材料加工组织性能控制(第四章)
材料加工工艺习题【考研】【复习】

《材料加工工艺》考研习题第一章绪论第二章液态金属成形1.金属及合金的结晶包括哪两个基本过程?什么是均质形核和非均质形核?在实际铸造生产中铸造合金结晶的形核是以哪种形核为主,为什么?2.什么是液态金属的充型性能,它与哪些因素有关?铸造合金流动性的好与差对铸件质量有何影响?影响铸造合金流动性的主要因素有哪些?生产中如何采取措施提高铸造合金的流动性?3.铸造合金由液态冷却到室温时要经过哪三个收缩阶段?收缩对铸件质量有什么影响?其收缩大小与哪些因素有关?4.缩孔、缩松是铸件中的常见缺陷之一,哪些因素影响其形成?生产中如何采取措施进行防止?5.什么是铸造应力?铸造应力大小对铸件质量有什么影响?热应力是如何形成的?哪些因素影响其大小?生产中常采取哪些措施来防止和减小应力对铸件的危害?6.铸造合金中的气体主要来源于哪些方面?又以哪些形式存在于铸造合金中?对铸件质量有什么影响?7.铸造合金中的夹杂物是如何分类的?对铸件质有什么影响?如何防止和减小其对铸件的危害?8.湿型粘土砂的主要成分是什么?它有哪些优缺点?适合生产哪些铸件?9.湿型粘土砂的造型方法有哪些?试比较应用震击、压实、射压、高压、气冲和静压等各种造型方法的紧实的砂型紧实度分布(沿砂箱高度方向)。
为什么需要用高密度湿粘土砂型生产铸件?10.树脂自硬砂、水玻璃砂与粘土砂比较有哪些优点?各适用于哪些铸件的生产?11.砂芯的作用是什么?经常使用哪些粘结剂来制芯?常用的制芯工艺有哪些?12.砂型和砂芯涂料的作用是什么?其主要组成有哪些?13.什么是顺序凝固原则?什么是同时凝固原则?各需采用什么措施来实现?上述两种凝固原则各适用于哪些场合?14.铸件的壁厚为什么不能太薄,也不能太厚,而且应尽可能厚薄均匀?为什么要规定铸件的最小壁厚?不同铸造合金要求一样吗?为什么?。
15.为便于生产和保证铸件质量,通常对铸件结构有哪些要求?16.何谓铸件的浇注位置?它是否指铸件上的内绕道位置?铸件的浇注位置对铸件的质量有什么影响?应按何原则来选择?17.试述分型面与分模面的概念?分模造型时,其分型面是否就是其分模面?从保证质量与简化操作两方面考虑,确定分型面的主要原则有哪些?18.试确定图2-116所示铸件的浇注位置及分型面。
第2章 金属材料的组织与性能控制

1. 同素异构转变。 2. 匀晶相图的分析方法。 3. 合金相图与性能的关系。
思考题
1. 为什么要生产合金?与纯金属相比,合金有哪些优越性? 2. 固溶体中,溶质元素含量增加时,其晶体结构和性能会发生什么变化? 3. 试比较共晶反应和共析反应的异同点。 4. 为什么铸造合金常选用接近共晶成分的合金,而压力加工的合金常选用
ES线:C在A中的固溶线
PQ线:C在F中的固溶线
2.铁碳合金的平衡结晶过程
Fe-C 合金分类
工业纯铁 —— C % ≤ 0.0218 %
钢 —— 0.0218 % < C % ≤ 2.11 % 亚共析钢 < 0.77 % 共析钢 = 0.77 % 过共析钢 > 0.77 %
白口铸铁 —— 2.11 % < C % < 6.69 %
室温组织
F + Fe3CⅢ (微量)
500×
(2)共析钢 ( C % = 0.77 % )结晶过程
P中各相的相对量:
Fe3C % = ( 0.77 – xF ) / ( 6.69 – xF )
≈ 0.77 / 6.69 = 12 %
F % ≈ 1 – 12 % = 88 %
珠光体
强度较高,塑性、韧性和硬度介于 Fe3C 和 F 之间。
Ni 80 100
匀晶合金的结晶过程
