小方坯连铸过程实时温度场预报模型的开发
连铸坯热装热送中的温度分布监测与控制技术优化

连铸坯热装热送中的温度分布监测与控制技术优化近年来,随着连铸技术的发展和应用,连铸坯热装热送技术在钢铁制造中得到了广泛应用。
然而,由于连铸坯的温度分布不均匀,给生产工艺和产品质量带来了一系列的挑战。
为了解决这一问题,温度分布监测与控制技术优化显得尤为重要。
本文将探讨连铸坯热装热送过程中的温度分布监测与控制技术的优化方法。
一、温度分布监测技术优化温度分布监测是确保连铸坯热装热送过程中温度均匀的关键。
目前,常用的温度分布监测技术有红外热像仪、热电偶和红外线测温技术等。
红外热像仪适用于对连铸坯表面温度分布进行实时监测。
通过红外线将连铸坯表面的温度信息转化成电信号,并利用图像处理技术进行显示和分析,可以实现对连铸坯温度分布的监测。
然而,由于红外热像仪对连铸坯表面的反射率较为敏感,因此在实际应用中需要进行校正和修正。
热电偶是一种常用的温度传感器,通过热电效应测量连铸坯表面的温度。
热电偶具有精度高、响应速度快等优点,但由于其自身热容量大,对连铸坯表面温度分布的监测存在一定的滞后性。
红外线测温技术则是一种非接触式的温度测量技术,适用于连铸坯表面温度的实时测量。
该技术通过探测连铸坯表面发射的红外线能量,利用斯特藩—玻尔兹曼定律来计算连铸坯的表面温度。
红外线测温技术具有快速响应、测量范围广等优点,但在一些特殊情况下,如强烈的辐射场或表面被污染等情况下,测温精度可能会受到一定的影响。
二、温度分布控制技术优化温度分布控制是保证连铸坯质量和生产过程稳定的关键环节。
常用的温度分布控制方法有静态控制和动态控制两种。
静态控制主要是通过合理设置连铸机的结构参数,如结晶器的冷却水量、冷却方式等,来调整连铸坯的温度分布。
例如,通过调节结晶器冷却水量和结晶器壁面的冷却方式,可以改变连铸坯中心和表面的温度差异,从而实现温度分布的优化。
动态控制则是利用连铸过程中的温度测量数据和数学模型,对连铸机进行实时控制。
通过测量连铸坯表面的温度变化,结合模型预测和实时调整,可以实现对连铸坯温度分布的精确控制。
连铸方坯动态轻压下位置

连铸方坯动态轻压下位置张松;杨彦宏【摘要】为准确确定铸坯凝固末端的位置,合理选择压下区域,为实施动态轻压下提供有效技术手段,利用数值模拟方法计算某炼钢厂2#铸机连铸方坯中温度场,用传热模型分析了45#钢在某工艺下的铸坯温度分布图.固相率0.3为轻压下初始点,压下区间总长度为10 m且拉速0.76 m/min时的压下量为0.7 mm/m.【期刊名称】《辽宁科技大学学报》【年(卷),期】2010(033)002【总页数】4页(P132-135)【关键词】连铸方坯;温度场;动态轻压下【作者】张松;杨彦宏【作者单位】辽宁科技大学,材料科学与冶金学院,辽宁,鞍山,114051;辽宁科技大学,机械工程与自动化学院,辽宁,鞍山,114051【正文语种】中文【中图分类】TF777在连铸生产中,板坯内部一般都会存在中心偏析、中心疏松及内裂等缺陷,影响了铸坯内部质量。
抑制内部缺陷问题最有效且经济的方法是采用轻压下技术[1]。
凝固末端的轻压下技术始于20世纪70年代末,是在辊缝收缩的基础上发展起来的。
在铸坯凝固末端,对铸坯施以2%-3%的压下量,以阻止凝固末端富集偏析元素的钢液向下流动,减少中心偏析[2]。
动态轻压下技术已成为现代连铸机关键技术的重要组成部分[3]。
在铸坯凝固过程中,坯壳至中心分为固态、固-液态、液-固态和液态四个区域。
由于选分结晶,在铸坯凝固末端的残余液相中含有的溶质浓度很高,当这些残余液相在铸坯中心部位凝固时,会产生很严重的中心偏析[4]。
