一窑四线平拉玻璃熔窑设计
玻璃熔窑结构
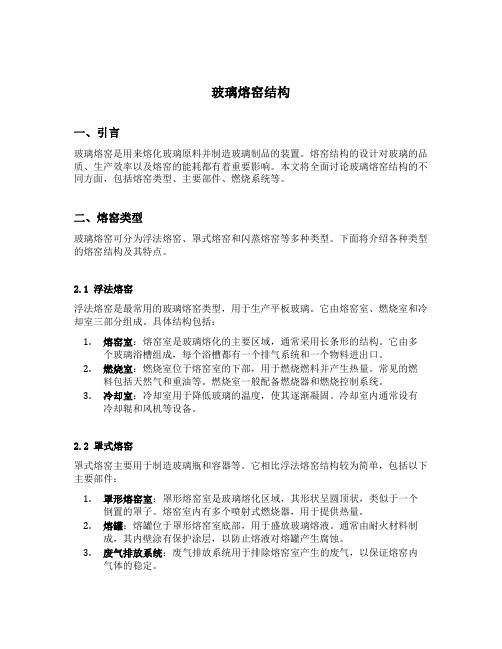
玻璃熔窑结构一、引言玻璃熔窑是用来熔化玻璃原料并制造玻璃制品的装置。
熔窑结构的设计对玻璃的品质、生产效率以及熔窑的能耗都有着重要影响。
本文将全面讨论玻璃熔窑结构的不同方面,包括熔窑类型、主要部件、燃烧系统等。
二、熔窑类型玻璃熔窑可分为浮法熔窑、罩式熔窑和闪蒸熔窑等多种类型。
下面将介绍各种类型的熔窑结构及其特点。
2.1 浮法熔窑浮法熔窑是最常用的玻璃熔窑类型,用于生产平板玻璃。
它由熔窑室、燃烧室和冷却室三部分组成。
具体结构包括:1.熔窑室:熔窑室是玻璃熔化的主要区域,通常采用长条形的结构。
它由多个玻璃浴槽组成,每个浴槽都有一个排气系统和一个物料进出口。
2.燃烧室:燃烧室位于熔窑室的下部,用于燃烧燃料并产生热量。
常见的燃料包括天然气和重油等。
燃烧室一般配备燃烧器和燃烧控制系统。
3.冷却室:冷却室用于降低玻璃的温度,使其逐渐凝固。
冷却室内通常设有冷却辊和风机等设备。
2.2 罩式熔窑罩式熔窑主要用于制造玻璃瓶和容器等。
它相比浮法熔窑结构较为简单,包括以下主要部件:1.罩形熔窑室:罩形熔窑室是玻璃熔化区域,其形状呈圆顶状,类似于一个倒置的罩子。
熔窑室内有多个喷射式燃烧器,用于提供热量。
2.熔罐:熔罐位于罩形熔窑室底部,用于盛放玻璃熔液。
通常由耐火材料制成,其内壁涂有保护涂层,以防止熔液对熔罐产生腐蚀。
3.废气排放系统:废气排放系统用于排除熔窑室产生的废气,以保证熔窑内气体的稳定。
2.3 闪蒸熔窑闪蒸熔窑是一种高温熔炼玻璃的特殊类型熔窑。
其结构相对简单,主要包括以下部件:1.熔化室:闪蒸熔窑的熔化室是玻璃熔化的主要区域。
熔化室内有多个加热电极,通过电阻加热的方式提供热量,使玻璃原料迅速熔化。
2.废气处理系统:废气处理系统用于处理熔窑室出口产生的废气,通常采用除尘和脱硫等工艺,以减少环境污染。
三、主要部件除了不同类型的熔窑有不同的结构,熔窑还包括许多常见的主要部件。
下面将介绍几个关键的部件。
3.1 熔化室熔化室是进行玻璃熔化的核心部分。
玻璃窑炉设计技术

玻璃窑炉设计技术第一章单元窑用来制造E玻璃和生产玻璃纤维的窑炉,通常采用一种称为单元窑的窑型。
它是一种窑池狭长,用横穿炉膛的火焰燃烧和使用金属换热器预热助燃空气的窑炉。
通过设在两侧胸墙的多对燃烧器,使燃烧火焰与玻璃生产流正交,而燃烧产物改变方向后与玻璃流逆向运动。
因此在单元窑内的玻璃熔化、澄清行程长,比其它窑型在窑内停留时间长,适合熔制难熔和质量要求高的玻璃。
单元窑采用复合式燃烧器,该燃烧器将雾化燃料与预热空气同时从燃烧器喷出,经烧嘴砖进入窑炉内燃烧。
雾化燃料处在燃烧器中心,助燃空气从四周包围雾化燃料,能达到较好的混合。
所以与采用蓄热室小炉的窑型相比,燃料在燃烧过程中更容易获得助燃空气。
当空气过剩系数为1.05时能完全燃烧,通过调节燃料与助燃空气接触位置即可方便地控制火焰长度。
由于使用多对燃烧器,分别调节各自的助燃风和燃料量,则可以使全窑内纵向温度分布和炉内气氛满足玻璃熔化与澄清的要求,这也是马蹄焰窑所无法达到的。
单元窑运行中没有换火操作,窑内温度、气氛及窑压的分布始终能保持稳定,这对熔制高质量玻璃有利。
现代单元窑都配置有池底鼓泡,窑温、窑压、液面及燃烧气氛实行自动控制等系统,保证了难熔的E玻璃在较高熔化率下能获取用于直接拉制玻璃纤维的优质玻璃液。
