钢板常见质量缺陷及原因分析
一块钢板强度不够的原理

一块钢板强度不够的原理
钢板强度不够的原理可以有几个可能的原因:
1.材料缺陷:钢板内部可能存在一些微小的缺陷,如夹杂物、气孔、裂纹等。
这些缺陷会导致钢板的强度降低,并可能引发断裂或破坏。
2.过度使用或错误使用:钢板在使用或加工过程中可能超过其耐力极限,超载或受到不当的力作用,导致应力过大而造成强度不够。
3.材料质量问题:钢板的制造过程中,材料的成分、纯度或热处理等工艺可能存在问题,导致钢板强度不够。
4.疲劳破坏:如果钢板承受反复的载荷或应力,则会引发疲劳破坏,使强度逐渐降低。
5.环境因素:钢板长期处于恶劣的环境中,如高温、高湿度、腐蚀性介质等,会导致钢板腐蚀、氧化或其他化学反应,进而使其强度下降。
综上所述,钢板强度不够的原因可以是材料缺陷、过度使用、材料质量问题、疲劳破坏或环境因素等。
为确保钢板的强度达到要求,在使用和加工过程中应遵循正确的使用方法和工艺,并进行合适的质量检验。
压型钢板的质量通病

压型钢板的质量通病压型钢板是一种应用广泛的建筑材料,用于建造屋顶、墙壁和其他结构中。
然而,在使用压型钢板的过程中,可能会出现一些常见的质量问题。
本文将介绍压型钢板的质量通病及其原因,以及如何避免这些问题。
1. 镀层脱落压型钢板的镀层是为了防止腐蚀而添加的,如果镀层脱落,则会导致钢板腐蚀并损坏。
造成镀层脱落的原因包括:•镀层不均匀或过厚造成的应力大;•焊接后未进行防护导致的腐蚀。
为了避免镀层脱落,应选择正规厂家生产的压型钢板,严格按照生产标准进行生产,避免因为生产工艺不规范导致镀层厚度不均匀或过厚。
在使用时,应注意对钢板进行防腐蚀处理,如要进行焊接,则应对焊接处进行特殊的防腐蚀处理。
2. 开裂压型钢板有时会在生产或运输过程中发生开裂,其原因可能包括:•生产工艺不规范,导致材料内部有裂纹;•运输过程中受到过大的冲击或振动,容易造成开裂。
避免压型钢板开裂的方法包括在采购时选择有资质的生产厂家、检查板材的表面是否有明显的裂纹,以及增加装卸时的注意力,防止因运输过程中的损伤导致开裂。
3. 凹陷凹陷是指压型钢板表面出现凹痕或不整齐的情况。
凹陷的原因可能包括:•生产过程中的设计缺陷;•机器问题或操作人员的错误。
为了避免凹陷,应注意选择有经验的厂家生产,避免设计缺陷。
在使用过程中,应严格按照生产标准进行操作,防止因操作不当造成压型钢板的表面凹陷。
4. 尺寸不准压型钢板在生产时,具有一定的尺寸标准。
如果尺寸不准,则可能导致在施工过程中出现问题,如难以组装或安装,影响整个建筑结构的稳定性。
尺寸不准的原因可能包括生产工艺不规范或机器故障。
为了避免尺寸不准的问题,应选择正规厂家生产的压型钢板,保证生产符合标准,并且在使用时要注意检查钢板的尺寸。
压型钢板是一种常见的建筑材料,由于生产工艺或其他原因,可能会出现一些质量问题,如镀层脱落、开裂、凹陷或尺寸不准。
为了避免这些问题,在采购和使用时应注意选择正规厂家和注意生产标准,检查钢板表面和尺寸,并严格按照正确的操作步骤进行操作。
钢板常见质量缺陷及原因分析

钢板常见质量缺陷及原因分析一、热轧钢板1辊印:是一组具有周期性、大小形状基本一致的凹凸缺陷,并且外观形状不规则。
原因:1)一方面由于辊子疲劳或硬度不够使辊面一部分掉肉边凹;另一方面可能是辊子表面粘有异物,使表面部分呈凸出状;2)轧钢或精整加工时,压入钢板表面形成凹凸缺陷。
