粘胶纤维生产各工序对其白度的影响
粘胶纤维指标对纺纱的影响分析

粘胶纤维指标对纺纱的影响分析刘辉;朱娜娜;高会元【摘要】粘胶纤维出厂时,根据指标的不同,可以划分为不同的等级.纤维的强力、超长、倍长、疵点、含油、回潮等指标不仅决定着纤维产品的品质、等级,而且对纺纱加工过程起着重大影响,直接决定成纱质量.本文鉴于工业生产中的经验,针对各指标的变化,针对性地调整工艺并加强日常检测、管理,以保持企业的竞争力,并为企业带来可观的经济效益.【期刊名称】《化学工程师》【年(卷),期】2015(029)008【总页数】3页(P57-58,49)【关键词】纺纱过程;粘胶纤维;指标;品质评定【作者】刘辉;朱娜娜;高会元【作者单位】华北理工大学化学工程学院,河北唐山063009;华北理工大学化学工程学院,河北唐山063009;华北理工大学化学工程学院,河北唐山063009【正文语种】中文【中图分类】TQ341+.1粘胶纤维,化学纤维的一个主要品种。
由天然纤维素经碱化而成碱纤维素,再与CS2 作用生成纤维素黄酸酯,溶解于稀碱液内得到的粘稠溶液称粘胶,粘胶经湿法纺丝和一系列处理工序后即成粘胶纤维。
粘胶纤维[1]具有良好的吸湿性能和染色性能,织物手感柔软,穿着舒适,光稳定性和热稳定性高。
但其形态稳定性和弹性较差,湿态时强度下降,伸度增加。
为了对粘胶纤维的品质做出评价,划分等级,便于企业根据不同等级合理定价,根据粘胶纤维物理、化学性能与外观疵点进行品质评定。
一般分为优、一、二、三等。
粘胶纤维在出厂前,企业重点检测纤维的以下指标[2]:一般包括干断裂强度及其变异系数、湿断裂强度、干断裂伸长率、线密度偏差率、长度偏差率、超长纤维、倍长纤维、残硫、疵点、油污黄纤维、白度、纤度、长度、卷曲数、含油、回潮率等。
根据不同品种的粘胶纤维特点还需对其他指标进行检验,如无纺布用洁净高白纤维需检测pH 值、表面活性物、黄变、灰分、吸水性等,阻燃纤维需检测灰分、锌离子等。
本文中纤维的强力、超长、倍长、疵点、含油、回潮等指标对纺纱过程影响很大,针对各指标的变化,针对性地调整工艺,并且对日常检测管理具有一定的经济效益。
粘胶纤维的质量控制(1)

常见故障1.喂粕机堵料2.浸渍桶搅干浆3.浸渍中投料艰难4.预粉碎或者细粉碎的堵料5.粉碎机粘壁6.老成进口堵料7.老成出口堵料8.老成温度不许9.杂物落入黄化机内10.黄化“串料”产生原因1.分页刀摆动速度与喂粕速度不匹配,拨下叠太多2.浆粕堆码压得太紧实3.浆粕太软,立不起1.喂粕投料速度太快,浆粕成叠投入,使浸渍不透2.浸渍桶液面太低,出浆快,进碱少3.浆粕吸碱值太低1.浆泵效率下降,浆浓逐渐增加2.浆粕吸碱速度偏低,不易润湿,浆料上浮1.碱纤维素过干或者过湿引起预粉碎堵料2.落料斗中碱垢落下,引起细粉碎的堵料3.细粉碎转速降低1.纤维素中半纤维素和树脂等含量过高,粉碎时会形成粘性颗粒,易于粘附在粉碎机壁上1.压榨开始后忘开老成鼓搅拌轴,使细粉碎堵料2.老成鼓跳闸未及时发现3.老成鼓出口料走不动未及时发现1.输送带滑料2.老成出口碱纤塞得太紧1.温度失灵2.温度计周围有碱纤结垢1.