磨削烧伤检查规定
《法医学人体损伤检验规范》

《法医学人体损伤检验规范》《法医学人体损伤检验规范》1总则1.1 目的本规程的制定使法医学人体损伤检验有一个统一的方法和步骤,为可能出现的重新鉴定或复合及学术交流奠定基础。
1.2 要求1.2.1 对被鉴定的人身检验应由两名以上的执业鉴定人同时进行。
1.2.2 对体表损伤,肢体畸形、缺失或者功能障碍应尽量拍摄局部彩照以存档备查。
1.2.3 检验所用的器械须经质量检定机构检验认可。
1.2.4 检查女性身体时,原则上应由女性执业鉴定人进行。
如果没有女执业鉴定人,可由男性执业鉴定人进行但须有女性工作人员在场。
1.2.5 检查女性身体隐私部位时,应征得其本人或者监护人的同意,如需拍照,须获得其本人或者监护人的书面同意。
2 活体检验2.1 发育与营养2.1.1 发育状况;包括被检者性别、年龄、身长、体重、智力等综合评判为;(1)良好:身高、体重和智力水平均在其性别和年龄组的正常范围;(2)异常:身高、体重和智力水平均超出其性别和年龄组的正常范围;(3)中等:介于二者之间。
(注:儿童发育状况应由儿科专家根据《儿童躯体发育水平评定表》和〈儿童智力和社会行为水平评定表〉进行平定)2.1.2 营养:包括皮肤润泽度和弹性,毛发的光泽和疏密,皮下脂肪的多少及肌肉的发达程度。
记录为(1)良好:粘膜红润、皮肤光泽且弹性良好、皮下脂肪丰满而有弹性,肌肉结实,指甲、毛发润泽,肋间隙及锁骨上窝平坦,肩胛骨和髂骨部肌肉丰满;(2)不良;皮肤粘膜干燥、弹性减低、皮下脂肪薄,肌肉松弛无力,指甲粗糙无光泽,毛发稀疏,肋间隙及锁骨上窝凹陷,肩胛骨和髂骨棱角突出:(3)中等:介于二者之间。
2.2 体表检查2.2.1 皮肤擦伤:应检查皮肤表面有无表面脱落、有无出血或血清渗出。
擦伤的方向:典型的擦伤痕起始端较深,末端较浅,据此可以推断暴力伤的方向。
2.2.2 皮肤挫伤:应检查皮肤的颜色、表面有无局部肿胀、皮下出血和压痛等。
2.2.3 皮肤挫裂创:应检查创口的形状(不规则,如线状、棱状、类圆状、椭圆形、星芒状或不规则形),创缘(粗糙,成锯齿状,或细波浪状。
磨削烧伤、工件裂纹

磨削烧伤1. 磨削烧伤的分类磨削时,由于磨削区域的瞬时高温(一般为900-1500℃)形成零件层组织发生局部变化,并在表面的某些部分出现氧化变色,这种现象称为磨削烧伤。
磨削烧伤对零件质量性能影响很大,在实际加工过程中应尽量避免。
磨削烧伤有多种不同的分类方法。
根据烧伤外观不同,可分为全面烧伤(整个表面被烧伤)、斑状烧伤(表面上出现分散的烧伤斑点)、均匀线条状烧伤、周期线条状烧伤;按表层显微组织的变化可分为回火烧伤、淬火回火烧伤;还可根据烧伤深度分为浅烧伤(烧伤厚度<0.05mm)、中等烧伤(烧伤层厚度在0.005~0.01mm之间)、深度烧伤(烧伤层厚度>0.01mm)。
在生产中,最常见的是均匀的或周期的线条状烧伤。
由于在磨削烧伤产生时往往伴有表面氧化作用,而在零件表面生成氧化膜。
又因为氧化膜的厚度不同而使其反射光线的干涉状态不同;因此呈现出多种颜色。
所以,人们通常用磨削表面的颜色来判断烧伤的程度。
