表面淬火工艺
表面淬火工艺
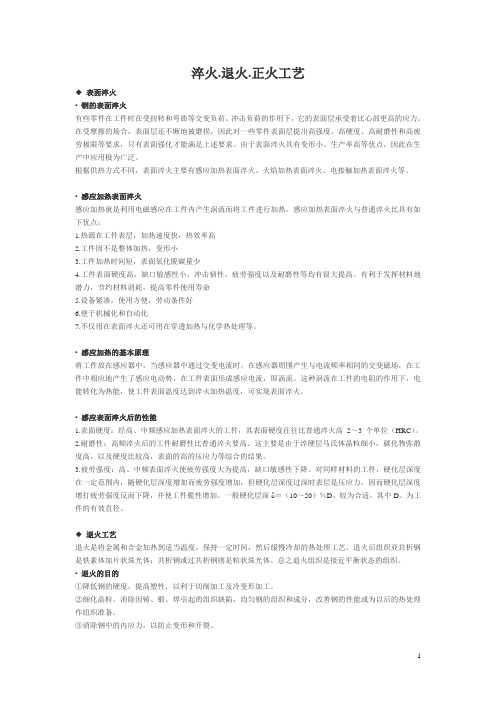
淬火.退火.正火工艺◆表面淬火• 钢的表面淬火有些零件在工件时在受扭转和弯曲等交变负荷、冲击负荷的作用下,它的表面层承受着比心部更高的应力。
在受摩擦的场合,表面层还不断地被磨损,因此对一些零件表面层提出高强度、高硬度、高耐磨性和高疲劳极限等要求,只有表面强化才能满足上述要求。
由于表面淬火具有变形小、生产率高等优点,因此在生产中应用极为广泛。
根据供热方式不同,表面淬火主要有感应加热表面淬火、火焰加热表面淬火、电接触加热表面淬火等。
• 感应加热表面淬火感应加热就是利用电磁感应在工件内产生涡流而将工件进行加热。
感应加热表面淬火与普通淬火比具有如下优点:1.热源在工件表层,加热速度快,热效率高2.工件因不是整体加热,变形小3.工件加热时间短,表面氧化脱碳量少4.工件表面硬度高,缺口敏感性小,冲击韧性、疲劳强度以及耐磨性等均有很大提高。
有利于发挥材料地潜力,节约材料消耗,提高零件使用寿命5.设备紧凑,使用方便,劳动条件好6.便于机械化和自动化7.不仅用在表面淬火还可用在穿透加热与化学热处理等。
• 感应加热的基本原理将工件放在感应器中,当感应器中通过交变电流时,在感应器周围产生与电流频率相同的交变磁场,在工件中相应地产生了感应电动势,在工件表面形成感应电流,即涡流。
这种涡流在工件的电阻的作用下,电能转化为热能,使工件表面温度达到淬火加热温度,可实现表面淬火。
• 感应表面淬火后的性能1.表面硬度:经高、中频感应加热表面淬火的工件,其表面硬度往往比普通淬火高2~3 个单位(HRC)。
2.耐磨性:高频淬火后的工件耐磨性比普通淬火要高。
这主要是由于淬硬层马氏体晶粒细小,碳化物弥散度高,以及硬度比较高,表面的高的压应力等综合的结果。
3.疲劳强度:高、中频表面淬火使疲劳强度大为提高,缺口敏感性下降。
对同样材料的工件,硬化层深度在一定范围内,随硬化层深度增加而疲劳强度增加,但硬化层深度过深时表层是压应力,因而硬化层深度增打疲劳强度反而下降,并使工件脆性增加。
表面淬火定义

表面淬火定义表面淬火是一种金属热处理技术,通过控制金属材料的加热和冷却过程,使其表面形成一层具有较高硬度和耐磨性的淬火层。
这种技术广泛应用于各种机械零件和工具的制造中,能够提高其使用寿命和性能。
表面淬火的过程可以分为加热、保温和冷却三个阶段。
首先,将金属材料加热到适当的温度,以激活材料内部的晶体结构。
然后,通过保温使材料中的晶体结构重新排列,形成一种具有高硬度的相态结构。
最后,通过迅速冷却来固定这种相态结构,使其在表面形成一层淬火层。
表面淬火的关键是控制加热和冷却的速度。
加热温度和时间的选择需要根据金属材料的性质和要求进行调整。
过高的温度和时间可能导致材料内部的晶体结构发生变化,影响淬火效果;过低的温度和时间则无法激活和重组晶体结构。
冷却过程一般采用水、油或盐浴等介质,通过迅速吸热来实现快速冷却。
冷却介质的选择取决于材料的类型和形状。
表面淬火的优点是能够在保持材料的韧性和强度的同时,提高其硬度和耐磨性。
淬火层的硬度一般远高于材料的基体,能够有效抵抗磨损和变形。
因此,表面淬火广泛应用于汽车发动机零件、工具刀具、轴承等高负荷和高磨损的零件制造中。
然而,表面淬火也存在一些局限性和注意事项。
首先,淬火层的深度一般较浅,只有几个毫米左右,对于需要较深淬火层的零件不适用。
其次,淬火过程中会产生应力,可能导致材料的变形和开裂。
因此,在淬火后需要进行适当的回火处理,以减缓应力并提高材料的韧性。
