超声波塑料件的结构设计
浅谈塑料超声波产品的设计
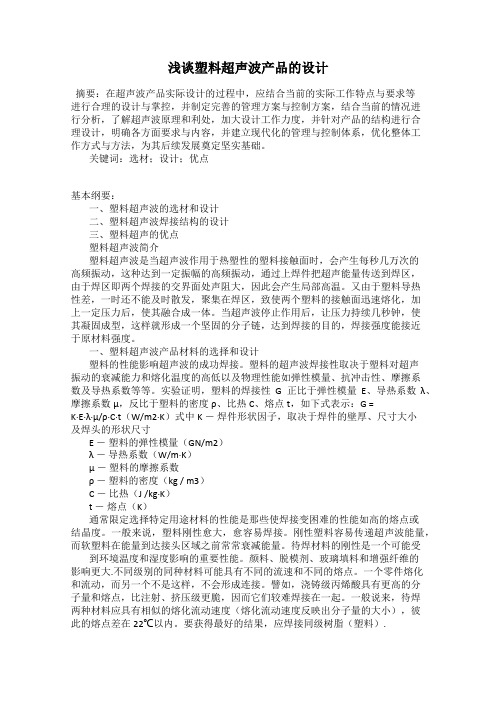
浅谈塑料超声波产品的设计摘要:在超声波产品实际设计的过程中,应结合当前的实际工作特点与要求等进行合理的设计与掌控,并制定完善的管理方案与控制方案,结合当前的情况进行分析,了解超声波原理和利处,加大设计工作力度,并针对产品的结构进行合理设计,明确各方面要求与内容,并建立现代化的管理与控制体系,优化整体工作方式与方法,为其后续发展奠定坚实基础。
关键词:选材;设计;优点基本纲要:一、塑料超声波的选材和设计二、塑料超声波焊接结构的设计三、塑料超声的优点塑料超声波简介塑料超声波是当超声波作用于热塑性的塑料接触面时,会产生每秒几万次的高频振动,这种达到一定振幅的高频振动,通过上焊件把超声能量传送到焊区,由于焊区即两个焊接的交界面处声阻大,因此会产生局部高温。
又由于塑料导热性差,一时还不能及时散发,聚集在焊区,致使两个塑料的接触面迅速熔化,加上一定压力后,使其融合成一体。
当超声波停止作用后,让压力持续几秒钟,使其凝固成型,这样就形成一个坚固的分子链,达到焊接的目的,焊接强度能接近于原材料强度。
一、塑料超声波产品材料的选择和设计塑料的性能影响超声波的成功焊接。
塑料的超声波焊接性取决于塑料对超声振动的衰减能力和熔化温度的高低以及物理性能如弹性模量、抗冲击性、摩擦系数及导热系数等等。
实验证明,塑料的焊接性G 正比于弹性模量E、导热系数λ、摩擦系数μ,反比于塑料的密度ρ、比热C、熔点t,如下式表示:G = K·E·λ·μ/ρ·C·t(W/m2·K)式中K -焊件形状因子,取决于焊件的壁厚、尺寸大小及焊头的形状尺寸E -塑料的弹性模量(GN/m2)λ -导热系数(W/m·K)μ -塑料的摩擦系数ρ -塑料的密度(kg / m3)C -比热(J /kg·K)t -熔点(K)通常限定选择特定用途材料的性能是那些使焊接变困难的性能如高的熔点或结晶度。
塑料超声波焊接结构

塑料超声波焊接结构摘要:I.塑料超声波焊接简介A.塑料焊接的定义B.超声波焊接的工作原理II.塑料超声波焊接结构分类A.结构形式1.点焊2.缝焊3.对接焊B.结构设计1.焊接模具2.超声波发生器3.焊接头III.塑料超声波焊接的应用领域A.电子行业B.汽车制造C.医疗设备D.包装行业IV.塑料超声波焊接的优势与局限A.优势1.焊接速度快2.焊接精度高3.节能环保B.局限1.焊接材料限制2.设备成本较高V.塑料超声波焊接技术的发展趋势A.自动化焊接B.超声波焊接新材料研究C.设备小型化、智能化正文:塑料超声波焊接是一种利用超声波振动能量将塑料材料熔接在一起的技术。
在塑料焊接中,超声波通过焊接模具传递到焊接材料上,使材料分子间产生摩擦热,从而实现熔接。
这种焊接方法具有速度快、精度高、节能环保等优点,广泛应用于电子、汽车、医疗设备、包装等行业。
塑料超声波焊接结构主要包括点焊、缝焊、对接焊等。
其中,点焊是在两个塑料部件的接触点产生焊接,常用于电子行业的连接器生产;缝焊是在两个塑料部件的接缝处进行焊接,广泛应用于汽车制造中的塑料零部件连接;对接焊是在两个塑料部件的端面进行焊接,常用于医疗设备和包装行业的容器及设备生产。
在塑料超声波焊接结构设计中,焊接模具、超声波发生器和焊接头是三个关键部件。
焊接模具用于固定待焊接的塑料部件,并传递超声波振动;超声波发生器产生超声波振动能量,通过焊接头传递给焊接材料;焊接头将振动能量集中于焊接部位,使塑料材料熔接在一起。
尽管塑料超声波焊接具有诸多优势,但也存在一定的局限性。
首先,焊接材料受到一定限制,仅适用于部分热塑性塑料;其次,设备成本较高,对生产成本有一定影响。
超声波模具的设计原理_概述说明以及解释

超声波模具的设计原理概述说明以及解释1. 引言1.1 概述超声波模具是一种应用超声波技术进行加工和成型的重要设备。
它可以通过超声波的传导和振动作用,有效地加工各种材料,并实现精确的形状控制和高效率生产。
随着现代科学技术的不断进步,超声波模具在许多领域得到了广泛应用,如塑料成型、金属焊接、食品加工等。
