如何控制标签印刷颜色的一致性
印刷色差控制
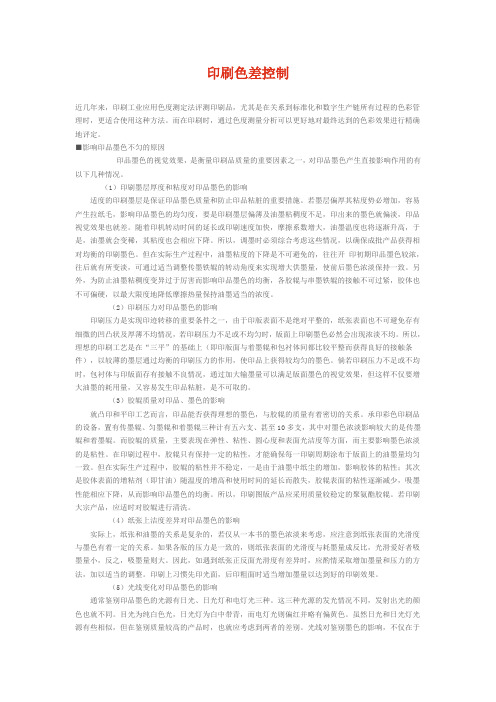
印刷色差控制近几年来,印刷工业应用色度测定法评测印刷品,尤其是在关系到标准化和数字生产链所有过程的色彩管理时,更适合使用这种方法。
而在印刷时,通过色度测量分析可以更好地对最终达到的色彩效果进行精确地评定。
■影响印品墨色不匀的原因印品墨色的视觉效果,是衡量印刷品质量的重要因素之一,对印品墨色产生直接影响作用的有以下几种情况。
(1)印刷墨层厚度和粘度对印品墨色的影响适度的印刷墨层是保证印品墨色质量和防止印品粘脏的重要措施。
若墨层偏厚其粘度势必增加,容易产生拉纸毛,影响印品墨色的均匀度,要是印刷墨层偏薄及油墨粘稠度不足,印出来的墨色就偏淡,印品视觉效果也就差。
随着印机转动时间的延长或印刷速度加快,摩擦系数增大,油墨温度也将逐渐升高,于是,油墨就会变稀,其粘度也会相应下降。
所以,调墨时必须综合考虑这些情况,以确保成批产品获得相对均衡的印刷墨色。
但在实际生产过程中,油墨粘度的下降是不可避免的,往往开印初期印品墨色较浓,往后就有所变淡,可通过适当调整传墨铁辊的转动角度来实现增大供墨量,使前后墨色浓淡保持一致。
另外,为防止油墨粘稠度变异过于厉害而影响印品墨色的均衡,各胶辊与串墨铁辊的接触不可过紧,胶体也不可偏硬,以最大限度地降低摩擦热量保持油墨适当的浓度。
(2)印刷压力对印品墨色的影响印刷压力是实现印迹转移的重要条件之一,由于印版表面不是绝对平整的,纸张表面也不可避免存有细微的凹凸状及厚薄不均情况,若印刷压力不足或不均匀时,版面上印刷墨色必然会出现浓淡不均。
所以,理想的印刷工艺是在“三平”的基础上(即印版面与着墨辊和包衬体间都比较平整而获得良好的接触条件),以较薄的墨层通过均衡的印刷压力的作用,使印品上获得较均匀的墨色。
倘若印刷压力不足或不均时,包衬体与印版面存有接触不良情况,通过加大输墨量可以满足版面墨色的视觉效果,但这样不仅要增大油墨的耗用量,又容易发生印品粘脏,是不可取的。
(3)胶辊质量对印品、墨色的影响就凸印和平印工艺而言,印品能否获得理想的墨色,与胶辊的质量有着密切的关系。
包装胶印纸盒印刷品颜色的控制
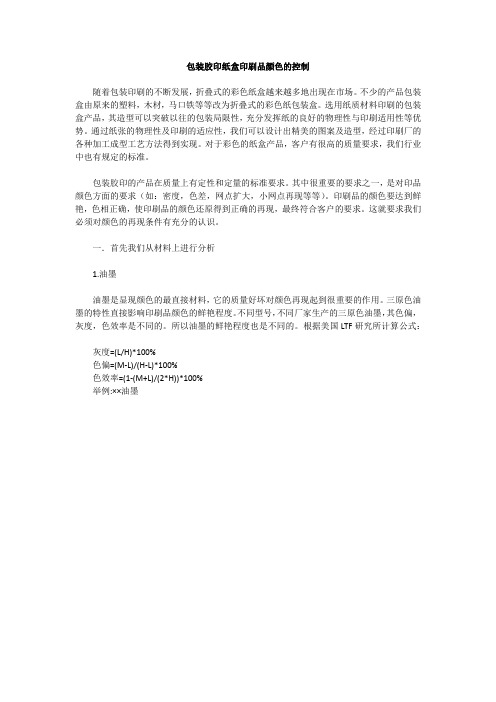
包装胶印纸盒印刷品颜色的控制随着包装印刷的不断发展,折叠式的彩色纸盒越来越多地出现在市场。
不少的产品包装盒由原来的塑料,木材,马口铁等等改为折叠式的彩色纸包装盒。
选用纸质材料印刷的包装盒产品,其造型可以突破以往的包装局限性,充分发挥纸的良好的物理性与印刷适用性等优势。
通过纸张的物理性及印刷的适应性,我们可以设计出精美的图案及造型,经过印刷厂的各种加工成型工艺方法得到实现。
对于彩色的纸盒产品,客户有很高的质量要求,我们行业中也有规定的标准。