料斗上的铁件久后脱落2.机口周围的小杂物清扫时未及时发现一并倒入1.黄化机进出料阀门关启差错2.黄化机阀门失灵及封闭不严解决方法1.调快分页刀摆动次数2.调整浆粕堆码松紧程度,并稍有一点倾斜度即可3.调换浆粕1.调整喂粕速度,使浆粕每次 1~2 张均匀投入2.调整出浆量和浸渍进碱量,保证出浆和进碱平衡3.调整浸渍温度和浓度,添加助剂,保证低吸碱值浆粕的浸渍效果1.改善浆泵转子和泵壳之间的配合状况:间隙小则扬程高,但流量小;间隙大,则扬程低而流量大2.提高浆粕的吸碱速度1.调节压辊速度2.清理碱垢3.增加细粉碎转速1.控制半纤维素和树脂含量1.浸压粉住手压榨,检查细粉碎是否受损2.开启老成鼓或者检查跳闸原因3.排除出料口故障继续走料1.皮带原因、料层太厚、料层太湿2.用细棍掏通1.更换温度计2.疏通以除去碱垢1.发现后清除黄化机内杂物2.加强对料斗和机口周围检查,有杂物主动清除1.粘胶抽入量不多:可降低黄化温度;延长黄化时间;添加浓碱液;增加二硫化碳用量2.粘胶抽入量较多: 则不宜补救, 应报废1.关闭有关阀门 2.检修机台密封系统 3.增加真空泵中的水1.住手进料2.纠正操作错误 3.纠正操作错误3.前面一批料未走完就进下一批料常见故障 产生原因 1.成品中有粗纤维或者 1.个别纺丝部位烛形滤芯由于包扎不良 并丝 而使粘胶短路 2.个别喷丝孔被杂质阻塞2.丝束上有粒状细微 1.脱泡不良 胶块3.丝束上有大胶块 1.凝固浴硫酸浓度过低造成成形差2.喷丝头组件泄露,粘胶连续被丝条带 出 3.喷丝头损伤4.纺前进口压力大,出口压力过低,形 成压力降过大4.断头(闷头) 1.纺前不能连续供胶(换滤布后没有充 胶而存在气泡) 2.喷丝头组件破裂3.计量泵齿轮啮合不良,发生间歇式转 动或者不转动5.异状纤维 1.脱泡不良2.黄化时 CS2 量过多3.更换喷丝头及滤器时未排尽气泡6.出塑化浴的丝束出 1.凝固浴酸度过高导致反应剧烈而浮现 现毛丝 脆丝,经不起拉伸 2.粘胶熟成度过大导致流动差,份子运 动被束缚,不易拉伸 3.塑化浴内拉伸倍数过高 4.丝束在塑化机内机械磨损7.复丝中单丝根数不 1.喷丝孔阻塞2.部份断头缠牵伸盘11.黄化时抽不起真 1.机台有阀门未关到位 空 2.机台密封系统漏气3.真空泵无水或者水太少12.后溶解溢胶 1.进料机台搞错,使后溶解机内粘胶满 料2.阀门开错或者该关的未关到位 1.酸站补加硫酸2.更换喷丝头组件 3.更换喷丝头4.加强头、 二道过滤, 改善粘胶质量或者增 加纺前滤机换布次数 1.有效脱泡 2.减少 CS2 用量 3.更换组件前用 N2 排空 1.降低硫酸浓度 2.减少熟成度3.降低塑化拉伸倍数4.检修塑化槽内部 1.严格纺前滤机开新车操作2.更换喷丝头组件 3.修理计量泵传动部位1.减少粘胶中树脂、蜡质等杂质 2.在粘胶中加助剂,防止结垢1.重新包扎烛形滤芯 2.清洗喷丝头组件1.提高真空度,保证脱泡时间解决方法足3.部份单丝合并到邻丝的丝条上3.提高酸浴清洁度,防止硫及硫化锌沉淀到喷丝头表面4.在酸浴中加助剂,防止结垢8.纺丝机件漏胶1.机件质量差,互换性不好2.