对钢件来说,随烧伤的加强,颜色一般呈现白、黄、褐、紫、兰(青)的变化。
不同磨削深度下,加工表面的烧伤颜色和氧化膜厚度。
值得注意的是:烧伤颜色仅反映了较严重的烧伤现象,而当零件表面颜色不变时,其表面组织也可能已发生了烧伤变化,这类烧伤通常不易鉴别,所以对零件使用性能危害更大。
目前,人们为了更好地控制烧伤的程度,已根据表面组织的变化时烧伤进行了分级,一般从0-8共分九级,其中,0级最轻,8级烧伤最严重。
1.烧伤产生机理轴承套圈在磨加工中,由于磨粒对工件的切削、刻划和摩擦作用,使金属表面产生塑性变形,由工件内部金属分子间相对位移产生内摩擦而发热;砂轮切削时,相对于工件的速度很高,与工件表面产生剧烈的外摩擦而发热,又因为每颗磨料的切削都是瞬间的,其热量生成也在瞬间,又不能及时传散,所以在磨削区域的瞬时温度较高,一般可达到800~1500℃,如果散热措施不好,很容易造成工件表面的烧伤,也就是在工件的表层(一般有几十微米到击败微米)发生二次淬火及高温回火,破坏了工件表面的组织,肉眼可以看出严重的烧伤。
磨削烧伤检测操作指导书
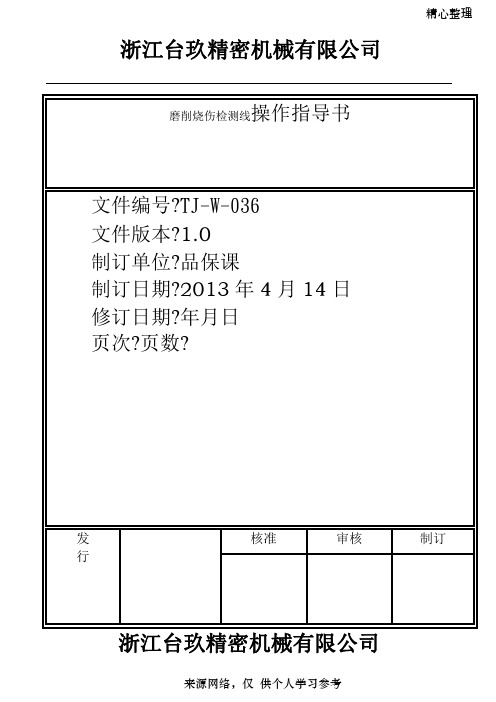
防锈
备注:1.检验必须按池1至池9依次进行检验,时间控制必须符合规定的时间。2.烧伤检验应由经过培训的品保课人员进行。
3.第1池需要加热至50摄氏度以上,所以试验前需加热,试验完成后需关闭开关
2.3检验范围
主要针对蜗杆磨加工工件。即齿部表面烧伤检验。
2.4磨削烧伤检验的判定和记录
A类:无磨削烧伤,表面呈现均匀的灰色.见图2中的无烧伤区域
ph值都须用专门的PH器具或溶度计来检验。
2)浸池定期更换,7、8池12周更换一次;2、4、6池一周更换;1池即洗涤池12周更换
一次;3、5酸池6周更换一次;9浸油池一年更换一次。
当酸溶液更新后,我们需用一件已烧伤的工件来检验腐蚀功能和浸泡时间,并对溶液的腐
蚀效果记录。
品保课
页次/页数
5/7
图1-A级无烧伤
图2B级轻微烧伤
图3D级严重磨削烧伤
图4E级烧伤
2.5检验频率
按客户要求
浙江台玖精密机械有限公司
标题:
腐蚀检测线操作指导书
文件编号
TJ-W-036
文件版本
1.0
制修订日期
2013年4月15日
制订单位
品保课
页次/页数
6/7
2.6磨削烧伤的维护和保养
1)因磨削烧伤线的功能有效性,应每周检验一次,并记录在相应表格中,各池的浓度或
磨削过程中会产生大量的磨削热,一部分被冷却液带走,另一部分被传导入加工件的浅表层内。并使工件表层温度升高。在磨
削热大量产生时会在齿表面形成回火层。当温度达到熔化
温度时,则经冷却液冷却形成二次淬火层,从而形成磨削烧伤。磨削烧伤工件表层会形成回火
层,其表层组织是回火马氏体,会和酸发生腐蚀反应,根据这个原理,我们可以使用硝酸腐蚀
烧伤诊疗规范

烧伤诊疗规范一、诊断要点:根据烧伤史和体格检查对烧伤作出正确诊断。
1. 烧伤史:应注意烧伤时间及环境。
(1)烧伤时间:烧伤时间越长越严重。
(2)烧伤环境:如火焰伤,在密闭环境下就有可能引起吸人性损伤。