1.2 文章结构本文将首先介绍超声波原理简介,包括超声波的基本概念、传播方式以及其与材料相互作用的特点。
接着我们将详细阐述超声波模具的设计要点,包括模具结构、材料选择、连接方式等方面。
然后,我们将深入探讨模具设计原理与超声波相互作用关系,分析超声波对模具加工过程的影响和作用机制。
同时,还会介绍模具制备方法与工艺流程,并提出优化措施以提高生产效率和产品质量。
最后,我们将重点讨论在模具设计中需要考虑材料属性、结构特征、连接方式及节能效果评估等因素和挑战,并给出相应的解决方案。
1.3 目的本文的目的是系统地介绍超声波模具的设计原理、制备方法与工艺流程,分析模具设计中需考虑的因素和挑战,并总结重述主要观点和结果。
同时,对超声波模具设计提出启示和展望,为相关领域研究人员提供参考和借鉴。
通过全面而深入地探讨超声波模具的设计原理和实操经验,我们可以更好地理解超声波技术在工程领域的应用潜力,并为优化设计和改进工艺提供指导。
2. 超声波模具的设计原理2.1 超声波原理简介超声波是指频率高于人类听觉范围(20kHz)的机械振动波。
在超声波模具设计中,利用超声波的特性可以实现高效的材料切割、焊接和成型等工艺。
超声波通过在模具中产生机械振动,将能量传递给材料,从而实现所需的加工过程。
2.2 模具的设计要点在超声波模具设计中,需要考虑以下要点:- 模具形状和尺寸:根据加工要求和材料特性确定模具形状和尺寸,以确保超声波能够有效传递到待加工材料上。
- 超声波振动系统:选择合适的超声波振动系统,并确保其能够输出所需频率和幅度的振动。
关於超声波结构的设计要点

關於超聲波結構的設計要點看到論壇上有問到關於超聲波結構的設計問題,在這裡我把我的設計經驗拿出來和大家分享,不足之處,請大蝦們包涵。
超音波應用原理:利用超音波振動頻率,接觸摩擦產生熱能使塑膠熔融而結合,依目前較普遍的,即為每秒振動二萬次﹙20KHZ﹚與每秒振動1.5萬次﹙15KHZ﹚二種(另外尚有數種特殊振動頻率)。
一般來說,在設計超聲波結構之前,需考慮1.選擇什麼塑料?2.是否只需要結構性的熔接,如果需要的話,要求它能承受多少壓力?3.是否需要水氣密?4.是否有外觀上的要求?5.是否允許有任何溢膠/微粒的產生?6.是否還有其他特殊要求?等問題。
那超聲波結構設計中,最重要的就是熔接面的設計。
為了獲得可接受的、穩定性高的熔接效果,必需遵循下述三項基本設計準則:1.兩熔接面的最初接觸面積必須減小,以降低初期與最後的完全熔化所需要的總能量,使焊頭與工件的接觸時間降低至最少因而減低造成傷痕的機會,也因此減少溢膠;2.提供一種能使二熔接面相互對位的方式,在搭配塑件的設計中可採用插針與插孔,階梯或溝槽的方式,而不應採用固定在焊頭或底模內的方式,這樣可確保準確與穩定的對位並避免造成傷痕;3.整個熔接面必須均勻一致與緊密接觸,盡可能保持在同一平面,這樣的形狀能使能量均勻傳導,有利于取得一致的與可控制的熔接效果,並且能減低溢膠產生的可能性;熔接面有導熔線和剪切兩種主要設計類形[color]首先,先講講導熔線導:導熔線實際上是在二熔接面之一上形成一條三角形凸出材料,導熔線的基本作用是聚集能量並且迅速把要熔接的另一面熔解,導熔線能快速熔解並達到最高的熔接強度,原因是導熔線本身的材料熔解並且流到整個熔接區域,導熔線設計是非晶型材料所採用最廣泛的熔接面設計,當然半晶材料亦可採用這種設計.導熔線的尺寸和位置取決于以下因素:1.材料;2.熔接要求;3.工件大小;導熔線必須愈尖愈好,圓頂或扁平的導熔線將減低熔膠流動的效率,當熔接相對容易熔接的塑料(如高硬度和低熔解溫度的PS),建議導熔線的高度不可低于0.25㎜,若熔接半晶型或高熔解溫度之非晶型塑料(如PC),導熔線高度不可低于0.5㎜;對於採用導熔線設計的半晶型塑料(如PA),熔接強度是來自導熔線三角型的底線之寬度.頂角隨壁厚而改變;原則上導熔線設置在哪一邊的塑件的熔接面上是沒有任何分別的.