湿式离合器设计计算
汽车设计0204第二章 离合器设计 第四节 设计与计算

Gd ns 3 8D p K
切变模量G=83~103 N/mm24§2-Fra bibliotek离合器的设计与计算
二、圆柱弹簧 3.弹簧工作圈数ns,总圈数ns'
弹簧刚度K=20~45 N/mm
或
F F K f
Δf—分离过程弹簧的变形量Δf(mm) 单盘 1.1~2.6
双盘
3.0~3.6
ns' =ns +(1.5~2.0)
三、膜片弹簧
2.弹簧特性计算公式
Eh1 ln( R / r ) Rr 1 R r 2 F1 ( H 1 )( H )h 2 2 6(1 ) ( R1 r1 ) R1 r1 2 R1 r1
膜片弹簧的计算公式由碟形弹簧的计算 公式得来。
假设膜片弹簧在承载过程中,其子午断面刚 性地绕此断面上的某中性点O转动(图2-10)。
通过支承环和压盘加在膜片弹簧上的载荷 F1(N)集中在支承点处,加载点间的相对轴向变 形为λ1(mm) (图2-12b),则膜片弹簧的弹性特性 (图2-11)如下式表示。
§2-4离合器的设计与计算
§2-4离合器的设计与计算
§2-4离合器的设计与计算
4.计算弹簧自由状态的高度H
H=ns' d+(ns +1)δ+ Δf+f δ=0.5~1.5 f=F/K 分离状态下的最小长度 Hmin=(ns +1)δ+ ns' d mm
§2-4离合器的设计与计算
三、膜片弹簧的弹性特性
1.膜片弹簧的优点:见前述。
2.膜片弹簧的载荷与变形的关系
膜片弹簧自由状态下碟簧部分的内截锥高度 H; 膜片弹簧钢板厚度 h ; 自由状态下碟簧部分大端半径 R;
离合器计算2

离合器摩擦片计算多片摩擦离合器的摩擦转矩fc T 与摩擦副数、摩擦系数、压紧力和作用半径有关。
其关系式为:e fc z T Fr μ=式中fc T —摩擦转矩()N M ⋅;μ—摩擦系数,从动力换档传递扭矩出发,取动摩擦系数; F —摩擦片压紧力()N ;e r —换算半径,将摩擦力都换算为都作用在这半径上;z —摩擦副数。
下面求换算半径e r :(如下图示)一对摩擦副上一个单元圆环的摩擦转矩为:fc dT p dA μρ=⋅⋅⋅式中 p —单位压力或比压;ρ—圆环半径;dA —单位圆环面积。
而 2dA d πρρ=⋅带入前式可得22fc dT p d πμρρ=摩擦副全部面积的摩擦转矩为ρυπd p u T Rrfc ⎰=22式中r 、R —分别为摩擦片的内外半径。
单位圆环上的压紧力为2dF pdA p d πρρ==摩擦片上全部压紧力为⎰=Rrd P F ρρπ2假定为一个摩擦副,将以上式子带入上式,得到换算作用半径为2eR fc r R r r T p d F p d ρρμρρ=⎰=⎰由以上式子,积分可得2eR fc r R r r T p d F p d ρρμρρ=⎰=⎰2r R +=压紧力P 与摩擦副数i假设压强均匀分布时,根据许用压强[P]可以计算出最大允许的压紧力,c p k p b R P ⨯⨯⨯⨯=][2πk 为摩擦表面利用系数,无沟槽时 k =1,有沟槽时应按实际情况确定。
初步计算时,有螺旋槽的可取0.65—0.85,有螺旋槽和径向槽的可取0.5—0.6.当已选定材料和几何尺寸时,可将式(4—4)代入式(4—3)以求出所需的最少摩擦片数i[]c p m bk R P M i 22πμ=求出i 后应圆整成偶数,以达到轴向力的平衡。
然后再把圆整后的i 代入式(4—4),计算出实际需要的压紧力P ,以供设计加压弹簧或加压油缸时用。
压板行程多片式离合器分离时,各摩擦表面间隙并不均匀,但可以使用平均间隙δ来衡量,无论干式或湿式,初步计算时可取5.0=δ毫米。
