离合器参数设计
(整理)离合器摩擦片技术参数.
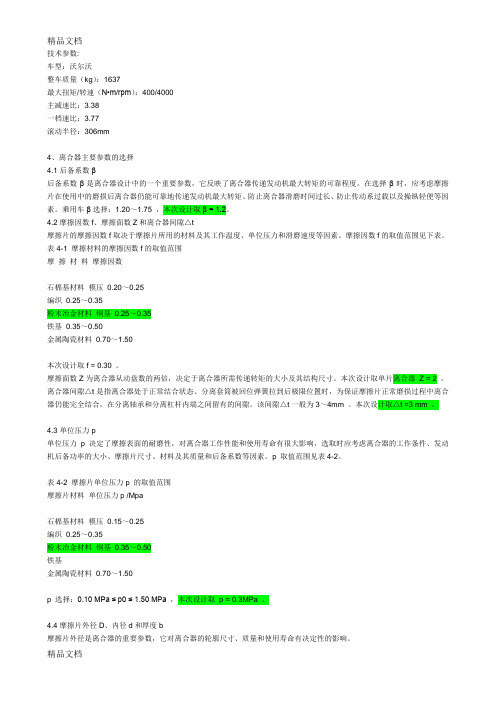
技术参数:车型:沃尔沃整车质量(kg):1637最大扭矩/转速(N•m/rpm):400/4000主减速比:3.38一档速比:3.77滚动半径:306mm4、离合器主要参数的选择4.1后备系数β后备系数β是离合器设计中的一个重要参数,它反映了离合器传递发动机最大转矩的可靠程度。
在选择β时,应考虑摩擦片在使用中的磨损后离合器仍能可靠地传递发动机最大转矩、防止离合器滑磨时间过长、防止传动系过载以及操纵轻便等因素。
乘用车β选择:1.20~1.75 ,本次设计取β = 1.2。
4.2摩擦因数f、摩擦面数Z和离合器间隙△t摩擦片的摩擦因数f取决于摩擦片所用的材料及其工作温度、单位压力和滑磨速度等因素。
摩擦因数f的取值范围见下表。
表4-1 摩擦材料的摩擦因数f的取值范围摩擦材料摩擦因数石棉基材料模压0.20~0.25编织0.25~0.35粉末冶金材料铜基0.25~0.35铁基0.35~0.50金属陶瓷材料0.70~1.50本次设计取f = 0.30 。
摩擦面数Z为离合器从动盘数的两倍,决定于离合器所需传递转矩的大小及其结构尺寸。
本次设计取单片离合器Z = 2 。
离合器间隙△t是指离合器处于正常结合状态、分离套筒被回位弹簧拉到后极限位置时,为保证摩擦片正常磨损过程中离合器仍能完全结合,在分离轴承和分离杠杆内端之间留有的间隙。
该间隙△t一般为3~4mm 。
本次设计取△t =3 mm 。
4.3单位压力p单位压力p 决定了摩擦表面的耐磨性,对离合器工作性能和使用寿命有很大影响,选取时应考虑离合器的工作条件、发动机后备功率的大小、摩擦片尺寸、材料及其质量和后备系数等因素。
p 取值范围见表4-2。
表4-2 摩擦片单位压力p 的取值范围摩擦片材料单位压力p /Mpa石棉基材料模压0.15~0.25编织0.25~0.35粉末冶金材料铜基0.35~0.50铁基金属陶瓷材料0.70~1.50p 选择:0.10 MPa ≤ p0 ≤ 1.50 MPa ,本次设计取p = 0.3MPa 。
汽车离合器基本参数的优化分析)

汽车离合器基本参数的优化分析机电学院机械设计制造及其自动化专业摘要离合器是汽车传动系统中直接与发动机相连的部件,它是依靠主从动片之间的摩擦力矩来传递动力的,并通过分离、接合来控制车辆动力传动系的工作状态。
其主动部分和从动部分可以暂时分离,又可逐渐接合,并且在传动过程中还可以相对转动。
离合器分离、接合过程的质量影响车辆换挡品质、车辆换挡冲击。
离合器的性能对汽车平稳起步、换挡时工作平顺和传动系过载有着重要影响。
汽车离合器的基本参数主要有离合器的后备系数、摩擦面单位面积上的压力p0、摩擦片外径D和内径d 等,这些参数的变化直接影响离合器的结构尺寸和工作性能。
本文采用优化设计方法来确定最佳的离合器基本参数,实例计算表明了该方法的实用性。
