反球化元素
球墨铸铁件产生缺陷的原因有哪些?

球墨铸铁件产生缺陷的原因有哪些?球墨铸铁件产生缺陷的原因不单是球化处理问题,那么还有什么问题?在球墨铸铁件生产中,常见的铸件缺陷除有灰铸铁件的一般缺陷外,还有球化不良、球化衰退、夹渣、缩松、石墨漂浮、皮下气孔等。
通常,产生这些缺陷的原因不单是球化处理问题,有时还有造型制芯、熔炼浇注、配砂质量、落砂清理等许多生产工序的问题,因此必须具体分析。
以便采取相应的合理措施加以解决。
(1)球化不良特征:在铸件或试棒断面上分布有明显可见的小黑点,愈往中心愈密。
金相组织中.有聚集分布的厚片状石墨原因分析:1.原铁液硫含量过高2.铁液氧化3.残余球化剂量不足4反球化元素的干扰防止方法:1.尽量选用低硫的焦炭和新生铁。
若原铁液含硫量过高,应采用炉内、炉外脱硫或相应提高球化剂的加入量。
交界铁液一定要分离干净,灰铸铁的铁掖不应混入球墨铸铁中。
球化处理时,防止炉渣出到浇包中2.操作中严防铁液氧化3.熔制配比适当、成分稳定的中间合金,并采用合适的处理温度,注意球化处理操作。
防止铁液与合金作用过分激烈或“结死”在包底4镁球墨铸铁中。
加人少量的稀土,可中和反球化元素的干扰(2)球化衰退特征:球墨铸铁铁液,停留一定时间后,球化效果会消失原因分析: 铁液的残余镁量和残余稀土量随着时间的延长会逐渐减少,过了一定时间后。
球化剂残余量已减少到不足以保证铸件球化时,就造成球化衰退镁量和稀土量逐渐减少的原因是:1. 在铁液表面的MgS、CeS与空气中氧作用,发生下列反应:2MgS+O2=2MgO气↑+2S2CeS+ O2=2CeO气+2S烟状的MgO和CeO在空气中逸损,S返回铁液与Mg、Ce作用又生成MgS、CeS,这样循环,Mg、Ce不断损失2.镁在铁液中溶解度极小,大部分镁以微小的气泡悬浮在铁液中。
当有搅拌、回包、浇注、机械振动等情况时,镁气泡会集聚上浮,并穿出铁液表面。
遇空气燃浇而损失3.镁、稀土与氧有极大的亲和力。
铁液表面的镁和稀土要逐渐氧化、镁还有蒸发损失等防止方法:1.经球化处理的铁液应有足够的球化剂残余量2.降低原铁液硫含量,并防止铁液氧化3.球化处理后应扒净渣子4.缩短铁液经球化处理后的停留时间5.在铁液表面加覆盖熔剂,如石墨粉、木炭粉、冰晶石粉等(3)夹渣(黑渣)特征: 在铸件断面上呈现暗黑色,没有光泽,主要由琉化镁、硫化锰、氧化镁、二氧化硅、氧化铁、氢化镁等所组成,是一种非金属夹杂物,可用硫印、氧印等方法显示出来。
球墨铸铁化学成分

