发动机叶片动应力测量
高温动应力测量技术简析
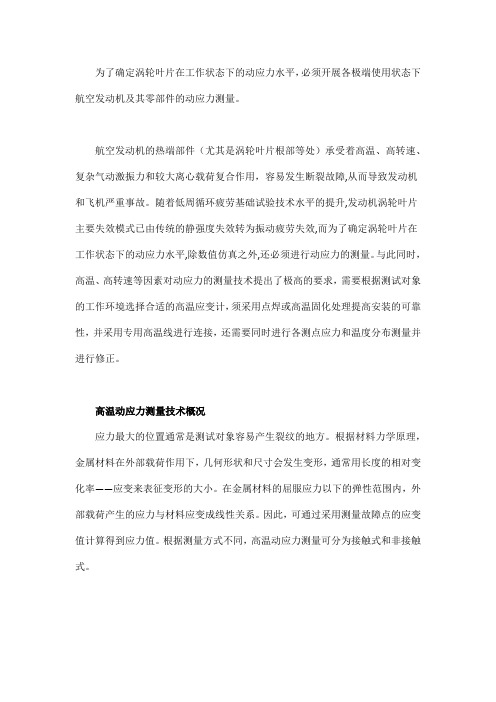
为了确定涡轮叶片在工作状态下的动应力水平,必须开展各极端使用状态下航空发动机及其零部件的动应力测量。
航空发动机的热端部件(尤其是涡轮叶片根部等处)承受着高温、高转速、复杂气动激振力和较大离心载荷复合作用,容易发生断裂故障,从而导致发动机和飞机严重事故。
随着低周循环疲劳基础试验技术水平的提升,发动机涡轮叶片主要失效模式已由传统的静强度失效转为振动疲劳失效,而为了确定涡轮叶片在工作状态下的动应力水平,除数值仿真之外,还必须进行动应力的测量。
与此同时,高温、高转速等因素对动应力的测量技术提出了极高的要求,需要根据测试对象的工作环境选择合适的高温应变计,须采用点焊或高温固化处理提高安装的可靠性,并采用专用高温线进行连接,还需要同时进行各测点应力和温度分布测量并进行修正。
高温动应力测量技术概况应力最大的位置通常是测试对象容易产生裂纹的地方。
根据材料力学原理,金属材料在外部载荷作用下,几何形状和尺寸会发生变形,通常用长度的相对变化率——应变来表征变形的大小。
在金属材料的屈服应力以下的弹性范围内,外部载荷产生的应力与材料应变成线性关系。
因此,可通过采用测量故障点的应变值计算得到应力值。
根据测量方式不同,高温动应力测量可分为接触式和非接触式。
在接触式测量中,所用传感器都是应变片,其中使用最广泛的是电阻应变计(如图1所示),一般由敏感栅、引线、黏结剂、基底和盖层组成。
将电阻应变计安装在构件表面,构件在受载荷后表面产生的微小变形(伸长或缩短),会使应变计的敏感栅随之变形,应变计的电阻就发生变化,其变化率与安装应变计处构件的应变成比例,测出此电阻的变化,即可按公式算出构件表面的应变和相应的应力。
这种测量方式具有测量精度和灵敏度高、量程大、尺寸小和技术成熟的特点,也是目前在航空发动机领域应用最广泛的一类方法。
尽管这种测量方式比较实用,但弊端颇多,例如需要一系列的应变仪、传输电缆、遥测发射器或滑动环,装在发动机内的应变片及滑动环容易损坏,会降低发动机性能,安装过程及伴之而来的修理过程都需要拆卸发动机,费工耗时。
轮廓法测量镍基高温合金单晶叶片内部残余应力分布

轮廓法测量镍基高温合金单晶叶片内部残余应力分布-概述说明以及解释1.引言1.1 概述概述:镍基高温合金单晶叶片是航空发动机中常用的关键零部件,其内部残余应力分布对其性能和寿命具有重要影响。
因此,准确测量内部残余应力分布是对叶片健康状态进行评估和预测的关键步骤。
本文将介绍轮廓法作为一种常用的测量内部残余应力的方法,探讨其在镍基高温合金单晶叶片中的应用。
通过对轮廓法的原理和方法进行介绍,以及对其优势和局限性进行讨论,希望能为相关领域的研究和应用提供参考和启示。
"1.2 文章结构":本文分为引言、正文和结论三个部分。
在引言部分中,将对镍基高温合金单晶叶片内部残余应力分布的重要性进行概述,并介绍本文的目的和结构。
正文部分将详细介绍镍基高温合金单晶叶片的特点,轮廓法测量原理及方法,以及轮廓法在测量内部残余应力分布中的应用。
在结论部分,将总结内部残余应力分布的测量价值,讨论轮廓法的优势和局限性,并展望未来研究方向。
整篇文章将围绕着如何利用轮廓法来测量镍基高温合金单晶叶片内部残余应力分布展开论述。
1.3 目的本文旨在探讨轮廓法测量镍基高温合金单晶叶片内部残余应力分布的可行性和有效性。
通过对该方法的原理和应用进行详细描述,旨在揭示该技术在实际工程中的重要性和应用前景。