关键词:离合器;基本参数;优化设计AbstractClutch auto transmission system is connected directly with engine parts,it relies on master-slave move between the friction torque tablet to transfer power,and through the separation, joints to control vehicle power transmission system working condition. The performance of clutch has an important influence on auto start,the smooth of shift and the overload of transmission system。
The basic parameters of clutch are the backup coefficient , the pressure per unit area of friction plane p0, the outer diameter of friction plate D, the inner diameter of friction plate d, etc. These parameters affect the structure dimension and performance of clutch directly. This paper determines the optimal basic parameters of clutch with optimum method. The practicability of optimum method is testified by the example.Keywords: clutch; basic parameters ; optimum design目录摘要I第一章绪论 11.1 研究背景 11.2 研究意义 21.3 国内外现状 31.3.1 离合器的总类与发展 31.3.2 离合器的研究现状 41.3.3 主要研究内容 5第二章离合器的介绍 62.1 离合器结构组成与工作过程 6 2.2 摩擦离合器的介绍82.2.1 摩擦离合器的分类82.2.2 摩擦离合器的结构形式82.2.3 摩擦离合器的摩擦面材料9 2.2.4 摩擦离合器压盘的传力方式9 2.2.5 离合器的操作机构10第三章离合器基本参数的分析13 3.1 离合器主体部分基本参数133.1.1 后备系数143.1.2 单位面积压力143.1.3 摩擦片外径、内径和厚度15 3.2 离合器扭转减震器基本参数16 3.2.1 扭转减震器刚度163.2.2 扭转减振器最大摩擦力矩16 3.3.3 扭转减振器的预紧力矩163.3 离合器操纵机构的基本参数17 3.3.1 踏板力173.3.2 踏板行程18第四章优化分析194.1 优化设计概论194.1.1 基本概念194.1.2 优化过程194.1.3 优化设计建模204.2 离合器基本参数优化建模 214.2.1 基于离合器尺寸形状的优化214.2.2 基于离合器扭转振动特性的优化244.2.3 基于离合器操作舒适性的优化27第五章总结与展望305.1 总结305.2 展望30参考文献34致谢35第一章绪论1.1 研究背景1953年我国成立了第一汽车制造厂,最初汽车作为一种交通工具产生。
汽车膜片弹簧离合器设计---设计说明书
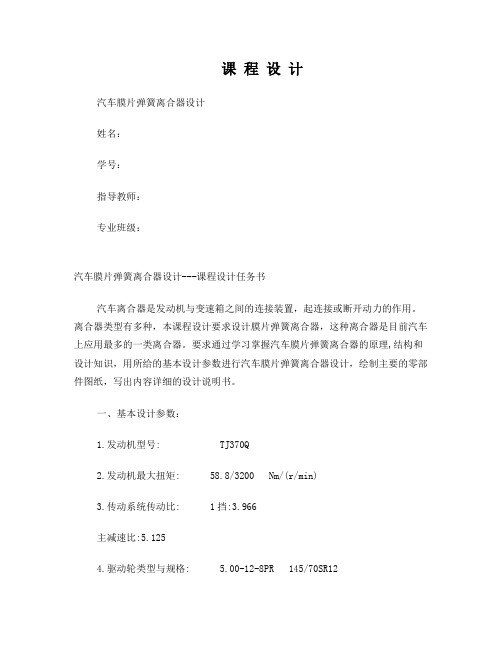
