.2 截割部电机及传动系统的选择切割电机的选择应根据工作条件选取,由设计要求可知,所设计的掘进机可截割硬度为小于85Mpa的中硬岩,查表2-1可知应该选取功率为200KW的截割电动机。
关于EBZ160掘进机截割部结构形式的探讨
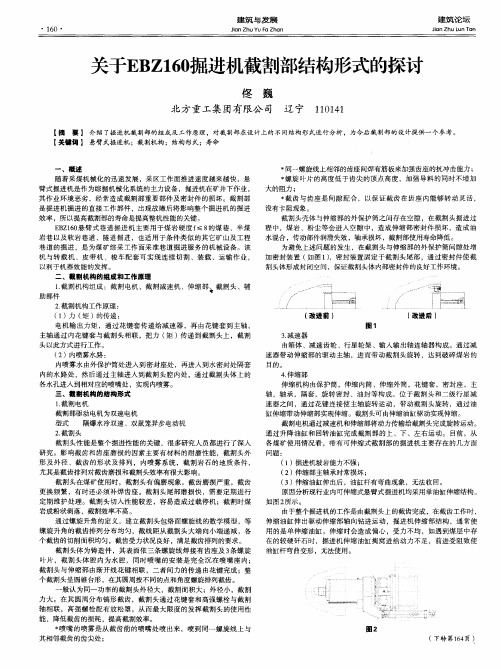
同一螺旋线上相邻 的齿座 间焊有筋板来加强齿座的抗 冲击能力 ; 螺旋 叶片 的高度 低于齿 尖的顶点高 度 ,加强导 料的 同时不增加 大的阻力 ; 截齿 与齿 座是 间隙配 合 ,以保证截 齿在 齿座 内能够 转动 灵活 , 没有卡阻现象。 截 割头壳体与伸缩部 的外保 护筒之间存在 空隙 ,在截割头掘进 过 程 中,煤 岩、粉尘等会 进入空隙 中 , 造 成伸缩部 密封件损 坏 ,造成油 水混合 ,传动部件润滑失效 , 轴 承损坏 ,截割部使用寿命降低。 为避免上述问题 的发生 ,在 截割头与伸缩部 的外保护筒 间隙处 增 加密封装 置 ( 如图 1 ) ,密封装置 固定于截 割头尾部 ,通过 密封件使截 割头体形成封闭空间 ,保证截 割头体 内部密封件 的良好工作环境 。
( 1)掘进机坡 岩能力不强 ; ( 2 ) 伸缩部主轴承时常损坏 ; ( 3 ) 伸缩油缸 伸出后 , 油缸杆有弯 曲现象 ,无法收 回。
原 因分析现行业内可伸缩式悬臂式掘进机均采用 单油缸伸缩结构 。 如图2 所示 。 由于整个掘进机的工作 是由截 割头上 的截齿完成 ,在截齿工作时 , 伸缩油缸伸 出驱动伸缩部 轴 向钻进 运动 ,掘进 机伸缩部结 构 ,通常使 用 的是单 伸缩油缸 ,伸缩 时会造成 偏心 ,受力 不均 ,如遇 到煤层 中存 在的较硬矸石 时 ,掘进机伸 缩油缸 掏窝进给动 力不足 ,前进 受阻致使
建筑 与 发展
・
建 筑论 坛
J i an Zh u L un T an
1 6 O・
J i a n Z h uY u F a Zh a n
关于E B Z 1 6 0 掘进机截割部结构形式的探讨
EBZ135 掘进机装配图册A3版
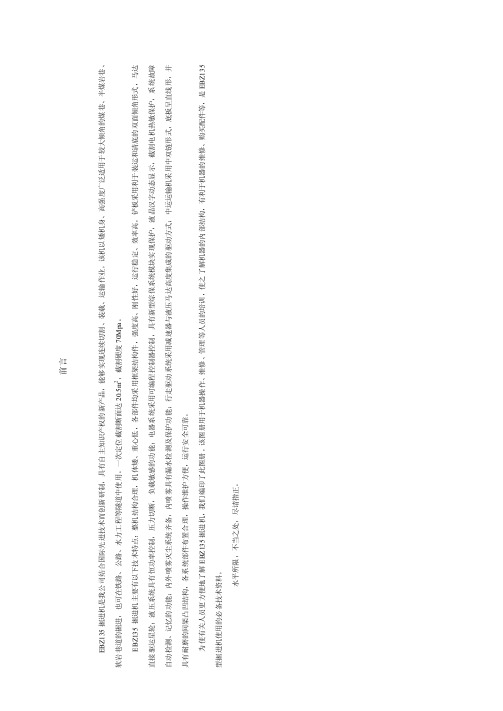
30 S135-01017 29 GB5783-86 28 GB93-87 27 GB5783-86 26 S135-0108 25 S135-0107 24 S100E-0106 23 S135-01005 22 S135-01014 21 S135-0106 20 GB5783-86 19 GB93-87 18 S135-01004 17 GB91-86 16 GB93-87 15 S135-01013 14 GB6178-86 13 S135-01015 12 GB5782-86 11 GB95-85 10 S135-01003 9 S135-01016 8 GB77-85 7 S135-01010 6 GB95-85 5 GB5782-86 4 S135-0103A 3 GB5782-86 2 S135-0102B 1 S135-0101B
名
称
8 8级 10 9级
8 8级
8级 10 9级
10 9级 10 9级
材
料
2
8 0 08
4 0 01
4 0 05
1 100 6
1 114 4
2 12 5
250
211
2 3 08
4 3 0 02
5 1 0 004
287
4 0 01
5 1 0 004
4 0 06
4 0 12
222
16 0 4
1 6 0 03
10
38
39
1026
180 5
46
45
44
43
42
41
40
标记 处数 设计 制图 审核 标准化 计量
文件号
签字
工艺会签
审定
批准