包装胶印的产品在质量上有定性和定量的标准要求。
其中很重要的要求之一,是对印品颜色方面的要求(如:密度,色差,网点扩大,小网点再现等等)。
印刷品的颜色要达到鲜艳,色相正确,使印刷品的颜色还原得到正确的再现,最终符合客户的要求。
这就要求我们必须对颜色的再现条件有充分的认识。
一.首先我们从材料上进行分析1.油墨油墨是显现颜色的最直接材料,它的质量好坏对颜色再现起到很重要的作用。
三原色油墨的特性直接影响印刷品颜色的鲜艳程度。
不同型号,不同厂家生产的三原色油墨,其色偏,灰度,色效率是不同的。
所以油墨的鲜艳程度也是不同的。
根据美国LTF研究所计算公式:灰度=(L/H)*100%色偏=(M-L)/(H-L)*100%色效率=(1-(M+L)/(2*H))*100%举例:××油墨所以我们一般对油墨的色彩度进行检测,对于一些印刷品颜色要求高的,在油墨的色彩度上进行挑选,也就是用色彩度高的油墨。
印刷厂自己在调配油墨时,尽量不要在原墨中加过多的辅助料,这样很容易造成油墨的饱和度降低,同时油墨也容易乳化。
墨层的厚度在实际印刷中影响着颜色的再现。
墨层的厚度偏薄,呈现的图文画面灰暗,平淡,墨层的厚度偏厚,呈现的图文处网点扩大,而且发糊,画面沉闷,层次不清。
所以我们要按照样张,控制好油墨用量,控制好油墨的密度值。
印刷品密度范围(CY/T5-1999)包装胶印产品,除了四色以外,经常要用到专色。
标签印刷色彩管理方法探讨

■■■Technology Platform技术看台标签印刷色彩管理方法探讨文/张波在各大超市琳琅满目的货架上陈列着各式各样的包装产品,它是品牌商与消费者沟通的媒介之一。
为了获得消费者的喜欢,品牌商需要更加频繁的更新包装的设计,并且要求包装产品的颜色达到严格的一致性,这其中就包括对个性化标签印刷的颜色要求。
然而,对标签印厂来讲,如何达到品牌商的期望及如何保证颜色的高度一致性是他们面临的一大挑战。
颜色质量需要持续改进从产品设计到上机打样,然后到生产过程控制,整个流程都涉及到颜色管理。
对于印厂而言,越是能够在早期发现问题,越能够避免大量的生产和经济损失。
而对于标签印刷色彩的流程控制又需要我们随着品牌客户的需求变化而变化,那么我们需要在控制方面进行持续改进,如图1所示。
颜色管理的整个过程是印厂制定颜色标准、试验颜色标准、确定合理的容差及完善颜色标准的过程,其中在如何界定颜色是否合格的过程中,我们也可以发现生产环境和印刷机存在哪些根本问题,如图2所示。
每个颜色问题的背后涉及到的根本原因都十分复杂,需要我们在实际印刷过程中不断积累经验。
下面,具体介绍几个在标签印刷色彩控制中经常遇到的问题难点及具体应对方法。