所以迄今在国际上单元窑始终是E玻璃池窑拉丝的首选窑型。
单元窑与其它窑型相比的不足之处是能耗相对较高。
这是因为单元窑的长宽比较大,窑炉外围散热面积也大,散热损失相对较高。
采用金属换热器预热助燃空气的优点是不用换火,缺点是空气预热温度,受金属材料抗氧化、抗高温蠕变性能的制约,一般设计金属换热器的出口空气温度为650—850。
大多数单元窑热效率在15%以内,但如能对换热器后的废气余热再予利用,其热效率还可进一步提高。
配合料在单元窑的一端投入,投料口设在侧墙的一边或两边,也有设在端墙上的。
熔化好的玻璃从另一端穿过沉式流液洞流至称为通路的拉丝作业部。
第一节单元窑的结构设计一、单元窑熔化面积的确定单元窑熔化面积可用公式F= G/g表示。
平板玻璃熔窑电助熔设计与计算

0引言玻璃液在高温熔融状态下是一种电导体。
电熔化已在玻璃行业广泛使用,电助熔热效率高、玻璃的热稳定性和均匀性好,具有提高玻璃质量和降低能耗等优点,有广阔的发展空间。
传统大型平板玻璃熔窑电助熔负荷未超过10%,节能效果有限,实现节能减排技术性突破,增大电助熔负荷势在必行。
平板玻璃熔窑稳定的玻璃液流和合理的液流位置及形态对玻璃熔窑的操作至关重要,电助熔玻璃熔窑的电功率输入及位置设计同样要以保证玻璃熔窑的配合料层、环流Ⅰ、环流Ⅱ以及生产流的稳定为前提。
电助熔功率分配和分区设计及电极布置是电助熔玻璃熔窑的设计难点和设计关键,需结合火焰空间热负荷保证工艺制度和温度梯度,为保证设计合理,必要时需借助数学模拟或物理模型等辅助手段。
1电助熔玻璃熔窑的设计与计算(1)电助熔加热功率及装机功率计算普通平板玻璃(12%碎玻璃)理论熔化热由以下几部分组成:①生成硅酸盐耗热:272 kJ/kg玻璃液;②玻璃液加热至1400 ℃所需热量:1842 kJ/kg玻璃液;③生成玻璃耗热:314 kJ/kg玻璃液;④蒸发水分耗热:104 kJ/kg玻璃液;理论熔化总热耗:2533 kJ/kg玻璃液(不含玻璃液生成气加热耗热),转换为电能为0.7 kWh/kg玻璃液,考虑到电极水套及变压器等能量损失,电助熔的热效率可达85%~90%,那么玻璃液所需输入功率为32~34 kW/t玻璃液(不包含窑炉散热损失),装机功率按40~45 kVA/t玻璃液配置。
(2)电助熔分区设计投料口区域池底温度低,一般理所当然地认为电助熔大部分功率应增设在该区域,事实上国内确实有厂家这样分区布置电助熔,但效果并不理想。
对此做数学模拟,方案1:前置四区均布电极,装机功率3600 kVA;方案2:前区均布三排电极,装机功率1500 kVA,热障区两排电极,装机功率2100 kVA 。
图1为600 t/d颜色玻璃电助熔数学模拟玻璃液流示意图。
图1 600 t/d颜色玻璃电助熔数学模拟玻璃液流示意图数学模拟对比显示,方案1池底热点前移,较大地改变了玻璃窑炉纵向液流形态,不利于玻璃的熔化和澄清。
玻璃熔窑设计-2---副本
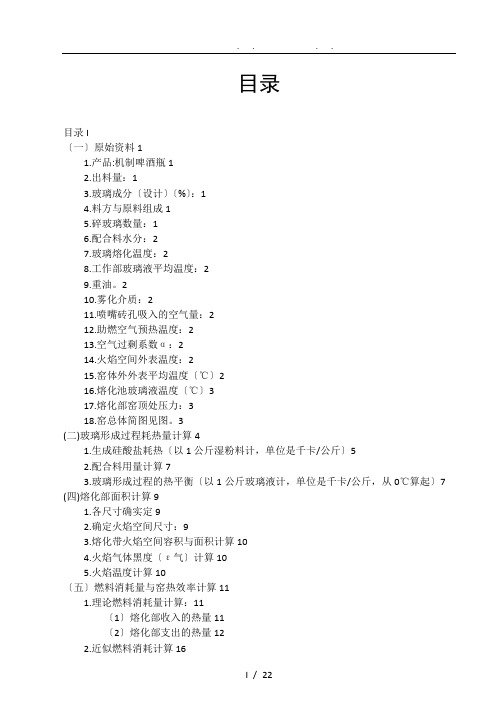
目录目录I〔一〕原始资料11.产品:机制啤酒瓶12.出料量:13.玻璃成分〔设计〕〔%〕:14.料方与原料组成15.碎玻璃数量:16.配合料水分:27.玻璃熔化温度:28.工作部玻璃液平均温度:29.重油。