湿式多片离合器的设计分析

湿式多片离合器的设计分析作者:佴晓珣袁海环来源:《企业技术开发·下旬刊》2015年第08期摘要:湿式多片离合器作为双离合变速器的关键部件,对整车传动效率、换挡品质有着重要的作用,文章阐述了湿式多片离合器设计分析方法,并且结合工程实际,提出简化的摩擦片当量半径和油压推算公式,为工程设计提供了理论依据。
关键词:离合器;设计;分析中图分类号:U463.211 文献标识码:A 文章编号:1006-8937(2015)24-0027-01双离合变速器(Dual Clutch Transmission)DCT有别于一般的自动变速器系统,它基于手动变速器而又不是自动变速器,除了拥有手动变速器的灵活性及自动变速器的舒适性外,还能提供无间断的动力输出。
目前国外汽车工业强国已经开始量产,在一些高档车型上开始普及,可见离合器作为重要的传动接合部件对整车性能的重要。
本文以某型双离合变速的输入来研究湿式多片离合器的设计分析。
1 模型通常设计人员依据整车厂提供的技术要求和变速器的布局来设计离合器,在保证满足技术的前提下竟可能降低成本,整体结构如图1所示。
[图1 湿式多片离合器结构简图]离合器的结构中,摩擦片对离合器工作性能影响很大。
离合器摩擦副元件由摩擦元件及对偶元件两部分组成。
其特点是:可在主、从动轴转速差较大的状态下实现平稳、柔顺的结合。
因为最大传输扭矩较小,使用金属摩擦材料,如铜基粉末冶金就可以满足轿车、货车等机械的制动上的需求。
2 传递扭矩关系的确定湿式多片摩擦离合器的摩擦转矩与摩擦副数、摩擦系数、压紧力和作用半径有关。
其关系式为:T=βμFrez式中,T为摩擦转矩;μ为摩擦系数,从动力换档传递扭矩出发,取动摩擦系数0.1;F为摩擦片压紧力;z为摩擦副数,采用4对摩擦副;re为摩擦副当量半径;β为储备系数,乘用车β选择:1.20~1.75摩擦片单元结构,如图2所示。
[图2 摩擦片示意图]一对摩擦副上一个单元圆环的摩擦转矩为:dT=2βπμpρ2dρ式中,p为单位压力;ρ为圆环半径。
湿式离合器滑摩功计算

06 结论与展望
结论总结
计算方法的适用性
滑摩功影响因素
湿式离合器的滑摩功计算方法适用于各种 工况和材料,为设计和优化离合器提供了 有力工具。
摩擦系数滑摩速度和滑摩温度是影响滑 摩功的主要因素,需综合考虑以获得最佳 性能。
实验与理论的一致性
实际应用价值
实验结果与理论计算结果基本一致,验证 了计算方法的可靠性和准确性。
湿式离合器与其他离合器的比较
与干式离合器相比,湿式离合器具有更高的承载能力和更 长的使用寿命,因为摩擦片在油液中工作,可以起到润滑 和冷却的作用。
与自动离合器相比,湿式离合器通常结构较为简单,成本 较低,但在使用过程中需要定期更换油液。
综上所述,湿式离合器是一种广泛应用于汽车、机械和工 业领域的传动装置,具有较高的承载能力和使用寿命,与 其他类型的离合器相比具有明显的优势。
优化摩擦副材料组合
根据工作需求选择合适的摩擦副材料,如选 择具有良好摩擦性能的摩擦片和硬度适中的 钢片,以提高离合器的传动效率和减小滑摩 功的损失。
使用与维护建议
定期检查与更换摩擦片
定期检查离合器的磨损情况,及时更换磨损 严重的摩擦片,保持离合器的良好工作状态 。
保持清洁与润滑
在使用过程中保持离合器的清洁,避免杂物 和污垢对离合器工作的影响。同时,定期对 离合器进行润滑,减小摩擦阻力,降低滑摩
湿式离合器滑摩功计算
contents
目录
• 湿式离合器简介 • 滑摩功计算基础 • 湿式离合器滑摩功计算方法 • 滑摩功对湿式离合器性能的影响 • 优化湿式离合器滑摩功的措施 • 结论与展望