掘进机截割部改造方案说明
掘进机截割部改造方案说明山东兖煤黑豹矿业装备有限公司的含有锚护功能的截割部完全能够满足掘进、临时支护和打锚杆的功能需要,真正实现了掘进和支护工作的快速切换,大大的降低了人工的劳动强度。
一、项目背景:随着我国经济的快速发展,煤炭工业不断朝着机械化,自动化的方向发展,综合机械化才没设备越来越广泛的应用于各种地质条件的煤炭生产中。
巷道掘进环节,除掘进机本身质量有所提高以外,整体工艺水平仍然保持着上世纪七、八十年代的程度。
其主要原因是受地质条件限制,空顶距较小,不能实现掘进与支护工作平行作业。
并且目前所采用的锚杆支护方式,设备简单,主要由人工劳动完成。
目前,在国内中使用过的掘锚机主要有两侧式掘锚机、龙门式掘锚护一体机以及连(采机)锚机。
1、两侧式掘锚机(一代机),山东兖煤黑豹矿业装备有限公司研制。
多斯科、奥钢联等研制过类似的产品,但使用效果不理想,并未形成推广。
该掘锚机主要是以现有掘进机为平台,并利用掘进机的截割部,使锚杆机完成位置的转移,从而完成锚护工作。
思路简洁,容易实现,但锚杆机构与掘进机易发生干涉,两者功能相互影响。
其具体缺点在于:锚杆机易刮帮损坏;打锚杆时截割部不能落地,不满足安全要求;空顶距大,至少空顶一排锚杆;锚杆定位效率低;适应范围窄,不能用于拱形、梯形巷道。
两侧式掘锚护一体机2、龙门式掘锚护一体机(二代机),由三一重装研制,是利用安装在掘进机两侧的伸缩臂,将龙门架推移至设备最前端,锚杆机可以在龙门架上左右横移,从而完成临时支护、锚杆支护功能与掘进机的融合。
克服了两侧式掘锚机的一些不足,如解决了刮帮现象,截割部可以落地,提高了锚杆定位效率,基本实现了零空顶距等。
但仍然存在一些问题,如遮挡截割视线,两主臂同步及刚性问题等。
龙门式掘锚护一体机3、连锚机,奥钢联和久益的进口设备,在国内主要在榆林、鄂尔多斯等地有少量应用。
该机是在连采机基础上,将锚杆机融合在一体上,理论上可以实现截割与支护作业的同步进行,从而提高工作效率。
纵轴式掘进机截割头的设计
纵轴式掘进机截割头的设计作者:廉浩冯健来源:《中国新技术新产品》2014年第03期摘要:本文介绍了纵轴式掘进机截割头的设计原则,讨论了提高截割头截割效率的合理方案,提供了设计用的主要数据。
关键词:截割头;设计原则;截割效率中图分类号:TD42 文献标识码:A1 概要本文以纵轴式掘进机的截割头为研究对象。
截割头是掘进机的关键部件,它直接参与对工作面的掘进工作。
其设计参数较多,这些参数之间互相影响和制约,同时截割头的设计质量的好坏决定了掘进机整机的截割性能,这对截割头的使用寿命,以及整机的稳定性和可靠性都有着直接的影响。
2 工作原理掘进机的工作过程是:操纵行走机构向工作面推进,使截割头在工作面的左下角钻入,水平摆动油缸使截割头横向截割到巷道的右侧。
然后利用升降油缸把截割头上升接近等于截割头直径的距离,并使截割头向巷道左侧截割。
如此往复截割运动,截割头就可以完成整个工作面的截割。
当然掘进机的截割方式与掘进巷道断面的大小,形状,煤岩的分布情况有关。
在截割头截落煤岩后,由装运机构将其装进掘进机中间的输送机构,再最终装进矿车或巷道输送机。
因此,纵向截割头通常的截割过程可以总结为纵向钻进、水平摆动截割和垂直摆动截割三种工作方式。
3 结构研究3.1 影响设计的因素如果能保证在旋转截割的过程中,使参加截割的每个截齿都截割相同大小的煤岩,让各截齿的受力相等、运行平稳,并且产生的磨损也基本相同,这样的截割头设计是最理想的。
但是有很多因素影响截割头的设计,主要有以下几个方面:(1)煤岩自身的性质,主要有抗截强度、硬度、磨蚀性、坚固性系数等;(2)截割头的结构参数,主要有截割头的几何形状、外形尺寸、截齿排列、截齿数量以及截线间距等;(3)截割头的工艺性参数,主要有摆动速度、截割头转速、切削厚度、切削深度等。