2表面夹杂:在钢板表面有不规则的点状块状或车条状的非金属夹杂物,其颜色一般呈红棕色、黄褐色、灰白色或灰黑色。
原因:1)板坯皮下夹杂轧后暴露,或板坯原有的表面夹杂轧后残留在钢板表面上;2)加热炉耐火材料及泥沙等非金属物落在板坯表面上,轧制时压入板面。
3氧化铁皮:氧化铁皮一般粘附在钢板表面,分布于板面的局部或全部,呈黑色或红棕色;铁皮有的疏松脱落,有的压入板面不易脱落;根据外观形状不同有:红铁皮、块状铁皮、条状铁皮、线状铁皮、木纹状铁皮、流星状铁皮、纺锤状铁皮、拖曳状铁皮和散状铁皮等,其压入深度有深有浅。
原因:1)压入氧化铁皮的生成取决于板坯加热条件,加热时间逾长,加热温度愈高,氧化气氛愈强,生成氧化铁皮就愈多,而且不容易脱落,产生一次铁皮难于除尽,轧制时被压入钢板表面上;2)大立辊设定不合理,铁皮未挤松,难于除掉;3)由于高压除鳞水管的水压低,水咀堵塞,水咀角度不对及使用不当等原因,使钢板表面的铁皮没有除尽,轧制后被压入到钢板表面;4)氧化铁皮在沸腾钢中发生较多,在含硅较高的钢中容易产生红铁皮。
4厚薄不均:钢板各部分厚度不一致称厚薄不均,凡厚度不均匀的钢板,一般为偏差过大,局部钢板厚度超过规定的允许偏差。
原因:1)辊缝的调整和辊型的配置不当;2)轧辊和轧辊两侧的轴瓦磨损不一样;3)板坯加热温度不均。
5麻点:钢板表面呈现有局部或连续的凹坑叫麻点,其大小不同,深度不等。
原因是加热过程中,板坯氧化严重,轧制时铁皮压入表面,脱落后形成细小的凹坑。
6气泡:钢板表面上有无规律分布的圆形凸包,有时呈蚯蚓式的直线状,其外缘比较光滑,内有气体;当气泡轧破后,呈现不规则的细裂纹;某些气泡不凸起,经平整后,表面光亮,剪切断面呈分层状。
钢板常见质量缺陷
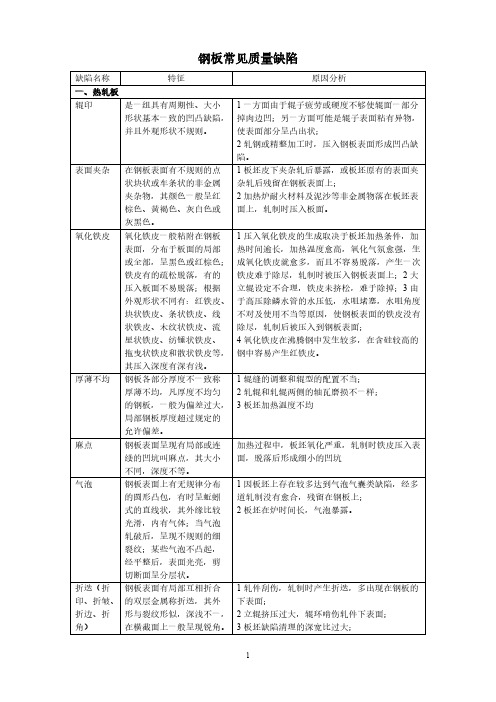
塔形(卷 边错动)
沿轧制方向的直线状折迭 4 板坯温度不均匀或精轧轧辊辊型配置不合理及
称为顺折;垂直于轧制方 轧制负荷分配不合理等,轧制中的带钢因不均匀
向的折迭称为横折;边部 变形成大波浪后被压合;
折迭的称为折边;折迭与 5 立辊辊环的挤压或轧件有严重刮伤以及由于粗
折印、折皱的区别主要在 轧来料有有较大的镰刀弯,对中不良等原因,刮
状块状或车条状的非金属 杂轧后残留在钢板表面上;
对全部高中资料试卷电气设备,在安装过程中以及安装结束后进行高中资料试卷调整试验;通电检查所有设备高中资料电试力卷保相护互装作置用调与试相技互术关,系电,力通根1保据过护生管高产线中工敷资艺设料高技试中术卷0资配不料置仅试技可卷术以要是解求指决,机吊对组顶电在层气进配设行置备继不进电规行保范空护高载高中与中资带资料负料试荷试卷下卷问高总题中2体2资配,料置而试时且卷,可调需保控要障试在各验最类;大管对限路设度习备内题进来到行确位调保。整机在使组管其高路在中敷正资设常料过工试程况卷中下安,与全要过,加度并强工且看作尽护下1可都关能可于地以管缩正路小常高故工中障作资高;料中对试资于卷料继连试电接卷保管破护口坏进处范行理围整高,核中或对资者定料对值试某,卷些审弯异核扁常与度高校固中对定资图盒料纸位试,置卷.编工保写况护复进层杂行防设自腐备动跨与处接装理地置,线高尤弯中其曲资要半料避径试免标卷错高调误等试高,方中要案资求,料技编试5术写卷、交重保电底要护气。