但在熔接兩種不同材料的特殊情況下,一般是將導熔線設置在熔解溫度和硬度較高的那一邊的工件的熔接面上;導熔線的設計要有能相互對位的功能如插針與插孔,肋狀對位片,溝槽設計,或需要良好的支撐.熔接區域不可放置頂針;下面是幾種比較典型的導熔線的結構設計:階梯熔接面一階梯熔接面設計主要用于需要精確對位與完全不可接受過熔或溢膠出現在外露表面的高品質要求上;設計注意(圖1.)圍繞整個工件接口之額外0.25至0.64㎜的空隙,這新增的“影線(美工線)”設計特性使熔接完畢後接口四週將出現0.25至0.64㎜之空隙.如此會產生美觀的效應,因為工件與工件之間的變形不易被發覺.如果完全密合,很可能會在某些位置出現溢膠,在別的位置卻出現微隙;美工線的設置使微小的變形不易被察覺.這款導熔線設計採用與平頭加導熔線設計一樣的基本概念(就是:材料、熔接要求、工件大小).注意這款設計的壁厚要求最小尺寸為2㎜图片附件: 1.gif (2007-4-30 14:41, 10.02 K)溝槽式之熔接面設計—這種設計的主要優點是能從裹外二面防止溢膠,並且可提供對位功能.由於熔膠被封,因此提高達到水氣密的機會.也由於溝槽的設計需要一定的公差配合,因此也增加成型的困難度.同時,由於熔接面積的減少,往往造成它的熔接強度比不上平頭接面設計,這款導熔線設計採用與平頭加導熔線設計一樣的基本概念(就是:材料、熔接加工要求、工件大小).注意這款設計的壁厚要求最小尺吋為2㎜图片附件: 2.gif (2007-4-30 14:49, 13.02 K)咬花面設計--此設計是專為配合導熔線設計使用,熔接面有咬花形狀可改善整体熔接品質和強度,原因在于粗糙面能增進摩擦與控制熔解(圖 3.).通常咬花深度0.076至0.152㎜,其變化視導熔線高度而定.往往得到的優點包括強度的增進、溢膠或微粒的減少、熔接時間的減短以及振幅的減低;图片附件: 3.gif (2007-4-30 14:54, 10.42 K)十字交叉熔接面設計—在塑件的二熔接面上都設計導熔線並且使它們互呈垂直交叉,使初接觸面減至最低並使大量的塑料熔接以增加熔接強度(圖4).這種導熔線的每一段尺寸可採取標準導熔線尺寸的60%左右.若欲取得水氣密的熔接效果,建議一方的導熔線設計採用如圖5.所示之連續鉤齒狀.同時建議導熔線的頂角角度為600而非標準型的900,同時還建議把比鉤齒狀設計之導熔線設置在與焊頭接觸邊的塑件上.應注意的是,此款設計將產生大量的溢膠,因此必須考慮溢膠的問題或採用有溢料槽設計的熔接面如溝槽式的熔接面設計图片附件: 4.gif (2007-4-30 15:04, 6.42 K)图片附件: 5.gif (2007-4-30 15:04, 8.72 K)垂直于牆壁的導熔線設計—用于增加抗撕裂與減少溢膠(圖6),這種設計僅適用於只需要結構性的熔接而已;間斷的導熔線設計—可減少熔接面積因此降低能量或所需的功率層級,這種設計只能用于非水氣密的結構性熔接而已(圖7);图片附件: 6.gif (2007-4-30 15:12, 6.7 K)图片附件: 7.gif (2007-4-30 15:12, 7.22 K)鑿子型導熔線—為壁厚不及1.524㎜之工件所採用(圖10.)如果在此等薄壁厚之塑件上使用標准導熔線,熔接強度將會減弱.尖刀處可採0.381至0.508㎜之高度並且採用450角.由於熔接強度取決於導熔線之寬度,當採用此款導熔線設計時必須配合使用咬花面;图片附件: 8.gif (2007-4-30 15:16, 11.17 K)特殊熔接面設計—為了使較難熔接的塑料或外型不規則之塑件達到水氣密熔接,可能需要使用彈性油封與旋繞道以阻隔熔膠之流動.圖9.顯示一種配合“O”型環的熔接面設計.有一要點應注意“O”型環在熔接完畢后只壓縮10%至15%而已.柱狀塑件與插孔(大頭柱子熔接)亦可成功的配合“O”型環以達到水氣密;图片附件: 9.gif (2007-4-30 15:22, 4.29 K)下面再來介紹一下剪切的設計注意點:剪切式熔接面設計—在熔接尼龍、乙縮醛、聚乙烯、聚丙烯和熱塑性聚酯這類半晶型塑料時,採用導熔線設計有時是不能達到預期效果的.