精益生产之价值流图Value Stream Mapping
精益生产之价值流分析streammapping_EN

Value Stream Analysis - Actual-Situation - Customer
Takt Time =
available factory hours production quantity - customer demand
Example:
21 shifts per week x 8h x 3,600 12,000 pieces per week
• Afterwards please draw a "Target-Situation" how the value streams should look in the future.
2
What is Value Stream Analysis and Design used for?
• Visualizing the entire value stream and developing an ideal value stream • Relationships between information flow and material flow are visually illustrated and easily
Criteria to be observed
II.1
II.2
II.3
II.4
drafting of customer requirement
and process steps
recording of the process parameters and
Inventories
depiction of the information and
4600 L 2400 R
7,6 Tage
价值流程图-VSM

PROCESSES
Products
Receiving Cutting Strip Soldering Crimp Insertion molding test inspect Pack
A
x
x
x
x
x
x
x
x
x
B
x
x
x
x
x
x
x
x
x
C
x
x
x
一次质量
2 x/ day
发运
I
500 pcs
Inventory Part A = 750 pcs Part B = 600 pcs Part C = 1650 pcs
# of shifts =
环节6:定义信息流
绘制从收到订单到下达生产订单(客户旳订单,生产订 单,采购订单)旳信息流。
统计生产订单及有关产品。 统计生产计划系统及随产品经过系统旳文件材料。 统计你怎样与供给商和客户沟通。 统计信息怎样整顿和发放,例如:电子方式,手工方式,
区别流动中旳推动和拉动。 包括产品接受和质量检验旳全部控制。
推动
流程生产不考虑下游(内部 )客户流程旳实际需求,直 接推动未完毕产品经过流程 。生产根据既定计划。
VS
拉动
每个后续生产环节都是前一 流程环节旳客户。当需要时 (拉动)由客户要求数量, 而不是简朴旳根据前面生产 环节生产并直接送到客户处 (推动)。
怎样辨认流程中旳挥霍?
价值流图(VSM)
价值流图消除挥霍
价值流图旳目旳在揭发挥霍旳起源。
我们应着眼于回答下述问题: “我们怎样能够仅生产下个流程所需,并仅在该流程需要时生产旳方式
精益生产3VSM(价值流图及价值流分析

针对每个评估指标,制定相应的评估标准,明确达标的具体要求 和标准。
定期调整评估指标
随着企业生产和管理水平的提升,需要定期调整评估指标,以适 应新的发展需求。
绩效评估结果分析
数据收集与整理
收集与评估指标相关的数据,并进行整理、分类 和汇总。
结果分析
运用统计分析方法,对收集的数据进行分析,找 出存在的问题和不足之处。
降低成本
降低生产过程中的成本,包括原材料、 人力、设备等方面的成本。
缩短交货期
通过优化生产流程,缩短产品生产周期 和交货期,提高客户满意度。
流程优化方法
01
价值流分析
通过对生产流程中的价值流进 行分析,识别浪费和非增值活
动,并进行优化。
02
工艺流程再造
对现有的工艺流程进行重新设 计和优化,以提高生产效率和
现场观察
02
深入生产现场,仔细观察员工操作、设备运行、物料流动等实
际情况,发现浪费现象。
员工参与
03
鼓励员工积极参与浪费识别,利用他们对生产过程的了解,发
现潜在的浪费问题。
浪费消除策略
精益改善
通过精益工具和方法,对生产过程 进行持续改进,消除浪费,提高效
率。
自动化与智能化
引入自动化设备和智能化技术,减 少人工操作,降低浪费发生的可能
精益生产3VSM(价值流图及 价值流分析
目录
• 精益生产3VSM概述 • 价值流图绘制及分析 • 浪费识别与消除 • 流程优化与改善 • 绩效评估与持续改进 • 案例分析与应用实例
01
精益生产3VSM概述
精益生产3VSM定义
价值流图(Value Stream Mapping,VSM)是一种 可视化的工具,用于描述产品或服务从原材料到最终
精益生产之价值流图Value-Stream-MappingPPT课件

可编辑
2
Define
Define
Learning Objectives
The learning objectives for this course are:
Be able to create Current State and Future State Value Stream Maps
Assign Value Stream Manager
One person to manage the mapping of the total flow Has the capability to make changes across departmental
boundaries Leads the creation and prioritization of the implementation
It gives the team a basis for prioritizing improvement efforts.