又如高空电击伤就可能引起复合伤,如骨折、脑外伤等。
2. 明确受伤原因。
3. 明确伤情:根据烧伤面积、深度、部位、年龄、原因,有无复合伤等综合判断。
4. 鉴别诊断:伤情判断最基本的要求是烧伤面积和深度(1)烧伤面积的估算是烧伤的基本鉴别诊断,常用以下三种方法:①中国新九分法:按体表面积划分为11个9%的等份,另加1%,构成100%的体表面积,即头颈部:1×9%;躯干:3×9%;两上肢:2×9%;双下肢:5×9%+1%,共为11×9%+1%(表)。
中国新九分法成人女性的臀部和双足各占6%②手掌法:不论性别、年龄,病人并指的掌面约占体表面积的1%,如医者的手掌大小与病人相近,可用医者手掌估算,此法可辅助九分法。
③儿童烧伤面积计算:12岁以下儿童,年纪越小,头越大,下肢越小,可按下法计算:头颈部面积:〔(9+12-年龄)〕%;双下肢面积:〔46-(12-年龄)〕%。
(2)烧伤深度的鉴别:①三度四分法:分为I°、浅II°、深II°、III°。
其中I°、浅II°烧伤一般称为浅度烧伤;深Ⅱ°和Ⅲ°烧伤则属深度烧伤。
I°烧伤:红斑浅Ⅱ°烧伤:水疱形成,内含淡黄色澄清液体,水疱皮如剥脱,创面红润、潮湿、疼痛明显。
深Ⅱ°烧伤:水疱,但去疱皮后,创面微湿,红白相间,痛觉较迟钝。
III°烧伤:焦痂(3)烧伤伤情的判断:根据面积、深度、部位、年龄、原因,有无复合伤等综合判断。
但为了对烧伤严重程度有一基本估计,作为设计治疗方案的参考,采用下列分度方法:轻度烧伤:Ⅱ°烧伤面积9%以下。
齿轮零件磨削烧伤的危害、检测和预防

齿轮零件磨削烧伤的危害、检测和预防作者:许红平鲁建锋吴伟明徐嘉军来源:《专用汽车》 2019年第1期齿轮类零件作为机构中的重要零部件,在渗碳淬火后往往要进行磨削加工。
在磨削加工工艺中,砂轮与零件的接触区会因摩擦产生大量热量,而大部分热量会通过传导进入零件浅表层,容易导致表层金相组织的变化。
若磨削参数设置和砂轮选择不当,在加工的过程中,会引起表层金相组织改变,并出现较大的残余应力,形成“磨削烧伤”。
零件磨削烧伤会使零件表层的耐磨性、耐腐蚀性和接触疲劳强度降低,使用寿命大大降低,严重的情况下会出现裂纹,从而引发质量问题。
本文通过研究淬火类齿轮的磨削烧伤现象,总结和分析了磨削烧伤的种类和危害,提出了针对不同种类烧伤的不同检测方法,并在此基础上探讨了磨削烧伤的预防措施。
1.磨削烧伤的种类齿轮零件磨削加工的过程中,接触区域的瞬时高温(可达looooc)使得零件表面的金相组织产生局部变化。
根据磨削烧伤表面组织结构的不同,可以将磨削烧伤分成两类。
1.1回火烧伤当磨削接触区表面层温度显著超过马氏体转变温度,而低于相变临界温度Acl的时候,零件表面马氏体产生回火,转变成硬度较低的索氏体和屈氏体,这种烧伤称为“回火烧伤”,如图l(a)所示。
此时该表面的硬度一般为HRC51~57。
1.2二次淬火烧伤淬火钢的马氏体组织在7500C~8000C以上的磨削高温下转变成奥氏体。
如果冷却速度较低,则会重新变为马氏体,零件表层比原淬火硬度稍有提高,一般在HRC63左右。