最后,表面淬火的工艺要求较高,需要严格控制加热和冷却的参数,以保证淬火效果的稳定性和一致性。
表面淬火是一种能够提高金属材料硬度和耐磨性的热处理技术。
通过控制加热和冷却的过程,能够在材料表面形成一层具有高硬度的淬火层。
这种技术在机械制造和工具制造中得到广泛应用,能够提高零件的使用寿命和性能。
然而,表面淬火也存在一些局限性和注意事项,需要在实际应用中进行合理选择和控制。
45钢表面淬火工艺
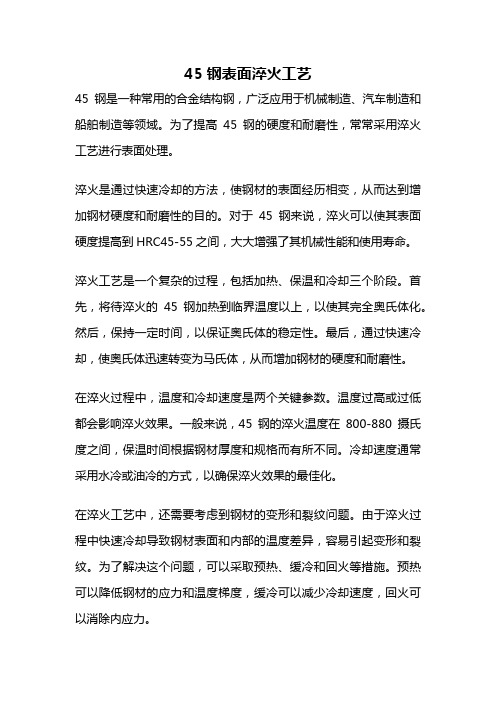
45钢表面淬火工艺45钢是一种常用的合金结构钢,广泛应用于机械制造、汽车制造和船舶制造等领域。
为了提高45钢的硬度和耐磨性,常常采用淬火工艺进行表面处理。
淬火是通过快速冷却的方法,使钢材的表面经历相变,从而达到增加钢材硬度和耐磨性的目的。
对于45钢来说,淬火可以使其表面硬度提高到HRC45-55之间,大大增强了其机械性能和使用寿命。
淬火工艺是一个复杂的过程,包括加热、保温和冷却三个阶段。
首先,将待淬火的45钢加热到临界温度以上,以使其完全奥氏体化。
然后,保持一定时间,以保证奥氏体的稳定性。
最后,通过快速冷却,使奥氏体迅速转变为马氏体,从而增加钢材的硬度和耐磨性。
在淬火过程中,温度和冷却速度是两个关键参数。
温度过高或过低都会影响淬火效果。
一般来说,45钢的淬火温度在800-880摄氏度之间,保温时间根据钢材厚度和规格而有所不同。
冷却速度通常采用水冷或油冷的方式,以确保淬火效果的最佳化。
在淬火工艺中,还需要考虑到钢材的变形和裂纹问题。
由于淬火过程中快速冷却导致钢材表面和内部的温度差异,容易引起变形和裂纹。
为了解决这个问题,可以采取预热、缓冷和回火等措施。
预热可以降低钢材的应力和温度梯度,缓冷可以减少冷却速度,回火可以消除内应力。
淬火工艺的优点是可以提高钢材的硬度和耐磨性,增加其使用寿命。
同时,淬火还可以改善钢材的综合机械性能,提高其强度和韧性。
因此,淬火广泛应用于机械制造、汽车制造和船舶制造等领域。
45钢表面淬火工艺是提高45钢硬度和耐磨性的一种有效方法。
通过控制温度和冷却速度,可以使钢材表面经历相变,从而增加其硬度和耐磨性。
同时,合理的预热、缓冷和回火等措施可以解决淬火过程中的变形和裂纹问题。
淬火工艺可以大大提高45钢的机械性能和使用寿命,广泛应用于各个领域。
表面淬火

3、高频感应加热表面淬火后的组织和性能
快速加热时钢的相变特点
1)临界温度升高,转变在较宽的温度范围内完成 2)奥氏体晶粒较细 3)奥氏体成分不均匀
ρ—工件电阻率 μ——工件的相对导磁率 f——电流频率 可见: 1)f愈高, δ小,淬硬层深度越浅。 2) ρ愈大, μ愈小,δ越大。
工频:50Hz,功率密度0.1~100W/cm2; 中频:<10kHz,功率密度< 5 W/cm2;
3.3、表面淬火
3.3 、表面淬火 3.3、表面淬火
• 要点:用快速加热法,使零件表面层很快地达到淬火温 度(A化),在热量传至内部之前,立即冷却使表 面层淬硬。 • 材料:中碳钢及中碳合金钢,如40、45、40Cr。 感应加热 • 分类(加热方法) 火焰加热 激光加热
(一)感应加热表面淬火
感应加热表面淬火示意图
下一页 返 回 金属热处理工艺 , SMSE,CUMT 本章首页 上一页
集肤效应示意图
表面淬火的发展
感应淬火原
50300
f
返 回
金属热处理工艺 , SMSE,CUMT
本章首页 上一页
下一页
返
回
金属热处理工艺 , SMSE,CUMT
本章首页 上一页
下一页
50300
f
2、分类(按电源频率)
