游梁式抽油机53型减速器设计
游梁式抽油机减速箱维修标准化及常见故障分析
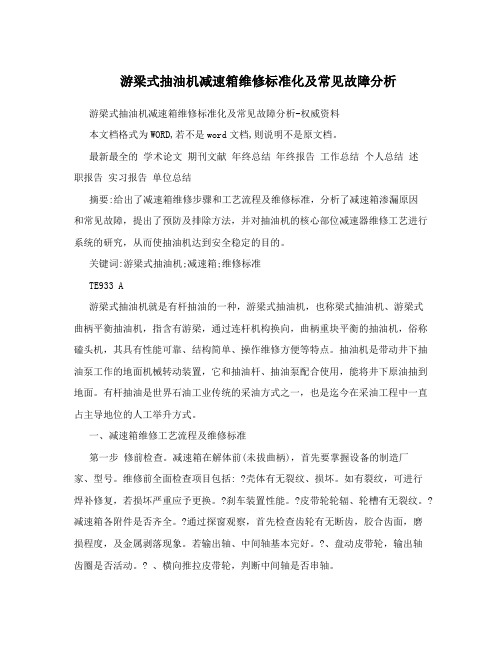
游梁式抽油机减速箱维修标准化及常见故障分析游梁式抽油机减速箱维修标准化及常见故障分析-权威资料本文档格式为WORD,若不是word文档,则说明不是原文档。
最新最全的学术论文期刊文献年终总结年终报告工作总结个人总结述职报告实习报告单位总结摘要:给出了减速箱维修步骤和工艺流程及维修标准,分析了减速箱渗漏原因和常见故障,提出了预防及排除方法,并对抽油机的核心部位减速器维修工艺进行系统的研究,从而使抽油机达到安全稳定的目的。
关键词:游梁式抽油机;减速箱;维修标准TE933 A游梁式抽油机就是有杆抽油的一种,游梁式抽油机,也称梁式抽油机、游梁式曲柄平衡抽油机,指含有游梁,通过连杆机构换向,曲柄重块平衡的抽油机,俗称磕头机,其具有性能可靠、结构简单、操作维修方便等特点。
抽油机是带动井下抽油泵工作的地面机械转动装置,它和抽油杆、抽油泵配合使用,能将井下原油抽到地面。
有杆抽油是世界石油工业传统的采油方式之一,也是迄今在采油工程中一直占主导地位的人工举升方式。
一、减速箱维修工艺流程及维修标准第一步修前检查。
减速箱在解体前(未拔曲柄),首先要掌握设备的制造厂家、型号。
维修前全面检查项目包括: ?壳体有无裂纹、损坏。
如有裂纹,可进行焊补修复,若损坏严重应予更换。
?刹车装置性能。
?皮带轮轮辐、轮槽有无裂纹。
?减速箱各附件是否齐全。
?通过探窗观察,首先检查齿轮有无断齿,胶合齿面,磨损程度,及金属剥落现象。
若输出轴、中间轴基本完好。
?、盘动皮带轮,输出轴齿圈是否活动。
? 、横向推拉皮带轮,判断中间轴是否串轴。
第二步拔曲柄。
卸掉曲柄紧固螺栓,打上垫铁,胀开曲柄,用拉拔机拔下曲柄,同时对曲柄键及连接螺栓统一编号放在规定位置。
对拆卸下曲柄进行检查,曲柄销是否完好,曲柄有无裂痕,键槽是否损坏或磨损过大。
第三步开箱。
开箱前,再次检查箱体,拆下各配件编号置于工具台上(去污、整齐摆放)。
开箱后,检查齿轮换坏情况,轴承有无裂痕,换坏跑外圈,间隙是否超过极限。
游梁式抽油机课程设计说明书
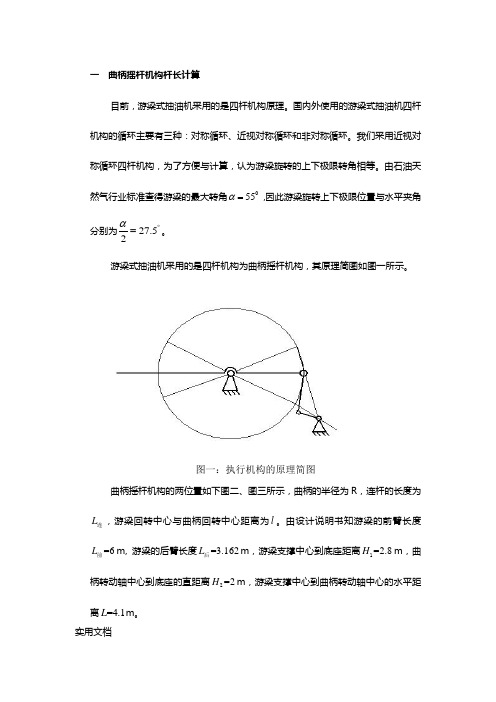
一曲柄摇杆机构杆长计算目前,游梁式抽油机采用的是四杆机构原理。
国内外使用的游梁式抽油机四杆机构的循环主要有三种:对称循环、近视对称循环和非对称循环。
我们采用近视对称循环四杆机构,为了方便与计算,认为游梁旋转的上下极限转角相等。
由石油天然气行业标准查得游梁的最大转角055α=,因此游梁旋转上下极限位置与水平夹角分别为27.52α︒=。
游梁式抽油机采用的是四杆机构为曲柄摇杆机构,其原理简图如图一所示。
图一:执行机构的原理简图曲柄摇杆机构的两位置如下图二、图三所示,曲柄的半径为R,连杆的长度为L连,游梁回转中心与曲柄回转中心距离为l。
由设计说明书知游梁的前臂长度=6L前m, 游梁的后臂长度=3.162L后m,游梁支撑中心到底座距离=2.8H1m,曲柄转动轴中心到底座的直距离2=2H m,游梁支撑中心到曲柄转动轴中心的水平距离=4.1L m。
实用文档实用文档图二:游梁水平示意图图三:游梁后臂上仰最大角示意图由图示两位置状态知:222212() 4.1(2.82) 4.18l L H H m=+-=+-=实用文档1221120.8arctan()arctan()11.054.127.5211.0527.539 2.6314.18 3.162=1.0181.8245;0.8065.H H L L R m L R l L m L m R m οοοοοβαββββ-======+=+=+===-=-=-==连后连连二 驴头的结构设计及重量计算驴头用来将游梁前端的往复圆弧运动变为抽油杆的垂直直线往复运动,为了保证在一定冲程长度下,将圆弧运动变为悬点的直线运动,驴头的圆弧面长度应为:max =~S 弧(1.2 1.3)Smax S 为驴头悬点的最大冲程。
由设计说明书知:max S =6m ,取max 1.2S S =弧,则1.267.2S m =⨯=弧驴头的最大转角为55α︒=, S R α=⋅弧驴,因此7.2===7.504m 55 3.14180S R α⨯弧驴 驴头的材料选厚为100mm 耐磨板的45钢。
抽油机减速器优化设计
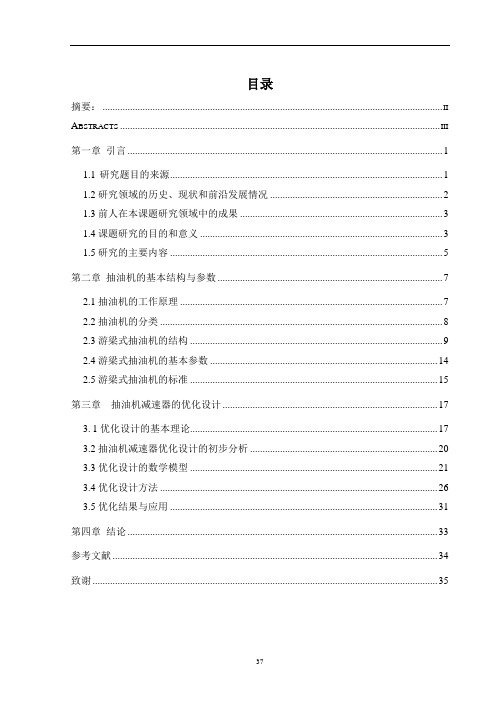
