表面淬火工艺
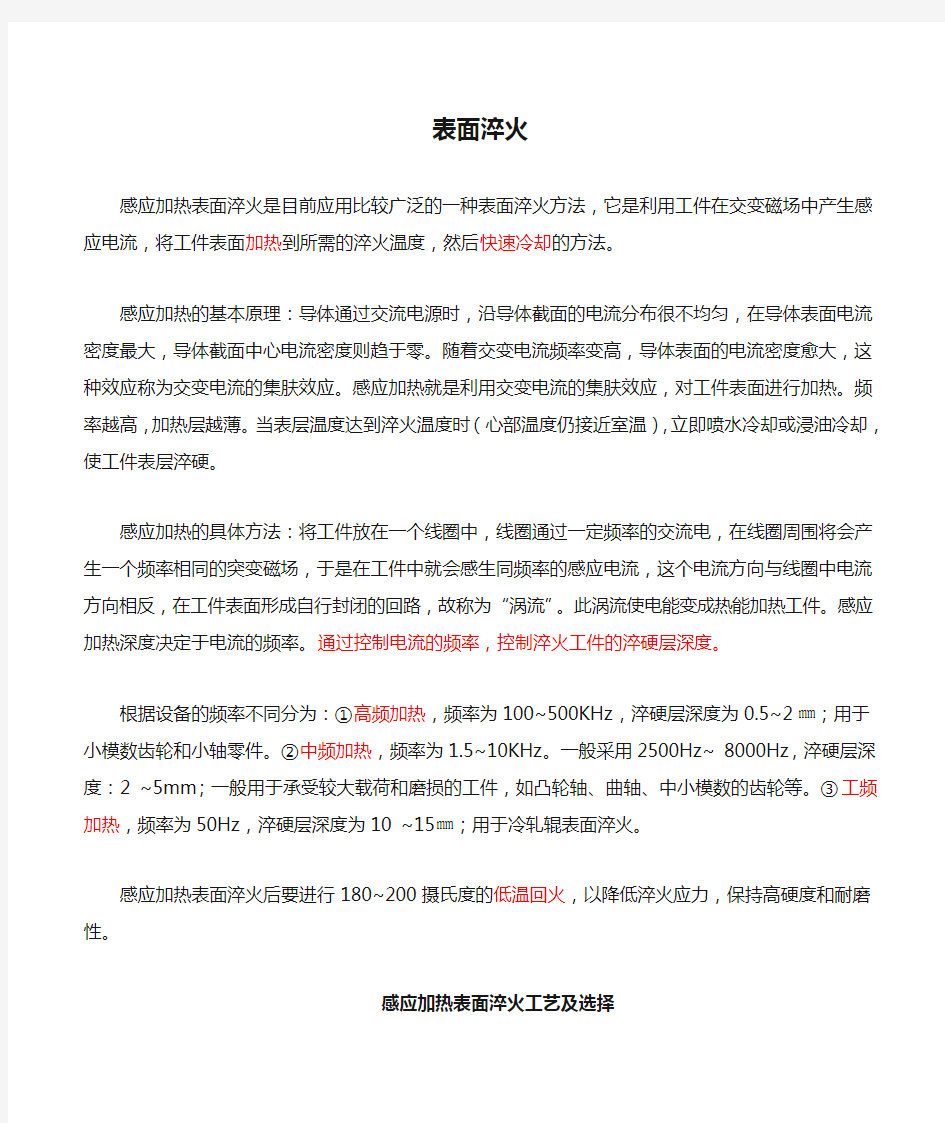
- 1、下载文档前请自行甄别文档内容的完整性,平台不提供额外的编辑、内容补充、找答案等附加服务。
- 2、"仅部分预览"的文档,不可在线预览部分如存在完整性等问题,可反馈申请退款(可完整预览的文档不适用该条件!)。
- 3、如文档侵犯您的权益,请联系客服反馈,我们会尽快为您处理(人工客服工作时间:9:00-18:30)。
表面淬火
感应加热表面淬火是目前应用比较广泛的一种表面淬火方法,它是利用工件在交变磁场中产生感应电流,将工件表面加热到所需的淬火温度,然后快速冷却的方法。
感应加热的基本原理:导体通过交流电源时,沿导体截面的电流分布很不均匀,在导体表面电流密度最大,导体截面中心电流密度则趋于零。随着交变电流频率变高,导体表面的电流密度愈大,这种效应称为交变电流的集肤效应。感应加热就是利用交变电流的集肤效应,对工件表面进行加热。频率越高,加热层越薄。当表层温度达到淬火温度时(心部温度仍接近室温),立即喷水冷却或浸油冷却,使工件表层淬硬。
感应加热的具体方法:将工件放在一个线圈中,线圈通过一定频率的交流电,在线圈周围将会产生一个频率相同的突变磁场,于是在工件中就会感生同频率的感应电流,这个电流方向与线圈中电流方向相反,在工件表面形成自行封闭的回路,故称为“涡流”。此涡流使电能变成热能加热工件。感应加热深度决定于电流的频率。通过控制电流的频率,控制淬火工件的淬硬层深度。
根据设备的频率不同分为:①高频加热,频率为100~500KHz,淬硬层深度为0.5~2㎜;用于小模数齿轮和小轴零件。②中频加热,频率为1.5~10KHz。一般采用2500Hz~ 8000Hz,淬硬层深度:2 ~5mm;一般用于承受较大载荷和磨损的工件,如凸轮轴、曲轴、中小模数的齿轮等。③工频加热,频率为50Hz,淬硬层深度为10 ~15㎜;用于冷轧辊表面淬火。
感应加热表面淬火后要进行180~200摄氏度的低温回火,以降低淬火应力,保持高硬度和耐磨性。
感应加热表面淬火工艺及选择感应加热工艺参数包括着热处理参数和电参数。热处理参数包括加热温度、加热时间、加热速度以及淬火层深度。电参数包括设备的频率、零件单位面积功率等。