预处理: 表面淬火前,须对零件进行正火或调质处理,以保证 零件心部具有良好的综合性能。 硬化层深度的确定: 抗磨损:1~6.5mm 抗疲劳:2~12mm 感应加热淬火温度 由于感应加热速度快,但组织转变又具有热滞后,为使组织 转变充分,所以感应加热温度应比常规加热温度提高30~50℃。 后处理: 表面淬火后,一般要对零件进行低温(160~200 ℃)回火 处理,以降低淬火应力和脆性。
表面淬火工艺
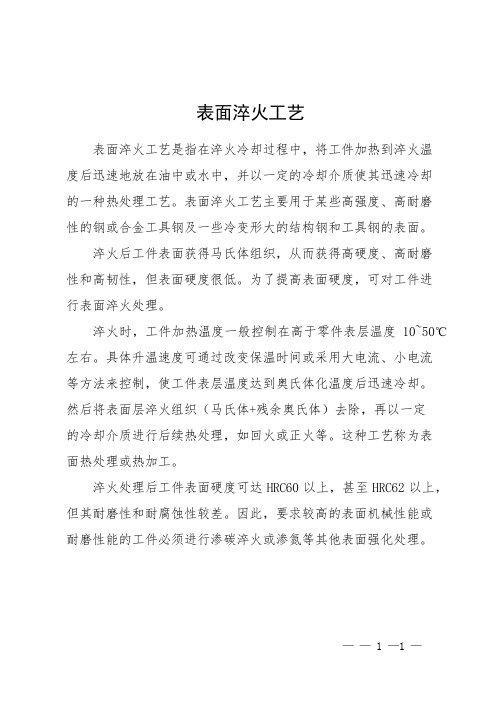
表面淬火工艺
表面淬火工艺是指在淬火冷却过程中,将工件加热到淬火温
度后迅速地放在油中或水中,并以一定的冷却介质使其迅速冷却
的一种热处理工艺。
表面淬火工艺主要用于某些高强度、高耐磨
性的钢或合金工具钢及一些冷变形大的结构钢和工具钢的表面。
淬火后工件表面获得马氏体组织,从而获得高硬度、高耐磨
性和高韧性,但表面硬度很低。
为了提高表面硬度,可对工件进
行表面淬火处理。
淬火时,工件加热温度一般控制在高于零件表层温度10~50℃左右。
具体升温速度可通过改变保温时间或采用大电流、小电流
等方法来控制,使工件表层温度达到奥氏体化温度后迅速冷却。
然后将表面层淬火组织(马氏体+残余奥氏体)去除,再以一定
的冷却介质进行后续热处理,如回火或正火等。
这种工艺称为表
面热处理或热加工。
淬火处理后工件表面硬度可达HRC60以上,甚至HRC62以上,但其耐磨性和耐腐蚀性较差。
因此,要求较高的表面机械性能或
耐磨性能的工件必须进行渗碳淬火或渗氮等其他表面强化处理。
—— 1 —1 —。
表面淬火概念
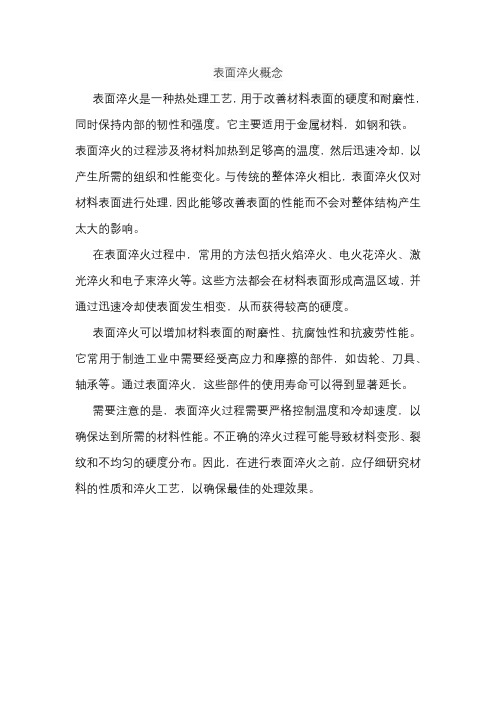
表面淬火概念
表面淬火是一种热处理工艺,用于改善材料表面的硬度和耐磨性,同时保持内部的韧性和强度。
它主要适用于金属材料,如钢和铁。
表面淬火的过程涉及将材料加热到足够高的温度,然后迅速冷却,以产生所需的组织和性能变化。
与传统的整体淬火相比,表面淬火仅对材料表面进行处理,因此能够改善表面的性能而不会对整体结构产生太大的影响。
在表面淬火过程中,常用的方法包括火焰淬火、电火花淬火、激光淬火和电子束淬火等。
这些方法都会在材料表面形成高温区域,并通过迅速冷却使表面发生相变,从而获得较高的硬度。
表面淬火可以增加材料表面的耐磨性、抗腐蚀性和抗疲劳性能。
它常用于制造工业中需要经受高应力和摩擦的部件,如齿轮、刀具、轴承等。
通过表面淬火,这些部件的使用寿命可以得到显著延长。
需要注意的是,表面淬火过程需要严格控制温度和冷却速度,以确保达到所需的材料性能。
不正确的淬火过程可能导致材料变形、裂纹和不均匀的硬度分布。
因此,在进行表面淬火之前,应仔细研究材料的性质和淬火工艺,以确保最佳的处理效果。
金属热处理工艺学-表面淬火
钢表面淬火后的残余应力
图12. 不同钢材硬化层深度与残余压应力的关系 1----45号钢;2----18Cr2Ni4W; 3----40CrMnMo;4----40CrNiMo
钢表面淬火强化层应与工件负载匹配
x
o
图13. 表面强化与承载应力匹配示意图 1.截面为圆形的工件负载时的应力分布情况 2.表面淬火较浅时,沿表面向内部的应力承载能力曲线 3.表面淬火较深时,沿表面向内部的应力承载能力曲线
特点3.提高加热速度可显著细化奥氏体晶粒。
形核处增加:铁素体与碳化物相界、铁素体亚晶界; 形核时间短、晶粒来不及长大。
特点4.快速加热对过冷奥氏体的转变及马氏体回火有明显影响。
奥氏体成分不均及晶粒细化,减小了过冷奥氏体稳定性,C曲线左移; 成分不均使马氏体转变点和形态都不相同,出现低碳、高碳马氏体。