但此变质层性能稳定性较差,脆性较高,二次淬火烧伤区域周围通常伴有一圈严重的回火层,如图1(b)所示。
2.磨削烧伤和磨削裂纹磨削烧伤的变质层内存在较大的残余应力,当残余应力超过材料的极限强度时,容易导致裂纹的出现。
磨削烧伤不一定伴随磨削裂纹出现,但是磨削裂纹通常都伴随磨削烧伤产生。
磨削裂纹的方向一般与砂轮的轴向进给方向垂直,如图2(a)所示。
齿面存在裂纹后,润滑油会侵入裂纹。
酸浸法检查磨削烧伤

酸浸法简单易懂,一学就会,现介绍如下(包括样品图),本方法与GB/T17879中的方法略有差别,仅供参考:试剂:5%硝酸溶液3%盐酸酒精溶液5%碳酸钠溶液清水无水乙醇步骤:工件放在5%硝酸溶液浸蚀15~30秒→水中清洗20~30秒→3%盐酸酒精溶液浸蚀20~30秒后→水中清洗30秒→立即放入5%碳酸钠溶液中中和1min→无水乙醇中浸入约10秒→取出立即观察磨削表面是否有黑色区域(如附图),黑色区域的多少即为烧伤程度的大小。
至于合格程度可能要双方协议规定或参照GB/T17879-1999 《齿轮磨削后表面回火的浸蚀检验》这一阵忙,上网本是找个别的问题的,即然来了就说说,酸洗磨削烧伤是每个轴承厂必不可少的检验,但真的在下面进行酸洗的又是些工人,而且酸洗成份控制并不容易(随酸洗量的增加,使用时间变化,酸洗液成份要发生变化)我们酸洗的配方与JB1255的略有不同的,用的是1 脱脂无水碳酸钠25-35 g磷酸三钠25-35 g氢氧化钠10-20 g水玻璃2-3 g水1000毫升2 热水清洗水100%3 流动水清洗水100%4 酸洗硝酸15-25ml水 1000ml5 流动冷水洗水100%6 明化1铬酐130-150g硫酸4 g水1000ml7 流动水清洗水100%8 明化2盐酸(d=1.19)100-200ml二氯化锡2g金属锡100-200g水1000ml9 流动冷水洗水100%10 中和无水碳酸钠4-6%水余量11 流动冷水洗水100%12 防锈亚硝酸钠6-8kg无水碳酸钠1-2kg水余量酸洗后烧伤部位呈黑色,无烧伤呈灰色(白烧伤很少见,一般如磨削发生严重操作失误时可能会出现)磁弹仪测烧伤还是很有效的,但有时磁弹值会受附近电磁信号的干扰,还有就是检测位置比较受限,受探头的影响一些位置测不到,特别是内表面,另外测试效率低,测试仅及一条线,不可能所有表面都测到谢谢各位了.我搜索到了一份操作指导书,原文贴出,供大家参考:磨削烧伤痕迹的显示:1 浸蚀溶液配方:4%硝酸酒精浸蚀:工件在溶液中浸蚀2分钟2 清洗工件在清水中清洗2分钟。
磨削烧伤的检测方法

磨削烧伤的检测方法可能形成网状裂纹,它会导致齿面剥落.这当然是绝对不允许的。
用硬度测试法鉴别磨削烧伤的方法,并用超声波硬度计进行了实验,证明该方法简单易行,可以广泛应用于磨削加工中。
磨削烧伤及其常用检查方法在机械类产品中,很多重要零部件如轴承、齿轮、曲轴、凸轮轴、活塞销和万向节等,在热处理之后均需经过磨削加工。
相比之下,磨削时单位切削面积上的功率消耗远远超过其它加工方法,所转化热量的大部分会进入工件表面,因此容易引起加工面金相组织的变化。