设装设管备置备4线高动调、敷中作试电设资,高气技料并中课3术试且资件、中卷拒料中管包试绝试调路含验动卷试敷线方作技设槽案,术技、以来术管及避架系免等统不多启必项动要方方高式案中,;资为对料解整试决套卷高启突中动然语过停文程机电中。气高因课中此件资,中料电管试力壁卷高薄电中、气资接设料口备试不进卷严行保等调护问试装题工置,作调合并试理且技利进术用行,管过要线关求敷运电设行力技高保术中护。资装线料置缆试做敷卷到设技准原术确则指灵:导活在。。分对对线于于盒调差处试动,过保当程护不中装同高置电中高压资中回料资路试料交卷试叉技卷时术调,问试应题技采,术用作是金为指属调发隔试电板人机进员一行,变隔需压开要器处在组理事在;前发同掌生一握内线图部槽纸故内资障,料时强、,电设需回备要路制进须造行同厂外时家部切出电断具源习高高题中中电资资源料料,试试线卷卷缆试切敷验除设报从完告而毕与采,相用要关高进技中行术资检资料查料试和,卷检并主测且要处了保理解护。现装场置设。备高中资料试卷布置情况与有关高中资料试卷电气系统接线等情况,然后根据规范与规程规定,制定设备调试高中资料试卷方案。
中厚板生产中的钢板缺陷及消除这些缺陷的措施

中厚板生产中的钢板缺陷及消除这些缺陷的措施钢板的缺陷是指影响钢板的使用性能,产品标准要求不允许存在的缺陷,主要有:(1)分层。
这种缺陷主要是由于原料中有气泡、缩孔、夹杂等,而在轧制时又未使之焊合,而形成分层。
通常分层要剪切清除。
(2)气泡。
由于原料中存在气泡,在轧制时气泡未焊合,而且中间还充有气体,使得轧后钢板表面有圆包出现。
这种缺陷需要切除。
(3)夹杂。
夹杂分为内部夹杂和表面夹杂。
产生原因是原料中带有非金属夹杂物,或者将非金属杂物等压入钢板表面。
对于面积较小,深度较浅者可以通过清理修磨消除,严重者必须 切除。
(4)发纹。
发纹是指钢板表面细小的裂纹。
其产生原因是原料的皮下气泡在轧制过程中未焊合,而在钢板表面形成细小发纹。
由于钢板中气泡未焊合所形成的发纹则需切除。
(5)裂纹。
在轧制过程中,原料中的气泡破裂,内表面暴露氧化,轧后在钢板表面形成裂纹。
原料清理时,由于沟槽过深也有可能形成裂纹。
如果裂纹较浅,可以修磨清除,否则则需切除。
(6)结疤。
产生结疤的原因是由于原料表面质量不好,或原料表面原有的结疤没有彻底清除所致。
轻微者可以通过修磨清除,严重者则需 切除。
(7)凸包。
在钢板表面形成有周期的凸起。
其产生原因是轧辊或矫直辊表面破坏,形成凹坑所造成。
如果凸包轻微,可通过修磨清除,而严重时则为不合格产品。
(8)麻点。
麻点是指在钢板表面形成的粗糙表面。
产生原因是由于加热时燃料喷溅侵蚀表面或者是氧化严重而形成的粗糙平面,轻微者可以修磨,严重者则需切除。
加热时应控制好加热炉温度波动与喷油量均匀,防止氧化严重,并加强除鳞。
(9)氧化铁皮压入。
在轧制时由于氧化铁皮没有清除干净,而被压入钢板表面,形成粗糙的平面。
为防止氧化铁皮压入,要加强清除氧化铁皮。
较轻微的氧化铁皮压入可以通过修磨清除,而严重影响质量时则要切除。
(10)划伤。
钢板的划伤是指在钢板的表面留有深浅不等的划道。
纵向划伤多为辊道、导板等部位的不光滑棱角刮伤。
钢板常见质量缺陷