此外,我们将分析内部残余应力分布的测量价值,讨论轮廓法的优势和局限性,并展望未来可能的研究方向,为相关领域的研究和应用提供有益的启示和指导。
通过本文的研究,有望为提高镍基高温合金单晶叶片的设计和制造质量,提供有效的技术支持和指导。
2.正文2.1 镍基高温合金单晶叶片的特点镍基高温合金单晶叶片具有以下几个显著特点:1. 高温性能优越:镍基高温合金单晶叶片能够在高温环境下保持良好的力学性能,具有很好的抗氧化、耐高温蠕变和抗疲劳性能。
2. 组织稳定性高:由于采用了单晶生长技术,叶片中不存在晶间界面和晶界,因此具有优异的热稳定性和高温强度。
用模态分析测定发动机叶片振动特性

用模态分析测定发动机叶片振动特性作者:杨伟来源:《科学与财富》2011年第09期[摘要] 本文主要介绍了利用模态分析的方法,对发动机叶片进行振动特性分析。
重点介绍了利用锤击法测定某发动机1级涡轮叶片的模态参数。
详细分析了在模态试验中的各项工作以及容易引起测量误差的地方,并结合试验总结了一些在模态分析中的经验教训。
[关键词] 模态分析锤击静频振型传递函数固有频率激励一、前言在发动机的生产、研制和使用中,必须测定叶片振动特性参数。
叶片振动特性参数通常是指:叶片的静频、振型、阻尼和振动应力等。
用锤击法作结构振动的模态分析是近年来迅速发展起来的。
对叶片做锤击振动试验,首先要在叶片的叶身部分划线确定敲击点。
由于敲击点信息在数据处理后可以反映该点的振动位移,所以最好要避开节线。
一般情况下用锤击法作叶片静频参数测定,如单求频率和阻尼时,只要敲击一点并只测一点响应即可。
二、模态理论简述由振动理论可知:一个线性振动系统,当它按自身某一阶固有频率作自由谐振时,整个系统将具有确定的振动形态(简称振型或模态)。
所谓振动模态分析法,就是利用系统固有模态的正交性,对通常所选取的物理坐标进行线性变换,这个用模态坐标和模态参数所描述的各个独立方程,称为模态方程。
【1】模态分析的首要任务是要求出系统各阶的模态参数(例如系统的固有频率和振型;模态质量或模态刚度,以及模态阻尼等)。
一个具有N个自由度的线性振动系统,若不计及阻尼的影响,则其自由振动的运动微分方程的一般形式可以表示为:因此模态试验的目的是为模态参数识别提供可靠的频率响应函数或脉冲相应函数【1】。
三、模态试验模态试验测试系统主要由以下几个部分组成:激振部分、信号测量与数据采集部分、信号分析和频响函数估计部分。
3.1结构的安装进行模态试验的结构在实际的工作环境中,总处于一定的约束状态。
设置试验时,选择结构的支承方式首先考虑是否模拟其真实的约束状态。
通常用一种非常柔软的悬挂系统将被试结构支承起来,以模拟自由支承。
航空发动机叶片振动特性试验研究
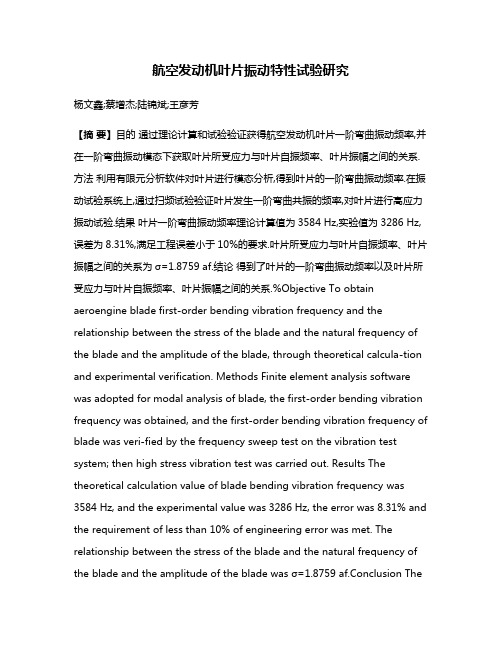
航空发动机叶片振动特性试验研究杨文鑫;蔡增杰;陆锦斌;王彦芳【摘要】目的通过理论计算和试验验证获得航空发动机叶片一阶弯曲振动频率,并在一阶弯曲振动模态下获取叶片所受应力与叶片自振频率、叶片振幅之间的关系.方法利用有限元分析软件对叶片进行模态分析,得到叶片的一阶弯曲振动频率.在振动试验系统上,通过扫频试验验证叶片发生一阶弯曲共振的频率,对叶片进行高应力振动试验.结果叶片一阶弯曲振动频率理论计算值为3584 Hz,实验值为3286 Hz,误差为8.31%,满足工程误差小于10%的要求.叶片所受应力与叶片自振频率、叶片振幅之间的关系为σ=1.8759 af.