两工位钻孔_攻丝组合机床液压控制系统的设计
钻孔机床的液压控制系统毕业设计论文概要
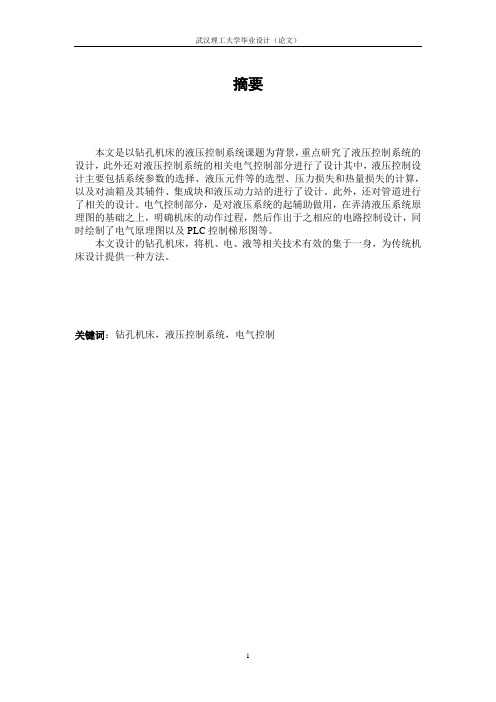
摘要本文是以钻孔机床的液压控制系统课题为背景,重点研究了液压控制系统的设计,此外还对液压控制系统的相关电气控制部分进行了设计其中,液压控制设计主要包括系统参数的选择、液压元件等的选型、压力损失和热量损失的计算,以及对油箱及其辅件、集成块和液压动力站的进行了设计。
此外,还对管道进行了相关的设计。
电气控制部分,是对液压系统的起辅助做用,在弄清液压系统原理图的基础之上,明确机床的动作过程,然后作出于之相应的电路控制设计,同时绘制了电气原理图以及PLC控制梯形图等。
本文设计的钻孔机床,将机、电、液等相关技术有效的集于一身,为传统机床设计提供一种方法。
关键词:钻孔机床,液压控制系统,电气控制AbstractThis paper pays more attention to the research of hydraulic control system based on the problem of hydraulic control system of drill-machine, and more takes some design of electric control system. The content of hydraulic control design includes select of system parameter, select of the hydraulic component, pressure loss, energy loss, oil box and its complement design, integration block design and the design of the central power station. And more, makes correlative design of the pipeline. The function of the part of electric control is to assistant the hydraulic system, makes sure the course of machine tool action based on understanding the principle of hydraulic system, then makes the corresponding design of circuit control and protracts the electric principle drawing and PLC control trapezoid drawing.This design of drill-machine integrates the function of machine, electricity, fluid. Provides a new design thought to the traditional design of the drill-machine.Key words: drill-machine ,hydraulic control system ,electric control目录绪论 (1)1.1研究的背景和意义 (1)1.2本文的内容和结构 (1)第一章系统的初步计算和系统原理图的拟定 (2)2.1系统设计的主要参数 (2)2.2钻孔机床的工况分析 (2)2.3确定液压系统参数 (6)2.4拟定系统原理图 (7)第三章液压元件的选型 (10)3.1液压泵和电动机的选择 (10)3.2元、辅件的选择 (11)第四章液压辅件的设计计算与选型 (16)4.1 液压油箱的设计 (16)4.2 液压管路的设计 (17)4.3 过滤器的选择 (18)4.4 液压工作介质的选择 (19)第五章液压系统的验算 (19)5.1液压系统压力损失的计算 (20)5.2液压系统升温验算 (21)第六章液压动力站和集成块的设计 (23)6.1液压动力站设计 (23)6.2集成块的设计 (24)第七章液压系统的电气控制设计 (25)7.1液压系统的电气控制 (25)7.2PLC控制 (25)第八章工作总结和展望 (27)8.1工作总结 (27)8.2工作展望 (27)致谢 (28)参考文献 (29)1 绪论1.1课题研究的背景和意义本次研究的课题是一个多轴(16个轴)组合机床的液压驱动系统,而传统的钻床的加工轴都是比较少,比如单轴,双轴,3、4轴等,总体上同本课题研究的钻孔机床存在一定的差别。