在铸坯凝固过程中,如果柱状晶发达,会在凝固末端形成“搭桥”,阻碍上游钢液向下游动,凝固末端的残余液相不能被上游溶质浓度低的钢液稀释,就会在铸坯中心形成一条偏析带。
同时,残余液相在凝固末端急速凝固时,会急剧收缩,产生缝隙,如不能得到钢液的补充,就会产生疏松[5]。
轻压下的目的,就是要通过机械压下来补偿铸坯凝固后期体收缩,抑制枝晶间浓化钢水向中心富集,减轻或焊和中心疏松,减轻中心偏析。
连铸过程原理及数值模拟

连铸过程原理及数值模拟连铸是一种重要的金属成形工艺,广泛应用于钢铁、铝合金等金属材料的生产和加工中。
连铸过程原理及数值模拟是研究连铸工艺的关键内容,通过对连铸过程的原理分析和数值模拟,可以优化连铸工艺参数,提高产品质量和生产效率。
连铸过程是将熔融金属直接注入到连续运动的铸坯中,通过冷却和凝固过程,将熔融金属转化为固态铸坯。
连铸的基本原理是利用连续运动的铸坯带走热量,使熔融金属迅速凝固,形成连续的固态铸坯。
在连铸过程中,主要包括液相区、液固两相区和固相区三个区域。
在液相区,熔融金属通过连续浇注,填充到铸坯的空腔中。
熔融金属的温度高于固相线,处于液态状态。
随着熔融金属的注入,液相区的长度逐渐增加。
在液固两相区,熔融金属和正在凝固的铸坯同时存在。
由于熔融金属的温度高于固相线,所以熔融金属仍然保持液态。
而铸坯由于受到液相的热量传递,开始逐渐凝固。
在这个区域中,液相区的长度逐渐减小,凝固铸坯的长度逐渐增加。
在固相区,整个铸坯都已经完全凝固。
熔融金属已经完全转化为固态,形成连续的固态铸坯。
在这个区域中,液相区的长度为零,凝固铸坯的长度为整个连铸过程的长度。
为了研究连铸过程的细节和优化连铸工艺参数,数值模拟成为一种重要的方法。
数值模拟是通过数学模型和计算机仿真技术,对连铸过程进行模拟和分析。
数值模拟可以准确地计算连铸过程中的温度场、流场和凝固结构等关键参数,为工艺优化提供科学依据。
在连铸过程的数值模拟中,需要考虑多个物理过程的相互作用。
首先是流体力学过程,包括熔融金属的流动和铸坯带走热量的过程。
其次是热传导过程,包括熔融金属的冷却和凝固过程。
最后是凝固结构演化过程,包括铸坯的晶粒生长和偏析等现象。
为了建立连铸过程的数值模型,需要考虑材料的物理性质、流体力学和热传导方程等方面的参数。
同时,还需要考虑边界条件和初始条件等参数。
通过数值模拟,可以预测连铸过程中的温度分布、流速分布和凝固结构等重要参数,为工艺优化提供指导。
安徽工业大学科技成果——方坯连铸机动态轻压下控制系统

安徽工业大学科技成果——方坯连铸机动态轻压下
控制系统
成果简介
方坯连铸机动态轻压下控制系统能够实现对在线铸坯进行适当压下,以解决高拉速条件下的铸坯中心偏析、中心缩孔问题,提高铸坯的内部质量。
系统主要由铸坯凝固传热模型、二冷动态配水控制模型、轻压下动态控制模型三部分组成,其中铸坯凝固传热模型能够根据实时工艺条件计算在线铸坯当前的温度分布;二冷动态配水控制模型能够根据中包钢水温度、拉速的变化对二冷水量实时动态调节,优化铸坯冷却条件,提高铸坯质量;轻压下动态控制模型能够根据铸坯凝固特点选择最优的压下制度对铸坯进行压下操作,优化铸坯内部质量。
成熟程度和所需建设条件
成熟程度:本控制系统已在苏钢应用,使用效果较好。
所需建设条件:本控制系统需要在连铸机上配置动态压下装置。
社会经济效益分析
采用方坯动态轻压下技术后,显著的提高了铸坯内部质量,尤其是对轴承钢、弹簧钢等高附加值钢种,有力的保证了最终产品的质量,提高了企业的经济效益。