在截割头的设计上,这些因素的影响并不是孤立的,它们之间相互关联和制约。
3.2 结构形式3.2.1 外形截割头的外形是指截割头的几何形状,它是由截齿的齿尖所形成的外部轮廓,通常称为截割头包络面。
连续采煤机总体设计及截割部设计
前言连续采煤机是一种集机械、电气和液压为一体的大型复杂系统,在很大程度上与目前国内煤矿使用的掘进机相似,都有履带行走系统、铲煤板、电控箱、液压系统和刮板输送机等。
整体布局也很相似,铲煤板在截割头下,刮板输送机从前向后纵贯整机,装载部和输送机共用一个动力。
连续采煤机和掘进机的最大区别就在截割部。
截割部的动作较掘进机复杂,而内部传动及其结构比较复杂,形式也多样化。
1976年我国开始引进连续采煤机,以单机为主。
目前,这一批设备由于多数不配套,掘进巷道断面偏小,备件供应困难,维护管理技术跟不上等原因,在生产中基本上已不在使用。
20世纪90年代以配套引进为主。
这一时期,由于国内外高效高产矿井的迅速发展,煤层平巷的机械化掘进滞后问题引起了国内外普遍重视。
国内一些煤矿企业针对适合使用连续采煤机的矿井及煤层,为了解决好采掘接替,是高产高效长臂回采工作面充分发挥设备的生产能力,实现快速回采,借鉴国外的先进经验,陕西黄陵矿区、神华集团神东煤炭公司进行配套引进连续采煤机设备的工作,近几年先后引进了包括连续采煤机、锚杆机、破碎机、铲车、运煤车等设备在内的机械化掘进设备。
主要使用在房柱式开采、边角煤回收及长臂工作面煤层平巷的掘进。
这一时期,由于单机引进改为配套引进,同时在配套选型时密切结合矿井煤层地质条件和生产技术条件,连续采煤机的使用率和开机率大幅提高,经济效益好,掘进效率及出煤量均有较大的突破,不断刷新纪录。
综上所述,我国使用连续采煤机的时间不长、经验不足。
还存水沟挖掘、备件供应等问题,仍需通过生产实践逐步探索解决。
1 设计目的及要求设计用途:设计符合要求的连续采煤机及其截割部基本要求1)最大掘高4.5m;2)最大掘宽5.6m;3)巷道坡度±16°;4) 机高大于1M 小于2M,机重大于45t;5)能够在煤层、半煤层下施工,切割煤岩最大单向抗压强度可达100Mpa,可切割性能指标适用切割煤岩硬度,普氏系数f小于等于8,岩石的研磨系数小于等于Mg152连续采煤机的基本概况2.1 连续采煤机的发展概况连续采煤机是美国现代化采掘设备,有近半个世纪的发展讨程。
掘进机截割部讲义
振动过大
振动过大可能是由于轴承损坏、转动 部件不平衡等原因,需拆检修复。
温度过高
如发现截割部温度过高,可能是由于 润滑不足、轴承损坏等原因,需及时 排查。
无法启动
如无法启动,可能是电源故障、控制 线路问题或电机损坏等原因,需逐一 排查解决。
04
掘进机截割部优化与改 进
截割效率优化
截割头转速优化
根据不同地质条件,调整截割头的转速,以提高截割效率。
维护保养规范
制定合理的维护保养规范, 定期对截割部进行检查和 保养,延长使用寿命。
截割部节能技术
能耗监测与控制
实时监测截割部的能耗情况,通过智能控制技术降低能耗。
高效电机与传动系统
采用高效电机和传动系统,减少能量损失,提高能效比。
截割部轻量化设计
通过优化设计,减轻截割部重量,降低能耗和运行成本。
05
案例三:某岩石破碎项目的截割应用
总结词
高效率破碎
详细描述
在某岩石破碎项目中,掘进机截割部展现出高效率的破碎能力。通过对岩石进行精确截割,实现了高 效破碎,满足了工程需求,提高了生产效率。
06
掘进机截割部发展趋势 与展望
技术发展趋势
高效截割技术