垫圈裂边,缺口和带胶皮3.曲管(鹅颈管)边缘破损4.摇摆杆罗纹或者滤套罗纹磨损5.纺丝泵装配不良或者平整度差1.纺丝机件在进厂时应检查质量,保证机件的互换性2.选用弹性和抗疲劳性好的密封圈或者平整的纸垫3.使用中对不合格的机件要剔除,如罗纹磨损的摆杆、滤套、边缘破损的曲管和垫圈等不得使用4.正确装配纺丝泵9.卷曲丝饼1.漏斗偏离离心罐中心2.漏斗本身偏斜3.漏斗或者离心罐振动1.纠正漏头位置2.纠正漏头位置3.制止漏斗或者离心罐振动10.大小头丝饼1.漏斗口距离心罐底部过高或者过低1.调节漏斗口距离心罐底部应为 5mm 摆布11.条纹丝饼1.整台纺丝机浮现条纹丝饼,是漏斗升降次数和离心罐转速配合不良造成的2.个别锭子产生条纹丝饼,是升降架跳动或者个别离心罐转速下降造成1.调节漏斗升降次数和离心罐转速使配合良好2.防止升降架跳动,提高离心罐转速12.羽毛丝饼1.离心罐或者内套中有废丝1.清除离心罐或者内套中废丝13.小丝饼1.纺丝时间不足2.断头时间过长3.漏胶1.增加纺丝时间2.检修设备14.大丝饼1.超时落丝1.缩短落丝时间15.乳白丝1.CS2 超过黄化用量的 20%2.酸浴中硫酸和硫酸钠含量偏高,浴温也过高3.纺丝胶熟成度过低(过嫩胶),氯化铵值>12mL4.浆粕中树脂含量太低5.纤维烘干过于迅速1.保证二硫化碳加入量的准确性2.严格控制酸浴组成和温度。
纺丝速度对粘胶纤维成型的影响分析

纺丝速度对粘胶纤维成型的影响分析【摘要】:随着社会经济不断发展,人们日常生活质量出现翻天覆地的变化,对粘胶纤维质量提出更高要求,传统制造方法已无法满足日常生产要求。
因此,在制造粘胶纤维过程中,会通过提升纺丝速度来增加产量。
基于此,本文通过阐述粘胶纤维成型的基本原理,如物理化学变化、化学反应等,再通过实验研究,分析纺丝速度对粘胶纤维成型的影响,找到最适合粘胶纤维成型的纺丝速度,给粘胶纤维生产匹配最佳工艺参数,全面提高粘胶纤维产品品质。
【关键词】:纺丝速度;纤维成型;影响分析一、前言在粘胶纤维生产过程中,经常通过提升纺丝速度来增加产量。
目前,纤维成型过程是指粘胶通过喷丝头喷出,在纺丝酸浴中产生各种化学反应,如再生、分解、中和、凝固等反应,再通过各种专业操作,最终形成丝条。
但从目前粘胶纤维生产情况来看,随着纺丝速度不断提高,给生产过程带来各种问题,如纤维强度低、可纺性差、成品毛丝多等特征,严重影响到粘胶纤维质量。
可见,纤维形成过程和粘胶纤维质量有直接联系,工作人员通过分析纺丝速度对纤维成型带来的影响,能得到粘胶纤维成型规律,满足纤维成型的基本要求,从而得到大量高质量纤维产品【1】。
二、纤维成型的基本原理(一)化学反应首先,中和反应。
通过进行2NaOH+H2SO4→2H2O+Na2SO4,分解出纤维素黄酸脂,中和粘胶中的副反应产物,H2SO4和纤维素黄酸钠相互结合,分解出游离的纤维素黄酸。
C6H7O2(OH)3-X(OCSSNa)x+0.5XH2SO4→C6H7O2(OH)3-x(OCSSH)+0.5XNa2SO4;其次,纤维素黄酸酯分解和纤维素再生。