钢材销售业务中经常会碰到客户的质量投诉,业务员需要对其进行仔细的了解、分析、判断,并给予正确的反馈,本人根据工作中的经验,对常用的板材会出现的一些质量问题进行了归纳,供有关人员作参考,如有错误的地方请予指正:冷轧钢板1表面夹杂:表面呈现点状、块状或线条状的非金属夹杂物,沿轧制方向间断或连续分布,其颜色为好棕色、深灰色或白色。
严重时,钢板出现孔洞、破裂、断带。
原因:1)炼钢时造渣不良,钢水粘度大,流动性差,渣子不能上浮,钢中非金属夹杂物多;2)铸温低,沸腾不良,夹杂物未上浮;3)连铸时,保护渣带入钢中;4)钢水罐、钢锭模或注管内的非金属材料未清扫干净。
2介在物:缺陷呈点状,一般色泽与钢带不同,多呈白色、灰白色。
长度不是很长,多存在于钢带的头、屋部,程度严重时即形成剥片、孔洞。
分为闭口状和开口状。
原因是由于炼钢时钢水中有夹杂物,或热轧时钢带表面存在刮痕、凿痕等缺陷,经过冷轧时,在钢带表面即形成点状之痕迹。
3轧入污物:缺陷呈块状,一般呈白色,易集中发生在钢带某段长度。
原因是由于外来物(如衬纸、胶粒)被轧入钢带表面,而形成大面积、块状之缺陷。
4气孔和夹层:切断面上呈上下两层裂纹,但无分离。
原因是由于炼钢、热轧时钢带表面残留有气泡。
5结疤:表面出现不规则的“舌状”、“鱼鳞状”或条状翘起的金属起层,有的与钢板本体相连接,有的与钢板本体不相连,前面叫开口结疤,后者叫闭口结疤,闭口结疤在轧制时易脱落,使板面成为凹坑。
原因:1)炼钢方面:锭模内壁清理不净,横壁掉肉,上注时,钢液飞溅,粘于横壁,发生氧化,铸温低,有时中断注流,继续注钢时,形成翻皮;下注时,保护渣加入不当,造成钢液飞溅;2)轧钢方面:板坯表面残留结疤未清除干净,经轧制后留在钢板上。
6氧化铁皮:缺陷呈点状、条状或鱼鳞状的黑色斑点,分布面积大小不等,压入的深浅不一。
这类铁皮在酸洗工序难于洗尽,当铁皮脱落时形成凹坑。
原因:1)板坯加热温度过高,时间过长;炉内呈强氧化气氛,炉生氧化铁皮轧制时压入;2)高压水压力不足,连轧前氧化铁皮未清除干净;3)高压水喷咀堵塞,局部氧化铁皮未清除;4)集鳞管道打开组数不够,除鳞不干净。
热轧钢板表面缺陷的检测与分析

热轧钢板表面缺陷的检测与分析热轧钢板是一种广泛应用于建筑、汽车制造、机械制造等领域的重要原材料。
然而,在生产过程中,由于各种原因,表面缺陷的出现可能会导致产品质量下降和成本增加。
因此,对热轧钢板表面缺陷的检测与分析显得尤为重要。
一、热轧钢板表面缺陷的类型及对产品的影响热轧钢板表面缺陷主要包括凹坑、麻点、龟裂、氧化皮以及斑纹等。
其中凹坑是表面缺陷中最为常见的一种,其直径通常不超过2mm。
麻点是一种颗粒状的表面缺陷,由于其分布不规则,对产品外观产生明显的影响。
龟裂是一种纵向裂纹,可能会导致磨损、开裂或断裂等问题。
氧化皮是由于表面未被充分清理而形成的一层轻微氧化层,对产品表面的涂层质量产生影响。
斑纹则是一种颜色不均匀的表面缺陷。
这些表面缺陷对产品质量产生的影响主要包括以下几个方面:1. 外观问题:表面缺陷对产品的外观产生明显的影响。
对于一些高端产品来说,外观质量尤为重要,因此表面缺陷自然也成为一个重要的质量指标。
2. 磨损和勾边问题:由于表面缺陷可能会导致产品表面更容易受到磨损,因此,这些表面缺陷也可能会导致产品的使用寿命更短。
3. 性能问题:表面缺陷可能会导致产品的强度、硬度、弯曲性等方面的性能下降,这可能会对产品的应用带来负面影响。