知识回顾
图 Fe-C相图及其平衡组织
钢表面淬火的金相组织
钢经过表面淬火后的金相组织与钢的成分、淬火前的原始组织以及淬火 加热时截面的温度梯度分布有关。
图3. 共析钢表面淬火沿截面温度分布(a) 及淬火后金相组织(b)
原始材料:退火态共析钢
钢表面淬火的金相组织
图4. 45钢表面淬火沿截面温度分布(a) 及淬火后金相组织(b)
图 感应加热原理示意图
感应加热基本原理
感应电势的瞬时值:
d e d
e
-感应电势的瞬时值,V;
-感应线圈电流回路包围面积内的总磁通,Wb,随交变电流强度 和零件磁导率增加而增加,并于零件与感应器之间的间隙有关;
感应电流(涡流)值: Z
I
e e Z R X
2
2
X
-自感电抗,Ω; -零件材料的电阻,Ω;
热处理工艺中的表面淬火处理及其应用
热处理工艺中的表面淬火处理及其应用热处理工艺是一种通过加热、保温和冷却等操作,改变材料的内部组织和性能的方法。
在热处理工艺中,表面淬火处理是一项重要的技术,它通过在材料表面形成硬度高、耐磨性好的淬硬层,提高材料的使用寿命和性能。
本文将重点探讨表面淬火处理的原理、方法以及在工业生产中的应用。
一、表面淬火处理的原理表面淬火处理是指在材料表面形成具有淬硬层的过程。
其原理是利用材料的相变规律,通过加热材料到相应的温度,使固态材料转变为奥氏体相,然后迅速冷却以保持其固体态,从而在材料表面形成淬硬层。
表面淬火处理的原理是基于材料的相变规律,也称为固溶-析出相变原理。
通过加热材料到固溶温度以上,使固溶体中的溶质原子溶解在基体中,形成固溶体。
随后迅速冷却使得不同原子浓度的固溶体开始析出,形成新的相,从而使材料表面形成淬硬层。
二、表面淬火处理的方法表面淬火处理有多种方法,常见的包括火焰淬火、电火花淬火和激光淬火等。
1. 火焰淬火火焰淬火是利用高温火焰对材料进行加热,然后迅速冷却进行淬火处理的方法。
通过喷射高温火焰使材料表面快速加热,然后利用喷射介质(如水)迅速冷却,使材料产生高温和高压的效果,形成淬硬层。
2. 电火花淬火电火花淬火是一种利用电放电产生的高温和高压作用在材料表面进行淬火处理的方法。
通过在材料表面施加高压电流,产生高温电弧和高能量火花,使材料表面瞬间加热至高温状态,然后迅速冷却,形成淬硬层。
3. 激光淬火激光淬火是利用激光束对材料表面进行加热,然后快速冷却的方法。
激光束能够精确聚焦在材料表面,产生高温和高能量的作用,使材料表面快速加热,然后通过冷却介质的喷射迅速冷却,形成淬硬层。
三、表面淬火处理的应用表面淬火处理在工业生产中有广泛的应用,主要体现在以下几个方面。
1. 增加材料的硬度和耐磨性表面淬火处理可以使材料在表面形成高硬度和耐磨性的淬硬层,提高材料的硬度和耐磨性。
这对于一些工作条件苛刻、需要耐磨性能的零件非常重要,如汽车发动机的曲轴、凸轮轴等。
四、表面淬火
快速加热: 要在工件表面有限深度内达到相变点以上的温度, 必须给工件表面以极高的能量密度来加热,使工件表面的热量来 不及向心部传导,以造成极大的温差。
-
2
三、表面淬火的分类: 表面淬火常以供给表面能量的形式不同而命名及分类。目前表
面淬火可以分成以下几类: 1.感应加热表面淬火 2.火焰淬火 3.电接触加热表面淬火 4.电解液加热表面淬火 5.激光加热表面淬火 6.电子束加热表面淬火
-
4
2. 奥氏体成分不均匀性随着加热速度的增加而增大 如前所述,随着加热速度的增大,转变温度提高,转变温度范