It gives the team a visual tool for representing their improvement ideas, so they are better able to communicate with people inside and outside the organization.
plan for getting from present state to future state Monitors implementation and updates implementation plan Driver for results
可编辑
7
Current State VSM
精益生产培训之十大工具
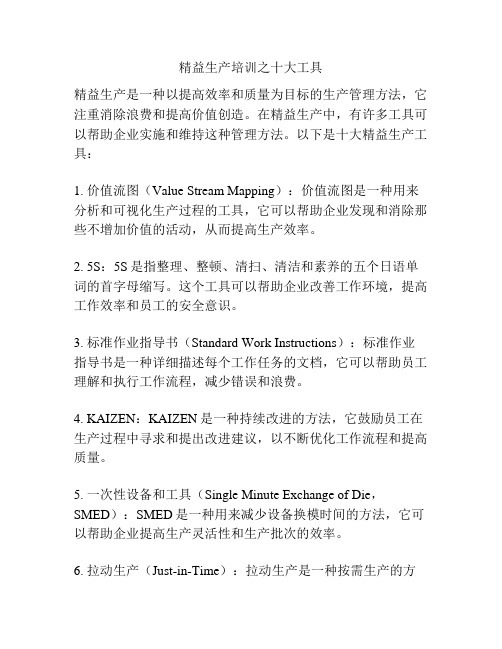
精益生产培训之十大工具精益生产是一种以提高效率和质量为目标的生产管理方法,它注重消除浪费和提高价值创造。
在精益生产中,有许多工具可以帮助企业实施和维持这种管理方法。
以下是十大精益生产工具:1. 价值流图(Value Stream Mapping):价值流图是一种用来分析和可视化生产过程的工具,它可以帮助企业发现和消除那些不增加价值的活动,从而提高生产效率。
2. 5S:5S是指整理、整顿、清扫、清洁和素养的五个日语单词的首字母缩写。
这个工具可以帮助企业改善工作环境,提高工作效率和员工的安全意识。
3. 标准作业指导书(Standard Work Instructions):标准作业指导书是一种详细描述每个工作任务的文档,它可以帮助员工理解和执行工作流程,减少错误和浪费。
4. KAIZEN:KAIZEN是一种持续改进的方法,它鼓励员工在生产过程中寻求和提出改进建议,以不断优化工作流程和提高质量。
5. 一次性设备和工具(Single Minute Exchange of Die,SMED):SMED是一种用来减少设备换模时间的方法,它可以帮助企业提高生产灵活性和生产批次的效率。
6. 拉动生产(Just-in-Time):拉动生产是一种按需生产的方法,它可以帮助企业减少库存和生产浪费,并且能够更好地满足顾客需求。
7. 故障模式与影响分析(Failure Mode and Effects Analysis,FMEA):FMEA是一种用来分析和评估潜在故障模式和其影响的方法,它可以帮助企业识别潜在风险,并采取措施进行预防和改进。
8. 委托管理(Gemba Walk):委托管理是一种通过实地走访生产现场来了解问题和挑战的方法,它可以帮助管理层与现场员工保持沟通,并及时解决问题。
9. PDCA循环:PDCA循环是指计划、实施、检查和行动的四个步骤,它是一种持续改进的管理方法,可以帮助企业不断优化工作流程和提高绩效。
精益生产常用工具
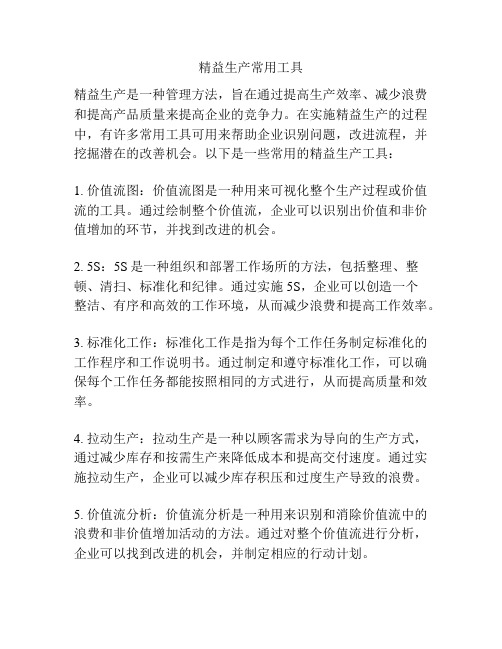
精益生产常用工具精益生产是一种管理方法,旨在通过提高生产效率、减少浪费和提高产品质量来提高企业的竞争力。
在实施精益生产的过程中,有许多常用工具可用来帮助企业识别问题,改进流程,并挖掘潜在的改善机会。
以下是一些常用的精益生产工具:1. 价值流图:价值流图是一种用来可视化整个生产过程或价值流的工具。
通过绘制整个价值流,企业可以识别出价值和非价值增加的环节,并找到改进的机会。
2. 5S:5S是一种组织和部署工作场所的方法,包括整理、整顿、清扫、标准化和纪律。
通过实施5S,企业可以创造一个整洁、有序和高效的工作环境,从而减少浪费和提高工作效率。
3. 标准化工作:标准化工作是指为每个工作任务制定标准化的工作程序和工作说明书。
通过制定和遵守标准化工作,可以确保每个工作任务都能按照相同的方式进行,从而提高质量和效率。
4. 拉动生产:拉动生产是一种以顾客需求为导向的生产方式,通过减少库存和按需生产来降低成本和提高交付速度。
通过实施拉动生产,企业可以减少库存积压和过度生产导致的浪费。
5. 价值流分析:价值流分析是一种用来识别和消除价值流中的浪费和非价值增加活动的方法。
通过对整个价值流进行分析,企业可以找到改进的机会,并制定相应的行动计划。
