浮法玻璃熔窑热耗计算
玻璃熔窑烟道热工计算

玻璃熔窑烟道热工计算张凯赵亮(秦皇岛玻璃工业研究设计院有限公司秦皇岛066001)摘要以1000询平板玻璃熔窑为例,提岀了运用”水力最优断面”的概念来计算烟道断面尺寸的方法,并给岀了计算步骤;计算了烟道阻力;并对烟道采用不同保温层情况下的隔热性和经济性两方面进行了比较计算。
关键词玻璃熔窑;烟道断面;烟道阻力;保温层中图分类号:TQ171文献标识码:A文章编号:1003-1987(2021)06-0022-06Thermal Calculation of Flue in the Glass Melting FurnaceZHANG Kai,ZHAO Liang(Qinhuangdao Glass Industry Research and Design Institute Company Limited,Qinhuangdao066001,China)Abstract:Taking a1000t/d flat glass furnace as an example,puts forward a method to calculate the section size of the flue by using the concept of“hydraulic optimal section”,gives the calculation steps;calculates the resistance of the flue;and compares the heat insulation and economy of the flue with different insulation layers. Key Words:glass furnace,the cross section size of flue,flue resistance,insulation layer0引言当今,节约能源和环境保护依然是玻璃行业乃至整个工业领域重点关注的两大课题,玻璃熔窑生产过程中产生的高温烟气经过蓄热室格子体的回收后,在进入烟道时依然有较高的温度,对于大型熔窑来说,进入烟道内的烟气温度可以达到550甚至更高,最大限度地利用此部分烟气的余热正日益引起人们的重视。
窑体散热的相关热工公式
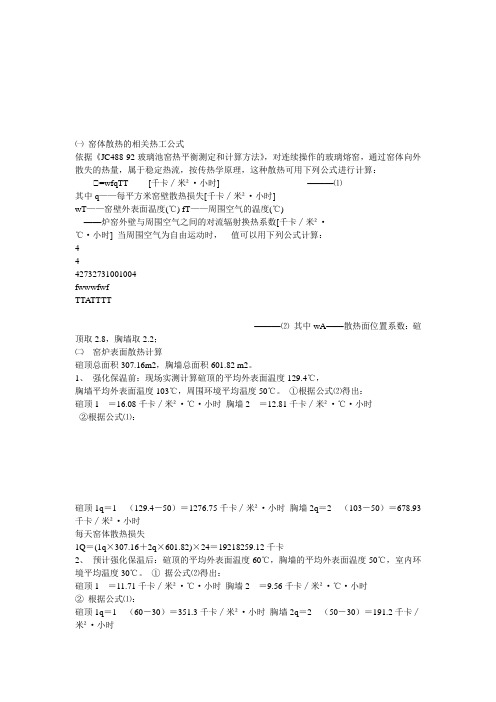
㈠窑体散热的相关热工公式依据《JC488-92玻璃池窑热平衡测定和计算方法》,对连续操作的玻璃熔窑,通过窑体向外散失的热量,属于稳定热流,按传热学原理,这种散热可用下列公式进行计算: =wfqTT [千卡∕米²·小时] ———⑴其中q——每平方米窑壁散热损失[千卡∕米²·小时]wT——窑壁外表面温度(℃) fT——周围空气的温度(℃)——炉窑外壁与周围空气之间的对流辐射换热系数[千卡∕米²·℃·小时] 当周围空气为自由运动时,值可以用下列公式计算:4442732731001004fwwwfwfTTATTTT———⑵其中wA——散热面位置系数:碹顶取2.8,胸墙取2.2;㈡窑炉表面散热计算碹顶总面积307.16m2,胸墙总面积601.82 m2。
1、强化保温前:现场实测计算碹顶的平均外表面温度129.4℃,胸墙平均外表面温度103℃,周围环境平均温度50℃。