二、热轧钢板表面缺陷的检测方法为了保证产品质量,必须对热轧钢板表面缺陷进行检测。
以下是一些常见的热轧钢板表面缺陷检测方法:1. 眼识法:这是一种非常简单的方法,但是准确性低。
该方法要求对热轧钢板表面进行肉眼观察,以判断是否存在表面缺陷。
这种方法最大的缺点是可能漏检或误判。
2. 磁粉检测法:这种方法通过在表面涂上一种磁性粉末,并通过施加磁场来发现表面缺陷。
该方法可以检测出一些微小的缺陷,但对于一些更深的缺陷或者色素较浅的缺陷则无法做到有效的检测。
3. 磷酸色泽检测法:这种方法通过在热轧钢板表面涂上一种含有钯的磷酸液体,钯会与表面缺陷处的氧化皮反应并产生一种黑色沉淀物,从而揭示出表面缺陷。
钢板常见质量缺陷

带状不光亮痕迹。
钢带表面因油膜破裂,钢带与工作辊直接接触而造成。
乳化液斑
经退火的钢板表面呈现不规则的或小岛状的黑色、褐色图形。
1在轧机出口处乳化液未加尽,加热时碳化,形成斑点;
2末机架出口吹风机压力小,吹不净;
3穿带时风机未开,甩尾时风机关闭;
4装炉后,预吹洗时间不足,加热时乳化液碳化形成斑点
4气刀的缝隙发生局部堵塞;
5气刀局部缺口或损坏;
6板形不好。
边厚(花纹)
镀锌钢带边沿的锌层比中间或其它部分的锌层厚称边厚,一般边部呈条状花纹。
1气刀角度调整不佳;
2边部冷却快;
3当钢带速度低于30米/分以下时,由于喷咀两端的气流向外散失一部分,这样减少了边部气流冲量,造成边部刮锌量比中部小;
4原板板型不好,有边浪;
油焦
轧延油由于氧化在钢带表面形成淡黄色或茶褐色的痕迹。
粘胶
钢带上附有黑色的胶状物体。
锈斑
钢卷运输过程中进海水或雨水,后经冷轧退火后呈一块块的水责状缺陷。
亮度不够
钢带的光泽度不足。
光泽度差异
表面光泽度不同,局部较亮,局部较暗,有时上下表面间的光泽度也会不同。
条纹
沿着钢带表面轧延方向的直线,其色泽与钢带不同。
3连铸时,保护渣带入钢中;
4钢水罐、钢锭模或注管内的非金属材料未清扫干净。
介在物
缺陷呈点状,一般色泽与钢带不同,多呈白色、灰白色。长度不是很长,多存在于钢带的头、屋部,程度严重时即形成剥片、孔洞。分为闭口状和开口状。
由于炼钢时钢水中有夹杂物,或热轧时钢带表面存在刮痕、凿痕等缺陷,经过冷轧时,在钢带表面即形成点状之痕迹。
三、镀锌板
露钢(漏镀)
在镀锌钢带上有露出原钢的黑点或黑块称露钢。这些黑点或黑块未镀上锌,形状不定,大小各异,有时遍班布整个钢带上下表面。
- 1、下载文档前请自行甄别文档内容的完整性,平台不提供额外的编辑、内容补充、找答案等附加服务。
- 2、"仅部分预览"的文档,不可在线预览部分如存在完整性等问题,可反馈申请退款(可完整预览的文档不适用该条件!)。
- 3、如文档侵犯您的权益,请联系客服反馈,我们会尽快为您处理(人工客服工作时间:9:00-18:30)。
钢板常见质量缺陷j及原因分析一、热轧钢板1辊印:是一组具有周期性、大小形状基本一致的凹凸缺陷,并且外观形状不规则。
原因:1)一方面由于辊子疲劳或硬度不够使辊面一部分掉肉边凹;另一方面可能是辊子表面粘有异物,使表面部分呈凸出状;2)轧钢或精整加工时,压入钢板表面形成凹凸缺陷。
2表面夹杂:在钢板表面有不规则的点状块状或车条状的非金属夹杂物,其颜色一般呈红棕色、黄褐色、灰白色或灰黑色。
