组件设计规范-电池篇
电芯设计方案规范
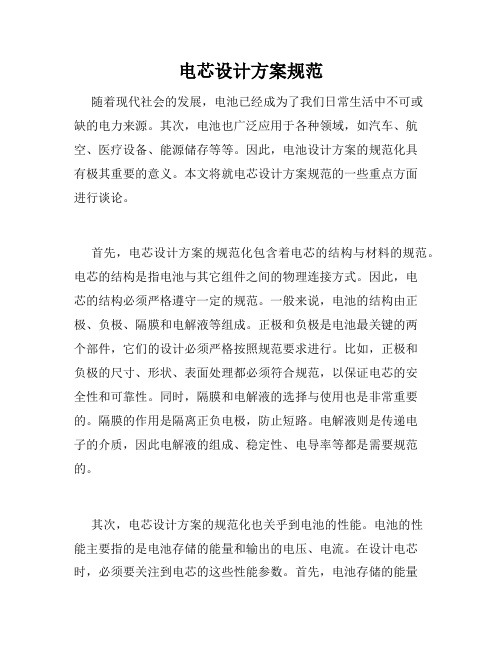
电芯设计方案规范随着现代社会的发展,电池已经成为了我们日常生活中不可或缺的电力来源。
其次,电池也广泛应用于各种领域,如汽车、航空、医疗设备、能源储存等等。
因此,电池设计方案的规范化具有极其重要的意义。
本文将就电芯设计方案规范的一些重点方面进行谈论。
首先,电芯设计方案的规范化包含着电芯的结构与材料的规范。
电芯的结构是指电池与其它组件之间的物理连接方式。
因此,电芯的结构必须严格遵守一定的规范。
一般来说,电池的结构由正极、负极、隔膜和电解液等组成。
正极和负极是电池最关键的两个部件,它们的设计必须严格按照规范要求进行。
比如,正极和负极的尺寸、形状、表面处理都必须符合规范,以保证电芯的安全性和可靠性。
同时,隔膜和电解液的选择与使用也是非常重要的。
隔膜的作用是隔离正负电极,防止短路。
电解液则是传递电子的介质,因此电解液的组成、稳定性、电导率等都是需要规范的。
其次,电芯设计方案的规范化也关乎到电池的性能。
电池的性能主要指的是电池存储的能量和输出的电压、电流。
在设计电芯时,必须要关注到电芯的这些性能参数。
首先,电池存储的能量与当前流通状态有直接关系。
因此,电芯设计方案必须充分考虑电池在不同工作状态下的能量变化,并确定最佳工作状态。
其次,电池的输出压力和电流也需要设计时考虑。
比如,在汽车电池的设计中,电池需要能够输出高强度的电流,在冷启动时能够启动发动机。
因此,电池的输出电压、电流也需在设计阶段考虑明确。
此外,电池的安全性也是电芯设计方案规范的重要考量。
电池的安全性主要涉及到电池在工作中可能发生的危险及风险。
因此,电芯设计方案需要考虑到多种安全因素。
比如,防止电池瞬间过充或过放,防止电芯间隔短路,防止温升过高等等。
因此,电芯设计方案中必须设置一个安全回路,当电池发生异常时,可以及时断开电池电路以保证电池的安全。
最后,电芯设计方案的规范化也涉及到电池的成本问题。
电池的成本在设计阶段就应该考虑到。
为了控制电池的成本,要尽量降低电芯的制造成本与材料成本。
太阳能电池组件及方阵的设计方法案例图文说明

太阳能电池组件及方阵的设计方法案例图文说明上面已经说过,太阳能电池组件的设计就是满足负载年平均每日用电量的需求。
所以,设计和计算太阳能电池组件大小的基本方法就是用负载平均每天所需要的用电量(单位:安时或瓦时)为基本数据,以当地太阳能辐射资源参数如峰值日照时数、年辐射总量等数据为参照,并结合一些相关因素数据或系数综合计算而得出的。
在设计和计算太阳能电池组件或组件方阵时,一般有两种方法。
一种方法是根据上述各种数据直接计算出太阳能电池组件或方阵的功率,根据计算结果选配或定制相应功率的电池组件,进而得到电池组件的外形尺寸和安装尺寸等。
这种方法一般适用于中小型光伏发电系统的设计。
另一种方法是先选定尺寸符合要求的电池组件,根据该组件峰值功率、峰值工作电流和日发电量等数据,结合上述数据进行设计计算,在计算中确定电池组件的串、并联数及总功率。
这种方法适用于中大型光伏发电系统的设计。
下面就以第二种方法为例介绍一个常用的太阳能电池组件的设计计算公式和方法,其他计算公式和方法将在下一节中分别介绍。