八流方坯中间包流场及温度场数值模拟

·研究与设计·八流方坯中间包流场及温度场数值模拟向宏学1,2① 夏芳勇1,2 逯巍1,2 武国平1,2(1:北京首钢国际工程技术有限公司冶金工程分公司炼钢事业部 北京100043;2:北京市冶金三维仿真设计工程技术研究中心 北京100043)摘 要 随着小方坯连铸机拉速的提高,中间包的冶金功能越来越受到重视。
对于高拉速连铸,钢液中夹杂物需控制严格,中间包内钢水温度和成分的均匀性也至关重要。
合理的中间包流场不仅可以增加夹杂物上浮时间从而减少钢液夹杂,更有利于均匀中间包内钢液温度及成分。
本文基于八流小方坯铸机一体式中间包展开流场、温度场数值模拟计算,计算了三个方案中间包的流场及温度场分布情况。
计算结果表明,挡墙、档坝的设计有利于均匀中间包内钢液流场,减少死区13 2%,延长平均停留时间52s。
湍流抑制器的设置,将中间包液面附近流速由0 2m/s降低至0 14m/s左右,有效的抑制湍流产生,减少卷渣。
关键词 小方坯连铸;中间包;流场;温度场中图法分类号 TG243 TF777.2 文献标识码 ADoi:10 3969/j issn 1001-1269 2024 02 001NumericalSimulationoftheFlowandTemperatureFiledinEightStrandTundishXiangHongxue1,2 XiaFangyong1,2 LuWei1,2 WuGuoping1,2(1:SteelMakingBusinessDivisionofMetallurgicalEngineeringBranch,BSIET,Beijing100043;2:BeijingMetallurgy3 DSimulationDesignEngineeringTechnologyResearchCenter,Beijing100043)ABSTRACT Asthecastingspeedofbilletgrowsupdaily,thetundishmetallurgicalfunctionsarepaidmoreattentions.Forhighspeedcontinuouscasting,theinclusionsinmoltensteelshouldbestrictlycontrolled,alsothetemperatureandcompositionuniformityofmoltensteelintundishareveryimportanttoo.Qualifiedflowfieldintundishcannotonlyreduceinclusionsinmoltensteelbyincreasingthefloatingtime,butalsobegoodtouniformthetemperatureandcompositionofmoltensteel.Inthispaper,basedonthenumericalsimulation,thedistributionofflowandtemperaturefieldofthetundishforeight strandbilletcasteriscalculated.Thecalculationresultsshowthatthedesignofretainingwallanddamisbeneficialtotheuniformoftheflowfield.Thedeadzoneofflowfieldisreducedby13 