随着截割功率和效率的不断提升,未来掘进机截割部将更 加注重高效截割技术的研发和应用,以适应高效掘进的需 求。
1 2 3
市场需求持续增长
随着地下工程建设的不断增多和掘进技术的不断 发展,掘进机截割部的市场需求将持续增长,未 来市场前景广阔。
技术创新推动市场发展
随着技术的不断创新和进步,掘进机截割部产品 的性能和质量将得到不断提升,推动市场不断发 展壮大。
国际市场竞争加剧
随着国际市场的不断开放和竞争的加剧,掘进机 截割部企业需要不断提升自身的技术水平和产品 质量,增强国际竞争力。
- 1、下载文档前请自行甄别文档内容的完整性,平台不提供额外的编辑、内容补充、找答案等附加服务。
- 2、"仅部分预览"的文档,不可在线预览部分如存在完整性等问题,可反馈申请退款(可完整预览的文档不适用该条件!)。
- 3、如文档侵犯您的权益,请联系客服反馈,我们会尽快为您处理(人工客服工作时间:9:00-18:30)。
2.1.2 各部件的结构型式的确定2.1.2.1 切割机构(3)行星减速器主要由箱体、减速齿轮、二级行星轮架、输入、输出轴构成。
太阳轮与行星轮相啮合,此行星轮通过两个轴承装在星轮轴上,两端装有孔用弹性挡圈,星轮装在第一级行星架相应的轴孔内,内轮与箱体组成一体并与行星轮啮合带动第一级行星架,实现第一级减速[7]。
第二级的太阳轮与第一级行星架为渐开县花键联结,太阳轮与第二行星轮啮合,此行星轮装在第二级的轮轴,此轮轴装在第二级行星架相应轴孔内。
这里内轮与减速器壳体组成一体与行星轮啮合,此星轮不仅自转还绕太阳轮公转,从而实现第二级减速器。
图2-1 EBZ200E掘进机的截割部行星减速器结构Fig.2-1 EBZ200E roadheader in Jiamusi Coal Mine Machinery Co. Ltd.2.2.4 截割机构技术参数的初步确定2.2.4.3 电动机的选择根据行业标准MT477-1996YBU系列掘进机用隔爆型三相异步电动机选择,确定截割功率为200kw,额定电压AC1140 /660 V,转速1500rpm表2-2电动机的基本参数[13]功率/kW 效率η/%功率因数/cosϕ堵转转矩堵转电流最小转矩最大转矩冷却水流量/31m h-⋅额定转矩额定电流额定转矩额定转矩200 92 0.85 2.0 6.5 1.2 2.6 1.33悬臂式掘进机截割机构方案设计3.1截割部的组成掘进机截割部主要由截割电动机、截割机构减速器、截割头、悬臂筒组成。
见图3-1.截割部是掘进机直接截割煤岩的装置,其结构型式、截割能力、运转情况直接影响掘进机的生产能力、掘进效率和机体的稳定性,是衡量掘进机性能的主要因素和指标。
因此,工作部的设计是掘进机设计的关键。
1 截割头2 伸缩部3 截割减速机4 截割电机图3-1 纵轴式截割部•3.2 截割部电机及传动系统的选择切割电机的选择应根据工作条件选取,由设计要求可知,所设计的掘进机可截割硬度为小于85Mpa的中硬岩,查表2-1可知应该选取功率为200KW的截割电动机。
电机动力经传动系统传向截割头进行截割,且机体为焊接结构,前端与行星减速器相联,后端联接回转台。
电机输出力矩,通过花键套传递给减速器,再由花键套传到主轴,主轴通过内花套键与截割头相联,把力(矩)传递到割头上,截割头以此方式进行工作。
3.5 传动方案设计悬臂式掘进机的传动方式为电机输出轴通过联轴器将转矩传递给减速器的输入轴,减速器输出轴通过联轴器将转矩传递给主轴,主轴带动截割头转动。
3.5.2 传动类型的设计由于行星齿轮传动具有多分流传动、低压力啮合、作用力平衡和运行多变性等一系列特点,所以在同等工作条件下与定轴齿轮传动相比,行星齿轮传动具有外形尺寸小,重量轻、传动效率高、工作可靠和同轴传动等许多突出优点,因此国内外纵轴式掘进机的截割结构传动系统均采用行星齿轮传动,以期在提高承载能力、效率和可靠性的同时,尽可能地减轻重量、缩小外廓尺寸、降低制造成本。