它们分别是:颜色标准规范包含哪些内容、专色色库的数据格式、专色配图1标签印刷色彩流程控制•油墨质量•网纹辗或印版质量•基材或不透明白墨的影响•印刷压力•油墨粘度・印版曲线•网纹辐或印版质量•油墨色序•网点增大图2在界定颜色是否合格过程中可以发现的根本问题28标签技术2020.3技术看台Technology Platform IM墨、上机打样的控制方法,如图3所示。
这些环节也是标签印刷中需要控制颜色的关键环节。
色彩控制易出现问题的环节1.定义颜色标准和印刷生产颜色控制相对于商业印刷来说,标签印刷颜色标准的标准化程度普遍不高,很多时候我们是在随着品牌客户的要求逐步改进和完善自己的颜色标准控制过程,比如非常重要的订单、新纸张的加入、更严格容差的要求。
胶印印刷图像颜色控制技术
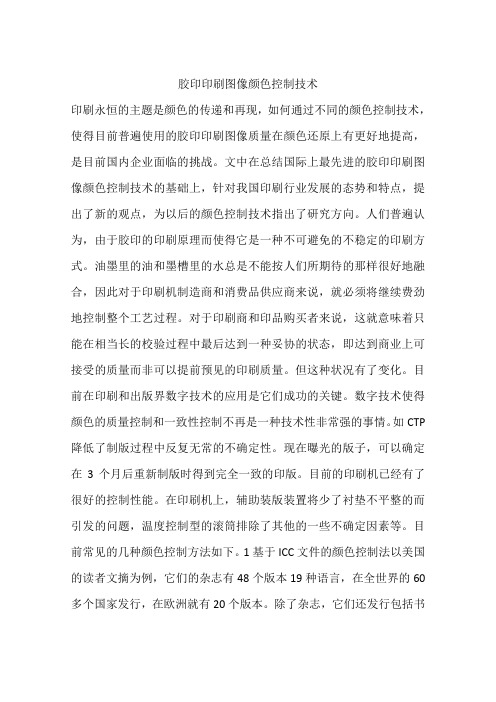
胶印印刷图像颜色控制技术印刷永恒的主题是颜色的传递和再现,如何通过不同的颜色控制技术,使得目前普遍使用的胶印印刷图像质量在颜色还原上有更好地提高,是目前国内企业面临的挑战。
文中在总结国际上最先进的胶印印刷图像颜色控制技术的基础上,针对我国印刷行业发展的态势和特点,提出了新的观点,为以后的颜色控制技术指出了研究方向。
人们普遍认为,由于胶印的印刷原理而使得它是一种不可避免的不稳定的印刷方式。
油墨里的油和墨槽里的水总是不能按人们所期待的那样很好地融合,因此对于印刷机制造商和消费品供应商来说,就必须将继续费劲地控制整个工艺过程。
对于印刷商和印品购买者来说,这就意味着只能在相当长的校验过程中最后达到一种妥协的状态,即达到商业上可接受的质量而非可以提前预见的印刷质量。
但这种状况有了变化。
目前在印刷和出版界数字技术的应用是它们成功的关键。
数字技术使得颜色的质量控制和一致性控制不再是一种技术性非常强的事情。
如CTP 降低了制版过程中反复无常的不确定性。
现在曝光的版子,可以确定在3个月后重新制版时得到完全一致的印版。
目前的印刷机已经有了很好的控制性能。
在印刷机上,辅助装版装置将少了衬垫不平整的而引发的问题,温度控制型的滚筒排除了其他的一些不确定因素等。
目前常见的几种颜色控制方法如下。
1基于ICC文件的颜色控制法以美国的读者文摘为例,它们的杂志有48个版本19种语言,在全世界的60多个国家发行,在欧洲就有20个版本。
除了杂志,它们还发行包括书在内的其他产品,如音乐、视频和其他特殊产品。
随着他们发行和递送方法的拓展,公司也相应地拓展了它们印刷产品的范围,包括电子媒体和传统的印刷媒体。
图像印品是所有印刷读者文摘的印刷场所的任务,它涉及到很多重复的工作和费用。
不同的印刷场所又使得不同版本的图像质量控制几乎是不可能的达到的,颜色管理尤其是个问题。
颜色质量和外观差异从阶调不一致到严重的颜色偏差都会出现。
为此,他们为了避免类似的问题而采用了一套ColourSystems。
包装印刷中同批不同色的原因及消除措施