目录摘要: ........................................................................................................................................ I I A BSTRACTS ................................................................................................................................ I II 第一章引言 (1)1.1研究题目的来源 (1)1.2研究领域的历史、现状和前沿发展情况 (2)1.3前人在本课题研究领域中的成果 (3)1.4课题研究的目的和意义 (3)1.5研究的主要内容 (5)第二章抽油机的基本结构与参数 (7)2.1抽油机的工作原理 (7)2.2抽油机的分类 (8)2.3游梁式抽油机的结构 (9)2.4游梁式抽油机的基本参数 (14)2.5游梁式抽油机的标准 (15)第三章抽油机减速器的优化设计 (17)3.1优化设计的基本理论 (17)3.2抽油机减速器优化设计的初步分析 (20)3.3优化设计的数学模型 (21)3.4优化设计方法 (26)3.5优化结果与应用 (31)第四章结论 (33)参考文献 (34)致谢 (35)抽油机减速器优化设计目录目录第一章 引言 (1)1.1 研究题目的来源 (1)1.2研究领域的历史、现状和前沿发展情况 (2)1.2.1研究领域的历史 (2)1.2.2研究现状 (3)1.3前人在本课题研究领域中的成果 (3)1.4课题研究的目的和意义 (4)1.4.1课题研究的目的 (4)1.4.2课题研究的意义 (5)1.5研究的主要内容 (5)1.5.1抽油机的基本结构与参数 (6)1.5.2减速器双圆弧齿轮的优化设计 (6)第二章 抽油机的基本结构与参数 (7)2.1抽油机的工作原理 (7)2.2抽油机的分类 (9)2.3游梁式抽油机的结构 (9)2.3.1驴头设计 (10)2.3.2游梁设计 (11)2.3.3横梁及连杆设计 (11)2.3.4曲柄和平衡重 (13)2.3.5支架设计 (13)2.3.6减速器设计 (14)2.3.7悬绳器总成 (14)2.3.8动力机 (15)2.3.9底座 (15)2.4游梁式抽油机的基本参数 (15)2.4.1驴头悬点(挂抽油杆处)的最大允许载荷m ax P 。
一种两轴油田游梁抽油机变速器[实用新型专利]
![一种两轴油田游梁抽油机变速器[实用新型专利]](https://img.taocdn.com/s3/m/74b20848284ac850ac02425b.png)
专利名称:一种两轴油田游梁抽油机变速器专利类型:实用新型专利
发明人:陈平
申请号:CN202021298321.1
申请日:20200706
公开号:CN212564282U
公开日:
20210219
专利内容由知识产权出版社提供
摘要:本实用新型公开了一种两轴油田游梁抽油机变速器,包括变速箱壳体和输入轴,所述输入轴横向设置于所述变速箱壳体内底部,且所述输入轴上方平行设置有输出轴,所述输出轴横向延伸且转动设置于所述变速箱壳体中部,所述输出轴外侧设置有同步器,所述变速箱壳体正面上方设置有连接所述同步器的换挡组件。
有益效果在于:本实用新型设置两轴四挡式变速器结构,以对电动机输入扭矩增大后带动抽油机工作,以通过使用更小功率的电动机,从而节约电能,启动电流更小,运转平稳,满足游梁抽油机调整冲次要求,无需更换变速箱即可实现1到4冲次任意调节操作,实用性强。
申请人:陈平
地址:433100 湖北省潜江市江汉油田广华江汉路1号10栋201室
国籍:CN
代理机构:深圳贝谷知识产权代理事务所(普通合伙)
代理人:段啸冉
更多信息请下载全文后查看。
常规游梁式抽油机设计
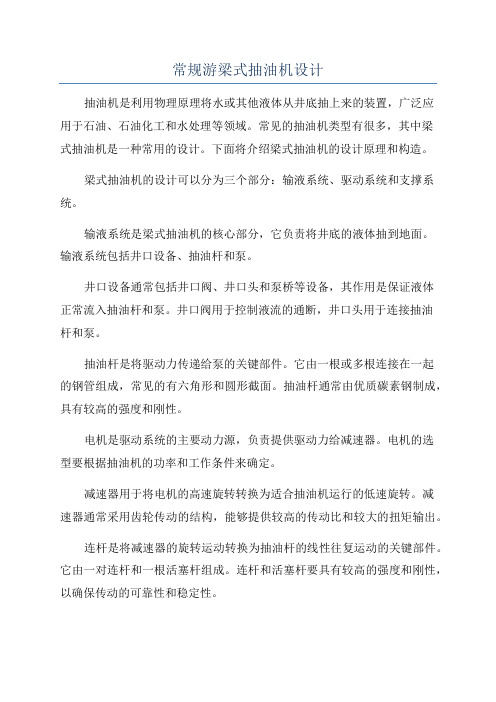
常规游梁式抽油机设计抽油机是利用物理原理将水或其他液体从井底抽上来的装置,广泛应用于石油、石油化工和水处理等领域。
常见的抽油机类型有很多,其中梁式抽油机是一种常用的设计。
下面将介绍梁式抽油机的设计原理和构造。
梁式抽油机的设计可以分为三个部分:输液系统、驱动系统和支撑系统。
输液系统是梁式抽油机的核心部分,它负责将井底的液体抽到地面。
输液系统包括井口设备、抽油杆和泵。
井口设备通常包括井口阀、井口头和泵桥等设备,其作用是保证液体正常流入抽油杆和泵。
井口阀用于控制液流的通断,井口头用于连接抽油杆和泵。
抽油杆是将驱动力传递给泵的关键部件。
它由一根或多根连接在一起的钢管组成,常见的有六角形和圆形截面。