课程设计汽车膜片弹簧离合器设计姓名:学号:指导教师:专业班级:汽车膜片弹簧离合器设计---课程设计任务书汽车离合器是发动机与变速箱之间的连接装置,起连接或断开动力的作用。
离合器类型有多种,本课程设计要求设计膜片弹簧离合器,这种离合器是目前汽车上应用最多的一类离合器。
要求通过学习掌握汽车膜片弹簧离合器的原理,结构和设计知识,用所给的基本设计参数进行汽车膜片弹簧离合器设计,绘制主要的零部件图纸,写出内容详细的设计说明书。
一、基本设计参数:1.发动机型号: TJ370Q2.发动机最大扭矩: 58.8/3200 Nm/(r/min)3.传动系统传动比: 1挡:3.966主减速比:5.1254.驱动轮类型与规格:5.00-12-8PR 145/70SR125.汽车总质量: 1429KG二、设计内容及步骤1、离合器主要参数的确定(1)根据基本设计参数确定离合器主要参数:①后备系数;②单位压力;③摩擦片内外径D、d和厚度b;④摩擦因素f、摩擦面数Z等。
(2)摩擦片尺寸校核与材料选择。
2、扭转减震器的设计(1)确定扭转减震器结构(2)确定扭转减震器主要参数(3)确定减震弹簧尺寸3、从动盘总成设计(1)从动片设计(2)从动盘毂设计(3)确定从动盘摩擦材料4、离合器盖总成的设计(1)选择压盘内外径、厚度及材料,并进行校核(2)离合器盖设计(3)支撑环设计5、膜片弹簧的设计(1)膜片弹簧基本参数选择(2)膜片弹簧强度计算三、设计成果要求1、设计计算说明书(1)设计计算说明书要包括:封面、课程设计任务书、目录、中英文摘要、正文、参考文献等。
(2)正文主要体现:进行各零部件的参数选择与计算时的理论依据、计算步骤及对计算结果合理性的阐述。
(3)课程设计说明书统一用A4纸打印或撰写,要求排版整洁合理,字迹工整,图文并貌。
2、设计图纸(1)零件图纸包括: 磨擦片、从动片、从动盘毂、压盘、膜片弹簧图(2)离合器总成结构装配图尺寸标注、公差标注、技术要求、明细栏等完整。
离合器设计说明书

目录一离合器结构设计 (2)离合器结构选择与论证离合器结构设计要点离合器主要零件的设计二离合器的设计计算及说明 (7)离合器设计所需数据摩擦片主要参数选择摩擦片基本参数设计优化膜片弹簧主要参数的选择膜片弹簧的优化设计膜片弹簧的载荷与变形关系膜片弹簧的应力计算扭转减震器设计减震弹簧的设计踏板行程及踏板力计算从动轴的计算从动盘毂分离轴承的寿命计算三心得体会 (25)四参考文献 (26)一离合器的结构设计为了达到计划书所给的数据要求,设计时应根据车型的类别、使用要求、制造条件,以及“系列化、通用化、标准化”的要求等,合理选择离合器结构。
离合器结构选择与论证摩擦片的选择单片离合器因为结构简单,尺寸紧凑,散热良好,维修调整方便,从动部分转动惯量小,在使用时能保证分离彻底接合平顺,所以被广泛使用于轿车和中、小型货车,因此该设计选择单片离合器。
摩擦片数为2。
压紧弹簧布置形式的选择离合器压紧装置可分为周布弹簧式、中央弹簧式、斜置弹簧式、膜片弹簧式等。
其中膜片弹簧的主要特点是用一个膜片弹簧代替螺旋弹簧和分离杠杆。
膜片弹簧与其他几类相比又有以下几个优点[9]:(1)由于膜片弹簧有理想的非线性特征,弹簧压力在摩擦片磨损范围内能保证大致不变,从而使离合器在使用中能保持其传递转矩的能力不变。