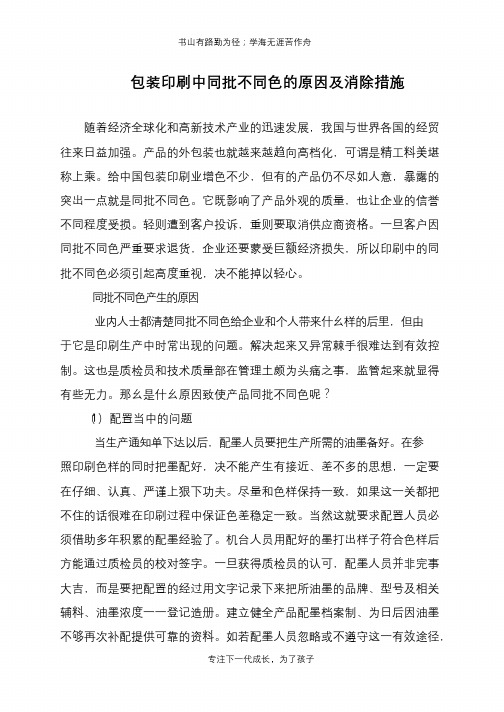
包装印刷中同批不同色的原因及消除措施随着经济全球化和高新技术产业的迅速发展,我国与世界各国的经贸往来日益加强。
产品的外包装也就越来越趋向高档化,可谓是精工料美堪称上乘。
给中国包装印刷业增色不少,但有的产品仍不尽如人意,暴露的突出一点就是同批不同色。
它既影响了产品外观的质量,也让企业的信誉不同程度受损。
轻则遭到客户投诉,重则要取消供应商资格。
一旦客户因同批不同色严重要求退货,企业还要蒙受巨额经济损失,所以印刷中的同批不同色必须引起高度重视,决不能掉以轻心。
同批不同色产生的原因业内人士都清楚同批不同色给企业和个人带来什幺样的后里,但由于它是印刷生产中时常出现的问题。
解决起来又异常棘手很难达到有效控制。
这也是质检员和技术质量部在管理土颇为头痛之事,监管起来就显得有些无力。
那幺是什幺原因致使产品同批不同色呢?(1)配置当中的问题当生产通知单下达以后,配墨人员要把生产所需的油墨备好。
在参照印刷色样的同时把墨配好,决不能产生有接近、差不多的思想,一定要在仔细、认真、严谨上狠下功夫。
尽量和色样保持一致,如果这一关都把不住的话很难在印刷过程中保证色差稳定一致。
当然这就要求配置人员必须借助多年积累的配墨经验了。
机台人员用配好的墨打出样子符合色样后方能通过质检员的校对签字。
一旦获得质检员的认可,配墨人员并非完事大吉,而是要把配置的经过用文字记录下来把所油墨的品牌、型号及相关辅料、油墨浓度一一登记造册。
建立健全产品配墨档案制、为日后因油墨不够再次补配提供可靠的资料。
如若配墨人员忽略或不遵守这一有效途径,势必产生同批不同色。
如果生产的产品,印刷批量大,反复出现配墨次数,也及容易造成同批不同色。
原因是很多印刷企业大都是两班或三班作业制,不同班次有各自的配墨人员,配墨的手法也会有一定出入。
如果配置人员不能认真执行交接手续或是不能及时沟通交流,无疑也会埋下同批不同色的质量隐患。
(2)生产过程中出现的几种可能的因素在印刷生产过程中,机台领机应在交接班后先检查印品墨色是否和校对样颜色一致,如有变动应及时调整墨量。
印刷颜色开印前后保持一致的方法
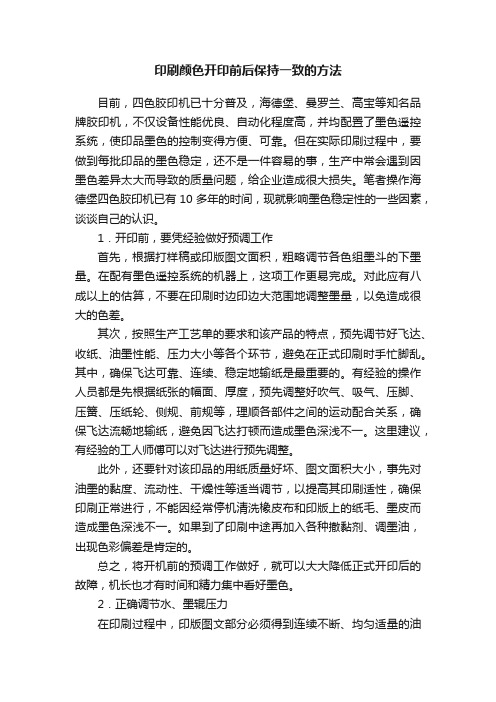
印刷颜色开印前后保持一致的方法目前,四色胶印机已十分普及,海德堡、曼罗兰、高宝等知名品牌胶印机,不仅设备性能优良、自动化程度高,并均配置了墨色遥控系统,使印品墨色的控制变得方便、可靠。
但在实际印刷过程中,要做到每批印品的墨色稳定,还不是一件容易的事,生产中常会遇到因墨色差异太大而导致的质量问题,给企业造成很大损失。
笔者操作海德堡四色胶印机已有10多年的时间,现就影响墨色稳定性的一些因素,谈谈自己的认识。
1.开印前,要凭经验做好预调工作首先,根据打样稿或印版图文面积,粗略调节各色组墨斗的下墨量。