球墨铸铁化学成分重要包含碳.硅.锰.硫.磷五大罕有元素.对于一些对组织及机能有特别请求的铸件,还包含少量的合金元素.同通俗灰铸铁不合的是,为包管石墨球化,球墨铸铁中还须含有微量的残留球化元素.1.碳及碳当量的选择原则:碳是球墨铸铁的根本元素,碳高有助于石墨化.因为石墨呈球状后石墨对机械机能的影响已减小到最低程度,球墨铸铁的含碳量一般较高,在3.5~3.9%之间,碳当量在4.1~4.7%之间.铸件壁薄.球化元素残留量大或孕育不充分时取上限;反之,取下限.将碳当量选择在共晶点邻近不但可以改良铁液的流淌性,对于球墨铸铁而言,碳当量的进步还会因为进步了铸铁凝固时的石墨化膨胀进步铁液的自补缩才能.但是,碳含量过高,会引起石墨沉没.是以,球墨铸铁中碳当量的上限以不消失石墨沉没为原则.2.硅的选择原则:—3.0%.选定碳当量后,一般采纳高碳低硅强化孕育的原则.硅的下限以不消失自由渗碳体为原则.球墨铸铁中碳硅含量肯定今后,可用图2进行磨练.假如碳硅含量在图中的暗影区,则成分设计根本适合.假如高于最佳区域,则轻易消失石墨漂显现象.假如低于最佳区域,则轻易消失缩松缺点和自由碳化物.3.锰的选择原则:因为球墨铸铁中硫的含量已经很低,不须要过多的锰来中和硫,球墨铸铁中锰的感化就重要表示在增长珠光体的稳固性,促进形成(Fe.Mn)3C.这些碳化物偏析于晶界,对球墨铸铁的韧性影响很大.锰也会进步铁素体球墨铸铁的韧脆性改变温度,锰含量每增长0.1%,脆性改变温度进步10~12℃.是以,球墨铸铁中锰含量一般是愈低愈好,即使珠光体球墨铸铁,锰含量也不宜超出0.4~0.6%.只有以进步耐磨性为目标的中锰球铁和贝氏体球铁破例.4.磷的选择原则:℃.是以,球墨铸铁中磷的含量愈低愈好,一般情形下应低于0.08%.对于比较重要的铸件,磷含量应低于0.05%. 球墨铸铁中碳硅含量肯定今后,可用图2进行磨练.假如碳硅含量在图中的暗影区,则成分设计根本适合.假如高于最佳区域,则轻易消失石墨漂显现象.假如低于最佳区域,则轻易消失缩松缺点和自由碳化物.5.硫的选择原则:硫是一种反球化元素,它与镁.稀土等球化元素有很强的亲合力,硫的消失会大量消费铁液中的球化元素,形成镁和稀土的硫化物,引起夹渣.气孔等锻造缺点.球墨铸铁中硫的含量一般请求小于0.06%.。
球化参考资料衰退原因(1)

球化衰退原因
一是铁水“回硫”造成。
这是由于球化铁水停留时间较长,残留镁和稀土逐渐减少,熔渣没有及时扒除,硫还会回到铁水中,发生下列反应:
2MgS+O2=2MgO+2S 2Ce2S3+3O2=2Ce2O3+6S
回到铁水中的硫,又再次与镁、稀土发生反应:
Mg+S=MgS 2Ce+3S=Ce2S3
这种反应随着铁液停留时间的延长,硫、镁、稀土和空气中的氧循环作用,消耗了大量的镁和稀土,进而引起因残留镁和稀土不足造成球化衰退这种球化衰退除铁水停留时间较长外,还与球化剂中稀土含量较低、或者球化剂加入量偏低有一定的关系,但紧靠增加其加入量也很不可取,这不但增加成本,而且因为镁和稀土残余量高了,气孔、熔渣量和渗碳体都会增加,在厚大断面中还会使石墨球蜕变为蝌蚪状石墨。
生产实践表明,原铁水含硫量低对防止球化衰退才是最有效的。