组合机床控制系统设计安装与调试

组合机床控制系统设计安装与调试学校: 姓名:1、组合机床概述两个位钻孔、攻丝组合机床, 能自动完成工件钻孔和攻丝加工, 自动化程度高, 生产效率高。
机床关键由床身、移动工作台、钻孔滑台、钻孔动力头、攻丝滑台、攻丝动力头、滑台移动控制凸轮系统等组成, 如图1所表示。
图1 两工位钻孔攻丝组合机床示意图移动工作台用以完成工件移动, 实现自动加工。
钻孔滑台和钻孔动力头, 用以实现钻孔加工量调整和钻孔加工。
攻丝滑台和攻丝动力头, 用以实现攻丝加工量调整和攻丝加工。
工作台移动(左移和右移)由电动机正反转控制; 钻孔滑台移动(上移和下移)直接由钻孔主轴电机(单向)拖动凸轮机构实现自动进给和退刀控制; 攻丝滑台移动(上移和下移)直接由攻丝主轴电机正、反转拖动凸轮机构实现自动进给和退刀控制。
2、加工工艺及控制要求若机床各部分在原位(工作台在钻孔工位 SQ1 动作, 钻孔滑台在原位 SQ2 动作, 攻丝滑台在原位 SQ4动作)。
若不在原位则需手动回原位。
将工件放在工作台上, 手工夹紧。
按下开启按钮, 开启钻孔动力头电机 M1正转, 且由凸轮机构带动钻孔动力头自动进给, 进行钻孔加工。
当钻孔滑台抵达终点时, 钻孔滑台自动后退, 到原位时停, M1同时停止。
等到钻孔滑台回到原位后, 工作台左/右移电动机M3正转使工作台右移, 当工作台到攻丝工位时, 限位开关SQ3动作, 工作台停止。
开启攻丝动力头电机M2正转, 攻丝滑台开始前移, 进行攻丝加工, 当攻丝滑台到终点时(终点限位 SQ5动作), 5S 后攻丝动力头电机 M2反转, 同时攻丝滑台由控制凸轮控制使其自动后退。
攻丝电动机由变频器拖动实现变频调速, 运行曲线如图2所表示。
(加速时间1.5S, 减速时间1S)0··图2 攻丝主轴电机运行曲线当攻丝滑台后退到原位时, 攻丝动力头电机M2停止, 延时3S后工作台左/右移电动机M3反转, 工作台左移, 到钻孔工位时停。
双工位枪钻组合机床控制系统设计

区 微 动 3种 手 动 运 行 方 式 。
由 P C发 出 命 令 , 以 进 行 高 速 J G, 速 J G, 可 O 低 O
● 位 控 模 块 的 数 据 传 送
3 双 工位 枪钻 组 合机 床 的 控 制 原 理
职工 位 枪 钻 组 合 机 床 控 制 系 统 主 要 采 用 了 欧 姆 龙 C 0 HX可 编 程 控 制 器 , 姆 龙 NC 1 位 置 控 制 模 20 欧 12 块, 日本 安 川 的 交 流 伺 服 驱 动 系 统 以 及 常 规 的 交 流 接
触 器 等 进 行 控 制 。 其 机 床 控 制 原 理 流 程 图 如 图 1所
习 o
存储在 P C中 DM 区域和其 它 内部继 电 器 区域 中 的位置 动作 和 速 度 的数 据 , 由 P 能 C根据 数 据传 送 指 令, 很快 传 送 刊 该 位 控模 块 。这样 P C能 够 实现 超 过 位控模 块本 身 控 制 能力 ( 置 控 制 点 2 , 度 控制 点 位 O速
圈 1 机 床 控 制 原 理 流 程 图
该 模块 是 C 0 H P s 2 0 C 一种 特殊 的 I 0单 元 , 是 / 它
根据 P C程 序 的 控 制 命 令 输 出 相 应 的 脉 冲 串 到 步 进 电 机或 伺服 电机 驱动 器。 ● 控 制 轴 数 和 控 制 内容
钻镗两用组合机床的液压控制系统及电气控制系统设计

