磨削烧伤检查
磨削烧伤、工件裂纹

磨削烧伤1. 磨削烧伤的分类磨削时,由于磨削区域的瞬时高温(一般为900-1500℃)形成零件层组织发生局部变化,并在表面的某些部分出现氧化变色,这种现象称为磨削烧伤。
磨削烧伤对零件质量性能影响很大,在实际加工过程中应尽量避免。
磨削烧伤有多种不同的分类方法。
根据烧伤外观不同,可分为全面烧伤(整个表面被烧伤)、斑状烧伤(表面上出现分散的烧伤斑点)、均匀线条状烧伤、周期线条状烧伤;按表层显微组织的变化可分为回火烧伤、淬火回火烧伤;还可根据烧伤深度分为浅烧伤(烧伤厚度<0.05mm)、中等烧伤(烧伤层厚度在0.005~0.01mm之间)、深度烧伤(烧伤层厚度>0.01mm)。
在生产中,最常见的是均匀的或周期的线条状烧伤。
由于在磨削烧伤产生时往往伴有表面氧化作用,而在零件表面生成氧化膜。
又因为氧化膜的厚度不同而使其反射光线的干涉状态不同;因此呈现出多种颜色。
所以,人们通常用磨削表面的颜色来判断烧伤的程度。
对钢件来说,随烧伤的加强,颜色一般呈现白、黄、褐、紫、兰(青)的变化。
不同磨削深度下,加工表面的烧伤颜色和氧化膜厚度。
值得注意的是:烧伤颜色仅反映了较严重的烧伤现象,而当零件表面颜色不变时,其表面组织也可能已发生了烧伤变化,这类烧伤通常不易鉴别,所以对零件使用性能危害更大。
目前,人们为了更好地控制烧伤的程度,已根据表面组织的变化时烧伤进行了分级,一般从0-8共分九级,其中,0级最轻,8级烧伤最严重。
1.烧伤产生机理轴承套圈在磨加工中,由于磨粒对工件的切削、刻划和摩擦作用,使金属表面产生塑性变形,由工件内部金属分子间相对位移产生内摩擦而发热;砂轮切削时,相对于工件的速度很高,与工件表面产生剧烈的外摩擦而发热,又因为每颗磨料的切削都是瞬间的,其热量生成也在瞬间,又不能及时传散,所以在磨削区域的瞬时温度较高,一般可达到800~1500℃,如果散热措施不好,很容易造成工件表面的烧伤,也就是在工件的表层(一般有几十微米到击败微米)发生二次淬火及高温回火,破坏了工件表面的组织,肉眼可以看出严重的烧伤。
磨削烧伤检测操作指导书
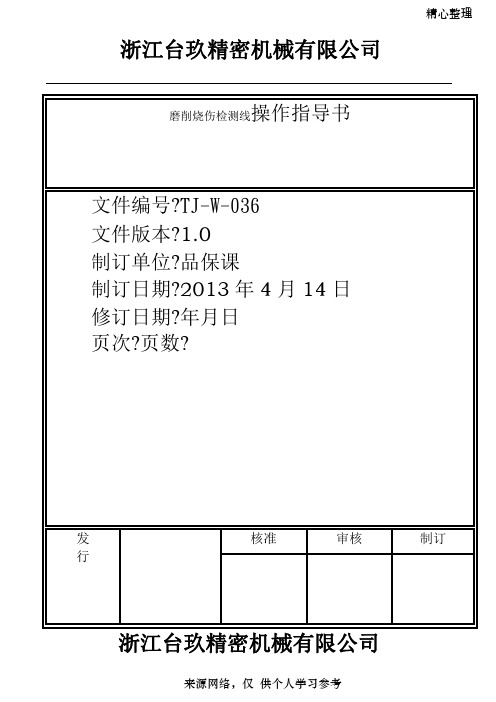
防锈
备注:1.检验必须按池1至池9依次进行检验,时间控制必须符合规定的时间。2.烧伤检验应由经过培训的品保课人员进行。
3.第1池需要加热至50摄氏度以上,所以试验前需加热,试验完成后需关闭开关
2.3检验范围
主要针对蜗杆磨加工工件。即齿部表面烧伤检验。
2.4磨削烧伤检验的判定和记录
A类:无磨削烧伤,表面呈现均匀的灰色.见图2中的无烧伤区域
ph值都须用专门的PH器具或溶度计来检验。
2)浸池定期更换,7、8池12周更换一次;2、4、6池一周更换;1池即洗涤池12周更换
一次;3、5酸池6周更换一次;9浸油池一年更换一次。
当酸溶液更新后,我们需用一件已烧伤的工件来检验腐蚀功能和浸泡时间,并对溶液的腐
蚀效果记录。
品保课
页次/页数
5/7
图1-A级无烧伤
图2B级轻微烧伤
图3D级严重磨削烧伤
图4E级烧伤
2.5检验频率
按客户要求
浙江台玖精密机械有限公司
标题:
腐蚀检测线操作指导书
文件编号
TJ-W-036
文件版本
1.0
制修订日期
2013年4月15日
制订单位
品保课
页次/页数
6/7
2.6磨削烧伤的维护和保养
1)因磨削烧伤线的功能有效性,应每周检验一次,并记录在相应表格中,各池的浓度或