01 湿式离合器简介
湿式离合器的定义与工作原理
定义
湿式离合器是一种用于传递动力的装 置,通常用于汽车、机械和工业领域 。
湿式双离合同步器拨环力矩的计算
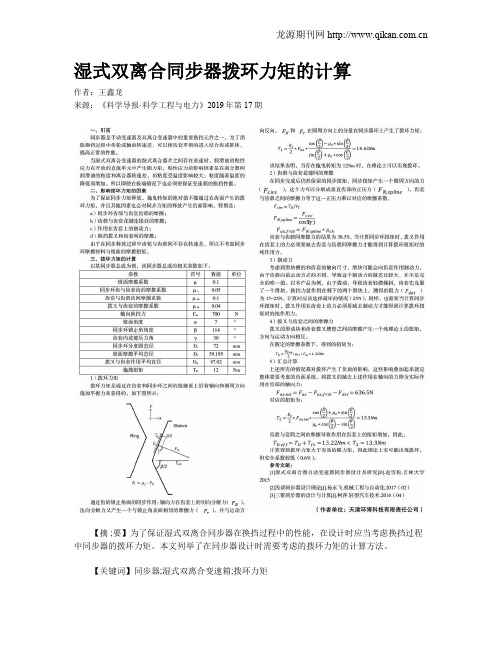
湿式双离合同步器拨环力矩的计算作者:王鑫龙来源:《科学导报·科学工程与电力》2019年第17期【摘 ;要】为了保证湿式双离合同步器在换挡过程中的性能,在设计时应当考虑换挡过程中同步器的拨环力矩。
本文列举了在同步器设计时需要考虑的拨环力矩的计算方法。
【关键词】同步器;湿式双离合变速箱;拨环力矩一、引言同步器是手动变速器及双离合变速器中的重要换挡元件之一,为了消除换挡过程中齒轮或轴的转速差,可以使齿套平滑的进入结合齿或锥体,提高正常的性能。
当湿式双离合变速器的湿式离合器片之间存在差速时,润滑油的粘性应力在开放的直流单元中产生阻力矩,粘性应力的影响因素是在离合器间润滑油的粘度和离合器转速差,而粘度受温度影响较大:粘度随着温度的降低而增加。
所以即使在极端情况下也必须要保证变速箱的换挡性能。
二、影响拨环力矩的因素为了保证同步力矩释放,拖曳转矩的绝对值不能超过在齿面产生的拨环力矩,并且其他因素也会对同步力矩的释放产生负面影响,特别是:a)同步环齿部与齿套齿部的摩擦;b)齿毂与齿套花键连接处的摩擦;c)作用在齿套上的制动力;d)换挡拨叉和齿套间的摩擦;由于在同步释放过程中齿轮与齿毂间不存在转速差,所以不考虑同步环摩擦材料与锥面的摩擦扭矩。
三、拨环力矩的计算计算得到拨环力矩大于有效的阻力矩,因此理论上有可能出现拨环,但安全系数较低(0.6%)。
参考文献:[1]湿式双离合器自动变速器同步器设计及研究[D].赵雪松.吉林大学 2015[2]浅谈同步器设计理论[J].杨永飞.机械工程与自动化.2017(02)[3]三锥同步器的设计与计算[J].柯萍.轻型汽车技术.2014(04)(作者单位:天津环博科技有限责任公司)。
毕业设计(论文)-湿式离合器设计-含DCT湿式双离合器
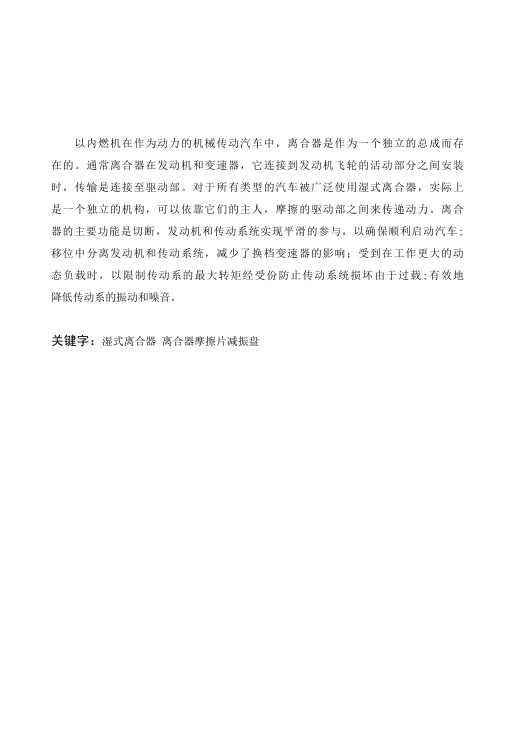
以内燃机在作为动力的机械传动汽车中,离合器是作为一个独立的总成而存在的。
通常离合器在发动机和变速器,它连接到发动机飞轮的活动部分之间安装时,传输是连接至驱动部。
对于所有类型的汽车被广泛使用湿式离合器,实际上是一个独立的机构,可以依靠它们的主人,摩擦的驱动部之间来传递动力。
离合器的主要功能是切断,发动机和传动系统实现平滑的参与,以确保顺利启动汽车; 移位中分离发动机和传动系统,减少了换档变速器的影响;受到在工作更大的动态负载时,以限制传动系的最大转矩经受份防止传动系统损坏由于过载;有效地降低传动系的振动和噪音。
关键字:湿式离合器离合器摩擦片减振盘第1章绪论1.1引言1.3. 3湿式离合器的优点 (6)第2章基本尺寸参数选择2.1离合器基本性能关系式 ......................................................... 8 2. 2后备系数的选择 .. (8)第1章绪论1.1 引言以内燃机在作为动力的机械传动汽车中,离合器是作为一个独立的总成而存 在的。
通常离合器在发动机和变速器,它连接到发动机飞轮的活动部分之间安装 时,传输是连接至驱动部。
对于所有类型的汽车被广泛使用湿式离合器,实际上 是一个独立的机构,可以依靠它们的主人,摩擦的驱动部之间来传递动力。