目录摘要 (1)Abstract (2)1、绪论 (1)1.1、课题的背景 (1)1.2、组合机床概述 (1)1.3、专用组合机床的介绍 (3)1.4、 PLC简介 (4)1.4.1 PLC的定义 (5)1.4.2 PLC的基础知识 (6)1.4.3 PLC的用途 (8)2、钻镗两用组合机床控制概述 (9)2.1、钻镗两用组合机床主电路原理图 (10)2.2、钻镗两用组合机床的工作流程图 (11)2.3、钻镗两用组合机床的控制过程 (11)2.3.1各电磁阀动作状态 (12)2.3.2专用组合机床的总控制过程 (12)3、钻镗两用组合机床的液压系统设计 (12)3.1、确定系统方案 (13)3.2、拟定液压系统图 (14)3.3、液压缸的设计计算 (14)3.3.1液压缸的类型及结构形式 (15)3.3.2液压缸的工作压力 (15)3.3.3计算液压缸的尺寸 (16)3.3.4液压缸各工作阶段的压力、流量和功率计算 (17)3.4、液压缸工况图 (18)3.5、液压缸推力的计算 (19)3.6、液压系统的压力损失计算 (19)4、专用钻孔机床的PLC设计 (19)4.1、输入输出点分配 (21)4.2 、PLC的选择 (22)4.3、专用组合机床PLC控制系统接线图 (23)5、钻镗两用组合机床PLC控制程序 (24)结论 (25)致谢 (26)参考文献 (27)摘要钻镗两用组合机床,属于机械加工用机床。
它由工作台、安装在工作台两端及一侧的导轨,导轨与工作台的边缘平行,钻架通过吊铁和锁紧螺钉安装在导轨上;导轨上设有燕尾,钻架可在导轨上水平移动;钻架包括溜板、溜板上装有传动机构,溜板底面上设有与导轨上的燕尾相配合的燕尾槽,机械滑台上装有主支撑架,主支撑架上装有纵向机械滑台及控制系统,控制系统连接一控制活动按钮站,纵向机械滑台上装有附属支撑架,附属支撑架上通过机械滑台装有水平方向的钻削动力头。
它解决了现有的钻床加工大型零部件特别是回转体直径较大时操作不方便、加工困难等技术问题。
双面钻孔组合机床液压系统设计毕业设计

双面钻孔组合机床液压系统设计毕业设计1 绪论1.1 组合机床的发展现状及前景组合机床(transfer and unit machine)是根据工件加工需要,以大量通用部件为基础,配以按工件特定形状和加工工艺设计的专用部件和夹具,组成的一种高效的半自动或自动专用机床[5]。
在我国,组合机床发展已有28年的历史,其科研和生产都具有相当的基础,应用也已深入到很多行业。
是当前机械制造业实现产品更新,进行技术改造,提高生产效率和高速发展必不可少的设备之一。
它的特征是高效、高质、经济实用,因而被广泛应用于工程机械、交通、能源、军工、轻工、家电等行业[8]。
我国传统的组合机床及组合机床自动线主要采用机、电、气、液压控制,它的加工对象主要是生产批量比较大的大中型箱体类和轴类零件(近年研制的组合机床加工连杆、板件等也占一定份额),完成钻孔、扩孔、铰孔,加工各种螺纹、镗孔、车端面和凸台,在孔内镗各种形状槽,以及铣削平面和成形面等[5]。
随着技术的不断进步,一种新型的组合机床——柔性组合机床越来越受到人们的青睐,它应用多位主轴箱、可换主轴箱、编码随行夹具和刀具的自动更换,配以可编程序控制器(PLC)、数字控制(NC)等,能任意改变工作循环控制和驱动系统,并能灵活适应多品种加工的可调可变的组合机床。
另外,近年来组合机床加工中心、数控组合机床、机床辅机(清洗机、装配机、综合测量机、试验机、输送线)等在组合机床行业中所占份额也越来越大。
由于组合机床及其自动线是一种技术综合性很高的高技术专用产品,是根据用户特殊要求而设计的,它涉及到加工工艺、刀具、测量、控制、诊断监控、清洗、装配和试漏等技术。
我国组合机床及组合机床自动线总体技术水平比发达国家要相对落后,国内所需的一些高水平组合机床及自动线几乎都从国外进口。
工艺装备的大量进口势必导致投资规模的扩大,并使产品生产成本提高。
因此,市场要求我们不断开发新技术、新工艺,研制新产品,由过去的“刚性”机床结构,向“柔性”化方向发展,满足用户需求,真正成为刚柔兼备的自动化装备[16]。
钻、镗两用组合机床液压系统的设计(二)毕业设计

钻、镗两用组合机床液压系统的设计(二)毕业设计