在配有墨色遥控系统的机器上,这项工作更易完成。
对此应有八成以上的估算,不要在印刷时边印边大范围地调整墨量,以免造成很大的色差。
其次,按照生产工艺单的要求和该产品的特点,预先调节好飞达、收纸、油墨性能、压力大小等各个环节,避免在正式印刷时手忙脚乱。
其中,确保飞达可靠、连续、稳定地输纸是最重要的。
有经验的操作人员都是先根据纸张的幅面、厚度,预先调整好吹气、吸气、压脚、压簧、压纸轮、侧规、前规等,理顺各部件之间的运动配合关系,确保飞达流畅地输纸,避免因飞达打顿而造成墨色深浅不一。
这里建议,有经验的工人师傅可以对飞达进行预先调整。
此外,还要针对该印品的用纸质量好坏、图文面积大小,事先对油墨的黏度、流动性、干燥性等适当调节,以提高其印刷适性,确保印刷正常进行,不能因经常停机清洗橡皮布和印版上的纸毛、墨皮而造成墨色深浅不一。
如果到了印刷中途再加入各种撤黏剂、调墨油,出现色彩偏差是肯定的。
总之,将开机前的预调工作做好,就可以大大降低正式开印后的故障,机长也才有时间和精力集中看好墨色。
2.正确调节水、墨辊压力在印刷过程中,印版图文部分必须得到连续不断、均匀适量的油墨,才能获得墨色一致的印品。
因此,墨辊与墨辊之间、墨辊与印版之间,必须保持恰当的接触和滚动关系,以实现油墨的良好传递。
如果这项工作做得不细致,不正确,墨色就不会保持一致。
印刷色彩控制技术

印刷色彩控制技术印刷品质量与所用纸张、油墨、印刷机以及印刷条件有关。
但印刷品的质量状况需要通过测量才能确定。
以往的做法是由印刷机操作人员或者质量检查人员抽取一些印张,利用目视对比法将这些印张与付印样张做比较。
目前国内大部分印刷厂对印刷质量的控制由于种种原因,沿用的依然是目测对比法,靠的是操作者的经验。
由于存在个人色彩接受的偏好、心理和生理的因素影响,不同人生产的产品必将存在色彩的差异,难以保证产品优质稳定,主观的判定结果也往往难以满足客户的要求。
为保证印品色彩质量的稳定再现,必须采用数据化管理。
一、测量原理通过使用分光光度仪进行测量,对印品质量进行控制。
其依据的原理是:分光光度计把色彩作为一种不受观察者支配的物理现象进行测量,它测量的是一个物体的整个可见反射光谱,在可见光谱范围内逐点测量,通常是每隔10nm或20nm测量一个点,然后对反射光谱进行积分求和得到三刺激值,这里的积分实际上仍然是一个累加的过程,具体可以用以下公式描述:在实际计算时,仍是采用求和的方法,即公式转变成:其中,380nm-720nm为可见光谱的波长范围,也即测量的整个光谱范围,可能不同的仪器之间会有微小区别:S(λ)为光源的相对能量分布;、、为标准观察者光谱三刺激值;为计算时所选用的波长间隔,一般为10nm;K为调整因数,其目的是将光源的Y值调整为100,可按下式计算:令,从而可以计算出K值。