L
T,C
T,C
L
1500
1455
L
1400 1300
c
a
L+
匀晶转变 L
1200d
1100 1000 1083
b
L
C匀u 晶合金与纯金属不同,它没有一个恒定的N熔i 点,
《金属材料与热处理》第四章铁碳合金
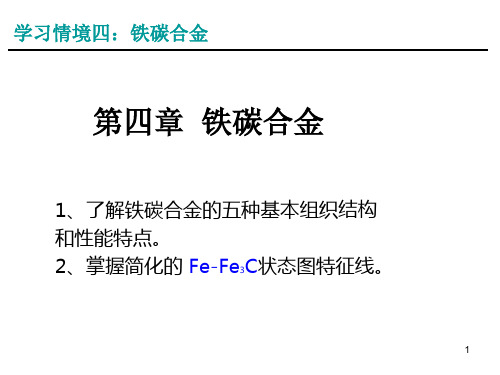
学习情境四:铁碳合金 4.3
4、在焊接方面的应用 焊接时由焊缝到母材各区域的温度是不同的,根据Fe-Fe3C 相图可知,受到不同加热温度的各区域在随后的冷却中可能 会出现不同的组织和性能。这需要在焊接之后采用相应的热 处理方法加以改善。 5、在热处理方面的应用
Fe-Fe3C相图是制订热处理工艺的依据。应用Fe-Fe3C相 图可以正确选择各种碳钢的退火、正火、淬火等热处理的 加热温度范围。由于含碳量的不同,各种碳钢热处理的加 热温度和组织转变也各不相同,都可从状态图中求得。
31
学习情境四:铁碳合金 4.4
1、在钢铁材料选用方面的应用
Fe-Fe3C相图反映了铁碳合金的组织、性能随成分的变化 规律,为钢铁材料的选用提供了依据。如各种型钢及桥梁、船 舶、各种建筑结构等,都需要强度较高、塑性及韧性好、焊接 性能好的材料,故一般选用含碳量较低(WC<0.25%)的钢材; 各种机械零件要求强度、塑性、韧性等综合性能较好的材料, 一般选用碳含量适中(WC=0.30%~0.55%)的钢;各类工具、 刃具、量具、模具要求硬度高,耐磨性好的材料,则可选用含 碳量较高(WC=0.70%~1.2%)的钢。纯铁的强度低,不宜 用作工程材料。白口铸铁硬度高、脆性大,不能锻造和切削加 工,但铸造性能好,耐磨性高,适于制造不受冲击、要求耐磨、 形状复杂的工件,如冷轧辊、球磨机的铁球等。
29
学习情境四:铁碳合金 4.4
低碳钢:Wc=0.1-0.25% 中碳钢:Wc=0.25-0.6% 高碳钢:Wc=0.6-1.4% 随着Wc的增加,硬度、强度都增加。
30
学习情境四:铁碳合金 4.3
三、铁碳合金状态图的应用
1、在钢铁材料选用方面 2、在铸造生产上的应用 3、在锻造方面的应用 4、在焊接方面的应用 5、在热处理方面的应用
塑性成形理论基础

内力和应力
当所加外力使工件内部原子间距发生变化时,原子间便出现 相应的内力与外力平衡。
内力的强度(大小)称为应力。 如图,工件受若干外力 F1 …….Fn作用。在其内 一点Q处 截取一微小面素dA ,由于平衡, 面素两侧的应力相等dFA= dFB = dF则:
23 2 3
2
31 3 1
2
12 2 1
2
根据主应力的排序规则,最大切应力为:
max 1 3
2
球应力张量与偏差应力张量
应力张量可作如下分解:
xx xy xz xx m xy
xz m 0 0
ij yx
yy
yz
yx
yy m
yz
0
m
0
zx zy zz zx
材料成形原理
第四章 塑性成形理论基础 (物理基础、力学基础)
塑性加工原理的内容
力 1. 塑性加工力学条件
学 基
2. 塑性加工中的摩擦与涧滑
础 3. 不均匀变形
4. 塑性变形机制
物 理
5. 塑性变形中组织性能演变
基 础
6. 金属的塑性与变形抗力
7. 塑性变形中组织性能控制
塑性加工/成形原理
力学基础(塑性力学基础)
应力、应变分析,屈服准则 本构关系,塑性问题
物理基础(金属学基础)
变形机制、组织性能演变、塑性与 变形抗力
材料科学与工程学科基础课
塑性成形理论基础
之
力学基础
应力、应变分析,屈服准则 本构关系,塑性问题
材料成形原理
一、应力分析
塑性成形/加工中工件所受外力