①根据公式⑵得出:碹顶1=16.08千卡∕米²·℃·小时胸墙2=12.81千卡∕米²·℃·小时②根据公式⑴:碹顶1q=1(129.4-50)=1276.75千卡∕米²·小时胸墙2q=2(103-50)=678.93千卡∕米²·小时每天窑体散热损失1Q=(1q×307.16+2q×601.82)×24=19218259.12千卡2、预计强化保温后:碹顶的平均外表面温度60℃,胸墙的平均外表面温度50℃,室内环境平均温度30℃。
①据公式⑵得出:碹顶1=11.71千卡∕米²·℃·小时胸墙2=9.56千卡∕米²·℃·小时②根据公式⑴:碹顶1q=1(60-30)=351.3千卡∕米²·小时胸墙2q=2(50-30)=191.2千卡∕米²·小时每天窑体散热损失2Q=(1q×307.16+2q×601.82)×24=5351359千卡㈢保温节能量及价值估算①保温前每天窑体散热损失合标准煤(7000000千卡/吨) 2.745吨,全年(按365天)损失约1001.925吨标煤。
玻璃熔窑使用不同燃料的能耗计算

玻璃熔窑使用不同燃料的能耗计算维普资讯 ////0>.全国性建材科技期刊??《玻璃》第期总第期玻璃熔窑使用不同燃料的能耗计算唐福恒秦皇岛玻璃工业研究设计院秦皇岛市摘要国内浮法玻璃熔窑多数是以重油为燃料的,少数以天然气、焦炉煤气、发生炉热煤气为燃料。
每种燃料的热值不同,对应的理论燃烧温度、实际燃烧温度、能够达到的炉壁热点温度也都不相同。
从而各种燃料玻璃熔窑的单位能耗指标、熔窑热效率也不同。
本文给?了使用不同燃料的玻璃熔窑计算单位能耗指标的经验公式。
关键词浮法玻璃熔窑燃料中图分类号: 文献标识码: 文章编号: ?? ?一玻璃工厂是耗能大户,玻璃熔窑又是玻璃生产不同空气过剩系数时的单位空气耗量,线中耗能最大的热工设备,生产优质浮法玻璃时,/ 。
熔窑内热点的温度需要达到以上。
国内外传要计算某种燃料的理论燃烧温度,只要把上式统的玻璃熔窑一般都采用重油热值≥中右侧分子和分母的全部代号的数据都通过查表找/、天然气热值≥ / ’等高热值的、或通过计算得出,这种燃料的理论燃烧温度就燃料,少数是以焦炉煤气、发生炉热煤气为燃料。
很容易计算出来了。
. 燃料的实际燃烧温度火焰温度燃料的理论燃烧温度、实际燃烧温度和燃料在燃烧中实际上总有一部分热量损失掉,玻璃熔窑内壁温度并凡燃烧也经常不能完全,所以实际的燃烧温度总是以矿物燃料为能源的玻璃熔窑内的温度取决于低于理论燃烧温度。
通常人们所说的某种燃料的“火燃料的燃烧温度,燃料的燃烧温度分为理论燃烧温焰温度”就是指这种燃料能够达到的实际燃烧温度。
度和实际燃烧温度。
各种窑炉可以达到的最高实际燃烧温度即火. 燃料的理论燃烧温度焰温度 ,可从表所列的各种窑炉高温系数又当燃料在燃烧反应时所放出的全部热量都用于称为燃烧热效率求得。
加热燃烧产物时,能够达到的温度称为燃料的理论表各种窑炉的高温系数燃烧温度。
窑炉名称高温系数窑炉名称高温系数燃料的理论燃烧温度是从能量守衡定律得出的。
连续式玻璃窑 . ~ . 隧道窑 . ? .坩埚窑 . ~ . 窑 . ? .公式为:间隙式作业窑~ 旋窑 . ? .目前的大型玻璃熔窑都属于连续式的,计算实际燃烧温度时的高温系数可按 . 取。
浮法玻璃熔窑热耗计算
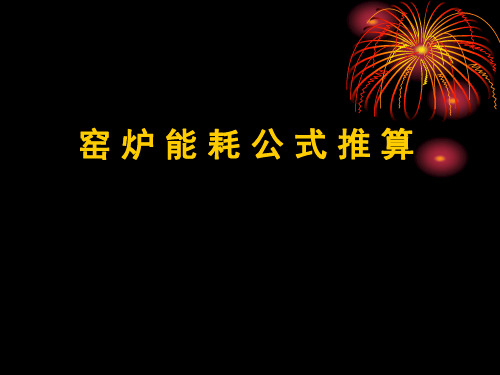
思考题:
• 1、无拉引量时,窑炉应如何设定各小 炉燃料分配? • 2、依热耗表达式,怎样采取有效措施, 提高窑炉热效率?