原因:1)板坯皮下夹杂轧后暴露,或板坯原有的表面夹杂轧后残留在钢板表面上;2)加热炉耐火材料及泥沙等非金属物落在板坯表面上,轧制时压入板面。
3氧化铁皮:氧化铁皮一般粘附在钢板表面,分布于板面的局部或全部,呈黑色或红棕色;铁皮有的疏松脱落,有的压入板面不易脱落;根据外观形状不同有:红铁皮、块状铁皮、条状铁皮、线状铁皮、木纹状铁皮、流星状铁皮、纺锤状铁皮、拖曳状铁皮和散状铁皮等,其压入深度有深有浅。
原因:1)压入氧化铁皮的生成取决于板坯加热条件,加热时间逾长,加热温度愈高,氧化气氛愈强,生成氧化铁皮就愈多,而且不容易脱落,产生一次铁皮难于除尽,轧制时被压入钢板表面上;2)大立辊设定不合理,铁皮未挤松,难于除掉;3)由于高压除鳞水管的水压低,水咀堵塞,水咀角度不对及使用不当等原因,使钢板表面的铁皮没有除尽,轧制后被压入到钢板表面;4)氧化铁皮在沸腾钢中发生较多,在含硅较高的钢中容易产生红铁皮。
4厚薄不均:钢板各部分厚度不一致称厚薄不均,凡厚度不均匀的钢板,一般为偏差过大,局部钢板厚度超过规定的允许偏差。
原因:1)辊缝的调整和辊型的配置不当;2)轧辊和轧辊两侧的轴瓦磨损不一样;3)板坯加热温度不均。
5麻点:钢板表面呈现有局部或连续的凹坑叫麻点,其大小不同,深度不等。
原因是加热过程中,板坯氧化严重,轧制时铁皮压入表面,脱落后形成细小的凹坑。
6气泡:钢板表面上有无规律分布的圆形凸包,有时呈蚯蚓式的直线状,其外缘比较光滑,内有气体;当气泡轧破后,呈现不规则的细裂纹;某些气泡不凸起,经平整后,表面光亮,剪切断面呈分层状。
原因:1)因板坯上存在较多达到气泡气囊类缺陷,经多道轧制没有愈合,残留在钢板上;2)板坯在炉时间长,气泡暴露。
7折迭(折印、折皱、折边、折角):钢板表面有局部互相折合的双层金属称折迭,其外形与裂纹形似,深浅不一,在横截面上一般呈现锐角。
沿轧制方向的直线状折迭称为顺折;垂直于轧制方向的折迭称为横折;边部折迭的称为折边;折迭与折印、折皱的区别主要在于缺陷的形状,程度不同而异,折边、折角程度根据角度大小不同相区别。
横向折迭多发生在薄规格的带钢中。
含碳量小于0.08%的软钢中,因开平机没有安装张力辊易产生折皱。
原因:1)轧件刮伤,轧制时产生折迭,多出现在钢板的下表面;2)立辊挤压过大,辊环啃伤轧件下表面;3)板坯缺陷清理的深宽比过大;4)板坯温度不均匀或精轧轧辊辊型配置不合理及轧制负荷分配不合理等,轧制中的带钢因不均匀变形成大波浪后被压合;5)立辊辊环的挤压或轧件有严重刮伤以及由于粗轧来料有有较大的镰刀弯,对中不良等原因,刮框后再次被轧制成压合;6)卷取机前的侧导板严重磨损出现沟槽,开口度过小,夹送辊缝呈楔形,易使带钢跑偏,在侧导斑沟槽处达到部位被夹送辊压入;7)因故没及时卷取,使卷取温度过低或卷取速度设定不合适;8)钢卷卷边错动,或因钢卷松动,在用吊车上吊,下降落地时易产生折边、折角,此时,常发生在厚度比较薄的钢卷上;9)带钢开卷温度过高,或开卷时的张力及压紧的辊的压力设定不合适。
8塔形(卷边错动):钢卷上下端不齐,一圈比一圈高(或低)称塔形。
卷边上下错动称卷边错动。
原因:1)助卷辊间隙调整不当;2)夹送辊辊缝呈楔形;3)带钢进卷取机时对中不良;4)卷取张力设定不合适;5)成形导板的间隙调整不当;6)卷取机前的侧导板动作时间不同步;7)卷筒与推卷之间有间隙;8)卷筒传动端磨损严重,回转时有较大的离心差;9)带钢有较大的镰刀弯或板形不好。