离合目录1. 4设计内容 ....1.5方案选择 31.3湿式离合器的结构及其优点 (5)1.3.1湿式离合器的结构 (5)7器的主要功能是切断,发动机和传动系统实现平滑的参与,以确保顺利启动汽车; 移位中分离发动机和传动系统,减少了换档变速器的影响;受到在工作更大的动态负载时,以限制传动系的最大转矩经受份防止传动系统损坏由于过载;有效地降低传动系的振动和噪音。
1.2 离合器的发展在离合器结构,最成功的锥形离合器的早期发展。
其原型已被安装在1889 年德国戴姆勒公司生产的汽车钢制车轮。
它是发动机飞轮的内孔锥形制成的离合器的积极成员。
牵引车湿式离合器的设计研究
力 变矩 器共 同工 作 输 出特 性 的 最 大 扭 矩 计 算 出 的 车 辆 主 动 轮 的转 矩 , 可能 因 为 附 着 条 件 的 因 素 而 不 能 实 现 动力 的 平 稳 传 递 。此 时 的 额 定 转 矩 应 是 以车 辆 刚 启 动 时 主 动 轮 的转 矩 ,可 通 过 下 式 “ 计 算 :
身 零 部 件 寿命 提 高 ,更 易 于 实 现 系 列 化 、标 准 化 。本 文 对
牵 引 车 的换 档离 合器 进 行 了设 计 并 通 过 台架 试 验 验 证 了设
计 的正 确 性 。
2离 合 器 的 结 构 及 工 作 过 程
图 】 示 为 3吨 牵 引 车 所 用 的 倒 档 离 合 器 。 主 要 是 所
中 圈 分 类 号 :U 6 .1 4 32 1 文 献标 识 码 :A 文章 编 号 :10 —4 2 (00 7 0 4 — 4 0 9 9 9 2 1)0 — 0 8 0
I 言 引
工 程 机 械 传 动 系 统 广 泛 采 用 液 力 传 动 形 式 , 即在 发 动 机 和 变速 器 之 间 配置 液 力 变矩 器 .并 在 变 速 箱 内采 用 液 力
控 制缓 冲 阀使 压力 油经 由离合 器 油道 进 入油 缸 。然 后 ,
压 力 油 推 动 活 塞 压 缩 回 位 弹 簧 使 摩 擦 片 和 从 动 片 相 互 接
触 并 压 紧 ,此 时 离 合 器 通 过 摩 擦 力 将 主 、 被 动 齿 轮 连 接 并 进 行 传 递 动 力 : 当车 辆 需 要 换 档 时 ,通 过 控 制 单 元 使 缓 冲 阀 的进 油 口 与 输 出 油 口 接 通 ,离 合 器 在 回 位 弹 簧 的 作 用 下 实 现 分 离 ; 同 时 ,在 换 档 阀 的 配 合 下 实 现 油 路 切 换 .使 其 他 离 合 器 充 油 1 作 。 为 了 消 除 旋 转 油 缸 中 油 液 二
湿式离合器设计计算
湿式离合器设计计算
1.转矩传递计算:湿式离合器的主要作用是传递动力,因此需要计算
离合器的转矩传递能力。
转矩传递计算需要考虑摩擦片的摩擦系数、接触
面积和压力等因素。
2.离合器片数计算:湿式离合器通常由多个摩擦片组成,片数的设计
需要考虑到传动功率和摩擦片的承载能力。
片数过少会导致传动效率下降,片数过多则可能导致离合器尺寸过大。
3.摩擦片材料选择:摩擦片的材料选择对于湿式离合器的性能至关重要。
常用的摩擦片材料有石棉板、摩擦片和钢制板等。
不同材料具有不同
的摩擦系数和耐磨性能,需要根据实际需求进行合理选择。
4.冷却系统设计:湿式离合器在传动过程中会产生大量的热量,因此
需要设计有效的冷却系统,以保证离合器的正常工作。
冷却系统可以采用
利用油液进行冷却的方式,也可以采用风扇和散热片等被动式冷却方式。
5.润滑系统设计:湿式离合器的工作需要有良好的润滑条件。
润滑系
统的设计需要考虑到离合器内部各个摩擦副之间的润滑需求,以确保离合
器在使用过程中不会出现摩擦副过热、磨损或润滑不良的问题。
以上是湿式离合器设计和计算的一般步骤和要点。
在实际应用中,还