当离合器分离时,弹簧压力不像圆柱弹簧那样升高,而是降低,从而降低踏板力;(2)膜片弹簧兼起压紧弹簧和分离杠杆的作用,使结构简单紧凑,轴向尺寸小,零件数目少,质量小;(3)高速旋转时,压紧力降低很少,性能较稳定;而圆柱弹簧压紧力明显下降;(4)由于膜片弹簧大断面环形与压盘接触,故其压力分布均匀,摩擦片磨损均匀,可提高使用寿命;(5)易于实现良好的通风散热,使用寿命长;(6)平衡性好;(7)有利于大批量生产,降低制造成本。
但膜片弹簧的制造工艺较复杂,对材料质量和尺寸精度要求高,其非线性特性在生产中不易控制,开口处容易产生裂纹,端部容易磨损。
离合器摩擦片技术参数
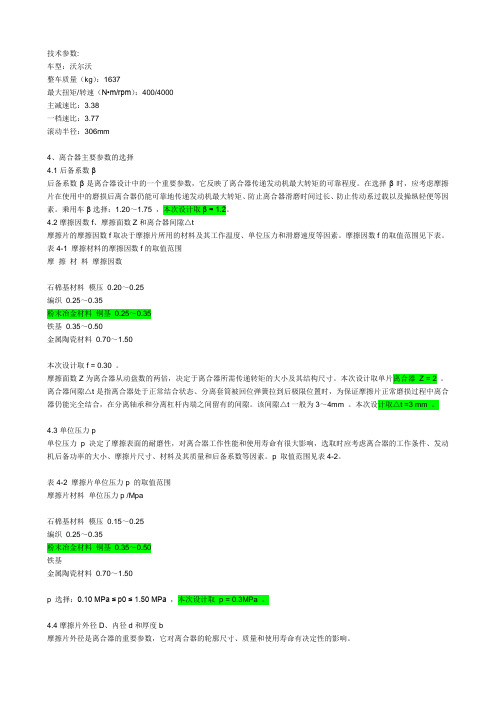
技术参数:车型:沃尔沃整车质量(kg):1637最大扭矩/转速(N•m/rpm):400/4000主减速比:3.38一档速比:3.77滚动半径:306mm4、离合器主要参数的选择4.1后备系数β后备系数β是离合器设计中的一个重要参数,它反映了离合器传递发动机最大转矩的可靠程度。
在选择β时,应考虑摩擦片在使用中的磨损后离合器仍能可靠地传递发动机最大转矩、防止离合器滑磨时间过长、防止传动系过载以及操纵轻便等因素。
乘用车β选择:1.20~1.75 ,本次设计取β = 1.2。
4.2摩擦因数f、摩擦面数Z和离合器间隙△t摩擦片的摩擦因数f取决于摩擦片所用的材料及其工作温度、单位压力和滑磨速度等因素。
摩擦因数f的取值范围见下表。
表4-1 摩擦材料的摩擦因数f的取值范围摩擦材料摩擦因数石棉基材料模压0.20~0.25编织0.25~0.35粉末冶金材料铜基0.25~0.35铁基0.35~0.50金属陶瓷材料0.70~1.50本次设计取f = 0.30 。
摩擦面数Z为离合器从动盘数的两倍,决定于离合器所需传递转矩的大小及其结构尺寸。
本次设计取单片离合器Z = 2 。
离合器间隙△t是指离合器处于正常结合状态、分离套筒被回位弹簧拉到后极限位置时,为保证摩擦片正常磨损过程中离合器仍能完全结合,在分离轴承和分离杠杆内端之间留有的间隙。
该间隙△t一般为3~4mm 。
本次设计取△t =3 mm 。
4.3单位压力p单位压力p 决定了摩擦表面的耐磨性,对离合器工作性能和使用寿命有很大影响,选取时应考虑离合器的工作条件、发动机后备功率的大小、摩擦片尺寸、材料及其质量和后备系数等因素。
p 取值范围见表4-2。
表4-2 摩擦片单位压力p 的取值范围摩擦片材料单位压力p /Mpa石棉基材料模压0.15~0.25编织0.25~0.35粉末冶金材料铜基0.35~0.50铁基金属陶瓷材料0.70~1.50p 选择:0.10 MPa ≤ p0 ≤ 1.50 MPa ,本次设计取p = 0.3MPa 。
湿式离合器设计计算

3.2多片湿式离合器的设计 3.2.1摩擦副元件材料与形式离合器的结构中,摩擦片对离合器工作性能影响很大,而摩擦片材料的选择就尤为重要。
下面进行摩擦副元件的选择:离合器摩擦副元件由摩擦元件及对偶元件两部分组成。
其特点是:可在主、从动轴转速差较大的状态下接合,而且接合时平稳、柔顺。
离合器摩擦副(又称摩擦对偶)可分为两大类:第一类是金属性的,它的摩擦衬面具有金属性质,如钢对钢,钢对粉末冶金等;第二类是非金属性的,它的摩擦衬面摩擦材料具有非金属性质,如石墨树脂等,它们的对偶可用钢和铸铁。