主要有作用力和约束反力。
第四章 工件材料的切削加工性

二二、、金金属属材材料料化化学学成成分分的的影影响响
铬能在铁素体中固溶,又能形成碳化物。 当含铬量小于0.5%,对切削加工性的影响 很小。含铬量进一步增加,则钢的硬度、强 度提高,切削加工性有所下降。
镍:镍能在铁素体中固溶,使钢的强度 和韧性均有所提高,导热系数降低,使切削 加工性变差。当含镍量大于8%后,形成了 奥氏体钢,加工硬化严重,切削加工性就更 差了。
3.普通铸铁:与具有相同基体组织的碳素 钢相比,切削加工性好
其金相组织是金属基体加游离态石墨。 石墨:降低了铸铁的塑性,切屑易断,有
润滑作用,使切削力小,刀具磨损小。 但石墨易脱落,使已加工表面粗糙。切削
铸铁时形成崩碎切屑,造成切屑与前刀面 的接触长度非常短,使切削力、切削热集 中在刃区,最高温度在靠近切削刃的后刀 面上。
二、金属材料化学成分的影响
氮:它在钢中会形成硬而脆的 氮化物,使切削加工性变差。
各种元素在小于2%的含量时对钢的切削加工性的影响
三、金属材料热处理状态和金相组织的影响
铁素体 : 由于铁素体含碳很少,故其性能接近
于纯铁,是一种很软而又很韧的组织。在 切削铁素 体时,虽然刀具不易被擦伤, 但与刀面冷焊现象严重,使刀具产生冷焊 磨损。又容易产生积屑瘤,使加工表面质 量恶化。故铁素体的切削加工性并不好。 通过热处理(如正火)或冷作变形,提高其 硬度,降低其韧性,可使切削加工性得到 改善。
二、金属材料化学成分的影响
钼:钼能形成碳化物,能提高钢的硬度, 降低塑性。含钼量在0.15%—0.4%范围内, 切削加工性略有改善。大于0.5%后,切削 加工性降低。
钒:钒能形成碳化物,并能使钢的 组织细密,提高硬度,降低塑性。当 含量增多后使切削加工性变差,含量 少时对切削加工性略有好处。
西华大学《材料性能学》总复习题
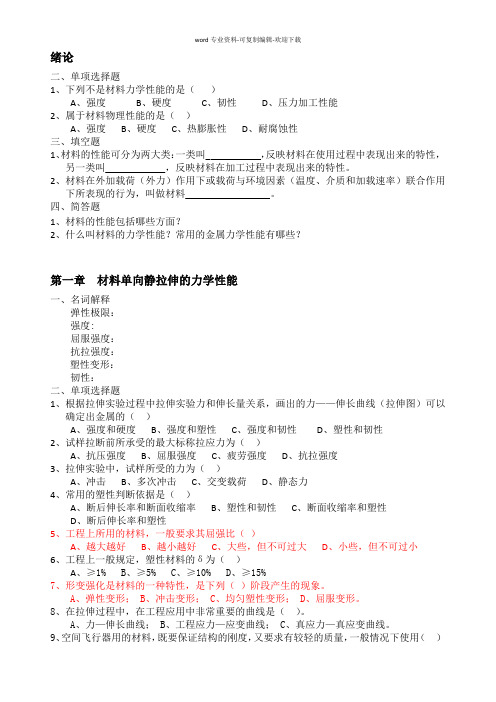
绪论二、单项选择题1、下列不是材料力学性能的是()A、强度B、硬度C、韧性D、压力加工性能2、属于材料物理性能的是()A、强度B、硬度C、热膨胀性D、耐腐蚀性三、填空题1、材料的性能可分为两大类:一类叫_ _,反映材料在使用过程中表现出来的特性,另一类叫_ _,反映材料在加工过程中表现出来的特性。
2、材料在外加载荷(外力)作用下或载荷与环境因素(温度、介质和加载速率)联合作用下所表现的行为,叫做材料_ 。
四、简答题1、材料的性能包括哪些方面?2、什么叫材料的力学性能?常用的金属力学性能有哪些?第一章材料单向静拉伸的力学性能一、名词解释弹性极限:强度:屈服强度:抗拉强度:塑性变形:韧性:二、单项选择题1、根据拉伸实验过程中拉伸实验力和伸长量关系,画出的力——伸长曲线(拉伸图)可以确定出金属的()A、强度和硬度B、强度和塑性C、强度和韧性D、塑性和韧性2、试样拉断前所承受的最大标称拉应力为()A、抗压强度B、屈服强度C、疲劳强度D、抗拉强度3、拉伸实验中,试样所受的力为()A、冲击B、多次冲击C、交变载荷D、静态力4、常用的塑性判断依据是()A、断后伸长率和断面收缩率B、塑性和韧性C、断面收缩率和塑性D、断后伸长率和塑性5、工程上所用的材料,一般要求其屈强比()A、越大越好B、越小越好C、大些,但不可过大D、小些,但不可过小6、工程上一般规定,塑性材料的δ为()A、≥1%B、≥5%C、≥10%D、≥15%7、形变强化是材料的一种特性,是下列()阶段产生的现象。
A、弹性变形;B、冲击变形;C、均匀塑性变形;D、屈服变形。
8、在拉伸过程中,在工程应用中非常重要的曲线是()。
