Unit14 limits and tolerances
机械工程专业英语课翻译

Unit1Two methods of designating limit dimensions are considered as standard.One method is the maximum material method in which the large dimension is placed above the smaller dimension for male parts, and the reverse is true for female parts.This method is well suited for small lot quantities because it is likely that the machinist himself may check the dimension of the parts .In so doing he will be verifying initially the large dimension of the male parts and the smaller dimension of the female part.other method is the maximum number method and is preferred by production and quality control departments .In this method of designating a dimension , the large number is always placed above the smaller number ,regardless of whether the part is male or female.两种方法都被看作是指定极限尺寸标准。
一种方法是最大的资料法,大尺寸较小的尺寸摆在上面男性部件,事实正相反对女性的部分。
机械工程专业英语Unit 14
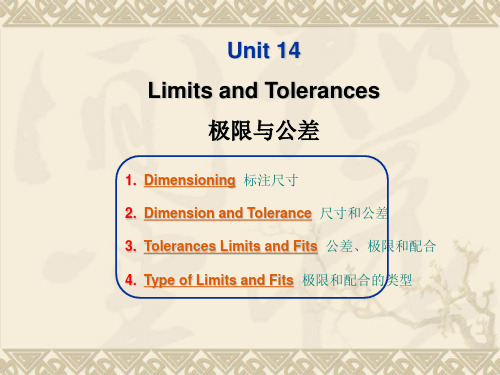
性。因此设计者必须确定单个零件的合适公差以及配合零件装配允许的 正确间隙或过盈量。
2. Dimension and Tolerance 尺寸和公差
➢ Tolerance is the amount of variation permitted in the part or the total variation allowed in a given dimension. 公差是零件允许的变动量或给定 尺寸允许的总变动。
Unit 14 Limits and Tolerances
极限与公差
1. Dimensioning 标注尺寸 2. Dimension and Tolerance 尺寸和公差 3. Tolerances Limits and Fits 公差、极限和配合 4. Type of Limits and Fits 极限和配合的类型
➢ Tolerances may be either unilateral [单边的] or bilateral [双边的].公差 可以是单向的也可以是双向的。
Unilateral tolerance means that any variation is made in only one direction from the nominal or basic dimension. 单向公差意味着任何变动都是 只ห้องสมุดไป่ตู้名义或基本尺寸出发向一 个方向变动的。
1.500 0.003
Bilateral tolerance means
that the tolerance would
vary both over and under the nominal dimension. 它 可以在名义尺寸之上或之下变 化。
中英文翻译(Engineering Tolerance)

英文:Engineering ToleranceIntroductionA solid is defined by its surface boundaries. Designers typically specify a component’s nominal dimensions such that it fulfils its requirements. In reality, components cannot be made repeatedly to nominal dimensions, due to surface irregularities and the intrinsic surface roughness. Some variability in dimensions must be allowed to ensure manufacture is possible. However, the variability permitted must not be so great that the performance of the assembled parts is impaired. The allowed variability on the individual component dimensions is called the tolerance.The term tolerance applies not only to the acceptable range of component dimensions produced by manufacturing techniques, but also to the output of machines or processes. For example , the power produced by a given type of internal combustion engine varies from one engine to another. In practice, the variability is usually found to be modeled by a frequency distribution curve, for example the normal distribution (also called the Gaussian distribution).One of the tasks of the designer is to specify a dimension on a component and the allowable variability on this value that will give acceptable performance.Component TolerancesControl of dimensions is necessary in order to ensure assembly and interchangeability of components. Tolerances are specified on critical dimensions that affect clearances and interferences fits. One method of specifying tolerances is to state the nominal dimension followed by the permissible variation, so a dimension could be stated as 40.000mm ± 0.003mm.This means that the dimension should be machined so that it is between 39.997mm and 40.003mm.Where thevariation can vary either side of the nominal dimension, the tolerance is called a bilateral tolerance. For a unilateral tolerance, one tolerance is zero, e.g. 40+0.006 .0.000Most organizations have general tolerances that apply to dimensions when an explicit dimension is not specified on a drawing. For machined dimensions a general tolerance may be ±0.5mm. So a dimension specified as 15.0mm may range between 14.5mm and 15.5mm. Other general tolerances can be applied to features such as angles, drilled and punched holes, castings,forgings, weld beads and fillets.When specifying a tolerance for a component, reference can be made to previous drawings or general engineering practice. Tolerances are typically specified in bands as defined in British or ISO standards.Standard Fits for Holes and ShaftsA standard engineering ask is to determine tolerances for a cylindrical component, e.g. a shaft, fitting or rotating inside a corresponding cylindrical component or hole. The tightness of fit will depend on the application. For example, a gear located onto a shaft would require a “tight” interference fit, where the diameter of the shaft is actually slightly greater than the inside diameter of the gear hub in order to be able to transmit the desired torque. Alternatively, the diameter of a journal bearing must be greater than the diameter of the shaft to allow rotation. Given that it is not economically possible to manufacture components to exact dimensions, some variability in sizes of both the shaft and hole dimension must be specified. However, the range of variability should not be so large that the operation of the assembly is impaired. Rather than having an infinite variety of tolerance dimensions that could be specified, national and international standards have been produced defining bands of tolerances. To turn this information into actual dimensions corresponding tables exist,defining the tolerance levels for the size of dimension under consideration.Size:a number expressing in a particular unit the numerical value of a dimension.Actual size:the size of a part as obtained by measurement.Limits of size:the maximum and minimum sizes permitted for a feature.Maximum limit of size the greater of the two limits of size.Minimum limit of size:the smaller of the two limits of size.Basic size:the size by reference to which the limits of size are fixed.Deviation:the algebraic difference between a size and the corresponding basic size.Actual deviation:the algebraic difference between the actual size and the corresponding basic size.Upper deviation:the algebraic difference between the maximum limit of size and the corresponding basic size.Lower deviation:the algebraic difference between the minimum limit of size and the corresponding basic size.Tolerance:the difference between the maximum limit of size and the minimum limit of size.Shaft:the term used by convention to designate all external features of a part.Hole:the term used by convention to designate all internal features