這是因為這類半晶型塑料在相對很狹窄的溫度變化範圍內迅速從固態再變回固態.導熔線熔化時還未來得及與對面塑件熔合即開始固化,因此熔接強度只賴由三角形之寬度所提供.因此當熔接以上塑料,如果外型許可的話的建議採用剪切式熔接面設計,可達到理想的熔接效果.剪切式熔接面的熔接過程是,首先熔化開始接觸的小面積材料,然後沿著壁面繼續垂直向下而有控制的導引入下工件裹頭去(請觀看圖10).這種熔接方式絕對不會讓四週的空氣接觸到熔解區域,因此可獲得高強度的結構性或水氣密的熔接.由于上述原因,剪切式熔接設計特別適用於半晶型塑膠材料;熔接強度與熔接面垂直向下的熔接面積有直接關系.強度可由改變熔接深度去達到個別應用的熔接要求.注意:若熔接強要求超過牆壁的接強,建議熔接深度為壁厚之1.25倍;剪切式熔接需要有堅固的側邊牆壁支撐以避免熔接時變形.下工件的四週牆壁高度必須高至接口位置,內壁必須與工件外部型体完全吻合.上工件的整体結構也應十分堅固以防止內傾變形.對於熔接部位在牆壁中央位置,可採用圖11.所示的變體溝槽設計.這種設計也適用于大型塑件的熔接.建議採用單邊干涉如圖12.所示图片附件: 10.gif (2007-4-30 15:35, 9.95 K)图片附件: 11.gif (2007-4-30 15:35, 3.69 K)图片附件: 12.gif (2007-4-30 15:35, 5.94 K)應當注意的是如果工件最大尺吋在89㎜或更大並且復雜或者有直角的轉角就不宜採用剪切式熔接設計,因為這會給上下工件之間所必須保持的成型公差帶來困擾.也就是難於保持穩定的熔接效果.在這種情況下只能建議採用導熔線設計.當只需要結構性熔接而已.(即不要求強度與水氣密),可採用圖13.所示的間斷性的垂直導熔線設計.如此可減少整個熔接面積,也因此減少所需的能量或功率.傷痕出現的機會亦可大大的減少圖14提供干涉尺吋與工件尺吋公差對應於最大之工件外形尺吋图片附件: 13.gif (2007-4-30 15:40, 7.3 K)图片附件: 14.gif (2007-4-30 15:43, 4.35 K)熔接面設計的其他考慮:1.直角轉角會聚集應力.如果塑件上面有若干應力聚集點,在經過超音波機械振動後,塑件的高應力區域如轉角、邊沿與交界處可能出現斷裂或其他的傷痕.補救的措施是儘量增加轉角之圓弧度(0.508㎜).請參閱圖152.塑件上的孔位或缺口像氣孔類的開口會阻斷焊頭傳送出來的超音波能量(圖16).它對熔接的影響取決于塑件材料種類(尤其是半晶型塑料)和開口的大小,在缺口的正下方幾乎沒有辦法熔接.當塑件上有缺口或有轉彎形狀,塑料將會阻礙能量的傳導,使能量更難到達熔接面,尤其是剪切式熔接.在塑件設計過程當中應特別注意避免此類問題的發生.由於鋼模設計不當造成塑件內出現氣孔,這種情況也會使能量傳導受阻或使塑件穿孔;3.近場與遠場熔接之對比一近場熔接指的是熔接面距離焊頭接觸位置在6.35㎜以內;大于6.35㎜的距離則為遠場熔接(圖17),如上所述,因為半晶型分子結構塑料會阻礙振動能量的傳導,所以難以對它們作遠場熔接.至於非晶型塑料,由於分子隨意排列,振動能量容易在其間傳導並且衰減也很小.在低硬度塑料裹頭也會發生振動能量的衰減現象.因此在設計塑膠產品過程當中應考慮到是否有足夠的能量傳達熔接面;图片附件: 15.gif (2007-4-30 15:52, 6.02 K)图片附件: 16.gif (2007-4-30 15:52, 9.93 K)图片附件: 17.gif (2007-4-30 15:52, 13.72 K)4.塑件的分肢,柄,或其他細節—機械振動會影響塑件內外表面上的各種突出物,可能造成斷裂(圖18.)下列各種措施能減低或消除這種影響:․將突出物與主体連接處設計成最大的圓弧狀.․利用外加手段削減連接處的扭折.․增加材料的厚度.․評估採用其他頻率的超音波5.薄膜效應—一種能量聚集效應造成塑件出現燒穿現象.在平的圓形的、壁厚較薄的位置最為常見,通過採取下列一個或結合數個措施可以克服這種現象(圖19)․減少熔接時間․改變振幅․採用振幅剖析․在焊頭上設計節點活塞․增加壁厚․使用內部支撐肋骨․評估其他頻率6.