围扩大. 随着转变温度的升高,与铁素体相平衡的奥氏体碳浓度 降低,而与渗碳体相平衡的奥氏体碳浓度增大. 因此,与铁素体 相毗邻的奥氏体碳浓度将和与渗碳体相毗邻的奥氏体中碳浓度有 很大差异。由于加热速度快,加热时间短,碳及合金元素来不及 扩散,将造成奥氏体中成分的不均匀,且随着加热速度的提高, 奥氏体成分的不均匀性增大。例如0.4%C碳钢,当以130℃/s 的加热速度加热至900℃时,奥氏体中存在着1.6%C的碳浓度区. 显然,快速加热时,钢种、原始组织对奥氏体成分的均匀性有很 大影响. 对热传导系数小,碳化物粗大且溶解困难的高合金钢采 用快速加热是有困难的。
快速加热使奥氏体成分不均匀及晶粒细化,减小了过冷奥氏体 的稳定性,使c曲线左移. 由于奥氏体成分的不均匀性,特别是亚 共析钢,还会出现二种成分不均匀性现象。在珠光体区域,原渗 碳体片区与原铁素体片区之间存在着成分的不均匀性,这种区域 很傲小,即在微小体积内的不均匀性. 而在原珠光体区与原先共 析铁素体块区也存在着成分的不均匀性,这是大体积范围内的不 均匀性. 由于存在这种成分的大体积不均匀性,将使这二区域的 马氏体转变点不同,马氏体形态不同. 即相当于原铁素体区出现 低碳马氏体,原珠光体区出现高碳马氏体. 由于快速加热奥氏体 成分的不均匀性,淬火后马氏体成分也不均匀,所以,尽管淬火 后硬度较高,但回火时硬度下降较快,因此回火温度应比普通加 热淬火的略低。
中频表面淬火工艺技术报告
关于中频表面淬火工艺的技术报告热处理是机械制造中热加工工艺的一种。
它对保证机械产品的质量,延长使用寿命,有着重大的作用。
钢的热处理就是利用钢在加热、保温和冷却作用下,其内部发生组织状态(晶体结构、组织形态)、物理状态(比容、残余内应力等)和化学成分分布的变化,而使工件具有预期的工艺性能、机械性能、物理性能和化学性能,以达到便于冷热加工,提高使用寿命,充分发挥材料潜力的目的。
钢的热处理基本工艺包括退火、正火、淬火、回火和化学热处理等。
根据在车间实习和工作情况,我将主要负责车间中频表面淬火工序的工艺编制。
所以将重点放在中频表面淬火工序上。
一、感应加热原理及分类中频加热是感应表面加热的一种。
感应表面加热是利用导体(零件)在高频磁场作用下产生的感应电流(涡流损耗)以及导体内磁场的作用(磁滞损耗)引起导体自身发热而进行加热的。
根据设备的频率不同分为:①高频加热,频率为100~500千赫。
淬硬层深度为0.3~3㎜,加工工件最小直径为Φ28㎜;②中频加热,一般采用8000赫兹和2500赫兹二种,淬硬层深度:8000赫兹 1.3-5.5㎜,加工工件最小直径为Φ16㎜;2500赫兹 2.4-10㎜,加工工件最小直径为Φ28㎜;③工频加热,频率为50赫兹,淬硬层深度为17-70㎜,加工工件最小直径为Φ200㎜。
目前,我车间使用的设备是中频立式淬火机床,频率为8000赫兹。
而多年不用的高频淬火机床在车间搬、拆迁过程中已经拆除了。
二、感应加热表面淬火工艺及选择感应加热工艺参数包括着热处理参数和电参数。
热处理参数包括加热温度、加热时间、加热速度以及淬火层深度。
电参数包括设备的频率、零件单位面积功率等。
感应加热淬火工艺中几个主要问题:1、确定零件的技术要求表面淬火零件的技术要求包括:表面硬度、淬火层深度及淬硬区分布、淬火层组织等。
⑴.表面硬度:感应淬火后零件的表面硬度要求与材料的化学成分和使用的条件有关。
⑵.淬火层深度:淬火层深度主要是根据零件的机械性能确定的。
- 1、下载文档前请自行甄别文档内容的完整性,平台不提供额外的编辑、内容补充、找答案等附加服务。
- 2、"仅部分预览"的文档,不可在线预览部分如存在完整性等问题,可反馈申请退款(可完整预览的文档不适用该条件!)。