of a part.Heat Treatment of MetalThe generally accepted definition for heat treating metals and metal alloys is “heating and cooling a solid metal or alloy in a way so as to obtain specific conditions and I or properties.”Heating for the sole purpose of hot working(as in forging operations) is excluded from this definition.Likewise,the types of heat treatment that are sometimes used for products such as glass or plastics are also excluded from coverage by this definition.Transformation CurvesThe basis for heat treatment is the time-temperature-transformation curves or TTT curves where,in a single diagram all the three parameters are plotted.Becauseof the shape of the curves,they are also sometimes called C-curves or S-curves.To plot TTT curves,the particular steel is held at a given temperature and the structure is examined at predetermined intervals to record the amount of transformation taken place.It is known that the eutectoid steel (T80) under equilibrium conditions contains,all austenite above 723℃,whereas below,it is pearlite.To form pearlite,the carbon atoms should diffuse to form cementite.The diffusion being a rate process,would require sufficient time for complete transformation of austenite to pearlite .From different samples,it is possible to note the amount of the transformation taking place at any temperature.These points are then plotted on a graph with time and temperature as the axes.Classification of Heat Treating ProcessesIn some instances,heat treatment procedures are clear cut in terms of technique and application.whereas in other instances,descriptions or simple explanations are insufficient because the same technique frequently may be used to obtain different objectives .For example, stress relieving and tempering are often accomplished with the same equipment and by use of identical time and temperature cycles.The objectives,however,are different for the two processes .The following descriptions of the principal heat treating processes are generally arranged according to their interrelationships.Normalizing consists of heating a ferrous alloy to a suitable temperature (usually 50°F to 100 °F or 28 ℃to 56℃) above its specific upper transformation temperature. This is followed by cooling in still air to at least some temperature well below its transformation temperature range.For low-carbon steels.the resulting structure and properties are the same as those achieved by full annealing ;for most ferrous alloys, normalizing and annealing are not synonymous.Normalizing usually is used as a conditioning treatment, notably for refining the grain of steels that have been subjected to high temperatures for forging or other hot working operations.The normalizing process usually is succeededby another heat treating operation such as austenitizing for hardening, annealing,or tempering.Annealing is a generic term denoting a heat treatment that consists of heating to and holding at a suitable temperature followed by cooling at a suitable rate.It is used primarily to soften metallic materials,but also to simultaneously produce desired changes in other properties or in microstructure.The purpose of such changes may be,but is not confined to, improvement of machinability, facilitation of cold work ( known as in-process annealing),improvement of mechanical or electrical properties, or to increase dimensional stability.When applied solely to relieve stresses, it commonly is called stress-relief annealing, synonymous with stress relieving.When the term “anneali ng is applied to ferrous alloys without qualification, full annealing is implied.This is achieved by heating above the alloy’s transformation temperature,then applying a cooling cycle which provides maximum softness.This cycle may vary widely, depending on composition and characteristics of the specific alloy.Quenching is the rapid cooling of a steel or alloy from the austenitizing temperature by immersing the workpiece in a liquid or gaseous medium.Quenching media commonly used include water,5% brine,5% caustic in an aqueous solution,oil,polymer solutions,or gas(usually air or nitrogen).Selection of a quenching medium depends largely on the hardenability of the material and the mass of the material being treated(principally section thickness).The cooling capabilities ofthe above-listed quenching media vary greatly.In selecting a quenching medium, it is best to avoid a solution that has more cooling power than is needed to achieve the results,thus minimizing the possibility of cracking and warp of the parts being treated.Modifications of the term quenching include direct quenching,fog quenching,hot quenching,interrupted quenching selective quenching,spray quenching, and time quenching.Tempering .In heat treating of ferrous alloys ,tempering consists of reheating the austenitized and quench-hardened steel or iron to some preselected temperature that is below the lower transformation temperature (generally below 1300°F or 705℃) .Tempering offers a means of obtaining various combinations of mechanical properties.Tempering temperatures used for hardened steels are often no higher than 300°F (150℃).The term “tempering”should not be confused with either process annealing or stress relieving.Even though time and temperature cycles for the three processes may be the same,the conditions of the materials being processed and the objectives may be different.Stress Relieving.Like tempering, stress relieving is always done by heating to some temperature below the lower transformation temperature for steels and irons .For nonferrous metals,the temperature may vary from slightly above room temperature to several hundred degrees,depending on the alloy and the amount of stress relief that is desired.The primary purpose of stress relieving is to relieve stresses that have been imparted to the workpiece from such processes as forming, rolling,machining or welding.The usual procedure is to heat workpieces to the pre-established temperature long enough to reduce the residual stresses (this is a time-and temperature-dependent operation) to an acceptable level;this is followed by cooling at a relatively slow rate to avoid creation of new stresses.Introduction to CAD/CAMThroughout the history of our industrial society, many inventions have been patented and whole new technologies have evolved. Perhaps the single development that has impacted manufacturing more