二是界面反应造成。
在与铁水接触的铸型表面,造型材料中的SiO2和S和铁水中的镁反应造成了铁液中的镁损耗:2Mg+O2=2MgO 2Mg+SiO2=Si+2MgO Mg+S=MgS
所以,我们常用的造型材料中,煤粉和新砂中的含硫量不能超过1.0%、0.1-0.15%,另外树脂砂造型时,树脂或固化剂中的N、S 含量应尽可能低,这些都是厂家常常忽略的。
三是铁液中残留镁
超过0.07%时,出现球片状(蝌蚪状)石墨。
严控炉料,不要混入不需要的杂物,很多我们不方便检测的元素导致的后果比钛大多了,可是我们检测不了,刚好钛是去不掉的元素,又确实有害,就都赖它上了。
在球铁中Ti是反球化元素,而且促进碳化物的生成,在球铁中尽量低,在灰铁中过量的TI会促使石墨形成D型过冷石墨。
球墨铸铁的球化与孕育处理工艺
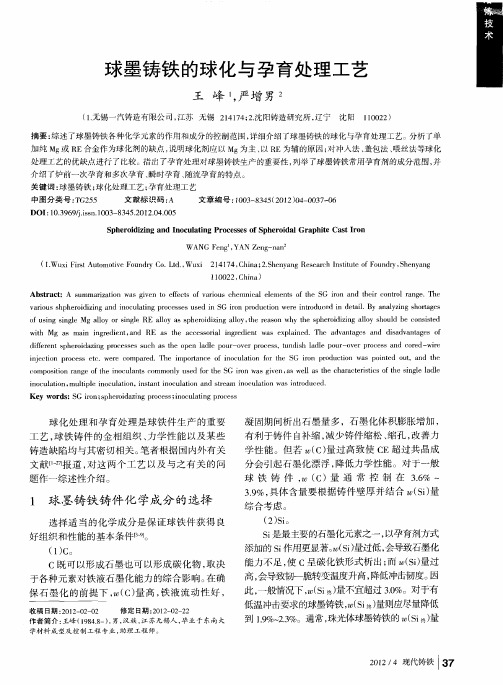
( )。 5 S
c 强烈促进形成碳化物, r 稳定珠光体 。 r c 的 加 入能提 高强 度 和硬 度 , 加 入量 以不 出现 游离 但
碳 化物 为 限 , 于高 韧性铁 素 体球 墨铸 铁要 严 格 对
限 制 ( r 量 。对 于珠 光 体 球 墨 铸 铁 , C) 当加 入 ( r量 02 03 C ) .%~ . %时 , 即可起 到 显 著 的稳 定 珠
10 2 ) 10 2
摘要 : 综述 了球墨铸铁各种化学元素的作 用和成分 的控制范 围, 细介绍 了球墨铸铁 的球化与孕育处理工艺 。 详 分析 了单 加 纯 Mg R 或 E合金作为球化剂的缺点 , 明球化剂应 以 Mg为主 、 R 说 以 E为辅 的原 因 ; 对冲入法 、 盖包法 、 喂丝法等球化 处理工 艺的优缺点进行 了比较 。 出了孕育处理对球墨铸铁生产的重要性 , 指 列举 了球墨铸铁 常用孕育剂的成分范围, 并 介绍 了炉前一次孕育和多次孕育 、 瞬时孕育 、 随流孕育的特点 。 关键词 : 球墨铸铁 ; 球化处理工艺 ; 孕育处理工艺 中图分类号 :G 5 T 25 文献标 识码 : A 文章编号 :0 3 84 (0 2 0 — 0 7 0 10 — 3 5 2 1 )4 0 3 — 6
往需要 进行脱 S处理 ;感 应 电炉熔 炼 由于不用焦 炭, 原铁液 州 S量一般在 0 1% ̄ . %。 () . 5 0 3 不需要进 0 0
R E元 素 中和 , 则会 引起球 化不 良。 E与 s 否 R b并
用 还可 以改 善大 断面件 的球 化 。
( 1微量 干扰 元素 。 1) 球 墨铸 铁 中常存 在 一 些 非 特 意加 入 的微 量
喂丝球化工艺在球墨铸铁生产线上的应用