需要根据具体的传动需求和设备条件进行合理设计和计算。
离合器的相关计算
通过气压传递扭矩,适 用于高速运转和重载工
况。
离合器规格
离合器尺寸
根据工作需求选择合适的尺寸,包括直径、宽度 和长度等参数。
离合器转速
根据输入输出转速选择合适的离合器转速,确保 正常工作。
离合器负载
根据工作负载选择合适的离合器,确保能够承受 足够的扭矩和冲击。
离合器材料
01
02
03
金属材料
如铸铁、铸钢、铝合金等, 具有较高的强度和耐磨性。
离合器的相关计算
• 离合器基本参数 • 离合器计算公式 • 离合器设计流程 • 离合器性能测试 • 离合器应用案例
01
离合器基本参数
离合器类型
摩擦片离合器
电磁离合器
液力离合器
气压离合器
利用摩擦力传递扭矩, 具有缓冲和减震作用。
通过磁场传递扭矩,响 应速度快,控制精度高。
利用液体介质传递扭矩, 具有自动调节和缓冲功
热对流
热对流是指离合器表面与周围空气之间的热量交换过程。 计算热对流的方法需要考虑周围空气的温度、速度和换热 系数等因素。
03
离合器设计流程
需求分析
确定设计目标
明确离合器的使用场景、性能要求和 使用寿命等。
市场调研
了解同类产品的性能、价格和用户反 馈,以便进行有针对性的设计。
参数设定
输入参数
设定离合器的输入功率、转速和转矩 等参数。源自扭矩传递计算扭矩传递
扭矩传递是衡量离合器传递扭矩的能力,它是衡量离合器性能的重要指标。计算扭矩传递的方法需要根据离合器的具 体结构和工况进行选择。
静态扭矩传递
静态扭矩传递是指在静止状态下,离合器能够传递的最大扭矩。计算方法是根据离合器的几何尺寸、摩擦系数和最大 静摩擦力矩进行计算。
(20)2.4离合器的设计与计算
2.4离合器的设计与计算[P2]-离合器基本参数优化设计离合器要确定离合器的性能参数和尺寸参数,这些参数的变化影响离合器的结构尺寸和工作性能。
因此,离合器基本参数的优化设计变量选为离合器工作压力F和离合器的主要尺寸参数D和d o[P3]离合器基本参数优化设计追求的目标是在保证离合器性能要求条件下,使其结构尺寸尽可能小,即目标函数为[P4]约束条件包括摩擦片的外径D的最大圆周速度、摩擦片的内外径比C f为保证离合器可靠传递转矩,选定合适的B范围;为保证扭转减振器的安装,选取合适的摩擦片内径d;为降低离合器清磨时的热负荷,选定单位压力pθ的范围;为减少汽车起步过程中离合器的滑磨,防止摩擦片表面温度过高而发生烧伤,限定每一次接合的滑磨功。
[P5](全屏或小窗口)二、膜片弹簧的弹性特性假设膜片弹簧在承载过程中,其子午断面刚性地绕此断面上的某中性点0转动(图2-9)β[P6](全屏或小窗口)通过支承环和压盘加在膜片弹簧上的载荷Fl集中在支承点处,加载点间的相对轴向变形为入1,则有如下公式(如图)式中,E为材料的弹性模量,μ为材料的泊松比;H为膜片弹簧自由状态下碟簧部分的内截推高度;h为膜片弹簧钢板厚度;R、r分别为自由状态下碟簧部分大、小端半径;Rl.11分别为压盘加载点和支承环加载点半径。
[P7]在膜片弹簧的基本参数中,比值H/h对膜片弹簧的弹性特性影响极大。
通过分析上述公式,为保证离合器压紧力变化不大和操纵轻便,汽车离合器用膜片弹簧的H/h取在根号2和2倍根号2之间,一般为1.5~2.0,板厚h为2~4mm.[P8](全屏或小窗口)(如图)这是我们确定了H/h的合理比值后,得到的膜片弹簧理想的弹性特性曲线。
曲线的拐点H对应着膜片弹簧的压平位置。
新离合器在接合状态时,膜片弹簧工作点B一般取在凸点M和拐点H之间,且靠近或在H点处。
以保证摩擦片在最大磨损限度范围内压紧力Fl变化不大。
当分离时,膜片弹簧工作点从B变到C,为最大限度地减小踏板力,C点应尽量靠近N点。