quickly and significantly than any previous technology is the digital computer. Computers are being used increasingly for both design and detailing of engineering components in the drawing office.Computer-aided design (CAD) is defined as the application of computers and graphics software to aid or enhance the product design from conceptualizationto documentation. CAD is most commonly associated with the use of an interactive computer graphics system, referred to as a CAD system. Computer-aided design systems are powerful tools and are used in the mechanical design and geometric modeling of products and components.There are several good reasons for using a CAD system to support the engineering design function:⑴To increase the productivity⑵To improve the quality of the design⑶To uniform design standards⑷To create a manufacturing data base⑸To eliminate inaccuracies caused by hand-copying of drawingsand inconsistency between drawingsComputer-aided manufacturing (CAM) is defined as the effective use of computer technology in manufacturing planning and control. CAM is most closely associated with functions in manufacturing engineering, such as process and production planning, machining, scheduling, management, quality control, and numerical control (NC) part programming. Computer-aided design and computer-aided manufacturing are often combined into CAD/CAM systems.This combination allows the transfer of information from the design stage into the stage of planning for the manufacturing of a product, without the need to reenter the data on part geometry manually. The database developed during CAD is stored; then it is processed further, by CAM, into the necessary data and instructions for operating an controlling production machinery, material-handling equipment, and automated testing and inspection for product quality.Rationale for CAD/CAMThe rationale for CAD/CAM is similar to that used to justify any technology-based improvement in manufacturing. It grows out of a need to continually improve productivity, quality and competitiveness. There are also other reasons why a company might make a conversion from manual processes toCAD/CAM:⑴Increased productivity⑵Better quality⑶Better communication⑷Common database with manufacturing⑸Reduced prototype construction costs⑹Faster response to customersCAD/CAM HardwareThe hardware part of a CAD/CAM system consists of the following components:(1) one or more design workstations,(2) digital computer, (3) plotters, printers and other output devices, and (4) storage devices. In addition, the CAD/CAM system would have a communication interface to permit transmission of data to and from other computer systems, thus enabling some of the benefits of computer integration.The workstation is the interface between computer and user in the CAD system. The design of the CAD workstation and its available features have an important influence on the convenience, productivity, and quality of the user’s output. The workstation must include a graphics display terminal and a set of user input devices. CAD/CAM applications require a digital computer with a high-speed control processing unit (CPU). It contains the main memory and logic/arithmetic section for the system. The most widely used secondary storage medium in CAD/CAM is the hard disk, floppy diskette, or a combination of both.Input devices are generally used to transfer information from a human or storage medium to a computer where “CAD functions” are carried out. There are two basic approaches to input an existing drawing:model the object on a drawing or digitize the drawing. The standard output device for CAD/CAM is a CRT display. There are two major types of CRT displays: random-scan-line-drawing displays and raster-scan displays. In addition to CRT, there are also plasma paneldisplays and liquid-crystal displays.CAD/CAM SoftwareSoftware allows the human user to turn a hardware configuration into a powerful design and manufacturing system. CAD/CAM software falls into two broad categories, 2-D and 3-D, based on the number of dimensions visible in the finished geometry. CAD packages that represent objects in two dimensions are called 2-D software. Early systems were limited to 2-D. This was a serious shortcoming because 2-Drepresentations of 3-Dobjects is inherently confusing. Equally problem has been the inability of manufacturing personnel to properly read and interpret complicated 2-D representations of objects. 3-D software permits the parts to be viewed with the three-dimensional planes-height, width, and depth-visible. The trend in CAD/CAM is toward 3-D representation of graphic images. Such representations approximate the actual shape and appearance of the object to be produced; therefore, they are easier to read and understand.Applications of CAD/CAMThe emergence of CAD/CAM has had a major impact on manufacturing, by standardizing product development and by reducing design effort, tryout, and prototype work; it has made possible significantly reduced costs and improved productivity.Numerical ControlNumerical control (NC) is a form of programmable automation in which the processing equipment is controlled by means of numbers,letters,and other symbols.The numbers,letters,and symbols are coded in an appropriate format to define a program of instructions for a particular workpart or job. Theinstructions are provided by either of the two binary coded decimal systems: the Electronic Industries Association (EIA) code, or the American Standard Code for Information Interchange (ASCII). ASCII-coded machine control units will not accept EIA coded instructions and vice versa. Increasingly, however, control units are being made to accept instructions in either code. Automation operation by NC is readily adaptable to the operation of all metalworking machines. Lathes, milling machines, drill presses, boring machines, grinding machines, turret punches, flame or wire-cutting and welding machines, and even pipe benders are available with numerical controls.Basic Components of NCA numerical control system consists of the following three basic components:(1) Program instructions(2) Machine control unit(3) Processing equipmentThe program instructions are the detailed step by step commands that direct the processing equipment In its most common form,the commands refer to positions of a machine tool spindle with respect to the worktable on