喂丝球化工艺在球墨铸铁生产线上的应用张 军1,解戈奇2,权国英1,薛 挺1,秦 剑1(1. 陕西金鼎铸造有限公司,陕西宝鸡 722405;2. 陕西远大新材料技术有限公司,陕西咸阳 713800)摘要:通过控制原铁液中反球化元素的含量,尤其是S、Ti含量,并辅以优质包芯线,分别采用双线喂丝球化、单线喂丝球化处理及含钡孕育剂,有效防止了球化衰退,而且提高了铸件综合性能,改善了铸造环境,简化了操作流程,节约了生产成本。
关键词:球墨铸铁;双线喂丝工艺;单线球化处理;包芯线;成本控制作者简介:张军(1988-),男,助理工程师,学士,主要从事铸造熔炼工艺制定工作。
E-mail: zhangjun@ 中图分类号:TG 255文献标识码:A文章编号:1001-4977 (2019)02-0128-04收稿日期:2018-09-13收到初稿,2018-12-29收到修订稿。
近年来,随着球墨铸铁件在制造业中越来越广泛的应用,球墨铸铁的生产技术也在不断提高,以满足国内外用户对球墨铸铁件提出的高标准高要求。
在球墨铸铁的生产过程中,球化处理是生产球墨铸铁的关键。
国内外部分大型企业都在进行喂丝法处理球墨铸铁的技术研究、开发和应用,喂丝法生产球墨铸铁的技术也日渐成熟,并取得了不错的成绩,其经济性与球化品质的可靠性及可控性已为愈来愈多的企业所重视。
1 喂丝法处理球墨铸铁的工艺及质量控制要点喂丝法的原理:将一定成分、一定粒度的球化剂,经卷线设备包裹在一定厚度、宽度的钢皮内,形成适当强度、填充率的电缆状包芯线卷,利用自动化喂丝装置,以一定速度喂入带有包盖的处理包中,实现球化处理的工艺。
其实质是以喂丝的方式,以钢带作为载体将球化剂以一定的速度送入处理包底,实现球化剂的加入过程[1]。
喂丝球化处理流程见图1。
根据镁在包芯线中的不同形态,市场上有两种包芯线。
一种是物理混合法配制,就是将经过特殊处理的纯镁颗粒和其他合金材料机械混合而成,其优点是成本低,氧化镁含量低,球化反应迅速,镁吸收率能够保证;缺点是成分均匀性难控制,镁是以单质形式进入铁液中,爆发剧烈。
合金元素的作用

0.4-0.6
0.40
0.15
HT150
<20
20-30
>30
3.5-3.7
3.4-3.6
3.3-3.5
2.2-2.4
2.0-2.3
1.8-2.2
0.4-0.6
0.40
0.15
HT200
<20
20-40
>40
3.3-3.5
3.2-3.4
3.1-3.3
1.9-2.3
1.8-2.2
1.6-1.9
Sb(锑)
1.强烈促进形成珠光体
2.0.002%~0.01%时,对球墨铸铁有使石墨球细化的作用,尤其对大断面球墨铸铁有效
3.其干扰球化的作用,可用稀土元素中和
4.灰铸铁中的加入量为<0.02%,球墨铸铁中的适宜量为0.002%~0.010%
Bi(铋)
1.球墨铸铁中加铋能很有效地细化石墨球
2.大断面球墨铸铁中加铋能防止石墨畸变
0.15
0.10