结论得到了叶片的一阶弯曲振动频率以及叶片所受应力与叶片自振频率、叶片振幅之间的关系.%Objective To obtain aeroengine blade first-order bending vibration frequency and the relationship between the stress of the blade and the natural frequency of the blade and the amplitude of the blade, through theoretical calcula-tion and experimental verification. Methods Finite element analysis software was adopted for modal analysis of blade, the first-order bending vibration frequency was obtained, and the first-order bending vibration frequency of blade was veri-fied by the frequency sweep test on the vibration test system; then high stress vibration test was carried out. Results The theoretical calculation value of blade bending vibration frequency was 3584 Hz, and the experimental value was 3286 Hz, the error was 8.31% and the requirement of less than 10% of engineering error was met. The relationship between the stress of the blade and the natural frequency of the blade and the amplitude of the bl ade was σ=1.8759 af.Conclusion Thefirst-order bending vibration frequency of blade and the relationship between stress of blade and the natural frequency of blade and the amplitude of blade are obtained.【期刊名称】《装备环境工程》【年(卷),期】2018(015)002【总页数】4页(P84-87)【关键词】叶片;模态分析;振动试验;振动特性【作者】杨文鑫;蔡增杰;陆锦斌;王彦芳【作者单位】青岛苏试海测检测技术有限公司,山东青岛 266109;青岛苏试海测检测技术有限公司,山东青岛 266109;青岛苏试海测检测技术有限公司,山东青岛266109;青岛苏试海测检测技术有限公司,山东青岛 266109【正文语种】中文【中图分类】TJ07;TH122航空发动机叶片受力复杂,工作环境严酷,叶片振动疲劳损伤故障是整个发动机故障的主要故障模式[1-2]。
发动机原理_叶片振动

Structural Stressing and Vibration in Aircraft Gas Turbine Engines