210.雾化介质:211.喷嘴砖孔吸入的空气量:212.助燃空气预热温度:213.空气过剩系数α:214.火焰空间外表温度:215.窑体外外表平均温度〔℃〕216.熔化池玻璃液温度〔℃〕317.熔化部窑顶处压力:318.窑总体简图见图。
3(二)玻璃形成过程耗热量计算41.生成硅酸盐耗热〔以1公斤湿粉料计,单位是千卡/公斤〕52.配合料用量计算73.玻璃形成过程的热平衡〔以1公斤玻璃液计,单位是千卡/公斤,从0℃算起〕7(四)熔化部面积计算91.各尺寸确实定92.确定火焰空间尺寸:93.熔化带火焰空间容积与面积计算104.火焰气体黑度〔ε气〕计算105.火焰温度计算10〔五〕燃料消耗量与窑热效率计算111.理论燃料消耗量计算:11〔1〕熔化部收入的热量11〔2〕熔化部支出的热量122.近似燃料消耗计算163.实际燃烧消耗量计算164.列熔化部热平衡表165.熔化部热负荷值,单位耗热量与窑热效率计算〔按实际耗油量〕17 〔六〕蓄热室受热外表计算17〔七〕排烟系统阻力计算181.局部阻力计算列下表182.摩擦阻力计算列表:193.蓄热室几何压头计算:20〔八〕烟囱计算201.烟囱高度〔H〕计算202.烟囱出口直径〔D〕计算:20〔一〕原始资料1.产品:翠绿料2.出料量:每天熔化玻璃135吨。
3.玻璃成分〔设计〕〔%〕:4.料方与原料组成5.碎玻璃数量:占配合料量的50%。
6.配合料水分:靠石英砂和纯碱的外加水分带入,不另加水。
7.玻璃熔化温度:1400℃。
8.工作部玻璃液平均温度:1300℃。
9.重油。
10.雾化介质:用压缩空气,预热到120℃,用量为0.6标米3/公斤油。
11.喷嘴砖孔吸入的空气量:0.5标米3/公斤油。
玻璃炉窑的设计与运行

玻璃炉窑的设计与运行摘要:玻璃熔制是玻璃制造中的主要过程之一,是通过燃料的燃烧,将热量传递给配合料,从而达到熔化目的的过程。
玻璃的熔制过程是在玻璃窑炉内实现的。
着玻璃生产技术的不断发展进步,电子玻璃、浮法玻璃等生产行业在追求高质量和高效益的同时,对玻璃生产的环保也有了更高的要求.传统的玻璃熔制工艺已经很难满足更高的环保要求,此时采用全氧燃烧技术的玻璃窑炉的出现无疑成为解决行业生产“节能、环保”问题的一个有效途径。
关键词:玻璃炉窑节能环保设计与运行全氧燃烧玻璃炉1.窑炉的设计原则熔窑是浮法玻璃生产线三大热工设备之首,是实现全线产量、质量目标的关键设备之一,必须做到能耗低、产量高、熔化玻璃质量好、窑龄长等要求。
为了实现上述要求,具体提出了如下设计原则:(1)认真总结国外同级别浮法熔窑的经验和教训,结合国内生产线的实际情况、操作特点,围绕生产优质玻璃液这个重点来进行设计。
(2)着重节能降耗,采用国际先进的节能措施和节能产品,降低生产成本。
(3)全窑工艺尺寸确定既要注重以往的经验数据,同时要有理论创新,要在总结以往经验数据的基础上对新结构确立理论依据。
(4)本熔窑出现的超出国内设计手册的结构设计,必须确保结构安全,此类结构需建立相应的力学模型,并经过常温和热态理论论证通过后方可用于设计。
(5)设计中充分考虑延长窑龄的方法和措施,既要注重耐火材料装备水平,又要充分考虑生产后期保窑操作的可能性及方便性。
(6)节省投资,材料配置上注重实用性,不搞花架子。
主要材料立足于国内采购,尽量少引进硬件,以减少外汇开支。
2.全氧燃烧炉的设计我国已经有很多大学院校和设计单位对全氧燃烧窑炉进行过理论上的研究探讨,但是目前国内的全氧燃烧窑炉基本上是完全引进国外的设计、技术,甚至整条生产线,不仅投资很大,而且使我们自己的全氧燃烧技术发展缓慢。