C6H7O2(OH)3-x(OCSSH)xx→C6H10O5+XCS2。
(二)物理化学反应按照粘胶纤维的纺丝工艺,要利用计量泵测量出原液车间运输的粘胶,再通过纺丝机喷丝孔传输到纺丝浴,从喷丝孔口流出的粘胶出现先膨胀后变细操作,从而形成初级纤维,然后经过导丝轮运行,拉细径向、拉长轴向【2】。
粘胶纤维工艺学

1
熟成时间:熟成时间主要取决于熟成温度,熟成度的高低,过滤脱泡所需要的时间。提高脱泡速度,可缩短熟成时间;升高熟成温度和降低粘胶中的含碱量,也可以加快熟成速度,但粘胶稳定性差,不利于纺丝。
2
熟成温度:升温可以缩短熟成时间,每升高1℃,在达到相同熟成度下,时间可缩短8~10h,但温度过高,会加速黄酸酯分解,一般熟成温度控制在15~20℃。
影响黄化因素
(1)颜色判断法:纯粹的纤维素黄酸酯应是纯白色,但黄化副反应生成的Na2CS3带有桔黄色。而在正常情况下,副反应速度与纤维素的酯化反应速度大致相等,因此黄化机内物料逐渐由白色变成黄色、桔黄色时,即可认为黄化到达终点。 (2)时间温度结合判断:黄化时间、温度达工艺要求 (3)机内气压判断法:在黄化前,先抽真空(-0.9bar),机内呈负压状态。当CS2注入黄化机内后,由于CS2挥发使压力上升。反应开始后,CS2逐步被消耗掉,压力又回复到负压状态,表明CS2已消耗完毕,黄化到达终点。一般若设备密封性好,可用此法作参考。 (4)电动机负荷(电流值)判断法:随着黄酸酯的逐步生成,物料开始发粘,使电动机负荷逐步增大。若在负荷达到峰值时,加入中途水,负荷即迅速下降,随着物料的搅拌,开始形成团状,负荷又有所回升,黄化到达终点。 我们生产线判断不便于用颜色来判断终点,需根据酯化度的测定来确定合适的黄化温度和时间,再参照机内气压变化或电动机负荷法来判断终点。
干法黄化、湿法黄化,我们采用干法黄化。
黄化方法:
温度;2)时间;3)CS2加入量;4)碱纤维素组成(甲纤和含碱);5)真空度(加CS2前抽真空利于CS2在规定时间内安全加入,又能使CS2加入机台后成为气态,有利于渗透到碱纤维素中,同时也减少了副反应,使黄化反应完全);6)搅拌速度(高,有利于反应进行。干法黄化速度太快易使物料成粒或结团,易使磺酸脂酯化度不均匀)7)半纤含量
粘胶纤维制作过程

粘胶纤维制作过程
粘胶纤维是一种常用的制作纺织品的材料,其制作过程包括以下几个步骤:
1. 原材料准备:粘胶纤维的原料主要是聚酯、尼龙等合成纤维,这些原料需要经过加工处理,如熔融、拉丝和卷绕等,形成适合制作粘胶纤维的纱线或丝线。
2. 粘胶纤维的生产:将原料纱线或丝线通过喷丝、纺丝等工艺制成粘胶纤维。
其中,喷丝是将原料通过高压喷嘴喷出,形成微细的纤维,通过气流或静电力使其成为网状结构;纺丝则是将原料通过旋转的方式拉丝成细丝,再通过加热使其凝固成为纤维。
3. 粘胶纤维的加工:将生产好的粘胶纤维进行加工处理,如拉伸、切断、染色等,制成适合各种用途的产品,如衣物、织物、地毯等。
4. 质量检验:对制成的粘胶纤维和制品进行质量检验,包括检查纤维的细度、强度、拉伸率、耐热性等指标,以及制品的外观、功能等性能。