- 3、如文档侵犯您的权益,请联系客服反馈,我们会尽快为您处理(人工客服工作时间:9:00-18:30)。
淬火.退火.正火工艺◆表面淬火• 钢的表面淬火有些零件在工件时在受扭转和弯曲等交变负荷、冲击负荷的作用下,它的表面层承受着比心部更高的应力。
在受摩擦的场合,表面层还不断地被磨损,因此对一些零件表面层提出高强度、高硬度、高耐磨性和高疲劳极限等要求,只有表面强化才能满足上述要求。
由于表面淬火具有变形小、生产率高等优点,因此在生产中应用极为广泛。
根据供热方式不同,表面淬火主要有感应加热表面淬火、火焰加热表面淬火、电接触加热表面淬火等。
• 感应加热表面淬火感应加热就是利用电磁感应在工件内产生涡流而将工件进行加热。
感应加热表面淬火与普通淬火比具有如下优点:1.热源在工件表层,加热速度快,热效率高2.工件因不是整体加热,变形小3.工件加热时间短,表面氧化脱碳量少4.工件表面硬度高,缺口敏感性小,冲击韧性、疲劳强度以及耐磨性等均有很大提高。
有利于发挥材料地潜力,节约材料消耗,提高零件使用寿命5.设备紧凑,使用方便,劳动条件好6.便于机械化和自动化7.不仅用在表面淬火还可用在穿透加热与化学热处理等。
• 感应加热的基本原理将工件放在感应器中,当感应器中通过交变电流时,在感应器周围产生与电流频率相同的交变磁场,在工件中相应地产生了感应电动势,在工件表面形成感应电流,即涡流。
这种涡流在工件的电阻的作用下,电能转化为热能,使工件表面温度达到淬火加热温度,可实现表面淬火。
• 感应表面淬火后的性能1.表面硬度:经高、中频感应加热表面淬火的工件,其表面硬度往往比普通淬火高2~3 个单位(HRC)。
2.耐磨性:高频淬火后的工件耐磨性比普通淬火要高。
这主要是由于淬硬层马氏体晶粒细小,碳化物弥散度高,以及硬度比较高,表面的高的压应力等综合的结果。
3.疲劳强度:高、中频表面淬火使疲劳强度大为提高,缺口敏感性下降。
对同样材料的工件,硬化层深度在一定范围内,随硬化层深度增加而疲劳强度增加,但硬化层深度过深时表层是压应力,因而硬化层深度增打疲劳强度反而下降,并使工件脆性增加。
一般硬化层深δ=(10~20)%D。
较为合适,其中D。
为工件的有效直径。
◆退火工艺退火是将金属和合金加热到适当温度,保持一定时间,然后缓慢冷却的热处理工艺。
退火后组织亚共析钢是铁素体加片状珠光体;共析钢或过共析钢则是粒状珠光体。
总之退火组织是接近平衡状态的组织。
• 退火的目的①降低钢的硬度,提高塑性,以利于切削加工及冷变形加工。
②细化晶粒,消除因铸、锻、焊引起的组织缺陷,均匀钢的组织和成分,改善钢的性能或为以后的热处理作组织准备。
③消除钢中的内应力,以防止变形和开裂。
• 退火工艺的种类①均匀化退火(扩散退火)均匀化退火是为了减少金属铸锭、铸件或锻坯的化学成分的偏析和组织的不均匀性,将其加热到高温,长时间保持,然后进行缓慢冷却,以化学成分和组织均匀化为目的的退火工艺。
均匀化退火的加热温度一般为Ac3+(150~200℃),即1050~1150℃,保温时间一般为10~15h,以保证扩散充分进行,大道消除或减少成分或组织不均匀的目的。
由于扩散退火的加热温度高,时间长,晶粒粗大,为此,扩散退火后再进行完全退火或正火,使组织重新细化。
②完全退火完全退火又称为重结晶退火,是将铁碳合金完全奥氏体化,随之缓慢冷却,获得接近平衡状态组织的退火工艺。
完全退火主要用于亚共析钢,一般是中碳钢及低、中碳合金结构钢锻件、铸件及热轧型材,有时也用于它们的焊接构件。