HT400
>25
2.8-3.0
1.0-1.5
0.8-1.2
0.15
0.10
反球化元素的界限量
元素
Al
Ti
Pb
As
Sb
Bi
Zr
Sn
Te
Se界限量(%)0.Fra bibliotek50.07
0.002
0.05
0.01
0.002
0.03
0.05
0.003
0.0SSS3
2.能细化石墨,增加化合碳量,白口倾向有所增加,强度、硬度有提高趋势,加入量可在0.1%~0.3%
球墨铸铁化学成分
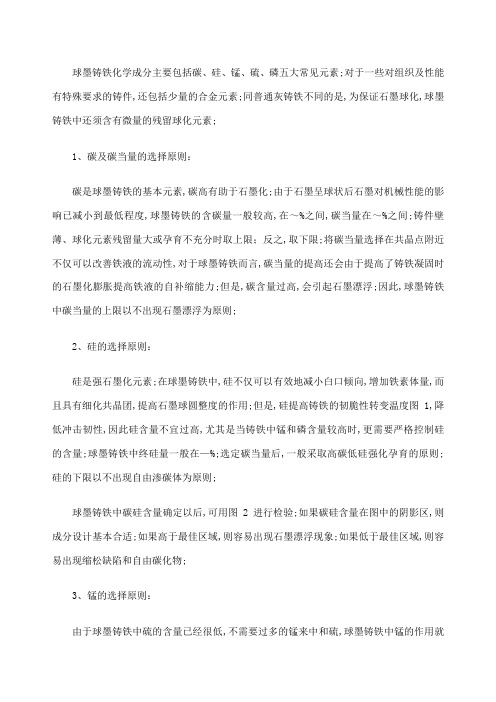
球墨铸铁化学成分主要包括碳、硅、锰、硫、磷五大常见元素;对于一些对组织及性能有特殊要求的铸件,还包括少量的合金元素;同普通灰铸铁不同的是,为保证石墨球化,球墨铸铁中还须含有微量的残留球化元素;1、碳及碳当量的选择原则:碳是球墨铸铁的基本元素,碳高有助于石墨化;由于石墨呈球状后石墨对机械性能的影响已减小到最低程度,球墨铸铁的含碳量一般较高,在~%之间,碳当量在~%之间;铸件壁薄、球化元素残留量大或孕育不充分时取上限;反之,取下限;将碳当量选择在共晶点附近不仅可以改善铁液的流动性,对于球墨铸铁而言,碳当量的提高还会由于提高了铸铁凝固时的石墨化膨胀提高铁液的自补缩能力;但是,碳含量过高,会引起石墨漂浮;因此,球墨铸铁中碳当量的上限以不出现石墨漂浮为原则;2、硅的选择原则:硅是强石墨化元素;在球墨铸铁中,硅不仅可以有效地减小白口倾向,增加铁素体量,而且具有细化共晶团,提高石墨球圆整度的作用;但是,硅提高铸铁的韧脆性转变温度图1,降低冲击韧性,因此硅含量不宜过高,尤其是当铸铁中锰和磷含量较高时,更需要严格控制硅的含量;球墨铸铁中终硅量一般在—%;选定碳当量后,一般采取高碳低硅强化孕育的原则;硅的下限以不出现自由渗碳体为原则;球墨铸铁中碳硅含量确定以后,可用图2进行检验;如果碳硅含量在图中的阴影区,则成分设计基本合适;如果高于最佳区域,则容易出现石墨漂浮现象;如果低于最佳区域,则容易出现缩松缺陷和自由碳化物;3、锰的选择原则:由于球墨铸铁中硫的含量已经很低,不需要过多的锰来中和硫,球墨铸铁中锰的作用就主要表现在增加珠光体的稳定性,促进形成Fe、Mn3C;这些碳化物偏析于晶界,对球墨铸铁的韧性影响很大;锰也会提高铁素体球墨铸铁的韧脆性转变温度,锰含量每增加%,脆性转变温度提高10~12℃;因此,球墨铸铁中锰含量一般是愈低愈好,即使珠光体球墨铸铁,锰含量也不宜超过~%;只有以提高耐磨性为目的的中锰球铁和贝氏体球铁例外;4、磷的选择原则:磷是一种有害元素;它在铸铁中溶解度极低,当其含量小于%时,固溶于基体中,对力学性能几乎没有影响;当含量大于%时,磷极易偏析于共晶团边界,形成二元、三元或复合磷共晶,降低铸铁的韧性;磷提高铸铁的韧脆性转变温度,含磷量每增加%,韧脆性转变温