2.液压系统组成
液压系统主要由以下组成部分构成:液压泵、液压缸、液压阀、压力表等。
在这些部
件中,液压泵是液压系统的重要原件,其主要作用是将机床所需的液体压力转换为动能,
供液压系统的其他部件使用。
液压缸是液压系统中的执行部件,其主要功能是根据系统的
压力变化,控制机床设备的运动、位置、速度等参数。
液压阀则是液压系统中的控制部件,其主要用途是根据操作员的指令,调节系统的压力、流量等参数,以控制液压缸的运动状态。
3.液压系统设计原则
设计一个合理稳定的液压系统,需要遵循以下原则:
(1)在设计过程中,需根据机床的工艺特点,合理选择液压泵、液压缸等液压装置的型号、规格。
(2)在进行设计时,需要对液压管路的长度、直径、弯曲处的变形程度等进行考虑,以确保系统的流通性与稳定性。
(3)需要根据液压系统的工作压力与流量,确定合适的液压阀的类型、规格、数量。
(4)在液压系统设计后,需要进行系统试验,以检验其稳定性、运行正常性、各部件的适用性等。
5.结论
本文通过对钻、镗两用组合机床液压系统的设计研究,得出了一系列液压系统方案和
设计原则。
在液压系统方案选择过程中,应结合机床的工艺特点、液压泵的选型、液压管
路的布置、液压阀的安装、液压油的使用等因素,并严格遵循相关液压系统设计标准,以
确保长期稳定、可靠的机床工作状态。
二轴钻孔机床液压系统设计_毕业设计 推荐
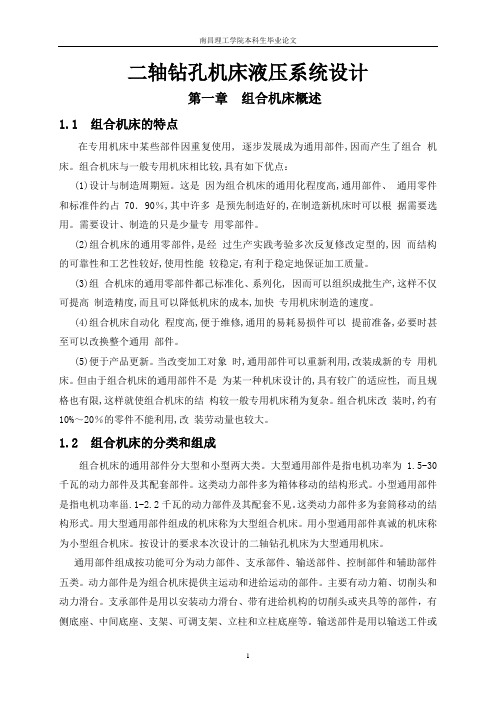
二轴钻孔机床液压系统设计第一章组合机床概述1.1 组合机床的特点在专用机床中某些部件因重复使用, 逐步发展成为通用部件,因而产生了组合机床。
组合机床与一般专用机床相比较,具有如下优点:(1)设计与制造周期短。
这是因为组合机床的通用化程度高,通用部件、通用零件和标准件约占70.90%,其中许多是预先制造好的,在制造新机床时可以根据需要选用。
需要设计、制造的只是少量专用零部件。
(2)组合机床的通用零部件,是经过生产实践考验多次反复修改定型的,因而结构的可靠性和工艺性较好,使用性能较稳定,有利于稳定地保证加工质量。
(3)组合机床的通用零部件都己标准化、系列化, 因而可以组织成批生产,这样不仅可提高制造精度,而且可以降低机床的成本,加快专用机床制造的速度。
(4)组合机床自动化程度高,便于维修,通用的易耗易损件可以提前准备,必要时甚至可以改换整个通用部件。
(5)便于产品更新。
当改变加工对象时,通用部件可以重新利用,改装成新的专用机床。
但由于组合机床的通用部件不是为某一种机床设计的,具有较广的适应性, 而且规格也有限,这样就使组合机床的结构较一般专用机床稍为复杂。
组合机床改装时,约有10%~20%的零件不能利用,改装劳动量也较大。
1.2 组合机床的分类和组成组合机床的通用部件分大型和小型两大类。
大型通用部件是指电机功率为 1.5-30千瓦的动力部件及其配套部件。
这类动力部件多为箱体移动的结构形式。
小型通用部件是指电机功率甾.1-2.2千瓦的动力部件及其配套不见。
这类动力部件多为套筒移动的结构形式。
用大型通用部件组成的机床称为大型组合机床。
用小型通用部件真诚的机床称为小型组合机床。
按设计的要求本次设计的二轴钻孔机床为大型通用机床。
通用部件组成按功能可分为动力部件、支承部件、输送部件、控制部件和辅助部件五类。
动力部件是为组合机床提供主运动和进给运动的部件。
主要有动力箱、切削头和动力滑台。
支承部件是用以安装动力滑台、带有进给机构的切削头或夹具等的部件,有侧底座、中间底座、支架、可调支架、立柱和立柱底座等。
双面钻通卧式组合机床液压系统设计毕业设计

沈阳理工大学毕业设计(论文)题目:双面钻通卧式组合机床液压系统设计学院:机械与运载学院专业班级: 11焊接1班学生姓名:张顺指导教师:王强完成日期: 2013年7月12日毕业设计(论文)任务书毕业设计(论文)题目:双面钻通卧式组合机床液压系统设计。
主要内容:1.液压系统工况图分析。
2.液压系统原理图。
3.液压系统计算与选液压元件。
4.验算液压系统。
5.绘工作图和遍技术文件。