窑炉单耗表达式
窑炉单耗,Kcal/Kg Glass =(耗热当量/周拉引量+28.0)* 25.2*[1+(20% - 碎玻璃占全部 玻璃的比例)*1/2]
推算耗热当量(无功系数)
表达式说明 常数:28,单位:Therm
(英制热量,1 Therm=25.2 kcal)
钠钙平板玻璃形成耗热:705 kcal/kg,合28 therm *与成份、碎玻璃量、澄清温度相 关
推算公式资料
1. 2010年12月各线窑炉玻璃单耗
(NG C.V.=8400 Kcal/NM3) 一线:186.31NM3/MT = 1565 Kcal/kg glass 二线:188.22NM3/MT = 1581 Kcal/kg glass 三线:162.40NM3/MT = 1364 Kcal/kg glass
cullet每增加或减少2相当于load拉引量降低或升高1推算耗热当量无功系数推算步骤窑龄增加量周拉引量耗能当量实指窑炉窑体散热玻璃回流重复加热出蓄热室烟气稀释风冷却水带走热量系数
窑炉能耗公式推算
目的
• 合理利用燃料之热能,并使其与 窑炉负载(拉引量)相匹配。
• 使炉内热工过程、参数得到有效 控制。 • 针对特殊工况,合理燃料分配。 • 节约能源,降低生产成本。 • 减少环境污染。
*二线热耗计算: • =(159687/Load + 28)*25.2*(1+(20%-Cullet ratio%)/2)
*三线热耗计算: • =(186476/Load + 28)*25.2*(1+(20%-Cullet ratio%)/2)
浮法玻璃耗能计算公式
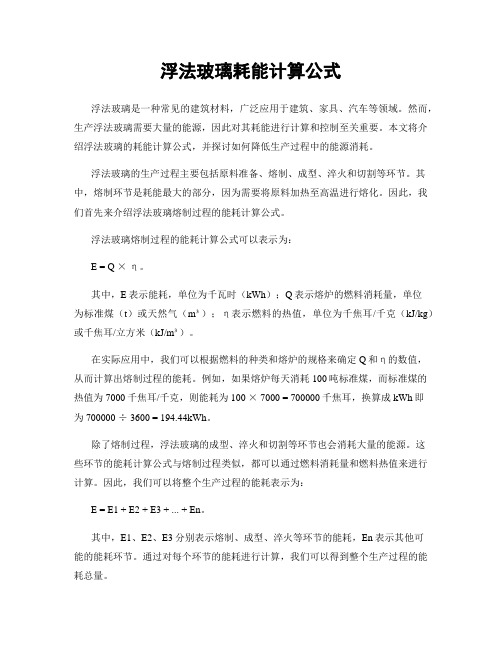
浮法玻璃耗能计算公式浮法玻璃是一种常见的建筑材料,广泛应用于建筑、家具、汽车等领域。
然而,生产浮法玻璃需要大量的能源,因此对其耗能进行计算和控制至关重要。
本文将介绍浮法玻璃的耗能计算公式,并探讨如何降低生产过程中的能源消耗。
浮法玻璃的生产过程主要包括原料准备、熔制、成型、淬火和切割等环节。
其中,熔制环节是耗能最大的部分,因为需要将原料加热至高温进行熔化。
因此,我们首先来介绍浮法玻璃熔制过程的能耗计算公式。
浮法玻璃熔制过程的能耗计算公式可以表示为:E = Q ×η。
其中,E表示能耗,单位为千瓦时(kWh);Q表示熔炉的燃料消耗量,单位为标准煤(t)或天然气(m³);η表示燃料的热值,单位为千焦耳/千克(kJ/kg)或千焦耳/立方米(kJ/m³)。
在实际应用中,我们可以根据燃料的种类和熔炉的规格来确定Q和η的数值,从而计算出熔制过程的能耗。
例如,如果熔炉每天消耗100吨标准煤,而标准煤的热值为7000千焦耳/千克,则能耗为100 × 7000 = 700000千焦耳,换算成kWh即为700000 ÷ 3600 = 194.44kWh。
除了熔制过程,浮法玻璃的成型、淬火和切割等环节也会消耗大量的能源。
这些环节的能耗计算公式与熔制过程类似,都可以通过燃料消耗量和燃料热值来进行计算。
因此,我们可以将整个生产过程的能耗表示为:E = E1 + E2 + E3 + ... + En。
其中,E1、E2、E3分别表示熔制、成型、淬火等环节的能耗,En表示其他可能的能耗环节。
通过对每个环节的能耗进行计算,我们可以得到整个生产过程的能耗总量。
在实际生产中,降低浮法玻璃的能耗是一个重要的课题。
为了降低能耗,我们可以从以下几个方面进行改进:1. 提高设备效率,更新熔炉、成型机等设备,提高其能效,减少能源的浪费。
2. 优化生产工艺,通过优化原料配比、控制熔炉温度等手段,降低生产过程中的能耗。
浮法玻璃炉窑蓄热室格子体设计

神雾500t/d浮法玻璃炉窑蓄热室格子体设计(一)一、基本参数及蓄热室结构1.基本参数:●生产能力:P=500t / d;●燃料:热值为Q=1400kcal / Nm3的发生炉煤气;●单耗:r=1600 kcal / kg;●空气过剩系数:α=1.1;●换向周期:f=20分钟;●高温段格孔尺寸:150×150mm。
2.蓄热室结构高低温两段格子体结构,煤气和助燃空气独立预热。
流过格子体的烟气、助燃空气和煤气温度变化情况如下图所示:二、高温段蓄热室热平衡计算(一)高温段蓄热室气体温度及其热容量(二)全窑基础数据计算1.单位煤气所需理论空气量L0=(0.85Q / 1000)+Δ=(0.85×1400 / 1000)+0.03=1.22(Nm3 / Nm3)2.单位煤气所需实际空气量L a=α·L0=1.1×1.22=1.342(Nm3 / Nm3)3.全窑单位时间(秒)耗热量R s=(P×1000×r)÷(24×3600)=(500×1000×1600)÷(24×3600)=9260(kcal/ s)4.单位时间(秒)煤气消耗量MQ=R s / Q=9260 / 1400=6.614(Nm3 / s)5.单位时间(秒)实际助燃空气消耗量KQ a=L a·MQ=1.342×6.614=8.876(Nm3 / s)6.