度提高4~℃;因此,球墨铸铁中磷的含量愈低愈好,一般情况下应低于%;对于比较重要的铸件,磷含量应低于%;球墨铸铁中碳硅含量确定以后,可用图2进行检验;如果碳硅含量在图中的阴影区,则成分设计基本合适;如果高于最佳区域,则容易出现石墨漂浮现象;如果低于最佳区域,则容易出现缩松缺陷和自由碳化物;5、硫的选择原则:硫是一种反球化元素,它与镁、稀土等球化元素有很强的亲合力,硫的存在会大量消耗铁液中的球化元素,形成镁和稀土的硫化物,引起夹渣、气孔等铸造缺陷;球墨铸铁中硫的含量一般要求小于%;。
高质量球墨铸铁微量元素和合金元素的选择与控制
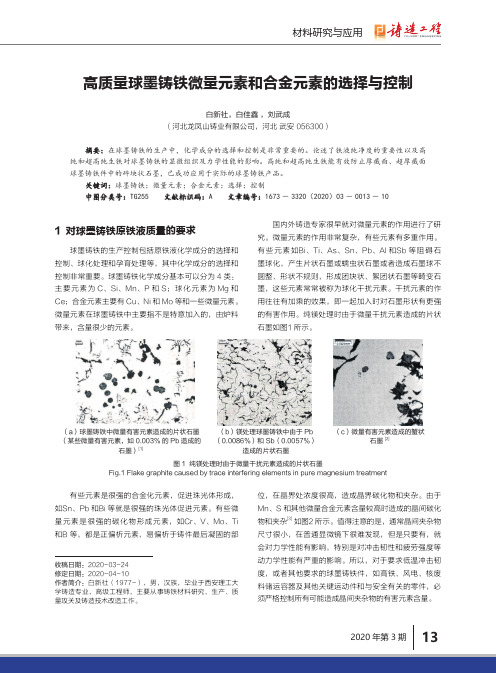
高质量球墨铸铁微量元素和合金元素的选择与控制1 对球墨铸铁原铁液质量的要求球墨铸铁的生产控制包括原铁液化学成分的选择和控制、球化处理和孕育处理等,其中化学成分的选择和控制非常重要。
球墨铸铁化学成分基本可以分为4类:主要元素为C、Si、Mn、P和S;球化元素为Mg和Ce;合金元素主要有Cu、Ni和Mo等和一些微量元素。
微量元素在球墨铸铁中主要指不是特意加入的,由炉料带来,含量很少的元素。
国内外铸造专家很早就对微量元素的作用进行了研究。
微量元素的作用非常复杂,有些元素有多重作用。
有些元素如Bi、Ti、As、Sn、Pb、Al和Sb等阻碍石墨球化,产生片状石墨或蠕虫状石墨或者造成石墨球不圆整、形状不规则,形成团块状、絮团状石墨等畸变石墨,这些元素常常被称为球化干扰元素。
干扰元素的作用往往有加乘的效果,即一起加入时对石墨形状有更强的有害作用。
纯镁处理时由于微量干扰元素造成的片状石墨如图1所示。
有些元素是很强的合金化元素,促进珠光体形成,如Sn、Pb和Bi等就是很强的珠光体促进元素。
有些微量元素是很强的碳化物形成元素,如Cr、V、Mo、Ti和B 等,都是正偏析元素,易偏析于铸件最后凝固的部位,在晶界处浓度很高,造成晶界碳化物和夹杂。
由于Mn、S 和其他微量合金元素含量较高时造成的晶间碳化物和夹杂[3]如图2所示。
值得注意的是,通常晶间夹杂物尺寸很小,在普通显微镜下很难发现,但是只要有,就会对力学性能有影响,特别是对冲击韧性和疲劳强度等动力学性能有严重的影响。
所以,对于要求低温冲击韧度,或者其他要求的球墨铸铁件,如高铁、风电、核废料储运容器及其他关键运动件和与安全有关的零件,必须严格控制所有可能造成晶间夹杂物的有害元素含量。
白新社,白佳鑫 ,刘武成(河北龙凤山铸业有限公司,河北 武安 056300)摘要:摘要:在球墨铸铁的生产中,化学成分的选择和控制是非常重要的。
论述了铁液纯净度的重要性以及高纯和超高纯生铁对球墨铸铁的显微组织及力学性能的影响。
- 1、下载文档前请自行甄别文档内容的完整性,平台不提供额外的编辑、内容补充、找答案等附加服务。