第三章 叶片振动 Chapter 3 Blade Vibrations
能源与动力工程学院 School of Energy and Power Engineering
C3=C4=0满足上式,为平凡解;非零解的条件为
shal sin al chal cos al chal cos al shal sin al 0
6/15/2014 10:57:40 PM School of Energy and Power Engineering 19
强迫振动—共振(Resonance) 高循环疲劳(High Cycle Fatigue, HCF) 颤振(Flutter) 低/高循环疲劳(Low Cycle Fatigue, LCF) 旋转失速 随机振动
School of Energy and Power Engineering 4
200
5064
约为:5000m/s
6/15/2014 10:57:40 PM
School of Energy and Power Engineering
23
典型叶片自然频率值
梁 频率方程
1 chal cos al 0
1 chal cos al 0
基频
3.515 EI 1 2 A l
3.2.1 基本方程
实际叶片都是有扭向的变截面叶片,两端边界条件也比 较复杂。为此首先讨论无扭向等截面悬臂梁 ( 根部固装 的叶片),目的是找出叶片振动的基本规律和特征。 假设 细长梁--梁的截面尺寸远小于梁的长度; 纯弯 -- 振动只发生在一个平面内,仅有关于最小惯性 轴的弯曲变形,没有扭转变形; 不考虑剪力对变形的影响;
动态应力的测量实验
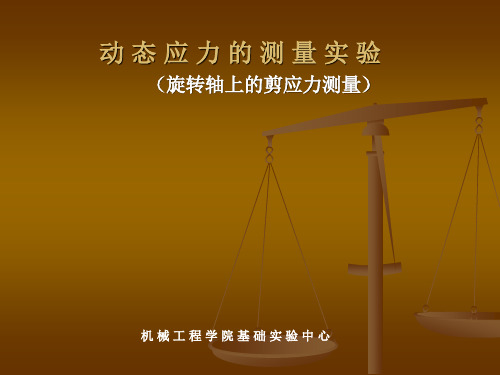
三、动态应力测量的目的 三、动态应力测量的目的
1、认识动态应力对被测构件的强度及使用壽命的影响。 2、 通过对动应力的测量,对被测构件的强度和刚度有所了 解和掌控,从而确保被测构件能安全、合理正常地工作。 3、在今后的机械设计工作中可以帮助我们校核构件的强度 及使用寿命。 4、通过对动应力的测量实验,初步了解,掌握其测量的原 理,方法。
输出轴
电机
变速箱
集流环
制动器
应变片
出轴便产生了一对动态剪应变。 出轴便产生了一对动态剪应变。
图1 集流环式的加载装置
二)、
实验的测量装置
根据“材料力学”中扭转理论, 根据“材料力学”中扭转理论,在纯扭矩载荷 作用下,与轴线成±450方向上的剪切力值为最大 作用下,与轴线成± 值。再根据桥路联接基本关系式的特性,选择使用 再根据桥路联接基本关系式的特性,
铜环 旋转环
固定环罩
输出轴
二)、使用扭矩传感器的实验装置
变 速 电机 箱 扭矩传感 器 器 动 制
器 输出
使用扭矩传感器的实验
置
1、输入能源的耦合器 2、稳压器 3 、应变测量桥 4、应变信号放大器 5、V / F变换器 (电压/ 频率变换器) 6、输出信号的耦合器 7、 F / V变换器 (频率/电压变换器) 扭矩传感器的 : 电源 耦合器 1) 能源 传感器 的 稳压器 2) 变 稳 电压 传感器 应变测量桥 3) 传感器 测 的 变 量 换 应变电压信号 放大器 4) 应变信号放大 V/F 变换器 5) V/F变换器 5) 电 压 信号 变 频率信号 频率信号耦合 器 6) 输出 F / V变换器 7)
3、周期性变化的动应力
发动机工作时,连杆构件上 发动机工作时, 的应力值是作周期性变化的动应力。 的应力值是作周期性变化的动应力。
