复合材料加工研究进展
三维立体织物复合材料研究与进展
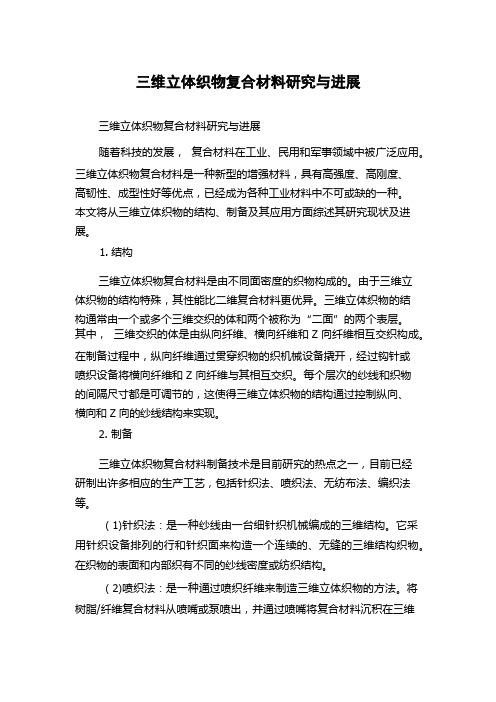
三维立体织物复合材料研究与进展随着科技的发展,复合材料在工业、民用和军事领域中被广泛应用。
三维立体织物复合材料是一种新型的增强材料,具有高强度、高刚度、高韧性、成型性好等优点,已经成为各种工业材料中不可或缺的一种。
本文将从三维立体织物的结构、制备及其应用方面综述其研究现状及进展。
1. 结构三维立体织物复合材料是由不同面密度的织物构成的。
由于三维立体织物的结构特殊,其性能比二维复合材料更优异。
三维立体织物的结构通常由一个或多个三维交织的体和两个被称为“二面”的两个表层。
其中,三维交织的体是由纵向纤维、横向纤维和Z 向纤维相互交织构成。
在制备过程中,纵向纤维通过贯穿织物的织机械设备撬开,经过钩针或喷织设备将横向纤维和Z 向纤维与其相互交织。
每个层次的纱线和织物的间隔尺寸都是可调节的,这使得三维立体织物的结构通过控制纵向、横向和Z 向的纱线结构来实现。
2. 制备三维立体织物复合材料制备技术是目前研究的热点之一,目前已经研制出许多相应的生产工艺,包括针织法、喷织法、无纺布法、编织法等。
( 1)针织法:是一种纱线由一台细针织机械编成的三维结构。
它采用针织设备排列的行和针织面来构造一个连续的、无缝的三维结构织物。
在织物的表面和内部织有不同的纱线密度或纺织结构。
( 2)喷织法:是一种通过喷织纤维来制造三维立体织物的方法。
将树脂/纤维复合材料从喷嘴或泵喷出,并通过喷嘴将复合材料沉积在三维织物上。
在制备过程中,纵向纤维通过喷嘴或滚轮决定,横向纤维和Z向纤维则通过喷射进行构造。
( 3)无纺布法:是一种制造无纺布的方法,其特点是不需要经过织造过程,可以快速制造出优质的三维立体织物。
目前,无纺布法主要采用热风交织、喷丝和湿法交织等方法来实现。
(4) 编织法:与纺织品的编法类似,纵向纤维被编织成为连续结构,然后横向纤维和Z 向纤维被插入编织的结构中,形成一个具有三维立体结构的织物。
3. 应用三维立体织物复合材料具有优异的力学性能及成型性等特点,因此广泛应用于航空航天、军事、汽车、建筑和医疗等领域。
金属基复合材料制备工艺的研究进展
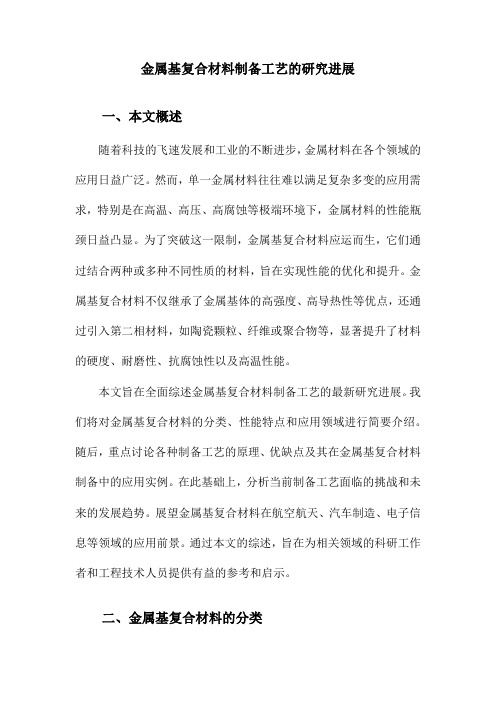
金属基复合材料制备工艺的研究进展一、本文概述随着科技的飞速发展和工业的不断进步,金属材料在各个领域的应用日益广泛。
然而,单一金属材料往往难以满足复杂多变的应用需求,特别是在高温、高压、高腐蚀等极端环境下,金属材料的性能瓶颈日益凸显。
为了突破这一限制,金属基复合材料应运而生,它们通过结合两种或多种不同性质的材料,旨在实现性能的优化和提升。
金属基复合材料不仅继承了金属基体的高强度、高导热性等优点,还通过引入第二相材料,如陶瓷颗粒、纤维或聚合物等,显著提升了材料的硬度、耐磨性、抗腐蚀性以及高温性能。
本文旨在全面综述金属基复合材料制备工艺的最新研究进展。
我们将对金属基复合材料的分类、性能特点和应用领域进行简要介绍。
随后,重点讨论各种制备工艺的原理、优缺点及其在金属基复合材料制备中的应用实例。
在此基础上,分析当前制备工艺面临的挑战和未来的发展趋势。
展望金属基复合材料在航空航天、汽车制造、电子信息等领域的应用前景。
通过本文的综述,旨在为相关领域的科研工作者和工程技术人员提供有益的参考和启示。
二、金属基复合材料的分类金属基复合材料(Metal Matrix Composites, MMCs)是一类由金属或合金作为基体,与一种或多种增强体组合而成的先进材料。
这些增强体可以是颗粒、纤维、晶须或纳米尺度的强化相等。
根据其增强体的不同形态和性质,金属基复合材料可分为以下几类:颗粒增强金属基复合材料(Particle Reinforced Metal Matrix Composites, PRMMCs):这类复合材料中,增强体为颗粒形态,如氧化铝(Al₂O₃)、碳化硅(SiC)、氮化硅(Si₃N₄)等陶瓷颗粒,或者碳黑、石墨等碳质颗粒。