1.基本计算方注计算太阳能电池组件的基本方法是用负载平均每天所消耗的电量(Ah)除以选定的电池组件在一天中的平均发电量(Ah),就算出了整个系统需要并联的太阳能电池组件数。
这些组件的并联输出电流就是系统负载所需要的电流。
具体公式为:负载用电10A,负载工作8小时。
(220V ))组件日平均发电量()负载日平均用电量(电池组件并联数Ah Ah =其中, 组件日平均发电量=组件峰值工作电流(A)×峰值日照时数(h)。
假设告知负载日耗电(KWh ),如何计算负载日平均用电量(Ah )。
再将系统的工作电压除以太阳能电池组件的峰值工作电压,就可以算出太阳能电池组件的串联数量。
这些电池组件串联后就可以产生系统负载所需要的工作电压或蓄电池组的充电电压。
具体公式为:组件峰值工作电压系数)系统工作电压(电池组件串联数 1.43V ⨯=系数1.43是太阳能电池组件峰值工作电压与系统工作电压的比值。
电动汽车动力电池系统设计规范03
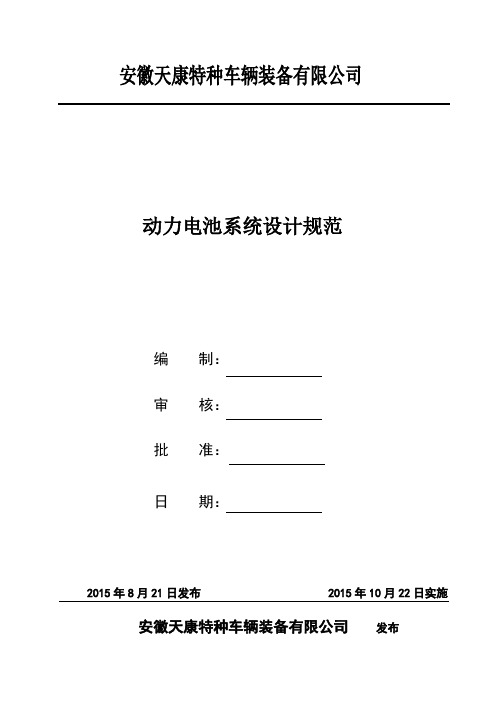
安徽天康特种车辆装备有限公司动力电池系统设计规范编制:审核:批准:日期:2015年8月21日发布2015年10月22日实施安徽天康特种车辆装备有限公司发布目录前言.................................................................................................................................... I I 电动汽车动力系统设计规范 . (1)1.概述 (1)2.设计原则 (1)3.参考引用标准 (1)4.术语和定义 (2)5.设计要求 (4)6.设计验证 (24)前言本规范规定山东省普天新能源汽车(山东)有限公司开发的专用车辆时的线束设计规范。
本规范由安徽天康特种车辆装备有限公司产品开发部提出。
本规范由安徽天康特种车辆装备有限公司批准。
本规范主要起草人:李劲松本规范于2015年8月首次发布。
电动汽车动力系统设计规范1.概述动力电池系统是电动汽车的重要组成部分,为电动汽车驱动提供能量来源。
由于电池系统是高电压高能量密度产品,在设计电池系统时,主要从箱体设计、电池成组设计、电池安全、以及电池管理系统设计等方面进行。
2.设计原则动力电池系统设计以满足车辆动力要求为前提,同时从电池系统自身内部结构和安全设计、电池管理等方面进行设计,主要包括以下几个部分:(1)电池箱外观尺寸:电池箱体尺寸主要根据车辆提供的电池安装空间进行设计,并且要考虑到接插件和机械连接部位的尺寸影响。
电池箱内部尺寸,主要从整体设计考虑,从电池的排布、线束的排布以及电池管理系统尺寸位置、热管理系统尺寸及位置等方面进行设计。
电池箱的外观设计主要从材质、表面防腐蚀、绝缘处理、产品标识等方面进行设计。
(2)电池性能参数:电池系统参数,比如电压平台、额定容量、额定能量、最大可持续放电电流、瞬间峰值放电电流、瞬间峰值充电电流等,在设计时要根据车辆的动力参数和要求进行匹配。
锂电池设计规范范文

锂电池设计规范范文1.引言锂电池作为一种重要的电源技术,广泛应用于移动通信、电动车辆、储能等领域。
为了确保锂电池的安全性、性能和可靠性,需要制定相应的设计规范。
本文档旨在提供一套完整的锂电池设计规范,帮助设计人员在设计过程中遵循相关安全和技术要求。