A、力—伸长曲线;B、工程应力—应变曲线;C、真应力—真应变曲线。
9、空间飞行器用的材料,既要保证结构的刚度,又要求有较轻的质量,一般情况下使用()的概念来作为衡量材料弹性性能的指标。
A、杨氏模数;B、切变模数;C、弹性比功;D、比弹性模数。
机械制造工艺学的课程设计
机械制造工艺学的课程设计一、课程目标知识目标:1. 让学生掌握机械制造工艺学的基本概念、工艺过程和加工方法;2. 使学生了解不同材料的机械加工性能及其对加工工艺的影响;3. 帮助学生理解机械制造中的精度、表面质量等关键技术指标及其控制方法。
技能目标:1. 培养学生运用机械制造工艺学知识解决实际问题的能力;2. 提高学生分析加工过程中出现的问题,并提出合理解决方案的能力;3. 培养学生熟练使用机械加工设备、工具和量具,进行简单零件的加工操作。
情感态度价值观目标:1. 培养学生热爱机械制造专业,树立良好的职业素养;2. 培养学生具有团队合作精神,学会尊重、关心、帮助他人;3. 增强学生的环保意识,养成节能、减排、低碳的生产和生活方式。
课程性质分析:本课程为机械制造工艺学的基础课程,旨在让学生掌握机械加工的基本知识和技能,为后续专业课程打下坚实基础。
学生特点分析:学生为初中年级,具有一定的物理、数学基础,但对机械制造工艺学了解较少,动手能力有待提高。
教学要求:1. 理论联系实际,注重培养学生的动手操作能力;2. 采用启发式教学,引导学生主动思考、分析问题;3. 注重学生的个体差异,因材施教,提高学生的学习兴趣和积极性。
二、教学内容1. 基本概念:机械制造工艺基本术语、工艺过程、加工方法;2. 材料加工性能:金属材料的力学性能、切削性能、热处理性能;3. 加工工艺:车削、铣削、磨削、钻孔、镗孔、刨削等加工方法及其适用范围;4. 精度与表面质量:加工精度、表面粗糙度、精度控制方法;5. 加工设备与工具:常用机械加工设备、刀具、量具的选用和使用方法;6. 零件加工:典型零件的加工工艺分析、加工顺序、工艺参数选择;7. 机械加工新技术:数控加工、激光加工、精密加工等。
教学大纲安排:第一周:基本概念、工艺过程;第二周:材料加工性能;第三周:加工工艺(车削、铣削);第四周:加工工艺(磨削、钻孔、镗孔);第五周:精度与表面质量;第六周:加工设备与工具;第七周:零件加工;第八周:机械加工新技术。
材料基础-第四章固体材料的缺陷
例如,Fe的剪切模量大约100GPa,则理论剪切 模量应为3000MPa。但是,单晶体Fe的实际强度仅 为1-10MPa,晶面之间的滑移用相当小剪力就能移 动。理论值与实际值相差巨大。因而,人们就猜测 晶体中存在着象位错这样的线缺陷。 当时仅是理论上的一种推测,没有真正看到。 直到50年代,透射电镜(TEM)的研发成功,才从 实验中观察到实际的位错形貌。 当晶体的一部分相对于另一部分进行局部滑移 时,晶体的已滑移部分与未滑移部分的交界线形成 分界线,即位错,用TEM可观察到(见图4-4)。 位错主要分两种类型:刃型位错和螺型位错。
按晶体缺陷的几何特征,可以分成四种 基本类型:点缺陷、线缺陷(位错)、面缺陷 和体缺陷,如图4-1所示。 但需记住,这些缺陷只代表理想原子排 列中的缺陷。而实用上,为了获得所要求的 材料性能如强度、硬度、塑性等,有时要有 意地制造一些缺陷,即通过合金化、扩散、 热处理和表面处理,设计和控制这些缺陷。 因此,设计和控制晶体缺陷是改进产品 质量的关键,特别是对晶体生长以及使用过 程中控制缺陷的形成、类型以及变化,都是 极为重要的。
图4-3 晶格节点的置换原子
