分层实体制造快速成型技术
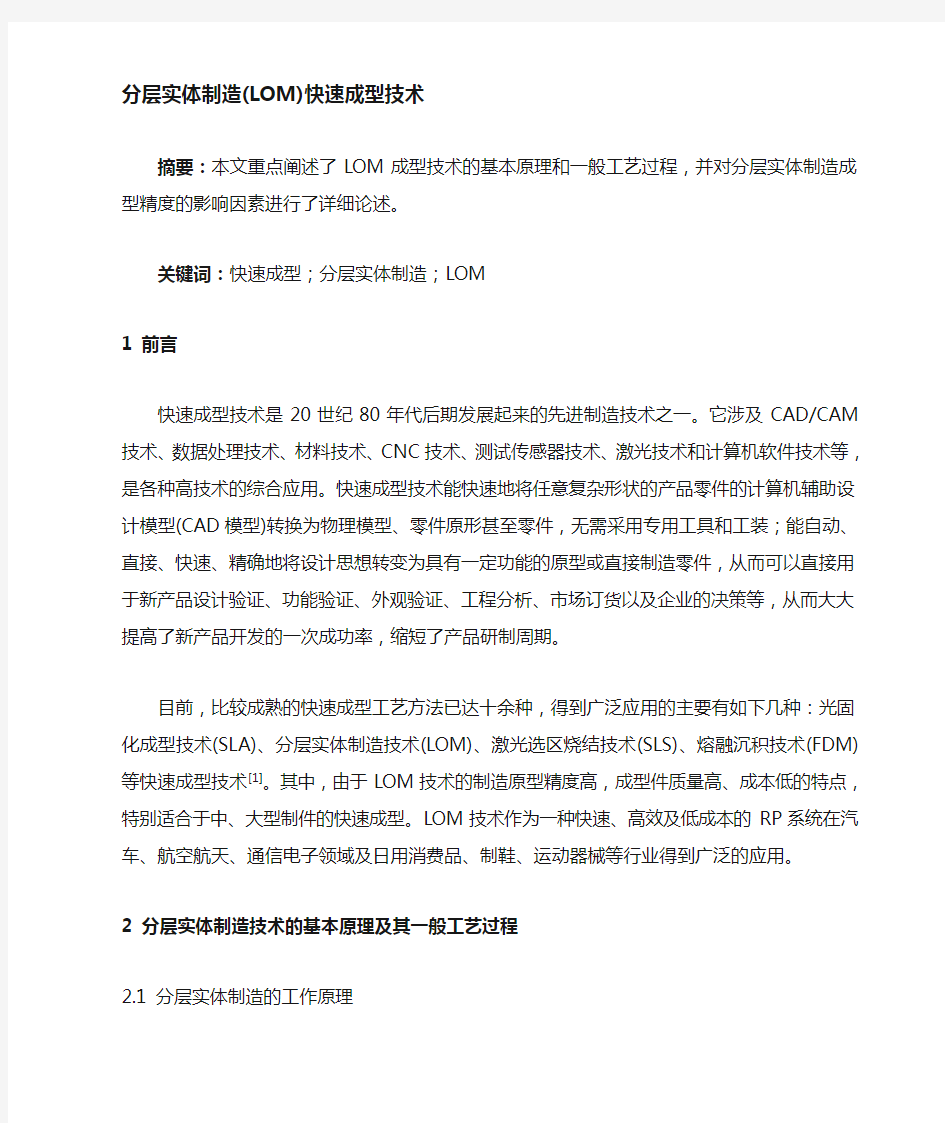
- 1、下载文档前请自行甄别文档内容的完整性,平台不提供额外的编辑、内容补充、找答案等附加服务。
- 2、"仅部分预览"的文档,不可在线预览部分如存在完整性等问题,可反馈申请退款(可完整预览的文档不适用该条件!)。
- 3、如文档侵犯您的权益,请联系客服反馈,我们会尽快为您处理(人工客服工作时间:9:00-18:30)。
分层实体制造(LOM)快速成型技术
摘要:本文重点阐述了LOM成型技术的基本原理和一般工艺过程,并对分层实体制造成型精度的影响因素进行了详细论述。
关键词:快速成型;分层实体制造;LOM
1 前言
快速成型技术是20世纪80年代后期发展起来的先进制造技术之一。它涉及CAD/CAM技术、数据处理技术、材料技术、CNC技术、测试传感器技术、激光技术和计算机软件技术等,是各种高技术的综合应用。快速成型技术能快速地将任意复杂形状的产品零件的计算机辅助设计模型(CAD模型)转换为物理模型、零件原形甚至零件,无需采用专用工具和工装;能自动、直接、快速、精确地将设计思想转变为具有一定功能的原型或直接制造零件,从而可以直接用于新产品设计验证、功能验证、外观验证、工程分析、市场订货以及企业的决策等,从而大大提高了新产品开发的一次成功率,缩短了产品研制周期。
目前,比较成熟的快速成型工艺方法已达十余种,得到广泛应用的主要有如下几种:光固化成型技术(SLA)、分层实体制造技术(LOM)、激光选区烧结技术(SLS)、熔融沉积技术(FDM)等快速成型技术[1]。其中,由于LOM技术的制造原型精度高,成型件质量高、成本低的特点,特别适合于中、大型制件的快速成型。LOM技术作为一种快速、高效及低成本的RP系统在汽车、航空航天、通信电子领域及日用消费品、制鞋、运动器械等行业得到广泛的应用。
2 分层实体制造技术的基本原理及其一般工艺过程
2.1 分层实体制造的工作原理
分层实体制造(LOM)是被广泛应用的一种快速成型工艺,其成型系统主要由计算机、原材料送进机构、热压装置、激光切割系统、可升降工作台和数控系统等组成。其工作原理如下:
在CAD软件系统上建立产品的三维CAD模型,并传递到快速成型系统上的计算机,通过数据处理软件,将CAD模型沿成型方向切成一系列具有一定厚度的“薄片”。原材料送进机构将底面涂有热熔胶和添加剂的纸或塑料等薄层材料送至工作台的上