2%,andtheaverageresidencetimeisincreasedby52s.Theturbulenceinhibitorcanreducetheflowvelocityneartheliquidleveloftundishfromabout0 2m/stoabout0 12m/s,whicheffectivelyinhibitsturbulenceandreducesslagentrapment.KEYWORDS Billetcontinuescasting;Tundish;Flowfiled;Temperaturefiled1 前言随着中间包冶金技术的不断提升,中间包不再是传统意义上的钢水储存、稳流、缓冲容器,逐渐转变成实现夹杂物上浮、夹杂物改质变性处理以及钢水微合金化的冶金反应容器。
procast指导书_实验五实验六

43铸造过程数值模拟综合实验前言一、铸造过程数值模拟的来源、内容和意义为了生产出合格的铸件,就要对影响其形成的因素进行有效的控制。
铸件的形成主要经历了充型和凝固两个阶段,宏观上主要涉及到液态金属充型流动、金属凝固和冷却收缩、高温金属冷却和收缩3种物理现象。
在充型过程中,流场、温度场和浓度场同时变化,凝固时伴随着温度场的变化的同时存在着枝晶间对流和收缩现象;收缩则导致应力场的变化。
与流动相关的主要缺陷有:浇不足、冷隔、气孔、夹渣;充型中形成的温度场分布直接关系到后续的凝固冷却过程;充型中形成的浓度场分布与后续的冷却凝固形成的偏析和组织不均匀有关。
凝固过程的温度场变化及收缩是导致缩孔缩松的主要原因,枝晶间对流和枝晶收缩是微观缩松的直接原因,热裂冷裂的形成归因于应力场的变化。
可见,客观地反映不同阶段的场的变化,并加以有效的控制,是获得合格铸件的充要条件。
传统的铸件生产因其不同于冷加工的特殊性,只能对铸件的形成过程进行粗糙的基于经验和一般理论基础上的控制,形成的控制系统——铸造工艺的局限性表现在:1)只是定性分析;2)要反复试制才能确定工艺。
铸造过程数值模拟的目的就是要对铸件形成过程各个阶段的场的变化进行数值解析以获得合理的铸件形成的控制参数,其内容主要包括温度场、流场、浓度场、应力场等的计算模拟。
二、铸造过程数值模拟原理铸造过程数值模拟技术的实质是对铸件成型系统(包括铸件—型芯—铸型等)进行几何上的有限离散,在物理模型的支持下,通过数值计算来分析铸造过程有关物理场的变化特点,并结合铸造缺陷的形成判据来预测铸件质量。
数值解法的一般步骤是:1)汇集给定问题的单值性条件,即研究对象的几何条件、物理条件、初始条件和边界条件等。
2)将物理过程所涉及的区域在空间上和时间上进行离散化处理。
3)建立内部节点(或单元)和边界节点(或单元)的数值方程。
4)选用适当的计算方法求解线性代数方程组。
5)编程计算。
其中,核心部分是数值方程的建立。
用控制容积法求解连铸方坯温度场

·16·
图7铸坯网格划分示意图
万方数据
A
伽。B
o
~
o
埘。o
川。B
一 捌。o 坍。 川。B
~
~
一
~
~
~
~
~
~
~
~
~
~
~
~
~
~
~
~
o
o
~
~
o
即E J扩0
式中
A=B 11 C
D =D
})
,L,L ,.7
+
-
.0
一
1
钮%o
~
分峨帆也o
~
~
I
理,尤其C(T),A(丁)其最大与最小值相差一倍。本课题对其进行高次曲线拟合,其应用的前提是:首先 对传热方程进行前述的变换,使其不对模型的求解造成困难。p(T),C(T),A(丁)的拟合曲线如图2、图3、 图4所示。
·14·
万方数据
肌,m.℃
3 4 5 6 7 8 9 10 11 12’3’4×10015℃
¨.
¨. . ~.