这些颗粒均匀分布在金属基体中,能够有效地提高材料的硬度、耐磨性和高温性能。
纤维增强金属基复合材料(Fiber Reinforced Metal Matrix Composites, FRMMCs):纤维增强体包括碳纤维、玻璃纤维、硼纤维、氧化铝纤维等。
基于材料力学的纤维增强复合材料研究进展

基于材料力学的纤维增强复合材料研究进展纤维增强复合材料是一种具有高强度、高模量和轻质特性的材料,广泛应用于航空航天、汽车制造、建筑工程等领域。
而基于材料力学的纤维增强复合材料研究是指利用力学原理和实验手段对纤维增强复合材料的力学性能进行研究和分析。
本文将介绍纤维增强复合材料的基本原理、研究方法和一些研究进展。
首先,纤维增强复合材料由纤维和基体组成。
纤维通常采用碳纤维、玻璃纤维、聚合物纤维等,基体通常采用环氧树脂、树脂胶粘剂等。
纤维增强复合材料的性能取决于纤维的性质、排列方式和基体的性质。
因此,研究如何改善纤维增强复合材料的性能成为学者关注的焦点。
在基于材料力学的纤维增强复合材料研究中,有多种研究方法被广泛应用。
一种常用的方法是拉伸试验,通过对材料进行拉伸,得到其应力-应变曲线,从而分析材料的强度、刚度和断裂性能等。
另外,压缩试验、剪切试验、弯曲试验等也是常用的研究方法。
这些试验能够揭示纤维增强复合材料的力学特性,为其性能改进和设计提供依据。
随着科学技术的不断发展,研究者不断提出新的方法和理论,推动了纤维增强复合材料的研究进展。
例如,在计算力学方面,有限元分析被广泛应用于模拟纤维增强复合材料的力学行为。
这种方法能够精确地预测材料的应力分布、应变分布和破坏模式,为复合材料的设计和优化提供了有力的工具。
此外,还有许多新的纤维增强复合材料的研究方向,如多尺度力学、多功能复合材料等。
多尺度力学研究了不同尺度下材料的力学行为,从宏观到微观的尺度。
这种方法能够更准确地描述纤维增强复合材料的性能和异常行为,为新材料的开发提供了重要的理论基础。
而多功能复合材料则是指具有多种功能的复合材料,如耐磨、防火、导电等。
研究者通过改变复合材料的组分和结构,使其具有特定的功能,满足不同领域的需求。
总结起来,基于材料力学的纤维增强复合材料研究是一个广泛而深入的领域,涉及到材料力学原理、研究方法和研究进展等方面。
通过对纤维增强复合材料的力学性能进行研究和分析,可以为其性能的改进和设计提供有力的依据。
聚合物基复合材料的发展现状和最新进展
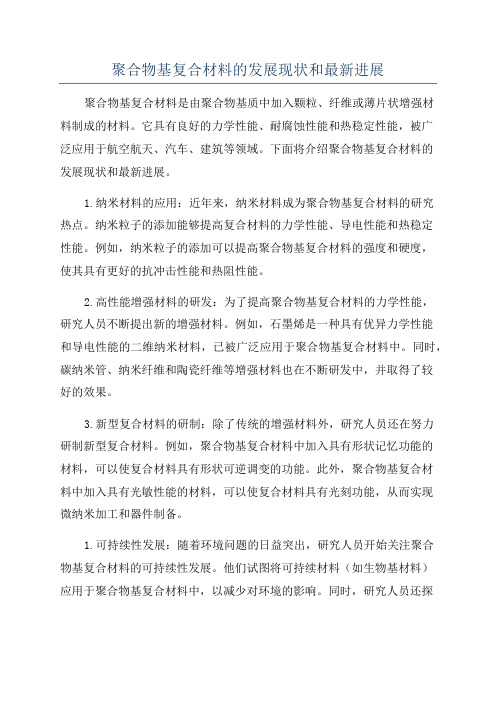
聚合物基复合材料的发展现状和最新进展聚合物基复合材料是由聚合物基质中加入颗粒、纤维或薄片状增强材料制成的材料。
它具有良好的力学性能、耐腐蚀性能和热稳定性能,被广泛应用于航空航天、汽车、建筑等领域。
下面将介绍聚合物基复合材料的发展现状和最新进展。
1.纳米材料的应用:近年来,纳米材料成为聚合物基复合材料的研究热点。
纳米粒子的添加能够提高复合材料的力学性能、导电性能和热稳定性能。
例如,纳米粒子的添加可以提高聚合物基复合材料的强度和硬度,使其具有更好的抗冲击性能和热阻性能。
2.高性能增强材料的研发:为了提高聚合物基复合材料的力学性能,研究人员不断提出新的增强材料。
例如,石墨烯是一种具有优异力学性能和导电性能的二维纳米材料,已被广泛应用于聚合物基复合材料中。
同时,碳纳米管、纳米纤维和陶瓷纤维等增强材料也在不断研发中,并取得了较好的效果。
3.新型复合材料的研制:除了传统的增强材料外,研究人员还在努力研制新型复合材料。
例如,聚合物基复合材料中加入具有形状记忆功能的材料,可以使复合材料具有形状可逆调变的功能。
此外,聚合物基复合材料中加入具有光敏性能的材料,可以使复合材料具有光刻功能,从而实现微纳米加工和器件制备。
1.可持续性发展:随着环境问题的日益突出,研究人员开始关注聚合物基复合材料的可持续性发展。
他们试图将可持续材料(如生物基材料)应用于聚合物基复合材料中,以减少对环境的影响。