以上就是粘胶纤维的制作过程,其中每个步骤都需要严格控制,以保证最终产品的质量和性能。
- 1 -。
粘胶纤维生产过程对环境影响方程式

粘胶纤维生产过程对环境影响方程式粘胶纤维的生产过程对环境影响是一个复杂的问题,涉及到多个环节和因素。
以下是一个大致的方程式,可以用于描述粘胶纤维生产过程对环境的影响:1.原材料消耗:粘胶纤维的主要原材料是木浆,其生产需要大量的木材资源。
这会带来森林砍伐和生态环境退化的问题。
2.能源消耗:粘胶纤维生产过程中需要大量的热能和电能,这会造成对煤炭、石油和天然气等化石能源的消耗,同时也会产生大量的二氧化碳等温室气体排放。
3.废物排放:粘胶纤维生产过程中会产生大量废水和废弃物,其中含有有机物、无机盐和重金属等污染物,如果处理不当会对水体和土壤造成污染。
4.污染物排放:在纤维的生产和加工过程中,会产生一些有害物质的排放,如二氧化硫、氮氧化物等大气污染物,这些物质会对大气环境产生不良影响。
5.化学品使用量:粘胶纤维生产过程中需要使用多种化学品,如碱性溶液、硫酸和蒸发剂等,其中部分化学品存在环境风险,如有毒性和生物累积性等,如果不正确使用和处理,会对环境造成污染。
6.运输范围:粘胶纤维的原材料和成品需要进行长距离的运输,包括木材的采伐和运输、成品纤维的配送等,这会导致对道路、港口以及交通方式的压力增大,同时也会增加能源消耗和空气污染。
7.水资源消耗:粘胶纤维生产过程中需要大量的水资源,包括纤维素溶解、废水处理等环节,这会对当地水资源造成压力,并可能引发水源枯竭和水体污染等问题。
8.土地占用:粘胶纤维生产需要用于种植木材的土地,大量的森林和土地资源被占用,在一定程度上会导致生态系统破坏和生物多样性减少。
9.生态系统影响:粘胶纤维生产对当地生态系统的影响是一个长期的过程,涵盖了原材料采集、森林砍伐、土地占用以及生物多样性的丧失等方面。
总结起来,粘胶纤维生产过程对环境的影响主要包括资源消耗、能源消耗、废物排放、污染物排放、化学品使用量、运输范围、水资源消耗、土地占用和生态系统影响等多个方面。
为了降低这些影响,应当采取有效的措施,如优化生产工艺、加强废物处理和回收利用、推广清洁能源和可持续发展等,以减少环境负荷和资源消耗。
粘胶短纤维成品质量影响因素分析
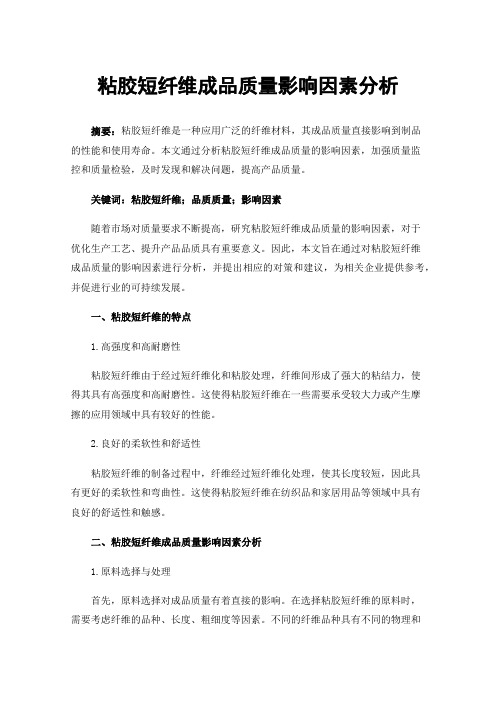
粘胶短纤维成品质量影响因素分析摘要:粘胶短纤维是一种应用广泛的纤维材料,其成品质量直接影响到制品的性能和使用寿命。
本文通过分析粘胶短纤维成品质量的影响因素,加强质量监控和质量检验,及时发现和解决问题,提高产品质量。
关键词:粘胶短纤维;品质质量;影响因素随着市场对质量要求不断提高,研究粘胶短纤维成品质量的影响因素,对于优化生产工艺、提升产品品质具有重要意义。
因此,本文旨在通过对粘胶短纤维成品质量的影响因素进行分析,并提出相应的对策和建议,为相关企业提供参考,并促进行业的可持续发展。
一、粘胶短纤维的特点1.高强度和高耐磨性粘胶短纤维由于经过短纤维化和粘胶处理,纤维间形成了强大的粘结力,使得其具有高强度和高耐磨性。
这使得粘胶短纤维在一些需要承受较大力或产生摩擦的应用领域中具有较好的性能。