抽油杆通常由优质碳素钢制成,具有较高的强度和刚性。
电机是驱动系统的主要动力源,负责提供驱动力给减速器。
电机的选型要根据抽油机的功率和工作条件来确定。
减速器用于将电机的高速旋转转换为适合抽油机运行的低速旋转。
减速器通常采用齿轮传动的结构,能够提供较高的传动比和较大的扭矩输出。
连杆是将减速器的旋转运动转换为抽油杆的线性往复运动的关键部件。
它由一对连杆和一根活塞杆组成。
连杆和活塞杆要具有较高的强度和刚性,以确保传动的可靠性和稳定性。
支撑系统是梁式抽油机的支撑和定位装置,它负责固定抽油机的各个部件,并保持其稳定运行。
支撑系统包括井口支撑装置、牵引装置和平衡装置。
井口支撑装置用于支撑并固定抽油机的上部分,通常由一个支撑架和一个固定架组成。
支撑架用于支撑抽油杆和泵,固定架用于固定井口设备。
牵引装置用于将抽油杆与支撑架连接起来,并通过定位轮对其进行固定。
牵引装置具有较高的刚性和可靠性,以确保抽油机的稳定运行。
平衡装置用于平衡抽油机在运行过程中产生的力和扭矩,以减少对井口设备和支撑系统的冲击和磨损。
通过合理的设计和选型,梁式抽油机能够高效地将井底的液体抽上来,并保持稳定的运行。
在设计过程中,需要考虑井深、产液量、液体性质和工作环境等因素,并且要根据实际情况进行调整和改进,以提高抽油机的性能和可靠性。
常规型游梁抽油机传动装置设计
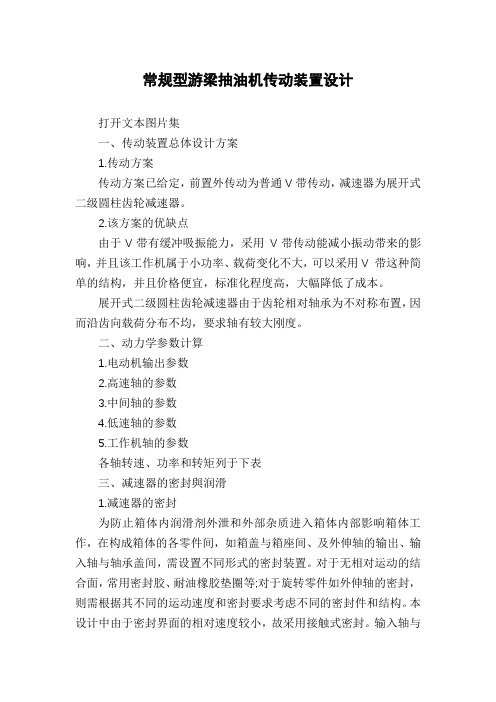
常规型游梁抽油机传动装置设计打开文本图片集一、传动装置总体设计方案1.传动方案传动方案已给定,前置外传动为普通V带传动,减速器为展开式二级圆柱齿轮减速器。
2.该方案的优缺点由于V带有缓冲吸振能力,采用V带传动能减小振动带来的影响,并且该工作机属于小功率、载荷变化不大,可以采用V 带这种简单的结构,并且价格便宜,标准化程度高,大幅降低了成本。
展开式二级圆柱齿轮减速器由于齿轮相对轴承为不对称布置,因而沿齿向载荷分布不均,要求轴有较大刚度。
二、动力学参数计算1.电动机输出参数2.高速轴的参数3.中间轴的参数4.低速轴的参数5.工作机轴的参数各轴转速、功率和转矩列于下表三、减速器的密封與润滑1.减速器的密封为防止箱体内润滑剂外泄和外部杂质进入箱体内部影响箱体工作,在构成箱体的各零件间,如箱盖与箱座间、及外伸轴的输出、输入轴与轴承盖间,需设置不同形式的密封装置。
对于无相对运动的结合面,常用密封胶、耐油橡胶垫圈等;对于旋转零件如外伸轴的密封,则需根据其不同的运动速度和密封要求考虑不同的密封件和结构。
本设计中由于密封界面的相对速度较小,故采用接触式密封。
输入轴与轴承盖间V 3m/s,输出轴与轴承盖间也为V 3m/s,故均采用半粗羊毛毡封油圈。
2.齿轮的润滑通用的闭式齿轮传动,其润滑方式根据齿轮的圆周速度大小决定。
由于低速级大齿轮的圆周速度v≤12m/s,将大齿轮的轮齿浸入油池进行浸油润滑。
这样,齿轮在传动时,就把润滑油带到啮合的齿面上,同时也将油甩到箱壁上,借以散热齿轮浸入油中的深度通常不宜超过一个齿高,但一般亦不应小于10mm。
为了避免齿轮转动时将沉积在油池底部的污物搅起,造成齿面磨损,大齿轮齿顶距离油池地面距离不小于30mm,取齿顶距箱体内底面距离为30mm。
由于低速级大齿轮全齿高h=6.75mm≤10mm,取浸油深度为10mm。
则油的深度H为H=30+10=40mm根据齿轮圆周速度查表选用负荷工业齿轮油(GB 5903-2011),牌号为320润滑油,黏度推荐值为266cSt。
游梁式抽油机设计毕业设计开题报告
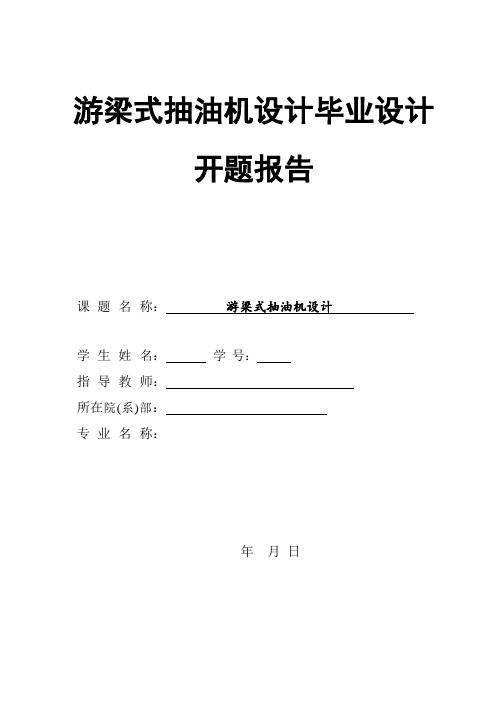
[1]刘长年.全状态调控式液压抽油机.北京:石油工业出版社, 2014
[2]陈宪侃.抽油机采油技术.北京:石油工业出版社, 2014
[3]张建军.游梁式抽油机设计计算.北京:石油工业出版社,2013
[4]吉效科.油田设备技术与管理.北京:中国石化出版社, 2012
[5]大港油田集团钻采工艺研究院.国内外钻井与采油设备新技术.北京:中国石化出版社, 2005
4.成本的节约问题是企业面对一项可能付诸实际的设计时首先会考虑的。这个设计在此方面有所注意。
指导教师
意见
指导教师签名
年月日
教研室意见
院部意见
主任签名:
年月日
教学院长签名:
年月日