磨削过程中会产生大量的磨削热,一部分被冷却液带走,另一部分被传导入加工件的浅表层内。并使工件表层温度升高。在磨
削热大量产生时会在齿表面形成回火层。当温度达到熔化
温度时,则经冷却液冷却形成二次淬火层,从而形成磨削烧伤。磨削烧伤工件表层会形成回火
层,其表层组织是回火马氏体,会和酸发生腐蚀反应,根据这个原理,我们可以使用硝酸腐蚀
齿轮零件磨削烧伤的危害、检测和预防

齿轮零件磨削烧伤的危害、检测和预防作者:许红平鲁建锋吴伟明徐嘉军来源:《专用汽车》 2019年第1期齿轮类零件作为机构中的重要零部件,在渗碳淬火后往往要进行磨削加工。
在磨削加工工艺中,砂轮与零件的接触区会因摩擦产生大量热量,而大部分热量会通过传导进入零件浅表层,容易导致表层金相组织的变化。
若磨削参数设置和砂轮选择不当,在加工的过程中,会引起表层金相组织改变,并出现较大的残余应力,形成“磨削烧伤”。
零件磨削烧伤会使零件表层的耐磨性、耐腐蚀性和接触疲劳强度降低,使用寿命大大降低,严重的情况下会出现裂纹,从而引发质量问题。
本文通过研究淬火类齿轮的磨削烧伤现象,总结和分析了磨削烧伤的种类和危害,提出了针对不同种类烧伤的不同检测方法,并在此基础上探讨了磨削烧伤的预防措施。
1.磨削烧伤的种类齿轮零件磨削加工的过程中,接触区域的瞬时高温(可达looooc)使得零件表面的金相组织产生局部变化。
根据磨削烧伤表面组织结构的不同,可以将磨削烧伤分成两类。
1.1回火烧伤当磨削接触区表面层温度显著超过马氏体转变温度,而低于相变临界温度Acl的时候,零件表面马氏体产生回火,转变成硬度较低的索氏体和屈氏体,这种烧伤称为“回火烧伤”,如图l(a)所示。
此时该表面的硬度一般为HRC51~57。
1.2二次淬火烧伤淬火钢的马氏体组织在7500C~8000C以上的磨削高温下转变成奥氏体。
如果冷却速度较低,则会重新变为马氏体,零件表层比原淬火硬度稍有提高,一般在HRC63左右。
但此变质层性能稳定性较差,脆性较高,二次淬火烧伤区域周围通常伴有一圈严重的回火层,如图1(b)所示。
2.磨削烧伤和磨削裂纹磨削烧伤的变质层内存在较大的残余应力,当残余应力超过材料的极限强度时,容易导致裂纹的出现。
磨削烧伤不一定伴随磨削裂纹出现,但是磨削裂纹通常都伴随磨削烧伤产生。
磨削裂纹的方向一般与砂轮的轴向进给方向垂直,如图2(a)所示。
齿面存在裂纹后,润滑油会侵入裂纹。
磨削烧伤的检测方法

磨削烧伤的检测方法可能形成网状裂纹,它会导致齿面剥落.这当然是绝对不允许的。
用硬度测试法鉴别磨削烧伤的方法,并用超声波硬度计进行了实验,证明该方法简单易行,可以广泛应用于磨削加工中。
磨削烧伤及其常用检查方法在机械类产品中,很多重要零部件如轴承、齿轮、曲轴、凸轮轴、活塞销和万向节等,在热处理之后均需经过磨削加工。
相比之下,磨削时单位切削面积上的功率消耗远远超过其它加工方法,所转化热量的大部分会进入工件表面,因此容易引起加工面金相组织的变化。
在工艺参数、冷却方法和磨料状态选择不当的情况下,工件在磨削过程中极易出现相当深的金相组织变化层(即回火层),并伴随出现很大的表面残余应力,甚至导致出现裂纹,这就是所谓的磨削烧伤问题。
零部件的表面层烧伤将使产品性能和寿命大幅度地下降,甚至根本不能使用,造成严重的质量问题。
为此,生产企业一方面通过执行正确、科学的工艺规范,减轻和避免出现磨削烧伤现象;另一方面,加强对零部件的检验,及时发现不合格工件,并判断正在进行的磨削工艺状况。