在工艺参数、冷却方法和磨料状态选择不当的情况下,工件在磨削过程中极易出现相当深的金相组织变化层(即回火层),并伴随出现很大的表面残余应力,甚至导致出现裂纹,这就是所谓的磨削烧伤问题。
零部件的表面层烧伤将使产品性能和寿命大幅度地下降,甚至根本不能使用,造成严重的质量问题。
为此,生产企业一方面通过执行正确、科学的工艺规范,减轻和避免出现磨削烧伤现象;另一方面,加强对零部件的检验,及时发现不合格工件,并判断正在进行的磨削工艺状况。
但长期以来,对工件表面磨削烧伤的检验,除了最简单的目测法外,就是采用已延续多年的传统方法——酸洗法,即在被检零部件表面涂上酸液或将其浸入盛有按规定配制的酸液槽中。
之后(或在把工件取出后)根据表面呈现的不同颜色,对磨削烧伤的程度作出相应的判断。
一般地说,若色泽没有变化,就表明情况正常;而当颜色变成灰色,则说明已有烧伤情况存在,随着色泽变得越来越深,表示工件表面因温度更高,引起的磨削烧伤更为严重。
酸洗法具体如下:This is only a suggestion from my collegue ( Dino Calvanelli ) to find theburns on the gears此为有关过烧检测的建议:Clean each sample (part) to be inspected (free ofdirt,oil,grease,fingermarks,protective coatings,etc.).清洗产品,确保无灰尘、油污、手印、表面覆盖物等。
磨削烧伤的检测方法(5篇)

磨削烧伤的检测方法(5篇)第一篇:磨削烧伤的检测方法磨削烧伤的检测方法可能形成网状裂纹,它会导致齿面剥落.这当然是绝对不允许的。
用硬度测试法鉴别磨削烧伤的方法,并用超声波硬度计进行了实验,证明该方法简单易行,可以广泛应用于磨削加工中。
磨削烧伤及其常用检查方法在机械类产品中,很多重要零部件如轴承、齿轮、曲轴、凸轮轴、活塞销和万向节等,在热处理之后均需经过磨削加工。
相比之下,磨削时单位切削面积上的功率消耗远远超过其它加工方法,所转化热量的大部分会进入工件表面,因此容易引起加工面金相组织的变化。
在工艺参数、冷却方法和磨料状态选择不当的情况下,工件在磨削过程中极易出现相当深的金相组织变化层(即回火层),并伴随出现很大的表面残余应力,甚至导致出现裂纹,这就是所谓的磨削烧伤问题。
零部件的表面层烧伤将使产品性能和寿命大幅度地下降,甚至根本不能使用,造成严重的质量问题。
为此,生产企业一方面通过执行正确、科学的工艺规范,减轻和避免出现磨削烧伤现象;另一方面,加强对零部件的检验,及时发现不合格工件,并判断正在进行的磨削工艺状况。
但长期以来,对工件表面磨削烧伤的检验,除了最简单的目测法外,就是采用已延续多年的传统方法——酸洗法,即在被检零部件表面涂上酸液或将其浸入盛有按规定配制的酸液槽中。
之后(或在把工件取出后)根据表面呈现的不同颜色,对磨削烧伤的程度作出相应的判断。
一般地说,若色泽没有变化,就表明情况正常;而当颜色变成灰色,则说明已有烧伤情况存在,随着色泽变得越来越深,表示工件表面因温度更高,引起的磨削烧伤更为严重。