主要技术参数:工作循环:工件夹紧→左、右动力部件快进→左、右动力部件工进→左动力部件快退,右动力部件继续工进→左动力部件停止,右动力部件快退→左右动力部件皆停止,工件松开。
工件夹紧力为30000牛,两侧加工切削负载皆为15000牛,动力部件的重量皆为9.8×103牛,快进、快退速度为6m/min,快进行程为100mm。
工进速度为(20—1000)mm/min,左动力部件工进行程为50mm,右动力部件工进行程为80mm。
往复运动的加速、减速时间为0.2s,滑台为平导轨,静、动摩擦系数分别为0.2和0.1。
指导教师:院长签字:年月日双面钻通卧式组合机床液压系统设计论文作者:张顺指导教师:王强目录摘要 (2)外文摘要 (3)引言 (5)⒈液压系统的设计与计算 (6)1.1负载分析 (6)1.2件主要参数的确定 (8)1.3系统原理图 (9)1.4压元件 (14)1.5验算液压系统的性能 (18)⒉集成块的设计 (22)2.1底座设计 (22)2.2下块设计 (22)2.3上块设计 (22)2.4油孔直径的确定 (22)2.5油孔间最小间隙的确定 (23)结论 (24)致谢 (25)参考文献 (26)摘要对于设计双面钻通卧式组合机床的液压系统来说,基本任务是使该系统能够高效、稳定、快捷的完成孔加工问题。
我主要设了适合本机床工作循环和性能的液压系统,合理选用液压阀并设计安装了管接头的集成块。
首先对负载进行分析,确定执行元件(液压缸)的主要技术参数,再算出液压缸各工作阶段的工作压力、流量和功率。
- 1、下载文档前请自行甄别文档内容的完整性,平台不提供额外的编辑、内容补充、找答案等附加服务。
- 2、"仅部分预览"的文档,不可在线预览部分如存在完整性等问题,可反馈申请退款(可完整预览的文档不适用该条件!)。
- 3、如文档侵犯您的权益,请联系客服反馈,我们会尽快为您处理(人工客服工作时间:9:00-18:30)。
学号:毕业设计说明书设计题目:两工位钻孔、攻丝组合机床液压控制系统的设计系部机械电子系专业机电一体化班级机电102班姓名指导教师2012年10月17日摘要本课题主要研究的是用PLC控制的两工位钻孔攻丝组合机床的运作。
两工位钻孔攻丝组合机床经系统通电后能自动完成工件的钻孔和攻丝加工,此机床主要由床身、移动工作台、夹具、钻孔滑台、钻孔动力头、攻丝滑台、攻丝动力头、滑台移动控制凸轮和液压系统组成。
工作台的移动包括左移、右移及夹具的动作包括加紧和放松,钻孔滑台的移动包括前移和后移,均由液压系统执行,其中钻孔滑台和攻丝滑台的移动是通过控制凸轮来控制滑台移动液压系统的液压阀实现的,电气系统不参与。
只需启动控制凸轮点击即可,但要注意凸轮转动的周期。
该系统由PLC的控制,工作台和滑台的移动将严格的按规定的时序同步进行,使两种运动密切配合,提高实际生产的工作效率。
关键词组合机床 PLC控制程序编程调试AbstractThe main research of this paper is to use PLC to control the two position drilling combined machine tool operation. Two position drilling combined machine tool the system power can automatically complete the drilling and tapping machine, which is mainly composed of a bed body, movable bench, fixture, drilling, drilling, tapping power head slider slider, tapping power head, slider mobile control cams and hydraulic system. Work bench mobile includes shift left, right and jig moves include a stepped up and relax, drilling the movement of