- 1、下载文档前请自行甄别文档内容的完整性,平台不提供额外的编辑、内容补充、找答案等附加服务。
- 2、"仅部分预览"的文档,不可在线预览部分如存在完整性等问题,可反馈申请退款(可完整预览的文档不适用该条件!)。
- 3、如文档侵犯您的权益,请联系客服反馈,我们会尽快为您处理(人工客服工作时间:9:00-18:30)。
3.2多片湿式离合器的设计 3.2.1摩擦副元件材料与形式离合器的结构中,摩擦片对离合器工作性能影响很大,而摩擦片材料的选择就尤为重要。
下面进行摩擦副元件的选择:离合器摩擦副元件由摩擦元件及对偶元件两部分组成。
其特点是:可在主、从动轴转速差较大的状态下接合,而且接合时平稳、柔顺。
离合器摩擦副(又称摩擦对偶)可分为两大类:第一类是金属性的,它的摩擦衬面具有金属性质,如钢对钢,钢对粉末冶金等;第二类是非金属性的,它的摩擦衬面摩擦材料具有非金属性质,如石墨树脂等,它们的对偶可用钢和铸铁。
对于坦克离合器摩擦副,由于其工况和传递动力的要求,选择金属型摩擦材料。
目前广泛应用的是铜基粉末冶金,它的主要优点是:1、 有较高的摩擦系数,单位面积工作能力为0.22千瓦/Fp FAA =厘米2;2、 在较大温度变化范围内,摩擦系数变化不大;3、允许表面温度高,可达350C ,非金属在250C 以下。
故高温耐磨性好,使用寿命长;4、 机械强度高,有较高的比压力;5、导热性好,加上表面开槽可获得良好冷却,允许较长时间打滑而不致烧蚀。
此次设计选择摩擦副材料为钢对铜基粉末冶金,根据坦克设计180页表6—1可得:可取摩擦副的摩擦系数μ=0.08,许用压强[]p =4MPa 。
3.2.2摩擦转矩计算多片摩擦离合器的摩擦转矩fc T 与摩擦副数、摩擦系数、压紧力和作用半径有关。
其关系式为:e fcz T Fr μ=式中fc T —摩擦转矩()N M ⋅;μ—摩擦系数,从动力换档传递扭矩出发,取动摩擦系数;F —摩擦片压紧力()N ;e r —换算半径,将摩擦力都换算为都作用在这半径上;z —摩擦副数。
下面求换算半径e r :(如下图示)一对摩擦副上一个单元圆环的摩擦转矩为:fc dT p dA μρ=⋅⋅⋅式中p —单位压力或比压;ρ—圆环半径;dA —单位圆环面积。
而 2dA d πρρ=⋅ 带入前式可得22fcdT p d πμρρ=摩擦副全部面积的摩擦转矩为ρυπd p u T Rrfc ⎰=22式中r 、R —分别为摩擦片的内外半径。
单位圆环上的压紧力为2dF pdA p d πρρ==摩擦片上全部压紧力为⎰=Rrd P F ρρπ2假定为一个摩擦副,将以上式子带入上式,得到换算作用半径为2eR fc r R r r T p d F p d ρρμρρ=⎰=⎰由上式可见换算作用半径,决定与摩擦片内外圆半径r 、R 和压p 。
在摩擦副上,比压p 的分布规律与摩擦副衬面材料的硬度和施加压紧力的方法有关。
大量的实验研究表明,应用最广的粉末冶金衬面对钢的摩擦副的磨损量,在整个摩擦面是均匀的。
所以pv =常数由于 v =ρω,在同一摩擦件上ω值不变,得p ρ=常数由以上式子,积分可得2eR fc r R r r T p d F p d ρρμρρ=⎰=⎰2r R += 所以,对金属型摩擦材料的摩擦副,其换算作用半径即为平均半径。
离合器的摩擦转矩应大于所传递的工作转矩,才能可靠工作,即在摩滑过程中能保证一定时间内的结合,在结合后工作时不打滑,当作主离合器时还应起负荷保护作用,所以离合器摩擦转矩fc T 应为fcc TT β=式中cT —离合器主动件的计算转矩; β—离合器的储备系数(1)β>。