2.良好的柔软性和舒适性粘胶短纤维的制备过程中,纤维经过短纤维化处理,使其长度较短,因此具有更好的柔软性和弯曲性。
这使得粘胶短纤维在纺织品和家居用品等领域中具有良好的舒适性和触感。
二、粘胶短纤维成品质量影响因素分析1.原料选择与处理首先,原料选择对成品质量有着直接的影响。
在选择粘胶短纤维的原料时,需要考虑纤维的品种、长度、粗细度等因素。
不同的纤维品种具有不同的物理和化学性质,在成品的性能和外观上会有所差异。
此外,纤维的长度和粗细度也会影响到成品的强度和手感等特性。
因此,在选择原料时,需要根据产品的要求进行合理的选择,以确保成品的质量达到预期。
其次,原料的处理过程也对成品质量产生重要影响。
处理过程包括原料的清洁、染色、漂白等环节。
首先,原料要经过充分的清洁处理,去除其中的杂质和污染物,以保证纤维本身的质量。
其次,在染色和漂白过程中,需要控制好温度、时间和药剂浓度等参数,以确保颜色的均匀度和纤维的亮度。
处理过程中的不当操作或者使用低质量的药剂可能会导致纤维受损或者出现色差等问题,进而影响到成品的质量[1]。
2.纺纱过程中的工艺参数控制首先是纺纱过程中的喷丝压力和喷丝速度。
浅析纤维生产工艺或粘胶短纤维

通过实验与试生产分析,我们首先确定了影响超短纤维品质的关键因素,以其针对关键因素制定解决方案。粘胶超短纤维对纤维的长度与精度提出了很高要求。
(1)普通粘胶短纤维水流式切断机造成纤维长短不一。
(2)粘胶超短纤维的分散性品质达不到要求。
五、根据关键因素制定工艺
1、切断机选型
一、粘胶纤维概述
粘胶纤维又称粘纤,是一种以棉或其他天然纤维为原料调配生产而成的纤维素纤维。在我国现阶段粘胶纤维可以分为普通、改性、高湿模量、强力纤维4种。但近几年来,粘纤又出现了一种名为天丝,竹纤维的比较高档的新品种。但不管怎么变化,粘纤都还是以棉或者其他的天然纤维为原料生产出来的纤维素纤维。一般地,粘胶纤维具有与棉十分相似的吸湿性能,经常与棉、毛或各种合成纤维混纺、交织,用于各类服装及装饰用纺织品,随着生产生活的各类需要,粘胶纤维更是一种应用较为广泛的化学纤维。
3、降低乱丝缠绕丝
影响超短纤维分散性的另一要素是乱丝缠绕丝所形成的打结丝,丝团,在切断后造成超短纤维中的单双眼丝,在应用时会导致纸面不美观。因此必须降低纺丝与后处理过程中的乱丝与缠绕丝。乱丝缠绕丝的成因主要是牵伸在成形过程中因各种外在原因将单丝拉断在水流或蒸汽流的作用下打散发生缠绕造成的。因此从纺丝部位开始与丝条接触部位,所经过的水流和蒸汽流都要考虑进去。首先纺丝及机内二浴部分、后处水洗槽内,塑化浴槽内的导丝部件,由于采用的陶瓷件,在使用一段时间受磨损影响,表面釉质脱落,露出里层,表面光洁度不够,与丝接触时易粘丝,导致单线断裂。之后受所接触水流蒸汽流后,断丝从丝束内游离到表面形成乱丝。因此,需要对这些导丝件的材质进行研究考察,选用耐磨耐酸碱的导丝件,经过对比,选用高品质的三氧化二铝制作的导丝件,在与丝条接触,发生磨损后,由于内外部材质一致,光洁度不发生变化,可满足粘胶超短纤维的使用需求。缺点是价格昂贵。但由于延了使用周期,总体成本仅略有增加。其次调整纺丝工艺,主要是降低盘间牵伸比和塑化浴牵伸比,在保证强度的同时尽量减少单丝拉断现象。