对于坦克离合器摩擦副,由于其工况和传递动力的要求,选择金属型摩擦材料。
目前广泛应用的是铜基粉末冶金,它的主要优点是:1、 有较高的摩擦系数,单位面积工作能力为0.22千瓦/Fp FAA =厘米2;2、 在较大温度变化范围内,摩擦系数变化不大;3、允许表面温度高,可达350C ,非金属在250C 以下。
故高温耐磨性好,使用寿命长;4、 机械强度高,有较高的比压力;5、导热性好,加上表面开槽可获得良好冷却,允许较长时间打滑而不致烧蚀。
此次设计选择摩擦副材料为钢对铜基粉末冶金,根据坦克设计180页表6—1可得:可取摩擦副的摩擦系数μ=0.08,许用压强[]p =4MPa 。
3.2.2摩擦转矩计算多片摩擦离合器的摩擦转矩fc T 与摩擦副数、摩擦系数、压紧力和作用半径有关。
其关系式为:e fcz T Fr μ=式中fc T —摩擦转矩()N M ⋅;μ—摩擦系数,从动力换档传递扭矩出发,取动摩擦系数;F —摩擦片压紧力()N ;e r —换算半径,将摩擦力都换算为都作用在这半径上;z —摩擦副数。
下面求换算半径e r :(如下图示)一对摩擦副上一个单元圆环的摩擦转矩为:fc dT p dA μρ=⋅⋅⋅式中p —单位压力或比压;ρ—圆环半径;dA —单位圆环面积。
而 2dA d πρρ=⋅ 带入前式可得22fcdT p d πμρρ=摩擦副全部面积的摩擦转矩为ρυπd p u T Rrfc ⎰=22式中r 、R —分别为摩擦片的内外半径。
2 离合器基本参数分析

2 离合器基本参数分析摩擦离合器靠摩擦表面间的摩擦力矩来传递发动机转矩。
根据摩擦定律,离合器的静摩擦力矩可表示为:T =fFZR (1)式中,T 为静摩擦力矩(N·m);f为摩擦表面间的静摩擦系数;F为压盘施加在摩擦面上的工作压力(N);R 为摩擦片的平均摩擦半径(m);Z为摩擦面数。
假设摩擦片上压力均匀,则有:Rc一一丽D2+Dd+d2F—p。
A—p。
~—r(D 2-dz)汽车离合器基本参数的优化设计式中,P。
为摩擦面单位面积上的压力(N/m。
);A为一个摩擦面的面积(m );D 为摩擦片外径(m);d为摩擦片内径(m)。
将式(2)、式(3)代入式(1)得:T = fZp。
D。
(1一c。
) (4)上厶式中,c为摩擦片内外径之比,c=d/D。
为了保证离合器在任何工况下都能可靠地传递发动机的最大转矩,设计时Tc应大于发动机最大转矩,即:T 一一 (5)式中,T一为发动机最大转矩(N·m);p为离合器的后备系数,p>1。
由以上分析可知,离合器的基本参数主要有性能参数p和P。
、尺寸参数d和D。
后备系数p反映了离合器传递发动机最大转矩的可靠程度,是重要的离合器设计参数,各类汽车p的取值范围见表1。
单位面积压力P。
对离合器工作性能和使用寿命有很大影响,选取时应考虑离合器的工作条件、发动机后备功率大小、摩擦片尺寸、摩擦片材料、质量和后备系数等因素。
根据摩擦片材料,P。
按表2选取。
表1 各类汽车B的取值范围轿车和轻型货车 p一1.2~1.75中型和重型货车 p一1.5~2.25越野车、带拖挂的重型汽车和牵引汽车 p一1.8~4.0表2 po的取值范围石棉基材料 po一0.10~0.35MPa烧结金属材料 P0-0.35~0.60MPa金属陶瓷材料 po一0.70~1.50MPa当离合器结构型式及摩擦片材料已选定,发动机最大转矩T一已知,结合式(1)和式(5),适当选取后备系数p和单位压力P。