1.游梁式抽油机(1)常规游梁式抽油机是油田使用历史最悠久,使用数量最多的一种抽油机。该机采用具有对称循环四杆机构或近似对称循环四杆机构,结构简单,运行可靠,操作维护方便,但长冲程时平衡效果差,效率低,能耗大,不符合节能要求基本停止了生产。(2)异相型游梁抽油机是近30余年来改造成功的一种性能较好的抽油机。与常规游梁抽油机相比有两点改进:其一是将减速箱背离支架后移,增大了减速箱输出轴中心和游梁摆动中心之间水平距离,形成较大极位夹角;其二是平衡块重心与曲柄轴中心连线和曲柄销中心与曲柄轴中心连线之间构成夹角。其所需电动机功率小,在一定条件下有节能效果。(3)前置型游梁抽油机其悬点载荷较低,抽油机承载状况较合理,运行平稳,减速箱齿轮基本无反向负荷,连杆、游梁不易疲劳损坏,机械磨损小,噪声比常规式抽油机低,整机寿命长。前置式抽油机可配置较小功率的电动机,节能效果显著。与常规式抽油机相比,具有体积小、重量轻、节省钢材的优点。(4)气动平衡游梁抽油机,这种抽油机实际上是前置式抽油机的变型。其不同之处是不用平衡重来实现平衡而是利用气缸内气体压力产生的推力来实现平衡。优点是无笨重的平衡块,总机重量减轻约1/3,用调整气包内压力实现平衡的调节工作,调整平衡时不用停机,操作十分方便,而且有利于减小减速箱的负扭矩平衡效果好。缺点是气缸加工费用高。
毕业设计(论文)-常规游梁式抽油机设计[管理资料]
![毕业设计(论文)-常规游梁式抽油机设计[管理资料]](https://img.taocdn.com/s3/m/4e565075ec3a87c24128c449.png)
摘要常规型抽油机,是机械采油设备中问世最早,应用最广泛,结构最简单的设备。
抽油机是石油工业中的一项重要组成部分,在抽油机驱动下,带动其他设备运转,实现油井的机械式开采。
主要分为游梁式和无梁式两大类。
游梁式抽油机主要由发动机、三角带、曲柄、连杆、横梁、游梁、驴头、悬绳器、支架、撬座、制动系统及平衡重组成。
随着时代的发展,对环保节能要求的不断提高,在理论与实践相结合的基础之上,目前国内外抽油机的总的发展趋势是向着超大载荷,长冲程,低冲次,精确平衡,自动化,智能化,节能化,高适应性,无游梁长冲程方向发展。
本设计主要根据抽油机的四杆机构(曲柄——连杆——横梁——游梁)的工作原理。
本文介绍了常规抽油机工作原理与节能原理,以及设计过程中对抽油机运动学和动力学分析与计算,阐述了这种设备的运动规律。
游梁式抽油机驴头的悬点载荷标志抽油机的工作能力的重要参数之一,而看它是否节能,其技术指标是抽油机的电动机实耗功率的大小及减速器的工作状态。
本设计全面概述了常规性抽油机的发展概况,抽油机的优化设计及其节能原理。
另外,设计者对抽油机得几何参数,运动参数,动力学参数进行了全面的分析计算。
此外,本设计不仅采用了计算机编程来计算抽油机的运动和动力学参数,而且采用了Auto CAD绘图软件,并附有中英文对照资料。
关键词:常规型抽油机;悬点载荷;结构;设计计算AbstractConwentional beam-pumping unit to take out the oil machine,publishing in the machine oil extraction equapments at the earliest stage,applied extensive,the most simple equipments in unit is an important component in the petroleum industry, driving by the pumping units,and the other equipments are running in order to achieve the mechanized exploitation of the oil well. It is mainly classified beam and non- beam two categories. Beam style pumping unit mainly consists of the engine, triangle belt, crank, connecting rod, beam, beam, donkey head, hanging a rope device, cradles, pry block, brake system and balance weight. With the development of the ages, the requirements of energy-saving and the consciousness of environmental protection enhancement, on the basis of the combining of the