同时,研究人员还探索了聚合物基复合材料的循环利用和回收利用技术,以实现资源的有效利用。
2.多功能复合材料的研究:为了满足不同领域的需求,研究人员开始研究多功能复合材料。
多功能复合材料可以同时具有力学性能、光学性能、导电性能、热学性能等多种功能。
例如,研究人员研制出了具有自修复功能的聚合物基复合材料,可以在受损后自动修复,延长使用寿命。
3.智能复合材料的研制:智能复合材料是指能够根据环境和外界刺激自主调整性能的复合材料。
例如,研究人员设计了具有温度响应性能的聚合物基复合材料,可以根据温度的变化改变其形状和力学性能,实现智能控制。
国内外复合管材的研究现状

国内外复合管材的研究现状全文共四篇示例,供读者参考第一篇示例:国内外复合管材是一种具有多种优秀性能的新型管材,其由不同材料的层间结构构成,各层材料之间通过粘结剂或者机械锁合等方式进行连接。
复合管材的研究与应用在水利、石油化工、建筑等领域具有广泛的应用前景。
本文将对国内外复合管材的研究现状进行详细介绍。
一、国内复合管材研究现状在国内,复合管材的研究开始较晚,但近年来得到了飞速发展。
目前,国内研究机构和企业在复合管材领域的研究涉及到材料的选择、结构设计、制备工艺等多个方面。
在复合材料的选择方面,国内研究机构主要关注于炭纤维、玻璃纤维、碳纳米管等高强度材料的应用,以及聚合物、金属等基体材料的选择。
在结构设计方面,国内研究机构尝试不同的层间结构与连接方式,以提高管材的性能。
在制备工艺方面,国内研究机构致力于开发新的管材生产工艺,以提高管材的生产效率和质量。
三、国内外复合管材的应用前景国内外复合管材具有优异的性能,如高强度、耐腐蚀、耐磨损等特点,适用于各种领域的管道输送和结构支撑。
在水利工程领域,复合管材能够提高管道输送效率,减少管道堵塞和泄漏问题;在石油化工领域,复合管材能够提高管道的耐化学腐蚀性能,延长管道的使用寿命;在建筑领域,复合管材能够降低结构的重量,提高结构的抗震性能。
国内外复合管材的研究现状处于快速发展阶段,未来将有更广泛的应用前景。
随着先进的材料与制备技术的不断推进,复合管材将在各个领域展现出更大的潜力和应用价值。
希望国内外研究机构和企业能够共同努力,加快复合管材领域的研究与开发,推动管材领域的创新与发展。
第二篇示例:国内外复合管材的研究现状复合管材是由两种或两种以上不同材料组成的管材,具有优良的综合性能,广泛应用于管道输送、建筑工程、汽车制造等领域。
随着科技的发展和材料工艺的进步,复合管材在国内外的研究和应用也取得了长足的进步。
在国内,复合管材的研究主要集中在材料的组合和工艺的改进上。
目前,广泛应用的复合管材主要有玻璃钢管、碳纤维管、聚乙烯复合管等。
复合材料研究新进展

复合材料研究新进展近年来,复合材料研究领域取得了许多新的进展。
复合材料是由两种或两种以上的材料组成的材料,通过将它们的优点结合起来,可以创造出具有优良性能的新材料。
本文将介绍几个复合材料研究的新进展。
首先,纳米复合材料是目前研究的热点之一、纳米复合材料是由纳米颗粒和基础材料组成的材料,具有独特的物理和化学性质。
例如,纳米颗粒的添加可以显著提高复合材料的强度、硬度和热稳定性。
研究人员通过控制纳米颗粒的形状、大小和分布来调节复合材料的性能。
纳米复合材料在电子、医疗、能源等领域具有广泛的应用前景。
其次,生物复合材料是另一个研究的热点。
生物复合材料是指由生物可降解聚合物和无机或有机增强物组成的复合材料。
它具有优异的力学性能和生物相容性,可以被用于骨组织工程、药物载体等领域。
研究人员通过改变聚合物的组分和结构,以及增强物的类型和含量,来调控生物复合材料的性能。
生物复合材料的研究对于解决生物医学领域中的问题具有重要的意义。
第三,多功能复合材料是近年来的一个新研究方向。
多功能复合材料是指具有多种功能的复合材料,可以同时满足不同的应用需求。
例如,研究人员将导电颗粒、磁性颗粒和荧光颗粒等添加到复合材料中,使其具有导电、磁性和荧光功能。
多功能复合材料在电子、传感器、光学等领域有着广泛的应用前景。