which the part is fixed.More advanced instructions include selection of spindle speeds,cutting tools,and other functions.The machine control unit (MCU) consists of the electronics and control hardware that reads and interprets the program of instructions and convert it into mechanical actions of the machine tool or other processing equipment .The processing equipment is the component that performs metal process.In the most common example of numerical control ,it is used to perform machining operations. The processing equipment consists of the worktable and spindle as well as the motors and controls needed to drive them.Types of NCThere are two basic types of numerical control systems:point to point and contouring .Point to point control system, also called positioning, are simpler than contouring control system.Its primary purpose is to move a tool or workpiece from one programmed point to another. Usually the machine function,such as a drilling operation,is also activated at each point by command from the NC Program.Point to point systems are suitable for hole machining operations such as drilling, countersinking,counterboring,reaming,boring and tapping. Hole punching machines,spotwelding machines,and assembly machines also use point to point NC systems.Contouring system,also known as the continuous path system,positioning and cutting operations are both along controlled paths but at different velocities.Because the tool cuts as it travels along a prescribed path ,accurate control and synchronization of velocities and movements are important.The contouring system is used on lathes,milling machines,grinders,welding machinery,and machining centers.Movement along the path,or interpolation, occurs incrementally,by one of several basic methods .There are a number of interpolation schemes that have been developed to deal with the various problems that are encountered in generating a smooth continuous path with a contouring type NC system.They include linear interpolation, circular interpolation, helical interpolation, parabolic interpolation and cubic interpolation. In all interpolations,the path controlled is that of the center of rotation of the tool.Compensation for different tools,different diameter tools,or tools wear during machining,can be made in the NC program.Programming for NCA program for numerical control consists of a sequence of directions that causes an NC machine to carry out a certain operation ,machining being the most commonly used process .Programming for NC may be done by aninternal programming department,on the shop floor,or purchased from an outside source.Also,programming may be done manually or with computer assistance.The program contains instructions and commands.Geometric instructions pertain to relative movements between the tool and the workpiece. Processing instructions pertain to spindle speeds,feeds,tools,and so on.Travel instructions pertain to the type of interpolation and slow or rapid movements of the tool or worktable.Switching commands pertain to on/off position for coolant supplies,spindle rotation,direction of spindle rotation tool changes,workpiece feeding,clamping,and so on. The first NC programming language was developed by MIT developmental work on NC programming systems in the late 1950s and called APT(Automatically Programmed Tools).DNC and CNCThe development of numerical control was a significant achievement in batch and job shop manufacturing,from both a technological and a commercial viewpoint.There have been two enhancements and extensions of NC technology,including:(1) Direct numerical control(2) Computer numerical controlDirect numerical control can be defined as a manufacturing system in which a number of machines are controlled by a computer through direct connection and in real time.The tape reader is omitted in DNC,thus relieving the system of its least reliable component.Instead of using the tape reader,the part program is transmitted to the machine tool directly from the computer memory.In principle,one computer can be used to control more than 100 separate machines.(One commercial DNC system during the l970s boasted a control capability of up to 256 machine tools.) The DNC computer is designed to provide instructions to each machine tool on demand .When the machine needs control commands ,they are communicated to it immediately.Since the introduction of DNC ,there have been dramatic advances in computer technology.The physical size and cost of a digital computer has been significantly reduced at the same time that its computational capabilities have been substantially increased.In numerical control,the result of these advances has been that the large hard-wired MCUs of conventional NC have been replaced by control units based on the digital computer.Initially,minicomputers were utilized in the early 1970s .As further miniaturization occurred in computers ,minicomputers were replaced by today’s microcomputers.Computer numerical control is an NC system using dedicated microcomputer as the machine control unit .Because a digital computer is used in both CNC and DNC,it is appropriate to distinguish between the two types of system.There are three principal differences:(1) DNC computers distribute instructional data to,and collect data from, a large number of machines.CNC computers control only one machine,or a small number of machines.(2) DNC computers occupy a location that is typically remote from the machines under their control. CNC computer are located very near their machine tools.(3) DNC software is developed not only to control individual pieces of production equipment, but also to serve as part of a management information system in the manufacturing sector of the firm. CNC software is developed to augment the capabilities of a particular machine tool.中文翻译:工程公差引言固体由其表面边界确定界限。
国际商务函电(第二版)unit14 Complaints and Claims
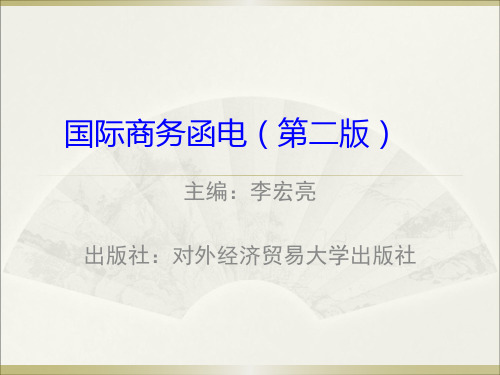
Part III Key Sentence Patterns
1. We received the order No. 456 last week. 2. We have received our order No.0990 for digital cameras. 3. We require you refund the invoice amount and inspection fee of the goods amounting to RMB 3,000,000.00. 4. In support of our claim, we will send you a survey report issued by CIQ. 5. All the expenses will be for you account. 6. On opening the cases we noticed that we had received the wrong goods. 7. Please advise us when we can expect to receive our order.