近年来我院实际参与了国内几台全氧池炉的引进、,设计转化工作,对国外先进技术进行了一些研究,在全氧玻璃池炉的设计上积累了一些经验。
玻璃熔制及熔窑---熔制的工艺制度

熔制的工艺制度
2.温度制度的作用 (1)影响配合料熔化、玻璃形成、玻璃液的澄清均化速度: 1400~1450℃,熔制温度每提高1℃,可使熔制能力提高2%, 澄清温度提高5℃使玻璃液的再澄清带停留的时间缩短50%。 (2)影响玻璃熔窑的窑龄,增加燃料消耗量。随着熔制温度 的升高和产量的提高,耐火材料的侵蚀加快,窑龄将缩短。 (3)影响到玻璃液的对流。 (4)影响到玻璃的成型作业
熔制的工艺制度
料层跑偏—因各加料机投料不一,致使沿窑宽的料层厚 度不均,数量上产生差异,料层集于一侧,极易导致泡 界线的偏斜。 d.温度 当熔化部温度高时,玻璃液粘度减小,回流速度加快, 参与回流的玻璃降低时,玻璃液粘度变大,回流慢,液量少, 未熔配合料增多,泡界线挪后变远;当窑内横向温差变 大时,横向液流明显加剧,泡界线紊乱、模糊,直至偏 斜,发生“跑料”现象。
熔制的工艺制度
B.气氛制度的制定 主要与配合料组成、澄清剂种类、生产玻璃颜色等有关。 a.采用芒硝做澄清剂 为保证芒硝的高温分解,必须添加煤粉做还原剂,因此, 通常采用的气氛制度为:1#、2#小炉需要还原焰,不使 碳粉烧掉;3#、4#小炉是热点区,需要中性焰,不能用 氧化焰,否则液面会产生致密的泡沫层,使澄清困难; 5#、6#小炉是澄清、均化区,为烧去多余的碳粉,不使 玻璃着色,需用氧化焰。 实际生产中空气过剩系数略大些,提供过量的氧,以保 证燃料完全燃烧。
1570 1550 21.7 19
熔制的工艺制度
“双高”曲线:即“双高热负荷点”温度制度,核心是减少 处在泡沫稠密区的小炉燃料分配量,降低了此处的热负荷; 配合料入窑预助熔。 目前,国内浮法熔窑均采用此法。
小炉序号
1
2
3
4
5
6
玻璃生产线熔窑控制方案
燃 气混 合燃料 炉窑 的控 制 方案 为 例 进行 说 明 , 换 火流 程如 图 1 所示 。具体 的换 火步骤 如下 : ( 1 )关 东油 : 预警 响铃 , 通知 操 作 人 员准 备 换 火 ,
5 S 后 关闭东 油 同时打 开东吹扫 , 吹扫时 间一般 为 1 0 S
玻 璃 生产 线熔 窑控 制方 案粜
郭 玮 , 陈祖 建
( 1 . 山 西农 业 大 学 . T - 学 院 , 山西 太 谷 0 3 0 8 0 1 ;2 沦茨 ( 上 海) 传 动 系统 有 限公 司 , 上海 2 0 0 0 0 0 )
摘 要 :介 绍 了浮 法 玻 璃 生产 的一 般 工 艺 流 程 和 控 制 要 点 ,重 点 介 绍 了熔 窑换 火控 制 方 式及 注 意 要 点 ,并 对 混
( 5 )开 西煤气 : 开西 油 2 S 之后 开 西煤 气 , 然后 进 入燃 烧 过 程 , 设 定燃 烧 时 间. 燃 烧 过 程 一 般 持 续
2 0 mi n。
蓄 热室 的热效率 与诸 多 因素有 关 , 包 括 蓄 热室 结 构、 格 子体体 积 、 换 火周 期 等 。一个 窑 炉投 产 后 , 蓄 热
第l 期( 总第 1 7 6期 )
2 0 1 3年 2月
机 械 工 程 与 自 动 化
M EC H ANI CAI ENGI NEE RI NG & AUT( ) M ATI ( ) N
NO. 1
Feb .