最后,可再生复合材料是一个具有重要意义的研究方向。
传统的复合材料通常由非可再生资源制备而成,对环境造成了一定的压力。
随着可再生能源的发展和环境保护意识的提高,研究人员正在探索以可再生资源为原料制备复合材料的方法。
例如,纤维素、淀粉和玉米等天然资源可以用来制备生物复合材料,其具有良好的生物可降解性和可再生性。
可再生复合材料的研究对于实现可持续发展具有重要意义。
综上所述,复合材料研究在纳米材料、生物材料、多功能材料和可再生材料等方面取得了许多新的进展。
这些新进展为材料科学和工程领域的发展提供了新的方向和机会。
随着技术的不断进步,相信复合材料将在更多领域得到应用并取得更大的突破。
石墨烯增强铝基复合材料的研究进展
石墨烯增强铝基复合材料的研究进展1. 引言1.1 石墨烯增强铝基复合材料的研究背景石墨烯是一种二维晶格结构的碳原子薄膜,由于其独特的物理、化学和力学性质,被认为是一种具有巨大潜力的新型材料。
石墨烯具有极高的导热性、机械强度和化学稳定性,因此在材料科学领域备受关注。
铝及其合金由于具有较低的密度和良好的加工性能,在航空航天、汽车工业等领域有着广泛的应用。
传统铝材料在强度和硬度方面存在一定局限性。
为了克服传统铝材料的缺点,研究者们开始探索引入石墨烯来增强铝基复合材料。
石墨烯的加入不仅可以提高复合材料的力学性能,还可以优化其导热和电导特性。
石墨烯增强铝基复合材料成为当前研究的热点之一。
通过将石墨烯与铝基材料进行复合,可以有效提高材料的强度、硬度和耐磨性,同时减轻材料的重量,提高材料的导热性能。
石墨烯增强铝基复合材料被认为具有广阔的应用前景,对于推动材料科学领域的发展具有重要意义。
【字数:220】1.2 石墨烯在材料科学中的应用潜力1. 电子器件:石墨烯具有优异的电子输运性能,高载流子迁移率和高电导率,使其成为理想的电子器件材料。
石墨烯可以应用于场效应晶体管、光电探测器、透明导电膜等领域,为电子器件的性能提升提供了新的可能性。
3. 柔性电子:由于石墨烯的柔韧性和透明性,可将其应用于柔性电子领域,如柔性显示器、柔性传感器、可穿戴设备等。
石墨烯材料的应用为柔性电子产品带来了更广阔的发展空间。
石墨烯在材料科学中的应用潜力巨大,其优异的性能和特殊的结构使得其可以在多个领域发挥重要作用,推动材料科学的发展和创新。
对石墨烯的研究不仅有助于拓展其应用领域,还将促进整个材料科学领域的进步和发展。
2. 正文2.1 石墨烯增强铝基复合材料的制备方法石墨烯增强铝基复合材料的制备方法主要包括机械合金化、粉末冶金、湿法涂覆、化学气相沉积以及熔体混合等几种方法。
机械合金化是其中一种常用的方法,通过球磨或挤压将石墨烯与铝粉进行混合,使二者在微观层面有所聚集和弥散,从而增加界面结合强度。
难熔金属基复合材料的研究进展
难熔金属基复合材料的研究进展难熔金属基复合材料是一种具有卓越性能和广泛应用潜力的材料。
它由高熔点金属基体和分散相组成,具有高温强度、耐腐蚀性、耐磨损性和导电性等优点。
难熔金属基复合材料的研究已经取得了显著的进展,并在航空航天、能源、汽车和冶金等领域得到广泛应用。
难熔金属基复合材料的研究主要涉及材料的制备技术、性能优化和应用研究。
目前,常用的制备技术包括粉末冶金、熔融混合、机械合金化和表面改性等方法。
其中,粉末冶金是一种常用的制备难熔金属基复合材料的方法。
通过粉末冶金技术可以得到具有均匀分散相的复合材料,从而提高材料的力学性能和耐热性能。
难熔金属基复合材料的性能优化主要通过合金化和微结构控制实现。
通过合金化可以改变金属基体的组成,调整材料的力学性能和导热性能。
通过微结构控制可以调控分散相的尺寸、形状和分布,进一步提高材料的力学性能和耐热性能。
此外,难熔金属基复合材料的表面改性也是一种常用的性能优化手段。
通过在金属基体的表面引入功能性涂层,可以提高材料的表面硬度、耐磨损性和耐腐蚀性。
难熔金属基复合材料在航空航天领域具有广泛的应用前景。
在航空发动机中,难熔金属基复合材料可以作为高温结构材料使用,用于制造涡轮叶片、燃烧室和燃气轮机等部件。