theory and practice, the current domestic and international pumping unit’s overall development trend is toward super-load, long stroke, low stroke times, precise balance, automatic, intelligent, energy- saving, high adaptability and non-beam long stroke direction. This design was mainly according to the principle of four-pole framework (crank -- connecting rod -- beam -- beam) of pumping unit’s.In this article ,working routine and power-saving technology of the conventional beam-pumping unit will be introduced, and during the designing procedure, the analysis of kinetic and dynamic to the pumping units express law of motion of this kind of equipment .The air load of beam style pumping unit is one of the important parameters, which is the first sign of the work capacity, and see it whether energy-saving, the technical indicators are the size of the electromotor consumption power and the work state of the this design said the difference al mutually a development general situation that took out the oil machine excellent to turn the design and it economized on energy the principle .Moreover,designed to taking ou the oil machine get several parameter,sport parameter ,the dynamics parameter carried on the analytical calculation completely.In addition, not only computer programming to calculate the movement and dynamics parameters is used in the design, but also the application of the Auto CAD software, simultaneously with Chinese-English information.Key words: Conventional Pumping Unit,;Horsehead load,;Structural Characteristic,;Design Calculation目录第一章绪论 (1) (1) (1) (2) (2) (2) (4) (4) (5) (5) (5) (5)第二章计算部分 (7) (7) (7) (8) (8) (9) (9)(悬点)加速度计算式 (10) (10) (10) (10) (11) (11) (11) (11) (12)第三章主要部件的设计计算 (14) (14) (14) (14) (15) (15) (15) (16)第四章抽油机的各结构的强度校核 (19) (19) (20) (22) (25) (28)结论 (30)参考文献 (31)致谢 (32)附录一中文译文 (i)附录二外文资料原文 (v)常规游梁式抽油机设计第一章绪论抽油机产生和使用由来已久,迄今已有百年的历史。
- 1、下载文档前请自行甄别文档内容的完整性,平台不提供额外的编辑、内容补充、找答案等附加服务。