单位时间(秒)产生的烟气量YQ=[L a +0.98-(0.13×Q/1000)]·MQ=[1.342 +0.98-(0.13×1400/1000)]×6.614=14.154(Nm3 / s)(三)空气蓄热室与煤气蓄热室的烟气分配1.单位时间(秒)空气预热所需热量Q KQ=KQ a·(C KQ1350·1350℃-C KQ500·500℃)=8.876×(0.355×1350-0.326×500)=8.876×(479.25-163)=2807(kcal / s)2.单位时间(秒)煤气预热所需热量Q MQ=MQ·(C MQ1350·1350℃-C MQ500·500℃)=6.614×(0.361×1350-0.330×500)=6.614×(487.35-165)=2132(kcal / s)3.单位时间(秒)空气、煤气预热所需热量之和Q q=Q KQ+Q MQ=2807+2132=4939(kcal / s)4.单位时间(秒)空气蓄热室所需要的烟气量Y KQ=Q KQ / Q q·YQ=2807/4939×14.154=8.044(Nm3 / s)――――――――――――――――――――57%5.单位时间(秒)煤气蓄热室所需要的烟气量Y MQ=Q MQ / Q q·YQ=2132/4939×14.154=6.110(Nm3 / s)――――――――――――――――――――43%(四)高温段空气蓄热室热平衡1.单位时间(秒)烟气带入热量Q J1=Y KQ·C YQ1450·t YJ=8.044×0.391×1450=4560(kcal / s)――――――――――――――――――――100%2.单位时间(秒)烟气带出热量Q C1=Y KQ·C YQ600·t YC=8.044×0.358×600=1728(kcal / s)――――――――――――――――――――37.89%3.单位时间(秒)空气预热所需热量Q KQ=2807(kcal / s)――――――――――――――――――61.56%4.单位时间(秒)空气蓄热室结构散热Q KQSR=Q J1-Q C1-Q KQ=4560-1728-2807=25(kcal / s)――――――――――――――――――――0.55%(五)高温段煤气蓄热室热平衡1.单位时间(秒)烟气带入热量Q J2=Y MQ·C YQ1450·t YJ=6.110×0.391×1450=3464(kcal / s)――――――――――――――――――――100%2.单位时间(秒)烟气带出热量Q C2=Y MQ·C YQ600·t YC=6.110×0.358×600=1312(kcal / s)――――――――――――――――――――37.87%3.单位时间(秒)煤气预热所需热量Q MQ=2132(kcal / s)――――――――――――――――――61.55%4.单位时间(秒)煤气蓄热室结构散热Q MQSR=Q J2-Q C2-Q MQ=3464-1312-2132=20(kcal / s)――――――――――――――――――――0.58%(六)整个高温段蓄热室热平衡1.单位时间(秒)烟气带入总热量Q J=Q J1+Q J2=4560+3464=8024(kcal / s)――――――――――――――――――――100%2.单位时间(秒)烟气带出总热量Q C=Q C1+Q C2=1728+1312=3040(kcal / s)――――――――――――――――――――37.89%3.单位时间(秒)空气、煤气预热所需总热量Q q=Q KQ+Q MQ=2807+2132=4939(kcal / s)――――――――――――――――――――61.55%4.单位时间(秒)空气、煤气蓄热室结构总散热Q ZSR=Q KQSR+Q MQSR=25+20=45(kcal / s)――――――――――――――――――――0.56%三、低温段蓄热室热平衡计算(一)低温段蓄热室气体温度及其热容量(二)低温段空气蓄热室热平衡1.单位时间(秒)烟气带入热量Q J1=Y KQ·C YQ600·t YJ=8.044×0.358×600=1728(kcal / s)――――――――――――――――――――100%2.单位时间(秒)烟气带出热量Q C1=Y KQ·C YQ200·t YC=8.044×0.337×150=407(kcal / s)――――――――――――――――――――23.55%3.单位时间(秒)空气预热所需热量Q KQ=KQ a·(C KQ500·500℃-C KQ50·50℃)=8.876×(0.326×500-0.316×50)=8.876×(163-15.8)=1306(kcal / s)――――――――――――――――――75.58%4.单位时间(秒)空气蓄热室结构散热Q KQSR=Q J1-Q C1-Q KQ=1728-407-1306=15(kcal / s)――――――――――――――――――――0.87%(三)低温段煤气蓄热室热平衡1.