难熔金属基复合材料具有出色的高温强度和耐热性能,可以提高发动机的工作效率和可靠性。
此外,在航天航空热保护系统中,难熔金属基复合材料也可以作为热隔断材料使用,有效减少空气动力热、压力热和辐射热对航天器的影响。
在能源领域,难熔金属基复合材料可以用于制造高温燃料电池和核能反应堆等设备。
难熔金属基复合材料具有优异的导电性能和耐腐蚀性,可以提高燃料电池和核能反应堆的运行效率和安全性。
此外,难熔金属基复合材料还可以用于制造高温储能设备,用于储存太阳能和风能等可再生能源。
在汽车领域,难熔金属基复合材料可以用于制造发动机和制动系统等关键部件。
难熔金属基复合材料具有出色的耐磨损性和耐高温性能,可以提高发动机和制动系统的性能和寿命。
石墨烯复合材料研究进展
石墨烯复合材料研究进展摘要:近年来石墨烯因其优良的力学、电学、热学和光学等特性, 且添加到基体材料中可以提高复合材料的性能,拓展其功能,因此石墨烯复合材料的制备成为研究热点之一。
本文介绍了国内外对石墨烯复合材料的研究,对石墨烯复合材料的研究进展及现状进行了详细的介绍,并对石墨烯复合材料的发展趋势进行了展望。
关键词:石墨烯;复合材料;研究进展一、引言石墨烯因其优异的物理性能和可修饰性, 受到国内外学者的广泛关注。
石墨烯的杨氏模量高达1TPa、断裂强度高达130GPa,是目前已知的强度性能最高的材料,同时是目前发现电阻率最小的材料, 只有约10-8Ω·m;拥有很高的电子迁移率,且具有较高的导热系数。
氧化石墨烯作为石墨烯的重要派生物,氧化石墨烯薄片在剪切力作用下很容易平行排列于复合材料中, 从而提高复合材料的性能。
本文总结介绍了几种常见的石墨烯复合材料。
二、石墨烯复合材料(1)石墨烯及氧化石墨烯复合材料膜聚乙烯醇(PVA)结构中有非常多的羟基,因此其能与水相互溶解,溶解效果很好。
GO和PVA都可以在溶液中形成均匀、稳定的分散体系。
干燥成型后,GO在PVA中的分散可以达到分子水平,GO表面丰富的含氧官能团可以与PVA的羟基形成氢键,因此添加少量的GO可以显著提高复合材料的力学性能。
樊志敏[1]等制备出了氧化石墨烯纳米带/TPU复合膜。
通过机械测试显示,当加入氧化石墨烯纳米带的量为2%时,复合薄膜的弹性模量和抗拉强度与不加氧化石墨烯纳米带的纯TPU薄膜相比都得到了非常大的提高,分别提高了160%和123%。
马国富[2]等人发现,在聚乙烯醇(PVA)和氧化石墨烯(GO)复合制备的得复合薄膜中,GO均匀的分散在PVA溶液中,PVA的羟基与GO表面的含氧基团发生相互作用复合而不分相。
加入GO之后,大大提高了复合膜的热稳定性,当加入的GO量为3%时,纳米复合膜力学性能测试出现最大值,此时断裂伸长率也出现了最大值,这表明在此GO含量时复合膜有最佳性能;与不加GO的纯PVA膜相比,当加入的GO量为3%时,耐水性也大大地提高。
国内外木塑复合材料的研究进展
国内外木塑复合材料的研究进展摘要:阐述了木塑复合材料在21世纪的研究进展,涉及国内外在近几年的主要研究成果,介绍了包括界面相容性的改善方法、加工工艺的改进以及木塑复合材料的相关性能探讨,并提出了我国木塑复合材料今后的发展方向。
关键词:木塑;复合材料;研究进展木塑复合材料是国内外近年蓬勃兴起的一类新型复合材料,指利用聚乙烯、聚丙烯和聚氯乙烯等,代替通常的树脂胶粘剂,与超过50%以上的木粉、稻壳、秸秆等废植物纤维混合成新的木质材料,再经挤压、模压、注射成型等塑料加工工艺生产出的板材或型材。
主要用于建材、家具、物流包装等行业。
将塑料和木质粉料按一定比例混合后经热挤压成型的板材,称之为挤压木塑复合板材。
1 国内木塑复合材料研究进展木塑复合材料这种新兴的环保材料产品在世界范围得到越来越多的关注和认可,其生产量和使用量都在逐年快速增加。
我国在木塑复合材料方面的研究也一直处于进步状态,进行了大量有益的试验并取得不少成果。