文章编号 : 1 6 7 2 — 6 4 1 3 ( 2 0 1 3 ) 0 1 — 0 1 4 6 — 0 2
般为 3 0 s 左右 。
有的使 用煤气做 燃料 , 有的使用 煤油做 燃料 , 也有使 用 燃 气和燃 油混合 燃 料 。此外 换 火程 序 也 与熔 窑 结 构 、 燃料、 窑炉规模 、 助燃风 供给方 式等诸 多 因素 有关 。
(整理)浮法玻璃熔窑的结构 (自动保存的)
浮法玻璃熔窑的结构浮法玻璃熔窑和其他平板玻璃熔窑相比,结构上没有太大的区别,属浅池横焰池窑,但从规模上说,浮法玻璃熔窑的规模要大得多,目前世界上浮法玻璃熔窑日熔化量最高可达到1100t以上(通常用1000t/d表示)。
浮法玻璃熔窑和其他平板玻璃熔窑虽有不同,但它们的结构有共同之处。
浮法玻璃熔窑的结构主要包括:投料系统、熔制系统、热源供给系统、废气余热利用系统、排烟供气系统等。
图1-1为浮法玻璃熔窑平面图,图1-2为其立面图。
一投料池投料池位于熔窑的起端,是一个突出于窑池外面的和窑池相通的矩形小池。
投料口包括投料池和上部挡墙(前脸墙)两部分,配合料从投料口投入窑内。
1.投料池的尺寸图1-1 浮法玻璃熔窑平面图1-投料口;2-熔化部;3-小炉;4-冷却部;5-流料口;6-蓄热室图1-2 浮法玻璃熔窑立面图1-小炉口;2-蓄热室;3-格子体;4-底烟道;5-联通烟道;6-支烟道;7-燃油喷嘴投料是熔制过程中的重要工艺环节之一,它关系到配合料的熔化速度、熔化区的热点位置、泡界限的稳定,最终会影响到产品的质量和产量。
由于浮法玻璃熔窑的熔化量较大,采用横焰池窑,其投料池设置在熔化池的前端。
投料池的尺寸随着熔化池的尺寸、配合料状态、投料方式以及投料机的数量。
配合料状态有粉状、颗粒状和浆状(目前一般使用粉状);投料方式由选用的投料机而确定,有螺旋式、垄式、辊筒式、往复式、裹入式、电磁振动式和斜毯式等。
(目前多采用垄式投料机和斜毯式投料机)。
(1)采用垄式投料机的投料池尺寸采用垄式投料机的投料池宽度取决于选用投料机的台数,投料池的长度可根据工艺布置情况和前脸墙的结构要求来确定。
(2)采用斜毯式投料机的投料池尺寸斜毯式投料机目前在市场上已达到了普遍使用,它的投料方式与垄式投料机相似,只是投料面比垄式投料机要宽得多,因此其投料池的尺寸在设计上与采用垄式投料机的投料池尺寸没有太大的区别,仍然决定于熔化池的宽度和投料面的要求。
玻璃熔窑设计
摘要设计介绍了一套规模为900t/d浮法玻璃生产线的工艺流程,在设计过程中,原料方面,对工艺流程中的配料进行了计算;熔化工段方面,参照国内外的资料和经验,对窑的各部位的尺寸、热量平衡和设备选型进行了计算;分析了环境保护重要性及环保措施参考实习工厂资料,在运用相关工艺布局的基础下,绘制了料仓、熔窑、锡槽、成品库为主的厂区平面图,具体对熔窑的结构进行了全面的了解,绘制了熔窑的平面图和剖面图,还有卡脖结构图,整个设计参照目前浮法玻璃生产的主要设计思路,采用国内外先进技术,进行全自动化生产,反映了目前浮法生的较高水平。
关键词:浮法玻璃、熔窑工段、设备选型、工艺计算。
AbstractThe design introduced the technical process of 900t/d float glass production line. During the planning, for the raw material, the computation of material has been made; and for the melt section, the melting kiln various spots size, The heat balance and the choose of the equipment have been calculated with reference to the domestic and foreign materials and the experience, the environmental protection importance and environmental protection measure have been analyzed. With reference to factory date, under the technology arrangement correlation knowledge foundation, the factory horizontal plan about the storage, the melting kiln, the tin trough and product storage has been finished. The melting kiln structure has been concretely introduced, the horizontal plan and the sectional drawing of the melting kiln, small mouth composition and card neck structure drawing have been draw up. The