单位时间(秒)烟气带入热量Q J2=Y MQ·C YQ600·t YJ=6.110×0.358×600=1312(kcal / s)――――――――――――――――――――100%2.单位时间(秒)烟气带出热量Q C2=Y MQ·C YQ150·t YC=6.110×0.337×150=309(kcal / s)――――――――――――――――――――23.55%3.单位时间(秒)煤气预热所需热量Q MQ=MQ·(C MQ500·500℃-C MQ50·50℃)=6.614×(0.330×500-0.317×50)=6.614×(165-15.85)=986(kcal / s)――――――――――――――――――――75.15%4.单位时间(秒)煤气蓄热室结构散热Q MQSR=Q J2-Q C2-Q MQ=1312-309-986=17(kcal / s)――――――――――――――――――――1.30%(四)整个低温段蓄热室热平衡1.单位时间(秒)烟气带入总热量Q J=Q J1+Q J2=1728+1312=3040(kcal / s)――――――――――――――――――――100%2.单位时间(秒)烟气带出总热量Q C=Q C1+Q C2=407+309=716(kcal / s)――――――――――――――――――――23.55%3.单位时间(秒)空气、煤气预热所需总热量Q q=Q KQ+Q MQ=1306+986=2292(kcal / s)――――――――――――――――――――75.39%4.单位时间(秒)空气、煤气蓄热室结构总散热Q ZSR=Q KQSR+Q MQSR=15+17=32(kcal / s)――――――――――――――――――――1.06%四、全窑蓄热室热平衡1.单位时间(秒)烟气带入总热量Q J=8024(kcal / s)――――――――――――――――――――100%2.单位时间(秒)烟气带出总热量Q C=716(kcal / s)――――――――――――――――――――8.92%3.单位时间(秒)空气、煤气预热所需总热量Q q=4939+2292=7231(kcal / s)―――――――――――――90.12%4.单位时间(秒)空气、煤气蓄热室结构总散热Q ZSR=45+32=77(kcal / s)―――――――――――――――0.96%五、高温段蓄热室格子体设计(一)高温段空气蓄热室格子体1.采用以碱性砖为主的筒型砖格子体,格子体参数如下:(1)格孔尺寸:d g=150mm×150mm(2)筒型砖格子体壁厚:δ=30mm(3)格孔当量直径:d e=156mm(4)格孔断面积:A d=0.022m2(5)格子体单位体积换热面积(平均值)/比表面积:A gk=17.4m2 / m3(6)格子体单位体积砖体积:V gk=0.32m3 / m3(7)单位助燃空气单位时间(秒)所需要的格子体换热面积:A kk=800m2 / Nm3·s 2.助燃空气耗量:KQ a=8.876Nm3 / s3.每侧所需要的格子体换热面积:A g=KQ a·A kk=8.876×800=7101m24.每侧所需要的格子体体积:V g=A g/A gk=7101÷17.4=408m35.初步设格子体高度、长度尺寸:H=8m,L=18m6.求得格子体宽度:B=V g/(H·L)=408 /(8×18)=2.83(m)7.蓄热室每侧腔道数(小炉数):n=78.腔道纵向尺寸:小炉中心线间距-分隔墙厚=3.1-0.462=2.638(m)9.蓄热室纵向腔道总长:2.638m×7=18.466m10.腔道纵向格孔数:n1=1411.腔道横向格孔数:n2=1612.每侧腔道格孔总流通面积:0.022×14×16×7=34.5m213.格子体中空气标态流速:8.876÷34.5=0.257Nm / s14.格子体中烟气标态流速:8.044÷34.5=0.233Nm / s15.单侧蓄热室格子体总体积为:V t=[n1×(0.15+δ)]×[16×7×(0.15+δ)]×H=(14×0.18)×(16×7×0.18)×8=406.42m316.单侧蓄热室格子体总换热面积为:A=V t·A gk=406.42×17.4=7072(m2)17.单侧蓄热室格子体格子砖的总体积为:V=V t·V gk=406.42×0.32=130.05m3G gz=130.05×2.8=364.15t(二)高温段煤气蓄热室格子体1.采用以碱性砖为主的筒型砖格子体,格子体参数如下:(1)格孔尺寸:d g=150mm×150mm(2)筒型砖格子体壁厚:δ=30mm(3)格孔当量直径:d e=156mm(4)格孔断面积:A d=0.022m2(5)格子体单位体积换热面积(平均值)/比表面积:A gk=17.4m2 / m3(6)格子体单位体积砖体积:V gk=0.32m3 / m3(7)单位煤气单位时间(秒)所需要的格子体换热面积:A kk=800m2 / Nm3·s 2.煤气耗量:MQ=6.614Nm3 / s3.