要求传动装置体积小、结构紧凑,并满足一定的强度要求和减速比要求。
因此,这种工作机构的传动装置多采用行星齿轮传动,以满足以上要求。
如果采用一级减速,则传动比太大,导致齿轮结构很难满足现实要求,因此,决定采用2级齿轮减速。
齿轮系的选取有定轴轮系和周转轮系两种。
由于悬臂采用内伸缩式,电动机、联轴器、的减速器相对于轴向是固定的,从传动装置体积小、结构紧凑等考虑,采用双级行星齿轮传动。
工作机构传动系统布置图3-1。
图3-6传动系统Fig 3-6 The transmission system截割电动机通过联轴节、中心轮、行星轮、内齿轮、中心轮、行星轮和联轴节驱动切割头进行切割。
中心轮固定在悬臂主轴上,行星轮与之啮合,同时又与一个内齿轮啮合,内齿轮固定在箱体上。
使减速器的强度能满足电动机的最大转矩和动载荷,即使电动机过载以至停止,减速器也不至于出现机械故障。
若减速器的强度不能满足电动机的最大转矩,必须设过载保护装置,如安全销、压紧弹簧、液压或摩擦联轴器等。
4截割部减速机构设计4.1 电机选择4.1.1 截割速度根据设计要求,截割头转速n=46r/min4.1.2 截割功率根据所截割煤岩的特性、工作机构的类型,参照类似工作条件、工作范围的国内外各种掘进机,来选定截割电机功率。
表4-1 我国主流掘进机的主要技术性能表Tablet.4-1 Table of mainly performance of roadheader in China 技术参数AM50 S-100 EBJ-120TP EBZ200TY S150J ELMB-75C EBJ-200SH 断面/㎡6~18 8~23 8~18 9~21 9~23 6~17 8~24 可截割硬度/MPa60 70 60 80 80 70 80~100 机重/t 26.8 27 36 51.5 44.6 23.4 53总功率/kW 174 145 190 250 205 130 314截割功率/kW 100 100 120 200 150/80 75 200适应坡度/(°)16 16 16 16 16 16 16系统压力/MPa 16 16 16 23 16 16 16外形尺寸/m×m×m 7.5×2.1×1.6512.2×2.8×1.88.6×2.1×1.559.8×2.55×1.79.0×2.8×1.88.22×2.5×1.5610.8×2.7×1.5生产厂家淮南佳木斯太原分院太原分院佳木斯南京晨光上海分院根据设计要求,截割硬度小于85Mpa,选择截割功率为200kW。
4.1.3选择电机根据截割功率选择电动机型号为:YBUD-200隔爆电动机其主要性能数据如下:表4-1 Tablet.4-14.2 截割减速器结构设计根据性能要求:传动比大,输入轴与输出轴具有同轴性,选用行星齿轮传动。
因传动比较大,采用两级行星传动,传动系统简图如图4-2:图4-1传动系统简图Fig 4-1 The diagram of transmission system行星减速器主要由箱体、减速齿轮、二级行星轮架、输入、输出轴构成。
太阳轮与行星轮相啮合,此行星轮通过两个轴承装在星轮轴上,两端装有孔用弹性挡圈,星轮装在第一级行星架相应的轴孔内,内轮与箱体组成一体并与行星轮啮合带动第一级行星架,实现第一级减速[7]。
第二级的太阳轮与第一级行星架为渐开县花键联结,太阳轮与第二行星轮啮合,此行星轮装在第二级的轮轴,此轮轴装在第二级行星架相应轴孔内。
这里内轮与减速器壳体组成一体与行星轮啮合,此星轮不仅自转还绕太阳轮公转,从而实现第二级减速器。