但长期以来,对工件表面磨削烧伤的检验,除了最简单的目测法外,就是采用已延续多年的传统方法——酸洗法,即在被检零部件表面涂上酸液或将其浸入盛有按规定配制的酸液槽中。
之后(或在把工件取出后)根据表面呈现的不同颜色,对磨削烧伤的程度作出相应的判断。
一般地说,若色泽没有变化,就表明情况正常;而当颜色变成灰色,则说明已有烧伤情况存在,随着色泽变得越来越深,表示工件表面因温度更高,引起的磨削烧伤更为严重。
酸洗法具体如下:This is only a suggestion from my collegue ( Dino Calvanelli ) to find theburns on the gears此为有关过烧检测的建议:Clean each sample (part) to be inspected (free ofdirt,oil,grease,fingermarks,protective coatings,etc.).清洗产品,确保无灰尘、油污、手印、表面覆盖物等。
磨削烧伤的检测方法

磨削烧伤的检测方法可能形成网状裂纹,它会导致齿面剥落.这当然是绝对不允许的。
用硬度测试法鉴别磨削烧伤的方法,并用超声波硬度计进行了实验,证明该方法简单易行,可以广泛应用于磨削加工中。
磨削烧伤及其常用检查方法在机械类产品中,很多重要零部件如轴承、齿轮、曲轴、凸轮轴、活塞销和万向节等,在热处理之后均需经过磨削加工。
相比之下,磨削时单位切削面积上的功率消耗远远超过其它加工方法,所转化热量的大部分会进入工件表面,因此容易引起加工面金相组织的变化。
在工艺参数、冷却方法和磨料状态选择不当的情况下,工件在磨削过程中极易出现相当深的金相组织变化层(即回火层),并伴随出现很大的表面残余应力,甚至导致出现裂纹,这就是所谓的磨削烧伤问题。
零部件的表面层烧伤将使产品性能和寿命大幅度地下降,甚至根本不能使用,造成严重的质量问题。
为此,生产企业一方面通过执行正确、科学的工艺规范,减轻和避免出现磨削烧伤现象;另一方面,加强对零部件的检验,及时发现不合格工件,并判断正在进行的磨削工艺状况。
但长期以来,对工件表面磨削烧伤的检验,除了最简单的目测法外,就是采用已延续多年的传统方法——酸洗法,即在被检零部件表面涂上酸液或将其浸入盛有按规定配制的酸液槽中。
之后(或在把工件取出后)根据表面呈现的不同颜色,对磨削烧伤的程度作出相应的判断。
一般地说,若色泽没有变化,就表明情况正常;而当颜色变成灰色,则说明已有烧伤情况存在,随着色泽变得越来越深,表示工件表面因温度更高,引起的磨削烧伤更为严重。
酸洗法具体如下:This is only a suggestion from my collegue ( Dino Calvanelli ) to find theburns on the gears此为有关过烧检测的建议:Clean each sample (part) to be inspected (free ofdirt,oil,grease,fingermarks,protective coatings,etc.).清洗产品,确保无灰尘、油污、手印、表面覆盖物等。
磨削烧伤检查规定

通常应对有回火显示的零件进行磁粉探伤检验,尤其是渗碳淬火硬化的零件。
7.2. 显微硬度计检查
7.2.1. 7.2.2. 7.2.3.