2001年贺德留[1]等在低温和中温环境中进行两个阶段的化学反应引发聚合固化,实验中以速生劣质材杨木为基材,以有机单体甲基丙烯酸甲酯作为浸滞剂,并着以适当颜色,在真空状态下作浸滞处理,处理件在石蜡包围下,制造出木塑复合材料。
该技术实际应用中出现的问题有很多,但在此工艺基础上,通过制作杨木木塑复合材料地板试验已基本解决。
研究得出相关结果有:木材的含水率需要达到一定的指数才可以进行浸注;采用甲基丙烯酸甲酯为浸注液时,偶氮二异丁腈的有机单体量也有一定规定,而且把偶谈二异丁腈作为化学引发剂;微量加入还原剂亚铁离子的方法可以改变和强化复合材料的性能,但须注意要定期往循环浸注液中补加亚铁离子和化学引发剂;制作高硬度的木塑地板时可以在有机单体中加入色素(而且加入量是有一定的规定),这样既改变了复合材料颜色,同时增强了复合材料的性能;浸注过程的真空度尽可能保持不变,当浸注真空度和浸注时间达到要求的数值时可以制作木塑复合材料地板同时也满足材料的硬度要求很大时的情况;最后一步一定要及时进行石蜡包裹,石蜡油温度在一定数值时才能达到理想的包裹效果;有机单体在木材内的聚合固化程序时间也在实验中得到验证。
- 1、下载文档前请自行甄别文档内容的完整性,平台不提供额外的编辑、内容补充、找答案等附加服务。
- 2、"仅部分预览"的文档,不可在线预览部分如存在完整性等问题,可反馈申请退款(可完整预览的文档不适用该条件!)。
- 3、如文档侵犯您的权益,请联系客服反馈,我们会尽快为您处理(人工客服工作时间:9:00-18:30)。
复合材料加工技术的最新研究进展摘要:本主要综述了陶瓷基、树脂基这两种主要的非金属基复合材料的加工技术。
通过对传统加工和新型加工技术的比较,认为今后研究非金属基复合材料加工工艺参数的优化,工艺过程中关键步骤的改进,新技术的研究,生产设备自动化、智能化程度的提高,生产线的规模化、专业化、可控制化,是其加工技术发展的关键。
关键词:陶瓷基、树脂基、复合材料加工复合材料是由两种或两种以上不同化学性能或不同组织结构的材料,通过不同的工艺方法组成的多相材料,主要包括两相:基体相和增强相。
20世纪40年代,因航空工业需要而发展了玻璃纤维增强塑料,是最早出现的复合材料,从此以后,陆续发展了碳纤维、石墨纤维和硼纤维等高强度和高模量纤维。
70年代出现了芳纶纤维和碳化硅纤维。
这些高强度、高模量纤维与合成树脂、碳、石墨、陶瓷、橡胶等非金属基体或铝、镁、钛等金属基体复合,构成了格局特色的复合材料。
复合材料由于其具有各方面独特的性质,广泛应用与军事工业,汽车工业、医疗卫生、航空、航海以及日常生活的各个方面。
对于复合材料的加工技术的研究,将是扩大其适用范围的关键之一[1]。
1 陶瓷基复合材料的加工由于陶瓷材料同时具有高硬度、高脆性和低断裂韧性等特点,使得其加工、特别是成形加工,至今仍非常困难。
在陶瓷材料加工中,使用金刚石工具的磨削加工仍然是目前最常用的加工方法,占所有加工工艺的80%。
而陶瓷材料磨削加工不仅效率低,而且在加工中很容易产生变形层、表面/亚表面微裂纹、材料粉末化、模糊表面、相变区域、残余应力等缺陷,这对于航空、航天、电子等高可靠性、高质量要求的产品是决不允许的。
陶瓷精密元件的加工费用一般占总成本的30%~60%,有的甚至高达90%。
因此,通过新的陶瓷加工制造技术的探索,能够很好的提高产品制造精度和降低生产成本[2]。
1.1新型加工技术1.1.1 放电加工放电加工(EDM)是一种无接触式精细热加工技术,当单相或陶瓷/陶瓷、陶瓷/金属复合材料的电阻小于100Ω.m时,陶瓷材料可以进行放电加工。
首先将形模(刻丝)和加工元件分别作为电路的阴、阳极,液态绝缘电介质将两极分开,通过悬浮于电介质中的高能等离子体的刻蚀作用,表层材料发生熔化、蒸发或热剥离而达到加工材料的目的。
由于加工过程模具未与工件直接接触,故无机械应力作用于材料表面,因此放电加工是理想的加工高脆、超硬陶瓷材料的方法[3]。
1.1.2 ELID精密磨削加工技术ELID精密磨削技术一金属基超硬磨料砂轮在线电解修整(简称ELID)磨削技术是国外近年发展起来的一种适应于工程陶瓷等硬脆材料的精密和超精密加工新技术。