每侧所需要的格子体换热面积:A g=MQ·A kk=6.614×800=5291m24.每侧所需要的格子体体积:V g=A g/A gk=5291÷17.4=304m35.初步设格子体高度、长度尺寸:H=6m,L=18m6.求得格子体宽度:B=V g/(H·L)=304 /(6×18)=2.81(m)7.蓄热室每侧腔道数(小炉数):n=78.腔道纵向尺寸:小炉中心线间距-分隔墙厚=3.1-0.462=2.638(m)9.蓄热室纵向腔道总长:2.638m×7=18.466m10.腔道纵向格孔数:n1=1411.腔道横向格孔数:n2=1412.每侧腔道格孔总流通面积:0.022×14×14×7=30.2m213.格子体中煤气标态流速:6.614÷30.2=0.219Nm / s14.格子体中烟气标态流速:6.110÷30.2=0.202Nm / s15.单侧蓄热室格子体总体积为:V t=[n1×(0.15+δ)]×[14×7×(0.15+δ)]×H=(14×0.18)×(14×7×0.18)×6=266.72m316.单侧蓄热室格子体总换热面积为:A=V t·A gk=266.72×17.4=4641(m2)17.单侧蓄热室格子体格子砖的总体积为:V=V t·V gk=266.72×0.32=85.35m3G gz=85.35×3.4=290.19t(三)整个高温段蓄热室格子体数据汇总1.空气蓄热室单侧格子孔数量:14×16×7=15682.煤气蓄热室单侧格子孔数量:14×14×7=13723.单侧空气蓄热室格子体总换热面积:7072(m2)4.单侧煤气蓄热室格子体总换热面积:4641(m2)5.单侧空气蓄热室格子体总体积:406.42m36.单侧煤气蓄热室格子体总体积:266.72 m37.单侧空气蓄热室格子砖的总重量为:364.15t8.单侧煤气蓄热室格子砖的总重量为:290.19t9.全窑高温段蓄热室格子砖总重量:1308.68t六、低温段蓄热室格子体设计(一)低温段空气蓄热室格子体1.采用以碱性砖为主的筒型砖格子体,格子体参数如下:(1)格孔尺寸:d g=150mm×150mm(2)筒型砖格子体壁厚:δ=30mm(3)格孔当量直径:d e=156mm(4)格孔断面积:A d=0.022m2(5)格子体单位体积换热面积(平均值)/比表面积:A gk=770m2 / m3(6)格子体单位体积砖体积:V gk=0.423m3 / m3(7)单位助燃空气单位时间(秒)所需要的格子体换热面积:A kk=416m2 / Nm3·s 2.助燃空气耗量:KQ a=8.876Nm3 / s3.每侧所需要的格子体换热面积:A g=KQ a·A kk=8.876×416=3692m24.每侧所需要的格子体体积:V g=A g/A gk=3692÷770=4.79m35.初步设格子体高度、长度尺寸:H=8m,L=18m6.求得格子体宽度:B=V g/(H·L)=408 /(8×18)=2.83(m)7.蓄热室每侧腔道数(小炉数):n=78.腔道纵向尺寸:小炉中心线间距-分隔墙厚=3.1-0.462=2.638(m)9.蓄热室纵向腔道总长:2.638m×7=18.466m10.腔道纵向格孔数:n1=1411.腔道横向格孔数:n2=1612.每侧腔道格孔总流通面积:0.022×14×16×7=34.5m213.格子体中空气标态流速:8.876÷34.5=0.257Nm / s14.格子体中烟气标态流速:8.044÷34.5=0.233Nm / s15.单侧蓄热室格子体总体积为:V t=[n1×(0.15+δ)]×[16×7×(0.15+δ)]×H=(14×0.18)×(16×7×0.18)×8=406.42m316.单侧蓄热室格子体总换热面积为:A=V t·A gk=406.42×17.4=7072(m2)17.单侧蓄热室格子体格子砖的总体积为:V=V t·V gk=406.42×0.32=130.05m318.单侧蓄热室格子体格子砖的总重量为:G gz=130.05×2.8=364.15t(二)低温段煤气蓄热室格子体1.采用以碱性砖为主的筒型砖格子体,格子体参数如下:(1)格孔尺寸:d g=150mm×150mm(2)筒型砖格子体壁厚:δ=30mm(3)格孔当量直径:d e=156mm(4)格孔断面积:A d=0.022m2(5)格子体单位体积换热面积(平均值)/比表面积:A gk=17.4m2 / m3(6)格子体单位体积砖体积:V gk=0.32m3 / m3(7)单位煤气单位时间(秒)所需要的格子体换热面积:A kk=800m2 / Nm3·s 2.煤气耗量:MQ=6.614Nm3 / s3.每侧所需要的格子体换热面积:A g=MQ·A kk=6.614×800=5291m24.每侧所需要的格子体体积:V g=A g/A gk=5291÷17.4=304m35.初步设格子体高度、长度尺寸:H=6m,L=18m6.求得格子体宽度:B=V g/(H·L)=304 /(6×18)=2.81(m)7.