颜色测量仪器中,其它表色空间(如:CIELab,CIELuv)的坐标值均由CIEXYZ得出。
我们在用分光光度计进行色度测量时,常用CIELab空间作为颜色测量空间。
其计算公式如下:其中,X0 、Y0 、Z0为CIE标准照明体的三刺激值;X、Y、Z为物体的三刺激值。
在该色彩空间中,L*表示心理明度,取值范围0-100,a*、b*为心理色度,+a*表示红色,-a*表示绿色,+b*表示黄色,-b*表示蓝色。
为分析印品结构,应直接在印品上选取测量点,以此来控制质量。
传统印刷机如何进行色彩校准

传统印刷机如何进行色彩校准对于传统印刷机来说,色彩校准的基本目标,一是要让印刷机能免印刷出均匀的、清晰的图文,基本上能够做到印刷出均匀灰度梯尺;二是要让印刷机能够遵从某个印刷标准,能够接近或者达到这个标准的要求。
那么传统印刷机如何进行色彩校准呢?下面介绍两种方法:方法一:方法一是进行印刷机的优化,使印刷机的各项指标都达到最大能力,而不必考虑外界的技术指标和标准规定。
如印刷机网点扩大到可能的最小值、油墨密度达到可能的最大值以及可以实现的最佳对比度。
如果印刷机可以达到比标准中规定的指标还要高的性能,那就保持这样的指标。
这样做会产生特殊的印刷条件,不能直接采用标准的和通用的分色方法和打样方法。
可以为优化后的印刷机制作特征文件,通过在应用软件中做颜色转换,制作符合要求的分色文件。
方法二:方法二是使印刷机符合某种参考标准。
通过改变印刷的油墨密度,或在RIP、照排机或直接制版机上指定特殊的自定义传递曲线,或改变水墨平衡、温度、印刷压力、油墨黏度及其他条件,使印刷效果达到某种特定的状态。
这种状态可以是企业内部的打样标准,也可以是通用的标准,如美国SWOP/TR001标准、欧洲的FOGRA标准。
对达到标准的印刷机,不必为其再做特性化,可直接使用标准化的特征文件。
由于对印刷机进行优化会产生特殊的印刷条件,可能无法在特征文件中记录这种特殊性。
所以,使印刷机符合需要的标准可能比校准或优化印刷机的性能更重要,否则可能就根本不能对印刷机进行特性化。
目前欧美印刷过程控制采用更新的理念和技术方法,即印刷和打样都遵从某一印刷标准,颜色复制过程都按照同一标准去工作,在颜色上做到与这个标准一致。
既然都达到了标准的要求,那么打样和印刷就能够做到接近或一致了,目前在业界比较热门的是GRACoL规范或者ISO 12647-2标准。
GRACoL是General Requirements for Applications in Offset Lithography的缩写,是美国IDEAlliance联盟制定的一个印刷规范。
- 1、下载文档前请自行甄别文档内容的完整性,平台不提供额外的编辑、内容补充、找答案等附加服务。