焊頭接觸與放置位置在塑件熔接時可扮演舉足輕重的角色.一般而言,焊頭的尺寸應該大到足以遮蓋整個工作,因此從頂直接施壓在熔接區域上,(圖20.)這有利于機械振動能量的傳導並可避免接觸面留下傷痕.焊頭或塑件的表面也可以在熔接區域凸起以增進接觸的效能;如此將改善熔接效果的穩定度,注意:焊頭與工件的接觸面必須大于熔接區域的總面積,否則將有可能導至表面傷痕.图片附件: 18.gif (2007-4-30 16:08, 7.8 K)图片附件: 19.gif (2007-4-30 16:08, 4.76 K)图片附件: 20.gif (2007-4-30 16:08, 12.5 K)另:1.相同熔點的塑膠材質熔接強度愈強。
超声波焊接结构设计

振动焊接结构
外侧无溢料
振动焊接结构
2mm壁厚5mm凸 沿,焊接2.4mm宽 1.5mm高
振动焊接结构
较小的厚度 包括凸沿的结构
振动焊接结构
典型应用 用于较薄容器 盖子的焊接
振动焊接结构
典型应用 用于较薄且有 压力容器盖子 的焊接
振动焊接结构
无凸沿产品的 焊接,常用于 ABS
振动焊接结构
用于高压力产品
(如储液容器)
振动焊接结构
典型应用 有凸沿,高压力 容器焊接
振动焊接结构
典型设计 避免在焊接过程 中产品产生晃动
振动焊接结构
典型焊接 把一个工件放入 另一工件内,在 一个焊接周期内 同时焊接
振动焊接结构
典型焊接 不同材料(金属过滤网) 在一起,使之熔为一体
低矮型
Low Profile Stake
Horn
D/2
0.6 D
1.5 D
0.25 D
Before
After
D = Stud diameter
超声铆接结构
半圆型铆接
Dome Stake
0.5 D
2.1 D
2D 0.5 D
Before
After
D = Stud diameter
超声铆接结构
( 0.5 )
0.37
0.4
45 °
超声焊接结构
阶梯型
Step Joint
0.40
0.03
( 0.30 )
0.17
0.20
超声焊接结构
阶梯型
Energy Director with Opposing Textured Surface
浅谈超声波焊接塑料件的设计塑料件
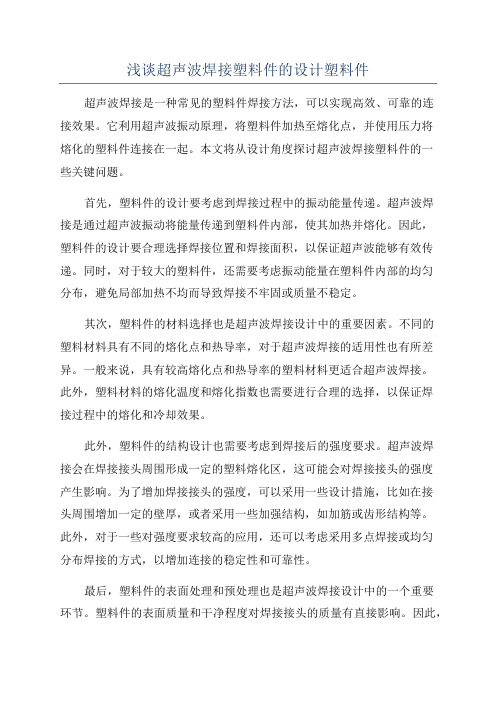
浅谈超声波焊接塑料件的设计塑料件超声波焊接是一种常见的塑料件焊接方法,可以实现高效、可靠的连接效果。
它利用超声波振动原理,将塑料件加热至熔化点,并使用压力将熔化的塑料件连接在一起。
本文将从设计角度探讨超声波焊接塑料件的一些关键问题。
首先,塑料件的设计要考虑到焊接过程中的振动能量传递。
超声波焊接是通过超声波振动将能量传递到塑料件内部,使其加热并熔化。
因此,塑料件的设计要合理选择焊接位置和焊接面积,以保证超声波能够有效传递。
同时,对于较大的塑料件,还需要考虑振动能量在塑料件内部的均匀分布,避免局部加热不均而导致焊接不牢固或质量不稳定。
其次,塑料件的材料选择也是超声波焊接设计中的重要因素。
不同的塑料材料具有不同的熔化点和热导率,对于超声波焊接的适用性也有所差异。
一般来说,具有较高熔化点和热导率的塑料材料更适合超声波焊接。
此外,塑料材料的熔化温度和熔化指数也需要进行合理的选择,以保证焊接过程中的熔化和冷却效果。
此外,塑料件的结构设计也需要考虑到焊接后的强度要求。
超声波焊接会在焊接接头周围形成一定的塑料熔化区,这可能会对焊接接头的强度产生影响。
为了增加焊接接头的强度,可以采用一些设计措施,比如在接头周围增加一定的壁厚,或者采用一些加强结构,如加筋或齿形结构等。
此外,对于一些对强度要求较高的应用,还可以考虑采用多点焊接或均匀分布焊接的方式,以增加连接的稳定性和可靠性。
最后,塑料件的表面处理和预处理也是超声波焊接设计中的一个重要环节。
塑料件的表面质量和干净程度对焊接接头的质量有直接影响。
因此,在进行超声波焊接之前,需要对接头表面进行适当的处理,如去除油污、杂质和氧化层等。
此外,还可以考虑采用一些增粘剂或者使用专用的焊接剂,以提高焊接接头的质量和品质。