- 2、"仅部分预览"的文档,不可在线预览部分如存在完整性等问题,可反馈申请退款(可完整预览的文档不适用该条件!)。
- 3、如文档侵犯您的权益,请联系客服反馈,我们会尽快为您处理(人工客服工作时间:9:00-18:30)。
反球化元素
反球化元素指那些只要少量存在于铁水时,就能部分或全部破坏石墨球化的元素。
硫和氧是工业铸铁中常存的反球化元素。
此外,还有一些偶存的反球化元素,如锡、锑、砷、铅、铝、铋、钛、硼等。
反球化元素按其作用机理可划分为两类。
一类是消耗型反球化元素,包括硫、氧、硒(Se)碲(Te)等,它们与镁及稀土元素形成MgS、MgO、MgSe、MgTe及稀土化合物消耗了球化元素。
另一类是晶界偏析型反球化元素,包括锡、锑、砷、铜、硼、钛铝等,它们在奥氏体中的平衡分配系数很小,并增加铁水中碳的活度,共晶结晶时,这些元素富集到共晶团边界,促使碳在共晶后期结晶成畸形的枝晶状等石墨,如果这些元素浓度很高,也可在共晶中期促成石墨畸变,形成团状或厚片状石墨。
此外还有一些元素属于中间型反球化元素,如铅和铋,在含量较低时主要通过偏析作用促成石墨畸变,含量较高时也消耗球化元素。
消耗型反球化元素使石墨由球状演变为厚片状、共晶状、以致片状石墨,它使热分析曲线逐渐变为具有灰铁的特征,即共晶结晶中期出现等温平台,后期明显回升。
晶间偏析型反球化元素对热分析曲线无明显影响,其中钛、硼、砷使过冷度增加,石墨演变为保留球墨多晶结构的各种畸变石墨,但不演变为片状石墨。
中间型反球化元素含量少时则与晶间偏析型影响相同,含量多时也可促成片墨并使热分析曲线回升。
因此,消耗型反球化元素造成球化不良,偏析型反球化元素造成石墨畸变。
反球化元素的原子量越大,反球化作用也越大,即允许的临界含量越小。
某一个反球化元素单独存在时,允许的临界含量比较大,例如单独存在铜,即使达到2~3%也不影响球化,含钛0.04%时,再含有1%的铜,就使球铁被破坏。
几种反球化元素共存时,其作用是叠加的。
钛促进其他反球化元素的破坏作用尤为恶劣。
铸件越厚,冷却速度越慢,反球化元素的破坏作用越强烈。
各种球化元素处理的球铁对反球化元素的敏感程度不同。
铈、镧、钍、镱等元素在不同程度上可以中和反球化元素的作用,放宽其临界含量。
例如可以抵消钛、铅、锑、铝的反球化作用所需的铈量分别为0.005%~0.007%、0.014%、0.015%和0.008%。
反球化元素对基体组织有不同的影响:碲、硼强烈促进形成白口;铜、砷、锡、锑、铅、铋稳定珠光体;铝、锆促进形成铁素体;硒没有影响。
在一定含量范围内,或者采用稀土镁球化剂时在稍宽的含量范围内,某些反球化元素可以减小厚断面铸件中心的石墨畸变。
例如加锡0.025%可以使125毫米厚的铸件中心石墨形状改善。
加碲0.005%,或者加入微量的铅、砷、铋也可起同样作用。