In the international trade, complaints and claims often happens because of shortage of quantity, the delivery of wrong goods, the delivery of damaged or defective merchandise or delay of delivery and improper packing, etc. After receiving the complaints or claims, the seller will make immediate investigations and settle the problem as soon as possible. That is called the adjustment.
Unit 14 Complaints and Claims《外贸英语函电》PPT课件
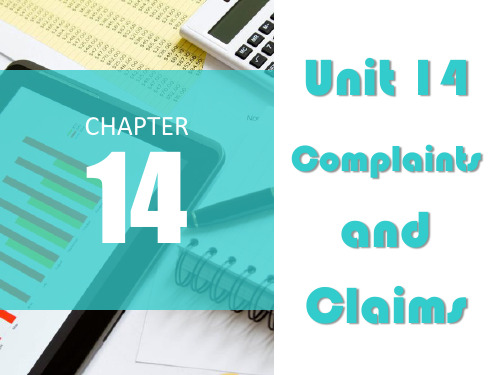
replacement.
If the delay is very long,the buyer may cancel the order,
and there may be a great loss to the supplier and the buyer.
from delay.
Text A
Complaints about damage are usually the business of insurance
companies,but if the damage is caused by the negligence of
the packer,then the insurance companies will not take
clearly does not match the samples you left with us.
The printed shirting complained about is part of the batch of
100 pieces of 50 yards supplied to our order No.AD-190 of May
as possible.
Bad,inferior or inadequate packing may cause damage to goods
in transit.The buyer may accept damaged goods if the supplier
offers a discount,but if the goods are badly damaged,they
Unit-14-教学参考

Get familiar with the words and expressions listed below, and then complete each of the following sentences with a proper word from the list.多孔的,漏洞多的骨质减少鉴定,识别密度,浓度生育,分娩双膦酸盐类药物阿仑膦酸钠片碳酸钙伊班膦酸钠片甲状旁腺素骨折,破裂骨裂粉碎性骨折弓形骨折绿枝性骨折复合骨折头昏眼花的使人眩晕的,引起头晕的威胁生命的金属固定板固定用敷料,石膏夹板筛查最初的,开始的老年保健医疗更年期,绝经期重申反复灌输关键的,决定性的限额,折扣自体免疫的不确定的,不能使人信服的矛盾的不足的,缺乏的大剂量著名的,杰出的,突出的适当的,恰当的肾结石1.Autoimmune disorders are conditions in which a person’s immune system attack s the body’s own cells, causing tissue destruction.2. A fracture usually results from traumatic injury to a bone, causing thecontinuity of bone tissues or bony cartilage to be disrupted or broken.3. The government should be playing a more prominent role in healthpromotion.4. I keep getting contradictory advice - some people tell me to keep itwarm and some tell me to put ice on it.5. If he doesn’t eat something at lunchtime he will start to feel lightheaded by mid-afternoon.6. Initial reports say that seven people have died, though this has not yetbeen confirmed.7. A diet deficient in vitamin D may cause the disease rickets.8. A life-threatening disease is a very serious one that can cause death.9. Identification of osteoporosis and osteopenia is made by measuring the mineral density of a person’s bones.10. Doctors urge more older women to be screened for osteoporosis.11. A bone density test done on older women measures the risk ofgetting osteoporosis.12. The medical tests were inconclusive, and will need to be repeated.13. The baggage allowance for most flights is 20 kilos.14. The survey is only concerned with women of childbearing age.15. Modern scientific techniques have made it possible for a womanpast menopause to have a baby.Write down three questions you find interesting to explore on the topic “Bone Health”. The first two questions are given as a prompt. Discuss brieflyeach of them with your deskmates.1. What major functions do our bones have?2. What risk factors affect bone health?3. _______________________________________________4. _______________________________________________5. _______________________________________________Listen to a passage three times and while listening, you are to put the missing word in each numbered blank according to what you hear.The word osteoporosis means porous bones, or bones that are not (1) solid enough. The disease harms bones by removing calcium and other (2) minerals from tissue. The National Osteoporosis Foundation says eight of every ten osteoporosis patients are women.Before people (3) develop osteoporosis, they have a condition called osteopenia. Treatment can (4) prevent this condition from becoming osteoporosis. Doctors agree that the best way to deal with osteopenia or osteoporosis is to find and treat it before the disease (5) progresses. Bone damage need not be permanent. Drugs can help replace lost bone.