- 1、下载文档前请自行甄别文档内容的完整性,平台不提供额外的编辑、内容补充、找答案等附加服务。
- 2、"仅部分预览"的文档,不可在线预览部分如存在完整性等问题,可反馈申请退款(可完整预览的文档不适用该条件!)。
- 3、如文档侵犯您的权益,请联系客服反馈,我们会尽快为您处理(人工客服工作时间:9:00-18:30)。
样 号
白度 (% )
表 5
脱 硫 后 纤 维 的 白度
1
3
平 均
60.7 59.8 59.2
1 2 3
平 均
77.4 88.2 78.4
79.7
作者简介 :黄方庆 (1959年 ~),男,高级 工程 师,从 事粘胶 纤维生产管理。
【 7 】
2016年第 2期
2016,No.2
人 造 纤 维
A ̄ificial Fibre
总第 252
Sum 252
从 表 1可 以看 出 ,浆 粕通 过 浸 、压 、粉形 成 碱 纤维 素后 ,其 白度 值 由 原 料 浆 粕 的 90% 下降 到 79.7% ,这 主要 是 浆 粕 通 过 浸 渍 时纤 维 素 在碱 的作 用下 醛基 受到 氧化 的缘 故 。 2.3 初生 纤维 的 白度
因为 5D粘胶 短纤 维 的 白度 最 低 ,所 以选 其 作为试 验对 象 。 1.2 试样 准 备
从原 料浆 粕开 始到 成 品纤 维 为止 的整个 工 艺 过程 中 ,所 取 样 品除浆 粕 和纤 维 两 项 以外 , 其余 试样 均需 用温 蒸 留水洗 涤处 理至 中性 ,烘 干备 用 。
52.9
硫 酸 ),在 使 纤 维 素 黄 酸 盐 继 续 分 解 的 同 时 , 还洗 去 了大部 分硫 黄 杂质 的缘故 ,此 时纤维 内 硫 黄 已下 降到 100mg/100g纤 维 以下 。 2.5 脱硫 前纤 维 的 白度
取精 炼机 第一 水洗 后 的纤 维样 品 ,用温 蒸 馏水 洗 至 中性 ,常温 凉干 。测 得 的 白度 数据 列 于表 4。
2 试 结果和讨 论
2.1 原料 浆粕 的 白度 试验 采用 国产 开 山屯木 浆为 原料 ,其 白度
值 为 90% 。 根据 调查 ,有 时在 包装 损坏 ,浆 粕受 到 污
染的情况下 ,其白度值会显著降低 ,被污染浆 粕 的平 均 白度 为 85% ,比未 污染 浆 粕 的 白度 下 降 5%左 右 。 2.2 连续 浸 、压 、粉后 的碱 纤维 素 白度
表 4
脱 硫 前 纤 维 的 白度
样号
白度 (% )
1
平均
60.8 61.3 60.5
60.9
从 表 2可 以看 出 ,初 生纤 维 白度平 均值 为 52.9% ,比碱 纤 维 素 低 26.8% ,这 可 能 是 由 于 刚从 喷 丝 头 喷 出 的丝 束 附着 过 多 硫 黄 杂 质 (约 1000mg/100g纤维 ) 的缘故 。 2.4 切 断 纤维 的 白度
第 46卷第 2期
Vo1.46.№ .2
人 造 纤 维
Artificial Fibre