方。计算机自动控制激光切割系统,按“薄片”的横截面轮廓线,在工作台上方的薄层材料上切割出该层横截面的轮廓形状,并将材料的无轮廓区切割成小碎片。可升降工作台支撑正在成型的零件,并在每层成型之后,降低一个分层厚度,然后新的一层材料叠加在上面。通过恒温控制的热压装置将其与下面的己切割层粘合在一起,激光束再次切割出物体的新一层截面轮廓,如此往复,层层堆积,直到所有的层都加工完后,便得到最终需要的三维产品[2]。其工作原理如图1所示。
图1 LOM工艺的成型原理图[2]
2.2 分层实体制造的一般工艺过程
LOM成型的一般工艺过程大致如下:
(1)料带移动,使新的料带移到工件上方。
(2)工作台往上升,同时热压辊移到工件上方,工件顶起新的料带,工作台停止移动,热压辊来回碾压新的薄材材料,将最上面一层的新材料与下面已成型的工件部分粘结起来,添加一新层。
(3)系统根据工作台停止的位置,测出工件的高度,并反馈回计算机,计算机根据当前零件的加工高度,计算出三维实体模型的交截面。
(4)交截面的轮廓信息输入到控制系统中,控制CO2激光器沿截面轮廓切割。激光的功率设置在只能切透一层材料的功率值上。轮廓内、外面无用的材料用激光切成方形的网格,以便工艺完成后分离。
(5)工作台向下移动,使刚切下的新层与料带分离。
(6)料带移动一段比切割下的工件截面稍长一点的距离,并绕在复卷辊上。
(7)重复上述过程,直到最后一层。分离掉无用碎片,得到三维实体。
LOM成型的工艺过程如图2所示。
图2LOM成型过程示意图[3]
LOM技术的特点是制造的原型精度高,分层实体制造中激光束只需按照分层信息提供的截面轮廓,而不用扫描整个截面,且无需设计和制作支撑,所以制作效率高、速度快、成本低。结构制件能承受高达200℃的温度,有较高的硬度和较好的机械性能,可进行各种切削加工。缺点是由于材料质地原因,加工的原型抗拉性能和弹性不高,易吸湿膨胀,需进行表面防潮处理。
3 分层实体制造成型精度分析
3.1 成型系统对成型精度的影响
(l)高度传感器的测量误差。高度传感器用于测量热压后纸面的实时高度,并将此数据反馈给计算机并进行转换,一方面,使当前要切割的纸面正好处于焦平面上,另外,根据此数据调用相应高度处的分层截面数据(为了满足高度的要求,有可能忽略掉某层或某几层截面的加工),或者计算切片高度,进行实时切片,得到对应的切片轮廓。因此,高度传感器的精度会直接影响成型件的加工精度。此外,由于高度传感器安装在X向热压板的中间,所以只能测得成型件X方向中间位置附近处的高度值,而不能对整个成型件的上表面进行测量,同时,侧量的准确性还受温度和机械振动等的影响,这些都会导致成型件的尺寸和形状误差[4]。