(6) Identification of osteoporosis and osteopenia is made by measuring the mineral density of a person’s bones. In this ca se, density means the (7) strength of the bones.Differences in bone mineral density among body parts are most often found in women who recently ended their (8) childbearing years. The density may be normal at one place but low at another. Bone mineral density in the (9) spine decreases first. A woman’s bone mineral density becomes about the same in all parts of her body after she is 70 years old.Doctors who treat osteoporosis patients say physical exercise can help the bones. For active people, (10)lifting weights or playing tennis, slow running and dancing can be helpful.Several kinds of drugs treat osteoporosis. America’s Mayo Clinic medical centers say bisphosphonates are the most popular. Fosamax, Actonel and Boniva are (11) products of this family of drugs. The Mayo Clinic advises that these drugs are very effective and appear safe for most people if taken as (12) directed.Listen to a passage “Fracture” twice. While listening, you are to give an answer as short as possible to each of the questions below.1. What kind of fracture is it when a bone is broken in more than two places?A comminuted fracture.2. What kind of fracture is it when the bone breaks the skin?An open or compound fracture.3. What happens to people if they are seriously injured?People can go into shock.4. Why should broken bones be treated quickly?They can restrict blood flow or cause nerve damage.5. Why in some cases is a splint, instead of casts, put around the area of the break?To restrict movement.Listen to each sentence, repeat it aloud, listen to it again, and then write down the whole sentence on the space provided. You will listen to each sentence for a third time to have a check.1. Along with the bone damage there is a risk of infection in the openwound.2. While broken bones can be painful, they are generally not life-threatening.3. People who are seriously injured can go into shock. They might feel cold, dizzy and unable to think clearly.4. Broken bones should be treated quickly because they can restrict blood flow or cause nerve damage.5. X-rays are taken to see the break. Treatment depends on the kind of fracture that is identified.Watch a video clip “Bone Density Test” twice and decide whether each of the statements below is TRUE (T) or FALSE(F)._T_ _T_ _F_ _F_ 1. Osteoporosis is the hidden danger that millions of women face as they age.2. A bone density test measures the risk of gettingosteoporosis.3. According to a new study, women with healthy bones need to be tested as often as they have been.4. Dr. Ethel Cyrus emphasizes the importance ofgetting a bone density test every year after theage of 65._F__T_ _F_ 5. The bone starts to thin after menopause aroundage 50 so it is worth the money to test most women at this age. 6. A good thing to do for bone health is getting enough calcium.7. Frequent follow-up scans can be dangerous forwomen with thinning bones.Watch a video clip “Bone Health and Calcium Supplements” twice and choose the best answer to each of the questions below.1. Which of the following statement is TRUE of a new report from theInstitute of Medicine?A) It says women need more calcium to keep their bones healthy.B) It says much of what has been told about vitamin D is a myth.C) It has been hammered into ma ny healthy women’s heads.D) It says women need more vitamin D rather than calcium.2. The report holds a surprise that _______.A) calcium is added to everythingB) there is no debate over vitamin DC) both calcium and vitamin D are criticalD) many peop le don’t need calcium supplements3. It is mentioned that vitamin D might lower the risk of thefollowingEXCEPT _______.A) heart diseaseB) various cancersC) respiratory diseases D) autoimmune disorders4. The panel found most people ______.A) get vitamin D from supplementsB) worry they are vitamin D deficientC) get enough vitamin D from their dietD) need to take extra vitamin D supplement5.For some people, the studies about vitamin supplements are _______.A) confusing B) convincingC) appropriate D) specificKey to Task 71. B2. D3. C4. C5. AListen to the five sentences twice and interpret each into Chinese.1. The word osteoporosis means porous bones, or bones that are not solid enough. The disease harms bones by removing calcium骨质疏松这个词的意思是多孔的骨头,或骨骼不够坚实。
Lesson 32 Limits and Tolerances 机械工程专业英语 教学课件

机械工程专业英语
常州工学院机电工程学院
徐红丽
机械工程专业英语
Lesson 32 Limits and Tolerances
一、预备知识 Fixture
A fixture is a workholding or support device used in the manufacturing industry. What makes a fixture unique is that each on is built to fit a particular part or shape. The main purpose of a fixture is to locate and in some cases hold a workpiece during either a machining operation or some other industrial process. A jig differs from a fixture in that it guides the tool to its correct position in addition to locating and supporting the workpiece.