总而言之,超声波焊接塑料件的设计需要综合考虑焊接过程中的振动能量传递、塑料材料的选择、结构设计的强度要求、表面处理和预处理等因素。
通过合理的设计,可以实现高效、稳定和可靠的超声波焊接效果,为塑料件的应用提供可靠的连接方式。
超声骨刀结构
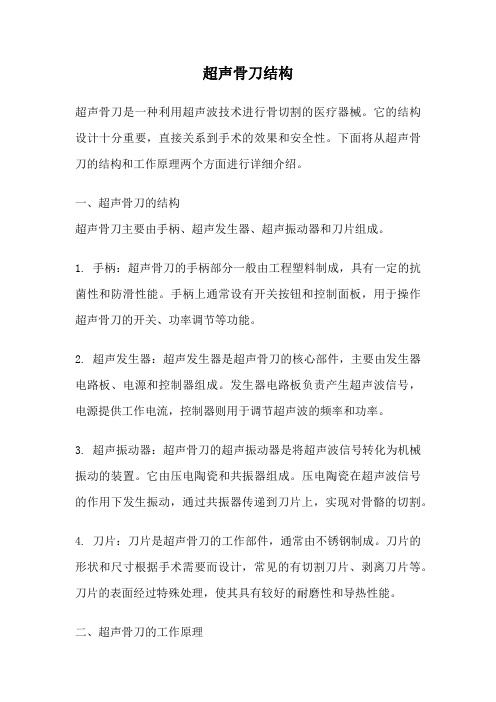
超声骨刀结构超声骨刀是一种利用超声波技术进行骨切割的医疗器械。
它的结构设计十分重要,直接关系到手术的效果和安全性。
下面将从超声骨刀的结构和工作原理两个方面进行详细介绍。
一、超声骨刀的结构超声骨刀主要由手柄、超声发生器、超声振动器和刀片组成。
1. 手柄:超声骨刀的手柄部分一般由工程塑料制成,具有一定的抗菌性和防滑性能。
手柄上通常设有开关按钮和控制面板,用于操作超声骨刀的开关、功率调节等功能。
2. 超声发生器:超声发生器是超声骨刀的核心部件,主要由发生器电路板、电源和控制器组成。
发生器电路板负责产生超声波信号,电源提供工作电流,控制器则用于调节超声波的频率和功率。
3. 超声振动器:超声骨刀的超声振动器是将超声波信号转化为机械振动的装置。
它由压电陶瓷和共振器组成。
压电陶瓷在超声波信号的作用下发生振动,通过共振器传递到刀片上,实现对骨骼的切割。
4. 刀片:刀片是超声骨刀的工作部件,通常由不锈钢制成。
刀片的形状和尺寸根据手术需要而设计,常见的有切割刀片、剥离刀片等。
刀片的表面经过特殊处理,使其具有较好的耐磨性和导热性能。
二、超声骨刀的工作原理超声骨刀利用超声波的机械振动和热效应来实现对骨骼的切割。
其工作原理可以分为以下几个步骤:1. 发生器产生超声波信号:超声骨刀的发生器电路板通过电流激励压电陶瓷,产生超声波信号。
控制器可以调节超声波的频率和功率,以适应不同手术需求。
2. 超声波信号传递到刀片:发生器产生的超声波信号通过超声振动器传递到刀片上。
超声振动器将电能转化为机械能,使刀片发生高频振动。
3. 刀片对骨骼施加振动力:刀片的高频振动使其对骨骼产生振动力,从而实现切割的效果。
此时,超声波的机械振动能量转化为骨骼内部的微小位移和应力,导致骨骼的断裂。
4. 热效应促进切割:除了机械振动效应外,超声骨刀还利用超声波的热效应来促进切割。
超声波的高频振动会产生摩擦热,局部升高刀片与骨骼接触面的温度,使骨骼蛋白质变性,进一步降低骨骼的强度,有利于切割。
超声波焊接塑料件的设计

超声波焊接塑料件的设计超声波焊接是一种常见的塑料焊接方法,它利用高频率的声波振动将塑料件的表面加热并压合,从而达到焊接的效果。
相比于传统的热熔焊接方法,超声波焊接具有快速、高效、环保、经济等优点,因此得到了广泛的应用。
在超声波焊接塑料件时,为了保证焊接效果,需要对塑料件的设计进行一定的考虑。
下面将探讨超声波焊接塑料件设计的一些要素。
1、材料选择超声波焊接适用于大部分塑料材料,例如ABS、PP、PE、PC等。
在选择材料时需要考虑到材料熔点、熔体流动性、工艺操作温度等因素。
同时也需要考虑到塑料件的用途和环境因素等。
不同的材料可能会呈现不同的熔化状态,选择合适的材料有助于提高焊接效果。
2、结构设计超声波焊接的结构设计需要考虑到焊接面积、夹紧方式、固定件的形态等因素。
同时还需要考虑到焊接面的平整度,避免因平整度不良导致焊接质量下降。
以及线缆的合理布局等因素。
3、设计焊接区域超声波焊接时需要将塑料件的焊接区域考虑在内,这通常要求在设计时将两个零件上的边缘设计成接触面。
在设计过程时也要注意一些特殊的形状,例如圆形、锥形、椭圆形等比较特殊的零件设计。
4、加强件的设计在一些合并的塑料件上设计加强件,能够帮助增强焊点的强度,提升焊接的质量。
例如在汽车零部件、家电等领域,经常使用加强件来增强焊点的结构强度。
5、生产工艺考虑在设计时还需要考虑到生产工艺方面,例如机器设备的限制、操作人员工艺水平等因素。
这需要对焊接过程进行一定的分析,为生产提供方便实用的方案。
总之,超声波焊接塑料件设计需要综合考虑塑料材料、加强件、结构、焊接区域等方面。