离合器的设计
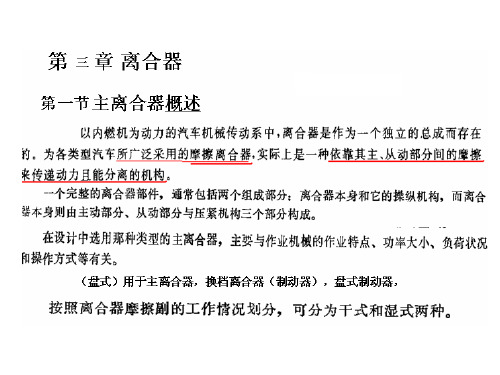
第六节
与制动器助力相似
例题
干式
P=M.N
1)外摩擦片
2)内摩擦片
图4-1 摩擦片结构示意图
轴向压力F---摩擦力---传递转矩 。
图4-2 摩擦离合器结构示意图 1-主动盘; 2-从动盘; 3-滑环
主动轴1与外壳2相联接
图4-3 多片式摩擦离合器 1-主动轴; 2-外鼓; 3-被动片; 6-压板; 4-摩擦片;
离合器的选型:
1).干式: 摩擦片数多可以增大所传递的转矩。但片数过多, 将各层间压力分布不均匀。
6. 摩擦片外径D,内径d和厚度
摩擦片外径D(mm)也可根据如下经验公式选用: DKD Temax 式中:KD为直径系数,KD =14.5~24.0。 摩擦片的厚度b主要有3.2mm、3.5mm和4.0mm三种
7.离合器传递的转矩 T m
8. 离合器的储备系数
离合器在接合过程中除承受工作载荷外,还要承受惯性载荷。
并引起摩擦片的磨损和发热。为了限制磨损和发热, 应使接合面上的单位压力不超过许用单位压力 。 2.对湿式离合器而言,摩擦副的面积应为扣除油槽面积后的 有效摩擦工作面面积
4.摩擦副材料的摩擦系数f,基本许用单位压力见表4-1。
5.摩擦片单位压力值p对离合器工作性能和使用寿命有很大影响,选取时应考虑
离合器的工作条件,发动机后备功率大小,摩擦片尺寸,材料及其质量和后备系数等因素。 离合器使用频繁,发动机后备系数较小时, 应取小些;当摩擦片外径较大时,为了降 低摩擦片外缘处的热负荷, 应取小些;后备系数较大时,可适当增大 。 工程机械在工作时经常需要频繁地使用离合器,而且它们的工作条件差,属于重载荷类 型,因此应选用较小的值
摩擦转矩、储备系数、摩擦副数量和摩擦衬片的内外径等。
- 1、下载文档前请自行甄别文档内容的完整性,平台不提供额外的编辑、内容补充、找答案等附加服务。
- 2、"仅部分预览"的文档,不可在线预览部分如存在完整性等问题,可反馈申请退款(可完整预览的文档不适用该条件!)。
- 3、如文档侵犯您的权益,请联系客服反馈,我们会尽快为您处理(人工客服工作时间:9:00-18:30)。
离合器参数设计
3.1后备系数的选择
离合器的后备系数反映了离合器传递发动机最大扭矩的可靠度,它是离合器设计的一个重要参数。
在选择β时,应考虑摩擦片磨损后仍能可靠地传递发动机最大扭矩、防止离合器滑磨时间过长、防止传动系数过载以及操纵轻便等因素。
表3.1 后备系数表
车型乘用车及总质量
小于6t的商用车最大总质量为
6~14t的商用车
挂车
后备系数 1.20~1.75 1.50~2.25 1.80~4.00
本设计是基于一款轻型货车,故选择后备系数1.2~1.75,取后备系数β=1.5。
3.2摩擦片外径及其他尺寸的确定
摩擦片外径是离合器的基本尺寸参数,它对离合器的结构尺寸、质量的大小和使用寿命的长短都有很大的影响。
摩擦片外径D(mm)也可根据发动机最大扭矩T emax(N.m)按如下经验公式进行初选:
(3-1)式中:K D为直径系数,轻卡取17;最大总质量为1.8~14.0t的商用车,单片离合器取16.0~18.5;T emax是发动机最大扭矩,原始设计数据为110N.m:
由公式(3-1)代入相关数据,取得:D=178mm
根据离合器摩擦片的标准化,系列化原则,根据下表3.2“离合器摩擦片尺寸系列和参数”(即GB1457—74)
表3.2离合器摩擦片尺寸系列和参数
外径/D mm内径/d mm厚度/h mm 内外径之比
/d D
单位面积
2
/
F mm
160110 3.20.68710600
180125 3.50.69413200
200140 3.50.70016000
225150 3.50.66722100
250155 3.50.62030200
280165 3.50.58940200
300175 3.50.58346600
325190 3.50.58554600
35019540.55767800
38020540.54072900取摩擦片外径D=250mm,选定摩擦片的内径d=155mm,厚度b=3.5mm。
单位压力的确定
离合器摩擦力矩T c的计算
(3-2)
离合器压盘施加在摩擦面上的工作压力的计算
(3-3)施加在摩擦面的工作压力为
(3-4)式中:z为摩擦面数,单片离合器的z=2,f为摩擦面间的静摩擦系数,这里取0.25。
单位压力:
(3-5)粉末冶金铁基材料单位压力要求小于0.35MPa,本离合器的单位压力比规定值小,故满足要求。
5.3膜片弹簧基本参数的选择
1、比值H/h和h的选择:此比值对膜片弹簧的弹性特性影响极大,因此,要利用H/ h 对弹簧特性的影响正确地选择该比值,以得到理想的特性曲线及获得最佳的使用性能。
一般汽车的膜片弹簧H/h值在如下范围之内:H/h=1.5~20。
2、R及R/r确定: 比值R/r对弹簧的载荷及应力特性都有影响,从材料利用率的角度,比值在1.8~2.0时,碟形弹簧储存弹性的能力为最大,就是说弹簧的质量利用率和好。
因此设计用来缓和冲击,吸收振动等需要储存大量弹性能时的碟簧时选用。
对于汽车离合器的膜片弹簧,设计上并不需要储存大量的弹性能,而是根据结构布置与分离的需要来决定,一般R/r取值为1.2~1.35.对于R,膜片弹簧大端外径R应满足结构上的要求和摩擦片的外径相适应,大于摩擦片内径,近于摩擦片外径。
此外,当H,h及R/r等不
变时,增加R有利于膜片弹簧应力的下降。
初步确定R/r= 3、膜片弹簧起始圆锥底角
: 汽车膜片弹簧一般起始圆锥底角在9°~15°之间,=13
4、膜片弹簧小端半径rf 及分离轴承的作用半径r p: r f的值主要由结构决定,最小值应大于变速器第一轴花键外径,分离轴承作用半径r p大于r f。
5、分离指数目n、切槽宽、窗孔槽宽、及半径r c: 分离指数目n常取18,大尺寸膜片弹簧可取24,小尺寸膜片弹簧可取12,本设计取n=18。
切槽宽约为4mm;窗孔槽宽;窗孔半径r c一般情况下由计算。
6、承环的作用半径l和膜片与压盘接触半径L:由于采用推式膜片弹簧,l,L的大小将影响膜片弹簧的刚度,一般来说,l值应尽量靠近r而略大与r。
L应接近R略小于R。
7、膜片弹簧材料:制造膜片弹簧用的材料,应具有高的弹性极限和屈服极限,高的静力强度及疲劳强度,高的冲击强度,同时应具有足够大的塑性变形性能。
按上述要求,国内常用的膜片弹簧材料为硅锰钢60Si2MnA。