entire design consulted the main design mentality of present float glass production; took the domestic and foreign advanced technologies; carried on the entire automated production; reflected at present floats production to compare the high level.keywords: float glass; melting section; choose of the equipment; process calculation.目录前言 (1)第一章浮法玻璃工艺方案的选择与论证 (3)1.1平板玻璃工艺方案 (3)1.1.1有曹垂直引上法 (3)1.1.2垂直引上法 (3)1.1.3压延玻璃 (3)1.1.4 水平拉制法 (3)1.2浮法玻璃工艺及其产品的优点 (4)1.3浮法玻璃生产工艺流成图见图1.1 (5)图1.1 (5)第二章设计说明 (6)2.1设计依据 (6)2.2工厂设计原则 (7)第三章玻璃的化学成分及原料 (8)3.1浮法玻璃化学成分设计的一般原则 (8)3.2配料流程 (9)3.3其它辅助原料 (10)第四章配料计算 (12)4.1于配料计算相关的参数 (12)4.2浮法平板玻璃配料计算 (12)4.2.1设计依据 (12)4.2.2配料的工艺参数; (13)4.2.3计算步骤; (13)4.3平板玻璃形成过程的耗热量的计算 (15)第五章熔窑工段主要设备 (20)5.1浮法玻璃熔窑各部 (20)5.2熔窑主要结构见表5.1 (21)5.3熔窑主要尺寸 (21)5.4熔窑部位的耐火材料的选择 (24)5.4.1熔化部材料的选择见表5.3 (24)5.4.2卡脖见表5.4 (25)5.4.3冷却部表5.5 (25)5.4.4蓄热室见表5.6 (25)5.4.5小炉见表5.7 (26)5.5玻璃熔窑用隔热材料及其效果见表5.8 (26)第六章熔窑的设备选型 (28)6.1倾斜式皮带输送机 (28)6.2毯式投料机 (28)6.3熔窑助燃风机 (28)6.4池壁用冷却风机 (29)6.5碹碴离心风机4-72NO.16C (29)6.6L吊墙离心风机9-26NO11.2D (29)6.7搅拌机 (29)6.8燃油喷枪 (29)6.9压缩空气罐C-3型 (29)第七章玻璃的形成及锡槽 (30)第八章玻璃的退火及成品的装箱 (32)第九章除尘脱硫工艺 (33)9.1除尘工艺 (33)9.2烟气脱硫除尘 (33)第十章技术经济评价 (34)10.1厂区劳动定员见表10.1 (34)10.2产品设计成本编制 (35)参考文献 (38)致谢 (39)前言英国Pilkington兄弟在20世纪50年代浮法玻璃生产技术的发明付出了坚持不懈的努力,自1953年开始到1959年取得了成功耗时7年,投入了400万英镑。
平拉法玻璃熔窑和退火窑的合理设计
平拉法玻璃熔窑和退火窑的合理设计
法玻璃熔窑和退火窑是玻璃工业中非常重要的设备,它们的设计与运行对于产品的质量和生产效率具有直接的影响。
在设计这些设备时,需要考虑许多因素,包括温度控制、能源消耗、生产容量等。
本文将详细介绍平拉法玻璃熔窑和退火窑的合理设计及其重要性。
首先是熔窑的设计。
在平拉法熔窑中,最重要的是对于温度的控制。
温度的稳定性能够确保玻璃材料能够均匀熔化,从而产生均匀质量的玻璃产品。
因此,熔窑应该具有恒温功能,并且能够控制温度在精确的范围内波动,这可以达到使用者的需求,在整个加工中稳定达到一定的温度。
此外,为了提高生产效率,熔窑的内部空间应该充分利用,使得生产过程中能够产生更多的玻璃材料。
其次是退火窑的设计。
在生产过程中,退火窑具有非常重要的作用,它能够改善玻璃结构,使得其更加耐用、坚韧。
因此,在退火窑的设计上需要非常注重温度控制。
退火窑必须具备刚性和稳定的结构,以确保玻璃材料的温度在整个加工过程中能够保持恒定。
另外,退火窑的便利使用也是设计的重要方面之
一,应该设计出人性化的操作界面,使得操作过程更加简单、易懂。
此外,在设计平拉法玻璃熔窑和退火窑时需要考虑的关键因素还包括:能源消耗、环境影响、可持续性等等。
在设计中应该考虑到可以更加深入的挖掘环保的潜力,发现绿色的制品能够大幅度的改良生产成本,并为后续的使用者提供更加的绿色环保的选择。
总之,合理的平拉法玻璃熔窑和退火窑设计对于玻璃工业的发展至关重要。
熔窑和退火窑通过创造稳定、高效、节能的生产环境,能够提高玻璃产品的质量,降低生产成本,进一步推动玻璃工业的可持续发展。
- 1、下载文档前请自行甄别文档内容的完整性,平台不提供额外的编辑、内容补充、找答案等附加服务。
- 2、"仅部分预览"的文档,不可在线预览部分如存在完整性等问题,可反馈申请退款(可完整预览的文档不适用该条件!)。
- 3、如文档侵犯您的权益,请联系客服反馈,我们会尽快为您处理(人工客服工作时间:9:00-18:30)。
摘要介绍了260~300td一窑四线平拉玻璃熔窑的设计情况,包括:熔化部设计,分支通路的布置原则,分支通路长度尺寸的设计,全窑池底结构形式和不同池深的窑底结构处理。