蓄热室每侧腔道数(小炉数):n=78.腔道纵向尺寸:小炉中心线间距-分隔墙厚=3.1-0.462=2.638(m)9.蓄热室纵向腔道总长:2.638m×7=18.466m10.腔道纵向格孔数:n1=1411.腔道横向格孔数:n2=1412.每侧腔道格孔总流通面积:0.022×14×14×7=30.2m213.格子体中煤气标态流速:6.614÷30.2=0.219Nm / s14.格子体中烟气标态流速:6.110÷30.2=0.202Nm / s15.单侧蓄热室格子体总体积为:V t=[n1×(0.15+δ)]×[14×7×(0.15+δ)]×H=(14×0.18)×(14×7×0.18)×6=266.72m316.单侧蓄热室格子体总换热面积为:A=V t·A gk=266.72×17.4=4641(m2)17.单侧蓄热室格子体格子砖的总体积为:V=V t·V gk=266.72×0.32=85.35m318.单侧蓄热室格子体格子砖的总重量为:G gz=85.35×2.8=238.98t(三)整个低温段蓄热室格子体数据汇总1.空气蓄热室单侧格子孔数量:14×16×7=15682.煤气蓄热室单侧格子孔数量:14×14×7=13723.单侧空气蓄热室格子体总换热面积:7072(m2)4.单侧煤气蓄热室格子体总换热面积:4641(m2)5.单侧空气蓄热室格子体总体积:406.42m36.单侧煤气蓄热室格子体总体积:266.72 m37.单侧空气蓄热室格子砖的总重量为:364.15t8.单侧煤气蓄热室格子砖的总重量为:238.98t9.全窑高温段蓄热室格子砖总重量:1202.26t11。
玻璃熔窑设计第四章热工计算

玻璃熔窑设计第四章热工计算IMB standardization office【IMB 5AB- IMBK 08- IMB 2C】第4章总工艺计算耗热量的计算已求得的数据①原料组成见表4-1表4-1原料组成单位:质量分数(%)②碎玻璃用量占配合料的20%。
③配合料(不包含碎玻璃)水分:4%。
④玻璃熔化温度1465℃湿粉料中形成氧化物的数量见表3-2表4-2形成玻璃液的各氧化物的量单位:质量分数(%)湿粉料逸出气体组成见表4-3表4-3逸出气体组成配合料用量的计算碎玻璃量粉料量=2080(4-1)即:碎玻璃量=2080×粉料量即1㎏粉料中需要加入㎏碎玻璃,可以得到玻璃液:%×1+=因此,熔制成为1㎏玻璃液需要粉料量:G粉=1=0.9530G粉=0.251.0493=0.2383熔化成1㎏玻璃液需要的配合料量为:+=生成硅酸盐耗热量(以1㎏湿粉料进行计算,单位kJ/kg)由CaCO3生产CaSiO3时反应耗热量q1:q1==×(++)/100=由MgCO3生成MgSiO3时反应耗热量q2:q2==×++/100=由CaMg(CO3)2生成CaMg(SiO3)2时反应耗热量q3:q3==×(+)/100=由NaCO3生成NaSiO3时耗热量q4:q4==×100=由Na2SO4生成NaSO3时耗热量q5:q5=×100=1㎏湿粉料生成硅酸盐耗热量:q0=q1+q2+q3+q4+q5=++++=(kJ)玻璃形成过程的热量平衡(以生成1㎏玻璃液计,单位是kJ/kg,从0℃算起)①支出热量a.生成硅酸盐耗热量:qⅠ=q0G粉=×=b.形成玻璃耗热量:qⅡ=347G粉(1-气)kJ=347××(1-×)=c.加热玻璃液到1465℃耗热量:qⅢ=C玻t玻C玻=+×10-4t玻=+×10-4×1465=qⅢ=C玻t玻=×1465=d.加热逸出气体到1465℃耗热量:qⅣ=气G粉C气t熔式中V气=粉=熔=1465℃C气=C CO2(CO2%+SO2%)+C H2O H2O% =×(+)%+×%=qⅣ=气G粉C气t熔=××××1645=e.蒸发水分耗热量:qⅤ=2491G粉G水qⅤ=2491G粉G水=2491××4%=共计支出热量:q支=qⅠ+qⅡ+qⅢ+qⅣ+qⅤ=++++=②收入热量(设配合料入窑温度为36℃)a.由碎玻璃入窑带入的热量:qⅥ=C碎玻璃G碎玻璃t碎玻璃C碎玻璃=+×10-4×36=qⅥ=C碎玻璃G碎玻璃t碎玻璃=××36=b.由粉料入窑带入的热量:qⅦ=C粉G粉t粉qⅦ=C粉G粉t粉=××36=共计支出热量:q收=qⅥ+qⅦ=+=③熔化1㎏玻璃液在玻璃形成过程中的耗热量:q=q支-q收=-=燃烧计算烟气组成计算[5]1.重油成分见下表4-4表4-4重油成分单位:质量分数(%)2.计算基准:100g重油;条件:重油完全燃烧;窑内气体或火焰按其化学组成成分以及具有的氧化或还原能力分为氧化气氛、中性气氛、还原气氛三种。
二代浮法新型节能技术在玻璃熔窑应用实例

我国是玻璃生产大国,截至2021年9月中旬,我国浮法玻璃熔窑共计305座,在产265座,日熔化量174925吨,占全世界浮法玻璃在产产能58%;超白压延玻璃熔窑66座,日熔化量40210吨,占全世界超白压延玻璃在产产能90%。
而玻璃企业是能耗大户,燃料成本占玻璃生产总成本的40%。