2.锂电池基本知识2.1锂电池分类:按照锂电池的结构和性能特点,可将其分为锂离子电池、锂聚合物电池和锂离子聚合物电池等几类。
2.2锂电池组成:锂电池主要由正极、负极、电解质和隔膜等组成,其中正极材料常见有三元材料和钴酸锂材料等。
3.锂电池设计安全要求3.1电池外壳设计:电池外壳应采用阻燃材料,并具备良好的散热性能和抗冲击性能,以防止外力引起电池短路或起火等事故。
3.2温控系统设计:锂电池在高温或低温环境下工作容易引发安全问题,因此需要设计合理的温控系统,包括温度传感器、温度调节器等,以确保电池在合适的温度范围内工作。
3.3过充保护设计:通过设计过充保护电路,确保电池在充电时不会超过额定电压,避免发生过充现象,降低安全风险。
3.4过放保护设计:通过设计过放保护电路,确保电池在放电时不会低于最低允许电压,避免发生过放现象,延长电池寿命。
3.5短路保护设计:通过设计短路保护电路,确保电池在遭受外力短路时能够及时切断电路,防止电池起火或爆炸。
4.锂电池设计性能要求4.1能量密度:电池的能量密度决定了其储能能力,设计中应追求高能量密度,以提高电池的使用时间和续航里程。
4.2功率密度:电池的功率密度决定了其输出能力,设计中应追求高功率密度,以满足高功率需求,如电动车加速等。
4.3循环寿命:电池的循环寿命是指电池充放电循环次数达到规定条件的次数,设计中应追求长循环寿命,提高电池的使用寿命和可靠性。
4.4自放电率:电池的自放电率影响其长时间储存能力,设计中应追求低自放电率,以保证电池长时间存储后能够正常工作。
5.锂电池设计可靠性要求5.1组件设计可靠性:设计中应合理选择电池正负极材料和电解液,以确保电池组件的可靠性和稳定性。
光伏组件电池板检验要求规范

光伏组件电池板检验要求规范一、材料要求:1.硅片:硅片应符合国家或国际标准,具有良好的质量和纯度。
2.连接线:连接线应具有良好的导电性和耐久性,不得出现划痕、脱漆等情况。
3.玻璃:玻璃应具有良好的透光性和耐候性,不得出现裂纹、气泡等缺陷。
二、外观要求:1.表面平整度:光伏组件电池板的表面应平整、无明显凹凸、起皱、熔融或漏胶等缺陷。
2.玻璃表面质量:玻璃表面应光滑、无划痕、气泡、模糊等缺陷。
3.边框:边框应平直、无断裂、变形等缺陷,并且固定牢固。
三、性能要求:1.转换效率:光伏组件电池板的转换效率应符合国家或行业标准,具有良好的能量转换性能。
2. 开路电压(Voc):光伏组件电池板的开路电压应符合设计要求,并具有稳定的电压输出。
3. 短路电流(Isc):光伏组件电池板的短路电流应符合设计要求,并具有稳定的电流输出。
4.填充因子(FF):光伏组件电池板的填充因子应符合设计要求,达到最佳电池效能。
5.绝缘电阻:光伏组件电池板的绝缘电阻应符合国家或行业标准,确保安全使用。
6.抗PID性能:光伏组件电池板应具有良好的抗PID性能,保证在高湿度和高温环境下的稳定性能。
7.抗反射性能:光伏组件电池板的表面应具有良好的抗反射性能,提高光吸收效率。
四、标识要求:1.标识清晰:光伏组件电池板的标识应清晰、易读,能够准确表示产品的型号、生产日期、生产厂家等信息。
2.防伪标识:光伏组件电池板的防伪标识应具有高度的防伪性,防止假冒产品的流通。
3.认证标识:光伏组件电池板应标明通过的相关认证,如国家质量认证、国际质量认证等。
以上是光伏组件电池板检验要求规范的主要内容。