预备知识
机械工程专业英语
Lesson 32 Limits and Tolerances 一、预备知识 The primary purposes of jigs and fixtures is to: Reduce the cost of production Maintain consistent quality Maximize efficiency Enable a variety of parts to be made to correct specifications
外贸英语对话(第四版)UNIT 14 Claims (II)
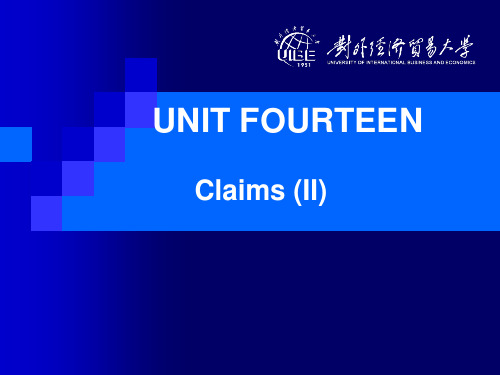
B: (Studying the photos) This is most unfortunate. Our manufacturers have always attached great importance to the quality of their products. But maybe the rust stains are due to dampness at sea. If that’s the case, the liability should rest with the insurance people. A: Our experts hold the opinion that the rust stains are not due to dampness but to poor workmanship. Please look at the picture. They surely prove that the derusting of the roller before plating was not thoroughly done.
3. to take up
Shall we take up the items one by one? I hope to take up the question of quantity after we’ve settled the price.
University of International Business and Economics
Answer Key-translation
A: Mr. Tom, we would like to have you help straighten out the trouble concerning the rollers for the rolling mill. B: Of course, can you give me the facts? A: We have here a copy of the inspection certificate issued by the Tianjin Entry-Exit Inspection and Quarautine Bureau and a set of photos. The inspection certificate states that the rollers were found rusty when they were unpacked and the photos taken on the spot back up the findings.
- 1、下载文档前请自行甄别文档内容的完整性,平台不提供额外的编辑、内容补充、找答案等附加服务。
- 2、"仅部分预览"的文档,不可在线预览部分如存在完整性等问题,可反馈申请退款(可完整预览的文档不适用该条件!)。
- 3、如文档侵犯您的权益,请联系客服反馈,我们会尽快为您处理(人工客服工作时间:9:00-18:30)。
DimensioningThe design of a machine includes many factors other than those of determining the loads and stresses and selecting the proper materials. Before construction or manufacture can begin, it is necessary to have complete assembly and detail drawings to convey all necessary information to the shop men. The designer frequently is called upon to check the drawings before they are sent to the shop. Much experience and familiarity with manufacturing processes are needed before one can become conversant with all phase s of production drawings. [1]Drawings should be carefully checked to see that the dimensioning is done in a manner that will be most convenient and understandable to the production departments. It is obvious that a drawing should be made in such a way that it has one and only one interpretation. In particular, shop personnel should not be required to make trigonometric or other involved calculations before the production machines can be set up. [2]Dimensioning is an involved subject and long experience is required for its mastery. [3]Tolerance s must be placed on the dimensions of a drawing to limit the permissible variation s in size because it is impossible to manufacture a part exactly to a given dimension. Although small tolerances give higher quality work and a better operating mechanism, the cost of manufacture increases rapidly as the tolerances are reduced, as indicated by the typical curve of Fig 14.1. It is therefore important that the tolerances be specified at the largest values that the operating or functional considerations permit.Tolerances may be either unilateral or bilateral. In unilateral dimensioning, one tolerance is zero, and all the variations are given by the other tolerance. In bilateral dimensioning, a mean dimension is used which extends to the midpoint of the tolerance zone with equal plus and minus variations extending each way from this dimension.The development of production processes for large-volume manufacture at low cost has been largely dependent upon interchangeability of component parts. Thus the designer must determine both the proper tolerances for the individual parts, and the correct amount of clearance or interference to permit assembly with the mating parts. The manner of placing tolerances on drawings depends somewhat on the kind of product or type of manufacturing process. If the tolerance on a dimension is not specifically stated, the drawing should contain a blanket note which gives the value of the tolerance for such dimensions. [4] However, some companies do not use blanket notes on the supposition that if each dimension is considered individually, wider tolerances than those called for in the note could probably be specified. [5] In any event it is very important that a drawing be free from ambiguities and be subject only to a single interpretation.Dimension and ToleranceIn dimensioning a drawing, the numbers placed in the dimension lines represent dimension that are only approximate and do not represent any degree of accuracy unless so stated by the designer. [6] To specify a degree of accuracy, it is necessary to add tolerance figure s to the dimension. Tolerance is the amount of variation permitted in the part or the total variation allowed in a given dimension. A shaft might have a nominal size of 2.5 in. (63.5 mm), but for practical reasons this figure could not be maintain ed in manufacturing without great cost. Hence, a certain tolerance would be added and, if a variation of±0.003 in. (±0.08 mm) could be permitted, the dimension would be stated 2.500±0.003 (63.5±0.08 mm).Dimensions given close tolerance s mean that the part must fit properly with some other part. Both must be given tolerances in keeping with the allowance desired, the manufacturing processes available, and the minimum cost of production and assembly that will maximize profit. Generally speaking, the cost of a part goes up as the tolerance is decreased. If a part has several or more surfaces to be machined, the cost can be excessive when little deviation is allowed from the nominal size. Allowance, which is sometimes confused with tolerance, has an altogether different meaning. [7] It is the minimum clearance space intended between mating parts and represents the condition of tightest permissible fit. If a shaft, size, is to fit a hole of size l.500±, the minimum size hole is l. 500 and .1000.0003.0+-498the maximum size shaft is l. 498. Thus the allowance is 0. 