- 2、"仅部分预览"的文档,不可在线预览部分如存在完整性等问题,可反馈申请退款(可完整预览的文档不适用该条件!)。
- 3、如文档侵犯您的权益,请联系客服反馈,我们会尽快为您处理(人工客服工作时间:9:00-18:30)。
本科生毕业设计(论文)题目:游梁式抽油机53型减速器设计摘要本文阐述了我国齿轮减速器的现状及发展趋势,着重对游梁式抽油机53型双圆弧齿轮减速器进行设计计算,其中包括驱动装置的选择、总传动比的设定及各级传动比的分配、齿轮传动设计和各级传动轴的设计计算,并结合设计对系统进行了动态校正和强度校核。
用CAXA绘制二维装配图,Autodesk Inventor绘制三维图,最终设计出符合要求的齿轮减速器关键字双圆弧齿轮;齿轮减速器;分流式人字齿结构;强度校核ABSTRACTThis paper expounds the present situation and development of gear reducer trend .Focusing on the beam pumping unit double-arced gear reducer 53 type design calculation, including drives choice, total ratio setting and the distribution of transmission ratio at all levels, gear transmission design and various design and calculation of the drive shaft ,and according to the design of the system dynamic correction and strength check. Using CAXA Autodesk Inventor, assembly drawing two-dimensional drawing three-dimensional graph, finally designed to meet the requirements of gear reducerKeywords: Double-arced gear ; Gear reducer ;Shunt person handwriting toothstructure ;Strength check目录第1章概论 (1)1. 齿轮减速器的现状及发展趋势 (1)2. 我国抽油机减速器现状 (2)第2章传动方案的拟定 (4)1. 传动方案 (4)2. 电动机的选择 (4)3. 总传动比确定及各级传动比分配 (6)4. 计算传动装置的运动和动力参数 (7)第3章齿轮传动设计 (9)1. 高速级齿轮传动设计 (9)2. 低速机齿轮传动设计 (16)第4章轴的设计 (24)1. 输入轴的设计 (24)2. 中速轴的设计 (26)3.低速轴的设计 (29)第5章轴承的选择和校核计算 (34)1. 输入轴承的选择与计算 (34)2. 中间轴上轴承的校核与计算 (35)3. 输出轴上的轴承选择与计算 (36)第6章键连接的选择与校核计算 (37)1. 输入轴与带轮的键连接 (37)2. 齿轮2与中间轴的键连接 (37)3. 齿轮3与轴的键连接 (38)第7章减速器附件设计及润滑密封 (39)1. 减速器附件设计 (39)2. 润滑与密封 (40)第8章减速器的二维装配图与三维设计图 (41)总结 (42)科瑞集团实习报告 (42)致谢 (44)参考文献 (45)第1章概论1. 齿轮减速器的现状及发展趋势20世纪70年代末以来,世界减速器技术有了和打发展。
产品发展的总趋势是小型化、高速化、低噪声和高可靠性;技术发展中最引人注目的是硬齿面技术、功率分支技术和模块化设计技术。
到80年代,国外硬齿面技术已日趋成熟。
采用优质合金钢锻件、渗碳淬火磨齿的硬齿面齿轮,精度不低于ISO1328-1975的6级,综合承载能力为中硬齿面调质齿轮的3~4倍,为软齿面齿轮的4~5倍。
一个中等规格的硬齿面减速器的重量仅为中硬齿面减速器的1/3左右,且噪声低、效率高、可靠性高。
功率分支技术主要用于行星及大功率双分支以及多分支装置,如中心传动讲的水泥磨主减速器。
其核心技术是均载。
对通用减速器而言,除普遍采用硬齿面技术外,模块化设计技术已成为其发展的一个主要方向。
它旨在追求高性能的同时,即可能减少零部件及毛坯的品种规格和数量,以便于组织生产,形成批量,降低成本,获得规模效益。