通过对光伏组件电池板的材料、外观、性能和标识等方面的检验,可以确保产品的质量和性能符合要求,并且提供准确的产品信息和防伪保障。
光伏组件电池板的检验要求规范的制定和实施,对于推动光伏产业的发展、增强产品竞争力具有重要意义。
太阳能电池组件技术规范

太阳电池组件成品技术规范编写:校对:审核:会签:、、、、、、批准:太阳电池组件技术总规范1目的通过制定太阳电池组件技术总规范,使公司所生产的太阳能电池组件的生产及质量处于规范、可控的状态。
保证产品质量,满足客户要求。
2适用范围2.1本技术规范规定了太阳电池组件的技术要求、外观质量及性能要求。
2.2本技术规范适用于本公司生产的太阳能电池组件(客户另有要求除外)。
2.3本技术规范不能取代本公司与客户签订的技术协议。
3职责权限3.1技术开发部制定太阳能电池组件成品技术总规范;3.2公司各相关部门在电池组件生产、检验等环节依据本规范执行。
4引用文件4.1 GB/T 9535 地面用晶体硅光伏组件——设计鉴定和定型(IEC 61215-2005,IDT);4.2 GB/T 20047.1-2006 光伏(PV)组件安全鉴定第1部分:结构要求(IEC 61730-1:2004);4.3 GB/T 20047.2-2006光伏(PV)组件安全鉴定第2部分:试验要求(IEC 61730-2:2004);4.4 QEH-2011-RD-I139A太阳电池组件用晶硅电池片技术规范V1.0;4.5 QEH-2011- RD-I115A太阳电池组件用钢化玻璃技术规范V2;4.6 QEH-2011- RD-I121A太阳电池组件用EVA技术规范V2;4.7 QEH-2011- RD-I122A太阳电池组件用背板材料技术规范 V2;4.8 QEH-2011- RD-I114A太阳电池组件用焊带技术规范V1.2;4.9 QEH-2011- RD-I123A太阳电池组件用接线盒技术规范V2.0;4.10 QEH-2010-RD-I118A太阳电池组件用铝合金边框技术规范;4.11 QEH-2011-RD-I119A 太阳电池组件用透明胶带技术规范V1.0;4.12 QEH-2011-RD-I124太阳能电池组件制造工艺过程卡汇总V4.0;4.13 IEC 60364-2005 Electrical installations of buildings-Part 5-51 Selection and erection of electrical equipment-Common rules.5定义5.1 组件:具有封装及内部连接的、能单独提供直流电输出的、不可分割的最小太阳能电池组合装置。
太阳能光伏电池组件设计与制造
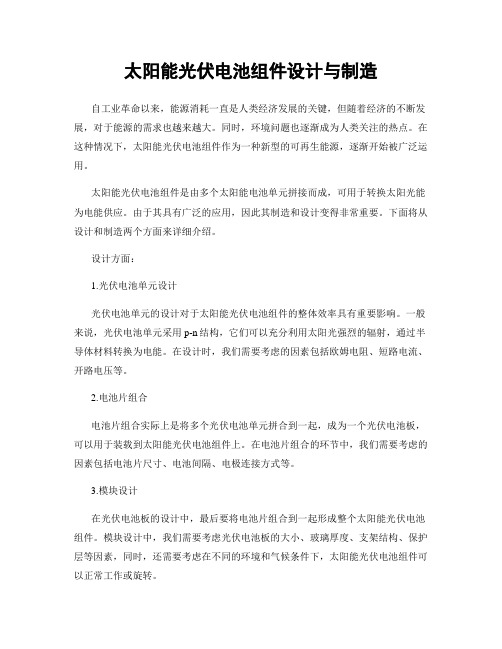
太阳能光伏电池组件设计与制造自工业革命以来,能源消耗一直是人类经济发展的关键,但随着经济的不断发展,对于能源的需求也越来越大。
同时,环境问题也逐渐成为人类关注的热点。
在这种情况下,太阳能光伏电池组件作为一种新型的可再生能源,逐渐开始被广泛运用。
太阳能光伏电池组件是由多个太阳能电池单元拼接而成,可用于转换太阳光能为电能供应。
由于其具有广泛的应用,因此其制造和设计变得非常重要。
下面将从设计和制造两个方面来详细介绍。
设计方面:1.光伏电池单元设计光伏电池单元的设计对于太阳能光伏电池组件的整体效率具有重要影响。