为了使离合器可靠工作,减少摩滑功和离合器温升,储备系数应取较大值。
针对此次设计的需要,选取储备系数 1.2β=。
离合器摩擦表面尺寸参数包括摩擦片内、外半径r 、R ;表面接触系数ψ;摩擦副数z 等。
这些参数对离合器工作特性由不同程度的影响。
1、摩擦片内、外半径选择设计离合器时,其摩擦表面的最大半径(外半径)为R ,m α——内外半径比,且m αr R =,通过统筹得对于金属型摩擦片,m α值为0.68~0.82,其中50%的m α值为0.73,故在计算中可取m α0.73=;ψ——摩擦面接触系数,它的值等于摩擦表面总面积减去油槽面积后的净面积与总面积之比。
对于开有油槽的离合器,初步计算时,通常取,ψ=0.6。
[]p —材料允许比压,取[]p 4MPa =;c T —离合器主动件的计算转矩;;β—离合器的储备系数,取 1.2β=;z —摩擦副数。
对于摩擦面对数m 的选择,由1m z =-,查机械设计手册可得公式:8122()[]T cm z D d D p e πμ=-≥-其中,z 取为奇数,m 取为偶数。
式中cT —计算转矩,D 、d —摩擦片内、外直径;D e —压力作用直径,2D r e e =[]P —材料允许比压;μ—摩擦系数,由上述知1.0=μ下面进行摩擦片相关参数的计算。
3.2.3摩擦片尺寸的计算此次设计中,摩擦片的内、外半径以及摩擦副对数均未知,摩擦副数的选择,应在保证传递所需转矩的前提下尽量少。
摩擦副数少,则分离彻底,分离状态下的磨损小,功率损失少。
对湿式离合器来说,有利于润滑、冷却。
但在定轴变速箱中,为减小变速箱轮廓尺寸,应减小摩擦片的径向尺寸,而增加摩擦副数。
由于摩擦片导向齿与主动鼓、被动鼓的连接间存在摩擦力,在摩擦副z 较多的情况下,设计应考虑压紧力的损失。
则根据经验以及传动转矩的大小,此次设计初步选定摩擦表面最大半径R=130㎜,则摩擦片外直径D=260㎜。
再由式m r R α=得,0.73mr R R α=*=且摩擦片的外直径 20.73dr D ==摩擦片的换算作用半径e r 由式:2e r R r =+可得出:0.865e r R =,0.865e D D =又由式 PD d D T z m e Cμπ)(8122-≥-= 带入数据得,m ≥11.167。
综上所述,取m=12, R=130;由rm R α=及0.73m α=得:mm m R R r 9.94130*73.073.0*====α 故选取r=94.9,则d=189.8。
摩擦片的换算作用半径由er =2r R +,得:r e =112.45 则D e =2r e =224.9mm 。
由摩擦面对数m=12得,摩擦片总数Z=12+1=13 故可分外摩擦片71=i ,内摩擦片62=i ;综上所述,所设计离合器基本参数为:外径D=260㎜,内径d=189.8㎜,摩擦片总数Z=13,换算作用半径r e =224.9mm 。
3.2.4摩擦片的压紧力根据上面所得出的基本参数的尺寸,由摩擦片的压紧力的公式: 2T cQ y D me μ=将数据带入得N Q y 39.3229212*1.0*9.2245354.4357*2==摩擦面的比压公式()22[]Q yp p R rπ=≤-将所得数据带入得222/130)49.913(*39.32292cm N P =-=π查手册表得许用压强2[]400/p N cm =,即满足[]p p ≤,符合设计要求。
3.2.5压板行程多片式离合器分离时,各摩擦表面间隙并不均匀,但可以用平均间隙δ来衡量。
δ值按统筹学在初步计算时取δ0.5mm =。