关键词平拉玻璃熔窑设计天津玻璃厂是我国采用平拉工艺(格法)生产平板玻璃的重点骨干企业。
该厂于1986年全套引进了比利时格拉威伯尔公司(Glaverbe1)的平拉玻璃生产技术及主要设备。
建设初期为一窑二线,并留有可热接第三线的接口。
后来在不停产的情况下,成功地热接了第三线,建成了国内第一条一窑三线的平拉玻璃生产线。
长期稳定地生产2 mm厚优质薄玻璃,工厂取得了良好的经济效益,同时为国内多家平拉玻璃企业提供了技术支持。
随着天津市城市建设的发展和环境保护的要求,该生产线所在的地理位置已被规划为商住区,玻璃厂需要搬迁到新址。
由于原一窑三线已经完成了两个窑期近17年的运行,拆后可利用的设施已不多,以及要扩大生产能力的考虑,工厂决定新建一条一窑四线平拉玻璃生产线。
设计熔化能力260~300t/d,燃料为重油,窑龄8年,玻璃原板宽度4000 mm,耐火材料立足于全部国产,现将有关设计情况介绍如下:1 熔化部设计在80年代引进的一窑三线平拉玻璃熔窑,从窑型尺寸到各部位细部结构看,该熔窑的熔化部在现在看来仍是一座200 t/d级的技术比较先进的熔窑。
本次工厂搬迁需要新建同样技术先进的一窑四线,熔化能力为260~300 t/d的熔窑,并要积极采用近年来的各项熔窑新技术。
本设计确定一窑四线平拉玻璃熔窑的熔化部,采用近年来在国内浮法玻璃熔窑上广泛采用的熔化部结构形式,并以某建成投产多年的300 t/d浮法线熔窑做为参照,进行熔化部设计。
1.1 熔化部主要尺寸的确定按照熔化部的池宽尺寸计算公式:B=9000+ (P-300) ×7求得该熔窑(按P=300 t/d)的熔化部池宽为:B=9 000 mm。
对于浮法玻璃熔窑来说,熔化部和熔化区的长宽比分别为:K1=3~3.3;K2=1.8~2.0。
对于平拉玻璃熔窑来说,为了保证长通路末端玻璃液的成形温度,这两个比值要取得小一些,初步设定熔化部的长宽比为:K1=2.9;熔化区的长宽比为:K2=1.85。
计算出熔化部和熔化区池长的初步尺寸:熔化部池长:L=9 000×2.9=26100 mm,熔化区池长:Ll=9 000×1.85=16650 mm。
根据这两个初步的长度尺寸设定以下数据:1#小炉前长:La=3500 mm,小炉对数:Pn=5小炉中心线间距:1#~4#:3100mm,4#~5#:2900mm ,5#小炉后长:Lz=10300mm。
与浮法熔窑相比,末对小炉后的尺寸要偏小一些,主要是为了提高进入通路的玻璃液温度,以保证通路末端玻璃的成形温度。
根据以上的设定数据,求出一窑四线熔窑的熔化区和熔化部的实际池长尺寸如下:熔化区池长:3500+3100×3+2900+1000=16700 mm。
熔化部池长:3500+3100×3+2900+10300=26000 mm。
熔化部池深:1180 mm (同一窑三线)。
1.2 投料池结构20世纪90年代出现的“全窑宽投料池”结构,对于大型横火焰玻璃池窑来说是一项重要的新技术。
近年来,国外新建或改建的大型横火焰玻璃熔窑上多已采用了全窑宽投料池结构。
全窑宽投料池的优点是:投料口结构简单、增加熔窑的熔化能力、提高玻璃液的熔化质量、节能降耗、节省建设投资。
国内多家玻璃厂已在新建或改扩建的熔窑上采用了全窑宽投料池结构,取得了良好的经济效果,显示了全窑宽投料池的优势,已是国内一项成熟可靠的玻璃熔窑新技术。
本一窑四线熔窑确定采用全窑宽投料池:池宽9000 mm,池长1700 mm。
前脸墙采用L型吊墙及其配套密封设施。
l_3 燃烧系统原一窑三线熔窑为4对小炉,采用顶插式燃油喷枪,顶插式喷枪燃烧效率高,在大型玻璃熔窑上常被采用,但这种喷枪目前国内还无厂家生产,需要引进。
而另一种在国内玻璃熔窑上大量采用的“炉下式燃油喷枪”,也是燃烧效率较高的喷枪,国内有多个厂家生产此种喷枪及系统,配套方便。
炉下式燃油喷枪在操作和维修方面,比其他类型的喷枪都简单容易。
本一窑四线熔窑确定采用国产的炉下式燃油喷枪及配套系统,5对小炉,每个小炉两支枪。
2 通路设计通路是平拉玻璃在进入成形室之前要经过的关键部位,此部位直接关系到平拉玻璃产品的产量和质量。
一窑四线的通路设计是按以下的原则进行的:首先根据生产操作要求确定好四条分支通路的分布位置形式;然后根据通路温降情况和通路结构要求确定各分支通路的长度;最后在通路窑体结构上进行配套设计。
2.1 四条分支通路横向分布尺寸的确定原一窑三线的通路布置形式为:直形横通路连接三条平行的分支通路,运行17年多来效果良好,是很成熟的“宽板深池”通路结构。
本次一窑四线设计确定:横通路仍采用直线形的,后面连接四条平行的分支通路,横通路和四条分支通路对称布置在熔窑纵向中心线延长线的两侧。
玻璃原板宽度4 000 mm 的分支通路,其通路砖结构的外宽约为5800mm,钢结构外宽约为7000mm。
各平行分支通路中心线间距尺寸的要求是:对于需要有更换转向辊操作位置的,最小尺寸为12000mm;对于无更换转向辊操作位置的:最小尺寸为8500 mm。
根据这样的尺寸要求,4条分支通路中心线的横向间距分布尺寸,考虑了以下两个方案:方案1:12000+8500+12000=32500 mm,此方案是考虑更换转向辊的操作位置为两处,分别在1#与2#分支通路之间和3#与4#分支通路之间。