9松卷:钢卷未卷紧,层与层之间有间隙称松卷。
原因:1)卷取张力设定不合适;2)带钢有严重浪形或因卷取故障,带钢在辊道上有变形;3)钢材屈服强度高,而卷取温度又过低;4)卷取完毕后,因故卷筒打反转;5)捆带未打紧,或捆带断。
10扁卷:钢卷端呈椭圆形称扁卷。
容易发生在较软的或较薄的钢卷中。
原因:1)钢卷在吊运过程中,承受了大冲击;2)钢卷卷的太紧,温度较高,平放在地面上或上面又堆放钢卷。
11镰刀弯:钢板两纵边向同一侧弯曲,形似镰刀。
原因:1)板坯有镰刀弯或严重的厚度不均;2)粗轧、精轧辊磨损程度不均,辊缝间出现楔形;3)轧机两侧温度不均或加热温度不均;4)轧机调整不良,两边压下量不一致;5)立辊的中心线有偏差;6)轧辊发生轴向串动或两侧轴承磨损不均匀;7)侧导板开口度过大,轧件跑偏或轧件对中不好;8)用圆盘剪剪边时,两剪刃重合量不一致。
12楔形:钢板一边厚,一边薄,在钢板有宽度方向的横断面上看,类似楔形,楔形程度有大有小。
原因:1)轧辊磨损严重;2)辊缝调整不合适;3)轧件跑偏;4)轧件温度不均。
13凸度:钢板中间厚,两边薄,从钢板宽度方向的横端面来看,类似弧形,弧形程度有大有小。
原因:1)轧辊严重磨损;2)轧辊的热膨胀的冷却不均;3)辊型设计不合理;4)轧制负荷分配不均,轧辊弹跳变形过大;5)弯辊装置不好;6)加热温度不均或轧件温度不均。
14瓢曲:钢板的纵横部分同时在同一个方向出现的翘曲称瓢曲。
原因:1)钢板两面冷却条件不一致,上下表面温差大;2)轧件温度不均,轧制过程变形不均;3)钢带在轧钢辊道上喷水冷却不均;4)终轧压下率过小;5)钢带在精整时,矫直机压下设定不良,开卷温度过高,压力辊、矫直辊磨损严重。
二、冷轧钢板1表面夹杂:表面呈现点状、块状或线条状的非金属夹杂物,沿轧制方向间断或连续分布,其颜色为好棕色、深灰色或白色。
严重时,钢板出现孔洞、破裂、断带。
原因:1)炼钢时造渣不良,钢水粘度大,流动性差,渣子不能上浮,钢中非金属夹杂物多;2)铸温低,沸腾不良,夹杂物未上浮;3)连铸时,保护渣带入钢中;4)钢水罐、钢锭模或注管内的非金属材料未清扫干净。
2介在物:缺陷呈点状,一般色泽与钢带不同,多呈白色、灰白色。
长度不是很长,多存在于钢带的头、屋部,程度严重时即形成剥片、孔洞。
分为闭口状和开口状。
原因是由于炼钢时钢水中有夹杂物,或热轧时钢带表面存在刮痕、凿痕等缺陷,经过冷轧时,在钢带表面即形成点状之痕迹。
3轧入污物:缺陷呈块状,一般呈白色,易集中发生在钢带某段长度。
原因是由于外来物(如衬纸、胶粒)被轧入钢带表面,而形成大面积、块状之缺陷。
4气孔和夹层:切断面上呈上下两层裂纹,但无分离。
原因是由于炼钢、热轧时钢带表面残留有气泡。
5结疤:表面出现不规则的“舌状”、“鱼鳞状”或条状翘起的金属起层,有的与钢板本体相连接,有的与钢板本体不相连,前面叫开口结疤,后者叫闭口结疤,闭口结疤在轧制时易脱落,使板面成为凹坑。
原因:1)炼钢方面:锭模内壁清理不净,横壁掉肉,上注时,钢液飞溅,粘于横壁,发生氧化,铸温低,有时中断注流,继续注钢时,形成翻皮;下注时,保护渣加入不当,造成钢液飞溅;2)轧钢方面:板坯表面残留结疤未清除干净,经轧制后留在钢板上。
6氧化铁皮:缺陷呈点状、条状或鱼鳞状的黑色斑点,分布面积大小不等,压入的深浅不一。