故压板行程mm Z f 5.613*5.01===δ3.3液压油缸压力的计算油缸是实现离合器工作的重要元件,关于油缸的设计和压力计算如下:油缸的结构一般如下图示可初步选取R 2=132㎜。
由设计任务知离合器操纵系统压力为1.4Mpa ,取1.4p Mpa =计算。
主油压作用在活塞上的压力P R R F )(2122-=π------------错误!未找到引用源。
式中 P —离合器操纵油压,取 1.4p Mpa =;而活塞缸压紧力F 应满足式:t f y F F Q F ++=-----------错误!未找到引用源。
其中f F —密封圈的摩擦阻力。
t F —复位弹簧力f F 封圈的摩擦阻力,对于o 型圈,由式: 0.03f F F =-------错误!未找到引用源。
对于转动缸复位弹簧力t F ,其计算式为:f t F F F +=0------------------------------------错误!未找到引用源。
0F —排油需要的压力。
且有式()22021F R R p π=-∆----------------------------错误!未找到引用源。
式中 p ∆—排油需要压力,通常取0.06p Mpa ∆=。
将式错误!未找到引用源。
、错误!未找到引用源。
、错误!未找到引用源。
、错误!未找到引用源。
、错误!未找到引用源。
联力解得=1R 96㎜ 则复位弹簧力t F 可由:f t F F F +=0得47.2628=t F 。
且活塞缸压紧力F 为:368.36082=F3.4回位弹簧的设计选择在离合器中,弹簧对离合器的整体性能有很大影响,当弹簧设计不当时,会使离合器产生阻滞现象和离合器早期打滑失效。
根据离合器结构的要求,离合器弹簧可分为拉伸弹簧和压缩弹簧两种,根据此次设计的要求,选择压缩弹簧,且为圆柱螺旋压缩弹簧。
选用代号为RY I 的热卷压缩弹簧,两端并紧并磨平。
对于弹簧的材料选择,因需回位力较大,故选用弹簧材料为油淬火回火硅锰弹簧钢丝602Si MnA ;在根据弹簧受负荷的性质,,受到变载荷作用,次数在3510~10之间,故为第II 类弹簧。
查机械设计手册表,得出:该弹簧的许用切应力[]τ590Mpa =。
3.4.1弹簧平均直径D 和钢丝直径d 的确定一般圆截面圆柱螺旋弹簧的主要尺寸有:平均直径D ,弹簧的钢丝直径d ,有效圈数n 和自由长度0l 等。
当外径D 和钢丝直径d 中有一个决定后,按卷绕比C 来确定另一个。
卷绕比由式:DC d=得出。
由1D D d =-,可得:()11D d C =+式中1D —弹簧的最大外径。
对于坦克离合器用的压缩弹簧,其卷绕比通常取为5~8C =,在此取6C =。
初步确定钢丝直径为mm d 5=,弹簧数量为12t Z =弹簧的静强度条件为:d≥式中K —曲度系数,计算公式为:410.61544C K C C-=+-将数据带入可得 1.25K =。
由此可以检验弹簧钢丝直径:d≥610*590*1247.2628*6*25.1*6.1==2.27㎜ 故选取钢丝直径为mm d 4=满足要求。
则有mm D 246*4==,圆整取mm D 50=3.4.2确定弹簧圈数n 和长度l 及刚度弹簧参数与刚度的关系为:348nD Gd k =其中 G —材料的剪切弹性模数,查机械手册表276-得78G Gpa =。
由上式和公式t aF k Z z δ=可得弹簧工作圈数:438t Z zGd n aQD δ=式中 a —弹簧压缩到最大行程时,比离合器分离时负荷增加的百分数,通常取0.25a =。
将数据带入可得:2.603.0*368.36082*25.0*8004.0*10*78*13*5.0*12349==n查机械设计手册表,圆整得 6.5n =。