设计优秀的塑料件有助于提高超声波焊接的质量和效率。
- 1、下载文档前请自行甄别文档内容的完整性,平台不提供额外的编辑、内容补充、找答案等附加服务。
- 2、"仅部分预览"的文档,不可在线预览部分如存在完整性等问题,可反馈申请退款(可完整预览的文档不适用该条件!)。
- 3、如文档侵犯您的权益,请联系客服反馈,我们会尽快为您处理(人工客服工作时间:9:00-18:30)。
.1塑料件的结构
塑料件必须有一定的刚性及足够的壁厚,太薄的壁厚有一定的危险性,超声波焊接时是需要加压的,一般气压为2-6kgf/cm2 。
所以塑料件必须保证在加压情况下基本不变形。
1.2罐状或箱形塑料等,在其接触焊头的表面会引起共振而形成一些集中的能量聚集点,从而产生烧伤、穿孔的情况(如图1所示),在设计时可以罐状顶部做如下考虑
○1 加厚塑料件
○2 增加加强筋
○3 焊头中间位置避空
1.3尖角
如果一个注塑出来的零件出现应力非常集中的情况,比如尖角位,在超声波的作用下会产生折裂、融化。
这种情况可考虑在尖角位加R角。
如图2所示。
1.4塑料件的附属物
注塑件内部或外部表面附带的突出或细小件会因超声波振动产生影响而断裂或脱落,例如固定梢等(如图3所示)。
通过以下设计可尽可能减小或消除这种问题:
○1 在附属物与主体相交的地方加一个大的R角,或加加强筋。
○2 增加附属物的厚度或直径。
1.5塑料件孔和间隙
如被焊头接触的零件有孔或其它开口,则在超声波传递过程中会产生干扰和衰减(如图4所示),根据材料类型(尤其是半晶体材料)和孔大小,在开口的下端会直接出现少量焊接或完全熔不到的情况,因此要尽量预以避免。
1.6塑料件中薄而弯曲的传递结构
被焊头接触的塑件的形状中,如果有薄而弯曲的结构,而且需要用来传达室递超声波能量的时候,特别对于半晶体材料,超声波震动很难传递到加工面(如图5所示),对这种设计应尽量避免。
1.7近距离和远距离焊接
近距离焊接指被焊接位距离焊头接触位在6mm以内,远距离焊接则大于6mm,超声波焊接中的能量在塑料件传递时会被衰减地传递。
衰减在低硬底塑料里也较厉害,因此,设计时要特别注意要让足够的能量传到加工区域。
远距离焊接,对硬胶(如PS,ABS,AS,PMMA)等比较适合,一些半晶体塑料(如POM,PETP,PBTB,PA)通过合适的形状设计也可用于远距离焊接。
1.8塑料件焊头接触面的设计
注塑件可以设计成任何形状,但是超声波焊头并不能随意制作。
形状、长短均可能影响焊头频率、振幅等参数。
焊头的设计需要有一个基准面,即按照其工作频率决定的基准频率面。
基准频率面一般占到焊头表面的70%以上的面积,所以,注塑件表面的突超等形状最好小于整个塑料面的30%。
一滑、圆弧过渡的塑料件表面,则比标准可以适当放宽,且突出位尽量位于塑料件的中部或对称设计。
塑料件焊头接触面至少大于熔接面,且尽量对正焊接位,过小的焊头接触面(如图6所示),会引起较大损伤和变形,以及不理想的熔接效果。
在焊头表面有损伤纹,或其形状与塑料件配合有少许差异的情况下,焊接时,会在塑料件表面留下伤痕。
避免方法是:在焊头与塑料件表面之间垫薄膜(例如PE膜等)。
焊接线的设计
焊接线是超声波直接作用熔化的部分,其基本的两种设计方式:
○1能量导向
○2 剪切设计
2.1能量导向
能量导向是一种典型的在将被子焊接的一个面注塑出突超三角形柱,能量导向的基本功能是:集中能量,使其快速软化和熔化接触面。
能量导向允许快速焊接,同时获得最大的力度,在这种导向中,其材料大部分流向接触面,能量导向是非晶态材料中最常用的方法。
能量导向柱的大小和位置取决于如下几点:
○1 材料
○2 塑料件结构
○3 使用要求
图7所示为能量导向柱的典型尺寸,当使用较易焊接的材料,如聚苯乙烯等硬度高、熔点低的材料时,建议高度最低为0.25mm。
当材料为半晶体材料或高温混合树脂时(如聚乙碳),则高度至少要为0.5mm,当用能量导向来焊接半晶体树脂时(如乙缩荃、尼龙),最大的连接力主要从能量柱的底盘宽带度来获得。