感应加热淬火工艺中几个主要问题:
1.确定零件的技术要求:表面硬度、淬火层深度及淬硬区分布、淬火层组织等。a.表面硬度:感应淬火后零件的表面硬度要求与材料的化学成分和使用的条件有关。b.淬火层深度:淬火层深度主要是根据零件的机械性能确定的。
c.淬硬区分布:按零件的几何形状与工作条件的不同,各种表面淬火零件的硬化区部分和尺寸有不同的要求。
d.金相组织:按零件的材料及工作条件,规定各格的等级范围。按评级标准进行金相评级。
2.加热温度的选择:感应加热速度快,与一般加热相比,必须选用较高的加热速度,适宜的加热温度是与钢材的化学成分、原始组织状态及加热速度等因素有关。
3.设备频率的选择:主要是根据淬火层深度和零件的尺寸大小来确定。当设备给定或选定以后,设备的频率就是一个不可调的参数。
感应加热方法及工艺操作
感应加热方法基本分为两种:
a..同时加热法,这种加热法是被加热的表面同时共热升温,零件需要加热的整个部分都被感应器包围着。在大批量生产时,为充分发挥设备潜力,提高生产效率,只要设备输出功率足够的条件下,尽可能采用同时加热。
b..连续加热法,零件表面的加热和冷却时连续不断进行的。连续加热生产率较低,但加
热面积减小,设备的功率可以降低,因而扩大了设备的应用范围。
感应加热后的冷却方式
冷却方法有喷射冷却、浸液冷却、埋油淬火等。
a..喷射冷却,是常用的方法。将冷却液通过感应器上的许多小孔,喷射到加热面上,进行冷却。
b..浸液冷却,主要是用于同时加热。零件表面同时加热完毕后,立即将淬火部分浸入淬火槽(冷却介质)中,进行冷却。
c..埋油淬火,当采用连续加热法时,为避免喷油时产生油烟,可将感应器降至油面以下,进行油面以下的连续加热和冷却。我车间就有我厂自行制造的埋油淬火机床。
感应淬火后的回火
感应加热淬火后,应力分布不均,组织不稳定。为了降低拉应力,稳定组织,达到所要求的机械性能,有必要进行回火。
回火方法有:炉内回火,自回火和感应加热回火。
a..炉内回火:在电炉内回火,回火时间一般为1~2小时
b..自回火:对于形状简单,大量生产的零件可采用自回火。
c..感应加热回火:感应加热回火时,为了达到回火要求,回火时的加热层深必须大于淬火层深,且必须采用相当慢的加热速度,故生产效率较低。