在3060碳达峰、碳中和“双碳战略”以及“十四五”能耗总量控制、能耗强度控制“双控目标”国家政策的高压态势下,玻璃行业迫切需要节能新材料和节能新技术,来进一步降低燃料消耗并减少污染排放,同时降低运行成本、提高玻璃企业的产品竞争力。
中建材蚌埠玻璃工业设计研究院(以下简称“中建材蚌埠院”)在熔窑节能领域做了大量研发工作,并取得了卓有成效的创新成果。
其中,玻璃熔窑用红外高辐射节能涂料(以下简称“红外节能涂料”)与二代新型保温节能技术,作为玻璃熔窑节能新材料和节能新技术,被评为“二代浮法玻璃技术与装备优秀创新成果”,成为二代浮法玻璃熔窑标志性节能创新成果和设计标配。
01节能原理1.1 红外高辐射节能涂料的节能原理随着玻璃生产工艺的改进和节能技术水平的提升,我国普白玻璃单耗大约在1300~1550 Kcal/kg玻璃液,熔窑热吸收效率在42%~50%,平均热效率在46%左右。
这与国外工业炉的平均热效率均在50%以上存在一定的差距[1]。
那么,如何才能提高窑炉的热效率呢?众所周知,高温环境下炉膛内部的热量传递以辐射为主,辐射传热所传递的能量占总能量的80%以上。
而一般耐火材料(如优质硅砖)高温下的发射率只有0.4左右[2](如图1所示)。
因此,提高炉膛内表面的发射率,就可以提高熔窑的热吸收效率。
图1 玻璃熔窑内部耐火材料传热示意图中建材蚌埠院研发的“玻璃熔窑用红外高辐射节能涂料”,正是这样一种高发射率的功能性涂料。
将它涂覆在玻璃熔窑内表面,可以将高温下(1600℃)熔窑内表面的发射率从0.4提高到0.9以上。
也就是说,可以将窑炉内表面辐射传热效率提高一倍以上。
- 1、下载文档前请自行甄别文档内容的完整性,平台不提供额外的编辑、内容补充、找答案等附加服务。
- 2、"仅部分预览"的文档,不可在线预览部分如存在完整性等问题,可反馈申请退款(可完整预览的文档不适用该条件!)。
- 3、如文档侵犯您的权益,请联系客服反馈,我们会尽快为您处理(人工客服工作时间:9:00-18:30)。
思考题:
• 1、无拉引量时,窑炉应如何设定各小 炉燃料分配? • 2、依热耗表达式,怎样采取有效措施, 提高窑炉热效率?
*二线热耗计算: • =(159687/Load + 28)*25.2*(1+(20%-Cullet ratio%)/2)
*三线热耗计算: • =(186476/Load + 28)*25.2*(1+(20%-Cullet ratio%)/2)
应用实例、思考
*参见一、二、三线计算公式(Excel文档) 只需输入对应data,各小炉燃料用量即可 自动生成。 data: 1-NG 低位热值; 2-窑炉负荷,即拉引量; 3-碎玻璃比率; 4-各小炉热负荷分配
推算耗热当量(无功系数)
推算步骤
1. 先将目前Load(拉引量),转化计 算成Cullet% = 20 时之拉引量。 *Cullet每增加或减少2%,相当于 Load(拉引量)降低或升高1%
推算耗热当量(无功系数)
推算步骤 2. 耗热当量=(目前单耗/25.2 – 28 - 窑龄增加量) *周拉引量 * 耗能当量实指窑炉窑体散热,玻 璃回流重复加热,出蓄热室烟气、 稀释风、冷却水带走热量系数。
窑炉单耗表达式
窑炉单耗,Kcal/Kg Glass =(耗热当量/周拉引量+28.0)* 25.2*[1+(20% - 碎玻璃占全部 玻璃的比例)*1/2]
推算耗热当量(无功系数)
表达式说明 常数:28,单位:Therm
(英制热量,1 Therm=25.2 kcal)
钠钙平板玻璃形成耗热:705 kcal/kg,合28 therm *与成份、碎玻璃量、澄清温度相 关
窑炉能耗公式推算
目的
• 合理利用燃料之热能,并使其与 窑炉负载(拉引量)相匹配。
• 使炉内热工过程、参数得到有效 控制。 • 针对特殊工况,合理燃料分配。 • 节约能源,降低生产成本。 • 减少环境污染。
推算公式资料
1. 2010年12月各线窑炉玻璃单耗
(NG C.V.=8400 Kcal/NM3) 一线:186.31NM3/MT = 1565 Kcal/kg glass 二线:188.22NM3/MT = 1581 Kcal/kg glass 三线:162.40NM3/MT = 1364 Kcal/kg glass
2.各线碎玻璃比例:12.%璃量+粉料所得玻璃量>为准)
推算耗热当量(无功系数)
基准条件
以现在各线窑炉热耗为基准,推 算出各线窑炉目前的燃料消耗量。 基准:天然气低位热值8400 碎玻璃比例:20%
碎玻璃量/<碎玻璃量+粉料所得玻璃量>
推算耗热当量(无功系数)
影响因素
• • • • • 窑体结构设计、窑体保温状况 燃烧系统效率、蓄热室回收热量效率 窑压、气氛、温度制度 卡脖水包压入深度 玻璃配方、碎玻璃加入量
• 配合料颗粒级配及表面能、细粉含量、 配合料料温、水分 • 窑龄、窑炉密封
各线窑炉耗能公式
*一线热耗计算: • =(125038/Load + 28)*25.2*(1+(20%-Cullet ratio%/2)