一般来说,光伏电池单元采用p-n结构,它们可以充分利用太阳光强烈的辐射,通过半导体材料转换为电能。
在设计时,我们需要考虑的因素包括欧姆电阻、短路电流、开路电压等。
2.电池片组合电池片组合实际上是将多个光伏电池单元拼合到一起,成为一个光伏电池板,可以用于装载到太阳能光伏电池组件上。
在电池片组合的环节中,我们需要考虑的因素包括电池片尺寸、电池间隔、电极连接方式等。
3.模块设计在光伏电池板的设计中,最后要将电池片组合到一起形成整个太阳能光伏电池组件。
模块设计中,我们需要考虑光伏电池板的大小、玻璃厚度、支架结构、保护层等因素,同时,还需要考虑在不同的环境和气候条件下,太阳能光伏电池组件可以正常工作或旋转。
制造方面:1.制造材料太阳能光伏电池组件的制造材料是多种多样的。
一般来说,我们使用的是具有较高转换效率的单晶硅或多晶硅。
在制造时,以单晶硅为例,需要先准备晶状硅块,之后将其进行切割后形成光伏电池片。
因此,材料的准备对于光伏电池组件的制造至关重要。
2.组件制造光伏电池组件的制造通常分为以下几个环节:切割、清洗、钝化、涂覆等。
组件制造的目的是在制造过程中尽可能减少组件中光电效应失效的可能性,促进其在太阳光下的工作。
总之,太阳能光伏电池组件的制造和设计是一个复杂的过程,需要各个环节相互配合、相互支持,始能最终制造出高效率、高质量的太阳能光伏电池组件。
动力电池技术的国际标准与规范

动力电池技术的国际标准与规范随着全球能源转型和汽车产业的快速发展,动力电池作为电动汽车的核心组件之一,其技术标准与规范的制定和实施变得至关重要。
本文将对动力电池技术的国际标准和规范进行探讨,以期为相关行业提供参考和借鉴。
一、动力电池技术的国际标准1. ISO/IEC 62660系列标准ISO/IEC 62660系列标准是国际上最重要的动力电池标准之一。
该系列标准主要规定了动力电池的性能测试方法、耐久性能要求、安全性能要求等内容,为动力电池的设计、研发、制造和使用提供了一致的技术规范。
2. UN R100UN R100是联合国制定的动力电池国际标准,适用于电动汽车和混合动力汽车的高压动力电池系统。
该标准对动力电池的安全性能、机械强度、电气安全性和安全管理等方面进行了详细规定,确保了动力电池的安全可靠性。
3. GB/T 31485-2015GB/T 31485-2015是中国制定的动力电池技术标准,是中国汽车工业领域的动力电池技术标准,与国际标准相互衔接。
该标准细化了电池的性能指标、测试方法和试验条件,有力地推动了我国动力电池行业的规范化和标准化发展。
二、动力电池技术的国际规范1. ISO/IEC 29167系列规范ISO/IEC 29167系列规范是国际电工委员会和国际标准化组织联合制定的,主要规范了动力电池与车辆之间的通信标准。
该系列规范确保了动力电池在不同车辆之间的互操作性和通信的安全性,为电动汽车的发展提供了技术保障。
2. SAE J2929SAE J2929是美国汽车工程师协会制定的动力电池规范,详细规定了动力电池的构造、性能和测试方法。
该规范对动力电池的设计、制造、测试和使用提供了指导,为动力电池的研发和市场应用奠定了基础。
3. GB/T 31467.3-2015GB/T 31467.3-2015是中国制定的动力电池规范之一,主要规定了动力电池的储存、运输和安全要求。