完全退火不适用于过共析钢,因为过共析钢完全退火需加热到Acm以上,在缓慢冷却时,渗碳体会沿奥氏体晶界析出,呈网状分布,导致材料脆性增大,给最终热处理留下隐患。
完全退火的加热温度碳钢一般为Ac3+(30~50℃);合金钢为Ac3+(500~70℃);保温时间则要依据钢材的种类、工件的尺寸、装炉量、所选用的设备型号等多种因素确定。
为了保证过冷奥氏体完全进行珠光体转变,完全退火的冷却必须是缓慢的,随炉冷却到500℃左右出炉空冷。
③不完全退火不完全退火是将铁碳合金加热到Ac1~Ac3之间温度,达到不完全奥氏体化,随之缓慢冷却的退火工艺。
不完全退火主要适用于中、高碳钢和低合金钢锻轧件等,其目的是细化组织和降低硬度,加热温度为Ac1+(40~60)℃,保温后缓慢冷却。
④等温退火等温退火是将钢件或毛坯件加热到高于Ac3(或Ac1)温度,保持适当时间后,较快地冷却到珠光体温度区间地某一温度并等温保持,使奥氏体转变为珠光体型组织,然后在空气中冷却的退火工艺。
等温退火工艺应用于中碳合金钢和低合金钢,其目的是细化组织和降低硬度。
亚共析钢加热温度为Ac3+(30~50)℃,过共析钢加热温度为Ac3+(20~40)℃,保持一定时间,随炉冷至稍低于Ar3温度进行等温转变,然后出炉空冷。
等温退火组织与硬度比完全退火更为均匀。
⑤球化退火球化退火是使钢中碳化物球化而进行的退火工艺。
将钢加热到Ac1以上20~30℃,保温一段时间,然后缓慢冷却,得到在铁素体基体上均匀分布的球状或颗粒状碳化物的组织。
球化退火主要适用于共析钢和过共析钢,如碳素工具钢、合金工具钢、轴承钢等。
这些钢经轧制、锻造后空冷,所得组织是片层状珠光体与网状渗碳体,这种组织硬而脆,不仅难以切削加工,且在以后淬火过程中也容易变形和开裂。
而经球化退火得到的是球状珠光体组织,其中的渗碳体呈球状颗粒,弥散分布在铁素体基体上,和片状珠光体相比,不但硬度低,便于切削加工,而且在淬火加热时,奥氏体晶粒不易长大,冷却时工件变形和开裂倾向小。
另外对于一些需要改善冷塑性变形(如冲压、冷镦等)的亚共析钢有时也可采用球化退火。
球化退火加热温度为Ac1+(20~40)℃或Acm-(20~30)℃,保温后等温冷却或直接缓慢冷却。
在球化退火时奥氏化是“不完全”的,只是片状珠光体转变成奥氏体,及少量过剩碳化物溶解。
因此,它不可能消除网状碳化物,如过共析钢有网状碳化物存在,则在球化退火前须先进行正火,将其消除,才能保证球化退火正常进行。
球化退火工艺方法很多,最常用的两种工艺是普通球化退火和等温球化退火。
普通球化退火是将钢加热到Ac1以上20~30℃,保温适当时间,然后随炉缓慢冷却,冷到500℃左右出炉空冷。
等温球化退火是与普通球化退火工艺同样的加热保温后,随炉冷却到略低于Ar1的温度进行等温,等温时间为其加热保温时间的1.5倍。
等温后随炉冷至500℃左右出炉空冷。
和普通球化退火相比,球化退火不仅可缩短周期,而且可使球化组织均匀,并能严格地控制退火后的硬度。
⑥再结晶退火(中间退火)再结晶退火是经冷形变后的金属加热到再结晶温度以上,保持适当时间,使形变晶粒重新结晶成均匀的等轴晶粒,以消除形变强化和残余应力的热处理工艺。
⑦去应力退火去应力退火是为了消除由于塑性形变加工、焊接等而造成的以及铸件内存在的残余应力而进行的退火工艺。
锻造、铸造、焊接以及切削加工后的工件内部存在内应力,如不及时消除,将使工件在加工和使用过程中发生变形,影响工件精度。
采用去应力退火消除加工过程中产生的内应力十分重要。
去应力退火的加热温度低于相变温度A1,因此,在整个热处理过程中不发生组织转变。