6. 周期时间分析:周期时间分析是一种用来测量和分析整个生产过程或价值流的时间的方法。
通过测量各个环节的时间,并分析其比例和关系,企业可以找到时间浪费和瓶颈,并采取相应的改进措施。
7. 柔性生产:柔性生产是一种以快速响应市场需求为导向的生产方式,通过灵活地调整生产线和生产能力,以适应需求的变化。
通过实施柔性生产,企业可以降低库存、提高交付速度和灵活性。
8. 产能平衡:产能平衡是指在不同工序间平衡产能,以避免过剩和瓶颈的发生,从而提高效率和质量。
通过进行产能平衡,企业可以合理安排生产能力,以满足顾客需求并避免资源浪费。
综上所述,以上提到的工具是精益生产中常用的工具,通过使用这些工具,企业可以识别问题,改进流程,并发现潜在的改善机会,从而提高生产效率和产品质量,降低成本,提高竞争力。
精益管理之精益生产中如何做价值流分析
精益管理之精益生产中如何做价值流分析新益为5S咨询公司概述:在精益生产中,价值流分析一般是指通过绘制价值流图,进行价值流图分析来发现并消灭浪费、降低成本,改善企业运营状况,提升企业竞争力。
因此进行价值流分析离不开价值流图。
价值流图(Value Stream Mapping,VSM)是一种用来描述物流和信息流的形象化工具。
通过从客户到供应商进行图形化的描述,让我们可以通过价值流图全览整个制造供应链的各个环节,从而从战略层面发掘出大的浪费和改进空间,避免盲目的执行改善。
而且价值流图是运用统一的图标进行绘制的,是一种通用的精益管理工具,用起来也比较方便。
绘制一张完整的价值流图,具体步骤如下。
1、计算客户节拍时间:
客户节拍时间是基于客户需求和计划工作时间计算出的一种节拍时间,其目的是让生产节拍时间能够与客户需求相适应,即避免过量生产的浪费,也确保能够覆盖客户的需求波动。
2、选择产品族:
选择工厂典型的产品绘制价值流图,在选择的时候可以从产品的工艺过程长短,产品的复杂程度两个角度进行衡量,选择有代表性的产品。
3、绘制现状价值流图:
动手绘制之前首先要理解一些注意点:亲自在工厂内走一遍,从
成品发货到原材料收货,不要漏掉重要的环节;用标准的图标来进行绘制,重点在于绘制清晰的物料流和信息流。
使用现场统计的真实数据而不是理论或标准数据;准备好纸和笔,先进行手绘,事后可以进行电子档整理;邀请团队成员,需有生产,质量,物流,设备等部门人员参加。
4、绘制未来价值流图。
精益生产培训之价值流图析VSM
成品仓
烤漆 成品 一个客户
供应商B
塑胶
装配
测试
價值流分析范圍
SIPOC保证我们关注的重点
Key to Excellence
深圳谋事精益信息咨询有限公司
Page 20 of 60
0. 准备工作
0.3 工艺流程
1.电阻成型 IC组装 插电阻R1 插电阻R2 插IC
切脚
浸锡
外检
插电容C2
插电容C1
Page 6 of 60
1. VSM概念
1.5 价值流分类-1
精益供应链 精益企业 精益管理 精益制造 精益消费
制造现场 公司 直接的供应链 延伸的供应链
顾客 购买 使用 质保 维修 转让
完整顾客体验
随着精益概念的延伸,价值流种类也在丰富当中
Key to Excellence
深圳谋事精益信息咨询有限公司
Page 13 of 60
3. 推行要点
3.3 选择一个产品系列-2:产品分族
产品族定义:流经相似工艺或者相同设备 产品族作用:同族产品水平推广,并推进混流生产
Key to Excellence
深圳谋事精益信息咨询有限公司
Page 14 of 60
3. 推行要点
3.3 选择一个产品系列-3:评估关键产品族
Key to Excellence
深圳谋事精益信息咨询有限公司
Page 12 of 60
3. 推行要点
3.3 选择一个产品系列-1:缘由
客户只关心他 们自己的产品
+
所有产品的价 值流非常复杂
﹦
利用产品分族矩 阵区分产品族
评估并选择一个 关键产品系列
Key to Excellence
精益生产之价值流图ValueStreamMapping
7
Current State VSM
SUPPLIER
5
Value Stream Mapping Process Steps
Identify Current State