为了尽量减小减速器体积和重量,将行星减速器的外壳与两级行星传动的内齿圈设计型号额定 功率 同步转速 满载转速 YBUD-200200KW1500 r/min1460r/min成一体。
这种结构使得低速级和高速级的内齿圈齿数相等,整个轮系中齿轮的模数也相等。
4.2.1 传动比的分配确定总传动比并根据传动比分配理论分配各级传动比,并选择齿轮齿数 i 总=0/w n n =1460/46=31.739 高速级的传动比:1i 6.546=低速级的传动比:214.849ii i == 4.2.2 各轴功率、转速和转矩的计算按指导书表4.2-9确定各零件效率取: 联轴器效率 联η=0.99齿轮啮合效率齿η=0.97(齿轮精度为7级) 滚动轴承效率承η=0.98 滚筒效率 卷筒η=0.96 开式齿轮啮合效率开齿η=0.95 0轴(电动机轴): P 0=P r =200kw n 0=1460r/minT 0=9.55P 0/n 0=9.55×200×103/1460=1308.22N.m Ⅰ轴:P 1= P 0×联η=P 0×联η=200×0.99=198kw n 1=1460r/minT 1=9.55×P 1/n 1=9.55×198×103/1460=1295.14N.mⅡ轴:P 2=P 1×12η=P 0×齿η×承η=200×0.97×0.98=190.12kw n 2= n 1/i 1=1460/6.546=223.04r/minT 2=9.55×P 2/ n 2=9.55×190.12×103/223.04=8127.33N.m Ⅲ轴:P 3=P 2×23η= P 2×齿η×承η=190.12×0.97×0.98=180.73kw n 3= n 2/2i =223.04/4.849=45.997r/minT 3=9.55×P 3/ n 3=9.55×180.73×103/45.997=37523.57N.m4.2.3 齿轮部分设计4.2.3.1 高速级齿轮传动的设计(1)选择齿轮材料:太阳轮选用45#钢 调质处理HRC1=56—62 行星轮选用45#钢 调质处理HRC2=56—62 (2)按齿面接触疲劳强度设计计算:齿宽系数 d ψ,查教材表8-23按齿轮相对轴承为非对称布置,取d ψ=0.5 齿轮齿数的选择: 传动比条件:3113/1z z i =-同心条件(各齿轮模数相同):3122z z z =+均布条件(N 为整数):13()/z z k N +=邻接条件:*122()/sin(180/)2a z z k z h +>+根据以上四个条件选择1z =21 2z =57 3z =135 k=3实际传动比 u=Z 3/Z 1+1=7.429传动比误差u u /∆=(7.429-7.399)/7.429=0.0041 误差在±5%内,合适 1)确定齿轮传动精度等级,比照公式:(0.0130.022)t v n =--(4-1) 估取圆周速度V t =6.08m/s,参考教材表8-14,8-15选取II 公差组7级 2)太阳轮分度圆直径d 1, 由下式得:1d ≥(4-2) a 齿宽系数d ϕ : 查表按齿轮相对轴承为非对称布置,取d ϕ=0.8 b 太阳轮转矩T 1 : T 1 =108494N.mmc 载荷系数K : K=K A K v K βK α (4-3) 使用系数K A : 查表得K A =1.3 动载荷系数K v : 查表得K v =1.2 齿向载荷分布系数K β: 查表取K β=1 齿间载荷分配系数K α :由下式及其β=0得1211[1.88 3.2()]cos Z Z γαεεβ==-+=[1.88-3.2(112080+)]=1.68 