~. O 0
O 0
¨
~ ~
~凡~
~ ~
1+4Fo
一“o
一2Fo
—-d
~
~
I
州一".H—。.。.L ~o I
~
o
~
o
~
o
~
研。
~
~
~
~
~
一
~
B
盯。o 一2订 。坷c 0
n+
.巾
O .“
n + 、J
连铸坯热装热送中的温度分布监测与控制技术改进与优化
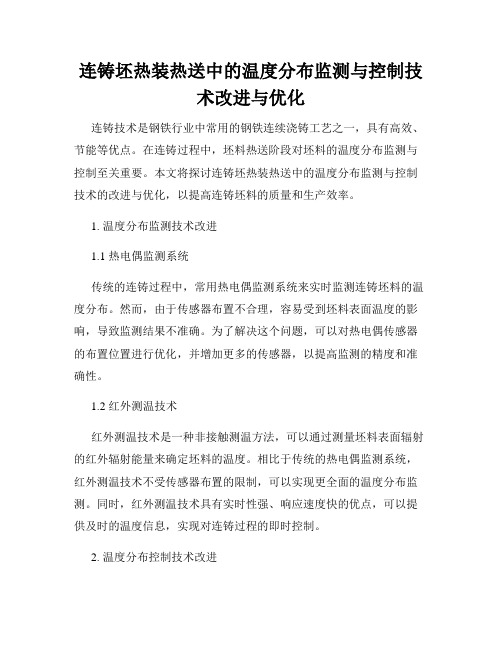
连铸坯热装热送中的温度分布监测与控制技术改进与优化连铸技术是钢铁行业中常用的钢铁连续浇铸工艺之一,具有高效、节能等优点。
在连铸过程中,坯料热送阶段对坯料的温度分布监测与控制至关重要。
本文将探讨连铸坯热装热送中的温度分布监测与控制技术的改进与优化,以提高连铸坯料的质量和生产效率。
1. 温度分布监测技术改进1.1 热电偶监测系统传统的连铸过程中,常用热电偶监测系统来实时监测连铸坯料的温度分布。
然而,由于传感器布置不合理,容易受到坯料表面温度的影响,导致监测结果不准确。
为了解决这个问题,可以对热电偶传感器的布置位置进行优化,并增加更多的传感器,以提高监测的精度和准确性。
1.2 红外测温技术红外测温技术是一种非接触测温方法,可以通过测量坯料表面辐射的红外辐射能量来确定坯料的温度。
相比于传统的热电偶监测系统,红外测温技术不受传感器布置的限制,可以实现更全面的温度分布监测。
同时,红外测温技术具有实时性强、响应速度快的优点,可以提供及时的温度信息,实现对连铸过程的即时控制。
2. 温度分布控制技术改进2.1 水箱布置优化连铸过程中,水箱对冷却坯料起到重要作用。
优化水箱的布置可以提高冷却效率,进而改善坯料的温度分布。
通过建立数值模拟模型,分析坯料在水箱中的流动和冷却情况,确定最优的水箱布置方案。
此外,可考虑引入新型的冷却装置,如水雾喷淋系统或喷水帘,以提高水箱的冷却效果。
2.2 温度自动调控系统为了实现连铸坯料的精确温度控制,可以采用温度自动调控系统。
该系统通过对连铸坯料的温度实时监测,并通过控制流量调节阀、喷水量等参数,自动调整冷却水的供应,以实现坯料温度的精确控制。
同时,为了提高系统的控制精度和稳定性,可以引入先进的控制算法,并结合联合控制策略,如模糊控制或神经网络控制,以进一步优化控制效果。
3. 技术改进与优化带来的效益3.1 提高坯料质量通过优化温度分布监测与控制技术,可以实现对连铸坯料温度的精确控制,避免温度偏差过大而导致坯料质量不稳定。
- 1、下载文档前请自行甄别文档内容的完整性,平台不提供额外的编辑、内容补充、找答案等附加服务。
- 2、"仅部分预览"的文档,不可在线预览部分如存在完整性等问题,可反馈申请退款(可完整预览的文档不适用该条件!)。
- 3、如文档侵犯您的权益,请联系客服反馈,我们会尽快为您处理(人工客服工作时间:9:00-18:30)。
DEVELOPM ENT oF FORECAS M ODEL OR T F REAL —TI E M TENⅡ R . A 】 _ FⅡⅡ I C0NTⅡ J S CAS RE D N 0U TⅡ OF BⅡ . G LET
和优 化控 制是 获得 高质 量铸 坯 的前 提和 保证 。在
总 第 19期 8
2 1年 第 9 期 0I
河 北 冶全
H EBEI M ETA LLU R GY
Tபைடு நூலகம் a l 9 tl 8 2 N Ulb r9 0I 1 l e I
小 方 坯 连 铸 过 程 实 时 温 度 场 预 报 模 型 的 开 发
范 佳, 朱开 军 , 玉虎 , 建文 孙 李
me i a i ie dfe e c eho nson lfnt if r n e m t d,a d t e c lu ai n pr g a i e e o e . Thr ug e g t e p a — n h ac l to o r m sd v l p d by US o h d bu h r c