Step 1: SIPOC Chart Step 2: Top Down Flow Chart Step 3: Determine Product Family Step 4: Draw Process Flow Step 5: Draw Material Flow Step 6: Draw Information Flow Step 7: Process Data Collection Step 8: Add Process and Lead Time data Step 9: Verify Current State Map
精益生产之价值流图 ValueStreamMapping
2020/8/21
Agenda
Monday
Kick-Off Introductions Current State Steps 1-4
Tuesday
Current State Steps 5-7
Wednesday
Current State Steps 8-9 Identify and Prioritize Improvement Opportunities Create Future State
6 Month Forecast Weekly FaxASLeabharlann EMBLYProduction
VSM价值流程图
批量大小
设置时间
设置频率
废品
返工 停机
收集数据
价值流程图要素之价值流程图要素之三信息流
现状图绘制步骤
1、现状图首先要表示顾客需求
2、画出所有过程、数据柜及库存三角
3、 画出材料流
现状图绘制步骤
4、画出信息流和推动箭头
现状图绘制步骤
5、画出生产时间线条和数据完成现状图
价值流分析的原则
1.从客户的角度给价值下定义。价值流是将具有价值的产品和服务提供给顾客所需 要的一系列的活动。对顾客而言,产品的增值过程只包括产品经历物理变化与化学 变化过程的一组特定的活动。 2.寻找价值流及后续动作。在识别价值流时我们从流程分析、程序分析、操作分析、 动作分析这五个方面由宏观到微观的对价值流进行识别、分析、改善、实施、控制。 3.消除有害的八种浪费现。不良的浪费,过分加工的浪费,动作的浪费,搬运的浪 费,库存的浪费,制造过多/过少的浪费,等待的浪费,管理的浪费。 4.使信息流动起来。找出管理中的关键工序,即扩宽信息流的流动渠道,如采用扁 平化的管理模式
*大多生产时间是无附加值 most of the production time is non-value added *不稳定的生产制程造成有效解决问题的困难 an unstable production process makes effective problem solving difficult, if not impossible *不稳定生产制程迫使危机管理取代了策略领导 an unstable production process forces crisis management instead of strategic leadership
- 1、下载文档前请自行甄别文档内容的完整性,平台不提供额外的编辑、内容补充、找答案等附加服务。
- 2、"仅部分预览"的文档,不可在线预览部分如存在完整性等问题,可反馈申请退款(可完整预览的文档不适用该条件!)。
- 3、如文档侵犯您的权益,请联系客服反馈,我们会尽快为您处理(人工客服工作时间:9:00-18:30)。
•O-ring, bearing, snap ring • Daily schedule
Assembly DIST
C/T = 30 Sec C/O = 30 Min Uptime 75% Batch Size 100
1000 pcs
C/T = 45 Sec C/O = 60 Min Uptime 95% Batch Size 100
The learning objective for this course is not:
To teach Lean Tools to help achieve Future State
Value Stream Mapping
3
What’s in It for Me?