002 and the maximum clearance is 0.008 as based on the minimum shaft size and maximum hole dimension. Tolerances may be either unilateral or bilateral. Unilateral tolerance means that any variation is made in only one direction from the nominal or basic dimension. Referring to the previous example, the hole is dimensioned l.500±, which represents a unilateral tolerance. If the dimensions were given as l.500±0.003, the tolerance would be bilateral; that is, it would vary both over and under the nominal dimension. The unilateral system permits changing the tolerance while still retain ing the same allowance or type of fit. With the bilateral system, this is not possible without also changing the nominal size dimension of one or both of the two mating pats. In mass production, where mating parts must be interchangeable, unilateral tolerances are customary. To have an interference or force fit between mating parts, the tolerances must be such as to create a zero or negative allowance. Tolerances, Limits and FitsThe drawing must be a true and complete statement of the designer’s requirements expressed in such a way that the part is convenient to manufacture. Every dimension necessary to define the product must be stated once only and not repeated in different views. Dimensions relating to one particular feature, such as the position and size of a hole, should, where possible, appear on the same view.There should be no more dimensions than are absolutely necessary, and no feature should be located by more than one dimension in any direction. [8] It may be necessary occasionally to give an auxiliary dimension for reference, possibly for inspection. When this is so, the dimension should be enclosed in a bracket and mark ed for reference. Such dimensions are not govern ed by general tolerances. [9]Dimensions that affect the function of the part should always be specified and not left as the sum or difference of other dimensions. If this is not done, the total permissible variation on that dimension will form the sum or difference of the other dimensions and their tolerances, and this will result in these tolerances having to be made unnecessarily tight. [10] The overall dimension should always appear. All dimensions must be governed by the general tolerance on the drawing unless otherwise stated. Usually, such a tolerance will be governed by the magnitude of the dimension. Specific tolerances must always be stated on dimensions affecting function or interchangeability.A system of tolerances is necessary to allow for the variations in accuracy that are bound to occur during manufacture, and still provide for interchangeability and correct function of the part.A tolerance is the difference in a dimension in order to allow for unavoidable imperfections in workmanship. The tolerance range will depend on the accuracy of the manufacturing organisation, the machining process and the magnitude of the dimension. The greater the tolerance range, the cheaper the manufacturing process.A bilateral tolerance is one where the tolerance range is disposed on both sides of the nominal dimension. A unilateral tolerance is one where the tolerance zone is on one side only of the nominal dimension, in which case the nominal dimension may form one of the limits.Limits are the extreme dimensions of the tolerance zone. For example, nominal dimension30 mm tolerance ± limits ±Fits depend on the relationship between the tolerance zones of two mating parts, and may be broadly classified into a clearance fit with positive allowance, a transition fit where the allowance may be either positive or negative (clearance or interference), an interference fit where the allowance is always negative. Type of Limits and FitsThe ISO System of Limits and Fits, widely used in a number of leading metric countries, is considerably more complex than the ANSI system.In this system, each part has a basic size. Each limit of size of a part, high and low, is defined by its deviation from the basic size, the magnitude and sign being obtained by subtracting the basic size from the limit in question. The difference between the two limits of size of a part is called the tolerance, an absolute amount without sign.There are three classes of fits: 1) clearance fits, 2) transition fits (the assembly may have either clearance or interference), and 3) interference fits. Either a shaft-basis system or a hole-basis system may be used. For any given basic size, a range of tolerances and deviations may be specified with respect to the line of zero deviation, called the zero line. The tolerance is a function of the basic size and is designated by a number symbol, called the grade——thus the tolerance grade. The position of the tolerance with respect to the zero line also a function of the basic size——is indicated by a letter symbol (or two letters), a capital letter for holes and a lowercase letter for shafts. Thus the specificationfor a hole and shaft having a basic size of 45mm might be 45 H8/g7.Twenty standard grades of tolerances are provided, called IT 01, IT 0, IT l - 18, providing numerical values for each nominal diameter, in arbitrary steps up to 500 mm (for example 0 - 3, 3 - 6, 6 - 10, …, 400 - 500 mm). [11] The value of the tolerance unit, i, for grades 5 - 16 isi = ……where i is in microns and D in millimeters.Standard shaft and hole deviations similarly are provided by sets of formulas, however, for practical application, both tolerances and deviations are provided in three sets of rather complex tables. Additional tables give the values for basic sizes above 500 mm and for “Commonly Used Shafts and Holes” in two categories ——“General Purpose” and “Fine Mechanisms and Horology”.。