该规范要求电池制造商和使用者制定和执行相应的管理制度和操作规程,确保动力电池的安全运输和存储。
- 1、下载文档前请自行甄别文档内容的完整性,平台不提供额外的编辑、内容补充、找答案等附加服务。
- 2、"仅部分预览"的文档,不可在线预览部分如存在完整性等问题,可反馈申请退款(可完整预览的文档不适用该条件!)。
- 3、如文档侵犯您的权益,请联系客服反馈,我们会尽快为您处理(人工客服工作时间:9:00-18:30)。
太阳能电池根据所用材料的不同,分为:硅太阳能电池、多元化合物薄膜太阳能电池、聚合物多层修饰电极型太阳能电池、纳米晶太阳能电池、有机太阳能电池,其中硅太阳能电池是目前发展最成熟的,在组件应用中居主导地位。
1.硅电池片的类别硅太阳能电池分为单晶硅太阳能电池、多晶硅薄膜太阳能电池和非晶硅薄膜太阳能电池三种。
表表12. 常见硅电池片●Sunpower特点:采用只在背面配置电极的背接触式(Back Contact)结构。
由于表面没有遮光的电极,因此,不仅转换效率高,而且整个电池单元呈黑色,富于创意性。
●EverGreen特点:背面采用方形电极。
●Motech(茂迪)/JA(晶澳)/JW(珈伟)/GE/SM(西门子)/SF(林洋)3. 太阳能电池的电性能参数3.1转换效率η太阳能电池转换效率是太阳能电池的输出功率P与投射到太阳能电池面积上的入射光功率S 之比,其值取决于工作点。
如果阵列不工作于最大功率点,则阵列的效率实际上都低于按此定义的效率致,世纪效率可以任意的低,甚至低到零。
此外,只有当所有的其他重要参数(如日照强度、光谱、温度等)都已确定时,效率才能被唯一的定义。
3.2 填充因子FF可以定义为最大输出功率与Isc、V oc之比,也就是最大功率矩形面积对Isc、Voc矩形面积的比例。
对于太阳能电池来说,填充因子是一个重要的参数,它可以反映太阳能电池的质量。
太阳能电池的串联电阻越小,并联电阻越大,填充系数就越大,反映到太阳能电池的电流-电压特性曲线上,曲线就越接近正方形,此时太阳能电池的转换效率就越高。
3.3 短路电流Isc当V=0时,电流达到最大,称短路电流Isc(Short-Circuit Current)。
3.4 开路电压Voc当I=0时,电压达到最大,称开路电压Voc(Open Circuit Voltage)。
3.5 最大工作功率Pm在I=Isc,V=0及V=V oc,I=0处,其功率值P=0。
V=Vm,I=Im,可得最大功率Pm(Maximum Power Point)=VmIm,功率取之于0~Pm之间。
4. 电池片的使用流程电池片的作为组件最核心的原材料,在进行组件装配之前会进行一系列的前期准备工作。
包括弱光、分选、电性能测试、划片等或其中的几个步骤。
下面列举常用的Sunpower电池片和EverGreen电池片的使用流程。
4.1 Sunpower电池片使用流程:4.1.1 将Sunpower的Q档电池片进行弱光测试,将弱光测试≥0.1V的电池片进行第3步(外观分选);将<0.1V的电池片进行下一步(单片热斑测试)4.1.2 进行单片热斑测试,合格片进行第3步(外观分选);不合格片进行第5步(切片);4.1.3 进行外观分选,将外观合格片进行下一步(电性能测试);不合格片进行第5步(切片);4.1.4 进行功率或电流分选,电性能合格片将入库;不合格片进行下一步;4.1.5 激光划片机切割成1/3片;或将1/3片切割成做小板型。