酸洗法具体如下:This is only a suggestion from my collegue(Dino Calvanelli)to find theburns on the gears此为有关过烧检测的建议:Clean each sample(part)to be inspected(free ofdirt,oil,grease,fingermarks,protective coatings,etc.).清洗产品,确保无灰尘、油污、手印、表面覆盖物等。
- 1、下载文档前请自行甄别文档内容的完整性,平台不提供额外的编辑、内容补充、找答案等附加服务。
- 2、"仅部分预览"的文档,不可在线预览部分如存在完整性等问题,可反馈申请退款(可完整预览的文档不适用该条件!)。
- 3、如文档侵犯您的权益,请联系客服反馈,我们会尽快为您处理(人工客服工作时间:9:00-18:30)。
通常应对有回火显示的零件进行磁粉探伤检验,尤其是渗碳淬火硬化的零件。
7.2. 显微硬度计检查
7.2.1. 7.2.2. 7.2.3.
把要检查的部位用 800-1000 号的砂纸磨削 ,尽量少磨,能检查显微硬度即可。 工件要检查的部位不便于进行显微硬度检测,用线切割切下,并镶样。 用显微硬度计检测时,载荷 0.3Kg。对于用线切割切下零件的检验工件 0.05mm 处硬度≥695HV0.3,不允
7. 检验准则
7.1. 目视的外观与分类 未出现回火的零件在清洗和侵蚀后呈现均匀的灰色。局部回火区域在侵蚀后的零件上呈现深灰或黑色。通常,
随着颜色变的越深暗,说明回火烧伤程度越严重。如果在磨削过程中出现严重过热,将导致再硬化,再硬化
区域是一块白色或浅颜色的未回火马氏体,周围是黑色回火面。
所有的磨削后回火,尤其是再硬化的烧伤(即未回火马氏体)会影响零件的寿命,但零件仍可使用。
a)避免直接接触酸碱、溶剂。
b)将酸加入水中或酒精中,防止加反。
c)浸泡箱不用时加盖盖好。
d)遵守可燃和易燃液体储存及使用的安全措施。
有烧伤
无烧伤
机后要检查磨销烧伤。
做好记录。
10. 维护和管理 根据溶液的使用程度或当新配制溶液时,为检验溶液的性能,建议用该溶液侵蚀已知有回火显示的样品零件。
在侵蚀和检验后,该样品应再防锈保护备用,这类样品应定期更换。
根据使用程度,应定期检验溶液的浓度和杂质。
样品和溶液每 7 天更换一次。
11. 安全和环境保护。
磨削烧伤检查规定 1. 目的
保证工件在磨削工序中质量得到保证。 2. 适用范围
本标准规定了用化学侵蚀方法对磨削表面的局部过热进行检验及其分类的标准操作程序和要求,同时硬度法 作为对化学侵蚀方法的校核。 本标准适用于工件在热处理后,进行磨削工序中的检查。对于调质后、高频淬火后、渗碳淬火后的工件都适 用。 本标准不适用氮化零件和不锈钢零件。 化学侵蚀方法对表面硬度的变化的反映比大多数硬度测试方法更为敏感。 表面回火侵蚀检验应在表面磨削后,并在进一步精加工工序之前进行。比如连杆在珩磨前、曲柄销在研磨前。 3. 引用标准 GB/T 17879-1999 齿轮磨削后表面回火的浸蚀检验 4. 设备 4.1. 