在对硬脆陶瓷进行磨削时,砂轮将因磨损和堵塞而很快钝化,这将增加脆性断裂比例。
为了使砂轮在磨削全过程保持锋利,必须对砂轮进行在线修整。
应用ELID磨削技术,可对工程陶瓷等硬脆材料实现高效率磨削和精密镜面磨削。
国内外研究结果表明,ELID磨削过程中磨削力明显小于普通磨削,因为砂轮保持在良好的修整状态。
由于磨轮表面绝缘层处于形成、破裂循环之中,导致磨削力周期变化,提高脉冲电源占空比可以提高磨削力的稳定性和降低表面粗糙度,但是增加了砂轮磨损率。
ELID磨削应使用弱电解质水溶液,既具有电解性能又可做为磨削液,且对机床无腐蚀性。
金属结合荆也会影响ELID磨削过程中的适应性、磨削效率和表面质量,铸铁基砂轮磨削效果及稳定性好,且砂轮寿命高[4]。
1.1.3 激光加工激光加工是利用高能量密度(108~1010w/m2)的均匀激光束作为热源,在加工陶瓷材料表面局部点产生瞬时高温,局部点熔融或汽化而去除材料。
激光加工是一种无接触、无摩擦式加工技术,加工过程中不需模具,通过控制激光束在陶瓷材料表面的聚焦位置,实现三维复杂形状材料的加工。
一般激光钻孔和切割所需激光功率为150w~15kW。
但同放电加工一样,由于陶瓷材料热导率低,高能束可能会在材料表面产生热应力集中,形成微裂纹、大的碎屑、甚至材料断裂。
1.1.4 超声波加工1927年,美国物理学家伍德和卢米斯最早做了超声加工试验,利用强烈的超声振动对玻璃板进行雕刻和快速钻孔,但当时并未应用在工业上。
l951年,美国的科恩制成了第一台实用的超声打孔机,并引起广泛关注,为超声加工技术的发展奠定了基础。
上世纪五六十年代,利用超声波钻孔已经开始应用,八十年代末,前苏联已经生产系列超声振动钻削装置。
九十年代以后,旋转超声加工开始应用于这类材料加工上,同时加工设备已经开始向自动化、智能化、集成化、附件化方向发展。
如德国DMG 公司生产出旋转超声加工机床,开发出旋转超声专用磨头附件,机床采用智能控制算法ADC/自适应控制和ACC/Acoustic控制以及APC/压力自动控制,可以在无人值守的条件下完成加工[5]。
2 树脂基复合材料的加工树脂基复合材料于1932年在美国出现,1940年以手糊成型的方法制成了玻璃纤维增强聚酯的军用飞机雷达罩。
其后不久,美国莱特空军发展中心设计制造了一架以玻璃纤维增强树脂为机身和机翼的飞机,并于1944年3月在莱特一帕特空军基地试飞成功。
从此纤维增强复合材料开始受到军界和工程界的关注。
第二次世界大战以后这种材料迅速扩展到民用领域,风靡一时,发展很快[1]。
2.1 传统加工方法树脂基复合材料的加工已经有多年的研究历史了。
传统的加工方式时主要有接触挤压加工成型、拉挤成型、模压成型、缠绕成型这几种。
以下将做简单介绍。
2.1.1 接触低压成型加工接触低压成型工艺的过程是,先将材料在阴模、阳模或对模上制成设计形状,通过加热或常温固化,脱模后再经过辅助加工获得制品。
1963年前后在美、法、日等国先后开发了高产量、大幅宽、连续生产的玻璃纤维复合材料板材生产线,使复合材料制品形成了规模化生产。
这一举措使复合材料成型工艺走向了自动化、高效化、专业化的方向,对复合材料工业的发展起到了决定性的作用。
接触成型工艺的最大优点是设备简单,适应性广,投资少,见效快。
但其同时存在着生产效率低、劳动强度大、产品重复性差等显著缺点。
于是改进这种工艺成为先进复合材料的成型工艺下一步发展的关键[6]。
2.1.2 拉挤成型加工树脂基复合材料拉挤成型工艺的研究始于20世纪50年代。
到60年代中期,拉挤成型工艺已投入到连续化生产中。
70年代,拉挤技术又有了重大的突破。
该工艺将已润湿的树脂胶液的连续纤维束或带在牵引结构拉力的作用下,通过成型模成型,并在模中或固化炉中固化,连续生产出长度不受限制的复合型材。
由于在成型过程中需经过成型模的挤压和外牵引拉拔,而且生产过程和制品长度是连续的,故又称为拉挤连续成型工艺。
该工艺具有生产效率高,易于控制,产品质量稳定和制造成本较低等优点;而且纤维按纵向排列,使制品具有高的拉伸强度和弯曲强度。