Define
Value stream mapping is a visual tool to help understand the current value stream.
Define
Assign Value Stream Manager
One person to manage the mapping of the total flow Has the capability to make changes across departmental boundaries Leads the creation and prioritization of the implementation plan for getting from present state to future state Monitors implementation and updates implementation plan Driver for results
5000 pcs
C/T = 60 Sec C/O = 5 Min Uptime 95% Batch Size 100
100 pcs
C/T = 50 Sec
C/O = 10 Min Uptime 95% Batch Size 100
200 pcs
15 hours 30 sec 45 sec
83 hours 60 sec
Value Stream Mapping
5
Value Stream Mapping Process Steps
Define
Identify Current State
Step 1: SIPOC Chart Step 2: Top Down Flow Chart Step 3: Determine Product Family
Step 4: Step 5: Step 6: Step 7:
Hale Waihona Puke Draw Process Flow Draw Material Flow Draw Information Flow Process Data Collection
Step 8: Add Process and Lead Time data Step 9: Verify Current State Map
Mat Bin
Forge Machine
Module
Assembly
TPM
Batch
200 pcs
Set-up Reduction
FIFO
Max 100 pcs
Assembly
2/Day
FIFO
Max 200 pcs
DIST
C/T = 30 Sec C/O = 30 Min Uptime 95% Batch Size 100
Define
ASSEMBLY
90/60/30 Day
Customer
Production Control
Daily Order Daily Order
20,000 pcs/mo Module=100
Daily
Mat
1) Set-up reduction 2) Pull Systems 3) TPM
Receiving Warehouse
Value Stream Mapping
7
Current State VSM
6 Month Forecast
SUPPLIER
Define
ASSEMBLY
90/60/30 Day
Customer
MRP
1/Week
Production Control
Daily Order
Weekly Fax
20,000 pcs/mo Module=100
Measure
Value Stream Mapping
SIPOC Top-Down
Analyze
Map Mapping
Value-Stream
Improve
Control
Process Mapping Hierarchy
SIPOC chart
S U P P L I E R I N P U T
Value Stream Mapping
2
Learning Objectives
Define
The learning objectives for this course are:
Be able to create Current State and Future State Value Stream Maps Be able to use customer and business requirements to prioritize improvement opportunities
Identify and Prioritize Improvement Opportunities Determine Future State Implement Improvements to Achieve Future State
6
Value Stream Mapping
Value Stream Manager
2.5 hours 30 sec
10 hours
2 hours 60 sec
4 hours
Production lead time = 18 hours 33 min Processing time = 185 seconds
45 sec
50 sec
9
Value Stream Mapping
9
Define
C/T = 45 Sec
C/O = 10 Min Uptime 95% Batch Size 100
500 pcs
C/T = 60 Sec C/O = 5 Min Uptime 95%
Module Size100
C/T = 50 Sec C/O = 10 Min Uptime 95%
Module Size 100
300 Per Day 400 Min Avail 1 Shift C/T 12 Min
Single Plant
1200 Min Avail
3 Shift C/T 3 Min
Process Steps
Value Stream Mapping
11
Router Steps
Define
Measure
Analyze
Supplier Input Process Output Customer (SIPOC) Map
Step 1
Improve
Control
Step 1: High-Level SIPOC Chart
Define
Supplier Input Process Output Chart (SIPOC)
13
Step 1: The SIPOC Chart
Translate
Define
Customer requirements into output specifications and identify related Key Process Output Variables (KPOVs) Go Upsteam to the Process Steps(s) which most impact the OUTPUT and determine the Key Process Input Variables (KPIVs) Try to use Leading Measure(s) (instead of Lagging Measures – if lagging, then Close/Reduce amount of Lagging)
Define
PROCESS
O U T P U T
C U S T O M E R
Company
Top Down Process Flow
Step 1
4
Mult. Plants
VSM
48
I
Step 2 2
180 Per Day
22
I
Step 3 1
450 Per Day 400 Min Avail 1 Shift C/T 7 Min
Define
Measure
Value Stream Mapping
Analyze
Improve
Control
Agenda
Define
Monday
Kick-Off Introductions Current State Steps 1-4
Tuesday
Current State Steps 5-7
It allows people to easily understand where waste exists in the process. It gives the team a basis for prioritizing improvement efforts.