4. 点缺陷对材料性能的影响 在一般情况下,点缺陷主要影响晶体的物 理性质,如比容、比热容、电阻率等。 (1)比容 为了在晶体内部产生一个空位,需将该处 的原子移到晶体表面上,这就导致体积的增加。
(2)比热容 由于形成点缺陷,需向晶体提供附加的能 量(空位生成焓),因而引起附加的比热容。
断裂,而不会沿垂直截面的方向断裂,原因在于 材料在变形过程中发生了滑移,如图4-10所示。
图4-10 单晶体的拉伸断裂 及晶面滑移形貌
这是因为,材料的塑性变形通常会沿着晶体原子 的密排方向滑移,见图4-11 外加拉应力、滑移方向和滑移面的关系
特殊过程控制管理规定(3篇)
第1篇第一章总则第一条为确保产品质量,加强特殊过程的管理,根据《中华人民共和国产品质量法》及相关法律法规,结合本单位的实际情况,特制定本规定。
第二条本规定适用于本单位所有涉及特殊过程的生产、加工、检验等环节。
第三条特殊过程是指那些对产品质量有显著影响,难以通过常规检验手段进行控制的过程。
主要包括:1. 高精度加工过程;2. 特种合金熔炼过程;3. 高温、高压、高真空等特殊环境下的加工过程;4. 高分子材料成型过程;5. 精密计量过程;6. 特种表面处理过程;7. 其他对产品质量有重大影响的过程。
第四条特殊过程控制管理的目标是:1. 确保产品质量符合国家标准和客户要求;2. 提高生产效率和产品质量稳定性;3. 保障员工安全和环境保护。
第二章组织机构与职责第五条本单位成立特殊过程控制管理小组,负责特殊过程控制的全面管理工作。
第六条特殊过程控制管理小组的职责:1. 制定特殊过程控制管理制度和操作规程;2. 组织特殊过程能力验证;3. 监督特殊过程执行情况;4. 对特殊过程进行定期评审;5. 处理特殊过程发生的质量问题。
第七条各部门负责人对本部门特殊过程控制工作负直接责任,应确保本部门特殊过程控制工作的有效实施。
第八条各岗位操作人员应按照特殊过程控制管理制度和操作规程进行操作,确保产品质量。
第三章特殊过程识别与评审第九条各部门应识别本部门涉及的特殊过程,并填写《特殊过程识别表》。
第十条特殊过程控制管理小组对各部门提交的特殊过程进行评审,确认其特殊性质和风险等级。
第十一条评审内容包括:1. 特殊过程对产品质量的影响程度;2. 特殊过程的操作难度;3. 特殊过程的设备、材料、环境要求;4. 特殊过程的检验方法和手段;5. 特殊过程的控制措施。
第十二条评审结果分为“必须控制”、“需要控制”和“可接受”三个等级。
第四章特殊过程控制措施第十三条对必须控制的特殊过程,应制定详细的操作规程和控制计划。
第十四条操作规程和控制计划应包括以下内容:1. 操作步骤;2. 设备、材料、环境要求;3. 操作人员要求;4. 检验方法和手段;6. 异常情况处理。
8材料科学基础课件-第四章回复与再结晶
ln t 如图:
斜率=Q/R
ln t D Q / RT
或: ln
t1 Q 1 1 ( ) t2 R T1 T2
1 T
由实验斜率可求得Q,据此推算其机制。
返回
一般来讲,激活能Q ln t
不只是一个,常按回复温
度高低分为低温、中温和 高温回复。对应的激活能 为Q1、Q2、Q3。
Q3 Q2
第四章
回复与再结晶
变形金属的热行为
返回
章目录:
4.1 4.2 4.3 4.4 冷变形金属在加热时的变化 回 复
再结晶 再结晶后的晶粒长大
4.5
4.6 4.7
再结晶退火及其组织
金属的热变形 超塑性加工
返回
经冷变形的金属具有如下特点:
• 机械性能和理化性能发生明显变化。强度、硬度升高,塑性韧性下降。
迁移的大角度晶界,成为核心。
• 特点:
(高层错能材料Al,Ni等)
位错易于攀移,位错重排成稳定的亚晶界,胞内位错密度低。
返回
② 亚晶生长
通过亚晶界移动生长,成为大角度晶界。
(低层错能材料,位错难以重组,胞内位错密度高。如 Co、Ag、Cu、Au变量较小时)
A • 作ΔP — T℃曲线如图,能量释放 峰对应于新晶粒的出现 — 再结 0 A — 纯金属,B — 合金
返回
B
T℃
晶,在此之前为回复。
三、性能的变化
经冷变形的金属
缓慢加热,测其性能
的变化,如图所示。
性能急变区对应于新
晶粒的出现,再结晶
之前为回复,之后为
晶粒长大。
返回
总之:由以上变化说明,冷变形金属在加热时要 经历三个阶段:回复、再结晶和晶粒长大。
- 1、下载文档前请自行甄别文档内容的完整性,平台不提供额外的编辑、内容补充、找答案等附加服务。
- 2、"仅部分预览"的文档,不可在线预览部分如存在完整性等问题,可反馈申请退款(可完整预览的文档不适用该条件!)。
- 3、如文档侵犯您的权益,请联系客服反馈,我们会尽快为您处理(人工客服工作时间:9:00-18:30)。
4.2 控制轧制过程中微合金元素碳氮化合物 的析出 4.2.1 各阶段中Nb(C、N)的析出状态 (1)出炉前: 加热到1200C,均热2h:90%以上铌都固溶到 奥氏体基体中,有极少数粗大Nb(C、N)没有 固溶到奥氏体中。 1260C :保温30min,Nb(C、N)全部溶解。
4.2.2 影响Nb(C、N)析出的因素 (1)变形量和析出时间
开始随时间增 长而增加,但 很快达到饱和。
随变形量增加, 析出量增加。
图4-6 在含有0.06%C、0.041%Nb和0.0040%N的钢中,变形量对沉淀的影响 1-67%变形;2-50%变形;3-33%变形;4-17%变形
(2)变形温度
VC: NbC和TiC: (2)晶格结构特点; (3)氮化物与碳化物的比 较; (4)含钛钢:首先形成氮 化钛。
图4-1 中碳化物和氮化物的溶度积
对晶粒的细化作用:
特点: (1)铌钢: (2)钒钢和Si-Mn钢: (3)钛钢: 机理:沉淀对奥氏体晶 粒边界起钉扎作用使钛 钢具有高于1250℃的极 高的晶粒细化温度。
(2)出炉后到轧制前:
出炉后尚未变形
加热1200 C , 分别冷到1050 C 、930 C 、 820 C ,钢中 析出物数量与 1200 C时未固 溶的量相当。
在轧制前,从固溶体中析出Nb(C、N)数量很少。
(3)在变形奥氏体中:
在 1图N0b904(00P-03)C:钢C:变在中约形沉析为后淀出5N0相Nb(1中b量C2、5的与NNÅ变);b析量形在出占变1的0钢量0质0种和~点N变1b:2量形030的后0C~%停:5留0为Å时;1间1950的~0关27系0 Å。 析■出为质未点变大形小的与奥与氏变体形;温∆度为、形保变温量时43间%;有○关为。形变量73%
1)析出量相等时,未 再结晶区轧制所需时间 短。原因:
2)析出量一定时,在 高温所需等温时间短, 低温所需等温时间长。
图4-7 温度-时间-沉淀动力学曲线、形变对沉淀动力学的影响 规程1:在再结晶区变形、发生了再结晶
规程2:附加有未再结晶区变形、未发生再结晶
(3)钢的成分变化Fra bibliotek不同成分的钢随 析出时间增加析 出量都增加,但 钢的成分不同, 析出量不同。
图4-10 铌对三种基本成分相同钢的奥氏体晶粒度的影响(1h, 加热到1250C)
4.3.2 再结晶的延迟
(1) 微合金元素的作用
含铌量增加,再 结晶开始时间 显著延长。含碳 0.002%钢中, 几乎所有铌原子 均会固溶,会延 迟回复和再结晶 的发生。