- 2、"仅部分预览"的文档,不可在线预览部分如存在完整性等问题,可反馈申请退款(可完整预览的文档不适用该条件!)。
- 3、如文档侵犯您的权益,请联系客服反馈,我们会尽快为您处理(人工客服工作时间:9:00-18:30)。
如何控制标签印刷颜色的一致性
在日常的生产过程中,如何保持标签印刷颜色的一致性一直是困扰生产操作人员的一道难题。
不少标签印刷企业因为标签产品色差问题遭到客户投诉甚至退货。
那么,如何在标签生产过程中控制好产品颜色的一致性呢?笔者从以下几个方面和大家进行探讨。
建立合理的颜色管理制度
我们知道印刷品想要完全避免色差是不可能的,问题的关键在于如何将色差控制在合理的范围之内。
那么,标签印刷企业控制好标签产品颜色一致性的第一步就是要建立一个完善合理的颜色管理制度,让操作人员懂得合格产品的范围。
具体有以下几点。
1.明确产品颜色上下限
当我们第一次生产某标签产品时,应制定出该标签产品颜色的上限、标准和下限,经客户确认后定为“样张”。
日后的生产中以样张的标准颜色为基础,并严格规定颜色的波动不能超过上下限,这样,在保证标签产品颜色一致性的同时,还能给生产人员一个合理的颜色波动范围,也使产品的颜色标准更具可操作性。
2.完善首尾件签样、巡检及抽检制度
想进一步保证颜色标准的执行还应将标签产品颜色的检验项目加入到标签产品首尾件签样制度中,这样便于生产管理人员对标签产品颜色差异进行控制,不合适的标签产品坚决不予检验通过。
同时加强巡检和抽检,以保证在标签产品印刷生产过程中能及时发现和处理超出色差合理范围的标签产品。
印刷标准光源很重要
据笔者了解目前许多标签印刷企业并没有使用印刷标准照明光源,这就给标签产品颜色一致性控制造成了隐患。
许多标签印刷企业在上夜班的时候采用照明光源看到的颜色与白天在日光下看到的颜色差别很大,从而导致了印刷颜色差异。
因此建议广大的标签印刷企业一定要使用印刷标准照明光源来进行照明,有条件的企业还需要配备标准光源箱,以便让员工在标准光源下面进行标签产品的颜色对比。
这样可以有效地避免由于照明光源不标准导致的印刷品色差问题。
油墨问题会导致色差
笔者也曾经遇到过这样的情况:标签产品在客户处放置一段时间后,其油墨颜色逐渐发生变化(主要表现为褪色),但前几个批次的产品未发生同样的现象。
这种情况一般是由于使用了过期油墨造成的。
普通UV油墨的保质期通常为一年,使用过期油墨很容易出现标签产品褪色等情况。
因此,标签印刷企业在使用UV油墨时一定要注意使用正规厂家生产的油墨,同时要注意油墨的保质期,及时更新库存,以免使用过期油墨。
另外,在印刷生产过程中要注意油墨添加剂的使用量,如果油墨添加剂使用过量,也可能导致印刷后油墨的颜色产生变化。
因此,在使用各种油墨添加剂时最好先与油墨供应商进行沟通,再确定添加剂的正确比例范围。
专色油墨的颜色一致性