内应力主要是通过工件在保温和缓冷过程中消除的。
为了使工件内应力消除得更彻底,在加热时应控制加热温度。
一般是低温进炉,然后以100℃/h左右得加热速度加热到规定温度。
焊接件得加热温度应略高于600℃。
保温时间视情况而定,通常为2~4h。
铸件去应力退火的保温时间取上限,冷却速度控制在(20~50)℃/h,冷至300℃以下才能出炉空冷。
◆正火工艺正火工艺是将钢件加热到Ac3(或Acm)以上30~50℃,保温适当的时间后,在静止的空气中冷却的热处理工艺。
把钢件加热到Ac3以上100~150℃的正火则称为高温正火。
对于中、低碳钢的铸、锻件正火的主要目的是细化组织。
与退火相比,正火后珠光体片层较细、铁素体晶粒也比较细小,因而强度和硬度较高。
低碳钢由于退火后硬度太低,切削加工时产生粘刀的现象,切削性能差,通过正火提高硬度,可改善切削性能,某些中碳结构钢零件可用正火代替调质,简化热处理工艺。
过共析钢正火加热刀Acm以上,使原先呈网状的渗碳体全部溶入到奥氏体,然后用较快的速度冷却,抑制渗碳体在奥氏体晶界的析出,从而能消除网状碳化物,改善过共析钢的组织。
焊接件要求焊缝强度的零件用正火来改善焊缝组织,保证焊缝强度。
在热处理过程中返修零件必须正火处理,要求力学性能指标的结构零件必须正火后进行调质才能满足力学性能要求。
中、高合金钢和大型锻件正火后必须加高温回火来消除正火时产生的内应力。
有些合金钢在锻造时产生部分马氏体转变,形成硬组织。
为了消除这种不良组织采取正火时,比正常正火温度高20℃左右加热保温进行正火。
正火工艺比较简便,有利于采用锻造余热正火,可节省能源和缩短生产周期。
正火工艺与操作不当也产生组织缺陷,与退火相似,补救方法基本相同。
淬火工艺与淬火介质淬火工艺是将钢加热到AC3或AC1点以上某一温度,保持一定时间,然后以适当速度冷却获得马氏体和(或)贝氏体组织的热处理工艺。
淬火的目的是提高硬度、强度、耐磨性以满足零件的使用性能。
淬火工艺应用最为广泛,如工具、量具、模具、轴承、弹簧和汽车、拖拉机、柴油机、切削加工机床、气动工具、钻探机械、农机具、石油机械、化工机械、纺织机械、飞机等零件都在使用淬火工艺。
(1)淬火加热温度淬火加热温度根据钢的成分、组织和不同的性能要求来确定。
亚共析钢是AC3+(30~50℃);共析钢和过共析钢是AC1+(30~50℃)。
亚共析钢淬火加热温度若选用低于AC3的温度,则此时钢尚未完全奥氏体化,存在有部分未转变的铁素体,淬火后铁素体仍保留在淬火组织中。
铁素体的硬度较低,从而使淬火后的硬度达不到要求,同时也会影响其他力学性能。
若将亚共析钢加热到远高于AC3温度淬火,则奥氏体晶粒回显著粗大,而破坏淬火后的性能。
所以亚共析钢淬火加热温度选用AC3+(30~50℃),这样既保证充分奥氏体化,又保持奥氏体晶粒的细小。
过共析钢的淬火加热温度一般推荐为AC1+(30~50℃)。
在实际生产中还根据情况适当提高20℃左右。
在此温度范围内加热,其组织为细小晶粒的奥氏体和部分细小均匀分布的未溶碳化物。
淬火后除极少数残余奥氏体外,其组织为片状马氏体基体上均匀分布的细小的碳化物质点。
这样的组织硬度高、耐磨性号,并且脆性相对较少。
过共析钢的淬火加热温度不能低于AC1,因为此时钢材尚未奥氏体化。
若加热到略高于AC1温度时,珠光体完全转变承奥氏体,并又少量的渗碳体溶入奥氏体。
此时奥氏体晶粒细小,且其碳的质量分数已稍高与共析成分。
如果继续升高温度,则二次渗碳体不断溶入奥氏体,致使奥氏体晶粒不断长大,其碳浓度不断升高,会导致淬火变形倾向增大、淬火组织显微裂纹增多及脆性增大。