现在,拉挤工艺主要用于生产各种玻璃钢型材,如玻璃钢棒,工字型、角型、槽型、方型、空腹型及异形断面型材等。
目前最大的拉挤成型机,可以生产断面为800×800(mm)的空腹玻璃钢型材[6]。
2.1.3 模压成型加工模压成型工艺是复合材料生产中最古老而又富有无限活力的一种成型方法。
它是将一定量的预混料或预浸料加入金属对模内,经加热、加压来固化成型的一种方法。
模压成型工艺的主要优点是生产效率高,便于实现专业化和自动化生产,可有效降低制造成本;产品尺寸精度高,重复性好;表面光洁,无需二次修饰;能一次成型结构复杂的制品。
另外,模压法制备基体试件可以有效地避免分子取向,能较客观地反映非晶态高聚物的性能。
近几年来,以长短纤维为增强材料,以热塑性、热固性树脂为基体材料的各类复合材料模压成型工艺发展很快,产品性能价格比高,对环境污染小,生产率高,正在不断适应汽车、航空航天、通讯等工业发展[6]。
2.1.4 缠绕成型加工纤维缠绕成型技术1946年在美国出现至今,缠绕成型工艺已历经半个世纪的发展,经过了从纤维缠绕和带缠绕的发展过程,成为聚合物基复合材料制造的重要手段之一。
缠绕成型工艺是将浸过树脂胶液的连续纤维(或布带、预浸纱)按照一定规律缠绕到芯模上,然后经固化、脱模,最终获得制品。
目前,缠绕技术的发展关键在缠绕设备的发展方面,主要在计算机控制,设备的精度、浸刮胶方式、立体多轴缠绕及张力控制,正向着高自动化、高集成化、高产量化的方向发展。
高性能的树脂基体及高强纤维都在逐步应用到缠绕领域,这促使缠绕工艺有更大的应用领域和发展前景[7]。
2.2 先进加工技术2.2.1 铺放成型加工[7]纤维铺放成型技术是自动铺丝束成型技术和自动窄带铺放成型技术的统称,是在已有缠绕和自动铺放技术基础上发展起来的一种全自动制造技术。
纤维铺放技术最早是作为缠绕技术的改革(新型缠绕技术)提出的,主要用于生产航空航天的大型的、特殊结构的构件。
自动铺放技术源于20世纪60年代,在美国空军实验室支持下起步,后经ACT、CAI(计算机辅助设计)等计划支持,迅速发展。
该技术于20世纪70年代由Boeing、Cincinnati Milacron、Hercules等公司联合开发,已经经历近40年的发展。
1982年Boeing公司的机械工程师提出了“A VSD铺放头”设想,解决了纤维束压实、切断和重送的问题,1985年Hercules公司研制出第一台原理样机,1989年,Cincinnati Milacron公司设计出第一台纤维铺放系统并于1990年投入使用,1995年Ingersoll公司研制出其第一台铺放成型机。
随着自动铺放技术的不断发展,控制系统从模拟控制升级到全数字控制。
20世纪90年代还开发了专用的CAD/CAM软件与硬件配套,使其功能日臻完善。
设备制造商和飞机部件制造商也不断开发出自动铺放新技术,包括双向铺放头技术、丝束重定向控制技术、张力控制技术、预浸丝束整形技术、Fi.ber Steer技术、柔性压辊技术、热塑性自动铺放技术、超声固接成型技术和CAD/CAM软件技术等。
2.2.2 RTM成型加工RTM(Resin Transfer Molding 树脂传递模塑)技术是模压成型技术的一种,是为适应飞机雷达罩成型发展起来的。
从20世纪50年代起,英、美国家开始采用此技术。
经过多年的发展,现已成功地用于各种纤维增强复合材料的生产中。
复合材料RTM 工艺技术是目前欧美树脂基复合材料低成本技术发展的两大主要方向之一。
RTM是将树脂注入到闭合模具中浸润增强材料并固化的工艺方法,是近年来发展迅速的适宜多品种、中批量、高质量先进复合材料制品生产的成型工。
RTM成型虽然有很多优点,但是也有不足之处:树脂纤维的浸渍不够理想,制品里存在空隙率较高、制品的纤维含量较低、,模塑过程中树脂的流动不均衡,不能进行预测和控制、,模具成本高,脱模困难等[8]。
针对RTM存在的这些不足,国内外开展了大量颇有成效的研究,使得RTM技术渐趋成熟。