把要检查的部位用 800-1000 号的砂纸磨削 ,尽量少磨,能检查显微硬度即可。 工件要检查的部位不便于进行显微硬度检测,用线切割切下,并镶样。 用显微硬度计检测时,载荷 0.3Kg。对于用线切割切下零件的检验工件 0.05mm 处硬度≥695HV0.3,不允
7. 检验准则
7.1. 目视的外观与分类 未出现回火的零件在清洗和侵蚀后呈现均匀的灰色。局部回火区域在侵蚀后的零件上呈现深灰或黑色。通常,
随着颜色变的越深暗,说明回火烧伤程度越严重。如果在磨削过程中出现严重过热,将导致再硬化,再硬化
区域是一块白色或浅颜色的未回火马氏体,周围是黑色回火面。
所有的磨削后回火,尤其是再硬化的烧伤(即未回火马氏体)会影响零件的寿命,但零件仍可使用。
a)避免直接接触酸碱、溶剂。
b)将酸加入水中或酒精中,防止加反。
c)浸泡箱不用时加盖盖好。
d)遵守可燃和易燃液体储存及使用的安全措施。
有烧伤
无烧伤
机后要检查磨销烧伤。
做好记录。
10. 维护和管理 根据溶液的使用程度或当新配制溶液时,为检验溶液的性能,建议用该溶液侵蚀已知有回火显示的样品零件。
在侵蚀和检验后,该样品应再防锈保护备用,这类样品应定期更换。
根据使用程度,应定期检验溶液的浓度和杂质。
样品和溶液每 7 天更换一次。
11. 安全和环境保护。
磨削烧伤检查规定 1. 目的
保证工件在磨削工序中质量得到保证。 2. 适用范围
本标准规定了用化学侵蚀方法对磨削表面的局部过热进行检验及其分类的标准操作程序和要求,同时硬度法 作为对化学侵蚀方法的校核。 本标准适用于工件在热处理后,进行磨削工序中的检查。对于调质后、高频淬火后、渗碳淬火后的工件都适 用。 本标准不适用氮化零件和不锈钢零件。 化学侵蚀方法对表面硬度的变化的反映比大多数硬度测试方法更为敏感。 表面回火侵蚀检验应在表面磨削后,并在进一步精加工工序之前进行。比如连杆在珩磨前、曲柄销在研磨前。 3. 引用标准 GB/T 17879-1999 齿轮磨削后表面回火的浸蚀检验 4. 设备 4.1. 容器的材料与容器内溶液不得发生反应,也不得损伤被处理的零件。所有容器都应贴上所盛溶液的标签,并 在不用时盖好。本公司采用玻璃烧杯,并用平板玻璃盖好。 4.2. 被检验区域照明 被检验区域应有充分的照明,没有阴影和反射。摧荐被检验区域的光照度应不低于 3200lx。 4.3. 计时装置 应使用适当的计时器(秒表)。保证一组中的所有零件处理过程一致。 4.4. 清洗装置 应采用碱清洗器、蒸汽去油器、溶液清洗装置或相应的清洗装置。 5. 试剂 所有的化学试剂应为工业级或更纯的等级。 5.1. 清洗材料 所有清洗材料应保证能去除所有的污渍、磨粒和油渍,使被检表面可形成不破水膜。不破水膜是指表面用低 于 40℃的清水漂洗干净后,水膜至少应在 15S 内保持不破。 5.2. 硝酸 硝酸密度ρ=1.42Kg/l 5.3. 盐酸 盐酸密度ρ=1.19Kg/l 5.4. 酒精 应使用清洁的、不含油等杂质的甲醇或变性乙醇。 5.5. 水 清洁、无杂质。 5.6. 碱溶液 应使用 4%——6%的氢氧化钠溶液,其 PH≥10。 6. 检验程序 工件清洗→清洗后零件表面应达到能形成不破水膜→侵蚀→检验 6.1. 清洗 a)采用蒸汽清洗。 b)碱洗或超声波清洗。 6.2. 侵蚀 6.2.1. 腐蚀液的配制。