没有规则说明能量导向应做在塑料件哪一面,特殊情况要通过实验来确定,当两个塑料件材质,强度不同时,能量导向一般设置在熔点高和强度低的一面。
根据塑料件要求(例如水密、气密性、强度等),能量导向设计可以组合、分段设计,例如:只是需要一定的强度的情况下,分段能量导向经常采用(例如手机电池等),如图8所示。
2.2能量导向设计中对位方式的设计
上下塑料件在焊接过程中都要保证对位准确,限位高度一般不低于1mm,上下塑料平行检动位必须很小,一般小于0.05mm,基本的能量导向可合并为连接设计,而不是简单的对接,包括对位方式,采用能量导向的不同连接设计的例子包括以下几种:
插销定位:图9所示为基本的插销定位方式,插销定位中应保证插销件的强度,防此超声波震断。
台阶定位:图10所示为基本的台阶定位方式,如h大于焊线的高度,则会在塑料件外部形成一条装饰线,一般装饰线的大小为0.25mm 左右,创出更吸引人的外观,而两个零件之间的差异就不易发现。
图11所示台阶定位,则可能产生外溢料。
图12所示台阶定位,则可能产生内溢料。
图13所示台阶定位为双面定位,可防止内外
溢料。
○1 企口定位:如图14所示,采用这种设计的好处是防止内外溢料,并提供校准,材料容易有加强密封性的获得,但这种方法要求保证凸出零件的斜位缝隙,因此使零件更难能可贵于注塑,同时,减小于焊接面,强度不如直接完全对接。
○2 底模定痊:如图15所示,采用这种设计,塑料件的设计变得简单,但对底模要求高,通常会引致塑料件的平行移位,同时底模固定太紧会影响生产效果。
○3 焊头加底模定位:如图16所示,采用这种设计一般用于特殊情况,并不实用及常用。
○4 其它情况:
A:如图17所示,为大型塑料件可用的一种方式,应注意的是下支撑模具必须支撑住凸缘,上塑料件凸缘必须接触焊头,上塑料件的上表面离凸缘不能太远,如必要情况下,可采用多焊头结构。
B:如连接中采用能量导向,且将两个焊面注成磨砂表面,可增加摩擦和控制熔化,改善整个焊接的质量和力度,通常磨砂深度是0.07mm-0.15mm。
C:在焊接不易熔接的树脂或不规则形状时,为了获得密封效果,则有必要插入一个密封圈,如图18所示,需要注意的是密封圈只压在焊接末端。
图19所示为薄壁零件的焊接,比如热成形的硬纸板(带塑料涂层),与一个塑料盖的焊接。
2.3剪切式设计
在半晶体塑料(如尼龙、乙缩醛、聚丙烯、聚乙烯和热塑聚脂)的熔接中,采用能量导向的连接设计也许达不到理想的效果,这是因为半晶体的树脂会很快从固态转变成融化状态,或者说从融化状态转化为固态。
而且是经过一个相对狭窄的温度范围,从能量导
向柱流出的融化物在还没与相接界面融合时,又将很快再固化。
因此,在这种情况下,只要几何原理允许,我们推荐使用剪切连接的结构。
采用剪切连接的设计,首先是熔化小的和最初触的区域来完成焊接,然后当零件嵌入到下起时,继续沿着其垂直壁,用受控的接触面来融化。
如图20所示,这样可能性获得强劲结构或很好的密封效果,因为界面的熔化区域不会让周围的空气进来。
由于此原因,剪切连接尤其对半晶体树脂非常有用。
剪切连接的熔接深度是可以调节的,深度不同所获得的强度不同,熔接深度一般建议为0.8-1.5mm,当塑件壁厚及较厚及强度要求高时,熔接深度建议为1.25X壁厚。
图21所示为几种基本的剪切式结构:
剪切连接要求一个塑料壁面有足够强度能支持及防止焊接中的偏差,有需要时,底模的支撑高于焊接位,提供辅助的支撑。
下表所示为零件大小尺寸和接触面、零件误差的大概尺寸:
零件最大尺寸接触面尺寸零件尺寸允许误差
<18mm 0.2mm-0.3mm ±0.025mm
18mm-35mm 0.3mm-0.4mm ±0.05mm
>35mm 0.4mm-0.6mm ±0.075mm
当零件尺寸大于90mm时,或零件有不规则的形状时,建议不采用剪切连接。
这时因为注塑时很难控制误差及变形使其保持一致。
如果是上述情况,建议采用能量导向的形式。
图22所示为双面剪切式设计
图23所示为扣式焊线设计,用于高强度,但上下塑料件不接触的情况下,在特殊情况下,可用于增加密封圈的情况。