the sliding platform includes forward and backward, implementation by the hydraulic system, wherein the drilling platform and tapping the movement of the sliding platform is controlled by a cam to control a slider mobile hydraulic system hydraulic valve, electrical system does not participate in. Just start the control cam click, but attention should be paid to the cam rotation cycle. The system consists of a PLC control, work station and the movement of the sliding platform will be strictly in accordance with the provisions of the timing synchronization, the two movement closely, improve production efficiency.Key words combination machine tool control procedures PLC programming debugging目录摘要...............................................................................................................错误!未定义书签。
Abstract.......................................................................................................... ..I前言 (1)正文1 组合机床设计简介1.1 组合机床加工方式 (2)1.2 组合机床的发展 (2)1.3 组合机床部件分类 (2)1.4 组合机床的发展 (3)1.5 在中小批量生产组合机床是如何应用 (3)2可编程控制器的概述2.1 可编程控制器的由来 (4)2.2 可编程控制器的特点 (5)2.3 可编程控制器的应用领域 (6)2.4 可编程控制器的发展趋势 (6)2.5 PLC的结构 (7)2.6 PLC的基本技术特征 (9)3两工位钻孔攻丝组合机床的设计3.1 两工位钻孔攻丝组合机床示意图 (10)3.2 两工位钻孔攻丝组合机床的控制要求 (11)3.3 动力滑台液压系统的工作原理 (13)3.4 液压缸参数的计算 (14)3.5 各液压缸工作循环时的工作参数表 (16)3.6 液压系统的发热和温升验算 (18)3.7 组合机床控制系统设计 (18)3.8 硬件接线图设计 (19)3.9 软件系统设计 (19)4系统的调试4.1 FXGP/WIN软件应用 (21)4.2 上机调试步骤 (22)5 小结 (23)致谢 (24)参考文献 (25)河南化工职业学院毕业设计说明书前言组合机床 transfer and unit machine 组合机床是以通用部件为基础配以按工件特定形状和加工工艺设计的专用部件和夹具组成的半自动或自动专用机床。
二十世纪 70 年代以来随着可转位刀具、密齿铣刀、镗孔尺寸自动检测和刀具自动补偿技术的发展组合机床的加工精度也有所提高。
铣削平面的平面度可达0.05毫米1000毫米表面粗糙度可低达0.63微米镗孔精度可达IT76级孔距精度可达0.02微米。
专用机床是随着汽车工业的兴起而发展起来的。
在专用机床中某些部件因重复使用逐步发展成为通用部件因而产生了组合机床。
最早的组合机床是1911年在美国制成的用于加工汽车零件。
初期各机床制造厂都有各自的通用部件标准。