自制件烧伤零件检测详细过程

自制件烧伤零件检测详细过程磨削烧伤在传动工件的加工工艺过程中不可避免。
这些零件在精磨前一般会经过淬火处理,使表面硬度值达到一定的范围。
但在磨削工艺过程中,由于进给量、冷却液类型和流速、砂轮表面状况等因素综合影响,使得磨削产生的热量并不能总被均匀消散,部分没有消散掉的热量进入金属表面,引起回火现象的发生,更严重的情况还会产生二次淬火现象,使得受影响的部位的硬度值超出合格范围,同时伴随金相硬度的变化,应力场还会朝着有害的方向发展,这就是磨削烧伤的成因。
磨削烧伤的现象一旦发生,烧伤的部位的表面抗疲劳强度就会显著地下降。
这样的工件在服役过程中,会发生逐渐开裂甚至表面脱落的情况,造成整个动力系统的失效。
因此对传动工件进行表面磨削质量的检测非常的重要。
传动的检测磨削烧伤有不同的方法,例如目视法、金相法、硬度法以及酸洗法。
磨削烧伤产生的部位具有一定随机性,因此局部的检测方法会有遗漏的问题发生,所以目视法、金相法以及硬度法在实践过程中一般较少应用,对于要求较高的零件这些方法还会被禁止使用。
酸洗法是传统方法中使用最广泛的一种方法,因为检测形式是将工件整个浸润到酸液中,所有的磨削表面都会被覆盖到,因此从方法上来说发生漏检的情况较少。
但是,酸洗法的判别主要是通过颜色的变化,而颜色的变化判断比较依赖于检测人员的经验,经验的不足通常也会造成一定的误判。
此外随着对土壤环境保护的政策越来越严格,酸洗工艺残留的酸液处理也非常麻烦,导致酸洗方法的应用空间变得逐渐狭窄,甚至逐渐被强制摒弃。
在方法局限和政策限制下,另一种纯物理形式的检测方法,巴克豪森噪声法(磁弹法)受到越来越广泛的认可。
巴克豪森噪声法利用了金属部件的应力场和硬度(金相组织)会影响其本身的磁滞回线效应,然后通过激励并捕捉磁滞回线的变化,来间接定性判断零件表面的硬度分布与应力分布异常与否,进而判断是否有烧伤的发生。
该方法的理论成熟,市场商业化应用也得到全球知名动力系统公司如GE、奔驰、大众、沃尔沃、康明斯以及其供应链的认可。
磨削烧伤检查规定

a)避免直接接触酸碱、溶剂。
b)将酸加入水中或酒精中,防止加反。
c)浸泡箱不用时加盖盖好。
d)遵守可燃和易燃液体储存及使用的安全措施。
有烧伤
无烧伤
许表面硬度出现严重的低头现象。对于高频或调质后的零件,检测后显微硬度转换为洛氏硬度应不低于
没有磨削时的表面硬度,但应低于没有磨削时的表面硬度加 4HRC。 8. 回火侵蚀的去除
回火侵蚀后的颜色,采用珩磨去除。
9. 检验人员及检验频次 检验人员车间质检员。
按照工艺(修砂轮的频次)检查,每 2 小时检查 1 件,砂轮更换、设备维修、操作工更换、异常停机重新开
机后要检查磨销烧伤。
做好记录。
10. 维护和管理 根据溶液的使用程度或当新配制溶液时,为检验溶液的性能,建议用该溶液侵蚀已知有回火显示的样品零件。
在侵蚀和检验后,该样品应再防锈保护备用,这类样品应定期更换。
根据使用程度,应定期检验溶液的浓度和杂质。
样品和溶液每 7 天更换一次。
11. 安全和环境保护。
酒精
浸泡并干燥 去水
零件应浸泡足够的时间,以使零
4.