4.1.6 将切割的1/3片进行弱光测试,将弱光测试≥0.1V的电池片进行第3步,将<0.1V的电池片返回进行第2步(单片热斑测试);4.2 Evergreen电池片使用流程:4.2.1 整片进行外观分选4.2.24.2.34.2.45. 电池片的划片在组件设计过程中有时候需要将整片电池片切割成更小的单体电池片,再进行串并联电路连接。
针对不同的电池片,激光划片操作略有不同,下面针对两种典型的Sunpower电池片和Evergreen电池片的划片操作进行说明。
5.1 Sunpower电池片划片操作规程:5.1.1开启电源、水循环、水温控制空调、吸尘泵、吸附泵并确认已正常工作;5.1.2启动激光调制和载片平台;5.1.3启动计算机,进入系统,开启程序,按切割图纸要求的尺寸设定载片台的运行路径和速度(如果之前已设定好,可直接载入);5.1.4调整激光切割机工作电流直至切割后的电池好掰为止;5.1.5调整操作台初始位置,关闭频率,放一片电池在载片台上,运行一次程序。
看切割后电池的尺寸是否按图纸要求,是否切割在绝缘线内;5.1.6把光滑平整的纸用胶带固定到载片台非切割区域堵住吸附孔,防止气体流通;5.1.7将一定数目的电池(背面向上),放到载片台上非切割区域;5.1.8双手轻轻拿起一片电池(背面向上)放到载片,负极这一边紧靠铁条,然后启动切割程序,按照图纸要求进行切割。
将已切割好的电池放到托盘上,再将正极这一边紧靠铁条,按上述步骤操作;5.1.9切片完后,用一张白纸轻轻插入切好的电池正面下面,然后用白纸将切好的电池托起放到工作台上,再用白纸放在已掰好电池的正面,将一定数量的电池按大角、小角、直片分类摆放并做好标识,放入托盘内,在切割区域放上下一片电池准备切割;5.1.10将切割不良的电池挑出,做好标识。
5.2 Evergreen电池片划片操作规程:5.2.1打开激光机电源,启动激光切割程序,校准载片台的初始位置;5.2.2打开吸尘泵,确认激光机和吸尘泵工作正常;5.2.3按所需切割尺寸进行编程,然后将分选好电池紧靠中心铁条放在切片平台上;5.2.4用压条压在被切割电池上,如被切割的电池上、下两端翘起,应用手把电池压住,然后开始切割;5.2.5关闭吸尘泵,小心拿起切片平台上切好的电池,力度均匀的掰开;5.2.6将切割后的电池按照《EG电池检验标准》自检,然后纵向有序地放置在周转纸箱里;5.2.7操作的过程中,发现不良品,挑出并存放在指定区域。
3.电池片的分选3.1 单片电性能测试制作太阳能电池组件时,要分选出电性能参数一致的单体电池片进行组合和封装,以保证太阳能电池组合的损失最小。
常见分选方式:1.电流分档:以定电压测电流的方法,将电池片分为若干个档位,通常电压取经验值0.52V,测得电流以0.00~0.09A的电流区间分档。
2.功率分档:直接测得单片电池片的工作功率Pm,通常以0.00~0.09W的功率区间进行分档。
单片测试操作规程:1.准备工作1.1穿好工作衣、工作鞋,戴好工作帽、手套。
1.2清洁、整理工作场地、设备和工具。
2.自检:对上道工序来料进行检验。
检验要求如下:2.1芯片无破损、裂纹、无栅线断线。
2.2缺角面积不大于1mm2,每片不超过2个。
3.分检操作过程:3.1按单片测试仪设备操作规程打开分检测试仪电源开关。