为了提高不同制造厂的通用部件的互换性,便于用户使用和维修1953年美国福特汽车公司和通用汽车公司与美国机床制造厂协商确定了组合机床通用部件标准化的原则即严格规定各部件间的联系尺寸,但对部件结构未作规定。
组合机床是以通用部件为基础配以按工件特定外形和加工工艺设计的专用部件和夹具组成的半自动或自动专用机床。
它一般采用多轴、多刀、多工序、多面或多工位同时加工的方式生产效率比通用机床高几倍至几十倍。
由于通用部件已经标准化和系列化可根据需要灵活配置能缩短设计和制造周期。
因此组合机床兼有低成本和高效率的优点在大批、大量生产中得到广泛应用并可用以组成自动生产线。
组合机床一般用于加工箱体类或非凡外形的零件。
加工时工件一般不旋转由刀具的旋转运动和刀具与工件的相对进给运动来实现钻孔、扩孔、锪孔、铰孔、镗孔、铣削平面、切削内外螺纹以及加工外圆和端面等。
有的组合机床采用车削头夹持工件使之旋转由刀具作进给运动也可实现某些回转体类零件 ( 如飞轮、汽车后桥半轴等)的外圆和端面加工。
专用机床是随着汽车工业的兴起而发展起来的。
在专用机床中某些部件因重复使用逐步发展成为通用部件因而产生了组合机床。
河南化工职业学院毕业设计说明书第一章组合机床设计简介组合机床(transfer and unit machine)组合机床是以通用部件为基础,配以按工件特定形状和加工工艺设计的专用部件和夹具,组成的半自动或自动专用机床。
1.1 组合机床加工方式组合机床一般采用多轴、多刀、多工序、多面或多工位同时加工的方式,生产效率比通用机床高几倍至几十倍。
由于通用部件已经标准化和系列化,可根据需要灵活配置,能缩短设计和制造周期。
因此,组合机床兼有低成本和高效率的优点,在大批、大量生产中得到广泛应用,并可用以组成自动生产线。
组合机床一般用于加工箱体类或特殊形状的零件。
加工时,工件一般不旋转,由刀具的旋转运动和刀具与工件的相对进给运动,来实现钻孔、扩孔、锪孔、铰孔、镗孔、铣削平面、切削内外螺纹以及加工外圆和端面等。
有的组合机床采用车削头夹持工件使之旋转,由刀具作进给运动,也可实现某些回转体类零件(如飞轮、汽车后桥半轴等)的外圆和端面加工。
1.2 组合机床的发展史二十世纪70年代以来,随着可转位刀具、密齿铣刀、镗孔尺寸自动检测和刀具自动补偿技术的发展,组合机床的加工精度也有所提高。
铣削平面的平面度可达0.05毫米/1000毫米,表面粗糙度可低达2.5~0.63微米;镗孔精度可达IT7~6级,孔距精度可达O.03~O.02微米。
专用机床是随着汽车工业的兴起而发展起来的。
在专用机床中某些部件因重复使用,逐步发展成为通用部件,因而产生了组合机床。
最早的组合机床是1911年在美国制成的,用于加工汽车零件。
初期,各机床制造厂都有各自的通用部件标准。
为了提高不同制造厂的通用部件的互换性,便于用户使用和维修,1953年美国福特汽车公司和通用汽车公司与美国机床制造厂协商,确定了组合机床通用部件标准化的原则,即严格规定各部件间的联系尺寸,但对部件结构未作规定。
河南化工职业学院毕业设计说明书通用部件按功能可分为动力部件、支承部件、输送部件、控制部件和辅助部件五类。
动力部件是为组合机床提供主运动和进给运动的部件。
主要有动力箱、切削头和动力滑台。
支承部件是用以安装动力滑台、带有进给机构的切削头或夹具等的部件,有侧底座、中间底座、支架、可调支架、立柱和立柱底座等。
输送部件是用以输送工件或主轴箱至加工工位的部件,主要有分度回转工作台、环形分度回转工作台、分度鼓轮和往复移动工作台等。
控制部件是用以控制机床的自动工作循环的部件,有液压站、电气柜和操纵台等。
辅助部件有润滑装置、冷却装置和排屑装置等。
1.4 组合机床的发展为了使组合机床能在中小批量生产中得到应用,往往需要应用成组技术,把结构和工艺相似的零件集中在一台组合机床上加工,以提高机床的利用率。
这类机床常见的有两种,可换主轴箱式组合机床和转塔式组合机床。
组合机床未来的发展将更多的采用调速电动机和滚珠丝杠等传动,以简化结构、缩短生产节拍;采用数字控制系统和主轴箱、夹具自动更换系统,以提高工艺可调性;以及纳入柔性制造系统等。