脱色
盐酸 50% (容积)
件上呈现出均匀的棕灰色。脱色 10 秒(10-20 秒) 时间应重复试验以确定确切时
间。
5
漂洗
水
8秒
去酸
6
中和
碱性溶液 PH≥10 20 秒(10-60 秒) 浸入后搅动零件
7
漂洗
水
8秒
去碱
8
酒精浸泡
酒精
浸泡并干燥 去水
9
通常应对有回火显示的零件进行磁粉探伤检验,尤其是渗碳淬火硬化的零件。
7.2. 显微硬度计检查
- 1、下载文档前请自行甄别文档内容的完整性,平台不提供额外的编辑、内容补充、找答案等附加服务。
- 2、"仅部分预览"的文档,不可在线预览部分如存在完整性等问题,可反馈申请退款(可完整预览的文档不适用该条件!)。
- 3、如文档侵犯您的权益,请联系客服反馈,我们会尽快为您处理(人工客服工作时间:9:00-18:30)。
磨削烧伤检查
2#酸洗液配制
合成:将5L浓度为69%~71%的工业硝酸缓缓注入酒精中,稀释成100L溶液,搅拌均匀,混合成酸洗溶液。
3#酸洗液配制
合成:10L浓度为36%~38%的工业盐酸缓缓注入甲醇中,配制成100L溶液, 搅拌均匀。
4#中和液配制
合成:1Kg的碳酸钠加入100Kg水中,搅拌均匀,混合成中和液(碳酸钠与水的重量比为0.01:1)。
加入足够的酚酞指示液,目视观察溶液的中和点(浅粉红色)。
当溶液不在为浅粉红色时,需将溶液废弃。
酸洗程序:
1.清洗液:粗磨或精磨完了的零件上残留的可溶乳剂要用1#热水快速漂洗,再放在60~66C°的1#
清洗液中清洗至少5分钟。
如果是超精研零件表面有油污时,可先用特殊的1#清洗液清洗煤油清洗后,再按正常程序进行。
2.酸洗液:将零件浸入2#酸洗液中,并且上下搅动,直到磨削面都变成黑色(不要超过10秒)。
通
常腐蚀的时间为3~5秒,如果一定要超过10秒钟零件才能变黑,就要更换溶液。
3.自来水漂洗:将酸洗后的零件立即用流动的自来水冲洗。
4.2#酸洗液:将零件浸入3#酸洗液上下搅动。
通常搅动的时间为10秒钟(但不要超过20秒钟),
如果一定要超过20秒钟,就要更换溶液。
5.自来水漂洗:酸洗后的零件用流动的自来水冲洗。
6.中和液:将零件浸入中和液中搅动2~5秒钟。
7.自来水漂洗:将中和后的零件再用流动的自来水冲洗。
8.防锈:酸洗完了的零件应立即浸入专用防锈水中,取出仔细检查烧伤。
9.酸洗检验员检验后,将结果记录在“轴承零件表面酸洗检查记录”中。
酸洗结果的观察及解释:
1.中度的灰色:意味着正常的磨加工表面。
2.黑色或深色区域:意味着表面存在再回火烧伤。
3.亮色或白色区域:意味着表面存在再淬火烧伤,在任何情况下均不可接受。
特例:非常浅的表面
再淬火烧伤如经过二次酸洗可以除去,则可以接受。
在接受批量前,请再二次酸洗有代表性的产品后,根据结果判定。
4.当目视判断有困难时,可进行二次酸洗。
其他要求:
1.对于NSK产品,应保留一粒酸洗实验品和酸洗的检查记录,发货时随产品发给客户。
编制:
批准:
TER-QS201510001。