航空发动机叶片的无损检测毕业设计说明书
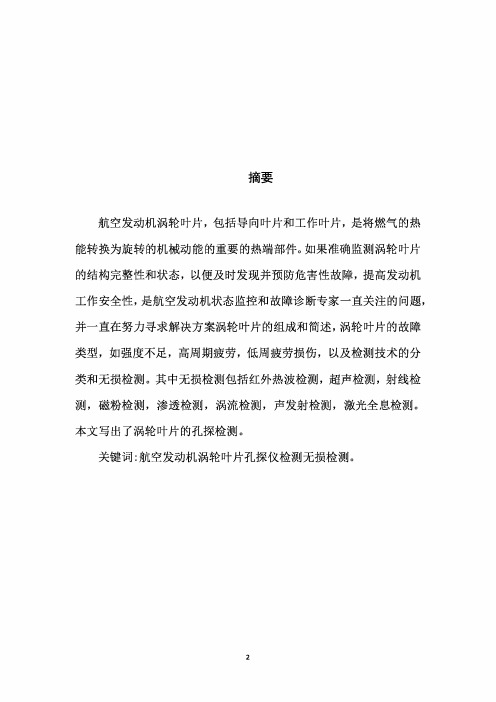
摘要航空发动机涡轮叶片,包括导向叶片和工作叶片,是将燃气的热能转换为旋转的机械动能的重要的热端部件。
如果准确监测涡轮叶片的结构完整性和状态,以便及时发现并预防危害性故障,提高发动机工作安全性,是航空发动机状态监控和故障诊断专家一直关注的问题,并一直在努力寻求解决方案涡轮叶片的组成和简述,涡轮叶片的故障类型,如强度不足,高周期疲劳,低周疲劳损伤,以及检测技术的分类和无损检测。
其中无损检测包括红外热波检测,超声检测,射线检测,磁粉检测,渗透检测,涡流检测,声发射检测,激光全息检测。
本文写出了涡轮叶片的孔探检测。
关键词:航空发动机涡轮叶片孔探仪检测无损检测。
目录摘要 (2)绪论 (1)第一章涡轮叶片的简述 (2)1.1涡轮的工作叶片 (2)1.2导向叶片 (2)第二章故障类型 (3)2.1强度不足及其故障模式 (3)2.2高周期疲劳损伤及其故障模式 (3)2.3低周疲劳损伤及故阵模式 (3)2.4涡轮叶片的常见故障及概率 (3)2.5注意事项 (5)第三章机上孔探检测 (6)3.1涡轮叶片的机上孔探检查 (6)3.2涡轮叶片的不同部位孔探检查 (6)3.3孔探技术的发展和实际应用的需求 (7)3.4修理车间检测前的清洗预处理 (7)3.5叶片完整性检查 (8)3.6探孔注意事项 (8)第四章涡轮叶片孔探案例分析 (9)4.1高压涡轮叶片断裂 (9)4.2典型案例分析 (10)4.3叶片断裂的原因 (11)4.4叶片修理与孔探检测 (13)4.5总结 (14)参考资料 (15)致谢 (16)航空发动机涡轮叶片无损检测技术绪论航空发动机涡轮叶片,包括导向叶片和工作叶片,是将燃气的热能转换为旋转的机械动能的重要的热端部件。
基于提高推重比和单位推力的需要,涡轮前燃气温度日益提高,目前国外新型的航空燃气涡轮发动机涡轮前的温度已达到1700K以上。
涡轮叶片在高压腐蚀性燃气的神击下高速旋转,除承受巨大的拉应力外,还承受频率、幅值变化都很大的交变拉应力和扭转应力,此外还存在高温氧化、热腐蚀和磨损问题。
航空发动机涡轮叶片的故障分析

故障分析结论
通过上述分析可得出如下结论:
1一级涡轮工作叶片从伸根处疲劳断裂,断裂的叶片飞出后打坏后面的涡轮工作叶片和导向叶片,导致发动机失效;
2一级涡轮工作叶片疲劳断裂的原因是伸根处存在大应力区,并且在大应力区存在不应有的冶金铸造缺陷和工艺污染;正是这些在大应力区内的缺陷和污染成为疲劳源,并萌生裂纹,裂纹迅速扩展导致叶片折断;
为了在短时间内提高叶片的使用寿命和寿命期内的可靠性,针对叶片伸根段局部应力过大问题,对叶片进行了局部改进设计,降低了伸根段的应力;经过试验器试验和长期试车考核,证明改进后的叶片寿命有所提高;局部改进设计后的叶片寿命为1500小时/1500次循环;
第三阶段
为彻底克服叶片伸根受力不合理的状况,进一步提高叶片质量和可靠性,延长叶片使用寿命,决定研制全新叶片;新叶片研制的设计原则是:保证与原叶片能够互换,采用成熟的工艺方法早日实现生产;新叶片设计时采用大型三维有限元计算程序对叶片进行了应力和振动计算,计算表明,新研制叶片的应力水平较原叶片有较大幅度的降低,彻底消除了原叶片伸根存在大应力区问题;在试验器上进行的对比试验证明,新设计叶片的伸根寿命比原叶片有大幅提高;通过台架试车考核验证,新叶片的寿命已达到2000小时/2000次热循环;