图4-11 不同含铌量的0.002%C-1.54%Mn 钢中,铌含量对软化行为的影响
硫(S)、钙(Ca)、稀土金属(REM)及锆(Zr)。 影响
钢的塑性。
微合金化元素: 特点:与碳、氮结合成碳化物、氮化物和 碳氮化物,高温下溶解,低温下析出。 作用:(1)加热:阻碍原始奥氏体晶粒长 大;(2)轧制:抑制再结晶及再结晶后的晶 粒长大;(3)低温:析出强化作用。
特点: (1)TiN:
Nb(C、N)平均析出速度:
高温、低 温析出都 很慢。
终轧控温制度轧的制影就响是:应用这种微细的Nb(C、N)析出质 高温点轧固制定后亚(晶再界结而晶阻轧止制奥,氏如体10晶50粒C再)结:铌晶的,平达到 均析细出化速晶度粒不的大目、的析。出颗粒较大( 200 Å左右)。
原因: 低温轧制后(未再结晶轧制,如900800C) : 加大了铌的析出速度,析出颗粒细( 50100Å )。
原因:
(4) 奥氏体向铁素体转变过程中 碳氮化物在和中的溶解度不同相变后,产 生快速析出。 相间析出(相间沉淀): 冷却速度大、析出温度低相间沉淀排间距小 析出质点也小。 析出时间长质点长大。
(5)在铁素体内 相变后内剩余的固溶铌继续析出,质点大小决 定于冷却速度。
(6)冷却到室温,1015%左右的铌未从铁素体 中析出。
图4-8 铌钢经50%变形 后在900C 时的沉淀图
曲线
钢号
铌,%
氮,%
碳,%
钼,%
1
76320
0.04
0.003
0.19
-
2
D43
0.04
0.008
0.10
-
3
D45
0.05
0.005
0.12
0.23
4
32675A 0.045
0.006
0.10
0.17
4.3 微量元素在控制轧制控制冷却中的作用 4.3.1 加热时阻止奥氏体晶粒长大
(3)温度和含碳量的作用
图4-13 含铌0.097%的钢中,温度和 含碳量对软化行为的影响
含碳较高的钢 在900C和850C 时,软化速率比 含碳低的钢慢得 多,而在1000C 时,这两种钢几 乎表现出相同的 软化行为。
图4-14 0.002%C-0.097%Nb钢、0.006%C0.097%Nb钢和0.019%C-0.095%Nb钢于900C 时,碳氮化铌应变诱发沉淀析出的过程
4. 微合金元素在控制轧制中的作用
HSLA钢中常用合金元素及夹杂元素分类:
1)微合金化元素:铌(Nb)、钒(V)、
控制钢的强
钛(Ti)、铝(Al)(B)。
度、韧性、
2)置换元素:硅(Si)、锰(Mn)、 钼(Mo)、铜(Cu)、镍(Ni)(Cr)。
相变显微组 织
3)夹杂及硫化物形状控制的添加元素:磷(P)、
图4-3 中的静态再结晶动力学 (a)Si-Mn钢;(b)含0.04%Nb的钢
预应变为0.50
图4-4 中的静态再结晶动力学 (含0.08%Ti的钢;(b)含0.10%V的 钢 变形温度900C预应变为0.50
(2)温度的作用
而对于含铌钢, 随温度的下降, 再结晶开始受到 显著延迟。
图4-12 含铌或不含铌的0.002%C1.56%Mn钢的软化行为与温度的关系
Nb Ti
V
图4-9 碳化物及氮化物形成元素的 含量对奥氏体晶粒粗化温度的影 响
作用:
铌、钛含量在0.10%以下时, 可以提高奥氏体粗化温度到 1050-1100C,作用明显。 高对止钒长含度奥晶在大量弥氏界小的大散体迁于作于的晶移00用..碳界,不1100氮起阻大%%时时化固止,,,物定晶当阻随小作界铌止合颗用长和晶金粒,大钒粒含,阻。 量的增多粗化温度继续提高, 当含量达到0.16%时则趋于稳 定,粗化温度不再提高。