容器的材料与容器内溶液不得发生反应,也不得损伤被处理的零件。所有容器都应贴上所盛溶液的标签,并 在不用时盖好。本公司采用玻璃烧杯,并用平板玻璃盖好。 4.2. 被检验区域照明 被检验区域应有充分的照明,没有阴影和反射。摧荐被检验区域的光照度应不低于 3200lx。 4.3. 计时装置 应使用适当的计时器(秒表)。保证一组中的所有零件处理过程一致。 4.4. 清洗装置 应采用碱清洗器、蒸汽去油器、溶液清洗装置或相应的清洗装置。 5. 试剂 所有的化学试剂应为工业级或更纯的等级。 5.1. 清洗材料 所有清洗材料应保证能去除所有的污渍、磨粒和油渍,使被检表面可形成不破水膜。不破水膜是指表面用低 于 40℃的清水漂洗干净后,水膜至少应在 15S 内保持不破。 5.2. 硝酸 硝酸密度ρ=1.42Kg/l 5.3. 盐酸 盐酸密度ρ=1.19Kg/l 5.4. 酒精 应使用清洁的、不含油等杂质的甲醇或变性乙醇。 5.5. 水 清洁、无杂质。 5.6. 碱溶液 应使用 4%——6%的氢氧化钠溶液,其 PH≥10。 6. 检验程序 工件清洗→清洗后零件表面应达到能形成不破水膜→侵蚀→检验 6.1. 清洗 a)采用蒸汽清洗。 b)碱洗或超声波清洗。 6.2. 侵蚀 6.2.1. 腐蚀液的配制。
硝酸溶液 浓度摧荐 5% 。(可在 3%——5%选择) 盐酸溶液 浓度摧荐 50% 。1 份盐酸+1 份水。 6.3. 侵蚀步骤:
步骤
过程
溶液
Байду номын сангаас
摧荐时间
备注
硝酸
1
侵蚀
硝酸 5% (容积)
20S(15-30 秒)
出现黑色氧化膜的时间会有所 不同,应重复试验以确定确切时 间。
2.
漂洗
水
8秒
去酸
酒精
3.
浸泡
涂油
防锈油
只浸泡
防锈蚀并增强颜色对比度
1) 零件在浸入相应的侵蚀液时和漂洗时,均应搅动零件。前者是为避免点状侵蚀并获得完全的
中和,后者是为漂洗干净。
2)所有溶液均在室温下使用。 3)允许与摧荐的时间有所不同。 4)对不需要作表面回火侵蚀检验并且公差很小的区域应适当的掩盖,以避免金属被蚀除。每次
在进行该侵蚀过程时,每个表面约有 0.003mm 厚的金属被蚀除。 5)可选步骤;用≥65℃的热水漂洗,然后用干燥空气吹干。该步骤可用来代替酒精浸泡。
许表面硬度出现严重的低头现象。对于高频或调质后的零件,检测后显微硬度转换为洛氏硬度应不低于
没有磨削时的表面硬度,但应低于没有磨削时的表面硬度加 4HRC。 8. 回火侵蚀的去除
回火侵蚀后的颜色,采用珩磨去除。
9. 检验人员及检验频次 检验人员车间质检员。
按照工艺(修砂轮的频次)检查,每 2 小时检查 1 件,砂轮更换、设备维修、操作工更换、异常停机重新开
酒精
浸泡并干燥 去水
零件应浸泡足够的时间,以使零
4.
脱色
盐酸 50% (容积)
件上呈现出均匀的棕灰色。脱色 10 秒(10-20 秒) 时间应重复试验以确定确切时
间。
5
漂洗
水
8秒
去酸
6
中和
碱性溶液 PH≥10 20 秒(10-60 秒) 浸入后搅动零件
7
漂洗
水
8秒
去碱
8
酒精浸泡
酒精
浸泡并干燥 去水
9