同时,利用基本零件,增加产品的型式和花样,尽可能多地开发使用地变型设计或派生系列产品,如由一个通用系列派生出多个专用系列;摆脱了传统地单一有底座实心轴输出地安装方式,增添了空心轴输出的无底座悬挂式、多方位安装面等不同型式,扩大了使用范围。
改革开放以来,我国陆续引进先进加工装备,通过引进、笑话、吸收国外先进技术和科研攻关,开始掌握了各种高速和低速重载齿轮装置的设计制造技术。
材料和热处理质量级齿轮加工精度都有较大提高,通用圆柱齿轮的制造精度可以从JB179-60的8~9级提高到GB10095-88的6级,高速齿轮的制造精度可稳定在4~5级。
目前我国已可设计制造2800kW的水泥磨减速器、1700mm轧钢机各种齿轮减速器。
各种棒、线材轧机用减速器已全部采用硬齿面。
我国自行设计制造的高速齿轮装置的功率已达44000kW,齿轮圆周速度达168m/s。
80年代末至90年代初,我国相继制订了近100各齿轮和蜗杆减速器的标准,研制了许多新型减速器,大体上实现了通用减速器的更新换代。
许多产品达到了80年代的国际水平。
部分减速器采用硬齿面厚,体积和重量明显减小,承载能力、使用寿命、传动效率和可靠性有了大幅度提高,对节能和提高主机的总体水平起到明显的作用,为发展我国的机械产品作出了贡献。
进入90年代中后期,国外又陆续推出了更新换代的减速器,不但更突出了模块化设计的杰特点,而且,在承载能力、总体水平,外观质量方面又有明显提高。
面对这方面差距,我们的对策应该是:有条件的企业应该瞄准国际最先进的水平,尽快研究开发面向21世纪的新产品。
要研究出更好的模块化设计方法,以期形成较大的批量,求得规模效益。
现在国内有的企业已经先走了一步,开发出这类产品。
研究、开发、推广成本较低而承载能力又能接近硬齿面的中硬齿面滚齿的新齿形和新结构。
国内多年来使用行之有效的双圆弧齿轮、三环减速器和已成功应用的点线捏合齿轮等技术、应不断完善,大力推广。
2. 我国抽油机减速器现状抽油机减速器是一种承受重复交变载荷、长期连续运转的减速装置。
对于我国的抽油机主要有以下几种指标:第一种,目前最多应用也是市面上出售最多的一种抽油机的型号是JHL 型油田抽油机专用减速机。
它采用了双圆弧齿形圆柱齿轮,其具有承载能力大,使用寿命长,工作平稳,噪音小,密封性能好,安全可靠,安装使用方便等特点,适用各种野外条件下的连续作业,也可适用于矿用绞车。
第二种,油田用硬齿轮减速机是按照国家标准(GB19004-88)生产的,主要包括ZDY(单级)、ZLY(两级)、ZSY(三级)很ZFY(四级)四大系列。
性能特点:1、中心距,传动比等主要均优化设计,主要零、部件性好。
2、齿轮均采用优质合金刚渗碳、淬火而成,齿轮硬度达HRC58-62。
3、体积小、重量轻、精度高、承载能力大、寿命长、可靠性高、传动稳、噪音低。
4、一般采用池润滑,自然冷却,当热力率不能满足时,可采用循环油润滑或风扇,冷却盘管冷却。
第三种,抽油机专用摆线针轮减速机。
采用行星传动原理,摆线针轮啮合,设计先进、结构新颖。
特点:1、传动比大。
一级减速时传动比为1/6--1/87。
两级减速时传动比为1/99--1/7569;三级传动时传动比为1/5841--1/658503。
另外根据需要还可以采用多级组合,速比达到指定大。
2、传动效率高。
由于啮合部位采用了滚动啮合,一般一级传动效率为90%--95%。
3、结构紧凑,体积小,重量轻。
体积和普通圆柱齿轮减速机相比可减小2/1--2/3。
4、故障少,寿命长。
主要传动啮合件使用轴承钢磨削制造,因此机械性能与耐磨性能均佳,又因其为滚动摩擦,因而故障少,寿命长。
5、运转平稳可靠。
因传动过程中为多齿啮合,所以使之运转平稳可靠,噪声低。
6、拆装方便,容易维修。
7、过载能力强,耐冲击,惯性力矩小,适用于起动频繁和正反转运转的特点。
第四种,三环减速机由三片相同的内齿环板带动一个外齿齿轮输出,故称为三环减速器,属平行轴一动轴齿轮传动减速器,齿轮啮合运动属于动轴轮系,具有少齿差行星传动特征,输出与输入轴间平行配置,又有平行轴圆柱齿轮减速器的特征。
具有承载和超载能力强、传动比大、分级密集、效率高、结构紧凑、体积小、质量轻、装拆维修方便、适用性宽广等优点。
工作特点:1、工作环境温度为-40℃ C~+45℃,环境温度低于0℃时,启动前润滑油应预热。
2、高速轴转速不得超过功率表中规定的最高值。
3、瞬时允许尖锋转矩为额定转矩的2.7倍。
4、适用于连续,短时或断续工作制,可正反转。
5、减速器与原动机(常用电动机)和工作机之间应用非刚性联轴器且其轴心线应严格对中。
第2章传动方案的拟定1. 传动方案抽油机由电动机驱动,电动机1皮带2将动力传入减速器3,在输出端带动曲柄工作。