这类铁皮在酸洗工序难于洗尽,当铁皮脱落时形成凹坑。
原因:1)板坯加热温度过高,时间过长;炉内呈强氧化气氛,炉生氧化铁皮轧制时压入;2)高压水压力不足,连轧前氧化铁皮未清除干净;3)高压水喷咀堵塞,局部氧化铁皮未清除;4)集鳞管道打开组数不够,除鳞不干净。
7欠酸洗:带钢上下表面整个板面呈现条片状、黑灰色条斑,无光泽。
原因:1)热轧带钢各部分温度和冷却速度不同,即沿带钢长度方向的头、中、尾以及沿宽度方面的边部和中部的温度和冷却速度不同,使同一带钢各部分的铁皮结构和厚度不同,一般说,热轧带钢的头、中部比尾部温度高30-50℃,因此,头部铁皮较厚,尾部铁皮较薄,因此,在酸洗速度相同的情况下,易产生局部未洗净;2)酸洗工艺不适当,如酸洗的浓度、温度偏低,酸洗速度太快,酸洗时间不足,或亚铁浓度过高未及时补充酸液等;3)拉伸除鳞机拉伸系数不够,使铁皮未经充分破碎、剥离,影响酸洗效果;4)带钢外形差,如镰刀弯、浪形等,使机械除鳞效果差,易造成局部欠酸洗。
8酸洗不良:表面有大面积点状缺陷,一般呈单面出现,全面性,退火后呈白色,平整后呈黑点状。
原因是热轧钢卷表面氧化不均匀,酸洗退火未完全去除其表面之氧化物。
9碱洗污染:表面呈点状污滓、块状污滓或水痕。
原因是碱洗不良。
10粘结痕:退火钢卷间相互粘合在一起称为粘结,平整后产生点状圆弧折痕是点粘;沿轧制方向呈现成排弧状折痕的是条状粘结;严重的面粘结,平整开卷被撕裂或出现孔洞成为废卷。
原因:1)轧钢卷取张力过大或张力波动,板形不好,造成隆起,在层间压力较大部位产生粘结;2)带钢表面粗糙度太小;3)钢质太软,碳、硅含量少;4热处理炉温过高或退火冷却速度过快;钢卷在装炉前碰撞受伤。
11氧化色:表面被氧化,其颜色由边部的深蓝色逐步过渡到浅蓝色、棕色、淡黄色,统称氧化色。
原因:1)退火时保护罩密封不严或漏气,导致钢卷氧化;2)罩式炉退火工序,高温出炉(钢卷温度大于110℃),导致钢卷氧化;3)保护气体露点过高或氢含量过低,加热前予吹洗时间不足,炉内存在残氧,钢卷在氧化性气氛中退火。
12热烧伤:带状不光亮痕迹。
原因是钢带表面因油膜破裂,钢带与工作辊直接接触而造成。
13乳化液斑:经退火的钢板表面呈现不规则的或小岛状的黑色、褐色图形。
原因:1)在轧机出口处乳化液未加尽,加热时碳化,形成斑点;2)末机架出口吹风机压力小,吹不净;3)穿带时风机未开,甩尾时风机关闭;4)装炉后,预吹洗时间不足,加热时乳化液碳化形成斑点14划伤:表面呈现直而细、深浅不一的沟槽。
平行于轧向,连续或断续,疏密不一,无一定规律,平整前划伤较平滑,沟槽处颜色为灰黑色,平整后划伤,有毛刺,呈金属亮色。
原因:1)酸洗、轧钢、平整、精整各机组与带钢相接触的零件有尖锐棱角或硬物,产生相对运动;2)精整线的各种辊(夹送辊、压紧辊、导板)不运转产生划伤;3)开卷或卷取时,带钢速度变化或层间相对运动。
15折皱:表面呈现凹凸不平的皱折,多发生在小于0.8mm以下的薄板,皱纹边部成一定角度,严重折皱成压褶。
原因:1)带钢跑偏,一边拉伸,另一边产生褶皱;2)板形不良,有大边浪或中间浪,带钢过平整机、矫直机或夹送辊时,有浪形处产生褶皱;3)矫直机调整不当,变形不均造成。
16分层:是基材内部的夹层,这种缺陷不一定出现在表面上,往往表现为单面或双面鼓泡。
原因是热轧时气泡未焊合或焊合不良。