2016年 4月版
April,2016
粘 胶 纤 维 生产 各 工序 对 其 白度 的影 响
黄 方 庆 河 北纺 织工 程学会 河北 石 家庄 050000
【摘要】从原料浆粕开始到成品纤维为止的整个粘胶 纤维生产过程 ,对粘胶纤维白度影响 最严 重 的是 连 续浸压 粉 工序和 纺 丝工序 ,碱 纤 维素 白度和初 生纤 维 白度 比原 料浆 粕 大幅度 下 降 ,而精 炼各工序 (不经过 漂 白)可使 纤 维 白度 回升 10% 。
测定 初 生纤维 的 白度 ,是将 从 纺丝 机牵 伸 盘 上引 出 的丝 束 剪 断 ,用 温 蒸 馏 水洗 至 中性 , 常温 凉 干 。表 2列 出 了初生 纤 维 的 白度值 。
表 2
初 生 纤 维 的 白度
样号
白 度 (% )
1
j
平 均
52.2 53.8 52.6
59.9
样 号
l
白度 (% )
61.7 61.3 61.2
从表 3可 以看 出 ,丝条 经过 塑化 浴 到切 断 其白度为 59.9% ,比初生纤维 的 白度提 高 了 7.0% 。这 是 因为 从 纺 丝 机 到 切 断 机 要 经 过 长 达 10m以上的高温稀酸塑化浴 (98℃ ,10 L
为 了测 定连 续 浸 、压 、粉后 的碱纤 维 素 白 度 ,从 老 成 鼓 进 口处 取 碱 纤 维 素 样 品 ,用 90℃以上的热蒸馏水反复洗至 中性 ,烘干 ,测 定 的碱 纤维 素 白度如 表 1所示 。
表 1 浸 、压 、粉 后 的 碱 纤 维 素 白 度值
样号
白度 (% )
关键 词 粘胶短 纤 维 白度 生产 工序
本 着 “提 高纤 维 白度 ,不 单 纯 是纤 维 漂 白 问题 ”的这个 观点 ,对粘 胶 纤 维 生 产 中各 工 序 过 程对纤 维 素及纤 维 白度 的影响 进行 了试验 分 析 。下 面分别 简述 粘胶 纤维 生产 系统从 原料 浆 粕 开始 到成 品 纤 维 (不 经 过 漂 白)为 止 的 白度 情 况 。
从 切 断机 取切 断后 的纤 维 ,以凉 蒸馏 水洗 至 中性 ,常 温 凉干 。测得 的切 断 纤维 的 白度如 表 3。
表 3
切 断 纤 维 的 白度 值
从 表 4可看 出 ,第一 水洗 后脱 硫前 所测 得 的纤 维 平 均 白度 为 60.9% ,从 数 字 看 , 比切 断 纤维 的平 均 白度 高 出 1% ,这 可 能 是 因为 从 切 断 到 脱硫 前 纤 维 需 经过 给 纤 槽 和第 一 水 洗 , 由于水 的冲洗 除去 了部分 杂 质 的缘 故 。 2.6 脱硫 后纤 维 的 白度
1 试验准备
1.1 试验 对象 1.5D、2.5D、3D 和 5D粘 胶 短 纤 维 ,虽
然生 产工 艺大致 相 同 ,但 纤维 的 白度随其 纤度 的增 加 而 降 低。1.5D纤 维 的 白度 约 72% , 2.5D和 3D的纤 维 白度 约 66% ,5D纤 维 的 白 度 在 60% ~65% 。这 是 由于纤 维 的纤度 越 细 , 使 纤维 反射 光线 的面积 增加 的缘 故 。