方案2:8500+12000+8500=29000 mm,此方案是考虑更换转向辊的操作位置为3处,分别在1# 、4#分支通路的外侧和2与3分支通路之间。
方案1的1#和4#分支通路外侧不需更换转向辊操作,只需留有人行和物流通道即可,对于玻璃原板宽度为4000 mm 的通路来说,分支通路的半宽加上通道之和的尺寸应不小于6000 mm,这样一窑四线的通路区域工作面的总宽度尺寸最小为:6000+32500+6000=44500mm,需要配跨度为45000mm的厂房。
方案2的1#和4#分支通路外侧要进行换转向辊操作,需要留有较宽的尺寸,对于玻璃原板宽度为4000 mm 的通路来说,通路半宽加换辊操作空间尺寸应不小于9000 mm,则通路区域的工作面总宽度尺寸最小为:9000+ 29000+ 9000=47 000 mm,这就需要配跨度为48000mm的厂房。
比较这两个方案,可见方案1具有优势:厂房跨度少3000mm、换转向辊操作位置少1处、换辊用的天车运动区间也小,由此本项目选定了方案1做为四条分支通路的横向间距尺寸。
2.2 各分支通路长度尺寸的确定确定了4条分支通路的横向分布尺寸之后,再根据通路温降情况和通路结构要求确定各分支通路的长度尺寸。
为了表达方便,首先定义一个术语——“通路起点”,它是指熔窑纵向中心线与横通路中心线交点处。
根据热工计算和现场测定,能够确定出原一窑三线的通路起点和3条分支通路的C形砖前的温度。
实测结果与计算结果略有不同,边部的两条支通路(1#和3#)C形砖前的温度比中部的2#通路平均高出20℃左右。
为什么会出现这种情况呢?分析原因可能主要是中间通路离卡脖较近,产生回流的玻璃液比边部通路的多一些,多带走了一些热量所至。
实际生产中也是边部通路末端温度偏高,拉引量偏低,与测定结果一致。
搞清楚这一点对于掌握一窑多线的各通路温度情况是很必要的。
根据原一窑三线通路区域的温度制度,结合新设计一窑四线通路区域的窑体结构变化情况,特别是窑体的保温结构情况,可以确定出一窑四线熔窑的玻璃液在通路区域不同区段里的温度变化情况。
在本次设计中,考虑到4条线的布置需要,各分支通路长度要比3条线的加长一些。
但仍要保持各分支通路c形砖前的温度,经过多次计算进行优化,本设计确定将“通路起点”玻璃液温度要略提高一些,从同吨位浮法玻璃熔窑的温度制度来看,这是不难办到的。
确定好了一窑四线通路区域的温度制度,就可以确定各部位通路的长度尺寸了。
计算结果,一窑四线的通路起点到C形砖前的长度为:17000 mm,到板根处为:18750 mm。
根据前面已确定好的各分支通路横向布置尺寸,中间的2#和3#分支通路从横通路中心线算起到板根处的长度为:18750-(8500/2)=14500mm;边部的1#和4#分支通路这一长度为:18750-(8500/2)-12000=2500mm。
显然2500mm是太短了,不能满足分支通路末端的结构设计要求,必须加长。
根据分支通路末端的结构情况,边部1#和4#分支通路的这一长度最小应为6250 mm。
由此边部的1#和4#分支通路从通路起点到板根处的长度是:(8500/2)+12000+6250=22500mm,到C形砖前的长度为:22500-1750=20750mm。
按这一长度计算,边部的1#和4#分支通路到C形砖前的温度要比中间的2#和3#分支通路温度低近30℃,这是按玻璃液在各分支通路区域的温降速率相同时的计算结果。
前面已述及一窑三线的边部通路温度要比中部的平均高20℃左右,一窑四线的边部分支通路也会出现这一情况,因此边部的1#和4#分支通路C形砖前的实际温度可以达到设计的温度。
至此,一窑四线平拉玻璃熔窑的通路布置平面尺寸就全部确定好了。
一窑四线平拉玻璃熔窑平面简图见图1。
图1 一窑四线平拉玻璃熔窑平面简图3 窑底结构设计原一窑三线熔窑的窑池深度为:熔化部池深1180mm,通路池深1265mm,相差85mm。
池底砖结构总厚度也不同,分别是:熔化部570mm,通路485mm,也相差85mm。
熔化部与通路两部分的池深与池底砖结构厚度之和正好相等,全窑池底砖结构下平面标高相同。
新设计的一窑四线熔窑的池深与原一窑三线的相同:熔化部1180mm,通路1265mm。
在窑底结构上,特别是池底铺面结构做了比较大的改动:池底铺面砖厚度减薄了,池底大砖厚度适当加厚了些,这种改动在满足设计指标对窑体要求的前提下,可节省近200万元的建窑投资。
熔化部(包括卡脖)池底采用“合页窗式” 活动保温结构,可开可闭,池底砖结构总厚度为550mm;通路池底采用固定保温结构,池底砖结构总厚度为520mm。
熔化部与通路两部分的池深与池底砖结构厚度之和不相等,全窑池底砖结构下平面标高不相同。
采用这样的池底砖结构设计有两个原因:一是如何设计不同池深的窑底结构,及池深不同的过渡区域结构的处理,二是减薄池底铺面砖要确保通路区域的池底采用固定保温结构后不漂砖,通路池底安全可靠。
3.1 不同池深的窑底结构及其过渡区结构原一窑三线熔窑的熔化部和通路的池底大砖上平面为同一标高,不同池深是通过不同厚度的池底捣打料和不同厚度的池底铺面砖来实现的,结构比较简单。