(2)热压板表面温度分布不均匀导致的误差。由于热压板表面温度沿x向分布不可能很均匀,同时,升降工作台与z轴的垂直度误差引起成型件上表面高度不一致,
这些因素使胶的最高热压温度分布不均匀,导致胶厚分布不均匀,从而影响z向尺寸精度[4]。
3.2 切片方式对成型精度的影响
理想的分层方法应是沿成型方向将三维CAD模型分解为一系列精确的层片,即每个层片不仅具有内外轮廓线,还具有三维几何特征,使该层片的侧面与三维CAD 模型对应位置处的几何特征完全一致。然而在实际成型中,不能采用理想的分层方法,其主要原因在于:
(l)理想分层后每个层片仍具有三维几何特征,不能用二维数据进行精确描述,因而在生成数控程序方面,将由简单的两坐标数控加工问题转变为比较复杂的四坐标或五坐标数控加工问题;
(2)具体的工艺难于保证层片厚度方向的轮廓形状,因为对于激光切割系统来说,需要激光加工头能绕X和Y轴摆动,以便沿轮廓曲线进行切割。
因此,每一层片只能用直壁层片近似,用二维特征截面近似代替整个层片的几何轮廓信息。LOM成型工艺中,有以下两种分层方法:
①定层厚分层。根据所选定的分层厚度(一般为纸的名义厚度)一次性对三维CAD 模型或STL格式化模型进行切片处理,将各层的数据存贮在相应的数据文件中,计算机顺序调用各层的数据至数控卡,控制成型机完成原型的制作。这种分层方法比较简单,但纸厚的累积误差导致成型件Z向尺寸精度无法控制。如果安装Z方向高度实时检测反馈控制系统,虽然能控制成型件最终的Z向尺寸,但又不能保证成型件每一高度处的截面轮廓完全符合CAD模型或STL模型相应高度处的截面轮廓,因为在加工过程中,为了满足高度的要求,对于某些层片数据将不会加工。
②实时测厚,实时分层。对升降工作台采用闭环控制,根据成型件当前层的实测高度,对CAD模型或STL模型进行实时分层,以获取相应截面的数据。这不仅能较真实地反映模型相应高度处的截面轮廓,而且可以消除纸厚的累积误差对零件Z向尺寸精度的影响[5]。
另外,对于某些快速成型工艺如FDM工艺等,还可采用变层厚分层(又称自适应切片方法),即根据CAD模型的表面几何信息(曲率和斜率)及给定的误差要求自动调整分层厚度。但这种自适应切片方法对LOM工艺来说不适合,因为LOM工艺的成型材料为固定厚度的纸。