5.4膜片弹簧的计算
参考同种类产品,并结合本车具体情况,初步选定弹簧的一些参数和尺寸如下:,,,R=112.5mm
确定膜片弹簧的所有尺寸
H=7.4mm, h=3.7mm,R=112.5mm,r=90mm,l=92mm
L=110mm,rf=27mm,rp=29mm,n=18,,
1、根据下式(5.1)画出P
1—λ
1
曲线
(5-1)
式中,E—弹性模数,钢材料取E=2.0×105Mp;
μ—泊松比,钢材料取0.3;
h—弹簧片厚,㎜;
H—碟簧部分内截锥高,㎜;
1
λ—大端变形,㎜;
R—碟簧部分外半径(大端半径),㎜;
r—碟簧部分内半径,㎜;
L—膜片弹簧与压盘接触半径,㎜;
l—支承环平均半径,㎜;
(2)推式轴向变形的关系式
(5-2) (3)膜片弹簧小端分离轴承处作用有分离力P2时膜片弹簧压盘接触处的变形和P2的关系式
(5-3) (4)在P2力作用下膜片弹簧小端部分轴承处的变形
(5-4)
(5-5)
式中
,
为宽度系数:
(5-6)
(5-7)
设
因此式(5.1)就成为:
把有关数值代入上述各式得
P 1=1429.3
=3.71λ
=0.8521λ-0.641λ2+0.1461λ3
图5.1 膜片弹簧特性曲线
2、确定膜片弹簧的工作点位置
取离合器结合时膜片弹簧的大端变形量为,由特性曲线图可查得磨片弹簧的压紧力:
校核后备系数:
离合器彻底分离时,膜片弹簧大端的变形量为
压盘的行程为,故
离合器刚开始分离时,压盘的行程,此时膜片弹簧最大端的变形量为
摩擦片磨损后,其最大磨损量,故
3、求离合器彻底分离时分离轴承时轴承作用的载荷P2由公式(5-3),取则得
代入有关数值,得
4、求分离轴承的行程
由公式(5-2),取,则
由公式(5-6)(5-7)得
由公式(5-5)得
代入有关数值,得
=1.72 mm
5、强度校核
膜片弹簧大端的最大变形(离合器彻底分离时)。
将有关数值代入,得
7.1从动盘毂花键的设计计算
花键的结构尺寸可根据从动盘外径和发动机转矩按国标GB1144-74选取。
从动盘外径D/mm 发动机转矩
max
e
T/N•m
花键
齿数
n
花键
外径
D/mm
花键
内径
d/mm
键齿宽
b/mm
有效
齿长
l/mm
挤压
应力
σ/MPa
1605010231832010
1807010262132011.8
20011010292342511.3
22515010322643011.5
25020010352843510.4
28028010353244012.7
30031010403254010.7
32538010403254511.6
35048010403255013.2
38060010403255515.2
41072010453656013.1
43080010453656513.5
45095010524166512.5
这里,所选择的相关尺寸参数为:花键齿数z1=10;花键齿长L=35mm;花键齿宽b=4mm;花键外径D外=35;花键内径D内=28mm;从动盘数n=1。
作用在一个从动盘花键上的圆周力为
(7-1)挤压应力为
(7-2)以上所得的挤压应力值小于推荐许用值(30MPa),故满足设计要求。
花键的剪切应力计算
(7-3)计算结果表明,剪切压力较低,故满足要求。
如有侵权请联系告知删除,感谢你们的配合!。