3.2按下“量程”、“分标”、“小片”按钮,测试仪自动闪光(需自动闪光半小时,对设备进行预热)。
3.3将标准电池片置于测试铜板上校准,功率误差不超过±1%W,否则请维修人员调整。
将校准结果做好记录。
3.4将待测电池沁片置于测试台铜板上,并将电极压在电池芯片正面的主栅极上,保证正、负电极其接触良好,在电脑显示器上设定一栏里设定芯片面积,单晶125电池片面积为0.14857mm2,156电池片为0.241 mm2,多晶片输入实际的边长尺寸即可。
3.5设备预热后进行分检测试,按最大功率1W以上的每0.1W一个档次进行分档,1W以下的每0.05W一个档次进行分档。
3.6每隔2个小时校准一次标准片,若发现功率超出标准范围后,前2个小时测试的芯片重新进行检测。
3.7检测结束后,进行自检。
4.自检要求如下:4.1芯片无碎片、裂纹,缺角面积符合要求。
4.2记录清晰,堆放整齐,无混档现象。
4.3符合要求,做好相关记录,并流下道工序。
4.4发现有批质量问题,立即报告生产主管。
5. 注意事项5.1分检测试仪的铜电极一定要与电池芯片背表面的印刷电极接触良好。
5.2将操作时产生的待处理片和废片分类放置。
5.3不符合自检要求的单片,为待处理片。
3.2电池片的外观分检由于不同厂家生产的电池片制作工艺及结构均有差异,故外观分选的标准各有差异。
通常观察以下几个方面:电池片缺口、崩边、表面污点、花斑、划伤、磨花、裂纹、栅线破损等,依据缺陷的程度分为A,B…等级。
1. 准备工作1.1穿好工作衣、工作鞋,戴好工作帽、手套。
1.2清洁、整理工作场地、设备和工具。
2. 自检:对上道工序来料进行检验。
检验要求如下:2.1对来料包装进行确认与生产任务书上要求的芯片效率一致。
2.2对生产商进行确认与生产任务书上生产商一致,包装完好无破损。
2.3对来料数量进行确认,来料数量与领料单上的数据相符再进行拆箱分检。
3. 分检要求如下:3.1外观缺陷检验,来料电池片必须完好,缺角面积不大于1mm2的每片不超过两处,无碎片、无隐裂、无栅线断线、无银铝浆脱落、无鼓包等现象,若有以上缺陷现象挑出后按照不同的缺陷现象进行分类包装并做好记录。
3.2规格尺寸及印刷图案检验,来料的电池片尺寸必须一致,无平行四边形、斜边或缺边现象,印刷图案一致。
3.3按单片不同的颜色进行分类,把颜色相近的电池片放在一起。
3.4按不同的电池片效率进行分类,把相同效率的电池片放在一起3.5把相同颜色、相同效率的电池片按照当日生产规格组件规定的串联电池片的数量要求进行分类。
3.6按照当日生产组件的数量分好相应数量的电池片。
3.7把分检好的电池片按照总数量的千分之二进行电性能抽检,按照单片测试操作规程进行检测,电性能误差不超过《原材料检验规范》的规定即可通过,检测完成后的电池片必须放回原来的分类档次里边。
3.7检测结束后,进行自检。
4. 自检要求如下:4.1检测分类好的电池片必须是完好的,外观缺陷检验必须是百分百的检验,不能有漏检现象,分类要清晰,标识要准确。
4.2记录清晰准确,堆放整齐,无混档现象。
4.3符合要求,做好相关记录,并流下道工序。
4.4发现有批质量问题,立即报告生产主管。
5. 注意事项5.1分检过程中必须戴好手套或指套,不可以用手直接接触电池片。
5.2将操作时产生的碎片按大小形状分类放置。