( 北 钢 铁 集 团 邯 钢 公 司 技 术 中心 , 北 邯 郸 0 6 1 ) 河 河 50 5 摘 要 : 于 凝 固 传 热 学 基 本 理 论 和 对 小 方 坯 连 铸 工 况 的分 析 , 用 二 维 有 限差 分 法 建 立 了 小 方 坯 连 铸 过 基 采 程 实 时温 度 场 预 报 模 型 , 自主 开 发 了 计 算 程 序 。通 过 调 试 , 证 了 该 模 型 的 实 用 性 和 准 确 性 , 现 了 并 验 实 生 产 过 程 中 小 方 坯 温 度 场 的实 时 预 报 , 动 态 配 水 及 动态 轻 压 下 技 术 的 开 发 打 下 了基 础 。 为 关 键 词 : 方 坯 ; 铸 ; 度场 ; 报 ; 型 ; 发 小 连 温 预 模 开
na i i tpr s e h qu m c lgh e s tc ni e.
K e or s: il t on i uo a tn yW d b le ;c tn us c s i g; t m p r t r i l e e a u e fe d; f r c s ;m o l e l pme oe at de ;d ve o nt
铸坯 温度 场 和凝 固终 点 进 行 动态 跟 踪 和 计 算 ; 仪 不
为过 程动 态二 冷 配水 与动态 轻压 下在 线控 制 系统 的 实现 提供 了重要 保 证 , 可 以降低 开 发在 线 控 制 系 还
统 的 风 险 、 本 和周 期 , 时 为 连 铸 技 术 和 操 作 人 员 成 同
1
前 言
坯 断 面 10 rm ×10 mm, 计 冷 却 区为 4个 。基 5 u 5 设 于 上述设 备 特点 , 文 开 发 的连 铸 过 程 实 时温 度 场 本 预报 模 型可 以在 线 或 离 线 模 拟实 际 的连 铸 工 况 , 对
连铸 过程 是一 个 铸 坯 温 度 场 连 续 变 化 的过 程 , 不合 理 的铸坯 温 度 分 布 往 往会 导致 裂 纹 等 缺 陷 , 因 此 , 连铸 现场 铸 坯 的温 度 场 进 行 动 态 的 跟踪 监 测 对
F n Ja a i ,Zh i n,S n Yu u,L in n u Kaj u u h iJ we a
( e h iu Ce tr Ha d n rn n te mp n T c nq e ne , n a Io a d Se lCo a y, He e rn a d te o p, Ha d n , He e , b i o n Se lGr u I na bi
0 601 5 5)
Absr c : s d on ba i o i fc to a ta t Ba e sc s ldiia in he t— ta se he y n n l i o o kig c nd t fc tn us r n f r t or a d a ayss fw r n o ii on o on iuo
c s i il t t o e a t m o e f r al tm e t m pe a u e fe d i a t il t i u l wih t at ng of b le , he f r c s d l o e — i e r t r l n c s i of b l s b it i ng e t wo — d — i
tc bi t n c ur c he mod l a e v r fe i a l y a d a c a y of t i e r e i d. W ih i t e l—tm e f e a t o e i t t he r a i or c s f t mpe a u e f e d i o— r t r i l n pr du to f bil t i e lz d, a s s f u e o e l pm e t o y m i a e o ori n n n y— c in o l sr aie e nd a ba e i o nd d f r d ve o n f d na c w t r pr p t o i g a d d