由于抽油机的载荷变化大,传动系统中采用两级对称分流式双圆弧圆柱齿轮减速器结构较复杂,高速级齿轮相对于轴承位置对称,沿齿宽载荷分布较均匀,高速级和低速级均为人字齿双圆弧圆柱齿轮传动。
传动方案如图2-1图2-1传动方案示意图2. 电动机的选择2.1 选择电动机类型按已知工作条件和要求,选用Y系列一般用途的三相异步电动机2.2.1减速器输出功率w Pw P = w6Tn 9.5510⨯出(2-1) 由公式(2-1)得w P = 27.749kw抽油机输出转速w n 等于抽油机的冲程w n =5r/min2.2.2 电动机至减速器之间传动装置的总效率为η32123ηηηη=⋅⋅(2-2) 1η,2η,3η 分别为皮带,轴承及齿轮传动的效率,1η=0.96,2η=0.98,3η=0.97由公式(2-2)得32321230.960.980.96=0.8327ηηηη=⋅⋅=⨯⨯2.2.3 确定电动机的额定功率ed Pd P =w P /η(2-3) 电动机的输出功率为d P由公式(2-3)得d P =33.3kw选定电动机的额定功率ed P =37kw抽油机的冲程w n =5 r/min 该传动系统为分流式圆柱齿轮传动,查阅教材表18-1推荐传动比为12i i i =⋅=8~60,则总传动比可取 8至60之间则电动机转速的可选范围为'1d n =8w n =8×57.32=458.56r/mi '2d n =60wn =60×57.32=3439.2r/min 可见同步转速为1000r/min ,1500r/min ,3000r/min 的电动机都符合,这里初选同步转速为1000r/min ,1500r/min ,3000r/min 的三种电动机进行比较,由参考文献[1]中表16-1查得:表2-1方案电动机型号 额定功率 (KW ) 电动机转速n/(r/min) 额定转矩堵转转矩 额定转矩最大转矩质量/kg 同步转速 满载转速1Y160M1-2 37 3000 2930 2.0 2.2 200 2Y160M-4 37 1500 1460 2.2 2.2 230 3Y160L-6 37 1000 970 2.0 2.0 200 4 Y180L-8 37 750 740 1.7 2.0 220由表中数据,综合考虑电动机和传动装置的尺寸、重量,价格以及总传动比,即选定方案43. 总传动比确定及各级传动比分配3.1 计算总传动比由参考文献[1]中表16-1查得:满载转速nm=740 r / min ;总传动比i=nm /w n =740/5=148 r / min3.2 分配各级传动比 查阅参考文献[1]《机械设计课程设计》中表2—3各级传动中分配各级传动比;取高速级的圆柱齿轮传动比2i =3(1.3~1.4)i =6.10,则低速级的圆柱齿轮的传动比为3i =4.78 4. 计算传动装置的运动和动力参数4.1 各轴转速电动机轴为电机轴0,减速器高速级轴为轴1,中速轴为轴2低速级轴为轴3,则0n = 740 r/min 011740r /min =145.78r /min 5.076n n i == 12223.89r /min n n i == 2335r /min n n i ==4.2 按电动机额定功率ed P 计算各轴输入功率2331.970.980.97kw 30.68kw II I P P ηη=⋅=⨯⨯=133.30.9631.97I d P P KW η==⨯=23III II P P ηη=⋅⋅=10.89×0.96×0.97 kw =28.30kw4.3 各轴转矩9550P T n=⨯(2-4)由公式(2-4)得311131.9795509550 2.09410145.78P T N m N m n =⨯=⨯=⨯ 2295502P T n =⨯×30.68/23.89 =12.26310N m ⨯⋅ 333395509550(28.30/5)53.910P T N m N =⨯=⨯=⨯∙ 将轴的运动参数汇总于下表以备查用: 表1-3轴名功率P (kw )转矩T(N.mm )转速n(r/min )传动比i效率η电机轴33.307405.0760.961轴31.972.10610⨯145.786.100.942轴 30.6812.26610⨯23.894.780.943轴28.3053.9610⨯5.00第3章 齿轮传动设计1. 高速级齿轮传动设计1.1 选择材料、精度及参数1.1.1 按图1所示传动方案,选用圆弧圆柱齿轮传动1.1.2抽油机为一般工作机器,速度不高,故选用7级精度(GB10095-88) 1.1.3 材料选择。