查表并插值得 K α=1.16则载荷系数K 的初值K t K t =1.3×1.2×1×1.16=1.81d 弹性系数E Z : 查表取得E Ze 节点影响系数(120,0x x β===): 根据条件查图可得H Z =2.5f 重合度系数Z ε : 查表(0βε=) ,取Z ε=0.87g 许用接触应力[]H δ: lim1[]/H H N w H Z Z S δσ=∙∙ (4-4)接触疲劳极限应力lim1H σ,lim 2H σ,查表可得lim1H σ=570N/mm 2, lim 2H σ=460N/mm 2 应力循环次数N : 1016060146030085 1.0510h N njL ==⨯⨯⨯⨯=⨯21/N N u ==101.0510/7.429⨯=1.42×109则查表得出接触强度的寿命系数12,N N Z Z (不允许有点蚀),121N N Z Z == 硬化系数w Z : 根据设计条件查图可取w Z =1接触强度安全系数S H ,按照一般可靠度查S Hmin =1.0—1.1,取S H =1.1,1[]H δ=570×1×1/1.1=518N/mm 2 2[]H δ=460×1×1/1.1=418N/mm 2所以太阳轮分度圆直径d 1的设计初值d 1t 为173.49t d mm ≥=齿轮模数m : m= 11/t d Z =73.49/21=3.50 取m=4 太阳轮分度圆直径的参数圆整值: 11't d Z m ==21×4=84mm圆周速度v : 11'/60000841460/60000 6.42/t v d n m s ππ==⨯⨯= 与估取值 6.08/t v m s =相近,对K V 取值影响不大,不必修正K V 所以可以取定: K V =K Vt =1.2,K=K t =1.81 太阳轮分度圆直径d 1: d 1=1't d =84mm 行星轮分度圆直径d 2: d 2=mZ 2=4×57=228mm 中心距a : a=12()4(2157)16022m Z Z ++==mm 齿宽b : 1min 0.573.4936.74d t b d ϕ=∙=⨯=mm ,取37 行星轮齿宽b 2 : b 2=b=37mm太阳轮齿宽b 1: b 1=b 2+(5--10) 取b 1=45 内齿圈分度圆直径:d 3=mZ 3=4×135=540mm4.2.3.2 低速级齿轮传动的设计(1)选择齿轮材料:太阳轮选用45#钢 调质处理HRC1=56—62 行星轮选用45#钢 调质处理HRC2=56—62 (2)按齿面接触疲劳强度设计计算:齿宽系数 d ψ,查教材表8-23按齿轮相对轴承为非对称布置,取d ψ=0.5 齿轮齿数的选择: 传动比条件:3113/1z z i =-同心条件(各齿轮模数相同):3122z z z =+均布条件(N 为整数):13()/z z k N +=邻接条件:*122()/sin(180/)2a z z k z h +>+根据以上四个条件选择1z =29 2z =53 3z =135 k=3 实际传动比 u=Z 3/Z 1+1=5.5传动比误差u u /∆=(5.5-5.481)/5.5=0.0035 误差在±5%内,合适1)确定齿轮传动精度等级比照公式:(0.0130.022)t v n =--(4-5) 估取圆周速度V t =1.29m/s,参考教材表8-14,8-15选取II 公差组7级 2)太阳轮分度圆直径d 1, 由下式得:2d ≥(4-6) a 齿宽系数d ϕ : 查表按齿轮相对轴承为非对称布置,取d ϕ=0.5 b 太阳轮转矩T 2 : T 2 =7287860N.m mc 载荷系数K : K=K A K v K βK α (4-7) 使用系数K A : 查表得K A =1.3 动载荷系数K v : 查表得K v =1.2 齿向载荷分布系数K β: 查表取K β=1齿间载荷分配系数K α : 由下式及其β=0得1211[1.88 3.2()]cos Z Z γαεεβ==-+=[1.88-3.2(112080+)]=1.68 查表并插值得 K α=1.16则载荷系数K 的初值K t K t =1.3×1.2×1×1.16=1.81 d 弹性系数E Z : 查表取得E Ze 节点影响系数(120,0x x β===): 根据条件查图可得H Z =2.5f 重合度系数Z ε : 查表(0βε=) ,取Z ε=0.87g 许用接触应力[]H δ: lim1[]/H H N w H Z Z S δσ=∙∙ (4-8) 接触疲劳极限应力lim1H σ,lim 2H σ,查表可得lim1H σ=570N/mm 2, lim 2H σ=460N/mm 2 应力循环次数N : 816060197.3230085 1.4210h N njL ==⨯⨯⨯⨯=⨯21/N N u ==81.4210/5.5⨯=2.58×107则查表得出接触强度的寿命系数12,N N Z Z (不允许有点蚀),121N N Z Z == 硬化系数w Z : 根据设计条件查图可取w Z =1接触强度安全系数S H ,按照一般可靠度查S Hmin =1.0—1.1,取S H =1.1,1[]H δ=570×1×1/1.1=518N/mm 2 2[]H δ=460×1×1/1.1=418N/mm 2所以太阳轮分度圆直径d 1的设计初值d 1t 为2113.8t d mm ≥=齿轮模数m : m= 22/t d Z =113.8/29=3.92 取m=4 太阳轮分度圆直径的参数圆整值: 11't d Z m ==29×4=116mm圆周速度v : 12'/60000120197.32/60000 1.24/t v d n m s ππ==⨯⨯= 与估取值 1.29/t v m s =相近,对K V 取值影响不大,不必修正K V 所以可以取定: K V =K Vt =1.2,K=K t =1.81 太阳轮分度圆直径d 1: d 1=1't d =116mm 行星轮分度圆直径d 2: d 2=mZ 2=4×53=212mm 中心距a : a=12()4(2953)16422m Z Z ++==mm 齿宽b : 1min 0.5113.856.9d t b d ϕ=∙=⨯=mm ,取57 行星轮齿宽b 2 : b 2=b=57mm太阳轮齿宽b 1: b 1=b 2+(5--10) 取b 1=65mm 内齿圈分度圆直径: d 3=mZ 3=4×135=540mm4.2.4 轴设计及校核输入轴、中间空心轴和输出轴只承受转矩作用而无弯矩作用,所以在设计计算时只需按照许用转应力计算公式计算出最小轴径,然后按照轴上零部件进行设计,不需要再对轴进行校核计算 输入轴:材料40Cr (100.798A =) 功率158.4P =KW 转速1460n =r/min10047.7d ≥==输入 (4-9) 输出轴:材料40Cr (100.798A =) 功率143.14P =KW 转速36n =r/min100158.4d ≥==输出 (4-10) 中间空心轴材料40Cr (100.798A =) 功率150.58P =KW 转速197.32n =r/min0.53d dν== (4-11)1.03== (4-12)()3411001.03108.71d nν≥==-中间 (4-13) 行星轮轴行星轮轴不仅承受啮合作用力对其施加的载荷,而且还要承受行星齿轮的离心力对其施加的载荷。