标签印刷生产过程中经常需要配制专色油墨,不少标签印刷企业配制专色油墨时与样品的颜色差距甚远。
造成这类情况的主要原因是油墨配比不对。
专色油墨由多种原色油墨配制而成,而大多数UV油墨都是彩通(PANTONE)色系,所以我们配制专色油墨时往往会按彩通色卡上给出的比例来配制。
但这里要指出的是,彩通色卡上的油墨配比不一定完全准确,经常会有微小的差别。
这时,就对印刷人员的经验有一定要求,因为印刷人员对油墨颜色的敏感度十分重要。
印刷人员应该多学多练,不断积累这方面的经验才能达到熟练掌握的水平。
这里想提醒大家的是,不是所有的油墨都以彩通色系为基础,遇到非彩通色系的油墨时就不能以彩通色卡上的配比为准,否则很难配制出所需要的颜色。
另外,目前许多标签印刷企业为了保证油墨比例的准确性都配备了电子秤,这一行为值得提倡,标准化是工业生产进步的重要措施之一。
首次配制的专色油墨应由操作人员将其油墨配比记录在工艺卡上,以便为下次再配制该专色油墨时提供数据基础,同时还能保证不同班次、不同操作人员配制专色油墨颜色的一致性。
印前制版与颜色一致性
许多标签印刷企业都遇到过这样的情况:追样时自己印出的标签产品与客户提供的样品颜色相差甚远。
这类问题多数是由于印版上的网点密度和大小与样品上的网点密度和大小不对等造成的。
遇到这类情况笔者建议按以下步骤来做改善。
首先,用专用的网线尺测量样品加网线数,以确定印版加网线数与样品的加网线数一致,这一步骤至关重要。
其次,通过放大镜观察各颜色印版上网点大小与样品对应颜色的网点大小是否一致,如果不一致则需要调整为一致或者近似大小。
这里要注意的是,由于印刷后的网点会扩大,
因此制版时所设置的网点大小要比样品上的网点略小。
最后,再观察印刷用油墨的色相是否与样品油墨色相一致。
一般情况下,能做到上述三项,印刷出的标签产品与客户样品颜色则基本一致,不会相差过大。
柔印中网纹辊参数关乎颜色一致性
不少标签印刷企业使用柔印设备印刷标签时出现过这样的情况:在追客户提供的样品颜色时无论怎样也无法达到与样品颜色一致或接近的程度,在放大镜下看印版上面的网点发现其大小与密度已经与客户样品非常接近了,使用油墨的色相也差不多。
那么导致色差的原因是什么呢?
柔印标签产品颜色除了受油墨色相、网点大小和密度的影响以外,还受网纹辊的网线数和网穴深浅的影响。
一般情况下,网纹辊的加网线数与印版加网线数的比例为3∶1或者4∶1。
因此,在使用柔印设备印刷标签产品时,为了保持与样品颜色接近,除了在制版过程中要注意网点的大小与密度尽量与样品一致外,还要注意网纹辊网线数和网穴的深浅,通过调整这些参数来达到标签产品与样品颜色接近的效果。
当然柔印在颜色一致性控制方面也有得天独厚的优点,那就是它的短墨路、计量式给墨方式。
一旦将这些参数确定下来,那么今后生产的每个批次的同类标签颜色都会基本保持一致。
内容来源于网络,真诚与您分享!。